Расчёт и проектирование металлорежущих инструментов, чертежи




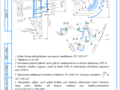
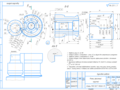
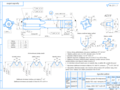
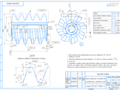
- Добавлен: 24.01.2023
- Размер: 1 MB
- Закачек: 0
Описание
Состав проекта
![]() |
![]() |
![]() ![]() ![]() ![]() |
![]() ![]() ![]() ![]() |
![]() ![]() ![]() ![]() |
![]() ![]() ![]() ![]() |
![]() ![]() ![]() ![]() |
![]() ![]() ![]() |
Дополнительная информация
Протяжка D65.cdw

Черновые и переходные
Протяжка для цилинд-
Сталь Р6АМ5 ГОСТ 19265-73
Материал хвостовых частей - сталь 40Х.
Твёрдость: режущей и задней направляющей частей 63 66 HRC
передней направляющей части
хвостовой части 43 51 HRC.
Технические требования к протяжке по ГОСТ 9126-76*.
Неуказанные предельные отклонения валов h14
.Выкружки располагать в шахматном порядке. Шлифовальный круг для выкружек черновых
переходных и чистовых зубьев R25.
Биение режущей части относительно оси протяжки не более 0
Маркировать: диаметр протяжки
квалитет поля допуска отверстия
пределы длин протяги-
марку стали обрабатываемого изделия
значение переднего угла
товарный знак завода-изготовителя (65H7-40-120-Ст20Х-
Профиль зубьев М (1:1)
Долбяк.cdw

номинальным делительным диаметром
Сталь Р18 ГОСТ 19265-73
Долбяк должен удовлетворять техническим требованиям ГОСТ 9323-19*.
Твёрдость 64 66 HRC.
Отклонение профиля рабочей части зуба от теоретического не должно превышать 0
Разность соседних окружных шагов не более 0
6 мм Накопленное отклонение окружного
Неуказанные предельные отклонения отверстий H14
число зубьев долбяка
обозначение класса точности
товарный знак завода-изготовителя
Фреза.cdw

Направление витков фрезы
Направление стружечной канавки
Шаг стружечной канавки
Профиль зубьев в нормальном сечении
Фреза червячная чистовая для
цилиндрических зубчатых колёс
Сталь Р18 ГОСТ 19265-73
Фреза червячная должна удовлетворять техническим требованиям ГОСТ 9324-80.
Твёрдость 63 66 HRC.
Неуказанные предельные отклонения отверстий H14
Маркировать: последние четыре цифры обозначения
ход винтовой стружечной канавки
товарный знак завода-изготовителя (4367-m20-
Метчик.cdw

Предельное отклонение шага резьбы на длине до 28 мм
Метчики ручные для метрической
Сталь У10А ГОСТ 1435-99
Метчики должны удовлетворять техническим требованиям ГОСТ 3449-84*.
Твёрдость рабочей части 61 63 HRC
хвостовой части 37 52 HRC.
Центровые отверстия формы А по ГОСТ 14034-74*.
Обратная конусность калибрующей части от 0
Предельные отклонения элементов резьбы
нарезанной чистовым метчиком
соответствовать полям допусков степени точности Н3.
На хвостовике метчиков нанести риски (на черновом одну
чистовой без рисок).
Неуказанные предельные отклонения отверстий H14
Маркировать: обозначение резьбы
класс точности метчика (только для чистового)
товарный знак завода-изготовителя (М36-Н3-У10А).
Профиль канавочной фрезы (шаблон)
Исполнительные размеры резьбы
Резец фасонный.cdw

Твёрдость резца 63 66 HRC.
Материал шаблона и контршаблона - сталь Х12 или другая для измерительного инструмента.
Твёрдость шаблона и контршаблона 62 65 HRC.
Размеры контурных точек профиля резца получить коррекционным расчётом с отклонением
Неуказанные предельные отклонения размеров отверстий Н14
Маркировать: код (номер) обрабатываемой заготовки
товарный знак завода-изготовителя (00736-Р18-h
Курсовая.doc
Казахский национальный технический университет имени К.И. Сатпаева
Кафедра «Станкостроение материаловедение и технология
машиностроительного производства»
На тему «Расчёт и проектирование металлорежущих инструментов»
0712 – «Машиностроение»
(шифр и наименование специальности)
Научный руководитель
(должность уч. степень звание)
Р.К. Карпеков И.О.Ф.
