Производство глиноземистого цемента



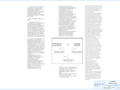
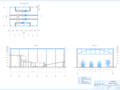
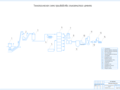
- Добавлен: 24.01.2023
- Размер: 1 MB
- Закачек: 0
Описание
Состав проекта
![]() |
![]() |
![]() ![]() ![]() ![]() |
![]() ![]() ![]() |
![]() ![]() ![]() ![]() |
![]() ![]() ![]() ![]() |
Дополнительная информация
1 лист.cdw

Производство глиноземистого
Технологическая схема
производства глиноземистого цемента
Сушильный барабан для боксита
Первичное дробление известняка
Технологическая схема производства глиноземистого цемента
Гомогенизационные силосы
Центробежная мельница
Пояснительная_записка.docx
Пояснительная записка к курсовой работе состоит из 28 страниц печатного текста таблиц и рисунков 3 патентов. Использовано 14 источников информации. В ней приведены: характеристика выпускаемого вяжущего; характеристика сырьевых материалов; выбор и обоснование способа производства; режим работы предприятия; расчет производительности цеха; расчет состава сырьевой смеси; расчет потребности предприятия в сырье; выбор технологического оборудования; расчет основных механизмов; расчет складов сырьевой продукции. Графическая часть представлена на 3 листах формата А1 на которых изображены план помольного отделения его разрез технологическая схема производства и процессы происходящие при твердении глиноземистого цемента.
Ключевые слова: цемент вяжущее вещество производство обжиг дробление помол алюминатный модуль.
Анализ существующих технологий производства вяжущего
1. Характеристика выпускаемого вяжущего
2. Характеристика сырьевых материалов для производства вяжущего
3. Выбор и обоснование технологии производства вяжущего
4. Новое в производстве вяжущего
Технологическая часть
1. Режим работы предприятия
2. Расчет производительности предприятия
3. Расчет состава сырьевой смеси
4. Расчет потребности предприятия в сырьевых материалах
5. Выбор технологического оборудования
6. Расчет складов сырьевых материалов и готовой продукции
7. Разработка технологии производства вяжущего
8. Контроль производства и качества выпускаемой продукции
Охрана труда на предприятии
Алюминатный цемент был изготовлен впервые почти 80 лет назад. С тех пор механизм его схватывания и твердения является предметом изучения. Вначале было интересно сравнить условия его схватывания и твердения с аналогичными условиями портландцемента с тем чтобы подвести под общий знаменатель силикатные и алюминатные цементы. Однако очень скоро стало ясно что такой аналогии нет условия совершенно различны процессы гидратации и твердения алюминатных цементов отличаются от известной и привычной картины характерной для портландцементов. А в формировании прочности в том числе и в развитии процессов во времени обнаружили такие явления которые никак не могли быть вписаны в знакомую картину портландцементов. У портландцементов прочность в функции времени очень длительно повышается постепенно замедляясь. При исследовании алюминатных цементов в некоторых случаях встречались с очень опасным снижением прочности причину которого не могли объяснить. Особую сложность представляло изучение повышения температуры роли воды действие которых также сильно отличалось от влияния этих факторов на портландцементы. Так родилась проблема алюминатных цементов одна из наиболее сложных проблем гидравлических вяжущих материалов до сих пор еще не решенная во всех аспектах. К сожалению потребуется еще много времени для того чтобы наши знания достигли такого уровня когда мы приблизимся к решению этой научной проблемы. До сих пор приходилось сталкиваться с некомпетентностью даже с неграмотностью специалистов с многочисленными устремлениями включить алюминатные цементы из-за их ценных свойств в качестве гидравлических вяжущих в ряд строительных материалов используя при этом их большую начальную прочность и высокую сульфатостойкость. Долгим был путь к получению ответа (правда еще не во всех областях окончательного и последнего) на вопрос как идет гидратация алюминатных цементов как формируется прочность почему и когда происходит ее опасное снижение. В большинстве случаев можно однозначно сформулировать физические и химические причины снижения прочности те факторы которые воздействуют на алюминатные цементы или на структуру бетонов на их основе. Более того исследуя предельные состояния алюминатных цементов мы на основе этого научились в определенных границах "предсказывать" их поведение.
Важнейшим достижением является то что мы уже не видим тайны в повреждениях и разрушениях бетонов на алюминатных цементах а также то что путем строгого выполнения всех предписанных мероприятий можем предотвратить полное разрушение или снизить в значительной степени ущерб от него. Алюминатный цемент обладает рядом ценных свойств наиболее важные из которых — сульфатостойкость и жаростойкость. Быстрое твердение происходит с выделением большого количества тепла поэтому его часто применяют для зимнего бетонирования. Он является основой для получения расширяющихся и напрягающих цементов а также многих специальных цементов применяемых при строительстве водонепроницаемых сооружений бурении нефтяных и газовых скважин ликвидации аварий ремонте после пожаров.
Бетоны на высокоалюминатном цементе обладают высокой прочностью термостойкостью сопротивлением против воздействия расплавленных шлаков и других химических реагентов восстановительной среды с высоким содержанием СО и Н2.
