Расчёт цилиндрического редуктора с внутренними зубьями




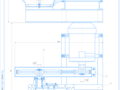
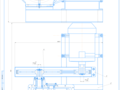
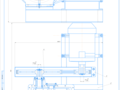
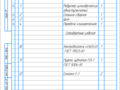
- Добавлен: 24.01.2023
- Размер: 2 MB
- Закачек: 0
Описание
Состав проекта
![]() |
![]() |
![]() ![]() ![]() |
![]() ![]() ![]() ![]() |
![]() ![]() ![]() |
![]() ![]() ![]() ![]() |
![]() ![]() ![]() |
![]() ![]() ![]() ![]() |
![]() ![]() ![]() ![]() |
![]() ![]() ![]() |
![]() ![]() ![]() ![]() |
![]() ![]() ![]() |
![]() ![]() ![]() ![]() |
![]() ![]() ![]() |
![]() ![]() ![]() ![]() |
![]() ![]() ![]() |
![]() ![]() ![]() ![]() |
![]() ![]() ![]() ![]() |
![]() ![]() ![]() ![]() |
![]() ![]() ![]() |
![]() ![]() ![]() ![]() |
![]() ![]() ![]() |
![]() ![]() ![]() ![]() |
![]() ![]() ![]() ![]() |
![]() ![]() ![]() |
![]() ![]() ![]() ![]() |
![]() |
![]() ![]() ![]() |
Дополнительная информация
кинем схема В18-10-5 — копия.frw

Приводная установка-5 — копия.cdw

Общее передаточное отношение привода 12.2 .
Частота вращения выходного вала
Крутящий момент на выходном валу
Ведущий вал-5 — копия.frw

Деталировка-5 — копия.cdw

Угол наклона линии зуба
Направление линии зуба
Степень точности и вид
сопряжения по ГОСТ 1643-81
Неуказанные фаски 2 х45
Покрытие: Хим.Окс.прм.
Сталь 40Х ГОСТ 4543-71
Ведомый вал-5 — копия.frw

