Проектирование привода ленточного конвейера




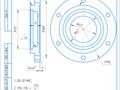
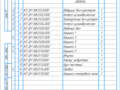
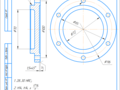
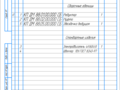
- Добавлен: 24.01.2023
- Размер: 636 KB
- Закачек: 1
Описание
Проектирование привода ленточного конвейера
Состав проекта
![]() |
![]() |
![]() ![]() ![]() |
![]() ![]() ![]() ![]() |
![]() ![]() ![]() |
![]() |
![]() |
![]() ![]() ![]() ![]() |
![]() ![]() ![]() ![]() |
![]() ![]() ![]() ![]() |
![]() ![]() ![]() ![]() |
![]() |
![]() ![]() ![]() ![]() |
![]() ![]() ![]() ![]() |
![]() ![]() ![]() ![]() |
![]() ![]() ![]() ![]() |
![]() |
![]() ![]() ![]() ![]() |
![]() ![]() ![]() ![]() |
![]() ![]() ![]() ![]() |
![]() ![]() ![]() ![]() |
![]() ![]() ![]() ![]() |
![]() ![]() ![]() ![]() |
![]() ![]() ![]() ![]() |
Дополнительная информация
Содержание ДМ.doc
РАСЧЕТ МЕХАНИЧЕСКИХ ПЕРЕДАЧ
РАСЧЕТ ВАЛОВ РЕДУКТОРА
ПОДБОР И РАСЧЕТ ШПОНОК И ПОДШИПНИКОВ
Схемы валов.cdw

