Проектирование схвата промышленного робота




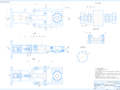
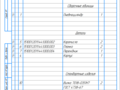
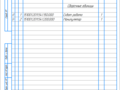
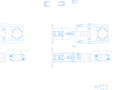
- Добавлен: 24.01.2023
- Размер: 643 KB
- Закачек: 4
Описание
Проектирование схвата промышленного робота
Состав проекта
![]() |
![]() |
![]() |
![]() ![]() ![]() ![]() |
![]() ![]() ![]() |
![]() ![]() ![]() |
![]() ![]() ![]() |
![]() ![]() ![]() |
![]() ![]() ![]() ![]() |
![]() ![]() ![]() |
![]() ![]() ![]() ![]() |
![]() |
![]() ![]() ![]() |
![]() ![]() ![]() ![]() |
![]() ![]() ![]() |
![]() ![]() ![]() |
![]() |
![]() ![]() ![]() ![]() |
Дополнительная информация
Планировка РТК.cdw

Положение робота при складировании деталей
Циклограмма работы оборудования РТК
Титул.doc
Южно-Уральский Государственный Университет
Миасский Машиностроительный факультет
Кафедра «Технология производства машин»
Курсовая работа по курсу
«автоматизация производства в машиностроении».
Расчетно-пояснительная записка.
Руководитель проекта
Робот.cdw
Число степеней подвижности 4
Число программируемых координат 3
Наибольший вылет руки
качание звеньев руки в вертикальной
Поворот кисти руки вокруг продольной оси
- горизонтальное перемещение руки
- качание звеньев руки
- поворот кисти руки
Погрешность позиционирования
Число захватных устройств 1
Склад.frw

Фрагмент.frw

Робот.spw

Аннотация автомати.docx
В данной курсовой работе для детали 75-1802161-10 «обойма дифференциала передняя» спроектирован схват промышленного робота для перемещения детали по роботизированном технологическому комплексу. Произведен Анализ известных типовых схем схватов произведено обоснование выбранной конструкции схвата и описание его работы. Был произведен расчет потребного усилия захвата заготовки и приводного пневмоцилиндра определены усилия в элементах схвата и его конструктивные параметры. Также был произведен выбор привода промышленного робота и выбор транспортно-складской системы.
Спецификация.spw