Общий привод-5- — копия.spw

Передача клиноременная
Электродвигатель 4А160S4У3
Редуктор цилиндр-5 — копия.cdw

Зазоры в зацеплении и пятно контакта - по степени точности
Редуктор обкатать без нагрузки втечение двух часов.
Перед сборкой во внутреннюю полость корпуса залить масло
Индустриальное И-20" ГОСТ20799-75 в количестве 4 литров..
записка 18-10.doc
Т4=1050 Нм n4=120 мин-1 h=5 лет.
График изменения нагрузки также представлен на рисунке 1.
- асинхронный электродвигатель
- клиноременная передача.
- редуктор цилиндрический прямозубый
Кинематический расчёт привода.
Требуемая мощность электродвигателя Р1:
кВт – мощность на валу транспортёра
-КПД ременной передачи
-КПД пары подшипников
-КПД зубчатой передачи
Принимаем электродвигатель 4А160S4У3 с nэд=1465 обмин Рэд =15 кВт.
Рассчитаем кинематические параметры для каждого вала:
1 Вал электродвигателя. Р1=14.681 кВт
2 Ведущий вал редуктора:
Р2=Р1=14.681·0.95=13.947 кВт
3 Выходной вал редуктора:
Р3=Р2=13.9470.970.995=13.46 кВт
Расчет клиноременной передачи.
Ременные передачи относятся к категории быстроходных передач и потому в проектированном приводе клиноременная передача принята первой ступенью.
Исходные данные для расчета:
Частота вращения валов:
быстроходного nдв =1465 мин-1
тихоходного n1 = 488.3 мин-1.
на быстроходном валу Рдв = 14.683 квт
на тихоходном валу Р1 =13.947 квт.
Крутящий момент на быстроходном валу Тдв = 95.7 Н · м.
Нагрузка спокойная переменная.
Передаточное число uкп = 3 .
Расчет ременных передач проводится в два этапа: первый – проектный расчет с целью определения геометрических параметров передачи; второй – проверочный расчет ремней на прочность.
Выбираем сечение ремня .
Выбор сечения ремня делаем по табл.2.12 [2]. Принимаем при
Рдв = 14.68 кВт nдв = 1465 мин-1 сечение ремня В“ с размерами:
bp = 19мм; b0 =22 мм; y0=4.8 мм; h = 13.5 мм; A = 230мм2; q = 0.3 кг м;
где q – удельный вес избранного ремня (1 погонного метра).
Определение минимального допустимого диаметра ведущего шкива.
По таблице 2.12 [2] в зависимости от вращающего момента на валу двигателя Тдв = 95.7 Нм и выбранного сечения ремня задаемся расчетным диаметром ведущего шкива d1 min=200мм.
Определяем диаметр ведомого шкива.
где = 001 0 002принимаем = 002 – коэффициент скольжения.
Полученное d2 округляем к ближайшему стандартному значению. Диаметр ведущего шкива d2 = 560 мм.
Определим фактическое передаточное число uкл ф передачи и проверим его отклонение Δu от расчетного uкл.
Отклонения от фактического не должно превышать
1.1 Определение межосевого расстояния.
Межосевое расстояние определяем по формуле:
1.2 Определения расчетной длины ремня.
Принимаем L =2360 мм.
Уточняем значение межосевого расстояния.
Минимальное межосевое расстояние для удобства монтажа и снятия пасов должно быть меньше а на 001L.
Максимальное межосевое расстояние для создания необходимого натяжения пасов.
Определим угол обхвата ремнём ведущего шкива.
; α1 должен быть ≥ 110.
Определяем скорость ремня.
h1 – диаметр ведущего шкива; [v] – скорость которая допускается;
мс для клиновых ремней.
Определим частоту пробегов ремня.
где – частота пробегов который допускается.
Определим допустимую мощность переданную одним клиновым ремнем.
Где [P0] – приведенная допустимую мощность переданным одним клиновым ремнем.
[P0] = 5.8 кВт – по таблице 2.15 [2] .
С – поправочные коэффициенты.
CL – коэффициент отношения расчетной длины к базовой: CL = 089.
Cp = 1 – при спокойной нагрузке.
Cα = 089 по таблице 2.18 для α=140.7 [2] методом интерполяции.
Cz = 095 – при количестве ремней 2 3.
Определим расчётное количество клиновых ремней.
Коэффициент учитывающий неравномерность нагрузки (см. стр. 28)
Сz =0.9 принимаем : z=3.
Определим силу предварительного натяжения ремней.
Общая сила натяжения ремней.
Определим окружную силу переданную комплектом ремней.
Определим силы натяжения ведущей и известной областей.
Для всей клиноременной передачи:
Определим силу давления на вал.
Для комплекта клиновых ремней:
2 Проверочный расчет.
Проверяем прочность одного ремня по максимальным напряжениям в сечении ведущей ветви.
– напряжение растягивания.
А – площадь сечения ремня.
n – напряжение изгиба.
Еn = 80 100Нмм2 – модуль продольной упругости для прорезиненных ремней. Принимаем Еn = 90 Нмм2.
ρ – плотность материала ремней для клиновых ремней ρ = 1250 1400кгм3 принимаем ρ = 1300 кгм3;
[p] – допускаемое напряжение растягивания;
[p] = 10 Нмм2 – для клиновых ремней.
max = 2.2 + 6 + 002 = 8.22 [p].
Условия прочности выполнены.
Таблица 2.1 Параметры клиноременной передачи мм
