Расчет одноступенчатого редуктора




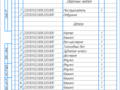
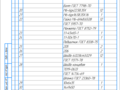
- Добавлен: 24.01.2023
- Размер: 5 MB
- Закачек: 0
Описание
Расчет одноступенчатого редуктора
Состав проекта
![]() |
![]() |
![]() ![]() ![]() ![]() |
![]() |
![]() ![]() ![]() |
![]() ![]() ![]() |
![]() ![]() ![]() ![]() |
![]() ![]() ![]() |
![]() ![]() ![]() ![]() |
Дополнительная информация
РЕДУКТОР Марат готовое.cdw

Частота вращения быстроходного вала
Частота вращения тихоходного вала
Передаточное число 3
Основные параметры зацепления:
Плоскость разъема редуктора покрыть тонким слоем герметика
ВКГ-18 №2 МРТУ 07-6012-63 при окончательной сборке
Необработанные наружные поверхности редуктора покрыть серой
внутреннее-маслостойкой краской
Масло И-Г-А-32. Уровень масла должен находится между отметками
Редуктор обкатать без нагрузки при частоте вращения
быстроходного вала n=900 обмин в течении 2-х часов
масло слить и проверить проворачиваемость
Максимальный уровень масла
Минимальный уровень масла
Курсовая прик.мех..doc
Исходные данные к проектированию привода:
- кинематическая схема редуктора
- вращающий момент на тихоходном валу Т2 = 20 Нм;
- частота вращения тихоходного вала n2 = 280 мин-1;
- число зубьев шестерни на тихоходном валу Z3 = 48 шт.;
- время работы передачи (ресурс) L = 12000 час;
- типовой режим работы привода – II ГОСТ 21354-87
По этим данным прежде всего подбираем электродвигатель.
1.Определение требуемой мощности электродвигателя.
Требуемую мощность электродвигателя определяют на основании исходных данных. Определим мощность на тихоходном валу:
- КПД привода в общем случае равный произведению частных КПД ступеней редуктора:
- КПД зубчатой передачи;
Значения КПД для различных передач приведены в таблице 1.1
Определим мощность электродвигателя:
2.Определение частоты вращения вала электродвигателя.
Требуемая частота вращения вала электродвигателя определяется по формуле:
i – передаточное отношение привода
В дальнейших расчётах вместо передаточного отношения применяют передаточное число где
Z1 – число зубьев шестерни (Z2 > Z1)
Z2 – число зубьев колеса.
Применение u вместо i связано только с принятой формой расчётных зависимостей для контактных напряжений значения которых не зависят от того какое из зубчатых колёс является ведущим.
Руководствуясь рекомендациями по выбору значений передаточных чисел в соответствии с заданным типом передачи в редукторе (см. табл. 1.2) определяют возможный диапазон частот вращения вала электродвигателя.
Таблица 1.2. Рекомендуемые значения передаточных чисел одноступенчатого редуктора.
По рассчитанной мощности РР и диапазону nЭ.Д. из табл.1.3 выбирают электродвигатель таким образом чтобы его номинальная мощность Рном РР а номинальная частота nном вращения вала была самой близкой (из возможных вариантов) к большему значению диапазона nЭ.Д. В этом случае размеры и стоимость электродвигателя будут наименьшими.
Электродвигатель – 4А80A6У3
По выбранному электродвигателю определяют расчётное передаточное число зубчатой передачи редуктора:
РАСЧЕТЫ ЗУБЧАТЫХ ПЕРЕДАЧ.
1. Выбор материалов зубчатых передач и вид термообработки.
При выборе материалов зубчатых колёс следует учитывать назначение проектируемой передачи условия эксплуатации требования к габаритным размерам и возможную технологию изготовления колёс. Основным материалом для изготовления зубчатых колёс является сталь. Необходимую твёрдость в сочетании с другими механическими характеристиками (а следовательно желаемые габариты и массу передачи) можно получить за счёт назначения соответствующей термической или химико-термической обработки стали.
В условиях индивидуального и мелкосерийного производства в мало- и средненагруженных передачах а также в передачах с большими габаритами колёс (когда термообработка их затруднена) обычно применяют стали с твёрдостью не более 350 ВН которая обеспечивается нормализацией или термоулучшением материала. При этом возможно чистовое нарезание зубьев непосредственно после термообработки с высокой точностью изготовления а при работе передачи обеспечивается хорошая прирабатываемость зубьев без хрупкого разрушения их при динамических нагрузках.
Для равномерного изнашивания зубьев и лучшей их прирабатываемости твердость шестерни НВ1 рекомендуют назначать больше твёрдости НВ2 колеса не менее чем на (10 15) НВ.
В условиях крупносерийного производства целесообразно применять зубчатые колёса с высокотвёрдыми зубьями. При твёрдости более 350 НВ её обычно выражают в единицах Роввелла – НRC (1 HRC = 10 HB).
Такая твёрдость обеспечивается после проведения упрочняющих видов термической и химико-термической обработки: закалки (объёмной или поверхностной) цементации с последующей закалкой азотирования и др.
Применение высокотвердых материалов является резервом повышения нагрузочной способности зубчатых передач уменьшения их габаритов и массы.
Однако с высокой твёрдостью материала связаны дополнительные трудности: плохая прирабатываемость зубьев прогрессирующее усталостное выкрашивание рабочих поверхностей зубьев необходимость проведения термообработки после зубонарезания. Большинство видов упрочняющей термообработки сопровождается значительным короблением зубьев. Для исправления формы зубьев восстановления требуемой степени точности требуются дополнительные дорогостоящие зубоотделочные операции (шлифование полирование притирка и т.п.) что удлиняет технологический процесс изготовления зубчатых колёс и значительно повышает стоимость передачи.
