Проектирование техпроцесса детали вал




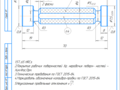
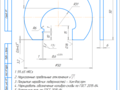
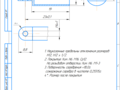
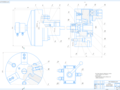
- Добавлен: 24.01.2023
- Размер: 440 KB
- Закачек: 0
Описание
Состав проекта
![]() |
![]() |
![]() ![]() ![]() ![]() |
![]() ![]() ![]() ![]() |
![]() ![]() ![]() ![]() |
![]() ![]() ![]() ![]() |
![]() ![]() ![]() |
![]() ![]() ![]() |
![]() ![]() ![]() |
![]() ![]() ![]() ![]() |
Дополнительная информация
Патрон 3х кулачковый.cdw

смазкой ЛИТОЛ-24 ГОСТ 21150-75.
Маркировать:номер партии
завода изготовителя.
Карта наладки.cdw

Чертеж детали.cdw

Покрытие Хим. Н6. М16. Ср12.
На резьбовом отверстии Хим. Н6. М1-3
Поверхность серебрения =18
сожержание серебра в чистоте 0
*. Размер после покрытия
Сталь 45 ГОСТ 1050-74
Калибр-пробка.cdw

Сталь У8 ГОСТ 18355-73
Покрытие рабочих поверхностей Хр
нерабочих поверх- ностей -
Технические требования по ГОСТ 2015-84.
Маркировать обозначение калаибра-пробки по ГОСТ 2015-84
Неуказанные предельные отклонения
Операционная карта.doc
Наименование операции
Сталь 45 ГОСТ1050-74
Оборудование устройство ЧПУ
Обозначение программы
Установить заготовку
ххх патрон 3-х кулачковый самоцентрирующий
Точить заготовку выдерживая размеры 7.
ххх резец проходной прямой левый ГОСТ 18869-73 Р9К5
ххх калибр-скоба ГОСТ 18355-73
Сталь 45 ГОСТ 1050-74
Сверление заготовки выдерживая размеры 9
ххх Сверло по металлу с коническим хвостиком ГОСТ 10903-77 P6M5
ххх Калибр-пробкаГОСТ-18355-73
Курсовая работа ПЗ .docx
Анализ базового техпроцесса .. 9
Задачи проекта пути совершенствования техпроцесса . .10
Выбор стратегии и выбор производства .. 12
Выбор заготовки . .14
Выбор технологических баз .. 17
Выбор средств технологического оснащения ..18
Расчет режимов резания . 21
Токарно-фрезерный ОЦ GOODWAY 27
Серебрение и меднение 33
Список литературы ..36
Машиностроение является важнейшей отраслью промышленности. Его продукция — машины различного назначения поставляются всем отраслям народного хозяйства. Рост промышленности и народного хозяйства а также темпы перевооружения их новой техникой в значительной степени зависят от уровня развития машиностроения. Технический прогресс в машиностроении характеризуется не только улучшением конструкций машин но и непрерывным совершенствованием технологии их производства. Важно качественно дешево и в заданные плановые сроки с минимальными затратами живого и овеществленного труда изготовить машину применив высокопроизводительное оборудование технологическую оснастку средства механизации и автоматизации производства. От принятой технологии производства во многом зависит надежность работы выпускаемых машин а также экономичность их эксплуатации.
Совершенство конструкции машины характеризуется ее соответствием современному уровню техники экономичностью в эксплуатации а также тем в какой мере учтены возможности использования наиболее экономичных и производительных технологических методов ее изготовления применительно к заданному выпуску и условиям производства.
В период научно-технической революции и при высоких темпах технического прогресса важное значение имеет всемерное ускорение технологической подготовки производства новых объектов. Эта задача может быть решена путем разработки и широкого использования типовых технологических процессов применения гибких быстропереналаживаемых средств производства нормализованной и обратимой оснастки.