Схема.frw

Чертеж.cdw

Пояснительная запискалл.DOC
Обоснование выбранной конструкции схвата и описание
Расчет потребного усилия захвата заготовки и приводного
Определение усилий в элементах схвата и его конструктивных
Конструкция и расчет губок схвата 13
Выбор привода промышленного робота 14
Выбор транспортно-складской системы 15
Расчет цикла обработки в РТК 17
Графическая часть на 3 листах ф. А1
Спецификация на 3 листах ф. А4
Промышленный робот — автономное устройство состоящее из механического манипулятора и перепрограммируемой системы управления которое применяется для перемещения объектов в пространстве и для выполнения различных производственных процессов.
Промышленные роботы являются важными компонентами автоматизированных гибких производственных систем (ГПС) которые позволяют увеличить производительность труда.
Появление станков с числовым программным управлением (ЧПУ) привело к созданию программируемых манипуляторов для разнообразных операций по загрузке и разгрузке станков. В 1954 году американский инженер Д. Девол запатентовал способ управления погрузочно-разгрузочным манипулятором с помощью сменных перфокарт. Вместе с Д. Энгельбергом в 1956 г. он организовал первую в мире компанию по выпуску промышленных роботов. Ее название «Unimation» (Юнимейшн) является сокращением термина «Universal Automation» (универсальная автоматика). В 1962 году в США были созданы первые промышленные роботы «Юнимейт» и «Версатран». Их сходство с человеком ограничивалось наличием манипулятора отдаленно напоминающего человеческую руку. Некоторые из них работают до сих пор превысив 100 тысяч часов рабочего ресурса.
В первых ПР соотношение затрат на электронику и механику в стоимости составляло 75 % и 25 % поэтому многие задачи управления решались за счет механики. Сейчас это соотношение изменилось на противоположное причем стоимость электроники продолжает снижаться. Предлагаются необычные кинематические схемы манипуляторов. Быстро развиваются технологические роботы выполняющие такие операции как высокоскоростные резание окраска сварка. Появление в 70-х гг. микропроцессорных систем управления и замена специализированных устройств управления на программируемые контроллеры позволили снизить стоимость роботов в три раза сделав рентабельным их массовое внедрение в промышленности. Этому способствовали объективные предпосылки развития промышленного производства.
В составе робота есть механическая часть и система управления этой механической частью которая в свою очередь получает сигналы от сенсорной части. Механическая часть робота делится на манипуляционную систему и систему передвижения.
Манипулятор — это механизм для управления пространственным положением орудий и объектов труда.
Манипуляторы включают в себя подвижные звенья двух типов:
-звенья обеспечивающие поступательные движения;
-звенья обеспечивающие угловые перемещения.
Сочетание и взаимное расположение звеньев определяет степень подвижности а также область действия манипуляционной системы робота.
Для обеспечения движения в звеньях могут использоваться электрические гидравлический или пневматический привод.
Частью манипуляторов (хотя и необязательной) являются захватные устройства. Наиболее универсальные захватные устройства аналогичны руке человека — захват осуществляется с помощью механических «пальцев». Для захвата плоских предметов используются захватные устройства с пневматической присоской. Для захвата же множества однотипных деталей (что обычно и происходит при применении роботов в промышленности) применяют специализированные конструкции.
Вместо захватных устройств манипулятор может быть оснащен рабочим инструментом. Это может быть пульверизатор сварочные клещи отвёртка и т. д.
Внутри помещений на промышленных объектах используются передвижения вдоль монорельсов по напольной колее и т. д.
Для перемещения по наклонным вертикальным плоскостям используются системы аналогичные «шагающим» конструкциям но с пневматическими присосками.
Управление ПР бывает нескольких типов:
-Программное управление — самый простой тип системы управления используется для управления манипуляторами на промышленных объектах. В таких роботах отсутствует сенсорная часть все действия жёстко фиксированы и регулярно повторяются. Для программирования таких роботов могут применяться среды программирования типа VxWorksEclipse или языки программирования например Forth Оберон Компонентный Паскаль Си. В качестве аппаратного обеспечения обычно используются промышленные компьютеры в мобильном исполнении PC104 реже MicroPC. Может происходить с помощью ПК или программируемого логического контроллера.
-Адаптивное управление — роботы с адаптивной системой управления оснащены сенсорной частью. Сигналы передаваемые датчиками анализируются и в зависимости от результатов принимается решение о дальнейших действиях переходе к следующей стадии действий и т. д.
-Основанное на методах искусственного интеллекта.
-Управление человеком (например дистанционное управление).
Современные роботы функционируют на основе принципов обратной связи подчинённого управления и иерархичности системы управления роботом.
