Расчёт установки для приготовления моющих растворов


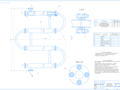
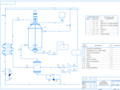
- Добавлен: 24.01.2023
- Размер: 347 KB
- Закачек: 1
Узнать, как скачать этот материал
Подписаться на ежедневные обновления каталога:
Описание
Расчёт установки для приготовления моющих растворов
Состав проекта
![]() |
![]() |
![]() ![]() ![]() ![]() |
![]() ![]() ![]() ![]() |
![]() ![]() ![]() |
Дополнительная информация
Контент чертежей
Лист№2.cdw

При изготовлении аппарата руководствоваться ОСт-26-01-112-79
Корпус аппарата и детали
изготовить из стали 1Х18Н10Т ГОСТ5832-72
детали из стали Ст 3сп. ГОСт 380-71
Аппарат испытать на прочность и плотность гидравлически в
горизонтальном положении под давлением 0.9 МПа.
Аппарат подлежит приемке согласно правилам Гостехнадзора.
Сварные соединения контролировать ренгеносвечением в объеме
0% по ОСТ26-291-71. Сварные соединения нержавеющей стали
контролировать на стойкость против межкристаллитной корозии
Техническая характеристика
Аппарат предназначен для подогрева воды до температы 30
Производительность по исходному продукту 900 кгч.
Поверхность теплообмена 0
Болт М8 ГОСТ 7798-70
Гайка М10 ГОСТ 5515-70
Вход исходного продукта
Выход нагретого продукта
Лист№1.cdw

Вода после 1-й стадии подогрева
Вода после 2-й стадии подогрева
Аппарат для перемешивания
Подогреватель типа "Труба в трубе
Спиральный регенератор
Вентиль регулирующий
Технологическая схема
ПРОПЕЛЛЕРНАЯ.doc
Технические описания и расчёты . ..
1.Описание принципа работы технологической схемы
2.Описание принципа работы проектируемого аппарата
3.Материальный расчёт установки ..
4. Конструктивный расчёт аппарата .
5.Тепловой расчёт установки
6.Расчёт комплектующего оборудования
6.1.Расчет подогревателя типа «труба в трубе»
6.2.Расчет спирального регенератора
7.Гидравлический расчёт продуктовой линии и подбор нагнетательного оборудования .
Требование техники безопасности и ПС .. ..
Список использованных источников .. . .
Перемешивание — это вспомогательный процесс применяющийся в пищевой промышленности для приготовления эмульсий суспензий смесей гомогенизации растворов а также интенсификации тепло- и массообменных процессов химических и биохимических реакций.
Осуществление процесса перемешивания требует подвода энергии. При этом достигается определенный эффект — увеличение производительности или при той же производительности повышение качества готового продукта и увеличение его выхода за счет более полного использования сырья.
Чтобы оценить эффективность перемешивания достигаемый технологический эффект сопоставляют с расходом энергии на перемешивание. Эффективнее то перемешивающее устройство которое при том же расходе энергии обеспечивает больший эффект или для достижения аналогичного эффекта требует меньше энергии.
Ввиду многообразия технологических процессов разнообразны и получаемые технологические эффекты что затрудняет сравнение эффективности различных перемешивающих устройств и способов перемешивания. Поэтому качество перемешивания обычно оценивают по таким показателям:
при суспендировании и гомогенизации — по степени однородности системы;
при интенсификации теплообмена — по величине коэффициента теплоотдачи;
при интенсификации массообмена — по значению коэффициента массоотдачи.
Поскольку оценить эффективность перемешивания бывает сложно расчет процесса зачастую сводится к определению расхода энергии на перемешивание с целью подбора соответствующего ее источника.
В зависимости от агрегатного состояния перемешиваемого объекта различают перемешивание жидких сред газов а также сыпучих материалов и пластических масс. В настоящее время разработаны основы теории расчета лишь для перемешивания жидких сред. Оно бывает механическим поточным и пневматическим.
Механическое перемешивание производится в аппаратах с механическими перемешивающими устройствами.
Поточное перемешивание применяется для перемешивания хорошо
растворимых жидкостей.
Пневматическое перемешивание осуществляется газами (чаще всего воздухом) или водяным паром. Пневматическое перемешивание широко используется в микробиологической и бродильной промышленности при культивировании микроорганизмов.
