Расчет шестигранной протяжки и фасонного резца


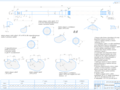
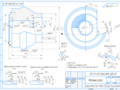
- Добавлен: 24.01.2023
- Размер: 2 MB
- Закачек: 0
Узнать, как скачать этот материал
Подписаться на ежедневные обновления каталога:
Описание
Расчет шестигранной протяжки и фасонного резца
Состав проекта
![]() |
![]() |
![]() ![]() ![]() |
![]() ![]() ![]() ![]() |
![]() ![]() ![]() ![]() |
Дополнительная информация
Контент чертежей
620481_01.doc
Кафедра: «ИНСТРУМЕНТАЛЬНЫЕ И МЕТРОЛОГИЧЕСКИЕ СИСТЕМЫ»
по дисциплине: «Режущий инструмент»
(индекс группы) [дата подпись] (фамилия и инициалы)
Академическая оценка
Министерство образования и науки РФ
Государственное образовательное учреждение
высшего профессионального образования
«Тульский государственный университет»
Кафедра: "ИНСТРУМЕНТАЛЬНЫЕ И МЕТРОЛОГИЧЕСКИЕ СИСТЕМЫ
на курсовой проект по дисциплине:
«Режущий инструмент»
(шифр группы) (фамилия и инициалы)
СРОК ЗАЩИТЫ РАБОТЫ до 30.05.11
ИСХОДНЫЕ ДАННЫЕ № __7-68 1-100_
ПЕРЕЧЕНЬ ВОПРОСОВ ПОДЛЕЖАЩИХ РАЗРАБОТКЕ:
Разработать теоретическую часть.
Спроектировать фасонный резец для обработки заданного профиля.
Спроектировать шестигранную протяжку для обработки заданного отверстия детали.
ГРАФИЧЕСКИЙ МАТЕРИАЛ:
Рабочий чертеж круглого фасонного резца.
Рабочий чертеж протяжки для обработки шестигранного отверстия.
РЕКОМЕНДУЕМАЯ ЛИТЕРАТУРА:
Методические материалы кафедры ИМС и указанная в них литература
ФИО студента * индекс группы*
Расчет шестигранной протяжки и фасонного резца
Работа представленная на рецензию содержит:
- пояснительную записку на __36__ листах.*
- графический материал на _2_ листах форматов _А1_ и _А3_.
Содержание работы соответствует (не соответствует) названию и техническому заданию.
Теоретическая и расчетная части работы выполнены в полном (необоснованно сокращенном) объеме и не содержат (содержит отдельные содержит грубые) ошибок.
Содержание обоих разделов в основном полностью (отдельные части работы) соответствует требованиям нормативной документации ЕСКД.
Работа выполнена в хорошем стиле изложения с использованием достаточного (не достаточного) количества литературных источников.
Электронный вариант работы соответствует напечатанному.
По существу излагаемого материала к представленной работе замечаний нет.
В целом работа соответствует (не соответствует) требованиям предъявляемым к работам данного вида и заслуживает оценки
Резюмируя изложенное по моему мнению работу следует рекомендовать для защиты.
графы заполняются студентом
В результате выполнения курсовой работы были проведены расчёты и проектирование режущих инструментов выданных на основании заданий для закрепления знаний по предмету « Режущий инструмент». Вследствие чего был разработан круглый фасонный резец спроектирована шестигранная протяжка. Выполняя работу было освоено последовательность ведения работы в проектировании инструмента всесторонне-объективный подход к поставленной задаче и более чёткое привлечение требуемой литературы.
Теоретическая часть курсовой работы по теме: инструментальные материалы7
Спроектировать режущий инструмент для протягивания шестигранного отверстия.12
1. исходные данные13
2. схема резания при протягивании шестигранных отверстий.14
3. подъём на зуб и биение число зубьев протяжки.15
4. размеры зубьев протяжки.16
5. геометрические параметры зубьев протяжек17
6. Определение усилия протягивания и расчёт протяжки на прочность.19
8. параметры формообразующий части протяжки21
9. размеры гладких частей протяжек22
10. термообработка протяжек.23
11. допуски на элементы и размеры протяжек.23
Расчет круглого фасонного резца.24
1 Расчёт средних размеров профиля.24
2 Выбор положения базовой линии.24
3. Расчёт габаритных размеров резца.25
4. Коррекционный расчёт профиля.26
5 Анализ величин передних и задних углов режущей части резца31
Список использованной литературы35
Целью данного курсового проекта является расчет и проектирование режущих инструментов: протяжка шестигранная круглый фасонный резец.
