Проектирование призматического фасонного резца и машинного метчика М36-6Н




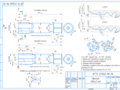
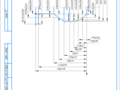
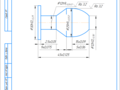
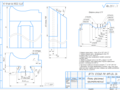
- Добавлен: 24.01.2023
- Размер: 967 KB
- Закачек: 0
Описание
Состав проекта
![]() |
![]() ![]() ![]() |
![]() |
![]() ![]() ![]() ![]() |
![]() ![]() ![]() ![]() |
![]() ![]() ![]() ![]() |
![]() ![]() ![]() ![]() |
![]() ![]() ![]() ![]() |
![]() ![]() ![]() ![]() |
![]() ![]() ![]() |
Дополнительная информация
Отклонения.docx
Задаются чертежом детали
Базовый радиус имеет наименьший допуск
Высота профиля детали переносимая с резца на деталь hi
Определяется как разность и
Высота точки профиля резца проставляемая на рабочем чертеже Pi’
Отсчитывается от точки (участка) обрабатывающий базовый радиус детали
Допуск на высоту профиля переносимую с резца на деталь
У всех точек кроме базовой должно быть положительным и больше 002
Часть допуска высоты отводимая на погрешности от неточной заточки и установки резца
Считается по формуле
Часть допуска высоты отводимая на неточности выполнения высот профиля Pi’
Допуск на высоту профиля Pi’
Верхнее и нижнее отклонения высоты профиля Pi’
Проставляются на чертеже резца у соответствующих размеров
Таблица 7 – Расчет отклонений высот профиля
Метчик М4.cdw

Рабочую часть цианировать на глубину 0
Сварка контактная стыковая оплавлением
Центровые отверстия притереть
Затыловать по профилю на всей длине калибрующей части величина
Неуказанные предельные отклонения H14
Обратная конустность 0
2 мм на 100 мм длинны
ВГТУ. 121268. РИ. М4
Отверстия центровые по ГОСТ 14034-74
2-Технологическая схема.cdw

3-График изменения залнего угла.cdw

4-Резец круглый.cdw

Материал режущей части - быстрорежущая сталь Р18
или другой марки по ГОСТ 19265-73*.
Ружущая часть резца приваривается методом контактной
Твердость у режущей части 62 66 HRC
у корпуса 41 46 HRC.
Размеры контургых точек профиля резца получить коррекционным
расчетом с отклонением до 0
Неуказанные придельные отклонения размеров
Маркировать: код (номер) обрабатываемой заготовки
товарный знак завода-изготовителя.
ВГТУ. 121268. РИ. ФРI-04. 04
1-Эскиз детали.cdw

5-Шаблон и контшаблон.cdw

или другой марки для измерительного инструмента.
Твердость у шаблона и контршаблона 62 65 HRC.
Неуказанные предельные отклонения размеров
Маркировать: код обрабатываемой детали резцом
для которой предназначен шаблон и контр шаблон
ВГТУ. 121268. РИ. ФРI-04. 05
ФР I-04-М4.docx
4 Выбор материала инструмента8
5 Выбор конструктивных параметров инструмента (предварительно)9
6 Определение режимов резания и вида оборудования10
7 Составление технологической схемы обработки детали13
8 Cоставление расчетной схемы и расчетного формуляра23
9 Коррекционный расчет24
10 Расчет допусков на профиль инструмента и шаблона25
11 Расчет задних углов в нормальном сечении к проекции режущей кромки26
12 Мероприятия по уменьшению трения по задней грани резца.29
14 Схема износа инструмента. Причины факторы и вид износа30
16 Определение технических требований и маркируемых параметров32
ПРОЕКТИРОВАНИЕ РЕЗЬБОНАРЕЗАЮЩЕГО ИНСТРУМЕНТА33
1 Выбор типа метчика определение числа метчиков в комплекте33
2 Выбор схемы резания34
3 Выбор материала режущей части инструмента35
5 Предварительный выбор35
6 Проектный расчет36
СПИСОК ИСПОЛЬЗОВАННЫХ ИСТОЧНИКОВ41
ПРОЕКТИРОВАНИЕ ФАСОННОГО ИНСТРУМЕНТА
Материал детали: сталь (НВ 150);
Конструкция резца – призматический.
Определяем возможность обеспечения заданной точности и шероховатости поверхностей детали проектируемым резцом.
Точность изготовления детали соответствует 12-ому квалитету. Неуказанные допускаемые отклонения на свободные размеры заданной детали выполняем по 12 квалитету точности: валы по h12 остальные .
Для достижения такой точности и соответствующей шероховатости поверхности можно не применять операцию шлифования а непосредственно получить ее окончательно при помощи проектируемого круглого фасонного резца в несколько переходов:
-подача прутка 2-порезка торца 3-фасонное точение 4-отрезка детали.
