Производство биоэтанола из целлюлозосодержащего сырья



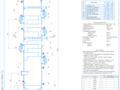
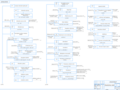
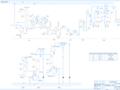
- Добавлен: 24.01.2023
- Размер: 2 MB
- Закачек: 0
Описание
Состав проекта
![]() |
![]() |
![]() ![]() ![]() ![]() |
![]() ![]() ![]() |
![]() ![]() ![]() |
![]() ![]() ![]() |
![]() ![]() ![]() |
![]() ![]() ![]() |
![]() |
![]() ![]() ![]() |
![]() ![]() ![]() ![]() |
![]() ![]() ![]() |
![]() ![]() ![]() |
![]() |
![]() ![]() ![]() |
![]() ![]() ![]() |
![]() ![]() ![]() |
![]() ![]() ![]() ![]() |
![]() |
![]() ![]() ![]() |
![]() ![]() ![]() |
Дополнительная информация
apparaturka.cdw

Розділ 5 (табл.5.2).docx
Назва виробничої дільниці лабораторії установки
Шкідливі речовини що виділяються причини їх виділення
Група шкідливої речовини характеристика шкідливого впливу
ГДК шкідливої речовини у повітрі робочої зони
Клас небезпечності шкідливої речовини
Засоби індивідуального захисту: тип марка ГОСТ
Засоби долікарніної допомоги
Методи контролю вмісту шкідливих речовин у повітрі робочої зони
Клас підприємства згідно з СН 245-71
Санітарна група виробничого процесу згідно зі СниП 2.09.04-87
Лабораторія вирощування дріжджів цех зброджування
Мікрофлора дріжджів та контамінуюча мікрофлора які можуть потрапляти у повітря при посіві або відкритті-закритті кришки бродильного чану
Біологічні викликають алергічні захворювання
ГОСТ 12.4.004-74; халат бавовняний ГОСТ 12.4.103-83
Антиале-ргічні препарати
Мікробіологічний аналіз
Цех приготування розчину сірчаної кислоти
Сірчана кислота порушення герметичності гідролізного апарату
Подразнюючі. Подразнення слизових оболонок очей органів дихання
Окуляри по ГОСТ 12.4.013-85 рука виці гумові по ГОСТ 3-88 марлева пов’язка
Промивання ураженого місця великою кількістю води. Нейтралізування малоконцентрованим розчином соди
Пари фурфуролу порушення герметичності нейтралізаторів
Загальноток-сичні. Викликають асфіксію отруєння всього організму порушення ЦНС
Респіратор «Пелюсток» ГОСТ 12.4.02.8
Постраждалого винести на свіже повітря. При відсутності дихання штучне дихання з рота в рот. При відсутності пульсу – непрямий масаж серця
Газоаналізатори ДАК з блоками БПС-21М та інші прилади
Вуглекислий газ порушення герметичності бродильних чанів
Загальнотоксичні. Отруєння всього організму
Промивання шлунку розчином марганцево- кислого калію
Датчики-газоаналізатори ДАК з блоками БПС-21М
Гашене вапно порушення герметичності нейтралізаторів
Промивання ураженого місця великою кількістю води. Нейтралізуваннямалоконцентрованим розчином оцтової кислоти
Датчики-газоаналізатори
Реферат.docx
В данному дипломному проекті розроблено технологію виробництва біоетанолу з целюлозовмісної сировини з метою отримання якісного та екологічно безпечного палива яке має високе октанове число і відповідає екологічним нормам. В проекті обгрунтовано вибір обладнання за допомогою яких здійснюють гідроліз зброджування та ректифікаційне очищення. Обрано та описано характеристики вихідної сировини та наведені вимоги до неї наведена і описана технологічна схема виробництва біоетанолу з целюлозовмісної сировини розраховано матеріальний баланс технології вказані точки і параметри контролю етапів процессу необхідні для забезпечення якості кінцевого продукту охорони праці та довкілля.
БОЕТАНОЛ ЦЕЛЮЛОЗОВМСНА СИРОВИНА ГДРОЛЗ СПИРТОВЕ БРОДННЯ ДРЖДЖ РЕКТИФКАЦЯ РЕКТИФКАЦЙНА КОЛОНА КОНТРОЛЬ МАТЕРАЛЬНИЙ БАЛАНС.
Explanatory note: 137 p. 27 fig. 17 tab. 91 references.
It was designed the project of technology for production of bioethanol from cellulose-containing raw material to obtain high-quality and ecologically safe fuel which has a high octane and comply with environmental standards.
It was explained the choice of equipment which is using for such processes as hydrolysis fermentation and distillation treatment in this project. It was described characteristics of the initial raw material and was listed the requirements for it. The technological scheme of production of bioethanol from cellulose-containing raw materials was listed and described. It was calculated the material balance of technology also were listed specific terms and parameters of controlling the process steps what is necessary to provide quality of the final product occupational health and preservation of environment.
It was show the technological calculation of the distillation column which has a perforated plate with a diameter 600 mm and a height 8950 m.
BIOETHANOL CELLULOSE-CONTAINING RAW MATERIAL HYDROLYSIS ALCOHOL FERMENTATION YEAST RECTIFICATION RECTIFICATION COLUMN CONTROL THE MATERIAL BALANCE.
Розділ 5.docx
Проект виконано з урахуванням вимог охорони праці пожежної та екологічної безпеки виробництва. На основі виявленого аналізу шкідливих і небезпечних факторів проектом передбачено заходи і засоби щодо забезпечення здорових безпечних умов праці та пожежної безпеки [76].
1. Виявлення та аналіз ШНВФ на проектному об’єкті. Заходи з охорони праці
1.1. Повітря робочої зони
Роботи що виконуються на дільниці згідно з ДСН 3.3.6.042-99 можна віднести до фізичних робіт середньої важкості категорії а. В таблиці 5.1 наведені санітарні норми параметрів мікроклімату для названих приміщень [77].
Оптимальний мікроклімат у приміщеннях [77]
У виробничих приміщеннях
Температура (взимкувлітку) °С
Вологість (взимкувлітку) %
Швидкість руху повітря мс
Допустима температура зовнішніх поверхонь обладнання становить:
де – оптимальна температура повітря робочої зони в теплий період року =27 [78].
Температуру повітря вимірюють термометрами з ціною поділки 02 ºС.
Заходами санітарних норм мікроклімату і належної чистоти повітря згідно вимог ДСН 3.3.6.042-99 забезпечено вдосконалення технологічних процесів та їх апаратурного оформлення шляхом розміщення деяких апаратів поза приміщеннями використання теплозахисної ізоляції апаратів та трубопроводів які є джерелом виділення теплової енергії. В холодну пору року передбачена система центрального водяного опалення низького тиску виробничих приміщень. Технологічний процес повністю автоматизований та забезпечується системами дистанційного управління.
Вибір схеми виробництва проводився з урахуванням зниження тепловиділення і зведення до мінімуму надходження шкідливих речовин у повітря робочі зони.
Для запобігання забруднення повітря виробничих приміщень проектом передбачено забезпечення герметичності ємностей обладнання комунікацій та засобів відбирання проб згідно ГОСТ 12.2.003 [77]. Як засіб видалення вологи із повітря приміщення використовується вентиляція.
Вимірюванням параметрів метеорологічних умов та їх порівнянням з нормами займаються санітарні лабораторії. Вимірювання та контроль проводяться по затвердженому графіку на певних виробничих ділянках у відповідності до загальних вимог ГОСТ 12.1-005-76.
В таблиці 5.2 наведена коротка санітарна характеристика цеху що проектується [79].
1.2. Проектування системи загальнообмінної припливної вентиляції
Для нормалізації параметрів мікроклімату виробничий цех передбачено обладнати загальнообмінною механічною вентиляцією згідно з СНиП 2.04.05 та ДСТУ Б А.3.2-12 [80]. Кратність повітрообміну виробничого приміщення становить 3 год-1.
Схема розташування обладнання загальнообмінної системи припливної вентиляції забражена на рисунку 5.1.
Рис.5.1. Схема розміщення обладнання систем припливної вентиляції кондиціонування повітря та повітряного опалення [80]:
-припливна установка установка повітряного опалення та кондиціонер; 2-приміщення з виробництвом категорії А Б або Е та приміщення 1-го та 2-го класів небезпеки; 3- приміщення з виробництвом категорії В; 4- приміщення з виробництвом категорії Г; 5-приміщення з виробництвом категорії Д; 6-допоміжне приміщення підприємства; 7-приміщення для вентиляційного обладнання; 8-самозакривний оборотній клапан; 9-підлога приміщення; 10-накриття; 11-перегородка.
Згідно з проектом вентиляційні прилади припливної системи вентиляції розміщені поза виробничими приміщеннями тобто в ізольованих приміщеннях та технічних поверхах. Передбачено також обслуговування вентиляційних установок з пересувних вишок. Обладнання систем припливної вентиляції виробничих приміщень розміщується в одному приміщення так як в ньому не відбувається рециркуляції повітря.
Фільтри для очистки від пилу повітря що подається в приміщення розміщені на початку процесу обробки повітря. На цьому етапі за необхідності також здійснюється підігрів повітря до необхідної нормованої температури [81].
Розрахунок повітрообміну потужності калорифера та робочого тиску проводиться для кожного приміщення окремо за формулою:
де L – необхідна продуктивність припливної вентиляції м3год; n=12 – 20 – нормована кратність повітрообміну для виробничого приміщення; S – площа приміщення м2; H – висота приміщення.
Висота виробничих приміщень становить H=3 м середня площа приміщення S= 50 м2 кратність повітрообміну приймаємо n=15 тоді:
Знаючи необхідний повітрообмін для забезпечення вентиляції виробничих приміщень обираємо вентилятори типу Breezart 2500 MC.
Потужність калорифера який використовується для підігріву зовнішнього повітря розраховують виходячи з продуктивності необхідної температури повітря на виході системи та мінімальної температури зовнішнього повітря. Температура повітря яке надходить у виробниче приміщення повинна бути не менше +18 ºС а мінімальна температура зовнішнього повітря залежить від кліматичної зони і для Києва становить –22 ºС.
Необхідна потужність калорифера розраховується за формулою:
де = 40 – різниця температур повітря на виході та вході системи припливної вентиляції ºС; Р – потужність калорифера Вт; L – продуктивність по повітрю м3год.
Знаючи необхідну потужність обираємо калорифери типу СФО-30 (ПНЕ-30).
Задля забезпечення компромісу між рівнем шуму необхідною продуктивністю вентилятора та діаметром повітропроводів використовуємо гнучкі повітропроводи з перетином 200х200 мм. Швидкість потоку повітря при цьому буде становити 25 – 4 мс що задовольняє нормам СНиП -33-75 [82].
1.3.Виробниче освітлення
Згідно з ДБН В.2.5.28-06 розряд робіт за зоровими умовами відноситься до VIIIа (загальне постійне спостереження за ходом виробничого процесу) [83].
Проектом передбачається у приміщенні виробничого цеху використовувати систему штучного комбінованого освітлення. Для освітлення виробничих приміщень передбачено використання люмінесцентних ламп ЛД-80. Передбачено використання вологонепроникних та вибухобезпечних закритих світильників ВЗГВ4А-200М переважно прямого світла. Передбачається система аварійного освітлення. Найменша освітленість робочих поверхонь при аварійному режимі повинна складати не менше 2 лк усередині будівель та не менше 1 лк на відкритих ділянках. Для аварійного освітлення проектом передбачаються лампи розжарювання Г 220-200 та
люмінесцентні лампи ЛХБ 80 [84].
За ДБН В.2.5-28-99 з урахуванням галузевих норм у таблиці 5.3 вказані норми освітлення приміщень робочим освітленням.
Санітарні норми освітленості при штучному освітленні та КПО при природному і суміщеному освітленні [84]
Характеристика зорової роботи
Штучне освітлення лк
Суміщене верхнє і бічне
Загальне спостереження за ходом виробничого процесу
1.4. Захист від виробничого шуму та вібрацій
Джерелами шуму та вібрації при виробництві біоетанолу є насоси вентилятори газодувки мішалки вентиляційні системи.
Згідно ДСН 3.3.6.037-99 санітарні норми параметрів шуму в приміщеннях і на території підприємства становлять 80 дБА [85]. Гранично допустимі рівні локальної непостійної переривчатої вібрації встановлені у ДСН 3.3.6.039-99 [86]. Для забезпечення допустимого рівня шуму та вібрації проектом передбачено наступні дії:
-витяжні системи обладнати глушниками шуму;
-віброізоляція насосних агрегатів;
-вентилятори закріпити на віброізолюючих пружинах всмоктуючі та напірні патрубки вентиляторів з’єднати з вентиляторними трубами м’якими вставками;
Для вимірювання і аналізу шуму і вібрації передбачені шумоміри ВШВ - 003 і частотні аналізатори [85].
Згідно з проектом електрообладнання виробничого цеху живиться від трьохфазної чотирьохпровідної електричної мережі змінного струму частотою 50 Гц напругою 380220 В з глухозаземленою нейтраллю.
Основними причинами ураження електричним струмом у цеху з виробничим обладнанням є випадковий дотик до відкритих струмопровідних частин обладнання які знаходяться під напругою або до частин що проводять електричний струм при порушенні електроізоляції також ураження кроковою напругою та через електричну дугу статична електрика.
Відповідно до ПУЕ приміщення виробничого цеху за небезпекою електротравм належить до категорії з підвищеною небезпекою.
Норми Uд Iл згідно ГОСТ 12.1.038-82при аварійному режимі:
л6 мА при дії довше 1с
де Uд–напруга дотику В; Iл– струм який проходить через людину мА.
При однофазному доторканні струм який проходить через людину буде дорівнювати:
де Uф=220 В – фазна напруга; Rл=2 кОм – опір людини; Rо=4 Ом – опір заземлення нейтралі. Тоді
Як видно з порівняння розрахункових та допустимих величин при порушенні вимог ПУЕ в цеху можливі електротравми з тяжкими наслідками [87].
Статична електрика виникає при терті газоподібних речовин при випусканні повітря чи газів з ресиверів.
Проектом передбачено такі основні засоби захисту від статичної електрики як відведення зарядів у землю за допомогою заземлення трубопроводів запобігання виникненню та накопиченню статичної електрики та її нейтралізації.
Все устаткування та комунікації захищено від статичної електрики згідно з ГОСТ 12.4.124 та ДНАОП 0.00-1.29. Для зменшення заряду статичної електрики передбачено підвищення вологості повітря до 70% напилення на діелектричній поверхні електропровідних плівок [88].
Безпека експлуатації електрообладнання досягається системою організаційних і технічних засобів які забезпечують безпеку в нормальному режимі роботи електроустановок та в аварійному їх стані. Серед них колективними засобами захисту є:
-електричне розділення мереж живлення;
-малі напруги (≤42 В);
До основних та додаткових засобів індивідуального захисту на підприємстві відносяться:
-діелектричні рукавички;
-діелектричне взуття [89].
1.6. Безпека технологічних процесів та обслуговування обладнання
Проектом передбачена комплексна механізація автоматизація та дистанційне управління технологічними процесами задля забезпечення безпеки технологічних процесів та обслуговування апаратів передбачено усунення безпосереднього контакту працюючих з шкідливими речовинами та герметизація обладнання.
Причинами виникнення аварії в цеху можуть бути потрапляння сторонніх продуктів в апарати зміна складу компонентів які подаються в вигляді суміші або розчину зміна витрат холодоагента чи теплоагента які подаються відповідно для охолодження чи нагріву. Для попередження виникнення аварійних ситуацій передбачено створення автоматичних систем захисту.
Виробничий процес виробництва біоетанолу здійснюється у відповідності з вимогами чинної нормативно-технічної документації затвердженої у встановленому порядку.
Тиск в трубопроводах температурний режим і рівень рідини в ректифікаційних колонах швидкість подачі стічних вод підтримується у відповідності з вимогами технологічного регламенту.
Проектом передбачено неможливість виконання робіт на несправному обладнанні при несправності контрольно-вимірювальних приладів захисних огороджень блокувань пристроїв електроустаткування пускової апаратури кнопок і важелів керування автоматичного блокування роботи обладнання.
Вимоги безпеки що стосуються будови виготовлення та експлуатації посудин що працюють під тиском відповідають представленим вимогам у ДНАОП 0.00-1.07–94 [90]. Ректифікаційні колони обладнані люками доступними для обслуговування апарату. Зварні шви виконуються тільки стиковими. Контроль якості зварних швів виконується за допомогою зовнішнього огляду та гідравлічно. Проектом передбачено встановлення ректифікаційних колон на відкритих майданчиках.
Вимоги до роботи з компресорним обладнанням відповідають ГОСТ 12.2.016-81 за яким безпечність такого обладнання забезпечується використанням змащувальних матеріалів при роботі з компресорами та їх охолодженням що передбачено проектом. Всі трубопроводи прокладені згідно з СНиП 1П-Г.9-62 надземно на рухомих опорах. Трубопроводи що транспортують біоетанол обладнані дренажними системами для відведення конденсату.
Будова та безпечна експлуатація трубопроводів пари та гарячої води відповідає вимогам НПАОП 40.3-1.11-98. В результаті виникаючих теплових навантажень у трубопроводах можливі розриви (при охолодженні) або випинання (при нагріванні) і відрив фланців. Тому на трубопроводах передбачено встановлення компенсуючих елементів. Відповідно до ГОСТ 14202-69 передбачено фарбування трубопроводу для подачі гарячої води зеленим кольором біоетанолу – жовтим розчину сірчаної кислоти – фіолетовим.
На обладнанні в небезпечних зонах ділянках виробництва частинах устаткування що рухаються проектом передбачено нанесення табличок на яких вказано найменування і порядковий номер відповідно до технологічної схеми [91].
Причинами загорання і вибуху на виробництві можуть бути:
-порушення герметичності бродильних чанів ректифікаційних колон та комунікацій;
-прямий удар блискавки або занесення її високого потенціалу у приміщення по видовжених елементах;
Для забезпечення пожежної безпеки передбачено виготовити вибухобезпечними згідно з ГОСТ 12.1.030 ГОСТ 12.1.018 та НПАОП 40.1-1.32 штучне освітлення електрокомунікації електричне обладнання та електричне устаткування. Для пожежогасіння передбачено застосовувати розпилену воду піну вогнегасні порошки класів В та АВС; під час об'ємного гасіння – вуглекислий газ вогнегасні порошки класів В та ABC а також аерозольні вогнегасні речовини.
Проектом передбачено наступні будівельні заходи пожежної безпеки: ступінь вогнестійкості будівлі – два запасних виходи з шириною дверних прорізів 06 м легкоскидні конструкції а саме одинарне засклення вікон.
Виробничий цех передбачено обладнати автоматичними дренчернимиустановками загального та локального пожежогасіння та пожежної сигналізації згідно з НАПБ Б.06.004.
Устаткування та комунікації передбачено захистити від статичної електрики згідно з ГОСТ 12.4.124 та ДНАОП 0.00-1.29. Для відведення заряду з рідкого продукту на завантажувальному трубопроводі безпосередньо біля входу в апарат що заповнюється передбачено обладнати індукційним нейтралізатором зі струнами.
Споруди і будівлі що віднесені заСН 305-77 до категорії по влаштуванню блискавкозахиступроектом передбачено захистити від блискавки шляхом встановлення подвійного стрижневого громовідводу висотою 138 м.
Нижче в таблиці 6.4 приведена характеристика пожежо- і вибухонебезпечних речовин які використовуються при виробництві біоетанолу [91].
Розділ 4.docx
1. Принцип роботи ректифікаційного колони
Зазвичай ректифікаційний апарат складається з двох частин: верхньої та нижньої кожна з яких являє собою організовану поверхню контакту фаз між парою і рідиною.
У нижній частині вихідна суміш взаємодіє з парою початковий склад якого дорівнює складу кубового залишку. Внаслідок цього із суміші витягується низькокиплячий компонент (НКК).
У верхній частині пара початкового складу що відповідає складу вихідної суміші взаємодіє з рідиною початковий склад якої дорівнює складу дистиляту. Внаслідок цього пар збагачується НКК до потрібної межі а висококиплячий компонент (ВКК) витягується з парової фази.
Пара для живлення ректифікаційної колони (РК) виходить багаторазовим випаровуванням рідини що має той же склад що і кубовий залишок а рідина – багаторазовою конденсацією пари що має склад однаковий за складом дистиляту.
Отриманий конденсат ділиться на дві частини. Одна частина спрямовується назад в колону – флегма інша є відібраним продуктом – дистилят. Відношення кількості повернутого в колону дистиляту (флегми) до кількості дистиляту відібраного у вигляді продукту – називається флегмовим числом R [63].
У ректифікаційному апараті знизу вгору рухаються пари а зверху подається рідина що представляє собою майже чистий НКК. При зіткненні парів що піднімаються зі стікаючою рідиною відбувається часткова конденсація парів і часткове випаровування рідини. При цьому з пари
конденсується переважно ВКК а з рідини випаровується переважно НКК. Таким чином стікаюча рідина збагачується ВКК а пари що піднімаються збагачуються НКК в результаті чого пари які виходять з апарату являють собою майже чистий НКК. Ці пари надходять у конденсатор званий дефлегматором і конденсуються. Частина конденсату що повертається на зрошення апарату називається флегмою інша частина відводиться в якості дистиляту.
Як і для всіх масообмінних апаратів ефективність процесів ректифікації залежить від поверхні контакту фаз. Для збільшення поверхні массобміну використовують різні контактні пристрої насадочного або барботажного типу [64].
2. Класифікація ректифікаційних установок по конструкції внутрішнього влаштування апарату
У промисловості застосовують ковпачкові сітчасті насадкові плівкові трубчасті колони і відцентрові плівкові ректифікатори. Вони розрізняються в основному конструкцією внутрішнього устрою апарату призначення якого – забезпечення взаємодії рідини і пари. Ця взаємодія відбувається при барботуванні пари через шар рідини на тарілках (ковпачкових або сітчастих) або при поверхневому контакті пари і рідини на насадці або поверхні рідини що стікає тонкою плівкою.
