Проектирование АТП на 250 автомобилей МАЗ-534019




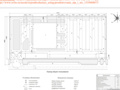
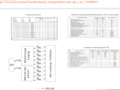
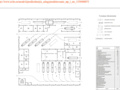

- Добавлен: 25.01.2023
- Размер: 2 MB
- Закачек: 0
Описание
Состав проекта
![]() |
![]() |
![]() ![]() ![]() ![]() |
![]() ![]() ![]() ![]() |
![]() ![]() ![]() ![]() |
![]() ![]() ![]() ![]() |
![]() ![]() ![]() ![]() |
![]() ![]() ![]() ![]() |
![]() ![]() ![]() |
Дополнительная информация
генплан.dwg

Условные обозначения
- гидравлический подъемник
- направление движения автомобилей
Слесарно-механический участок
Склад прочих материалов
Склад промежуточного хранения
Сварочно-кузовной участок
Электро-аккумуляторный участок
Участок ремонта топливной аппаратуры
Шиномонтажный участок
Склад смазочных материалов
Склад лакокрасочных изделий
Генеральный план АТП
Контрольно-технический пункт
Административный корпус
- направление движения
Территория проходной АТП
Стоянка для личного автотранспорта
Общая площадь участка - 31573 м Площадь застройки - 12114 м Площадь озеления - 7420 м Плотности застройки - 38
% Коэффициент озеленения - 0
Коэффициент использования территории - 0
Проезд общего пользования
АТП на 250 атомобилей МАЗ-534019 для
перевозки продовольственных грузов
Выполнение дипломных проектов по проектированию АТП
эксплуатационная часть.dwg

Показатели производственной программы АТП по эксплуатации
Схема грузопотоков перевозок
стоимость основных фондов АТП
и показатели производственной
программы АТП по эксплуатации
Стоимость основных фондов АТП
АТП на 250 атомобилей МАЗ-534019 для
перевозки продовольственных грузов
Выполнение дипломных проектов по проектированию АТП
экономическая часть.dwg

График безубыточности
Формирование и распределение прибыли в АТП
Технико-экономические показатели АТП График безубыточности Формирование и распределение прибыли в АТП
АТП на 250 атомобилей МАЗ-534019 для
перевозки продовольственных грузов
Выполнение дипломных проектов по проектированию АТП
технология ремонта.dwg

Измеренные параметры
Предельно допустимые параметры
Наименование средств контроля
Код средств контроля
Профессия исполнителя
Износ отверстия под наружное кольцо наружного подшипника
Нутромер НИ 50-100 ГОСТ 868-72
уста- новить ремонт- ные втулки с пос- ледующей рас- точкой
Карта дефектации корпуса водяного насоса
Износ отверстия под наружное кольцо внутреннего подшипника
Износ резьбового отверстия под шпильку крепления патрубка
Непроходной калибр ГОСТ 2015-69
Ремонт корпуса водяного насоса автомобиля "МАЗ-534019
ус- тановить на клей резьбовую втулку
Черновое растачивание
Чистовое растачивание
Технологический эскиз к операции 005 "Растачивание подшипниковых диаметров
Координатно-расточной станок 2431СФ10
Технологический эскиз к операции 010 "Рассверливание отверстия и нарезание резьбы
Вертикально - сверлильный станок 2А 135
Клей Д-9 ОСТ4 ГО.029.204
Технологический эскиз к операции 015 "Впрессовка втулок и установка на клей резьбовой втулки
Установка втулок по ø145
ø116 и 2-х по ø24 мм
Технологический эскиз к операции 020 "Растачивание ремонтных втулок
АТП на 250 атомобилей МАЗ-534019 для
перевозки продовольственных грузов
Выполнение дипломных проектов по проектированию АТП
агрегатный участок.dwg

- розетка штепсельная трехфазная
- потребитель электроэнергии
- розетка штепсельная однофазная
- подвод холодной воды
Стенд для разборки и сборки КПП i-4
Установка для расточки тормозных барабанов и обточки тормозных колодок i0
Пpecc гидравлический Стеллаж для деталей Ванна для мойки деталей Сушильная установка Заточный станок Стенд для разборки
сборки и регулировки сцеплений Верстак слесарный Ларь для обтирочных материалов Ларь для отходов Ящик с песком Стенд для разборки
сборки и регулировки рулевых механизмов Стенд для разборки и сборки редуктора заднего моста Стенд для ремонта двигателя Шкаф для приборов и инструмента Стенд для срезания накладок с тормозных колодок Стенд для приработки и испытания двигателя Стенд для приработки и испытания КПП Контрольное приспособление Кран-балка Огнетушитель
Слесарно-механический участок
Сварочно-жестяницкий участок
Кузнечно-кузовной участок
- подвод горячей воды
- подвод сжатого воздуха
Стенд для разборки и сборки КПП
Ванна для мойки деталей
Ларь для обтирочных материалов
сборки и регулировки
Стенд для разборки и сборки редуктора
Стенд для ремонта двигателя
Шкаф для приборов и инструмента
Стенд для приработки и испытания
Стенд для приработки и испытания КПП
- подвод холодной воды с отводом в канализацию
- подвод горячей воды с отводом в канализацию
Условные обозначения:
Сварочно-медницкий участок
АТП на 250 атомобилей МАЗ-534019 для
перевозки продовольственных грузов
Выполнение дипломных проектов по проектированию АТП
производственный корпус.dwg

Условные обозначения
- направление движения автомобилей
Зона ЕО Зона ТО Участок диагностики Зона ТР Сварочно-жестяницкий участок Малярный участок Агрегатный участок Слесарно-механический участок Электротехнический участок Аккумуляторный участок Участок ремонта топливной аппаратуры Шиноремонтный участок Кузнечно-кузовной участок Участок ОГМ
Склад смазочных материалов Склад резины Склад запчастей Склад металлов Склад лакокрасочных изделий Склад прочих материалов Склад агрегатов Склад промежуточного хранения
Насосная мойки Санузел Вентиляционная Тепловой пункт Компрессорная Трансформаторная Комната мастеров Комната ОТК Электрощитовая
- канавный подъёмник
АТП на 250 атомобилей МАЗ-534019 для
перевозки продовольственных грузов
Выполнение дипломных проектов по проектированию АТП
записка.doc
МИНИСТЕРСТВО ОБРАЗОВАНИЯ И НАУКИ РОССИЙСКОЙ ФЕДЕРАЦИИ
МОСКОВСКИЙ ПОЛИТЕХНИЧЕСКИЙ УНИВЕРСИТЕТ (МОСКОВСКИЙ ПОЛИТЕХ)
Кафедра «Наземные транспортные средства»
«ДОПУСКАЕТСЯ К ЗАЩИТЕ»
Пояснительная записка
К ВЫПУСКНОЙ КВАЛИФИКАЦИОННОЙ РАБОТЕ:
«Проектирование АТП - 250 автомобилей МАЗ-534019 для
продовольственных перевозок»
Руководитель работы консультант по технологической части
(ученая степень должность)
Консультант по эксплуатационной части
Консультант по конструкторской части
Консультант по технологии ремонта
Консультант по части безопасности и экологичности проектных решений
Консультант по организационно-экономической части
на выпускную квалификационную работу
Орехову Николаю Павловичу
(Фамилия имя отчество)
«Проектирование АТП – 250 автомобилей МАЗ-534019 для
Консультант по части безопасности и экологичности проектных решений
По эксплуатационной части
Разработать схему и таблицу грузопотоков разработать маршруты перевозок произвести расчет показателей работы подвижного состава на маршрутах и в целом по АТП.
По технологической части
Выполнить технологический расчет АТП произвести обоснование планировочных решений и описать организацию и технологию работ на агрегатном участке.
По конструкторской части
Выбрать гидравлический съёмник для съёма подшипников втулок ступиц при ремонте узлов автомобилей на агрегатном участке методом априоронго ранжирования.
По технологии ремонта
Выполнить дефектацию корпуса водяного насоса для автомобиля МАЗ-534019 выявить дефекты и разработать технологию ремонта корпуса.
По части безопасности и экологичности проектных решений
Провести анализ потенциальной опасности АТП для персонала и окружающей среды характеристику производства производственной среды производственного здания на примере агрегатного участка выполнить расчет искусственного освещения агрегатного участка.
По организационно-экономической части
Разработать организационную структуру управления предприятием рассчитать стоимость основных фондов и рассчитать себестоимость перевозок и рентабильность АТП.
(Фамилия инициалы) (подпись студента)
Эксплуатационная часть
1. Назначение АТП и условия эксплуатации
2. Исходные данные для расчета
4. Схема грузопотоков и таблица грузопотоков
5. Выбор модели подвижного состава
5.1 Технические характеристики МАЗ-534019
6. Расчет маршрутов перевозок
6.1. Расчет маршрута № 1
7. Технология перевозок
8. Организация перевозок грузов
9. Показатели производственной программы АТП по эксплуатации
Технологическая часть
1. Технологический расчет
1.1. Исходные данные для проектирования
1.2. Расчет программ технического обслуживания и ремонта
1.3. Распределение объемов работ ТО и ТР по видам работ
1.4. Корректирование трудоемкости ТО и ТР с учетом выделения диагностических работ
1.5. Расчет объемов работ по самообслуживанию
1.6. Обоснование режима работы и принимаемых форм организации производства
1.7. Расчет численности ремонтно-обслуживающего персонала
1.8. Формирование производственной структуры технической службы АТП
1.9. Расчет линий и постов в производственных зонах и отделениях
1.10. Подбор технологического оборудования и оснастки для производственных зон и отделений
1.11. Расчет площадей производственных зон и отделений
1.12. Расчет хранимых запасов и площадей складских помещений
2. Обоснование планировочных решений
2.1. Обоснование планировочного решения производственного корпуса
2.2. Разработка генерального плана АТП
3. Организация и технология работы агрегатного участка
3.1. Назначение отделения
3.3. Организация и управление технологическим процессом
3.4. Обоснование планировочного решения агрегатного участка
Конструкторская часть
1. Выбор основного технологического оборудования для агрегатного участка
2. Выбор конкретной модели методом априорного ранжирования
3. Проверка согласованности и не случайности мнений экспертов
4. Ранжирование факторов по значимости
5. Проверка согласованности и не случайности мнений экспертов
6. Выбор конкретной модели съёмника
7. Техническая характеристика и принцип работы выбранной модели стойки-подъёмника
1. Описание и принцип работы ремонтируемой детали и её узла
2. Обоснование необходимости разработки технологического процесса восстановления детали
3. Выбор рационального способа восстановления детали
4. Разработка технологического процесса восстановления корпуса
Маршрутная карта ремонта корпуса водяного насоса автомобиля МАЗ-534019
Ведомость оборудования
Безопасность и экологичность проектных решений
1 Выбор объекта анализа
2 Анализ потенциальной опасности АТП для персонала и окружающей среды
3 Анализ производственных воздействий АТП на окружающую среду
4 Анализ возможности возникновения чрезвычайных ситуаций на АТП
5 Характеристика производственной среды производственного здания
6 Мероприятия и средства по защите окружающей среды от воздействия АТП
6.1 Очистка ливневых и производственных вод
6.2 Очистка воздуха выбрасываемого в атмосферу из системы вентиляции АТП
7 Расчетная часть по охране окружающей среды
7.1 Расчет нефтеловушки
8. Расчетная часть безопасности труда
8.1. Расчет искусственного освещения агрегатного участка
9. Мероприятия и средства по обеспечению безопасности в чрезвычайных ситуациях
Организационно-экономическая часть
1. Организационный раздел
1.1. Организационно-правовая форма собственности предприятия
1.2. Организационная структура предприятия
2. Экономический раздел
2.1. Расчет стоимости основных производственных фондов
2.2. Расчёт потребности АТП в материальных затратах
2.3. Расчет численности и фонда оплаты труда по категориям работающих
2.4. Затраты на амортизацию подвижного состава
2.5. Прочие затраты
2.6. Смета эксплуатационных затрат
2.7. Калькуляция себестоимости перевозок
2.8. Расчёт потребности нормируемых оборотных средств
2.9. Расчёт финансовых показателей
2.10. Расчёт показателей использования производственных фондов
2.11. Оценка экономической эффективности инвестиций
2.12. Расчёт точки безубыточности
Список используемой литературы
В задании на дипломный проект поставлена задача выполнить проектирование грузового автотранспортного предприятия на 250 автомобилей “МАЗ-534019” для пригородных перевозок между населёнными пунктами в умеренных климатических условиях. Обоснованием для проектирования является постоянно растущий объем перевозок продовольственных грузов в крупных пригородах в связи с расширением производств данных товаров.
Исходя из этого в дипломном проекте ставятся следующие задачи: провести расчёт необходимых производственных площадей количества производственных рабочих занятых выполнением работ по поддержанию автомобилей в исправном состоянии. Рассчитать необходимое количество постов зон и участков. Определить необходимое производственное оборудование и разработать технологический процесс ремонта одного из узлов автомобиля “МАЗ-534019” и выполнить его планировочное решение.
На основании выполненных расчетов провести технико-экономическое обоснование проектирования АТП и определить экономическую эффективность инвестиций в проектируемое предприятие.
Разработать мероприятия по обеспечению условий безопасного труда в производственном корпусе и экономическую безопасность АТП для окружающей среды.
При разработке дипломного проекта необходимо использовать последние достижения науки и техники в области эксплуатации автомобильного транспорта ремонта и технического обслуживания защиты окружающей среды от вредного воздействия транспортных средств.
Эксплуатационная часть
1 Назначение АТП и условия эксплуатации
Проектируемое АТП предназначено для обеспечения продовольственными грузами (молоко творог сметана и мясные полуфабрикаты: котлеты пельмени и т.д.) предприятий среднего бизнеса а так же для выполнения работ по ТО и ТР хранению и материально-техническому обеспечению подвижного состава.
Номенклатура продовольственных грузов разнообразна поэтому для их перевозок используют различные типы подвижных составов.
Продовольственные грузы перевозят от мест складирования или производства до мест продажи по различным схемам перевозок.
АТП расположено в зоне умеренного климата.
Перевозки осуществляются по автомобильным дорогам первой категории с асфальтобетонным покрытием.
Рельеф местности равнинный и слабохолмистый. Перевозка грузов осуществляется на постоянной основе в течение всего года.
2 Исходные данные для расчета
Согласно заданию годовой объем перевозок по всему АТП определяется возможным объемом перевозок осуществляемыми автомобилями МАЗ-534019 в количестве 250 единиц.
Средняя величина партии перевозимого груза за одну ездку определяется грузоподъемностью принимаемой марки автомобиля.
Режим работы выбираю следующий: 305 дней в году в 1 смену.
Перевозка осуществляется на моделях МАЗ-534019 с изотермическими фургонами это необходимо так как данные грузы являются продовольственными нуждаются в определенном температурном режиме перевозки и последующей санитарной обработке кузова.
В этом случае среднее время нахождения в наряде автомобилей АТП составляет величину:
Тн = nсм · (tсм-tпз) = 1 · (8-03) = 77 ч. где
Nсм=1 - сменность работы автомобилей;
Tсм=8 ч. - продолжительность одной смены;
Tпз=18 мин =03 ч. - подготовительно-заключительное время за одну смену.
4 Схема грузопотоков и таблица грузопотоков
Учитывая характеристику перевозимых грузов составляем схему грузопотоков а затем таблицу грузопотоков. Потребителями продовольственных грузов в основном являются магазины района а грузоотправителями заводы изготовления данных грузов.
Принимая во внимание большое количество магазинов реализующих товары маршруты разбиты на усредненные имеющие длину ездки с грузом от соответствующего производственного предприятия до каждого из магазинов. Кроме того среднесуточный пробег отдельного автомобиля по АТП колеблется в зависимости от того на которые маршруты он попадает. Автомобили на маршрутах взаимозаменяемые в целях предотвращения срыва поставок по организационно-техническим причинам.
Распределение коэффициента γ от перевозимого груза
Молочные продукты (молоко масло творог сметана)
Мясные полуфабрикаты (пельмени котлеты фарши)
Рис. 1.1 Схема грузопотоков
Распределение общего объема перевозок по маршрутам
Объект-грузоотправитель
Объект-грузополучатель
Количество автомобилей на маршруте
Объем перевозок тонн
Мясные полуфабрикаты
Определяем среднее расстояние перевозки груза.
Среднее расстояние перевозки грузов (lпг) определяется делением суммарного грузооборота (Робщ) на общий объем перевозок (Qобщ):
lг = Робщ Qобщ = 290869581183224 = 246 км.
5 Выбор модели подвижного состава
Согласно номенклатуре перевозимых грузов в качестве подвижного состава берется шасси автомобиля МАЗ-534019. Он предназначен для перевозки продовольственных грузов требующих соблюдения определенных температурных условий поэтому данная модель состоит из холодильной установки и герметичного теплоизолирующего фургона
Стенки фургона изготавливают из панелей толщиной до 8 сантиметров. Между собой панели соединяются герметичными стыками во избежание появления тепловых мостиков. На двери холодильного отделения фургона устанавливают эластичный уплотнительный контур из износостойкой резины.
Для обшивки фургона изнутри и снаружи используются оцинкованная сталь с полимерным защитным покрытием утеплитель из пенополиуретан (ППУ). Низкий коэффициент теплоизоляции позволяет минимизировать толщину теплоизолирующего слоя. Другие достоинства материала – водостойкость малый вес неподверженность коррозии гниению биологическим факторам.
Автомобиль данной марки имеет кабину повышенной комфортабельности с улучшенным экстерьером и интерьером.
Конструкция автомобиля обеспечивает выполнение требований действующих законодательств распространяющихся на автомобили данного класса и назначения.
Полная масса автомобиля кг
Распределение полной массы на переднюю ось кг
Распределение полной массы на задний мост кг
Масса снаряженного автомобиля кг
Мощность двигателя кВт (л.с.)
Максимальный крутящий момент Нм (кгсм)
Модель коробки передач
пневматическая 4-х баллонная
Размер шин автомобиля
Максимальная скорость кмч
Рис.1.3 Автомобиль МАЗ-534019
6.1 Расчет маршрута № 1.
В качестве примера рассмотрим первый маршрут.
Исходные данные для расчета:
Аи = 30 ед.. – инвентарное кол-во автомобилей на данном маршруте;
αв = 091 - коэффициент выпуска;
Tн = 77 ч. – планируемое время в наряде;
Lег = 20 км – длина ездки с грузом;
Lнул = (15+15)= 30 км – нулевой пробег (в обе стороны);
е = 05 – коэффициент использования пробега;
q = 83 т. – грузоподъемность автомобиля;
Дрг = 305 дн. – количество дней работы в году;
tпр = 09 ч. – время погрузки - разгрузки;
γ = 06 – коэффициент использования грузоподъемности;
nег = 1 - количество ездок с гузом за оборот;
Vт = 49 кмч. – техническая скорость;
Рис. 1.4 Схема 1-го маршрута
Объем перевозок за оборот:
Qоб=qф1+qф2+ +qф.n = 83 [т].
Пробег с грузом за оборот:
lг.об=lг1.об+lг2.об+ +lгn.об =20 [км].
Пробег холостой за оборот:
lх.об=lх1.об+lх2.об+ +lхn.об =20 [км].
lоб=lг.об+lх.об=20+20=40 [км].
