Проект цеха литье по газифицируемым моделям




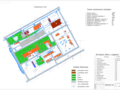
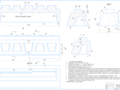
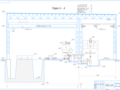
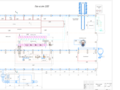
- Добавлен: 24.01.2023
- Размер: 4 MB
- Закачек: 0
Описание
Состав проекта
![]() |
![]() ![]() ![]() ![]() |
![]() ![]() ![]() |
![]() ![]() ![]() |
![]() ![]() ![]() ![]() |
![]() ![]() ![]() |
![]() ![]() ![]() ![]() |
![]() ![]() ![]() ![]() |
![]() ![]() |
![]() ![]() ![]() ![]() |
Дополнительная информация
Бронеплита приклиновая ЦМ - 166.cdw

- Размеры для справок.
Материал 110Г13Л ГОСТ 977 - 88
Точность отливки 7 - 7 - 8 ГОСТ 26645 - 85
Формовочные уклоны по ГОСТ 3212 - 92
Не указанные литейные радиусы 5 мм.
Допускается без исправления поверхности литейные дефекты не снежащие прочность не ухудшающие
товарный вид раковины
механический пригар засоры
поражающие поверхность глубина
дефектов не более 3 мм. Общая площадь дефектов не более 3 % поверхности детали.
Допускается на всех поверхностях исправление литейных дефектов с помощью сварки
не более 3 % поверхности детали.
Термообработка (закалка в воде). Твердость после термообработки НВ 200 .230.
Поверхности (А) зачистить на маятниковом наждаке и контролировать макетом угла 30
В местах подвода металла
в радиусах перехода допускается выломы
на ширину питателя глубиной не более 3 мм.
Маркировать номер плавки.
Сталь 110Г13Л ГОСТ 977-88
ДП.050709.050723.ЗМет-08
Изготовление моделей.docx
В условиях мелкосерийного производства модели из пенополистирола изготавливаются автоклавным способом. При этом ручная пресс-форма заполняется гранулами пенополистирола с помощью специального задувного устройства и затем помещается в автоклав. После тепловой обработки пресс-форма извлекается из автоклава охлаждается в водяной ванне разбирается и модель извлекается. Затем цикл повторяется. Для изготовления моделей могут использоваться медицинские автоклавы моделей ГПД-400 ГПД-600 и др.
На рис. 7.9 представлено задувное устройство которое состоит из корпуса 1 и рукоятки 2. Воздух от цеховой сети подается через штуцер 9 в камеру смешивания куда поступает пенополистирол в гранулах через штуцер 6. В корпусе расположено сопло 11 положение которого относительно рабочего сопла 7 регулируется резьбовым соединением. Корпус 1 соединен с рукояткой 2 гайкой 4. Рабочее сопло 7 регулируется относительно сопла 11 и фиксируется гайкой 3. Герметизация камеры смешивания достигается резиновыми прокладками 17 и 18. В рукоятке расположен клапан состоящий из пружины 14 осей б и 13 втулки 5 курка 10 соединенного с пружиной осью 15. Прокладки 13 12 я пробка 16 герметизируют клапан подачи воздуха в камеру смешивания. Задувное устройство работает следующим образом. При нажатии курка 10 ось 6 перемещается в сторону пружины сжимает ее и воздух через штуцер 9 по каналам в рукоятке 2 поступает в камеру смешивания и далее в канал рабочего сопла 7. В камере смешивания образуется разрежение в результате которого по каналу штуцера 8 поступают гранулы пенополистирола которые увлекаются воздушным потоком в рабочее сопло 7 и далее через отверстие в пресс-форме в ее полость. Штуцер 8 соединен с бункером пенополистирола прозрачным полиэтиленовым шлангом что позволяет визуально наблюдать за ходом заполнения пресс-формы гранулами пенополистирола. Для прекращения работы задувного устройства отпускается курок который под действием пружины возвращается в исходное положение перекрывая канал поступления воздуха.
Рис. 7.9. Задувное устройство для ручного заполнения пресс-форм пенополистиролом
Предварительное вспенивание полистирола
В условиях мелкосерийного производства предварительное вспенивание полистирола осуществляется в пару над кипящей водой в водяной ванне или автоклаве. Простейшая установка для подвспенивания полистирола в пару представлена на рис. 111. Вспениватель паровой включает в себя бак со встроенными ТЕНами (термические электронагреватели); стенки которые защищены теплоизоляционным материалом; крышку с рамкой которая имеет возможность перемещения внутри бака. В положении над баком рамка посредством рычажного механизма может опускаться в бак до определенного регулируемого упора. На рамку устанавливается сетчатый противень для полистирола. Работает подвспениватель следующим образом. В бак до определенного уровня заливается вода и доводится до кипения при открытой крышке. Затем рамка с противнем на которой равномерным тонким слоем насыпан полистирол опускается в бак до упора и крышка закрывается. После определенного времени выдержки над водяной ванной крышка бака открывается рычажным механизмом рамка с противнем извлекается из бака и противень со вспененным полистиролом снимается с рамки. Затем цикл подвспенивания новой порции полистирола повторяется.
Рисунок 1111 Установки для предварительного вспенивания
Установка для предварительного вспенивания
Предвспениватель периодического действия под давлением X15
- макс. рабочее давление 049 bar
- мощность привода мешалки 15 кВт 80 оборотов в минуту
- объем сосуда для вспенивания 015 м3
- достигаемая плотность 13-120 кгл
- при плотности (колонка 1) производительность*
*при западноевропейском стандартном материале.
- подача сырья системой Вентури от сосуда с сырьем к бункеру наполнения
- электронное взвешивание для точного дозирования
- сосуд для вспенивания из алюминия с теплоизоляционным слоем
- мешалка с прерывателями из нержавеющей стали
- вал мешалки и нижние скребки никелированные
- верхнее размещение привода мешалки
- равномерное пропаривание через щелевые решетки в днище сосуда для вспенивания (ширина щелей 02 мм)
- вентили увеличенного диаметра для быстрого снятия давления
- система безопасности на случай отключения электроснабжения (подача холодного воздуха)
- специальный датчик уровня для предотвращения сваривания материала
- защита вентилей от попадания материала автоматическая чистка паровой решетки посредством продувки воздухом после каждого цикла
- контроль объёма вспененного материала специальным вибродатчиком внутри сосуда вспенивания
- система поддерживающей продувки при заполнении и разгрузке
- устройство для автоматического отключения и полной разгрузки предвспенивателя
- терминал с 15" дисплеем
-Устройство протоколирования основных параметров рабочего цикла
Сушилка с псевдоожиженным слоем
для постоянной сушки и стабилизации свежевспененого материала
вкл. просеивающее устройство шлюз барабанный воздуходувка для транспортировки материала на расстояние
Мощность воздуходувки 05 кВт
Габариты предвспенивателя:
Электронное регулирование давления пара
Электропривод для мешалки бесступенчатый регулируемый 50-120 оборотов в мин.
Хранение пенополистирола после предварительного вспенивания
Бункер представляет собой минимальный модуль состоящий из двух емкостей. В зависимости от программы заказывается необходимое количество модулей. Бункер состоит из двух сшитых из прочной воздухопроницаемой ткани и изолированных друг от друга мешков 1 закрытых тканевыми крышками и подвешенных на петлях внутри сварно-сборочного каркаса 2. Мешки заужены в нижней части и снабжены шиберными устройствами 3.
Рисунок 2222 бункер для пенополистирола модели 4222
Техническая характеристика бункера для пенополистирола модели 4222
Полезный объем одной емкости м3
Масса пенополистирола в бункере при плот
Габариты: длинаширинавысота мм
В условиях серийного и массового производства модели изготавливаются на полуавтоматических и автоматических установках.
На рис. 7.10 представлена автоматическая установка для изготовления моделей из пенополистирола с вертикальной плоскостью разъема оснастки модели К 810 сконструированная Kurtz Германия.
Для изготовления предлагается формовочный автомат K810 с размером рамы для монтажа пресс-формы 800х1000 мм.
Время цикла 40 – 90 сеунд.
Формовочный автомат имеет универсальное применение и подходит для производства любых изделий с учётом размера паровой камеры: моделей Lost Foam упаковки или любых других изделий из EPS.
Установка включает в себя сварную раму с решетчатыми панелями и дверцами а также подвижную и неподвижную подмодельные рамки которые после крепления к ним половинок пресс- форм образуют соответственно подвижную и неподвижную паровые камеры со встроенными трубопроводами для подачи пара воздуха воды для охлаждения пресс-формы создания вакуума и сброса конденсата. Подвижная подмодельная рамка перемещается по четырем направляющим закрепленным на раме установки с помощью гидроцилиндра который служит и для запирания пресс-формы во время формообразования модели. На раме закреплены также расходный бункер для пенополистирола и манипулятор для извлечения модели. Кроме того в состав установки входит система подачи пара воды вакуумирования а также пневмо- гидро- и электрооборудование.
Для заполнения пресс-формы пенополистиролом используются специальные задувные устройства — инжекторы.
Установка модели К 810 работает следующим образом. С началом автоматического цикла подвижная рама быстро а в конце хода медленно перемещается до смыкания половинок пресс-форм. Одновременно с началом цикла в паровые камеры подается пар для разогрева пресс-формы. По истечении заданного времени подача пара прекращается. После слива конденсата и вакуумирования паровых камер открывается шибер и пенополистирол под давлением сжатого воздуха из бункера подается в пресс-форму. Подача пара для спекания модели вакуумирование паровых камер подача воды для охлаждения пресс-формы и ее слив в зависимости от технологического процесса осуществляются одним из способов предусмотренных на установке. При раскрытии пресс-формы в подвижную паровую камеру подается воздушный импульс для прижатия модели к неподвижной части пресс-формы. Далее подвижный захват манипулятора снабженный вакуумными присосками посредством пневмоцилиндров подводится вплотную к модели извлекает ее из пресс-формы и вынося за пределы установки укладывает в специальную тару или на цеховой транспортер. Установка может поставляться по требованию заказчика без манипулятора. Извлечение моделей в этом случае производится сжатым воздухом или механическими выталкивателями. Техническая характеристика автоматической установки для изготовления моделей из пенополистирола модели К 810.
Основные особенности установки модели К 810:
простота конструкции (при наличии всех необходимых устройств для получения качественных моделей);
жесткость конструкции с четырьмя направляющими обеспечивающая стабильность и высокую точность изготовления моделей;
компактное расположение аппаратуры для подачи пара сжатого воздуха и воды обеспечивающее легкий доступ для осмотра и обслуживания;
наличие манипулятора с вакуумными присосками для съема моделей приспособленного для работы с различными пресс- формами.
На установке модели К 810 можно также изготавливать:
фасонную упаковку для хранения и транспортировки теле- аудио- видеоаппаратуры всевозможных бытовых приборов и т. д.;
легкую прочную и безвредную тару многоразового использования для сбора транспортировки и хранения в подвалах и холодильных камерах овощей фруктов и другой сельскохозяйственной продукции;
декоративные и шумоизолирующие панели с торцевым замком и габаритными размерами 500 х 500 х 15 мм;
теплоизолирующие панели с торцевым замком для жилищного строительства с габаритными размерами 1000 х 800 х 20-100 мм.
Формовочный автомат К 810
Внутренние размеры паровой камеры:
Глубина паровых камер:
Максимальное открывание паровых камер:
Максимальное рабочее давление:
Стандартное напряжение:
Включает в себя следующие позиции:
- гидравлическую систему
- вакуумную систему включающую вакуумный насос 385 кВт и конденсатор
- объемное дозирование охлаждающей воды отдельно
для подвижной и неподвижной стороны
- редуктор паровой камеры для уменьшения расхода пара;
- стандартное электронное управление
- регулировка поперечного пропаривания отдельно для
подвижной и неподвижной стороны;
- охлаждающая проводка на неподвижной стороне паровой
- наполнение формы с подвижной стороны паровой
- регулируемая система механических выталкивателей с
выталкивающей решеткой
- система заполнения под давлением 60л.
Техническое описание:
Основа машины представляет собой жесткую сварную конструкцию из стальных профилей и стального листа. Просторная и просматриваемая основа машины позволяет со всех сторон подойти к гидравлической системе к системе управления а так же к прессовым рамам с подвижной и неподвижной стороны.
Прессовые рамы не оборудованы как паровые камеры а предназначены для использования в качестве закрепляющей площадки для прессформы моноблок. Это позволяет адаптировать различные прессформы моноблок.
Кроме того все существующие системы форм могут быть приспособлены при помощи специальной адаптерной рамы.
Горизонтально расположенная система запирания состоит из подвижной и неподвижной запирающих рам. Подвижная запирающая рама скользит по 4 направляющим посредством направляющих втулок.
Направляющие диаметром 70 мм расположены далеко снаружи от прессовочной поверхности. Решётки безопасности на передней и задней части расположены примерно в 500 мм. от фиксирующей площадки в результате чего появляется возможность установки цилиндров вытяжки стержней во всех направлениях.
Компактный блок со встроенными вентилями управляет паром сжатым воздухом вакуумом а также удалением воздуха из паровой камеры. Все центральные вентили для обеих половинок паровой камеры удобно и компактно расположены что обеспечивает также удобство при профилактических работах.
Привод подвижной запирающей рамы осуществляется посредством 2 гидравлических цилиндров обеспечивающих движение вперед и назад в ускоренном и замедленном режимах и высокое усилие запирания.
Заполнение пресс-формы и выталкивание изделий предусмотрено с подвижной стороны.
Объемное дозирование охлаждающей воды обеспечивает стабильное охлаждение независимо от давления питающей воды и тем самым гарантирует минимальное потребление тепловой энергии при повторяющемся нагревании пресс-формы.
Пульт управления автоматом с микропроцессорным управлением в ручном полуавтоматическом и автоматическом режимах подготовлен для включения в центральную систему управления производственным процессом предприятия со сбором и регистрацией данных. На экране возможна установка в диалоговом режиме и изменение технологических параметров. Это возможно также во время протекания производственного цикла автомата. Отнимающая много времени регулировка концевых выключателей отпадает. Расстояние движений паровой камеры а также величина открывания пресс-формы при заполнении устанавливается путем задачи данных на экране. Кроме того возможно оснащение автомата блоком памяти для хранения данных.
Автоклав WS-150YDA предназначен для тепловой обработки паром пресс-форм при ручном способе изготовления мтоделей. Загрузка и выгрузка пресс-форм осуществляется оператором автоклава (модельщиком). Основные узлы стерилизаторов изготовлены из нержавеющей стали. Время обработки паром давление в камере настраиваются в соответствии с конфигурацией пенополистирольной модели.
В автоклаве можно производить предвспенивание небольших порций полистирола например при отработке технологии на новом сырье.
Технические характеристики автоклава:
Диаметр стеркамеры мм
Номинальная мощность кВт
Высота стерилизатора мм
Ширина стерилизатора мм
Длина стерилизатора мм
Режим обработки паром
2МПа 40~134ºС 0~60мин.
СТОЛ ДЛЯ РЕЗКИ МОДЕЛЕЙ "СРП-КОНТУР
Модели простой конфигурации и литниковая система вырезаются из полистирольного блока на станках при помощи раскалённой Ni-Cr нити.
Рабочее поле 750х490х1350мм
Длина режущих струн1350мм
Потребляемая мощность150Вт
Силовой трансформатор для питания струнв комплекте
Склеивание небольших моделей в блоки производится вручную. Аналогично выполняется литниковая система.
СТАНОК СРП-3221 «МАКСИ-УНИВЕРСАЛ»
Рабочее поле 2200х1100х1500мм
Длина режущих струн1500мм
Потребляемая мощность1300Вт
Подготовка моделей к формовке
Заключительной операцией перед формовкой модели или модельного блока является нанесение противопригарного покрытия к которому при ЛГМ предъявляются особые требования вытекающие из технологии производства отливок и процессов происходящих в формах при заливке их металлом. Противопригарное покрытие наносится на поверхность модели которая имеет низкую шероховатость поэтому покрытие должно хорошо смачивать материал модели образуя с поверхностью прочную адгезионную связь. При формовке модели и уплотнении формы формовочный материал непосредственно воздействует на противопригарное покрытие поэтому оно должно обладать высокой стойкостью к истиранию и достаточной когезионной прочностью. При заливке формы металлом модель дестругирует с образованием парогазовой фазы которая должна свободно транспортироваться из зоны взаимодействия модели с металлом через противопригарное покрытие поэтому покрытие должно обладать достаточной газопроницаемостью. Однако необходимо чтобы пористость покрытия не снижала его технологическую прочность и при сохранении необходимой газопроницаемости обеспечивала получение отливок без пригара.
Свойства противопригарных покрытий которые применяются при изготовлении разовых форм по извлекаемым моделям не соответствуют вышеизложенным требованиям поэтому их не должны использовать при ЛГМ [5 6 14 15].
Рис. 2.33. Газопроницаемость красок на водной а) и спиртовой (б) основах в зависимости от толщины слоя покрытия и вида огнеупорного наполнителя: 1 — перлит; 2 — тальк; 3 — пирофилит; 4 — трепел; 5 — циркон; б — дистен силлиманит; 7 — перлит и маршалит; 8 — графит;
— пылевидный кварц; 10 — без наполнителя
На рис. 2.34 представлено влияние газопроницаемости покрытия на заполняемость формы при различных температурах заливки металла для бронзы и латуни. Зависимость величины давления в зоне взаимодействия модели с расплавленным металлом при его заливке в форму от газопроницаемости покрытия представлена на рис. 2.35.
Приведенные результаты исследования показывают что противопригарное покрытие не только обеспечивает качество поверхности отливки но и непосредственно влияет на основные параметры процесса ЛГМ: скорость заполнения формы металлом температуру заливки заполняемость формы. Следовательно свойства противопригарного покрытия при прочих равных условиях предопределяют формирование отливки ее качество. В подтверждение сказанного в работе [10] установлено что с увеличением толщины слоя противопригарного покрытия и снижением его газопроницаемости увеличивается поверхностное науглероживание отливок из стали. Установлено [10 11] что толщина слоя покрытия на модели должна быть тем больше чем больше пористость формы из песка чем выше температура металла и его гидростатический напор при заливке формы. Рекомендуется найосить на модель слой покрытия толщиной 025-15 мм. Чем выше температура металла и металлостатический напор тем толще должен быть слой краски при сохранении ее газопроницаемости. Взвешивание блока моделей до окрашивания и после сушки покрытия дает массу
Рис. 2.35. Влияние газопроницаемости покрытия на давление газа в форме при заливке металла с Т= 1393 К:
— газопроницаемость 31 см4(г с); 2 — газопроницаемость 1 см4(г с)
К противопригарному покрытию при ЛГМ предъявляются и требования которые при традиционных способах литья не свойственны ему. Покрытие должно повышать жесткость модели увеличивать ее прочность уменьшать возможность деформации стенок модели и элементов литниковой системы при формовке. Исследования показали что увеличение прочности покрытия до 25 МПа увеличивает прочность модели на изгиб при ее плотности 20 кгм3 в 4 раза. Получено уравнение прочности модели с покрытием в зависимости от прочности самого покрытия:
I = 27 + 13 5Xi + 37X2 + 34Хз + 25X2X3 + 26X1X2
где Х — прочность покрытия на изгиб; Х2 — толщина слоя покрытия; Х3 — объемная плотность модели.
Из уравнения следует что прочность системы модель—покрытие в большей степени определяется прочностью покрытия. Для мелкого стального и чугунного литья хорошо зарекомендовали себя быстросохнущие покрытия на основе раствора поливинилбу- тираля в спирте состав которых приведен в табл. 2.21 [7].
Противопригарная краска готовится в краскомешалках.
Размер: 600x500мм. Мощность двигателя 4кВт.
Поставляется в комплекте со шкафом управления.
Готовые модельные блоки красятся противопригарным покрытием после чего производится сушка.
После сушки модельный блок готов к формовке.
Оборудование для формовки заливки охлаждения и выбивки отливок
Для изготовления литейных форм из сухого кварцевого песка применяются вибрационные столы различной конструкции. Простейший вибростол структурная схема которого представлена на рис. 7.29 включает в себя плиту 1 с двумя электрическими вибраторами 3 вращающего действия установленную с помощью пружин 6 на втулках 2 основания 7. На плите 1 предусмотрены ограничители 5 для установки опоки и подкладки 4 из твердой резины для уменьшения шума при работе стола. Вибраторы вращаются в разные стороны и установлены так что результирующая сила приложена к середине линии соединяющей центры вибраторов и всегда перпендикулярна к ней. На механизированных линиях обычно вместо ограничителей используют центрирующие штыри и во избежание отрыва опоки от опорной поверхности плиты 1 применяют устройства для закрепления опоки во время вибрации чаще всего гидрозажимы.
Рисунок вибростол Модель: SZ-04K
Вибростол работает благодаря 6 вибродвигателям. Каждая пара синхронно вращается в противоположных направлениях образуя 3 осевых направления (X Y Z) что позволяет поверхности стола и установленной на ней опоке вибрировать с определенным ускорением завершая уплотнение песка внутри опоки. Время по каждой оси можно настроить в соответствии с технологией получения отливки.
