Проектирование приводов с цилиндрическими редукторами




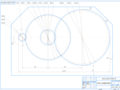
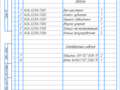
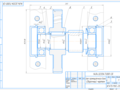
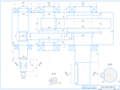
- Добавлен: 24.01.2023
- Размер: 1 MB
- Закачек: 0
Описание
Проектирование приводов с цилиндрическими редукторами
Состав проекта
![]() |
![]() |
![]() ![]() ![]() |
![]() |
![]() ![]() ![]() ![]() |
![]() ![]() ![]() ![]() |
![]() |
![]() |
![]() ![]() ![]() ![]() |
![]() |
![]() ![]() ![]() |
![]() ![]() ![]() ![]() |
Дополнительная информация
содержание введение спецификация Фомин.doc
Государственное образовательное учреждение высшего профессионального
Уфимский государственный авиационный технический университет
Кафедра «Основы конструирования механизмов и машин»
Проектирование узла промежуточного вала
Пояснительная записка
к курсовой работе по дисциплине
«Детали машин и основы конструирования»
Задание на курсовой проект ..4
Расчёт рабочего органа машины ..6
1 Расчет диаметра грузового каната .6
2 Определение диаметра и длины барабана .6
3 Определение крутящего момента и частоты вращения барабана ..6
Выбор электродвигателя .6
1 Определение потребляемой мощности для подъема груза 6
2 Определение диапазона частот вращения вала электродвигателя . 7
Определение передаточного числа привода и редуктора 7
Разработка исходных данных для ввода в ЭВМ 7
1 Крутящий момент на выходном валу . . .7
2 Назначение термообработки и допускаемых контактных напряжений 8
3 Назначение относительной ширины колес ..8
4 Номинальная частота вращения электродвигателя . 8
5 Эквивалентное время работы редуктора . . 8
Анализ полученных данных и выбор оптимальной компоновки редуктора ..8
Определение вращающих моментов и частот вращения валов для оптимального варианта .11
1 Определение вращающих моментов 11
2 Определение частот вращения валов . .11
Геометрический расчет зубчатых передач ..12
Проверочный расчет зубчатой передачи тихоходной и быстроходной ступеней .14
1 Выбор материала и термообработки зубчатых передач 14
2 Определение расчетных контактных и изгибных напряжений допускаемых контактных и изгибных напряжений для тихоходной ступени .14
3 Определение расчетных контактных и изгибных напряжений допускаемых контактных и изгибных напряжений для косозубой быстроходной ступени ..18
4 Вывод о работоспособности передачи 21
Разработка эскизного проекта редуктора .22
1 Определение диаметров валов .22
2 Определение расстояний между деталями передач ..25
3 Выбор типа подшипников ..26
4 Конструирование зубчатых колес ..27
Расчет промежуточного вала на усталостную прочность 28
1 Определение усилий действующих на вал .28
2 Расчетная схема для промежуточного вала 30
3 Определение реакций и построение эпюр изгибающих моментов в вертикальной плоскости .31
4 Расчетная схема сил нагружения вала в горизонтальной плоскости определение реакций в опорах 32
5 Определение суммарного изгибающего момента в опасных сечениях 32
6 Определение суммарных реакций в опорах А и D .32
7 Определение фактического запаса усталостной прочности вала в сечении В 33
8 Определение фактического запаса усталостной прочности вала в сечении С 35
Проверка долговечности подшипников качения опор промежуточного вала 35
Подбор и расчет шпоночных соединений 37
Эскизы стандартных изделий .38
Обоснование выбора конструкции крышек подшипников 39
Смазывание зубчатой части .40
Описание сборки узла промежуточного выла 40
Список литературы .. 41
МХС-313-д Фомин С. PEДУKTOP 20
MOM= 1592. SIG1=1100. PSI1= .30 L1=2 CH= 960.
I= 23.94 SIG2=1140. PSI2= .32 L2=1 TE= 2340.