Аппараты с перемешивающими устройствами являются наиболее распространенным видом оборудования используемого в пищевой промышленности для проведения различных физических и химических процессов. Выбор аппаратов с перемешивающими устройствами и конструктивные особенности аппаратов определяются характеристикой процесса свойствами перемешиваемой среды производительностью технологической линии температурными параметрами — процесса и давлением при котором процесс осуществляется. В задании по курсовому проектированию предложен аппарат с механическим перемешивающим устройством.
И так рассмотрим конструкции перемешивающих устройств. Механические перемешивающие устройства в большинстве случаев являются устройствами вращающегося типа и включают рабочий орган (мешалку) привод и вал передающий вращение от привода к мешалке. Наряду с ними существуют виброперемешивающие устройства с возвратно-поступательным движением рабочего органа.
При работе перемешивающих устройств среда приводится в движение что и вызывает ее перемешивание. Характер движения среды зависит от конструкции и параметров движения перемешивающего устройства а также от конструкции аппарата в котором происходит процесс.
Для вертикальных аппаратов с вращающимися механическими перемешивающими устройствами разработан ГОСТ 20680—75. Он распространяется на аппараты объемом от 001 до 100 м3 предназначенные для проведения различных физико-химических процессов в жидких средах с динамической вязкостью не более 500 Па-с и плотностью до 2000 кгм при температуре рабочей среды — 40 +350°С и условном давлении не менее 067 Па и не более 64 МПа.
Мешалки аппарата должны быть расположены вертикально по оси аппарата. Допускается установка на одном валу двух и более мешалок. Согласно стандарту аппараты изготовляются десяти типов:
(1)— с эллиптическим днищем и крышкой;
(3) — с коническим отбортованным днищем (угол при вершине конуса 90°) и эллиптической крышкой;
(5) — с эллиптическим днищем и плоской крышкой;
(7) — с коническим неотбортованным днищем (угол при вершине конуса 120°) и плоской крышкой;
(9) — с плоским днищем и плоской крышкой.
Аппараты типов 0 24 6 8 имеют отъемную крышку а типов 13 5 7 9 — неразъемный корпус.
В зависимости от конструкции теплообменных устройств различают аппараты с гладкой приварной рубашкой рубашкой из полутруб рубашкой с вмятинами отъемной рубашкой с электронагревателем. Давление теплоносителя в теплообменнике должно соответствовать ряду МПа: 04; 06; 10; 16; 25; 32; 40; 64.
Приводы мешалок следует устанавливать на крышке аппарата но допускается установка и на отдельной металлоконструкции либо на днище. Внутри аппарата могут располагаться отражательные перегородки змеевики направляющие трубы барботеры.
Оптимальной является конструкция перемешивающего устройства которая позволяет достичь требуемого качества перемешивания при минимальных затратах энергии в кратчайший срок. Для маловязких жидкостей обычно используют быстроходные мешалки. Винтовые (пропеллерные) мешалки обеспечивают достаточно интенсивное перемешивание при сравнительно низкой энергоемкости.
Для оптимизации процесса перемешивания (восстановления) сухого молока при минимальных затратах энергии в кратчайший срок целесообразно использовать быстроходные мешалки а точнее пропеллерную т.к. динамическая вязкость восстановленного продукта = 05743× 10-3 Па×с.
Рабочей частью пропеллерной мешалки является пропеллер (рис. 1)— устройство с несколькими фасонными лопастями изогнутыми по профилю гребного винта. Наибольшее распространение получили трехлопастные пропеллеры. На валу мешалки который может быть расположен вертикально горизонтально или наклонно в зависимости от высоты слоя жидкости устанавливают один или несколько пропеллеров.
Вследствие более обтекаемой формы пропеллерные мешалки при одинаковом числе Рейнольдса потребляют меньшую мощность чем мешалки прочих типов что является одним из ее достоинств. Переход в автомодельную область для них наблюдается при относительно низких значениях критерия Рейнольдса (ReM ~ 10 4). К достоинствам пропеллерных мешалок следует отнести также относительно высокую скорость вращения и возможность непосредственного присоединения мешалки к электродвигателю что приводит к уменьшению механических потерь.
