Расчет и конструирование привода главного движения металлорежущего станка модели 1Н713





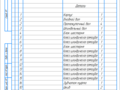
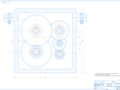

- Добавлен: 25.01.2023
- Размер: 542 KB
- Закачек: 0
Описание
Расчет и конструирование привода главного движения металлорежущего станка модели 1Н713
Состав проекта
![]() |
![]() |
![]() ![]() ![]() ![]() |
![]() ![]() ![]() |
![]() ![]() ![]() ![]() |
![]() ![]() ![]() ![]() |
![]() ![]() ![]() ![]() |
Дополнительная информация
схемы _ МРС.cdw

График структурной сетки
Кинематическая схема
записка.docx
Псковский государственный университет
Механико-машиностроительный факультет
Пояснительная записка
к курсовому проекту
Тема: расчет и конструирование привода главного движения металлорежущего станка модели 1Н713
ОБОСНОВАНИЕ ТЕХНИЧЕСКОГО ЗАДАНИЯ.3
1.Определение диапазона регулирования3
КИНЕМАТИЧЕСКИЙ РАСЧЁТ.3
1.Выбор оптимального кинематического варианта структуры3
2.Выбор электродвигателя4
3.Разработка кинематической схемы5
4.Определение кинематических параметров принципиальной схемы6
ПРОЕКТНЫЙ РАСЧЁТ ОСНОВНЫХ ДЕТАЛЕЙ ПРИВОДА.8
1.Определение диаметров валов и шпинделя9
2.Определение геометрических характеристик зубчатых колёс10
РАСЧЁТ КЛИНОРЕМЕННОЙ ПЕРЕДАЧИ12
РАСЧЁТ ВАЛОВ И ШПИНДЕЛЯ.12
1.Расчёт шпинделя на изгибную жесткость.12
РАСЧЁТ ПОДШИПНИКОВ ШПИНДЕЛЯ15
РАСЧЁТ ВИБРОУСТОЙЧИВОСТИ ШПИНДЕЛЯ16
ПРОВЕРОЧНЫЕ И УТОЧНЁННЫЕ РАСЧЁТЫ ЭЛЕМЕНТОВ ПРИВОДА.17
1.Определение слабого элемента конструкции и его расчёт17
1.1.Расчёт шпоночного соединения17
1.2.Расчёт шлицевого соединения17
ПРОЕКТИРОВАНИЕ КОНСТРУКЦИИ СОГЛАСНО ДОПОЛНИТЕЛЬНЫМ УСЛОВИЯМ.18
В моём курсовом проекте рассчитывается коробка скоростей для многорезцового токарного полуавтомата 1Н713 с устройством для измерения крутящего момента на шпинделе . Этот станок является станом нормальной точности.
Станки модели 1н713 предназначены для токарной обработки деталей в патроне деталей сложной конфигурации: обточки цилиндрических конических и сферических поверхностей в условиях серийного крупносерийного производства
Диаметр детали над станиной 400 мм
Диаметр детали над суппортом 250 мм
Диаметр обрабатываемой детали 500 мм
Пределы частот вращения шпинделя 50..1000 обмин
Мощность главного привода 17 кВт
ОБОСНОВАНИЕ ТЕХНИЧЕСКОГО ЗАДАНИЯ.
1.Определение диапазона регулирования
Диапазон регулирования определяется по формуле:
где: и - максимальная и минимальная частота вращения шпинделя
Для станков с вращательным главным движением минимальная и максимальная частота вращения шпинделя определяются по формулам:
где: и - максимальный и минимальный обрабатываемые диаметры.
и - максимальное и минимальное значение скоростей резания
Определение осуществляется выявлением операций выполняемых станком данной модели. Характерными операциями являются: обточки цилиндрических конических и сферических поверхностей в условиях серийного крупносерийного производства.
Выбираем характерную операцию и по общемашиностроительным нормативам режимов резания находим минимальную скорость вращения заготовки режущий инструмент изготовлен из быстрорежущей стали Р18 при обработке заготовок из стали 18ХГТ .
Фасонное точение: ; ;
КИНЕМАТИЧЕСКИЙ РАСЧЁТ.
1.Выбор оптимального кинематического варианта структуры
Наименьшие затраты времени на поиск оптимального кинематического варианта заданной структуры обеспечивает графоаналитический метод который заключается в построении структурной сетки и графика частот вращения.
Для данной структуры с односкоростным асинхронным электродвигателем главным показателем коробки скоростей является знаменатель ряда который характеризует величину интервала изменения частоты вращения шпинделя при переходе на следующую передачу.