Тарілчасті ковпачкові колони найбільш часто застосовують у ректифікаційних установках. Пари з попередньої тарілки потрапляють в парові патрубки ковпачків і барботують через шар рідини у яку частково занурені ковпачки. Ковпачки мають отвори або зубчасті прорізи які розбивають пару на дрібні струмки для збільшення поверхні стикання її з рідиною. Переливні трубки служать для підведення і відведення рідини і регулювання її рівня на тарілці. Основною областю масообміну і теплообміну між парами і рідиною як показали дослідження є шар піни та бризок над тарілкою що створюється в результаті барботажу пари. Висота цього шару залежить від розмірів ковпачків глибини їх занурення швидкості пари товщини шару рідини на тарілці фізичних властивостей рідини тощо. Слід зазначити що крім ковпачкових тарілок застосовують також клапанні жолобчасті S-подібні лускаті провальні та інші конструкції тарілок. У розрахунках необхідно враховувати особливості конструкцій тарілок.
Клапанні тарілки показали високу ефективність при значних інтервалах навантажень завдяки можливості саморегулювання. В залежності від навантаження клапан переміщується вертикально змінюючи площу живого перетину для проходу пари причому максимальний перетин визначається висотою пристрої що обмежує підйом. Площа живого перерізу отворів для пари становить 10 – 15% площі перерізу колони. Швидкість пари досягає 12 мс. Клапани виготовляють у вигляді пластин круглого або прямокутного перерізу з верхнім або нижнім обмежувачем підйому.
Тарілки зібрані з S-подібних елементів забезпечують рух пари і рідини в одному напрямку сприяючи вирівнюванню концентрації рідини на тарілці.
Лускаті тарілки подають пару в напрямку потоку рідини. Вони працюють найбільш ефективно при струминному режимі що виникає при швидкості пари в лусках понад 12 мс. Площа живого перерізу становить 10% площі перерізу колони. Луски бувають арочними і пелюстковими; їх розташовують на тарілці в шаховому порядку. Простота конструкції ефективність і велика продуктивність – переваги цих тарілок.
Пластинчасті тарілки зібрані з окремих пластин розташованих під кутом 4 – 9° до горизонту. У зазорах між пластинами проходить пар зі швидкістю 20 – 50 мс. Над пластинами встановлені відбійні щитки які зменшують винос бризок. Ці тарілки відрізняються великою продуктивністю малим опором і простотою конструкції.
До провальних відносять тарілки гратчасті колосникові трубчасті сітчасті (плоскі або хвилясті без зливних пристроїв). Площа живого перерізу тарілок змінюється в межах 15 – 30%. Рідина і пара проходять поперемінно через кожен отвір у залежності від співвідношення їх напорів. Тарілки мають малий опір високий ККД працюють при значних навантаженнях і відрізняються простотою конструкції.
Насадкові колони отримали широке поширення в промисловості. Вони являють собою циліндричні апарати заповнені інертними матеріалами у вигляді шматків певного розміру або насадочными тілами що мають форму наприклад кілець кульок для збільшення поверхні фазового контакту та інтенсифікації перемішування рідкої і парової фаз. Масо- і теплообмін в колонах з насадкою характеризуються не тільки явищами молекулярної дифузії що визначаються фізичними властивостями фаз але і гідродинамічними умовами роботи колони які визначають турбулентність потоків: ламінарний проміжний і турбулентний при яких потік пари є суцільним неперервним і заповнює вільний об'єм насадки не зайнята рідиною в той час як рідина стікає лише по поверхні насадки. Подальший розвиток турбулентного руху може призвести до подолання сил поверхневого натягу і порушення граничної поверхні між потоками рідини і пари. При цьому газові вихри проникають в потік рідини відбувається емульгування рідини парою і масообмін між фазами різко зростає. У разі емульгування рідина розподіляється не на насадці а заповнює весь її вільний об'єм не зайнятий парою; рідина утворює суцільну фазу а газ – дисперсну фазу розподілену в рідині тобто відбувається інверсія фаз. Насадокову колону слід розраховувати виходячи з оптимальної швидкості. При перевищенні оптимальної швидкості починається обернений рух рідини знизу вгору відбувається так зване “захлинання” колони та порушення режиму її роботи.
Трубчасті плівкові ректифікаційні колони складаються з пучка вертикальних труб по внутрішній поверхні яких тонкою плівкою стікає рідина взаємодіючи з парою яка піднімається по трубам. Пара надходить з куба в трубки. Флегма утворюється в дефлегматорі безпосередньо на внутрішній поверхні трубок охолоджуваних водою у верхній їх частині. Діаметр застосовуваних трубок – 5 – 20мм. Ефект роботи плівкового апарату зростає зі зменшенням діаметра трубок. Трубчасті колони характеризуються простотою виготовлення високими коефіцієнтами масопередачі і дуже малими гідравлічними опорами руху пари. Багатотрубні (і довготрубні) колони з штучним зрошенням мають значно менші габаритні розміри і масу ніж тарілчасті.
Сітчасті колони застосовують головним чином при ректифікації спирту та рідкого повітря. Допустимі навантаження по рідини і парі для них відносно невеликі і регулювання режиму їх роботи ускладнене. Масо- та теплообмін між парою і рідиною в основному відбуваються на деякій відстані від дна тарілки в шарі піни та бризок. Тиск і швидкість пари що проходить через отвори сітки повинні бути достатні для подолання тиску шару рідини на тарілці і створення опору її набряканню через отвори. Сітчасті тарілки необхідно встановлювати строго горизонтально для забезпечення проходження пари через всі отвори тарілки а також щоб уникнути стікання рідини через них. Зазвичай діаметр отворів сітчастої тарілки приймають в межах 08 – 30мм [65].
3. Вибір ректифікаційної колони
В ректифікаційних колонах застосовуються сотні різних конструкцій контактних пристроїв які істотно різняться за своїми характеристиками і техніко-економічними показниками. При цьому в експлуатації знаходяться поряд з найсучаснішими конструкціями контактні пристрої таких типів (наприклад жолобчасті тарілки та ін) які хоча і забезпечують отримання цільових продуктів але не можуть бути рекомендовані для сучасних і перспективних виробництв.
Найбільш поширеними ректифікаційними установками є барботажні колони з різними типами тарілок: ковпачковими сітчастими провальними тощо. Добре зарекомендували себе апарати з сітчастими тарілками що відрізняються простотою конструкції і легкістю в обслуговуванні.
При виборі типу контактних пристроїв зазвичай керуються наступними основними показниками:
б) гідравлічним опором;
в) коефіцієнтом корисної дії;
г) діапазоном робочих навантажень;
д)можливістю роботи на середовищах схильних до утворення смолистих чи інших відкладень;
е) матеріаломісткістю [66].
Сітчасті тарілки з відбійниками мають відносно низький гідравлічний опір підвищену продуктивність але більш вузький робочий діапазон порівняно з ковпачковими тарілками. Застосовуються переважно у вакуумних колонах.
Кращі показники по гідравлічному опору мають тарілки сітчасті і S-подібні з клапанами а по ККД – клапанна баластна і S-подібна з клапаном.
Слід зазначити що універсальних конструкцій тарілок ефективно працюючих «завжди і скрізь» не існує. При виборі конкретного типу тарілок з безлічі варіантів слід віддати перевагу тій конструкції основні (не обов'язково всі) показники ефективності якої в найбільшій мірі задовольняють вимогам що пред'являються. Переважно застосування контактних пристроїв що мають якомога менший гідравлічний опір [67].
3.1. Колони з сітчастими тарілками для розділення суміші «етиловий спирт-вода»
Колони з сітчастими тарілками набагато простіше по влаштуванню і дешевше ніж наприклад колони з ковпачковими тарілками. Колони з сітчастими тарілками (рис.4.1) складаються з вертикального циліндричного корпусу 1 з горизонтальними тарілками 2 в яких рівномірно по всій поверхні просвердлено значне число дрібних отворів. Для зливу рідини і регулювання її рівня на тарілці є переливні трубки 3. Нижні кінці трубок занурені у стакани 4 що знаходяться на тарілках що лежать нижче і утворюють гідравлічні затвори.
Рис.4.1. Схема будови сітчастої колони [68]:
– корпус; 2 – сітчаста тарілка; 3 – переливна трубка; 4 – стакан
Газ (пара) проходить в отвори тарілки (рис.4.2) і розподіляється в рідині у вигляді дрібних струмків; лише на деякій відстані від дна тарілки утворюється шар піни та бризок – основна область масообміну і теплообміну на тарілці.
Рис.4.2. Схема роботи сітчастої тарілки [68]
В певному діапазоні навантажень сітчасті тарілки володіють досить великою ефективністю. Для того щоб ККД тарілки не різко зменшувався тиск і швидкість газу (пари) що проходить через отвори тарілки повинні бути достатніми для того щоб подолати тиск шару рідини на тарілці і запобігти тим самим стіканню рідини через отвори.
Крім того протікання рідини через отвори збільшується із збільшенням діаметру тарілки і при відхиленні від строго горизонтального положення. Тому діаметр і число отворів слід підбирати такими щоб рідина утримувалася на тарілках і не захоплювалася механічно парою. Зазвичай приймають діаметр отворів сітчастих тарілок 08 – 3мм.
Очищення промивка та ремонт сітчастих тарілок проводяться відносно зручно і легко.
Але є й мінуси. Сітчасті колони ефективно працюють тільки при певних швидкостях ректифікації і регулювання режиму їх роботи. При значних навантаженнях втрата напору досить велика. Крім того як зазначалося раніше тарілки повинні бути розташовані строго горизонтально тому що інакше газ (пара) буде проходити через частину отворів не стикаючись з рідиною. А в разі раптового припинення надходження газу (пара) або значного зниження його тиску тарілки сітчастої колони повністю звільняються від рідини і для досягнення заданого режиму процесу потрібно знову пустити колону.
Чутливість до коливань навантаження а також забруднень і опадів які швидко забивають отвори тарілки обмежують область використання сітчастих колон. Але для ректифікації спирту та рідкого повітря (кисневі установки) головним чином застосовують саме їх.
Для підвищення ефективностісітчастих тарілок збільшують тривалість контакту між рідиною і газом (паром) наприклад примусовим круговим рухом рідини на тарілці при однаковому напрямку її руху на всіх тарілках колони [68].
3.2. Вибір допоміжного обладнання і конструкційного матеріалу
Розміри і конструкції перегонного куба дефлегматора і кінцевого холодильника залежать від продуктивності установки фізичних властивостей суміші що переганяється і режиму процесу (періодичний або неперервний).
Дефлегматор зазвичай являє собою кожухотрубний теплообмінник. У ряді випадків в дефлегматорі відбувається конденсація всіх парів що вийшли з колони. В кінцевому холодильнику дистилят охолоджується до заданої температури.
ноді в дефлегматорі конденсується лише частина парів для отримання флегми а повна конденсація і охолодження відбуваються в холодильнику.
Ректифікаційні установки забезпечують також приладами для регулювання і контролю режиму роботи і нерідко апаратами для утилізації тепла.
Етанол і вода не є корозійно-активними речовинами робоча температура в колоні не вище 100°С тому в якості конструкційного матеріалу для основних деталей апарату вибираємо сталь Ст3 ГОСТ380-94 яка використовується для виготовлення деталей хімічної апаратури при роботі з неагресивними середовищами при температурах від 10 до 200 °С [69].
4. Технічна характеристика
Апарат призначений для розділення суміші етиловий спирт – вода
концентрацією 10% (мол.);
Номінальний діаметр:490 мм;
Виробнича потужність:083 кгс;
Тиск у колоні:01 МПа;
Температура середовища:
- вихідної суміші:8650 0С
- дистиляту:7840 0С;
- кубового залишку:97400С;
Середовище в апараті: нетоксичне корозійне;
Тип тарілок:ситчасті;
5. Технологічні розрахунки
5.1. Матеріальний розрахунок колони
Температури кипіння та молекулярні маси компонентів що розділяються
Молекулярні маси вихідної суміші дистиляту і кубового залишку:
де хF= 10 %(мол.) – вміст НКК (етанолу) у вихідній суміші; –молярні маси етанолу і води відповідно (табл.4.1).
Аналогічно для MD та MW:
де хD= 75 % (мол.) – вміст НКК в дистиляті; xW= 1% (мол.) – вміст НКК в кубовому залишку.
Матеріальний баланс ректифікаційної колони неперервної дії описується за допомогою рівнянь [70]:
які можна об’єднати у систему.
В даних рівняннях GF GD GW – масові або мольні витрати суміші при надходженні дистиляту та кубовому залишку;хF xD xW – вміст низькокиплячого компоненту (етилового спирту) у суміші при надходженні дистиляті та кубовому залишку.
Перед тим як знаходити витрату дистиляту і кубової рідини переведемо мольні долі компонентів суміші в масові:
Розрахунок оптимального флегмового числа та знаходження числа теоретичних тарілок.
Будуємо діаграму рівноваги між парою та рідиною в системі етиловий спирт-вода (рис.4.3) використовуючи данні по рівновазі (табл.4.2).
Рівноважні дані системи етиловий спирт-вода[70]
Тоді мінімальне флегмове число:
Робоче число флегми:
Побудуємо за отриманим значенням R робочі лініїта ступені зміни концентрацій(кількість тарілок на ній). Для цього згідно до методики [45 відкладемо на осі у значення В:
Отримане значення з’єднаємо із точкою А яка відповідає концентрації хD. з точки перетину даної лінії із значенням концентрації вихідної суміші (С) опустимо лінію до точки (D) яка відповідає значенню концентрації кубового залишку. По отриманим робочим лініями визначимо число теоретично необхідних тарілок.
Рис.4.3. Х-Y-діаграма. Залежність між рівноважними та робочими складами фаз для суміші етиловий спирт-вода [70]
Виконавши на діаграмі (рис.4.3) побудову ламаної лінії знаходимо необхідне число ступенів зміни концентрації: в верхній частині воно складає ~ 6 в нижній ~ 3; всього – 9.
Розрахунок витрат пари у верхній та нижній частині колони.
Знайдемо рівняння робочих ліній:
а) для верхньої частини колони:
б) для нижньої частини колони:
де f – відносна мольна витрата живлення.
Середні молярні маси пари:
Масові витрати рідини у верхній та нижній частині колони.
Середні концентрації рідини:
Середні молярні маси рідини:
Розрахунок діаметра ректифікаційної колони
Знаходимо температури для нижньої та верхньої частини колони для рідини і пари з таблиці «Залежність температури від рівноважних складів пари та рідини» (табл.4.3).
Тоді температура для верхньої та нижньої частини колони для рідини становить:
Залежність температури від рівноважних складів пари та рідини [70]
Знайдемо середні густини пари у верхній та нижній частинах колони:
де і – середні температури пари що знаходяться по значеннямуср.в та уср.н.
Густини рідини у верхній і нижній частинах колони знаходять за формулою:
де - густини легколетючого та важколетючого компонентів при відповідних температурах (табл.4.4) кгм3.
Густини легколеткого та важколеткого компонентів при відповідних температурах [71]
Розрахунок швидкості пари в колоні.
Швидкість пари у верхній частині колони:
де С= 0059 (при відстані між тарілками 400 мм) – коеффіцієнт що залежить від конструкції тарілок відстані між ними робочого тиску в колоні навантаження колони по рідині (рис.4.4).
Рис.4.4. Значення коефіцієнта С [71]:
А Б – для ковпачкових тарілок з круглими ковпачками; В – для ситчастих тарілок
Швидкість пари в нижній частині колони:
Розрахунок діаметру колони.
Так як швидкості и мало відрізняються одна від одної в розрахунках використовуємо середню швидкість парів:
Приймаємо середній потік пари в колоні G:
Середня густина в колоні:
Орієнтовний діаметр колони визначаємо з рівняння витрат:
Приймаємо стандартний апарат з діаметром 600 мм [45] і уточнюємо робочу швидкість:
Характеристика тарілки.
По каталогу [45] для колони діаметром 600 мм обираємоситчасті тарілки типу ТС (ОСТ 26-01-108-85) (рис.4.3):
Виконання I – нерозбірне;
Діаметр тарілки – 58000 мм (рис.5.4);
Висота тарілки – 40мм;
Вільний перетин колони – 028 м2;
Робочий перетин тарілки – 0165 м2;
Вільний перетин тарілки – 051 м2;
Відносний вільний перетин тарілки (при dотворів=5 мм) – 723%;
Крок між отворами приймаємо 13 мм;
Периметр зливу – 0570м;
Перетин переливу – 00012 м2;
Відносна площа переливу – 41%;
Рис.4.5. Ситчата тарілка типу ТС [72]
Рис.4.6. Основа тарілки по ОСТ 26-01-108-85 [72]
5.3. Розрахунок числа тарілок
В’язкість рідини на тарілці:
де – в’язкість етанолу;
Звідси в’язкість рідини буде:
Коеффіцієнт відносної летючості:
де = 1120 мм рт.ст. – тиск насиченої пари етанолу;
= 525 мм рт.ст. – тиск насиченої пари води.
По діаграмі для наближеного визначення ККД тарілки (рис.4.7) знаходимо значення =051.
Рис.4.7. Діаграма для наближеного визначення ККД тарілки [73]
в верхній частині колони
в нижній частині колони
5.4. Розрахунок висоти колони
Приймаємо відстань між тарілками Нт=250 мм тоді висота верхньої та нижньої частини складає:
Товщина тарілки – 004 м;
Висота сепараційноо простору– 07 м;
Висота кубового простору – 23 м;
Висота опори – 12 м.
Загальна висота колони:
5.5. Гідравлічний розрахунок колони
Гідравлічний опір сухої тарілкивизначається за формулою:
Рс = wп2п (22) (4.49)
де = 00723 – відносний вільний перетин тарілки;
= 15 – коефіцієнт опору тарілки(табл.5.5)
Значення коефіцієнтів опору сухих тарілок різних конструкцій [73]
Провальна з щілиноподібними отворами
для нижньої частини колони
для верхньої частини колони
Гідравлічний опір обумовлений силами поверхневого натягувизначається за формулами:
де = 0017 Нм – поверхневий натяг етанолу;
= 0059 Нм – поверхневий натяг води.
де dэ = 0005 м – діаметр отворів.
Гідравлічний опір газорідинного шару визначається за формулою:
де h0 – висота освітленого шару рідини на тарілці.
Висота визначається як:
нижня частина колони
верхня частина колони
де – питома витрата рідини;
П = 057 м – периметр зливного пристрою;
hП = 003 м – висота зливного порогу;
wт = wпSкSт – швидкість пари віднесена до робочої площі тарілок;
в = 0059 Нм – поверхневий натяг води;
m= 005 – 46hп = 005 – 46003 = –0088 – показник степені.
Знаючи висоту обчислимо опір:
Повний опір тарілки визначається за формулою:
Р = Рс + Р + Ргр (4.59)
Рн =2381 + 304 + 1640 = 4325 Па (4.60)
Рв = 2493 + 304 + 1318 = 4115 Па (4.61)
Сумарний гідравлічний опір робочої частини колони:
Рк = 43256 + 411512 =7533 Па (4.62)
5.6. Тепловий розрахунок колони
Витрата теплоти що віддається воді в дефлегматорі.
де rр – теплота конденсації флегми
де rВ = 2500 кДжкг –теплота конденсації води;
rА = 882 кДжкг – теплота конденсації етанолу.
В якості холодоагента приймаємо воду з початковою температурою 20°С і кінцевою 30°С. Тоді середня різниця температур складе (температуру дистиляту tD =7840°C знаходимо з таблиці):
tб =784 – 200 = 584 С (4.65)
tм = 784 – 300 = 484С (4.66)
tcр = (tб + tм)2 = (584 + 484)2 = 534 С (4.67)
Орієнтовне значення коефіцієнта теплопередачі: К = 400 Вт(м2К).
Тоді необхідна поверхня теплообміну:
F = QД(Ktср) = 50709 103(400534) = 237 м2 (4.68)
Приймаємо стандартний кожухотрубний конденсатор з діаметром кожуха 400 мм і довжиною труб 3 м для якого поверхня теплообміну рівна 24 м2.
Витрата охолоджуючої води:
Витрата теплоти в кубі випарнику.
де сD– теплоємність дистилляту кДж(кгК);
сw– теплоємність кубового залишку кДж(кгК);
сF– теплоємність вихідної суміші кДж(кгК);
3 – коефіцієнт що враховує втрати в навколишнє середовище.
Теплоємність дистиляту знаходять по формулі:
де сА – теплоємність етилового спирту кДж(кг °C);
сВ – теплоємність води кДж(кг °C)
Аналогічно розраховуємо теплоємності вихідної суміші та кубового залишку:
Тоді витрата теплоти у кубі випарнику буде становити:
Витрата гріючої пари
Приймаємо пару з тиском 03МПа для якого теплота конденсаціїr = 2171 кДжкг тоді:
Gп = Qкr= 1137982171 = 052 кгc. (4.75)
Середня різниця температур у випарнику:
tср = tп – tw = 167 – 976 = 694 C (4.76)
Орієнтовне значення коефіцієнта теплопередачіК = 300 Вт(м2К) тоді необхідна площа теплообміну:
F = Qк(Ktср) = 113798103(300694) = 5466 м2 (4.77)
Приймаємо стандартний кожухотрубний теплообмінник з діаметром кожуха 600 мм та довжиною труб 4 м для якого поверхня теплообміну рівна 63 м2 [74].
5.7. Конструктивний розрахунок
Корпус колони діаметром до 1000 мм виготовляють з окремих царг (додаток Б) що з’єднуються між собою за допомогою фланців.
де р=01 МПа – тиск в колоні;
[]=138 МПа – допистиме навантаження для сталі;
φ= 08 – коефіцієнт послаблення зварного шва;
с=0001 – поправка на корозію.
Приймаємо товщину обечайки s=8мм.
Найбільшого розповсюдження в хімічному машинобудуванні отримали еліптичні відбортовані днища по ГОСТ 6533 – 78 (рис.4.8). Товщину стінки днища приймаємо рівною товщині обечайки: sд = s = 8 мм.
Рис.4.8. Днище колони [74]
Характеристика днища:
h = 40 мм – висота борта днища;
маса днища mд = 169 кг;
об'єм днища Vд = 0086 м3.