Технические характеристики:
Грузоподъемность: 5 т
Размер рабочего стола: 1720х1820х750 мм
Работа указанного модуля осуществляется следующим образом. Оператор с помощью соответствующих кнопок на пульте управления включает вибраторы и цилиндр подъема вибростола в результате чего опока находящаяся на позиции вибростола под бункером поднимается над рольгангом. Открывается шиберная заслонка и песок поступает в опоку до образования в ней уплотненной подушки из песка высотой до 50 мм. Затем опока опускается на рольганг и «ручную перемещается от бункера на свободную позицию. Здесь оператор устанавливает куст моделей на песчаную постель и во избежание опрокидывания куста фиксирует его относительно опоки с помощью специального приспособления. Далее опока перемещается оператором под бункер вибростол поднимает опоку и при включенных вибраторах производится засыпка песка и его уплотнение в опоке. После формовки опока перемещается оператором в зону заливки минуя позицию опрокидывания. Аналогичным образом после формовки в зоне заливки устанавливается вторая опока. В случае изготовления отливок из черных сплавов опоки соединяются оператором с системой вакуумирования после чего производится заливка их металлом. После выдержки для остывания отливок опоки перемещаются на позицию опрокидывания где опока освобождается от песка и отливки и цикл повторяется.
Для увеличения производительности работа может быть организована иначе. После формовки и заливки опоки тельфером снимаются с рольганга формовочно-заливочного модуля и устанавливаются на плацу цеха для остывания отливок. В этом случае может быть задействовано большое количество опок. Производительность при этом увеличивается до 10 съемов в час.
Технология формовки в серийном производстве
В серийном производстве применяются формы из сыпучих огнеупорных материалов к которым предъявляются следующие требования:
формовочный материал должен обладать хорошей текучестью обеспечивать заполнение отверстий и внутренних полостей модели при вибрации;
гранулометрический состав сыпучего огнеупорного материала должен после вибрации обеспечить максимальную плотность формы при минимальной пористости и высокую газопроницаемость;
материал должен обладать минимальным пылеобразованием в процессе формовки и последующей регенерации содержание фракций размером менее 005 не допускается или должно быть предельно минимальным (не более 05 %);
влажность материала не должна быть более 10 %;
огнеупорность материала должна быть выше температуры заливаемого в форму металла;
материал должен быть недефицитным и недорогим;
материал не должен оказывать вредного влияния на здоровье человека.
Вышеперечисленным требованиям в большей степени удовлетворяет кварцевый песок класса 061К-063К и 1К-ЗК зернистостью 020 и 016 (ГОСТ 2138-74) категории А или Б с остроугольной или округлой формой зерна. Для повышения плотности формы при виброуплотнении применяются смешанные пески двух фракций 0315 и 016 в соотношении 1:1 при этом при низкой пористости сохраняется высокая газопроницаемость. Для получения отливок с повышенными механическими свойствами применяются металлические колотые и литые дроби марок ДСК-03 и ДЧК-03 которые соответствуют фракционному составу кварцевого песка марки 1К0315.
При производстве отливок из стали применяют цирконовые пески которые обладают высокой огнеупорностью (до 2000 °С) низким коэффициентом теплового расширения и более высокой по сравнению с кварцевым песком теплопроводностью [9]. Некоторые зарубежные фирмы применяют для формовки оливиновые пески которые имеют повышенную огнеупорность низкую химическую активность не вызывают заболеваний силикозом.
Однако использование природных сыпучих огнеупорных материалов (песков) при ЛГМ показало что они не полностью соответствуют вышеперечисленным требованиям. Кварцевые пески имеют повышенный коэффициент расширения при нагревании что приводит как к снижению точности отливок так и к образованию поверхностных дефектов при литье из черных сплавов. Кроме того в силу своей угловатости эти пески плохо уплотняются в узких каналах для них характерно повышенное пылеобразование в процессе эксплуатации.
В 1994 г. университетом Бирмингема (шт. Алабама США) были представлены материалы по разработке двух марок синтетического огнеупорного керамического материала специально созданного для ЛГМ-процесса. Исходным сырьем являются порошкообразные алюмосиликаты из которых при помощи связующего и воды формируют мелкие округлые частицы потом гранулы сушатся и спекаются при температуре 1470-1649 °С. Затем материал рассеивается по фракциям. В процессе спекания материал зерна приобретает кристаллическую структуру высокую твердость износостойкость и термическую стабильность низкий коэффициент термического расширения и высокую способность к регенерации. Округлая форма зерен обеспечивает хорошую текучесть и уплотняемость вибрацией. Были представлены две разновидности керамического материала: ID и LD химический состав которых представлен в табл. 6.4 термические свойства — в табл. 6.5 минералогический состав — в табл. 6.6 физические свойства — в табл. 6.7. Исследование гранулометрического состава и газопроницаемости проводилось по системе компьютерного моделирования литейных процессов AFS принятой в США. Всего было представлено по 6 марок каждого материала которые отличались зерновым составом и соответствовали отечественным пескам зернистостью от 063 до 016.
диплом не отредоктирован Калиев М. М..docx
Общая пояснительная записка6
Технико - экономическая часть7
2 Расчет годовых эксплуатационных расходов7
3 Калькуляция себестоимости товарной продукции8
4 Расчет оптовой стоимости готовой продукции10
5 Расчет технико – экономических показателей10
1 Генеральный план10
Технология производства. Обеспечение энергоресурсами.11
1 Технология производства11
1.1 Перспективы развития черной металлургии11
1.2 Общая характеристика проектируемого литейного цеха11
1.3 Режим работы цеха11
2.1 Расчет производительности цеха 11
2.2 Расчет количества необходимого оборудования11
2.3 Расчет шихты для выплавки стали 35ХМЛ 45Л 110Г13Л45
2.3.1 Расчет плавки. Материальный баланс 12
2.3.2 Тепловой баланс плавки13
Организация труда и система управления предприятием13
1 Организация труда13
2 Система управления предприятием14
Строительная часть14
1 Архитектурно-строительные решения14
2 Отопление вентиляция и конденционирование14
3 Водоснабжение и канализация14
Специальная часть 15
Казахстана является одной из богатейшей Республикой. По залежам полезных ископаемым и перерабатывающей индустрии. Металлургическая отрасль в отдельных регионах обеспечивает до 85% промышленного производства области. За счет налоговых поступлений у предприятий металлургического комплекса обеспечивается наполнение большого количества местных и региональных бюджетов. Кроме того отрасль дает значительные валютные поступления от экспорта продукции на внешние рынки.
В связи с условиями в которых развивалась отрасль сложилась ситуация когда предприятия черной металлургии зачастую являются градообразующими а потому эффективное развитие отрасли является залогом успешного функционирования предприятий. Последнее гарантирует сохранение рабочих мест что очень важно для многих регионов Казахстана.
В настоящее время около половины произведенной продукции отправляется на экспорт. Это является следствием с одной стороны избыточных производственных мощностей а с другой резкого сокращения емкости внутреннего рынка из – за экономического кризиса последовавшего вслед за распадом СССР. Таким образом наряду с нефтяной и газовой отраслями черная металлургия обеспечивает сырьем многие страны мира подтверждая тем самым сложившийся статус Казахстана как сырьевого придатка развитых стран. В результате сложилось противоречие: с одной стороны дальнейшее развитие отрасли ведет экономику Республики Казахстан так и в странах СНГ возникла необходимость решения сложнейших задач которые встали перед металлургией при переходе к рыночной экономике в условиях глобализации. Это осложняется высоким физическим и моральным износом технологического оборудования относительно малой долей продукции с высоким качеством продукций. Поэтому металлургическая отрасль Казахстана и стран содружества независимых государств нуждается в серьезной реструктуризации для которой необходимы качественные проекты соответствующие требованиям постиндустриального общества.
Необходимость изучения основ проектирования металлургических объектов вызвана как изменениями так и новизной самого подхода к проектированию отдельных установок и сооружений; участков отделений цехов производств определяемого оригинальными требованиями принятия инвестиционного решения в условиях рынка сопряженного во времени и согласованного с административно – надзорными и другими участниками инвестиционного процесса. Интеграция системы проектирования в мировую систему предполагает соединение традиционного подхода к проектированию с новыми взглядами на такие системы как металлургический комплекс в целом. Это не отменяет некоторой стадийности: необходимости появления инвестиционного замысла и документального его оформления выполнения технико – экономических и иных обоснований строительства нового объекта или модернизации существующих; разработки документации детализирующей технические решения до установки конкретной единицы оборудования и привязки его к обеспечивающим сетям.
С улучшением внешнего вида а следовательно с повышением конкурентоспособности изделий повысились требования к качеству поверхности и внешнему виду отливок.
Неоспоримо время диктует внедрением литейного оборудования экономичного безопасного экологического не требующие большие ресурсы уменьшением числа работающих.
Литье по газифицируемым моделям (ЛГМ) является одним из новейших способов производства отливок появившихся в результате научно-технической революции во второй половине XX в. наряду с такими технологическими процессами как вакуум - пленочная формовка непрерывное литье литье под низким давлением импульсная формовка и др. Однако наибольший интерес у литейщиков вызвало сообщение о способе литья по моделям которые не удаляются из формы а остаются в ней и газифицируются под действием тепловой энергии металла заливаемого в форму. Такая технология названная литьем по газифицируемым моделям решала важнейшую задачу литейного производства — повышение точности отливок до уровня литья по выплавляемым Моделям при издержках производства литья в песчано-глинистые формы.
Но прежде чем ЛГМ-процесс стал промышленной технологией был проделан значительный объем научно-исследовательских и опытно-конструкторских работ в результате которых были созданы специальные модельные материалы и противопригарные покрытия технология и оборудование для изготовления моделей инженерная методика проектирования технологического процесса Оборудование для изготовления форм и т. д.
В развитии ЛГМ-процесса можно условно выделить четыре периода. Первый период охватывает 1958-1970 гг. и характеризуется внедрением данной технологии для производства единичных отливок массой от нескольких килограмм до Юти более. Первая промышленная отливка массой 12 т была получена в Германии в 1962 г. Спустя год для фирмы «Ford Motors Со» были отлиты две заготовки для штампов массой 6750 и 2700 кг. К концу 1964 г. в 10 литейных цехах различных фирм США применялся ЛГМ-процесс для производства единичных отливок [3]. Активные работы по внедрению ЛГМ проводились в ФРГ группой специалистов возглавляемой проф. А. Виттмозером которая в 1958 г. приобрела права на патент Шроера. В 1965 г. в таких промышленно развитых странах как США Англия ФРГ Франция и Япония было произведено более 40 тыс. т отливок причем только в США данный способ литья для производства отливок из черных сплавов применяли 35 литейных цехов [4]. В 1963 г. на Международной выставке в Дюссельдорфе экспонаты по ЛГМ-процессу были широко представлены различными фирмами. В 1967 г. создается Международная ассоциация литья по газифицируемым моделям которая объединила 150 фирм с общим выпуском отливок 800 т в сутки. Быстрое распространение ЛГМ для производства единичных отливок из черных сплавов стало возможным благодаря явным преимуществам данного способа по сравнению с литьем по извлекаемым моделям. Главными из этих преимуществ являются: снижение трудоемкости и стоимости изготовления моделей увеличение точности отливок и снижение их массы уменьшение трудоемкости изготовления форм и значительное сокращение цикла изготовления литых заготовок начиная с разработки технологии и заканчивая получением отливки.
Наряду с расширением производства единичных отливок многие научные центры различных фирм проводили интенсивные работы по применению ЛГМ в серийном производстве чему способствовало опубликование в 1960 г. патента X. Неллина о применении песка без связующего для изготовления формы [6]. По данному патенту модель из пенополистирола помещается в контейнер засыпается сухим песком или другим сыпучим огнеупорным материалом и форма уплотняется вибрацией после чего она заливается металлом. Однако применение данного способа для получения отливок сложной конфигурации приводило к браку из-за обвала формы. Поэтому исследования были направлены на изыскание способа упрочнения формы из несвязанных сыпучих материалов. Так в 1966 г. был опубликован патент Гофмана на способ получения отливок по газифицируемым моделям в магнитной форме [7]. На 35-м Всемирном конгрессе литейщиков проф. А. Виттмозер впервые сделал доклад о магнитной формовке. При данном способе изготовления формы применяется металлический ферромагнитный песок или дробь размером 03-05 мм. После уплотнения формы вибрацией она помещается в постоянное магнитное поле которое обеспечивает магнитную связь между частицами наполнителя что придает форме необходимую прочность предотвращая ее разрушение при заливке металла. Магнитная формовка получила применение в США Японии и в странах Западной Европы для производства серийных отливок из различных сплавов. В 1970 г. в разных странах работало более 10 полуавтоматических установок магнитной формовки. Швейцарская фирма «Brown Bovery» организовала серийное производство полуавтоматических установок магнитной формовки. В Бельгии одна из фирм применяла магнитную формовку для отливки стальной цепи из 40 тыс. звеньев в Англии другая фирма получала тормозные колодки для железнодорожного транспорта в ФРГ изготавливались магнитной формовкой тройники из серого чугуна массой до 20 кг и муфты из высокопрочного чугуна в Нидерландах — сложные тонкостенные отливки из чугуна [8]. В Японии работала линия магнитной формовки производительностью 20 форм в час при металлоемкости одной формы до 70 кг [9]. Однако магнитная формовка не получила должного применения т. к. использование дорогостоящего металлического песка (дроби) сводило на нет экономические преимущества ЛГМ относительно традиционных способов литья хотя и обеспечивало более высокое качество отливок. Этому способствовало и появление в 1968 г. патента на способ получения отливок по газифицируемым моделям в формах из песка с применением вакуума [10]. Согласно патенту для формовки используется специальный контейнер оборудованный системой вакуумирования. Газифицируемая модель заформовывается в кварцевом песке который уплотняется вибрацией. Сверху на форму накладывается полиэтиленовая пленка после чего форма вакуумируется и заливается металлом. Считается что вакуум предохраняет форму от разрушения во время ее заливки расплавом.
В научно-исследовательском центре фирмы «Ford Motors» проводились работы по применению ЛГМ для получения отливок из серого и высокопрочного чугунов и алюминиевых сплавов широкой номенклатуры деталей автомобиля (сплошные и полые коленвалы зубчатые колеса шатуны коллекторы головка и блок цилиндров и др.). Соответствующие работы проводились фирмами «Fiat» «General Motors» «Jut Board Marine» «Deereand Co» «Агсо» и мн. др.
К концу 1970-х гг. уже более чем в 70 литейных цехах различных фирм технология ЛГМ находилась на стадии внедрения или осуществлялся выпуск серийных отливок в промышленных масштабах [12]. Накопленный за это десятилетие научный и практический опыт применения ЛГМ для получения отливок из черных и цветных сплавов стал основой для внедрения данной технологии в серийном производстве широкой номенклатуры отливок в различных отраслях машиностроения в 1980-е гг. которые определяют третий период в развитии ЛГМ-процесса. Наибольшие успехи во внедрении ЛГМ были достигнуты автомобильными фирмами. Фирма «Ford Motors» в 1980 г. освоила промышленную установку для производства отливок впускного коллектора из алюминиевого сплава и выпустила 25 000 коллекторов высокого качества. В 1984 г. в этом же цехе была установлена вторая полуавтоматическая линия производительностью 180 форм в час на которой производство коллекторов было доведено до 3 млн в год при этом максимальный брак литья составлял около 5 %. На старой установке было освоено производство отливок из чугуна: корпус водяного насоса тормозной диск выхлопной коллектор полый коленвал. Данный цех имел производственную площадь 2700 м2 и являлся в то время самым крупным литейным цехом по производству отливок ЛГМ [13]. Фирма «General Motors» в 1982 г. на предприятии «Сатурн» установила автоматическую линию производства ЛГМ головки и блока цилиндров из алюминиевого сплава для дизельного двигателя в количестве 1000 отливок в сутки при трехсменной работе. В настоящее время в цехе работают две автоматические линии. На второй линии получают отливки из чугуна: коленвал корпус дифференциала впускной коллектор и др. В цехе автоматизированы все технологические операции за исключением заливки форм металлом. Отмечается высокое качество отливок которые по точности соответствуют литью под давлением а по качеству поверхности — литью в кокиль. Фирма успешно решила экологическую проблему. При вакуумировании форм во время заливки их металлом продукты термодеструкции модели поступают в установку каталитического дожигания газов до углекислого газа и паров воды. В цехе работает 180 человек (по 60 в каждой смене). Цех расположен под одной крышей с механическим цехом что говорит об экологической чистоте производства отливок ЛГМ [14]. Фирма «Robert's Со» изготовила и освоила шестипозиционную установку производительностью 180 форм в час. Модельные блоки подаются по монорельсу и манипулятором устанавливаются в опоку- контейнер который засыпается сухим кварцевым песком посредством телескопической трубы-дозатора. Форма уплотняется вибрацией с регулируемым направлением и величиной амплитуды. После заливки формы и извлечения отливки из нее песок поступает в установку кипящего слоя в которой он обеспыливается а содержащиеся в нем продукты термодеструкции мод еда дожигаются. После охлаждения песок вновь поступает на формовку [15]. Эта же фирма заключила соглашение с фирмой «Badine Aluminum» о создании совместного предприятия по производству отливок из алюминиевых сплавов. Новое предприятие оснащено формовочной линией производительностью 30 форм в час с размером контейнера в плане 1016 х 813 мм. Предприятие обеспечивает литьем свыше 10 потребителей которые производят строительные машины электродвигатели и детали для ЭВМ.
По мнению американских специалистов ЛГМ-процесс является одним из лучших современных способов литья который может удовлетворить потребности крупносерийного производства отливок высокой точности. В сочетании с системой автоматического управления на базе микропроцессорной техники и роботов применение данного способа литья позволит создать гибкое производство отливок. Такое положение основано на единой опоке в которой используется весь ее объем в отличие от разъемной формы едином формовочном материале — песке простоте формовки неограниченном сроке хранения моделей и недорогой оснастке [15].
В 1990-е гт. ЛГМ находит широкое применение в Японии Корее и Китае. В Японии около 200 фирм используют ЛГМ для производства отливок из различных сплавов. Фирма «Morikawa Sandino» в кратчайший срок приобрела репутацию лидера в производстве отливок ЛГМ и стала ведущей фирмой в разработке технологии и оборудования для данного способа производства отливок. В 1984 г. она начала проводить исследования данного процесса а уже в 1985 г. стала производить в промышленном масштабе втулки подшипника для двигателя «Honda» гильзы цилиндров из фос- форванадиевого чугуна коробку дифференциала из высокопрочного чугуна впускные коллекторы из алюминиевого сплава [16]. В КНР создано специализированное предприятие по производству отливок соединительных деталей трубопровода [17]. Фирма «Dong Кик» (Корея) освоила производство фитингов из высокопрочного чугуна по газифицируемым моделям. В 1988 г. в промышленно развитых странах производство отливок ЛГМ осуществлялось более чем в 100 литейных цехах с месячным выпуском 400 т чугунного и 2000 т алюминиевого литья. Еще в 100 литейных цехах велись опытно-промышленные работы по освоению производства отливок из различных сплавов [18]. В Англии в конце 1980-х гг. было сдано в эксплуатацию шесть опытно-промышленных установок для изготовления отливок данным способом. По данным зарубежных специалистов количество цехов работающих по технологии ЛГМ в ближайшие несколько лет будет ежегодно удваиваться [18].
Расширению объемов производства отливок ЛГМ в различных странах способствовало дальнейшее совершенствование технологии и оборудования. Так фирмы «Castek» (Англия) и «Teksid» (Италия) разработали технологический процесс под фирменным названием Policast который включает в себя технологию изготовления моделей сборку модельных блоков их окраску и формовку заливку формы металлом. Фирмы «FATA» и «Fiat Teksid» построили в Италии два цеха для производства коллекторов автомобильных двигателей по Policast-wpoiiQCcy. В одном цехе выпускаются выхлопные коллекторы из серого чугуна на автоматической линии производительностью 40 форм в час причем в форме одновременно отливаются 8 коллекторов. В другом цехе на автоматической линии производительностью 50 форм в час отливаются впускные коллекторы из алюминиевого сплава.
Ассоциация «SCRATA» (Steel Casting Rusers and Trade Association) разработала технологический процесс ЛГМ под фирменным названием Replicast в двух вариантах. При Replicast-FM модель из пенополистирола с литниковой системой устанавливается в контейнер и засыпается сухим песком который затем уплотняется вибрацией. Верх контейнера закрывается полиэтиленовой пленкой и в форме создается вакуум порядка 004-005 МПа после чего форма заливается металлом. Такая технология ЛГМ позволяет получать отливки в форме из песка массой до 2 т что значительно расширяет область применения ЛГМ-процесса. Способ Replicast-CS (Shell moulding refractory) разработан для производства отливок из высококачественных малоуглеродистых сталей и других сплавов которые чувствительны к продуктам термодеструкции пенополистирола. По данному способу на модель из пенополистирола повышенной плотности (40-50 кгм3) наносится керамическая оболочка из 4-5 слоев как при литье по выплавляемым моделям. Толщина оболочки составляет 32-47 мм. Затем полученная керамическая форма помещается в печь где при температуре 9300 °С происходит спекание оболочки и выгорание модели. Полученная керамическая оболочка помещается в контейнер засыпается кварцевым песком который уплотняется в контейнере вибрацией затем полученная форма накрывается полиэтиленовой пленкой и перед заливкой формы металлом в ней создается вакуум порядка 004-005 МПа. Такая технология позволяет получать точные и качественные отливки из низкоуглеродистых марок стали без поверхностного и объемного науглероживания. Ассоциация «SCRATA» передала все права на продажу лицензии по Replicas t-процессу фирме «Foseco International» которая за короткое время реализовала 13 лицензий. Фирма «Glencast Ltd» по лицензии фирмы «Foseco» производит до 90 % заготовок штампов. Аналогичные отливки данным способом получает фирма «Haffer- sley Neuman Hender» [20]. Фирма «Bradey and Foster» (Англия) на линии производительностью 6 форм в час получает литьем по газифицируемым моделям в вакуумируемые формы из песка крупные отливки из жаро- и износостойких чугунов. Это позволило ей полностью отказаться от стержней а в ряде случаев и от механической обработки при этом трудозатраты на очистку отливок сократились на 29 % на формовку — на 28 % на механическую обработку — на 9 %. Точность отливок возросла на 13 % [20].