Коэффициент использования пробега за оборот:
об=lг.обlоб=2040=05.
Время погрузки-разгрузки за оборот:
tпр.об=tпр1+tпр2+ +tпр.n=09 [ч].
Время движения за оборот:
tдв.об=lобvт=4049=082 [ч]..
tоб=tдв.об+tпр.об=082+09=172 [ч].
Тм=Тн-lнулvт=77-3049=709 [ч].
Количество оборотов за время в наряде:
Тн=tоб · zоб+lнулvт=172 · 4+3049=75 [ч].
Пробег одного автомобиля за сутки:
lсут=lоб · zоб+lнул =40·3+30=190 [км].
Среднее значение коэффициента использования грузоподъемности:
γc=(qnег)Qоб=(83·06)83=06
Количество автомобилей на маршруте:
Ам = Аи αв = 30 091 = 273. Принимается Ам = 27.
Годовой объем перевозок на маршруте:
Q = q γc zоб nег Ам Дрг=83 06 4 1 27 305 = 164041 [т].
Коэффициент использования грузоподъемности:
γc=Q(q · nег · zоб · Ам ·Дрг)= 164041(83 · 1 · 4 · 27 ·305)=06.
Пробег с грузом всех автомобилей на маршруте за год:
АLгр.год=Ам · lг.об · Zоб · Дрг.= 27 · 20 · 4 · 305= 658800 [км.].
Пробег всех автомобилей на маршруте за год:
АLгод=Ам · lсут · Дрг = 27 · 190 · 305 = 1564650 [км.].
Коэффициент использования пробега:
=АLгр.годАLгод = 658800 1564650=0421.
Количество автомобиле-часов в наряде за год:
АТн.год=АмТн Дрг =2775305= 61763 а-ч.
Годовой грузооборот на маршруте:
Р = (qф1lг1.об+qф2lг1.об)zобАмДрг = 83 20 4 27 305 = 3280820 [т км]
Расчет остальных маршрутов проводится аналогично с учетом значений параметров - количества автомобилей в эксплуатации на данном маршруте длины ездки с грузом нулевого пробега времени погрузки – разгрузки грузоподъемности. Результаты расчета заносим в таблицу 1.4. Приведенный выше алгоритм эксплуатационного расчета представлен в виде программы расчета на ЭВМ с использованием электронных таблиц Microsoft Exсel.
Таблица 1.4 Расчет работы АТП на основании расчета маршрутов
Дрг- количество дней работы в году.
Асп - количество автомобилей на маршруте
αв - коэффициент выпуска.
q - грузоподъемность автомобиля
Тн-время в наряде [ч].
lнул - нулевой пробег [ч].
vт - техническая скорость [ч].
nег - количество ездок за оборот.
Зарузка за ездку в обороте
qф1 - загрузка за первую ездку оборота [т].
qф2 - загрузка за вторую ездку оборота [т].
Длина ездки с грузом в обороте
lг1.об - длина первой ездки с грузом в обороте [км].
lг2.об - длина второй ездки с грузом в обороте [км].
Пробег без груза в обороте:
lх1.об - длина первой ездки без груза в обороте [км].
lх2.об - длина первой ездки без груза в обороте [км].
Время погрузки разгрузки:
tпр1- время погрузки-разгрузки за первую ездку в обороте [ч].
tпр2- время погрузки-разгрузки за вторую ездку в обороте [ч].
Qоб=qф1+qф2+ +qф.n [т].
Пробег с грузом за оборот:
lг.об=lг1.об+lг2.об+ +lгn.об [км].
Пробег холостой за оборот:
lх.об=lх1.об+lх2.об+ +lхn.об [км].
lоб=lг.об+lх.об [км].
Время погрузки-разгрузки за оборот:
tпр.об=tпр1+tпр2+ +tпр.n [ч].
Время движения за оборот
tоб=tдв.об+tпр.об [ч].
Тн=tоб zоб+lнулvт [ч].
lсут=lобzоб+lнул [км].
Среднее значение коэффициента использования грузоподъемноcти
Коэффициент использования грузоподъемности
γc=Qм(qnегzобАмДрг).
АLгр.год=Амlг.обZобДрг.
=АLгр.годАLгод [км].
АТн.год=АмТн Дрг [а-ч].
Грузооборот на маршруте:
Р = (qф1lг1.об+qф2lг1.об)zобАмДрг
Количество автомобилей в эксплуатации:
Среднесуточный пробег одного автомобиля:
lcc=ALгод(AмДрг) [км].
Коэффициент использования пробега автомобилей АТП
Количество автомобиле-дней в эксплуатации за год:
Среднее время нахождения в наряде:
Количество автомобиле-часов в наряде за год:
Объем перевозок за год:
7. Технология перевозок
Погрузочно-разгрузочные работы как правило осуществляют подсобные рабочими промышленных предприятий. При доставке мелких партий грузов с массой одного места до 50 кг на водителей (по их согласию) может возлагаться помимо обязанностей экспедитора выполнение погрузочно-разгрузочных работ. При перевозках фасованных товаров какими обычно являются промышленные грузы используют специальные контейнеры-ящики в которых можно перевозить по нескольку десятков килограммов товара. Такие контейнеры-ящики очень удобны для пакетирования.
Продовольственные товары сдаются получателям с тщательным взвешиванием или пересчетом. При этом могут быть случаи расхождения между количеством товаров принятых к перевозке и товаров сдаваемых получателю возникшие в процессе перевозки в результате естественной убыли которая является следствием естественных свойств самого груза характера упаковки условий перевозки как то: бой посуды (при перевозках жидкостей в стеклянной таре и т.д.). нормы естественной убыли устанавливают дифференцировано: по роду тары расстоянию перевозки периода года. При перевозах штучных и фасованных товаров нормы не применяют.
Для осуществления погрузочно-разгрузочных работ с грузами перевозимыми транспортными средствами грузоотправители и грузополучатели должны располагать погрузочно-разгрузочными площадками с подъездными путями к ним обеспечивающими беспрепятственный проезд и маневрирование автомобилей а также возможность работы в темное время суток с надлежащим освещением рабочих мест.
Погрузочно-разгрузочные площадки должны быть оборудованы устройствами для выполнения погрузки и разгрузки грузов; обеспечивать соблюдение противопожарных санитарно-гигиенических и экологических нормативов; обеспечивать сохранность груза и безопасность труда персонала работающего на этих площадках; иметь при необходимости весовое и другое оборудование для определения массы и качества перевозимого груза.
Количество и оснащенность постов погрузки (разгрузки) устройствами для выполнения погрузочно-разгрузочных операций на площадках должно соответствовать виду и объему перевозимого груза и обеспечивать минимальные простои автомобилей под погрузкой и разгрузкой.
Погрузку груза на автомобиль в пунктах погрузки производит грузоотправитель; разгрузку грузов в пунктах разгрузки осуществляет грузополучатель.
Ответственность за порчу и повреждение груза при погрузке возлагается на грузоотправителя а при разгрузке – на грузополучателя; ответственность за последствия ненадлежащего крепления и размещения груза в кузове автомобиля (повреждение груза во время перевозки его смещение опрокидывание и др.) возлагается на грузоотправителя.
Перевозчик должен контролировать осуществляемые грузоотправителем указанные процессы погрузки крепления и размещения груза в кузове автотранспортного средства. При невыполнении грузоотправителем требований перевозчика о размещении и креплении грузов а также и других указанных выше операций перевозчик может отказаться от осуществления перевозки грузов с возмещением ему грузоотправителем соответствующих затрат.
Перед началом движения и в пути следования водитель обязан при наличии объективной возможности контролировать размещение крепление и состояние груза на автомобиле во избежание его смещения и падения. Если размещение крепление состояние груза создают угрозу безопасности дорожного движения водитель должен принять меры к устранению возникшей опасности либо прекратить дальнейшее движение.
В случае когда перевозчик по договору с заказчиком принимает на себя производство погрузочно-разгрузочных работ размещение и крепление груза в кузове автомобиля и другие операции ответственность за порчу и повреждение груза во время производства этих работ и за последствия ненадлежащего осуществления соответствующих операций возлагается на перевозчика.
Участие водителя автомобиля в погрузке и разгрузке груза возможно только при его согласии в порядке не противоречащем Правилам охраны труда и техники безопасности при производстве погрузочно-разгрузочных работ на автомобильном транспорте. При этом при погрузке водитель принимает груз на платформу (кузов) автомобиля а при разгрузке – подает груз с платформы (кузова) автомобиля.
Грузоотправитель должен загружать автотранспортное средство до полного использования вместимости кузова но не выше его грузоподъемности или установленных Правилами дорожного движения весовых и габаритных ограничений автотранспортных средств в реальных условиях перевозки грузов.
Штучные грузы погрузка и разгрузка которых требует больших затрат времени до начала погрузки грузоотправителем должны быть уложены в укрупненные грузовые единицы.
Схемы и порядок формирования транспортных пакетов должны соответствовать техническим условиям на изготовление транспортировку и хранение продукции предприятий изготовителей а также соответствующим Правилам перевозки грузов.
При осуществлении погрузочных работ грузоотправитель обязан:
- до начала погрузки обеспечить очистку настила платформы автотранспортного средства и опорных поверхностей груза от снега льда и загрязнений;
- равномерно размещать грузы по всей площади пола кузова автомобиля не допуская эксцентричное распределение нагрузки в кузове и нагрузки по осям с превышением величин установленных для данного автомобиля;
- штабелировать однородные штучные грузы в кузове автомобиля с соблюдением одинакового количества ярусов и обеспечением надежного крепления верхнего яруса штабеля;
- более тяжелые грузы размещать ближе к оси симметрии платформы автотранспортного средства а более легкие – ближе к бортам платформы;
- обеспечивать установление центра тяжести груза как можно ниже над платформой и в середине длины кузова автотранспортного средства;
- не допускать укладку грузов с большей объемной массой на грузы с меньшей объемной массой;
- заполнять зазоры между штабелем груза и стенками кузова при помощи различных крепежных средств (прокладок надувных емкостей и других устройств);
Для предотвращения опрокидывания или смещения груза в кузове во время движения автотранспортного средства грузоотправитель обязан надежно закрепить его в кузове автотранспортного средства с использованием собственных средств крепления если иное не предусмотрено в договоре перевозки.
Средства крепления грузов подразделяются на:
прижимные (ремни цепи тросы и другое);
растяжные (ремни тросы и другое);
распорные (деревянные устройства бруски упоры и другое);
фрикционные (противоскользящие маты и другое).
Выбор средства и метода крепления грузов в кузове автотранспортного средства осуществляется грузоотправителем с учетом обеспечения безопасности дорожного движения сохранности перевозимого груза и автотранспортного средства.
Крепление груза гвоздями скобами или другими способами повреждающими автотранспортное средство не допускается.
В случае обнаружения перевозчиком несоответствия укладки или крепления груза на автотранспортном средстве требованиям безопасности дорожного движения а также требованиям обеспечения сохранности груза или автотранспортного средства перевозчик должен поставить об этом в известность заказчика и отказаться от выполнения перевозки до устранения заказчиком замеченных недостатков если иное не предусмотрено договором.
Время прибытия автотранспортного средства под погрузку исчисляется с момента предъявления водителем грузоотправителю путевого листа и документа удостоверяющего личность а время прибытия автотранспортного средства под разгрузку – с момента предъявления грузополучателю автотранспортной накладной в пункте разгрузки.
Погрузка груза в автотранспортное средство считается законченной если груз погружен в кузов автотранспортного средства и на него надлежащим образом оформлена автотранспортная накладная.
При подаче перевозчиком автотранспортного средства под погрузку ранее согласованного времени считается что перевозчик приступил к выполнению договора в согласованное время. В этом случае грузоотправитель может принять автотранспортное средство к погрузке с момента его фактического прибытия.
Разгрузка груза с автотранспортного средства считается законченной если груз полностью выгружен с автотранспортного средства оформлены автотранспортная накладная путевой лист и другие документы на перевозку груза а также выполнены все необходимые работы по уборке кузова.
При наличии у грузоотправителя или грузополучателя въездных ворот или контрольно-пропускного пункта время прибытия автотранспортного средства под погрузку или разгрузку исчисляется с момента предъявления водителем путевого листа или автотранспортной накладной грузоотправителю (грузополучателю) у въездных ворот или контрольно-пропускном пункте.
Время пробега автотранспортного средства от ворот или контрольно-пропускного пункта к месту погрузки или разгрузки и обратно исключается при исчислении времени нахождения автомобиля под погрузкой или разгрузкой.
Грузоотправители (грузополучатели) должны отмечать в автотранспортной накладной время прибытия автотранспортного средства под погрузку (разгрузку) и время его убытия после окончания погрузки (разгрузки).
После выгрузки груза кузов автотранспортного средства должен быть очищен грузополучателем. Указанные операции по очистке и санобработке кузова автотранспортного средства по соглашению сторон могут быть выполнены перевозчиком.
На основании заключённых договоров на перевозку грузов в которых указываются сроки выполнения обязанности и ответственность в случае невыполнения условий договора. Составление договора производится с проверкой состояния подъездных путей режима работы и оснащённости механизмами погрузочно-разгрузочных пунктов службой эксплуатации АТП составляется план перевозок грузов и маршруты движения автомобилей.
Выпуск автомобилей на линию производится с учётом режима работы погрузочно-разгрузочных пунктов и производится с 7 до 9 часов возврат с линии с 16 до 18 часов. Водители работают по односменному режиму по 8 часов с перерывом на обед на 1 час. До выезда из АТП водитель получает в диспетчерской путевой лист с суточным заданием. При возвращении в АТП оформленный путевой лист сдаётся также в диспетчерскую.
Служба эксплуатации состоит из двух групп: грузовой и диспетчерской.
Грузовая группа - ведёт приём заказов производит заключение договоров на грузоперевозки. При составлении договоров и приёме заявок выявляются все условия перевозок и обследуются объекты (характер и количество груза фронт погрузки-разгрузки подъездные пути время перевозок и т. д.). По результатам обработки данных составляет сводный план перевозок на сутки с учётом очерёдности их осуществления.
Диспетчерская группа - разрабатывает оперативный суточный план перевозок производит выдачу приём и первичную обработку путевых листов непосредственно руководит работой автомобилей на линии составляет суточный отчёт о работе автопарка.
Грузоотправитель должен представить АТП на предъявляемый к перевозке груз товарного характера товарно-транспортную накладную составляемую как правило в четырёх экземплярах:
первый - грузоотправителю;
второй - грузополучателю;
третий - прилагается к счёту за перевозку и служит основанием для расчёта с грузоотправителем (грузополучателем);
четвёртый - прилагается к путевому листу и служит основанием для учёта транспортной работы. При перевозке однородных грузов от одного грузоотправителя в адрес одного грузополучателя может производиться оформление выдачей талона на каждую отдельную ездку. Талон действует только на день выдачи и заполняется в трёх экземплярах:
третий - грузополучателю;
При приёмке груза к перевозке водитель - экспедитор АТП предъявляет грузоотправителю служебное удостоверение или путевой лист заверенный печатью АТП.
Приём грузов к перевозке от грузоотправителя удостоверяется подписью водителя - экспедитора во всех экземплярах товарно-транспортной накладной один из которых вручается грузоотправителю.
Грузоотправитель обязан до прибытия автомобиля под погрузку подготовить груз к перевозке (заготовить товарно-транспортные документы пропуска на право проезда к месту погрузки и выгрузки груза) с тем чтобы обеспечить рациональное использование подвижного состава и сохранность груза в пути следования.
Время прибытия автомобиля под погрузку исчисляется с момента предъявления водителем путевого листа в пункте а время прибытия автомобиля под разгрузку - с момента предъявления водителем товарно-транспортной накладной в пункте разгрузки.
Погрузка и разгрузка считаются законченными после вручения водителем надлежаще оформленных товарно-транспортных документов на погруженный или выгруженный груз.
Время пробега автомобиля от ворот или контрольно-пропускного пункта (КПП) к месту погрузки (разгрузки) и обратно исключается при исчислении времени нахождения автомобиля под погрузкой или разгрузкой. При городских и пригородных перевозках в случаях отказа грузополучателя принять груз по причинам независящим от АТП груз переадресовывается грузоотправителем в порядке установленном Правилами другому грузополучателю или возвращается грузоотправителю. В этих случаях стоимость перевозки груза в оба конца а также штраф за простой автомобиля оплачиваются грузоотправителем. Грузополучатель обязан сделать в товарно-транспортной накладной отметку об отказе в приёмке груза заверенную подписью и печатью (штампом).
Расчёты с АТП за перевозку грузов производятся грузоотправителем (грузополучателем) в порядке установленном Правилами. Окончательный расчёт за перевозку грузов производится грузоотправителем или грузополучателем на основании счёта АТП. Основанием для выписки счёта за осуществлённую перевозку служат товарно-транспортные накладные либо акты замера или акты взвешивания груза а за пользование автомобилями оплачиваемыми по повременному тарифу - данные путевых листов заверенных грузоотправителем или грузополучателем.
АТП несёт ответственность за не вывоз грузов в количестве предусмотренных в декадном плановом задании за не обеспечение сохранности перевозимого груза за несвоевременную подачу подвижного состава в пункт первой погрузки.
9 Показатели производственной программы АТП по эксплуатации
Наименование параметра
Обозначение параметра
Число дней работы в году
Число автомобилей в эксплуатации
Среднесуточный пробег
Коэффициент использования пробега
Номинальная грузоподъемность
Среднее расстояние перевозки груза
Время погрузки - разгрузки
Техническая скорость в пригороде
Автомобиле-дни в эксплуатации
Автомобиле-часы в наряде за год
Общий годовой пробег АТП
Годовой пробег всех автомобилей с грузом
Общий объем перевозок
Технологическая часть
1. Технологический расчет
1.1. Исходные данные для проектирования
Таблица 2.1 Исходные данные и условия проектирования
Показатель (условие)
Значение (характеристика) по моделям и АТП
Грузовое для перевозки грузов
Списочное число автомобилей
Категория условий эксплуатации подвижного состава
Природно-климатические условия
Режим работы предприятия
Число рабочих дней в году
Время на транспортировку подвижного состава в капитальный ремонт
Продолжительность капитального ремонта
Нормативные пробеги
Нормативы трудоёмкости
чел·ч на одно обслуживание
Нормативы простоя в ТО и ТР
1.2. Расчет программ технического обслуживания и ремонта
А) Корректировка нормативов
Скорректируем нормативы приведенные в исходных данных к реальным условиям эксплуатации. Для этого сведем все корректировочные коэффициенты в табл. 2.2.