2.1 выполняем анализ точности изготовления детали
По таблице 32 [2 c.70] экономическая точность обработки и шероховатость поверхности при обработке на токарных станках наружной поверхности при чистовой обработке соответствует 2-5 классу точности и 5-7 классу шероховатости (в системе ОСТУ) что соответствует 7-10 квалитету точности и параметру шероховатости Ra 32-08 мкм. То есть фасонная обработка лезвийным инструментом возможна если точность изготовления не превышает 9 квалитет.
Деталь удовлетворяет требованиям экономически достижимой точности.
Назначаем шероховатость обрабатываемых поверхностей по таблице 3 [3 c. 8].
- для 12 квалитета точности – значение шероховатости поверхности составит Ra=125 мкм.
Определяем квалитеты степени точности на размеры не указанные на эскизе в задании:
Допуск на неуказанные размеры при механической обработке резанием - по 12 квалитету точности; ±.
По источнику [1] определяем допускаемые отклонения:
Неуказанная шероховатость Ra 125
По принципу работы и направлению подачи токарные фасонные резцы разделяются на радиальные и тангенциальные [4 с. 10] [5 с. 165].
Принцип работы радиальных фасонных резцов основан на постепенном срезании в виде стружки всего подлежащего удалению объема металла режущим лезвием. По мере движения резца в работу вступают все новые и новые точки режущего лезвия и к концу обработки стружка срезается всем режущим лезвием. Так как в конечный момент резания деталь обрабатывается одновременно всем режущим лезвием поверхность детали должна быть ровной и гладкой.
В отличие от радиальных тангенциальные резцы устанавливают на станках на таком расстоянии от оси вращения детали чтобы прямолинейная подача осуществлялась по касательной к обработанной фасонной поверхности. Фасонные лезвия тангенциальных резцов образованы пересечением задних фасонных поверхностей резцов с передними поверхностями наклоненными под углами Y и X. Детали обработанные тангенциальными фасонными резцами не имеют совершенно гладкой и ровной фасонной поверхности как при обработке радиальными фасонными резцами. Обработанная поверхность представляет собой сочетание винтообразно расположенных отрезков спиральных поверхностей резания образованных за каждый оборот детали «скользящим» участком лезвия резца. В силу этих же причин контур диаметрального сечения детали представляет собой нс сплошную линию а сочетание (сопряжение) отрезков однополых гипербол образуемых осевым сечением винтообразно расположенных спиральных поверхностей резания.
Из вышеизложенного следует что для получения высокого класса точности и шероховатости обрабатываемых поверхностей целесообразно применение резца с радиальным врезанием.
Выбираем схему резания с радиальным врезанием резца. [4 с. 10] [5 с. 166] (см. рисунок 2).
Рисунок 2 – Схема резания
Форма среза изображен на рисунке 3.
Рисунок 3 – Форма среза
где: S-подача a-сечение среза;
4 Выбор материала инструмента
Выбор геометрии режущего клина
Материалом для фасонных резцов служит преимущественно быстрорежущая сталь (например Р6М5 или Р18) [6 с. 132]. Применение твердых сплавов для фасонных резцов затруднено из-за сложности изготовления и особенно сложных профилей [5 с. 165].
Геометрические элементы лезвия фасонных резцов (передний угол и задний ) зависят от материала обрабатываемой детали.
Для стали (НВ 235-280) из табл. 47 [6 с. 136]: = 25° = 8° 15°
Рисунок 4 – углы режущего клина
5 Выбор конструктивных параметров инструмента (предварительно)
Конструктивные и габаритные размеры фасонных резцов выбираются в зависимости от наибольшей глубины профиля обрабатываемой детали (рис. 1) tmax [6 с. 132].
По табл. 44 [6 с. 133] определяем размеры резца (рисунок 5) и данные сводим в таблицу 1.
Таблица 1 – Конструктивные параметры резца мм
Глубина профиля заготовки tmax не более мм
6 Определение режимов резания и вида оборудования
При фасонном точении подача определяется в зависимости от диаметра обработки d ширины резца В. При диаметре обработки 40 мм и ширине резца 40 подачу принимаем S = 003-006ммоб [7 с. 269 табл. 16]. Меньшие значения принимаются для более сложных и глубоких профилей и твердых металлов большие - для простых профилей и мягких металлов. Принимаем значение подачи:
Скорость резания [7 c.268]:
где Су — коэффициент; у m - показатели степени;
Т - период стойкости инструмента;
Kv - общий поправочный коэффициент на скорость резания
[7 с. 270 табл. 17] при обработке фасонным точением конструкционных углеродостых сталей резцами из быстрорежущей стали Р18.