Рекомендуемые для изготовления зубчатых колёс марки конструкционных сталей виды их термообработки соответствующие основные механические характеристики приведении в таблице 2.1. При этом важно чтобы размеры заготовки колёс (диаметр Dзаг и толщина обода или диска Sзаг) не превышали предельных значений Dпред и Sпред.
Марка Dnpeд Snpeд ТО Твердость е m -1
стали мм мм заготовки (НB) Н мм3
80 50 У 220 ÷230 890 650 380
125 80 У 197÷217 780 540 335
При этом HBср1 - HBср2 = 225-207= 18 ед. следовательно обеспечивается приработка зубьев Z1 и Z2.
2. Определение числа циклов перемены напряжений.
По таблице интерполированием находим число циклов перемены напряжений:
- для шестерни: NHO1 = 225 × 106 циклов;
- для колеса: NHO2 = 162 × 106 циклов.
Рекомендуемое значение: NFO = 4 × 106 циклов.
Число циклов нагружения на весь срок эксплуатации:
3. Определение коэффициентов долговечности.
По таблице 2.3 определяем минимальные значения коэффициентов долговечности в зависимости от режима работы:
4. Определяем допускаемое контактное напряжение.
5. Расчет допускаемых напряжений с учётом ресурса передачи.
6. Определение расчётного коэффициента.
- коэффициент ширины зубчатого венца определяем по таблице:
Находим относительную ширину колеса:
Коэффициент неравномерности нагрузки по длине контакта KH и коэффициент неравномерности нагрузки по величине изгиба KF выбираем по кривым на графиках рис.2.3 (а б) в соответствии с расположением колёс относительно опор и твёрдости рабочих поверхностей зубьев колёс.
7. Определение межосевого расстояния передачи.
При проектном расчете прежде всего определяем главный параметр цилиндрической передачи межосевое расстояние - в мм. Расчет производим по следующей формуле:
По нормальным линейным размерам Ra40 принимаем мм;
8. Предварительное определение основных размеров колеса.
Ширина зубчатого венца равна:
9. Определение модуля зубьев передачи.
Полученное значение модуля округляем до стандартного значения по 1-му ряду модулей: 10; 125; 15; 2; 25; 3; 4; 5; 6; 8; 10 мм.
По ГОСТ 9563-60 принимаем m=15 мм.
10. Определяем суммарное число зубьев передачи.
Число зубьев шестерни: шт.;
Число зубьев колеса: шт.
11. Нахождение фактического передаточного числа.
12. Определение фактических размеров передачи.
Делительный диаметр шестерни: мм;
Делительный диаметр колеса: мм;
Уточняем межосевое расстояние: мм;
Определяем диаметр вершин:
Определяем диаметр впадин:
13. Определение пригодности заготовок шестерни и колеса.
14. Определение окружной скорости зубчатого колеса.
15. Определение силы в зацеплении.
16. Принимаем коэффициенты динамической нагрузки.
По табл.2.6 определяем степень точности зубчатой передачи в зависимости от скорости вращения колеса:
мс мс степень точности 8
Далее по табл.2.7 находим значения коэффициентов KHV и KFV.
17. Определяем расчёт контактных напряжений.
По данному примеру недогруз составляет 8% это меньше 10% поэтому контактная прочность зуба обеспечивается.
18. Расчётные напряжения изгиба в основании ножки зуба.
- коэффициент формы зуба находим по табл.2.9.
При: Z1 = 28– YF1 = 3.81;
Прочность зуба на изгиб обеспечивается.
ПРОЕКТНЫЙ РАСЧЕТ ВАЛОВ И ОПОРНЫХ КОНСТРУКЦИЙ.
В различных узлах машин (в том числе и механических передачах) содержится ряд деталей предназначенных для поддерживания вращающихся элементов зубчатых и червячных колес шкивов звездочек и т.д. Такие детали называются валами и осями. По конструкции оси и прямые валы мало отличаются друг от друга но характер их работы существенно различен: оси являются поддерживающими деталями и воспринимают только изгибающие нагрузки; валы представляют собой звенья механизмов передающие крутящие моменты и помимо изгиба испытывают кручение. Нагрузки воспринимаемые валами и осями предаются на корпуса рамы и станины через опорные устройства подшипники.
Части валов и осей непосредственно соприкасающиеся с подшипниками носят общее наименование «цапфы». Цапфу расположенную на конце вала называют типом а цапфу на средней части вала шейкой цапфы передающие на опоры осевые нагрузки называют пятами. Оси могут быть неподвижными или вращаться вместе с насаженными на них деталями. Валы при работе механизма всегда вращаются. Признаками для классификации валов служат их назначение форма геометрической оси конструктивные особенности.
Основными критериями работоспособности проектируемых редукторных валов являются прочность и выносливость. Они испытывают сложную деформацию совместное действие кручения изгиба и растяжения (сжатия). Но так как напряжения в валах от растяжения небольшие то их обычно не учитывают.
Расчет редукторных валов производим в два этапа: 1-ый-проектный (приближенный) расчет валов на чистое кручение 2-ой-проверочный (уточненный) расчет валов на выносливость по напряжениям изгиба и кручения.
1. Выбор материалов валов
Марка Dnpeд Snpeд ТО Твердостье m -1
125 80 У 235 ÷ 262 780 540 335
2. Выбор допускаемых напряжений на кручение.