Определяем знаменатель ряда
где: - число ступеней заданной структуры
Определяем количество конструктивных вариантов:
Определяем количество кинематических вариантов
Выбираем оптимальный вариант структурной формулы т.к. масса зубчатых колёс на одном валу будет минимальной если число передач в группе будет уменьшаться а их характеристики будут увеличиваться.
Строим структурную сетку и график частот вращения шпинделя:
2.Выбор электродвигателя
Мощность электродвигателя привода главного движения определяется по максимальной эффективной мощности резания:
где: - эффективная мощность на шпинделе (резания)
- КПД кинематической цепи привода
Исходя из этих данных выбираем двигатель:
3.Разработка кинематической схемы
Разработка кинематической схемы это одна из главных составляющих данного курсового проекта поскольку простота конструкции коробки скоростей её эксплуатационные технологические и другие характеристики в значительной мере определяют уже при разработке кинематической схемы привода.
В первую очередь на кинематической схеме условно наносятся валы.
Далее надо наметить колеса которые будут закреплены неподвижно и колеса которые будут включаться электромагнитными муфтами.
Вид согласующей передачи между электродвигателем и коробкой скоростей на базовой модели станка является муфта упругая втулочно-пальцевая. Мы ввели соединительную втулку.
Так как станок нормальной точности то шпиндель не обязательно разгружать.
Для обеспечения передачи крутящего момента от 5 вала к шпинделю используем шлицевое соединение .
Оформляем кинематическую схему:
4.Определение кинематических параметров принципиальной схемы
К основным параметрам кинематической схемы относятся: мощность частота вращения электродвигателя и фактические значения передаточных отношений всех передач. Характеристики электродвигателя определены в предыдущем пункте а передаточное отношение определяется по графику частот вращения шпинделя.
При подборе числа зубьев передачи с двумя парами колёс использовать метод наименьшего общего кратного. Правильность выбора чисел зубьев колёс проверяется по фактическим частотам вращения шпинделя для всех ступеней коробки скоростей.
Рассмотрим согласующую группу:
Рассмотрим первую группу
Рассмотрим вторую группу
Рассмотрим одиночные группы:
Составляем уравнение кинематического баланса для определения фактических частот вращения а затем относительной погрешности по частоте.
Определяем правильность выбора чисел зубчатых колёс:
Расчётная формула частоты вращения
Допускаемое отклонение относительной погрешности:
Условие выполняется.
Окончательно строим кинематическую схему коробки скоростей.
ПРОЕКТНЫЙ РАСЧЁТ ОСНОВНЫХ ДЕТАЛЕЙ ПРИВОДА.
Для разработки конструкции привода надо определить габаритные характеристики его основных деталей: валов зубчатых колёс шкивов ремённой передачи муфт
Основной расчётной нагрузкой для деталей привода является крутящий момент который определяется по расчётной частоте вращения вала:
Для дополнительного вала:
Для четвёртого вала:
Для шпиндельного вала:
1. Определение диаметров валов и шпинделя
Предварительное определение диаметра вала необходимо для выполнения эскизной компоновки и проводиться он по расчёту на кручение.
Для сплошных валов диаметр определяется как:
Где:- крутящий момент
- допускаемое напряжение при кручении принимаем равной 20мПа
- отношение диаметра отверстия вала к наружному диаметру для сверлильных станков берем равным 08
Полученные значения диаметров будут минимальными для рассчитываемого вала. Размеры вала в других сечениях выбираются конструктивно.
2. Определение геометрических характеристик зубчатых колёс
Расчёт зубчатых передач регламентирован ГОСТом 213554-75. Для зубчатых передач коробки скоростей металлорежущих станков которые имеют как правило упрочнённую поверхность зубьев проектировочный расчёт выполняем с целью обеспечения прочности зубьев на изгиб. При этом минимальный допустимый модуль определяется по формулам:
Материал 40Х и объёмная закалка
Диаметр делительной окружности:
Диаметр окружности впадин:
Диаметр окружности вершин зубьев:
где:- расчётный момент
- вспомогательный коэффициент для прямозубых колёс равен 14
- коэффициент учитывающий распределение нагрузки по ширине венца при несимметричном расположении колёс относительно опор он равен 104
- коэффициент формы зуба
- число зубьев шестерни т.е. наименьшего колеса в группе.
- отношение ширины венца b к делительному диаметру шестерни d.
- допускаемое напряжение изгиба материала шестерни.
Где:- предел изломной выносливости соответствующий базовому числу циклов нагружения.
- коэффициент долговечности
По принятым значениям модулей в группах передач и числам зубьев колёс определяем их основные геометрические характеристики необходимые для эскизной компоновки.