З’єднання обечайки з днищами здійснюється за допомогою плоских приварних фланців по ОСТ 26–428–79.
Приєднання трубопроводів до апарату відбувається за допомогою штуцерів.
Діаметр штуцерів визначається як:
де wшт – швидкість середовища в штуцері.
Приймаємо швидкість рідини wшт=1 мс газової суміші wшт=25 мс.
Густини компонентів при різних температурах кгм3 [74]
Штуцер для входу вихідної суміші:
приймаємо d1 = d2 = 40 мм.
Штуцер для входу флегми:
приймаємо d3 = 20 мм.
Штуцер для виходу кубового залишку:
приймаємо d4 = 300 мм.
Штуцер для виходу парів:
приймаємо d5 = 700 мм.
Штуцер для входу парів:
приймаємо d4 = 700 мм.
Усі штуцери повинні бути забезпечені плоскими приварними фланцями по ГОСТ 12820-80. Конструкція фланця приводиться на рис.4.9 а розміри вказані в таблиці 4.7.
Рис.4.9. Фланець штуцера [75]
Розміри приварного фланця штуцера [75]
Апарати вертикального типу з співвідношенням НD> 5 що розмішуються на відкритих майданчиках оснащують так званими юбочними циліндричними опорами конструкція яких приводиться на рис.4.10.
Рис.4.10. Опора юбочна [75]
Орієнтовна маса апарату
де m = 160 кг – маса однієї тарілки.
Загальна маса колони
Приймаємо що маса допоміжних пристроїв (штуцерів вимірювальних приладів люків тощо) складає 10% від основної маси колони тоді:
Маса води при гідровипробуванні:
Максимальна вага колони:
Приймаємо внутрішній діаметр опорного кільця D1 = 055 м зовнішній діаметр кільця 080 м.
Площа опорного кільця:
Питоме навантаження опори на фундамент:
– для бетонного фундаменту [47].
Отже на основі матеріального розрахунку розраховані матеріальні потоки в колоні та визначений діаметр ректифікаційної колони – 600 мм. Знайдено оптимальне флегмове число R = 148. Розраховане дійсне число тарілок: 6 в верхній частині колони та 12 в нижній. На основі теплового розрахунку було обрано дефлегматор (діаметр кожуха 400 мм довжина труб 3 м поверхня теплообміну 24 м2) та випарник (діаметр кожуха 600 мм довжина труб 4 м поверхня теплообміну 63 м2) визначено витрату охолоджуючої води та гріючої пари. Проведено конструктивний розрахунок та підібрані нормалізовані конструктивні елементи.
Розділ 1.docx
1. Характеристика целюлозовмісної сировини
Загальна площа лісів на земній кулі становить 3620 млн. га. Світові запаси деревини в усьому світі складають 359 млрд. м3. Заготівля деревини в усіх країнах світу становить більше 3 млрд. м3. При заготівлі деревини в залежності від типів застосовуваних рубок вихід ділової деревини складає 50 – 85 % дров'яної 10 – 25 % і лісосічних відходів 15 – 20 % від деревної біомаси. Приблизно 30 % від заготовленої деревини використовується в народному господарстві без переробки інша частина направляється на лісо-та шпалорозпил в фанерне сірникове і тарне виробництво на отримання деревоволокнистих і деревостружкових плит в целюлозно-паперову гідролізну та лісохімічну промисловость. Хімічними методами переробляють близько 15 % заготовленої деревини [1].
При сучасних обсягах лісозаготівель і переробки деревини щорічно утворюється близько 100 млн. м3 відходів деревини. Використовується щорічно 30 млн. м3 деревних відходів. На розпилювання направляється більше 30 % від загальної кількості заготовленої ділової деревини. Загальний вихід відходів в деревообробці залежить від породи сортності розмірів і вологості пиломатеріалів характеру готових виробів і дорівнює 20 – 85 % від обсягу пиломатеріалів [2].
На гідролізних заводах переробляється щорічно близько 7 млн. м3 деревини в тому числі приблизно 80 % деревних відходів і близько 20 % дров. На частку хвойної сировини припадає приблизно 60 % від загального споживання деревини. На нових гідролізних підприємствах великої
виробничої потужності в якості основної сировини використовується щепа одержувана при подрібненні деревини листяних порід – берези та осики.
Рослинна сировина яка використовується для гідролізу в спирт повинна задовольняти певним вимогам. Для виробництва біоетанолу сировина повинна містити максимальну кількість гексозанів (наприклад деревина хвойних порід).
ншою вимогою до сировини є її дешевизна. З цієї причини на гідролізних заводах використовують у першу чергу відходи лісопилки деревообробки а також відходи переробки сільськогосподарської сировини. Для використання цих відходів у якості гідролізної сировини необхідна наявність їх у достатній кількості на обмеженій території з тим щоб транспортні витрати на перевезення сировини до заводу були мінімальними. Постачання цією сировиною заводу повинно бути розраховано на десятки років тобто на весь період експлуатації підприємства [3].
Найбільш цінною целюлозовмісної сировиною для виробництва біоетанолу є подрібнені відходи деревини: дрібна стружка тирса тріска. В найбільших кількостях вони отримуються на лісопильних заводах при розпилі колод на дошки та бруски. Вихід дощок з колод зазвичай складає близько 64 – 66 % по об’єму кількість відходів – 35 % з них 10 % тирси і 25% рейок та обаполів. Останні перед відправкою на стадію гідролізу подрібнюються в дробарках на тріску певного розміру. По технічним умовам така тріска повинна мати товщину до 5 мм та довжину вздовж волокон до 35 мм.
Подрібнена деревина що надходить на гідроліз повинна мати не менше
% мінеральних домішок (пил пісок) не більше 6 % гнилі і не більше 12 % кори. Оскільки присутність кори знижує загальний вміст полісахаридів в сировині її вміст повинен бути мінімальним. Тому бажано колоди перед розпилом окорювати у лісі при заготовці або на лісопильному заводі перед постачанням на лісопильну раму. Останнім часом в лісопилці з'явився новий прогресивний метод заснований на переробці попередньо окорених колод. Колоди проходять через спеціальну дробарку яка подрібнює в технологічну тріску бічні частини колод і надає їм форму чотирикутного бруса. Останній потім надходить на лісопильну раму де розпилюється на дошки необхідних кондицій. Рейки і обаполки при новому способі розпилювання не утворюються так як ця частина деревини відразу перетворюється на технологічну тріску. Вихід тирси в цьому випадку скорочується до 5% [4].
На деяких гідролізних заводах особливо таких які переробляють листяну деревину частина сировини надходить на біржу у вигляді дров. Звідси дрова в міру необхідності подаються за допомогою транспортерів в дробарки де вони перетворюються в технологічну тріску. Серйозним недоліком цього виду сировини є його підвищена вартість високі експлуатаційні витрати з обслуговування біржі особливо в зимовий час а також високий вміст кори що досягає 10 – 15 %. Ще більш високий вміст кори спостерігається в трісках отриманої з лісосічних відходів. Цим пояснюється знижений вміст в них полісахаридів.
Деревна стружка (з деревообробних заводів) використовується обмежено завжди в суміші з тирсою або тріскою через її невелику щільність. Відходи фанерної і меблевої промисловості що складаються з шматків деревини або шпону склеєних фенолформальдегідними смолами не рекомендуються для переробки на гідролізних заводах що використовують мікробіологічні процеси.
На гідролізних заводах з успіхом використовується дубова тріска з заводів дубильних екстрактів і соснова тріска з каніфольно-екстракційних заводів.
Вологість тріски і тирси з лісопильних заводів коливається від 40 до 57% з деревообробних і каніфольно-екстракційних заводів - від 10 до 20%. Хімічниий склад абсолютно сухої деревини вказаний у таблиці 1.1 [5].
Хімічний склад абсолютно сухої деревини [5]
Щільність клітинних стінок абсолютно сухої деревини коливається від 149 до 157 гсм3. Теплоємність її дорівнює 032 калл (г°С). Маса 1 м3 деревини в перерахунку на абсолютно суху речовину залежить від породи дерева і умов його зростання і становить у середньому для сосни 460 кг модрини 520 кг ялини 395 кг берези 570 кг осики 450 кг. Маса абсолютно сухої речовини 1 кг круглих лісоматеріалів у штабелі в середньому становить 07 від маси щільної деревини [6].
Як вказувалося вище в якості сировини для гідролізного виробництва біоетанолу використовуються також різні рослинні відходи сільськогосподарського походження. До них відноситься: бавовняне лушпиння кукурудзяний качан соняшникове лушпиння вівсяне і рисове лушпиння тощо. ноді використовується очерет. Потенційною сировиною може бути також верхівковий торф (ступінь процесів розкладу до 15 %) і стебла бавовнику або гузапая.
З відходів сільськогосподарської сировини найбільший інтерес для гідролізний промисловості представляють: бавовняне лушпиння кукурудзяний качан і соняшникове лушпиння. Бавовняне лушпиння являє собою тверду оболонку насіння бавовнику покриту короткими волокнами бавовни. Вона є відходом бавовноочисних і маслоробних заводів. Вихід її становить 40-45% від маси насіння. Довжина їх 15 - 30 мм ширина 6-20 мм насипна питома маса 012. Бавовняні насіння зовні покриті волокнами бавовни. Довгі волокна відокремлюються від насіння і йдуть на текстильні підприємства. При цьому на насінні залишається деяка кількість коротко волокнистого хлопка який іноді відділяється на делінтеровочних машинах утворюючи лінтер і ще більш короткі волокна – делінт.
Звільнені від волокон насіння розколюють їх оболонка утворює бавовняне лушпиння а ядро йде на віджим бавовняного масла. Залежно від способу відділення волокон в лушпинні насіння міститься від 12 до 31% (за масою) коротких волокон. Зазвичай бавовняне лушпиння містить на своїй поверхні лінтер. Лушпиння вільне від волокон лінтера і делінта носить назву бавовняної лузги. Хімічний склад їх відповідно різниться.
Кукурудзяний качан є відходом підприємств на яких кукурудзяні зерна відокремлюються від качанів і потім використовуються для одержання крохмалю глюкозної патоки кукурудзяного борошна тощо. Вихід качана –
– 35 % від качанів. Довжина її в середньому дорівнює 10 – 15 см діаметр 15 – 20 мм.
Соняшникове лушпиння є відходом виробництва соняшникової олії з насіння соняшнику. Вихід її становить близько 50% від маси зерен що переробляються. Довжина шматочків лузги коливається від 4 до 8 мм ширина дорівнює 15 – 3 мм. Насипна маса 0324 гкг вологість близько 16 % [6].
Хімічний склад рослинних відходів представлений в таблиці 1.2.
Хімічний склад рослинних відходів сільського господарства [5]
2. Обгрунтування вибору технології отримання біоетанолу з целюлозовмісної сировини
На сьогодні відомо три основні технології виробництва біоетанолу:
Виробництво біоетанолу з цукровмісної сировини – спиртове бродіння органічних продуктів що містять вуглеводи (виноград плоди тощо) під дією ферментів дріжджів і бактерій. В результаті бродіння виходить розчин що містить не більше 15 % етанолу так як в більш концентрованих розчинах дріжджі зазвичай гинуть. Отриманий таким чином етанол потребує очищення і концентрування зазвичай шляхом дистиляції.
Виробництво біоетанолу з крохмалевмісної сировини що включає такі етапи:
підготовка та подрібнення крохмалистої сировини - зерна (жита пшениці картоплі кукурудзи і т. п.);
ферментація. На переважній більшості спиртових виробництв світу ферментативне розщеплення крохмалю до спирту за допомогою дріжджів не проводять. Для цих цілей застосовуються рекомбінантні препарати альфа-амілази отримані біоінженерним шляхом - глюкамілаза амілосубтилін.
Виробництво біоетанолу з целюлозовмісної сировини або гідролізне виробництво що складається з трьох етапів: гідролізу сировини зброджування моносахаридів та ректифікація одержаного спирту [7].
Гідроліз целюлозовмісної сировини – це перший етап багатостадійного процесу отримання субстрату для біохімічної переробки. Реальний вихід моносахаридів при гідролізі залежить від співвідношення швидкостей утворення та розпаду цукру. Для підвищення виходу цукру при гідролізі необхідне скорочення тривалості перебування моносахаридів у зоні реакції з метою зменшення їх розкладу.
Гідроліз деревини може здійснюватися з використанням концентрованих або розведених мінеральних кислот або за допомогою ферментів одноступінчатим методом або методом перколяції.
З практичної точки зору принцип одноступінчатого гідролізу можна застосовувати при гідролізі легкогідролізованих геміцелюлозних компонентів сировини. Гідроліз важкгідролізованих полісахаридів з використанням такого принципу ефективний лише у високотемпературній області.
Перколяційний гідроліз на сьогодні являється найбільш ефективним технічним рішенням що дозволяє проводити гідроліз легко- та важкогідролізованих полісахаридів рослинної сировини з прийнятними техніко-економічними показниками процесу. Різноманітні варіанти перколяційного процесу отримали широке застосування в гідролізній промисловості [8].
Сучасна промислова технологія перколяційного гідролізу рослинної сировини заснована на застосуванні розведених розчинів сірчаної кислоти в якості каталізатора і відборі моносахаридів з гідролізапарату по мірі їх утворення.
Схема процесу гідролізу целюлозовмісної сировини розведеною сірчаною кислотою представлена на рис.1.1.
Подрібнена деревина зі складу сировини по транспортеру 1 надходить в направляючу воронку 2 і далі в горловину гідролізапарату.
При завантаженні сировини через трубу 5 надходить нагріта до 70 – 90 ºС розведена сірчана кислота яка змочує сировину сприяючи його згущенню. При такому методі завантаження в 1 м3 гідролізапарату поміщається близько 135 кг тирси або 145 – 155 кг тріски у перерахунку на абсолютно суху деревину. По закінченню завантаження вміст гідролізапарату підігрівається гострою парою що надходить в нижній конус. Як тільки буде досягнута температура 150 – 170 ºС в гідролізапарат по трубі 5 починає надходити 05 – 07 %-ва сірчана кислота нагріта до 170 – 200 ºС. Гідролізат який одночасно утворюється через фільтр 4 починає виводитись у випарник 6. Реакція гідролізу в гідролізапараті триває від 1 до 3 годин. Чим коротший час гідролізу тим вища температура та тиск в гідролізапараті.
Рис.1.1. Схематичне зображення процесу гідролізу целюлозовмісної сировини розведеною сірчаною кислотою [9]:
– транспортер; 2 – направляюча воронка; 3 – гідролізапарат; 4 – фільтр; 5 7 9 10 12 14 21 23 25 28 – труби; 6 8 – випарники гідролізату; 11 13 – решофери; 15 – насос; 16 – бак оборотної води; 17 – змішувач води з кислотою; 18 – кислотний насос; 19 – мірник кислоти; 20 – клапан; 22 – циклон для лігніну; 24 – транспортер для лігніну; 25 – мішалка; 27 – водонагрівальна колона; 29 – диски; 30 – вагомір; 31 – бокові дверцята.
В процесі гідролізу полісахариди деревини переходять у відповідні моносахариди що розчинні у розведеній кислоті яка розчиняється в гарячій воді. Для запобігання розчинення моносахаридів при високій температурі гідролізат безперервно протягом усієї варки виводять через фільтр 4 і швидко охолоджують у випарнику 6. Так як за умовами процесу гідролізована рослинна сировина в гідролізапараті увесь час повинна бути залита рідиною заданий рівень її підтримується гарячою кислотою яка надходить по трубі 5.
Такий метод роботи і носить назву перколяція. Чим швидше іде перколяція тобто чим швидше через гідролізапарат протікає гаряча кислота тим швидше цукор що утворюється виводиться з реакційного простору і тим менше він розкладається. З іншої сторони чим швидше іде перколяція тим більше витрачається на варку гарячої кислоти і тим менше виходить концентрація цукру в гідролізаті і відповідно більша витрата пари.
Практично для отримання достатньо високих виходів цукру (при економічно доцільній концентрації його в гідролізаті) приходиться вибирати деякі середні умови перколяції. Зазвичай зупиняються на виході цукру в 45 – 50 % від маси абсолютно сухої деревини при концентрації цукру в гідролізаті 35 – 37 %. Ці оптимальні умови реакції відповідають відбору через нижній фільтр з гідролізапарату 12 – 15 м3 гідролізату на 1 т абсолютно сухої деревини завантаженої в гідролізапарат. Кількість гідролізату що відбирається за варку на кожну тонну гідролізованої сировини називають гідромодулем витікання і він являється одним із основних показників застосованого на заводі режиму гідролізу.
В процесі перколяції між верхньою та нижньою горловинами гідролізапарату виникає деяка різниці тисків яка сприяє стисканню сировини по мірі розчинення полісахаридів які містяться в ньому.
Стискання сировини призводить до того що в кінці варки лігнін який залишається нерозчиненим займає близько 25 % початкового об’єму сировини. Оскільки за умовами реакції рідина повинна покривати сировину рівень її в процесі варки відповідно знижується. Контроль за рівнем рідини в процесі варки здійснюється за допомогою вагоміра 30 який показує вимірювання сумарної ваги сировини та рідини в гідролізапараті.
По закінченню варки в апараті залишається лігнін який містить на 1 кг сухої речовини 3 кг розведеної сірчаної кислоти нагрітої до 180 – 190 ºС.
З гідролізапарату лігнін вивантажують в циклон 22 по трубі 21. Для цієї цілі швидко відкривають клапан 20 який з’єднує внутрішній простір гідролізапарату з циклоном 22. Завдяки швидкому зниженню тиску між шматочками лігніну перегріта вода яка міститься в ньому миттєво скипає утворюючи великі об’єми пари. Останній розриває лігнін і захоплює його у вигляді зважених частинок по трубі 21 в циклон 22. Труба 21 підходить до циклону по дотичній завдяки чому струмінь пари з лігніном вриваючись в циклон рухається вздовж стінок здійснюючи обертальний рух. Лігнін центр обіжною силою відкидається до бокових стінок і втрачаючи швидкість падає на дно циклону. Звільнену від лігніну пару через центральну трубу 23 викидають в атмосферу [9].
Готовий гідролізат з гідролізапарату надходить у випарник 6 високого тиску. Плівкові випарні апарати з падаючою плівкою (рис.1.2) виконуються у вигляді теплообмінників які складаються з вертикального пучка труб 1 закріплених в трубних решітках 2. Для подачі оброблюваної рідини у вигляді плівки на внутрішній поверхні труб є розподільні пристрої 3. У міжтрубний простір випарника подається теплоносій [10].
Рис.1.2. Плівковий випарний апарат з падаючою плівкою [10]:
-вертикальний пучок труб; 2-трубна решітка; 3-розподільний пристрій.
Частково охолоджений гідролізат з випарника 6 по трубі 7 надходить у випарник 8 низького тиску де охолоджується до 105 – 110 ºС в результаті скипання при більш низькому тиску який зазвичай не перевищує 1 атм. Пара що утворилася при цьому по трубі 14 подається в другий решофер 13 де також конденсується. Конденсати з решоферів 11 і 13 містять 02 – 03 % фурфуролу і використовуються для його виділення на спеціальних установках.
Кислий гідролізат з випарного апарату низького тиску 8 по трубі 9 подають в апаратуру для його нейтралізації та подальшої переробки. Температура такого гідролізату 95 – 98 ºС [9].
Основна задача процесу нейтралізації – зниження активної кислотності гідролізату з підвищенням рН від 13 до 35 – 5 що досягається нейтралізацією сірчаної та частково органічних кислот гідролізату за допомогою нейтралізуючих агентів. В якості нейтралізуючих агентів застосовуються вапняне молоко а також аміачна вода.
В результаті нейтралізації сірчаної кислоти гідроокисом або карбонатом кальцію утворюється сульфат кальцію який повинен достатньо повно виводитися з напівпродуктів виробництва з метою запобігання гіпсації обладнання та комунікацій. Для підвищення глибини виведення сульфату кальцію з нейтралізат запропоновані наступні технологічні прийоми: нейтралізація з направленою кристалізацією гіпсу нейтралізація паралельних потоків гідролізату а також заміщуючи нейтралізація.
Основне практичне значення в гідролізно-спиртовому виробництві отримала двоступенева нейтралізація гідролізату вапняним мкм та аміаком з направленою кристалізацією гіпсу.
В ряді районів країни вапно являється дефіцитним матеріалом. Необхідність її транспортування та приготування вапняного молока вносить додаткові труднощі в організацію виробництва. У зв’язку з цим на ряді підприємств перейшли на аміачну нейтралізацію. Недоліком цього методу являється введення в субстрат надлишкової кількості амонійного азоту що негативно проявляється на процесах ферментації. При такому методі нейтралізації вміст сполук азоту в нейтралізат досягає 700 мгл ( в перерахунку на N2) та вище.
Тому краще обирати нейтралізацію у дві стадії в спеціальних реакторах-нейтралізаторах (рис.1.3) [11].
Рис.1.3. Реактори-нейтралізатори [11]:
-мірник; 2-корпус нейтралізаторів; 3-механічний перемішуючий пристрій.
Нейтралізують гідролізат вапняним молоком тобто суспензією гідрату окису кальцію у воді з концентрацією 150 – 200 г СаО в літрі.
Схема нейтралізації представлена на рис.1.4. Негашене вапно СаО безперервно подають в завантажувальну воронку обертального барабану для гасіння вапна 10. Одночасно в барабан подають необхідну кількість води. При обертанні барабану негашене вапно зв’язуючи воду переходить в гідрат окису кальцію. Останній диспергується у воді утворюючи суспензію.
Рис.1.4. Схема нейтралізації гідролізату [12]:
– труба; 2 – збірник для вапняного молока; 3 – потенціометр; 4 –
сурм’яний електрод; 56 – нейтралізатори; 7 – відстійник; 8 – шлам; 9 – збірник сусла; 10 – барабан для гасіння вапна; 11 – відокремлювач піску; 12 – труба; 1314 – баки для розчину поживних солей; 15 – холодильник.
Вапняне молоко в цьому апараті повільно тече справа наліво і далі по трубі 12 зливається в збірник 2. Одночасно з вапняним молоком в нейтралізатор 5 подаються слабо кислий водний екстракт суперфосфату з мірника-бачка 14.