AW B Z1 Z2 U MOD D1 D2 X BETA
KOC 90.0 29.9 22 95 4.32 1.50 33.85 146.15 12.839
ПPЯM 190.0 39.3 15 80 5.33 4.00 60.00 320.00 .000
ПOДШИПHИKИ I ШAPИKOBЫE PAДИAЛЬHЫE I POЛИKOBЫE KOHИЧECKИE I
KAЧEHИЯ I TИП 0000 I TИП 7000 I
BAЛ 1 I C1= 18.18 C2= 12.81 I C1= 15.44 C2= 16.87 I
BAЛ 2 I C1= 19.88 C2= 24.56 I C1= 17.73 C2= 22.15 I
BAЛ 3 I C1= 58.93 C2= 7.11 I C1= 55.63 C2= 30.11 I
KOC 100.0 31.8 16 81 5.06 2.00 32.99 167.01 14.070
ПPЯM 180.0 44.9 20 100 5.00 3.00 60.00 300.00 .000
BAЛ 1 I C1= 18.06 C2= 13.42 I C1= 15.33 C2= 17.31 I
BAЛ 2 I C1= 19.91 C2= 24.74 I C1= 17.82 C2= 22.49 I
BAЛ 3 I C1= 62.95 C2= 7.66 I C1= 59.43 C2= 32.19 I
KOC 110.0 31.3 16 91 5.69 2.00 32.90 187.10 13.412
ПPЯM 170.0 45.5 21 92 4.38 3.00 63.19 276.81 .169
BAЛ 1 I C1= 18.12 C2= 12.91 I C1= 15.39 C2= 16.95 I
BAЛ 2 I C1= 20.24 C2= 25.49 I C1= 18.20 C2= 22.91 I
BAЛ 3 I C1= 68.36 C2= 8.47 I C1= 64.53 C2= 35.01 I
KOC 120.0 30.9 16 101 6.31 2.00 32.82 207.18 12.839
ПPЯM 160.0 46.2 22 84 3.82 3.00 66.42 253.58 .341
BAЛ 1 I C1= 18.36 C2= 12.62 I C1= 15.59 C2= 16.83 I
BAЛ 2 I C1= 20.81 C2= 26.51 I C1= 18.77 C2= 23.92 I
BAЛ 3 I C1= 74.76 C2= 9.43 I C1= 70.57 C2= 38.35 I
KOC 130.0 30.1 13 88 6.77 2.50 33.47 226.53 13.795
ПPЯM 160.0 44.0 24 82 3.42 3.00 72.45 247.55 .341
BAЛ 1 I C1= 18.69 C2= 13.77 I C1= 15.87 C2= 17.82 I
BAЛ 2 I C1= 20.55 C2= 26.10 I C1= 18.62 C2= 23.64 I
BAЛ 3 I C1= 76.57 C2= 9.65 I C1= 72.28 C2= 39.28 I
Чертеж 1 вида.cdw

Чертеж promegutochnogo vala с рамкой.cdw

Чертеж 2 вида.cdw

Готовая пояснительная записка Фомин.doc
Рассчитать и спроектировать узел промежуточного вала двухступенчатого редуктора (схема №20) используемого в приводе лебедки (схема №92).
Быстроходная ступень с косозубым зацеплением тихоходная ступень с прямозубым.
Рисунок 1 – Схема привода
Сила тяги Fк = 112 кH;
Скорость подъема груза V = 34 ммин;
Длительность работы (ресурс) Lh = 13000 ч;
Режим нагружения III.
Серийность производства – мелкосерийное.
Привод грузоподъемной машины сконструирован для передачи крутящего момента на барабан который обеспечивает поднятие груза со скоростью 34 ммин.
Привод (рис. 1) состоит из электродвигателя муфты соединяющей вал электродвигателя и входной вал редуктора редуктора барабана троса. Подъем груза осуществляется тросом наматываемым на барабан. Барабан приводится в движение от электродвигателя через муфту и редуктор. Редуктор осуществляет повышение крутящего момента и снижает частоту вращения до требуемой величины.
Редуктор состоит из быстроходной цилиндрической прямозубой передачи и тихоходной цилиндрической косозубой передачи. Смазка редуктора осуществляется разбрызгиванием масла за счет погружения в него колес.
Расчет рабочего органа машины
1 Расчет диаметра грузового каната
Диаметр грузового каната dк определяется по формуле:
где Fк – усилие в канате H.
По ГОСТ 6636–69 принимаем dк = 106 мм.
2 Определение диаметра и длины барабана
Диаметр грузового барабана лебедки предварительно назначается из условия:
Полученное значение округляется в большую сторону по ряду нормальных линейных размеров.
Принимаем Dб = 270 мм.
3 Определение крутящего момента и частоты вращения барабана
Частота вращения барабана вычисляется по формуле:
где Vк – скорость каната навиваемого на барабан мс.
Крутящий момент барабана вычисляется по формуле:
Выбор электродвигателя
1 Определение потребляемой мощности для подъема груза
Потребляемую мощность определим по формуле
где - КПД привода определяемый по формуле
где -КПД барабана [2 табл.1.1];
-КПД тихоходной ступени [2 табл.1.1];
-КПД муфты [2 табл.1.1].
2 Определение диапазона частот вращения вала электродвигателя
Частота вращения вала электродвигателя определяется по формуле
где -диапазон передаточных чисел цилиндрического редуктора
Подбираем электродвигатель по табл. 24.8 [2]
AИР 132SM6960 ТУ (16-525.564-84) где 960 – номинальная частота вращения двигателя nэ = 960обмин.
Определение передаточного числа привода и редуктора
Передаточное число привода определяется формулой:
Передаточное число редуктора равно передаточному числу привода:
Разработка исходных данных для ввода в ЭВМ
1 Крутящий момент на выходном валу
Крутящий момент на выходном валу определяем по формуле:
2 Назначение термообработки и допускаемых контактных напряжений
Так как выбираем цементацию
3 Назначение относительной ширины колес
Для несимметричного расположения колес относительно опор коэффициенты относительной ширины колес для тихоходной и быстроходной ступеней при твердости ≥350 НВ назначаются из интервала [1 табл.8.4] : yba = 02..025 ybaт = ybaт + 002;
4 Номинальная частота вращения электродвигателя
5 Эквивалентное время работы редуктора
Эквивалентное время работы Lhe назначают с учетом категории режима работы по ГОСТ 21354-87 и находится по формуле:
где Lh – заданный срок службы час;
mh - коэффициент эквивалентности зависящий от режима нагрузки.