Протягивание является одним из наиболее высокопроизводительных процессов обработки деталей резанием. Высокая производительность процесса протягивания объясняется тем что одновременно находится в работе несколько зубьев инструмента с большой суммарной длиной режущих кромок. Протягивание позволяет получать поверхности высокой точности (6-го – 8-го квалитетов точности) и низкой шероховатости (Ra=0.63-0.25мкм).
Фасонные резцы обеспечивают идентичность формы и необходимую точность деталей высокую производительность обработки и обладают большой долговечностью благодаря значительному количеству допустимых переточек. Они применяются в мелкосерийном серийном и массовом производствах для обработки наружных и внутренних поверхностей на токарных автоматах полуавтоматах и револьверных станках.
Теоретическая часть курсовой работы по теме: инструментальные материалы
Инструментальный материал должен иметь?
1. высокую твёрдость5
2. низкую твёрдость2
3. высокую плотность 2
4. низкую плотность 2
5. низкую скорость резания2
Какие материалы не применяют для изготовления режущих инструментов?
1. техническое железо5
2. инструментальные стали (углеродистые легированные и быстрорежущие2
3. минералокерамические материалы2
4. абразивные материалы2
При какой температуре твёрдость сталей У10А У11А У12А резко уменьшается?
Какая сталь не применяется для производства быстрорежущей стали нормальной производительности?
Для чего инструментальный материал должен иметь высокую твердость?
1. для того чтобы в течение длительного времени срезать стружку5
2. для утяжеления веса 2
3. для уменьшения теплостойкости2
4. для точности резания2
5. для всего выше перечисленного2
Режущая часть инструмента должна иметь большую износостойкость в условиях?
1. высоких давлений и нагрева5
2. низкого давлений и нагрева2
3. низкой скорости резания2
4. высокой производительности2
5. низкой производительности2
При каких условиях происходит выкрашивание режущих кромок?
1. при недостаточной прочности5
2. при высокой прочности 2
3. при низких режимах резания2
4. при низком давлении2
5. при низком нагреве2
Почему инструментыиз углеродистых инструментальных сталей плохо шлифуются?
1. из-за низкой твёрдости2
2. из-за сильного нагревания отпуска и потери твердости режущих кромок5
3. из-за увеличения твёрдости2
4. из-за большой потери времени2
5. из-за низкой деформации2
С целью улучшения свойств углеродистых инструментальных сталей были разработаны?
1. минералокерамические материалы2
2. низколегированные стали5
4. высоколегированные стали2
5. быстрорежущие стали2
Чем отличаются легированные инструментальные стали от углеродистой?
1. более высокой прокаливаемостью и закаливаемостью5
2. более высокими режущими свойствами2
3. менее высокой прокаливаемостью и закаливаемостью2
5. менее высокими режущими свойствами2
Сталь Р18 особенно в крупных сечениях (диаметром более 50 мм) с большой карбидной неоднородностью целесообразно заменять?
1. на стали Р6М3 и Р125
2. на сталь Р10К5Ф52
5. на сталь Р18К5Ф22
К однокарбидиым сплавам группы ВК относятся сплавы?
1. ВК2 ВКЗ ВК4 ВК6 ВК8 ВК10 ВК155
2. Р18Ф2 Р18К5Ф2 Р9К5 Р9К10 Р14Ф4 Р9Ф5 Р10К5Ф52
5. Т30К4 Т15К6 Т14К8 Т5К10 Т5К12Б2
Из чего состоят твёрдые сплавы для производства режущих инструментов?