Иерархия системы управления роботом подразумевает деление системы управления на горизонтальные слои управляющие общим поведением робота расчётом необходимой траектории движения манипулятора поведением отдельных его приводов и слои непосредственно осуществляющие управление двигателями приводов.
Подчинённое управление служит для построения системы управления приводом. Если необходимо построить систему управления приводом по положению (например по углу поворота звена манипулятора) то система управления замыкается обратной связью по положению а внутри системы управления по положению функционирует система управления по скорости со своей обратной связью по скорости внутри которой существует контур управления по току со своей обратной связью.
Современный робот оснащён не только обратными связями по положению скорости и ускорениям звеньев. При захвате деталей робот должен знать удачно ли он захватил деталь. Если деталь хрупкая или её поверхность имеет высокую степень чистоты строятся сложные системы с обратной связью по усилию позволяющие роботу схватывать деталь не повреждая её поверхность и не разрушая её.
Управление роботом может осуществляться как человеком-оператором так и системой управления промышленным предприятием (ERP-системой) согласующими действия робота с готовностью заготовок и станков с числовым программным управлением к выполнению технологических операций.
Среди самых распространённых действий совершаемых промышленными роботами можно назвать следующие:
-перемещение деталей и заготовок от станка к станку или от станка к системам сменных паллет;
-сварка швов и точечная сварка;
-выполнение операций резанья с движением инструмента по сложной траектории.
Достоинства использования ПР:
- достаточно быстрая окупаемость;
- исключение влияния человеческого фактора на конвейерных производствах а также при проведении монотонных работ требующих высокой точности;
- повышение точности выполнения технологических операций и как следствие улучшение качества;
- возможность использования технологического оборудования в три смены 365 дней в году;
- рациональность использования производственных помещений;
- исключение воздействия вредных факторов на персонал на производствах с повышенной опасностью.
Производители промышленных роботов:
Анализ известных типовых схем схватов
К схватам (захватным устройствам) предъявляют следующие требования:
- надежность захватывания и удержания объекта во время разгона и торможения подвижных элементов ПР;
- точность базирования заготовки в губках схвата;
- недопустимость повреждения или разрушения транспортируемой заготовки. При этом особое внимание должно быть обращено на проверку допустимых для данного захватного устройства контактных и изгибающих напряжений и моментов на местах крепления;
- большой диапазон размеров захватываемых заготовок без переналадки;
- возможность автоматической или быстрой замены захватного устройства;
- компактность и простота конструкции.
В большом многообразии известных конструкций схватов их можно классифицировать по следующим основным признакам:
По типу закрепляемых деталей:
- для деталей типа валов;
- для деталей типа фланцев дисков шкивов зубчатых колес и т.д.;
- для деталей плоской и прямоугольной формы.
При выборе кинематической схемы и конструкции схвата необходимо обязательно учитывать характер движения губок схвата. Так для закрепления и надежного удержания и базирования деталей круглой формы (валы шкивы диски и др.) губки схвата могут перемещаться как по радиусу так и в плоско-параллельном направлении поскольку эти два перемещения практически не влияют на надежность закрепления и точность базирования. В то же время при захвате заготовок плоской и прямоугольной формы губки схвата должны перемещаться только в плоско-параллельном направлении. В противном случае не будет обеспечен правильный контакт губок схвата с закрепляемыми поверхностями.
По характеру базирования заготовок различают:
- центрирующие схваты обеспечивающие точное положение оси или плоскости симметрии захватываемого объекта. В таких схватах должно обеспечиваться одновременное перемещение всех губок в направлении к центру или плоскости симметрии заготовки;
- базирующие схваты определяют точное положение базовой поверхности закрепляемой заготовки. В этом случае одна из губок (базовая) остается неподвижной а вторая перемещается в направлении к закрепляемой поверхности;
- фиксирующие схваты в которых сохраняется точное положение объекта в момент захватывания его.
По числу рабочих позиций схваты можно разделить на:
По характеру работы многопозиционные схваты можно разделить на три группы:
- последовательного действия;
- параллельного действия;
- комбинированного действия.
К схватам последовательного действия относят двухпозиционные устройства имеющие загрузочную и разгрузочную позиции. Многопозиционные схваты параллельного действия имеют ряд позиций для одновременного захватывания или высвобождения группы деталей. Схваты комбинированного действия оснащены группами параллельно работающих позиций причем группы эти приводятся в действие независимо одна от другой.