РАСЧЁТ КЛИНОРЕМЕННОЙ ПЕРЕДАЧИ
РАСЧЁТ ВАЛОВ И ШПИНДЕЛЯ.
1.Расчёт шпинделя на изгибную жесткость.
Шпиндельный узел принадлежит к числу тех узлов станка от которых существенно зависит точность его работы.
Прежде всего надо определить величину силы Р а также опорную реакцию Ra. Сила Р определяется по крутящему моменту полученному для средней частоты диапазона регулирования.
Окружное усилие приводного колеса равно:
где:- делительный диаметр приводного зубчатого колеса которое обеспечивает вращение шпинделя с частотой
Силы резания следует определить для среднего диаметра обрабатываемого изделия:
Где: и - максимальный и минимальный диаметр заготовки.
Схема действия сил на вал:
Тогда окружная составляющая силы резания
Тогда радиальную составляющую находим как:
Упругое перемещение переднего конца шпинделя:
Суммарное перемещение конца шпинделя не должно превышать где - допуск на изготовление типовой детали. Для токарных станков нормальной точности в качестве допуска на изготовление типовой детали можно использовать допуск на обработку цилиндрической поверхности среднего диаметра dcp по 8 квалитету точности. Принимаем допускаемое радиальное биение оси шпинделя у переднего торца 8 мкм.
РАСЧЁТ ПОДШИПНИКОВ ШПИНДЕЛЯ
Точность вращения шпинделя важнейшей характеристикой шпиндельного узла в значительной степени определяющей точность обработки деталей на станках.
Определение радиального биения переднего конца шпинделя.
Выбираем 5 класс точности подшипников по ГОСТ 520-71 для станка нормальной точности. Допускаемое радиальное биение подшипников равно 5 мкм. Допускаемое радиальное биение оси шпинделя у переднего торца равно 8 мкм
По номограмме находим
Допускаемое радиальное биение оси шпинделя у переднего торца равно 8мкм
Так как условие то подшипник подобран правильно
Помимо расчёта точности подшипников необходимо определить долговечность работы подшипника.
Рассчитаем долговечность упорных подшипников:
где: - динамическая грузоподъёмность
- динамическая эквивалентная нагрузка для универсальных станков:
- число подшипников в опоре
- полная реакция в опоре
- расчётная частота вращения шпинделя
- для шарикоподшипников
Рассчитаем долговечность специального подшипника:
Так как для универсальных станков расчетная долговечность должна быть не менее 10000 часов а системы подшипников не менее 5000 часов делаем вывод о там что выбранные подшипники нам подходят.
РАСЧЁТ ВИБРОУСТОЙЧИВОСТИ ШПИНДЕЛЯ
Расчёт виброустойчивости шпинделя в первом приближении сводиться к расчёту частоты его собственных колебаний . Частоту собственных колебаний двух опорного шпинделя можно определить приближённо поскольку шпиндель и закреплённые на нём детали умеют сплошную конструкцию. Низшая частота собственных колебаний для шпинделя простой формы находиться по формуле:
где:- приведенная масса.
коэффициент приведения
- относительное расстояние между опорами
Определим собственную частоту колебаний на конце шпинделя:
Расчёт шпинделя на виброустойчивость заключается в сравнении частот собственных колебаний шпинделя и частот вынужденных колебаний с целью избежать явления резонанса. Источником вынужденных колебаний шпинделя может быть переменная жёсткость опор с подшипниками качения неуравновешенность шпинделя и прерывистый режим резания.
Частота возмущения от подшипников качения будет равна числу шариков проходящих в секунду в направлении действующей силы.
Частота возмущающей силы от дисбаланса шпинделя:
Таким образом получили что частоты собственных колебаний более чем в два раза больше частоты вынужденных колебаний следовательно явление резонанса не наступает.
ПРОВЕРОЧНЫЕ И УТОЧНЁННЫЕ РАСЧЁТЫ ЭЛЕМЕНТОВ ПРИВОДА.
Эти расчёты необходимо выполнять ввиду того что некоторые нормализованные размеры элементов привода выбирались конструктивно при эскизной компоновке.
1.Определение слабого элемента конструкции и его расчёт
1.1.Расчёт шпоночного соединения
Расчёт шпоночного соединения на первом валу под подвижным блоком на смятие:
где: - момент на расчитуемом валу
- выступ шпонки от шпоночного паза
- рабочая длинна шпонки равная ширине зубчатого венца
-допускаемое напряжение
Для конструкционной стали 45
- коэффициент запаса прочности
1.2.Расчёт шлицевого соединения
Расчёт шлицов под зубчатым колесом на пятом валу.
Проверим смятие зубья:
-ширина ступицы зубчатого колеса.