Совокупность методов и приемов изготовления машин выработанных в течении длительного времени и используемых в определенной области. Поэтому возникают такие понятия: технология обработки давлением литья сварки сборки машин. Все эти области производства относятся к технологии машиностроения охватывающей все этапы процесса изготовления автомобильной продукции.
Однако под “технологией машиностроения” принято понимать научную дисциплину изучающую процессы механической обработки деталей и сборки машин попутно затрагивающую вопросы выбора заготовки и методы их изготовления. В процессе технической обработки деталей машин возникает большое количество простейших вопросов связанных с необходимостью выполнения технических требований поставленными конструкторами перед изготовителями.
Эти обстоятельства объясняют развитие “технологии машиностроения“ как научной дисциплины в первую очередь в направлении изучения вопросов технологии механической обработки и сборки в наибольшей мере влияющих на производственную деятельность предприятия.
Анализ исходных данных
Анализ служебного назначения детали
Данная деталь называется «Вал» служит для установки сопрягаемых деталей и передачи крутящего момент.
Анализ материала детали
Данная деталь изготовлена из стали 45 по ГОСТ 1050-74 сталь конструкционная углеродистая качественная применяется для изготовления деталей средних размеров работающих без значительных динамических нагрузок.
Таблица 1.1 – Химический состав стали %
Таблица 1.2 Физико-механические свойства стали
Обозначения в таблице 1.2:
т – Предел пропорциональности (предел текучести для остановочной деформации) [МПа]
в – Предел кратковремменной прочности [МПа]
s – Относительное удлинение при разрыве [%]
– Относительное сужение [%]
KCU – Ударная вязкость [Джсм2]
HB – Твердость по Бринеллю
Согласно таблицам 1.1 и 1.2 химический состав и механические свойства стали 45 вполне соответствуют служебному назначению изготавливаемой из нее детали.
Классификация поверхностей детали
по служебному назначению
С целью выявления поверхностей имеющих определение для качественного выполнения деталью своего служебного назначения систематизируем поверхности детали
Рисунок 1.1 Систематизация поверхностей
Таблица 1.3 Классификация поверхностей детали по служебному назначению
Основные конструкторские базы (ОКБ)
Анализ технологичности конструкции детали
Анализ технологичности детали выполняем с целью выявления возможного снижения себестоимости обработки детали путем совершенствования ее конструкции.
К критериям технологичности детали относятся:
а) технологичность заготовки
б) технологичность базирования и закрепления
в) технологичность обрабатываемых поверхностей.
г) технологичность детали
Рассмотрим выполнение этих критериев применительно к заданной детали.
Технологичность заготовки
Деталь – вал изготавливается из стали 45 ГОСТ 1050-74 прутков фасонного проката. Для данной детали прокат является наилучшим видом получения заготовки наружный контур и конфигурация всей детали в целом не вызывает трудностей при обработке.
Таким образом заготовку можно считать технологичной.
Технологичность базирования и закрепления
Технологичность базирования и закрепления детали характеризуется наличием опорных поверхностей (баз) совпадением технологической и измерительной баз точностью и шероховатостью базовых поверхностей возможностью захвата детали роботом.
Целью анализа конструкции детали на технологичность является выявление недостатков конструкции по сведениям содержащимся в чертежах и технических требованиях а также возможное улучшение технологичности рассматриваемой конструкции.
Анализ технологичности проводится как правило в два этапа: качественный и количественный
Качественный анализ технологичности детали
Конфигурация детали достаточно технологична для обработки резанием на токарном станке все поверхности легкодоступны для инструмента.. Жесткость вала допускает получение высокой точности обработки (жесткость вала считается недостаточной если для получения точности 6 9-го квалитетов отношение его длины l к диаметру d свыше 10 12).
Определим жёсткость детали:
На чертеже указаны все необходимые размеры требуемая шероховатость обрабатываемых поверхностей допуски.