Межосевое расстояние а
Диаметр ведущего шкива d1
Диаметр ведомого шкива d2
Максимальное напряжение max МПа
Начальное натяжение
Угол обхвата меньшего шкива α1
По таблице 2.21 [2] находим основные размеры шкивов для клиновых ремней.
Для сечения шкива для клинового ремня В“ это размеры (табл..2.12):
В = 5.7 мм; Lp = 190 мм; е = 25.5 мм; F = 17 мм; h = 14.3 мм; α = 36° ;
Делительные диаметры шкивов: ведущего dp1 = 200 мм;
ведомого dp2 = 560 мм.
Внешние диаметры шкивов:
Диаметры посадочного отверстия:
для ведущего шкива d = dдв = 48мм;
для ведомого шкива d будет определен при расчете редуктора.
Уточнение передаточных чисел ступеней редуктора.
Расчёт цилиндрической передачи редуктора.
Рассчитать цилиндрическую прямозубую передачу редуктора общего назначения по следующим данным: номинальная мощность передаваемая шестерней N1=13.947 кВт; частота вращения шестерни п1= 488 мин-1 (51 радс); передаточное число редуктора и = 4.28; срок службы передачи t = 5 лет; нагрузка постоянная; кратковременно действующая максимальная нагрузка при пуске в 1.6 раза больше номинальной; передача нереверсивная; шероховатость поверхности зубьев по 6-му классу (ГОСТ 2789—73); габариты редуктора ограничены.
Выбор материала и допускаемых напряжений для шестерни и колеса.
1. По табл. 3.12 назначаем материал для шестерни и колеса — сталь 40ХН (поковка); термообработка — улучшение. Для шестерни при радиусе заготовки до 100 мм: ; ; 230 300НВ
-для колеса при радиусе заготовки до 300мм:.
2. Определяем допускаемое напряжение изгиба для шестерни (формула 3.51):
Предварительно зубьев при изгибе соответствующий эквивалентному числу циклов перемены напряжений (формула 3.52):
где предел выносливости при изгибе соответствующий базовому числу циклов перемены напряжений (табл. 3.19).
Коэффициент учитывающий влияние двухстороннего приложения нагрузки (табл. 3.20) при одностороннем приложении нагрузки Kfc= 10; коэффициент долговечности (формула 3.53):
При НВ 350 (см. с. 77) тР= 6; базовое число циклов перемены напряжений (см. с. 77):
эквивалентное (суммарное) число циклов перемены напряжений (формула 3.54)
Соответственно: принимаем КFL1 = 10.
Соответственно МПа.
Коэффициент безопасности (формула 3.56):
SF = S'f·S”F= 175 10= 175
где Sf= 175 (табл. 3.19) S”F= 10 (табл. 3.21). Коэффициент учитывающий чувствительность материала к концентрации напряжений (формула 3.57) YS = 1. Коэффициент учитывающий шероховатость переходной поверхности зуба (формула 3.58) YR= 10. Допускаемое напряжение изгиба для зубьев шестерни:
3. Определяем допускаемое напряжение изгиба для колеса (формула 3.51):
где Sf= 175 (табл. 3.19) S”F= 10 (табл. 3.21). Коэффициент учитывающий чувствительность материала к концентрации напряжений (формула 3.57) YS = 1. Коэффициент учитывающий шероховатость переходной поверхности зуба (формула 3.58) YR= 10. Допускаемое напряжение изгиба для зубьев шестерни
4. Допускаемое напряжение изгиба при расчете на действие максимальной нагрузки (формула 3.62) для шестерни:
Предварительно находим предельное напряжение не вызывающее остаточных деформации или хрупкого излома зуба (табл. 3.19):
коэффициент безопасности (см. с. 76)
здесь S’fm S’’fmi = S"fMi =10 (табл. 3.21).
Коэффициент учитывающий чувствительность материала к концентрации напряжений (формула 3.57) Ys = 10. Следовательно
5. Допускаемое напряжение изгиба при расчете на действие максимальной нагрузки (формула 3.62) для колеса:
здесь S’fm2= 175 (см. с. 80); S’’fm2 = S"fM2 =10 (табл. 3.21).
6. Допускаемое контактное напряжение для шестерни (формула 3.33):
Предварительно находим предел контактной выносливости поверхностей зубьев соответствующие эквивалентному числу циклов перемены напряжений (формула 3.34):
здесь предел контактной выносливости соответствующий базовому числу циклов перемены напряжений (табл. 3.17)
Коэффициент долговечности (формула 3.35):
где базовое число циклов перемены напряжений (рис. 3.16)
эквивалентное (суммарное) число циклов перемены напряжений
Предел контактной выносливости = 630 09 = 567 МПа. Коэффициент безопасности для зубьев с однородной структурой материала (см. с. 75)
SН1= 11. Коэффициент учитывающий шероховатость сопряженных поверхностей (таба. 3.18) ZR= 095. Коэффициент учитывающий окружную скорость (см. с. 75) Zv= 10. Допускаемое контактное напряжение для шестерни:
7. Допускаемое контактное напряжение для колеса (формула 3.33):
Предел контактной выносливости = 550 · 09 = 500 МПа.
