Проектирование редуктора




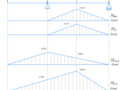
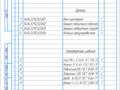
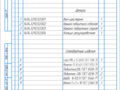
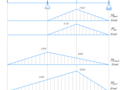
- Добавлен: 24.01.2023
- Размер: 3 MB
- Закачек: 0
Описание
Проектирование редуктора. Галаганов А.И
Состав проекта
![]() |
![]() |
![]() |
![]() ![]() ![]() |
![]() ![]() |
![]() ![]() ![]() |
![]() ![]() ![]() |
![]() ![]() ![]() |
![]() ![]() ![]() ![]() |
![]() ![]() ![]() |
![]() ![]() ![]() ![]() |
![]() ![]() ![]() |
![]() ![]() |
![]() ![]() ![]() ![]() |
![]() ![]() ![]() |
![]() ![]() ![]() |
![]() ![]() ![]() |
Дополнительная информация
Гайка.frw

Подшипник.frw

Стопорная шайба.frw

Шпонка.frw

Спецификация - Галаганов.spw

Крышка подшипника сквозная
Крышка подшипника глухая
Кольцо регулировочное
Манжета 1.1-30 x52-1 ГОСТ 8752-79
Подшипник206 ГОСТ 8338-75
Подшипник 206 ГОСТ 8338-75
Шайба 16 В12.31 ГОСТ 13466-77
Шпонка 5 х 5 х 18 ГОСТ 23360-78
эпюра8.frw

мертвй.spw

Крышка подшипника сквозная
Крышка подшипника глухая
Кольцо регулировочное
Манжета 1.1-30 x52-1 ГОСТ 8752-79
Подшипник206 ГОСТ 8338-75
Подшипник 205 ГОСТ 8338-75
Шайба 16 В12.31 ГОСТ 13466-77
Шпонка 5 х 5 х 18 ГОСТ 23360-78
Содержание - Галаганов.doc
Расчет данных для ЭВМ 3
1.Определение диаметра и частоты вращения барабана 3
2.Выбор электродвигателя 3
3.Определение момента на зубчатом колесе тихоходной передачи 4
4.Определение коэффициентов относительной ширины колес 5
5.Расчет эквивалентного времени работы 5
Выбор оптимального варианта компоновки редуктора 6
Статический расчет редуктора 8
1.Расчет частот вращения валов 8
2.Расчет моментов на колесах зубчатых передач и валах 8
3.Определение усилий в зацеплении зубчатых передач 8
Разработка эскизного проекта редуктора 10
1.Определение диаметров валов 10
2.Геометрические расчеты зубчатых колес 11
3.Определение расстояний между деталями передач 12
4.Выбор подшипников 14
5.Конструирование зубчатых колес 14
Проверочный расчет редуктора 17
1.Подбор материала твердости и термообработки зубчатых колес 17
2.Проверочный расчет быстроходной передачи 18
2.1.Расчет допускаемых напряжений 18
2.2.Расчет рабочих напряжений 20
2.3.Проверка прочности 21
3.Проверочный расчет тихоходной передачи 21
3.1.Расчет допускаемых напряжений 21
3.2.Расчет рабочих напряжений 23
3.3.Проверка прочности 25
4.Проверка быстроходного вала 25
4.1.Определение запаса прочности вала 25
4.2.Проверка правильности выбора подшипников 29
5.Решение вопроса о вале-шестерне 30
6.Подбор и расчет шпоночных соединений 31
Эскизы стандартных изделий ..33
Список литературы 36
Приложение. Распечатка из программы REDUCE 37
Быстроходный вал - Галаганов.cdw

пояснительная записка.doc
1.Определение диаметра и частоты вращения барабана
Диаметр каната dк можно определить по формуле
и округлить до значения установленного ГОСТ 6636-69.
Диаметр грузового барабана лебедки (мм) предварительно назначаем из условия:
где е – коэффициент диаметра барабана принимаем значение 16.
Полученное значение D округляется в большую сторону до размера Dб выбираемого из рада нормальных линейных размеров. Dб = 135 мм.