По закінченню цього часу нейтралізований гідролізат який називається «нейтралізатор» надходить у відстійник 7 напівбезперервної дії. Напівбезперервний процес заклечається в тому що нейтралізат протікає через відстійник безперервно а осідаючий на дно гіпс видаляється періодично по мірі накопичення.
Перед спуском в каналізацію шлам 8 в збірнику додатково промивається водою. Нейтралізат звільнений від зважених частинок перед зброджуванням охолоджується в холодильнику 15 з 85 до 30ºС [12].
Другий етап виробництва біоетанолу з целюлозовмісної сировини – зброджування деревного сусла.
Зброджують деревне сусло спеціальними акліматизованими в цьому середовищі спиртоутворюючими дріжджами. Схема зброджування гідролізату у етиловий спирт показана на рис.1.5.
Рис.1.5. Схема зброджування рослинних гідролізатів у етиловий спирт [13]:
2-бродильні чани; 3-труба; 4-сепаратор; 5-труба; 6-воронка; 7-збірник бражки; 8-дріжджанка.
Зброджування іде по безперервному методу в батареї послідовно з’єднаних бродильних чанів 1 та 2.
Дріжджова суспензія яка містить близько 80 – 100 г пресованих дріжджів в літрі подається безперервним потоком по трубі 5 в дріжджанку 8 а потім у верхню частину першого або головного бродильного чану 1. В дріжджанку одночасно з дріжджовою суспензією подається охолоджене деревне сусло. На кожен кубометр дріжджової суспензії в бродильний чан надходить 8 – 10 м3 сусла.
Часточки дріжджів що містяться в середовищі гексозних цукрів за допомогою системи ферментів розщеплюють цукри утворюючи етиловий спирт та вуглекислий газ. Етиловий спирт переходить у навколишню рідину а вуглекислий газ виділяється на поверхні дріжджових частинок у вигляді маленьких пухирців які поступово збільшуються в об’ємі отім поступово спливають на поверхню чана забираючи з собою дріжджові частинки.
При зіткненні з поверхнею пухирці вуглекислого газу лопаються а дріжджові частинки що мають питому вагу 11 тобто більше ніж у сусла (1025) осідають униз поки знову не будуть підняті вуглекислим газом на поверхню. Безперервний рух дріжджових частинок уверх та донизу сприяє переміщенню потоків рідини у бродильному чані створюючи перемішування або «бродіння» рідини. Вуглекислий газ який виділяється на поверхні рідини з бродильних чанів по трубі 3 надходить на установку для отримання рідкої або твердої вуглекислоти використовується для отримання хімічних продуктів (наприклад сечовини) або випускається в атмосферу.
Частково зброджене деревне сусло разом із дріжджами передається з головного бродильного чану у хвостовий чан 2 де бродіння завершується. Оскільки концентрація цукру у хвостовому чані невелика бродіння у ньому іде менш інтенсивно і частина дріжджів не встигаючи утворювати пухирці вуглекислого газу осідає на дно чану. Щоб не допустити цього у хвостовому чані влаштовують часто механічне перемішування рідини мішалками або центр обіжними насосами.
Зброджена рідина називається бражкою. По закінченню бродіння бражка передається в сепаратор 4 що працює по принципу центрифуги. Сепаратор ділить рідину на два потоки: великий який не містить дріжджів надходить у воронку 6 і менший який містить дріжджі надходить через воронку у трубу 5. Зазвичай перший потік у 8 – 10 разів більший за другий. По трубі 5 дріжджова суспензія повертається у головний бродильний чан 1 через дріжджанку 8. Скинуте і звільнене від дріжджів сусло збирається у проміжному збірнику бражки 7.
Періодично гідролізний завод зупиняють на планово-попереджувальний або капітальний ремонт. У цей час суспензію дріжджів за допомогою сепараторів згущують та заливають холодним деревним суслом. При низькій температурі бродіння різко сповільнюється і дріжджі вживають значно менше цукру.
Сепараційний метод зброджування являється більш ефективним порівняно зі способами по яким дріжджі закріплювались на плаваючих або нерухомих насадках [13].
Останній етап виробництва біоетанолу – ректифікація та абсолютизація спирту. Завданням цієї стадії є отримання абсолютного спирту який не містить бензол.
Технічний спирт можна одержувати на типових брагоректифікаційних (без включення епюраційної колони) установках з виділенням головної фракції і сивушного масла за тією ж технологією що й при виробництві спирту ректифікованого харчового. Також можна проводити процес в одноколонній ректифікаційній установці з частковим відбором головних домішок і компонентів сивушного масла або використовуючи ректифікаційну установку зі збільшеним числом тарілок у концентраційній частині колони (до 50 шт.) і збільшенням флегмового числа.
Так як паливний етанол не вимагає його глибокої очистки від домішок то найдоцільніше використовувати одноколонну ректифікаційну установку так як вона вимагає менших витрат енергії пари та води.
При одержанні паливних сумішей з великим вмістом етанолу потрібне його абсолютизування (зневоднення) тому що можливе розшарування бензину та спирту.
Відома установка безперервної дії для отримання бензанолу [14] що передбачає утворення потрійних нероздільнокиплячих (азеотропних) сумішей за допомогою додавання в якості третього компоненту до суміші спирт-вода бензину. Застосування саме такого компоненту пояснюється тим що циклогексан та бензол які також використовують для абсолютизації етанолу являються токсичними речовинами і можуть зашкодити здоров’ю людини.
Технічний результат досягається тим що установка безперервної дії для отримання абсолютного спирту містить послідовно встановлені бражну колону конденсатор бражної колони ректифікаційну колону оснащену боковим штуцером для подачі бензину конденсатор і термосифонний кип’ятильник ректифікаційної колони дегідраційну колону оснащену штуцером для подачі спирто-бензинової суміші та штуцером для подачі бензину дефлегматор конденсатор і термосифонний кип’ятильник дегідраційної колони.
Подача в штуцер де гідратаційної колони спирто-бензинової суміші що містить азеотропний спирт забезпечує стабільну роботу установки. Отримання абсолютного спирту що не містить бензол досягається за рахунок того що в штуцер подачі бензину яким оснащена дегідратаційна колона подається бензин А-92. Подача в дегідратаційну колону бензину сприяє утворенню потрійного азеотропну з підвищеним вмістом води який відводиться зверху де гідратаційної колони що і створює ефект дегідратації спирту та забезпечує отримання знизу колони абсолютного спирту що не містить бензол.
Таким чином сукупність суттєвих ознак дозволяє забезпечити стабільну роботу установки і отримати абсолютний спирт що не містить бензол і досягти бажаного технічного результату [15].
На рис.1.6 представлена установка безперервної дії для отримання абсолютного спирту (бензанолу біоетанолу).
Дана установка працює наступним чином. Бражка що підігрівається в конденсаторі бражної колони 3 подається на верхню 24-ту тарілку бражної колони 1 яка обігрівається гострою парою. З низу бражної колони 1 відводиться барда.
По виході з колони 1 пари що містять леткі домішки надходять у конденсатор бражної колони 3. Бражний конденсат подається на 16-ту тарілку 80-ти тарільчатої ректифікаційної колони 2що оснащена термосифонним кип’ятильником 5 і обігрівається глухою парою.
Рис.1.6. Схема безперервної установки для отримання біоетанолу [16]:
-бражна колона; 2-ректифікаційна колона; 3-конденсатор бражної колони; 4-дефлегматор; 5-термосифонний кип’ятильник; 6-дегідратаційна колона; 7-дефлегматор; 8-конденсатор; 9-термосифонний кип’ятльник.
Нижня частина колони оснащена штуцером для відбору сивушної фракції. Лютер що містить кислоти та незначну кількість вищих спиртів виводиться знизу ректифікаційної колони 2. На 80-ту тарілку ректифікаційної колони 2 подається бензин. Спиртово-бензинові пари з верху ректифікаційної колони 2 надходять у конденсатор 4. Частина спиртово-бензинової суміші яка відбирається з конденсатора 4 подається у якості живлення на 50-ту тарілку 65-ти тарільчатої де гідратаційної колони 6. нша частина направляється у вигляді флегми на зрошення ректифікаційної колони2. Дегідратаційна колона 6 оснащена термосифонним кип’ятильником 9 і обігрівається глухою парою. На верхню тарілку де гідратаційної колони 6 подається бензин. Пари з верху де гідратаційної колони проходячи дефлегматор повністю конденсуються в конденсаторі 8 з якого відбирається спиртово-вуглеводнева суміш. Абсолютний спирт який використовується в якості оксигенатної добавки для виробництва біоетанолу виводиться знизу дегідратаційної колони 6 [16].
Отже виходячи з аналізу представлених вище технологій були прийняті наступні технологічні рішення:
Гідроліз целюлозовмісної сировини слід проводити перколяційним способом використовуючи в якості каталізатору розведену сірчану кислоту.
Для випарювання гідролізату найдоцільніше використати плівковий випарний апарат з падаючою плівкою тому щ він являється найбільш ефективним і економічним випарним обладнанням має просту конструкцію та високу інтенсивність теплопередачі і дозволяє проводити процес випарювання з найменшими капітальними та експлуатаційними затратами.
Для нейтралізації гідролізату обираємо двохступінчату установку із застосуванням в якості нейтралізуючого агента вапняного молока так як така установка дозволяє ефективно досягнути оптимальний рівень рН і при цьому в нейтралізат додаються поживні речовини необхідні для наступного етапу зброджування.
Зброджування слід проводити сепараційним методом що дозволяє ефективно відділяти дріжджі від спирту і досягати високих виходів продукту.
Ректифікацію найдоцільніше проводити на одноколонній ректифікаційній установці так як вона вимагає менших витрат води пари та енергії.
Абсолютизацію спирту вирішено здійснювати на двохколонній установці азеотропним методом використовуючи в якості додаткового компоненту до суміші етанол-вода бензину.
3. Характеристика спиртових дріжджів
Цукри які утворюються після гідролізу целюлозовмісної сировини зброджуються у спирт дріжджами Saccharomyes cerevisiae які являють собою одноклітинні мікроорганізми що відносяться до класу аскоміцетів (сумчастих грибів).
У зв’язку з тим що дріжджі асимілюють готові органічні сполуки і не засвоюють Н2СО3 вони відносяться до гетеротрофних мікроорганізмів а по типу дихання – до факультативних анаеробів тобто здатні розвиватися як в анаеробних умовах за відсутності кисню так і в аеробних.
Зазвичай дріжджі розмножуються брунькуванням і дуже рідко (в умовах великого дефіциту поживних речовин) спороутворенням.
Дріжджові клітини бувають яйцеподібної еліпсоїдальної овальної чи витягнутої форми яка як і їх довжина (6 11 мкм) залежить від умов росту та виду дріжджів. Відношення поверхні клітини до її об’єму впливає на швидкість масообмінних процесів між клітиною та поживним середовищем і як наслідок на інтенсивність життєдіяльності дріжджів.
Дріжджова клітина складається із оболонки цитоплазми та ядра. Зовнішня частина оболонки утворена полісахаридами типу геміцелюлоз та невеликою кількістю хітину внутрішня частина – білковими речовинами фосфоліпідами і ліпоїдами. Оболонка регулює внутрішній стан клітини і має вибіркову проникливість що суттєво відрізняє її від звичайних напівпроникливих мембран. Товщина клітинної оболонки дріжджів до 400 нм.
Способами генетичної інженерії отримані високоефективні раси дріжджів які володіють амінокислотною активністю. Промислове використання таких дріжджів дозволить суттєво прискорити процес зброджування сусла і зменшити витрати оцукрюючи матеріалів.
До умов що забезпечують нормальну життєдіяльність дріжджів відносяться перш за все температура рН та склад поживного середовища [17].
3.1.Вплив температури та рН на життєдіяльність дріжджів
Дріжджі живуть і розмножуються в обмежених температурних умовах і для нормальної їх життєдіяльності необхідна температура 29 – 300С. за дуже великої чи дуже низької температури життєдіяльність дріжджів послаблюється чи припиняється. Максимальна температура для розвитку дріжджів 380С мінімальна 50С; при температурі 500С дріжджі гинуть.
Оптимальні температури для розвитку та виявлення максимальної бродильної активності не завжди співпадають. Дріжджі вирощені при температурі наприклад 17 – 220С мають велику бродильну енергію. Зброджування мелясного сусла при температурах вищих за 300С негативно відображається на виході та якості дріжджів як і відокремлені із зрілої бражкита використовуються в якості хлібопекарних. Ферментативна активність під’ємна сила та стійкість таких дріжджів при зберіганні знижується тому для вирощування дріжджів і зброджування мелясного сусла рекомендується наступний температурний режим: 28 – 290С в дріжджегенераторах 30 – 310С у двох головних бродильних апаратах і 28 – 290С в кінцевих апаратах.
При підвищенні температури дикі дріжджі та бактерії розмножуються значно швидше сахароміцетів. Якщо при 320С коефіцієнт розмноження диких дріжджів у 2 – 3 рази більше коефіцієнта розмноження сахароміцетів то при 380С вже у 6 – 8 разів більше. Внаслідок прискореного розвитку бактерій збільшується кислотність бражки. В обох випадках зменшується вихід спирту.
На життєдіяльність дріжджів значною мірою впливає активна кислотність середовища. Йони водню змінюють електричний заряд колоїдів плазмової оболонки клітин і залежно від концентрації можуть зменшувати чи збільшувати її проникливість для окремих сполук та йонів. Від значення рН залежить швидкість надходження поживних речовин в клітину активність ферментів утворення вітамінів. При зміні рН середовища змінюється і напрямок самого бродіння. Якщо рН зсувається в лужний край то збільшується утворення гліцерину.
Життєдіяльність дріжджів зберігається у рамках рН середовища від 2 до 8; для їх вирощування оптимальним являється рН 48 – 5. При рН нижче 42 дріжджі продовжують розвиватися тоді як ріст молочнокислих бактерій зупиняється. Цю властивість дріжджів використовують для пригнічення розвитку бактерій в інфікованому середовищі яке підкислюють до рН 28 – 4 і витримують визначений час [18].
3.2.Джерела харчування дріжджів
Розрізняють екзогенне та ендогенне харчування дріжджів: при екзогенному харчуванні поживні речовини потрапляють до клітини із зовнішнього середовища при ендогенному дріжджі використовують (в основному при голоданні) свої резервні речовини: глікоген трегалозу ліпіди азотисті сполуки.
Вуглецеве харчування.Дріжджі (Saccharomyes cerevisiae) використовують вуглець із різноманітних органічних сполук: глюкози маннози галактози фруктози (D - форми). Пентози Sacch. cerevisiaeне асимілюють. При відсутності гексоз джерелом вуглецю можуть бути також гліцерин маніт етиловий та інші спирти органічні кислоти (молочна оцтова яблучна лимонна).
Слід враховувати поліауксію – послідовність споживання різноманітних джерел вуглецю. При періодичному культивуванні в першу чергу споживаються глюкоза та фруктоза. Послідовність засвоювання жирних кислот залежить від раси дріжджів що використовуються та складу цих кислот. Наприклад оцтова кислота перешкоджає споживанню молочної а молочна – гліколевий. Оцтова кислота і глюкоза засвоюються одночасно. Як правило в першу чергу засвоюється з суміші те джерело вуглецю яке забезпечує найбільшу швидкість росту дріжджів.
При безперервному культивуванні дріжджів зі збільшенням швидкості розбавлення середовища в ньому залишається більше вуглецевого компоненту який засвоюється останнім.
Дисахариди з яких спиртові дріжджі використовують мальтозу та сахарозу попередньо підпадають під вплив гідролізу відповідними ферментами дріжджів до моносахаридів. При переході від анаеробних умов до аеробних послаблюється можливість дріжджів зброджувати глюкозу та мальтозу а сахарозна активність їх підвищується в 25 рази. Дріжджі споживають мальтозу тільки при відсутності в середовищі фруктози та глюкози. Мальтоза зброджується майже повністю під час стаціонарної фази росту дріжджів.
Органічні кислоти мають важливе значення при метаболізмі вуглецю енергетичному обміні мікроорганізмів синтетичних та дисиміляційних процесах. Використання кислот жирного ряду в якості джерела вуглецю залежить від виду та раси дріжджів концентрації кислоти довжини її вуглецевого ланцюга та ступеня електролітичної дисоціації. Непоганими субстратами служать кислоти з довжиною вуглецевого ланцюга від С2до С4при порівняно низькій концентрації. Калійні солі кислот що містять у молекулі від 2 до 5 атомів вуглецю стимулюють ріст дріжджів в 14 – 33 рази сильніше порівняно з відповідними кислотами.
Жирні кислоти з середньою довжиною вуглецевого ланцюга (від С6до С10) в значно меншій мірі споживаються дріжджами і тільки в умовах дуже низької концентрації (002 – 005%). При більш високій концентрації розвиток дріжджів пригнічується. Жирні кислоти з 12 – 17 атомами вуглецю в молекулі засвоюються вибірково в залежності від роду та виду дріжджів.
Будь-який з проміжних продуктів циклу Кребса (піровиноградна лимонна янтарна фумарола яблучна кислоти) можуть бути єдиними джерелами вуглецю для життєдіяльності дріжджів [19].
Азотне харчування.Дріжджі мають можливість синтезувати всі амінокислоти що входять до складу їх білка безпосередньо з неорганічних азотистих сполук при використанні в якості джерела вуглецю органічних сполук - проміжні продукти розпаду вуглеводів які утворюються при диханні та бродінні.
Дріжджі Sacch. Cerev однак при використанні його звільнюються кислоти що змінюють рН середовища. Аміачний азот використовується дріжджами краще ніж азот багатьох амінокислот.
Амінокислоти – одночасно джерело азоту та вуглецю при цьому останній засвоюється з кетокислот що утворюються в результаті відщеплення аміногруп. Можлива і безпосередня асиміляція амінокислот з поживного середовища яке містить їх повний набір та будь-який цукор що зброджується. Як наслідок знижуються витрати цукру середовища на харчування дріжджів та дещо збільшується вихід спирту при бродінні.
Завдяки асиміляції амінокислот забезпечується синтез білка в тому ж числі і ферментів активуються деякі ферменти що вже є в клітині прискорюється процес брунькування дріжджових клітин.
Для споживання органічного азоту (амінокислот амідов) багатьом дріжджам необхідні вітаміни (біотин пантотеновая кислота тіамін пірідоксін та ін.). дріжджі не засвоюють такі азотисті сполуки як білки бетаїн холін пурини та аміни у вигляді етіламіна пропіл- та бутіламіна. Пептиди займають середнє положення між амінокислотами та білками. Споживання дріжджами пептидів знижується з підвищенням їх складності. Деяка кількість пептидів в середовищі поряд з іншими формами азоту сприяють використанню амінокислот.
На утворення 10 млрд. дріжджових клітин витрати азоту в умовах анаеробіозу складають 66 – 77 мг в умовах аеробіозу 37 -53 мг. Про умови культивування та фізіологічний стан дріжджів говорять по вмісту азоту в них який залежить від складу середовища кількості додатково вводимих поживних речовин та від раси дріжджів. В дріжджах що отримують на спиртових заводах загального азоту 7 – 10% (іноді до 12) на суху речовину.
Фосфорне харчування.В анаеробних умовах дріжджі засвоюють фосфор головним чином у початковому періоді бродіння – 80-90% від максимальної кількості в дріжджах. Молоді дріжджові клітини що енергійно розмножуються багатші на фосфор у порівнянні зі старими що не брунькуються. Наприклад після 6 годин бродіння дріжджі містять 215% фосфору на суху речовину до кінця бродіння – лише 1% [20].
зміст.docx
1. Характеристика целюлозовмісної сировини .
2. Обгрунтування вибору технології отримання біоетанолу з
целюлозовмісної сировини
3. Характеристика спиртових дріжджів . .
3.1. Вплив температури та рН на життєдіяльність дріжджів.. .
3.2. Джерела харчування дріжджів ..
Біохімічні основи технологічного процесу виробництва біоетанолу
з целюлозовмісної сировини
1. Схема перебігу процесів
1.1. Механізм перетворення основних компонентів сировини
1.2. Біохімія спиртового бродіння
2. Характеристика біоетанолу
Технологія виробництва біоетанолу з целюлозовмісної сировини ..
1. Характеристика сировини і матеріалів
2. Опис технологічного процесу ..
3. Контроль виробництва ..
4. Матеріальний баланс .
Вибір та характеристика обладнання
1. Принцип роботи ректифікаційної колони
2. Класифікація ректифікаційних установок по конструкції
внутрішнього влаштування апарату .
3. Вибір ректифікаційної колони ..
3.1. Колони з сітчастими тарілками для розділення суміші
«етиловий спирт – вода» .
3.2. Вибір допоміжного обладнання і конструкційного
4. Технічна характеристика ..
5. Технологічні розрахунки ..
5.1. Матеріальний розрахунок колони
5.2. Розрахунок діаметра ректифікаційної колони ..
5.3. Розрахунок числа тарілок .
5.4. Розрахунок висоти колони
5.5. Гідравлічний розрахунок колони .
5.6. Тепловий розрахунок колони
5.7. Конструктивний розрахунок .
1. Виявлення та аналіз ШНВФ на проектному об’єкті. Заходи з
1.1. Повітря робочої зони .
1.2. Проектування системи загально обмінної припливної
1.3. Виробниче освітлення
1.4. Захист від виробничого шуму та вібрацій ..
1.5. Електробезпека ..
1.6. Безпека технологічних процесів та обслуговування
Перелік використаних джерел ..
ректификационная колонна.cdw

Висновки.docx
Схеми перебігу біохімічних процесів які наведені в дипломному проекті показали що з целюлозовмісної сировини можна одержувати високий вихід біоетанолу (з 1 тонни деревини 200 л біоетанолу).
В проекті було обрано і обрунтовано технологію виробництва біоетанолу з відходів деревини яка передбачає застосування перколяційного гідролізу використання плівкових випарних апаратів для випарювання гідролізату зброджування сепараційним методом; ректифікацію у ректифікаційних колонах з сітчастими тарілками і абсолютизацію азеотропним методом використовуючи в якості додаткового компоненту до суміші етанол-вода бензину А-92.