1. Характеристика выпускаемого вяжущего [5]
Глиноземистый цемент — быстротвердеющее в воде и на воздухе высокопрочное вяжущее вещество получаемое путем обжига до плавления или спекания смеси материалов богатых глиноземом с известью или известняком и последующего тонкого измельчения продукта обжига. В отличие от портландцемента клинкер которого состоит главным образом из силикатов кальция глиноземистый цемент получают из шлака (расплава) или клинкера содержащего преимущественно низкоосновные алюминаты кальция. Важнейшим минералом глиноземистого цемента является моноалюминат кальция (СаО А1203).
Рис.1 Микрофотография клинкера
В зависимости от количества окиси алюминия и нежелательных примесей в их составе глиноземистые цементы выпускаемые в России делятся на четыре вида:
обычный глиноземистый цемент выпускаемый по ГОСТ 969—91;
высокоглиноземистый цемент алюминотермического производства по ТУ 21-РСФСР-3.283-84;
высокоглиноземистый цемент — талюм изготовляемый в соответствии с ТУ 03-399-78;
особочистый высокоглиноземистый цемент (ОБ ГЦ) по ТУ 21-20 12-78.
Химический состав глиноземистых цементов разнообразен и зависит от состава исходных сырьевых материалов и технологии производства. Содержание важнейших оксидов характеризуется большими колебаниями (%): Si02 5—10 А1203 35—50 Fe203 5—15 (включая оксид железа СаО 35—45.
В зависимости от способа производства различают глиноземистые цементы: плавленые полученные плавлением в различных агрегатах и спеченные — при спекании сырьевой смеси.
При наличии в сырье значительного количества кремнезема оксидов -желееза цементы называют белито-глиноземистыми железосодержащими или алюмоферритными.
Введение в состав сырьевой смеси различных материалов приводит к изменению названия цемента при этом добавляется термин отражающий вид добавки. Например барийглиноземистый (при добавлении ВаО) бороглиноземистый (В2 03) сульфоалюминатный (CaS04) и т.д.
В ряде стран для повышения жаростойких свойств цемента используют оксид магния. В частности в глиноземистый цемент добавляют от 50 до 90 % порошкообразного оксида магния. Введение в сырьевую смесь MgC03 частично или полностью взамен СаС03 позволяет получить цемент с высокой огнеупорностью и хорошими прочностными свойствами.
Глиноземистый цемент — нормально схватывающееся гидравлическое вяжущее отличающееся от других цементов высокой прочностью достигаемой в раннем возрасте. По внешнему виду он представляет собой тонкий порошок цвет которого (от светло-серого до темно-коричневого) зависит от состава сырья и способа производства. Цвет нашего глиноземистого цемента доменной плавки светло-серый. Основные признаки позволяющие распознать глиноземистый цемемент — химический состав и быстрое нарастание прочности в раннем возрасте. Реакция на фенолфталеин — слабощелочная. Плотность — 3—31 она может достигать и 32; средняя плотность в рыхлом состоянии — 1000-1200 кгм3.
Нормальная густота раствора почти не отличается от нормальной густоты раствора портландцемента и составляет 23—28. Увеличение содержания воды в тесте на 1—2% сверх определенной по ГОСТ несколько замедляет схватывание особенно его начало. Глиноземистый цемент характеризуется нормальными сроками схватывания он отнюдь не быстросхватывающийся как считали раньше. Начало схватывания — не ранее 30 мин и конец схватывания не позднее 12 ч от начала затворения. Сроки схватывания глиноземистого цемента можно значительно изменять применяя добавки.
При этом следует учесть что некоторые добавки неблагоприятно влияют на прочность цемента поэтому применять их можно после соответствующих испытаний. Обращает на себя внимание сахар который в количестве 1% и более может не только замедлить схватывание на длительное время но и вовсе прекратить твердение.
Рис.2 Повышение температуры бетона на разных цементах в процессе твердения
Тепловыделение глиноземистого цемента имеет свои характерные особенности. При твердении выделяется значительное количество тепла — 315—399 кДжг в отдельных случаях 50-100 кДжг у цемента высоких марок и 252—291 кДжг у цемента средних и низких марок за 28 сут. твердения. Общее количество тепла находится примерно в тех же пределах что и у высокопрочного портландцемента но более быстрая гидратация глиноземистого цемента ускоряет тепловыделение. Экзотермические реакции начинаются не сразу после затворения водой и даже не непосредственно после конца схватывания а через 5- 8 ч. Начавшееся тепловыделение продолжается затем столь интенсивно что через сутки выделяется уже 70—80% общего количества тепла тогда как у портландцемента столько же тепла выделяется обычно к семисуточному возрасту. Приращение температуры в бетоне при твердении примерно пропорционально содержанию в нем цемента. Затворяют глиноземистый цемент только на пресной воде.
Выпускается глиноземистый цемент марок 400 500 и 600. Маркировка осуществляется по результатам испытаний стандартно изготовленных призм размером 40*40*160 мм из раствора пластичной консистенции состава 1:3 с нормальным Вольским песком погруженных в воду через 6 ч после начала затворения и испытанных через 3 сут твердения (табл. 33). Требовании ГОСТ 969—77 к глиноземистому цементу приведены в таблице ниже.