Рисунок 1 – пропеллерная мешалка
Пропеллерные мешалки создают преимущественно осевые потоки перемешиваемой среды и как следствие этого— большой насосный эффект что позволяет существенно сократить продолжительность перемешивания. Вместе с тем пропеллерные мешалки отличаются сложностью конструкции и сравнительно высокой стоимостью изготовления. Их эффективность сильно зависит от формы аппарата и расположения в нем мешалки. Пропеллерные мешалки следует применять в цилиндрических аппаратах с выпуклыми днищами. При установке их в прямоугольных баках или аппаратах с плоскими или вогнутыми днищами интенсивность перемешивания падает вследствие образования застойных зон.
Для улучшения перемешивания больших объемов жидкостей и организации направленного течения жидкости (при большом отношении высоты к диаметру аппарата) в сосудах устанавливают направляющий аппарат или диффузор.
Диффузор представляет собой короткий цилиндрический или конический стакан внутри которого помещают мешалку. При больших скоростях вращения мешалки в отсутствие диффузора в аппарате устанавливают отражательные перегородки.
Пропеллерные мешалки применяют для перемешивания жидкостей вязкостью не более 2 -103 мн*секм 2 для растворения образования взвесей быстрого перемешивания проведения химических реакций в жидкой среде образования маловязких эмульсий и гомогенизации больших объемов жидкости.
Для пропеллерных мешалок принимают следующие соотношения основных размеров: диаметр мешалки и — (02—05) D шаг винта s = — (10—30) D расстояние от мешалки до дна сосуда h = (05—l0)d и высота уровня жидкости в сосуде Н = (08—12) D. Число оборотов пропеллерных мешалок достигает 40 в секунду окружная скорость — 15 мсек.
Рисунок 2 – Лопастные мешалки: а) различный наклон лопастей; б) устройство лопастей; в) парные лопасти; г) мешалка с отражателями; д) решетчатая мешалка
Перемешивание применяется для образования эмульсий и суспензий и является средством для создания контакта между реагирующими массами жидкости и твердыми телами. Разнообразные случаи применения перемешивания могут быть классифицированы следующим образом:
)перемешивание в жидкой среде;
)перемешивание сыпучих масс;
)перемешивание пластических масс.
Так как массо- и теплообмен химические и биохимические процессы играют большую роль в пищевых производствах перемешивание широко применяется на предприятиях пищевой промышленности.
Перемешивание в жидкой среде может быть осуществлено одним из трех способов: механическим поточным пневматическим. Механическое перемешивание производится при помощи механизмов — мешалок; поточное — путем перемешивания жидких потоков в специальных смесителях; пневматическое перемешивание осуществляется за счет энергии газовых или паровых струй поступающих в жидкую массу.
Механическое перемешивание
Применяемые в пищевых производствах мешалки могут быть разделены на три основные группы: лопастные пропеллерные и турбинные. Кроме этих основных групп имеются еще некоторые конструкции не укладывающиеся в эту классификацию.
Лопастные мешалки. Лопастные мешалки имеют наиболее простую по
сравнению с другими конструкцию. Используются для перемешивания в этих аппаратах представляют собой плоские лопасти установленные перпендикулярно или наклонно к направлению движения.
Лопасти посажены на вращающийся вертикальный или горизонтальный вал в одной плоскости может находиться от 1 до 3 лопастей.
Рисунок 3 – Якорная мешалка
Количество рядов лопастей по высоте также различно обычно от 1 до 5. Форма лопастей может быть разнообразной начиная от простого прямоугольника до фигур весьма сложной конфигурации. Употребляются решетчатые якорные и другие лопасти. Выбор типа лопастей определяется характером перемешиваемой среды. Так якорные мешалки (рис. VII-2) применяются для перемешивания систем выделяющих осадок.
Для предотвращения вращательного движения жидкости вместе с лопастями (особенно при перемешивании вязких жидкостей) устанавливают отражатели.
При вращении мешалок поверхность жидкости приобретает форму параболоида глубина которого увеличивается с возрастанием частоты вращения лопастные мешалки делают не более 400 обмин. Обычная частота вращения 20—80 обмин.
Достоинством лопастных мешалок является простота устройства. Однако они не обеспечивают хорошего перемешивания в направлении перпендикулярном плоскости лопасти. Если лопасти установлены перпендикулярно направлению движения то они не обеспечивают удерживания частиц суспензии во взвешенном состоянии особенно если плотность частиц велика а вязкость жидкости мала.