Коэффициент безопасности для зубьев с однородной структурой материала (см. с. 75) : SН2= 11. Коэффициент учитывающий шероховатость сопряженных поверхностей (табл. 3.18) ZR= 095. Коэффициент учитывающий окружную скорость (см. с. 75) Zv= 10. Допускаемое контактное напряжение для шестерни:
8 . Допускаемое контактное напряжение передачи стр. 75:
=min (490 + 432) = 432 МПа.
Принимаем допускаемое контактное напряжение передачи = 432МПа.
9. Допускаемое контактное напряжение при расчете на действие максимальной нагрузки (см. с. 80) для шестерни:
= 28 = 28 600 = 1680 МПа
для колеса: = 28 = 28 580 = 1624 МПа
10. Расчет передачи на контактную выносливость. Вычисляем начальный диаметр шестерни (табл. 3.13 формула 3.16)
Предварительно определяем величины необходимые для расчета. Номинальный крутящий момент на шестерне (формула 3.12):
Ориентировочная окружная скорость (формула 3.27):
При данной скорости требуемая степень точности зубчатых колес (табл. 3.33) — 9-я.
Коэффициент учитывающий распределение нагрузки между зубьями для прямозубых колёс = 1. Коэффициент ширины зубчатого венца при симметричном расположении опор (табл. 3.33):
Коэффициент динамической нагрузки (табл. 3.16) для степени точности зубчатых колес на единицу грубее установленной (см. с. 80) т. е. для 9-й степени
точности Кнv= 105 (определяется интерполированием). Коэффициент учитывающий форму сопряженных поверхностей (формула 3.28') Zh= 169. Коэффициент учитывающий механические свойства материалов сопряженных колес (формула 3.29) Zm = 275 МПа12.
По табл. З.11 выбираем число зубьев шестерни Z1= 18 и коэффициент торцового перекрытия:.
Коэффициент учитывающий суммарную длину контактных линий (формула 3.30) .
Начальный диаметр шестерни :
Модуль зацепления: мм
Полученный модуль округляем по стандарту (см. приложение табл. 9):
Пересчитываем начальный диаметр: мм.
11 Проверочный расчет передачи на контактную выносливость .
. Определяем расчетную окружную скорость (формула 3.47) при начальном диаметре шестерни: мм.
При данной скорости требуемая степень точности передачи (табл. 3.33) — 9-я что соответствует принятой ранее степени точности. Уточняем по скорости v = 1.8 мс коэффициенты входящие в формулу (3.48): К’HV= 122 (табл. 3.16) К'Hα= 10 (рис. 3.13) Z’V= 101 (рис. 3.17).
Уточняем начальный диаметр шестерни (формула 3.48):
По уточнённому диаметру определяем модуль зацепления:
Полученный модуль вновь округляем до стандартного значения т = 5 мм что совпадает: с ранее принятой величиной модуля; следовательно диаметр начальной окружности шестерни dw= 90мм. Ширина зубчатого венца при
12 Прочный расчет зубьев на контактную прочность при действии максимальной нагрузки. Расчетное напряжение от максимальной нагрузки (формула 3.60):
где действующее напряжение при расчете на контактную выносливость (табл. 3.13 формула 3.15):
Расчетное контактное напряжение от максимальной нагрузки
где - задано в исходных данных расчета.
13 Проверочный расчет зубьев на выносливость по напряжениям изгиба.
Изгибающее напряжение для зуба шестерни (табл. 3.14 формула 3.22)
Предварительно определяем величины необходимые для расчета. Находим эквивалентное число зубьев для шестерни и колеса (формула 3.7):
Определяем коэффициенты учитывающие форму зуба (рис. 3.21): YF1= =413 YF2= 3.7.
Коэффициент учитывающий влияние наклона зуба на его напряженное состояние для прямозубых колес (см. с. 77) .
Расчетная удельная нагрузка (формула 3.25):
где TF1=257000 Нмм мм мм.
(стр.82) (рис.3.20) 5(для V=2.4мс).
Напряжение изгиба для зуба шестерни:
Для зуба колеса: МПаМПа
12 Окончательно принимаем параметры передачи.
Z1 = 18; z2 = 77; m=5 мм; d1 = 90 мм;
d2= 375 мм; b = 100 мм;
13 Принимаем межосевое расстояние мм;
Усилия действующие на вал:
-со стороны ременной передачи Q=1945H
-со стороны зубчатого зацепления :
Определяем реакции в опорах:
Мих(B)=RAX·80=456880 Н·мм
Миу(A)=Q·80=155600 Н·мм.
Миу(B)=Q·160-RAy·80=-166240 H·мм.
Суммарный изгибающий момент:
Крутящий момент Т=257000Нмм.
Приведенный момент :
Далее строим расчётную схему вала:
Усилия действующие на вал со стороны зубчатого зацепления :
Мих(С)=RAX·90=2858·790=257220 Н·мм
Миу(С)=RAy·90=1040·90= 93600 Н·мм
Крутящий момент Т= 1071700 Нмм.
Расчет шпоночных соединений.
Размеры шпонок в поперечном сечении устанавливают по стандарту в зависимости от диаметра вала и требований относительно работоспособности конструкций а их длину определяют конструктивно в зависимости от длины ступицы.
Принятые размеры шпоночных соединений проверяют расчетом на срез и смятие:
s3г = 4Т d · ep · h [s]3г МПа.
где Т – крутящий момент на вале Н мм.
d – диаметр вала мм;
ep – расчетная длина шпонки мм.