Частота вращения барабана (мин-1) вычисляется по формуле:
2.Выбор электродвигателя
Мощность двигателя Pэд связана (с учетом допускаемой перегрузки) с потребной мощностью P соотношением
гдеP – мощность привода определяемая по формуле:
где V – скорость набегания каната на барабан мс;
Fк – усилие в канате Н.
Значение потерь мощности учитывается КПД привода h рассчитываемым по универсальной формуле:
h=h2муф×h3подш×h2упл×h3зац×hмв×hбар
где hмуф – КПД муфты соединяющей валы электродвигателя и редуктора hмуф=1; [3 стр.9]
hподш – КПД пары подшипников hподш=099; [3 стр.9]
hупл – КПД уплотнительных манжет устанавливаемых на входном и выходном концах валов hупл=1; [3 стр.9]
hзац – КПД зацепления зубчатых передач hзац=097; [3 стр.9]
hмв – КПД масляной ванны hмв=1; [3 стр.9]
hбар – КПД барабана лебедки учитывающий потери за счет внутреннего трения в канате и трения каната в контакте с барабаном hбар=1.
h = 1×0993×12×0972×1×1 = 091.
Pэд ³ 088 ×4229=372 кВ.
Номинальную частоту вращения двигателя можно определить по формуле
где i – передаточное отношение редуктора i =10..30.
Отсюда получаем nном = 736..2208 мин-1.
В таблице 1.1 приведена выдержка из технических данных двигателей серии АИР из которой мы выбираем электродвигатель АИР132S4 с асинхронной частотой вращения nном=1445 мин-1
Технические данные двигателей серии АИР
Мощность двигателя кВт
Выбранной частоте вращения электродвигателя соответствует передаточное число редуктора
3.Определение момента на зубчатом колесе тихоходной передачи
Вращающий момент на барабане лебедки определяется по формуле
Момент на колесе тихоходной передачи Т2Т редуктора можно вычислить
4.Определение коэффициентов относительной ширины колес
Для несимметричного расположения колес относительно опор коэффициенты относительной ширины колес для тихоходной и быстроходной ступеней назначаются равными
yba Б = 06. [1 табл.8.4]
5.Расчет эквивалентного времени работы
Эквивалентное время работы Lhe назначают с учетом категории режима работы по ГОСТ 21354-87 и находится по формуле:
где Lh – заданный срок службы час;
mh - коэффициент эквивалентности зависящий от режима нагрузки.
В нашем случае режим нагрузки IV для которого mh = 0125 [1табл.8.9]
Lhe =018 × 9000 = 1620 ч.
Выбор оптимального варианта компоновки редуктора
Выбор оптимального варианта компоновки редуктора выбирается по двум условиям:
Согласно условию сборки колесо быстроходной передачи должно находиться на расстоянии Δ≥10..15 мм от выходного вала
Диаметры колес быстроходной и тихоходной передач должны быть близки по значению для обеспечения эффективного разбрызгивания смазки; кроме того d2Б d2Т
Для каждого из 6 предложенных вариантов компоновки проверим эти условия. Как видно из рисунка 2.1 расстояние Δ можно рассчитать по формуле:
Где aw2 – межосевое расстояние тихоходной передачи;
d2Б – делительный диаметр быстроходного колеса;
Dвых – диаметр выходного вала который можно приблизительно оценить по формуле
Рис. 2.1. Схема расположения зубчатых колес в редукторе
aw2=140 мм; d2Б=23429 мм
aw2=140 мм; d2Б=22857 мм
aw2=135 мм; d2Б=21543 мм
aw2=130 мм; d2Б=20286 мм
aw2=130 мм; d2Б=19714 мм
aw2=125 мм; d2Б=18391 мм
Как видно из расчетов условию сборки удовлетворяют только первые три варианта компоновки редуктора. Из этих трех вариантов исходя из условия смазки разбрызгиванием оптимальным вариантом будет вариант №3.
Статический расчет редуктора
6.Расчет частот вращения валов
Частоты вращения валов и зубчатых колес определяются частотой вращения электродвигателя и передаточными числами зубчатых передач. Для быстроходного вала имеем
nБ = nном = n1Б = 1445 мин–1;
Частота вращения промежуточного вала связана с частотой вращения быстроходного вала соотношением
nП = nБUБ = n2Б = n1Т
где UБ – передаточное число быстроходной передачи UБ=488;
nП = 1445488 = 2961 мин–1;
Частота вращения тихоходного вала равна
где UT – передаточное число тихоходной передачи UT=395;
nТ = 2961395 = 7418 мин–1.