Фирма «Wolverhampton Iron Founders» производит отливки ЛГМ массой от 022 до 70 кг. Модели из пенополистирола поставляет фирма «Foseco». На модели наносится противопригарное покрытие и затем с литниковой системой они устанавливаются в контейнер емкостью 1 м3 в котором заформовываются сухим песком.
Формовка заливка формы металлом охлаждение отливки в форме и ее выбивка производятся на горизонтально замкнутом конвейере. На позициях заливки и охлаждения формы вакуумируются. Цикл изготовления одной формы составляет 7 мин. Применение ЛГМ позволило в 3 раза повысить точность отливок и на 40 % сократить трудоемкость финишных операций. Фирма освоила производство отливок из высокопрочного чугуна и легированной стали [20].
За последние 40 лет на основе применения газифицируемой модели были разработаны технологические процессы которые предопределили широкое внедрение ЛГМ в промышленность (табл. 1).
Таблица 1 Перечень различных способов литья по газифицируемым моделям
Литье по газифицируемым моделям (ЛГМ)
Обобщенное название всех способов литья по газифицируемым моделям
ЛГМ в формах из сухого песка без связующих компонентов
Единичное серийное и крупносерийное производство отливок из СЧ ВЧ КЧ и стали медных и алюминиевых сплавов при массе отливок до 50 кг
ЛГМ в формах из песчано- глинистой формовочной смеси
Единичное производство отливок из черных и цветных металлов массой до 500 кг
ЛГМ в формах из жидких самотвердеющих смесей
Единичное производство отливок из черных металлов массой до 5000 т
ЛГМ в формах из холоднотвердеющих формовочных смесей
Единичное производство отливок из черных металлов массой до 30 т
ЛГМ в формах из ферромагнитных сыпучих материалов в магнитном поле магнитная формовка
Серийное и крупносерийное производство отливок из черных и цветных сплавов массой до 50 кг
ЛГМ в формах из песка с применением вакуума
Единичное серийное и массовое производство отливок из черных и цветных сплавов массой по чугуну до 2000 кг
ГАМОЛИВ-процесс — фирменное название ЛГМ в формах из песка с применением вакуума
Производство серийных отливок из чугуна массой до 2000 кг
ГАМОДАР-процесс — фирменное название ЛГМ в формах из песка с применением вакуума и регулируемого давления при заливке металла
В серийном производстве отливок из черных и цветных сплавов массой по чугуну до 20 кг
Policast — фирменное название ЛГМ-процесса при котором модели собираются в куст на стояке
Серийное и крупносерийное производство отливок в основном из алюминиевых сплавов
Replicast-FM— фирменное название производства отливок в формах из песка с применением вакуума
Серийное и крупносерийное производство отливок из черных и цветных сплавов
Replicast-CS-mpouficc — фирменное название процесса литья с применением пенополистиро- ловой модели которая предварительно удаляется из керамической формы при ее прокаливании. Затем оболочка заформовывается в песке и форма вакуумируется
Серийное производство отливок из низкоуглеродистых и легированных сталей
ЛГМ с заливкой формы методом вакуумного всасывания
В серийном производстве отливок из черных и цветных сплавов массой до 5 кг
ЛГМ с применением изостатиче- ского давления в процессе кристаллизации металла
Серийное производство отливок из алюминиевых сплавов
Литье по газифицируемым моделям по Stirocast-процессу (гарантия качества)
Серийное производство отливок из черных и цветных сплавов
Общая пояснительная записка
Завод Казогнеупор - единственное предприятие производящее огнеупорные смеси и изделия на территорий Казахстана. Завод введен в эксплуатацию в 1980 году. Полностью обеспечен местными казахстанскими ресурсами: глиноземом Павлодара высокоглиноземистые глины Костаная и Аркалыка. Завод оснащен современным оборудованием в том числе и импортным (прессы Laeis Bucher Fukai) тепловым оборудованием обеспечивающим рабочую температуру до 1750 оС. Технологический процесс заключается в плавке глинозема на корунд обжиге глин и бокситов на шамот в получении порошков требуемого зернового состава изготовлении из них огнеупорных изделий набивных масс мертелей с использованием технологических добавок
Более двух десятилетий занимается производством огнеупорной продукции алюмосиликатного состава которая используется для футеровки доменных мартеновских сталеплавильных и цементных печей сталеразливочных ковшей и других тепловых агрегатов. Строительство завода «Казогнеупор» начато в 1976 г. В декабре 1978 года выпущена первая продукция в экспериментальном цехе. Через 2 года введен в строй цех электроплавленых огнеупоров. Цех корундомуллитовых огнеупоров.
Завод «Казогнеупор» болеупоров запущен в 1987 году. За период работы завода были достигнуты значительные показатели по выпуску товарной продукции. В конце 80-х и в начале 90-х годов объем производства достигал около 100 тыс. тонн огнеупоров в год. Но был тяжелый период который длился почти 2 года когда завод переживал процесс банкротства и конкурсное управление. Возрождение завода началось с декабря 2000 года. В течение двух лет шло восстановление оборудования и технологических линий. В сентябре 2002 года завод возобновил производство товарной продукции основную часть которой составляют неформованные огнеупоры: порошки плавленого корунда муллита шпинели набивные массы бетонные смеси и мертели.
В настоящее время на заводе работают опытные специалисты давно работающие в огнеупорном производстве. Решен вопрос по обучению квалифицированных рабочих непосредственно на предприятии.
ТОО "Завод Казогнеупор" основан в 1980 году
Огнеупоры — формованные изделия и неформованные материалы используемые при различных технологических процессах проходящих при высоких температурах. Огнеупоры используются для защиты основных материалов тепловых агрегатов и окружающей среды от теплового воздействия.
Наиболее стойкими к высоким температурам (1750—1800°С) считаются корундовые высокоглиноземистые огнеупоры с содержанием Аl2О3 более 95%. Они почти универсальны для использования и пользуются сегодня повышенным спросом.
ТОО «Завод Казогнеупор» реализует следующую продукцию:
— массы корундовые и муллитокорундовые набивные предназначены для выполнения монолитных футеровок сталеразливочных ковшей электропечей и других тепловых агрегатов;
— изделия высокоогнеупорные муллитокорундовые на фосфатной связке используются для кладки воздухонагревателей и воздухопроводов горячего дутья доменных печей а также для футеровки различных тепловых агрегатов и других целей;
— порошки плавленых материалов применяются при изготовлении огнеупорных изделий и бетонов;
— глина сухая молотая незаменима в качестве связующего компонента при приготовлении растворов для кладочных штукатурных и облицовочных работ связанных с высокими температурными режимами до 1600o С;
— областью применения высокоглиноземистого цемента является производство жаростойких огнеупорных бетонов а также жаростойких сухих строительных смесей;
— заполнители огнеупорные корундовые сферические применяются главным образом для футеровки высокотемпературных пламенных и электрических печей для подставок при обжиге специальных изделий и различного вида изоляторов;
— смеси огнеупорные алюмосиликатные бетонные используются как для футеровки промышленных тепловых агрегатов так и для кладки высокотемпературных участков бытовых печей;
— мертели огнеупорные алюмосиликатные применяются в качестве связующего элемента алюмосиликатных изделий в огнеупорной кладке и заполнение швов.
ТОО «Завод Казогнеупор» единственное в Казахстане предприятие которое выпускает широчайший диапазон огнеупорной продукции на основе собственного корунда и шамота.
Коллектив ТОО «Завод Казогнеупор» - это огромный опыт и трудовые традиции складывающиеся десятилетиями. Инженерно-технический персонал завода вместе с квалифицированным рабочим составом отличается высокой степенью организации труда современным технологическим и испытательным оборудованием оснасткой и технологией то есть всем необходимым для обеспечения выпуска качественной продукции.
Со времен основания завод держал курс на созидание и на удовлетворение требований потребителей. За годы существования на рынке зарекомендовал себя как надежный поставщик качественной огнеупорной продукции. Физические и химические показатели нашей огнеупорной продукции выделяют её на внутреннем и на внешнем рынке.
Технико – экономическая часть
Бизнес – план по своей сути – это документ описывающий все основные аспекты будущего коммерческого предприятия с анализом проблем которые встретятся на пути реализации проекта и установлением способов решения этих проблем.
Но в то же время в нем имеются и значительные отличия в первую очередь связанные с оценкой рынка сбыта готовой продукции его емкостью и перспективой развития ибо здесь лежат наибольшие трудности в точности определения номенклатуры и объема производства и велика вероятность ошибки в величине объема сбыта.
Во вторую очередь бизнес – план должен оценить те затраты которые необходимы для начала производства поддержания его на должном уровне обеспечении сбыта производимого товара. При этом требуется сопоставление цены вновь производимой продукции с ценами по которым она может быть продана а значит определить прибыльность реализуемого проекта.
В третью очередь в нем должны быть установлены показатели по которым можно определить идет ли дело на подъем или уже начался спад и снижение эффективности производства.
В четвертую очередь в нем должны быть проанализированы главные проблемы с которыми может столкнуться инвестор и должны быть даны основные способы решения этих проблем.
Бизнес – план выполняет три основные функции:
– является инструментом с помощью которого инвестор может оценить фактические результаты проекта за определенный период;
– используется для разработки инвестирования в перспективе при дальнейшем развитии проекта строительства или реконструкции;
– является необходимым документом способным убедить потенциального инвестора в перспективности поддержки предлагаемого проекта.
В техно – экономической части основные вопросы рассматриваемые в проекте.
Характеристика предприятия наличие технических возможностей по выполнению разрабатываемой производственной программы повышения произведенной продукций увеличения объемов продаж схема управления предприятием вид оплаты стимулирования работников.
а.Выбор технологического процесса наиболее целесообразного для выполнения рассматриваемой производственной программы. Преимущества связанные с уникальностью продукции (сегмента): специалисты своего дела хорошая репутация фирмы – более долгосрочные контракты на поставку литья так как чтобы сравняться с результатами конкурентов необходимо либо разработать аналогичную продукцию либо придумать что – то более – лучшее и оригинальное на что потребуется время и дополнительные деньги. Значит если идти по этому пути конкурентоспособность будет гарантирована более устойчиво и на длительное время.
б.Выбор основного технологического оборудования (тип технические характеристика (марка) и возможность его приобретения по приемлемым ценам) какие потребности призвано удовлетворить наше литье в чем его особенность и чем оно будет отличаться от литья ваших конкурентов почему потребитель отдаст предпочтение нашему литью а не их как долго сохранятся преимущества нашего литья.
в.Состав цеха и компоновочные схемы кооперирование вспомогательных и обслуживающих хозяйств с указанием на долевое участие их в производстве продукций.
г.Долгосрочные договора снабжения исходными материалами электроэнергией и другими энергоресурсами в том числе водой.
д.Экологией района и воздействием проектируемого цеха на неё дается перечень мероприятий по защите воздушного и водного бассейнов.
е.С выбором площадки для складирования готовой продукций принятия основной транспортной схемы обеспечения предприятия (железнодорожной автомобильной смешанной) складирования отходов производства (отвалов) и долевого участия в строительстве внеплощадочных дорог и транспортных сооружений.
ж.С установлением численности обслуживающего и производственного персонала и возможностью их профессионального обучения.
з.Обоснование потребности продукции нового или реконструируемого цеха как по номенклатуре и массе отливок так и общему количеству продукции. Маркетинговое исследование которое позволит спрогнозировать объем продаж а следовательно и производства продукции. Здесь же следует объективно отразить возможности ваших конкурентов по производству продукции её качеству и примерным ценам. Это позволит будущему инвестору оценить полноту представления о рыночной номенклатуре и степени проработки вашего проекта. Подготовка таких сведений требует больших исследований и возможна силами специальных отделов по маркетингу при этом можно воспользоваться мнением экспертов по данному вопросу.
и.Определяющим обстоятельством при этом становится обеспечение конкурентоспособной продукции как в ближайшей перспективе так и на будущее развитие краткое содержание информаций о той цене по которой должен будет продаваться ваш товар затратах которые потребуются на его производство и примерная величина прибыли от каждой единицы произведенного товара.
к.Выбора наиболее приемлемого варианта проекта устанавливаются по укрупненным показателям технико – экономические показатели проектируемого цеха и проводится их сравнение с лучшими показателями по отрасли и мировыми показателями.
В заключении ТЭО содержатся выводы и предложения по экономической целесообразности строительства или реконструкции объекта.
Бизнес – план должен заканчиваться заключением после проведения всестороннего анализа проделанной работы. В заключение в четкой сжатой форме должны быть изложены. Основные результаты вашего исследования доступно и понятно изложены основные преимущества вашего проекта и за счет чего ваш продукт (литьё) будет пользоваться устойчивым спросом на рынке.
В самом конце заключения необходимо привести финансовые результаты которые вы ожидаете от вашего проекта.
Заключение должно дать четкое представление о том что будет производиться как и какого качества и что вложения в этот проект непременно дадут прибыль а риск вложений будет минимальным.
Производительность литейного цеха по выпуску годного литья в год согласно заданию на проектирование.
В СНГ – как высокомарганцевая сталь 110Г13Л. За прошедшее время проведено большое количество работ по исследованию стали 110Г13Л улучшению ее свойств а также созданию новых марок износостойких сталей взамен нее. Однако до сих пор сталь Гадфильда является основным материалом для изготовления отливок работающих при ударно – абразивном изнашивании. Из нее получают около 06 млн т литья в год.
Износостойкая сталь 110Г13Л содержит в своем составе 09 – 15 % С 115 – 15% Мn 03 – 10% Si до 005% S до 012% Р. Как правило соотношение Мn : С должно быть больше 10.
Из нее изготавливают корпуса вихревых и шаровых мельниц щеки дробилок трамвайные и железнодорожные стрелки и крестовины гусеничные траки зубья ковшей экскаваторов и другие детали работающие на износ.
После термической обработки сталь имеет следующие свойства:
в = 800 1000 МПа 1 = 250 400 МПа = 35 45 % = 40 50%
НВ = 170 230 KCU = 2000 3000 кДжм2.
Сочетание высокой износостойкости в случае приложения больших истирающих нагрузок когда твердость поверхностных слоев может достигать 550 – 600 ед. НВ с хорошей пластичностью и ударной вязкостью является главной особенностью этой стали. Однако при чисто абразивном износе когда преобладает механизм среза поверхностных слоев абразивными частицами сталь 110Г13Л со структурой аустенита не имеет существенных преимуществ перед другими сталями с аналогичной твердостью.
Годовой расход металлошихты (металлозавалки) для производства стали марки 110Г13Л согласно технологической части проекта составляет:6570 т. Таблица 1
Металлоломы и отходы собственного производства цехов должны соответствовать ГОСТ 2787 – 75 и обеспечить плотную укладку в бадью и печь.
Металлошихта не должна быть промасленной загрязненной токонепроводящими предметами мусором примесями и взрывоопасными предметами и др.
Таблица – 1 Годовой расход металлошихты
В таблице 2 представлены закупочные цены с НДС и норма расхода ферросплавов и вспомогательных материалов для производства 1 тонны литья высокомарганцовистой стали 110Г13Л
Таблица 2 – Расчет стоимости ферросплавов и вспомогательных материалов.
Ферромарганец высокоуглеродистый ФМн78
Ферросиликомарганец МнС17
Ферросилиций 45% ФС45
Ферросилиций 75% ФС75
Алюминий вторичный АВ86
Кокс металлургический
Порошок магнезитовый
Электроды графитированные
Продолжение таблицы 2
Кирпич ПХС № 1 (магнезитовый)
Кирпич ПХС № 9 (магнезитовый)
Кирпич ПХС № 10 (магнезитовый)
Вкладыш магнезитовый
Оборудование литейного цеха размещено на производственная площадь – 23025 м2 согласно технологической схеме производства литья в данном проектируемый цеху будет учтено что производство возрастет на 8000 т литья из крупно габаритных отливок но из – за того что масса отливок 0135 т а габариты отливки 1450 × 075 × 006 это затрудняло производство данного сегмента литья. Так как выполнялось на ручном плацу с одной моделью. Оборудование представлено в таблице .3
Таблица 3 – Оборудование литейного цеха.
Вакуумный распределить
Шкаф с пневматическими клапанами
Гидравлический аммортизатар
Видростол 3-х мерный
Видростол 2-х мерный
Перфорированная плита 1000x800
Формовочно-заливочные ветви
Передаточная тележка
Гидравлический толкатель
енточный транспортер
Вертикальный охладитель
Виброгрохот 2-е сито
Подстанция трансформаторная ПТ-5
Агрегат отопительный СТД-300
Пневматический шибер
Магнитный сепаратор
Видрогрохот транспортирующий
Выбивная решетка проходного типа
Аспирационная система №3
Гидравлический кантователь
Аспирационная система №8
Циклонный пылеуловитель
Сварочное оборудование ВДМ
Система транспорта песка для загрузки дозатора [03834]
Шкаф управления линией
Воздуходувка шкафа охлаждения
Грейфер без мех привода
Ковш сталеразливочный
Таль электрическая гп 2 т
Тележка моторная гп 5 т
Трансформатор ТД-500
Кран мостовой гп 10 т
Печь электр. варки жидкого стекла
Печь эл. индукционная тигельная ИСТа16
Печь электросушилкрупн и средних форм
Штатное расписание – это перечень личного состава работников цеха утверждаемый директором предприятия с наименованием штатных должностей размером окладов работника по каждой должности.
При составлении штатного расписания нужно учитывать что цех работает в три смены выходные в субботу и воскресеньем а так же праздничные дни и то есть по графику 1-Н.
Численность трудящихся рабочих и аппарата управления литейного цехапредставлена в таблице 4
Таблица 4 – Рабочие руководители специалисты в цеху
Уборщик пр. помещений
Газорезчик термо-обрубного участка
Машинист мостового крана
Машинист железного крана
Слесарь-ремонтник ГПМ
Мастер плавильного участка
Мастер термообрубного участка
Количество рабочих в литейном цеху
Всего по литейному цеху70
При проектировании применяют три вида годовых фондов времени работы оборудования:
календарный фонд Фк = 365 × 24 = 8760 ч;
номинальный фонд (Фн). Является временем в течение которого может выполняться работа по принятому режиму без учета неизбежных потерь.
действительный фонд времени (Фд). Определяется путем исключения из номинального фонда неизбежных потерь времени для нормального организованного производства.
Для определения действительного фонда времени работы оборудования из номинального фонда исключают время пребывания оборудования в плановых ремонтах установленное нормами системы планово – предупредительных ремонтов (ППР). Простои оборудования вызванные недостатками в организации производства по внешним причинам при определении Фд не учитывают.
Действительный фонд времени работы оборудования определим по формуле:
Фд= (К – В – П) × n × × (100 – Пр)100
где:К – календарное число дней в году (К=365)
В – число выходных дней в году (В=104)
П – число праздничных дней в году (П=12)
n – число смен (n = 3)
– продолжительность смены( = 8часов)
Пр – процент простоя оборудования (Пр = 12 % ).
Фд=(365 – 104 – 12) × 3 × 8 × (100 – 12)100 = 5259ч.
Действительный фонд времени работы рабочих определим по формуле:
Фд= (К – В – П ) × n ×
n – число смен (n = 1)
Фд= (365 – 104 – 12) × 1 × 8 = 1992 чгод
В средне месяц получается работает один рабочий 166 часов.
Оплата труда и расчет годового фонда оплаты труда
Численность персонала литейного цеха соответствует потребности обслуживания агрегатов оборудования с учетом действующих норм и нормативов по отдельным технологическим процессам операциям и службам.
Таким образом в рассматриваемом цеху работают рабочих – 141 и 14 человек ИТР.
Оплата труда – это вознаграждение в денежной или натуральной форме которое должно быть выплачено работодателем наёмному работнику за выполненную работу без вычета налогов и других удержаний.
Проведём расчёт заработной платы для формовщикаручой и машинной формовки. График работы сорока часовой с продолжительностью смены 8 часов. Система оплаты труда повременно – премиальная используется тарифная сетка для промышленных предприятий (8 – ми разрядная). Уровень производственной премии составляет от 10 – 40 %. Продолжительность очередного отпуска 27 рабочих дня. Размер тарифной ставки 4 – го разряда согласно с тарифной сеткой равный 282тн.час.
