Проектирование коробки скоростей горизонтально - консольно фрезерного станка




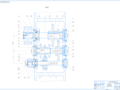
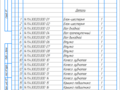
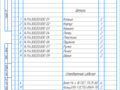
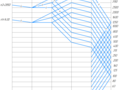
- Добавлен: 25.01.2023
- Размер: 1 MB
- Закачек: 0
Описание
Проектирование коробки скоростей горизонтально - консольно фрезерного станка
Состав проекта
![]() |
![]() |
![]() ![]() ![]() ![]() |
![]() ![]() ![]() ![]() |
![]() ![]() ![]() |
![]() ![]() ![]() ![]() |
![]() ![]() ![]() |
![]() ![]() |
![]() ![]() ![]() ![]() |
![]() ![]() ![]() |
![]() ![]() ![]() ![]() |
Дополнительная информация
Спецификация2.spw

Винт М4 х 18 ГОСТ 17475-80
Кольцо110-1 ОСТ92-8969-78
Штифт 3 х 20 ГОСТ 3129-70
Штифт 3 х 30 ГОСТ 3129-70
Лист 2.cdw

10. ТИТУЛ_ПЗ.doc
ПОЯСНИТЕЛЬНАЯ ЗАПИСКА
к курсовому проекту по металлорежущим станкам
(обозначение документа)
Лист 1.cdw

консервационной смазки и промыть.
Внутренние полости подшипников заполнить консистентной
смазкой ЦИАТИМ-201 ГОСТ 6267-74 на 0
В коробку залить масло ИС-20А ГОСТ20799-75
Обкатать коробку во всех диапозонах скоростей вращения
шпинделя в течении 2-х часов. И
оборотах шпинделя - 30 мин.
Температура корпуса не должна превышать 65
* Размеры для справок.
диаграмм1.frw

диаграмма11-1.frw

Пояснилка.docx
Разработка кинематической схемы станка 6
1 Построение структурной сетки 6
2 Построение диаграммы частот вращения 7
Определение параметров передач 8
1 Определение передаточных отношений 8
2 Определение чисел зубьев и диаметров шкивов 9
Определяем диаметры шкивов ременной передачи 11
Проверочный расчет фактических частот вращения 11
Определение мощности на валах 14
Определение крутящего момента на валах 14
Предварительный расчёт валов 15
Расчет зубчатых колёс 15
1 Расчёт межосевого расстояния 15
Геометрический расчёт зубчатой передачи 17
1 Нахождение делительного диаметра колёс 17
2 Определение ширины венца зубчатых колёс 18
Прочностные расчеты 18
1 Расчёт вала на прочность 18
2 Расчет зубчатых передач на прочность 22
3 Расчетное значение контактного напряжения 23
4 Расчетное напряжение изгиба в зубьях колеса 24
Проверка подшипников на грузоподъемность 25
1 Проверка подшипников на долговечность 26
Расчёт шлицевого соединения 26
Расчёт шпоночного соединения 27
Расчёт ремённой передачи 27
Список использованной литературы 28
При проектировании новых моделей станков необходимо учитывать повышение технологических возможностей металлорежущего инструмента с применением минералокерамики твердых сплавов с износостойким покрытием абразивных инструментов из синтетического алмаза эльбора и др. Решение стоящей перед станкостроением задачи требует развития науки о станках и подготовки высококвалифицированных специалистов в данной области.
Проектирование сложных агрегатов какими являются современные металлорежущие станки производится как правило на основе имеющихся прототипов или аналогичных конструктивных решений. При создании нового станка используются отработанные и всесторонне испытанные конструкции почти всех его основных узлов.
Конструирование станка начинают с подбора необходимы для выполнения проекта чертежей технических испытаний и других архивных материалов.
Одним из основных требований которые предъявляются к современным металлорежущим станкам является точность их работы т.е. стабильность обеспечения станком заданной геометрической формы обработанной детали качества ее поверхности определяющих основные параметры формы.