[s]3г = 140 180 МПа – допустимое напряжение смятия материала шпонки Ст.45;
t3р = 2Т d · ep · b [t]3р МПа;
где b – ширина шпонки гг.
[t]3р = 80 МПа – допустимое напряжение на срез;
1 Расчет шпоночного соединения вала :
Дано: Т = 257000 Н м ; d = 40 мм;
b х h = 12 х 8 мм; ep = 58 мм; t1 = 5 мм; t2 = 3.6 мм
s3г = 4Т d · ep · h = 4 · 257000 40 · 58 · 8 = 71 МПа [s]3г = 160 МПа
t3р = 2Т d · ep · b = 2 · 257000 40 · 58 · 12 = 31 МПа [t]3р = 80 МПа;
e = ep + b = 58 + 12 = 70 мм;
b х h х e = 12 х8 х 70 мм.
2 Расчет шпоночного соединения вала :
Дано: Т = 1071700 Н м ; d = 55 мм;
b х h = 16 х 10 мм; ep = 64 мм; t1 = 6 мм; t2 = 4.3 мм;
s3г = 4Т d · ep · h = 4 · 1071700 55 · 64 · 10 = 149 МПа [s]3г = 160 МПа;
t3р = 2Т d · ep · b = 2 · 1071700 55 · 64 · 12 = 48 МПа [t]3р = 80 МПа;
e = ep + b = 64 + 16 = 80 мм;
b х h х e = 16 х 10 х 80;
3 Расчет шпоночного соединения вала :
) Дано: Т = 1071700 Н · м ; d = 45 мм;
b х h = 14 х 9 мм; ep = 66 мм; t1 = 5.5 мм; t2 = 3.8 мм;
s3г = 4Т d · ep · h = 4 · 1071700 45 · 66 · 10 = 137 МПа [s]3г = 160 МПа;
t3р = 2Т d · ep · b = 2 · 1071700 55 · 34 · 16 = 27 МПа [t]3р = 80 МПа;
e = ep + b = 66 + 14 = 80 мм;
b х h х e = 14 х 9 х 80;
Для уменьшения затрат мощности на трение и снижение интенсивности износа поверхностей трения а также для предотвращения заедания задиров и коррозий лучшего отвода теплоты трущиеся поверхности деталей должны иметь надежную смазку.
Для смазывания зубчатых передач применяем картерную систему. В корпус редуктора заливаем смазочное масло так чтобы венцы колес были в него погружены. При их вращении масло захватывается зубцами разбрызгивается и попадает на внутренние стенки корпуса откуда стекает в нижнюю его часть. Внутри корпуса получается взвесь частичек смазочного масла в воздухе которая покрывает поверхности расположенных в середине корпуса деталей.
Глубина погружения цилиндрического колеса тихоходной передачи составляет (05 5) * m. Различие между верхним и нижним уровнем должна составлять не меньше чем 10 мм что в границах допустимого.
Рекомендуемая вязкость смазки по таблице (11.1 №3) составляет 50 * 10-6 м2 с. По таблице (11.2 №3) выбираем масло И – 50А с кинематической вязкостью 47 55 55 м2 с которое рекомендуется для цилиндрическо – конических передач с температурой 50 0С.
Vм = 04л · 14 квт = 5.6 » 6 л.
На практике смазывают подшипники тем же смазочным маслом что и детали передач. Но это возможно только для подшипников червяка. В нашем же случае подшипники расположены далеко от смазочной ванны поэтому будем смазывать их пластическим смазочным материалом. В этом случае подшипниковый узел закрывают мазеудерживающим кольцом а свободное пространство внутри заполняют смазывающим материалом.
Выбираем пластическое смазочное масло ВНИИ ЧП – 242 что рекомендуется для тяжелонагруженных подшипников а также для роликоподшипников.
Уровень масла в редукторе проверяется жезловым маслоуказателем и маслосливною пробкой с конической резьбой.
Для предотвращения вытекания смазочного материала из подшипниковых узлов а также защиты их от пыли и влаги устанавливаем на входе и выходе из редуктора манжетное уплотнение.
Стандартные муфты для привода подбирают по крутящему моменту с учетом диаметра вала. Подбираем муфту цепную двухрядную (МЗ -1 по ГОСТ 5006 – 55 . Она отличается простотой конструкции и удобством монтажа и демонтажа. Муфта смягчает удары и вибрации компенсирует небольшие погрешности монтажа и деформации валов. Допустимое радиальное смещение валов не больше 04 угловое смещение – не больше чем 10 . Материал обойм и втулки – сталь 45Л.
Для муфты принимаем количество зубьев z = 30. Ширина зубчатых венцов b=12 мм.
Допускаемый крутящий момент T = 7100Нм;
Павлище В.Т. Основы конструирования та расчёт деталей машин. – К.: Вища школа 1993 – 556 с.
Киркач Н.Ф. Баласанян Р.А. Расчёт и проектирование деталей машин. – Харков: Основа 1991 – 276 с.
Дунаев П.Ф. Леликов О.П. Конструирование узлов и деталей машин. – М.: Вища школа 1985 – 416 с.
Цехнович Л.И. Петриченко И.П. Атлас конструкций редукторов – К.: Вища школа 1990 – 152 с.
Анурьев В.И. Справочник конструктора машиностроителя. – М.: Машиностроителя 1978 – 559 с.
Методические указания к определению допускаемых напряжений при расчёте зубчатых передач с использованием ЭВМ в процессе выполнения самостоятельной работы по дисциплине «Детали машин» - Кудрявцев Г.П. Беспалько А.П. Паламаренко А.З. – К.: КТИПП 1989 – 52с.
Методические указания по выполнению и защите курсового проекта по дисциплине “Детали машин та ОК” - Кудрявцев Г.П.и др. - К.: КТИХП 1993 – 47с.
Редуктор ..spw