В ТОО «Завод Казогнеупор» системы оплаты труда – ПП (повременно – премиальная). По заданному графику работы. Заданный процент выполнения норм выработки – 100 %.
Величина фонда рабочего времени который рассчитывается по формуле:
мес = 249 × Ссут × 12 ×
где: мес – месячный фонд рабочего времени в расчете на одного работника человек час;
8 – количество рабочих суток в году;
Ссут – количество смен в сутках согласно графику работы;
см – продолжительность одной смены час;
– количество месяцев в году;
– количество бригад обслуживающих данный участок согласно графику работы.
мес = 249 × 3 × 8 12 × 3 = 166 чел.час
Определим сумму оплаты труда по тарифу:
где:ЗПтар – заработная плата по тарифу на одного работника в месяц тнмес;
tчас– тарифная ставка работника соответствующего разряда тн.час;
мес – месячный фонд рабочего времени в расчете на одного работника человек час;
ЗПтар = 282 × 166 = 46812тнмес.
Ночным считается время с 22 часов вечера до 6 часов утра что составляет 8 часов или 13 суток.
Продолжительность работы в ночное время рассчитаем по формуле:
ноч = 1 3 × 166 = 5533 чел. час
Величина приработка сдельщика рассчитывается по формуле
где: - приработок сдельщика за месяц тн.мес;
- планируемое выполнение норм выработки %;
Сумма производственной премии рассчитывается с учетом того что установленный размер премии составляет от 20 до 30 % к заработной плате по тарифу:
ЗПпрем = (ЗПтар + ЗПСД)
где:ЗПпрем – размер месячной производственной премии на одного работника тн.мес;
ρобщ– общий размер премии за выполнение условий премирования и перевыполнение установленных показателей (принимаем 30 %);
ЗПпрем = 46812 × 03 = 140436тн. мес.
Сумма доплат за работу в ночное время которую можно определить по формуле (установленный на предприятии размер таких доплат составляет 50 % от сдельного заработка):
ЗПночн = kночн 100 × tчас × ноч
где:ЗПпрем– сумма доплат за работу в ночное время на одного работника тнмес ;
kночн - коэффициент учитывающий размер доплат за работу в ночное время % (принимаем равным 50 %);
ЗПночн = 50 100 × 282 × 5533 = 780153тн. мес.
Сумма основной заработной платы равна:
ЗПосн = ЗПтар + ЗПсд +ЗПпрем + ЗПночн
где:ЗПосн – сумма основной заработной платы в расчете на одного работника тн. мес;
ЗПосн = 46812 + 0 + 140436 + 780153 = 6865713тн. мес.
Сумма дополнительной заработной платы равна:
ЗПдоп = kдоп 100 × ЗПосн
где:ЗПдоп– сумма дополнительной заработной платы в расчете на одного работника тн.мес;
kдоп– коэффициент определяющий соотношений между основной и дополнительной заработной платой %;
Величина коэффициента kдоп в наибольшей степени зависит от продолжительности очередного отпуска работников и в расчетах принимается в размерах 137 % (при длительности очередного отпуска 27 рабочих дня.
ЗПдоп = 137 100 × 6865713 =940602тн. мес.
Сумма среднемесячной заработной платы данного работника по среднегодовому расчету определяемая по формуле:
ЗПср = ЗПосн + ЗПдоп
где:ЗПср– месячная заработная плата i-ro работника по среднегодовому расчету тн.мес.
ЗПср = 6865713+ 940602 = 7806315тн. мес.
Общие затраты на ФОТ по цеху:
В результате полученных данных вывод что средняя заработная плата рабочих сталеплавильного участка формовщика составляет 7806315тн. мес.
573046 2000 = 327865 тн. тонну
А годовой ФОТ составит 65573046 тн. год.
Расчет годовых эксплуатационных расходов
Производительность проектируемого литейного цеха 2000 тонн в год. годовая производство литья согласно номенклатуре составляет:
от 100 до 500 кг. – 2500 т.
от 500 до 2000 кг. – 1000 т.
Общие капиталовложения составляют – 131805000 тн.
Стоимость зданий и сооружений и оборудования – 2545176 тн.
Численность трудящихся в литейном цеху – 70 чел.
Годовой фонд заработной платы составляет – 54644205 тн.
Себестоимость продукции – это выраженные в денежной форме текущие затраты предприятия на ее производство и сбыт. Себестоимость продукции является важнейшим показателем который отражает все стороны финансово – хозяйственной деятельности предприятия.
Себестоимость продукции (работ услуг) представляет собой стоимостную оценку используемых в процессе производства продукции природных ресурсов сырья материалов топлива энергии основных фондов трудовых ресурсов а также других затрат на ее производство и реализацию.
В состав себестоимости включаются следующие виды затрат:
)затраты непосредственно связанные с производством продукции обусловленные технологией и организацией производства включая расходы на обеспечение качества.
)затраты по обслуживанию производственного процесса.
)затраты связанные с управлением производством.
)затраты связанные с совершенствованием технологии и организации производства повышением качества и надежности продукции изобретательством и рационализаторством.
)затраты на содержание и эксплуатацию природоохранных сооружений.
)затраты по обеспечению нормальных условий труда и технике безопасности.
)затраты связанные с подготовкой и переподготовкой кадров.
)выплаты предусмотренные законодательством о труде.
)отчисления от расходов на заработную плату.
)платежи по обязательным установленным законом видам страхования и по кредитам банка.
)отчисления в специальные фонды.
)затраты на воспроизводство основных производственных фондов то есть амортизационные отчисления.
)износ нематериальных активов.
)предусмотренные законом налоги сборы платежи и др. обязательные отчисления.
)другие виды затрат в соответствии с установленным законодательством порядком.
Кроме того в фактической себестоимости отражаются:
б)затраты на гарантийный ремонт обслуживание;
в)потери от простоев по внутрипроизводственным причинам;
г)недостачи при отсутствии виновных лиц;
д)денежные пособия в установленном законом порядке.
Затраты на производство продукции включаются в себестоимость того отчетного периода к которому они относятся независимо от времени оплаты.
Классификация затрат
Затраты можно классифицировать по следующим признакам:
)по способу отнесения затрат на себестоимость единицы продукции:
a)прямые (связаны с производством конкретных видов продукции можно непосредственно включать в себестоимость единицы продукции);
б)косвенные или накладные (затраты связанные не с производством определенного вида продукции а с производством вообще);
)по однородности состава затрат:
а)простые – экономически однородные (затраты материальные одинакового целевого назначения);
б)комплексные – экономически разнородные затраты но одинакового целевого назначения (на содержание и эксплуатацию оборудования);
а)по экономическим элементам (в основу классификации положена экономическая однородность затрат вне зависимости от места возникновения затрат и направления использования (зарплата);
б)по статьям калькуляции (учитываются место возникновения и направления использования);
)по характеру связи с объемом производства:
а)условно – постоянные – кним принято относить такие затраты величина которых не изменяется с изменением степени загрузки производственных мощностей или изменением объема производства;
б)условно – переменные – к ним относятся затраты изменяющиеся в зависимости от изменения объема производства.
3 Калькуляция себестоимости товарной продукции
Калькуляция себестоимости 1 т жидкой стали при годовой потребности жидкого металла 2940 т. Технологически выход годного составит 2000 тонн отливок.
Таблица 3 Калькуляция себестоимости
Норма расхода на 1 т.
Сырьё и основные материалы
Ферромарганец высокоуглеродистый
Вспомогательные материалы
Продолжение таблицы 3
Расходы по энергозатратам
Топливо технологическое
электроэнергия на плавку кВт ч
Энергетические затраты:
Фонд оплаты труда (ФОТ)
Затраты на ремонт содержание и эксплуатацию оборудования – 5 % от балансовой стоимости
Затраты на содержание и ремонт дорог и авто транспорта - 5 % от балансовой стоимости
Затраты на содержание и ремонт строительных зданий – 5 % от балансовой стоимости
Отчисления на социальные нужды (11 % от ФОТ)
Амортизация основных фондов
Цеховая себестоимость
Общие расходы (10 % От ФОТ)
Производственная себестоимость (ПС)
Сбытовые расходы 3 5% от (ПС)
Полная себестоимость
Расчет капитальных затрат
При строительстве литейного цеха все инвестиционные вложения будут привлекаться главным образом от акционеров предприятия и от реинвестируемой прибыли т.е. чистой прибыли ТОО «Завод Казогнеупор» огнеупорной продукции полученной в предыдущих периодах.
Рассчитаем капитальные затраты предприятия на покупку и монтаж нового оборудования 14.
Капитальные затраты рассчитываются из стоимости приобретенного оборудования:
где:Кз – капитальные затраты цеха тн.;
Сн – затраты на приобретение нового оборудования тн.;
См – стоимость монтажа оборудования тн. Затраты на приобретение нового оборудования рассчитаем по формуле;
Сн = Со + Стр + Ссклад + Сисп + Сдов
где:Со – цена на приобретение тн.; 155805000
Стр – транспортные расходы (Со – 20%) тн.; 31161000
Ссклад – складские затраты ( (Стр+ Со) – 5%) тн.; 10906350
Сисп – цена испытаний ((Со+ Стр+ Ссклад) – 12 %) тн.; 23744682
Сдов – цена доводки и наладки оборудования ((Со + Стр + Ссклад+Сисп) – 10%) тн. 221617032
Затраты на монтаж оборудования берутся в размере 12 % от первоначальной стоимости. Стоимость и список приобретенного оборудования представлены в таблице 4.
Таблица 4 Стоимость оборудование
Наименование видов основных средств
Количество единиц шт.
Ленточный транспортер
Аспирационная система №8 (1489)
Общая сумма оборудования = 155805000 тн.
Затраты на монтаж оборудования 18696600 тн.
Рассчитаем затраты на приобретение и монтаж нового оборудования:
Сн = 155805000 + 31161000 + 10906350 + 23744682 + 221617032 = 2437787352 тн.
Рассчитаем стоимость монтажа оборудования:
См = 012 * 155805000 =18696600 тн.
Рассчитаем объем капитальных затрат на строительство литейного цеха:
К3 = Сн + См = 2437787352 + 18696600 = 2624753352тн.
Расчет амортизационных отчислений
В соответствии со стоимостью приобретенного оборудования вычислим амортизационные отчисления.
Амортизация – процесс денежного возмещения износа основных средств по средствам отчислений от стоимости основных средств на стоимость годовой продукции 15.
Сумма приобретенного оборудования составила 155805000 тенге. Срок полезного использования 120 месяцев.
Следовательно можно рассчитать месячную норму амортизации.
Определим месячную норму амортизации:
где: -месячная норма амортизаций %;
- период полезного использования мес;
Месячная сумма амортизационных отчислений:
где: месячная сумма амортизационных отчислений тн.;
- первоначальная стоимость нематериальных активов тн.;
месячная норма амортизаций нематериальных активов %.;
= 155805000 × 083 100 = 12931815 тн.;
Годовая норма амортизации составит:
=12931815 * 12 = 15518178 тн.
Расчет амортизационных отчислений. Найдем годовую сумму амортизационных отчислений на 1 тонну готовой продукции:
Агод. = 15518178 2000 = 7760 тн.т.
Оценка экономической эффективности строительства литейного цха.
Рассчитаем прибыль от реализации высоколегированного литья марки 110Г13Л.
Пр = В – Сбгод – НДС
где:Пр – валовая прибыль от реализации продукции тн;
В – выручка от реализации продукции тн.;
Сб – себестоимость годового выпуска продукции тн.;
НДС налог на добавленную стоимость (12%) тн.;
где:Ц– цена 1 тонны продукции тн.;
Qгод– годовой объем производства;
В = 500000 * 2000 = 1000000000 тн.
Сбгод = Сбуд × Qгод
где:Сбуд– удельная себестоимость продукции тн.;
Сбгод = 356588 * 2000 = 713176000 тн.;
НДС =1000000000 – 12% = 108000000тн.
НДС =1000000000 * 012 = 120000000тн.
Пр = 1000000000 – 713176000 – 120000000 = 166824000 тн.
Таким образом валовая прибыль от реализации продукции составит
Рассчитаем чистую прибыль от реализации продукции:
где:Пр чист – чистая прибыль от реализации продукции тн.;
Н пр – налог на прибыль (20%) тн.;
Пр чист = 166824000 – (166824000*02) = 133459200 тн.
Чистая прибыль проекта составила 133459200 тн.
Рентабельность производства составит:
Рпр = (Пр чист Сб год) × 100
где:Рпр – рентабельность производства %;
Рпр = (133459200713176000)*100 = 19
Рентабельность производства составила %.
Расчет периода окупаемости проекта:
где:То – период окупаемости год;
К – капитальные затраты в проект тн.;
То = 2624753352 133459200 = 2 года
Таким образом период окупаемости проекта составил 2 года.
Таблица 6 Технико-экономические показатели проекта литейного цеха
Наименование показателя
Числовые характеристики показателей
Годовой объем производства
Производственная себестоимость продукции
Рентабельность продукции
Количество трудящихся
Сумма капитальных затрат
Срок окупаемости проекта
Генеральный план. Транспорт
Выбор промышленной площадки и проведение изысканий и обследований на месте входит в комплекс работ по составлению технического проекта.
В соответствии с действующими нормами проектирования территория города расположена в соответствии с установленной санитарно-защитной зоной 300 м с подветренной стороны преобладающего направления ветра по отношению к промышленной зоне ТЭЦ.
Генеральный план объекта решен в соответствии с необходимым технологическим процессом а также с учетом норм и правил.
Функциональной зонирование территории проектируемого литейного цеха осуществляется с учетом технологических связей санитарно-гигиенических и противопожарных требований грузооборота соответствующих видов транспорта и очередности строительства.
Общая площадь зданий и сооружений более 141 тыс. м2 со всей необходимой инфраструктурой - электрогазоснабжением теплоснабжением водопроводной системой скважинами канализацией и пр.;
— складские помещения ремонтно-механические мастерские энергетический цех и другие вспомогательные сооружения;
— высокое качество выпускаемой продукции;
— квалифицированный управленческий и производственный персонал.
На генеральном плане запроектирована сеть автомобильных дорог которые по требованиям пожарной безопасности закольцованы и имеют достаточную ширину для двустороннего движения т.е. 6 м.
Водоотвод от зданий и сооружений решен открытым способом по спланированной поверхности площадки на пониженные участки рельефа уклон 005%.
Ориентация проектируемого здания на генеральном плане широтная. Ориентация здания относительно сторон света принята с учетом направления господствующих ветров – юго-западных которые приходятся на угол здания.
Расположение объектов производственно-вспомогательного комплекса сконцентрировано в общей зоне при большой плотности застройки что сокращает протяженность инженерных сетей водоснабжения канализации и теплоснабжения и транспортных коммуникаций – железнодорожного путевого развития и автодорог.
Минимальные противопожарные разрывы между производственными зданиями приняты в пределах 10–20 м.
Для пешеходного движения вдоль всех автомобильных дорог а также между отдельными зданиями и сооружениями устроены асфальтированные и пешеходные дороги и тротуары шириной 2 м.
Предусмотрено озеленение площадки. Устраиваются цветники газоны высаживаются деревья лиственных и хвойных пород рядовым и групповым способами.
Предусмотрено устройство наружного поливочного водопровода[2].
Для перевозки сырья товарной продукции и хозяйственно-эксплуатационных нужд проектируемого прокатного цеха предусматривается автомобильный железнодорожный и комбинированный (автомобильно-железнодорожный) транспорт. Транспортная система цеха состоит из электрокар кран-балок и мостовых кранов. На склад исходного материала заготовки привозятся на грузовых автомобилях и выгружается с помощью кран-балки.
На территории цеха имеется железнодорожная ветвь нормальной колеи протяженностью 6280 метров для перевозки грузов от промышленного предприятия к путям общей сети железных дорог.
Ширина колеи железных дорог составляет 1524 мм уклоны железнодорожных путей составляют 002. Погрузочно-разгрузочные пути располагаются на прямых участках с уклоном не круче 00025.
Нормальное расстояние между осями двух путей принимаются 4100 мм для широкой и 3000 мм для узкой колеи.
2.3 Автомобильные дороги
Протяженность автомобильных дорог составляет 1600 метров с шириной полосы 6м. Сеть автодорог обеспечивает удобную связь между производственными зданиями и складами. Въезды в здания соединяются с проездами под прямым углом. Проезды въезды в цехи установленные по производственным условиям используются и для противопожарных целей.
Продольный профиль автодорог связан с вертикальной планировкой заводской площадки.
Технология производства
1 Перспективы развития черной металлургии
В последние десятилетия в мировой черной металлургии появилось новое направление новый тип предприятий — металлургические минизаводы -передельные предприятия сравнительно небольшой производительности.
Появление и быстрый рост числа металлургических минизаводов обусловили следующие предпосылки.
Низкие удельные капиталовложения и короткий строительный цикл простая и компактная технология региональное сырье в виде металлического лома специализированный сортамент продукции ориентированный на конкретного потребителя высокая производительность труда при оптимизации производственных издержек появление новых технологий а также создание нового технологического оборудования - весь этот комплекс объективных предпосылок сделал металлургические минизаводы одним из наиболее динамично развивающихся и эффективных направлений в черной металлургии.
2 Современная технология производства металлических отливок
Развитие реального производства при сокращении временных и материальных затрат стремится к наукоемким технологиям по выпуску изделий с высокой добавленной стоимостью т. к. именно они в наибольшей мере используют «человеческий капитал» и позволяют сохранить природные ресурсы. Промышленники мало знают об одной из современных технологий получения металлических отливок – литье по газифицируемым моделям (ЛГМ). По этой технологии специализируется компания которая поставляет оборудование и занимается организацией и реконструкцией литейных цехов.
Литейные цеха обычно относят к наиболее загрязняющим экологию машиностроительным производствам. Свыше 75% отливок металлических деталей получают в песчаные формы которые при традиционных технологиях дают основные выделения газов загрязняющих атмосферу цеха и в основном состоящих из продуктов испарения и горения связующих материалов формовочного песка. По технологии ЛГМ англоязычное название Lost Foam Casting Process модели изготовляют из пенополистирола (реже из других пенопластов) и помещают в формы из сухого песка без связующего. За 50 лет со времени своего возникновения годовой объем выпуска отливок в мире этим способом достиг 15 млн. тонн.
Рыночные отношения жесткой конкуренции в литейном бизнесе с быстрым обновлением продукции вместо массового производства вызывают спрос на мелкие и средние серии отливок с повышенной размерно-весовой точностью. Развитие литейного производства большей частью сопровождается созданием самостоятельных некрупных цехов с гибкими технологиями получения отливок высокой точности и сложности когда метод ЛГМ оказался наиболее подходящим вместо литья в песчано-глинистые формы по выплавляемым моделям в металлические формы или других способов.
В этом способе литья получить модель отливки означает уже наполовину получить саму отливку из металла. Пенопластовая модель отливки на вид похожа на упаковку от телевизора или разовую пищевую тарелку которые штампуют миллионами на автоматах а плитами полистирола утепляют наружные стены высотных домов. По схожей технологии для серии отливок модели производят из порошка полистирола в легких алюминиевых пресс-формах при их нагреве до 130° С. Для разовых и крупных отливок (иногда весом до нескольких тонн) подходит вырезание моделей из плит пенопласта а также вырезание на гравировально - фрезерных станках с ЧПУ большое количество модификаций которых появилось по доступной цене на рынке в последнее время. Модель и полученная по ней отливка имеют высокую точность и конкурентный товарный вид чему способствует окраска модели быстросохнущей краской с порошком-огнеупором.
Экологическая безопасность технологического процесса обеспечивается исключением из применения токсичных связующих большого объема формовочных и стержневых песчаных смесей (обычно 2 т смеси со связующим идет в отвал на 1 т литья) транспортировки их и выбивки отливок. Например 1 куб. м пенополистирола модели весит 25 кг если он замещается 7 т жидкого чугуна то при этом на 1 т литья расходуется 257=36 кг полимера. Тогда как в формах из смоляных холодно-твердеющих смесей (ХТС) при потреблении 3% связующего в смеси на 3 т смеси на 1 т литья расход составляет 003х3000=90 кг полимерного связующего или в 9036=25 раз больше. Чтобы пенопластовая модель не дымила в цех при заливке металла в форму и в период его затвердевания из контейнера отсасывают насосом все газы – разрежение поддерживают примерно пол-атмосферы. Затем эти газы через трубу вакуумной системы подают для обезвреживания в систему термокаталитического дожигания где они окисляются до уровня не менее 98% и в виде водяного пара и двуокиси углерода выбрасываются в атмосферу за пределами помещения цеха. Традиционные формы после заливки металлом дымят в помещении как ни вентилируй рабочую зону цеха.
Такое удаление газов из сухого песка формы согласно проведенным измерениям концентраций примесей в воздухе цеха в 10-12 раз снижает показатели загрязнений атмосферы рабочей зоны цеха по сравнению с литьем в традиционные песчаные формы. Формовочный кварцевый песок после извлечения из формы отливок благодаря его высокой текучести обычно транспортируют по закрытой системе трубопроводов пневмотранспорта исключающей пыление его в воздухе цеха. Песок поступает в установку терморегенерации где освобождается от остатков конденсированных продуктов деструкции пенополистирола а затем после охлаждения в проходных закрытых охладителях подается опять на формовку при использовании около 97% оборотного песка.