Технологічний процес було спроектовано із зазначенням точок хімічного технологічного і мікробіологічного контролю. Розрахунки матеріального балансу показали що з 19 тонни вологої деревини яка складається на 50 % з хвойної і на 50 % з листяної можна отримати 02 тонни біоетанолу.
Також проектом було передбачено використання ректифікаційної колони з сітчастими тарілками для очищення біоетанолу від домішок і води наведено характеристику колони і її технологічний розрахунок.
список літератури.docx
Безуглий М.Б. Енергоносіям з біосировини – науковий підхід М.Б.Безуглий Аграрний тиждень. – 2010. - № 16. – С.10.
Калетник Г.М. Перспективи виробництва біоетанолу в Україні Г.М. Калетник Аграрна техніка та обладнання. – 2009. -№2. –С.50-55.
Паушкин Я.М. Нефтихимический синтез в промышленности. –М.:Наука 1966. – 404с.
Никишов В.Д. Комплексное использование древесины: Учебник для вузов. – М.: Лесн. пром-сть 1985. – 264с.
Азаров В.И. Химия древесины и синтетических полимеров: учебник В.И. Азаров А.В. Буров А.В. Оболенская. – СПб.: «Лань» 2010. – 624с.
Древесина модифицированная. Метод определения истирания: ГОСТ 21523.10-88. – введён в действие от 1989-01-01. – М.: Государственный комитет СССР по стандартам 1994. – 8 с.
Валакин В.П. Одержання синтетичного етилового спирту; [пер. з рос.]. – М.: Хімія 1976. – 102с.
Яровенко В.Л. Технология спирта В.А. Маринченко В.А. Смирнов и др.; под ред. проф. В.Л. Яровенко. – М.: Колос «Колос-Пресс» 2002. – 465с. ISBN 5-10-003574-9.
Шарков В.И. Технология гидролизных производств С.А. Сапотницкий О.А. Дмитриева И.Ф. Гуманов. – М.: Лесн. пром-сть 1973. – 408с.
Тароватый Д.В. Совершенствование плёночных испарителей для обработки продуктов на основе гидролизата растительного сырья: автореф. дис. на соискание учёной степени кандидата технических
наук: 05.21.03 Тароватый Денис Викторович; ФГБОУ ВПО «Сибирский государственный технологический университет». – Красноярск 2011. – 23с.
Юкельсон И.Ю.Технология основного органічного синтезу; [пер. з рос.]. - М.: Химия 1968. –125с.
Отвагина М.И. Промышленность минеральных удобрений и серной кислоты. В.И. Явор Н.С. Сретенская М.Ю. Шарифов. – М.: НИИТЭХИМ 1972. – 117с.
Агеев Л.М. Химико-технологический контроль и учёт гидролизного и сульфитно-спиртового производства С.И.Корольков. – М.: Гослесбумиздат 1953. – 406с.
Пат.83015А РФ 201010019522. Установка непрерывного действия для получения бензанола Е.Н. Константинов Т.Г. Короткова З.А.Ачегу А.В. Кикнадзе; патентообладатель ГОУ ВПО «КубГТУ». - № 2009106412; заявл. 11.01.2010; опубл. 10.04.2010 бюл. №14.
Спирт этиловый ректификованный. Технические условия: ГОСТ 5962-67. – введён в действие от 1968-01-01. – М.: Государственный комитет СССР по стандартам 1968. – 7с.
Цыганков П.С. Руководство по ректификации спирта С.П. Цыганков. – М.: Пищепромиздат 2001. – 201с. ISBN 5-89703-035-9.
Алмагамбетов К. Х. Биотехнология микроорганизмов К. Х. Алмагамбетов. – Астана 2008. – 244 с. – ISBN 9968-31-240-0.
Ерошкина Е.В. Исследование новых рас пивных дрожжей для интенсификации процессов брожения и дображивания пива и улучшение его качества: дис. на соискание научной степени канд. техн. наук: 04.18.07 Ерошкина Елена Валерьевна; Воронежская государственная техническая академия. – Воронеж 2000. – 199с.
Егоров Н. С. Биотехнология: учебное пособие для вузов. В 8 т. Т 6. Н. С. Егоров В. Д. Самуилов. – М.: Высш. шк. 1987. – 143 с.
Кузнецов А. Е. Научные основы экобиотехнологии: учебное пособие для студентов А. Е. Кузнецов Н. Б. Градова. – М.: Мир 2006. – 504 с. – ISBN 5-03-003765-9.
Маринченко В.О. Технологія спирту В.А. Домарецький П.Л. Шиян В.М. Швець П.С. Циганков .Д. Жолнер. – Вінниця: «Поділля-2000»2003. – 496с. ISBN 5-86248-114-1.
Костюкевич Н.Г. Химия древесины: учебное пособие. – СПб.: СПбГЛТУ 2011. – 84с.
Оболенская А.В. Лабораторные работы по химии древесины и целлюлозы: Учебное пособие для ВУЗов Ельницкая З.П. Леонович А.А. – М.: «Экология» 1991. – 320с.
Евстигнеев Е.И. Химия древесины: учебное пособие Евстигнеев Е.И. – СПб.: Изд-во Политех. ун-та 2007. – 148с.
Джатдоева М.Р. Теоретические основы прогрессивных технологий. Химический раздел. – Ессентуки: ЕГИЭиМ 1998. – 78 с.
Ethanol production from hexoses pentoses and dilute-acid hydrolyzate Sues A. [et al] FEMS 2005. – V.5. – P.669 – 676.
Роговин З.А. Химия целлюлозы. – М.: Химия 1972. – 520 с.
Иванов Ю.С. Современные способы варки сульфатной целлюлозы: учебное пособие. –СПб.: ГОУ ВПО СПбГТУРП 2005. – 305с.
Булгаков Н.И. Биохимия солода и пива. – М.: Пищевая пром-сть 1976. – 358с.
Грин Дж.Р. Растворимые ферменты и брожение. – М.: Химическая пром-сть1905. – 469с.
Пастер Л. Исследования о брожениях. – М.: Сельхозгиз 1937. – 488с.
Моргунова Е.М. Общая технология отрасли: конспект лекций Н.А. Шелегова. – Могилев: УО МГУП 2009. – 100с.
Чурикова В.В. Метаболизм микроорганизмов: учебное пособие М.А. Климова. – Воронеж: Изд-во ВГУ 2007. – 45с.
Спирт этиловый технический. Технические условия: ГОСТ 17299-78. – введён в действие от 1978-05-21. – М.: Государственный комитет СССР по стандартам 1978. – 7с.
Бензини томобільні підвищеної якості: ДСТУ 4839:2007. –введений в дію з 2013-03-07. – К.: Держспоживстандарт України 2007. – 11с.
Balat M. Production of bioethanol from lignocellulosic materials via the biochemical pathway: a review. Energ. Convers Manag. 2011. – V52. – P.858 – 875.
Стабников В.М. Етиловий спирт П.М.Мальцев .М.Ройтер Б.Д.Метюшов; під ред.. В.М.Стабникова. – К: Державне видавництво технічної літератури УРСР 1959. -336с.
Гордон Л.В. Технология и оборудование лесохимических производств С.О. Скворцов В.И. Лисов. – М.: Лесная пром-сть 1988. – 179с. ISBN 5-7120-0065-2.
Святченко С.. Економічні розрахунки витрат при виробництві біопалива Вісник ЦНЗ АПВ Харківської області. – 2010. №8. – С. 274-279.
Холькин Ю.И. Лабораторный практикум по гидролизным производствам В.М. Скачков. - Ленинград: ЛТА 1978. – 87с.
Гельфанд Е.Д. Основные технологии биоэтанола. - Архангельск: «Росалко» 2005. – 5с. ISBN 5-261-00196-Х.
Дёмин В.А. Технология и оборудование лесохимических производств. – Сыктывкар: СЛИ 2013. – 119с.
Равич Б.М. Комплексное использование сырья отходов В.П. Окладников. – М.: Химия 1988. – 288с.
Холькин Ю.И. Технология гидролизных производств. Учебник для ВУЗов. – М.: Лесная промышленность 1989. – 496с.
Морозов Е.Ф. Производство фурфурола (Вопросы катализа и новые виды катализаторов). – М.: Лесн. пром-сть1988. – 200с.
Коверинский И.Н. Комплексная химическая переработка древесины: учебник для вузов В.И. Комаров С.И. Третьяков Н.И. Богданович О.М. Соколов Н.А. Кутакова. – Архангельск: Изд-во Арханг. гос. техн. ун-та 2002. – 347с.
Славянский А.К. Химическая технология древесины В.И. Шарков А.А. Ливеровский. – М.: Гослебумиздат 1962. -576с.
Халаим А.Ф. Технологи спирта. – М.: Пищевая пром-сть 1972. – 192с.
Поляков В.А. Теоретические и практические аспекты спиртовой ликёрочной ферментной дрожжевой и уксусной отрасли промышленности - М.: ВНИИПБТ 2006. – 307с.
Лунин О.Г. Теплообменные аппараты пищевых производств В.Н. Вельтищев. –М.: Агропромиздат 1987. – 239 с.
Новикова И.В. Технология ликёро-водочного и дрожжевого производств Н.И. Алексеева А.Н. Яковлев Н.В. Зуева. – Воронеж: Изд-во ВГА 2010. – 84с.
Ламберова М.Э. Оценка эффективности культивирования и применение молочно-кислых бактерий Н.А. Шавыркина А.А. Ламберова. – Бийск: БТИ АлтГТУ 2009. – 90с.
Сулагаев А.В. Реальный сепаратор: Руководство пользоватля. – Тюмень: Гипротюменнефтегаз 2004. – 23с.
Гореликова Г.А. Основы современной пищевой биотехнологии. – Кемерово: КТИПП 2004. – 100с.
Циганков П.С. Виділення спирту із бражки та його очистка С.П. Циганков. – К.: Глобус 2000. – 121с. ISBN 5-86248-114-1.
Багатуров С.А. Курс теории перегонки и ректификации. М.: Гостоптехиздат 1954. – 479с.
Анисимов И.В. Автоматическое регулирование процесса ректификации. – М.: Гостоптехиздат 1961. – 180с.
Карпов С.А. Автомобилные топлива с биоэтанолом В.М. Капустин А.К. Старков. – М.: Колос 2007. – 219с.
Закис Г.Ф. Функциональный анализ лигнинов и их производных. – Рига: Зинатне 1987. – 230с.
Лекторский Д.Н. Современная лесохимия. – М.: Гослестехиздат 1935. – 142с.
Кафтанов С.В. Общая химическая технология топлива. – Москва-Ленинград: ГХИ НКТП СССР 1941. -770с.
Ручай Н.С. Расчёт материальных и тепловых балансов; расчёт и подбор оборудования биотехнологических производств Р.М.Маркевич. – Минск: Биотехнология и биоэкология 2004. – 65с.
Лащинский А.А. Основы конструирования и расчета химической аппаратуры А.Р. Толчинский. - М 1968. – 268с.
Павлов К.Ф. Примеры и задачи по курсу процессов и аппаратов химической технологии П.Г. Романков А.А. Носков. - Л.: Химия 1987. – 255с.
Романков П.Г. Методы расчета процессов и аппаратов химической технологии (примеры и задачи) В.Ф. Фролов О.М. Флисюк М.И. Курочкина. - Л.: Химия 1993. – 156с.
Машины и аппараты химических производств: Примеры и задачи. Учебное пособие для студентов вузов. И.В. Доманский та ін.; під ред. В.Н. Соколова. - Л.: Машиностроение 1982. – 364 с.
Иоффе И.Л. Проэктирование процессов и аппаратов химических технологий. – Л.: Химия 1991. – 352 с.
Тимонин А.С. Основы конструирования и расчёта химико-технологического и природоохранного оборудования : Справ. 2-е видання. –М.: Машиностроение 1970. -762 с.
Хижняков С.В. Практические расчёты тепловой изоляции (для промышленного оборудования и трубопроводов). –М.: Энергия 1976. – 200 с.
Расчёты основных процессов и аппаратов нефтепереработки: Справочник Рабинович Г.Г. и др.; Под. ред. Е.Н. Судакова. – 3-е изд. М.: Альфа-М 2006. – 608 с.
Печенегов Ю.Я. Расчёт теплотехнических свойств газовых и жидких теплоносителей. – Саратов: Сарат. Политехн. Ин-т 1982. – 84 с.
Пери Дж.Г. Справочник инженера-химика. –Л.: Химия 1969. – Т.1; Т.2.
Рудов Г.Я. Расчет тарельчато ректификационной колонны методические указания Д.А. Баранов. - М.: МГУИЭ 1998. – 102с.
Каталог «Емскостная стальная сварная аппаратура». М. «ЦИНТИХИМНЕФТЕМАШ» 1969.
Каталог «Кожухотрубчатые теплообменные аппараты общего и специального назначения». М. «ЦИНТИХИМНЕФТЕМАШ» 1991.
Орленко А.Т. Методичні вказівки до виконання розділу «Охорона праці» в дипломних проектах і роботах для студентів ф-ту біотехнології та біотехніки А.Т. Орленко Н.А. Праховнік Ю.О. Полукаров. – К.: НТУУ «КП» 2012. – 33с.
ДСН 3.3.6042-99. Санітарні норми мікроклімату виробничих приміщень.
Вредные вещества в промышленности. Справочник химиков инженеров и врачей. В Зт.-Л.: Химия 1976 г. – Т.1. – 592с.
СНиП -33-75. Отопление вентиляция и кондиционирование воздуха.
Фарамазов С.А. Охрана труда при эксплуатации и ремонте оборудования химических и нефтеперерабатывающих предприятий С.А. Фарамазов. – М.: Химия 1985. – 224 с.
СНиП 2.04.05.84. Отопление вентиляция и кондиционирование воздуха.
ДБН В.2.5.28-06. нженерне обладнання будинків і споруд. Природне і штучне освітлення. Київ 2006. – 76с.
ДНАОП 0.00-1.31-99. Правила охорони праці під час експлуатації електронно-обчислювальних машин. – Київ 1999. – 28с.
ДСН 3.3.6.037-99. Санітарні норми виробничого шуму ультразвуку та інфразвуку.
ДСН 3.3.6.039-99. Державні санітарні норми виробничої загальної та локальної вібрації
ГОСТ 12.1.038-82 Электробезопасность. Предельно допустимые значения напряжений прикосновения и токов.
ГОСТ 12.4.124. Система стандартов безопасности труда. Средства защиты от статического электричества. Общие технические требование.
Сабарно Р.В. Степанов А.Г. Электробезопасность на промышленных предприятиях. – М.: Медицина 1988. – 336с.
Калунянц К.А. Оборудование микробиологических производств К.А. Калунянц Л.И.Голгер В.Е. Балашов– М.: Агропромиздат 1987. – 397с.
ГОСТ 14202-69. Трубопроводы промышленых предприятий. Опознавательная окраска опознавательные знаки и маркировочные щитки.
Рябов И.В. Пожарная опасность веществ и материалов применяемых в химической промышленности: Справочник. – М.: Химия. – 1970. – 336с.
специфікація.docx
Найменування технічна характеристика обладнання
Об’ємно-ваговий дозатор для подрібненої сировини
Об’ємно-ваговий дозатор для сірчаної кислоти
Гідролізапарат вертикальної циліндричної конструкції футерований кислотостійкими керамічними плитками робочий тиск 16 МПа Корисний об’єм - 30 м3; внутрішній діаметр – 30 м; висота – 86 м; питома продуктивність – 190 – 210 кгм3.
Нержавіюча сталь 12Х18Н10Т
Концентратомір. Межа вимірювання 0 – 3 мгдм3
Манометр. Межа вимірювання 0 – 1 МПа. Клас точності 25
Циклон вертикальний апарат футерований шаром кислотостійкого бетону і оснащений двохлопатевою мішалкою зі швидкістю обертання 5 обхв. Місткість – 60 м3
Випарний апарат плівкового типу з падаючою плівкою футерований керамічними плитками. мність – 8 м3; поверхня теплообміну 100 м2; кількість труб – 195; робочий тиск – 08 МПа
Продовження додатку А
Решофер пластинчатий. Площа поверхні теплообміну 85 м2
Термометр. Межа вимірювання -50 – 550 ºС. Точність ±2 ºС
Випарний апарат плівкового типу з падаючою плівкою футерований керамічними плитками. мність – 8 м3; поверхня теплообміну 100 м2; кількість труб – 195; робочий тиск – 02 МПа
Нейтралізатор футерований кислотостійкими керамічними плитками оснащений вертикальними мішалками з гальмівними лопатками і конічним приводом зі швидкістю обертання 30 обхв. мність 35 м3
Потенціометр зі скляним електродом. Діапазон вимірювання рН – 0 – 14; точність ±02 %
Об’ємно-ваговий дозатор для вапняного молока
Об’ємно-ваговий дозатор для поживних речовин
Насос відцентровий горизонтальний консольний одноступеневий з робочим колесом закритого типу
Відстійник сталевий циліндричний. Діаметр – 12 м; продуктивність 07 м3(годм2); швидкість седиментації – 0025 – 25 мс
Збірник; наповнення – заливанням (самоплив); Обєм – 5м3
Холодильник пластинчатий. Продуктивність – 150 м3год; площа поверхні теплообміну - 65 м2
Дріжджанка оснащена мішалкою зі швидкістю обертання 30 обхв. Об’єм – 150 м3
Термометр. Межа вимірювання -20 – 100 ºС. Точність ±2 ºС
Головний бродильний чан вертикальний циліндричний з конічим дном і сферичною кришкою обладнаний штуцерами для подачі сусла та відводу бражки. мність 300 м3
Хвостовий бродильний чан вертикальний циліндричний з конічим дном і сферичною кришкою обладнаний штуцерами для подачі сусла та відводу бражки. Оснащений скребковою мішалкою встановлену на валу який обертається за допомогою електродвигуна з редуктором швидкість обертання – 5 обхв. мність 300 м3
Сепаратор закритого виконання оснащений станиною барабаном і приймально-вивідним пристроєм (ПВП). Частота обертання барабану – 5100 обхв.; продуктивність 35 м3год; кут нахилу тарілок 55º
Станина – чугун; барабан – титановий сплав АТ-6; ПВП - нержавіюча сталь 12Х18Н10Т
Фільтр герметично закритий сітчастий; діаметр пор 05 мм
Дефлегматор двохсекційний кожухотрубний. Площа поверхні теплообміну – 15 м3
Бражна колона. Діаметр – 1000 мм; висота – 1700 мм; тип тарілок – сітчасті; кількість тарілок – 26; відстань між тарілками – 500 мм; товщина стінки царг – 25 мм; висота царг – 1350 м
Нержавіюча сталь марки 12Х18Н10 алюміній фторопласт силікон
Ректифікаційна колона. Діаметр – 600 мм; висота – 8920 мм; тип тарілок – сітчасті; кількість тарілок – 80; товщина стінки царг – 4 мм; висота царг – 1550 мм
Нержавіюча сталь марки 12Х18Н10Т алюміній
Теплообмінник спіральний.
Робоча температура від -40 ºС до +400 ºС; робочий тиск – 2 МПа; площа поверхні теплообміну 15 м3
Нержавіюча сталь марки 12Х18Н10Т вуглеводнева сталь
Дегідратаційна колона. Діаметр – 800 мм; висота – 1700 мм; тип тарілок – сітчасті; кількість тарілок – 65; відстань між тарілками – 500 мм
Конденсатор. Місткість 01 м3; робочий тиск 06 МПа;продуктивність – 20 м3год; введення пари через сопло діаметром 25 мм
Вступ.docx
Основним завданням при організації виробництва біоетанолу є забезпечення його конкурентоспроможності по відношенню до органічних енергоносіїв. Великотоннажне виробництво паливного етанолу потребує стабільного ринку сировинних ресурсів. Найбільш перспективними культурами для виробництва паливного етанолу в Україні слід вважати цукровий буряк та зернові культури. Але при цьому виникає проблема зменшення площі земель для засіву харчових культур а також проблема утилізації відходів виробництва.
Великі масштаби виробництва біоетанолу висувають певні вимоги до економіки виробництва в першу чергу у вирішенні проблеми вибору сировини та раціонального оформлення технологічного процесу. Крім того ці вимоги направлені на зменшення числа стадій виробництва; укрупнення одиничних потужностей апаратів та установок в цілому; підвищення комплексності використання сировини; створення маловідходних технологічних процесів тощо.
У зв’язку з цим розробка нових економічно вигідних методів виробництва біоетанолу є досить актуальною.
Метою даного дипломного проекту є розробка і проектування технології виробництва біоетанолу з целюлозовмісної сировини.
Завданнями даного дипломного проекту є наступні:
-охарактеризувати целюлозовмісну сировину яка використовується для
-виробництва біоетанолу;
-навести схеми перебігу біохімічних процесів які відбуваються при проведенні технологічного процесу;
-обрати та обрунтувати технологічну схему виробництва біоетанолу із целюлозовмісної сировини;
-спроектувати технологічний процес з визначенням контрольних точок та матеріального балансу виробництва;
-запроектувати ректифікаційну колону в якій відбувається очищення і дистиляція етанолу;
-навести перелік заходів щодо охорони праці та охорони довкілля.
Розділ 2.docx
1.Схема перебігу процесів
Процес виробництва біоетанолу складається трьох послідовних стадій що об’єднані в єдину технологічну схему: гідролізу целюлозовмісної сировини за допомогою розведеної сірчаної кислоти зброджування гідролізату що утворився та ректифікація отриманої бражки.
Рис.2.1. Технологічна схема отримання біоетанолу з деревини [21]
Технологічна схема може дещо відрізнятися при використанні тої чи іншої целюлозовмісної сировини. Найбільш поширена сировина для
гідролізного виробництва етанолу – деревина – являє собою складну систему що складається з целюлози геміцелюлоз лігніну а також невеликих кількостей смол ефірних олій дубильних і фарбувальних речовин. Технологічна схема переробки деревини у етанол зображена на рис.2.1 [21].