Простые лопастные мешалки более всего пригодны для перемешивания маловязких жидкостей.
Для перемешивания более вязких жидкостей рекомендуются рамные мешалки или мешалки в сосудах с отражательными перегородками.
Эффективное перемешивание обеспечивает лопастная планетарная мешалка однако она сложна по конструкции.
Рисунок 4 – Планетарная мешалка: 1) неподвижное зубчатое колесо; 2) подвижное зубчатое колесо; 3) водило
Рисунок 5 – Пропеллерная мешалка
Пропеллерные мешалки имеют в качестве рабочего органа винт (пропеллер) насаженный на вертикальную или горизонтальную ось. Диаметр винта составляет обычно от 13 до 14 диаметра сосуда в котором производится перемешивание. Винты применяются двух- и трехлопастные.
Рисунок 6 – Турбинная мешалка
Благодаря изменяющемуся углу наклона лопастей по их длине частицы жидкости отталкиваются винтом по многим направлениям. Вследствие этого возникают встречные струи жидкости что обеспечивает хорошее перемешивание.
Для придания осевого направления потоку жидкости создаваемому пропеллером последний располагают иногда в коротком цилиндре с раструбом а для лучшего перемешивания на одной оси устанавливают два винта образующих встречные потоки. Частота вращения этих мешалок 150—1000 обмин.
Рисунок 7 – Основные типы смесителей для сыпучих тел: 1) лопастные; 2) и 3) шнековые; 4) барабанные; 5) ударные
Пропеллерные мешалки целесообразно применять для подвижных и умеренно вязких (до 6 Па×с) жидкостей. По сравнению с лопастными эти мешалки эффективнее но потребляют больше энергии. При направлении потока жидкости ко дну они хорошо взмучивают осадок с частицами до 015 мм. Эффективность мешалок повышает наклонное расположение оси винта.
Турбинные мешалки. Рабочим органом турбинных мешалок является турбинное колесо (турбинка) вращающееся на вертикальной оси. Колесо делает от 200 до 2000 обмин. Работа его аналогична работе колеса центробежного насоса. Жидкость входит в колесо по оси через центральные отверстия и получая ускорение от лопаток выбрасывается из колеса в радиальном направлении. Вращающееся колесо нередко устанавливают внутри неподвижного направляющего колеса с лопатками. Назначение этого колеса — плавно изменять направление жидкого потока и уменьшать гидравлические потери. Для лучшего перемешивания на вал мешалки насаживают две турбинки.
Турбинные мешалки — весьма эффективные аппараты. Они пригодны для перемешивания жидкостей как с малой так и с большой (до 500 Па×с) вязкостью. Эти мешалки могут применяться для взмучивания осадков в жидкостях содержащих до 60 % твердой фазы. Турбинные мешалки также используют для перемешивания в жидкостях сыпучих тел с частицами до 25 мм.
Основную трудность при выборе перемешивающего устройства представляет согласование особенностей конструкции мешалки с параметрами технологического процесса.
В процессе перемешивания возникают потоки жидкости различных направлений — радиальные аксиальные тангенциальные. Мешалка является своего рода насосом и может подобно ему характеризоваться напором и подачей. Более высокий напор соответствует большей скорости потоков и обеспечивает в них большую степень турбулентности; подача определяет циркуляцию среды в аппарате. Высокая степень турбулентности необходима для процессов протекающих на микроуровне а интенсивная циркуляция — для процессов скорость которых лимитируется переносом на макроуровне. Так для гомогенизации хорошо смешивающихся жидкостей нужна интенсивная циркуляция а для тепло- и массообменных процессов — высокая степень турбулентности.
Для интенсивного протекания технологического процесса важны оба фактора однако отношения между ними различны в зависимости от того какое явление лимитирует процесс.
Лопастные мешалки рекомендуется применять при перемешивании с целью суспендирования растворения и при проведении химических реакций. Они просты по устройству но работают недостаточно интенсивно.
Рисунок 8 – Лопастный шнек
Турбинные мешалки используют во всех случаях когда необходимо интенсивное перемешивание особенно жидкостей значительно различающихся по вязкости а также при диспергировании газа в жидкости.