Значительную часть бункеров трубопроводов и оборудования комплекса по охлаждению и складированию оборотного песка обычно монтируют за пределами помещения цеха у внешней его стены при этом сухой песок который не боится мороза быстрее охлаждается на открытом воздухе. Изолирование в закрытых трубопроводах потока песка отсасывание из формы и последующее дожигание газов в сочетании с весьма чистым модельным производством дает возможность создать экологически чистые цеха высокой культуры производства. На фотографиях модельного цеха видно что он похож на консервный или фармацевтический завод формовочный участок на фото тоже мало похож на «литейку как маленькую шахту».
Технологические потоки и пространственное размещение моделей в объеме контейнерной формы удобно компьютеризировать а при изготовлении модельной оснастки все чаще применяют 3D-графику для программирования станков с ЧПУ. Возрастающий поток патентной информации свидетельствует о серьезном интересе к этой технологии практически всех ведущих машиностроительных компаний. Созданы проектируются и внедряются в производство десятки видов конвейерных оснащенных манипуляторами и линий непрерывного действия которые хорошо зарекомендовали себя в авто - тракторном моторостроении литье трубоарматуры и деталей насосов корпусов электродвигателей деталей коммунального машиностроения и др. Однако чаще создаются небольшие производственные цеха состоящие из модельного формовочного плавильного и очистного участков. Они оснащаются простым оборудованием одинаковым для черных и цветных сплавов.
Если изготовление форм состоит в засыпании моделей сухим песком с вибрацией в течение около 1-15 минуты то отпадает потребность в высокоточных формовочных машинах прессования встряхивания устройствах сборки форм. Акцент внимания перенесен на производство моделей – этих «легчайших игрушек» с плотностью материала 15-16 кгкуб. м которое обычно «доверяют» женским рукам часто располагая на втором и выше этажах зданий. Для серийного производства отливок поставляются полуавтоматы цикл производства пенопластовых моделей на которых составляет около 2 5 3 мин. и которые «взяты» из упаковочной отрасли где их используют для производства фасонной упаковки легкой тары а также декоративных панелей и элементов фасада.
Способом ЛГМ получают отливки из чугуна и стали всех видов бронзы латуни и алюминия всех литейных марок. В ящике на «елке или кусте» могут сразу лить десятки отливок как в ювелирном производстве обычно с почти «ювелирной» точностью. До 90% отливок можно применять без механической обработки.
Цеха и участки с этой гибкой технологией стремительно множатся по всему миру - от Америки до Китая на заводах General Motors Ford Motors Fiat. Компания совершенствуя в этом деле «фирменную» специализацию спроектировала оборудование и запустила целый ряд литейных заводов цехов участков в странах ближнего и дальнего зарубежья один из недавно реализованных объектов – цех на 400 тмесяц в г. Усть – Каменогорск УкЗТЛ. Сейчас поставляет заводам базовое оборудование для литья 500 – 20 000 тгод с различной степенью механизации.
В литейном производстве компании в Киеве льют черные и цветные металлы развесом 01-2 500 кг. до 150 т месяц отрабатывают технологию и оснастку для новых цехов проектируют оборудование и линии точно под программу и площади цеха-заказчика которые затем поставляют литейным предприятиям под ключ. Выполняется пуско-наладка всего комплекса поставленного оборудования и внедрение технологии в этом цехе. Особенно крупная экономия получается при литье сложных отливок из износостойких сталей (шнеки для машин производства кирпича била молотки и детали дробилок) т. к. резко снижаются затраты на их механообработку. Льют без ограничений по конфигурации конструкций колеса звездочки корпуса сантехнику головки и блоки цилиндров бензиновых и дизельных двигателей художественное литье и др. Капитальные затраты на организацию производства сокращаются в 2-25 раза также как и сроки ввода его в эксплуатацию. Легко разместить такие участки при кузнях термических ремонтных и других цехах.
Производственный потенциал технологии ЛГМ далеко не исчерпан и настолько значителен что она позволяет лить не только металлы и сплавы но и получать композиты и армированные конструкции которые обладают повышенными в несколько раз служебными свойствами. При этом в модель предварительно вставляют различные детали или материалы которые формируют композит или армированную конструкцию а наложение газового давления на жидкий металл увеличивает стабильность пропитки таких изделий со вставками на длину свыше 1 м.
ЛГМ-процесс относят к технологиям будущего учитывая его экологичность высокие точность получаемых отливок и степень оборотного использования формовочного песка. Для предпринимателей планирующих создать или реконструировать литейный цех технология ЛГМ послужит тем бизнесом в котором металл своим оборудованием и рабочей силой переводится в высокотехнологичный товар. Качество продукции и повышение культуры производства заслуженно относят способ ЛГМ к высоким литейным технологиям которые ломают стереотип что высокие технологии - это обязательно сложные малодоступные производства. Освоение ЛГМ позволяют опередить на шаг конкурентов в направлении укрепления собственного машиностроения и наращивания возможностей экспортирования отливок.
3 Общая характеристика проектируемого литейного цеха
Проектируемый литейный цех предусматривает Литье по газифицируемым моделям
Литье по газифицируемым моделям — технология позволяющая получить отливки по точности равные литью по выплавляемым моделям при уровне затрат сопоставимом с литьем в землю. Литьё по газифицируемым моделям как новый технологический процесс появился в середине 50-х годов. Его главным назначением было повысить точность литья при значительном уменьшении затрат на оборудование и материалы по сравнению с технологией литья по выплавляемым моделям.
Развитие реального производства при сокращении временных и материальных затрат стремится к наукоемким технологиям по выпуску изделий с высокой добавленной стоимостью т. к. именно они в наибольшей мере используют «человеческий капитал» и позволяют сохранить природные ресурсы.
Промышленники мало знают об одной из современных технологий получения металлических отливок – литье по газифицируемым моделям (ЛГМ).
По этой технологии специализируется компания которая поставляет оборудование и занимается организацией и реконструкцией литейных цехов.
Литейные цеха обычно относят к наиболее загрязняющим экологию машиностроительным производствам.
Свыше 75% отливок металлических деталей получают в песчаные формы которые при традиционных технологиях дают основные выделения газов загрязняющих атмосферу цеха и в основном состоящих из продуктов испарения и горения связующих материалов формовочного песка.
По технологии ЛГМ англоязычное название LostFoamCastingProcess модели изготовляют из пенополистирола (реже из других пенопластов) и помещают в формы из сухого песка без связующего.
За 50 лет со времени своего возникновения годовой объем выпуска отливок в мире этим способом достиг 15 млн. тонн.
Рыночные отношения жесткой конкуренции в литейном бизнесе с быстрым обновлением продукции вместо массового производства вызывают спрос на мелкие и средние серии отливок с повышенной размерно-весовой точностью.
Способ «литье по газифицируемым моделям» (ЛГМ) обладает рядом преимуществ
Резко уменьшить затраты на оборудование
Сократить число технологических операций
Благодаря использованию в качестве формовочного материала оборотного кварцевого песка и упрочнения формы вакуумом исключается использование стержней и оборудования для их изготовления
Сократить операции финишной обработки отливок
Снизить до минимума количество отходов производства
Сократить трудозатраты в 2—4 раза
Снизить потребление электроэнергии в 2—3 раза
Сократить и оптимально использовать производственные площади
Уменьшить затраты на вспомогательные материалы в 3—5 раз
4 Вакуумные системы формовочно - заливочных участков
С появлением вакуумируемых форм из сухого кварцевого песка началось развитие технологии формовки без связующего. Первый патент (ФРГ) на литье по газифицируемым моделям (ЛГМ) в вакуумируемую форму выдан Е. Кржижановскому в 1968 г. а с 1971 г. началось освоение в Японии и далее по всему миру литья методом вакуумно-пленочной формовки (ВПФ). В обоих случаях формовка со склеиванием частиц формовочной смеси путем создания мостов между зернами песка когда прочность связывания зависит от сил когезии и адгезии уступила место уплотняющего ком песка перепаду атмосферного и пониженного внутриформенного давления воздуха в порах этого песка. Этот перепад вместо химической связи резко увеличил силы трения частиц песка и создал упругие сжимающие напряжения удерживающие песок формы в неподвижном состоянии при действии какой-либо технологической нагрузки включая давление залитого металла.
С одной стороны исключение связующего из формы на порядок и более уменьшило выбросы вредных газов в атмосферу цеха и значительно повысило культуру производства способствовало ресурсосбережению за счет многократного рециклинга песка без экологически вредных отходов (формы со связующим дают до 80% загрязнений литейного производства) повысило точность отливок за счет исключения прилипания к моделям смеси (снижены или устранены уклоны и припуски на моделях) и уплотнения ее без значительных силовых нагрузок. Но с другой стороны вакуумирование потребовало от литейщиков понимания сущности баланса давлений на поверхности полости формы и способов ее поддерживания в статичном состоянии что часто связано с регулированием газопроницаемости поверхностных слоев формы а также степенью и способом вакуумирования особенно важных в момент заливки и затвердевания отливки.
Слабое внедрение вакуумируемых форм в отечественное производство (и стран СНГ) объясняется низкой осведомленностью литейщиков о достаточно несложных принципах регулирования газового давления на границе металл- вакуумируемая форма весьма простом преимущественно отечественном оборудовании для обеспечения форм вакуумом однако смонтированном в части трубороводной разводки в комплекте с системой очистки газового потока по законам газодинамики и гидравлики. Опасение непроверенных собственным опытом технических принципов и неуверенность в сфере пока нетрадиционных для отечественного литейщика знаний дает предпочтение знакомой формовке со связующим при выборе технологических процессов для своего цеха тем более при обильной рекламе и др. стимулировании импортеров оборудования для ХТС. Расширение применения ХТС сопровождается усугублением неблагоприятной экологии литейного цеха что привело к тенденции вытеснения литейного производства из Западной в Восточную Европу если его не переводят на качественно новый в первую очередь экологический уровень.
Применению вакуума в форме при ЛГМ предшествовало то что газы от деструкции пенополистироловой (ППС) модели отводились через перфорации опок и проколы в песчаном наполнителе в атмосферу цеха что по сегодняшним меркам просто недопустимо. Дальнейшие исследования физико-химии процесса ЛГМ и применение вакуума дали новые положительные результаты для получения качественных отливок и повышения экологии производства. Проведенные специалистами нашими научно-исследовательские и опытно-конструкторские работы определили параметры необходимого вакуума в опоках что привело к созданию ряда новых разновидностей этого способа литья и соответствующего технологического оборудования обеспечивающего целостность литейной формы при заливке стабильного получения точных и качественных отливок.
Рассмотрим принципы вакуумирования форм и основы методики расчета параметров соответствующего оборудования на примере ЛГМ. Во многом это оборудование подобно используемому на участках ВПФ. Степень разрежения (вакуума) в литейной опоке (контейнере) зависит от вида заливаемого металла и обычно колеблется от 460 до 200 мм рт. ст. (06 - 025 атм.). Одним из главных факторов определяющих объем газов деструкции при одной и той же марке ППС модели является температура заливаемого металла от 650 С для алюминиевых сплавов до 1800 С для жаростойких железоуглеродистых.
Изучение физико-химических процессов взаимодействия жидкой фазы и паров ППС модели с затвердевающим и жидким металлом отливки в песчаной форме привело к выяснению требований к формовочным материалам – их плотности газопроницаемости и теплофизическим свойствам. Адсорбентом продуктов разложения твердого ППС при ЛГМ потенциально является как металл отливки так и формовочный материал. Одной из главных результатов применения вакуума при ЛГМ явилось во многих случаях практически полное исключение жидкого металла из числа таких адсорбентов при заливке и сопутствующих ей физико-химических процессах а также достижение устойчивого механизма получения прочной песчаной формы.
При этом были исследованы смачиваемость различных формовочных материалов продуктами деструкции ППС (адгезионные процессы) прямые и обратные химические реакции между материалом и формой диффузионные и тепловые процессы переноса зависимость прочности формы и скорости откачки газов от гранулометрического состава формовочных материалов их теплостойкость. Наиболее экономически приемлемыми и технически пригодными оказались кварцевые пески с размерами зерна в пределах 02-03 мм с содержанием пылевидных частиц размерами менее 005 мм не более 6-8 % плотностью в пределах 145-165 гсм3 и влажности не выше 05-06 %. Поскольку основным стабилизирующим прочность формы фактором является вакуум уплотняющий ее перепадом газового давления вне и внутри песка формы то надежность работы и грамотная эксплуатация всей вакуумной системы является определяющим в процессе формовки и заливки.
При расчете вакуумной системы участка (цеха) ЛГМ прежде всего исходят из ее функционального назначения будет ли она использоваться для формовки и заливки пневмотранспортирования формовочного материала (песка) обеспечения работы модельных полуавтоматов т.е. раздельной для всех технологических площадок или общей. Это обычно зависит от годовой производительности участка ЛГМ и организации производственного процесса. Порядок и правила расчета пневмотранспорта всасывающего типа (вакуум -транспортная система) приведены в учебниках и справочниках [1] а предварительные и приближенные расчеты вакуумных систем формовочно - заливочного участка (ФЗУ) ЛГМ можно вести по данным приведенным в [2-4].
Некоторая сложность расчетов вызвана отсутствием единых справочных численных характеристик протекающих физико-химических термо- и газогидродинамических процессов необходимых для определения скорости деструкции ППС модели образуемого объема газов с учетом газового взаимодействия этих продуктов деструкции с формовочным материалом подвергаемом вакуумированию. Многофакторность принимаемых во внимание изменяемых параметров усложняющих процесс расчетов демонстрируется следующим примером. Если пористость уплотненного формовочного кварцевого песка составляет 35-38% [4] то не ясно как будет изменяться площадь межзеренного сечения (как газового канала) при конденсации паров газа на поверхности песчинок. Модели из одной марки ППС при литье сплавов с разными температурами газифицируется по-разному создавая различные давление и объем газов деструкции за единицу времени.
Кроме этого происходит уменьшение пор за счет термического расширения зерен песка что также изменяет общую площадь проходного сечения формовочного материала. Одновременно по мере перемещения газов в толще песка происходит его охлаждение вызывающее соответствующее уменьшение объема газов исходящих преимущественно из зазора между зеркалом заливаемого жидкого металла и твердой частью ППС модели при ее термодеструкции. По законам гидродинамики при обтекании тела скорость текущей жидкости или газа на поверхности тела равна нулю. В межзеренном пространстве с порами составляющими микрометры сопротивление течению газа также зависит от шероховатости и угловатости зерен их фракционного состава. Шероховатость газовых каналов при ЛГМ - величина не постоянная т.к. вокруг песчинок образуется "рубашка" из сконденсированных продуктов испарения ППС. Кроме этого за счет вакуума жидкая составляющая деструкции ППС проникает до 60 мм вглубь песка формы также уменьшая площадь прохода газов. При многократном обороте песка песчинки покрываются углеводородными и сажистыми пленками очистку от которых выполняют в разработанных компанией установках терморегенерации песка. Вышеприведенные аргументы учитывают при закладывании запаса производительности вакуумных насосов в откачивающих системах формовочно - заливочных участков ЛГМ.
Другой особенностью работы вакуумных систем при ЛГМ и ВПФ является наличие частиц формовочного материала – песка в отсасываемых газах количество их может составлять 01-3 % от объема что зависит от конструкции опок. Попадая в насос частицы песка быстро изнашивают его внутренние части. Применение циклонов различных типов не решает полностью эту проблему т.к. теоретически степень их очистки составляет не более 97 % от их пропускной способности. Производственная практика специалистов компании при эксплуатации вакуумных систем ФЗУ показала необходимость разработки жидкостных песко- и пылеотделителей. Их использование на ряде предприятий показало высокую эффективность очистки газов что привело к увеличению срока службы насосов. Основным критерием выбора вакуумного насоса является требуемая производительность и величина вакуума на выходе из литейной формы или одновременно вакуумируемых форм.
Если производство проектируется для получения отливок из алюминиевых сплавов то степень разрежения создаваемого насосом в опоке-контейнере должна быть около 400-460 мм рт. ст. для отливок из черных металлов - 150-200 мм рт.ст. Проведенные исследования показали что температура газов деструкции в зазоре между зеркалом металла и моделью может достичь до 12 температуры заливаемого металла и далее перемещаясь на выходе из контейнера может иметь от 15 до 14 температуры металла. Объем и температура отсасываемых газов с учетом перечисленных физико-химических процессов; объема качества и физико-механических свойств формовочного материала; массы объема и вида металла отливки; расположения модели в контейнере; температуры окружающей среды; марки применяемого ППС – колеблются в широких пределах.
Для расчета объема отсасываемых газов необходимо исходить из законов сохранения массы и энергии термо- и гидрогазовой динамики тепло - массопереноса. Взаимосвязь объема газа V давления Р и температуры Т выражается формулой [2]:
где n - число молей в объеме V при температуре Т и давлении Р; R = k · N где k - коэф.- постоянная Больцмана N - число молекул в 1 грамм-молекуле. Исходя из этого можно использовать формулу:
(закон Бойля-Мариотта).
Зная температуру заливаемого металла массу ППС модели и используя вышеприведенные температуры при ЛГМ определяют объем газов V на выходе из литейной формы. Далее расчет всей вакуумной системы можно вести по формулам из работ [1 2 5].
Выбор насоса и элементов вакуумной системы. Исходя из предназначения вакуумной системы – раздельной по технологическим площадкам или общей на весь производственный цех ЛГМ производится расчет показателей потребного насоса насосов. Наиболее оптимальным по экономическим пожарно-санитарным эксплуатационным характеристикам является применение сухих кольцевых или водокольцевых вакуумных отечественных насосов серии ВВН или НRВ (Корея Hwahghae Electric). Применение сухих вакуум-насосов требует меньше площадей без наличия системы водоподготовки и водооборота или -питания но плохо стыкуется с системой утилизации откачиваемых газов с продуктами деструкции ППС. Конструктивные элементы насоса не должны корродировать в газовой среде. Количество частиц формовочного материала (песка) во входящем в насос газе должно быть предельно минимальным что требует усложнения элементов пылеулавливания вакуумной системы однако в целом применение сухих насосов как при монтаже так и при эксплуатации менее затратно.
Водокольцевые вакуумные насосы (ВВН) для своей работы требуют наличие системы водоподготовки и водоснабжения. Наибольшая эффективность у них достигается при использовании воды с температурой ниже +30 С. Другой особенностью их работы является наличие воды в выбрасываемом насосом газе что усложняет работу стоящих (как правило) за ними установок каталитического дожига газов с продуктами деструкции в процессе приведения выбрасываемых в атмосферу газов до санитарно-экологических норм – ПДК. Вода при работе ВВН нагревается что снижает их производительность а также при достижении температуры + 55 С минеральные включения из воды начинают выпадать в осадок. С целью экономии желательно создавать закрытые замкнутые системы водоснабжения изначально заполненные дистиллированной водой. Водоемы открытых систем особенно расположенных вне цеха летом зеленеют что требует их регулярной очистки. Разумеется этих проблем можно было бы избежать используя поршневые золотниковые роторно-пластинчатые насосы. Но этого нельзя делать т. к. во всех этих насосах имеется масло а откачиваемые газы при выходе из литейной формы имеют температуру намного выше +100С. Масло в таких насосах если не горит то коксуется и кроме того пары масла сконденсировавшиеся на входной трубопроводе - тоже источник возгорания.
Обязательным элементом вакуумной системы ФЗУ является вакуумный аккумулятор (ВА). Конструкции аккумуляторов разработанные компанией емкостью 1-3 м3 имеют защитные элементы в виде предохранительных пластин и обратных клапанов что позволяет легко производить работы по их очистке. Определение толщины стенки ВА производится по формуле [2]:
D - внутренний диаметр обечайки см; Рр - давление расчетное кгсм2; Еt - модуль продольной упругости материала при 20 С кгсм2; С – поправочный коэффициент (утоньшение стенки при эксплуатации); l - длина обечайки см. Основное предназначение ВА – обеспечение плавности работы вакуумного насоса.
Описание конструкции водного пылеосадителя разработанного компанией приведено в статье [6] а расположение рассматриваемого оборудования на планировке цеха – в статье [7]. Трубопроводы как указано в [2 3 5] должны быть по диаметру согласованы с диаметром всасывающего отверстия насоса и изготовлены максимально короткими. Но для ФЗУ соблюдение этого принципа не всегда оправдано т.к. отсасываемые газы имеют большую температуру и нагревают как элементы вакуумной системы так и воду тем самым снижая производительность ВВН. Пропускную способность трубопровода определяют по формуле [2]:
где: d - диаметр трубопровода см; l - длина трубопровода см. Необходимо стремиться чтобы он соответствовал производительности насоса и имел меньше изгибов.
Опыт эксплуатации запорно-регулирующей арматуры показал что наиболее надежны и дешевы шаровые краны которые массово выпускаются с проходными диаметрами от до 4 их легко монтировать. Как упоминалось выше откачиваемые газы с продуктами деструкции ППС или синтетической пленки при ВПФ должны перед выбросом в атмосферу очищаться в специальных установках. Для предварительного осаждения частиц формовочного материала рекомендуется использование серийно выпускаемых циклонов разработки ЦАГИ и "Союзэлеватор". С целью экономии производственных расходов и надежности работы вакуумной системы целесообразно вместо одного водного насоса требуемой производительности установить два насоса меньшей производительности и подключить их параллельно.