При фасонном точении резцами из стали Р18 с охлаждением Т = 120 мин [18 c.578 табл. 13].
где [7 c.261 табл.1] — коэффициент учитывающий влияние материала заготовки;
где: – коэффициент для материала инструмента [7 c.262 табл.2];
– показатель степени при обработке [7 c.262 табл.2];
- коэффициент учитывающий влияние состояния поверхности заготовки; (медные и алюминиевые сплавы) [7 с. 263 табл. 5];
- коэффициент учитывающий влияние материала инструмента; при обработке стали чугуна медных и алюминиевых сплавов резцами из быстрорежущей стали Р6М5 [7 с. 263 табл. 6].
Число оборотов шпинделя:
По паспорту станка вместо расчетного значения числа оборотов принимается ближайшее меньшее значение обеспечиваемое коробкой скоростей станка или большее не превышающее 5% расчетного.
Принимаем nст = 500 мин-1.
Фактическая скорость резания:
Главная составляющая силы резания [7 с. 271]
где Ср - коэффициент;
х у z - показатели степени;
Кр - поправочный коэффициент;
t = 53 мм - длина лезвия резца (расчет в п. 1.7.4).
При обработке конструкционных сталей фасонными резцами из быстрорежущей стали Ср = 212; х = 10; у = 075; n = 0 [7 табл. 22 с. 273].
При обработке конструкционных углеродистых и легированных сталей поправочный коэффициент [7 c. 264 табл. 9]:
где n=035 показатель степени.
Мощность резания [7 с. 271];
6.2 Выбор вида оборудования
Фасонные резцы в основном находят применение на токарно- револьверных станках и полуавтоматах.
Фасонные резцы чаще всего применяют на токарно-револьверных станках в качестве рассматриваемого станка используем станок модели 1А240.
Станки модели 1А240 предназначены для высокопроизводительного выполнения разнообразных сверлильных токарных (обточка расточка зенкерование развёртывание отрезка подрезка прорезка канавок) и резьбонарезных работ.
Техническая характеристика станка модели 1А240:
Наименование параметра
Класс точности по ГОСТ 8-82
Количество рабочих шпинделей
Диаметр отверстия в шпинделях мм
Наибольшая длина обработки мм
Наибольшая длина подачи прутка мм
Наибольший диаметр прутка мм
Наибольшая сторона квадратного прутка мм
Наибольшая сторона шестигранного прутка мм
Наибольший диаметр резьбы нарезаемой метчиками по стали мм
Наибольший диаметр резьбы нарезаемой метчиками по латуни мм
Наибольшая длина прутка мм
Наибольшая масса обрабатываемой детали кг
Инструментальные суппорты
Количество продольных суппортов
Количество поперечных суппортов
Наибольший общий рабочий ход продольного суппорта мм
Наибольший общий рабочий ход поперечного суппорта I II III мм
Наибольший общий рабочий ход поперечного суппорта IV V мм
Наибольший общий рабочий ход отрезного суппорта VI мм
Частота вращения шпинделей обмин
Величина подач продольного суппорта ммоб
Величина подач поперечных суппортов ммоб
Количество электродвигателей на станке
Электродвигатель главного привода (шпинделей) кВт
Электродвигатель наладочного вращения кВт
Электродвигатель привода транспортера стружки кВт
Электродвигатель насоса смазки кВт
Электродвигатель насоса охлаждения кВт
Установленная мощность кВт
Габариты и масса станка
Габариты станка без приставного оборудования (длина ширина высота) мм
Рисунок 6 – Общий вид станка модели 1Г340П
Распределительный вал
Верхний поперечный суппорт
Упор материала для ограничения подачи прутка
Направляющие трубы для прутка
Привод устройств с независимой подачей
Задний поперечный суппорт
Передний поперечный суппорт
7 Составление технологической схемы обработки детали
7.1 Составление фрагмента технологического маршрута обработки детали.
Содержание фрагмента технологического маршрута обработки детали:
-установка штучной заготовки или подача прутка по упору;
-проточка заготовки до кулачков;
-отрезка готовой детали;
7.2 Выбор нуля координат
Для определения профиля фасонного резца аналитическим способом необходимо описывать профиль детали в системе координат. В связи с этим целесообразно принять декартовую систему координат X - У таким образом чтобы ось X совпадала с осью детали а начало координат располагалось в правой торцевой плоскости. Рабочий чертеж детали содержит различную простановку размеров. Такая простановка размеров неверна как с технологической точки зрения (ввиду наложения погрешностей обработки предыдущего звена на последующее) так и для аналитического расчета [11 с. 126]. Поэтому приходится производить их перерасчет в принятую систему т.е. задавать размеры вдоль оси детали от одной базы - правого торца. Притом т.к. особых требований к точности детали в осевом направлении чертежом не предусматривается то допускаемые отклонения принимаются для вновь принятых размеров детали.