ПЗ ДМ.DOC
Объектом исследования является привод ленточного конвейера.
Целью проделанной работы является проектирование привода ленточного конвейера.
В результате проделанной работы было сделано:
Кинематический расчет привода;
Расчет цилиндрических косозубых передач;
Расчет цепной передачи;
Расчет валов редуктора;
ШЕСТЕРНЯ ВАЛ ЗУБЧАТОЕ КОЛЕСО ЦИЛИНДРИЧЕСКАЯ ПЕРЕДАЧА ЦЕПНАЯ ПЕРЕДАЧА ПРИВОД КОНВЕЙЕР ЗАЦЕПЛЕНИЕ ШПОНКА ПОДШИПНИК.
Проект – это комплекс технических документов относящихся к изделию предназначенному для изготовления и модернизации и содержащий чертежи расчеты описание с принципиальными обоснованиями макеты и др. В процессе проектирования инженер решает целый ряд сложных и разнообразных задач. Так например помимо того что он должен разработать машину способную выполнять заданные функции в течение заданного срока службы он должен учесть требования экономики технологии эксплуатации транспортировки техники безопасности и пр.
С развитием науки и техники проблемные вопросы решаются с учетом все возрастающего числа факторов базирующихся на данных различных наук поэтому умение работать на стыках различных научных дисциплин является показателем подготовленности современного специалиста и одним из необходимых условий для продуктивной творческой деятельности.
В этой связи следует отметить особую роль курсового проектирования по деталям машин завершающего цикл общетехнической подготовки студентов и являющегося первой самостоятельной конструкторской работой.
Спроектировать привод ленточного конвейера по приведенной схеме. Выходная мощность РВЫХ = 10 кВт угловая скорость вращения выходного вала ВЫХ = 4 с-1.
Кинематическая схема привода ленточного конвейера
Привод состоит из электродвигателя муфты двухступенчатого редуктора с двумя цилиндрическими косозубыми передачами цепной передачи.
Редуктор состоит из корпуса 3 – х валов 2 – х зубчатых колёс 2 – х шестерен. С каждой последующей ступенью увеличивается крутящий момент понижается частота вращения.
ЭНЕРГЕТИЧЕСКИЙ И КИНЕМАТИЧЕСКИЙ РАСЧЕТ ПРИВОДА
Расчет общего КПД привода:
общ = М ·зп2 × пкn × цп × бар
где hобщ – общий коэффициент полезного действия привода;
зп =0975 – коэффициент полезного действия зубчатой передачи;
пк =0993 – коэффициент полезного действия подшипников качения;
цп =093 – коэффициент полезного действия цепной передачи;
м =0993 – коэффициент полезного действия муфты;
бар =095 – коэффициент полезного действия приводного барабана;
n - количество пар подшипников качения; согласно принятой конструкции стенда n = 4.
Подставляя полученные значения получаем:
= 0993·09752·09934·093·095 = 081;
4. Требуемая мощность приводного электродвигателя:
Рд = PВЫХ 0 = 10 081 = 1235 кВт;
Принимаем электродвигатель асинхронный 3-х фазный короткозамкнутый закрытый обдуваемый с нормальным пусковым моментом типа 4А1604УЗ мощностью Nдв = 15 кВт и частотой вращения n = 1465 обмин ГОСТ 19523 – 81.
Общее передаточное число привода и разбивка по отдельным ступеням передач
Общее передаточное число привода:
где nд – частота вращения вала выбранного двигателя;
nвых – частота вращения выходного вала привода.
nвых = 30· ВЫХ = 30·4 = 120 обмин;
U = 1465 120 = 12208;
где U Ц.П – передаточное число цепной передачи принимаем U Ц.П = 3;
Uр – передаточное число редуктора.
Uр = UU Ц.П = 1223 = 407
Принимаем передаточное число первой ступени U1 = 16 U2 = 25 отсюда:
Uр = 16·25 = 4407 (погрешность – 175%).
Частоты вращения и крутящие моменты на валах
где Uд-j – передаточное отношение с двигателя на j-й вал.
где д-j – КПД элементов привода от вала двигателя до j-го вала.
Tд = P = P·30 (·nд) = 1235·103·30 (·1465) = 805 Н·м.
n1 = nд = 1465 обмин;
n2 = nд Uд-2 = 1465 16 = 915625 обмин;
n3 = nд Uд-3 = 1465 (16·25) = 36625 обмин;
n4 = nд Uд-4 = 1465 12 = 1221 обмин
T1 = Tд·д-1 = 805·099 = 797 Н·м;
T2 = Tд·д-2·Uд-2 = 805·096·16 = 1224 Н·м;
Т3 = Tд·д-3·Uд-3 = 805·099·0962·16·25 = 2938 Н·м;
Т4 = Tд·д-4·Uд-4 = 805·099·0962·088·12 = 7756 Н·м.
Полученные значения занесем в таблицу 1
РАСЧЕТ МЕХАНИЧЕСКИХ ПЕРЕДАЧ
1 Материал и допускаемые напряжения
1.1 Допускаемые контактные напряжения
где Hlimb – предел контактной выносливости поверхностных слоев соответствующий базе испытаний NH0
KHL – коэффициент долговечности;
[SH] – коэффициент безопасности.
Выбираем сталь марки 40Х.
Твердость HRC 45 – 50 термообработка – закалка по поверхности ТВЧ по контуру.
H lim b = 17· HRC+200 = 17·45+200 = 965 (МПа).
Примем [SH] = 12 – т.к применена закалка по поверхности ТВЧ по контуру;
KHL = 1 – т.к приведенное число циклов нагружения больше
Вычисляем допустимые контактные напряжения.