Проектный расчет валов редуктора выполняем только по напряжениям кручения (как при чистом кручении) то есть при этом не учитываем напряжений изгиба концентрации напряжений и переменность напряжений по времени (циклы напряжений). Для компенсации этого значения допускаемых напряжений на кручение выбираем заниженными в пределах [k]= 10 15 Нмм. Принимаем:
для быстроходного вала [k]= 10 Нмм;
для тихоходного вала [k]= 15 Нмм.
3. Определение геометрических параметров ступеней валов.
Редукторный вал представляет собой ступенчатое цилиндрическое тело количество и размеры которого зависят от количества и размеров установленных на вал деталей.
Проектный расчет валов определяет ориентировочно геометрические размеры каждой ступени вала ее диаметр d и длину l (см. таблицу 3.1) Для колеса: Таблица 3.1.1.
Под элемент открытой передачи
Под уплотнительные крышки и подшипник
d2 = d1 + 2 t t=25 по табл.З.1.1 [1] ;
d2 = 22+ 2 * 25 = 27 мм;
d3 = d2 + 32*r r=16 по табл. 3.1.1[1];
d3 = 30+ 32*16=3512 мм; d3=35мм;
Значение высоты буртика t = 25 мм ориентировочные величины фаски ступицы f = 1 мм и радиусы округления r = 16 мм определяются в зависимости от диаметра ступени d (Таблица 3.2):
d2 = d1 + 2 t t=25 по табл.З.1.1 [1];
d2 = 20 + 2 * 25 = 25 мм;
d3 = d2 + 3.2*r r=16 по табл. 3.1.1[1];
d3 = 25 + 32*16=30 мм;
4. Предварительный выбор подшипников качения.
Выбор наиболее рационального типа подшипников зависит от целого ряда факторов: передаваемой мощности редуктора типа передачи соотношения сил в зацеплении частоты вращения внутреннего кольца подшипника требуемого срока службы приемлемой стоимости схемы установки.
Из таблицы 24.10 [1] выбираем типоразмер подшипников по величине
диаметра d внутреннего кольца подшипника равного диаметру второй d2 и четвертой d4 ступеней вала под подшипники.
По выбранному типоразмеру определяем основные параметры подшипников:
) тихоходный вал: Тип 205 (d = 25 мм D = 52 мм B = 15 мм r = 15 мм
Cor = 14 кН Cr= 695 кН)
) быстроходный вал: Тип 206 (d = 30 ммD = 62 мм B = 16 мм r = 15мм
Cor = 195 кН Cr= 100 кН)
Здесь D -диаметр наружного кольца подшипника В - ширина шарикоподшипников.
5. Эскизная компоновка редуктора.
Для предотвращения задевания поверхностей вращающихся колес за внутренние стенки корпуса контур стенок проводят с зазором Δ = 8 10 мм.
Зазор принимаем равным 10 мм. Расстояние hм (рисунок 3.2) между дном корпуса и поверхностью выступов зубьев колес для всех типов редукторов
принимают hм > 4 * Δ (с целью обеспечения зоны отстоя масла).
6. Проверочный расчет валов на выносливость.
6.1. Составляем расчетную схему вала в соответствии с конструкцией принятой ранее.
6.2.Силы действующие на вал.
-1 =058* -1 =058 * 335= 1943 МПа;
d3 = m * Z3 = 15 * 48 = 72мм;
6.3.1. Определяем сумму изгибающих моментов в вертикальной плоскости:
6.3.2. Cтроим эпюру изгибающих моментов.
Изгибающие моменты в сечении.
6.3.3. Определяем сумму изгибающих моментов в горизонтальной плоскости:
6.3.4. Эпюра крутящих моментов:
Изгибающие моменты в сечении II-II
Результирующие моменты в сечении II-II
Определим напряжения в сечении II-II
6.4 Определяем коэффициенты запаса усталостной прочности.
При совместном действии изгиба и кручения запас усталостной прочности определяем по формуле:
- запас сопротивления усталости только по изгибу.
Коэффициент запаса сопротивления усталости только по кручению рассчитываем по формуле:
В предыдущих формулах а и а - амплитуды переменных составляющих
циклов напряжений т и m — постоянные составляющие
и - коэффициенты корректирующие влияние постоянной составляющей цикла напряжений на сопротивление усталости (таблица 3.3):
Так как в данной работе среднеуглеродистые стали то =01 =05; -1 и -1 - пределы выносливости материала вала при симметричном цикле нагружения. Их определяем по таблице 2.1 (см. выше):
-1 = 058 * -1 = 058 335= 1943 МПа;
Kd и KF - масштабный фактор и фактор шероховатости
По рис. 15.5 и 15.6 принимаем что Kd = 082 КF = 1;
K И К - эффективные коэффициенты концентрации напряжений при изгибе и кручении (ориентировочно назначаем по табл. 15.1):
из табл. стр. 62 [1]
Условие выполняется.
7. Проверка правильности подбора подшипников качения.
Выбранный в ходе проектирования узла вала типоразмер подшипника должен быть проверен на работоспособности по динамической грузоподъемности.
Проверку правильности выбор подшипников проводим следующим
По обеспечению заданной долговечности подшипника то есть
Lh3 LhФ где с учетом режима нагрузки Lh3=hLh..
Где h =0(см. табл. 8.10 [2]).