Окружная скорость быстроходной ступени определяется
VБ = p×dW1Б× nБ6×104
VБ = 314×34× 14456×104 = 257 мс;
Для тихоходной ступени окружная скорость запишется
VТ = p×dW1Т× nП6×104
VТ = 314×5457× 29616×104 = 0846 мс.
7.Расчет моментов на колесах зубчатых передач и валах
Моменты на колесах одной передачи связаны между собой через КПД зубчатого зацепления hзац=097; моменты на колесах сопряженных передач связаны через КПД пары подшипников hп=099. Момент на втором колесе тихоходной передачи равен выходному моменту: T2T=Tвых=5045 Н·м
Т1Т = 25225(395×097) = 65836 Н·м.
Т2Б = 2*65836099 = 133002 Н·м.
Т1Б = 133002488×097 = 28097 Н·м
Твх=28097099=28381 Н·м.
8.Определение усилий в зацеплении зубчатых передач
-для шестерни быстроходной передачи
Ft1Б = 2×Т1Б×103dW1Б
Ft1Б = 2×28×10334 =164706 Н;
где aW – начальный угол профиля или угол зацепления по ГОСТ 13755–81 aW=20°;
Fr1Б = 164706×tg 20° = 5995 Н;
-для колеса быстроходной передачи
Ft2Б = 2×Т2Б×103dW2Б
Ft2Б = 2×133×103166 =1602 Н;
Fr2Б = 1602×tg 20° = 58313 Н;
-для шестерни тихоходной передачи
Ft1Т = 2×Т1Т×103dW1Т
Ft1Т = 2×65836×1035457 =2412 Н;
Fr1Т = Ft1Т×tg aWcos2
где 2 – угол наклона зубьев тихоходной передачи 2=29498°;
Fr1Т = 2412×tg 20°cos 29498° = 99236 Н;
Fa1Т = 2412×tg 29498° = 13345 Н.
-для колеса тихоходной передачи
Ft2Т = 2×Т2Т×103dW2Т
Ft2Т = 2×25225×10321543 =2341 Н;
Fr2Т = Ft2Т×tg aWcos2
Fr2Т = 2341×tg 20°cos 29498° = 9687 Н;
Fa2Б = 2341×tg 29498° = 13244 Н.
Разработка эскизного проекта редуктора
9.Определение диаметров валов
Диаметры валов назначаются исходя из передаваемого ими момента а также фасок и радиусов скруглений. Для быстроходного вала определяются три диаметра – минимальный диаметр вала на входе d который необходимо согласовать с диаметром вала электродвигателя; диаметр цапфы вала для установки подшипника dП и диаметр буртика для упора кольца подшипника dБП.
После согласования этого диаметра с диаметром вала электродвигателя и рядом нормальных линейных размеров (ГОСТ 6636–69) устанавливаем d=24мм.
где t – высота заплечика t=2мм.
После согласования этого размера с рядом диаметров внутреннего кольца подшипников назначаем dП=30мм.
где r – координата фаски подшипника r=16 мм.
После согласования этого диаметра с рядом нормальных линейных размеров назначаем dБП=34мм
Для промежуточного вала необходимо также рассчитать диаметры dП и dБП а также dК – диаметр шейки вала в месте установки зубчатого колеса и dБК – диаметр упорного буртика для зубчатого колеса.
Согласовав этот диаметр с рядом нормальных линейных размеров устанавливаем dК=45мм (увеличили до 63мм для того чтобы одеть колесо).
где f – размер фаски колеса f=16мм.
После согласования принимаем dБК=50мм.
После согласования этого размера с рядом диаметров внутреннего кольца подшипников назначаем dП=35мм.
Расчет диаметров тихоходного вала аналогичен расчету диаметров быстроходного вала; для удобства осевого фиксирования зубчатого колеса также для этого вала рассчитаем диаметр упорного буртика для колеса.
Устанавливаем d=48мм.