Для зубчатого колеса:
[H2] = H2 lim b·KHL [SH] = 965·1 12 = 80417 МПа.
Расчетные контактные напряжения:
[H] = 045 ([H1] + [H2]) = 045 ( 80417+80417) = 72375 МПа 123 [H2] = 123·80417 = 989 МПа
1.2. Допускаемые изгибающие напряжения:
KFL – коэффициент долговечности. Принимаем KFL= 1 (твердость
[SF] – коэффициент безопасности [SF] = 175.
Вычисляем допускаемые изгибные напряжения
для зубчатого колеса:
Определение геометрических параметров цилиндрической косозубой передачи.
2 Расчет межосевого расстояния
Где: Ка – числовой коэффициент для косозубых передач Ка = 43;
- допускаемое контактное напряжение =72375 МПа;
u - принятое передаточное отношение
Т2 - вращающий момент на валу колеса Н·м;
Кн – коэффициент учитывающий неравномерность распределения нагрузки по длине зуба Кн = 108;
ba = 04 – коэффициент ширины венца по межосевому расстоянию;
Находим межосевое расстояние:
принимаем aw1 = 80 мм по ГОСТ 2185 – 66.
Принимаем aw2 = 100 мм по ГОСТ 2185 – 66.
Тогда ширина шестерни и колеса
b2 = ba· aw1 = 04·80 = 32 мм;
b1 = b2 + 5 = 4 + 5 = 37 мм;
b2 = ba· aw1 = 04·100 = 40 мм;
b1 = b2 + 5 = 4 + 5 = 45 мм;
3. Нормальный модуль зацепления принимаем по формуле:
mn = (001 002) aw1 = 1 2 мм
mn1 = 125 мм по ГОСТ9563 – 60*.
mn2 = 175 мм по ГОСТ9563 – 60*.
Примем предварительный угол наклона зубьев:
=arcsin(1.1·314· 12532) = 775°
=arcsin(1.1·314· 17540) = 869°.
Определим суммарное число зубьев:
Определим количество зубьев шестерни:
Тогда число зубьев колеса:
z2 = zΣ1-z1 = 127-49 = 78
Z4 = zΣ2-z3 = 112-32 = 80
Уточняем значение угла наклона зубьев:
= arccos(zΣ·mn (2· aw))
= arccos(127·125 (2· 80)) = 717°
= arccos(112·175 (2· 100)) = 1148°.
Основные размеры шестерни и колеса:
- диаметры делительных окружностей:
d1 = 2·аW1(U1+1) = 2·80(16+1) = 6154 мм;
d1 =2·аW1·U1(U1+1) = 2·80·1.6(16+1) = 98.46 мм;
d3 = 2·аW2(U2+1) = 2·100(2.5+1) = 57.14 мм;
d4 =2·аW2·U2(U2+1) = 2·100·2.5(2.5+1) = 142.86 мм;
аW1 = (d1+ d2)2 = (6154+9846)2 = 80 мм
аW2 = (d3+ d4)2 = (5714+14286)2 = 100 мм
- диаметры вершин зубьев:
da1 = d1 + 2mn = 6154 + 2·125 = 6404 мм;
da2 = d2 + 2mn = 9846 + 2·125 = 10096 мм;
da3 = d3 + 2mn = 5714 + 2·175 = 6064 мм;
da4 = d4 + 2mn = 14286 + 2·175 = 14636 мм.
- диаметры впадин зубьев:
df1 = d1 – 25mn = 6154 – 25·125 = 58415 мм;
df2 = d2 – 25mn = 9846 – 25·125 = 95335 мм;
df3 = d3 – 25mn =5714 – 25·175 = 52765 мм;
df4 = d4 – 25mn =14286 – 25·175 = 138485 мм.
3.1. Проверочный расчет на усталость по контактным напряжениям
Определяем окружную скорость:
V 1 = ·d1·n1 (60·103) = ·6154·1465 60·103 = 47 мс
V2 = ·d3·n3 (60·103) = ·5714·36625 60·103 = 29 мс
Назначаем 8-ю степень точности передачи.
Контактное напряжение:
КН – коэффициент нагрузки:
где КНα – коэффициент учитывающий распределение нагрузки между зубьями;
КН – коэффициент учитывающий распределение нагрузки по ширине венца;
КНv – коэффициент учитывающий динамическую нагрузку в зацеплении при расчете на контактную прочность поверхности зубьев.
КН = 109·106·10 = 1155;
Прочность по контактным напряжениям обеспечена.
КН = 108·109·10 = 1177
Определим силы действующие в зацеплении.
3.2. Прочностной расчет на усталость при изгибе
где YF – коэффициент учитывающий форму зуба (определяется в зависимости от эквивалентного числа зубьев);
zv1 = z1 cos3 = 49 0.9923 50; YF 1 = 366;
zv2 = z2 cos3 = 78 0.9923 80; YF 2 = 361;
zv3 = z3 cos3 = 32 0.9413 34; YF 3 = 378;
zv4 = z4 cos3 = 80 0.9413 85; YF 4 = 361;
Y – коэффициент учитывающий наклон зуба:
для косозубых Y1 = 1 – 140 = 1 – 717140 = 0948;
Y3 = 1 – 140 = 1 – 1148140 = 0918;
KF – коэффициент нагрузки:
где KF = 112 – коэффициент учитывающий распределение нагрузки по ширине венца при изгибе;
KFv = 13 – коэффициент учитывающий динамическую нагрузку возникающую в зацеплении.
KFα = 092 – коэффициент учитывающий неравномерное распределение нагрузки между зубьями при изгибе;
Расчет следует выполнить для того элемента у которого отношение [F] YF меньше.
[F1] YF1 = 400 366 = 1093 МПа;
[F2] YF2 = 400 361 = 1108 МПа.
[F3] YF3 = 400 378 = 1058 МПа;
Расчет ведется по шестерне.
Напряжение при изгибе:
Условие прочности на изгиб выполнено.
4 Расчет цепной передачи.
- частота вращения n1 = 36625 мин-1;
- передаточное число U = 3;
- работа в одну смену;
- нагрузка спокойная.
Цепь приводная роликовая однорядная передача расположена под углом 45° к горизонту смазка периодическая.
- ведущей звёздочки z1 = 31-2·U = 31-2·3 = 25;
- ведомой звёздочки z2 = z1· U =25·3 = 75.
Коэффициент эксплуатации передачи:
где Кд = 1 – коэффициент характера нагрузки;
Ка = 11 – коэффициент учитывающий влияние межосевого расстояния;