Предел прочности МПа (не менее) при сжатии через
Химическая стойкость глиноземистого цемента по сравнению с портландцементом также весьма высока из-за особенностей химико - минералогического состава цементного камня. Отсутствие в нем растворимого легко выщелачивающегося гидроксида кальция наличие мало растворимого гидроксида алюминия и плотных образований низкоосновных гндроалюмииатов кальция придают этому цементу весьма высокую коррозионную стойкость.
Твердение бетона на глиноземистом цементе можно ускорить путем более длительного перемешивания бетонной смеси в бетономешалке. Так например при расходе глиноземистого цемента 350 кгмл и ВЦ=04 перемешивание бетонной смеси в течение 30 мин при укладке вибрированием позволяет получить: через 6 ч прочность бетона 25—30 МПа и через 8—10 ч —40—45 МПа. В последующие сроки твердения прочность сколько-нибудь заметно не снижается. Бетонные работы на глиноземистом цементе целесообразно вести в теплое время года лишь когда прохладно - ночью ранним утром чтобы материалы не нагревались солнцем.
2. Характеристика сырьевых материалов для производства вяжущего [5]
Важнейшим глиноземосодержащим сырьевым компонентом в производстве глиноземистого цемента являются сравнительно малораспространенные бокситы. Это дефицитное сырье используемое главным образом для получения металлического алюминия. Боксит содержит гидраты глинозема в виде бемита. гидрагиллита и редко диаспора с примесями кремнезема оксидов железа магния титана и др. Так например в бокситах некоторых месторождении содержатся бемит и диаспор а также железо в виде гематита и кремнезем в виде кварца либо опала. Содержание глинозема в бокситах может достигать 70 %.
Качество боксита характеризуется содержанием Al2О3 и коэффициентом качества — отношением количества глинозема по массе к соответствующему количеству оксида железа. Для
производства глиноземистого цемента применяют бокситы главным образом марок Б-2 Б-3 и Б-7 с коэффициентом качества соответственно 7; 5 и 5.6; содержание глинозема в них должно быть не менее чем 46 и 30 %. Используют также бокситы марки Б-1 с коэффициентом качества 9 содержащие не менее 49 % глинозема. Месторождения бокситов имеются в ряде районов России.
Количество оксида железа хотя и не регламентируется ГОСТ но из изложенного выше видно что оно исключительно важно для технологии производства глиноземистого цемента. В используемых у нас уральских бокситах содержание оксида железа достигает 28%. В последнее время начали применять отвальные шлаки алюминотермического производства ферросплавов а также шлаки вторичной переплавки алюминия н его сплавов.
Для получения высокоглнноземнстого и особо чистого высокоглиноземистого цементов применяют чистый глинозем разных марок. Известковым компонентом служат известняки и в отдельных случаях обожженная известь. Имеются патенты на комплексное производство глиноземистого цемента и серной кислоты цемента и фосфора. В этих случаях вместо извести применяют гипс фосфориты и др. При восстановительной планке компонентом сырьевой шихты является также кокс от которого прежде всего требуется возможно более низкое содержание кремнекислоты в зольной части.
3. Выбор и обоснование технологии производства вяжущего [78]
Существует два принципиально различных способа производства глиноземистого цемента — плавление шихты и спекание. При выборе того или иного способа нужно учитывать ряд факторов и прежде всего химический состав боксита определенной марки и в особенности содержание в нем кремнекислоты и оксида железа. На основе экспериментальных исследований определяют температуры спекания и плавления и интервал между ними а также качество получаемого расплава либо клинкера. Технико-экономический анализ позволяет выявить какой способ производства в данных условиях рациональнее. При этом учитывают наличие и стоимость электроэнергии качество кокса и др.
Плавление. Глиноземистый цемент можно получать плавлением в ватержакетных печах (вагранках с водяным охлаждением). Боксит известняк и кокс в установленном расчетом соотношении загружают в верхнюю часть печи. Подогретый в рекуператорах воздух вдувают через фурмы; образующийся внизу печи расплав при 1773—I873K выпускается через летку; расплав металлического железа выпускается нз печи отдельно. Проводились опыты но применению для этих печен воздуха обогащенного кислородом. Производительность их достигала 50 т в сут при удельном расходе топлива около 500 кг на I т расплава. Для этого производства необходимы высококачественные бокситы с малым содержанием кремнезема так как восстановление кремнезема до кремния к получение одновременно кремнистого чугуна или ферросилиция происходят при высоких температурах которые в этих печах создать трудно. Расплав (шлак) охлаждается в специальных изложницах и в охлажденном виде измельчается в дробилках и затем подвергается тонкому измельчению в многокамерных трубных мельницах.
Во Франции и Англии применяются мартеновские пламенные печи снабженные вертикальной трубой через которую в печь поступает сырьевая шихта. Печи работают на пылевидном топливе при горячем дутье. Шлак выпускается при 1823—I873K. Производительность достигает 70 т в сут. Существует способ электроплавки глиноземистого цемента при применении которого продукт не загрязняется кремнекислотой содержащейся в золе кокса поскольку одновременно выплавляется ферросилиций.
Есть опыт использования дуговых печей работающих преимущественно на переменном токе. Для интенсификации процесса плавки сырьевые компоненты предварительно высушивали измельчали и после тщательного смешивания брикетировали или гранулировали. Во избежание выбросов нз печи которые бывают из-за быстрого выделения воды и углекислоты нз сырьевой шихты предварительно прокаливают боксит и кальцинируют известняк.