1. Из карбидов вольфрама титана тантала сцементированных небольшим количеством кобальта5
2. из титана тантала алюминия2
3. из карбидов вольфрама2
До какой температуры инструменты оснащенные твердым сплавом не теряют своих режущих свойств?
Для обозначения мелкозернистой структуры в конце марки сплава ставится буква?
Сколько структур может иметь вольфрамокобальтовый сплав ВК6?
Крупнозернистые сплавы в частности сплав ВК8В не применяют для?
1. резания с ударами при черновой обработке2
2. чистовой обработки при тонких сечениях среза стальных чугунных пластмассовых и других деталей5
3. обработки жаропрочных сталей с большими сечениями среза2
4. нержавеющих сталей2
5. для черновой обработки2
Сплавы группы ТК (Т30К4 Т15К6 Т14К8 Т5К10 Т5К12Б) цифра после буквы К показывает процентное содержание?
3. карбиды вольфрама2
При введение в состав сплава карбидов тантала?
1. уменьшается прочность2
2. уменьшается твёрдость2
3. не меняется режим резания2
4. увеличивает красностойкость2
5. снижает красностойкость5
С целью экономии дефицитного вольфрама разрабатываются безвольфрамовые металлокерамические твердые сплавы на основе карбидов какой из них не входит в это число?
Спроектировать режущий инструмент для протягивания шестигранного отверстия.
Размер между сторонами 22+004 мм.
Предварительное отверстие ø21+0.1 мм
Материал детали сталь 35Х в =69 кгмм2
Станок горизонтально-протяжной.
отверстие получаемое протягиванием задаётся расстоянием S между сторонами диаметром Dм по углам и длинной Lg протягиваемой детали. (рис.1)
расстояние между сторонами S=22+004 мм.
Диаметр отверстия под протягивание D0 =218+01 мм.
Длина детали Lg =40 мм.
Материал детали Ст 35Х;в=69 кгмм2
Протягивание осуществляется на горизонтально-протяжном станке модели 7520 с применением эмульсии.
Рассчитаем диаметр Dм по углам для шестигранного отверстия :
Величина радиуса скругления принимается равной 005 Dм
Rmax=2204(2*086607)=12724
Учитывая величину скругления наибольший диаметр
2. схема резания при протягивании шестигранных отверстий.
Схема резания характеризует последовательность удаления припуска с поверхности заготовки. Поэтому выбор схемы резания предшествует созданию конструкции инструмента.
Наиболее распространенной схемой протягивания при обработке профиля квадратных шестигранных и вообще многогранных отверстий является генераторная схема (рис. 2). Протяжка работающая по этой схеме имеет поперечное сечение по первому зубу соответствующее форме предварительного цилиндрического отверстия. Последующие зубья очерчиваются с углов дугами концентрических окружностей а с боков прямыми линиями расстояние между которыми является постоянным для всех зубьев и равным поперечному размеру квадрата или шестигранника. Радиус режущих лезвий обрабатывающих угловые участки увеличивается на каждом зубе на величину подъёма. По мере удаления припуска периметр этих лезвий укорачивается в то время как прямолинейные боковые лезвия удлиняются. Конструктивная форма зубьев показана на рис. 3.
Поскольку периметр режущих лезвий при такой схеме протягивания переменный то для обеспечения их равностойкости необходимо чтобы площади отдельных ими слоёв были одинаковыми.
f1=b1*Sz1=b2*Sz2= ..
Где b1 b2 - периметры режущего лезвия Sz1 Sz2 . -подъёмы на зуб (соответственно на зубья 1 2-м и т.д.)
Поэтому все зубья протяжки разбиваются на несколько стержней принимая подачу Sz постоянной в пределах каждой ступени.
Такие протяжки называются ступенчатыми.
Для шестигранных протяжек
При S≤ 20 мм. Принимаются 2 ступени.
При S> 20 мм. Принимаются 3 ступени.