В нашем случае режим нагрузки III для которого mh = 018 [1табл.8.9]
Lhe =018 × 13000 = 2340 ч.
Анализ полученных данных и выбор оптимальной компоновки редуктора
Выбор оптимального варианта компоновки редуктора выбирается по двум критериям:
Согласно условию сборки колесо быстроходной передачи должно находиться на расстоянии Δ≥10..15 мм от выходного вала
Диаметры колес быстроходной и тихоходной передач должны быть близки по значению для обеспечения эффективного разбрызгивания смазки; кроме того d2Б d2Т
Для каждого из 5 предложенных вариантов компоновки проверим эти условия. Как видно из рисунка 2 расстояние Δ можно рассчитать по формуле:
где aw2 – межосевое расстояние тихоходной передачи;
d2Б – делительный диаметр быстроходного колеса;
Dвых – диаметр выходного вала который можно приблизительно оценить по формуле
где – 15..30 МПа принимаем =20 МПа.
По стандартному ряду принимаем .
Рисунок 2 – Схема редуктора №20
где - диаметр шестерни быстроходной ступени
- диаметр колеса быстроходной ступени
- диаметр шестерни тихоходной ступени
- диаметр колеса тихоходной ступени
- ширина колеса быстроходной ступени
- ширина колеса тихоходной ступени
- межосевое расстояние.
aw2 = 190 мм; d2Б = 14615 мм;
aw2=180 мм; d2Б=16701 мм;
aw2 = 170 мм; d2Б = 1871 мм;
aw2 = 160 мм; d2Б = 20718 мм;
aw2 = 160 мм; d2Б = 22653 мм;
Из расчетов условию сборки удовлетворяют только четвертый вариант компоновки редуктора. Исходя из условия смазки разбрызгиванием оптимальным вариантом будет вариант № 4.
Определение вращающих моментов и частот вращения валов для оптимального варианта
1 Определение вращающих моментов
Моменты на колесах одной передачи связаны между собой через КПД зубчатого зацепления hзац = 097; моменты на колесах сопряженных передач связаны через КПД пары подшипников hп = 099. Момент на втором колесе тихоходной передачи равен выходному моменту: T2T = Tвых = 1316 Н·м
Т1Т = 16081(382×097) = 4295 Н·м.
Т2Б = 4295099 = 4339 Н·м.
Т1Б = 4339(631×097) = 70166 Н·м
Твх = 70166099=70875 Н·м.
2 Определение частот вращения валов
Частоты вращения валов и зубчатых колес определяются частотой вращения электродвигателя и передаточными числами зубчатых передач. Для быстроходного вала имеем:
nБ = nэ ном = n1Б = 960 мин–1;
Частота вращения промежуточного вала связана с частотой вращения быстроходного вала соотношением
nП = nБUБ = n2Б = n1Т
где UБ – передаточное число быстроходной передачи UБ = 680;
nП = 960631 = 152139 мин–1;
Частота вращения тихоходного вала равна
где UT – передаточное число тихоходной передачи UT = 332;
nТ = 152139382 = 3983 мин–1.
Геометрический расчет зубчатых передач
Необходимо определить диаметры окружностей вершин da1 и da2 диаметры окружностей впадин df1 и df2 коэффициент торцевого перекрытия ea коэффициент осевого перекрытия eb а также суммарный коэффициент перекрытия e для каждой из двух ступеней. Все колеса нарезаются реечным инструментом или долбяком с исходным контуром по ГОСТ 13755-81 с параметрами: угол профиля a = 20° коэффициент головки (ножки) зуба ha*=hf*=1; коэффициент радиального зазора с* = 025.
Диаметры окружностей вершин вычисляют по формуле
da = d + m × (2×ha* + 2×x)
где m – модуль зубьев соответствующей передачи mБ=2 mТ=3;
х – коэффициент смещения исходного контура хБ=0;хТ=0341.
Примем для xT1=0 xT2=0341.
Для быстроходной ступени:
da1Б = d1Б + mБ × (2×ha* + 2×xБ)
da1Б = 3282 + 2 × (2 + 2×0) = 3682 мм
da2Б = d2Б + mБ × (2×ha* + 2×xБ)
da2Б = 20718 + 2 × (2 + 2×0) = 21118 мм.
Для тихоходной ступени:
da1Т = d1Т + mТ × (2×ha* + 2×xТ)
da1Т = 6642+ 3 × (2 + 2×0) = 7242 мм
da2Т = d2Т + mТ × (2×ha* + 2×xТ)
da2Т = 25358 + 3 × (2 + 2×0341) = 261626 мм.
Диаметры окружностей впадин вычисляют по формуле
df = d – m × (2×hf* + 2×c* – 2×x)
df1Б = d1Б – mБ × (2×hf* + 2×c* – 2×xБ)
df1Б = 3282 – 2 × (2×1 + 2×025 – 2×0) = 2782 мм
df2Б = d2Б – mБ × (2×hf* + 2×c* – 2×xБ)
df2Б = 20718 – 2 × (2×1 + 2×025 – 2×0) =20218 мм
df1Т = d1Т – mТ × (2×hf* + 2×c* – 2×xТ)
df1Т = 6642 – 3 × (2×1 + 2×025* – 2×0) = 5892 мм
df2Т = d2Т – mТ × (2×hf* + 2×c* – 2×xТ)
df2Т = 25358 – 3 × (2×1 + 2×025 – 2×0)=248126 мм.