кинем схема В18-10.frw

Редуктор цилиндр.cdw

Зазоры в зацеплении и пятно контакта - по степени точности
Редуктор обкатать без нагрузки втечение двух часов.
Перед сборкой во внутреннюю полость корпуса залить масло
Индустриальное И-20" ГОСТ20799-75 в количестве 4 литров..
Ведомый вал.frw

Общий привод-.spw

Передача клиноременная
Электродвигатель 4А160S4У3
Ведущий вал-5.frw

Приводная установка-5.cdw

Общее передаточное отношение привода 12.2 .
Частота вращения выходного вала
Крутящий момент на выходном валу
Приводная установка.cdw

Общее передаточное отношение привода 12.2 .
Частота вращения выходного вала
Крутящий момент на выходном валу
Деталировка-5 .cdw

Угол наклона линии зуба
Направление линии зуба
Степень точности и вид
сопряжения по ГОСТ 1643-81
Неуказанные фаски 2 х45
Покрытие: Хим.Окс.прм.
Сталь 40Х ГОСТ 4543-71
кинем схема В4-9.frw

Деталировка .cdw

Угол наклона линии зуба
Направление линии зуба
Степень точности и вид
сопряжения по ГОСТ 1643-81
Неуказанные фаски 2 х45
Покрытие: Хим.Окс.прм.
Сталь 40Х ГОСТ 4543-71
Ведомый вал-5.frw

Общий привод-5-.spw

Передача клиноременная
Электродвигатель 4А160S4У3
Редуктор цилиндр-5.cdw

Зазоры в зацеплении и пятно контакта - по степени точности
Редуктор обкатать без нагрузки втечение двух часов.
Перед сборкой во внутреннюю полость корпуса залить масло
Индустриальное И-20" ГОСТ20799-75 в количестве 4 литров..
кинем схема В18-10-5.frw

Редуктор-5 ..spw

Ведущий вал.frw

Рекомендуемые чертежи
- 04.03.2023
- 04.11.2022