Винтовые (пропеллерные) мешалки обеспечивают достаточно интенсивное перемешивание при сравнительно низкой энергоемкости.
Якорные мешалки целесообразно применять для интенсификации теплообмена и предотвращения выпадения осадка.
Рамные мешалки используют в случаях когда необходимо обеспечить более интенсивное перемешивание по высоте а также при перемешивании вязких жидкостей в большом объеме.
Шнековые и ленточные мешалки применяют для перемешивания вязких жидкостей.
Поточное перемешивание.
Рисунок 9 – Поточные мешалки
Механические мешалки как правило работают периодически а поточные — непрерывно. В этих мешалках создается тесное соприкосновение потоков двух или большего числа жидкостей. Для этой цели применяют смесители снабженные перегородками или инжекторные устройства.
На рисунке изображены поточные мешалки применяемые в спиртовом производстве для смешивания патоки и воды.
Рисунок 10 – Эжекторный смеситель
На рисунке показан эжекторный смеситель для смешивания воды и дрожжевой суспензии.
Пневматическое перемешивание применяется для жидкостей вязкость которых не очень высока (приблизительно до 200 Па-с) а также для зерна при замачивании его в воде (при производстве солода).
Рисунок 11 – Пневматический перемешиватель
Иногда перемешивание производится паром тогда перемешиваемая жидкость одновременно подогревается. При пневматическом перемешивании газ или пар поступает в жидкость через отверстия сопла (барботёра). При этом струи газа (пара) распадаются на пузыри поднимающиеся в массе жидкости. Барботеры применяемые при перемешивании весьма разнообразны. Если при перемешивании необходимо одновременно привести в тесное соприкосновение газ и жидкость барботер устраивают со сложным распределением газа и с малыми отверстиями. Для перемешивания сыпучих тел (зерна) пневматическим способом используется принцип действия газоструйного насоса. Воздух подается компрессором в центральную трубу. При этом в трубе образуется смесь газа жидкости и зерна плотность которой меньше плотности смеси находящейся в остальном сосуде.
Технические описания и расчеты
1 Описание принципа работы технологической схемы
В данной технологической схеме (разработанной по заданию) осуществляется приготовление моющих растворов.
Вода которая подается из водопровода нагревается до температуры 30 С и с такой же температурой поступает в аппарат с пропеллерной мешалкой. Туда же со склада с температурой 15С через люк подается кальцинированная сода.
Из опытных данных известно что наиболее эффективнее процесс смешивания соды с водой происходит при температуре (50-60) С. Для подогрева кальцинированной соды воды и для ведения процесса при 55 С проектируемый аппарат обязательно должен содержать нагревательный элемент. На данной технологической схеме этот нагревательный элемент реализован в виде рубашки и внутреннего змеевика в которые непрерывно подается пар с давлением 03 МПа.
2 Описание принципа работы проектируемого аппарата
Сода в количестве 200 кг и вода 1800 кг подаются в аппарат с мешалкой где происходит растворение соды и приготовление моющего раствора. Аппарат содержит наружную однотельную теплообменную рубашку и внутренний змеевик куда подается пар с температурой 13354С.
В течении часа делают 2 загрузки в итоге получают 2 тонны моющего раствора.
3 Материальный расчёт установки
ХАХВХС – концентрации соды;
GА – расход воды кг;
GВ – расход соды кг;
GС – расход по готовому продукту кг.
Уравнение материального баланса по готовому продукту:
С учётом того что ХА = 0 GB×XB = GC×XC
- система уравнений материального баланса процесса смешивания.
Расход воды поступающей в аппарат для перемешивания равен 1800 кг расход соды – 200 кг. Принимаем что в аппарате единовременно приготавливается 1000 кг раствора: 900 кг воды и 100 кг соды. Время загрузки – 2 минуты время необходимое на обогрев аппарата – 6 мин время на ведение процесса – 15 мин время выгрузки – 2 мин.
4 Конструктивный расчёт аппарата
В аппарат подаётся 900 кг воды и 100 кг соды.
Вода при температуре 30°С имеет плотность 996 кгм³[3 стр.537 табл.39]
Сода при температуре 15°С имеет плотность 1450кгм³[7]
Рабочий обьем аппарата:
Геометрический обьем аппарата:
φ- коэффициент заполнения который принимается для аппаратов с мешалкой от 06 до 08
По значению геометрического объёма подбираем стандартный аппарат ближайшего размера VАП = 4 м3 D=1400мм (Таблица 17 [1]).