-высота поверхности контакта
-средний диаметр соединения
допускаемое напряжение
ПРОЕКТИРОВАНИЕ КОНСТРУКЦИИ СОГЛАСНО ДОПОЛНИТЕЛЬНЫМ УСЛОВИЯМ.
Дополнительным условием является установка устройства для измерения крутящего момента на шпинделе. Выбираем тип устройства - магнитоупругий датчик.
Принцип его действия основан на измерении магнитной проницаемости ферромагнитных материалов при измерении в них напряжений. Этот датчик выполняется в бесконтактном исполнении. Быстрота работы датчика определяется частотой питающего напряжения которая должна быть на порядок выше частоты исследуемого процесса. Повышение частоты ограничено магнитным насыщением материала чувствительного элемента который может быть выполнен из обычной конструкционной стали подвергнутой улучшению.
Датчик состоит из корпуса 1 внутрь которого устанавливают магнитопровод и прижимают крышкой 2. Магнитопровод 3 -пакет склеенных тонких листов стали которые центрируются штифтами 6. На средних выступах магнитопровода устанавливают катушки возбуждения 4 а на крайних выступах измерительные 5. Измерительные катушки соединяются в два независимых плеча и фиксируют ЭДС которые сравниваются на потенциометре.
Принципиальная схема включения магнитоупругого датчика:
Ветлицын А.М. Методические указания для выполнения курсового проекта «Расчёт и конструирование привода главного движения г.Псков 1999г.
Свирщевский Ю.И. Расчёт и конструирование коробок скоростей и подач. Минск Высшая школа 1976г.
Анурьев В.И. Справочник конструктора-машиностроения в 3-х томах М. Машиностроение 2001г.
Металлорежущие станки. Учебное пособие для вузов под редакцией Н.С. Колев М. Машиностроение 1981г.
Тарзиманов Г.А. Проектирование металлорежущих станков М. Машиностроение 1980г.
Общемашиностроительные нормативы режимов резания для технического нормирования работ на металлорежущих станках М. машиностроение 1974г.
Пушь В.Э. Конструирование металлорежущих станков М. Машиностроение 1977г.
Справочник технолога-машиностроителя в 2-х томах. Под редакцией Косиловой А.Г. М. машиностроение 1972г.
Рсчет и конструирование силового механического привода. Тихонов С.И. ППИ СПбГТУ. 2002г.
свертка коробки скоростей (Сборочный чертеж) _ МРС.cdw

уплотнительной пастой типа Герметик
После сборки валы должны проворачиваться свободно без заедания.
Развёртка коробки скоростей (Сборочный чертеж) Руководство по ремонту _ МРС.spw

Развёртка коробки скоростей
Колесо цилиндрическое прямозубое
Болт М10 х 30 ГОСТ 15589-70
Мaнжета 1-22 х 35-1 4 ГОСТ 8752-79
Мaнжета 1-35 х 50-1 4 ГОСТ 8752-79
Мaнжета 1-70 х 95-1 ГОСТ 8752-79
Подшипник 205 ГОСТ 8338-75
Подшипник 207 ГОСТ 8338-75
Подшипник 208 ГОСТ 8338-75
Подшипник 153512 ГОСТ 24696-81
Подшипник 7212 А ГОСТ 27365-87
Шайба 27 Н ГОСТ 6402-70
Шайба 36 Н ГОСТ 6402-70
Шайба 48 Н ГОСТ 6402-70
Шайба 76 Н ГОСТ 6402-70
Шайба 105 Н ГОСТ 6402-70
Шайба 20 ГОСТ 13465-77
Шайба 30 ГОСТ 13465-77
Шайба 70 ГОСТ 13465-77
Шпонка 6 х 6 х 14 ГОСТ 23360-78
Шпонка 8 х 7 х 50 ГОСТ 23360-78
Шпонка 12 х 8 х 40 ГОСТ 23360-78
Шпонка 12 х 8 х 50 ГОСТ 23360-78
Шпонка 18 х 11 х 50 ГОСТ 23360-78
Шпонка 20 х 12 х 56 ГОСТ 23360-78
Шпонка 8 х 11 ГОСТ 24071-97
Развёртка коробки скоростей (Сборочный чертеж) _ МРС.cdw

Осевую игру радиально-упорных ролико-
подшипников в пределах 0 0.05 мм
обеспечить подгонкой регулировочными
Поверхности соединения "корпус-крышка"
перед сборкой покрыть уплотнительной
пастой типа Герметик.
После сборки валы коробки скоростей
должны проворачиваться свободно
без стуков и заедания..
Необработанные наружные поверхности
литых деталей покрыть серой эмалью
Рекомендуемые чертежи
- 22.04.2022
- 22.11.2015
- 16.03.2019