Технологической базой при точении является черновая поверхность заготовки после переустановки детали – уже обработанная поверхность вала.
Количественный анализ технологичности детали
Количественная оценка технологичности выполняется согласно ГОСТ 14201–73 и содержит следующие показатели:
Коэффициент точности обработки Ктч определяется по формуле:
где Тср – средний квалитет точности обработки.
Коэффициент шероховатости поверхности определяется по формуле:
где Raср – средняя шероховатость поверхностей изделия.
Коэффициент использования материала Ким:
где q – масса детали кг;
Q – масса заготовки кг. ( Данные рассчитаны в программе Компас)
Анализ базового варианта техпроцесса
Задача анализа – выявить недостатки базового техпроцесса (ТП) устранение которых будет содействовать достижению цели ТП.
Технологический маршрут базового техпроцесса
Анализ технологического маршрута базового техпроцесса проводим с целью выявления недостатков последовательности и содержания операций.
Порядок и содержание операций базового маршрута приведены в таблице 1.4.
Базовый техпроцесс изготовления вала
Наименование операции
Краткое содержание операции
Отрезка заготовки из прутка
Горизонтально-расточная
Фрезеровка торцов в размер центровка торцов.
Точение черновое: поверхностей торцов
Точение черновое: поверхностей торцов:
Притирка центровых отверстий
Точение окончательное: поверхностей фаски канавки
Вертикально-сверлильная
Предварительная и окончательная шлифовка поверхностей
Задачи проекта. Пути совершенствования техпроцесса
Недостатки базового ТП
Анализ заводского ТП обработки вала показывает что базовый техпроцесс пригоден только для единичного и мелкосерийного производства. Применяемое оборудование и оснастка недостаточно производительны в условиях среднесерийного производства.
Анализ базового техпроцесса сделанный во время производственной практики и подготовки к курсовому проекту позволил выявить ряд недостатков сдерживающих повышение производительности обработки вала и снижение себестоимости.
Укажем основные недостатки базового техпроцесса:
Большое штучное время на токарных операциях вследствие большого припуска неоптимальных режимов резания и применения универсального оборудования.
Неоптимально выбрано оборудование – универсальные низкопроизводительные станки.
Большое штучное время на операциях вследствие применения универсальной оснастки с ручным зажимом.
Определить экономическую эффективность изменений внесенных в техпроцесс.
Выбор стратегии и выбор производства
В зависимости от типа производства будем определять общие подходы к выбору организации технологического процесса ввиду заготовки назначение припусков.
Различные типы производства характеризуются различной величиной коэффициента закрепления операций. Для его расчета необходимо знать трудоемкость изготовления детали последовательность обработки и количество станков.
Тип производства определим упрощенно в зависимости от массы детали и программы выпуска.
По при массе детали менее 1 кг и годовой программе выпуска Nг=15000производство – среднесерийное.
Таблица 2.1 – Основные характеристики среднесерийного производства
Критерий выбора техпроцесса
Форма организации техпроцесса для среднесерийного производства
Повторяемость выпуска изделий
Периодическое повторение партий
Унификация техпроцесса
Разработка специальных техпроцессов на базе типовых
Штамп прокат профильный прокат
Подробный по переходам от детали или по таблицам
Универсальное специализированное
Загрузка оборудования
Периодическая смена деталей на станках
По измерительным приборам и инструментам
Подробность разработки техпроцесса
Маршрутная карта операционная карта карта эскизов
Выбор метода получения заготовки
Для данной детали заготовкой может служить прокат стальной горячекатный круглый 9мм по ГОСТ 2590-88 из стали 45 по ГОСТ 1050-74. Класс точности проката А прокат высокой точности.
Предельные отклонения мм
при точности прокатки
Площадь поперечного сечения мм2
Масса 1 м профиля кг
По требованию потребителя прокат изготовляют длиной от 50 см до 24 м.