За нулевую точку (начало декартовой системы координат) принимаем точку расположенную на правом торце детали и наименьшем диаметре.
Ось X располагается параллельно оси детали a Y перпендикулярно ей.
7.3 Нумерация расчетных точек с учетом дополнительных точек
Вводим номера точек (см. рисунок 8) по которым будем производить расчет профиля. Расчетные точки выбираются на узловых точках профиля детали дополнительные вводим (точки 1236).
Рисунок 7 – Выбор декартовой системы координат
Рисунок 8 – Нумерация расчетных точек
7.4 Конструирование левой и правой дополнительных частей профиля резца
Кроме основной режущей части lд создающей фасонные очертания обрабатываемой детали (рисунок 9) фасонный резец должен иметь дополнительные режущие кромки подготовляющие отрезку детали от прутка и обрабатывающие фаску или часть детали срезаемую при подрезке.
Назначаем размеры элементов дополнительных режущих кромок по рекомендациям [6 с. 137]:
- дополнительная упрочняющая режущая кромка а=2 мм;
- высота участка режущей кромки предназначенной для протачивания канавки с целью облегчения отрезания детали t=5 мм;
- ширина участка режущей кромки предназначенной для протачивания канавки с целью облегчения отрезания детали b=5 мм;
- перекрытие режущей кромки под отрезание b1=1 мм;
- угол режущей кромки под отрезание .
Рисунок 9 – Дополнительные части профиля резца
7.4 Перевод размеров детали в средние размеры с семеричными допусками
Определим значения диаметров проходящих через дополнительные точки на радиусном и конусном участке детали.
Для определения диаметров и линейных размеров расположения дополнительных точек на радиусном и конусном участке построим профиль детали в графическом редакторе «Компас» и измерим диаметры с точностью до второго знака (см. рисунок 10).
Рисунок 10 – Эскиз детали для определения координат дополнительных точек
Координату середины симметричного поля допуска рассчитываем по формуле:
где верхнее отклонение; ei - нижнее отклонение.
Номинальное значение диаметр и с симметричным нолем допуска
Верхнее и нижнее отклонение на средний размер будет равно половине допуска на заданный размер соответственно со знаком «+» и «-».
Определяем средние размеры диаметров с симметричными допусками Расчет выполняем в виде таблицы 2.
Таблица 2 - Расчет средних размеров (мм)
Координаты середины поля допуска
Рисунок 11 – Схема для расчета
Линейные размеры (вдоль оси детали) назначаем от одной базы - правого торца являющегося началом отсчета координат. Номинальные значения размеров рассчитываем решая размерные цепи. (см. рисунок 11).
Вычерчиваем профиль детали и наносим ранее рассчитанные размеры.
Рисунок 12 – Профиль детали с размерами
7.7 Выполнение технологической схемы с координатами и допусками на них
Производим расчет координат основных и дополнительных точек профиля в выбранной декартовой системе координат (данные заносим в таблицу 2).
За ноль координат принимаем правый торец детали и минимальный радиус (участок профиля 7-8). Далее рассчитываем допуск на глубину профиля детали между выбранной базой и точками профиля. Глубина профиля для рассматриваемой точки является замыкающим звеном размерной цепи составляющими которой является радиус базы Rб и радиус рассматриваемой точки Ri. В этом случае если размеры детали при изготовлении подчиняются нормальному закону распределения а границы их вероятного рассеяния совпадают с границами полей допусков допуск на замыкающее звено можно определить как среднее геометрическое (квадратный корень из суммы квадратов) допусков составляющих размеров.
где -допуск на радиус базы;
-допуск на радиус точки.
Допуск на радиус при токарной обработке равен половине допуска на диаметр
Координаты точки по координате Y определяем по формуле:
Координаты по оси Y для:
Допуск на радиус базы
Результаты расчетов сводим в таблицу 3.
Таблица 3 - Координаты точек профиля
По данным таблицы 2 выполняем технологическую схему (см. рисунок 13):
Рисунок 13 – Технологическая схема
8 Cоставление расчетной схемы и расчетного формуляра
Расчетную схему (рисунок 14) выполняем используя в качестве примера рисунок 66 [5 c.169] и рисунок 313 [14 c86]. Расчетный формуляр см. таблицу 4. Исходные данные для расчета – таблица 5.
Таблица 4 – Расчетный формуляр (заголовок)
Рисунок 14 – Расчетная схема
9 Коррекционный расчет
По полученным выше параметрам производим коррекционный расчет профиля резца. Все расчеты выполняем в виде таблицы 5.