Шифр и наименование специальности 050712 – «Машиностроение»
на выполнение курсовой работы
Тема «Расчёт и проектирование металлорежущих инструментов»
Перечень подлежащих разработке в курсовой работе вопросов или краткое содержание курсовой работы
Рассчитать и спроектировать следующие металлорежущие инструменты:
а) круглый фасонный резец;
б) круглая внутренняя протяжка;
в) чашечный прямозубый долбяк;
г) червячная модульная фреза;
д) комплект метчиков.
Перечень графического материала (с точным указанием обязательных
чертежей) Рабочие чертежи круглого фасонного резца круглой внутренней протяжки чашечного прямозубого долбяка червячной модульной фрезы комплекта метчиков.
Рекомендуемая основная литература: Семенченко И.И. Матюшин В.М. Сахаров Г.Н. Проектирование металлорежущих инструментов. М.: Машгиз 1962. – 952 с.: ил.; Металлорежущие инструменты: Учебник для вузов по специальностям «Технология машиностроения» «Металлорежущие станки и инструменты» Г.Н. Сахаров О.Б. Арбузов Ю.Л. Боровой и др. – М.: Машиностроение 1989. – 328 с.: ил.
подготовки курсового проекта (работы)
Наименование разделов перечень
разрабатываемых вопросов
Сроки представления научному
Расчёт и проектирование фасонного резца
Расчёт круглой внутренней протяжки
Расчёт прямозубого долбяка
Расчёт червячной фрезы
Расчёт комплекта метчиков
Расчёт и проектирование фасонного резца ..
Расчёт круглой внутренней протяжки
Расчёт прямозубого долбяка ..
Расчёт червячной фрезы .
Расчёт комплекта метчиков
Список используемой литературы
Приложение А. Рабочий чертёж круглого фасонного резца ..
Приложение Б. Рабочий чертёж круглой внутренней протяжки
Приложение В. Рабочий чертёж прямозубого долбяка ..
Приложение Г. Рабочий чертёж червячной модульной фрезы ..
Приложение Д. Рабочий чертёж комплекта метчиков
По сравнению с другими методами получения деталей машин обработка резанием обеспечивает наибольшую их точность и наибольшую гибкость производственного процесса создает возможности быстрейшего перехода от обработки заготовок одного размера к обработке заготовок другого размера.
Режущий инструмент срезая сравнительно тонкие слои материала придает заготовке нужную форму и размеры. Работоспособность режущего инструмента его надежность оказывают существенное влияние на экономическую эффективность процесса производства.
Потребность в режущем инструменте колоссальна. По некоторым операциям обработки заготовки резанием стоимость инструмента составляет значительную часть стоимости операции.
Режущий инструмент обеспечивает внутренние связи процесса обработки. Качество и стойкость инструмента во многом определяют производительность и эффективность процесса обработки а в некоторых случаях и вообще возможность получения деталей требуемых формы качества и точности. Повышение качества и надежности режущего инструмента способствуют повышению производительности обработки металлов резанием.
В курсовой работе рассматривается расчёт и проектирование нескольких инструментов: круглого фасонного резца; круглой внутренней протяжки; чашечного прямозубого долбяка; червячной модульной фрезы; комплекта метчиков.
Дано: прутковый материал диаметром 60мм материал заготовки автоматная сталь А30 B = 600МПа. Заготовку обрабатывают с подготовкой под последующую отрезку (рисунок 1).
Необходимо рассчитать и сконструировать круглый фасонный резец с отверстиями под штифт для наружного обтачивания фасонной заготовки.
Рисунок 1. Эскиз заготовки
-Определить передний и задний углы α =10º γ =25º.
-Определить дополнительные режущие кромки под отрезку и подрезку: b1 =1 мм - перекрытие режущей кромки под отрезку; b = 5 мм - ширина режущей кромки под отрезку; с = 2 мм - ширина концевой режущей кромки; а = = 3 мм - ширина дополнительной упрочняющей режущей кромки; φ1 = 18º - угол концевой режущей кромки; φфас = 45º.
-Определить общую ширину резца вдоль оси заготовки:
LР = lД + а + с + b + b = 68 + 3 + 2 + 5 + 1 = 79 мм. (1)
-Наибольшая глубина профиля детали tmax =10 мм.
-Определить габаритные и конструктивные размеры резца с отверстиями под штифт для наибольшей глубины профиля tma d(Н8) = 22 мм; d1 = 34 мм; b = 15 мм; К = 4 мм; r = 2 мм; D1 = 42 мм; d2 = 5 мм; l2 = l = = 14 мм.