Благодаря высокий температуре в такой электропечи достигающей 2273К и применению кокса в шихте кремнезем шихты восстанавливается до кремния и в результате взаимодействия с металлическим железом образуется ферросилиций.
Недостаток этого способа — ограниченный предел восстановимости кремнезема из-за образования значительных количеств карбида кальция увеличивающихся с повышением температуры плавки.
Глиноземистый цемент в США получают сочетая процесс слабого спекания шихты во вращающейся печи с последующим расплавлением ее в ванной печи. Высказываются мнения о возможности плавления но вращающихся печах но этот способ в промышленности не применяется. Большое значение имеет способ доменной плавки чугуна и высокоглиноземистого шлака успешно разработанный советскими учеными. За рубежом его называют «русским способом производства глиноземистого цемента». Организации производства этого цемента в России предшествовали широкие экспериментальные исследования которые позволили установить рациональный состав доменной шихты условия плавки и в особенности режим охлаждения выплавляемого шлака. Исследования строительно-технических свойств получаемого цемента и технико-экономические показатели его производства и применения свидетельствовали об эффективности этого способа.
Спекание. Исследованию процесса спекания глиноземистого цемента уделялось у нас в свое время большое внимание потому что из-за сравнительно невысоких температур обычно составляющих около 1473—1673 К его можно вести в широко применяемых в промышленности обжигательных агрегатах.
Способ спекания во вращающихся и других печах при окислительном и восстановительном обжиге тщательно и глубоко исследовался но не был внедрен в производство по ряду причин. Это в частности малый интервал между температурами спекания и плавления что приводит к появлению колец и настылей в печи а также необходимость применения высококачественных низкокремнеземистых и маложелезистых бокситом необходимых для изготовления металлического алюминия.
Скорость охлаждения расплава (шлака) имеет большое значение так как она существенно влияет на его кристаллическую структуру отчего в значительной степени зависит качество цемента. Как известно быстрое охлаждение горячих расплавов (например доменных шлаков) для предупреждения их кристаллизации обычно существенно повышает их гидравлическую активность — в качестве добавки к цементу а также способность твердеть самостоятельно. Предполагалось что и высокоглиноземистые расплавы в стекловидном состоянии быстро охлажденные будут обладать более высокими вяжущими свойствами.
Однако оказалось что характерные для глиноземистых цементов строительно-технические свойства и. в первую очередь высокая начальная прочность проявляется только у равномерно закристаллизованных т. е. медленно охлажденных цементов. Было установлено что стекловидная фаза алюминатов кальция почти полностью утрачивает спою высокую активность. Можно считать что кристаллические образования алюминатов кальция обладающие вяжущими свойствами теряют их. если находятся н стекловидном состоянии. Казалось бы что высокоглиноземистые расплавы (шлаки) должны подвергаться медленному и равномерному охлаждению чтобы более полно и равномерно кристаллизоваться. Однако при таком способе наряду с алюминатами кальция будет кристаллизоваться и геленит кальция — соединение которое в кристаллическом состоянии инертно и приобретает гидравлическую активность только в виде стекловидной фазы Поэтому возникла необходимость изыскать комбинированный способ охлаждения при котором создавались бы условия для застывания геленита в виде стекла при кристаллизации алюминатов кальция. Физико-химическая основа его такова. В системе CaO— Al2O3—SiO2 есть поле устойчивости геленита в котором обычно располагаются составы выпускаемого у нас глиноземистого цемента. Равновесная кристаллизация таких расплавов приводит к появлению в первую очередь геленита. кристаллизующегося при 1683— 1793К. После этого при более низких температурах кристаллизуются алюминаты кальция также в виде твердых растворов. Поэтому било предложено создавать такие условия при которых расплав быстро проходил бы указанный температурный интервал за счет быстрого охлаждения. Это предупреждает кристаллизацию геленита и образование активного алюмосиликатного стекла при последующей по мере понижения температуры кристаллизации алюминатов кальция. Степень охлаждения при грануляции должна быть очень точной чтобы алюминаты кальция не перешли в состав стекловидной фазы что недопустимо. Опыты показали что спустя некоторое время после выпуска из домны расплав должен подвергаться не водной а паровоздушной грануляции. Для этого грануляционную установку разместили на некотором расстоянии от летки домны. При этом способе удалось существенно повысить качество глиноземистого цемента довести содержание в нем Si02 до 11 — 13%. Исследование полученных шлаков под микроскопом показало что поверхность образующихся гранул размером 20 — 30 мм состоит из стекло а внутри они содержат хорошо закристаллизованные алюминаты кальция и эвтектические прорастания моноалюмината кальция и двух- кальциевого силиката. Размалываемость быстро охлажденного шлака резко улучшается и соответственно повышается производительность цементных мельниц. Испытания опытных цементов показали что прочность их увеличивается примерно в 1.5—2 раза по сравнению с прочностью цементов полученных из расплавов медленного охлаждения.
В данном курсовом проекте для производства глиноземистого цемента был выбран способ спекания с использованием электродуговых печей. Этот способ отличается высокой производительностью отсутствием потребности в топливе высокой экологичностью однако требует большое количество электроэнергии.