высота аппарата с мешалкой равна
Площадь и объём боковой поверхности аппарата
Fбок = 2pRH=2×314×07×26=1143(м2);
Vбок = Fбок ×dст =1143×0004=0046(м3);
Площадь и объем рубашки:
Fруб = 2pRH=2×314×0414×26=676(м2);
Vруб = Fруб ×dст =676×0003=002(м3);
Площадь и объём днища аппарата
Fдн = pR2 =314×072 =154(м2);
Vдн = Fдн ×dст =154×0004=00062(м3);
МАП = VАП ×rст =( Vбок + Vруб + Vдн )×rст =(0046+002+00062)×7900=570 кг
Расчёт мощности перемешивания
Находим диаметр нормализованной мешалки:
dм = (025-05)D=04×14=056 м
Частота вращения мешалки в аппарате 10 обсек что получено на основании опытных данных.
Значение критерия мощности для пропеллерной мешалки:
Мощность потребляемая мешалкой при установившемся режиме:
Принимаем к установке электродвигатель:[1 стр.13 табл.1.2]
5 Тепловой расчёт установки
Уравнение теплового баланса:
Q=Qвода + QАП + Qсоль + Qпот где
Q – количество теплоты;
Qвода – количество теплоты поступившее в аппарат с водой;
QАП – количество теплоты пошедшее на обогрев аппарата;
Qсоль – количество теплоты поступившее в аппарат с содой;
Qпот – потери теплоты.
С учётом того что проектируемый аппарат периодического действия следует уточнить уравнение теплового баланса.
tап = 6мин=360с – время необходимое на обогрев аппарата;
tпр = 15мин=900с – время необходимое на поддержание температуры продукта в аппарате т.е. на ведение процесса.
Количество теплоты которую передаёт пар без учёта потерь:
Количество теплоты которую передаёт пар с учётом потерь:
Qобщ = 11×Q=11×1464433=16108763 Джс;
Согласно уравнению теплового баланса определим расход пара
Qобщ =Gпар ×спар ×(tпар нач. –tпар кон. )
При давлении пара P=03 МПа [4]
Коэффициент теплоотдачи пара поступающего в рубашку к стенке
Режим турбулентный Re>10000. Найдём коэффициент теплоотдачи в случае конденсации пара внутри рубашки [5].
Коэффициент теплоотдачи стенки к продукту в аппарате
Для аппарата с пропеллерной мешалкой с рубашкой [5 стр.15 табл.1.8]: (С=0514; m=067)
Коэффициент теплопередачи
Поверхность теплообмена мешалки:
6 Расчёт комплектующего оборудования
6.1.Расчёт подогревателя типа «труба в трубе».
Определение средней разности температур
Определение тепловой нагрузки в теплообменнике типа «труба в трубе»
Ориентировочный выбор теплообменника
Ориентировочное значение поверхности теплообмена:
По найденному значению Fор выбираем ближайший больший по поверхности теплообменник из стандартных элементов ТТ-25. Принимаем к установке теплообменник типа ТТ-25 с действительной поверхностью теплообмена равной 15 м2. [2стр.29 табл.211].
Параметры теплообменника:
Длина наружных труб м 15
Количество элементов1
Рассчитываем среднюю температуру горячего теплоносителя
и среднюю температуру нагреваемого продукта
Расход горячего теплоносителя составит
Уточняем ранее принятое значение коэффициента теплопередачи
Живое сечение потока горячего теплоносителя на одну трубу
Скорость горячего теплоносителя
Эквивалентный диаметр для межтрубного пространства
Критерий Рейнольдса для теплоносителя при его средней температуре
Критерий Рейнольдса для продукта при его средней температуре
Рассчитаем коэффициент теплопроводности
Теплообменник изготовлен из стали 18-нержавейка
Принимаем толщину стенки равной
Среднее значение тепловой проводимости загрязнений стенок
- для органической жидкости
Рассчитаем площадь теплопередающей поверхности
Окончательно принимаем ближайший больший теплообменник с элементами ТТ-25 с поверхностью теплообмена F=036 м2.