Проектирование металлорежущего станка начинается с разработки его принципиальной схемы которая должна определить принимаемый метод обработки возможность обработки с одной установки и ее последовательность а также необходимость и возможность применения многоинструментной обработки.
Теория металлорежущих станков – это прежде всего практическая наука направление её развития формируют технические требования к деталям машин которые выдвигает практика с решением задач высокой производительности и экономичности технологических операций. В связи с этим появилось много научных подходов к исследованию процессов обработки металлов конструкторских решений в проектных работах по созданию новых и модификации существующего металлорежущего оборудования направлений развития станкостроения в целом из них основные это прежде всего разработка методов кинематического расчёта станков методов оценки и расчёта точности станков методов исследований в области жёсткости станков и элементов станка методов расчёта механизмов и деталей станков; разработка теории производительности и автоматизации станков исследование и разработка научных основ по динамике станков исследования в области программного в том числе адаптивного управления станками разработки методов расчёта станков на надёжность долговечность и износостойкость.
Тип станка – горизонтально-фрезерный консольный;
Диапазон регулирования Rn = 100;
Размерная характеристика станка: №0 (стол станка 200 х 800 мм);
Обрабатываемый материал: конструкционная сталь твердость НВ160 260;
Характер обработки: черновая;
Компоновка привода: раздельая;
Структура привода: нормальная;
Способ регулирования: ступенчатое;
Электродвигатель: двухскоростной;
Способ переключения скоростей: ручное;
Сборочная единица: шпиндельный узел с переборным устройствром.
Знаменатель ряда значений скоростей главного движения: =125 (принят как рекомендуемое значение для фрезерных станков);
Определение технической характеристики проектируемого станка
1 Анализ технических характеристик станков аналогичных проектируемому
Тип станка: фрезерный;
Основная размерная характеристика: стол 200 × 800 мм ;
Метод определения: статистический.
Таблица 1 – Технические характеристики станков
Основные технические характеристики станка
Изготовитель (поставщик)
Читинский станкостроительный завод
Расчетный наибольший диаметр:
Принимаем dmax = 190 мм.
Расчетный наименьший диаметр:
dmin = ( 01 017) х dma
Принимаем dmin = 30 мм.
Скорость резания при обработке наименьшим диаметром фрезы
Максимальная частота вращения =4478
Проанализировав аналогичные станки принимаем
Минимальная частота вращения :
2 Определение ряда частот вращения:
Определение числа ступеней частот вращения шпинделя:
Принимаем ряд частот вращения шпинделя:
3 Выбор электродвигателя
По ГОСТу 13859-68 выбираем двухскоростной электродвигатель АИС100LB-42 (мощность P = 3 кВт частота вращения n1 = 1430 обмин
Разработка кинематической схемы станка
1 Построение структурной сетки
Структурная формула станка:
Р1=2 Р2=3 Р3=2 Р4=2
Х1=3 Х2=1 Х3=6 Х4=12
2 Построение диаграммы частот вращения
По структурной сетке построим диаграмму частот вращения по которой можно определить фактические частоты вращения и передаточные отношения передач в группах.
Диаграмма частот вращения
Рис.3 Диаграмма частот вращения привода главного движения
Определение параметров передач
1 Определение передаточных отношений
Передаточное отношение ременной передачи:
Передаточное отношение ременной передачи переборного устройства:
Частные передаточные отношения зубчатых передач:
2 Определение чисел зубьев и диаметров шкивов:
Определяем методом наименьшего кратного
Минимальный предел чисел зубьев:
Z=18÷20 (все зубья умножаем на 3)
Z=18÷20 (все зубья умножаем на 20)
Определяем диаметры шкивов ременной передачи
Для принятого в соответствии с ГОСТ 1284.3 – 80 диаметра меньшего шкива (d1 = 50 мм.) клиноремённой передачи ( = 002)
диаметр d2 большего шкива:
Для переборного устройства примем принятого в соответствии с ГОСТ 1284.3 – 80 диаметра меньшего и большего шкивов d12 = 112 мм без учета проскальзывания i=1
Проверочный расчет фактических частот вращения
Фактические частоты вращения шпинделя:
Допустимое значение погрешности:
[n] = 10 ( - 1) = 10 (125 – 1) = 25 %;
Все условия ni [n] выполняются – число зубьев колёс и диаметры шкивов подобраны - верно.