Таблица 5 – Коррекционный расчет
10 Расчет допусков на профиль инструмента и шаблона
10.1 При настройке резца на суппорте станка во время обработки деталей обычно измеряется наиболее точный из всех диаметров фасонной детали. Такой участок профиля и соответственно диаметр называют базовым (измерительным). В данном случае – диаметр точка 0.
Участок профиля резца обрабатывающий базовый диаметр называют базовым участком отсчета исполнительных высотных размеров профиля резца который может не совпадать с базовым участком (точкой) коррекционного расчета. В таком случае необходимо произвести простановку высотных размеров профиля резца от вновь выбранной базы. То же самое производится и на профиле детали. В нашем случае базовый участок отсчета исполнительных высотных размеров профиля резца совладает с базовым участком (точкой) коррекционного расчета. Расчет выполняем в виде таблицы 6.
Расчет выполняем по методике изложенной в источнике [14 с. 101].
10.2 Допуски на продольные размеры профиля резца
Допуски на продольные размеры детали значительно шире чем на ее диаметры. Поэтому допустимо приближенное назначение допусков на продольные размеры профиля резца. При этом допуски размеров берутся в 2 3 раза уже чем допуски соответствующих размеров детали.
Соответственно допускаемые отклонения составят:
Выполняем эскиз режущей части резца в нормальном сечении (рисунок 15) и проставляем на нем размеры с вычисленными допусками.
Рисунок 15 – Размер профиля инструмента в нормальном сечении
10.3 Допуски на профиль шаблона и контршаблона принимаются равными соответствующих допусков на профиль инструмента (рисунок 15) но не менее 0005 мм. Соответственно получим:
- допускаемые отклонения в радиальном направлении
- допускаемые отклонения в осевом направлении
11 Расчет задних углов в нормальном сечении к проекции режущей кромки
Задний угол в произвольной точке X в сечении N-N перпендикулярном к режущей плоскости резца определяется по формуле [9 с. 197]:
где — угол между касательной к профилю резца в рассматриваемой точке и прямой перпендикулярной к оси детали. Причем в переходных точках (на изломах плоскостей) имеет два значения;
- задний угол на вершине резца рассматриваемый в плоскости перпендикулярной к оси детали в данной точке.
Определим угла в каждой точке (см. рисунок 16). Угол в каждой точке определим графически при помощи геометрических построений в 2D- редакторе: ; ; ; ; ; ; ; ; ; ; ; ; ; ; ; ;
Рисунок 16 – Угол в плане в узловых точках
Определяем угол в каждой точке из выражения [4 c.30].
Где и – из таблицы 5.
Данные расчета заносим в таблицу 7.
Таблица 7 – Расчет заднего угла
По полученным результатам стоим график изменений заднего угла (см. рисунок 17). По абсциссе откладываем длину развертки линии профиля резца в миллиметрах с обозначением узловых точек а по ординате – значения углов в градусах.
Рисунок 17 – График изменения заднего угла
12 Мероприятия по уменьшению трения по задней грани резца.
Выбор соответствующих мероприятий.
Если задний угол на каких то участках профиля резца меньше то необходимо уменьшить трение на задней грани резца.
Это можно осуществить за счет следующих мероприятий [5 c.168]:
- поднутрения с углом (см. рисунок 18 а);
- ленточку на небольшом участке профиля резца (см. рисунок 18 б);
Для нашего варианта выбираем поднутрение с углом
Рисунок 18 – Уменьшение трения по задней поверхности резца
Призматические фасонные резцы имеют большое число переточек. Их вершину в осевой плоскости заготовки устанавливают регулировочным винтом. Задний угол у этих резцов получают при установке их в специальные
резцедержатели под углом α=10 12°. Крепление и базирование резца в резцедержателе осуществляется с помощью хвостовика типа ласточкина хвоста (Рисунок 18): [10с.256].
Рисунок 20 – Державка для призмитических радиальных резцов для работы на станка типа 1А240
После износа резца его перетачивают. Чтобы установить резец на ту же высоту используют регулировочный винт 4. Для достижения точности при установке по высоте используют шкалу на прихвате для зажима резца 5 и риску на резце 3.
14 Схема износа инструмента. Причины факторы и вид износа
Потеря режущей способности инструментов [5 с. 91] вызывается: изнашиванием или истиранием контактных поверхностей на рабочих площадках инструмента выкрашиванием мельчайших частиц на режущем лезвии которое характерно для инструментов из более хрупких материалов.
Основной причиной затупления инструментов при нормальных условиях работы является износ в результате истирания их рабочих поверхностей. Истирание контактных площадок может быть [5 с. 91]:
Износ по задней поверхности характеризуется высотой площадки hизн (Рисунок 21). Износ по передней поверхности характеризуется в основном шириной лунки b. В процессе работы инструмента износ как по передней так и по задней поверхностям увеличивается уменьшая площадку с. Когда ширина лунки b достигнет режущей кромки последняя разрушится и резец выйдет из строя. hизн=08 мм.