4. Новое в производстве вяжущего [13]
В ходе выполнения курсового проекта был произведен патентный поиск глубиной в 6 лет. Были найдены следующие технические решения:
Патент на изобретение № 2336239 «Способ обработки глиноземистого цемента»
Изобретение относится к области производства строительных материалов в частности к получению строительного раствора из глиноземистого цемента исходным сырьем которого является высокоглиноземистый шлак выплавляемый из боксита в доменных печах. Технический результат - снижение температуры обжига при высоком значении степени окисления серы. В способе обработки глиноземистого цемента предназначенного для получения строительного раствора при затворении водой путем его окислительного обжига указанному обжигу подвергают глиноземистый цемент с размером частиц 004-008 мм при температуре 800-890°С. Окислительный обжиг проводят во вращающейся трубчатой печи с внешним или внутренним обогревом. 2 з.п. ф-лы 4 табл. (см. Приложение 1)
Патент на изобретение № 2284971 «Высокоглиноземистое вяжущее»
Изобретение относится к промышленности строительных материалов а именно к производству жаростойкого вяжущего и может быть использовано для приготовления жаростойких бетонов и изделий на их основе изготовления монолитных элементов футеровок тепловых агрегатов а также для приготовления огнеупорных растворов клеев и других смесей. Высокоглиноземистое вяжущее включающее глиноземистый цемент и тонкомолотую добавку на основе оксида алюминия в качестве тонкомолотой добавки содержит кислородсодержащее соединение алюминия общей формулы Al2O3·nH2O где n=003-20 полученное быстрой частичной дегидратацией гидроксида алюминия при следующем соотношении компонентов мас.%: глиноземистый цемент 55-90 указанное кислородсодержащее соединение алюминия 10-45. Технический результат - повышение огнеупорности температуры деформации под нагрузкой сохранение высокой активности набора марочной прочности в течение трех суток способность набора марочной прочности как в нормальных условиях так и при пропарке а также удешевление вяжущего расширение сырьевой базы при использовании отходов промышленности. 1 з.п. ф-лы 1 табл. (см. Приложение 2)
Патент на изобретение № 93043807 «Способ переработки красного шлама глиноземистого производства»
Способ относится к области металлургии и включает плавку красного шлама совместно с шлакообразующим веществом и углеродистым восстановителем выплавление чугуна и шлака. Отличается тем что в качестве шлакообразующего вещества и углеродистого восстановителя применяют колошниковую пыль доменного производства и бокситовую руду с кремневым модулем 2-5 при этом колошниковую пыль вводят из расчета полного восстановления оксидов железа бокситовую руду вводят из расчета получения силикатного модуля 008-035. Регулируют соотношение между оксидом кальция и оксидом кремния из расчета получения гидравлического модуля 055-080. Регулирование осуществляют добавкой кальцийсодержащего вещества например в виде оксида или фторида либо добавкой кремнийвосстанавливающего вещества например кальция или алюминия. В способе в начале расплавляют красный шлам затем добавляют боксит а затем колошниковую пыль. Полученный шлак перерабатывают на глиноземистый цемент либо на глинозем. (см. Приложение 3)
Расчетный годовой фонд времени работы технологического оборудования в часах на основании которого рассчитывается производственная мощность предприятия в целом и отдельных линий установок определяют по формуле:
где Вр – расчетный годовой фонд времени работы технологического оборудования в часах;
Ср – расчетное кол – во рабочих суток в году;
Ч – количество рабочих часов в сутки;
Кн–среднегодовой коэффициент использования технологического оборудования.
Коэффициент использования печных установок по календарному времени зависит от длительности их остановки на капитальные средние и текущие механические ремонты а также от частоты замены футеровки и от других причин; обычно он принимается равным 09 – 092. При прерывной рабочей неделе с двумя выходными днями при двухсменной работе К принимается равным 0943; при трехсменной работе – 091.
Таблица 1. Режим работы предприятия
Наименование цехов отделений пролетов операций
Кол – во рабочих дней в году
Кол – во смен в сутки
Длительность рабочей смены
Годовой фонд эксплуатационного времени
Коэффициент использования эксплуатационного времени
Годовой фонд рабочего времени в часах
При расчете производительности следует учитывать возможный брак и другие производственные потери. Для заводов по производству вяжущих веществ средние величины возможных производственных потерь обычно принимаются 1-3%. В данном производстве они составляют около 20% так как используется технологическая операция сушка на которой возможны большие потери.
Производительность завода по готовой продукции определяется по формулам:
где Пгод – заданная годовая производительность завода
Ср – расчетное кол-во рабочих суток в году.
где Вр – расчетный годовой фонд рабочего времени в час.
Производительность по готовой продукции:
Псут = ПгодСр=200200365=548493 т
Псмен = 200200365*3=182831 т
Пчас = ПгодВр=2002007884=22854 т
3. Расчет состава сырьевой смеси
Таблица 2. Потребность в сырье на 1 т готовой продукции
Технологическая операция
Склад готовой продукции
Транспортирование готовой продукции на склад
Транспортирование клинкера на помол
Охлаждение клинкера после обжига
Обжиг в печах до плавления с получением клинкера:
Транспортирование смеси из силосов в обжиговую печь
Корректирование и хранение смеси в силосах
Совместный помол известняка и боксита
Дозировка компонентов
Корректирование и хранение известняка в силосах
Вторичное дробление известняка
Первичное дробление известняка
Транспортирование компонентов со склада в дробильное и сушильное отделения:
Таблица 3. Потребность цеха в сырье и полуфабрикатах
Удельный расход сырья
Потребность проектируемого цеха в сырье в час смену сутки год с учетом потерь при их транспортировании определяют по формуле:
Рм – расход сырья в час смену сутки и год в тоннах
П – производительность цеха соответственно в час смену сутки год в тоннах
Ру – удельный расход сырья в тоннах на тонну готовой продукции.