Определение мощности на валах
з.з. = 098 – КПД зубчатого зацепления;
п.к. = 0995 – КПД подшипников качения;
р.п. = 098 – КПД ремённой передачи;
Определяем мощности на валах:
= РЭд ×р.п ×п.к.2 = 3 ×098×0995 2 =291 кВт;
= ×з.з.×п.к.2 = 291 ×099 ×0995 2 = 285 кВт;
= ×з.з.×п.к.2 = 285 ×099 ×0995 2 = 279 кВт;
= Р3 ×р.п ×п.к.2 = 279 ×098×0995 2 =271 кВт;
= ×з.з.×п.к.2 = 271 ×099 ×0995 2 = 266 кВт;
Определение крутящего момента на валах
где np.i – частота вращения i-го вала.
np. для выходного вала от всего диапазона регулирования для сверлильных станков:
Определяем крутящие моменты на валах:
Предварительный расчёт валов
Приближённо определим диаметры валов по условию прочности для среднеуглеродистой стали (в = 5 ÷8 МПа) для напряжения кр = 500÷285 кПа:
Ограничение по жёсткости (для допускаемого угла закручивания [] (44 ÷88) ×10-3 рад (~025 ÷ 05) 0 на 1 мм длины вала):
Так как диапазоны минимально допустимых по условию жёсткости диаметров валов меньше чем по условию прочности принимаем за ориентировочный наименьший допускаемый - диаметр по условию прочности.
Округляем до стандартного значения по ГОСТ 12081 – 72 в сторону увеличения. Имеем: d1 = 25 мм; d2 = 30 мм; d3 = 35 мм.
Расчет зубчатых колёс
1 Расчёт межосевого расстояния
Расчёт производим по следующей формуле:
Ка – вспомогательный коэффициент: для прямозубых передач
u – передаточное число: ;
Т2H - крутящий момент на колесе;
ba bd – коэффициенты учитывающие ширину зуба ba= = 01 т. к. bd = а то bd = ;
КН=12 – коэффициент учитывающий неравномерность
распределения нагрузки по ширине венца;
НР – допускаемое контактное напряжение
H lim – предел контактной выносливости поверхности зубьев
соответствующий эквивалентному числу циклов перемен
H lim b = предел контактной выносливости поверхности зубьев
соответствующий базовому числу циклов перемен напряжений:
КHL – коэффициент долговечности: ориентировочно нагрузку станка принимаю за постоянную а NНЕ > NHO тогда КHL = 1 где NHE и NHO – эквивалентное и базовое число циклов перемен напряжений соответственно.
SH – коэффициент безопасности: SH = 12;
ZR – коэффициент учитывающий шероховатость сопряжённых поверхностей зубьев;
ZV – коэффициент учитывающий окружную скорость;
KL – коэффициент учитывающий влияние смазки;
= 09 по нормам точности зубчатых передач для станка нормальной точности;
Определяем межосевое расстояние:
Округляем до ближайшего большего стандартного значения по ГОСТ 9563-60:
Уточняем межосевое расстояние по формуле:
Геометрический расчёт зубчатой передачи
1 Нахождение делительного диаметра колёс
d1 = m123456×z1 =3 ×30 = 90 мм;
d2 = m123456×z2 =3 ×24 =72 мм;
d3 = m123456 ×z3 = 3 × 27 =81 мм;
d4 = m123456 ×z4 = 3×27 =81 мм;
d5 = m123456 ×z5 = 3 ×24 =72 мм;
d6 = m123456 ×z6 = 3 ×30 =90 мм;
d7 = m123456 ×z7 = 225×56=126 мм;
d8 = m123456×z8 = 225×35=7875 мм;
d9 = m78910×z9 = 225×26=585 мм;
d10 = m78910×z10 =225×65=14625 мм;
2 Определение ширины венца зубчатых колёс
bW = ba × aW = 01 ×
bWI = 01 × aWI-II = 01 × 81=81 мм.; Принимаем bWI =9 мм;
bWII = 01 × aWII-III = 01 ×102375 =102 мм.; Принимаем bWII =11 мм;
1 Расчёт вала на прочность
Определение реакций опор и изгибающих моментов на
наиболее нагруженном валу.