У фасонных резцов преимущественное затупление происходит по задней поверхности. Наиболее интенсивно изнашиваются лезвия вступающие в резание первыми [10 с. 187].
Рисунок 21 – Схема износа резца
Заточку фасонных резцов (рисунок 22) производят по передней поверхности т.к. задняя поверхность у резцов имеет сложную конфигурацию и поэтому переточка по ней затруднена. Заточка производится на универсально-заточных станках шлифовальными чашечными кругами [12 с. 111].
Применяем: универсально-заточной станок мод. ЗА64Д. Станок предназначен для затачивания основных видов режущих инструментов абразивными и алмазно-абразивными кругами. Все движения при затачивании инструмента и настройке производятся вручную. Вращение шпинделя шлифовальной головки станка – от двухскоростного электродвигателя.
По таблице 14.31 [15 с. 771] рекомендуется применять шлифовальные круги со следующими характеристиками:
- материал - электрокорунд 24А;
- зернистость - 40 25;
- степень твердости - СМ1 СМ2;
- связка - К (керамическая).
Для заточки принимаем абразивный шлифовальный круг типа 11 175x63x32 24А 25 СМ1 Кб 30 мс А 2 кл.
Рисунок 20 – Схема заточки
16 Определение технических требований и маркируемых параметров
Технические требования на резец составляем аналогично изложенным на рисунке 37 [6 рис. 145].
Твердость режущей части 63 66 HRC.
общие допуски по ГОСТ 25346-89: +1 IT122.
Маркировать: индекс детали марка стали резца передний угол задний угол (ФРI-04-Р18--).
Технические требования к шаблону и контршаблону:
Твердость шаблона и контршаблона 62 65 HRC.
Общие допуски по ГОСТ 25347-82: +1 IT122.
Маркировать: код обрабатываемой детали резцом для которого предназначен шаблон и контршаблон (ФРI-04).
ПРОЕКТИРОВАНИЕ РЕЗЬБОНАРЕЗАЮЩЕГО ИНСТРУМЕНТА
Метчик. Обрабатываемы материал: сталь . Резьба M36 – 6H. Длинна отверстия 30 мм. Разновидность метчика – машинный.
Эскиз детали представлен на рисунке 21.
1 Выбор типа метчика определение числа метчиков в комплекте
Для нарезания основной метрической резьбы (с крупным шагом) рекомендуются следующие комплекты: для глухих и сквозных отверстий диаметром 2–24 мм – два метчика; для глухих и сквозных отверстий диаметром 27–52 мм – три метчика. При нарезании резьбы в сквозных отверстиях небольшой длины диаметром 2–24 мм можно применять один метчик если его режущие и калибрующие зубья шлифованы по всему профилю. Метчики с мелкой метрической резьбой а также все машинные рекомендуется изготовлять: для глухих отверстий – комплект из 2а для сквозных – 1 шт.
Окончательное решение о количестве метчиков в комплекте принимается после проверки выполнения условия
где Mр – крутящий момент резьбонарезания;
Mкр – критический крутящий момент допускаемый прочностью метчика.
где d – номинальный наружный диаметр метчика (d = D);
CM qM YM – коэффициент и показатели степени учитывающие материал
заготовки и рабочей части метчика;
KM – коэффициент учитывающий тип метчика и обрабатываемый
K3 – коэффициент учитывающий влияние затупления метчика [17 с. 17 табл. 1.4].
Значение Mкр для метчиков приведены в [17 с. 17 табл. 15].
Условие не выполняется. Следовательно одним метчиком нарезать резьбу с заданными параметрами нельзя.
Проверим возможность нарезания резьбы комплектом из 2-х метчиков.
Момент резьбонарезания первым (черновым) метчиком:
Условие выполняется. Следовательно для нарезания резьбы необходимо рассчитать комплект из 2-х метчиков.
Поскольку исполнительные диаметры резьбы первого (чернового) метчика находятся в зависимости от размеров последнего (чистового) метчика то и расчет нужно начинать с последнего.
2 Выбор схемы резания
При формировании впадины резьбы режущая часть метчика может срезать припуск по одинарно-генераторной или одинарно-профильной схемам. Большинство метчиков работает по первой схеме. Вторую схему резания применяют для калибрующих (плашечных) и конических метчиков.
Рисунок 22 - Схемы формирования профиля резьбы одинарно-генераторным методом
При одинарно-генераторной схеме каждый зуб срезает стружку разной ширины bZ и одинаковой толщины az
Рекомендуемые и предельные значения az для различных обрабатываемых материалов приведены в [17 с. 18 табл. 1.7].
Рекомендуемая толщина срезаемой стружки для стали будет равно:
3 Выбор материала режущей части инструмента
Материал рабочей части метчиков определяется условиями его эксплуатации [14 с. 221 табл. 7.1].