В качестве примера ниже приведены две схемы вакуумной системы участков ЛГМ на рис. 1 – система предназначена только для формовки и заливки на рис. 2 – для формовки заливки обеспечения работы системы подготовки и пневмотранспортирования песка.
Рисунок 1 – вакуумная система участков формовки-заливки Q≤12 м3мин
Н1– насос ВВН; ОК – обратный клапан; ВА – вакуумный аккумулятор; М1М2 – вакуумметр 01; ПО – пылеосадитель ; К1-К7 – краны шаровые; В1-В4 – вентили; Р1-Р5 – рукава; В1-В12 – вентили;
Все стенки должны быть герметичными. Падение давления в сети не более 005 атм. (контроль по М1)
Технические характеристики:
Производительность 12м3мин;
Мощность двигателя 185 кВт;
Максимальное разряжение -0093 МПа;
Скорость вращения импеллера 730 об.мин;
Расход воды 70-100 литровмин;
Вес установки 2250 кг.
Таким образом рассмотрена методика конструирования и расчета вакуумных систем формовочных участков с учетом ряда разнообразных факторов принятых во внимание при определении производительности насосов пропускной способности очистных и трубопроводных элементов. Оборудование этих систем комплектуется преимущественно отечественными изделиями. Такая информация будет полезна при организации современных участков ЛГМ и ВПФ которые обладают возможностями поднять экологическую культуру производства и обеспечить выпуск высокоточных отливок из различных сплавов.
Газодинамика процессов в песчаной форме при литье по газифицируемым моделям – лгм – процесс
В литейном производстве ЛГМ (Lost Foam Casting Process) отнесено в раздел специальных видов литья из которых в вузах изучается около десятка видов. Большинство литейщиков и машиностроителей с ним малознакомо и недооценивает возможности этого десятилетиями отработанного и одного из наиболее ресурсосберегающих процессов производства высокоточных отливок массой от 01 кг до нескольких тонн. Многие литейщики даже с солидным опытом после ознакомления с успешно работающим литейным цехом ЛГМ или получения об этом технической информации задают вопрос: "Если эта технология более прогрессивна менее затратна используемое технологическое оборудование - преимущественно отечественное и весьма несложное а модель формуется просто в сухом песке то почему ЛГМ так медленно распространяется в отечественной производственной практике?». Имеются случаи когда увидев где-нибудь на производстве его кажущуюся простоту пытаются повторить и не получив результата начинают винить не свое незнание сути происходящих в нем явлений а способ литья.
На наш взгляд так случается из-за неочевидности для производственника сути протекающих одновременно за очень короткое время физико-химических тепловых газо-гидравлических процессов в вакуумируемой песчаной форме нередко цеховыми специалистами не вполне освоенной но наиболее часто используемой при ЛГМ. Понимание и направление в нужное русло взаимосвязанных перечисленных процессов составляет основу технологии получения качественных точных и недорогих отливок этим способом. Конечно во многих случаях более приемлемо и привычно получать отливки традиционным способом в пустотелых (чаще в парноопочных) формах тем более к этому «склоняет» многолетняя практика; видна полость для заливки металлом понятны и освоены в навыках протекающие процессы известны все приемы получения отливок.
Со времени появления способа получения пенополистирола (ППС) еще в 1928 г. и начала его промышленного производства с 1937 г. пожалуй не случайно первым подал патент на ЛГМ не литейщик а архитектор (Г. Шроер в 1956 г.). Видимо литейщику труднее преодолеть стереотип в том что можно лить не только в пустоту а и на модель из ППС. Почему это возможно? Взглянем «вглубь» технологии – на структуру такой модели представляющей твердую пену типичную для ячеистых пластмасс (пенопластмасс или поро- и пенопластов). Обычно такую пену получают либо спеканием тонких стенок вспениваемых гранул либо газонасыщением и экструзией пенопластмассы. Со временем ячейки пены полностью заполняет воздух и при увеличении в десятки раз на срезе эта пена выглядит как воздух упакованный в шарики или многогранники с едва различимыми тоненькими стенками. Тогда по аналогии с традиционной литейной формой можно сказать что при ЛГМ расплавленный металл также льют в пустоту полости литейной формы только в пустоту упакованную в мелкие шарики составляющие модель из ППС находящуюся в песке этой формы.
Приравнивать пеномодель к пустоте в какой-то мере позволяет такой пример. Если 1м3 ППС модели весит ~25 кг и замещается 7 т жидкого чугуна то на 1 т отливок расходуется 257=36 кг полимера как говорится меньше некуда при стоимости 1 кг импортного ППС в гранулах ~20 грн. Тогда как в формах из смоляных ХТС при потреблении 3% связующего (стоимость которого уже достигает ~500 на тонну литья) в песчаной смеси на 3 т смеси на 1 т литья расход составит 003х3000=90 кг полимерного связующего или в 9036=25 раз больше с соответственным увеличением газовыделений из формы и отходов отработанной смеси. Это также объясняет существенные экологические преимущества ЛГМ вместе с тем что при вакуумировании формы практически все продукты разложения полимеров откачиваются вакуум-насосом из формы в процессе заливки - затвердевания отливки и идут на очистку дожиганием. Традиционные формы дымят в помещении как ни вентилируй рабочую зону цеха а утилизация и складирование от них отходов скоро достигнет 20% себестоимости продукции.
Следующее неоспоримое преимущество перед остальными методами литья состоит в гибкости техпроцесса ЛГМ прежде всего благодаря многообразию способов модельного производства [1 2 3] простоте и скоротечности формовки что делает его пригодным и экономически обоснованным как для получения единичных отливок например в ремонтных целях так и в массовом производстве. В целом ЛГМ-процесс состоит из четырех частей: производство моделей из ППС формовка заливка и обрезкаочистка отливок [4]. Наиболее сложен для понимания физики сопутствующих явлений процесс заливки. Способ ЛГМ в форме без связующего базируется на поддержании газодинамического баланса в форме во время заливки. Напомним его суть без формул и диаграмм поскольку знать почему сухой песок не обваливается в полости формы когда модель разрушается и какие факторы на это влияют должны все от технологов до рабочих через руки которых «проходят» модель форма и металл поскольку от этого зависит качество получаемой отливки.
Полость формы с сифонной литниковой системой во время заливки можно представить как два сообщающихся сосуда: открытый с торца стояк (1) и закрытая полость формы с замещаемой металлом моделью (2). Процесс заливки металлом и газификации модели выглядит как перетекание из открытого сосуда в закрытый. Если в двух сосудах на одинаковом уровне имеется одинаковое давление то в стояке оно состоит из (главным образом) металлостатического давления в сумме с атмосферным а в форме – из давления металла в сумме с давлением газов от газификации модели. Это давление газов может на 24% превышать атмосферное давление и достигать 124 кПа [5]. Образно говоря газы от газификации металлом ППС при освобождении от модели полости формы изнутри этой полости как бы надувают песчаную форму. В толще герметично упакованного в контейнере и покрытого пленкой песка путем подключения формы вакуумному насосу поддерживается давление равное 50 60% от атмосферного (50 60 кПа). И перепад указанных значений давления на поверхности освобождаемой полости формы над зеркалом металла как раз и создает то прессующее песок давление которое удерживает его от обрушения [6]. Аналогичные явления происходят при ЛГМ с другими типами литниковой системы а также они составляют принцип упрочнения формы при ВПФ (V-Process) с тем отличием что там оба рассматриваемых сосуда (стояк и литейную полость формы) сообщают с атмосферой причем сечение открытых выпоров в 2 4 раза превышает сечение стояка [7].
Как поддержать давление в полости формы в течение заливки? Может здесь уместна аналогия с детской игрушкой когда снизу дуть в вертикальную трубку развернутую сверху то в потоке воздуха будет висеть горошина. Если слабо дуть горошина упадет на трубку если сильно - улетит прочь. В этой связи различают факторы способствующие увеличению и стабилизации давления газов в полости формы во избежание осыпания песка и ослабляющие это давление чтобы не повредить изнутри форму. Ниже мы рассмотрим их подробнее. Почти всегда ЛГМ-процесс обладает саморегулирующими свойствами ва время заливки металла когда вышеуказанный перепад давления уплотняет песок формы и удерживает его от осыпания. Саморегулирование (самобалансирование) формозаполнения металлом состоит в том что если при заливке металл слишком быстро газифицирует модель то рост давления газов от модели тормозит течение металла внутрь формы по литниковой системе [5] что ведет к уменьшению темпа газифицирования. А если газифицирование слабое то вакуум формы проникая в литейную полость подсасывает заливаемый металл стимулируя газовыделения от деструкции модели. Последнее явление используют при сочетании ЛГМ с литьем вакуумным всасыванием алюминиевых сплавов с нижним подводом металла в форму из печи когда применяемого разрежения в песке формы (с давлением до 20 кПа) достаточно как для удержания песка так и для подъема металла на высоту почти до 2 м. Если стояк во время гравитационной заливки не поддерживать заполненным металлом то часто в полость стояка подсасывается и воздух с характерным шипящим звуком что крайне нежелательно из-за высокой вероятности появления брака отливки.
Таким образом ввиду указанных сопутствующих явлений заливка при ЛГМ отличающаяся от заливки в традиционных способах литья которые имеют форму-«гнездо» (см. словарь В. И. Даля 1863 г.) из связанного песка с литейной полостью со стержнями или без. Отличие заливки при ЛГМ состоит в необходимости поддержания баланса сил газового давления с учетом сопротивления фильтрации газа на границе металл - форма гравитационных и термических сил. Металл как правило подается питателями вдоль стенок отливки с учетом минимизации появления спаев трещин нагрева тепловых узлов и удобного их питания прибылями местных размыва стенки формы и пригара др. видов возможных дефектов а также удобства отделения литниковой системы от отливки.
При сифонной заливке давление в зазоре между поднимающимся зеркалом металла и газифицируемой моделью из ППС зависит от скорости заливки температуры металла и его относительно легко регулировать. Но сифонную заливку не всегда можно осуществить особенно если модельотливка большой длины более 15 2 м т. к. жидкому металлу необходимо преодолевать длинные пути которые уменьшают скорость его течения с падением температуры и увеличением вязкости. Это в свою очередь изменяет режим деструкции пенополистироловой модели и при установившейся скорости откачки газов из формы может привести к пульсации газового давления с такими негативными последствиями как частичное или полное обрушение формы недоливы спаи газовые и шлаковые включения и т. д.
На процесс литья влияет не только способ подачи металла но и климатические и сезонные факторы. Например увеличение влажности воздуха ведет к увеличению влажности песка краски на поверхности модели изменению текучести металла. Влага в песке формы приводит к появлению водяных паров при нагреве его газами деструкции модели и контактной теплопроводности от металла отливки. При наличии в песке остаточной влаги 04% его текучесть снижается на 30% [7]. При деструкции модели возникает свободный водород который частично реагирует с кислородом воздуха образуя пары воды. Пары воды могут присутствовать в модели особенно если изготовленная модель не высушена как после изготовления так и после покраски как того требует технология ЛГМ. В целях нивелирования этих факторов формовщики располагают модели таким образом чтобы обеспечить равномерность вакуумирования модельных блоков которых нередко в форме имеется несколько (рис. 1) а технолог так проектирует подведение расплава к модели чтобы обеспечивались равномерные без резких пиков рост и последующее уменьшение объемов газов деструкции ППС при заливке. Примеры конструирования опочной оснастки со средствами вакуумирования и расчета вакуумных систем участков приведены в работах [8 9].
При литье трубчатых деталей для песка заполняющего канал вдоль трубы часто применяют дополнительное вакуумирование. Поясним это примером литейной технологии использованной опытными технологами компании в литейном цехе при получении таких отливок. Модель стальной отливки длиной более 25 м наружным диаметром около 400 мм толщиной стенки до 60 мм и утолщением на одном из концов модель при формовке устанавливали вертикально или с наклоном не более 10Для задержки шлаков в литниковой системе применяли центробежный уловитель с запиткой от него одной из
Рисунок 2 - . Примеры расположения в контейнерной форме двух моделей насосов в процессе формовки
(а) и вид готовой формы сверху с воронками на контрладе от шести независимых литниковых систем для поочередной заливки отдельно получаемых отливок (б).прибылей установленной на конце без утолщения.
При поэтапной засыпке внутреннего сквозного канала модели песком на удалении от стенки ~80 мм спирально укладывали гибкую трубу вакуумной системы контейнера аналогично выполнили по наружной стенке обходя холодильники. Этим обеспечили устойчивость вакуумируемого песка формы и получили качественную отливку. Соблюдением дистанции при формовке между элементами откачки и моделью в пределах 70 80 мм достигался оптимальный режим вакуумирования. Газы проходя эту дистанцию теряют 40 60% температуры от той которую они имели на входе в песок что увеличивает их вязкость. При укладке на расстоянии меньше 20 мм откачиваемые газы могут расплавить вакуумно-фильтровальный гибкий трубопровод контейнера или деформировать форму с вероятностью попадания металла внутрь этого трубопровода.
На соблюдение газодинамического баланса формы оказывает влияние соотношение размеров элементов литниково-питающей системы которую выполняют в соответствии с законами гидравлики поскольку неправильный подбор этих размеров может привести к созданию в ней разряжения с образованием полостей между металлом и стенкой каналов этой системы куда может обсыпаться песок. Такое разряжение в литниковых каналах предотвращают прежде всего применением запертых литниковых систем поток металла в которых регулируют увеличением отношения площади сечения стояка к питателю как наиболее тонкому месту (узкому сечению) т.е. уменьшением питателя или увеличением стояка с соответствующим увеличением размеров чаши. Заливка форм из несвязанного песка и конструкции литниковых систем во многом аналогичны для ЛГМ и ВПФ [6 7]. Эти способы как никакие другие требуют тщательного подбора размеров чаш или воронок с тем чтобы при заливке их без труда держать заполненными во избежание образования вихрей в литниковой системе и возможностью захвата металлом легких частиц воздуха шлака смытой формовочной смеси которые могут попасть в отливку.
Уменьшение расхода металла от расчетного приводит к разбалансированию давления в зазоре металл-пенополистироловая модель что несет угрозу обрушения формы. От того насколько заливщик понимает и соблюдает технологию заливки зависит качество отливки и целостность формы что особенно «чувствительно» для форм из несвязанного песка. Скорость подъема зеркала металла в полости формы при сифонной заливке либо скорость выгорания пенополистироловой модели при дождевой или продолжительность заливки выбирается в зависимости как от толщины стенок так и от теплосодержания заливаемого металла с возможностью некоторого саморегулирования упомянутого выше. Также и вид литниковой системы и ее размеры зависят от соотношения высоты и толщины стенки отливки с учетом того что недостаточная подача металла часто ведет к разрушению формы а превышение – к выбросу газов металла формовочного песка с сопутствующей разгерметизацией формы.
Для крупных толстостенных отливок (рисунок. 3) деструкция моделей которых дает большие объемы газа особенно при литье по такой разновидности ЛГМ-процесса как литье в формы со связующим (Full Mold Process) в частности в формы из ЖСС рационально выполнять вентиляционные каналы в выпорах из ППС выходящих на поверхность верхнего контрлада формы. При этом следует вводить эти вентканалы внутри стенки модели в места входа металла из литниковой системы через питатели в модель [10]. Начиная с момента попадания первых порций металла в тело модели он прожигает в ней полость которая сообщается каналом выпора с атмосферой. По этому каналу в период заливки «избыток» газов с давлением выше атмосферного уходит из формы а «недостаток» ниже атмосферного может заходить в форму тем самым над зеркалом металла всегда поддерживается давление близкое к атмосферному. Аналогичные вентиляционные каналы используют также для ЛГМ под низким давлением путем измерения в них газового давления преобразуют эти данные в електросигнал обратной связи для управления давлением подаваемого в форму металла [11].
Рисунок. 3 -. Примеры моделей крупных стальных отливок весом 2 7 т. деталей МНЛЗ.
Следующими важными факторами влияющими на газодинамический баланс являются наносимая на модель краска: ее газопроницаемость при заливке металлом зависящая от состава плотности толщины наносимого слоя адгезионнорй стойкости; а также клей для сборки составных моделей и литниково-питающей системы. Использование водных красок различного состава предпочтительно по экологическим соображением однако превышение их плотности выше 18 гсм3 часто приводит к их осыпанию после высыхания. Оптимальная толщина краски при которой приемлемо соблюдается баланс прочности целостности и газопроницаемости составляет 08 12 мм. Эта толщина может удивить опытного литейщика но ведь при ЛГМ краску наносят на точно выполненную модель сверх размера будущей отливки а на полых формах со связующим краску на поверхность полости формы обычно наносят более тонким слоем когда она как бы уменьшает размеры этой полости. В первом случае краска не влияет на точность отливки а во втором из-за потеков и неравномерности слоя может ее понизить.
Рисунок 4. Краскомешалка со шкафом управления.
Размер: 600x500мм. Мощность двигателя 4кВт.
Краски для вакуумируемых форм выполняют противопропригарную и герметизирующую (регулирующую газопроницаемость песчаного слоя формы) функции. Толщина краски на модели или модельном кусте непосредственно влияет на стойкость формы во время заливки предотвращение ее обрушения поэтому толщиной и составом краски регулируют газопроницаемость формы. Большая газопроницаемость уменьшает давление газов над зеркалом металла и грозит разупрочнением песка малая способствует торможению потока металла противодавлением газов вплоть до «кипения» формы с последующими газовыми дефектами отливки. Декстрин используемый в ряде составов красок как связующее при заливке выгорает чем увеличивает газопроницаемость краски. Для увеличения газопроницаемости в состав краски также добавляют асбест искусственные минеральные волокна пемзу и др.
Для сборки моделей и их блоков предпочтительно использование быстросохнущих клеев на органических растворителях. Качественную склейку дает 1020% раствор поливинилбутираля в спирте с выдержкой под нагрузкой в течение до 3 часов. Термическое склеивание оплавлением поверхности стыка при 110 120 С удобно для сборки моделей с литниково-питающей системой т.е. швов с малыми контактными площадями. В любом случае клеевой шов имеет другую плотность и химический состав и несомненно влияет на газодинамический баланс при заливке. Использование шпаклевки из парафина воска полиолефинов винилароматических смол для ремонта модели из ППС оказывают такое же воздействие как и клей. Поэтому стремятся реже их использовать а элементы литниково-питающих систем получать цельными с моделью.
Если от марки используемого ППС и клея зависит объем и состав продуктов деструкции то от песка как формовочного материала так же как и от конструкции вакуумной системы и краски зависит стабильность удержания газодинамического баланса при заливке. Проведенные исследования показали что кварцевый песок как и металлическая дробь обладает оптимальным сочетанием газопроницаемости и теплопроводности для ЛГМ. Учитывая относительную легкость варьирования плотностью модели физические свойства песка обычно рассматривают как стабильные среди основных формовочных параметров при ЛГМ. Использование песка с размером зерен 01 02 мм при формовке с вакуумированием дает наибольшую прочность и твердость формы но увеличение его мелкой фракции или глинистой составляющей снижает газопроницаемость. Песок мелкой фракции прогревается быстрее чем крупнозернистый. Форма зерен песка остроугольная или закругленная не оказывает значительного влияния на газодинамические процессы при ЛГМ. Пористость песка с концентрированной зерновой структурой составляет от 35 % (виброуплотненного) до 47 % (свободной засыпки) его объема в опоке. При наложении вибрации происходит уплотнение песка на величину составляющую до 20% первоначального объема после свободной засыпки. Песок при ЛГМ используют многократно с отсевом 5% после каждой заливки. Поэтому в нем может увеличиваться доля мелких частиц с размерами ≤005 мм из-за разрушения его зерен прежде всего при термическом воздействии температуры металла а так же при выбивке и прохождения линии очистки-охлаждения. Если доля мелких частиц превышает 8% то газопроницаемость песка резко снижается однако применение пневмотранспорта в линии оборота песка [4] достаточно эффективно его обеспыливает путем уноса пыли с воздухом и осаждения ее в циклонах.
Применяемые водокольцевые насосы вакуумных систем часто не имеют элементов регулирования производительности и создаваемого разряжения работают в одном режиме [9]. Частично пульсация разряжения компенсируется вакуумным аккумулятором но для получения сложных отливок этого следует избегать.
С каждым повторным использованием наружная поверхность частиц песка в примыкающем к модели слое формы покрывается остатками продуктов деструкции ППС включая твердые сажистые остатками. Конечно сажистое покрытие увеличивает термостойкость. Органические включения немного снижают текучесть песка что не оказывает заметного влияния на уплотняемость и газопроницаемость а часть из них выгорая от тепла залитого металла и проходящего горячего газового потока создают новые каналы для этого потока. Разработанная технология терморегенерации песка убирает с поверхности песка остатки сконденсировавшихся продуктов деструкции ППС но одновременно может увеличивать долю мелких частиц за счет термического растрескивания зерен поэтому нагрев песка ведут на нижнем температурном пределе до 400С.