Таблица 2.2 Корректировка нормативов
Коректируемые нормативы
Корректировочные коэффициенты
Простой в ТО и ТР Тдо-тр дни
- К1- коэффициент корректирования нормативов в зависимости от условий эксплуатации;
- К2- коэффициент корректирования нормативов в зависимости от модификации подвижного состава и организации работ;
– К3 - коэффициент корректирования нормативов в зависимости от природно-климатических условий;
– К4 - коэффициент корректирования нормативов трудоемкости ТО и ТР в зависимости от количества единиц технологически совместимого подвижного состава
– К5 - коэффициент корректирования нормативов технического обслуживания и текущего ремонта в зависимости от количества обслуживаемых и ремонтируемых автомобилей на АТП и количества технологически совместимых групп подвижного состава
Проводим корректировку нормативов по формулам:
LТО-1 = L'ТО-1 · К1 · К3 = 4000 · 1 · 1 = 4000 км
LТО-2 = L'ТО-2 · К1 · К3 = 16000 · 1 · 1 = 16000 км
Lкр = L'кр · К1 · К2 · К3 = 400000 · 1 · 1 · 1 = 400000 км
ТЕО = Т'ЕО · К2 = 04 · 13 = 052 чел·час на одно обслуживание
ТТО-1 = Т'ТО-1 · К2 · К4 = 75 · 13 · 1 = 98 чел·час на одно обслуживание
ТТО-2 = Т'ТО-2 · К2 · К4 = 24 · 13 · 1 = 312 чел·час на одно обслуживание
Ттр = Т'тр · К1 · К2 · К3 · К4 · К5 = 55 · 1 · 13 · 1 · 1 · 1 = 72 чел·час1000 км
Сводим полученные данные в таблицу 2.3
Корректируемые нормативы
Согласно руководству по эксплуатации
Простой в ТО и ТР Дто-тр дни
Моечные и обтирочные работы ЕО планируется механизировать. В зависимости от принимаемого уровня механизации работ ЕО расчетная трудоемкость еще раз корректируется результаты расчетов приведены в табл. 2.4.
Трудоемкость нормативная скорректированная
Принимаемый уровень механизации %
Трудоёмкость после механизации
Контрольно-осмотровые
Устранение мелких неисправностей (переноятся в зону ТР)
Другие виды ЕО (заправочные постановка автомобилей на стоянку проверка технического состояния автомобиля устранение мелких неисправностей) выполняются водителем за счет подготовительно-заключительного времени и механиком контрольно-пропускного пункта а также на посту ТР и в норматив трудоемкости ЕО не входят («Положением о техническом обслуживании и ремонте подвижного состава автомобильного транспорта»).
Б) Расчет количества технических воздействий
Согласно построению нормативов ТО и Р исходным периодом для расчета технических воздействий на автомобиль является цикл – период соответствующий пробегу автомобиля до капительного ремонта.
Расчет количества технических воздействий на автомобиль за цикл
Капитальный ремонт Nкр = 1
ТО-2: NТО-2 = Lкр Lto-2 - Nкр = 400000 16000 - 1 = 24
ТО-1: NТО-1 = Lкр Lto-1 - (Nкр + NТО-2) = 400000 4000 - (1 + 24) = 75
ЕО: NЕО = Lкр Lcc = 400000 193 = 2073
где Lкр LТО-2 LТО-1 Lсс - пробег до КР ТО-2 ТО-1 и среднесуточный пробег в км соответственно скорректированный для конкретных условий.
Расчет количества воздействий за год
Для перехода от цикла к году необходимо определить пробег за год и коэффициент перехода.
Количество дней эксплуатации за цикл:
ДЭЦ. = Lкр Lcc = 400000 193 = 2073
Количество дней простоя в ТО и ТР за цикл:
ДРЦ.АВТ. = ДКР + ДКР.тр + ДТО-ТР · Lкр 1000 = 22 + 2 + 048 · 400000 1000 = 216
где ДКР ДКР.тр ДТО-ТР – простой в капитальном ремонте время транспортировки в капитальный ремонт удельный простой в ТО и ТР на 1000 км пробега дни соответственно.
Определим коэффициент технической готовности за цикл по формуле:
αт. = ДЭЦ. (ДЭЦ. + ДРЦ.АВТ. ) = 2073 (2073 + 216) = 091
Пробег за год составит:
Lг. = Дрг · αт. · Lcc = 305 · 091 · 193 = 53567 км
где Дрг = 305 – количество дней работы подвижного состава в году.
Коэффициент перехода от цикла к году:
г. = Lг. Lц = 53567 400000 = 0134
где Lц – пробег за цикл ( равен Lкр).
С учетом коэффициента перехода количество технических воздействий в год на единицу (автомобиль) равно:
Nгкр = Nкр · г. = 1 · 0134 = 0134 ед.
NгТО-2 = NTO-2 · г. = 24 · 0134 = 32 ед.
NгТО-1 = NTO-1 · г. = 75 · 0134 = 101 ед.
NгЕО = NЕО · г. = 2073 · 0134 = 2778 ед.
Общая программа технических воздействий на весь парк данной группы подвижного состава:
Σ Nгкр = Nгкр · А = 0134 · 250 = 34 ед.
Σ NгТО-2 = NгТО-2 · А = 32 · 250 = 800 ед.
Σ NгТО-1 = NгТО-1 · А = 101 · 250 = 2525 ед.
Σ NгЕО = NгЕО · А = 2778 · 250 = 69450 ед.
где А = 250списочное число подвижного состава
Число диагностических воздействий за год определим по формулам:
Σ NгД1 = 11 · Σ NгТО-1 + Σ NгТО-2 = 11 · 2525 + 800 = 3578 ед.
Σ NгД2 = 12 · Σ NгТО-2 = 12 · 800 = 960 ед.
Расчет количества технических воздействий за сутки
Суточная программа по каждому виду обслуживаний определяется для того чтобы можно было спланировать производство на сутки и по сменам.
Количество обслуживаний в сутки определим по формуле
NiC = Σ Nгi ДРГi где ДРГi = 305 дней - количество дней в году выполнения данного вида обслуживания.
NсТО-2 = Σ NгТО-2 ДРГ = 800 305 = 26 ед.
NсТО-1 = Σ NгТО-1 ДРГ = 2525 305 = 83 ед.
NсЕО = Σ NгЕО ДРГ = 69450 305 = 2277 ед.
NсД1 = Σ NгД1 ДРГ = 3578 305 = 117 ед.
NсД2 = Σ NгД2 ДРГ = 960 305 = 31 ед.
Расчет объемов работ технических воздействий
Расчет объемов работ по ТО и ТР за год
Годовые объемы работ по ТО и ТР определим по формулам:
TгЕО = Σ NгЕО · TЕО = 69450 · 016 = 11112 чел·ч
TгТО-1 = Σ NгТО-1 · TТО-1 = 2525 · 98 = 24745 чел·ч
TгТО-2 = Σ NгТО-2 · TТО-2 = 800 · 312 = 24960 чел·ч
TгТР = (Lг. · A · ТТР) 1000 = (53567 · 250 · 72) 1000 = 96421 чел·ч
Трудоёмкость устранения мелких неисправностей из зоны ЕО в зоне ТР:
TгЕОтр = Σ NгЕО · TЕО = 69450 · 024 = 16668 чел·ч
1.3. Распределение объемов работ ТО и ТР по видам работ
Объем ТО и Р распределяется между различными подразделениями по технологическим и организационным признакам. ТО и ТР выполняются на постах и производственных участках. К постовым относятся работы по ТО и ТР выполняемые непосредственно на автомобиле (моечные уборочные смазочные крепежные диагностические и др.). К участковым работам относятся работы по проверке и ремонту узлов и агрегатов снятых с автомобиля и выполняемых на участках (агрегатном слесарно-механическом электротехническом и т.д.).
Работы по ЕО ТО-1и ТО-2 выполняются в самостоятельных зонах а работы по ТР выполняемые на отдельных универсальных постах производят в общей зоне. Распределим трудоемкость по видам работ в соответствии с [7]. Данные распределения сводим в таблицы 2.6. 2.7.
Таблица 2.5 Распределение годовой трудоёмкости ТО и ТР по видам работ
Моечные дозаправочные
Диагностирование общее (Д-1)
Крепежные регулировочные смазочные др.
Диагностирование углубленное (Д-2)
Крепёжные регулировочные смазочные др.
Регулировочные и разборочно-сборочные работы
Слесарно-механические работы
Электротехнические работы
Аккумуляторные работы
Ремонт приборов системы питания
Шиномонтажные работы
Вулканизационные работы (ремонт камер)
Кузнечно-рессорные работы
1.4 Корректирование трудоемкости ТО и ремонта с учетом выделения
диагностических работ
Доля диагностических работ%
Уровень совмещения %
Трудоемкость ТО и ТР принятаяt12TPпр чел·ч
Годовые расчетные объемы работ ТО-1 ТО-2 и ТР с учётом корректировки:
TгТО-1 = Σ NгТО-1 · TТО-1 = 2525 · 8820 = 22271 чел·ч
TгТО-2 = Σ NгТО-2 · TТО-2 = 800 · 28080 = 22464 чел·ч
TгТР = (Lг.борт.· Aборт.· ТТР) 1000 = (53567 · 250 · 7056) 1000 = 94492 чел·ч
Контрольно-диагностические работы из ТО-1 и ТО-2 выносим в отдельные посты Д-1 и Д-2 (соответственно). Контрольно-диагностические работы из текущего ремонта распределяем между Д-1 и Д-2 по 50% на каждый пост.
Все годовые объёмы работ сводим в таблицу
Таблица 2.7 Годовые объёмы работ ТО и ТР
Устранение мелких неисправностей
Работы по самообслуживанию обеспечивают содержание зданий сооружений оборудования и оснастки предприятия в исправном состоянии. Они выполняются подразделениями главного механика энергетика строительно-ремонтными группами.
Объем работ самообслуживания определяется в процентном отношении от суммарной годовой трудоемкости работ по техническому обслуживанию и ремонту подвижного состава выполняемых на территории предприятия по формуле
Тсам = (ТгЕО + ТгТО-1 + ТгТО-2 + Тгд1 + ТгД2 + Тгтр) · КС 100 = (11112 + 22271 + 22464 +3439 + 3460 + 94492) · 10 100 = 15724 чел·ч
где Кс = 10 -доля работ по самообслуживанию от суммарной годовой трудоемкости работ по ТО и ТР подвижного состава [7].
Распределение работ по самообслуживанию по видам работ приведено в таблице 2.8.
Для организации работ по самообслуживанию на предприятии создается отдел главного механика (ОГМ).
Таблица 2.8 Распределение работ по самообслуживанию
Ремонтно-строительные и деревообделочные
1.6. Обоснование режима работы и принимаемых форм организации производства
Режим работы производства ТО и ТР т.е. количество смен их продолжительность и распределение по сменам объемов каждого вида работ определяет параметры проектируемой производственно-технической базы (количество постов и рабочих мест площади зон и отделений и т.д.).
Чем больше смен и чем равномернее распределены по ним объемы работ ТО и ремонта тем меньше требуется производственных мощностей и капитальных вложений на строительство АТП.
Режим выполнения обслуживания и ремонта зависит от следующих факторов:
- режима работы подвижного состава на линии (количества рабочих дней в году и продолжительности работы на линии);
- требования ежедневного обслуживания (мойки уборки и пр.) зависящих от видов перевозок и климатических условий;
- наличия производственных мощностей и ограничения по их развитию;
- возможности привлечения рабочих к работе в вечернее и ночное время.
Чем больше суточное время работы подвижного состава тем меньше остается времени у технической службы АТП для выполнения ЕО ТО и ТР без потерь линейного времени. Исходя из этого рекомендуется организовывать работы [4]:
ЕО ТО-1 - в межлинейное время (во время отстоя подвижного состава т.е во вторую смену);
ТО-2 - в первую смену или с минимальными целодневными простоями автомобилей;
Д-2 - в первую или в первую и вторую смены;
ТР - максимальное количество мелких заявок между возвратом и выездом автомобилей на линию с организацией для этой цели дополнительной (второй и третьей) смены производства после окончания работы автомобилей.
Участки электротехнический топливной аппаратуры и другие выполняющие работы непосредственно на автомобиле должны работать во все организованные смены ТР.
Работы по восстановлению оборотного фонда агрегатов узлов приборов и деталей - в первую смену производства. Для сокращения потребного количества рабочих мест может организовываться вторая смена;
Работы самообслуживания - во все производственные смены.
Учитывая вышесказанное принимаем:
ЕО – работа в две снены.
ТО-1 – работа в две смены.
ТО-2 – работа в две смены.
Д-1 – работа в одну смену.
Д-2 – работа в одну смену.
ТР - работа в три смены.
Служба ОГМ – работа в в одну смену.
Участки – работа в 2 смены.
По рекомендациям [3] поточный метод ТО целесообразен если сменная программа составляет по ТО-1 не менее 12 15 а по ТО-2 не менее 5 6 обслуживаний. В нашем случае ТО-1 и ТО-2 проводим на универсальных постах. ЕО выполняем на отдельной поточной линии.
1.7. Расчет численности ремонтно-обслуживающего персонала
Технологически необходимое количество рабочих т.е. непосредственно обеспечивающее выполнение годового объема работ ТО и ремонта в общем или отдельно по каждому виду работ рассчитывается по формуле:
где Тг - годовой объем работ чел·ч ( по зоне или отделению);
Фт - годовой фонд времени рабочего места или технологически необходимого рабочего ч.
Штатное количество производственных рабочих т.е. принимаемое предприятием с учетом потерь рабочих дней на отпуска болезни и по другим причинам определяется по формуле:
где Фш – годовой фонд времени штатного рабочего ч.
Распределение рабочих по сменам проводим в соответствии с ранее принятыми рекомендациями. Результаты расчетов сводим в таблицу 2.10.
Таблица 2.9 Расчёт производственных рабочих
ТР (Крепёжно-регулировочные разборочно-сборочные устранение мелких неисправностей)
Слесарно-механические
Ремонт приборов системы питания
Работы самообслуживания выполняемые ОГМ
1.8. Формирование производственной структуры технической службы АТП
В этом разделе определим производственную структуру АТП.
Производственная структура отражает перечень производственных подразделений технической службы АТП их численность внутреннюю структуру (количество звеньев бригад) и взаимосвязи обуславливаемые технологическими и территориальными факторами.
По итогам расчёта ремонтных рабочих принимаем следующие организационные решения:
Объединяем вулканизационный участок и шиномонтажный в шиноремонтный участок.
Объединяем сварочный и жестяницкий участки в сварочно-жестяницкий участок.
Объединяем кузнечно-рессорный арматурно-кузовной и медницкий участки в кузнечно-кузовной участок.
1.9. Расчет линий и постов в производственных зонах и отделениях
А) Расчет поточных линий
Поточная линия непрерывного действия для ЕО
Такт линии непрерывного действия (ЕО) определяется исходя из следующих соображений:
- на линиях ЕО на специализированных постах выполняются различные виды работ (уборочные моечные обтирочные и др.) с равным уровнем механизации;
- равномерность работы линии может быть обеспечена при равенстве тактов всех постов;
- определяющим фактором такта поста может являться пропускная способность моечной установки (Ny - авт.ч.);
- такты других постов регулируются количеством рабочих.
Такт линии ЕО из условия пропускной способности мойки:
ео = 60 Nу = 60 15 = 4 мин.
Потребная скорость конвейера:
Vк = (Lа + а) ео =(86 + 2) 4 = 26 ммин
где Lа = 86 м - длина автомобиля
а = 2 м - принятый интервал между автомобилями стоящими на постах линии
RЕО = (ТЕОобсл. · 60) NEOc = (7 · 60) 2277 = 19 мин
где ТЕОобсл. = 7 ч.- продолжительность работы линии ЕО за смену
NEOc = 2277 - суточная программа воздействий ЕО ед.
Расчётное количество линий ЕО:
mЕО = ео RЕО = 4 19 = 21
Принимаем 1 линию с 2-х сменным режимом работы во вторую и третью смену;
Количество постов на линии ЕО принимаем ХЕО = 3 в соответствии с рекомендациями [7].
пост – уборочные работы;
пост – моечные работы;
пост – обтирочные смазочные и дозаправочные работы
Б) Расчет количества постов ТО ТР и производственных участков
ХТО-1=ТгТО-1·Kр(Дрг·С·Тсм·Кисп·Р)=22271·113(305·2·8·097·25)=21 принимаем 2 поста.
где: Тг - годовой объем работ чел. ч.;
Кр - коэффициент резервирования постов;
Дрг - число рабочих дней в году;
С - число смен работы в сутки;
Тсм - продолжительность смены ч.;
Р - численность одновременно работающих на одном посту чел.;
Кисп - коэффициент использования рабочего времени поста.
ХТО-2=ТгТО-2·Kр(Дрг·С·Тсм·Кисп·Р)=22464·113(305·2·8·097·25)=21 пост принимаем 2 поста.
ХД-1=ТгД-1·Kр(Дрг·С·Тсм·Кисп·Р)=3794·125(305·1·8·09·2)=11 пост.
ХД-2=ТгД-2·Kр(Дрг·С·Тсм·Кисп·Р)=3105·125(305·1·8·09·2)=09 пост.
Учитывая что работы Д-1 и Д-2 проводятся в разные смены принимаем один пост в зоне диагностики (первая смена работы Д-2 вторая Д-1).
Хтр=Тгтр·Kр(Дрг·С·Тсм·Кисп·Р)=50416·125(305·3·8·096·15)=6 пост.
Хмал=Тгмал·Kр(Дрг·С·Тсм·Кисп·Р)=5785·125(305·2·8·098·2)=08 пост. принимаем 1 пост.
Сварочно-жестяницкий:
Хсвар=Тгсвар·Kр(Дрг·С·Тсм·Кисп·Р)=6750·113(305·2·8·097·15)=11 пост. принимаем 1 пост.
Трудоёмкость Тгсвар взята из таблицы 2.6 для сварочных и жестяницких постовых работ.
Расчет постов ожидания ТО и ремонта:
«Посты ожидания предназначены для повышения эффективности использования рабочих постов за счёт сокращения времени поиска автомобилей на территории АТП и их перегона а также обеспечения возможности начать работу сразу после постановки автомобиля на пост особенно в зимнее время.
Общее количество постов ожидания ТО и ремонта в АТП может включать:
- посты подпора непосредственно на линиях ТО-1 ТО-2 диагностики.
- посты ожидания в зонах ТР и ТО-2.
- посты в зонах ожидания перед въездом производственный корпус.
- посты на накопительных площадках перед ЕО.
Количество постов ожидания принимается из расчета:
- перед ЕО и Д-1 – 50% часовой пропускной способности.
- перед ТО-1 ТО-2 – 50% сменной программы.
- перед ТР непосредственно в зоне 20-40% от числа рабочих постов а в зоне ожидания на открытой площадке исходя из 25% от расчетного количества неисправных автомобилей за сутки.»
Количество постов ожидания ЕО: 50% от т.е. 7 постов
Количество постов ожидания для зоны ТО: 50% от т.е. 1 пост внутри корпуса и 2 поста возле въезда.
Количество постов ожидания ТР: непосредственно в зоне 20% от т.е. 1 пост.
1.10. Подбор технологического оборудования и оснастки для производственных зон и отделений
Подбор технологического оборудования для постов и технологических зон проведен по имеющимся источникам [8 910].