1.1. Механізм перетворення основних компонентів деревини під час гідролізу
В макромолекулах полісахаридів елементарні ланки що являються по своїй будові залишками моносахаридів поєднані між собою глікозидними зв’язками. Тому основна мета процесу гідролізу – розщеплення саме глікозидних зв’язків причому ця реакція не повинна супроводжуватись розривом яких-небудь зв’язків в елементарних ланках полісахаридів або вторинними перетвореннями моносахаридів що утворюються.
Лінійні макромолекули целюлози мають постійну будову и складаються з однакових 15-ангідро--D-глюкопіранозних елементарних ланок що з’єднані між собою 14-глікозидними зв’язками (рис.2.2).
Рис.2.2. Хімічна формула макромолекули целюлози [22]
При дії розчину сірчаної кислоти на целюлозу іон гідроксонію може викликати часткове протонування одночасно двох атомів кисню що входять до глікозидного зв’язку та в циклічну структуру елементарної ланки (рис.2.3).
Рис.2.3. Схема протонування аатомів кисню целюлози під дією сірчаної кислоти [22]
У зв’язку з більшою активністю переважно протікає протонування та розщеплення глікозидного зв’язку за схемою що вказана на рис.2.4.
Рис.2.4. Схема протонування та розщеплення глікозидного зв’язку в молекулі целюлози [22]
На першому етапі гідролізу відбувається протонування глікозидного кисню що містить вільну електронну пару з утворенням оксонієвого макроіона що призводить до активації глікозидного зв’язку.
В результаті розщеплення оксонієвого макроіона утворюється частина макромолекули целюлози та макрокарбкатіон (макроіон карбонію або глікозилкатіон) який може знаходитись у рівновазі з оксонієвим іоном. У зв’язку із розподілом позитивного заряду між вуглецевим та кисневим атомами рівноважну систему іонів зазвичай називають карбоксонієвим іоном. При взаємодії карбкатіона з водою утворюється друга частина макромолекули целюлози; продуктом основного гідролізу проміжних продуктів є D-глюкоза. он водню який відщеплюється на останній стадії вступає в реакцію з водою і знову дає іон гідроксонію. Таким чином кислота яка застосовується при гідролізі виконує функції каталізатора вступаючи у взаємодію з проміжними продуктами реакції та звільняючись в кінці процесу [22].
В якості проміжних продуктів гідролізу целюлози утворюється комплекс розчинних в умовах реакції олігосахаридів: целобіоза целотріоза (рис.2.5) целотетраоза целопентаоза целогексаоза та інші
Рис.2.5. Хімічні формули проміжних продуктів гідролізу [23]:
– целобіоза; 2 – целотріоза.
У зв’язку з тим що швидкість гідролізу олігосахаридів набагато більша ніж швидкість гідролізу целюлози то в реакційному середовищі їх вміст дуже незначний та основним продуктом реакції є D-глюкоза. У водних розчинах а саме в гідролізатах D-глюкоза міститься у вигляді рівноважної суміші таутомерних форм утворення яких пов’язане з ізомерією циклів моносахаридів і хіральністю глікозидного центру [23].
Розглянемо механізм гідролізу полісахаридів концентрованими кислотами.
При гідролізі полісахаридів які містяться у деревних відходах та рослинних відходах сільського господарства існує велике різноманіття процесів які протікають при цьому. На рис.2.6 приведена загальна схема перетворень полісахаридів при дії концентрованих кислот здатних етерифікувати ОН-групи.
Набухання полісахаридів. Набухання високомолекулярних полісахаридів (органічне розчинення) супроводжується розривом частини міжмолекулярних зв’язків в результаті проникнення в структуру полімера молекул розчинника або реагента. Набухший полімер можна розглядати як розчин низькомолекулярного компонента у високомолекулярному. При набухання полісахаридів в залежності від їх надмолекулярної структури кількості концентрації та властивостей кислоти можливе поверхневе або міцелярне набухання при поглинання рідини поверхнею міцел і молекулярне або пермутоїдне набухання коли кислота проникає в товщу як неорієнтованих так і високо орієнтованих фракцій.
Рис.2.6. Загальна схема перетворень полісахаридів при обробці кислотами [24]
Набухання целюлози в H2SO4 починаєтьс при її концентрації більше 50 – 55 % в НC максимальне набухання целюлози спостерігається при 22 – 25 ºС. При обробці целюлози 55 – 80%-ною H2SO4 максимальне набухання відмічено при концентрації кислоти %.
Набухання і розчинення полісахаридів рослинної сировини в концентрованих кислотах гальмує лігнін.
Розчинення полісахаридів. Зі зростанням концентрації кислот обмежене набухання переходить в необмежене набухання – розчинення. Розчинення целюлози відбувається при концентрації H2SO4 більше 62 % геміцелюлоз більше 50 – 55 %.
Глибина розчинення полісахаридів зростає зі збільшенням тривалості обробки концентрації кислоти температури. При дії 75 %-ної H2SO4 при 17 ºС целюлоза розчиняється за 15 хв. Зі зростанням температури від 15 до 50 ºС спостерігається різке зростання розчинності целюлози в 62 %-вій H2SO4. Геміцелюлози березової деревини інтенсивно набухають в 50 %-вій H2SO4 і при підвищенні температури до 50 ºС повністю переходять в розчин.
Розчинення полісахаридів при дії концентрованих кислот – це комплекс фізичних та хімічних процесів що протікають одночасно. При набуханні та розчиненні полісахаридів змінюється їх надмолекулярна структура відбувається сорбція кислоти сольватація елементарних ланок макромолекул та їх агрегатів змін полярності та інших властивостей полісахаридів. У розчин переходять не лише макромолекули целюлози але й їх агрегати що є міцними ділянками мікрофібрил які в набухлому стані мають розміри міцел або кристалів. При достатньо високій концентрації целюлози в розчині її макромолекули можуть утворювати трьохмірну сітку.
Поряд з цим в результаті розщеплення глікозидних зв’язків відбувається де полімеризація полісахаридів ОН-групи частково етерифікуються можливе утворення міжмолекулярних комплексів кислоти і полісахарида (адитивних та оксонієвих сполук). Останній процес являється оборотнім і рівновагу в системі можна зсувати в будь-яку сторону змінюючи концентрацію кислоти [24].
Гідроліз глікозидних зв’язків. Пи дії концентрованих кислот процес гідролізу целюлози протікає з утворенням ряду проміжних продуктів:
Під гідроцелюлозою зазвичай розуміють частково гідролізовану целюлозу яка ще зберігає волокнисту структуру. Амілоїд включає полісахариди які випадають в осад з розчину целюлози в концентрованій кислоті після його розбавлення водою. Ці полісахариди відрізняються по своїй структурі та властивостям від природної целюлози і можуть бути віднесені до гідратцелюлози. Якщо після осадження амілоїда у водний розчин що залишився додати етанол то в осад випадуть целодекстрини а розчині залишаться найбільш розчинні олігосахариди зі ступенем полімеризації від 2 до 10 (целобіоза целотріоза тощо) і D-глюкоза.
Розглянемо особливості розщеплення глікозидних зв’язків на прикладі гідролізу целюлози концентрованою сірчаною кислотою.
Безводна H2SO4 (моногідрат) на 995 % складається з недисоційованих молекул а невелика частина дисоціює по двох напрямках:
Йон Н3SO4+ - один з самих сильних донорів протонів. Проте при додаванні навіть невеликих кількостей води переважно відбувається дисоціація кислоти за схемою:
В сірчаній кислоті з концентрацією 683 % коефіцієнт активності іонів водню α=23 та рН=20.
Таким чином з врахуванням високої концентрації іонів гідроксонію є необхідні передпосилання для протонування та розщеплення глікозидних зв’язків полісахаридів при дії концентрованої H2SO4.
При гідролізі полісахаридів концентрованими кислотами відносний вміст води в системі обмежено. Багато авторів вважають що в цих умовах процес гідролізу протікає по бімолекулярному механізму тобто лімітуючою стадією являється приєднання води по місцю розщеплення глікозидних зв’язків. Однак результати кінетичних досліджень виконаних з урахуванням сольватаційного ефекту показують що при гідролізі полісахаридів концентрованими кислотами розщеплення глікозидних зв’язків протікає по мономолекулярному механізму тобто аналогічно гідролізу розведеними кислотами.
У зв’язку із значною концентрацією іонів гідроксонію досягається висока швидкість протонування глікозидних зв’язків з утворенням оксонієвих макроіонів при дії концентрованих кислот. Проте через низьку температуру процеса швидкість розщеплення глікозидних зв’язків нижче ніж при дії розведених кислот. Через водовіднімаючі властивості концентрованої H2SO4 реакція приєднання гідроксилу до іона карбоксонію являється повільною та оборотною. В залежності від концентрації сірчана кислота може або виводити з системи або віддавати її для гідролізу.=
При підвищенні температури або збільшенні тривалості витримки реакційної суміші зростає число розірваних глікозидних зв’язків. Якщо суміш розвести водою після нетривалої витримки без термообробки то розкладання оксонієвих сполук відбувається без розриву глікозидних зв’язків [25].
Етерифікація вуглеводів. Окрім утворення порівняно нестійких оксонієвих сполук при дії концентрованої сірчаної кислоти на полісахариди відбувається часткова етерифікація ОН-груп елементарних ланок. А саме при дії цієї кислоти на целюлозу переважно етерифікується ОН-група при шостому вуглецевому атомі елементарної ланки
Глибина етерифікації порівняно невелика: при дії 75 – 80%-вої H2SO4 середня ступінь етерифікації =20 тобто етерифікована одна ОН-група кожного п’ятого елемента ланки целюлози.
Окрім часткової етерифікації ОН-груп елементарних ланок допускають можливість утворення оксонієвих сполук по глікозидним зв’язкам
В результаті ацидолізу глікозидний зв’язок розщеплюється з утворенням глікозиду. Цей процес можна віднести до глікозидуванню.
Сірчана кислота у вигляді оксонієвих сполук може також з’єднуватись з ОН-групами елементарних ланок полісахаридів реакційної суміші. Міцність таких зв’язків невелика - при збільшенні кількості води в системі вони легко розщеплюються. При промиванні осаду полісахаридів вони практично повністю звільняються від кислоти.
При дії концентрованих кислот на полісахариди відбувається достатньо глибоке зв’язування кислот з вуглеводами [26].
Процес реверсії. Характерною особливістю процесу обробки полісахаридів концентрованими кислотами є протікання реакції кислотної реверсії. Протіканню реверсії сприяють підвищена концентрація моносахаридів в розчині наявність кислотного каталізатора дефіцит в ситемі води який може зростати в присутності водовіднімаючої речовини ( наприклад концентрованої H2SO4). Для протікання реверсії як правило необхідна концентрація моносахаридів ≥ 2 %.
Кислотна реверсія – це процес поліконденсації відновлюючи цукрів по реакції Фішера з утворенням олігосахаридів або полісахаридів будова яких суттєво відрізняється від будови вихідного полісахариду. У вихідній целюлозі усі елементарні ланки однакові і по своїй будові являються 15-ангідридо--D-глюкопіранозами. Глюкоза яка утворюється при гідролізі целюлози в результаті муторації перетворюється у рівноважну систему α- -піранозних та α- -фуранозних ізомерів які при реверсії взаємодіють один з одним з утворенням відповідних глікозидних зв’язків.
Утворення цих сполук відбувається вірогідно за участі карбкатіонів з відкритим ланцюгом (рис.2.7).
Рис.2.7. Схема муторації глюкози [27]
Процес реверсії може протікати як шляхом конденсації молекул глюкози так і приєднанням глюкози до присутніх в реакційому середовищі олігосахаридів. При цьому утворюються продукти реверсії макромолекули яких побудовані за участі 14- та 16-зв’язків. Можливі поліконденсаційні процеси і за участі олігосахаридів наприклад целобіози. При дії концентрованих кислот на полісахариди з часом встановлюється рівновага між реакціями гідроліз-реверсія. З підвищенням температури швидкість реверсії зростає швидше ніж швидкість гідролізу.
Продукти кислотної реверсії глюкози відрізняються від целюлози не тільки за хімічною будовою але також більш низьким ступенем полімеризації та ступенем орієнтації макромолекул підвищеною розчинністю та реакційною здатністю [27].
нверсія. В результаті одночасного протікання всіх процесів що розглядалися вище при гідролізі полісахаридів концентрованими кислотами отримується складна реакційна суміш яка складається з проміжних продуктів гідролізу та продуктів реверсії які в свою чергу частково етерифіковані. Вміст моносахаридів в такій суміші невеликий. Для перетворення компонентів реакційної суміші в моносахариди проводять процес реверсії тобто додатковий гідроліз розведеною кислотою при температурі кипіння. При цьому відбувається розрив глікозидних зв’язків та відщеплення складно ефірних груп.
Таким чином гідроліз концентрованими кислотами можна розглядати як метод перетворення важкогідролізованих полісахаридів (в основному целюлози) в легкогідролізований стан.
Принципіальною особливістю гідролізу рослинної сировини концентрованими кислотами являється можливість отримання виходу моносахаридів близького до теоретичного. Процес перетворення полісахаридів в легкогідролізований стан під дією концентрованих кислот проводять при температурі 25 – 40 ºС процес інверсії при температурі близько 100 ºС. За цих параметрів розпад моносахаридів практично не протікає що й обумовлює їх високий вихід.
Завдання підвищення виходу цільових продуктів із сировини що переробляється надзвичайно актуальна у зв’язку з чим гідроліз рослинної сировини концентрованими кислотами має перспективне значення.
При гідролізі полісахаридів рослинних тканин розбавленими мінеральними кислотами біохімія процесу перетворення полісахаридів такий же але при нормальній температурі реакція утворення моносахаридів практично не протікає. Однак при підвищенні температури до 100 °С і вище гідроліз полісахаридів помітно прискорюється причому це прискорення різне для геміцеллюлоз і целюлози. Так геміцелюлози в цих умовах переходять в розчин і швидко гідролізуються до моносахаридів в гомогенному середовищі. Велика швидкість гідролізу геміцелюлози пояснюється вільним доступом каталізатора до кожної макромолекули полісахариду. Целюлоза при гідролізі розведеними кислотами поводиться зовсім інакше. Вона не розчиняється у воді навіть при температурах вище 200 °С. Тому реакція гідролізу целюлози протікає на обмеженій доступній поверхні її структурних елементів . З цієї причини целюлоза гідролізується в середовищі розбавлених кислот значно повільніше ніж геміцелюлози [28].
1.2. Біохімія спиртового бродіння
При спиртовому бродінні відбуваються ферментативні перетворення гексоз них моносахаридів в анаеробних умовах які призводять до їх неповного окиснення і супроводжуються виділенням енергії. В цих окисних реакціях акцептором водню являється не кисень а проміжні продукти перетворень вуглеводів наприклад оцтовий альдегід. Біохімічні процеси анаеробіозу протікають всередині дріжджової клітини куди через напівнепроникну оболонку надходять моносахариди та необхідні неорганічні поживні речовини. Продукти метаболізму – етанол двоокис вуглецю та домішки виділяються з клітини в зброджуване сусло [29].
Розглянемо основні стадії хімізму спиртового бродіння на прикладі перетворень D-глюкози яка являється основним вуглеводним компонентом гідролізних субстратів (рис.2.8).
Фосфорилювання D-глюкози відбувається за участі в якості каталізатора фермента гексокінази. Каталітична активність цього фермента підвищується в присутності йонів магнію. Переносником групи – РО3Н2 є три фосфат аденінової кислоти (аденозинтрифосфат – АДФ). D-глюкоза в цій реакції етерифікується в піранозній формі; її реакційна здатність при цьому зростає. Швидкість утворення фосфорного ефіру D-глюкози визначає загальну швидкість зброджування.
зомеризація глюкозо-6-фосфата у фруктозо-6-фосфат протікає за участі ферменту глюкозофосфатізомерази. Рівноважна система яка отримала назву ефіру Емдена складається на 70 – 75 % з фосфату глюкози і на 30 – 25 % з фосфату фруктози.
Рис.2.8. Схема хімізму спиртового бродіння [30]
Етерифікація ОН-групи при першому С-атомі фруктозо-6-фосфату відбувається за участі АТФ як переносника залишку ортофосфорної кислоти та фермента фосфофруктокінази в якості каталізатора. Відкриття піранозного циклу призводить до утворення лабільної оксоформи фруктозо-16-дифосфату.
В результаті оборотної реакції при дії альдолази розщеплюється С-С-зв’язок (реакція десмолізу) в дифосфаті фруктози та утворюються дві тріоди: фосфодіоксиацетон і 3-фосфогліцериновий альдегід які за участі фермента тріозофосфатізомерази здатні до взаємних перетворень. Основним компонентом рівноважної системи є 3-фосфогліцериновий альдегід який бере участь в подальших перетвореннях. В індукційний період бродіння (до утворення альдегіду) в якості побічного продукту за участі альдегідмктази утворюється фосфогліцерин а потім гліцерин.
Перетворення 3-фосфогліцеринового альдегіду у 13-дифосфогліцеринову кислоту протікає за участі неорганічної ортофосфорної кислоти за присутності тріозофосфатгідрогенази. У розрахунку на 1 молекулу глюкози необхідна 1 молекула кислоти. Переносником водню в окисному процесі є нікотинамідаденіннуклеотид (НАД) який як кофермент анаеробної дегідрогенази має властивість віднімати водень від фосфогліцеринового альдегіду.
Утворення 3-фосфогліцеринової кислоти протікає за участі фосфогліцераткінази; акцептором залишку фосфорної кислоти є АДФ який при цьому перетворюється в АТФ.
зомеризація 3-фосфогліцеринової кислоти в 2-фосфогліцеринову кислоту відбувається за участі фермента фосфогліцеромутази.
Дегідратація кислоти призводить до утворення фосфоенолпфровиноградної кислоти. Каталізатором слугує енолаза. Максимальна активність цього ферменту при рН 52 – 55; при рН 42 відбувається агрегатація макромолекул фермента і при рН 3 – 4 їх денатурація.
Енолпіровиноградна кислота утворюється в результаті дефосфорилювання її фосфату при дії піруваткінази.
В результаті ізомеризації нестійка енолпіровиноградна кислота перетворюється в її кето форму – піровиноградну кислоту яка відрізняється більш високою стабільністю.
Декарбоксилювання піровиноградної кислоти за участі піруватдекарбоксилази призводить до утворення оцтового альдегіду.
Відновлення ацетальдегіду в етанол протікає за участі НАД2Н+ та фермента алкогольдегідрогенази. При цьому кофермент регенерується шляхом окислення в НАД.
По такій же схемі відбувається біосинтез етанолу і з інших гексоз гідролізного субстрату – D-манози та D-галактози.
Зі схеми на рис.2.3 видно що для нормального протікання спиртового бродіння необхідна наявність в субстраті неорганічного фосфорного живлення і акро- та мікроелементів що активують ферменти [31].
Сумарне стехіометричне рівняння спиртового бродіння встановлене Гей-Люссаком:
Може бути представлене з урахуванням ролі АТФ у життєвих процесах наступним чином:
Зміна вільної енергії в цьому процесі складає більше 200 кДжмоль у тому числі 834 кДжмоль вловлюється у АТФ і використовується для здійснення життєвих функцій мікроорганізмів. Залишки фосфорної кислоти в АТФ приєднані макроергічними зв’язками при розщепленні яких звільняється приблизно в 3 рази більше енергії ніж при розщепленні звичайних хімічних зв’язків. Звільнення енергії макроергічних зв’язків відбувається при переносі – РО3Н2 груп а не шляхом гідролізу при якому вільна енергія переходить в теплову.
В анаеробних умовах відбувається повільне розмноження дріжджів. При біосинтезі білка та інших компонентів клітин крім енергії витрачається частина поживних речовин субстрату [32].
При спиртовому бродінні в якості домішки утворюється гліцерин вихід якого зростає в присутності бісульфіта або в лужному середовищі. У складі спиртової бражки міститься ацетальдегід який є проміжним продуктом біосинтезу етанолу. Серед багаточисленних легколетких домішок бражки знайдені альдегіди прості і складні ефіри кетони спирти кислоти та інші сполуки. Значний вихід ефірів при спиртовому бродінні пов’язаний з протіканням реакцій етерифікації що каталізується ферментами естеразами. Основний компонент ефірної фракції – етилацетат утворюється при взаємодії етанолу та оцтової кислоти:
В процесі обміну речовин головним чином при розмноженні мікроорганізмів в якості побічних продуктів бродіння утворюються вищі спирти. х вихід зростає за наявності амінокислот які потрапляють в субстрат з вихідної сировини а такод при автолізі відмерлих дріжджових клітин. В умовах бродіння відбувається декарбоксилування та гідролітичне дезамінування амінокислот з утворенням пропанову ізобутанолу амілолу ізоамілову та інших спиртів які при ректифікції утворюють фракцію сивушних масел.
Основним компонентом сивушних масел є ізоаміловий спирт який утворюється з лейцину:
На першій стадії відбувається процес пере амінування – обмін аміногрупою між амінокислотою 1 та кетокислотою 2 при цьому утворюється аланін 3 та ізопропілвиноградна кислота 4 декарбоксилування якої призводить до утворення ізовалеріанового альдегіду 5 при відновленні якого утворюється ізоамілол 6. Усі стадії процесу протікають за участі ферментів [33].
Отже при виробництві біоетанолу з целюлозовмісної сировини відбувається 2 основні біохімічні процеси: гідроліз целюлози за участі кислоти з утворенням моносахаридів і зброджування моносахаридів за допомогою спиртових дріжджів.
2.Характеристика біоетанолу
Біоетанол – це рідке спиртове паливо яке виробляється з сільськогосподарської продукції що містить крохмаль та цукор наприклад із кукурудзи зернових або цукрової тростини. На відміну від спирту з якого виготовляються алкогольні напої паливний етанол не містить води та виготовляється шляхом скороченої дистиляції (дві ректифікаційні колони замість п’яти) тому містить ще метанол та сивушні масла а також бензин що робить його не придатним для пиття.