Кн = 1 – коэффициент учитывающий влияние наклона цепи (менее 70°);
Кр = 125 – коэффициент способа регулировки межосевого растояния (неподвижная передача);
Ксм = 14 – коэффициент учитывающий способ смазки (периодическая смазка);
Кп = 10 – коэффициент учитывающий периодичность работы передачи.
КЭ = 1·1·1·125·14·1 = 175.
Для приводных роликовых двухрядных цепей 2ПР по ГОСТ13568-75 коэффициент опорной поверхности шарнира St = 0581.
Выбираем предварительно шаг цепи t = 4445 мм.
Допускаемее давление в шарнирах при n1 = 36625 мин-1:
[P] = 12·(1+001·( z1-17)) = 12·(1+001·(25-17)) = 13 МПа.
Выбираем стандартную цепь ПР-381-1270 по ГОСТ 13568-75 у которой шаг t=381 мм разрушающая нагрузка Qразр = 127 кН опорная поверхность шарнира Sоп = 394 мм2 масса одного погонного метра q = 55 кг.
Окружная скорость цепи:
V = z1n1t (60·103) = 25·36625·381 (60·103) = 58 мс.
Окружное усилие передаваемое цепью:
Ftц = Т1· V = 2938·38354 58 = 19428 Н.
Среднее удельное давление в шарнирах цепи:
P = Ftц· КЭ Sоп = 2938·175 394 = 863 МПа;
что меньше допускаемого давления [P] = 13 МПа принятого для частоты вращения n1 = 36625 мин-1.
Геометрический расчет передачи:
- Длина цепи выраженная в шагах:
Уточняем межосевое расстояние:
Для свободного провисания цепи возможно уменьшение межосевого расстояния на 04% т.е. Δац = 1532·0004 = 6 мм.
Основные размеры звездочек:
- делительные окружности звевздочек:
где d1 – диаметр ролика; d1 = 2223 мм.
Диаметр вершин зубьев ведущей звездочки:
De1 = 381·[ctg (18025) + 07] – 03·2223 = 322 мм;
De2 = 381·[ctg (18075) + 07] – 03·2223 = 929 мм.
- Диаметры впадин зубьев:
r = 05025·d1 + 005 = 05025·2223 + 005 = 1122 мм.
D1 = 304 - 2·1122 = 282 мм;
D2 = 910 - 2·1122 = 888 мм.
где Bвн = 254 – расстояние между пластинами внутреннего звена.
b = 09·254 – 0.15 = 227 мм.
Расчет нагрузок цепной передачи:
- натяжение от провисания ведомой ветви от собственной массы:
где Kf – коэффициент провисания Kf = 15 (для угла 45°);
Ff = 15·55·981·1532 = 124 Н.
- натяжение от центробежных сил при скорости цепи V =58 мс:
FV = q·V2 = 5.5·5.82 = 185 Н.
- нагрузка действующая на валы:
Fв = Ftц+2· Ff = 1943+2·124 = 2191 Н;
- проверка цепи по запасу прочности:
S = Qразр Ftц + FV + Ff = 127000 1943·1+185+124 = 564 > [S] = 11.8.
Условие прочности выполнено.
РАСЧЕТ ВАЛОВ РЕДУКТОРА
Для валов используем сталь 40Х (ГОСТ 4543-80) с термическим улучшением: закалка с высоким отпуском. Данный материал в сочетании с термическим улучшением обеспечивает следующие свойства: В 930 МПа; -1 400 МПа; -1 232 МПа; [к] = 45 МПа.
Предварительный расчет диаметров выходных концов валов осуществляем из расчета на кручение по формулам:
мм по ГОСТ 6636-69 принимаем 30мм;
мм по ГОСТ 6636-69 принимаем 30мм:
мм по ГОСТ 6636-69 принимаем 45мм;
мм по ГОСТ 6636-69 принимаем 55мм.
Диаметры остальных участков валов назначаем исходя из конструктивных соображений при компоновке редуктора.
1 Проверочный расчет валов.
- крутящий момент на валу Т1 = 797Н·м;
- делительный диаметр шестерни d1 = 6154 мм;
-окружная сила: Ft1 = 2590 H.
- радиальная сила: Fr1 = 950 H.
- осевая сила: Fa1 = 326 H.
Строим эпюры изгибающих моментов:
В горизонтальной плоскости:
Определяем опорные реакции.
Силовые реакции опор определяем из условия уравновешенности моментов в горизонтальной и вертикальной плоскости относительно каждой из опор.
- проверяем правильность определенный реакций:
ΣХ = RХА + RХБ –Ft1 = 836 + 1754 – 2590 = 0.
- строим эпюры изгибающих моментов МХ для чего определяем их значение в характерных сечениях вала:
МХ1(8025) = -836·008025 = 67 Н·м;;
МХ2(3825) = -1754·003825 = 67 Н·м;
В вертикальной плоскости:
Проверяем правильность определенных реакций:
Σ Y = RУА + RУБ – Fr1 = 222 + 728 – 950 = 0.
- строим эпюры изгибающих моментов МУ для чего определяем их значение в характерных сечениях вала:
МУ1(8025) = RУА·008025 = 178 Н·м;
МУ2(3825) = RУБ ·003825 = 278 Н·м;
Строим эпюру крутящих моментов:
крутящий момент передаваемый вдоль вала от середины ступицы муфты до середины первой шестерни: Т = 797 Н·м.
Расчетная схема 1-го вала.
Уточненный расчет состоит в определении коэффициентов запаса прочности s для опасных сечений и сравнении их с требуемыми (допускаемыми) значениями.
В соответствии с формой вала и эпюрами М и Т предположительно опасными сечениями вала подлежащими проверке на усталостную прочность являются сечения А-А Б-Б В-В Г-Г в которых имеются концентраторы напряжений и возникают наибольшие моменты.
Определяем запас усталостной прочности в сильно нагруженном сечении А – А в котором концентрация напряжений обусловлена шпоночной канавкой.