Здесь фактический срок работы подшипника рассчитывают по зависимости:
a1 - коэффициент надежности принимаем a1= 1;
a2 – обобщенный коэффициент совместного влияния качества метала деталей подшипника и условий его эксплуатации так как у нас обычные условия эксплуатации назначаем a2 = 07;
р - для шариковых подшипников р = 3;
Величина эквивалентной динамической Нагрузки на проверяемый подшипник рассчитываем в общем случае по формуле:
Где Frn и Fan — соответственно радиальная и осевая силы в опоре.
V - коэффициент вращения зависящий от того какое кольцо подшипника вращается у нас вращается внутреннее кольцо и V = 1;
K- коэффициент безопасности учитывающий характер нагрузки при умеренных толчках K =14;
K - температурный коэффициент для температуры подшипникового узла
X Y - коэффициенты соответственно радиальной и осевой нагрузок на подшипники. В данной курсовой работе малая осевая сила значит действие осевой силы в расчет не принимается то есть X = 1 Y = 0.
Рr =(11*89318+ 0) 141 =125045
8013≥ 756 – условие выполняется.
8. Расчет шпоночного соединения.
) Для соединения вала с колесом принимаем призматическую шпонку исполнения В.
) По справочнику (табл. 24.29 [1]) для d3 = 40 мм принимаем размеры сечения шпонки: b = 12 мм h = 8 мм t1 = 4 мм t2 = 33 мм.
) Выбираем длину шпонки: lшп = lст – 5мм в данном случае
Из стандартного ряда по справочнику:
) Для стальной шпонки при стальной нагрузке принимаем допускаемое напряжение сжатие:
03 МПа 120 МПа – условие выполняется.
Для смазывания передач широко применяют картерную систему. В корпус редуктора или коробки передач заливают масло так чтобы венцы
колес были в него погружены. Колеса при вращении увлекают масло разбрызгивая его внутри корпуса. Масло попадает на внутренние стенки корпуса откуда стекает в нижнюю его часть. Внутри корпуса образуется взвесь частиц масла в воздухе которая покрывает поверхность расположенных внутри корпуса деталей.
Картерное смазывание применяют при окружной скорости зубчатых колес и червяков до 125 мс. При более высоких скоростях масло сбрасывает с зубьев центробежная сила и зацепление работает при недостаточном смазывании. Кроме того заметно возрастают потери мощности на перемешивании масла повышается его температура. Выбор смазочного материала основан на опыте эксплуатации машин.
Преимущественное применение имеют масла. Принцип назначения сорта масла следующий: чем выше окружная скорость колеса тем меньше должна быть вязкость масла и чем выше контактные давления в зацеплении тем большей вязкостью должно обладать масло. Поэтому требуемую вязкость масла определяем в зависимости от контактного напряжения и окружной скорости колес (таб. 1 1.1 Г11):
Так как v = 202 мс а контактное напряжение H =25936 МПа то рекомендуемая кинематическая вязкость равна 22 мм2с .
По табл. 11.2 выбираем марку масла для смазывания зубчатой передачи.
Выбираем марку масла И-Л-А-22. Первый (И) - индустриальное второй - принадлежности группе по назначению: Г - для гидравлических систем третий - принадлежность к группе по эксплуатационным свойствам: А - масло без присадок.
Так как v > 1 м с то достаточно погружать в масло только зубчатое колесо. Глубина погружения:
hm = 025138 =345 мм.
Ориентировочно принимаем из соотношения: 1кВт = 1 литр масла.
В данном проекте по требуется около 1 литр масла.
Конструирование элементов редуктора.
1 Конструирование зубчатых колёс.
Длину lст. посадочного отверстия
принимают равной или большей ширине
Диаметр посадочного отверстия:
Диаметр dст. ступицы назначают в
зависимости от материала колеса:
dст. = 15d3+10 = 6268 мм;
Ширину S торцов зубчатого венца принимают:
S = 25m + 2 =25*25 + 2= 7 мм где
m – модуль зацепления;
На торцах зубчатого венца выполняют фаски - где
Для свободной выемки заготовок из штампа принимают значения штамповочных уклонов и радиусов закруглений мм.
Толщина диска С рекомендована для уменьшения влияния термической обработки на точность геометрической формы колеса:
С = (035 04)b2 = 04*66 =264 мм.
3. Корпус редуктора.
Корпус редуктора изготавливают из серого чугуна марки СЧ15.
В малонагруженных редукторах (Нм) толщины стенок крышки и основания корпуса принимают одинаковыми: мм где T2 – вращающий момент на колесе тихоходного вала Нм.
Опорная поверхность фланца выполняется в виде двух длинных параллельно расположенных или четырёх небольших платиков. Места крепления располагают на возможно большем (но в пределах корпуса) расстоянии друг от друга L1 .
Длина опорной поверхности платиков L = L1 + L = 4082 + 498 = 458мм;
ширина ; b1 = 24·15+15·6=498 мм;
высота ; h1 = 23·6=138 мм;
Диаметр отверстия в основании корпуса: d01 = 17 мм;
Длина крышки: L = 160 мм;
Высота фланца: h1 = 3 5 мм;
Толщина крышки: k = (0010 0012)·L = 5 мм;
Применяем полосы технической резины марки МБС толщиной 2 3 мм;
Для крепления смотрового люка к крышки применяем винты М6.
Применим овальный маслоуказатель из прозрачного материала.
7. Сливное отверстие.
8. Установочные штифты.
Под шайбу концевую:
Уплотняющее покрытие плоскости разъёма склеивает крышку и основание корпуса. Для того чтобы обеспечить их разъединение при разборке рекомендуют применять отжимные винты которые ставят в двух противоположных местах крышки корпуса. Диаметр отжимных винтов принимают равным диаметру соединительных d3 стяжных винтов.