Відповідно до Директиви Ради 200330 С вропейського парламенту та Ради від 8 травня 2003 року про використання біопалива або іншого відновлювального палива для транспорту: Біоетанол – це спирт етиловий зневоднений виготовлений з біомаси або спирту етилового-сирцю для використання як біопалива. Він призначений для виготовлення палива моторного сумішевого або добавок на основі біоетанолу – біокомпонентів моторного палива отриманих шляхом синтезу із застосуванням біоетанолу або змішуванням біоетанолу з органічними сполуками та паливом одержаним з вуглеводної сировини в яких вміст біоетанолу відповідає вимогам нормативних документів та які належать до біопалива [34].
У ДСТУ 4839:2007 «Бензини автомобільні підвищеної якості» встановлена максимальна об'ємна частина кисневмісного органічної сполуки етанолу – 5 % [35].
За результатами статичних напрацювань підприємств спиртової промисловості та науковців УкрНДспиртбіопрод фізико-хімічні показники біоетанолу унормовано до наведених у таблиці 2.1. Якість продукції відповідає вимогам ТУ У № 15.9-30219014-010:2007 і Технологічного регламенту №00375280-001-2010 виробництва біоетанолу (антидетонаційної кисневмісної присадки до бензинів) [36].
Якісні показники біоетанолу [36]
Зовнішній вигляд та колір
Прозора безбарвна рідина або світло жовтого забарвлення
Густина за температури (20±01)0С кгм3
Об'ємна частка води % не більше
Масова концентрація сухого залишку мгдм3 не більше
Об’ємна частка спирту етилового (органічних кисневмісних сполук) % не менше
Об’ємна частка метанолу % не більше
Об'ємна частка циклогексану % не більше
Масова частка кислот у перерахунку на оцтову кислоту % не більше
Масова концентрація вищих спиртів С3- С5 гдм не більше
Об’ємна частка бензину (вуглеводнів) %
Масова частка сірки мгкг не більше
Масова концентрація фосфору мгдм3 не більше
Масова частка міді мгкг не більше
Масова концентрація неорганічних хлоридів мгдм3 не більше
Біоетанол і компонент моторного палива альтернативний (КМПА) з об'ємним вмістом води 02 % об'ємним вмістом бензину 1 % і МТБЕ 01-0.5 % вмістом вищих спиртів 12 гдм ³ і кислотністю не більш 00025 % (мас.) є ідеальною кисневмісною органічною добавкою до бензинів.
Бензини з оксигенатів характеризуються поліпшеними миючими властивостями характеристиками горіння при згорянні утворюють менше оксиду вуглецю та вуглеводнів. Спільним для всіх оксигенатів є те що їх теплота згоряння нижча ніж вуглеводнів тому їх кількість у паливі обмежена можливістю роботи двигуна без додаткового регулювання.
При використанні біоетанолу в якості кисневмісної антидетонаційної присадки помітно покращуються миючі та екологічні властивості бензину відбувається очистка паливних систем двигунів.
Найбільша економічна доцільність досягається при виробництві високооктанових бензинів А-95 і А-98 так як вартість присадки співрозмірна з вартістю бензину А-92.
У разі надмірного введення в паливо води (більше 05% мас.) Можливе помутніння палива [37].
Отже біоетанол має такі технічні характеристики які дозволяють використовувати його в якості палива або як добавку до бензину яка покращує його якість. Головною особливістю і вимогою до біоетанолу є низький вміст води в ньому який має бути не більше 02 %.
технолог схема-1.cdw

Розділ 3.docx
1.Характеристика сировини і матеріалів
Дані про стан об’єм склад характеристика сировини та матеріалів що використовуються у виробництві представлені у таблиці 3.1.
Характеристика сировини матеріалів та напівпродуктів [38 39]
Категорія і номер НТД згідно якого перевіряється сировина
Показники що обов’язкові для перевірки та їх нормативне значення
ГОСТ 18320-78 «Опилки древесные технологические для гидролиза. Технические условия» ГОСТ 15815-83 «Щепа технологическая. Технические условия»
Вміст кори (не більше 8%) вміст гнилі (5%) вміст мінеральних домішок (05%) розміри частинок (1 – 30 мм) вміст металічних домішок (не допускається)
Анаеробне зброджування для отримання біоетанолу
ГОСТ 2184-77 «Кислота серная техническая. Технические условия»
Масова доля моногідрату (Н2SO4) ( не менше 925%) масова доля заліза (не більше 002%) колір (не більше 6 балів)
Гідроліз целюлозовмісної сирвини
Продовження таблиці 3.1
ГОСТ 9179-77 «Известь строительная. Технические условия»
Вологість (не більше 5%) густина (32) насипна густина (077 – 107 тм3) СО2 (не більше 5)
Нейтралізація гідролізату
ГОСТ 17790-78 «Суперфосфат аммонизированный из фосфоритов Каратау. Технические условия»
Масова доля Р2О5 (15%) вільної кислоти (05%) води (не більше 3%) азоту (не менше 15%)
5. Посівний матеріал дріжджів
ГОСТ 20083-74 «Дрожжи кормовые гидролизные. Технические условия»
Колір (від світло-жовтого до коричневого запах (властивий дріжджам) масова доля вологи (не більше 100%) білку (не менше 41%) золи (не більше 100%)
Зброджування деревного сусла
ГОСТ 31077-2002 «Топлива для двигателей внутреннего сгорания. Неэтидированный бензин. Технические условия» ГОСТ 8507-80 «Бензин для промішленно-технических целей. Технические требования»
Колір (прозорий) вміст сірки (не більше 0025%) густина (073 – 081)
Абсолютизація спирту
Наявність і кількість розчинених у ній газів
Приготування пари подача в сорочки апаратів миття обладнання
ГОСТ 25747-83 «Фильтры рукавные и карманные. Типы и основные параметры»
Розрідження у фільтрі (не більше 5000 Па) тиск повітря для регенерації (не більше 001 МПа) концентрації пилу на вході фільтра (не більше 30 гм3)
Гідроліз целюлозовмісної сировини
ГОСТ 55761-2013 «Замесы сусло бражка из пищевого сырья. Определение массовой концентрации катионов анионов неорганических и органических кислот методом капиллярного электрофорез»
рН (46 – 52) температура (30 – 30 ºС) вміст фурфуролу (не більше 003%)
Нейтралізація і охолодження гідролізату
ГОСТ 55792-2013 «Бражка из пищевого сырья. Газохроматографический метод определения содержания летучих органических примесей»
Вміст спирту (не більше 3 – 8 %) сухих речовин (4 – 10 %) вуглекислого газу (1 – 15 гл)
2.Опис технологічного проекту
ДР 1. Санітарна підготовка виробництва
Перед запуском виробництва необхідно провести підготовку виробничого персоналу до роботи та обладнання до експлуатації.
ДР 1.1. Підготовка персоналу
Перед початком роботи виробничий персонал повинен пройти санітарно-медичне обстеження та навчання повинен отримати засоби індивідуального захисту тощо.
ДР 1.2. Перевірка обладнання на герметичність
Для гідравлічної перевірки посудин використовується вода з температурою 15 – 25 С. При заповнені посудини водою повітря видаляється з внутрішніх порожнин. Швидкість підйому тиску не повинна перевищувати 05 МПа за хвилину. Надлишковий тиск становить 015 - 02 МПа. Час витримки посудини під пробним тиском 20 хв. Візуально перевіряється наявність негерметичних зварних швів за місцем протікання води. Після проведення гідравлічного випробування вода повністю видаляється з посудин. Водою для перевірки на герметичність відбувається одночасно миття обладнання. Дезінфекція обладнання стерилізація не є необхідною адже процес проходить в нестерильних умовах [40].
ДР 2. Підготовка технічної води.
Технічну воду для охолодження набирають з річки ця вода нефільтрована і скидається назад у річку після використання. Воду для використання на стадіях технологічного процесу у якості агенту попередньо фільтрують.
ДР 3. Підготовка пари.
Водяна пара використовується для підвищення температури деяких процесів. ї утворення відбувається у спеціальних котлах при тиску 40 атм. Пару з високим тиском передають через турбіну когенерації електрики щоб подавати пару низького тиску в 5 атм. для більшості технологічних стадій [41].
ДР 4. Приготування посівного матеріалу дріжджів.
ДР 4.1. Підготовка поживного середовища (сусла).
Набирають сусло температурою 55 – 58 °С додають в якості азотистого живлення солодове молоко і витримують від 1 до 2 год для оцукрювання крохмалю солоду. Після чого температуру підвищують до 75 °С пастеризують сусло протягом 30 хвилин і охолоджують до 30 °С.
Потім в охолоджене сусло додають розчин сірчаної кислоти до кислотності рН=38 – 40. Приготоване сірчанокисле сусло охолоджують до 30 °С стерильно набирають в пробірку і вносять музейну культуру дріжджів.
ДР 4.2. Вирощування дріжджів.
При нормальній роботі заводу чисту культуру дріжджів виводять приблизно один раз в рік зазвичай з пуском заводу іноді рідше.
Чисту культуру дріжджів з пробірки переводять в колбу з дробно пастеризованим солодовим суслом об'ємом 200 мл з неї в бутель з 2 л пастеризованого виробничого сусла а потім в бутель з 10 – 15 л такого ж сусла в збірник з 500 л сусла і нарешті в дріжджовий апарат (головний бродильний чан). Температура процесу 25 – 30 °С рН=35 – 40 [42].
ДР 5. Підготовка сировини
Технологічна схема (рис.3.1) передбачає підготовку привезеної
подрібненої сировини – тирси і технологічної тріски і переробку технологічних дров. Постачання сировини здійснюється автомобільним і залізничним транспортом і за допомогою конвеєрів з сусідніх лісопильних і деревообробних підприємств.
Рис.3.1. Технологічна схема підготовки деревної сировини [43]:
– автомобільні терези; 2 – залізничні терези; 3 – конвеєрні терези; 4 – консольно-козлові крани; 5 – майданчик розвантажування автотранспорту; 6 – штабелі довгомірної деревини; 7 – купа короткомірної деревини; 8 – пристрій для роз’єднання пачок колод; 9 – тарільчатий живильник; 10 – конвеєр коротокомірної деревини; 11 – конвеєр довгомірної деревини; 12 – мірник об’єму круглих лісо матеріалів; 13 – металошукач; 14 – лісонакопичувач; 15 – перевантажувач; 16 – ножова дробарка машина; 17 – багаторізцева дробарка машина; 18 – буророзпушуюча установка; 19 – розвантажувачі сипучих матеріалів; 20 – відкритий склад тирси; 21 – відкритий склад тріски; 22 – пристрій попередньої очистки; 23 – залізовідокремлювач; 24 – каменевловлювач; 25 – дезінтегратор крупних включень; 26 – сортування; 27 – дезінтегратор крупної фракції; 28 – склад підготованої тирси; 29 – склад підготованої тріски.
Кількість сировини що надходить заміряють за допомогою автомобільних 1 залізничних 2 і конвеєрних 3 терезів. Вивантаження технологічних дров проводять консольно-коаловими 4 або мостовими кранами. Довгомірну деревину укладають в штабелі 6 короткомірну – в купи 7. Привезену подрібнену сировину розвантажують за допомогою розвантажувачів сипучих матеріалів 19 і зберігають на відкритих складах 20 21.
ДР 5.1. Попередня обробка і подрібнення деревини
Після пристрою для роз'єднання пачок колод 8 технологічні дрова поштучно конвеєром 11 подаються в багаторізцеву дробарну машину 17. Пристрій для заміру круглих лісоматеріалів 12 і металошукач 13 зблоковані з приводом конвеєра що дозволяє фіксувати і видаляти з потоку за допомогою перевантажувача 15 колоди підвищеного діаметру і колоди з металевими включеннями.
Короткомірну деревину з купи 7 за допомогою грейферного крана подають в тарільчастий живильник 9 потім конвеєром 10 в ножову дробарну машину 16. Тріска з дробарних машин направляється на сортування.
Попереднє очищення подрібненої сировини від крупнокускових деревних металевих і мінеральних включень проводять на пристроях 22. На каменевловлювачах 24 проводиться гідравлічне очищення крупнокускових включень від важких домішок які видаляються у відвал; деревина на дезінтеграторі 25 подрібнюється в тріску.
ДР 5.2. Сортування сировини
Всі три технологічних сировинних потоки (тріску власної рубки привізну тріску і тирсу) піддають роздільному сортуванню на ситових сортувальних машинах 26 на яких відокремлюється велика фракція з розміром частинок більше 30 - 40 мм. Ця фракція піддається повторному подрібненню на дезінтегрувальному пристрої 27 (дробарній машині дезінтеграторі або молотковій дробарці).
Відсортована кондиційна сировина зберігається на закритих складах 28 29. Місткість бункерів цих складів повинна забезпечувати 1 - 2 - змінний запас сировини. Бункери повинні мати розвантажувачі з регульованою продуктивністю для подачі на гідроліз сировинної суміші з заданим співвідношенням [43].
ДР 6. Приготування розчину розведеної сірчаної кислоти.
ДР 6.1. Підігрів води
Теплота яка міститься в парі який виходить з випарників 6 (В-6) та 8 (В-8) (рис.3.2) використовуються для підігріву води яка надходить у змішувач 17.
Рис.3.2. Схема приготування розведеної сірчаної кислоти і її подачі на гідроліз [44]:
– транспортер; 2 – направляюча воронка; 3 – гідролізапарат; 4 – фільтр; 5 7 9 10 12 14 21 23 25 28 – труби; 6 8 – випарники гідролізату; 11 13 – решофери; 15 – насос; 16 – бак оборотної води; 17 – змішувач води з кислотою; 18 – кислотний насос; 19 – мірник кислоти; 20 – клапан; 22 –
циклон для лігніну; 24 – транспортер для лігніну; 25 – мішалка; 27 – водонагрівальна колона; 29 – диски; 30 – вагомір; 31 – бокові дверцята.
Для цієї цілі з баку 16 оборотної води насосом 15 теплу воду отриману з ректифікаційного відділу гідролізного заводу подають в ре шофер низького тиску 13 де вона нагрівається з 60 - 80 ºС до 100 – 110 ºС. Потім по трубі 12 підігріта вона надходить в решофер високого тиску 11 де парою при температурі 130 – 140 ºС нагрівається до 120 – 130 ºС. Далі температуру води підвищують до 180 – 200 ºС у водонагрівальній колоні 27. Остання представляє собою вертикальний сталевий циліндр з днищем та кришкою розрахованими на робочий тиск 13 – 15 атм.
Пара у водонагрівальну колонку подається по вертикальній трубі 26 на кінці якої закріплені 30 горизонтальних дисків 29. Пара з труби 26 проходить крізь отвори мі окремими дисками в колону заповнену водою. Остання безперервно подається в колону через нижній штуцер змішується з парою нагрівається до заданої температури і по трубі 28 надходить в змішувач 17.
ДР 6.2. Підігрів розчину сірчаної кислоти
Розчин сірчаної кислоти готують шляхом змішування у кислотостійкому змішувачі 17 перегрітої води що подається по трубі 28 з холодною концентрованою сірчаною кислотою яка надходить з мірного бачка 19 через поршневий кислотний насос 18 (рис.3.2). Для приготування розчину концентрацією 05 – 07% використовують приблизно 115 м3 води та 37 л концентрованої сірчаної кислоти .
Оскільки холодна концентрована сірчана кислота слабко піддає корозії залізо та чавун ці метали широко використовують для виготовлення баків насосів трубопроводів які призначені для її зберігання та транспортування до змішувача. Аналогічні матеріали застосовуються і для підводу перегрітої води до змішувача. Для захисту стінок змішувача від корозії застосовують фосфористу бронзу графіт або пластичну масу – фторопласт 4. Останні два використовуються для внутрішньої футеровки змішувачів і дають найкращі результати [44].
ТП 7. Гідроліз деревини
Подрібнена сировина що складається з деревини хвойних і листяних порід зі складу через об’ємно-ваговий дозатор Д-1 подається у верхню горловину гідролізапарату Г-3 яка герметично закривається автоматизованою кришкою. При такому методі завантаження в 1 м3 гідролізапарату поміщається близько 135 кг тирси або 145 – 155 кг тріски у перерахунку на абсолютно суху деревину.
Гідролізапарат представляє собою вертикальний сталевий циліндричний апарат з верхнім та нижнім конусами і горловинами. Внутрішня поверхня гідролізапарату покрита кислотостійкими керамічними плитками що закріплені на шарі бетону товщиною 80 м Шви між плитками заповнюються кислотостійкою замазкою. Верхня та нижня горловини гідролізапарату з внутрішньої сторони захищені від дії гарячої розведеної сірчаної кислоти шаром кислотостійкої бронзи. Корисний об’єм гідролізапарату становить 30 м3. Внутрішній діаметр гідролізапарату складає 30 м а висота – 86 м. Питома продуктивність гідролізапарату з такими габаритами 190 – 210 кгм3.
В гідролізапараті вмонтовані перфоровані кислотостійкі фільтри які розташовуються як в конічній так і в циліндричній частині апарату. До нижньої горловини приєднаний швидкодіючий клапан з дистанційним управлінням який приводиться до дії водою під тиском до 20 кгссм2 і призначений для вивантаження лігніну з апарату через видувну трубу.
Гідролізапарат розрахований на робочий тиск 16 МПа. Для контролю тиску простір над верхньою кришкою апарату з’єднується з вказівним та самопишучим манометром КП-3.2. Оптимальна температура роботи гідролізапарату – 180 ºС при концентрації сірчаної кислоти С≤09 %. Так як температура в гідролізапараті неоднакова по його висоті то постійний її контроль відсутній. Температуру наближено оцінюють по температурі кислоти що подається і тиску у верхній частині гідролізапарату. Концентрацію кислоти контролюють за допомогою концентратоміра КП-3.1.
По закінченню завантаження сировини вміст гідролізапарату підігрівається гострою парою що надходить в нижній конус через штуцер. Як тільки досягається температура 150 – 170 ºС в гідролізапарат через об’ємно-ваговий дозатор Д-2 у верхній частині апарату починає надходити 05 – 07 %-ва сірчана кислота нагріта до 170 – 200 ºС. Гідролізат який при цьому утворюється через фільтр надходить у трубопровід по якому подається на наступну стадію. Трубопроводи для гідролізату виготовляють з червоної міді та латуні. Арматура що складається з вентилів та клапанів виготовляється з фосфористої або паспортної бронзи.
Вивантаження лігніну проводиться за рахунок підвищеного тиску в гідролізапараті (06 – 07 МПа) і скипання рідини при відкритті швидкодіючого клапана в нижньому конусі апарату. Лігнін при цьому направляється в циклон Ц-4 який представляє собою вертикальний сталевий апарат об’ємом 60 м3 оснащений боковими дверцятами і двохлопатевою мішалкою зі швидкістю обертання 5 обхв яка допомагає при вивантажені лігніну з дна циклону на транспортер. Для запобігання корозії внутрішня поверхня циклонів іноді захищається шаром кислотостійкого бетону.
Цикл безперервної роботи гідролізапарату від завантаження сировини до вивантаження лігніну становить 2 – 5 годин. Після цього в апарат завантажують нову порцію деревної сировини [45].
ТП 7.1. Випарювання гідролізату
Випарні апарати В-5 та В-7 представляють собою типові плівкові випарні апарати з падаючою плівкою. Це сталеві апарати ємністю 8 м3 з поверхнею теплообміну 100 м2 при кількості труб 195 що працюють під тиском і футеровані зсередини керамічними плитками як і гідролізапарат. В даних апаратах внаслідок конденсації вторинної пари на поверхні змійовиків збільшується рушійна сила процесу; усувається рух вторинної пари по довжині труби що дозволяє збільшити продуктивність апарату та забезпечити великі навантаження при мінімальному гідравлічному опорі [46].
Гідролізат температурою 170 – 180 ºС по трубопроводу від гідролізапарату Г-3 подається через штуцер у верхнюю частину випарного апарату високого тиску В-5. У цій частині випарника ємністю 20 м3 є кришка. У випарнику підтримується тиск на 04 – 05 МПа нижче ніж в гідролізапараті. Завдяки цьому гідролізат який потрапляє до нього миттєво скипає частково випарюючись і охолоджується до 130 – 140 ºС. Пара що утворилася відділяється від крапель гідролізату і по трубі надходить в решофер (теплообмінник) Р-6 де конденсується.
Частково охолоджений гідролізат з нижньої частини випарника В-5 по трубі надходить у випарник низького тиску В-7 де охолоджується до 105 – 110 ºС в результаті скипання при більш низькому тиску який зазвичай не перевищує 02 МПа. Пара що утворилася при цьому по трубі подається в другий решофер Р-8 де також конденсується. Конденсати з решоферів Р-6 та Р-8 містять 02 – 03 % фурфуролу який надходить на стадію ЗВ 11.1. Решофери Р-6 та Р-8 представлені пластинчатими теплообмінниками з площею поверхні теплообміну 85 м2.
Контроль за температурою та тиском у решоферно-випарному вузлі здійснюється за допомогою датчиків температури КП-6.1 КП-8.1 і манометрів КП-5.1 КП-7.1 відповідно [47].
ТП 8. Нейтралізація кислого гідролізату
Процес нейтралізації відбувається в двох послідовно з’єднаних нейтралізаторах Н-9 та Н-10 які мають однакову будову. Нейтралізатори мають ємність 35 м3 і представляють собою сталевий бак футерований кислотостійкими керамічними плитками і оснащений вертикальними мішалками з гальмівними лопатками і конічним приводом закріпленими нерухомо на стінках бака.
Кислий гідролізат з рН= 1 – 12 та температурою t= 95 – 98 ºC від випарника В-7 по трубі безперервно подається в перший нейтралізатор Н-9 через штуцер вгорі апарату куди одночасно надходить вапняне молоко через дозатор Д-11. Суміш що утворилася по трубопроводу подається на другу ступінь нейтралізації до поз. Н-10 куди через об’ємно-ваговий дозатор одночасно додають поживні солі (наприклад суперфосфати апатити).
Контроль за повнотою нейтралізації проводять шляхом вимірювання концентрації іонів водню за допомогою потенціометрів з скляним електродом КП-9.1 КП-10.1. Потенціометр безперервно занотовує рН гідролізату і автоматично регулює його заданих межах посилаючи електричні імпульси реверсивному мотору з’єднаному з запірною арматурою на трубі яка подає вапняне молоко в перший нейтралізатор. В нейтралізаторах порівняно швидко протікає реакція нейтралізації і відносно швидко – процес кристалізації гіпсу з пересиченого розчину. Тому швидкість протікання рідини через нейтралізаторну установку обумовлена другим етапом нейтралізації який відбувається в нейтралізаторі Н-10 потребує для свого завершення 30 – 40 хв [48].