Высота заточки резца:
Н = R sin(α + γ) = 375 sin(10 + 25) = 21509 мм. (2)
Высота установки резца:
h = R sin α = 375 sin10 = 6511 мм. (3)
-Согласно размерам на чертеже заготовки радиусы окружностей узловых точек профиля заготовки и осевые расстояния до этих точек от торца до заготовки следующие:
-корректировка профиля резца (Таблица 1).
Коррекционный расчёт резца
продолжение таблицы 1
-Построить шаблоны и контршаблоны для контроля фасонного профиля резца т.е. определить разность радиусов всех узловых точек рассчитанного фасонного профиля относительно узловой контурной точки 1.
Р2 = R1 - R2 = 37500 - 37500 = 0 мм (4)
Р3 = R1 - R3 = 37500 - 34881 = 2658 мм (5)
Р4 = Р5= R1 - R4 = 37500 - 30178 = 7333 мм (6)
Р6 = R1- R6 = 37500 - 29474 = 8051 мм (7)
Р7 = R1 - R7 = 37500 - 34052 = 3448 мм. (8)
На рисунке 2 показано расположение координатных размеров профиля обрабатываемой заготовки круглого фасонного резца и шаблона по данным расчёта.
Рисунок 2. Расположение координатных размеров профиля круглого фасонного резца
Рабочий чертёж резца в приложении А.
-Протягиваемая заготовка: материал – 20ХН3А; твёрдость при протягивании НВ = 241; заготовка – после отпуска; отверстие предварительно обработано; диаметр отверстия до протягивания D0 = 636Н12(+019) мм; диаметр отверстия после протягивания D = 65Н7(+003) мм; параметр шероховатости поверхности Rа = 125 мкм; длина протягивания l = 120-1 мм.
-Тип станка – горизонтально-протяжной модель 7Б56 тяговая сила Q = 196200 Н максимальная длина хода штока Lmax = 1600 мм диапазон рабочих скоростей 15 – 11 ммин. Протяжка закрепляется в быстросменном патроне.
-Характер производства – массовый.
-Длина протяжки допустимая возможностями инструментального цеха и заточного отделения не более 1500 мм.
Необходимо рассчитать и сконструировать круглую протяжку для обработки цилиндрического отверстия.
-Установить группу обрабатываемости – сталь 20ХН3А относится ко II группе обрабатываемости.
-Установление группы качества – 1 группа качества по шероховатости.
-Выбор материала рабочей части протяжки – Р6АМ5.
-Конструкцию протяжки принимаем с приваренным хвостовиком материал хвостовика – сталь 40Х. Диаметр переднего хвостовика Dхв = 50 мм площадь опасного сечения Fоп = 11341 мм2. Рассчитать силу допустимую хвостовиком:
Рхв = []Р · Fоп = 11341 · 300 = 340230 Н ([]Р = 300МПа). (9)
-Выбор переднего и заднего углов (таблица 2)
Углы зубьев протяжки
Черновые и переходные (град)
-Установить скорость резания – V = 8 ммин.
-Определить подъём черновых зубьев из условия равной стойкости черновой и чистовой частей (TM = 56 м SZЧ = 003 ммзуб) - SZ0 = 01 мм. Принимаем поправочные коэффициенты на наработку: КТВ = 07; КТр = 1; КТЗ = 1; КТМ = 1; КТД = 1; КТО = 1 (назначаем СОЖ – сульфофрезол ГОСТ 122 – 54).
ТМН = ТМ · КТВ · КТр · КТЗ · КТМ · КТД · КТО = 56 · 07 ·1 · 1 · 1 · 1 · 1 = 392 мм (10)
-Определить глубину стружечной канавки h необходимой для размещения стружки при подъёме черновых зубьев SZС = 01 мм:
h = 11283 = 11283= 677 7 мм (11)
- суммарная длина протягивания = 01.
-Определить шаг черновых зубьев: t0 = 16 мм; r = 35 мм; b = 5 мм; R = = 11 мм; Fакт = 30 мм2; номер профиля 11. (Рисунок 3)
Рисунок 3. Размеры профиля черновых зубьев протяжки
Определить число одновременно участвующих в работе зубьев:
zр = +1 = + 1 = 8 (12)
-Сила резания ограничивается тяговой силой станка или прочностью протяжки в опасных сечениях по хвостовику и по впадине перед первым зубом:
Рст = 08 · 20000 · 981 = 156960 Н; Рхв = 340230 Н; (13)
Роп = Fоп · []Р = 1931 · 400 = 772400 Н ([]Р = 400МПа); (14)
Fоп = 0785 (D0 – 2h)2 = 0785 [636 – (2 · 7)] = 1931 мм2; (15)
-Определить число зубьев в группе:
где q0 = 212 H; zp = 8; КРм = 13; КР0 = 1; КРк = 1; КРр = 1.