После согласования этого размера с рядом диаметров внутреннего кольца подшипников назначаем dП=55мм.
Устанавливаем dБП=67мм.
Из ряда нормальных линейных размеров выбираем dБК=75мм.
10.Геометрические расчеты зубчатых колес
Необходимо определить диаметры окружностей вершин da1 и da2 диаметры окружностей впадин df1 и df2 коэффициент торцевого перекрытия ea коэффициент осевого перекрытия eb а также суммарный коэффициент перекрытия e для каждой из двух ступеней. Все колеса нарезаются реечным инструментом или долбяком с исходным контуром по ГОСТ 13755-81 с параметрами: угол профиля a = 20° коэффициент головки (ножки) зуба ha*=hf*=1; коэффициент радиального зазора с* = 025.
Диаметры окружностей вершин вычисляют по формуле
da = d + m × (2×ha* + 2×x)
где m – модуль зубьев соответствующей передачи mБ=2 mТ=25;
х – коэффициент смещения исходного контура хБ=хТ=0.
Для быстроходной ступени:
da1Б = d1Б + mБ × (2×ha* + 2×xБ)
da1Б = 34 + 2 × (2×1 + 2×0) = 38 мм
da2Б = d2Б + mБ × (2×ha* + 2×xБ)
da1Б = 166 + 2 × (2×1 + 2×0) = 170 мм.
Для тихоходной ступени:
da1Т = d1Т + mТ × (2×ha* + 2×xТ)
da1Б = 5457 + 25 × (2×1 + 2×0) = 5957 мм
da2Т = d2Т + mТ × (2×ha* + 2×xТ)
da1Т = 21543 + 25 × (2×1 + 2×0) = 22043 мм.
Диаметры окружностей впадин вычисляют по формуле
df = d – m × (2×hf* + 2×c* – 2×x)
df1Б = d1Б – mБ × (2×hf* + 2×c* – 2×xБ)
df1Б = 34 - 2 × (2×1 + 2×025 – 2×0) = 29 мм
df2Б = d2Б – mБ × (2×hf* + 2×c* – 2×xБ)
df1Б = 166 – 2 × (2×1 + 2×025 – 2×0) = 161 мм
df1Т = d1Т – mТ × (2×hf* + 2×c* – 2×xТ)
df1Т = 5457 – 25 × (2×1 + 2×025* – 2×0) = 4832 мм
df2Т = d2Т – mТ × (2×hf* + 2×c* – 2×xТ)
df2Т = 21543 – 25 × (2×1 + 2×025 – 2×0)=20918мм.
Коэффициенты торцевого перекрытия вычисляются по формуле
где z1 – число зубьев шестерни z1Т=19;
z2 – число зубьев колеса z2Т=75.
Коэффициенты осевого перекрытия вычисляются по формуле
где bw – ширина зубчатого венца bwБ = 55мм bwТ = 63мм.
Для тихоходной ступени
Суммарные коэффициенты перекрытия вычисляются по формуле
11.Определение расстояний между деталями передач
Чтобы поверхности вращающихся колес не задевали за внутренние поверхности стенок корпуса между ними оставляют зазор равный
где L – расстояние между внешними поверхностями деталей передач (см. рис. 4.1)
Принимаем значение зазора равное а = 12мм
Рис. 4.1. Расстояния между деталями передач
Расстояние b0 между дном корпуса и поверхностью колес принимают:
Расстояние между торцовыми поверхностями колес двухступенчатого редуктора принимают
Используя ряд нормальных линейных размеров выбираем значение .
12.Выбор подшипников
Предварительно подшипники выбираются по значению диаметра цапфы вала dп а также по предварительному значению динамической нагрузки приведенному в распечатке программы REDUCE.
Для быстроходного вала выбираем подшипник 206 ГОСТ 8338–75:
внутренний диаметр кольца подшипника d = dП(Б) = 30 мм;
наружный диаметр кольца подшипника D = 62 мм;
ширина кольца подшипника B = 16 мм;
динамическая грузоподъемность: Cr = 153 кН;
статическая грузоподъемность: С0r = 102 кН.