Коэффициент запаса прочности по напряжениям кручения определятся по формуле:
где t-1 – предел выносливости при симметричном цикле касательных напряжений;
tv tм – соответственно амплитуда и среднее значение напряжения отнулевого цикла;
k – коэффициент концентрации напряжений кручения принимаем для шпоночного участка вала k = 19;
– масштабные факторы принимаем = 072;
– коэффициент влияния среднего напряжения цикла на усталостную прочность для легированных сталей = 01.
Коэффициент запаса прочности по нормальным напряжениям определяем аналогично:
Расчетный коэффициент запаса прочности для сечение А-А
Такой большой коэффициент запаса прочности объясняется увеличением диаметра вала для соединения его стандартной муфтой с валом электродвигателя.
По той же причине проверять прочность в других сечениях нет необходимости.
- крутящий момент на валу Т1 = 1224 Н·м;
-окружная сила: Ft2 = 2590 H.
- радиальная сила: Fr2 = 950 H.
- осевая сила: Fa2 = 326 H.
- проверяем правильность определенных реакций:
ΣХ = RХА + RХБ –Ft2 – Ft3 = 3602 + 3272 – 2590 - 4284 = 0.
МХ1(36.25) = 3602·0.03625 = 130.6 Н·м;;
МХ2(28.75) = 3272·0.02875 = 94.1 Н·м;
Σ Y = RУА+ RУБ – Fr3+ Fr2 = 528.74 +112.46 – 1591.2 + 950 = 0
МУ1(36.25) = RУА·003625 = 19.2 Н·м;
МУ2(36.25) = RУA ·003625+Fa3·28.75= 44 Н·м;
МУ2(89.75) = RУA ·008975 – Fr3·0.0535 +Fa3·28.75= -12.9 Н·м;
МУ3(2875) = RУБ·002875 = 32 Н·м
крутящий момент передаваемый вдоль вала от середины второй шестерни до середины третьей шестерни: Т = 1224 Н·м.
Расчетная схема 2-го вала.
Определяем запас усталостной прочности в сильно нагруженном сечении Б-Б в котором концентрация напряжений обусловлена шпоночной канавкой и возникают наибольшие моменты.
Суммарный изгибающий момент в сечении Б-Б:
МБ = (МХБ2 + МУБ2)12 = (9412 + 322)12 = 950 Н·м.
- крутящий момент на валу Т1 = 2938 Н·м;
-окружная сила: Ft4 = 42842 H.
- радиальная сила: Fr4 = 1591 H.
- осевая сила: Fa4 = 8701 H.
- нагрузка на вал от цепной передачи: FПХ = FПУ = 1549 Н
ΣХ = RХА - RХБ –Ft4 + FПХ = 3953 – (-1218) – 4284 + 1549 = 0
МХ1(3375) = -3953·0.03375 = -133 Н·м;;
МХ2(68) = -1549·0.068 = -1053 Н·м;
Σ Y = RУА+ RУБ – Fr4- FПУ = 774 +2367 – 1591.2 -1549 = 0
МУ1(3375) = -RУА·003375 = 26 Н·м;
МУ2(3375) = -RУA ·003375+Fa4·7143= 36 Н·м;
МУ3(2875) = FПУ ·0068 = 105 Н·м
крутящий момент передаваемый вдоль вала от середины четвёртой шестерни ведущей звёздочке: Т = 2938 Н·м.
Расчетная схема 3-го вала.
Определяем запас усталостной прочности в сильно нагруженном сечении Г-Г в котором концентрация напряжений обусловлена шпоночной канавкой под зубчатое колесо и возникают наибольшие моменты.
МГ = (МХГ2 + МУГ2)12 = (1332 + 362)12 = 138 Н·м.
k – коэффициент концентрации напряжений кручения принимаем для шпоночного участка вала k = 15;
– масштабные факторы принимаем = 07;
Сечение Л-Л – посадка подшипника с натягом.
- суммарный изгибающий момент в сечении II-II:
МЛ = (МЛХ2 + МЛУ2)12 = (1052 + 1052)12 = 148 Н·м.
Осевой момент сопротивления:
Нормальное напряжение изменяется по симметричному циклу с амплитудой:
mаx = v = MЛ W = 148·104 8942 = 165 МПа.
При отнулевом цикле изменения напряжения кручения:
v = m = Т4 2·W =293.8·103 4·8942 = 8.2 МПа.
v – амплитудное значения напряжения цикла;
m – среднее значение напряжения кручения цикла.
- определяем коэффициент запаса прочности вала в сечении II-II по нормальным и касательным напряжениям:
Расчетный коэффициент запаса прочности вала в сечении II-II.
Усталостная прочность в сечении Л-Л обеспечена.
Сечение К-К шпоночный паз под звёздочку
Изгибающий момент в сечении К-К:
МК =2191·45 = 956 Н·м.
Расчетный коэффициент запаса прочности для сечение К-К
Усталостная прочность в сечении К-К обеспечена.
ПОДБОР И РАСЧЕТ ШПОНОК И ПОДШИПНИКОВ
1. Подбор и расчет шпонок.
Для соединения валов с деталями передающими вращение обычно применяются призматические шпонки из стали имеющей b≥600 МПа например из сталей 45 Ст 6.
Призматические шпонки рассчитываются:
где d – диаметр вала в месте установки шпонки мм;
h – высота шпонки мм;
t1 – глубина паза вала мм;
b – ширина шпонки мм;
[см] ≤ 120 МПа – допускаемое напряжение смятия при стальной ступице и спокойной нагрузке;
Шпонка в месте посадки муфты:
Шпонки стандартизованы и выбираются в зависимости от диаметра вала по ГОСТ 23360 - 78.
Т = 797·103 Н·мм d = 30 мм; b×h = 8х7; t1 = 40
Шпонка 8х7х70 ГОСТ 23360 - 78.
Проверяем шпонку под зубчатое колесо:
Т = 1224·103 Н·мм d = 40 мм; b×h = 12х8; t1 = 50
Шпонка 12х8х32 ГОСТ 23360 - 78.
Проверяем шпонку под звёздочку как более нагруженную что обусловлено небольшим диаметром вала:
Т = 2938·103 Н·мм d = 45 мм; b×h = 14х9; t1 = 55
Шпонка 14х9х60 ГОСТ 23360 - 78.
2 Проверка долговечности подшипников
Подбираем подшипники по более нагруженной опоре для чего определяем суммарные реакции опор:
Предварительно намечаем для установки на валу радиально-упорные роликовые подшипники средней серии 7206 (ГОСТ 333-79) со следующими параметрами: внутренний диаметр d = 30 мм наружный диаметр D = 62 мм толщина Т = 1725 мм С = 315 кН и С0 = 220 кН.
Эквивалентная нагрузка определяется по формуле:
РЭ = (Х·V·РrБ + Y·Ра)·Кб ·КT
где V= 1 (вращается внутреннее кольцо);
Кб = 1 – коэффициент безопасности для приводов ленточных конвейеров;
Отношение – этой величине соответствует е = 030.
Отношение е X = 1 и Y = 0.
РЭ = (1·1·1899 + 0·326)·1 ·1 =1899 Н.
Расчетная долговечность млн.об:
Расчетная долговечность ч:
что больше установленных ГОСТ 16162 – 85.
РЭ = (1·1·3641 + 0)·1 ·1 =3641 Н.
Предварительно намечаем для установки на валу радиально-упорные роликовые подшипники средней серии 7209 (ГОСТ 333-79) со следующими параметрами: внутренний диаметр d = 45 мм наружный диаметр D = 62 мм ширина Т = 2075 мм С = 500 кН и С0 = 330 кН.
Отношение – этой величине соответствует е = 033.
Смазывание зубчатого зацепления производится окунанием зубчатого колеса в масло заливаемое внутрь корпуса до уровня обеспечивающего погружение колеса примерно на 10 мм. Объем масляной ванны V определяем из расчета 025 дм3 масла на 1 кВт передаваемой мощности: V = 025·1235 = 31 дм3.
Устанавливаем вязкость масла. При контактных напряжениях н = 588 МПа и скорости v = 47 мс рекомендуемая вязкость масла должна быть примерно равна 28·10-6 м2с.
Принимаем масло индустриальное И – 30А (по ГОСТ 20799-75*).
Камеры подшипников заполняем пластичным смазочным материалом УТ-1 периодически пополняем его шприцем через пресс-масленки.
Перед сборкой внутреннюю полость корпуса редуктора тщательно очищают и покрывают маслостойкой краской.
Сборку производят в соответствии со сборочным чертежом редуктора начиная с узлов валов:
на ведущий вал насаживают мазеудерживающие кольца и роликоподшипники предварительно нагретые в масле до 80-100°С;
в промежуточный вал закладывают шпонку 12х8х32 и напрессовывают зубчатое колесо до упора в бурт вала; затем надевают распорную втулку мазеудерживающие кольца и устанавливают роликоподшипники предварительно нагретые в масле.
в ведомый вал закладывают шпонку 14х9х60 и напрессовывают зубчатое колесо до упора в бурт вала; затем надевают распорную втулку мазеудерживающие кольца и устанавливают роликоподшипники предварительно нагретые в масле.
Собранные валы укладывают в основание корпуса редуктора и надевают крышку корпуса покрывая предварительно поверхности стыка крышки и корпуса спиртовым лаком. Для центровки устанавливают крышку на корпус с помощью двух конических штифтов; затягивают болты крепящие крышку к корпусу.
После этого на ведомый вал надевают распорное кольцо в подшипниковые камеры закладывают пластичную смазку ставят крышки подшипников с комплектом металлических прокладок для регулировки.
Перед постановкой сквозных крышек в проточки закладывают войлочные уплотнения пропитанные горячим маслом. Проверяют проворачиванием валов отсутствие заклинивания подшипников (валы должны проворачиваться от руки) и закрепляют крышки винтами.
Далее на конец ведомого вала в шпоночную канавку закладывают шпонку устанавливают звездочку и закрепляют ее торцовым креплением; винт торцового крепления стопорят специальной планкой.
Затем ввертывают пробку маслоспускного отверстия с прокладкой и жезловый маслоуказатель.
Заливают в корпус масло и закрывают смотровое отверстие крышкой с прокладкой из технического картона; закрепляют крышку болтами.
Собранный редуктор обкатывают и подвергают испытанию на стенде по программе устанавливаемой техническими условиями.
В результате проделанной работы было проведено:
- Выбор кинематической схемы;
- Выбор электродвигателя привода конвейера;
- Расчет кинематических и силовых параметров привода;
- Расчет цилиндрических передач с косыми зубьями;
- Расчет цепной передачи;
- Расчет валов редуктора;
- Расчет и подбор шпонок;
- Проверка долговечности подшипников;
- Выбор сорта масла.
Курсовое проектирование деталей машин С. А. Чернавский К. Н. Боков И. М. Чернин и др. – М.: Машиностроение 1987. – 416 с.: ил.
Баласанян Р. А. Атлас деталей машин. – Х.: Основа 1996. – 256 с.
Подшипники качения: Справочник – каталог В. Н. Нарышкин. – М.: Машиностроение 1984. – 280 с.
Редукторы. Каталог М.: Изд. НИИМаш 1978. – 247 с.
Звездочка ведущая.cdw