Средняя цена за 1 тонну проката стали 45 9 по ГОСТ 2590-88 равна 25000 руб.
Стоимость заготовки из сортового проката:
Затраты на материал определяются по массе проката необходимого для изготовления детали и массе сдаваемой стружки:
где Q – масса заготовки кг; Q = 0013 кг;
S – цена 1 кг материала заготовки руб.;
q – масса готовой детали кг; q = 0009 кг;
Sотх – цена 1 т отходов руб.
По принимаем: S= 12руб.; Sотх= 7 руб.
Коэффициент использования материала по формуле :
Найдем стоимость заготовки из проката стального горячекатаного круглого:
Стоимость заготовки полученной штамповкой на ГКМ определяется по формуле:
kт – коэффициент зависящий от точности штамповки;
kс – коэффициент зависящий от группы сложности штамповки;
kв – коэффициент зависящий от массы штамповки;
kм – коэффициент зависящий от марки материала штамповки;
kп – коэффициент зависящий от объема производства заготовок.
Принимаем: С kт=1; kс=075; kв=087; kм=1; kп=1.
Определяем годовой экономический эффект от внедрения нового метода получения заготовки – штамповки на ГКМ:
где – стоимость заготовки по базовому варианту;
– стоимость заготовки по принятому варианту.
Для данной детали и выбранном типе производства нам потребуется 350 прутков длинной 50см.
Масса металла на всю программу выпуска
Масса деталей всей программы выпуска
Для серийного производства рассчитывается размер партии деталей по формуле:
где а – количество дней запаса деталей на складе;
Ф – количество рабочих дней в году.
Принимаем а=10 дней; Ф=257 дней.
Размер партии равен 584 детали за поток.
Выбор технологических баз
Разработка базирования
Установка детали в приспособлении при механической обработке должна отвечать принципам единства и постоянства баз что необходимо для обеспечения минимальных погрешностей баз что необходимо для обеспечения минимальных погрешностей изготовления детали.
Технологичность базирования и закрепления детали характеризуется наличием опорных поверхностей (баз) совпадением технологической и измерительной баз точностью и шероховатостью базовых поверхностей.
Благодаря использованию современного оборудования и конструкции детали мы можем принять для всех операций одну основную технологическую базу.
№ базовых поверхностей
№ обрабатываемых поверхностей
Заготовительная (прокат)
Выбор средств технологического оснащения
Задача раздела – выбрать для каждой операции технологического процесса такие оборудования приспособление и инструмент которые бы обеспечили заданный выпуск деталей заданного качества с минимальными затратами.
Обоснование выбора оборудования
Выбор станка должен основываться на следующих правилах:
Мощность производительность и точность должны быть минимальными но достаточно для выполнения требования предоставляемых к операции
Обеспечение концентрации производства с целью уменьшения числа операций количества оборудования повышения производительности и точность за счет уменьшения числа переустановок заготовки
В среднесерийном производстве следует применять высокопроизводительные станки-автоматы агрегатные станки станки с ЧПУ
Оборудование должно отвечать требования безопасности Эргономики и экологии.
Данные по выбору оборудованию занесены в таблицу 4.1.
Технологический маршрут обработки детали
Обоснование выбора режущего инструмента
При выборе режущего инструмента следует руководствоваться правилами:
Режущий инструмент выбирается исходя из метода обработки оборудования расположения обрабатываемой поверхности
Следует отдавать стандартным и нормализованным инструментам и только при их отсутствии применять нестандартные
Материал режущего инструмента выбирается исходя из обрабатываемого материала состояния поверхности и вида обработки.