Для промежуточного вала выбираем подшипник 12207 ГОСТ 8338–75:
внутренний диаметр кольца подшипника d = dП(П) = 35 мм;
наружный диаметр кольца подшипника D = 72 мм;
ширина кольца подшипника B = 17 мм;
динамическая грузоподъемность: Cr = 256 кН;
статическая грузоподъемность: С0r = 175 кН.
Для тихоходного вала выбираем подшипник 211 ГОСТ 8338–75:
внутренний диаметр кольца подшипника d = dП(Т) = 55 мм;
наружный диаметр кольца подшипника D = 100 мм;
ширина кольца подшипника B = 21 мм;
динамическая грузоподъемность: Cr = 34 кН;
статическая грузоподъемность: С0r = 256 кН.
13.Конструирование зубчатых колес
Форма цилиндрического зубчатого колеса зависит от серийности производства. В нашем случае производство малосерийное. В этом случае для изготовления зубчатого колеса применяют простейшие односторонние штампы. Форма колеса проектируется так как показано на рисунке 4.2.
Диаметр ступицы длину ступицы и ширину торцов зубчатого венца принимают:
где d = dк соответствующего вала на котором находится колесо.
Толщину диска принимают:
На торцах зубчатого венца выполняют фаски размер которых определяют как и угол выбирают в зависимости от твердости материала колеса.
Рис. 4.2. Конструкция зубчатого колеса
Для колеса быстроходной ступени эти параметры будут равны:
Согласовав эти значения с рядом нормальных линейных размеров принимаем:
Угол фаски при твердости колеса H ≤ 350HB принимают αф = 45°.
Для колеса тихоходной ступени эти параметры будут равны:
Проверочный расчет редуктора
14.Подбор материала твердости и термообработки зубчатых колес
Для выбора материала и его твердости прежде всего необходимо определить необходимый предел выносливости материала Hlim.
где [H] – допускаемое контактное напряжение;
SH – коэффициент безопасности;
ZN – коэффициент долговечности.
Для быстроходной передачи при предварительном расчете коэффициент долговечности можно принять ZN = 1; коэффициент безопасности зависит от вида термообработки в данном случае выбираем SH=11 [1 табл. 8.8].
Для тихоходной передачи при предварительном расчете коэффициент долговечности желательно принять большим единицы ZN = 107; коэффициент безопасности в данном случае выбираем SH = 11 [1 табл. 8.8].
Необходимую твердость материала для шестерни можно получить по формуле либо в единицах HRC либо в единицах HB.
Для шестерни быстроходной передачи назначаем [1 табл. 8.7]:
материал: сталь 40Х;
твердость: H1Б = 280
термообработка: закалка ТВЧ.
Для шестерни тихоходной передачи назначаем [1 табл. 8.7]:
твердость: H1Т = 260
Для колеса быстроходной передачи:
твердость: H2Б = 256
термообработка: улучшение.
Для колеса тихоходной передачи назначаем:
твердость: H2Т = 235
15.Проверочный расчет быстроходной передачи
15.1.Расчет допускаемых напряжений.
Для передач с твердостью колеса H2 ≤ 350HB допускаемое контактное напряжение определяется как
где [H]1Б – допускаемое контактное напряжение на шестерне;
[H]2Б – допускаемое контактное напряжение на колесе.
где NHG – предел контактной выносливости;
NHE – эквивалентное число циклов нагружения.
где n – частота вращения быстроходного вала n1Б = 1445 мин–1;
с – число зацеплений зуба за один оборот с = 1.
ZN должно быть числом не меньшим единицы следовательно принимаем ZN1Б = 1.
Коэффициент безопасности для закалки ТВЧ равен SH = 12.
Проводим аналогичные расчеты для колеса быстроходной передачи.
где n – частота вращения промежуточного вала n2Б = 2961 мин–1.
ZN должно быть числом не меньшим единицы следовательно принимаем ZN2Б = 1.
Коэффициент безопасности для улучшения равен SH = 11.
Допускаемые изгибные напряжения определяются по формуле:
где Fl для улучшения Flim = 18HB.
Flim2Б = 18·256 = 4608 МПа.
SF – коэффициент безопасности SF=175;
YA – коэффициент учитывающий влияние двустороннего приложения нагрузки для односторонней нагрузки YA = 1;
YN – коэффициент долговечности.