ТП 9. Відстоювання нейтралізату
Рідина разом з осадом із нейтралізатора Н-10 який містить 09 – 11 % зважених речовин і на 80 % складається з гіпсу перекачується за допомогою відцентового насосу НС-13 до відстійника ВС-14.
Для видалення зважених речовин застосовують сталеві циліндричні відстійники безперервної дії діаметром 12 м з середньою продуктивністю 07 м3(годм2). Швидкість седиментації залежить від розмірів та питомої ваги зважених частинок і коливається в межах 0025 – 25 мс. В середньому ступінь очистки нейтралізат на відстійнику складає 80 – 90 %.
Нейтралізат надходить у верхню частину відстійника В-13 через трубопровід. У відстійнику забезпечується повільне обертання рідких потоків в наступному напрямку: в центральній частині апарату зверху вниз а в нижній частині – до периферії апарату і біля стінок – знизу вверх. Шлам осідає на конічне дно відстійника а освітлений нейтралізат рівномірно зливається жолоб розташований по окружності відстійника ВС-14 звідки надходить по трубопроводу у збірник освітленого нейтралізату З-15 об’ємом 5 м3. На цьому етапі здійснюють відбір проби для перевірки концентрації гіпсу зважених твердих речовин у нейтралізації. Перевірку здійснюють спочатку візуальним методом а потім методом кондуктометричного титрування.
Вигрібний механізм згрібає шлам в центральну частину конічного днища де розташований штуцер для відбору шламової суспензії з вологістю 60 – 75 % через який осад надходить до ЗВ 14.2 [49].
Нейтралізат звільнений від зважених частинок з температурою 85 ºС зі збірника З-14 подається на охолодження в холодильник Х-16 де набуває температури 30 – 33 ºС. Холодильник представлений пластинчатим теплообмінником з продуктивністю 150 м3год і площею поверхні теплообміну 65 м2. Охолодження здійснюється водою яка має температуру 16 – 20 ºС і надходить у сорочку теплообмінника. Температура нейтралізату контролюється за допомогою термометра КП-16.1 [50].
ТП 11. Зброджування моносахаридів
При спиртовому бродінні відбувається наступна реакція:
С6Н12О6 = 2С2Н5ОН + 2СО2 + 2344 кДж
Як видно з цього рівняння теоретичний вихід етилового спирту зі 100 кг зброджуваних моносахаридів складає 5114 кг практичний вихід з урахуванням утворення побічних продуктів бродіння – 56 – 59 дм3 [51].
Зброджування моносахаридів відбувається сепараційним методом у двох послідовно з’єднаних бродильних чанах: головному і хвостовому.
Бродильні чани представляють собою вертикальні циліндричні апарати ємністю 300 м3 що містять штуцери які з’єднують їх з необхідною комунікацією. Вони мають конічне дно і сферичну плоску кришку. У верхній частині чану або в його кришці находиться штуцер для подачі сусла в нижній частині на висоті 09 – 12 м від дна штуцер для відводу бражки.
У хвостовому бродильному чані БЧ-21 інтенсивність зброджування набагато менша і перемішування вуглекислим газом не відбувається. Тому в центрі хвостового бродильного чану встановлений вертикальний вал який обертається за допомогою електродвигуна з редуктором (розміщуються на кришці чану). Внизу вал оснащений мішалкою зі скребками. При його русі шлам який складається з лігніну гумінових колоїдних речовин мертвих дріжджів та кристалічного гіпсу пересувається до центра дна і через штуцер спускається в каналізацію. Бродильні чани виготовлені з листкової сталі. Внутрішня поверхня гладенькоа без тріщин легко піддається миттю чистці і протидіє корозії. Для цього чани зсередини вкриті кислотостійкими лаками (етинолем) або покриттями (епоксидною смолою) а залізобетонні чани футеровані керамічними плитками.
Аналогічно бродильним чанам виготовлена і дріжджанка. Вона представляє собою ємність об’ємом 150 м3 і оснащена мішалкою для примусового перемішування рідини і барботером для подачі повітря у випадку ослаблення бродильної активності дріжджів. Дріжджанка слугує також для зберігання дріжджів та консервації їх на період планово-попереджувального або капітального ремонту [52].
Сепаратори мають продуктивність 35 м3год. Дріжджова суспензія потрапляє у них зверху в розподільну трубу і далі в дріжджову камеру. Сепаратор складається зі станини барабану оснащеного конічними тарілками та приймально-вивідним пристроєм. Конічні тарілки що розділяють потік рідини в напрямку дії центробіжної сили мають кут нахилу тарілок 55º. Загальна тривалість перебування дріжджової суспензії в барабані сепаратора складає 2 – 5 сек. Число обертів барабанів сепаратора складає 5100 обертів за хвилину [53].
Підготоване деревне сусло зі збірника З-17 по трубопроводу надходить у дріжджанку Д-18. Сюди ж самопливом із сепаратора С-22 надходить дріжджова суспензія яка відокремлюється від бражки. Концентрація дріжджової суспензії складає 90 – 120 г пресованих дріжджів (з вологістю 75 %) в 1 дм3. На кожен кубометр дріжджової суспензії подається 8 – 10 м3 сусла. Суміш сусла і дріжджів із дріжджанки Д-18 неперервно відцентровим насосом НС-19 подається в головний бродильний чан БЧ-20 бродильної батареї де відбувається головна стадія спиртового бродіння. Ферменти що містяться в дріжджах каталізують розщеплення гексоз при цьому утворюється етиловий спирт і вуглекислий газ. Бульбашки вуглекислого газу сприяють перемішуванню рідини в бродильному чані. З головного бродильного чану БЧ-20 бражка самопливом надходить у хвостовий чан БЧ-21 де відбувається доброджування – засвоювання дріжджами найбільш важко засвоюваних цукрів наприклад галактози та завершення ланцюжка проміжних реакцій. Концентрація дріжджів в бродильній батареї становить 17 – 25 гдм3. Тривалість бродіння 5 – 7 год температура процесу 32 – 33 ºС.
По закінченню зброджування бражка із хвостового чану БЧ-21 через герметично закритий сітчастий фільтр з діаметром пор 05мм Ф-21 на сепаратор С-22. У фільтрі відбувається вловлювання частинок лігніну кори та інших домішок що потрапили в бражку. На сепараторах під впливом центробіжної сили та внаслідок різниці густин відбувається розділення бражки на два потоки: дріжджову суспензію і від сепаровану спиртову бражку. Остання збирається в збірнику З-24 місткістю 5 м3 а дріжджова суспензія самопливом надходить у дріжджанку Д-18 де знову змішується зі свіжим суслом. Таким чином дріжджі повторно використовуються для зброджування сусла. Для контролю за роботою сепаратора через кожні 2 години відбирають проби і за допомогою мікроскопу перевіряють на наявність дріжджових клітин. При нормальній роботі сепаратора в полі зору мікроскопу повинно бути не більше 2 – 3 клітин дріжджів.
Вуглекислий газ що виділяється в процесі спиртового бродіння при надлишковому тиску газу в бродильних чанах випускається в атмосферу.
По закінченню бродіння і відокремлення дріжджів спиртова бражка містить від 92 – 106 % етилового спирту і близько 15 % пентозних цукрів.
Температура сусла вимірюється за допомогою термометрів КП-18.1 КП-20.1 КП-21.1 встановлених на трубопроводах при виході сусла з холодильника Х-16 і надходженні в бродильний чан. Періодично також перевіряється температура сусла в бродильних чанах БЧ-20 БЧ-21.
В бродильних чанах також проводять мікробіологічний контроль кожну годину відбираючи пробу у пробовідбірники знизу апарату. В усередненій пробі визначають фізіологічний стан дріжджів за допомогою мікроскопів при збільшенні в 500 – 600 разів [54].
ТП 12. Ректифікація і абсолютизація етанолу
Виділяють спирт із бражки очищують і абсолютизують в 3-колонному брагоректифікаційному апараті що складається з бражної колони БК-27 ректифікаційної колони РК-28 і дегідратаційної колони ДК-29.
Подача в штуцер де гідратаційної колони спирто-бензинової суміші що містить азеотропний спирт забезпечує стабільну роботу установки. Отримання абсолютного спирту що не містить бензол досягається за рахунок того що в штуцер у верхній частині ректифікаційної колони яким оснащена дегідратаційна колона подається бензин. Подача в дегідратаційну колону бензину сприяє утворенню потрійної азеотропної суміші з підвищеним вмістом води який відводиться зверху де гідратаційної колони що і створює ефект дегідратації спирту та забезпечує отримання знизу колони абсолютного спирту що не містить бензол [55].
ТП 12.1. Ректифікація у бражній колоні
Бражка з об’ємною концентрацією етанолу 92 – 104 % за допомогою насосу Н-25 надходить на брагоректифікаційну установку до поз. Д-26.
Бражна колона БК-27 представляє собою типову відкриту відгонну ректифікаційну колону що містить 26 сітчастих тарілок відстань між якими 500 мм. Діаметр колони – 1000 мм висота – 1700 мм. Товщина стінки царг де встановлюються тарілки складає 25 мм висота царг – 1350 мм.
Спочатку бражка підігрівається в дефлегматорі бражної колони Д-26 а потім подається на верхню живильну 24-ту тарілку бражної колони БК-27 яка обігрівається гострою парою. Температура контролюється за допомогою термометра КП-27.1 тиск – за допомогою манометра КП-27.2. У вичерпній частині бражної колони відбувається відгонка етанолу до залишкового вмісту в барді менше 002 %. Отримана барда відводиться знизу колони до ЗВ 14.2. По виході з колони пари що містять леткі домішки надходять у дефлегматор бражної колони Д-26. Дефлегматор представлє собою видовжений двохсекційний кожухотрубний теплообмінник з площею поверхні теплообміну 15 м3 [56].
ТП 12.2. Ректифікація
Бражний ректифікат подається на живильну 16-ту тарілку знизу ректифікаційної колони РК-28 що оснащена спіральним теплообмінником Т-29 і обігрівається глухою парою початковий склад якої дорівнює складу кубового залишку (води) внаслідок цього із суміші витягується низько киплячий компонент(етанол). Робоча температура теплообмінника знаходиться в діапазоні від -40 ºС до +400 ºС; робочий тиск – 2 МПа; площа поверхні теплообміну 15 м3. Температура і тиск в колоні контролюються за допомогою термометра КП-28.1 і манометра КП-28.2. Нижня частина колони оснащена штуцером для відбору сивушної фракції. Лютер що містить кислоти не більше 002 % етанолу та незначну кількість вищих спиртів також виводиться знизу ректифікаційної колони. На 80-ту тарілку ректифікаційної колони подається бензин. Тут пара початкового складу що відповідає складу вихідної суміші взаємодіє з рідиною початковий склад якої дорівнює складу дистиляту і з бензином утворюючи потрійний азеотроп. Спиртово-бензинові пари зверху ректифікаційної колони надходять у дефлегматоратор Д-30 аналогічний за будовою до дефлегматора Д-26. На верхніх тарілках такої колони концентрація спирту доводиться до 940 – 950 %.
Ректифікаційна колона представляє собою типову повну ректифікаційну колону з сітчатими тарілками відстань між якими 170 мм. Діаметр колони – 600 мм. Товщина стінки царг де встановлюються тарілки складає 4 мм висота царг – 1550 мм кількість тарілок – 80 [57].
ТП 12.3. Абсолютизація етанолу
Частина спиртово-бензинової суміші яка відбирається з конденсатора К-30 подається у якості живлення на 50-ту тарілку 65-ти тарільчатої дегідратаційної колони ДК-31. нша частина направляється у вигляді флегми на зрошення ректифікаційної колони. На 65-ту тарілку подається бензин А-92. Дегідратаційна колона оснащена теплообмінником Т-32 аналогічного за будовою до Т-29 і обігрівається глухою парою. На верхню тарілку де гідратаційної колони подається бензин. Пари з верху дегідратаційної колони проходячи дефлегматор Д-33 аналогічний за будовою Д-30 повністю конденсуються в конденсаторі К-34 місткістю 01 м3 робочим тиском – 06 МПа і продуктивністю 20 м3год з якого відбирається спиртово-вуглеводнева суміш. Температура і тиск контролюються за допомогою контрольно-вимірювальних приладів КП-31.1 і КП-31.2 відповідно.
Абсолютний спирт який використовується в якості оксигенатної добавки для виробництва біоетанолу виводиться знизу де гідратаційної колони і збирається у збірнику З-35 перед яким влаштований пробовідбірник для контролю концентрації спирту.
Потрійна суміш етанол – вода – бензин утворює азеотропную суміш що складається з 185 % етанолу 74 мас.% води і 741 мас.% бензину і кипить при температурі 6485°С. Азеотропна суміш поводиться в колоні як головна фракція при охолоджуванні вона розділяється на два шари: верхній що складається в основному з бензину і нижній – з суміші етанолу і води. При температурі 15°С у верхньому шарі міститься (у мас.%): бензолу 85 етилового спирту 133 і води 17; у нижньому – спирту 497 води 413 і бензолу 90. На отримання 1 дал абсолютного спирту витрачається 15 - 20 кг пари близько 025 м3 води і 001 кг бензину.
Дегідратаційна колона має 65 сітчастих тарілок зокрема 10 в концентраційній частині і закритий обігрів. Діаметр колони – 800 мм; висота – 1700 мм [58].
ПВ 13. Переробка відходів
ПВ 13.1. Переробка лігніну.
Лігніновий осад отриманий на стадії ТП 7 висушується до вологості приблизно 40%. З 1 тони деревини отримують 350 кг сухого лігніну [21]. Гідролізний лігнін після обробки представляє собою як і сажа активний наповнювач для синтетичних каучуків пластмас а також може бути використаний як складова частина фенолформальдегідних смол. При хімічній переробці лігніну утворюються ароматичні та інші хімічні сполуки а також активоване вугілля [59].
ПВ 13.2. Утилізація фурфуролу.
Фурфурол від ТП 7.1 надходить на цех виробництва фурфуролу який утворюється з пентозанів на стадії гідролізу сировини. Спосіб і система для утилізації фурфуролу включають переміщення фурфуролвмісної стічної води в систему випарювання стічної води з подальшим нагріванням для отримання пари стічної води повернення пари стічної води в реактор гідролізу для формування рециркуляції фурфуролвмісної стічної води утилізацію фурфуролвмісних залишків що утворилися після випарювання стічної води. Це дозволяє знизити вартість обладнання та забезпечити нульовий випуск фурфуролвмісної стічної води з виключенням повторного забруднення утилізувати горючі речовини. Фурфурол застосовується для селективної очистки нафти та рослинних олій у виробництві каучуку вітаміну А синтетичних барвників синтетичного волокна (нейлону) малеїнового ангідриду. З фурфуролу та його похідних отримають ще багато інших важливих хімічних сполук у тому числі і гербіциди. Слід відмітити що властивості та можливості використання фурфуролу ще недостатньо вивчені [60].
ПВ 13.3.Утилізація лютерної води
Лютер (лютерна вода) містить у своєму складі високо киплячі складні ефіри та кислоти. Кількість лютерної води на 1 дал спирту складає від 40 до 50 л. Строк придатності не перевищує 20 діб. Лютерна вода утилізується на біомембранній установці з полімерними наномембранами де вона розділяється на два потоки. Пермеат концентрація абсолютно сухих речовин в якому 008 % мас. відправляють на промивання сивушної фракції а концентрат що містить 3% мас. абсолютно сухих речовин скидається в каналізацію. Дана технологія утилізації лютерної води дозволяє: зменшити об’єми скиду забруднень зменшує споживання питної води дозволяє практично на 100 % рекуперувати тепло лютерної води.
ЗВ 14. Знешкодження відходів
ЗВ 14.1. Зневоднення
Тверді частинки з відстійника складають приблизно 70% сульфату кальцію з залишком що представлений головним чином смолами лігніном і невеликою кількістю піску. х зневоднюють до вологості 50 % завантажують у вантажний автотранспорт і відправляють на полігон [61].
ЗВ 14.2. Утилізація післяспиртової барди.
Барда від дистиляції бражки містить 085 - 11 % пентозанів цукрів головним чином ксилозу і арабінозу від гідролізу геміцелюлози деревини.
Бражка використовується в якості сировини для промислового виробництва кормових дріжджів. Кормові дріжджі продаються у вигляді порошку і у формі гранул для використання як доповнення білка в кормах для тварин.
Для очищення загальних стічних вод гідролізний завод повинен мати потужні очисні споруди повної біологічної очистки. За відсутності виробничих кормових дріжджів потужності очисних споруд мають бути збільшені у 3-4 рази. З економічної точки зору суто гідролізно-спиртові заводи існувати не можуть. Вони повинні мати цехи кормових дріжджів.
ЗВ 14.3. Утилізація сивушної фракції
Вищі спирти які входять до складу сивушних масел відносяться до проміжних фракцій і концентрується в зміцнюючій частині колони. Для регенерації етанолу сивушні масла відмивають водою і промивні води направляють в бродильний відділ тобто до ТП 11. Відмита фракція сивушних масел спалюється [61].
Контроль виробництва
Для забезпечення якості біоетанолу проектом передбачено поточний контроль процесу на усіх його етапах. В таблиці 3.2 наводиться перелік контрольних точок що забезпечують дотримання заданих параметрів процесу.
Точки і параметри контролю виробництва [13]
Назва стадії процесу місце заміру параметра або відбору проби
Пара-метр що контро-люється
Норми технологічного режиму та допустимі відхилення
Метод контролю параметра тип приладу
Підготовка сировини конвеєрні терези
Нульова точка терезів
Перед і після кожного завантаження сировини в автоклав Раз на добу
Встановлення нульової точки при холостому ході терезів
Поправка до показань лічильника терезів ºC
Зважування на десяткових терезах матеріалу пропущеного через автоматичні терези
Гідроліз деревини патрубок після змішувача
Концентрація розчину сірчаної кислоти %
Під час кожної варки
Продовження таблиці 3.2
Гідроліз деревини водонагрівальна колонка
Температура води що надходить на гідроліз ºC
Гідроліз деревини колектор пари
Тиск пари на колекторі МПа
Гідроліз деревини кришка гідролізапарату
Тиск пари в гідролізапараті МПа
Гідроліз деревини водяний трубопровід та кислотна станція
Акустичний витратомір
Витрата кислоти м3год
Гідроліз деревини гідролізапарат
Перед кожним завантаженням гідролізапарату
Шляхом огляду гідролізапарату
Нейтралізація кислого гідролізату нейтралізатор
По мірі необхідності під час нейтралізації
Титрування 01 н розчином їдкого натру із суміші метилового червоного та метиленового блакитного
Нейтралізація кислого гідролізату збірник вапняного молока
Густина вапняного молока тм3
По мірі необхідності під час приготування вапняного малока
Ареометр А-160. Клас точності 3.
Охолодження нейтралізату теплообмінники і сусловий трубопровід перед бродильними чанами
Температура сусла ºС
Зброджування моносахаридів фільтри
Органолептичний шляхом порівняння з етанолом прозорості у скляних стаканах
Зброджування моносахаридів бродильні чани і сусловий трубопровід
Сепарація бражки бражний жолоб після сепаратора
Мікроскоп М-9 мах збільшення - 1350
Ректифікація спирту бражний трубопровід і бражна колона
Температура бражки що надходить на колони ºС
Ректифікація спирту живильні тарілки
Ректифікація спирту виварні камери колон
Абсолютизація спирту спиртопроводи
Контрольний спиртометр КС-35
4. Матеріальний баланс
Для проведення процесу виробництва біоетанолу з целюлозовмісної сировини використовуються певні кількості реагентів таких як вапняне молоко поживні солі суперфосфати розчин сульфату амонію тощо. Також для забезпечення оптимальних умов процесів використовувалася вода і пара. Внаслідок проведення процесу за даною технологію також утворюється певна кількість осадів шламу побічних продуктів виробництва та основного продукту.
Для фіксування джерел та масштабів надходжень і витрат матеріальних ресурсів та відповідність їх обсягів зобразимо всі дані в таблиці 3.3.
Матеріальний баланс виробництва [62]
Назва сировини матеріалів та напівпро-дуктів
Назва кінцевого продукту або напівпродукту відходів та втрат
Вода на завантаж зава
Конденсат парів самовипарювання:
Продовження таблиці 3.3
Кількість рідини що випарюється у випарнику
Пара для збільшення тиску
Пара в атмосферу при вивантаженні лігніну
Лігнін вологістю 723 %
Гідролізат на нейтралізацію
Випарюється вологи при охолодженні
Розчин сульфату амонію
Сусло на зброджування
СО2 що вільно виділяється при бродінні
Охолоджений нейтралізат
Бражка на ректифікацію
Вода на розведено сусла
Дріжджі 10 %-вої вологості
Бражка на розведено сусла
Випарилося вологи присушінні дріжджів
Підсів чистої культури
Випарюється рідини у теплообмінниках
Розділ 5 (табл.5.4).docx
Назва виробничої дільниць приміщень
Речовини що мають бути у виробництві ГОСТ (ДСТУ)
Агрегатний стан речовин в нормальних умовах
Горючість займистість
Показники пожежо- і вибухонебез-печності 0С
Вибухонебезпечні суміші з повітрям
Категорія приміщення за ЗНТП-24-86
Клас приміщеннязони і зовнішніх установок згідно з ПУЕ
Категорія об’єктів і тип зони захисту і влаштування блисавко захисту згідно з БН305-77
Температура спалаху ºС
Температура займання ºС
Температура самозаймання ºС
Біоетанол (992 % об) ДСТУ 320.00149943.015-2000
Горючий легкозаймистий
Вогнегасник СИ-120 пісок войлочна або азбестова кошма
Вогнегасник пісок розпилювальна вода
Гетінакс ГОСТ 2718-74
Пісок двоокис вуглецю
Рекомендуемые чертежи
- 17.05.2023
- 29.07.2014
- 06.07.2016