Количество элементов коаксиальных труб
6.2.Расчёт спирального регенератора
Тепловой расчёт теплообменника
Тепловую нагрузку теплообменника находят из уравнений тепловых балансов. Если пренебречь потерями теплоты в окружающую среду уравнение теплового баланса выразится равенством:
QОбщ = QГор.воды = QХол.воды + Qпот где
QГор.воды – количество теплоты
QХол.воды – количество теплоты
Qпот = (5-10)%×QГор.воды
Вода из теплообменника подаётся в аппарат за 2 минуты.
Теплота которую получает холодная вода от горячего раствора в процессе теплообмена:
Теплота которую отдаёт горячий раствор холодной воде в процессе теплообмена с учётом потерь в окружающую среду:
QОбщ = 11×Q=11×8380=9218 Дж;
t = 55 оС – температура горячего раствора на входе в теплообменник;
t = 20 оС – температура раствора на выходе из теплообменника.
Определим ориентировочно значение поверхности теплообмена пологая что КОР = 1200 Вт(м2×К) т.е. приняв его таким же как и при теплообмене от жидкости к жидкости:
Эквивалентный диаметр спирального теплообменника определяем по формуле:
Примем ширину канала равную 0012м получим значение эквивалентного диаметра
Задавшись скоростью движения продукта 1 равной 05 мс находим площадь сечения канала теплообменника
откуда эффективная высота теплообменника (эффективная ширина ленты)
Принимаем ширину ленты 1 м тогда площадь поперечного сечения канала f=0012м2. Действительная скорость движения воды по каналу теплообменника
Скорость греющего раствора в канале теплообменника
Критерий Рейнольдса:
Приняв диаметр спирали теплообменника Dс =1 м находим критическое значение Re
Определим коэффициент теплоотдачи от стенки к воде
Определяем значение Re для раствора
Определим коэффициент теплоотдачи от раствора к стенке
Задаваясь толщиной стенки спирального теплообменника ст=0004 м и материалом стенки из стали 18 с коэффициентом теплопроводности λст=16 Вт(м2*ºC) находим значение коэффициента теплопередачи
Находим поверхность теплообмена спирального теплообменника
Длина листов спирали определяется из соотношения
Число витков спирали
где t=+ст=0012+0003=0015м
d=2r+t=2*0.098+0.015=0.21м
Наружный диаметр спирали с учетом толщины листа:
Dc=d+2Nt+ ст=0.21+2*1576*0.015+0.003=06858 м
Зная наружный диаметр спирали находим критическое значение Re
Reкр=20000(0.02406858)0.32=684092
Определяем потерю напора теплоносителями при прохождении через каналы спирального теплообменника.
7 Гидравлический расчёт продуктовой линии
Для всасывающего и нагнетательного трубопровода примем одинаковую скорость течения воды равную 1 мс тогда диаметр равен:
Фактическая скорость:
Примем что трубопровод стальной коррозия незначительна.
Определим потери на трения и местные сопративления
т.е. режим турбулентный.
Абсолютную шероховатость трубопровода принимаем D=00002м.
Т.о. имеет место смешанное трение и расчёт l следует проводить по формуле:
Определим сумму коэффициентов местных сопротивлений отдельно для всасывающей и нагнетательной линий.
Для всасывающей линии:
)Вход в трубу (принимаем с острыми краями)
Сумма коэффициентов местных сопротивлений во всасывающей линии:
Потери напора hп на преодоление сопротивление трения и местных сопротивлений во всасывающей линии:
Для нагнетательной линии:
)Внезапное расширение x4 = 081.
Потери напора hп на преодоление сопротивление трения и местных сопротивлений в нагнетательной линии:
Общие потери насоса:
hп = hп.вс. + hп.наг. =076+102=178 м
Находим напор насоса
Н=Нг +hп = 3+178=478 м
Полезная мощность насоса
Nп = g×G×H=981×028×478=131 Вт=0013кВт
Принимаем к аппарату насос
Электродвигатель для насоса
Требования техники безопасности и ПС
Меры безопасности технологических процессов закладываются при их проектировании. Поэтому учет требований безопасности при разработке и осуществлении технологических процессов имеет большое профилактическое значение для предупреждения производственного травматизма.
Общие требования безопасности к технологическим процессам изложены в ГОСТ 12.3.002—75 «ССБТ. Процессы производственные. Общие требования безопасности».