где NFG – предел изгибной выносливости для сталей NFG = 4·106;
NFE – эквивалентное число циклов нагружения.
где F – коэффициент эквивалентности зависящий от режима нагрузки. Для III режима нагрузки и закалки ТВЧ mF = 0036 для улучшения mF = 0065 [1табл.8.9].
YN1Б и YN2Б назначаем равным единице YN1Б = 1 YN2Б = 1.
15.2.Расчет рабочих напряжений
Величины рабочих контактных напряжений одинаковы для шестерни и колеса поэтому расчет выполняют только для шестерни. Контактное напряжение в зацеплении определяется по формуле:
где Eпр – приведенный модуль упругости. Для стальных колес и шестерен Епр = 21×105 МПа;
Т1 – момент на шестерне передачи Т1Б = 28097 Н×м;
u – передаточное число передачи uБ = 488;
KH – коэффициент нагрузки.
При расчете передачи коэффициент ZHb равен 1 т.к. быстроходная ступень состоит из прямозубой зубчатой передачи.
Коэффициент нагрузки KH представляется в виде
где KHb – коэффициент учитывающий распределение нагрузки по ширине венца. Назначается в зависимости от схемы нагружения от параметра ybd = bw dw1 и от сочетания твердости зубьев шестерни и колеса; для нашего случая ybd = 1397 и KHb = 105 [1 рис. 8.15]
KHV – коэффициент учитывающий динамическую нагрузку в зацеплении зависящий от вида передачи степени точности и окружной скорости V; KHV = 115 [1 табл. 8.3]
KH = 107 × 115 = 123
Получили контактное напряжение большее допустимого. Для обеспечения прочности необходимо увеличить ширину зубчатого венца. Назначаем bw = 55 мм. При этом изменится значение ybd а значит изменится значение KHb и KH.
Изгибные напряжения в основании зубьев косозубых колес определяются по формулам:
KFb=113 [1 рис. 8.15]
KF= KFb* KFV=1469 [1 стр. 133];
15.3.Проверка прочности по контактным и изгибным напряжениям
Чтобы проверить работоспособность передачи необходимо сравнить допустимые и рабочие контактные напряжения. Критерий прочности по контактным напряжениям:
Критерий прочности по напряжениям изгиба:
Оба критерия выполняются следовательно передача работоспособна.
16.Проверочный расчет тихоходной передачи
16.1.Расчет допускаемых напряжений
Для косозубых передач с твердостью колеса H2 ≤ 350HB допускаемое контактное напряжение определяется как
где [H]1Т – допускаемое контактное напряжение на шестерне;
[H]2Т – допускаемое контактное напряжение на колесе.
где n – частота вращения промежуточного вала n1Т = 2955 мин–1;
Полученное значение коэффициента ZN меньше единицы поэтому примем его равным 1.
Проводим аналогичные расчеты для колеса тихоходной передачи.
где n – частота вращения тихоходного вала n2Т = 7418 мин–1.
Полученное значение коэффициента ZN больше единицы.
Необходимо проверить условие :
Окончательное значение [H]T оставляем равным 528 МПа.
Flim2Т = 18·235 = 423 МПа.
YN1Т назначаем равным единице YN1Т = 1.
16.2.Расчет рабочих напряжений
Т1 – момент на шестерне передачи Т1Т = 658 Н×м;
u – передаточное число передачи uТ = 395;
При расчете косозубой передачи коэффициент ZHb определяется по формуле:
где KHa – коэффициент учитывающий распределение нагрузки между зубьями зависящий от степени точности KHa = 107 [1 стр. 133]
где KHb – коэффициент учитывающий распределение нагрузки по ширине венца. Назначается в зависимости от схемы нагружения от параметра ybd = bw dw1 и от сочетания твердости зубьев шестерни и колеса; для нашего случая ybd = 073 и KHb = 11 [1 рис. 8.15]
KHV – коэффициент учитывающий динамическую нагрузку в зацеплении зависящий от вида передачи степени точности и окружной скорости V; для V = 084 мс KHV = 102 [1 табл. 8.3]
KH = 11 × 102 = 1122
KF= KFb* KFV=125 [1 стр. 133];
16.3.Проверка прочности по контактным и изгибным напряжениям
17.Проверка быстроходного вала
17.1.Определение запаса прочности вала
Расчетная схема вала рассматривается в двух взаимно перпендикулярных плоскостях – плоскости YOX (вертикальной плоскости) и ZOX (горизонтальной плоскости). Также большинство муфт вследствие неизбежной несоосности соединяемых валов нагружают вал дополнительной силой FM поэтому дополнительно рассматривается плоскость в которой расположен вектор силы FМ – плоскость смещения рассчитываемого и присоединяемого к нему валов.