Одной из наиболее ответственных при ЛГМ является технологическая подготовка операции формовки несмотря на то что сама формовка может занимать до 10 мин. Формовщик при установке собранной с литниково-питающей системой одной или нескольких моделей модельного куста или кустов в литейный контейнер в первую очередь определяет соответствие их размеров и достаточность элементов вакуумирования контейнера возможному объему газов деструкции. Применение гибких элементов вакуумирования из металлорукава специльного типа позволяет расставить их таким образом и на таком расстоянии от модели чтобы не произошла их тепловая деформация и обеспечивался примерно одинаковый путь откачиваемым газам при термодеструкции модели с учетом возможного небольшого их смещения при виброуплотнении песка. Модели в контейнере располагают с возможностью заполнения песком по всей их поверхности без образования пустот или слабого уплотнения песка особенно если они имеют внутренние полости или поднутрения. При формовке моделей с установленными в них холодильниками последние желательно закреплять к литейному контейнеру с целью предотвращения смещения при заливке.
При ЛГМ отсутствуют стрежни и уплотненный песок заполняя каналы или пустоты модели выполняет функцию стрежней что часто открывает возможность получения нетехнологичных отливок. На рис. 3 показаны примеры моделей и отливок демонстрирующие диапазон применения ЛГМ от мелких (до 60моделей на стояке) - до каркасных и крупногабаритных. Хотя вибрация резко уменьшает угол внутреннего трения зерен песка и он
Рисунок 4 -. Примеры моделей:
а) мелких до 60на стояке г) крупных колес е) якоря; а также отливок: б) роторов многоступенчатых насосов в) муфеля термической печи из жаростойкой стали д) дозирующего шнека из силумина.
становится текучим равномерное заполнение внутренних полостей модели особенно в случае их криволинейной конфигурации и произвольного пространственного расположения представляет определенную трудность и требует особого внимания технолога. Неравномерность уплотнения песка или откачки газов приводит к несоответствию чертежным размерам отливки и ряду других литейных дефектов. Частично эти вопросы рассмотрены с работе [12]. Тепловые напряжения в зернах формовочного песка могут достигать 100 кгсм2 и часть этих сил передается на затвердевающую отливку. При несоответствии скорости откачки условиям газодинамического баланса действующие силы могут разрушить или деформировать как модель так и незатвердевшую отливку из-за непрочности образовавшейся корки.
Практика литья свидетельствует что оптимальные условия виброуплотнения формовочного песка достигаются при частоте 4 – 2 400 Гц и амплитуде 0001 14-16 мм. При ЛГМ максимальная прочность формы достигается при включении перед заливкой вакуумной системы а ее газопроницаемость при заливке остается практически постоянной - колеблется в пределах 5 10% в зависимости от температуры заливаемого металла. С уменьшением мощности вибратора уменьшается заполняемость поднутрений модели. Скорость перемещения песка в полостях и поднутрениях модели мало зависит от формы в плане но больше зависит от гидравлических радиусов поверхности модели. Заполняемость полости модели повышает закрепление контейнера к вибростолу. При формовке единичных крупных и пространственных моделей желательно использование литейных опок конструкция которых позволяет укладывать гибкие части вакуумной системы на различных уровнях что обеспечивает равномерную откачку газов деструкции позволяет обходить элементы холодильников а так же укладавать элементы вакуумной системы внутри крупных полостей для отливок трубчатого типа.
При соблюдении баланса давлений в песке формы меньшие плотность модели и объем газов ее деструкции при невысокой газопроницаемости краски и формовочного материала плавности начала газификации и стабильном давлении газов дают минимум твердых продуктов деструкции что повышает качество отливки точность и чистоту ее поверхности. Этого достигают согласованием объема продуктов испарения модели с объемом поступающего металла во времени с учетом его температуры для расчета литниковой системы и продолжительности заливки не вызывающей размыв защитной краски и кавитационных явлений. Например полученные опытным путем данные скорости газификации суспензионного литейного пенополистирола марки ПСВ-ЛТУ 605-00-041-345-72 при 900 С составляют (90 95)10-3 гс и 16 20 смс.
Однако в некоторых случаях замещение металлом модели не проходит незаметным для его химсостава это касается литья низкоуглеродистых сталей ниже Ст 20 когда в отливках наблюдается увеличение содержание углерода от 001 до 01 %. В случае получения отливок из медных и алюминиевых сплавов чугунных или углеродистых сталей с С03% это не происходит или не так важно но при литье из низкоуглеродистых или нержавеющих сталей явление науглероживания предотвращают подбором шихты или вида пенопласта модели. Специальный ППС для ЛГМ получен в еще 1962 г. в СССР – марка ПСВ и в ФРГ фирмой "BASF" - марка "Exporit" которые в дальнейшем улучшались по испаряемости и сажевыделению. Для увеличения испаряемости (теплопоглощения) в ППС добавляют красители. Поэтому для изготовления единичных моделей лучше применять цветной блочный ППС с удельным весом соответствующим получению модели отливки данного развеса и толщины стенки. Для серийных отливок разработаны пенопласты с атомами кислорода в их молекулярной структуре. Для уменьшения сажевыделения в исходный ППС на заводах по его производству добавляют перекись дикумила бензоил и др. Заслуживает внимания метод введения в краски для моделей реагентов выделяющих кислород при заливке металла с целью окисления сажистого углерода до газообразных продуктов однако технология его промышленного применения пока находится в стадии отработки.
Таким образом в статье кратко описаны основные положения технологии ЛГМ касающиеся поддержания газодинамического баланса в форме из несвязанного песка при замещении модели расплавленным металлом. По мере понимания инновационных возможностей ЛГМ все больше информации об этом появляется в технической периодике [13]. Отечественная практика дает примеры что для многих отливок в цехах ЛГМ техпроцесс литья доводят до уровня брака не выше 2%. Помещения предприятия ЛГМ (цех участок) занимают 30 50% от площади традиционного предприятия литья в песчано-глинистые формы той же производительности. ЛГМ по экологической чистоте и санитарно-гигиеническим условиям труда на ступень выше литья в формы со связующим.
ЛГМ относят к высокотехнологичным производствам которые дают выход к устойчивому развитию из технологической деградации когда в отечественной экономике нарастает сырьевая составляющая постепенно доминирует продукция с низкой добавленной стоимостью и снижается конкурентоспособность производства. Если в 80-е годы в структуре украинской промышленности и товарного экспорта вес машиностроения составлял порядка 30 40% а черной металлургии был в два-три раза меньше то сегодня наоборот. Здесь уместно замечание прозвучавшее в «Зеркале недели №46 за 2006 г.»: «Килограмм металла стоит в среднем 05. Килограмм металла в автомобиле или танке стоит уже 50 100 а в самолете —1500 2000».
5 Оборудование и технологии литья по газифицируемым моделям (ЛГМ)
Технология изготовления литья по газифицируемым моделям обладает рядом существенных преимуществ перед другими способами являющимися традиционными для литейных производств в России и за рубежем.
В частности эта технология позволяет получать отливки весом от 10 гр до 300 кг с чистотой поверхности Rz40 c весовой и размерной точностью до 7 класса по ГОСТ 26645-85.
Можно работать практически со свсеми существующими марками чугунов начиная от СЧ15 до ВЧ50 и износостойких марок применять практические любые стали от ординарных углеродистых (Ст.20-45) до прецизионных высоколегированных теплостойких и жаропрочных сплавов работать со всеми марками литейных бронз латуней и сплавов на основе алюминия.
Современный технологический уровень массового литейного производства предъявляет все более высокие требования к качеству отливок их сложности выходу годного и пр.
В этих условиях одним из перспективнейших направлений является внедрение на существующих литейных производствах технологии литя по газифицируемым моделям (ЛГМ).
Основным принципом ЛГМ является заливка расплава чугуна стали или цветного сплава в опоку находящуюся под пониженным давлением внутри которой в плотной песчаной смеси расположена пенополистирольная выжигаемая модель.
Практика доказала что применение предлагаемой нами технологии литья по газифицируемым моделям и оборудования для ЛГМ позволяет:
снизить затраты на расходные материалы в 3-5 раз;
сократить трудозатраты в 2-4 раза;
снизить расход электроэнергии в 2-3 раза;
в разы снизить процент брака и увеличить выход годного;
снизить потребности в цеховых площадях;
обеспечить максимальную безотходность;
улучшить условия труда песонала и многое другое.
5.2 Электроснабжение и электрооборудование
5.2.1 Характеристика потребителей электроэнергии
Основными потребителями электроэнергии является основное и вспомогательное оборудование лампы и светильники.
5.2.2 Источники электроснабжения
Цеховые сети промышленных предприятий выполняют на напряжение до 1 кВ (наиболее распространенным является напряжение 380 В). На выбор схемы и конструктивное исполнение цехов сетей оказывают влияние такие факторы как степень ответственности приемников электроэнергии режимы их работы и размещении по территории цеха номинальные токи и напряжения. Электроэнергия генерируется на тепло электроцентрали ТЭЦ и далее по воздушной линии электропередач поступает на 2-х трансформаторную районную понизительную подстанцию пст №90 на которой высшая сторона 35 кВ а низшая 6 кВ. Подстанция состоит из двух участков: открытое распределительное устройство ОРУ и закрытое распределительное устройство ЗРУ. На ОРУ электроэнергия преобразовывается с 35 кВ до 6 кВ с помощью 2-х силовых трансформаторов мощностью 25000 и 16000 кВт. Далее электроэнергия с трансформаторов по шинам поступает в ЗРУ. В ЗРУ имеются ячейки комплектных распределительных устройств КРУ на которые с шин подается электроэнергия. Далее схема потребления электроэнергии рассматривается относительно литейного цеха. С ячеек КРУ электроэнергия передается на пст №2 6 кВ по кабельным линиям проложенных в земле. С пст №2 запитывается прокатный цех. В прокатном цехе 1 нагревательная печь мощность электродвигателя которой составляет 600 кВт а также прокатный стан с суммарной мощностью электродвигателей 2944 кВт.
5.2.3 Электрическое освещение
Рациональное освещение рабочего места является одним из важнейших факторов влияющих на эффективность трудовой деятельности человека предупреждающих травматизм и профессиональные заболевания. Правильно организованное освещение создает благоприятные условия труда повышает работоспособность и производительность труда. Освещение на рабочем месте должно быть таким чтобы работник мог без напряжения зрения выполнять свою работу. Утомляемость органов зрения зависит от ряда причин:
- недостаточность освещенности;
- чрезмерная освещенность;
- неправильное направление света.
Недостаточность освещения приводит к напряжению зрения ослабляет внимание приводит к наступлению преждевременной утомленности. Чрезмерно яркое освещение вызывает ослепление раздражение и резь в глазах. Неправильное направление света на рабочем месте может создавать резкие тени блики дезориентировать работающего. Все эти причины могут привести к несчастному случаю или профзаболеваниям поэтому столь важен правильный расчет освещенности.
Расчет освещенности рабочего места сводится к выбору системы освещения определению необходимого числа светильников их типа и размещения. Процесс работы в цехе происходит в таких условиях когда естественное освещение недостаточно или отсутствует. Исходя из этого рассчитаем параметры искусственного освещения.
Целью расчета является выбор количества светильников определение мощности источников света расположение их в помещение цеха а также расчет осветительной сети.
Исходными данными являются: назначение цеха (прокатный цех) и его размеры:
В качестве источников света выбираем дуговую ртутную лампу высокого давления для общего освещения типа ДРЛ так как 1) высота помещения превышает 6м; 2) ДРЛ удобна в эксплуатации: Рассчитаны на большие сроки службы имеют большой световой поток высокую световую отдачу и незначительные размеры выпускаются на большие мощности; 3) работа ДРЛ не зависит от температуры окружающей среды.
Норма освещенности для данного производственного помещения: Еmin=200 Лк.
Для производственного помещения выбираем рабочее равномерное общее освещение а также аварийное освещение.
В качестве светильника выбираем светильник типа РСП 13 со степенью защиты 53 классом светораспределения - П КСС в нижнюю полусферу глубокий Г1 (08-12).
Расстояние от светильника до рабочей поверхности м:
Нр = Н - (hс - hр) (4.72)
где Н = 9 м- высота помещения;
hс = 07 м - высота свеса;
hр = 0 м - высота рабочей поверхности (пол).
Нр = 9 - (07 + 0) = 83 м.
Расстояние между светильниками для КСС Г1:
L = (08 - 12)·Н (4.73)
L = 08 · 83 = 664 м.
Расстояние от края светильника до стен:
I= 05 · 664 = 332 м.
Количество светильников в ряду:
Общее количество светильников:
Расстояние между светильниками в одном ряду:
Расстояние между рядами:
Определяем показатель помещения:
По справочнику с учётом коэффициентов отражения и показателя помещения находим коэффициент использования светового потока:
пот=05; ст=03; п=01:
Рассчитаем световой поток одой лампы в Лм если коэффициент минимальной освещённости z = Еср Еmin = 12:
где Kз = 2 - коэффициент запаса;
Еmin – нормированная освещённость лк.
По найденному значению Фл подбираем лампу поток которой должен отличаться не более чем на (-10 – +20)%.
Принимаем лампу ДРЛ 700(6) - 3 имеющую следующие технические данные:
номинальная мощность лампы Рн = 700 Вт; световой поток Фл = 406 клм.
Общая мощность световой установки:
Для аварийного освещения выбираем лампы типа ЛН (лампы накаливания).
Норма освещенности аварийного освещения составляет не менее 5% от нормы рабочего освещения то есть:
Е = Еmin·005 = 200·005 = 10 лк
Выбираем светильник типа НСП 20 источник света которого должен иметь мощность 500 Вт для создания кривой силы света Д3 класс светораспределения светильника - П степень защиты IP52.
По заданной мощности лампы светильника НСП 20 Рл=500Вт выберем ЛН типа Г125-135-500 с номинальным световым потоком Фл=9200 лм.
Определим количество ламп для аварийного освещения по формуле:
Выбираем светильники типа НСП.
Осветительные щиты. При выборе осветительного щитка необходимо чтобы выполнялось условие:
где Iном.щ- номинальный ток осветительного щитка А;
I-расчетный ток питающей линии А.
Для рабочего освещения выберем щит серии ЯОУ -8503 так как выполняется условие
Iном.щ = 63 А 50 А = I1-2
Для аварийного освещения выберем осветительный щиток серии ЯОУ - 8504 так как выполняется условие
Iном.щ = 63 А 28 А = I1-2
Таблица 4.5-Технические данные осветительных щитков серий ЯОУ - 8503 и ЯОУ - 8504 на напряжение 380220В.
Автоматический выключатель
Промышленная экология
1 Анализ состояния окружающей среды литейного цеха
Литейный цех ТОО «ЗаводКазогнеупор» является наиболее крупным источником пылегазовыделения и загрязнением воздушной среды. При производстве одной тонны отливок выделяется 150 кг оксида углерода около 15 кг S 25-60кг пыли. Примерный состав пыли % Fe03 -568; Mn2O3-10; А12О3-50; S СаО-69; MgO-58 остальное хлориды оксиды хрома и фосфора.
Средний состав пыли:
Размер частиц мкм 0-2 2-4 4-6 8-10 >10
Фракционный состав % 522 225 62 73 25 93
Их источниками являются дуговые сталеплавильные печи печи термической обработки сушила для стержней и ковшей.
При заливке форм в атмосферу попадают водяные пары водород и повышенное количество окиси углерода образующейся в результате реакции горения ограниченных примесей.
Окись углерода ПДК которой равна 20 мгм относится к наиболее вредным компонентам газа выделяющегося из литейных форм после заливки в них металла.
В состав выделяющихся газов входит более 50% Н2; 30-35% СО; и некоторое количество около 10% С02 H2S02.
При сушке стержней в сушке выделяются окись углерода и сернистый газ. Наименьшие выделения наблюдаются при сжигании природного газа всего 075 мгм3 СО.
Изготовление стержней связано с продувкой углекислым газом что вызывает дополнительное газовыделение.
В смесеприготовительных отделениях источниками пыли являются смесители. Выделяющаяся пыль насыщена парами сульфитного щелока различных углеводородов.
Операция выбивки отливок из опок - одна из наиболее вредных в литейном производстве. Запыленность воздуха составляет 12-25 кгм.
Большое количество пыли образуется в отделении обрубки и очистки литья. При обрубке концентрация ее в воздухе достигает 6-8 гм2.
Очистные барабаны выделяют пыли 4-7 кгт литья. Дробеметные аппараты 008кгт.
Повышенными вредными выделениями отличаются участок подготовки шихтовых материалов (запыленность воздуха 5-10%) и термической обработки.
Наиболее запыленные и загазованные участки оснащаются индивидуальными установками обеспечивающими местный отсос газов.
Отбор и очистка газов выходящих из дуговых печей осуществляется косвенным способом при помощи отсасывающего зонта.
В литейном цехе производственная вода расходуется на охлаждение оборудования для приготовления формовочных смесей проведения закалки отливок.[1]
1.1 Анализ опасных и вредных факторов в литейном цехе
Технологические процессы литейного производства сложны и разнообразны. В них широко используются материалы с различными свойствами используется технологическое оборудование многих видов которые нередко являются источником повышенной опасности.
Технологические процессы в литейном производстве отличаются один от другого поэтому и способы обеспечения безопасности работающих существенно отличаются. Для каждого технологического процесса разрабатываются инструкции по охране труда.
Основными процессами в литейном цехе являются:
-подготовка шихты и добавок;
-загрузка шихты в плавильные печи;
-выплавка жидкой стали и чугуна;
-выпуск металла и заливка в формы;
-подготовка формовочной и стержневой смеси;
-изготовление форм и стержней;
-обрубка очистка отливок;
-термическая обработка отливок
На всех стадиях получения отливки возможно действие опасных и вредных производственных факторов. К опасным и вредным факторам относятся такие которые вызываются движущими частями машин и механизмов транспортными средствами отлетающими частицами обрабатываемых материалов электрическим током неблагоприятными условиями труда слепящей яркостью загрязнённым вредными веществами воздухом шумом и сотрясениями.[1]
1.2 Мероприятия по улавливанию и обезвреживанию промышленных выбросов
В литейном цехе применяются для улавливания пыли циклоны. Они очищают отходящие газы от пыли с частицами более 10мкм на 80-95% и требуют небольших капитальных и эксплуатационных затрат. Их используют в качестве предварительной ступени очистки.
Наиболее эффективные пылеуловители - рукавные обеспечивают нормы ПДВ и применяются в качестве окончательной ступени очистки НО. Они имеют относительно низкий срок службы 6 12 мес. Натуральные ткани и нетканные материалы гарантируют эффективность очистки 989 % однако они недостаточно прочны. Разработан принципиально новый фильтрующий материал – бесшовные рукава которые лишены многих из указанных недостатков и обеспечивают эффективность очистки 995%.
Пылеуловительные камеры предназначаются для улавливания частиц размером более 50мкм и используются как предварительная степень очистки.
Инерционные пылеуловители применяются для предварительной очистки небольших объемов газов с очень высокой концентрацией пыли для отделения крупных частиц (более 100мкм).
Циклоны ЦН - 15 обеспечивают наибольшую степень очистки. Эффективность улавливания пыли составляет 81%.
По физической природе шумы могут иметь следующее происхождение:
- механическое связанное с работой машин и оборудования;
- аэродинамическое вызванное колебаниями в газах;
- гидравлическое связанное с колебаниями давления и гидроударами в жидкостях;
-электромагнитное вызванное колебаниями элементов электромеханических устройств под действием переменного электромагнитного поля или электрических разрядов.
Основными источниками шума являются все виды промышленных предприятий.
Одним из методов создания благоприятной акустической обстановки является установление предельно допустимых уровней (ПДУ) шума на предприятиях в жилых помещениях зонах отдыха и т.д. ПДУ установлены исходя из того что их действие в течение длительного времени не вызывает физиологических изменений в наиболее чувствительных к шуму системах организма то есть эти уровни безвредны для организма человека и являются допустимыми (пороговыми). Кроме установления ПДУ шума способами борьбы с акустическим загрязнением среды являются:
-снижение шума в источниках возникновения для чего нужна тщательная сборка и наладка каждого агрегата станка и машины; применение звукоизоляции;
-посадка зеленых насаждений;
-составление шумовой карты населенного пункта.
В качестве экранирующих шумозащитных устройств широко применяются специальные полосы озеленения сооружаемые на путях распространения шума нежилых объектов используется рельеф местности различные комбинации насыпей и земляных валов заглубление трасс магистральных улиц установка стенки-экрана на гребне.[14]
1.3 Описание системы очистки сточных вод и оборотного водоснабжения
Для очистки сточных вод применяются механические физико-химические биохимические и термические методы.
Механическая очистка сточных вод выполняется до биологической и физико-химической являясь первой ступенью очистки на станциях. При этом происходит отделение нерастворимых примесей процеживанием отстаиванием или фильтрованием. При этом используется соответствующее оборудование:
- решетки шириной проборов 16 мм и при угле наклона к горизонту 60—70°. Скорость протока стоков не превышает 1 мс. Очистка решетки выполняется вручную или механическим образом (решетки механические поворотные типа МГТ; решетки-дробилки типа РД); — песколовки для выделения из сточных вод тяжелых примесей (окалины) с гидравлической кратностью 132-242 ммс при скорости течения сточных вод 008—003 мс: Некоторые типы песколовок позволяют удалить из стоков до 80% песка.