где угол зацепления по ГОСТ 13755-81
Определим нагрузку в опорах.
Вертикальная плоскость.
Горизонтальная плоскость.
Находим изгибающий момент в горизонтальной плоскости.
My(l1)=Ray* l1=2699*58=156*10 3 Н*м
My(x)=Ray*x-Fr8*(x-l1)
My(l1+l2)=Ray*(l1+l2)-Fr8*l2=2699*(58+78)-7099*78=-187*10 3 Н*м
My(х)=Ray*x-Fr8*(x-l1)+Fr9*(х-(l1+l2))
My(l1+l2+l3)=Ray*(l1+l2+l3)-Fr8*(l2+l3)+Fr9*l3=0
Находим изгибающий момент в вертикальной плоскости.
Mx(l1)=Rax*l1=2759*58=16*10 3 Н*м
Mx(x)=Rax*x+Ft8*(x-l1)
Mx(l1+l2)=Rax*(l1+l2)-Ft8*l2=2759*(58+78)-7555*78=-214*10 3 Н*м
Mx(х)=Rаx*x-Ft8*(x-l1)+Ft9*(х-(l1+l2))
Mx(l1+l2+l3)=Rаx*(l1+l2+l3)+Ft8*(l2+l3)-Ft9*l3 =0
Суммарный изгибающий момент
М(l1+l2)==284*103 Н*м
Опасным сечением является место расположения колеса 7
Максимальный изгибающий момент М=284 x103 Нм
Крутящий момент Т=272 Нм
Примем что нормальные напряжения изменяются по симметричному циклу
а касательные напряжения- по пульсирующему циклу
Материал вала - сталь 45(т=500 МПа в=750 МПа -1=330 МПа
а=м=05 х =103 x Т(2 x WK)
а=м =(272 х 103)(2 х52987)=257 МПа
а =(284 х 103)26494=102 МПа
Запас прочности рассчитывается по формуле:
-1D и -1D пределы выносливости вала в рассматриваемом сечении
К и К - эффективные коэффициенты концентрации напряжений
Кd и Кd - коэффициенты влияния абсолютных размеров поперечного сечения
КF и КF - коэффициенты влияния качества поверхности
К - коэффициент влияния поверхностного упрочнения
К =23 К=215 [2таб.10.10]:
Кd = Кd=085 [2 таб.10.7]:
КF =085 КF=09 [2таб.10.8]:
D- коэффициент влияния асимметрии цикла для рассматриваемого сечения вала
- коэффициент чувствительности материала к асимметрии цикла напряжений
Так как [S]=15÷20 то условие прочности выполняется
2 Расчет зубчатых передач на прочность.
Выбор материала зубчатых колес
Материал колёс 40Х HRC 46÷48
термообработка улучшение и закалка ТВЧ
-твердость поверхности 46 .. 48
-твердость сердцевины240 .. 290
-предел текучестит = 720 МПа.
Допускаемые контактное напряжения []H = 835 МПа;
Допускаемые напряжения изгиба определяем по формуле
[]F = []F lim х YN х YR х Y SF .
YN – коэффициент долговечности учитывающий влияние ресурса;
YR – коэффициент долговечности учитывающий влияние шероховатости переходной поверхности между зубьями;
YA - коэффициент долговечности учитывающий влияние двустороннего приложения нагрузки - реверса;
SF – коэффициент запаса прочности.