Таким образом припуск (см. рис. 2) приходящийся на каждую из ступеней будет различным и может быть определено зависимости
Аот- припуск на диаметре для каждой ступени (индекс m соответствует порядковому номеру ступени)
Для шестигранной протяжки имеющий S=22 мм следует применить 3 ступени. Припуск для каждой из ступеней будет следующим
A01=0025*22=055 мм 06 мм
А02=0037*22=081 мм 08 мм
А03=009*22=198 мм 2 мм
Подсчитанное значение припуска не учитывает величину притупления по углам многогранника. Поэтому приняв притупление примерно005Dм что составляет 1 мм нужно на 3-й ступени уменьшить припуск на величину 1 мм.
3. подъём на зуб и биение число зубьев протяжки.
Sz1=005 мм ; 2Sz2=010 мм ; 2Sz3=015 мм ;
число режущих зубьев протяжки
Где Z1 Z2 Z3 .- число зубьев для каждой ступени рассчитанное по зависимостям
на 1-й ступени Z1=A012Sz ;
на 2-й ступени Z2=A022Sz ;
па 3-й ступени(последней) Z3=A032Sz +(2 4)
принимаем Z1 = 10мм; Z2=8 мм ; Z3=8 мм ;
калибрующие зубья Zк = 5
тогда общее число зубьев протяжки
Z=Z1+ Z2+ Z3+Zk=10+8+8+5=31
4. размеры зубьев протяжки.
Зубья протяжки характеризуются глубиной канавки h0 радиусом r скругления дна канавки и шагом tp (рис.4)
Минимальная глубина h0 min стружечной канавки режущих зубьева следовательно и все остальные размеры зуба рассчитываются из условий заполнения канавок стружкой
h0 min= 113 где kmin- минимальное значение коэффициента заполнения канавки стружкой.
h0 min1 =113=113*158=18 мм
h0 min2 =113=113*245=28 мм
h0 min3 =113=113*324=37 мм
Принимаем h0 min3 =4 мм . на последней ступени можно допустить невыполнение неравенства K>Kmin так как имеется достаточно места для размещения стружки.
Размеры шагов tp для трёх ступеней будут:
tp1=275*h0 min1=49 мм 5 мм
tp2=275*h0 min2=77 мм 75 мм
tp3=275*h0 min3=101 мм 10 мм
Пользуясь данными на основе канавки находим значения
g1=15 ; g2=3 ; g3=3 ; r1=1 ; r2=15 ; r3=2 ;
Шаг калибрующих зубьев принимается равным шагу режущих зубьев кроме протяжек для точных отверстий (2 и3 класса) у которых он делается меньше а именно tk=(06 07)tp но не менее 4 мм.
В данном случае размеры стружечной канавки на калибрующей части имеют такие же размеры как на последней ступени: tk=tp
5. геометрические параметры зубьев протяжек
зубья протяжки должны иметь передние и задние углы обеспечивающие наибольшую стойкость протяжек и требуемую чистоту образуемых ими поверхностей.
Величина переднего угла выбирается в зависимости от свойств обрабатываемого материала.
При выборе величины задних углов необходимо принимать во внимание необходимость сохранения размеров протяжки в течение длительного времени. Протяжки перетачиваются по передней поверхности причём размеры поперечного сечения протяжки по лезвию убывают интенсивнее при больших величинах задних углов.
Для отверстий 2-го и 3-го классов точности у квадратных и шестигранных протяжек рекомендуется задний угол αp=2 30 а для отверстий 4-го и ниже точности- αp=3 40
γp=150 ; αp=30 (рис 4)
У калибрующих зубьев передний угол принимается таким же как и у режущих зубьев протяжки. Задний угол αк=20 . вдоль лезвий калибрующих зубьев делается ленточка f которая предназначается для сохранения размеров протяжки при переточке. Ширина ленточки f делается равной 002мм. Канавки для деления стружки снабжаются режущие зубья протяжки обрабатывающие стали и другие вязкие материалы. При протягивании чугуна и других хрупких материалов канавки для деления стружки необязательны. Канавки располагаются в шахматном порядке (рис.5)
Форма канавок угловая с закруглённой впадиной. Канавки наносятся по направлению движения параллельно задней поверхности зуба протяжки.