Таблица 4.2 – Выбор инструмента
Мерительный инструмент
Резец токарный проходной прямой левый ГОСТ-18869-73
Калибр-скоба ГОСТ 18355-73
Фреза концевая с цилиндрическим хвостовиком ГОСТ 170250-718
Фреза концевая с цилиндрическим хвостовиком ГОСТ 170250-71 8
Калибр-пробка ГОСТ 18355-73
Калибр-резьба ГОСТ 18355-73
Резец отрезной двухсторонний
Штангенциркуль ШЦЦ-150-001 электронный ГОСТ 166-89
Сверло по металлу с коническим хвостовиком ГОСТ 10903-77 75
Расчет режимов резания
Расчет режимов резания на токарную операцию 010
Материал – сталь 45
Обработка – токарная
Тип производства – среднесерийное
Приспособление – Патрон трехкулачковый самоцентрирующий патрон
Закрепление заготовки – полуавтомат
Смена детали – автоматическая
Жесткость станка – высокая
Операция 010 токарная чистовая
Точить заготовку выдержать размер
Выбор режущих инструментов
Резец проходной прямой левый ГОСТ 18869-73
Расчет элементов режимов обработки
Глубина резания t=02 мм
Частота вращения шпинделя n обмин
– табличные данные.
- поправочный коэффициент
– поправочный коэффициент.
где - поправочный коэффициент
Частота вращения шпинделя
- номинальный диаметр
Основное технологическое время
L – длина обрабатываемой детали
Расчет режимов резания на сверлильную операцию 040
Операция 040 Сверлильная
Сверлить осевое отверстие на t = 19 выдерживать размеры 75H12
Сверло по металлу с коническим хвостовиком ГОСТ 10903-77 Р6М5
Глубина резания t мм
При сверлении глубину резания принято принимать половину диаметра:
Назначаем подачу на один оборот нарезаемого приводного колеса:
где - подача по таблице 026 ммоб
- коэффициент зависящий от обрабатываемого материала
- коэффициент зависящий от угла наклона зубьев
Для сверла при обработке заготовки из стали рекомендуется стойкости T=25 мин.
Определяем скорость резания допускаемую режущими свойствами сверла:
где - табличная скорость по таблице ммоб
– коэффициент зависящий от количества проходов
Частота вращения фрезы соответствующая найденной скорости резания
Корректируем частоту вращения по данным станка и устанавливаем действительную частоту вращения
Рассчитаем режимы резания на остальные операции техпроцесса. Результаты расчета в таблице 5.1
Таблица 5.1 – Итоговая таблица режимов резания
Обрабатываемый и длина мм
Расчет производительности приспособления
Расчет производительности приспособления производится для того чтобы определить каким конструировать приспособление: одноместным (для обработки одной детали) или многоместным (для обработки за одну установку одновременно нескольких деталей).
Определяем темп производства Т:
где Nг – заданная годовая программа выпуска деталей шт.; N= 15000 шт.;
Fг – годовой фонд одного производственного рабочего; Fг=4029ч.
Полученная величина темпа производства сравнивается с величиной нормы выработки N:
Так как величина N=027 Т=03 то приспособление многоместное.
Токарно-фрезерные ОЦ GOODWAY серии GS- 2000
Основанная в 1975 году компания Goodway является крупнейшим и наиболее передовым в Тайване производителем специализирующимся на разработке и выпуске токарных станков с ЧПУ. По своим качествам машины этой фирмы способны выдерживать конкуренцию на самых требовательных рынках.
GOODWAY TurnMill Machining Centers ofGS-2000 Series
Оборудование Goodway многократно завоевывало первые места на крупнейших промышленных выставках: в частности на TIMTOS 2007 (1-е место — модель GTS-200XY) 2005 (2-е место) и TIMTOS 2003 (1-е место).
Ежегодно потребителям более чем в тридцать стран мира отгружается более 1500 комплектов современных токарных многофункциональных станков с ЧПУ. Например на один из самых требовательных в мире— японский рынок — компания Goodway поставляет более 100 комплектов машин с ЧПУ в т.ч. и вертикальных токарных обрабатывающих центров. Около 55 % производимых фирмой станков поставляются в Европу.