По рабочему диапазону размеров закрепляемых деталей различают схваты:
- широкодиапазонные способные к центрированию и удержанию заготовок деталей и объектов в широком диапазоне размеров захватываемых поверхностей без переналадки или подстройки;
- узкодиапазонные способные к удержанию объектов в ограниченном диапазоне размеров захватываемых поверхностей. При использовании узкодиапазонных схватов для сокращения времени переналадки для перехода на другой закрепляемый объект применяют конструкции быстросменных или автоматически заменяемых схватов.
По типу привода различают схваты:
- с пневмоприводом использующим сетевой сжатый воздух с давлением 04МПа. Такой тип привода применяют для закрепления объектов массой до 10кг;
- с гидроприводом использующим специальную гидростанцию с рабочим давлением масла от 3 до 125МПа. Такой тип привода целесообразно применять для захватывания крупногабаритных тяжелых объектов массой более 20кг;
- с электроприводом использующим малогабаритные электродвигатели постоянного тока. Таким приводом оснащают захватные устройства для деталей массой от 5 до 20кг;
- неприводные схваты в которых детали удерживаются вследствие эффекта самозатягивания или запирающего действия губок. Как правило работа схватов такого типа возможна при их вертикальном положении при котором запирающее действие обеспечивается весом захватываемого объекта.
Обоснование выбранной конструкции схвата и описание его работы
Для данной детали (обойма дифференциала передняя 375-1802161-10) должен быть спроектирован схват для деталей типа «вал».
Схват должен обеспечивать точное положение оси симметрии детали. В таких схватах должно обеспечиваться одновременное перемещение всех губок в направлении плоскости симметрии поэтому выбираем центрирующий схват.
Так как проектируется схват для массового производства для конкретной детали и для конкретной операции то можно выбрать узкодиапазонный схват.
Масса готовой детали составляет 67кг поэтому привод используем пневматический использующий цеховой сетевой сжатый воздух давлением 04МПа.
Данное захватное устройство проектируется для двух токарных операций на горизонтальных токарно-револьверных станках с ЧПУ GOODWAY GA-2000. Деталь устанавливается в трехкулачковые патроны станка. На этих операциях производится черновая обработка детали с обеих сторон. Захватное устройство предназначено для взятия детали из тары-накопителя закрепления в патроне первого станка снятия детали после обработки перемещения и закрепления в патроне второго станка снятия детали после обработки и складирования в другую тару.
Вбираем схват со следующей схемой рычажного механизма:
Рисунок 1. Расчетная схема рычажного механизма схвата
Расчет потребного усилия захвата заготовки и приводного пневмоцилиндра
Определим потребное усилие для удержания транспортируемой детали считая что удержание происходит за счет сил трения:
где m – масса удерживаемой детали; m=67кг;
g – ускорение силы тяжести; g=981мс2;
а – ускорение центра масс при транспортировке; а=5мс2;
К1 – коэффициент зависящий от формы губок схвата положения детали по отношению к губкам схвата и направления действия силы тяжести; К1=05;
К2 – коэффициент запаса; К2=15 2.
Потребное усилие удержания Р:
Р=67·(981+5)·05·2=992Н.
Соотношение между силами Р1 Р2 и F на губках захватного устройства определяют из условия статического равновесия системы.
Из условия F=0 в точке В имеем:
Из условия М=0 относительно точки А имеем:
Р1h2-Fcosαh1=0 откуда
Из конструктивных соображений прнимаем h1=100мм h1=120мм. Тогда
Рассчитаем необходимый диаметр цилиндра по формуле:
где D – диаметр пневмоцилиндра мм;
р – давление масла; р=04МПа;
d – диаметр штока мм;
– механический КПД; =085;
Диаметр пневмоцилиндра принимаем из стандартного ряда: .
Сила на штоке при подаче воздуха в бесштоковую полость (рабочий ход):
Определение усилий в элементах схвата и его конструктивных параметров
Усилие действующее на шарнир А находим из суммы проекций сил на оси Х и У:
Суммарная нагрузка в шарнире А:
Диаметр шарниров выбираем из расчета на срез:
где - допустимое напряжение среза для стали 45 =120МПа;
Такой размер шарниров слишком мал. Конструктивно принимаем =12мм и =16мм.
Проверяем шарниры на смятие принимая допускаемое напряжение на смятие для стали 45 =80МПа:
где b=36мм – принятая ширина шарнира;
Конструкция и расчет губок схвата
Губки схвата контактируют с деталью и от их конструкции во многом зависит точность и надежность работы схвата. При конструировании следует учитывать что на губки действуют значительные нормальные усилия и силы инерции которые сдвигают губки со своего места. С другой стороны губки должны обеспечить наибольшую силу трения. Что позволит уменьшить размеры элементов схвата. Поэтому в конструкции крепления губок необходимо предусмотреть их жесткую фиксацию выполнение рабочей поверхности губок с высокой твердостью и возможностью их быстрой и легкой замены.
Размеры губок определяют исходя из расчета на контактную прочность:
где - приведенный модуль упругости материала губок схвата и материала детали; =215105МПа (сталь 40Х) =212105МПа (сталь 35Л);
l – ширина губок схвата.
Ширина губок схвата:
Такой размер губок конструктивно слишком мал. Принимаем l=55мм.
Выбор привода промышленного робота
Для перемещения рабочих органов ПР используют пневматические гидравлические электромеханические комбинированные приводы. Наиболее распространены пневматические приводы (45% общего мирового парка ПР).
Приводы ПР классифицируются по ряду признаков.
По числу двигателей различают групповой однодвигательный и многодвигательный привод.
Групповой привод обеспечивает одновременное перемещение нескольких звеньев ПР. Для передачи заданной мощности на несколько звеньев и ее распределения между ними используют трансмиссии поэтому такой привод также называют трансмиссионным.
Индивидуальный или однодвигательный привод обеспечивает движение только одного звена исполнительного механизма ПР. Это значительно упрощает конструкцию механических передач а в ряде случаев позволяет отказаться от них.
У многодвигательного привода двигатели совместно работают на общий вал что дает возможность распределить потребляемую мощность между отдельными двигателями и улучшить условия работа механической передачи.
По способу управления приводы делят на нерегулируемые (обеспечивающие движение звеньев с одной рабочей скоростью); регулируемые (обеспечивающие скорости движения звеньев под воздействием устройств управления); следящие (обеспечивающие отработку перемещений с определенной точностью согласно произвольно меняющемуся задающему сигналу); адаптивные (автоматически избирающие параметры управления при изменении условий работы с целью выработки оптимального режима).
На рис. 2 показана схема промышленного робота с пневматическим приводом и цикловым управлением. Привод состоит из пневмоцилиндра 7 со штоком 1 на котором закреплена скалка 5 с регулируемыми упорами 3 и 6 неподвижного упора 4 с демпфирующим устройством 2 воздухораспределителя 8 устройства управления УУ. Сигнал с УУ несущий логическую информацию о направлении перемещения штока 1 поступает на управляющий электромагнит воздухораспределителя 8 который в соответствии с управляющим воздействием соединяет одну из полостей пневмоцилиндра с гидростанцией а другую с окружающей средой. При этом шток 1 перемещается в требуемом направлении до соприкосновения упоров 3 или 6 с упором 4. Положение упоров 3 и 6 определяет величину перемещения штока при прямом и обратном ходе. Демпфирующее устройство 2 обеспечивает торможение штока 1 с заданным ускорением при нажатии упорами 3 и 6 на кнопки демпфера.
Рисунок 2. Схема пневматического привода промышленного робота
Выбор транспортно-складской системы
При построении автоматизированной транспортно-складской системы принимаем вариант с совмещенными транспортной и складской подсистемами. То есть спроектированный промышленный робот будет выполнять обе этих функции: транспортировать деталь от станков к складу и осуществлять складирование (см. рисунок 3). На ней промышленный робот 3 перемещающийся по направляющим рельсам 4 обслуживает два токарно-револьверных станка с ЧПУ 1 и 2 и перемещает их на склад 5.
Достоинства такой схемы: компоновка занимает мало места и имеет простую транспортную магистраль. Недостатки: робот обслуживает ограниченное количество станков затруднена уборка стружки (за станок).
Совмещенные компоновки АТСС относят к числу наиболее рациональных так как в этом случае склад максимально приближается к технологическому оборудованию (станкам) и транспортные связи в ГПС наиболее просты. Также часто (как в проектируемой компоновке) отпадает необходимость в применении специальных кранов-штабелеров.
Рисунок 3. Схема транспортно-складской системы
Расчет цикла обработки в РТК
Цикл работы РТК строится опираясь на расчеты основного технологического времени на механическую обработку детали (принимается из карт технологического процесса). Циклограмма работы оборудования РТК приведена на рис. 4 на котором:
tзаг.раз. – время на загрузку-разгрузку деталей роботом;
tмаш.– основное технологическое время (время мех. обработки детали станком);
tпер.– время на перемещение робота ко второму станку;
tпрост.ст.– время простоя станка;
ТМС– время цикла механической обработки детали;
tзан.– время занятости промышленного робота;
tпрост.роб.– время простоя робота;
tоп.max– максимальное из рассматриваемых оперативных времен на операциях.
Рисунок 4. Циклограмма работы оборудования РТК
Я.Н. Отений П.В. Ольштынский. Выбор и расчет захватных устройств промышленных роботов: Учебное пособие. – Волгоград: издательство РПК «Политехник» 2000г – 64с.
Л.М. Попов. Схваты промышленных роботов: Учебное пособие для курсового проектирования. – Челябинск: издательство ЮУрГУ 2001г – 39с.
В.Н. Шурков. Основы автоматизации производства и промышленные роботы: Учебное пособие. – М.: Машиностроение 1098г – 240с.
Ю.Г.Козырев. Промышленные роботы: Справочник 2-е изд. переработанное и дополненное. – М.: Машиностроение 1988г – 392с.
Механика промышленных роботов Т.3. – М.: Машиностроение 1098г – 383с.
Привод.frw

Циклограмма.frw