Таблица 2.10 Состав технологического оборудования
Наименование оборудования
Установка для мойки автомобилей
Воздухо-раздаточная колонка
Конвейер для передвижения автомобилей на линии ЕО
Машина подметально-пылесосная
Передвижная маслораздаточная колонка
Комплект инструментов для ТО и ТР электрооборудования автомобилей
Стеллаж для запасных частей
Тележка инструментальная
Линейка для проверки схождения колёс
Комплект инструментов автомеханика
Шкаф для приборов технической документации и инструмента
Установка для промывания системы смазки
Подставка для рабочих в осмотровой канаве
Бак с моторным маслом
Установка для мойки фильтров
Комплект приборов и инструментов для ТО аккумуляторов
Стол - тележка смазчика
Установка для слива масла
Прибор для проверки шкворневых соединений
Установка смазочно-заправочная
Бак с тормозной жидкостью
Бак с трансмиссионным маслом
Колонка воздухораздаточная для накачки шин
Гайковерт для стремянок рессор
Прибор для проверки карданных валов
Тележка для снятия колес
Установка для проверки рулевого управления
Линейка для проверки сходимости колес автомобиля
Стеллаж для деталей приспособлений
Ключ динамометрический
Комплект инструментов
Тележка для снятия и установки рессор
Приспособление для снятия и установки КПП
Тележка для снятия и установки колес
Тележка с набором инструмента для ремонта автомобилей
Тележка для перевозки агрегатов и узлов
Подставка под колеса
Прибор для проверки переднего моста
Шкаф для приборов и приспособлений
Приспособление для выпрессовки шкворней
Съемник универсальный
Емкость для слива охлаждающей жидкости
Емкость для слива масел
Солидолонагнетатель смазочный
Комплект диагностический
Комплект приборов для проверки тормозов
Прибор для проверки и регулировки света фар
Стенд для проверки тормозов грузовых автомобилей
Стенд для разборки и сборки КПП
Стеллаж для деталей
Ванна для мойки деталей
Ларь для обтирочных материалов
Стенд для разборки сборки и регулировки рулевых механизмов
Стенд для разборки и сборки редуктора заднего моста
Стенд для ремонта двигателя
Шкаф для приборов и инструмента
Устройство для притирки клапанов
Стенд для приработки и испытания двигателей
Стенд для приработки и испытания КПП
Слесарно-механический участок
Станок токарно-винторезный
Станок вертикально-сверлильный
Станок точильно-шлифовальный
Стеллаж для инструментов
Аккумуляторный участок
Комплект приспособлений и инструмента для ремонта АКБ
Стенд для проверки аккумуляторных батарей
Пробник аккумуляторный
Шкаф для зарядки АКБ
Бак для дистиллированной воды
Ванна для электролита
Тележка для транспортировки АКБ
Комплект оборудования для ТО АКБ
Участок ремонта топливной аппаратуры
Контрольно-испытательный стенд
Прибор для проверки топливной системы
Стенд для регулировки топливных агрегатов
Стенд для очистки и испытания форсунок
Шиноремонтный участок
Мульда для ремонта сквозных повреждений
Станок для шероховки
Домкрат гидравлический
Верстак для ремонта камер
Стенд для монтажа и демонтажа шин
Стенд для балансировки колес
Воздухораздаточная колонка
Компрессор воздушный поршневой
Сварочно-жестяницкий участок
Набор инструмента для правки кузовов автомобилей
Электроножницы ручные
Набор приспособлений и инструментов
Шкаф инструментальный
Инструмент и приспособление для правки
Пневматическое зубило ручное
Трансформатор сварочный
Преобразователь для ручной электродуговой сварки
Стол для сварочных работ
Шкаф для инструмента
Генератор ацетиленовый
Тележка для газовых баллонов
Редуктор кислородный
Р=15МПа Пропуск 60м3ч
Редуктор ацетиленовый
Горелка сварочная для ручной ацетиленокислородной сварки
Шкаф для хранения баллонов с отсосом воздуха
Кузнечно-кузовной участок
Установка для промывки и протравливания топливных баков
Стелаж для радиаторов бензобаков
Верстак для медницких работ с тумбой
Стенд для проверки и ремонта радиаторов автомобиля
Слесарный верстак с тисками
Ванна для испытаний топливных баков и радиаторов
Пресс гидравлический
Стенд для разборки и сборки рессор и рихтовки рессорных листов
Стеллаж для рессорных листов
Электротехнический участок
Контрольно-испытательный стенд для проверки электрооборудования
Прибор для проверки якорей
Пуско-зарядное устройство
Комплект инструмента для ремонта
Подставка под оборудование
Стенд для проверки генераторов стартеров и реле-регуляторов
Установка для окраски
Сушилка инфракрасного излучения
Стеллаж для покрасочных материалов
Прибор для полировки кабин
Обдирочно-шлифовальный станок
Шкаф для инструментов
Верстак универсальный
Комплект электротехнических приборов
Станок деревообрабатывающий
1.11. Расчет площадей производственных зон и отделений
А) Поточная линия ЕО
Для зоны ЕО размещенной на поточной линии применяется аналитический метод расчета площадей по формуле:
FEO = Lф · Нф = 52 · 77 = 400 м2
где LФ - фактическая длина линии м;
НФ - фактическая ширина линии м.
Фактическая длина линии по формуле
Lф = Lа · ХП + а · (ХП - 1) + 2 · (La + 2 · a) = 86 · 3 + 15 ·(3 - 1) + 2 · (86 + 2 · 15)= 434 м
где La = 86 м - длина автомобиля обслуживаемого на линии;
XП = 3 - рабоч. пост. на линии;
а = 15 м - нормативная величина расстояния между автомобилями стоящими на линии и от крайнего автомобиля до ворот линии;
Ширина линии определяется исходя из установленных нормативов [3] расстояния от боковой стороны автомобиля до стенки с учетом расстановки оборудования в нашем случае все будет определятся шириной мойки:
Нф = В + 2b = 47 + 2 · 15 = 77 м2
где В = 5 м- ширина мойки м:
b = 15 м - нормативная величина прохода между стеной и мойкой.
FТО-1ТО-2 = fa · XП · КП = 215 · 5 · 5 = 538 м2;
где fa - площадь занимаемая автомобилем (17 м2);
XП - суммарное число постов в зоне ТО: рабочих и ожидания;
КП - коэффициент плотности расстановки постов (5);
В) Участок диагностики
FД = (fa · XП + Fоб) · Кп = (215 · 1 + 61) · 4 = 110 м2
XП - количество постов зоны диагностики (1 пост);
Fоб - площадь занятая оборудованием (69 м2);
Кп - коэффициент плотности расстановки оборудования (5);
FТР = fa · XП · КП = 215 · 7 · 5 = 753 м2
Д) Производственные участки
Fсвар = (fa · Xп + Fоб) · Кп = (215 · 1 + 93) · 4 = 123 м2
Fмал = (fa · Xп + Fоб) · Кп = (215 · 1 + 7) · 4 = 114 м2
Fагр = Fоб · Кп= 195 · 4 = 72 м2
Fслес = Fоб · Кп= 74 · 4 = 30 м2
Fэлек = Fоб · Кп= 71 · 35 = 25 м2
Fак = Fоб · Кп= 51 · 35 = 18 м2
Fтоп = Fоб · Кп= 51 · 4 = 20 м2
Fшин = Fоб · Кп= 79 · 4 = 32 м2
Fкузн = Fоб · Кп= 93 · 45 = 42 м2
Fогм = Fоб · Кп= 92 · 35 = 32 м2
Результат расчётов сводим в таблицу 2.11
Наименование зоны. отделения
Площадь зани-маемая оборудованием м2
Расчётная площадь м2
Участок ремонта топлив ной аппаратуры
1.12. Расчет хранимых запасов и площадей складских помещений
А) Склад смазочных материалов
Суточный расход топлива на линейную работу подвижного состава определим по формуле
Gл = (Аи · аи · Lсс) · q 100 = (250 · 091 · 193) · 23 100 = 10099 л
где Аи =250 - списочное количество автомобилей;
Lсс = 193 км - среднесуточный пробег км;
q = 23 л100 км - линейный расход топлива по нормам.
аи = 091 - коэффициент использования парка.
Суммарный суточный расход топлива определим по формуле
Gсут = (Gл + Gт) · = (10099 + 10099 · 001) · 103 = 10506 л
где Gл – суточный расход топлива на линейную работу автомобилей л.;
Gт - суточный расход топлива на внутригаражное маневрирование и технологические надобности (составляет менее 1% от Gл) л.;
= 103 - коэффициент учитывающий принятые в АТП повышение или снижение нормы расхода топлива.
Запас смазочных материалов определим по удельным нормам расхода смазок на каждые 100 л планируемого расхода автомобильного топлива и продолжительности хранения материалов на складе АТП по формуле
Зм = 001 · Gсут · qн · Дз = 001 · 10506 · 32 · 15 = 5043 л - моторное масло
Зт = 001 · Gсут · qн · Дз = 001 · 10506 · 04 · 15 = 630 л - трансмиссионное масло
Зс = 001 · Gсут · qн · Дз = 001 · 10506 · 01 · 15 = 158 л - специальное масло
Зп = 001 · Gсут · qн · Дз = 001 · 10506 · 03 · 15 = 473 л - пластичная смазка
Объём отработанных масел - 15% от расхода свежих масел.
Qм = 015 · 5043 = 756 л - моторное масло
Qт = 015 · 630 = 95 л - трансмиссионное масло
Qс = 015 · 158 = 24 л - специальное масло
Qп = 015 · 473 = 71 л - пластичная смазка
Подбираем стандартные бочки для масел и смазок.
Моторное масло: V – 5 емк – 12 м3 Площадь Fм = 39 м2
Трансмиссионное масло: V – 3 емк – 023 м3 Площадь Fм = 081 м2
Специальное масло: V – 1 емк – 023 м3 Площадь Fм = 027 м2
Пластичные смазки: V – 5 емк – 01 м3 Площадь Fм = 085 м2
Моторное масло: V – 4 емк – 023 м3 Площадь Fм = 108 м2
Трансмиссионное масло: V – 1 емк – 01 м3 Площадь Fм = 017 м2
Специальное масло: V – 1 емк – 005 м3 Площадь Fм = 01 м2
Пластичные смазки: V – 4 емк – 002 м3 Площадь Fм = 024 м2
Оборудование: насос для перекачки масел – Fн = 022 м2
насосная установка – Fн = 17 м2.
Площадь склада смазочных материалов
Fсм = (Fоб + Fм) · Кп = (022 + 17 + 024 + 01 + 017 + 108 + 085 + 027 + 081 + 39) · 25 = 23 м2
Площадь склада резины определяем исходя из того что покрышки хранятся на стеллажах в два яруса в положении стоя вплотную одна к другой. Запас покрышек рассчитываем по формуле
Зрез = (Аи · аи · Lcc · Xк · Дз) (Lгн + Lгп) = (250 · 091 · 193 · 6 · 15) (45000 + 24000) = 57
где Хк = 6 - количество шин используемых на автомобиле (без запасной);
Lгн = 45000 км- гарантийная норма пробега новой покрышки без ремонта;
Lгп = 24000 км- гарантийная норма пробега шин после первого наложения нового протектора;
ДЗ - число дней запаса (15 дней).
Длину стеллажей определим из выражения
Lст = Зрез П = 57 6 = 95 м
где П = 6 - количество покрышек размещающихся на одном погонном метре стеллажа с учетом ярусности
Площадь занимаемая стеллажами с покрышками
FОБ.п = Lст · bст = 95 · 11 = 10 м2
Площадь занимаемая камерами на вешалах определяется исходя из значений П = 15 20 при двухъярусном хранении и ширине равной 06 диаметра камеры.
FОБ.к = (Зрез · 06 15) · bст = 57 · 11 · 0615 = 3 м2
Площадь склада резины
Fрез = (Fоб.п + Fоб.к) · Кп = (3 + 10) · 25 = 33 м2
В) Склад запасных частей агрегатов и материалов
Размер запаса склада запчастей определяем по формуле:
Мзч = (Аи · аи · Lcc · a · Ма · Дз) (10000 · 100) = (250 · 091 · 193 · 2 · 9800 · 20) (10000 · 100) = 17212 кг
где Ма = 9800 кг - масса автомобиля.
а = 2% - средний процент расхода запчастей на 10000 км пробега [4];
ДЗ - число дней запаса (20 дней).
Площадь под запчасти:
Fзч = Мзч mCзч = 17212 600 = 287 м2
где mс - допускаемая нагрузка на 1 м2 площади стеллажа (600 кг)
Площадь склада под запчасти: Fск.зч = Fзч · Кп = 287 · 25 = 72м2
Размер запаса склада металлов (ДЗ = 10 дней)
Мм = (Аи · аи · Lcc · a · Ма · Дз) (10000 · 100) = (250 · 091 · 193 · 1 · 9800 · 10) (10000 · 100) = 4303 кг
Площадь под металлы:
Fм = Мм mCм = 4303 650 = 66 м2
Площадь склада под металлы: Fск.м = Fм · Кп = 66 · 25 = 17м2
Склад лакокрасочных изделий и химикатов
Размер запаса склада лакокрасочных изделий (ДЗ = 10 дней)
Млк = (Аи · аи · Lcc · a · Ма · Дз) (1000 · 100) = (250 · 091 · 193 · 02 · 9800 · 10) (10000 · 100) = 861 кг
Площадь лакокрасочные покрытия:
Fлк = Млк mCлк = 861 250 = 34 м2
Площадь склада под лакокрасочные покрытия: Fск.лк = Fлк · Кп = 34 · 25 = 9м2
Склад прочих материалов
Размер запаса склада прочих материалов (ДЗ = 10 дней)
Мпр = (Аи · аи · Lcc · a · Ма · Дз) (10000 · 100) = (250 · 091 · 193 · 02 · 9800 · 10) (10000 · 100) = 861 кг
Площадь под прочие материалы:
Fпр = Мпр mCпр = 861 250 = 34 м2
Площадь склада под прочие материалы: Fск.пр = Fпр · Кп = 34 · 25 = 9м2
Размер запаса склада агрегатов определяется по количеству и массе оборотных агрегатов на каждые 100 однотипных автомобилей [23].
Мдв = (Кдв · qдв · Аи) 100 = (4 · 1058 · 250) 100 = 10580 кг
где Кдв = 4 – число оборотных двигателей на 100 автомобилей;
qдв = 1058 кг – вес двигателя.
Мк.п. = (Кк.п. · qк.п. · Аи) . 100 = (4 · 223 · 250) 100 = 2230 кг
Передний мост автомобиля
Мп.м. = (Кп.м. · qп.м. · Аи) 100 = (4 · 445 · 250) 100 = 4450 кг
Задний мост автомобиля
Мз.м. = (Кз.м. · qз.м. · Аи) 100 = (4 · 445 · 250) 100 = 4450 кг
Мрул = (Крул · qрул · Аи) 100 = (4 · 56 · 250) 100 = 560 кг
Площадь под агрегаты:
Fаг = Маг mаг = (10580 + 2230 + 4450 + 4450 + 560) 500 = 45 м2
Площадь склада под агрегаты:
Fск.аг = Fаг · Кп = 45 · 25 = 113 м2
Площадь складов промежуточного хранения принимаем 20% от общей площади складов.
Расчёты сводим в таблицу 2.13.
Таблица 2.12 Площадь складов
Коэффицент плотности
Склад смазочных материалов
Склад промежуточного хранения
Г) Зона хранения (стоянки) подвижного состава
Fx = fa · Аи · Кп = 215 · 250 · 3 = 16125 м2
2 Обоснование планировочных решений
2.1 Обоснование планировочного решения производственного корпуса
Размеры производственного корпуса определяется исходя из длин зон ТО и ТР. При этом ширину пролётов по периметру корпуса выбираем стандартную 6 м. Исходя из этого определяем длину и ширину корпуса (60 м х 66 м). Высота корпуса - 6 м. Производственный корпус спроектирован из сборных модульных конструкций.
Зоны ТО и ТР выполнены сплошными пролётами что значительно увеличивает пропускную способность автомобилей по сравнению с тупиковыми типами зон. В центре корпуса расположена зона ТР а вокруг расположены все складские помещения и участки. Рядом с 6 постами зоны ТР расположены агрегатный участок а также склады агрегатов и запчастей. Такая компоновка позволяет обеспечить агрегатный и данные склады единым подъемным краном который необходим для строповки и поднятия на перевозные тележки тяжёлые узлы со складов. Три поста зоны ТР также обемспечены подъёмным краном. Так как ремонты узлов часто связаны со станочной обработкой различных деталей входящих в них то возле агрегатного участка размещаем слесарно-механический. Возле остальных постов ТР размещаем сварочно-медницкий электротехнический аккумуляторный и участок топливной аппаратуры. Для более удобного доступа к днищу автомобиля на сварочно-жестяницком участке устанавливаем рабочий пост с ямой. Данный участок размещаем в отдельном помещении изолируя его от остальных помещений несгораемыми стенками учитывая его повышенную пожароопасность.
Малярный участок также располагаем в отдельном помещении. На малярном участке располагаем склад лакокрасочных материалов. Малярный участок находится в удалении от сварочных зон и зон с открытым пламенем. Шиномонтажный участок располагаем смежно со складом резиновых покрышек что сокращает время на транспортировку покрышек.
Размещение постов ТО и ТР исключает возможность встречных и пересекающихся потоков. Это удобно и безопасно.
Для более удобного взаимодействия ремонтных рабочих специалистов и ИТР персонала предусмотрен подземный переход между производственным и административным корпусами возле въезда в зону ТО. Нет необходимости выходить и идти по улице особенно это комфортно в зимнее время года.
2.2 Разработка генерального плана АТП
Генеральный план предприятия – это план отведенного под застройку земельного участка территории ориентированный в отношении проездов общего пользования и соседних владений с указанием в нем зданий и сооружений по их габаритному очертанию площадки для безгаражного хранения подвижного состава основных и вспомогательных проездов и путей движения подвижного состава по территории.
Генеральные планы разрабатываются в соответствии со СНиП II-89-80 "Генеральные планы промышленных предприятий" и другими нормативными документами.
Определим площади основных зданий и сооружений размещаемых на территории АТП:
Производственный корпус
Административно-бытовой корпус
Fад.-быт. = а-б · N · К1 · К2 · К3 · К4 = 87 · 250 · 114 · 103 · 094 · 1 = 2400 м2
где а-б = 87 м2авт. – удельная норма площади административно-бытовых зданий [12] табл.5;
N = 336 авт. – списочный состав автомобилей;
К1 = 114 – коэффициент учитывающий количество подвижного состава [12] табл.7;
К2 = 103 – коэффициент учитывающий тип подвижного состава [12] табл. 8;
К3 = 094 – коэффициент учитывающий среднесуточный пробег;
К4 = 1 – коэффициент учитывающий категорию эксплуатации.
На стадии технико-экономического обоснования потребную площадь участка предприятия можно определить по формуле
Fуч = (Fпр + Fад.-быт. + Fх.) Kз = (3960 + 2400 + 16125) 05 = 44970 м2
где Кз = 05 – коэффициент плотности застройки территории.
При разработке генерального плана необходимо учесть следующее:
- ширина проезжей части наружных проездов должна быть не менее 3 м. при одностороннем и не менее 6 м при двустороннем движении;
- исходя из противопожарных требований ко всем зданиям предприятия должен обеспечен подъезд пожарных автомобилей с двух сторон;
- должно быть предусмотрено два выезда с территории;
- минимальное расстояние от края дороги до ограждения территории и открытых площадок не менее 15 м;
- минимальное расстояние от края дороги до наружной стены здания не менее 3 м.
Агрегатные работы включают разборочно-сборочные моечные диагностические регулировочные и контрольные операции по двигателю коробке передач рулевому управлению ведомым и ведущим мостам и другим агрегатам и узлам снятым с автомобилей для текущего ремонта.