Итого в год потребности предприятия в сырьевых материалах составляет 30344314 тонн в год.
5. Выбор технологического оборудования [6 11 12]
Необходимое количество машин и другого оборудования определяют по формуле:
Где М – количество машин подлежащих установке;
Ппч – требуемая часовая производительность по данному технологическому переделу;
Пп – паспортная или расчетная часовая производительность машин выбранного типоразмера;
Кн – нормативный коэффициент использования оборудования во времени (принимается равным 0.92).
Mдроб щек = 22854 (14*092)= 177
Mдроб мол = 22854 (18*092)=13
Mсуш бар = 22854 (15*092)= 165
Mвалк мел = 22854 (9*092)=27
Mцентр мел= 22854 (25*092)=09
Наименование оборудования
Дробилка щековая PE 400*600 производительностью 14000 кгч
Дробилка молотковая СМД 147 А производительностью 18000 кгч
Сушильный барабан производительностью 15000 кгч
Валковая мельница LHG – 300 производительностью 9000 кгч
Центробежная мельница Титан М-160 производительностью 25000 кгч
Сырье – 10-суточный запас.
Рассчитываем объем складов сырья:
V (складов сырья) = (Псут. * число дней запаса) (ρнас. * Кзаполнения)
V (силосного склада известняка) = (249 39*10)( *14*09) = 1979 м3
V (силосного склада боксита )= (58195*10)(128*09) = 5051 м3
V (силосного склада готового цемента) = (548493*10)(151*09) = 403605 м3
В качестве складов используются силосы в количестве:
штуки (объемом 1700 и 500 м3)– для склада известняка 2 штуки (объемом 3000 м3) – для склада боксита 2 штуки (объемом 3000 и 1700 м3) – для склада готовой продукции.
7. Разработка технологии производства вяжущего [5 7 8]
Известняк из карьера доставляется на предприятие автотранспортом. В первую очередь он направляется на первичное дробление в щековые дробилки с диаметром впускного отверстия 500-750 мм. Затем известняк измельченный до размера кусков в диаметре 200-300 мм транспортируется на стадию вторичного дробления т.е. в молотковые дробилки из которых он измельченный до среднего размера куска 10-20 мм направляется на склад сырья (силосы в количестве 2 шт.).
Боксит доставляется на предприятие также автотранспортом. Перед непосредственным использованием его необходимо высушить до влажности 1% в сушильных барабанах. Затем он через дозаторы транспортируется на помол в валковую мельницу. Измельченный боксит хранится в силосах.
Известняк и боксит прошедшие предварительную обработку через дозировочный узел направляются на обжиг в электрическую печь. Обжиг является основным процессом при производстве глиноземистого цемента. Обжиг идет при температуре 14000С. Далее обожженная до спекания смесь боксита и известняка направляется в холодильники где медленно охлаждается.
Полученный клинкер измельчается до среднего размера частиц 006 – 3 мм в центробежных мельницах откуда полученный цемент подается на склад готовой продукции.
8. Контроль производства и качества выпускаемой продукции [18]
Ввиду того что химическая природа глиноземистого цемента различна от портландцемента и других вяжущих материалов необходимо раздельно хранить и перевозить его. Обращаясь к химическим уравнениям гидратации главнейших соединений входящих в состав глиноземистого цемента и портландцемента можно найти объяснение того замечательного факта что если например смешать в пропорции 1:1 глиноземистый цемент и высококачественный портландцемент то при эатворении такой смеси неожиданно получится совершенно отрицательный результат: смесь чрезвычайно быстро схватывается и дает неудовлетворительную прочность.
) 2 (А1203 . СаО) + ЮН20 = 2СаО . А120* 7Н2ОА12 (ОН)в для глиноземистого цемента.
) 3 СаО . Si02 + 45Н20 = СаО. Si02.25Н20 + 2Са (ОН)3 для портландцемента.
Сопоставление этих уравнений показывает что образцы цемента существенно отличаются друг от друга. Глиноземистый цемент требует значительно больше воды для гидратации чем портландцемент. Кроме того в затвердевшем глиноземистом цементе в отличие от портландцемента не содержится свободного гидрата извести. Низкая прочность смеси при соединении глиноземистого и портландцемента объясняется тем что гидратация трехкальциевого силиката дает значительное количество свободного гидрата окиси кальция а поэтому продукт гидратации глиноземистого цемента совершенно изменяет свой состав и характер.