Для тихоходной ступени
Определяем диаметры делительной окружности:
d1 = m× z1 = 3×22 = 66 мм
d2 = m× z2 = 3×84 = 252 мм.
Определяем диаметры начальной окружности:
Для быстроходной ступени
d1 = m× z1 = 2×16 = 32 мм
d2 = m× z2 = 2×101 = 202 мм.
Коэффициент торцевого перекрытия для быстроходной ступени вычисляются по формуле
где z1 – число зубьев шестерни z1Б = 16
z2 – число зубьев колеса z2Б = 101.
Коэффициент осевого перекрытия вычисляются по формуле
где bw – ширина зубчатого венца bwБ = 348 мм.
Суммарные коэффициенты перекрытия вычисляются по формуле
Проверочный расчет зубчатой передачи тихоходной и быстроходной ступеней
1 Выбор материала и термообработки зубчатых передач
Для шестерни и колеса тихоходной ступени выбираем марку 20Х с твердостью 595 HRC и термообработку – цементация.
Для шестерни и колеса быстроходной ступени выбираем марку 20Х с твердостью 574 HRC и термообработку – цементация.
2 Определение расчетных контактных и изгибных напряжений допускаемых контактных и изгибных напряжений для тихоходной ступени
Расчетное контактное напряжение для прямозубых колес определяется по формуле:
Определим окружную скорость колеса
Степень точности изготовления передачи примем равной 7.
Обобщающий параметр ширины шестерни относительно диаметра
Для редуктора с несимметричным расположение колес относительно опор и заданной твердостью bdдолжно быть из диапазона 065..08
[3табл. 8.4] следовательно корректировать ширину шестерни не нужно.
Коэффициент КН определяется по формуле
где - коэффициент концентрации нагрузки примем согласно [3рис.8.15]
- динамический коэффициент примем согласно
Подставляя значения получим
Епр - приведенный модуль упругости для стальных колес
Определим допускаемое контактное напряжение
- коэффициент безопасности для однородной структуры [3табл.8.9]
- коэффициент долговечности шестерни определяется формулой
где - базовое число циклов нагружения согласно
[3табл. 8.7рис. 8.40]
- циклическая долговечность определяется по формуле
где - длительность работы (ресурс) час;
- Коэффициент эквивалентности [3табл.8.10];
Вычислим допускаемые контактные напряжения
Предельное значение находится как меньшее из двух
Сравнивая это значение с расчетным контактным напряжением видно что условие прочности выполняется следовательно тихоходная ступень является работоспособной в заданном режиме нагружения по контактным напряжениям.
Определим расчетное напряжение изгиба по формуле
где - коэффициент расчетной нагрузки по изгибающим напряжениям определяется по формуле
где - коэффициент концентрации нагрузки согласно [3рис.8.15];
- динамический коэффициент согласно [3табл.8.3].
- окружное усилие определяется по формуле
- коэффициент формы зуба шестерни согласно [3рис.8.20]
Определяем допускаемое напряжение изгиба
Предельное напряжение изгиба для стали 20Х равно МПа согласно [3табл.8.9].
- коэффициент безопасности согласно [3табл.8.9].
- коэффициент типа движения при нереверсивной нагрузке.
- коэффициент долговечности
где m = 9 для Н > 350НВ согласно [3табл.8.10];
- базовое число циклов нагружения для стали ;
- эквивалентное число циклов определяется по формуле
где согласно [3табл.8.10].
т. к. коэффициент не удовлетворяет условию примем
Сравнивая эти значения с расчетными видим что условие прочности выполняется. Тихоходная ступень является работоспособной по изгибным напряжениям в заданном режиме нагружения.
3 Определение расчетных контактных и изгибных напряжений допускаемых контактных и изгибных напряжений для косозубой быстроходной ступени
Расчетное контактное напряжение для косозубой передачи определяется по формуле:
Определим окружную скорость шестерни
- коэффициент увеличения нагрузочной способности косозубых передач по сравнению с прямозубыми определяется по формуле
где - коэффициент концентрации напряжений примем ;
где С = 015 если твёрдости поверхностей зубьев шестерни и колеса >350HB .
- коэффициент торцевого перекрытия рассчитывается по формуле
Коэффициент КН определяется по формуле
где - коэффциент концентрации нагрузки примем согласно [3рис.8.15];
- динамический коэффициент согласно [3табл. 8.3].
Епр- приведенный модуль упругости для стальных колес
- коэффициент безопасности для однородной структуры
- коэффициент долговечности шестерни определяется формулой.
где - базовое число циклов нагружения согласно;
- циклическая долговечность определяется по формуле
Сравнивая это значение с расчетным контактным напряжением видно что
условие прочности выполняется следовательно тихоходная ступень является работоспособной в заданном режиме нагружения по контактным напряжениям.
где коэффициент определяется по формуле
где - коэффициент учитывающий распределение нагрузки между зубьями [3табл.8.7].