После диагностики технического состояния агрегаты снятые с автомобиля для текущего ремонта подвергаются наружной мойке. Предварительно из картеров агрегатов сливают масло из тормозной системы - тормозную жидкость из системы охлаждения двигателя - воду и т. д.
После наружной мойки агрегаты (двигатель передний и задний мост коробку передач) устанавливают на стенды и полностью или частично разбирают.
Ступицы колес дифференциалы сцепления и другие узлы разбирают и собирают на приспособлениях устанавливаемых на верстаках. При установке агрегатов на стенды используют подъемно-транспортные устройства кран-балка тельфер.
Разборку агрегатов узлов и механизмов производят с использованием пресса для выпрессовки подшипников втулок и других деталей а также различных съемников и приспособлений.
Разобранные агрегаты обезжиривают в горячем содовом растворе с последующей промывкой в горячей воде. Для этой цели применяют ванны с содовым раствором и водой подогреваемые паром при помощи трубчатого змеевика или специальную моечную установку ГАРО. В этой установке детали моют горячим (плюс 80-90оС) 4-5-процентным раствором едкого натра или каустической соды. Моечная камера установки рассчитана для деталей размером 1000х600х800 мм общим весом до 250 кг. Продолжительность мойки - несколько минут.
Некоторые детали и системы подвергают дополнительной механической и химической обработке для удаления смол нагара накипи и других отложений. Это клапаны детали системы вентиляции картера двигателей детали системы охлаждения блоки и головки цилиндров канавки поршней система газораспределения. В соответствии с техническими условиями на контроль и деффектовку детали сортируют на годные негодные и требующие ремонта. С помощью мерительного инструмента и специальных приспособлений определяют отклонения в размерах и форме деталей сопоставляя детали с техническими условиями.
Предприятие работает в три смены работы текущего ремонта выполняются так же в три смены. Режим работы агрегатного участка принимаем в две смены в первую и вторую так как основной производственный процесс проводится именно в эти смены.
В агрегатном участке выполняются ремонтно-восстановительные работы которые по своему характеру не могут быть выполнены на постах текущего ремонта и технического обслуживания автомобилей. К ним относятся восстановление изношенных разрушенных или деформированных деталей механической обработкой а так же сваркой пайкой склеиванием холодной правкой и другими ремонтными воздействиями.
В процессе работы агрегатный участок взаимодействует с рядом других участков и складских помещений. На приведённой ниже схеме виден технологический процесс работы этих подразделений.
Текущий ремонт выполняется агрегатно-узловым методом т.е. путём замены неисправного узла или агрегата исправным заранее отремонтированным. Для этого в АТП создан оборотный фонд количество которого зависит от суточной потребности в запасных частях. В отличии от индивидуального агрегатно-узловой метод ремонта значительно сокращает простои автомобилей в ремонте.
Доставка запасных частей и материалов необходимых для выполнения работ на рабочие места выполняются децентрализованным способом доставки т.е. комплектуются и доставляются основными ремонтными рабочими.
Работы по ремонту и восстановлению агрегатов узлов и деталей производятся исполнителями в соответствии с указанием старшего мастера с учётом наличия оборотного фонда в промежуточном складе и складе запасных частей. Проверка полноты выполнения заявок на ремонт осуществляется бригадиром или мастером. Качество ремонта в процессе его выполнения и после окончания контролируется персоналом ОТК. При необходимости для этого используются контрольно-диагностические средства т.е. автомобиль может быть направлен на универсальный пост диагностики.
Рис. 2.1. Схема взаимодействия агрегатного участка и других подразделений производственного корпуса
На складе запасных частей размещаются новые запасные части и материалы. На складе агрегатов капитально отремонтированные агрегаты и узлы. На промежуточном складе организуется хранение оборотного фонда агрегатов узлов и обеспечения производства по сменам.
Пополнение запасов в промежуточном складе производится в течение суток по номенклатуре уровень которой ниже неснижаемого запаса. Режим работы промежуточного склада должен обеспечивать бесперебойную работу всех смен производства.
Новые запасные части и из склада запчастей могут поступать непосредственно в агрегатный участок или на промежуточный склад для пополнения оборотного фонда. Неисправные агрегаты и узлы снятые с автомобилей поступают на промежуточный склад где в обмен на них выдаются новые или отремонтированные. Возможно поступление снятых с автомобилей агрегатов непосредственно в агрегатный участок с прохождением документации через склад.
Дефектовку и выбраковку неисправных деталей и узлов проводит рабочий участка. Неисправные и не подлежащие восстановлению детали отправляются в металлолом.
Отремонтированные агрегаты и узлы из агрегатного участка могут поступать на посты ТР или для пополнения запасов на промежуточный склад или склад агрегатов.
В документообороте на агрегатном участке используются: накладные на получение со склада и сдачу на склад запасных частей узлов и агрегатов; требования на получение запасных частей; план производства ТО и ремонта.
Оплата труда механиков КТП производится согласно окладу по тарифной сетке для специалистов а также в виде премий от 25 до 100% от должностного оклада.
Агрегатный участок располагается рядом с зоной ТР по планировочным решениям он обеспечивается отдельной от зоны ТР кран-балкой. Рядом с агрегатным участком располагается склад агрегатов в котором хранятся отремонтированные агрегаты и узлы что позволяет сократить время и затраты на их транспортировку. Транспортировка тяжелых агрегатов в агрегатный склад и установка их на стеллажи осуществляется имеющимся в ведомстве складских помещений штабелером. Так же в непосредственной близости от агрегатного участка располагается склад запасных частей склад промежуточного хранения и ОГМ.
Планировка непосредственно самого агрегатного участка и расположение в нём оборудования заключается в следующем. На производственной площади участка находится изолированное помещение. Это зона холодной обкатки двигателей и КПП. Зона холодной обкатки двигателей располагается изолированно из-за повышенного шума связанного с этим процессом. Для более удобного перемещения и установки двигателей и КПП на стенды зона оборудована электро-тельфером грузоподъёмностью 15 т.
Оборудование расставлено по площади агрегатного участка исходя из требований ОНТП СНиП и рекомендации по научной организации труда (НОТ) - комплексу технических технологических организационных санитарно-гигиенических экономических и прочих мероприятий направленных на повышение производительности и улучшение условий труда.
При проектировании производственного помещения наряду с соблюдением технологии выполнения работ правил техники безопасности и прочего мы стремились к созданию такой планировки при которой технологическое оборудование и оснастка размещались так чтобы сократить до минимума непроизводительные потери времени на выполнение операций переходы от оборудования к оборудованию улучшить условия работы повысить качество и производительность труда.
Основные рабочие места в производственном помещении размещаются на наиболее освещённых и удобных для работы участках. Вблизи рабочих мест устанавливается наиболее часто используемое оборудование. Чем реже используется оборудование тем дальше от рабочего места оно располагается. Оснастка и инструмент на рабочем месте размещаются в соответствии с последовательностью выполнения технологических операций.
Конструкторская часть
В процессе эксплуатации автотранспорта приходится систематически сталкиваться с ремонтом ходовых частей автомобилей особенно с такими работами как съём ступиц с осей ступиц на передних и задних мостах для их ремонта или замены заменой подшипников ступиц. Особенно демонтаж затрудняется когда у ступицы переднего колеса сворачивается внутреннее кольцо конусного подшипника и разваливается обойма сепаратора подшипника. Вследствие этого разборка ступицы усложняется в несколько раз при стягивании ступицы с поворотного кулака необходимо приложить максимум усилий средств приспособлений что не дает должного эффекта. В большинстве ремонтных мастерских используется механические ручные съёмники работающие посредством резьбового соединения “винт – гайка”. Рычаг винта такого съёмника необходимо прокручивать вручную что требует не мало физических усилий механика в результате чего возможны растяжения и боль в суставах а также получения травматизма при резком срыве рычага или ключа с винта съёмника.
Снятие сложных конструктивных элементов должно выполняться согласно определенным условиям. Важным из них является сохранение первоначальной формы и отсутствие повреждений. Именно поэтому для выполнения этого типа работ следует использовать съемник гидравлический.
С помощью данного съёмника можно проводить работы по снятию таких конструктивных элементов:
- подшипники различной формы;
- ступиц с осей колёс;
Для данных видов работ проведём подбор методом ранжирования наиболее оптимальной модели гидравлического съёмника из 4-х различных моделей.
Рис. 4.1 Съёмник гидравлический мод. MASTAK
Съемник гидравлический мод. MASTAK с выносным насосом предназначен для демонтажа подшипников шкивов втулок и других деталей имеющих посадку с натягом. Съемник обхватывает изделие тремя лапами-захватами. Непосредственно выпрессовывание осуществляет гидравлический поршень движение которого приводит механик путем воздействия на рукоять управления выносного насоса закачивая масло в полость поршня. Сброс давления осуществляется выкручиванием перепускного винта.
Рис. 4.2 Съёмник гидравлический с силовым винтом мод. СГ10П
Съемник гидравлический мод. СГ10П предназначен для демонтажа подшипников шкивов втулок и других деталей имеющих посадку с натягом. Съемник обхватывает изделие тремя лапами-захватами. Непосредственно выпрессовывание осуществляет гидравлический поршень движение которого приводит механик путем вкручивания штока поршня в резьбовом отверстии упорной платформы на которую крепятся захваты.
Сброс давления осуществляется выкручиванием штока поршня.
Рис. 4.3 Съёмник гидравлический мод. СГА8
Съемник гидравлический мод. СГА8 с встроенным насосом предназначен для демонтажа подшипников шкивов втулок и других деталей имеющих посадку с натягом. Съемник обхватывает изделие тремя лапами-захватами. Непосредственно выпрессовывание осуществляет гидравлический поршень движение которого приводит механик путем воздействия на рукоять управления встроенного насоса закачивая масло в полость поршня. Сброс давления осуществляется выкручиванием перепускного винта.
Рис. 4.4 Съёмник гидравлический мод. СГ38
Съемник гидравлический мод. СГ38 с встроенным насосом предназначен для демонтажа подшипников шкивов втулок и других деталей имеющих посадку с натягом. Принцип действия данного съёмника аналогичен как у съёмника мод. СГА8.
Таблица 3.1 Параметры съёмников
Максимальный внешний диаметр захвата мм
Для выбора конкретной модели съёмника был применён метод априорного ранжирования. Для этой цели выделили наиболее значимые факторы влияющие на конечный выбор оборудования:
) Стоимость съёмника;
) Удобство использования съёмника;
Для определения значимости факторов был произведён опрос экспертов. Им было предложено расставить ранги или просто значимость факторов.
В данной таблице цифра один обозначает наиболее значимый фактор по мнению эксперта цифра четыре – наихудший.
Для значимости факторов были опрошены 7 экспертов.
Удобство использования
S - сумма рангов расставленных экспертами по строке. По результатам этого столбца рассчитывается средняя сумма рангов равная 175;
D- разность между суммой рангов в данной строке и средним значением;
D2- квадрат разности между суммой рангов в данной строке и средним значением. По результатам данного столбца рассчитывается итоговая сумма квадратов разностей (145);
L - место занятое данным фактором;
qli - удельный вес данного фактора.
L - место занятое фактором в результате ранговой оценки;
Проверка согласованности мнений экспертов производится с помощью коэффициента конкордации рассчитываемого по формуле:
m- количество экспертов;
k- количество факторов.
Мнение экспертов считаются согласованными при коэффициенте конкордации большем 0558. Таким образом для рассматриваемого случая мнения экспертов согласованы.
p = 0592·7·(4 – 1)=1243
Хтабл2 =1243 (Методические указания по выполнению курсового проекта по дисциплине "Механизмы и приспособления для ремонта АМТС")
Расчетное значение критерия Пирсона больше табличного (1243>1134) это свидетельствует о не случайности совпадения мнений экспертов которое отображено втабл. 2 (Методические указания по выполнению курсового проекта по дисциплине "Механизмы и приспособления для ремонта АМТС") при числе степеней свободы ( k-1) = 3 и принятом уровне значимости q = 1 %.
В соответствии с табл.3.2. имеем ранжирование факторов по значимости:
) Удобство в использовании;
Таблица 3.3 Экспертная оценка удобства использования
Средняя сумма рангов равная 175;
D2- квадрат разности между суммой рангов в данной строке и средним значением. По результатам данного столбца рассчитывается итоговая сумма квадратов разностей (165);
Мнение экспертов считаются согласованными при коэффициенте конкордации большем 0558. Таким образом для рассматриваемого случая мнения экспертов согласованы
p = 0558·7·(4 – 1)=1172
Хтабл2 =1172 (Методические указания по выполнению курсового проекта по дисциплине "Механизмы и приспособления для ремонта АМТС")
Расчетное значение критерия Пирсона больше табличного (1172>1134) это свидетельствует о не случайности совпадения мнений экспертов которое отображено втабл. 2 (Методические указания по выполнению курсового проекта по дисциплине "Механизмы и приспособления для ремонта АМТС") при числе степеней свободы ( k-1) = 3 и принятом уровне значимости q = 1 %.
6. Выбор конкретной модели съёмника.
Для выбора конкретной модели съёмника провели опрос экспертов. Перед проведением опроса экспертам было предложено ознакомиться с техническими характеристиками отобранных моделей съёмников. Как и в предыдущем опросе экспертам было предложено поставить оценку по пятибалльной шкале для каждой из выбранных моделей съёмников отдельно по каждому критерию. Цифра один обозначает наивысшую оценку данного фактора экспертом четыре - наихудшую. Для занесения оценок каждому эксперту были выданы карточки в количестве семи штук отдельно по каждой из предложенных моделей.
Для выбранных моделей съёмников по каждому критерию в отдельности была рассчитана средняя оценка по следующей методике: из 7-ми чисел (оценки экспертов по одному из факторов какой-либо модели съёмника от одного до четырех) были отброшены высшая (или одна из высших) и низшая (или одна из низших) оценки. По остальным оценкам была найдена средняя арифметическая. Полученные данные были сведены в таблицу 3.4.
В качестве слагаемых совокупных средневзвешенных оценок моделей следует использовать относительные значения оценочных показателей вычисляемых следующим образом:
где: - наихудшее значение
- наилучшее значение i-го показателя по совокупности подобранных моделей.
Таким образом суммарная совокупная средневзвешенная оценка конкретной модели будет вычисляться:
Таблица 3.4 Выбор модели по суммарной средневзвешенной оценке
Значения показателей по моделям оборудования (i)
Максимальная величина сумм критериев Вj = 0871 у съёмника мод. СГА8. Следовательно данная модель обладает самым оптимальным набором параметров. Чертёж выбора съёмника представлен на листе № 5.
Итог: Агрегатный участок решено оборудовать гидравлическим съёмником СГА8 для сборочно-разборочных работ.
Таблица 3.5 Технические характеристики съёмника СГА8
Подготовка съемника к работе:
- Перед работой следует проверить все детали съемника на наличие повреждений. При обнаружении деформаций трещин и признаков сильного износа на деталях съемника использование съемника запрещено.
- Максимально точная оценка усилия требуемого для снятия детали с вала очень важна. Если усилия съемника недостаточно для снятия детали – не используйте его выберите модель съем- ника с подходящими характеристиками.
- Рабочая температура съемника СГ-5 находится в диапазоне от -5 до +45°C.
В лапах съемника имеются отверстия для соединения с серьгами. На конце штока расположен жестко закрепленный центрирующий конус. Лапы съемника накидываются на снимаемую деталь. Гидроцилиндр съемника с регулировочной резьбой ввинчивается в гайку с закрепленными на ней лапами пока шток не упрется в вал со снимаемой деталью. Коническая насадка штока должна встать в центровочное отверстие вала. Для ослабления упора необходимо открутить перепускной винт. С помощью рукоятки масло из бака нагнетается в гидроцилиндр при этом шток упирается в торец вала и снимаемая деталь начинает перемещаться. В процессе съема детали необ- ходимо следить за положением рабочих площадок лап съемника относительно детали для избе- гания срыва лап с детали.
Технология восстановления детали
В качестве ремонтируемой детали в данном дипломном проекте рассмотрен корпус водяного насоса автомобиля МАЗ-534019. Данный корпус выполнен литьём из серого чугуна марки СЧ 15-32 с последующей станочной обработкой под установку подшипников манжет крышек и присоединительных патрубков.
Узел в который входит ремонтируемая деталь является одним из главных элементов системы охлаждения двигателя – насос центробежного типа (рис.4.1).
Рис. 4.1. Общий вид водяного насоса
– сальник; 2 – корпус насоса; 3 - втулка; 4 – шпилька крепления подводящего патрубка; 5 – стопорное кольцо сальника; 6 – упорное кольцо сальника; 7 – пружина сальника; 8 – манжета сальника; 9 - крыльчатка; 10 - крышка; 11 - валик; 12 - гайка; 13 – стопорная шайба; 14 – перепускной ниппель трубки водных термостатов; 15 16 - шарикоподшипники; 17 - прокладка; 18 – корпус сальника; 19 – втулка сальника; 20 – гайка крепления боковины шкива; 21 – замковая шайба; 22 - гайка; 23 – ступица шкива; 24 – боковина шкива; 25 – регулировочные прокладки; 26 пресс-маслёнка.
При работающем двигателе насос создаёт циркуляцию охлаждающей жидкости он забирает её из нижнего бачка радиатора и нагнетает в правую и левую водяные рубашки блока цилиндров.
Жидкость омывает наружную поверхность гильз цилиндров поглощая при этом тепло нагревается затем из блока цилиндров поступает в водяные рубашки головок цилиндров к нагревающимся местам. Из рубашек охлаждения головок цилиндров жидкость поступает в водосборные трубопроводы а из них через проходы
в термостатах в радиатор где охлаждается потоком воздуха который создаёт вентилятор. Охлажденная в радиаторе жидкость вновь поступает к водяному насосу.
2. Обоснование необходимости разработки технологического процесса
восстановления детали
Износ различных деталей двигателя при эксплуатации автомобиля неодинаков. Норма пробега двигателя в целом - 400 тыс. км. Соответственно износ самих деталей в разных местах тоже различен. Так например при работе двигателя в камере сгорания повышается температура и если двигатель не охлаждать то будет повышаться температура что пагубно отразиться на ресурсе двигателя. Так на пример при работе водяного насоса в его корпусе наиболее подвержены механическому износу посадочные диаметры под подшипники так как они испытывают ударные динамические нагрузки. Данный дефект вполне устраним в производственных условиях АТП поэтому менять корпус насоса или сам насос не целесообразно. Следовательно на каждом конкретном предприятии исходя из возможностей АТП должен быть разработан технологический процесс ремонта частей агрегатов узлов деталей автомобилей с учетом экономической эффективности. АТП данного дипломного проекта состоит из 30 технологически совместимых по ремонту и обслуживанию грузовых автомобилей поэтому достаточно эффективно и экономически выгодно производить значительный объём по ремонту деталей в собственных мастерских. Исключение составляет ремонт деталей требующих особо дорогостоящего технологического оборудования (например восстановление подшипников и т.п.).
В результате дефектации были выявлены следующие несоответствия:
- износ отверстия под наружное кольцо внешнего подшипника;
- износ отверстия под наружное кольцо внутреннего подшипника;
- износ резьбового отверстия под шпильку крепления подводящего патрубка.