Класс точности по ГОСТ 591-69
Диаметр окружности впадин
Допуск на разницу шагов
Радиальное биение окружности впадин
Торцевое биение зубчатого венца
Ширина внутренней пластины
Расстояние между внутренними пластинами
Сталь 45 ГОСТ 1050-88
Колесо зубчатое1 А3.cdw

Коэффициент смещения
Степень точности СТ СЭВ641-77
Длинна общей нормали
Колебание длины общей нормали
Радиальное биение зубчатого венца
Погрешность профиля зуба
Показателб контакта зуба
Сталь 40Х ГОСТ 4543-71
0 220 НВ. Зубья ТВЧ h 0
Неуказанные граничные отклонения: H14
Радиусы скруглений 0.8 мм max
Вал ведомый.cdw

Термообработка-нормализация 180 200 НВ.
Неуказанные граничные отклонения: H14
Радиусы скруглений 0.8 мм max
Вал-шестерня ведущая.cdw

Коэффициент смещения
Степень точности СТ СЭВ641-77
Длинна общей нормали
Колебание длины общей нормали
Радиальное биение зубчатого венца
Погрешность профиля зуба
Показателб контакта зуба
Сталь 40Х ГОСТ 4543-71
0 220 НВ. Зубья ТВЧ h 0
Неуказанные граничные отклонения: H14
Радиусы скруглений 0.8 мм max
СПЕЦИФ1.cdw