Безопасность производственных процессов обеспечивается комплексом проектных и организационных решений предусматривающих соответствующий выбор технологических процессов рабочих операций и порядка обслуживания оборудования; производственного оборудования и условий его размещения; способов хранения и транспортирования исходных материалов заготовок полуфабрикатов и готовой продукции а также удаления отходов производства; средств защиты работающих.
Большое значение имеет правильное распределение функций между человеком и оборудованием в целях уменьшения тяжести и напряженности труда обеспечения его безопасности.
Производственные процессы должны быть пожаро- и взрывобезопасными а также не должны загрязнять окружающую среду выбросами вредных веществ не являться источниками вредных физических факторов (шума вибрации и т. п.).
Технологические процессы пищевых производств чрезвычайно разнообразны однако имеется ряд общих требований осуществление которых способствует их безопасности а именно:
-устранение непосредственного контакта людей с исходными веществами материалами и отходами производства оказывающими на работающих вредное действие;
-замена технологических процессов и операций связанных с возникновением вредных и опасных производственных факторов процессами и операциями на которых эти факторы отсутствуют или возможность их проявления сведена к минимуму;
-применение комплексной механизации автоматизации или дистанционного управления в тех случаях когда действие вредных и опасных производственных факторов нельзя устранить;
-обеспечение надлежащей герметизации и теплоизоляции производственного оборудования ведение процессов под вакуумом что предотвращает выделение вредных веществ теплоты и влаги в рабочую зону;
-оснащение оборудования средствами коллективной защиты работающих от воздействия опасных и вредных производственных факторов разной природы происхождения;
-замена сложных многостадийных процессов более безопасными мало- или одностадийными процессами вследствие их лучшей управляемости более широкой возможности их автоматизации устранение побочных часто опасных операций;
-переход от периодических процессов к непрерывным отличающимся устойчивостью режима и простотой регулировки;
-применение систем непрерывного контроля и управления технологическими процессами режимами работы оборудования обеспечивающими защиту работающих предупреждение аварий путем сигнализации и своевременное отключение производственного оборудования;
-оснащение технологических процессов устройствами обеспечивающими получение своевременной информации о возникновении пожаро- и взрывоопасных аварийных ситуаций превышении ПДК вредных веществ или допустимых уровней воздействия других вредных производственных факторов на отдельных технологических операциях;
-применение рациональной организации обслуживания технологических процессов режимов труда и отдыха для предупреждения физических и нервно-психологических перегрузок.
Рассчитали аппарат с мешалкой для приготовления моющих растворов. Производительность по готовому продукту 2тч. Соотношение воды и кальцинированной соды подаваемых в аппарат равно 10 : 1. Аппарат работает периодически.
В результате расчёта получили аппарат с D = 14 м и высотой Н =26м. Для процесса перемешивания подобрали мешалку пропеллерную с dM= 056м которая приводится во вращение электродвигателем типа АО2-52-2 N=13кВт дв=089. Известно что оптимальным температурным режимом растворения является температура воды в пределах 50 - 60 °С.
Рассчитали подогреватель типа «труба в трубе» который подогревает воду от 15°С до 30°С.
Для данного аппарата рассчитали спиральный регенератор который охлаждает раствор от 55°С до 20°С.
Список использованных источников
Дытнерский Ю.И. Основные процессы и аппараты химической технологии. Пособие по проектированию Москва Химия 1991 г.
Дытнерский Ю.И. Основные процессы и аппараты химической технологии. Пособие по проектированию Москва Химия 1983 г. 272 с.
Павлов К.Ф. Романков П.Г. Носков А.А. Примеры и задачи по курсу процессов и аппаратов химической промышленности.
Ривкин С.Л. Александров А.А. Термодинамические свойства воды и водяного пара. Справочник Москва Энергоатомиздат 1984 г.
Стабников В.Н. Проектирование процессов и аппаратов пищевых производств Киев В. школа 1982 г.
Стахеев И.В Пособие по курсовому проектированию процессов и аппаратов пищевых производств Минск Вс. школа 1975 г.
Чубик И.А. Маслов А.Н. Справочник по теплофизическим константам пищевых продуктов и полуфабрикатов.-М.:1965.
Рекомендуемые чертежи
- 09.07.2014
- 24.04.2014
Свободное скачивание на сегодня
Обновление через: 10 часов 6 минут