Размеры стружкоделительных канавок принимаются в зависимости от диаметра протяжки а количество канавок- в зависимости от ширины режущего лезвия. При ширине лезвия bi=4 10 мм делается одна канавка при ширине режущего лезвия bi=20 30 мм 3 канавки. На зубьях режущих лезвия которых представляют собой дуги окружностей количество канавок принимается такое же кА у протяжек для цилиндрических отверстий. Расстояние целесообразно принимать наименьшим. Но для обеспечения прочности не менее 2-25 мм.
В данном случае nk=12 hk=07 05 мм Sk=1=08 мм rk= 03 02 мм . С 2-го зуба по 14-й зуб включительно необходимо делать по 2 канавки на каждом участке режущего лезвия а с 15-го по 25-й зуб включительно по одной стружкоделительной канавке в шахматном порядке.
6. Определение усилия протягивания и расчёт протяжки на прочность.
При конструировании протяжек необходимо производить расчёт на прочность с тем чтобы предотвратить разрыв их от действия усилия протягивания. Усилие протягивания не должно превосходить тяговое усилие станка. Максимальное тяговое усилие обеспечивают только новые станки но и в этом случае рекомендуется проводить расчёт протяжек на положительную нагрузку (09 095)Q где Q -тяговое усилие станка по паспорту. Для станков не новых но находящихся в хорошем состоянии нужно ориентироваться на 08Q а для изношенных на 07Q.
Для 1-й ступени протяжки у которой режущие лезвия предоставляют отрезки дуг окружности силу протягивания можно подсчитать по зависимости:
Cp- величина зависящая от обрабатываемого материала и формы протяжки
Zi-наибольшее количество одновременно работающих зубьев
Поскольку на 1-й ступени
При конструировании протяжек стремятся обеспечить количество одновременно работающих зубьев от 3 до 8. нежелательно иметь Zi max>8 10 т.к. это ухудшает условие смазки протяжки и снижает чистоту обработанной поверхности.
KKK-поправочные коэффициенты характеризующие влияние переднего угла состава смазочно-охлаждающей жидкости и степени износа зубьев протяжки.
Сила протягивания отнесённая к началу каждой ступени может быть определена на основе эмпирических протяжек с учётом изменённой длины режущего лезвия.
Для шестигранных протяжек
Pm=Cp(dm-Szm)*(1-0m300)SxzZi max KKK
Где dm -диаметр первого зуба рассматриваемой ступени
Szm-величина подачи на первом зубе рассчитываемой ступени.
Для 1-й ступени сила протягивания.
P1=762*0043*22*9*093*1*1=6033 кг
P2=762*(2235-005)*(1-9036)*0078*6*093*1*1=5076 кг
Где 0m2=arccos[22(12235-005)]= arccos098655
m3=arccos[22(232-0075)]= arccos 09513
И сила протягивания:
P3=762*(232-0075)*(1-1704)*0111*5*093*1*1=3656 кг
Наибольшее тяговое усилие имеем на 1-й ступени. По этому усилию рассчитываем протяжку на прочность по формуле
Fmin-наименьшая площадь поперечного сечения протяжки мм2
[в]-величина допускаемого напряжения на растяжение
для шестигранных протяжек [в] = 30 35 кгмм2
проверку протяжки на прочность обычно производят по хвостовику или в сечении по 1-й стружечной канавке.
Хвостовик имеет следующие параметры D=20 мм l1=25 мм l2=25 ммD1=15 мм Fx=1767 мм2
Площадь поперечного сечения по первой стружечной канавке подсчитывается по зависимости
F1=(d1-2h0)24=260 мм2
Где d1 -диаметр первого зуба протяжки.
Направление в материале протяжки
=26001767=1471 кгмм2
Т.е. меньше допустимого
Общая длинна протяжки
где lгл=l'+lзд-длина гладких частей протяжки. Она включает длину l'протяжки до 1-го зуба и длину задней направляющей lзд
для быстродействующего патрона с ручным управлением длина хвостика до 1-го зуба
для быстродействующего патрона с автоматическим управлением длина хвостика до 1-го зуба
M=P-x (величины P и x выбираются в зависемости от размера патрона)
N=lпл+l+10 N=75+30+10=115
Где lпл – высота планшайбы
Длина режущей части протяжки определяется по зависимости:
Lp=Z1tp1+ Z2tp2+ +Zntpn=10*5+8*75+8*10=190 мм;
Длина калибрующей части:
Lk=Zk*tk=5*75=375 мм;
Общая длина протяжки :
Lп=322+190+375=550 мм;
Длина протягивания не превышает длину хода стола станка и рекомендуемую предельную длину.