- коэффициент учитывающий работу зуба как пластины определяется по формуле
- коэффициент расчетной нагрузки по изгибающим напряжениям определяется по формуле
- динамический коэффициент согласно [3табл.8.3];
- коэффициент формы зуба шестерни согласно [3рис.8.20].
- коэффициент безопасности согласно [3табл.8.9];
- коэффициент типа движения при нереверсивной нагрузке;
- коэффициент долговечности определяется по формуле
Сравнивая эти значения с расчетными видим что условие прочности выполняется. Быстроходная ступень является работоспособной по
изгибным напряжениям в заданном режиме нагружения.
4 Вывод о работоспособности передачи
Вывод: Спроектированный редуктор является работоспособным в заданном режиме нагружения по изгибным и контактным напряжениям.
Разработка эскизного проекта редуктора
1 Определение диаметров валов
Диаметры валов назначаются исходя из передаваемого ими момента а также фасок и радиусов скруглений.
-Для быстроходного вала определяются три диаметра – минимальный диаметр вала на входе d который необходимо согласовать с диаметром вала электродвигателя; диаметр цапфы вала для установки подшипника dП и диаметр буртика для упора кольца подшипника dБП.
После согласования этого диаметра с диаметром вала электродвигателя и рядом нормальных линейных размеров (ГОСТ 6636–69) устанавливаем d=32мм.
Рисунок 3 – Эскиз электродвигателя
Рисунок 4 – Эскизы валов
где t – высота заплечника t = 25 мм.
После согласования этого размера с рядом диаметров внутреннего кольца подшипников назначаем dП = 40мм.
где r – координата фаски подшипника r = 2 мм.
После согласования этого диаметра с рядом нормальных линейных размеров назначаем dБП = 48 мм
-Для промежуточного вала необходимо также рассчитать диаметры dП и dБП а также dК – диаметр шейки вала в месте установки зубчатого колеса и dБК – диаметр упорного буртика для зубчатого колеса.
Согласовав этот диаметр с рядом нормальных линейных размеров устанавливаем dК = 53 мм.
где f – размер фаски колеса f = 2мм.
После согласования принимаем dБК = 60 мм.
После согласования этого размера с рядом диаметров внутреннего кольца подшипников назначаем dП = 45мм.
После согласования этого диаметра с рядом нормальных линейных размеров назначаем dБП = 53 мм
-Расчет диаметров тихоходного вала аналогичен расчету диаметров быстроходного вала; для удобства осевого фиксирования зубчатого колеса также для этого вала рассчитаем диаметр упорного буртика для колеса.
Устанавливаем d = 67 мм.
После согласования этого размера с рядом диаметров внутреннего кольца подшипников назначаем dП = 75 мм.
Устанавливаем dБП = 85мм.
Из ряда нормальных линейных размеров выбираем dБК = 95мм.
2 Определение расстояний между деталями передач
Чтобы поверхности вращающихся колес не задевали за внутренние поверхности стенок корпуса между ними оставляют зазор равный
где L – расстояние между внешними поверхностями деталей передач (см. рис. 5)
Принимаем значение зазора равное а = 12 мм
Рисунок 5 – Расстояния между деталями передач
Расстояние b0 между дном корпуса и поверхностью колес принимают:
Расстояние между торцовыми поверхностями колес двухступенчатого редуктора принимают
3 Выбор типа подшипников
Рисунок 6 – Подшипник качения
Расшифруем основные параметры подшипника:
d – внутренний диаметр подшипника;
D – внешний диаметр подшипника;
B – ширина подшипника;
С0 – допустимая статическая радиальная нагрузка;
С – допустимая мгновенная радиальная нагрузка;
Предварительно подшипники выбираются по значению диаметра цапфы вала dп а также по предварительному значению динамической нагрузки приведенному в распечатке программы REDUCE.
Для быстроходного вала выбираем подшипник 208 ГОСТ 8338–75:
внутренний диаметр кольца подшипника d = dП(Б) = 40 мм;
наружный диаметр кольца подшипника D = 80 мм;
ширина кольца подшипника B = 18 мм;
динамическая грузоподъемность: Cr = 256 кН
статическая грузоподъемность: С0r = 181 кН.
Для промежуточного вала выбираем подшипник 309 ГОСТ 8338–75:
внутренний диаметр кольца подшипника d = dП(П) = 45 мм;
наружный диаметр кольца подшипника D = 100 мм;
ширина кольца подшипника B = 25 мм;
динамическая грузоподъемность: Cr = 378 кН ;
статическая грузоподъемность: С0r = 267 кН.
Для тихоходного вала выбираем подшипник 215 ГОСТ 8338–75:
внутренний диаметр кольца подшипника d = dП(Т) = 75 мм;
наружный диаметр кольца подшипника D = 130 мм;
динамическая грузоподъемность: Cr = 519 кН
статическая грузоподъемность: С0r = 419 кН.
4 Конструирование зубчатых колес
Форма цилиндрического зубчатого колеса зависит от серийности производства. В нашем случае производство мелкосерийное. В этом случае для изготовления зубчатого колеса применяют простейшие односторонние штампы. Форма колеса проектируется так как показано на рисунке 7.