При расчете валов приближенно можно принимать для входных валов редукторов . В нашем случае .
Эпюры моментов строим используя формулу разброса. Отмечу что для дальнейших расчетов нам безразличен знак полученного момента поэтому все эпюры (см. рис. 5.1) построены в положительной полуплоскости.
где a – расстояние от опоры В до середины шестерни а = 9325 мм;
b – расстояние от опоры А до середины шестерни b = 9325 мм;
с – расстояние от конца вала до опоры А с = 93 мм;
l – расстояние между опорами l = 187 мм.
Вертикальная плоскость:
Горизонтальная плоскость:
Плоскость смещения валов:
Максимальные реакции в опорах:
Для определения опасного сечения необходимо построить эпюру суммарного момента формула для расчета которого имеет вид:
где момент в вертикальной плоскости Мверт = Мr + Ma1(2).
Крутящий момент Т равен входному моменту Tвх. Полученные эпюры приведены на рисунке 5.1.
Анализируя полученную эпюру суммарного момента установили что опасным сечением будет сечение под шестерней. Так как шестерня нарезана на валу материал вала будет такой же как и у шестерни – сталь 40Х для которой В = 950 МПа Т = 700 МПа. Диаметр вала в этом месте можно принять d=df1Б=34 мм а само зубчатое колесо в плане концентратора напряжения можно рассматривать как нарезанные эвольвентные шлицы. Суммарный изгибающий момент в этом сечении равен Мсумм = 110496 Н·мм.
При совместном действии напряжений кручения и напряжения изгиба запас сопротивления усталости определяют по формуле
где – запас сопротивления усталости при изгибе;(5.1)
– запас сопротивления усталости при кручении.(5.2)
В этих формулах а и а – амплитуды переменных составляющих циклов нагружений а m и m – постоянные составляющие.
Рис. 5.1. Эпюры изгибающих и крутящего моментов
и – коэффициенты корректирующие влияние постоянной составляющей цикла напряжений на сопротивление усталости; их величины зависят от механических характеристик материала
–1 и –1 – пределы выносливости
где К и К – эффективные коэффициенты концентрации напряжений К = 17 К = 155 [1 табл. 15.3];
Подставляем полученные значения в (5.1) и (5.2):
Получаем запас сопротивления
Так как запас большой то расчет на жесткость не требуется.
Следовательно запаса сопротивления усталости достаточно для обеспечения работоспособности вала.
17.2.Проверка правильности выбора подшипников
При частоте вращения n ≥ 10 мин1 расчет производится по динамической грузоподъемности. В нашем случае очевидно что более нагружен левый подшипник следовательно расчет будем производить по нему. Для быстроходного вала мы выбрали подшипник 206 ГОСТ 8338–75: динамическая грузоподъемность Cr = 153 кН; статическая грузоподъемность С0r = 102 кН.
Эквивалентная динамическая нагрузка определяется уравнением:
где X – коэффициент радиальной нагрузки Х = 1;
V – коэффициент зависящий от того какое кольцо подшипника вращается в нашем случае равен 1 так как вращается внутреннее кольцо подшипника;
Fr – радиальная сила равная максимальной радиальной реакции опоры А Fr = RA = 5995 Н;
Y – коэффициент осевой нагрузки Y = 0;
Fa – осевая сила равная осевой силе зубчатого зацепления Fa=0;
КБ – коэффициент безопасности учитывающий характер нагрузки КБ = 125 [2 табл. 7.4];
КТ – температурный коэффициент равный 1 [2 стр. 107]
Полученное значение Сгр = 4272кН базовой меньше динамической грузоподъемности подшипника Cr = 153 кН следовательно подшипник 206 ГОСТ 8338–75 обеспечивает необходимую грузоподъемность.