8. параметры формообразующей части протяжки
Диаметр первого зуба протяжки и профиль его режущего лезвия соответствует размерам и форме предварительного отверстия.
где D0min – наименьший диаметр предварительного отверстия.
Диаметры последующих зубьев рассчитываются путём прибавления Kd1двойной величины подъёма на зуб 2Sz.
Диаметры калибрующего зуба принимается равными диаметру последнего режущего (переходного) зуба протяжки.
Для обеспечения наибольшей долговечности протяжки размеры калибрующих зубьев необходимо принимать равными наибольшими допустимым размером готового отверстия Dm с учётом его деформации возникающей при обработке протяжкой. Однако в данном случае величину можно принимать равной нулю. т.к. между отверстием и валом имеется зазор.
Поэтому dk=Dм max±=242 мм где - остаточная деформация отверстия.
Деформация отверстия обычно выражается или в увеличении размеров протянутого отверстия по сравнению с размерами зубьев протяжки или наоборот в уменьшении их. Явление разбивания отверстия свойственно толстостенным деталям. В этом случае в формуле принимается -. При протягивании тонкостенных деталей например втулок трубок вкладышей возможна «усадка» отверстия. В этом случае принимается +.
На основании производственного опыта и исследования величину разбивания ориентировочно принимают равной 0005 001мм для протяжек с наибольшей длиной (до 700 800мм) и 001 0015мм для протяжек большей длины.
Прямолинейные боковые лезвия зубьев протяжки является вспомогательными. Расстояния между ними для всех зубьев протяжки постоянные определяемые по зависимости
где Smax – наибольшее допустимое расстояние между сторонами отверстия.
Необходимо чтобы размеры Sn нее возрастая к концу протяжки а уменьшался в пределах допуска; в противном случае возможно заклинивание протяжки в отверстии. Если протяжки комплектные то расстояние между сторонами зубьев первой протяжки S1=Sn
Допустимое отклонение на размеры Sn принимают равным 13 14 допуска на отверстие со знаком минуса но оно не должно превышать отклонений посадки С3 по ГОСТ1013. Расстояние между сторонами второй протяжки S2=S1min с допустимым отклонением как у 1-й протяжки.
9. размеры гладких частей протяжек
Предельная направляющая часть предназначается для установки обрабатываемой детали на протяжке перед протягиванием. Она обеспечивает плавный без перекосов переход детали на режущую часть протяжки. В соответствии с назначением передней направляющей части длина её должна быть не меньше длинны протягиваемой детали.
Таким образом lп.н.=lg=40 мм
При этом длинной передней направляющей является расстояние от конца переходного конуса до первого зуба режущей части т.е. включая длину первой стружечной канавки.
Если протягиваемое отверстие очень большой длины (глубокое отверстие) то длинна передней направляющей обычно не превышает (1 15)dk.
В этом случае необходима более тщательная подготовка отверстия под протягивание. При протягивании деталей с предварительным отверстием некруглой формы - форма и размеры переднее направляющей должны соответствовать форме и размерам этого предварительного отверстия.
длина переходного конуса обычно принимается равной 10 25мм в зависимости от размеров протяжки.
Меньший диаметр переходного конуса принимается равным диаметру хвостовика а больший - диаметру переднее направляющей .
Задняя направляющая часть препятствует перекосу детали на протяжке и повреждению вследствие этого обработанной поверхности в момент выхода последних зубцов калибрующей части из отверстия.
10. термообработка протяжек.
Твердость режущей части и задней и направляющей HRC 62 65. Твёрдость передней направляющей HRC 60 65. Твёрдость хвостовой части HRC 40 47.
11. допуски на элементы и размеры протяжек.