Двухкальциевый гидроалюминат должен при наличии свободного гидрата извести перейти в более основные гидроалюминаты. Гидрат же глинозема получившийся при гидратации однокальциевого алюмината в весьма дисперсном коллоидальном состоянии встречаясь со свободным гидратом извести немедленно образует высокоосновные гидроалюминаты. Таким образом в смеси глиноземистого и портландцемента продукты получающиеся в правой части вышеприведенных уравнений 1 и 2 исчезаютпроцесс гидратации чрезвычайно ускоряется и приводит к быстрой коагуляции продуктов гидратации образующихся на поверхности зерен. Процесс схватывания ускоряется настолько что делается почти мгновенным и вследствие этого гидратация быстро прекращается. В конечном счете затворенная смесь не показывает механической прочности свойственной высоким сортам указанных цементов в отдельности. Склад для хранения глиноземистого цемента должен быть крытый и сухой на лагах на высоте не менее 30 см от земли и иметь проветриваемое подполье. Конструкция кровли и ее наклон должны обеспечить быстрое удаление воды с крыши. Свесы крыши должны быть достаточной длины для предохранения стен от косого дождя. Цемент лежащий на складе должен быть тщательно защищен от атмосферных влияний сквозняков и усиленного обмена воздуха в помещении склада. Большое внимание следует уделить также тому чтобы цемент не слеживался при хранении. В противном случае необходимо заботиться о хорошей распушке цемента перед подачей его в бетономешалку. В противоположность другим цементам глиноземистые цементы в хорошей таре и в хороших условиях хранения могут сохраняться более продолжительное время. Это обстоятельство подтвердили наши исследования над глиноземистым цементом пролежавшим бумажной таре более 1 года. Длительное же хранение глиноземистого цемента без тары нарушает его свойства. При применении глиноземистого цемента лежавшего без тары более б месяцев его нужно повторно проверить и испытать по ГОСТ. Применительно к специфическим условиям военного и транспортного строительства при перевозке цемента навалом можно рекомендовать:
а) покрывать цемент перевозимый на автомашине или прицепе обычного типа брезентом не прилегающим непосредственно к цементу
б) навешивать на продольные борты автомашин и прицепов специальные крыши на петлях закрывающие щели.
Охрана труда на предприятии [710]
При большой насыщенности предприятий цементной промышленности сложными механизмами и установками по добыче и переработке сырья обжигу сырьевых смесей и измельчению клинкера перемешиванию складированию и отгрузке огромных масс материалов наличию большого количества электродвигателей особое внимание при проектировании заводов и их эксплуатации должно уделяться созданию благоприятных условий для безопасной работы трудящихся. Организацию охраны труда следует осуществлять в полном соответствии с «Правилами по технике безопасности и производственной санитарии на предприятиях цементной промышленности».
Поступающие на предприятие рабочие должны допускаться к работе только после их обучения безопасным приемам работы и инструктажа по технике
безопасности. Ежеквартально необходимо проводить дополнительный инструктаж и ежегодное повторное обучение по техники безопасности непосредственно на рабочем месте. На действующих предприятиях необходимо оградить движущиеся части всех механизмов и двигателей а также электроустановки площадки и т.д. Должны быть заземлены электродвигатели и электрическая аппаратура. Обслуживание дробилок мельниц печей шлаков транспортирующих и погрузочно-разгрузочных механизмов должно осуществляться в соответствии с правилами безопасности работы у каждой установки. Шум возникающий при работе многих механизмов характеризуется высокой интенсивностью превышающей допустимую норму (90 Дб). К числу мероприятий по снижению шума у рабочих мест относят применение демпфицирующих прокладок между внутренней стеной мельниц и броне футерованными плитами замену в паровых мельницах стальных плит на резиновые. При этом звуковое давление снижается в 5-12 раз. Укрытие мельниц и дробилок шумоизолирующими кожухами облицовка источников шума звукопоглощающими материалами также дает хороший результат. В том числе большая задымленность на заводах ликвидируется при накладке аспирационных систем установки очистных систем (их герметичность). В задымленных местах рабочие должны применять средства защиты от пыли.
В данном курсовом проекте запроектировано промышленное здание по производству глиноземистого цемента производительностью 200 000 тгод. Для обеспечения этой производительности заводу потребуется 30344314 тгод сырьевых ресурсов и следующее технологическое оборудование: щековые дробилки молотковые дробилки Валковые и центробежные мельницы электрическая печь ленточные и пластинчатые транспортеры сушильные барабаны пневмотранспорт.
В ходе курсового проектирования были выполнены: план промышленного предприятия с размещением оборудования для производства глиноземистого цемента технологическая схема производства поперечный разрез здания с указанием оборудования производства произведены расчеты производительности предприятия состава сырьевой смеси складов сырьевых материалов и готовой продукции.
В записке содержится материал о способах производства глиноземистого цемента его видах свойствах и т.д. В приложении приведены патенты о нововведениях в производстве глиноземистого цемента.
Список используемой литературы
ТУ 21-РСФСР-3.283-84
Волженский А.В. Буров Ю.С. Колокольников В.С. Минеральные вяжущие вещества. – М.: Стройиздат 1986. – 476с.
Журавлев М.И. Толомеев А.А. Механическое оборудование прдериятий вяжущих материалов и изделий на базе их. – М.: Стройиздат 1983. – 239 с.
Кузнецова Т.В. Глиноземистый цемент. – М.: Стройиздат 1988. – 272 с.
Певзнер Р.Л. Глиноземистый цемент. – М.: Издательство Академии наук СССР 1943. – 14 с.