Для нарезания резьбы в сталях и цветных металлах по [14 с. 221 табл. 7.1] применяют быстрорежущие стали Р6М5 или Р6М3.
Скорость резания v зависит от материала детали диаметра и шага нарезаемой резьбы. При обработке чугуна скорость резания ниже чем при обработке конструкционной углеродистой стали [19 c.255 табл. 65]. Резьба в деталях из алюминиевых сплавов нарезается на более высоких скоростях резания. С увеличением диаметра резьбы скорость резания возрастает.
В [19 c.256 табл. 66] даны значения скоростей резания для обработки труднообрабатываемых материалов. На скорость резания существенное влияние оказывает прочность материала.
В нашем случае по заданию задана сталь с механическими характеристиками . По [19 c.255 табл. 65] для диаметра 36 мм и шага резьбы 2 мм примем рекомендуемые скорость резания:
5 Предварительный выбор
По ГОСТ 3266-81 примем предварительные габаритные размеры метчика:
Рисунок 23 – Предварительные размеры
На основании задания эту резьбу будем нарезать машинным метчиком с прямыми стружечными канавками.
По [17 с.21 табл. 110] для резьбы М36 находим число перьев:
По [17 с.12 табл. 13] находим номинальные средний и внутренний диаметры резьбы гайки:
В табл. 1.16 [17 с. 31 табл. 116] (ГОСТ 16093–2004) находим допуск на средний диаметр резьбы гайки степени точности 6Н-TD2:
По [17 с. 30 табл. 115] в зависимости от степени точности нарезаемой резьбы 6Н находим класс точности метчика – 3.
Для метчика класса точности 3 по [17 с.33 табл. 118] находим формулу расчета нижнего отклонения на средний диаметр метчика:
По формуле (1.18) [17 с. 30] находим допуск на средний диаметр метчика:
Подставив численные значения величин в формулу (1.17) [17 с.30] найдем средний диаметр резьбы метчика:
Верхнее отклонение на средний диаметр метчика определим по формуле (1.19) [17 с. 33]:
Гарантированный запас на износ по среднему диаметру определим по формуле (220) [17 с.34]:
По формуле (1.23) [17 с. 34] находим нижнее отклонение на наружный диаметр метчика:
Определяем допуск на наружный диаметр резьбы метчика по формуле (1.24) [17 с. 34]:
Подставив численные значения величин в формулу (1.22) [17 с. 34] найдем наружный диаметр метчика:
Внутренний диаметр d1=D1=33835 мм. Допуск на d1 не имеет нижнего отклонения.
Наружный диаметр чернового метчика рассчитываем по формуле [17 с. 34 табл. 1.19]:
Допуск на этот диаметр назначается в 25 раза меньше величины занижения:
По формуле в [17 с. 34 табл. 1.19] находим средний диаметр чернового метчика:
Допуск на этот диаметр определяем по Н9 = + 0062.
Внутренний диаметр чернового метчика:
Режущая часть метчика.
По формуле из [17 с. 20 табл. 18] находим торцовой диаметр метчика:
Длинна режущей части метчика определяется по формуле из [17 с. 21 табл. 19]:
для чистового метчика
для чернового метчика
Подставляя численные значения d dT L1 в формулу (16) [17 с. 18] найдем:
По [17 с. 24 табл. 1.12] выбираем формулу для определения диаметр сердцевины метчика:
Длина калибрующей части [17 c. 22 табл. 111]:
L2 = (06 08)d = 0836=288 мм.
Ширина пера [17 c. 24 табл. 112]
Угол скоса перьев на режущей части находим по формуле 1.8 [17]:
Передний угол [17 c. 27 табл. 1.14];
Задний угол [17 c. 27 табл. 1.14];
Задний угол αв на наружном диаметре заборного конуса метчика может иметь значение от 5° до 20° и образуется путем затылования задней поверхности по архимедовой спирали. Величина падения затылка определяется по формуле 110 [17 c.27].
Диаметр хвостовика [17 с. 40 табл. 1.22]
dхв = d1 – (025 – 15)
dхв = 33835 – 15 = 323 мм.
Принимаем стандартное значение из [17 с. 40 табл. 1.22]:
Размер квадрата на хвостовике находим по формуле 1.26 [17 с. 40]:
где x – выбирается по [17 с. 40 табл. 123]
Высота квадрата h = a + 3 = 24 + 3 = 27 мм.
По ГОСТ 3266-81 находим длинну метчика для нарезания резьбы М36 с шагом 2 мм:
Рисунок 24 – Схема расчета длинны метчика при нарезании резьбы
Проверяем значение L расчетом по формуле 128 [17 c.40]:
L = L1+ LB+ LP+LT+ LХn
L1 – длина режущей части;
LВ – длина выхода калибрующей части метчика из отверстия: для некорригированных метчиков:
LР – длина резьбы с полным профилем в заготовке.