[]Flim определяем по эмпирической формуле для способа обработки закалка ТВЧ сквозная:
Коэффициент долговечности YN учитывающий влияние ресурса определим по формуле в зависимости от числа циклов нагружения:
при условии 1 YN YNmax
где NFG – число циклов соответствующее перелому кривой усталости.
Для напряжений изгиба:
Т.к. число циклов Nk нагружения больше NFG:по сравнению другими колесами:
Nk = 95 х 107 > 4 х 106
YR – коэффициент долговечности учитывающий влияние шероховатости переходной поверхности между зубьями принимаем для зубошлифования:
YA - коэффициент долговечности учитывающий влияние двустороннего приложения нагрузки – реверса для закаленных сталей и реверсирующей нагрузки:
Минимальное значение коэффициент запаса прочности SF:
Определим допускаемые напряжения изгиба для шестерни и колеса:
Расчет будем вести для той зубчатой пары ступени которая обеспечивает наибольшее передаточное отношение
Число зубьев шестерни:
Число зубьев колеса:
Максимальное передаточное число:
u1 = z2 z1 = 56 35 = 16.
3 Расчетное значение контактного напряжения:
гдеZ = 9600 МПа12 для прямозубых колес;
KH - коэффициент нагрузки в расчетах на контактную прочность.
Определим KH по формуле:
гдеKHv – коэффициент учитывающий внутреннюю динамику нагружения связанную прежде всего с ошибками шагов зацепления и погрешностями профилей зубьев шестерни и колеса;
КH - коэффициент учитывающий неравномерность распределения нагрузки по длине контактных линий обусловливаемую погрешностями изготовления (погрешностями направления зуба) и упругими деформациями валов подшипников;
КH - коэффициент учитывающий приработку зубьев.
KHv – принимаем в зависимости от степени точности передачи по нормам плавности окружной скорости и твердости рабочих поверхностей.
Коэффициент КH определяем по формуле:
КH = 1 + (КH0 – 1) х КHw
где КHw – коэффициент учитывающий приработку зубьев его значения находят в зависимости от окружной скорости для зубчатого колеса с меньшей твердостью по табл.:
КH = 1 + (КH0 – 1) х КHw = 1 + (111 – 1) х 09 = 11.
Коэффициент КH определяем по формуле :
Начальное значение коэффициента KH0 распределения нагрузки между зубьями в связи с погрешностями изготовления определяем в зависимости от степени точности по нормам плавности для прямозубых передач 7 степени точности:
КH0 = 1 + 006 х (nст – 5) при 1 КH0 125.
Вычислим значение коэффициентов:
КH0 = 1 + 006 х (nст – 5) = 1 + 006 х (7 – 5) = 112.
КH = 1 + (КH0 – 1) х КHw = 1 + (112 – 1) х 09 = 111.
KH=KHv х KH х KH=109 х 11 х 111=133.
Определим расчетное контактное напряжение:
Отклонение расчетного контактного напряжения от допускаемого:
H = ([]H - H) []H х100%= (835 –653) 835х 100%= 17 %.
Расчетное контактное напряжение меньше допускаемого на 17% 20 % следовательно параметры передачи оставляем без изменения.
4 Расчетное напряжение изгиба в зубьях колеса:
гдеKF – коэффициент нагрузки при расчете по напряжениям изгиба;
YFS6 – коэффициент учитывающий форму зуба и концентрацию напряжений для колеса ;
Y – коэффициент учитывающий наклон зуба в косозубой передаче;
Y – коэффициент учитывающий перекрытие зубьев.
Определим KF по формуле :
гдеKFv – коэффициент учитывающий внутреннюю динамику нагружения связанную прежде всего с ошибками шагов зацепления шестерни и колеса;
KF — коэффициент учитывающий влияние погрешностей изготовления шестерни и колеса на распределение нагрузки между зубьями.
Значения KFv принимают в зависимости от степени точности по нормам плавности окружной скорости и твердости рабочих поверхностей:
Значения KF определяют так же как при расчетах на контактную прочность:
KF = 018 + 082 x KH0
KF = 018 + 082 x 112 = 11
KF = KFv x KF x KF = 109 x 109 * 112 = 133.