18.Решение вопроса о вале-шестерне
Шестерни для редукторов выполняют в двух конструктивных исполнениях – либо нарезанными на валу (вал-шестерня) либо отдельно от него (насадная шестерня). Для решения вопроса о конструктивном исполнении необходимо определить зазор Δ между дном шпоночного паза в шестерне и окружностью впадин зубьев. Этот зазор как видно из рисунка 5.2 можно определить как
где dвал – планируемый диаметр шейки вала для установки шестерни в нашем случае dвал = dБП;
t2 – глубина шпоночного паза в шестерне.
Если Δ > 25m то шестерня выполняется отдельно от вала.
Рис. 5.2. Шестерня в разрезе
Очевидно что шестерня быстроходной передачи не может быть выполнена в виде насадной шестерни так как зазор Δ будет отрицателен (df1Б = 34 мм; dБП = 34 мм). Для шестерни тихоходной передачи выполним расчет.
На вал диаметром dБП = 44 мм ставятся шпонки сечением 12х8 мм и в ступице выполняется паз глубиной t2 = 33 мм.
Для шестерни с df1Т = 4832 мм и модулем m = 25 зазор Δ будет равен:
Следовательно шестерня тихоходной передачи будет также выполнена непосредственно на валу.
19.Подбор и расчет шпоночных соединений
Для передачи вращающего момента в соединениях зубчатых колес с валами и на концах валов используем призматические шпонки ГОСТ 23360–78. Подбор шпонки заключается в выборе по стандартам ширины шпонки b и высоты h а также в определении рабочей длины lр и длины шпонки lш. Для нашего редуктора необходимо четыре шпонки – по одной на каждом из концов и по одной под каждым из колес зубчатой передачи.
Приняв [см] = 100 МПа определим параметры шпонок:
на конце быстроходного вала устанавливается шпонка сечением 8х7 мм [2 табл. 24.27]. Рабочая длина шпонки:
Данное значение длины есть в сортаменте шпонок сечения 8х7 мм следовательно на конец быстроходного вала устанавливаем шпонку 8х7х18 ГОСТ 23360–78.
на конце тихоходного вала устанавливается шпонка сечением 14х9 мм [2 табл. 24.27]. Рабочая длина шпонки:
Выбираем из сортамента длину шпонки lш=63 мм. Данное значение длины есть в сортаменте шпонок сечения 14х9 мм следовательно на конец быстроходного вала устанавливаем шпонку 14х9х63 ГОСТ 23360–78.
- под быстроходным колесом устанавливается шпонка сечением 10х8 мм [2 табл. 24.29]. Рабочая длина шпонки:
Из сортамента выбираем шпонку 10х8х32 ГОСТ 23360–78.
под тихоходным колесом устанавливается шпонка сечением 20х12 мм [2 табл. 24.29]. Рабочая длина шпонки:
Из сортамента выбираем шпонку 20х12х56 ГОСТ 23360–78.
Эскизы стандартных изделий
Иванов М.Н. Детали машин: Учеб. для студентов вузов. – 6-е изд. перераб. – М.: Высш. шк. 2000 – 383 с. ил.
Дунаев П.Ф. Леликов О.П. Конструирование узлов и деталей машин: учебное пособие. – 9-е изд. перераб. и доп. – М.: Академия 2006. – 496 с.
Прокшин С.С. Беляев Б.А. Методические указания к курсовому проектированию по дисциплине «Детали машин и основы конструирования»: Уфимск. гос. авиац. техн. ун-т. – Уфа 2006. – 58 с.
Дунаев П.Ф. Леликов О.П. Детали машин. Курсовое проектирование: Учеб. пособие. – 2-е изд. перераб. и доп. – М.: Высшая школа 1990 – 399 с.
эпюра.frw

Титульник - Галаганов.doc
Государственное образовательное учреждение высшего профессионального
Уфимский государственный авиационный технический университет
Кафедра «Основы конструирования механизмов и машин»
Проектирование узла быстроходного вала редуктора
Пояснительная записка
к курсовой работе по дисциплине
Детали машин и основы конструирования
Рекомендуемые чертежи
- 24.01.2023