Для подъёма и транспортировки крышки корпуса и собранного редуктора применяют проушины отливая их заодно с крышкой.
12. Крышки подшипника.
Применим крышки закладные:
- с отверстием для выходного конца вала.
= (09 1) = 1 · 6 = 6 мм;
S = (09 1) = 1 · 6 = 6 мм;
С 05 · S = 05 · 6 = 3 мм;
1.doc
Исходные данные к проектированию привода:
- кинематическая схема редуктора
- вращающий момент на тихоходном валу Т2 = 20 Нм;
- частота вращения тихоходного вала n2 = 280 мин-1;
- число зубьев шестерни на тихоходном валу Z3 = 48 шт.;
- время работы передачи (ресурс) L = 12000 час;
- типовой режим работы привода – II ГОСТ 21354-87
По этим данным прежде всего подбираем электродвигатель.
1.Определение требуемой мощности электродвигателя.
Требуемую мощность электродвигателя определяют на основании исходных данных. Определим мощность на тихоходном валу:
- КПД привода в общем случае равный произведению частных КПД ступеней редуктора:
- КПД зубчатой передачи;
Значения КПД для различных передач приведены в таблице 1.1
Определим мощность электродвигателя:
2.Определение частоты вращения вала электродвигателя.
Требуемая частота вращения вала электродвигателя определяется по формуле:
i – передаточное отношение привода
В дальнейших расчётах вместо передаточного отношения применяют передаточное число где
Z1 – число зубьев шестерни (Z2 > Z1)
Z2 – число зубьев колеса.
Применение u вместо i связано только с принятой формой расчётных зависимостей для контактных напряжений значения которых не зависят от того какое из зубчатых колёс является ведущим.
Руководствуясь рекомендациями по выбору значений передаточных чисел в соответствии с заданным типом передачи в редукторе (см. табл. 1.2) определяют возможный диапазон частот вращения вала электродвигателя.
Таблица 1.2. Рекомендуемые значения передаточных чисел одноступенчатого редуктора.
По рассчитанной мощности РР и диапазону nЭ.Д. из табл.1.3 выбирают электродвигатель таким образом чтобы его номинальная мощность Рном РР а номинальная частота nном вращения вала была самой близкой (из возможных вариантов) к большему значению диапазона nЭ.Д. В этом случае размеры и стоимость электродвигателя будут наименьшими.
Электродвигатель – 4А80A6У3
По выбранному электродвигателю определяют расчётное передаточное число зубчатой передачи редуктора:
РАСЧЕТЫ ЗУБЧАТЫХ ПЕРЕДАЧ.
1. Выбор материалов зубчатых передач и вид термообработки.
При выборе материалов зубчатых колёс следует учитывать назначение проектируемой передачи условия эксплуатации требования к габаритным размерам и возможную технологию изготовления колёс. Основным материалом для изготовления зубчатых колёс является сталь. Необходимую твёрдость в сочетании с другими механическими характеристиками (а следовательно желаемые габариты и массу передачи) можно получить за счёт назначения соответствующей термической или химико-термической обработки стали.
В условиях индивидуального и мелкосерийного производства в мало- и средненагруженных передачах а также в передачах с большими габаритами колёс (когда термообработка их затруднена) обычно применяют стали с твёрдостью не более 350 ВН которая обеспечивается нормализацией или термоулучшением материала. При этом возможно чистовое нарезание зубьев непосредственно после термообработки с высокой точностью изготовления а при работе передачи обеспечивается хорошая прирабатываемость зубьев без хрупкого разрушения их при динамических нагрузках.
Для равномерного изнашивания зубьев и лучшей их прирабатываемости твердость шестерни НВ1 рекомендуют назначать больше твёрдости НВ2 колеса не менее чем на (10 15) НВ.
В условиях крупносерийного производства целесообразно применять зубчатые колёса с высокотвёрдыми зубьями. При твёрдости более 350 НВ её обычно выражают в единицах Роввелла – НRC (1 HRC = 10 HB).
Такая твёрдость обеспечивается после проведения упрочняющих видов термической и химико-термической обработки: закалки (объёмной или поверхностной) цементации с последующей закалкой азотирования и др.
Применение высокотвердых материалов является резервом повышения нагрузочной способности зубчатых передач уменьшения их габаритов и массы.
Однако с высокой твёрдостью материала связаны дополнительные трудности: плохая прирабатываемость зубьев прогрессирующее усталостное выкрашивание рабочих поверхностей зубьев необходимость проведения термообработки после зубонарезания. Большинство видов упрочняющей термообработки сопровождается значительным короблением зубьев. Для исправления формы зубьев восстановления требуемой степени точности требуются дополнительные дорогостоящие зубоотделочные операции (шлифование полирование притирка и т.п.) что удлиняет технологический процесс изготовления зубчатых колёс и значительно повышает стоимость передачи.
Рекомендуемые для изготовления зубчатых колёс марки конструкционных сталей виды их термообработки соответствующие основные механические характеристики приведении в таблице 2.1. При этом важно чтобы размеры заготовки колёс (диаметр Dзаг и толщина обода или диска Sзаг) не превышали предельных значений Dпред и Sпред.
Марка Dnpeд Snpeд ТО Твердость е m -1
стали мм мм заготовки (НB) Н мм3
80 50 У 220 ÷230 890 650 380
125 80 У 197÷217 780 540 335
При этом HBср1 - HBср2 = 225-207= 18 ед. следовательно обеспечивается приработка зубьев Z1 и Z2.