Рисунок 7 – Конструкция зубчатого колеса
Для колеса быстроходной ступени эти параметры будут равны:
Согласовав эти значения с рядом нормальных линейных размеров принимаем:
Угол фаски при твердости колеса H > 350HB принимают αф = 15°..20°.
Для колеса тихоходной ступени эти параметры будут равны:
Расчет промежуточного вала на усталостную прочность
1 Определение усилий действующих на вал
Усилие действующее на колесо промежуточного вала
где T2Б – момент на колесе;
dw2 – диаметр начальной окружности;
Ft2 = 24338925361 = 342 кН.
Радиальное усилие на колесе промежуточного вала
где α – угол исходного контура;
– угол наклона линий зуба к оси;
Fr2 = 342tg 20º cos 12839º = 127 кН.
Осевое усилие действующее на колесо промежуточного вала
Fа2 = 342tg 12839º = 0779 кН.
Усилие действующее на шестерню промежуточного вала определим по формуле
где T1Т – вращающий момент на шестерне промежуточного вала Нм
dw1 – диаметр начальной окружности шестерни промежуточного вала мм
Ft1 = 2429556639 = 1294 кН.
Радиальное усилие на шестерне промежуточного вала
Fr1 = 1294tg 20º cos0º = 471 кН.
Осевое усилие действующее на шестерне промежуточного вала
Fа1 = 1294 tg 0º = 0 кН.
Изгибающий момент при перемене осевой силы на ось вала
Тизг= 0779·25361 2= 9878 Нм.
Крутящий момент на промежуточном валу будет равным вращающему моменту на колесе быстроходной ступени
Ткр = Т2Б = 43389 Нм.
2 Расчетная схема для промежуточного вала
Рисунок 8 – Расчетная схема для промежуточного вала
а - расчетная схема вала б - схема нагружения крутящими моментами в –эпюра крутящих моментов г - схема нагружения в вертикальной плоскости д -эпюра изгибающих моментов в вертикальной
плоскости е - схема нагружения в горизонтальной плоскости ж - эпюра изгибающих моментов в горизонтальной плоскости з - суммарная эпюра изгибающих моментов.
Определим расстояния l1 l2 l3:
l1 = 05В + 2+ a + 05 lст = 252 + 12 + 542 = 535
где В – ширина подшипника мм;
а – зазор между корпусом и зубчатыми колесами мм;
bw2б – ширина зубчатого венца колеса быстроходной ступени мм;
где bшест – ширина шестерни мм;
с – расстояние между торцами колес мм;
l3 = 0525 + 2 + 12 + 54 + 8 + 502 + 29+ 0525 = 1802 мм.
3 Определение реакций и построение эпюр изгибающих моментов в вертикальной плоскости
Уравнение равновесия моментов сил действующих на вал в вертикальной плоскости относительно опоры А:
Определяем реакцию в опоре D:
Уравнение равновесия всех сил действующих на вал в вертикальной плоскости:
Определяем реакцию в опоре А:
RАв = -Fr2 + Fr1 - RDв = -127 + 471 – 2044 = 1396 кН;
Значения изгибающих моментов в вертикальной плоскости в сечениях А В С D:
TиС’ = TиС - Tизг = -74686 – 9878 = -173466 кН;
По полученным значениям изгибающих моментов строим эпюру (рис.9д).
4 Расчетная схема сил нагружения вала в горизонтальной плоскости определение реакций в опорах
Уравнение равновесия моментов сил действующих на вал в горизонтальной плоскости относительно опоры А:
Уравнение равновесия в проекции на ось Х для определения реакции в опоре А:
Fх = RАг -Ft2 - Ft1 + RDг = 0;
RАг = Ft2 + Ft1 - RDг = 342 + 1294 –917 = 719 кН;
Изгибающий момент в горизонтальной плоскости в точке B:
Изгибающий момент в горизонтальной плоскости в точке С:
По полученным значениям изгибающих моментов строим эпюру (рис.9ж).
5 Определение суммарного изгибающего момента в опасных сечениях
Существует 2 опасных сечения В и С так как в них изгибающий момент максимален и в них имеется концентраторы напряжений:
Сечение 1: шпоночный паз в колесе быстроходной ступени;
Сечение 2: внутренний диаметр шестерни нарезанной на валу;
Суммарный изгибающий момент в опасном сечении В:
Суммарный изгибающий момент в опасном сечении С:
По полученным значениям изгибающих моментов строим эпюру (рис.9з).
6 Определение суммарных реакций в опорах А и D
Суммарная реакция в опоре А:
Суммарная реакция в опоре D:
Осевое усилие в опоре А:
FaА = Fа2 + Fa1= 0779+ 0 = 0779 кН;
Осевое усилие в опоре D отсутствует так как опора является подвижной.
7 Определение фактического запаса усталостной прочности вала в сечении В
Так как промежуточный вал выполнен в исполнении вал-шестерня то вал будет изготовлен из стали 20Х также как и шестерня поэтому для расчетов примем характеристики материала шестерни.
Фактический запас прочности вычислим по формуле:
где SB - запас сопротивления по деформации изгиба
SB = -1 ((а k kd kf) + т.В)
SB – запас сопротивления по кручению
SB = -1 ((а k kd kf) + т.В).