Значение коэффициента YFS2 определяем для z=56
Для прямозубой передачи :
Расчетное напряжение изгиба для зубьев колеса:
Напряжения изгиба меньше чем допускаемые – следовательно параметры передачи оставляем без изменений.
Проверка подшипников на грузоподъемность
Проведем расчет для второго вала.
Наиболее нагруженной опорой является опора В.
Выбираем подшипник №205-шарикоподшипник радиальный однорядный.
Требуемый ресурс Lh=10000ч
Эквивалентная нагрузка:
P=(X х V х Fr+Y х Fa) х K х K
Р=(1х1х14066)х13х1= 18278 Н
Эквивалентная долговечность:
Lhe=Lh х Khe=10000 х 0125=1250часов
Требуемый ресурс на расчетном режиме:
Lе=60 х 10-6 х n х Lhe=60 х 106 х 200 х 1250=15 млн.об.
Расчетная динамическая грузоподъемность:
Подшипник пригоден так как расчетная динамическая грузоподъемность меньше требуемой.
1 Проверка подшипников на долговечность
Lh>Lhe 1612>1250 час
Расчёт шличевого соединения
Проверим шлицевoе соединение. Шлицевое соединение считается на прочность по следующей формуле:
Допускаемое напряжение смятия =35 МПа
Так как то шлицевые соединения на промежуточном валу удовлетворяют условию прочности.
Расчёт шпоночного соединения
Для 35: b =10 мм. h = 8 мм. lр = 70 мм.
- условие выполняется
Расчёт ремённой передачи
Исходные денные: d2 = 559 мм.
Клиновая ременная передача:
При частоте вращения малого шкива d1 = 50 мм 2850 обмин и передаваемой мощности 3 кВт используется ремень с сечением В.
При частоте вращения малого шкива d1 = 50 мм 2850 обмин и передаваемой мощности 3 кВт при передаточном отношении i=112 мощность передаваемая одним ремнем Рp1 = 16 кВт
Число ремней необходимое для передачи мощности 3 кВт:
Список использованной литературы
Анурьев В.И. Справочник конструктора-машиностроителя. В 3-х т. Т. 2 - М.: Машиностроение 1978. - 559 с.
П.Ф.Дунаев О.П.Леликов «Конструирование узлов и деталей машин» - М.: Высшая школа 1985 - с.416.
Проников А.С. Расчет и конструирование металлорежущих станков Изд. 2-е. Высшая школа 1968 стр. 43
Методические указания к лабораторным работам по курсам:
«Оборудование машиностроительного производства» «Промышленное оборудование» «Металлорежущие станки и промышленные роботы» Уфимск. гос. авиац. техн. ун-т; Сост. Акмаев О.К. Уфа 1999.
Спецификация1.spw

Винт М4 х 14 ГОСТ 11644-75
Винт М5 х 16 ГОСТ 17475-80
Винт М3 х 8 ГОСТ 11644-75
Кольцо130-3 ОСТ92-8969-78
Кольцо120-3 ОСТ92-8969-78
Кольцо130-1 ОСТ92-8969-78
Мaнжета 1-30 х 50-1 2 ГОСТ 8752-79
Мaнжета 1-20 х 34-1 2 ГОСТ 8752-79
Подшипник 206 ГОСТ 8338-75
Подшипник 205 ГОСТ 8338-75
Подшипник 104 ГОСТ 8338-75
Шайба 7019-0630 ГОСТ 14734-69
Шайба 7019-0624 ГОСТ 14734-69
Шайба 3Н ГОСТ 6402-70
Шпонка 10 х 8 х 36 ГОСТ 23360-78
Шпонка 10 х 8 х 70 ГОСТ 23360-78
Шпонка 6 х 6 х 20 ГОСТ 23360-78
Шпонка 5 х 5 х 20 ГОСТ 23360-78