Конструкция всей станочной продукции Goodway основана на новейших японских стандартах и применении самых современных комплектующих. Высококачественные литые станины из термостабильного чугуна марки Meehanite проходят предварительную термообработку и дополнительный процесс старения в естественных условиях в течение минимум 6 месяцев. Механообработка и сборка оборудования осуществляются в Тайване под строгим контролем на соответствие системе контроля качества ISO 9001 и системе управления ISO 14001. Все станки Goodway изготавливаются на собственных производствах фирмы в цехах общей площадью более 30000кв. м (первый завод — 10000кв. метров в первом квартале 2008 года введен в эксплуатацию новейший производственный комплекс общей площадью более 23000кв. метров). Благодаря этому достигается полный контроль качества разработки конструкций изготовления и комплектации станков. Все ответственные детали контролируются на высококлассных измерительных системах Zeiss Taylor Hobson Renishaw и др. Сборка шпинделей производится в термоконстантных помещениях с компьютерной балансировкой и обязательными испытаниями в течение минимум 24 часов непрерывной работы.
Новая «линейка» токарно-фрезерных обрабатывающих центров GS-2000 (рис. 1)— результат глубокой модернизации станков успешной серии GS- 200. В ее основу легли подтвержденные годами эксплуатации технические решения:
станина с 30° наклоном направляющих отлита как единое целое методом FC35-Meehan
возможность установки противошпинделя;
количество осей управления от 2 до 6 по выбору заказчика ;
возможность оснащения револьвера вращающимся инструментом ;
оснащение станка в качестве опции автоматическими и роботизированными устройствами подачи заготовок и выгрузки деталей;
использование полуавтоматической измерительной системы с привязкой по координатам режущих кромок инструмента.
Одной из основных целей модернизации являлось увеличение производительности станка как при использовании вращающегося инструмента так и при точении. Однако чтобы простое увеличение мощности приводов не сказалось негативно на точности и надежности был осуществлен целый ряд изменений в конструкции и оснащении станка с использованием самых последних новинок:
вместо примененной в GS-200 клиноременной передачи привода шпинделя от консольно закрепленного двигателя установлен более мощный (до 26 кВт) встроенный в шпиндельную бабку электродвигатель ) что позволило выиграть в КПД и в плавности хода;
увеличена опорная площадь и количество точек крепления в месте сопряжения шпиндельной бабки и станины;
изменена система термостабилизации шпиндельного узла вместо обдува воздухом использован более эффективный охладитель с маслом в качестве рабочего тела;
существенно переработана конструкция станины станка: убраны концентраторы механических напряжений в виде различных углублений вместо тонкостенных отбортовок использованы мощные ребра жесткости увеличена площадь сечения станины в зоне установки направляющих;
целый ряд изменений внесен в конструкцию револьвера: значительно увеличен диаметр зубчатого колеса торцевой муфты что позволило повысить точность и жесткость фиксации инструмента. Изменена конструкция и увеличена до 55 кВт мощность привода вращающегося инструмента. Новая конструкция револьвера позволяет использовать цанги до ER40 (ранее — до ER32).