-Определяем расчётную силу протягивания:
Р = = = 225114 Н. (17)
-Определить полный припуск на диаметр который распределяется между черновыми переходными и чистовыми зубьями:
А = Dmax – D0min = 6503 – 636 = 143 мм. (18)
Припуск на черновые зубья:
А0 = А – (Ап + Ач) = 143 – (014 + 014) = 115 мм (19)
где Ап = 014; Ач = 014.
-Определить число групп черновых зубьев:
i0 = = = 975 9. (20)
Определить остаточную часть припуска:
Аост = А0 – 2Sz0i0 = 115 – 2 · 01 · 5 = 015 мм. (21)
Так как остаточный припуск Аост >= Szп1 то Аост оставляем в черновой части и увеличиваем число групп на одну; i0 = 6.
-Определить число черновых зубьев:
z0 = i0zc0 = 9 · 2 = 18 (22)
Число переходных зубьев zп = 4 чистовых зубьев zч = 12 калибрующих зубьев zк = 7.
Общее число всех зубьев:
= z0 + zп + zч + zк = 18 + 4 + 12 + 7 = 41. (23)
-Определить длину режущей части протяжки:
Lp = l0 + lп + lч + lк = t0(z0 + zп) + + (24)
где и - суммы переменных шагов соответственно чистовых и калибрующих зубьев.
Шаги чистовых и калибрующих зубьев — переменные t1= 11 мм t2 =12 мм t3 = 13 мм.
Lp = 16·(18 + 4) + (13 + 12 + 11)·4 + (13 + 12 + 11)·2 + 13 = 581 мм. (25)
-Диаметр калибрующих зубьев Dк = Dmax = 6503 мм.
-Число выкружек их ширина и радиус на черновых зубьях: N = 12 а0 = 85 мм Rв = 30 мм радиус шлифовального круга Rк = 25 мм.
-Число выкружек на переходных и чистовых зубьях:
Nч = 145 = 145= 12. (26)
Ширину выкружек на переходных и чистовых зубьях для обеспечения перекрытия выкружек режущими секторами последующих зубьев принимают на 2 – 3 мм меньше чем черновых:
ап = а0 – (2 ÷ 3) = 85 – 2 = 65 мм. (27)
Радиус выкружек Rв = 30 мм радиус шлифовального круга Rк = 25 мм
-Диаметр и длина передней направляющей:
Dп.н = 636е8 lп.н = 075 · 120 = 90 мм (28)
- Длина переходного конуса lп.к = 20 мм.
-Расстояние от переднего торца протяжки до первого зуба:
L1 = l1 + l2 + l3 + l + 25 = 160 + 25 + 40+120 + 25=370 мм. (29)
-Диаметр и длина задней направляющей: Dз.н = 65f7 мм lз.н = 50 мм. Протяжку выполняем с задним хвостовиком. Диаметр заднего хвостовика принимаем меньшим чем диаметр переднего хвостовика Dз.хв = 36 мм длина заднего хвостовика lз.хв = 125 мм.
-Общая длина протяжки:
L = L1 + Lp + lз.н + lз.хв = 370 + 581 + 50+125=1126 мм. (30)
Рабочий чертёж протяжки в приложении Б.
Дано: рассчитать чашечный прямозубый долбяк для обработки зубчатых колес с числом зубьев от z1 = 20 до z2 = 60 с модулем m0 = 25 мм углом зацепления α = 20° номинальным делительным диаметром Dt = 50 мм. Степень точности нарезаемых колес — 8-я. Материал заготовки — сталь 45 с B = 650 МПа.
-Определить число зубьев долбяка:
-Геометрические параметры режущей части: αВ – задний угол при вершине для чистовых долбяков - 6° передний угол γ = 5°. Основные конструктивные размеры принимаем по ГОСТ 9323-79* (для долбяков 3-го типа класса точности В); диаметр делительной окружности d0 = 50 мм; диаметр окружности вершин зубьев dа0 = 5675 мм; диаметр посадочного отверстия d1 = 20Н4(+0005); диаметр выточки d2 = 28 мм; диаметр ступицы d3 = 37 мм; расстояние исходного сечения от передней поверхности А = 24 мм; ширина ступицы b1 = 12 мм; длина зубьев b0 = 15 мм; высота долбяка В = 25 мм; число зубьев z0 = 20.