Расчет выполняется по номинальной нагрузке циклы напряжения принимаем ассиметричными для напряжения изгиба (рис.10) и кручения (рис.11).
Рисунок 10 – Ассиметричный цикл нагружения для изгиба
Рисунок 11 – Ассиметричный цикл нагружения для кручения
т.В - среднее напряжение кручения;
т.В = аВ = 05 = (05 T2Б)(02dк3)
где dк - диаметр промежуточного вала под колесом;
т.В = аВ = (05 4339)(02533) =723 МПа
аВ - амплитуда нормальных напряжений;
аВ = TиB(01dк3) = 422(01533) = 2835 МПа;
-1 - предел выносливости по нормальным напряжениям выбираем согласно [4 c. 620] равным 380 МПа;
k - эффективный коэффициент концентрации напряжения выбираем согласно [4 c. 569] равным 18;
kd - масштабный коэффициент выбираем согласно [4 c. 567] равным 09;
kf – коэффициент качества поверхности принимаем согласно [4 c. 568] равным 1;
– коэффициент чувствительности материала к нормальным напряжениям принимаем согласно [6 С. 571] равным 017;
т – среднее напряжение для симметричного цикла напряжения принимаем согласно [4 c. 560] равным 400;
-1 – предел выносливости по касательным напряжениям МПа выбираем согласно [4 c. 620] равным 190 МПа;
В – предел прочности выбираем согласно [4 c. 620] равным 650 МПа;
k – эффективный коэффициент концентрации напряжения выбираем согласно [4 c. 569] равным 16;
– коэффициент чувствительности материала к касательным напряжениям принимаем согласно [4 c. 571] равным 0075;
SB = 380((283518 091) + 017400) = 305;
SB = 190((723 16 09 1) + 0075 723) =1418
SB = (305 1418) = 3.
Условие по запасу усталостной прочности выполняется то есть SB > [S];
Так как условие выполняется то расчет на жесткость не проводим. В первом опасном сечении В работоспособность обеспечена.
8 Определение фактического запаса усталостной прочности вала в сечении С
где SС - запас сопротивления по деформации изгиба
SС = -1((а k kd kf) + т.С)
SС – запас сопротивления по кручению
где dк = df1 – диаметр впадин шестерни тихоходной ступени;
т.С = аС = 05 = (05 T1Т)(02dк3) = (05 4295)(0258923) = 525 МПа;
аС = TиС(01dк3) = 6257(0158923) = 306 МПа;
SС = 380((283518 091) + 017306) = 614;
SС = 190((52516 09 1) + 0075 525) = 195;
SС = (614 195) = 586.
Условие по запасу усталостной прочности выполняется то есть SС > [S];
Так как запас прочности достаточно большой то расчет на жесткость не проводим. Во втором опасном сечении С работоспособность обеспечена.
Проверка долговечности подшипников качения опор
Исходные данные для расчета:
Подшипник 309 – средняя серия;
Реакция в опоре А равна 732 кН;
Реакция в опоре D равна 939 кН;
Осевое усилие в опоре А равно 0779 кН;
Осевое усилие в опоре D отсутствует так как опора является подвижной;
Режим нагружения III ;
Динамическая грузоподъемность С = 378 кН;
Статическая грузоподъемность С0 = 267 кН;
Условие работоспособности подшипника Ср С
где Ср – расчетное значение грузоподъемности;
С – паспортное значение;
где р – эквивалентная нагрузка действующая на опору А и опору D:
pA=(xAАRA+yAFαA)kБkT
pD = (xDDRD + yDFαD)kБkT
где хA – коэффициент радиальной нагрузки для опоры А определим согласно [3 c. 360] по таблице 16.5 равен 056;
А – коэффициент вращения для подшипника в опоре А равен 1так как вращается внутреннее колесо;
D - коэффициент вращения для подшипника в опоре D равен 1 так как вращается внутренне колесо;
yA – коэффициент осевой нагрузки для опоры А определим согласно [3 c. 360] по таблице 16.5 равен 199;
yD – коэффициент осевой нагрузки для опоры D определим по таблице 16.5 согласно [3 c. 360] равен 0;
kБ – коэффициент безопасности учитываемый характер нагрузки при умеренном режиме работы равен 13;
kT – температурный коэффициент для стали 40ХН принимаем согласно [3 c. 358] равным 1.
pA = (0561732 + 1990779)131 = 734 кН
pD = (11939 + 0)131 = 1221 Н
а1 – коэффициент надежности подшипников [3табл.16.3] равен 1;
а2 – обобщенный коэффициент совместного влияния качества и условий эксплуатации согласно [3 табл.16.3] равен 08;
где Lh – время работы в часах ч.;
n – частота вращения промежуточного вала обмин;
L = (6015213913000018)106 = 214 млн.об.
Опора D является более нагруженной дальнейший расчет ведем по ней.
p – показатель степени определим согласно [3 c. 356] равен 3;
Условие работоспособности подшипника выполняется т.е. Ср С;
Приведенные расчеты показали что при заданном режиме эксплуатации тихоходная ступень обеспечивает необходимую долговечность по прочности зубьев а также обеспечена работоспособность промежуточного вала по усталостной прочности и по грузоподъемности подшипников качения.