Серия GS-200 GS-2000 GS-3000
Производственные возможности
Наибольший диаметр устанавливаемого изделия
Наибольший диаметр обточки
Максимальная длина обточки
0 мм 1550мм (модель L )
Наибольший диаметр обрабатываемого прутка
Точность позиционирования
Передний конец шпинделя
Тип двигателя шпинделя
Выходная мощность двигателя
Диапазон скоростей вращения шпинделя
Скорость быстрого перемещения по оси X
Скорость быстрого перемещения по оси Z
Перемещение по оси X
+10мм - 200мм - 30мм
Перемещение по оси Z
0 мм 1600мм (модель L )
Перемещение по оси Y
0 мм = +65 мм -55 мм
Скорость быстрого перемещения по оси Y
Револьверная головка (стандарт)
Тип привода индексации револьверной головки
Серводвигатель переменного тока
Время индексирования револьверной головки
Задняя бабка (опция)
Конус в центре пиноли
Общие характеристики
Fanuc Oi - TD 18i - TB
0 В переменного тока от +10% до -15% 3 фазы
Габариты станка Д х Ш х В
70 3500 х 1955 х 1890 мм
Серебрение и меднение
Покрытие поверхности изделий серебром или серебрение может преследовать различные цели. Основной из них по праву считается улучшение эстетических свойств и облагораживание простых предметов. Покрытие серебром повышает ранг обычных изделий и ставит их в один ряд с выполненными из драгоценных металлов. В настоящее время наиболее популярной технологией покрытия серебром считается гальваника. Применение гальванического метода нанесения серебра даёт наиболее равномерный слой покрытия и отличается существенной экономичностью. Гальваническое покрытие серебром подразумевает использование реактивов для серебрения или электрохимполировки серебра.
Результатом серебрения становится:
- улучшение внешнего вида и повышение рейтинга изделий. Поэтому покрытие серебром активно используется в ювелирном деле при производстве украшений сувениров и элементов декоративного оформления;
- увеличение отражающей способности поверхности обрабатываемых серебром деталей;
- улучшение электропроводности. Это открывает широкий спектр применения покрытия серебром при создании различных электрических контактов и деталей от которых требуется оптимальная токопроводимость. Покрытие серебром востребовано в радиоэлектронике робототехнике медицинской промышленности при создании бытовых приборов и в точном машиностроении.
Чаще всего серебром покрывают изделия из меди и её сплавов. Классическим примером могут служить покрытые серебром столовые приборы из мельхиора. Возможно и покрытие железа цинка олова и других металлов. В таком случае процесс обработки может включать в себя промежуточную стадию - нанесение на поверхность меди.
Гальваническое покрытие серебром позволяет проводить все технические операции в самые короткие сроки и является наиболее рациональным видом финальной обработки изделий. Поэтому гальванические технологии становятся полем для постоянных научных изысканий которые ведут за собой внедрение передовых форм и методов обработки поверхности различных предметов. Применение технологий гальванического покрытия серебром может быть оправданным при необходимости обработать сотни промышленных деталей.
В результате выполнения данного курсового проекта был разработан технологический процесс изготовления вала.
По базовому варианту в качестве заготовки используется горячекатаный прокат круглого сечения нормальной точности. По проектному варианту в качестве заготовки использована прокат но благодаря современному оборудованию удалось существенно сократить время на изготовление детали
Результатом использования предлагаемых решений является снижение трудоёмкости изготовления продукции снижению численности производственного персонала и площади участка что снижает величину затрат при изготовлении продукции и способствуют повышению конкурентоспособности выпускаемых изделий.
СПИСОК ИСПОЛЬЗУЕМОЙ ЛИТЕРАТУРЫ
«Справочник технолога-машиностроителя» Под ред. Косилова А.Г. и Мещерякова Р.К. – М.: Машиностроение. т.1 1985г.
Заплетухин В.А. Конструирование соединений деталей в приборостроении. – Л.: Машиностроение 1985.
Горошкин А.К. Приспособления для металлорежущих станков. Справочник. – М.: Машиностроение 1979.
Терликова Т.Ф. Мельников А.С. Баталов В.И. Основы конструирования приспособлений. – М.: Машиностроение 1980.
Гжиров Р.И. Краткий справочник конструктора – Л.: машиностроение 1983.
В.Н. Байкалова А.М. Колокатов И.Д. Малинина. Расчет режимов резания при точении. Методические рекомендации по курсу «Технология конструкционных материалов и материаловедение».
Калибр-скоба.cdw

Неуказанные предельные отклонения
Покрытие нерабочих поверхностей - Хим.Фос.прм.
Маркировать обозначение калибра-скобы по ГОСТ 2015-84.
Остальные т.т. по ГОСТ 2015-84.