Учитывая свойство материала детали качество рабочих поверхностей конструкцию принимаем что для восстановления работоспособности детали можно расточить прослабленные диаметры и по жёсткой посадке установить ремонтные втулки (рис. 4.2) с последующей доработкой до требуемых размеров. Материал для втулок допускается взять из материала корпуса (чугуна СЧ 15-32) либо из стали с таким же коэффициентом расширения и с такой же прочностной характеристикой (выберем сталь 35). Для восстановления резьбового М10 его необходимо рассверлить до диаметра 1437 мм затем нарезать резьбу М16х15. Стальную резьбовую втулку с внешним диаметром М16х15 и с внутренним М10 рациональней купить в магазине а не изготавливать на АТП так как она стандартизированная (ОСТ 4. ГО. 822. 009). Для большей прочности необходимо установить данную втулку в корпус на клей для металлов (выберем клей марки Д-9).
Рис. 4.2. Схема технологических втулок
По справочнику инженера-конструктора выберем посадки запрессовки втулок в ступицу Н8p7 это посадка с натягом и используется для соединений без дополнительного крепежа. Для впрессовки втулок в ступицу по этой посадке необходимо втулки охладить в морозильной камере холодильника и без дополнительного усилия пресса постукиванием молотка по торцевой части втулок установить их в расточенные отверстия. Для большей лёгкости установки допускается нагреть корпус насоса в масле до температуры 85-90ºС.
Весь техпроцесс состоит состоит из следующих видов работ:
- токарной сверлильной и резьбонарезной обработок корпуса;
- изготовления ремонтных втулок из прокатного прутка стали 35 токарной обработкой;
- установкой втулок в корпус;
- растачивание втулок в корпусе;
Более подробно рассчитаем и пронормируем технологический процесс механообработки корпуса:
Операция 005 – Расточная:
Оборудование: координатно-расточной станок 2431СФ10.
Приспособление: оправка.
Инструмент: резец расточной материал режущей кромки Т15К6.
-Расточить внутренние подшипниковые диаметры в размеры 51+0046 мм и 46+0039 мм.
глубина резания: t = 06 мм
назначаем подачу: SO = 03 ммоб
период стойкости резца: Т = 60 мин
KV – произведение коэффициентов.
KV = KMV KПV KИV = 1* 08 * 1 = 08
KMV – коэффициент учитывающий влияние материала заготовки.
KПV - коэффициент учитывающий состояние поверхности
KИV - коэффициент учитывающий влияние материала инструмента
Частота вращения шпинделя:
Корректируем частоту вращения шпинделя по паспортным данным
станка: nст = 650 обмин
Тогда действительная скорость резания равна:
Определяем главную составляющую силы резания:
PZ = 10 CP tx Sy Vn KP
KP – произведение ряда коэффициентов учитывающих
фактические условия резания.
KP = КМР KjP KgP KlP
KP = 074*094*1*1 = 069
PZ = 10 * 300 * 11 * 06075 * 104-015 * 069 = 560 Н
Мощность затрачиваемая на резанье:
Sм – минутная подача;
Т0 = 100·4195=206 мин
Вспомогательное время:
Туст – время на установку заготовки;
Тконтр – время на контроль и выставку инструмента.
Значения берем из справочника нормировщика
Время на обслуживание рабочего места:
Время на отдых и естественные надобности:
Операция 010 – Сверлильная:
Оборудование: вертикально - сверлильный станок 2А 135.
Приспособление: зажимные тиски.
Инструмент: сверло 1437 Т15К6 метчик Т15К6 М16х15.
- рассверлить резьбовое отверстие до диаметра 1437 мм;
- нарезать резьбу М16х15;
Режимы резания для рассверливания:
а) глубина резания: t = 22 мм.
б) назначаем подачу: So = 005 ммоб.
в) период стойкости сверла: Т = 60 мин.
Частота вращения сверла:
Корректируем частоту вращения шпинделя по паспортным данным станка: nст = 760 обмин;
Режимы резания для нарезания резьбы:
а) глубина резания: t = 09 мм.
б) назначаем подачу: So = 002 ммоб.
Корректируем частоту вращения шпинделя по паспортным данным станка: nст = 350 обмин;
Основное машинное время для рассверливания:
для резьбонарезания:
tоп = 079 + 429 + 2 = 708 мин.
tшт = 708 + 042 + 042 = 792 мин.
Операция 020 – Расточная:
-Расточить диаметры ремонтных втулок в размеры 47+0018 мм и 40+0018 мм.
Так как длины рабочих ходов инструмента глубины резаний и диаметры растачиваемых отверстий близко схожи с теми что в операции 005 то все режимы резания и нормированное время принимаем как в расточной операции 005.
5. Маршрутная карта ремонта корпуса водяного насоса автомобиля МАЗ-534019
Корпус водяного насоса
Код единицы величины
Наименование и содержание операции
Оборудование (наименование)
Приспособлениеи инструмент (наименование)
Кол.одн. обраб. дет.
Объемпроизвод. партии
Расточить внутренние подшипниковые диаметры в размеры 51+0046 мм и 46+0039 мм.
Координатно-расточной станок 2431СФ10
Резец расточной планшайба
Рассверлить резьбовое отверстие до диаметра 1437 мм нарезать в нём резьбу М16х15.
Вертикально-сверлильный станок 2А 135
Тиски зажимные сверло 1437 метчик М16х15
Маршрутная карта ремонта корпуса (продолжение)
Приспособление и инструмент (наименование)
Объемпроизв од.партии
Установить в расточенные отверстия две ремонтных втулки.
Слесарный стол пресс ручной
Расточить диаметры ремонтных втулок в размеры 47+0018 мм и 40+0018 мм.
Проверить ремонтные размеры на соответствие требуемым.
Штангенциркуль нутромер набор калибров
Карта дефектации корпуса водяного насоса
Наименование дефекта
Измеренные параметры мм
Предельные допустимые параметры без ремонта мм
Наименование средств контроля или способ установления дефекта
Код средств контроля
Заключение по дефекту
Профессия исполнителя
Износ отверстия под наружное кольцо наружного подшипника
Нутромер НИ 50-100 ГОСТ 868-72
Расточить установить ремонтные втулки с последующей расточкой
Токарь фре-зеровщик механик-сборщик
Износ отверстия под наружное кольцо внутреннего подшипника
Износ резьбового отверстия под шпильку крепления патрубка
Непроходной калибр ГОСТ 2015-69
Рассверлить нарезать резьбу установить на клей втулку
ВЕДОМОСТЬ ОБОРУДОВАНИЯ
РАЗРАБОТЧИК ПОСТАВЩИК
Вертикально - сверлильный станок
Координатно-расточной станок
Наименование приспособления и инструмента
Код приспособления и инструмента
НИ 50-100 ГОСТ 868-72
Ключи гаечные кольцевые 10 12 19
Молоток слесарный стальной
Резец расточной Т15К6
Безопасность и экологичность проектных решений
Объект анализа является агрегатный участок. В процессе выполнения производственной деятельности работающие на агрегатном участке могут подвергаться воздействию опасных и вредных факторов могущих привести к травматизму или профзаболеванию. Кроме того производственная деятельность АТП оказывает негативное воздействие на окружающую среду.
2 Анализ потенциальной опасности АТП для персонала и окружающей среды
Анализ потенциально опасных и вредных производственных факторов в агрегатном участке: на агрегатном участке постоянно или периодически действуют опасные и вредные производственные факторы которые согласно ГОСТ 12.0.003-74(99)80 подразделяются на физические химические биологические и психофизиологические. Наиболее характерные для диагностического участка факторы приведены в таблице 5.1.
Таблица 5.1 - Вредные и опасные факторы на агрегатном участке
Наименование факторов
Нормативный документ
Возможные последствия
Повышенное значение напряжения цепи замыкание которой может произойти через тело человека.
Зона электроустановки
ГОСТ 12.1.004-91 при длительном воздействии ( более 10 сек.) в аварийном режиме
Подвижные части производственного оборудования
Стенды тельфер и др.
Повышенная загазованность воздуха
ГОСТ 12.1.005-88 ПДК
Повышенная или пониженная температура и подвижность воздуха в рабочей зоне
ГОСТ 12.1.005-88 Оперативные параметры микроклимата
Перегрев или переохлаждение организма
Нерациональная освещенность рабочей поверхности
Утомляемость травматизм
Взрывоопасные концентрации паров горючей жидкости
Твердо горючие вещества и материалы
паромасляная. ветошь
Повышенное давление воздуха в сосудах и трубопроводах
Основным источником загрязнения воздушного бассейна при эксплуатации являются двигатели внутреннего сгорания которые загрязняют атмосферу вредными веществами выбрасываемыми с отработавшими газами картерными газами и топливными испарениями. В таблице 5.2 приведены данные по составу отработавших газов ( с сокращениями) обладающих большей токсичностью.
Таблица 5.2 - Состав отработанных газов двигателя внутреннего сгорания
Пределы концентраций компонентов В ОГ
Бензиновый двигатель в %
Дизельный двигатель в %
Загрязнение сточных вод АТП происходит в основном при мойке автомобилей их узлов и деталей при ремонте и заправке аккумуляторов ремонте системы охлаждения механической обработке металлов. К наиболее типичным видам загрязнения сточных вод относятся нефтепродукты щелочи кислоты смазочно-охлаждающая жидкость антифриз грязевые сборы частицы металла.
Основными причинами возникновения взрывов и пожаров на АТП являются:
неосторожное обращение с огнем нарушение правил пожарной безопасности при сварочных и других огневых работах нарушение правил эксплуатации электрооборудования неисправности отопительных приборов нарушение правил пожарной безопасности при аккумуляторных работах самовозгорание промасленных обтирочных материалов статическое электричество применение легковоспламеняющихся и горючих жидкостей для мойки двигателя взрыв сосудов работающих под давлением.
Кроме того причинами взрывов и пожаров может явиться атмосферное электричество при неисправной системе молниезащиты.
5 Характеристика производственной среды производственного здания
Данные характеризующие агрегатный участок определенные по действующим нормативным документам предоставлены в таблице 5.3.
Таблица 5.3 - Характеристика агрегатного участка
Категория по взрыво и пожаробезопасности
Степень огнестойкости зданий и сооружений
СНиП 2.01.02 - 85(3)
Класс помещения в зависимости от окружающей среды
Класс помещения по степени опасности поражения электрическим током
с повышенной опасностью
Класс взрывоопасной зоны
Класс противопожарной зоны
Группа производственного процесса по санитарной характеристике
Санитарный класс пр-ва и ширина защитной зоны
Для очистки ливневых сточных вод применены очистные сооружения с двумя вертикальными грязевыми отстойниками с фильтром доочистки бензо масло уловителями с одним вертикальным осветителем и масло сборной ёмкостью.
Внутренний диаметр железобетонных труб из которых изготовлены грязеотстойники и осветитель составляют 2000мм а высотой 2200 мм.
Для очистки производственных сточных вод от нефтепродуктов и взвешенных частиц применена палильная установка «Кристалл» позволяющая многократно использовать очищенную воду для технических нужд АТП. Принцип действия установки основан на последовательной фильтрации загрязненной воды сначала через фильтры грубой очистки а затем через фильтры тонкой очистки.
Таблица 5.4 - Данные по ПДК загрязнения сточных вод согласно СанНиП 4946-89
Нефть и нефтепродукты
Воздух выбрасываемый из системы вытяжной обще обменной вентиляцией проходит сначала грубую очистку в центробежном циклоне а затем более тонкую очистку в рукавных фильтрах.
Концентрация вредных веществ в выбрасываемом воздухе не превышает нормативных значений приведенных в таблице 5.5.
Таблица 5.5 - Допускаемые значения ПДК
ПДК мгкуб.м. средне-доп.
На проектируемой станции технического обслуживания для очистки сточных вод используется установка очистки сточных вод по замкнутому циклу «Кристалл». Определим параметры нефтеловушки предназначенной для удаления нефтепродуктов жиров и других нерастворимых в воде веществ.
Взвешенные вещества 2500 - 7 10
Нефтепродукт 1200 – 3 5
Установка «Вихрь» - очищение образующихся отходов.
Наружные сети и сооружения водоснабжения и канализации СНиП 3.05.04-90
В соответствии со СНиП принимаем:
- глубину проточной части Н=2 м;
- отношение длины к глубине - 15;
- ширину секции - 4 м;
- число секций - 2;
- среднюю гидравлическую крупность взвешенных частиц Uo=6 ммс;
- среднюю скорость течения воды в проточной части w=4 ммс.
Средний расход сточных вод –
Qср=600 м3сут=25м3ч=0417м3с1м3мин.
Коэффициент часовой неравномерности Кч=12.
Начальное содержание нефтепродуктов в воде С1=150 мгл.
Содержание нефтепродуктов в очищенной воде
C2=60 мгл=Слимит (Сн=ДКв=03мгл=300мгм3).
Максимальный секундный расход воды на нефтеловушку
Qc=QcpKч24·3600=600·1286400=007 м3c.
Эффект очистки воды от нефтепродуктов
Э=(C1-C2) 100C1=(150-60)·100150=60%.
В=Qс(nНw)=007(2·2·0004)=083 м.
А=Нw(К1Uo)=(2·0004)(05·0006)=134 м.
Масса уловленной нефти за сутки:
G = C1ЭK2Qcp106 = 150·06·1·6001000000=0047 тсут.
8 Расчетная часть безопасности труда
8.1 Расчет искусственного освещения агрегатного участка
Площадь участка составляет - 78 м2.
Общая высота помещения – 6 м.
В целях ограничения освещения от светильников общего назначения подвеску их надо производить над уровнем пола не менее 5 м при мощности 200 Вт.
Высота подъема светильников над освещаемой поверхностью:
гдеН - общая высота помещения ;
hp = 08 м - высота от пола до освещаемой поверхности;
hc= 03 м - высота от потолка до нижней части светильников
h= 6 - 08 - 03 = 49 м;
Расстояние между светильниками:
гдеl = 15 при прямоугольном расположении светильников.
Рисунок 5.1 Схема расположения светильников
Индекс помещения определяют по выражению:
i = E (h × (A + B)) = 200 (49 × (144 + 83)) = 18
где А и В длина и ширина помещения.
По индексу помещения определяю значение коэффициента использования светового потока h = 048
Количество светильников определяют по выражению:
Nс =(E × S × Z × k) (Фл × nл × h)
где Е = 200 лм - номинальная нормативная освещенность;
S – площадь участка;
Фл = 4250 лм - световой поток светильника ЛВПОЧ - 2 х 40 Д 64 - 01С люминесцентными лампами ЛД - 80 - 4 ;
Z = 11 - коэффициент неравномерности освещенности;
k =17 - коэффициент неравномерности освещенности ;
nл = 4 - число ламп в светильнике.
Nс = (200 × 78 × 11 × 17) (4250 × 4 ×048) = 33.
Принимаем 4 светильника.
Мощность лампы на м2 площади помещения составляет:
W = p × Nc × nл S = 80 × 3 × 4 73 = 13 Втм2 освещённость в норме.
p – мощность одной лампочки в светильнике (80 Вт);
9 Мероприятия и средства по обеспечению безопасности в чрезвычайных ситуациях
Взрыво и пожаробезопасность агрегатного участка обеспечивается организационно техническими мероприятиями и мерами противопожарной безопасности.
Здание участка имеет несгораемые стены перегородки и покрытия с пределом огнестойкости 075 - 2 час.
На участке запрещается курить пользоваться открытым огнем. Не допускается разлив масла и топлива в случае разлива производится тщательная уборка . Использованный обтирочный материал убирается в металлические ящики с крышками по оканчании работы обтирочный материал выносится в пожаробезопасное место.
Охранно-пожарная сигнализация на агрегатном участке осуществляется при помощи телефонной связи и электрической пожарной сигнализации (Э.П.С.) автоматического действия. В качестве тепловых извещателей применена конструкция датчика АТИМ - 3 срабатывающего при температуре окружающего воздуха 60; 80 или 100°С. Для ликвидации загорания на участке предусмотрены следующие средства пожаротушения (ППБ 01-03):
огнетушители ОУ-5 в количестве 2 штуки;
огнетушители ОВП-10 в количестве 1 штука (по норме 1на 100 м2);
ящик с песком 05 м3;
АТП находится в средней полосе РФ для которой характерна среднегодовая продолжительность гроз около 204 ч.Для разработки мероприятий по молниезащите АТП выбирают тип зоны и категории устройств молниезащиты которые приведены в таблице 5.6.
Таблица 5.6 - Типы зон и категории молниезащиты
Категория молниезащиты
Здания и сооружения с производственными помещениями в которых по ППБ 01-03.
В местах со средней грозовой деятельностью 20 час в году .
Для зданий и сооружений III степени огнестойкости при необходимой молниезащите 002 N 2 зона
Здания и сооружения II категории молниезащиты защищены от прямых ударов молний через наземные металлические коммуникации. Для молниезащиты АТП выбирается двойной стержневой молниеотвод высотой до 15 м.
Выводы: предложенные в проекте мероприятия по охране труда и защите окружающей среды позволяют сделать вывод о том что проектируемая станция технического обслуживания отвечает требованиям безопасности и экологичности предусмотренным для предприятий автомобильного транспорта.
Организационно-экономическая часть
1. Организационный раздел
1.1. Организационно-правовая форма собственности предприятия
Принимаем организационную форму предприятия на первом этапе его развития – акционерное общество закрытого типа (частные инвестиции). Предварительная оценка рынка показывает что потребность в таком предприятия есть. Потому форма предприятия в виде закрытого акционерного общества позволяет на первом этапе развития предприятия более гибко и быстро принимать различные организационные решения так как основные решения принимает небольшое количество людей.
В дальнейшем если работа предприятия будет успешной и оно будет расширяться то его можно преобразовать в акционерное общество открытого типа и получить таким образом дополнительное финансирование на развитие предприятия выпустив акции предприятия в свободную продажу.
1.2. Организационная структура предприятия
Организационная структура предприятия принимается упрощенная. Она приведена на рис. 6.1.Расчет штатного расписания АТП проводим методом укрупненного нормирования. Численность руководителей специалистов и служащих принимаем в размере 8 11% от общей численности рабочих. Численность вспомогательных рабочих принимаем в размере 10 25% от численности ремонтных рабочих. Штатное расписание предприятия дано в таблице 6.4.
Рис. 6.1 Схема организационной структуры АТП
Перечень должностных обязанностей руководителей основных структур АТП
Планирование и организация бухгалтерского учета.
Контроль за состоянием расчетов с предприятиями организациями учреждениями и лицами а также сохранность денежных средств и товарно-материальных ценностей.
Контроль за рациональным и экономным использованием материальных трудовых и финансовых ресурсов организации.
Формирование в соответствии с действующем законодательством и нормативно-правовыми актами о бухгалтерском учете учетной политики исходя из структуры и особенностей деятельности организации.
Проведение инвентаризации денежных средств товарно-материальных ценностей расчетов с организациями.
Проведение совместно со структурными подразделениями организации экономического анализа хозяйственно-финансовой деятельности по данным бухгалтерского учета в целях выявления внутрихозяйственных резервов предупреждение потерь и непроизводственных расходов.
Составление баланса и оперативных сводных отчетов о доходах и расходах средств об использовании бюджета другой бухгалтерской и статистической отчетности представление их в установленном порядке в соответствующие органы.
Руководство всем производственным процессом обеспечения подвижного состава комплексом работ по ТО и ТР.
Корректировка технической документации получаемой предприятием со стороны применительно к конкретным условиям.