2. Определение числа циклов перемены напряжений.
По таблице интерполированием находим число циклов перемены напряжений:
- для шестерни: NHO1 = 225 × 106 циклов;
- для колеса: NHO2 = 162 × 106 циклов.
Рекомендуемое значение: NFO = 4 × 106 циклов.
Число циклов нагружения на весь срок эксплуатации:
3. Определение коэффициентов долговечности.
По таблице 2.3 определяем минимальные значения коэффициентов долговечности в зависимости от режима работы:
4. Определяем допускаемое контактное напряжение.
5. Расчет допускаемых напряжений с учётом ресурса передачи.
6. Определение расчётного коэффициента.
- коэффициент ширины зубчатого венца определяем по таблице:
Находим относительную ширину колеса:
Коэффициент неравномерности нагрузки по длине контакта KH и коэффициент неравномерности нагрузки по величине изгиба KF выбираем по кривым на графиках рис.2.3 (а б) в соответствии с расположением колёс относительно опор и твёрдости рабочих поверхностей зубьев колёс.
7. Определение межосевого расстояния передачи.
При проектном расчете прежде всего определяем главный параметр цилиндрической передачи межосевое расстояние - в мм. Расчет производим по следующей формуле:
По нормальным линейным размерам Ra40 принимаем мм;
8. Предварительное определение основных размеров колеса.
Ширина зубчатого венца равна:
9. Определение модуля зубьев передачи.
Полученное значение модуля округляем до стандартного значения по 1-му ряду модулей: 10; 125; 15; 2; 25; 3; 4; 5; 6; 8; 10 мм.
По ГОСТ 9563-60 принимаем m=15 мм.
10. Определяем суммарное число зубьев передачи.
Число зубьев шестерни: шт.;
Число зубьев колеса: шт.
11. Нахождение фактического передаточного числа.
12. Определение фактических размеров передачи.
Делительный диаметр шестерни: мм;
Делительный диаметр колеса: мм;
Уточняем межосевое расстояние: мм;
Определяем диаметр вершин:
Определяем диаметр впадин:
13. Определение пригодности заготовок шестерни и колеса.
14. Определение окружной скорости зубчатого колеса.
15. Определение силы в зацеплении.
16. Принимаем коэффициенты динамической нагрузки.
По табл.2.6 определяем степень точности зубчатой передачи в зависимости от скорости вращения колеса:
мс мс степень точности 8
Далее по табл.2.7 находим значения коэффициентов KHV и KFV.
17. Определяем расчёт контактных напряжений.
По данному примеру недогруз составляет 8% это меньше 10% поэтому контактная прочность зуба обеспечивается.
18. Расчётные напряжения изгиба в основании ножки зуба.
- коэффициент формы зуба находим по табл.2.9.
При: Z1 = 28– YF1 = 3.81;
Прочность зуба на изгиб обеспечивается.
ПРОЕКТНЫЙ РАСЧЕТ ВАЛОВ И ОПОРНЫХ КОНСТРУКЦИЙ.
В различных узлах машин (в том числе и механических передачах) содержится ряд деталей предназначенных для поддерживания вращающихся элементов зубчатых и червячных колес шкивов звездочек и т.д. Такие детали называются валами и осями. По конструкции оси и прямые валы мало отличаются друг от друга но характер их работы существенно различен: оси являются поддерживающими деталями и воспринимают только изгибающие нагрузки; валы представляют собой звенья механизмов передающие крутящие моменты и помимо изгиба испытывают кручение. Нагрузки воспринимаемые валами и осями предаются на корпуса рамы и станины через опорные устройства подшипники.
Части валов и осей непосредственно соприкасающиеся с подшипниками носят общее наименование «цапфы». Цапфу расположенную на конце вала называют типом а цапфу на средней части вала шейкой цапфы передающие на опоры осевые нагрузки называют пятами. Оси могут быть неподвижными или вращаться вместе с насаженными на них деталями. Валы при работе механизма всегда вращаются. Признаками для классификации валов служат их назначение форма геометрической оси конструктивные особенности.
Основными критериями работоспособности проектируемых редукторных валов являются прочность и выносливость. Они испытывают сложную деформацию совместное действие кручения изгиба и растяжения (сжатия). Но так как напряжения в валах от растяжения небольшие то их обычно не учитывают.
Расчет редукторных валов производим в два этапа: 1-ый-проектный (приближенный) расчет валов на чистое кручение 2-ой-проверочный (уточненный) расчет валов на выносливость по напряжениям изгиба и кручения.
1. Выбор материалов валов
Марка Dnpeд Snpeд ТО Твердостье m -1
125 80 У 235 ÷ 262 780 540 335
2. Выбор допускаемых напряжений на кручение.
Проектный расчет валов редуктора выполняем только по напряжениям кручения (как при чистом кручении) то есть при этом не учитываем напряжений изгиба концентрации напряжений и переменность напряжений по времени (циклы напряжений). Для компенсации этого значения допускаемых напряжений на кручение выбираем заниженными в пределах [k]= 10 15 Нмм. Принимаем:
для быстроходного вала [k]= 10 Нмм;
для тихоходного вала [k]= 15 Нмм.
3. Определение геометрических параметров ступеней валов.
Редукторный вал представляет собой ступенчатое цилиндрическое тело количество и размеры которого зависят от количества и размеров установленных на вал деталей.
Проектный расчет валов определяет ориентировочно геометрические размеры каждой ступени вала ее диаметр d и длину l (см. таблицу 3.1) Для колеса: Таблица 3.1.1.