Подбор и расчет шпоночных соединений
Для передачи вращающего момента в соединениях зубчатых колес с валами и на концах валов используем призматические шпонки ГОСТ 23360–78. Подбор шпонки заключается в выборе по стандартам ширины шпонки b и высоты h а также в определении рабочей длины lр и длины шпонки lш. Для нашего редуктора необходимо четыре шпонки – по одной на каждом из концов и по одной под каждым из колес зубчатой передачи.
Принимаем [см] = 120 МПа ([см] = 80..150 МПа (для переходных посадок)) определим параметры шпонок:
на конце быстроходного вала (для диаметра 32) устанавливается шпонка сечением 6×6 мм [2 табл. 24.32].
Из сортамента шпонок принимаем мм следовательно на конец быстроходного вала устанавливаем шпонку 6×6×22 ГОСТ 23360–78.
на конце тихоходного вала (для диаметра 67) устанавливается шпонка сечением 20×12 мм [2 табл. 24.32].
Выбираем из сортамента длину шпонки мм.
Из сортамента выбираем шпонку 20×12×90 ГОСТ 23360–78.
- Под быстроходным колесом (для диаметра 53) устанавливается шпонка сечением 16×10 мм [2 табл. 24.29]. Рабочая длина шпонки:
Из сортамента примем шпонку сечением 16×10×45 ГОСТ 23360–78.
- Под тихоходным колесом (для диаметра 85) устанавливается шпонка сечением 25×14 мм [2 табл. 24.29].
Рабочая длина шпонки:
Из сортамента примем две шпонки сечением 25×14×71 ГОСТ 23360–78.
Эскизы стандартных изделий
Подшипник ГОСТ 8338-75
Шпонка ГОСТ 23360-78
Обоснование выбора конструкции крышек подшипников
Размеры крышки определяются прежде всего размером внешнего кольца подшипника. В данном случае используются закладные крышки. Эти крышки не требуют специального крепления к корпусу резьбовыми деталями. Они удерживаются кольцевым выступом для которого в корпусе протачивают канавку. Чтобы обеспечить сопряжение торцов выступа крышки и канавки корпуса по плоскости на наружной цилиндрической поверхности крышки перед торцом выступа делают канавку.
Рисунок 12 – Конструкция крышки подшипника
Толщина стенки крышки подшипника принимается по [2. стр 148]
Толщину стенки крышки корпуса 1 = (09 1) где = 5 мм -
-толщина стенки корпуса. Толщину стенки крышки корпуса принимаем
Принимаем b по [2. стр 139] b= 5 мм
l 25 5= 255 =125 мм.
По стандартному ряду принимаем l=14 мм.
Смазывание зубчатой части
Для уменьшения потерь мощности на трение и снижение интенсивности износа трущихся поверхностей а также для предохранения их от заедания задиров коррозии и лучшего отвода теплоты трущиеся поверхности деталей должны иметь надежную смазку.
Картерную систему смазки применяют при окружной скорости зубчатых колес от 03 до 125 мс. В нашем случае окружные скорости быстроходной и тихоходной ступеней находятся в этих пределах поэтому применение такой системы смазки вполне оправдано.
В двухступенчатой передаче при окружной скорости ≥ 1 мс в масло достаточно погрузить только колесо тихоходной ступени при вращении масло увлекается зубьями разбрызгивается попадает на внутренние стенки корпуса откуда стекает в нижнюю его часть. Внутри корпуса образуется взвесь частиц масла в воздухе которая покрывает поверхность расположенных внутри корпуса деталей.
Описание сборки узла промежуточного выла
На вал-шестерню в паз для шпонки зубчатого колеса устанавливается шпонка 16х10х45 ГОСТ 23360-78. Затем с левой стороны с натягом надевается зубчатое колесо надевается втулка упорная и насаживается подшипник.
Затем с правой стороны надевается маслоотражающее кольцо и насаживается подшипник.
После завершения сборки промежуточного вала его устанавливают в корпус редуктора и закрывают обе стороны промежуточного вала закладными крышками. После чего с помощью регулировочных колец выставляют и регулируют размеры.
Анурьев В.И. Справочник конструктора-машиностроителя: В 3-х т.Т2.–5-е изд. перераб. и доп. – М.: Машиностроение 1980. – 559с.
Дунаев П.Ф. Леликов О.П. Конструирование узлов и деталей машин: Учеб. пособие для машиностроит. спец. вузов.-4-е изд. перераб. и доп. – М.: Высш. шк. 1985.– 416с.
Иванов М.Н. Детали машин: Учеб. для студентов высш. техн. учеб. заведений. – М.: Высш. шк.1991.– 383с.
Писаренко Г.С. Справочник по сопротивлению материалов. – Киев: Наукова думка 1975. – 705 с.
Методические указания к выполнению расчетно-графической работы по дисциплине «Детали машин и основы конструирования» Сост.: С.С. Прокшин Б.А. Беляев А.А. Сидоренко В.А. Федоров С.М. Минигалеев.- Уфа 2006.-58 с.
Спецификация.cdw

Пояснительная записка
Кольцо маслоотражающее
Кольцо регулировочное
Подшипник 309 ГОСТ 8338-75
Шпонка 16х10х45 ГОСТ 23360-78
Рекомендуемые чертежи
- 09.07.2014