Разработка технических условий на проектирование изготовление и поставку стендов собственной разработки.
Рассмотрение и принятие решений по техническим вопросам возникающим в процессе ремонта автомобилей выдача разрешений на изменение чертежей.
Планирование производственного процесса ЕО и ТО и ТР.
Организация бесперебойного обеспечения АТП запчастями и технологическим оборудованием.
Начальник ремонтного производства:
Руководство производственным процессом работ по ЕО и ТО и ТР.
Начальник производственно-технического отдела:
Разрабатывает планы по внедрению новой техники и технологий.
Разрабатывает и проводит мероприятия по охране труда и технике безопасности.
Осуществляет работы по составлению технических нормативов и технической документации.
Осуществляет содержание в технически исправном состоянии зданий сооружений энергосилового и санитарно-технического хозяйства.
Обслуживание и ремонт технологического оборудования производства
Обеспечивает бесперебойное материально-техническое снабжение АТП.
Организует правильную работу складского хозяйства.
Осуществляет контроль качества работ на производстве.
Осуществляет контроль качества услуг АТП.
Осуществляет контроль состояния подвижного состава и технологического оборудования.
Зам. Гендиректора по эксплуатации:
Организует и руководит всей работой подвижного состава на линии.
Организует планирование работ подвижного состава
Начальник отдела эксплуатации:
Обеспечивает организацию работ подвижного состава и планирование грузовых перевозок
Руководитель группы организации перевозок
Обеспечивает организацию работ подвижного состава на линии непосредственно руководит перевозками грузов.
Выпускает автомобили на линию контролирует выездную документацию распределяет грузовые потоки.
Руководитель группы анализа перевозов:
Организует анализ состояния грузовых перевозок и разрабатывает планы повышения их эффективности.
Организует и контролирует мероприятия по безопасности движения подвижного состава.
Зам. Гендиректора по экономике:
Организует работу по разработке финансово-экономических планов предприятия. Анализирует экономические показатели предприятия и разрабатывает планы по их улучшению.
Начальник планово-экономического отдела:
Разрабатывает экономические планы развития предприятия контролирует текущее состояние финансово-экономической деятельности
Начальник отдела труда и заработной платы:
Организует работу по начислению и контролю заработной платы работников предприятия
Начальник отдела кадров:
Организует работу отдела кадров ведет учет всего работающего персонала предприятия
Начальник административно-хозяйственного отдела:
Решает социальные и хозяйственные вопросы на предприятии.
Руководит всеми вспомогательными службами в части хозяйственного обслуживания подразделений предприятия.
2. Экономический раздел
Таблица 6.1 Исходные технико-эксплуатационные показатели использования автотранспортных средств АТП
2.1. Расчет стоимости основных производственных фондов
Расчет стоимости основных производственных фондов АТП производится последующим группам: здания и сооружения; дорогостоящие инвентарь и приспособления; оборудование и рабочие машины; автотранспортные средства.
Стоимость зданий и сооружений
Стоимость зданий и сооружений определяется по формуле:
где Цз – общая стоимость здания руб м3;
цз – стоимость одного м3 здания руб м3;
Vз – объем здания м3;
Стоимость открытой стоянки и затраты на благоустройство незастроенной территории определяется по формуле:
где цс – стоимость одного м2 открытой стоянки или благоустройства территории рубм2;
Sо – площадь открытой стоянки или благоустройства территории м2.
Затраты на проектно–изыскательские работы (привязка к местности) принимаем в размере 15% от стоимости зданий и сооружений.
Стоимость дорогостоящего инструмента и приспособлений следует принимаем в размере 24% от стоимости зданий и сооружений.
Стоимость оборудования и рабочих машин определяется в размере 2030% для грузовых от стоимости зданий и сооружений.
Для средних условий эксплуатации стоимость грузового АТС составляет 6070 от стоимости всех основных фондов производственного назначения.
Балансовая стоимость Цаб парка АТС рассчитывается на основании среднесписочного количества АТС их оптовой цены и добавленной стоимости на доставку и приобретение по формуле:
где Ца – оптовая цена данной модели АТС руб.;
Кт – коэффициент учитывающий затраты на доставку и постановку на учет АТС (Кт=106108);
Кн - коэффициент учитывающий налог на приобретение АТС (Кн=11).
Определим балансовую стоимость АТС:
Цаб = Ца · Кт · Кн · Nавт = 1800000 · 105 · 11 · 250 = 519750 тыс. руб.
Результаты расчета стоимости основных фондов (ОФ) приведены в таблице 6.2.
Балансовая стоимость основных фондов создается за счет капитальных вложений. Источником финансирования капитальных вложений являются собственный капитал включая амортизационные отчисления бюджетные ассигнования и банковский кредит.
Таблица 6.2 Стоимость основных фондов АТП
Виды основных фондов
Общая площадь здания м2
Удельная стоимость рубм3 или рубм2
Балансовая стоимость единицы ОФ тыс. руб.
Благоустройство незастроенной территории
Привязка к местности (15% от суммы п.п.1-5)
Итого по зданиям и сооружениям (п.п.1-6)
Дорогостоящие инструменты приспособления и инвентарь (2 4% от п.7)
Оборудование и рабочие машины (30% от п.7)
Всего ОФ без АТС (п.7+п.8+п.9)
Автотранспортные средства
Всего ОФ (п.10+п.11)
2.2. Расчёт потребности АТП в материальных затратах
Расчет материальных затрат на выполнение прогнозируемого объема перевозок проводится в натуральном и стоимостном выражении по следующим группам: автомобильное топливо смазочные материалы керосин для технологических нужд обтирочные материалы прочие эксплуатационные материалы ремонтные материалы и запасные части восстановление износа и ремонт шин. Расчет ведем за год.
Объемный расход автомобильного топлива для АТС работа которых учитывается в тонно-километрах определим по формуле:
Gл = 001 · (Нл + Hткм · q · ·) · Kз · Kд · Kг · Lобщ = 001 · (23 + 13 · 83 · 06 · 0437 ) · 1042 · 085 · 1005 · 13362050 = 3072103 л
где Нл = 23 л100км – норма расхода топлива на пробег;
Нткм = 13 л100 км – норма расхода топлива на транспортную работу;
q = 83 т – грузоподъемность автомобиля;
К3 = 1042 – коэффициент учитывающий расход топлива в зимний период (три зимних месяца);
Kд = 085 - коэффициент учитывающий дорожные условия (для внегородских дорог с усовершенствованным покрытием;
Кг = 1005 – коэффициент учитывающий расход топлива на внутри гаражные нужды;
Lобщ = 13362050 км – общий пробег всех АТС;
= 06 - средний коэффициент статического использования грузоподъёмности;
= 0437 - средний коэффициент использования пробега;
Расход смазочных материалов по каждому виду (моторное масло трансмиссионное масло консистентная смазка) определяется по формуле:
где Ксм – норма расхода смазочных материалов в литрах от расхода топлива для масел или в килограммах от расхода топлива для консистентной смазки (приложение 2 табл. 12).
Моторные масла: Gм.м. = 3072103 · 005 = 153605 л
Трансмиссионные масла: Gт.м. = 3072103 · 0005 = 15361 л
Пластичные смазки: Gп.с. = 3072103 · 0003 = 9216 кг
Специальные масла:Gс.м. = 3072103 · 001 = 30721 кг.
Расход технического керосина Gк принимается в размере 0.5% от весового расхода топлива:
Gк = 0005 · Gл · т = 3072103 · 0005 · 0825 = 12672 кг
где т = 0825 кгл - плотность топлива.
Расход обтирочных материалов Gоб определяется по нормам Ноб расхода на одну единицу АТС в год: грузовые автомобили – 36 кгед.
Gоб = Асс · Ноб = 250 · 36 = 9000 кг
Затраты на прочие эксплуатационные материалы (электролит дистиллированную воду антифриз тормозную жидкость) можно принять в размере 10% от суммы затрат по всем видам масел и техническому керосину.
Затраты на ремонтные материалы (Зрм) и запасные части (3зч) необходимые для проведения технических обслуживаний и текущих ремонтов в денежном выражении определяются на основании норм затрат в руб. на 1000 км пробега и общего пробега парка по формуле:
- ремонтные материалы
Зрм = 0001 · Нрм · Lобщ = 0001 · 150 · 13362050 = 2004308 руб.
где Нрм = 150 руб.1000 км - норма затрат на ремонтные материалы (приложение 1 табл. 14);
Зз.ч. = 0001 · Нзч · Lобщ = 0001 · 134 · 13362050 = 1790515 руб.
Затраты на восстановление и ремонт шин определяются на основании нормативов на 1000 км пробега и норм пробега шин по типам автомобилей.
Расчет затрат на восстановление и ремонт шин проводится по формуле:
ш = 0001 · Цш · nк· Нш · Lобщ = 0001 · 8000 · 6 · 089 100 · 13362050 = 5708268 руб.
где Цш = 8000 руб. – стоимость одного комплекта шин (покрышка камера ободная лента);
nк = 6 – число колес на автомобиле без учета запасного колеса шт;
Нш = 089% - норма отчислений на восстановление и ремонт одного комплекта шин на 1000 км пробега для соответствующего размера шин и условий эксплуатации (приложение 1 табл. 15).
Результаты расчёта потребности в материальных затратах приведены в таблице 63
Таблица 6.3 Потребность АТП в материальных затратах
Автомобильное топливо л
Трансмиссионное масло л
Консистентная смазка кг
Технический керосин л
Обтирочные материалы кг
Всего масел и других эксплуатационных материалов (сумма п.п. 2-8)
Всего ремонтные материалы и запчасти
Восстановление и ремонт шин
2.3. Расчет численности и фонда оплаты труда по категориям работающих
А) Расчет фонда оплаты труда водителей
Среднесписочная численность водителей
Среднесписочная численность водителей определяется по формуле:
Nв = (АЧр + 0.2 · АЧТО-2 + АЧр · tп.з.) (Фг.в. · Кw) = (487086 + 02 · 22464 + 487086 · 0042) (1755 · 11) = 265 чел.
где АЧр = 487086 ч - автомобиле часы работы на линии (рассчитаны в эксплуатационной части проекта);
АЧТО-2 – объем времени участия водителей в ТО может быть принят равным 10-20% от трудоемкости ТО-2;
tп.з. – подготовительно – заключительное время водителей принимается 0.042 час на 1 час работы водителей;
Фг.в. = 1755 ч – годовой фонд рабочего времени водителя;
Кw = 1.1 – коэффициент роста производительности труда.
Расчет основной заработной платы водителей
Сдельная расценка за 1 т перевозимого груза и за 1 т·км транспортной работы определяется по формулам:
Sт = (Счас · tпр) (60 · q) = (160 · 41) (60 · 83 ) = 132 рубт;
Sткм = (Счас · (tдв + tпр) · Кзп) (60 · V · q · н) = (160 · (60+41) · 125) (60 · 49 · 83 · 044) = 19 рубт·км;
где Счас = 160 руб. – часовая тарифная ставка водителя третьего класса данной группы автомобилей руб.;
tпр = 41 мин. – норма времени простоя автомобиля под погрузкой и разгрузкой на ездку;
tдв = 60 мин. – норма времени движения автомобиля на 1 ч работы;
q = 83 т. - грузоподъемность автомобиля;
Кзп = 125 - коэффициент учитывающий изменение сдельных расценок от класса перевозимого груза (принимается для 2-го класса);
н = 044 – нормативный коэффициент использования пробега;
V = 49 кмч - норма пробега автомобилей для соответствующей категории дорог "I".
Sт – сдельная расценка за 1 тонну перевезенного груза руб.;
Рткм = 29086958 т·км – транспортная работа;
Sткм – сдельная расценка за 1 т·км транспортной работы.
Основная заработная плата водителей работающих по сдельным расценкам за перевезенные тонны и выполненные тонно-километры определяется по формуле:
ОЗП = Qт · Sт + Рткм · Sткм = 1183224 · 132 + 29086958 · 19 = 70884 тыс. руб.
где Qт = 1183224 т – объем перевоза груза;
Расчет доплат водителям
Водителям работающим на грузовых и легковых автомобилях выплачивается ежемесячная надбавка от часовой тарифной ставки водителя 3 класса в следующих размерах: водителям второго класса – 10% водителям первого класса – 25%.
Принимаем что на АТП работает:
- водителей первого класса – 10% 27 чел.;
- водителей второго класса – 20% 53 чел.
Надбавку за классность рассчитывают за отработанное время исходя из месячной тарифной ставки водителя 3 класса.
Нкл = Счас · Фмв · nм · (dкл2 · Nв2 + dкл1 · Nв1) = 160 · 1755 · 11 · (01 · 53 + 025 · 27) = 37220 тыс. руб
где nм = 11 - число месяцев работы водителя в планируемом периоде;
Nв2 Nв1 - численность водителей соответственно второго и первого классов;
dкл2 dкл1 - надбавка за классность водителям соответственно второго и первого классов;
Доплата бригадирам за руководство бригадой:
Дбр= 001 · Счас · Фгв · nбр · dбр = 001 · 160 · 1755 · 13 · 10 = 365 тыс. руб.
где nбр - количество бригад водителей; nбр = Nв nв = 265 20 = 13;
nв - количество водителей в бригаде;
dбр = 10% - доплата бригадирам за руководство бригадой.
Доплата за работу в сверхурочное время принимаем 5 ÷ 7% от основной заработной платы.
Дсв.у. = 005 · ОЗП = 005 · 70884 = 3544 тыс. руб.
Премии водителям за качественное выполнение работ принимает 40% от фонда основной заработной платы.
Дпр. = 04 · ОЗП = 04 · 70884 = 28354 тыс. руб.
Дополнительная заработная плата - 106% от фонда основной заработной платы.
Ддоп. = 0106 · ОЗП = 0106 · 70884 = 7514 тыс. руб.
Расчет отчислений на социальные нужды
Отчисления на социальные нужды для частного предприятия составляют 395% от суммы основной и дополнительной оплаты труда.
Осоц = 0395 · (ОЗП + Ддоп) = 0395 · (70884 + 7514) = 30967 тыс. руб.
Фонд оплаты труда водителей.
ФОТв = ОЗП + Нкл + Дбр + Дсв.у + Дпр +Ддоп = 70884 + 37220 + 365 + 3544 + 28354 + 7514 = 147881 тыс. руб.
Среднемесячная заработная плата одного водителя.
Зср.м. = ФОТв (12 · Nв) = 147881 (12 · 265) = 465тыс. руб.
Б) Расчёт фонда оплаты труда ремонтных рабочих
Численность ремонтных рабочих - Npp = 99 чел.
Расчёт заработной платы ремонтных рабочих
Основная заработная плата ремонтных рабочих включает: заработную плату рассчитанную по тарифам за отработанное время и различные виды доплат – за руководство бригадой сверхурочные работы работы в ночное время и др.
Заработная плата по тарифу производится по формуле:
ПРР = Счас · Т = 170 · 189630 = 32237 тыс. руб.
где Счас = 170 рубч – часовая тарифная ставка соответствующая условиям труда;
Т = 189630 чел·ч- трудоемкость работ выполняемых в соответствующих условиях труда чел·ч.
Общую величину доплат ремонтным рабочим по укрупненному расчёту целесообразно принимать в размере 810% от основной заработной платы по тарифу.
Добщ.доп = 01 · 3ПРР = 01 · 32237 = 3224 тыс. руб.
Премирование за выполнения задания по обеспечению выпуска автомобилей на линию – в размере до 30 % тарифной ставки.
Дпр = 03 · 3ПРР = 03 · 32237 = 9671 тыс. руб.
Основная заработная плата ремонтных рабочих.
ОЗПрр = 3ПРР + Добщ.доп + Дпр = 32237 + 3224 + 9671 = 45132 тыс. руб.
Дополнительную заработную плату принимаем в размере 11% от основной заработной платы ремонтных рабочих.
Ддоп = 011 · ОЗПрр = 011 · 45132 = 4965 тыс. руб.
Отчисления на социальные нужды
Осоц = 0395 · (ОЗПрр + Ддоп) = 0395 · (45132 + 4965) = 19788 тыс. руб.
Фонд оплаты труда ремонтных рабочих
ФОТрр = ОЗПрр + Ддоп = 45132 + 4965 = 50097 тыс. руб.
Среднемесячная заработная плата одного ремонтного рабочего
Зср.рр = ФОТрр (12 · Npp) = 50097 (12 · 99) = 42 тыс. руб.
В) Расчёт фонда оплаты труда вспомогательных рабочих
Численность вспомогательных рабочих принимаем в размере 2025% от численности ремонтных рабочих.
Nвр = 025 · Nрр = 99 · 025 = 25 чел.
Пвр = Счас · Т · Nвр = 150 · 1840 · 25 = 6900 тыс. руб.
где Т = 1840 ч – годовой фонд рабочего времени вспомогательного рабочего.
Доплаты за работу в ночное время за работу в праздничные дни а также премии могут быть приняты в размере 20% от заработной платы по тарифам.
Добщ.доп = 02 · 3Пвр = 02 · 6900 = 1380 тыс. руб.
ОЗПвр = 3Пвр + Добщ.доп = 6900 + 1380 = 8280 тыс. руб.
Дополнительная заработная плата принята в размере 106% от заработной платы по тарифам.
Дд = 0106 · О3Пвр = 0106 · 8280 = 878 тыс. руб.
Отчисления на социальные нужды
Осоц = 0395 · (ОЗПвр + Дд) = 0395 · (8280 + 878) = 3617 тыс. руб.
Фонд оплаты труда вспомогательных рабочих
ФОТвр = ОЗПвр + Дд = 8280 + 878 = 9158 тыс. руб.
Среднемесячная заработная плата одного вспомогательного рабочего
Зср.вр = ФОТвр (12 · Nвр) = 9158 (12 · 25) = 305 тыс. руб.
Г) Расчёт фонда оплаты труда ИТР
Численность ИТР принимаем 15% от числа водителей. В указанный процент не входят работники сторожевой службы и пожарной охраны а также производственно-линейный персонал.
Nитр = 265 · 015 = 40 чел.
Таблица 6.4 Штатный список ИТР АТП
Структурные подрапзделения
наименование должности
Генеральный директор АТП
Зам гендиректора по экономике
Зам гендиректора по эксплуатации
Планово-экономический отдел
Отдел труда и заработной платы
Руководитель группы по организации перевозок
Производственно-технический отдел
Диспетчер производства
Производственно-линейный персонал
Отдел технического контроля
Отдел материального-технического снабжения
Младший обслуживающий персонал и пожарная охрана (ПСО)
Прочие рабочие (ПВР)
Инструментальщик кладовщик
Доплаты за работу в ночное время за работу в праздничные дни могут быть приняты в размере 20% от заработной платы.
Добщ.доп = 02 · 3Питр = 02 · 16008 = 3202 тыс. руб.
Основная заработная плата ИТР
ОЗПитр = 3Питр + Добщ.доп = 16008 + 3202 = 19210 тыс. руб.
Дополнительная заработная плата принята в размере 106% от заработной платы.
Дд = 0106 · О3Питр = 0106 · 19210 = 2036 тыс. руб.
Премирование по результатам хозяйственной деятельности – в размере до 40 % тарифной ставки.
Дпр = 04 · 3Питр = 04 · 16008 = 6403 тыс. руб.