LТ – расстояние от торца патрона до заготовки
LХп – длина хвостовика находящаяся в патроне или в цанге [17 c.42 табл. 1.24].
L = 6+8+30+10+68= 122 мм
L' = 16+8+30+10+68= 132 мм
Выбираем большее значение L в данном случае принимаем гостовское значениен L=144 мм.
Зная длину метчика определим величину смещения заднего центра резьбошлифовального станка для создания обратной конусности
К0 = 005 – 01 мм на условной длине резьбы LУ = 100 мм по формуле:
СПИСОК ИСПОЛЬЗОВАННЫХ ИСТОЧНИКОВ
ГОСТ 25347-82 Основные нормы взаимозаменяемости. Единая система допусков и посадок. Поля допусков и рекомендуемые посадки.
Справочник металлиста. В 5-ти томах. Т5 Под ред. А.Н. Малова. - М.: Машгиз .1960.
Справочник технолога машиностроителя. В 2-х т. ТI под ред. А.Г. Косиловой и Р. Г. Мещерякова. - 4-е изд. перераб. и доп. - М.: Машиностроение 1986 -656 с.
Кузнецов Ю.И. Оснастка для станков с ЧПУ: Справочник Ю. И. Кузнецов А. Р. Маслов А. Н. Байков - 2-е изд. перераб. и доп. - М.:. Машиностроение 1990.-512 с.
Ящерицын П.И. Основы резания материалов и режущий инструмент; Учебник для машиностроит. спец вузов П. И. Ящерицын М. Л. Еременко Н. И. Жигалко - 2-е изд. доп. и перераб. - Мн.: Выш. школа 1981.- 560 с.
Нефедов Н.А. Сборник задач и примеров по резанию металлов и режущему инструменту: Учеб пособие для техникумов по предмету «Основы резания металлов и режущий инструмент» А.Н. Нефедов. - 5-е изд. перераб. и доп - М.; Машиностроение 1990.-448с.
Справочник технолога машиностроителя. В 2-х т. Т II под ред. А.Г. Косиловой и Р. Г. Мещерякова. - 5-е изд. перераб. и доп. - М.: Машиностроение 2003.-944 с.
Иноземцев Г.Г. Проектирование металлорежущих инструментов: Учебное пособие для втузов по специальности «Технология машиностроения металлорежущие станки и инструменты» Г. Г. Иноземцев. - М.: Машиностроение 1984. - 272 с.
Семенченко И.И. Проектирование металлорежущих инструментов И. И. Семенченко В. М. Матюшин Г. Н. Сахаров; под ред. И. И. Семенченко. - М.: Машгиз 1963. - 952 с.;
Грановский Г.И. Фасонные резцы Г. И. Грановский К. П. Панченко. - М.: Машиностроение 1975. - 309 с.
Ящерицын П.И. Основы проектирования режущих инструментов с применением ЭВМ П. И. Ящерицин Б. И. Синицын. - Мн.: Выш. школа 1979.-300 с.
Аршинов В.А. Резание металлов и режущий инструмент В. А. Аршинов Г. А. Алексеев. - 3-е изд. перераб. и доп. - М.; Машиностроение 1976. -410 с
Руководство по курсовому проектированию металлорежущих инструментов: Учеб. пособие для вузов по специальности «Технология машиностроения металлорежущие станки и инструменты» Под общ. ред. Г. Н. Кирсанова – М.: Машиностроение 1986. - 288 с.
Режущий инструмент. Курсовое и дипломное проектирование: учебное пособие под ред. Е.Э. Фельдштейна. Минск: Дизайн ПРО. 2002 – 320 с.
Справочник инструментальщика И. А. Ординарцев Г. В. Филиппов А. Н. Шевченко и др. Под общ. ред. И. А. Ордннарцева - Л: Машиностроение 1987. — 846 с.
Допуски и посадки. Справочник. В 2-х ч. Ч. 2 В. Д Мягков М А. Романов А. В. Романов В. А. Брагинский. 6-е изд. перераб. и доп. ~ Л.: Машиностроение 1983. - 448 с.
Киреев Г.И. Проектирование метчиков и круглых плашек: учебное пособие. – Ульяновск: УлГТУ 2008. -107 с.
Справочник машиностроителя. В2-х т. Т. II Под ред. А. Н. Малова - 2-е изд. перераб. и доп. -Москва; Машгиз 1963. - 912 с.
Драгун. А.П. Режущий инструмент для молодых рабочих А.П. Драгун.-Лениздат 1986 - с.271. ил.
Рекомендуемые чертежи
- 24.01.2023