Под элемент открытой передачи
Под уплотнительные крышки и подшипник
d2 = d1 + 2 t t=25 по табл.З.1.1 [1] ;
d2 = 22+ 2 * 25 = 27 мм;
d3 = d2 + 32*r r=16 по табл. 3.1.1[1];
d3 = 30+ 32*16=3512 мм; d3=35мм;
Значение высоты буртика t = 25 мм ориентировочные величины фаски ступицы f = 1 мм и радиусы округления r = 16 мм определяются в зависимости от диаметра ступени d (Таблица 3.2):
d2 = d1 + 2 t t=25 по табл.З.1.1 [1];
d2 = 20 + 2 * 25 = 25 мм;
d3 = d2 + 3.2*r r=16 по табл. 3.1.1[1];
d3 = 25 + 32*16=30 мм;
4. Предварительный выбор подшипников качения.
Выбор наиболее рационального типа подшипников зависит от целого ряда факторов: передаваемой мощности редуктора типа передачи соотношения сил в зацеплении частоты вращения внутреннего кольца подшипника требуемого срока службы приемлемой стоимости схемы установки.
Из таблицы 24.10 [1] выбираем типоразмер подшипников по величине
диаметра d внутреннего кольца подшипника равного диаметру второй d2 и четвертой d4 ступеней вала под подшипники.
По выбранному типоразмеру определяем основные параметры подшипников:
) тихоходный вал: Тип 205 (d = 25 мм D = 52 мм B = 15 мм r = 15 мм
Cor = 14 кН Cr= 695 кН)
) быстроходный вал: Тип 206 (d = 30 ммD = 62 мм B = 16 мм r = 15мм
Cor = 195 кН Cr= 100 кН)
Здесь D -диаметр наружного кольца подшипника В - ширина шарикоподшипников.
5. Эскизная компоновка редуктора.
Для предотвращения задевания поверхностей вращающихся колес за внутренние стенки корпуса контур стенок проводят с зазором Δ = 8 10 мм.
Зазор принимаем равным 10 мм. Расстояние hм (рисунок 3.2) между дном корпуса и поверхностью выступов зубьев колес для всех типов редукторов
принимают hм > 4 * Δ (с целью обеспечения зоны отстоя масла).
6. Проверочный расчет валов на выносливость.
6.1. Составляем расчетную схему вала в соответствии с конструкцией принятой ранее.
6.2.Силы действующие на вал.
-1 =058* -1 =058 * 335= 1943 МПа;
d3 = m * Z3 = 15 * 48 = 72мм;
6.3.1. Определяем сумму изгибающих моментов в вертикальной плоскости:
6.3.2. Cтроим эпюру изгибающих моментов.
Изгибающие моменты в сечении.
6.3.3. Определяем сумму изгибающих моментов в горизонтальной плоскости:
6.3.4. Эпюра крутящих моментов:
Изгибающие моменты в сечении II-II
Результирующие моменты в сечении II-II
Определим напряжения в сечении II-II
6.4 Определяем коэффициенты запаса усталостной прочности.
При совместном действии изгиба и кручения запас усталостной прочности определяем по формуле:
- запас сопротивления усталости только по изгибу.
Коэффициент запаса сопротивления усталости только по кручению рассчитываем по формуле:
В предыдущих формулах а и а - амплитуды переменных составляющих
циклов напряжений т и m — постоянные составляющие
и - коэффициенты корректирующие влияние постоянной составляющей цикла напряжений на сопротивление усталости (таблица 3.3):
Так как в данной работе среднеуглеродистые стали то =01 =05; -1 и -1 - пределы выносливости материала вала при симметричном цикле нагружения. Их определяем по таблице 2.1 (см. выше):
-1 = 058 * -1 = 058 335= 1943 МПа;
Kd и KF - масштабный фактор и фактор шероховатости
По рис. 15.5 и 15.6 принимаем что Kd = 082 КF = 1;
K И К - эффективные коэффициенты концентрации напряжений при изгибе и кручении (ориентировочно назначаем по табл. 15.1):
из табл. стр. 62 [1]
Условие выполняется.
7. Проверка правильности подбора подшипников качения.
Выбранный в ходе проектирования узла вала типоразмер подшипника должен быть проверен на работоспособности по динамической грузоподъемности.
Проверку правильности выбор подшипников проводим следующим
По обеспечению заданной долговечности подшипника то есть
Lh3 LhФ где с учетом режима нагрузки Lh3=hLh..
Где h =0(см. табл. 8.10 [2]).
Здесь фактический срок работы подшипника рассчитывают по зависимости:
a1 - коэффициент надежности принимаем a1= 1;
a2 – обобщенный коэффициент совместного влияния качества метала деталей подшипника и условий его эксплуатации так как у нас обычные условия эксплуатации назначаем a2 = 07;
р - для шариковых подшипников р = 3;
Величина эквивалентной динамической Нагрузки на проверяемый подшипник рассчитываем в общем случае по формуле:
Где Frn и Fan — соответственно радиальная и осевая силы в опоре.
V - коэффициент вращения зависящий от того какое кольцо подшипника вращается у нас вращается внутреннее кольцо и V = 1;
K- коэффициент безопасности учитывающий характер нагрузки при умеренных толчках K =14;
K - температурный коэффициент для температуры подшипникового узла
X Y - коэффициенты соответственно радиальной и осевой нагрузок на подшипники. В данной курсовой работе малая осевая сила значит действие осевой силы в расчет не принимается то есть X = 1 Y = 0.