Осоц = 0395 · (ОЗПитр + Дд) = 0395 · (19210 + 2036) = 8392 тыс. руб.
Фонд оплаты труда ИТР
ФОТитр = ОЗПитр + Дд + Дпр = 19210 + 2036 + 6403 = 27649 тыс. руб.
Среднемесячная заработная плата одного ИТРовца
Зср.итр = ФОТитр (12 · Nитр) = 27649 (12 · 51) = 45 тыс. руб.
Расчет фонда оплаты труда дан в таблице 6.5.
Таблица 6.5 Потребность в персонале и фонд оплаты труда
Категории работающих
Ср. мес. зп тыс. руб.
Отчисления на социальные нужды тыс. руб.
ФОТ с отчислениями на социальные нужды тыс. руб.
Вспомогательные рабочие
Руководители специалисты и служащие (ИТР)
2.4. Затраты на амортизацию подвижного состава
Затраты на амортизацию определяются исходя из балансовой стоимости и норм амортизационных отчислений с учетом срока службы по формуле:
Зам. = (Сатс · На.сл · Асс) 100 = (20790 · 15 · 250) 100 = 77963 тыс. руб.
Сатс - балансовая стоимость одного АТС руб.;
На.сл - норма амортизационных отчислений в зависимости от амортизационного срока службы АТС %;
Асс - среднесписочное количество АТС;
Норму амортизационных отчислений применительно к конкретным условиям эксплуатации определим для автомобилей с учетом амортизационного срока На.сл по формуле:
Нам.сл. = (100 · (Сатс - Со)) (Сатс · Тсл) = (100 · (20790 - 2079)) (20790 · 6) = 15 %
Нам.сл.нет = (100 · (Сатс - Со)) (Сатс · Тсл) = (100 · (00 - 0)) (00 · 6) = 0 %
где Со – остаточная стоимость одного АТС (можно принять 10% от Сатс) руб.;
Тсл – амортизационный (нормативный) срок службы одного АТС (можно принять 6 лет);
Нормы амортизационных отчислений по стационарным основным фондам (здания сооружения оборудование и т.п.) принимаем в размере 38%.
Затраты на амортизацию зданий и сооружений:
Зам.зд. = (Сзд · На.зд) 100 = (374854 · 5) 100 = 18743 тыс. руб.
где Сзд - балансовая стоимость зданий и сооружений.
Затраты на амортизацию технологического оборудования:
Зоб. = (Соб · На.зд) 100 = (119953 · 5) 100 = 5998 тыс. руб.
где Соб - балансовая стоимость технологического оборудования.
Результаты расчёта затрат на амортизацию по основным фондам представлены в таблице 6.6
Таблица 6.6 Затраты на амортизацию основных фондов
Балансовая стоимость ОФ тыс. руб.
Стоимость отчислений тыс. руб.
Здания сооружения производственного назначения
Технологическое оборудование
По укрупненному расчету величина прочих затрат должна составлять 57% общей величины сметы эксплуатационных затрат.
2.6. Смета эксплуатационных затрат
Расчет эксплуатационных затрат сводим в таблицу 6.7.
Таблица 6.7 Смета эксплуатационных затрат
Сумма затрат тыс. руб.
Структура затрат % к итогу
Автомобильное топливо
Восстановление и ремонт автомобильных шин
Амортизация ОПФ всех видов
2.7. Калькуляция себестоимости перевозок
Калькуляция себестоимости перевозок представляет собой расчет величины эксплуатационных затрат приходящихся на единицу транспортной работы.
При калькуляции себестоимости предусматривают статью затрат "Накладные расходы" которые не зависят от размеров движения (транспортной работы) и по производственному назначению относятся к постоянным затратам. Накладные расходы определяют как сумму прочих затрат фонда оплаты труда с отчислениями на социальные нужды вспомогательных рабочих руководителей специалистов и служащих амортизации основных фондов без АТС.
Для средних условий эксплуатации величина накладных расходов может составить 1520% от общей величины эксплуатационных затрат АТП.
Себестоимость перевозок по каждой статье определяют путем деления суммы эксплуатационных затрат ΣSэк соответствующей статьи за определенный период времени на выполненную транспортную работу
Себестоимость калькулируют по грузовым перевозкам на 10 т·км при применении тарифа за выполненные т·км.
Определим накладные расходы:
Нр = 41525 + 48816 + 24741 = 115082 тыс. руб.
Калькуляция себестоимости перевозок приведена в таблице 6.8
Таблица 6.8 Калькуляция себестоимости перевозок
Всего по АТП тыс. руб.
Себестоимость руб.10 т·км
Структкра затрат % к итогу
Фонд оплаты труда водителей с отчислением на социальные нужды
Смазочные и эксплуатационные материалы
Техническое обслуживание и ремонт АТС
2.8. Расчёт потребности нормируемых оборотных средств
Исходными данными для определения оборотных средств являются смета эксплуатационных затрат и установленные нормы запаса в днях по каждой группе материальных ценностей входящих в состав оборотных средств.
В соответствии с Положение о бухгалтерском учете и отчетности в Российской Федерации в составе средств в обороте (малоценные быстроизнашивающиеся предметы) учитываются предметы срок службы которых меньше года независимо от стоимости а также стоимостью на дату приобретения не более пятидесятикратного установленного законом минимального размера месячной оплаты труда за единицу без ограничения срока их службы.
Сумма потребных нормируемых оборотных средств Фн. об определяется по формуле:
Фн.об = (Si · Hi) Дк
Дк = 305 дней - число календарных дней расчетного периода.
К эксплуатационным материалам относятся: смазочные и обтирочные материалы технический керосин и др. Фонд оборотных агрегатов можно определить из расчета 7075% от норматива оборотных средств по статье “Запасные части”. Прочие нормируемые оборотные средства (топливо для хозяйственных нужд материалы лесоматериалы краски тормозная жидкость малоценный и быстро изнашивающийся инвентарь и инструменты спецодежда и т.п.) можно принять в размере 5% от их общей суммы.
Результаты расчета потребности нормируемых оборотных средств приведены в таблице 6.9.
Таблица 6.9 Потребность в нормируемых оборотных средствах
Наименование оборотных средств
Норматив оборотных средств тыс. руб.
По схеме затрат расходов
Эксплуатационные материалы
Фонд оборотных агрегатов
Прочие нормируемые средства
Всего нормируемые оборотные средства Фн.об
2.9. Расчёт финансовых показателей
Экономическая целесообразность хозяйственной деятельности предприятия определяется абсолютными и относительными показателями. Различают две основные группы показателей экономического эффекта и экономической эффективности.
Экономический эффект – показатель характеризующий общий результат хозяйственной деятельности предприятия. В АТП в качестве основного показателя безубыточности предприятия является прибыль. Однако по этому показателю взятому изолированно нельзя сделать обоснованный вывод по использованию вложенного капитала и ресурсов. Поэтому используют показатели экономической эффективности деятельности предприятия.
Экономическая эффективность – относительный показатель который соизмеряет полученный эффект с затратами и ресурсами при достижении этого эффекта.
В АТП в качестве основных относительных показателей характеризующих уровень экономической эффективности хозяйственной деятельности предприятия являются рентабельность общая (основных фондов и нормируемых оборотных средств) рентабельность производственных затрат и другие показатели. Расчет ведем за год.
Прибыль Пб от реализации работ и услуг определяется как разница между суммой всех доходов и поступлений и суммой всех затрат понесённых предприятием за период деятельности с начала года.
Прибыль (балансовая) определяется из выражения:
Пб = Д - Зэкс = 857207 - 634968 = 222239 тыс. руб.
где Д - общая сумма доходов за грузовые перевозки;
Зэкс – эксплуатационные затраты.
Доход предприятия определим по укрупненной формуле:
Д = Зэкс· КР = 634968 · 135 = 857207 тыс. руб.
где КР – коэффициент учитывающий рентабельную работу АТП для средних условий эксплуатации по грузовым перевозкам КР = 135
Эксплуатационные затраты определим по формуле:
Зэкс = 01 · Сусл · Р = 01 · 2183 · 29086958 = 634968 тыс. руб.
где Сусл = 2183 руб. (10 т·км) – себестоимость грузоперевозок;
Р = 29086958 т·км – произведенная работа за год.
Прибыль остающуюся в распоряжении предприятия (Пост) можно рассчитывать из выражения:
Пост = Пб - Нпр - Ним - Ндор - Ндр = 222239 - 53337 - 20501 - 17144 - 3334 = 127923 тыс. руб.
где Нпр – налог на прибыль (24% от Пб) руб.;
Нпр = 024 · 222239 = 53337 тыс. руб.
Ним – налог на имущество (2% от стоимости основных и нормируемых оборотных фондов) руб.;
Ним = 002 · (1014557 + 10503) = 20501 тыс. руб.
Ндор - налог на пользователей автомобильных дорог (2% от доходов за перевозки) руб.;
Ндор = 002 · 857207 = 17144 тыс. руб.
Ндр – другие виды налогов относимые на прибыль платежи кредиторам и собственникам предприятия (15% от Пб) руб.
Ндр = 0015 · 222239 = 3334 тыс. руб.
Фонд технического перевооружения и реконструкций (60% от Пост) тыс. руб.
ФТР = 127923 · 06 = 76754 тыс. руб.
Фонд социального развития (25% от Пост) тыс. руб.
ФСР = 127923 · 025 = 31981 тыс. руб.
Фонд материального стимулирования (10% от Пост) тыс. руб.
ФМС = 127923 · 01 = 12792 тыс. руб.
Резервный фонд (5% от Пост) тыс. руб.
РФ = 127923 · 005 = 6396 тыс. руб.
Рентабельность общая Rобщ по балансовой прибыли показывает сколько денежных единиц прибыли получено предприятием с единицы стоимости активов (основных фондов и нормируемых оборотных средств).
Rобщ = Пб (Фосн + Фн.об) · 100% = 222239 (1014557 + 10503) · 100 = 22 %
Рентабельность перевозок Rпер по балансовой прибыли показывает насколько эффективно предприятие ведет производственную деятельность по перевозкам (по выпуску продукции) и рассчитывается по формуле:
Rпер = Пб Зэкс · 100% = 222239 634968 · 100 = 35 %
Рентабельность по чистой (остающейся на предприятии) прибыли:
Rпер.чист = Пост Зэкс · 100% = 127923 634968 · 100 = 20 %
Показатель производительности труда в натуральном (Wн) и стоимостном выражении (Wс) определяется как объем транспортной работы или объем валового дохода на одного работающего:
- в натуральном выражении:
Wн = Р Nраб = 29086958 440 = 66107 т·кмчел.
- в стоимостном выражении:
Wс = Д Nраб = 857207 440 = 1948 тыс.руб.чел.
2.10. Расчёт показателей использования производственных фондов
Эффективность производства оценивается также и другими показателями характеризующими использование производственных фондов.
Фондоотдача Коф показывает размер дохода на один рубль основных фондов:
Коф = Д Фосн = 857207 1014557 = 084
Период окупаемости инвестиций Ток в проектируемое предприятие:
Ток = (Фосн + Фн.об) Пост = (1014557 + 10503) 127923 = 80 лет
2.11. Оценка экономической эффективности инвестиций.
Оценку варианта эффективности инвестиций рекомендуется проводить по показателю чистый дисконтированный доход (ЧДД). Вспомогательными показателями могут быть период окупаемости инвестиций индекс доходности и другие показатели отражающие интересы участников или специфику проекта.
ЧДД определяется как алгебраическая сумма текущих эффектов за весь расчетный период приведенных к базисному (начальному) шагу.
При равномерных инвестициях:
ЧДД = - [Kt (1+R)t] + [(Пч + Зам) (1+R)t] + Kл(1+R)t тыс. руб.
Где: t – номер шага расчета (год);
R – норма дисконта (0.15);
Kt – размер инвестиций t-го периода (Фосн + Фн.об);
Пч – чистая прибыль;
Зам – амортизационные затраты;
Кл – ликвидные капиталовложения за весь период расчета рекомендуется прибыль Кл = 01 · К;
ЧДД = - 1025060(1+015) + (127923+102704)(1+015)1 + (127923+102704)(1+015)2 + (127923+102704)(1+015)3 + (127923+102704)(1+015)4 + (127923+102704)(1+015)5 + (127923+102704)(1+015)6 + 01·1025060(1 + 015)7 = 19982 тыс. руб.
ЧДД инвестиционного проекта положителен проект является эффективным
( при данной норме дисконта) и может рассматриваться вопрос о его принятии.
2.12. Расчёт точки безубыточности
При оценке всех затрат инвестиционного проекта (в дипломе это создание АТП) их можно условно разделить на две составляющие :
- постоянные затраты (новые капвложения – это основные фонды табл.6.3.) они не изменяются в течение реализации проекта;
- переменные затраты зависящие от количества проданных услуг (в нашем случае грузоперевозки).
При методике расчета затрат в соответствии с [14] переменные затраты соответствуют себестоимости грузоперевозок (табл.6.8.).
Точкой безубыточности инвестиционного проекта называют количество проданных товаров услуг и т.д. после которого проект полностью окупается (включая все новые капвложения) и инвестор начинает получать чистую прибыль. Эту точку можно определить графически построив графики доходов и расходов в зависимости от количества проданных услуг и аналитически по формуле. При графическом определении точку безубыточности получают как точку пересечения графика доходов и расходов. Аналитически точку безубыточности определим по формуле:
Ркр = (Зпост · 10) (Цусл - Сусл) = (1025060000 · 10) (2943 - 2183) = 134876316 т·км
где Ркр – величина транспортной работы в т·км при которой проект полностью окупается;
Зпост = 1025060000 руб. – затраты постоянные (балансовая стоимость всех основных фондов + оборотные фонды);
Цусл = 2943 руб. (10т·км) – цена единицы услуги т.е. десяти т·км при рентабельности продажи 35%;
Сусл = 2183 руб (10т·км) – себестоимость единицы услуги т. е. десяти т·км.
График безубыточности проекта показан на рис. 6.2
Рис. 6.2 График безубыточности.
Результаты экономических расчетов сводим в таблицу 6.10.
Таблица 6.10 Технико-экономические показатели АТП
Наименование технико-экономических показателей АТП
Значение показателей
Среднесписочное количество подвижного состава АТП
Коэффициент технической готовности
Коэффициент использования парка
Годовой объем перевозок
Среднесуточный пробег одного автомобиля
Годовой пробег всего автопарка
Производительность труда водителей
Себестоимость перевозок
Стоимость основных производственных фондов
Стоимость нормируемых производственных средств
Срок окупаемости инвестиций
Общая рентабельность
Рентабельность перевозок
Таблица 6.11 Формирование и распределение прибыли в АТП тыс. руб.
Наименование показателей
Материальные затраты
Техническое обслуживание и ремонт автомобилей
Фонд оплаты труда персонала АТП
Амортизация основных фондов
Баланс (валовая прибыль)
Прибыль остающаяся в распоряжении предприятия
Платежи по кредитам и % по долгосрочным кредитам
Фонд развития производства
Фонд социального развития
Фонд материального поощрения
В дипломном проекте разработан проект АТП на 250 автомобилей МАЗ-534019 для перевозки промышленных грузов. Дипломный проект состоит из нескольких частей связанных друг с другом
В эксплуатационной части подобраны виды грузов под данную модель транспорта составлена схема перевозок разработаны 9 маршрутов. Пункт расположения АТП находится в районе с умеренными климатическими условиями годовое количество дней работы АТП выбрано - 305. Исходя из грузоподъёмности транспорта количества автомобилей в эксплуатации и схемы перевозок годовой объём перевозок составил 1183224 т. и годовой грузооборот составил 29086958 т·км.
В технологической части определены объем и виды технического обслуживания и текущего ремонта подвижного состава рассчитано количество ремонтных рабочих. Кроме этого здесь же разработан производственный корпус АТП подобрано технологическое оборудование для ремонта подвижного состава разработан генеральный план предприятия и подробно рассмотрена компоновка агрегатного участка.
В конструкторской части методом априоронго ранжирования был выбран гидравлический съёмник для демонтажа подшипников ступиц и втулок которые установлены по посадке с натягом. Была собрана группа экспертов и по их оценкам исходя из стоимости массы максимального усилия и удобства в эксплуатации наиболее оптимальной оказалась модель СГА8.
В ремонтно-технологической части дипломного проекта подробно рассмотрен текущий ремонт корпуса водяногонасоса автомобиля МАЗ-534019 разработан технологический маршрут станочной обработки определены и проанализированы возможные дефекты корпуса в результате эксплуатации.
В разделе " Безопасность и экологичность проектных решений" проведен анализ вредных и опасных производственных факторов возникающих на агрегатном участке и экологичной безопасности АТП разработаны мероприятия обеспечивающие нормы труда и экологичность. В этом разделе проведён расчет искусственного освещения агрегатного участка.
В организационно-экономической части дипломного проекта разработана организационно-структурная схема предприятия определены потребные капвложения и себестоимость перевозки грузов. В этом разделе показано что окупаемость проекта наступает через 8 лет при цене единицы услуги 2943 руб.(10т*км). В данном разделе определены основные технико-экономические показатели АТП.
В целом дипломный проект выполнен в сответствии с требованиями предъявляемыми к нему. Разработанное АТП конкурентноспособно и эффективно исходя из его рентабельности привлекательно для инвестиций.
Список используемой литературы
Общесоюзные нормы технологического проектирования предприятий автомобильного транспорта ОНТП-01-91. Росавтотранс 1991.
Напольский Г.М. Технологическое проектирование автотранспортных предприятий и станций технического обслуживания: Учебник для вузов. – М.: Транспорт 1993. – 271 с.
Положение о техническом обслуживании и ремонте подвижного состава автомобильного транспорта.М-во автом. трансп. РСФСР. – М.: Транспорт 1986. – 72 с.
Автомобили МАЗ-5336 -6303: Руководство по эксплуатации техническому обслуживанию и ремонту каталог запасных частей А.Кузнецов. – М.: Издательский дом Третий Рим 2007. – 216 с.
Техническая эксплуатация автомобилей: Учебник для вузов Под ред. Г.В. Крамаренко.- М.: Транспорт 1983.-488 с.
Проектирование авторемонтных предприятий. Справочник инженера-механика. Верещак Ф.П. Абелевич Л.А. Транспорт 1973. – 328 с.
Афанасьев Л.Л. и др. Гаражи и станции технического обслуживания автомобилей. (Альбом чертежей). – М.: Транспорт 1980. – 216 с.
Сарбаев В.И. и др. Механизация производственных процессов технического обслуживания и ремонта автомобилей: Учебное пособие. – М.: МГИУ 2006 – 284 с.
Техническая эксплуатация автомобилей: Учебник для вузов Под ред. Кузнецова Е.С. - М.: Транспорт 1991 – 413 с.
Бейлин В.И. Быховский М.Л. Проектирование предприятий автомобильного транспорта (Объемно-планировочные решения). Методические указания по дипломному проектированию М.: МГОУ. 2002.
Иванов М.Н. Детали машин. Учебник для студентов втузов. –М.: высшая школа. 1998.
Мариниченко А.В. Безопасность жизнедеятельности: Учебное пособие. М. "Дашков и К" 2007.
Рекомендуемые чертежи
- 25.01.2023
- 25.01.2023
- 25.01.2023
- 09.10.2023
- 09.07.2014
- 25.01.2023