РОССИЙСКАЯ ФЕДЕРАЦИЯ
ПО ИНТЕЛЛЕКТУАЛЬНОЙ СОБСТВЕННОСТИ
ПАТЕНТАМ И ТОВАРНЫМ ЗНАКАМ
(12) ОПИСАНИЕ ИЗОБРЕТЕНИЯ К ПАТЕНТУ
Статус: по данным на 10.05.2011 - действует
(21) (22) Заявка: 200613414303 25.09.2006
(24)начала отсчета срока действия патента:
(43)публикации заявки: 27.03.2008
(45) Опубликовано: 20.10.2008
(56) Список документов цитированных в отчете о
поиске: SU 50012 A 31.08.1936. SU 208512 A 20.03.1968. SU 101437 A 01.01.1955. RU 2101246 C1 10.01.1998.
Адрес для переписки:
0026 г.Екатеринбург ая 244 Г.Н. Шаховой рег.№ 873
Зашейко Ирина Львовна (RU)
Кашин Виктор Васильевич (RU)
Константинов Андрей Евгеньевич (RU)
Обухов Владимир Михайлович (RU)
Путилин Александр Иванович (RU)
Танутров Игорь Николаевич (RU)
Шариков Валерий Михайлович (RU)
(73) Патентообладатель(и):
Открытое акционерное общество "Уралгипромез" (RU)
(54) СПОСОБ ОБРАБОТКИ ГЛИНОЗЕМИСТОГО ЦЕМЕНТА
Изобретение относится к области производства строительных материалов в частности к получению строительного раствора из глиноземистого цемента исходным сырьем которого является высокоглиноземистый шлак выплавляемый из боксита в доменных печах. Технический результат - снижение температуры обжига при высоком значении степени окисления серы. В способе обработки глиноземистого цемента предназначенного для получения строительного раствора при затворении водой путем его окислительного обжига указанному обжигу подвергают глиноземистый цемент с размером частиц 004-008 мм при температуре 800-890°С. Окислительный обжиг проводят во вращающейся трубчатой печи с внешним или внутренним обогревом. 2 з.п. ф-лы 4 табл.
(21) (22) Заявка: 200510614303 05.03.2005
(45) Опубликовано: 10.10.2006
поиске: SU 482411 А 30.08.1975. RU 2233813 C1 10.08.2004. SU 568610 A 02.11.1976. SU 316697 A 23.11.1971. JP 200015798 A 13.06.2000.
Абызов Александр Николаевич (RU)
Абызов Виктор Александрович (RU)
Абрамов Анатолий Кузьмич (RU)
Сотников Валерий Васильевич (RU)
Сотникова Дарья Демьяновна (RU)
Общество с ограниченной ответственностью НПП "КРОНА-СМ" (RU)
(54) ВЫСОКОГЛИНОЗЕМИСТОЕ ВЯЖУЩЕЕ
Изобретение относится к промышленности строительных материалов а именно к производству жаростойкого вяжущего и может быть использовано для приготовления жаростойких бетонов и изделий на их основе изготовления монолитных элементов футеровок тепловых агрегатов а также для приготовления огнеупорных растворов клеев и других смесей. Высокоглиноземистое вяжущее включающее глиноземистый цемент и тонкомолотую добавку на основе оксида алюминия в качестве тонкомолотой добавки содержит кислородсодержащее соединение алюминия общей формулы Al2O3·nH2O где n=003-20 полученное быстрой частичной дегидратацией гидроксида алюминия при следующем соотношении компонентов мас.%: глиноземистый цемент 55-90 указанное кислородсодержащее соединение алюминия 10-45. Технический результат - повышение огнеупорности температуры деформации под нагрузкой сохранение высокой активности набора марочной прочности в течение трех суток способность набора марочной прочности как в нормальных условиях так и при пропарке а также удешевление вяжущего расширение сырьевой базы при использовании отходов промышленности. 1 з.п. ф-лы 1 табл.
(12) ЗАЯВКА НА ИЗОБРЕТЕНИЕ
По данным на 13.05.2011 состояние делопроизводства: Нет данных
(21) (22) Заявка: 9304380702 03.09.1993
(43)публикации заявки: 20.07.1996
Акционерное общество закрытого типа "Белый Соболь
(54) СПОСОБ ПЕРЕРАБОТКИ КРАСНОГО ШЛАМА ГЛИНОЗЕМНОГО ПРОИЗВОДСТВА
(57) Формула изобретения
Способ относится к области металлургии и включает плавку красного шлама совместно с шлакообразующим веществом и углеродистым восстановителем выплавление чугуна и шлака. Отличается тем что в качестве шлакообразующего вещества и углеродистого восстановителя применяют колошниковую пыль доменного производства и бокситовую руду с кремневым модулем 2-5 при этом колошниковую пыль вводят из расчета полного восстановления оксидов железа бокситовую руду вводят из расчета получения силикатного модуля 008-035. Регулируют соотношение между оксидом кальция и оксидом кремния из расчета получения гидравлического модуля 055-080. Регулирование осуществляют добавкой кальцийсодержащего вещества например в виде оксида или фторида либо добавкой кремнийвосстанавливающего вещества например кальция или алюминия. В способе в начале расплавляют красный шлам затем добавляют боксит а затем колошниковую пыль. Полученный шлак перерабатывают на глиноземистый цемент либо на глинозем.
2 лист.cdw

План на отметке 8.500
Ленточный транспортер
Центробежная мельница
3 лист.cdw

происходящие при твердении
глиноземистого цемента