К геометрической форме протяжек предъявляются следующие требования:
Биение в средней части длины не должно превышать следующие величины:
Отклонение длины протяжки к её диаметру мм
Допускаемое биение мм
На калибрующих зубьях и на задней направляющей части допускается биение не превышающее величины допуска на диаметр калибрующих зубьев.
Биение передней направляющей части не должно быть больше половины значения указанного в п.1.
На хвостовой части допускается биение в пределах допуска на диаметр этой части.
Взаимная непараллельность плоских сторон протяжек не должна выходить за пределы допуска на размеры между этими сторонами причём допускается только сужение протяжки от её начала к концу.
Биение опорного конуса на круглых хвостовиках под кулачковые патроны не должно выходить за пределы 003 мм.
Расчет круглого фасонного резца.
Требуемый профиль см. рис.4.
Матегшал летали сталь 45.
1 Расчёт средних размеров профиля.
Средние размеры совпадают с номинальными т. к. допуск по профилю расположен симметрично.
2 Выбор положения базовой линии.
Выберем базовую линию проходящую через точку 3 (см. рис. 5) т. к. в этой точке диаметр обрабатываемой детали наименьший.
3. Расчёт габаритных размеров резца.
Ширина резца (см. рис. 5):
По табл. 3.5. назначаем n=2.5 тогда:
Глубина профиля q в направлении перпендикулярном оси резца: q=11 (см. рис.5)
Определяем диаметр посадочного отверстия d0.
По табл. 2.3. подача S=0.01mmo6 тогда по табл. 2.2.методических указаний усилие резания на 1мм:
PZ(L=1) = 68H тогда: Pz = PZ(L=1) * L = 68 * 50 = 3400H.
Учитывая ширину резца и то что усилие резания относительно небольшое принимаем консольное крепление оправки. По табл. 2.1. диаметр посадочного отверстия d0 = 22мм.
Подсчитываем наименьшее допустимое значение наружного диаметра резца D (см. рис. 3):
Принимаем 1=4мм m=8мм тогда:
D=22+2(11+4+8)=68 мм.
Округляя до ближайшего значения по стандартному ряду диаметров резцов принимаем D=70 мм.
Рис. 6. Габаритные размеры резца.
4. Коррекционный расчёт профиля.
Выбираем геометрические параметры для точки 3 (см. рис. 6.). Для проектируемого резца принимаем по табл. 2. 4. методических указаний γ= 22° ( сталь 45 в = 600Нмм2 ) задний угол α = 12°. Подсчитываем размер hуст. (рис. 5):
hycm = R1 sin α = 35 sin 12 = 7.27
Окончательно принимаем hycm = 73мм.
Вычисляем координаты точек исходя из используемых размеров детали (см. рис. 7)
Рис. 7. Координаты точек профиля.
Рис. 8. Параметры точек профиля резца.
Для расчетов удобнее все уравнения записать в расчетную табл.1
Численная величина размера
C4=A4-A3=805775-649026=156749мм;
C12=A12-A3=96501-649026=З15984мм; C56=A56-A3=178079-649026=113176м.
Произведём расчёт профиля резца в осевой плоскости (см. рис. 9).
Tg4 =071302 4=354896°
Примечание к таблице 2.
H56 =R1 - R56 = 35 - 26.3876 = 8.6124мм;
H12 =R1 – R12= 35-32.4287 = 2.5713мм;
H4 =R1 – R4=35 -33.7164 = 1.2836мм.
Рис. 9. Расчёт профиля в осевой плоскости.