Рr =(11*89318+ 0) 141 =125045
8013≥ 756 – условие выполняется.
8. Расчет шпоночного соединения.
) Для соединения вала с колесом принимаем призматическую шпонку исполнения В.
) По справочнику (табл. 24.29 [1]) для d3 = 40 мм принимаем размеры сечения шпонки: b = 12 мм h = 8 мм t1 = 4 мм t2 = 33 мм.
) Выбираем длину шпонки: lшп = lст – 5мм в данном случае
Из стандартного ряда по справочнику:
) Для стальной шпонки при стальной нагрузке принимаем допускаемое напряжение сжатие:
03 МПа 120 МПа – условие выполняется.
Для смазывания передач широко применяют картерную систему. В корпус редуктора или коробки передач заливают масло так чтобы венцы
колес были в него погружены. Колеса при вращении увлекают масло разбрызгивая его внутри корпуса. Масло попадает на внутренние стенки корпуса откуда стекает в нижнюю его часть. Внутри корпуса образуется взвесь частиц масла в воздухе которая покрывает поверхность расположенных внутри корпуса деталей.
Картерное смазывание применяют при окружной скорости зубчатых колес и червяков до 125 мс. При более высоких скоростях масло сбрасывает с зубьев центробежная сила и зацепление работает при недостаточном смазывании. Кроме того заметно возрастают потери мощности на перемешивании масла повышается его температура. Выбор смазочного материала основан на опыте эксплуатации машин.
Преимущественное применение имеют масла. Принцип назначения сорта масла следующий: чем выше окружная скорость колеса тем меньше должна быть вязкость масла и чем выше контактные давления в зацеплении тем большей вязкостью должно обладать масло. Поэтому требуемую вязкость масла определяем в зависимости от контактного напряжения и окружной скорости колес (таб. 1 1.1 Г11):
Так как v = 202 мс а контактное напряжение H =25936 МПа то рекомендуемая кинематическая вязкость равна 22 мм2с .
По табл. 11.2 выбираем марку масла для смазывания зубчатой передачи.
Выбираем марку масла И-Л-А-22. Первый (И) - индустриальное второй - принадлежности группе по назначению: Г - для гидравлических систем третий - принадлежность к группе по эксплуатационным свойствам: А - масло без присадок.
Так как v > 1 м с то достаточно погружать в масло только зубчатое колесо. Глубина погружения:
hm = 025138 =345 мм.
Ориентировочно принимаем из соотношения: 1кВт = 1 литр масла.
В данном проекте по требуется около 1 литр масла.
Конструирование элементов редуктора.
1 Конструирование зубчатых колёс.
Длину lст. посадочного отверстия
принимают равной или большей ширине
Диаметр посадочного отверстия:
Диаметр dст. ступицы назначают в
зависимости от материала колеса:
dст. = 15d3+10 = 6268 мм;
Ширину S торцов зубчатого венца принимают:
S = 25m + 2 =25*25 + 2= 7 мм где
m – модуль зацепления;
На торцах зубчатого венца выполняют фаски - где
Для свободной выемки заготовок из штампа принимают значения штамповочных уклонов и радиусов закруглений мм.
Толщина диска С рекомендована для уменьшения влияния термической обработки на точность геометрической формы колеса:
С = (035 04)b2 = 04*66 =264 мм.
3. Корпус редуктора.
Корпус редуктора изготавливают из серого чугуна марки СЧ15.
В малонагруженных редукторах (Нм) толщины стенок крышки и основания корпуса принимают одинаковыми: мм где T2 – вращающий момент на колесе тихоходного вала Нм.
Опорная поверхность фланца выполняется в виде двух длинных параллельно расположенных или четырёх небольших платиков. Места крепления располагают на возможно большем (но в пределах корпуса) расстоянии друг от друга L1 .
Длина опорной поверхности платиков L = L1 + L = 4082 + 498 = 458мм;
ширина ; b1 = 24·15+15·6=498 мм;
высота ; h1 = 23·6=138 мм;
Диаметр отверстия в основании корпуса: d01 = 17 мм;
Длина крышки: L = 160 мм;
Высота фланца: h1 = 3 5 мм;
Толщина крышки: k = (0010 0012)·L = 5 мм;
Применяем полосы технической резины марки МБС толщиной 2 3 мм;
Для крепления смотрового люка к крышки применяем винты М6.
Применим овальный маслоуказатель из прозрачного материала.
7. Сливное отверстие.
8. Установочные штифты.
Под шайбу концевую:
Уплотняющее покрытие плоскости разъёма склеивает крышку и основание корпуса. Для того чтобы обеспечить их разъединение при разборке рекомендуют применять отжимные винты которые ставят в двух противоположных местах крышки корпуса. Диаметр отжимных винтов принимают равным диаметру соединительных d3 стяжных винтов.
Для подъёма и транспортировки крышки корпуса и собранного редуктора применяют проушины отливая их заодно с крышкой.
12. Крышки подшипника.
Применим крышки закладные:
- с отверстием для выходного конца вала.
= (09 1) = 1 · 6 = 6 мм;
S = (09 1) = 1 · 6 = 6 мм;
С 05 · S = 05 · 6 = 3 мм;
спец_2.cdw

ТИтульник.doc
УФИМСКИЙ ГОСУДАРСТВЕННЫЙ АВИАЦИОННЫЙ ТЕХНИЧЕСКИЙ УНИВЕРСИТЕТ
по дисциплине «Прикладная механика»
спец_1.cdw

Рекомендуемые чертежи
- 01.07.2015
- 06.04.2022