-Определить допустимое смещение передней плоскости от исходного сечения:
где Eu = 0095 – коэффициент смещения.
-Размеры профиля зубьев долбяка в проекции передней поверхности на плоскость перпендикулярную к оси: высота головки hа0 = 3375 мм; толщина зуба теоретически делительная S0 = 4109 мм; диаметр основной окружности db0 = 46933 мм.
-Технические требования на долбяк чашечный типа 3 класса В принимаем по ГОСТ 9323-79*.
Рабочий чертёж долбяка в приложении В.
Рассчитать червячную фрезу для обработки цилиндрических зубчатых колёс.
Дано: угол зацепления α = 20° модуль m = 20 мм материал заготовки – сталь 45 B =600МПа К = 2.
-Рассчитать профиль зуба фрезы:
а) рассчитать шаг по нормали:
tn = · m · K = 314 · 20 · 2 = 125664 мм. (33)
б) толщина зуба в нормальном сечении на диаметре делительного цилиндра червяка:
Sn = = = 3182 мм. (34)
в) высота головки зуба:
h' = 125 · m = 125 · 20 = 25мм. (35)
г) высота ножки зуба:
h'' = 125 · m = 125 · 20 = 25мм. (36)
д) полная высота зуба:
h = h'+h'' = 25 + 25 = 50 мм. (37)
е) радиус закругления головки зуба:
r1 = 025 · m = 025 · 20 = 5 мм (38)
Примем r1 = 76 по ГОСТ 9324-80.
ж) радиус закругления ножки зуба:
r2 = 03 · m = 03 · 20 = 6 мм (39)
Примем r2 = 4 по ГОСТ 9324-80.
з) толщина зуба на вершине:
Sa = Sn – 2h' · tg α = 3182 – 2 · 25 · tg 20 = 13621 мм. (40)
и) размеры канавок облегчения шлифования профиля:
b1 = 03 · Sn = 03 · 3182 = 6 мм – ширина канавки;
h3 = 05 ÷ 2 примем 1 мм – глубина канавки;
r3 = 06 ÷ 13 примем 1 мм – радиус канавки.
-Найти геометрические параметры режущей части фрезы:
а) определить задний угол в нормальном сечении:
tg αв = = = 01532 αв 9° (41)
где αб = 3° – задний угол на боковых сторонах профиля зуба червячной фрезы
α = 20° – угол зацепления.
б) определить затылование:
К = tg αв = tg 9 16 мм (42)
D = 250 мм из ГОСТ 9324-80.
в) определить дополнительное затылование:
К1 = (12 ÷ 15)К = 15 · 16 = 24 мм.
г) передний угол γ=0°.
д) определить угол подъема винтовой линии червяка на делительном цилиндре:
sin = = = 0101626 (43)
Dt = D – 25m – 025K = 250 – 25 · 20 – 025 · 5921 = 1968 мм (44)
е) шаг стружечной канавки:
Sк = = = 6052 мм. (45)
ж) ход витков на оси:
tос = = = 126318 мм. (46)
-Определить элементы стружечных канавок фрезы:
H = (h + r) + = (50 + 2) + = 72 мм (47)
б) угол профиля канавки = 20 ÷ 30° примем 30°
Рабочий чертёж фрезы в приложении Г.
Дано: размер нарезаемой резьбы и её точность М36х6Н; комплект из трёх метчиков; нарезается резьба в изделии из стали 45 с пределом прочности B = = 800МПа.
Необходимо рассчитать и сконструировать комплект ручных метчиков.
-выбрать номинальные размеры для метрической резьбы. Шаг Р – 4 мм; наружный диаметр d = 36 мм; средний диаметр d2 = 33402 мм; внутренний диаметр d1 = 31670 мм; высота резьбы Н = 2165 мм.
-выбрать допустимое отклонение на диаметр резьбы. (–) Тd = 118 мкм; (+) Тd2 = 165 мкм.
-рассчитать конструктивные размеры метчиков:
а) длину режущей части:
) чернового 6Р = 6 · 4 = 24 мм;
) среднего 4Р = 4 · 4 = 16 мм;
) чистового 2Р = 2 · 4 = 8 мм.