Расчёт значений задних углов ат в точках режущей кромки резца в плоскости
5 Анализ величин передних и задних углов режущей части резца
Расчет значений передних углов γх и задних углов αх в различных точках режущей кромки резца в плоскости перпендикулярной оси резца производится в расчетной таблице 3
Таблица3. Расчет профиля в плоскости перпендикулярной оси резца
Sinγ4=(78б47372)*0374161=030946
tg3=(1567*055919)(337164-082904*156749)=
α4=220+120 - 180266+154885'=175222
Sinγ12=(710)*0 37461=026223
Tg12=(315984*055919)(324287-315984*082904)=000103
=220+120-1502022+005901=188568
Sinγ56=(718)*037446=014586
Tg56=(113176*055919)(263876-315984*082904)=000649
=220+120-838'+037184=259848
перпендикулярной к рассматриваемому участку кромки производится по расчётной таблице 4. Таблица 4
Расчёт значений предельных углов αхп в точках режущей кромки резца в плоскости перпендикулярной к рассматриваемому участку кромки производится по расчётной таблице 5.
tg γxn= tg γx* Sinφx
Построим графики значений передних и задних углов каждого участка режущей кромки (см. рис. 10 11).
В ходе проделанной работы был произведён расчёт и проектирование заданных режущих инструментов разработаны их рабочие чертежи с указанием предельных отклонений их размеров и шероховатостей на поверхности инструмента а так же составлен тест из 20 вопросов по 5 вариантов ответов на каждый вопрос.
Список использованной литературы
Основы резания металлов: Т. А. Багдасарова — Санкт-Петербург Академия 2009 г.- 80 с.
Резание металлов и режущие инструменты: В. Г. Солоненко А. А. Рыжкин — Москва Высшая школа 2007 г.- 416 с.
Справочник конструктора-инструментальщика: — Санкт-Петербург Машиностроение 2006 г.- 544 с.
Обработка металлов резанием. Справочник технолога: — Санкт-Петербург Машиностроение 2004 г.- 784 с.
Металлорежущие инструменты. Справочник конструктора: Е. Э. Фельдштейн М. А. Корниевич — Москва Новое знание 2009 г.- 1040 с.
Режущий инструмент. Д. В. Кожевников В. А. Гречишников С. В.Кирсанов В. И. Кокарев А. Г. Схиртладзе; под ред. д-ра техн. наук С. В.Кирсанова 2:е изд. доп. - М.: Машиностроение 2005г. - 528 с
Лист регистрации изменений
Номера листов (страниц)
Всего листов(страниц) в докум.
Входящий № сопроводительного докум. И дата
620481_01 Протяжка.cdw

на зубе №-1 (цилиндрическом)
профиль режущих лезвий зубьев с №-11
по №-18 (по однойстружкоделительной
канавке в шахматном порядке)
профиль режущих и калибрующих
Режущие зубья должны затачиваться до остра
допускается ленточка не более 0.05 мм.
Биение в середине протяжки не должно
На колибрующих зубьях и на задне направляющей
части допускается биение не превышающее
величину допуска на диаметр колибрующих зубьев.
Биение передней направляющей части
не должно быть больше половины значения
указанного в пункте 2.
На хвостовой части допускается биение
в пределах допускана диаметр этой части.
Овальность всех зубьев направляющей и
хвостовой частей не должна выходить из
пределов допусков на диаметры
этих элементов протяжек.
Наибольший прогиб по плоским сторонам
протяжкидопускается в пределах величины
указанной в пункте 2.
Взаимная непараллнльность плоских сторон
протяжки не должна выходить за пределы
допуска на размер между этими сторонами.
Допускается только сужение протяжки
Твёрдость режущей части и задней
направляющей HRC 62 65
передне направляющей
хвостовойчасти HRC 40 47.
Маркировать : КП-11-39 2324-ИМС-ДБ-01.
профиль режущих зубьев
профиль режущих и колибрующих
зубьев с №19 по №31. Назубьях №27-№31
профиль режущих лезвий зубьев с №2 по №10 (по две стружкоделительные
канавки в шахматном порядке)
КП-11-39 2324-ИМС-ДБ-01
Протяжка шестигранная
Сталь ХВГ ГОСТ 5950-73
620481_01 Фасонный резец.cdw

Профиль резца в передней плоскости
Маркировать: КП-11-39 2160-ИМС-ДБ-01
КП-11-39 2160-ИМС-ДБ-01
сталь Р6М5 ГОСТ 19265-73
Рекомендуемые чертежи
- 24.01.2023
- 15.04.2024
Свободное скачивание на сегодня
Обновление через: 14 часов 18 минут