КП ДМ 88.01.00.000 СБ
КП ДМ 88.02.00.000 СБ
КП ДМ 88.05.00.000 СБ
Швеллер 10У ГОСТ 8240-97
Электродвигатель 4А1604У3
СПЕЦИФ2.cdw

Ведущий вал-шестерня
Колесо цилиндрическое
Промежуточный вал-шестерня
Крышка смотрового окна
СПЕЙИФ3.cdw

Подшипник 7209 ГОСТ 333-79
Болт М6 х 35 ГОСТ 7798-70
Шайба 6 ГОСТ 11371-78
Гайка М6 ГОСТ 5915-70
Болт М6 х 16 ГОСТ 7798-70
Шпонка 12х8х32 ГОСТ 23360-78
Шпонка 16х10х40 ГОСТ 23360-78
ЛИСТ№2 Редуктор.cdw

Материал колес - сталь 45
Регулировку осевого зазора в подшипниках производят
с помощью комплекта металлических прокладок
В собранном редукторе проверить боковой зазор в зацеплении
и величину пятна контакта
соответствовать степени точности В-С ГОСТ 1643-72
Тень масла по плоскости разъема и по контуру
крышек не выпускается.
Неровномерный шум чрезмерный нагрев при работе
редуктора не допускаются.
заливаемого в редуктор - 4 л
окраску и консервацию редуктора
производить по заводским техническим требованиям.
Не указанные предельные откланения H14
ТЕХНИЧЕСКИЕ ХАРАКТЕРИСТИКИ
Передаточное число 1-ой ступени u=1.6.
Передаточное число 2-ой ступени и=2.5.
Общее передаточное число редуктора и
Крышка глухаяая2 А4.cdw

Колесо зубчатое2 А3.cdw

Коэффициент смещения
Степень точности СТ СЭВ641-77
Длинна общей нормали
Колебание длины общей нормали
Радиальное биение зубчатого венца
Погрешность профиля зуба
Показателб контакта зуба
Сталь 40Х ГОСТ 4543-71
0 220 НВ. Зубья ТВЧ h 0
Неуказанные граничные отклонения: H14
Радиусы скруглений 0.8 мм max
Пробка.cdw

Вал-шестерня промежуточная.cdw

Коэффициент смещения
Степень точности СТ СЭВ641-77
Длинна общей нормали
Колебание длины общей нормали
Радиальное биение зубчатого венца
Погрешность профиля зуба
Показателб контакта зуба
Сталь 40Х ГОСТ 4543-71
0 220 НВ. Зубья ТВЧ h 0
Неуказанные граничные отклонения: H14
Радиусы скруглений 0.8 мм max
Крышка глухаяая1 А4.cdw

Крышка сквозная1 А4.cdw

Сборка ЛИСТ№1.cdw

Не указанные предельные откланения H14
* Размеры для справок.
ТЕХНИЧЕСКИЕ ХАРАКТЕРИСТИКИ
N=15 кВт; n=1465 мин
Редуктор (косозубые цилиндрические предачи)
Рекомендуемые чертежи
- 26.10.2015
- 17.04.2018
- 20.11.2015
Свободное скачивание на сегодня
- 23.08.2014
- 22.08.2014