б) длину калибрующей части:
lк = (6 ÷ 12)Р = 9 · 4 = 36 мм. (48)
в) диаметр сердцевины:
dс = (04 ÷ 05)d = 05 · 36 = 18 мм. (49)
b = 02d = 02 · 36 = 72 мм. (50)
-рассчитать размеры наружного внутреннего и среднего диаметров резьбы отдельных метчиков в комплекте.
Для чернового метчика наружный диаметр
= – 055Р = 36 – (055 · 4) = 338h11 мм. (51)
= d2 – 016Р = 33402 – (016 · 4) = 32762h9 мм. (52)
= d1 – (003 + 012) = 31670 – (003 + 012) = 314 мм. (53)
Для среднего метчика наружный диаметр
= – 017Р = 36 – (017 · 4) = 3532h11 мм. (54)
= d2 – 0067 = 33402 – 0067 = 33268h9 мм. (55)
= d1 – 009 = 31670 – 009 = 3149 мм. (56)
Для чистового метчика наружный диаметр
dmin = + 04t = 36 + (04 · 0047) = 36188 мм. (57)
d2min = d2 + 03t = 33402 + (03 · 0047) = 33416 мм. (58)
d2max = d2 + 05t = 33402 + (05 · 0047) = 33426 мм (59)
-определить диаметр заборной части на переднем торце метчика. Он берётся на 02 ÷ 025 мм меньше внутреннего диаметра резьбы 3167 – 025 = = 3142 мм.
-углы заборной части по ГОСТ 3266-81 чернового 5º30 среднего 8º30 чистового 17º.
-значения геометрических параметров режущих элементов:
а) передний угол γ = 10º;
б) задний угол α = 10º;
в) падение затылка по вершинам витков заборной части:
К = tg α = tg 10 5 мм (60)
где z – число стружечных канавок.
г) обратная конусность калибрующей части 016 ÷ 02 на 100 мм
-количество и форма стружечных канавок из приложения 1 ГОСТа 3266-81.
-выбрать центровые отверстия форма А ГОСТ 14034-74.
-выбрать размеры квадрата хвостовика по ГОСТ 9523-84.
Рабочий чертёж комплекта метчиков в приложении Д.
В машиностроении для обработки заготовок деталей машин необходимо много различных видов инструментов. Их классификация по различным признакам приведена в литературе. Для изучения наиболее целесообразно рассматривать инструменты по конструктивному признаку (резцы фрезы протяжки) с учетом их служебного назначения (для обработки отверстий резьбообразующие и др.).
При проектировании инструментов в особенности инструментов для обработки фасонных поверхностей необходимы сложные расчеты. Для их выполнения применяют систему автоматизированного проектирования режущих инструментов (САПР РИ). При использовании инструментов необходимо обеспечить их правильную эксплуатацию условия которой должны быть учтены при разработке конструкций.
СПИСОК ИСПОЛЬЗУЕМОЙ ЛИТЕРАТУРЫ
Кривоухов В.А. Петруха П.Г. Бруштейн Б.Е. Резание конструкционных материалов режущие инструменты и станки. М.: Машиностроение 1967. – 654 с.: ил.
Металлорежущие инструменты: Учебник для вузов по специальностям «Технология машиностроения» «Металлорежущие станки и инструменты» Г.Н. Сахаров О.Б. Арбузов Ю.Л. Боровой и др. – М.: Машиностроение 1989. – 328 с.: ил.
Нефедов Н. А. Осипов К. А Сборник задач и примеров по резанию металлов и режущему инструменту: Учеб. пособие для техникумов по предмету «Основы учения о резании металлов и режущий инструмент». – 5-е изд. перераб. и доп. – М.: Машиностроение 1990. – 448 с.: ил.
Протяжки для обработки отверстий Д.К. Маргулис М.М. Тверской В.Н. Ашихмин и др. – М.: Машиностроение 1986. – 232 с.: ил.
Руководство по курсовому проектированию металлорежущих инструментов: Учеб. пособие для вузов по специальности «Технология машиностроения металлорежущие станки и инструменты»Под общ. ред. Г. Н. Кирсанова – М.: Машиностроение 1986. – 288 с.: ил.
Семенченко И.И. Матюшин В.М. Сахаров Г.Н. Проектирование металлорежущих инструментов. М.: Машгиз 1962. – 952 с.: ил.
Справочник инструментальщикаИ.А. Ординарцев Г.В. Филиппов А.Н. Шевченко и др.; Под общ. ред. И. А. Ординарцева. – Л.: Машиностроение. Ленингр. отд-ние 1987. – 846 с.: ил.