- отстойники для гравитационного выделения из сточных вод нерастворённых субдисперсных примесей при плотности выше или ниже удельной плотности воды. Отстойники могут быть вертикальными горизонтальными радиальными и диагональными. Применение соответствующего вида зависит от требуемой производительностисут: вертикальные горизонтальные радиальные и диагональное. Тонкослойные отстойники применяются для очистки сточных вод от взвешенных частиц однородного состава после предприятий металлургической нефтяной угольной промышленности;
- гидроциклоны для выделения из сточных вод грубодисперсных примесей под действием центробежных сил. Часто это первая ступень очистки стоков которая обеспечивает отделение песка и минеральных частиц размером порядка 015 мм и плотностью более 12 гсм. Площади и объемы занимаемые циклонами неизмеримо меньше габаритов отстойников той же производительности. Для очистки тонких взвесей используются мультициклоны. Нашли применение открытые и напорные гидроциклоны;
- фильтры при очистке и доочистке стоков от тонкодисперсных примесей не удаляемых механически на других стадиях. При очистке городских стоков используются сетчатые фильтры с бактерицидными лампами установленными перед фильтрами с зернистой загрузкой. Фильтры с зернистой загрузкой (напорные) в первой ступени очистки или на доочистке вод. По типу конструкции применяются фильтры однослойные (из одного материала) двухслойные (из двух материалов разной плотности) многослойные каркасно-засыпные аэрируемые и с плавающей загрузкой. Фильтрующей загрузкой может служить кварцевый песок керамзит керамическая крошка пористая керамика горные породы дробленый антрацит. Размер зерен фильтрующей загрузки 05—2 мм высота фильтрующего слоя до 2 м.
Метод обратного отсоса (гиперфильтрации) получил широкое распространение из-за простоты оборудования способности работать при обычной температуре малой зависимости эффективности очистки от концентрации загрязнении возможность изъятия ценных продуктов. При этом методе очищаемые стоки непрерывно фильтруются под давлением через полупроводниковые мембраны задерживающие молекулы или ионы растворенных органических неорганических и бактериальных примесей. Недостатком метода является высокая стоимость мембран их быстрая изнашиваемость.
Физико-химические методы очистки применяют для удаления из стоков растворенных неорганических и органических веществ а также суспензированных и эмульгированных примесей. Хотя очистка с применением этих методов требует дорогих реагентов она широко используется из-за своей эффективности а иногда просто невозможно произвести очистку стоков другими способами (например многокомпонентных сточных вод с малой концентрацией загрязнений).
К физико-химическим методам относятся коагуляция и флокуляция флотация ионный обмен адсорбция экстракция ультрафикация кристаллизация дистилляция ректификация электродиализ дезорация.
Растворы коагулянтов и флокулянтов подаются дозировочным насосом в смеситель где смешиваются со сточной водой в течение нескольких минут. Затем эта смесь направляется в камеры хлопьеобразования где выдерживается до 30 мин в камере горизонтальной или до 10 минут вертикальной конструкции. После образования хлопьев обработанные стоки поступают на механические очистные сооружения (отстойники гидроциклоны).
Отходы производства вывозит автомобильным или железнодорожным транспортом в места определенного органами санитарного надзора.
1.4 Утилизация и ликвидация отходов
В процессе изготовления отливки в литейном цехе образуются следующие отходы:
-отходы металла лом брак отливок;
-промышленный мусор;
-осадки сточных вод;
-бой шамотного кирпича;
-бой периклазохромитового кирпича;
-бой электродов графитированных.
Лом металла - это изношенное и вышедшее из употребления детали и изделия например кокиля шаролитейной машины неподдающийся исправлению брак отливок крючки холодильники. Отходы металлов полностью используются в цехе при выплавке жидкого металла для мелющих шаров. Горелая земля не подлежащая использованию а так же шлаки образовавшиеся при выплавке жидкой стали и чугуна и весь промышленный мусор вывозятся транспортом на городскую сварку древесные отходы продаются населению для бытовых нужд. Осадки сточных вод складируются в специально отведенном месте бой шамотного кирпича складируется и хранится на предприятии пока не будет востребован бой периклазохромитового кирпича перемалываются на шаровой мельнице и используются как огнеупорный.
Опасные отходы в зависимости от степени их вредного воздействия на
здоровье человека подразделяются на классы опасности (I—IV) в соответствии с критериями установленными специально уполномоченными органами исполнительной власти.
Главным направлением в устранении или снижении вредного воздействия на окружающую среду токсичных отходов промышленности является их повторное использование в производственных циклах то есть организация малоотходных производств. Тем не менее для нейтрализации таких отходов часто устраивают специальные сооружения которые могут находиться как в пределах территории самого предприятия так и вне его. В последнем случае токсичные промышленные отходы могут складироваться перерабатываться на полигонах и станциях переработки и нейтрализации.
Полигоны устраивают двух видов: для обезвреживания одного вида отходов только захоронением или химическим способом а также комплексные. Во втором случае территорию полигона разделяют на зоны приема и захоронения твердых несгораемых отходов; приема и захоронения жидких химических отходов и осадков сточных вод не подлежащих утилизации; захоронения особо вредных отходов; огневого уничтожения горючих отходов.
Захоронение промышленных отходов осуществляют в котлованах глубиной до 10—12 м в специальной таре например стальных бочках. Их размещают в котлованах и железобетонных резервуарах (особо вредные отходы).
Выбор земельного участка для захоронения токсичных промышленных отходов должен производиться с соблюдением норм Санитарных правил о порядке накопления транспортировки обезвреживания и захоронения токсичных промышленных отходов и СНиП 2.01.28-85 «Полигоны по обезвреживанию и захоронению токсичных промышленных отходов. Основные положения по проектированию». В этих случаях отвод земельного участка подлежит обязательному согласованию с органами государственного экологического контроля и органами санитарно-эпидемиологического надзора.
Земельные участки выбранные для полигонов должны отвечать следующим требованиям: размещаться с подветренной стороны по отношению к населенным пунктам и зонам отдыха; находиться ниже мест водозаборов питьевой воды рыбоводных хозяйств мест нереста массового нагула и зимовальных ям рыбы; состоять из слабофильтрующих грунтов (глины суглинков сланцев и т.п.); залегание грунтовых вод при их наибольшем подъеме должно быть не менее 2 м от 3 нижнего уровня захороняемых отходов.
Запрещается размещать полигоны по обезвреживанию и захоронению токсичных промышленных отходов в заболоченных местах на территориях зеленых зон городов на землях занятых лесами или предназначенных для лесоразведения в зонах санитарной охраны курортов в зоне питания подземных источников питьевой воды в зонах активного карста в зонах оползней селевых потоков снежных лавин и т.п.
Вокруг полигона устраивают санитарно-защитную зону (СЗЗ) отделяющую их от населенных пунктов и открытых водоемов объектов используемых в культурно-оздоровительных целях. Величина СЗЗ устанавливается с учетом конкретных местных условий но не может быть менее 3000 м. Участки захоронения токсичных промышленных отходов должны размещаться не ближе чем в 200 м от сельскохозяйственных угодий автомобильных и железных дорог а также не ближе чем в 50 м от границ леса и лесопосадок не предназначенных для использования в рекреационных (для восстановления здоровья) целях. Размещение токсичных промышленных отходов под землей является пока одним из наиболее перспективных способов избавления от тех из них которые не могут быть утилизированы или полностью уничтожены путем сжигания а при накоплении их на земной поверхности представляют реальную опасность для биосферы. Подземное размещение промышленных отходов должно производиться при соблюдении ограничений относящихся к выбору места для создания подземных и заглубленных хранилищ (первая группа) и к их проектированию строительству и эксплуатации (вторая группа).
Первая группа ограничений. Подземное размещение промышленных отходов первого и второго классов может осуществляться только в геологических формациях создающих природный барьер для выноса подземными водами размещаемых веществ и продуктов их взаимодействия с окружающим массивом в биосферу. Регион их размещения не должен быть сейсмоопасен.
Приемлемыми формациями для размещения жидких промышленных отходов являются массивы горных пород представленные пористыми замкнутыми коллекторами.
Малотоксичные промышленные отходы могут размещаться и в иных геологических формациях если по этим формациям или через них не происходит миграция подземных вод и если нет опасности нарушения их водонепроницаемости под влиянием природных катаклизмов (землетрясения) или техногенных процессов при добыче полезного ископаемого с образованием такой миграции.
Вторая группа ограничений. Для создания подземных и заглубленных хранилищ малотоксичных промышленных отходов могут использоваться выработанные пространства вокруг которых по завершении эксплуатации хранилищ образуются водопроводящие каналы если воды проникшие в хранилища через эти каналы после контакта с отходами остаются в нем и не мигрируют в водоносные горизонты. Подземные хранилища для высокотоксичных отходов могут эксплуатироваться только после того как в них будут сооружены и опробованы средства изоляции выработанных пространств позволяющие при необходимости оперативно и навечно отделить размещенные отходы от биосферы.[15]
2 Статистические данные по заболеваемости рабочих литейного цеха от вредных веществ.
Рабочие трудятся на производстве где факторы окружающей среды характеризуются повышенной температурой подвижностью запыленностью и загазованностью воздуха ИК-излучением на рабочих местах в плавильном разливочномстержневомидругихотделениях.Неблагоприятные микрокли-матические условия на рабочих местах в значительной степени усугубляют влияние рабочей нагрузки. Для оценки уровня загрязнения воздуха рабочей зоны был составлен список вредных веществ (таблица 1) определяемых на данном производстве.
Таблица 1 - Характеристика токсичности используемых материалов в литейном цехе [17]
Степень воздействия фактора
(содержание SiO2>70%)
(содержание SiO2 10-70%)
(содержание SiO2 2-10%)
Промышленные и физические факторы производственной среды вызывают деструктивные изменения в уровне соматического здоровья степени постарения и коэффициенте здоровья.
В литейном цехе суммарный показатель загрязнения Рсум составил 134. Исходя из полученных результатов воздух рабочей зоны в данном цехе соответствует III степени загрязнения – «умеренно загрязненный». Однако помимо химических загрязнителей работники литейного цеха подвергаются таким физическим воздействиям как шум вибрация высокие температуры.
Трудовая деятельность в этих условиях предъявляет высокие требования к организму человека.
Рисунок 2 - Уровень физического воздействия
Лица работающие в условиях с более высокими показателями техногенной нагрузки имеют выраженное изменение параметров сердечнососудистой и дыхательной систем во всех возрастных группах.
У работников литейного цеха отмечено статистически достоверное увеличение артериального давления снижение жизненной емкости легких уменьшение времени произвольной задержки дыхания.
По количеству вредных веществ и величине комплексного показателя загрязнения воздух рабочей зоны в литейном цехе оценивается как умеренно загрязненный что соответствует III степени загрязнения.
Уровень функциональных и интегральных показателей физического здоровья у работников определяется сочетанным воздействием факторов физической и химической природы стажем работы на вредном производстве.[17]
3 Влияние литейного цеха на окружающую среду.
Литейный цех является наиболее крупным источником пылегазовыделения и загрязнением воздушной среды. При производстве одной тонны отливок выделяется 150 кг оксида углерода около 15 кг S 25-60кг пыли. Примерный состав пыли % Fe03 -568; Mn2O3-10; А12О3-50; S СаО-69; MgO-58 остальное хлориды оксиды хрома и фосфора.
Механическая очистка сточных вод выполняется до биологической и физико-химической являясь первой ступенью очистки на станциях. При этом происходит отделение нерастворимых примесей процеживанием отстаиванием или фильтрованием. При этом используется соответствующее оборудование.
Отходы металлов полностью используются в цехе при выплавке жидкого металла для мелющих шаров. Горелая земля не подлежащая использованию а так же шлаки образовавшиеся при выплавке жидкой стали и чугуна и весь промышленный мусор вывозятся транспортом на городскую сварку древесные отходы продаются населению для бытовых нужд. Осадки сточных вод складируются в специально отведенном месте бой шамотного кирпича складируется и хранится на предприятии пока не будет востребован бой периклазохромитового кирпича перемалываются на шаровой мельнице и используются как огнеупорный.
В целом влияние литейного цеха ТОО «ЗаводКазогнеупор» на экологию города Рудного и на экологию в целом оценивается как не значительное так как все нормы по очистке сточных вод по утилизации и ликвидации отходов соблюдены. Работа в литейном цехе ТОО «ЗаводКазогнеупор» является не опасной для жизни человека но оказывает незначительное влияние на его здоровье.[1]
1 Организация работы по охране труда на предприятии
Система управления промышленной безопасностью и охраной труда на ТОО «ЗаводКазогнеупор» (далее – система управления) определяет задачи по обеспечению здоровых и безопасных условий труда в соответствии с национальными законами и другими нормативными актами.
Управление охраной труда осуществляется путем организации работ в области охраны труда информации о состоянии охраны труда на рабочих местах участках в цехах и подразделениях и принятии управленческих решений. Информация о состоянии охраны труда на всех участках производства и об эффективности функционирования Системы управления должна являться основой для принятия управленческих решений.(Приложение И)
В отделе охраны труда работает один человек – заместитель главного инженера по охране труда и технике безопасности. Он подчиняется директору завода и главному инженеру. Выполняет контролирующую и организационную роль по обеспечению охраны труда на производстве. В должностную инструкцию каждого руководителя специалиста включены обязанности по организации и управлению охраной труда.
В целом управление охраной труда обеспечивается выполнением следующих функций:
- организация координация и регулирование работ по охране труда:
- планирование работ по охране труда:
- контроль за состоянием охраны труда:
-укрепление трудовой производственной и технологической дисциплины;
-повышение личной ответственности работников за состояние безопасности и охраны труда;
- учет анализ и оценка работ по охране труда;
- стимулирование работ по совершенствованию охраны труда.
В процессе функционирования Системы управления решаются следующие задачи:
- профотбор и обучение работающих безопасным приемам труда;
- пропаганда вопросов охраны труда и промышленной безопасности;
- обеспечение единой технической политики по созданию безопасных и здоровых условий труда;
- обеспечение безопасности производственного оборудования;
- обеспечение безопасности производственных процессов;
- обеспечение безопасности зданий и сооружений и сооружений и производственных территорий;
- разработка и внедрение новой высокопроизводительной и безопасной техники и технологии;
- нормализация санитарно-гигиенических условий труда;
- обеспечение работающих средствами индивидуальной защиты;
- обеспечение оптимальных режимов труда и отдыха;
- организация лечебно-профилактического обслуживания работающих;
- расследование несчастных случаев инцидентов аварий.
Ответственность за организацию работ и обеспечение выполнения требований охраны труда возлагается на руководителя (подразделения цеха производственного участка отделения службы) подразделения.
Оформление рабочих и служащих на тяжелые работы и работы с вредными опасными и неблагоприятными условиями труда а также подростков на все виды работ должно производиться на основании предварительных осмотров согласно приказу Министерства здравоохранения Республики Казахстан № 243 от 12.03.2004 года.
2 Освещение промышленного здания
Освещённость — это свет от какого-либо источника; создание освещенности поверхностей предметов обеспечивающей зрительное восприятие этих предметов.
Настоящие нормы должны соблюдаться при проектировании освещения помещений вновь строящихся и реконструируемых зданий и сооружений различного назначения мест производства вне зданий площадок промышленных и сельскохозяйственных предприятий и наружного освещения городов поселков и сельских населенных пунктов. Разделяют три типа освещения:
Помещения с постоянным пребыванием людей должны иметь как правило естественное освещение. Естественное освещение подразделяется на боковое верхнее и верхне-боковое (комбинированное). Установленные расчетом размеры световых проемов допускается изменять на +5 -10%. Неравномерность естественного освещения помещений производственных и общественных зданий с верхним или верхним и естественным боковым освещением и основных помещений для детей и подростков при боковом освещении не должна превышать 3:1. Солнцезащитные устройства в общественных и жилых зданиях следует предусматривать в соответствии с главами СНиП по проектированию этих зданий а также с главами по строительной теплотехнике.
Комбинированное освещение помещений жилых общественных и вспомогательных зданий допускается предусматривать в случаях когда это требуется по условиям выбора рациональных объемно-планировочных решений за исключением жилых комнат и кухонь жилых домов помещений для пребывания детей учебных и учебно-производственных помещений кабинетов врачей и палат лечебно-профилактических учреждений спальных помещений санаториев и домов отдыха. Применение ламп накаливания допускается в отдельных случаях когда по условиям технологии среды и требований оформления интерьера использование газоразрядных источников света невозможно или нецелесообразно.
3 Борьба с производственным шумом и вибрацией а так электробезопасность
Шумом называют комплекс звуков воспринимаемых органом слуха человека вне зависимости от характера и природы возникновения. Величина шума характеризуется двумя показателями: уровнем звукового давления и эквивалентным (по энергии) уровнем звука. Уровень звукового давления является показателем постоянного шума на рабочем месте и измеряется в децибелах (дБ). Эквивалентный уровень звука является показателем прерывистого импульсного шума на рабочем месте и измеряется в децибелах по шкале «А» (дБ).
Эффективным мероприятием по борьбе с шумом является снижение его в источнике образования т. е. в машинах механизмах и т. п. Для снижения шума в источнике заменяют например ударные процессы и механизмы безударными зубчатые и цепные передачи на клиноременные применяют принудительную смазку прокладочные материалы и упругие вставки в соединениях и т. п. Кроме того для борьбы с шумом в конструкцию оборудования встраивают амортизирующие и звукогасящие приспособления. В качестве индивидуальных средств защиты от воздействия производственного шума используют противошумные заглушки и наушники.
Вибрация – это колебательные процессы происходящие в механических системах. На практике вибрацию характеризуют по двум параметрам: колебательной скоростью т. е. максимальным перемещением колеблющейся точки в секунду (выражается смс) и интенсивностью т. е. количеством полных циклов колебаний в единицу времени. По аналогии с шумом интенсивность вибрации может измеряться децибелами.
Вибрацию подразделяют на местную и общую. Местная вибрация наблюдается при обрубке отливок пневматическими рубильными молотками. В условиях литейного производства общая вибрация образуется при сотрясении пола и других частей здания вследствие ударного действия выбивных решеток пневматических формовочных центробежных и других машин.
Снижение вибрации до предельно допустимых уровней достигается применением виброгасящих амортизирующих устройств и приспособлений систематическим ремонтом пневматического инструмента использованием виброзащитных рукавиц а также заменой рубильных молотков электрическими инструментами вращательного действия (абразивными станками с гибким валом и др.). Эти мероприятия одновременно снижают уровни вибрации и шума.
Согласно ГОСТу 12.1 – 0.13 – 78 производственные помещения проектируемого прокатного цеха с характерными для него высокими влажностью и температурой наличием токопроводящей пыли размещением оборудования на железобетонных перекрытиях относятся к группе II с повышенной опасностью.
Помещения предприятий в отношении поражения людей электрическим током разделяются на:
) особо опасные характеризующиеся наличием особой сырости (влажность близка к 100%) наличием химически активной среды разрушающе действующей на изоляцию и токоведущие части;
) с повышенной опасностью. Наличие сырости с влажностью более 75%. Наличие проводящей пыли наличие токопроводящих полов (металлических) наличие высокой температуры (более 30 градусов);
) без повышенной опасности.
Меры предупреждения: обеспечить невозможность случайного прикосновения к токоведущим частям применение токобезопасного напряжения 12-42 В установка защиты при переходе с токоведущих частей на нетоковедущие.
При нормальном режиме работы электроустановок защита человека обеспечивается: применением малых напряжений изолированием токоведущих частей изолированием электрических сетей от земли недоступностью токоведущих частей.
С целью предотвращения электротравматизма в аварийных режимах предусматривается: двойная изоляция защитное заземление защитное зануление защитное отключение.
4 Организационные мероприятия по технике безопасности.
Все работающие должны проходить обучение и инструктаж по правилам безопасности безопасным методам и приемам труда порядок и виды которого определены ГОСТ 12.0.004-90 «Положением о порядке инструктирования и обучения рабочих по безопасности труда» «Правилами проведения обучения инструктирования и проверок знаний работников по вопросам безопасности и охраны труда» утвержденными Приказом Министерства труда и социальной защиты Республики Казахстан от 03 апреля 2002 года № 314 «О промышленной безопасности на опасных производственных объектах».
Рабочие не реже двух раз в год должны проходить инструктаж и проверку знаний инструкций по безопасности и охране труда и системой управления охраной труда в комиссиях подразделения результаты проверки знаний оформляются протоколом.
В подразделении устанавливается следующая система контроля состояния охраны труда техники безопасности и промсанитарии:
- один раз в неделю (четверг) проводится день по технике безопасности и совещание постоянно действующей – Комитета по охране труда (по селектору);
- по графику проводиться целевая проверка состояния охраны труда инспекторскими группами главных специалистов срок согласованный службой охраны труда.
К нарушителям требований безопасности применяются меры дисциплинарного воздействия предусмотренные Трудовым кодексом Республики Казахстан.
В целях повышения материальной заинтересованности работников подразделения и повышения ответственности за состояние охраны труда систематическое ведение профилактической работы культуру производства в подразделении формируется фонд ОТ и ТБ.
5 Расследование несчастных случаев
Необходимость четкой классификации НС определяется различием в порядке расследования и учета НС а также возникновением неодинаковых правовых условий для пострадавшего. Так если НС классифицируется как связанный с производством то предусмотрено составление акта по установлено форме Н-1 определена обязательность учета и дополнительного возмещения ущерба причиненного здоровью пострадавшего. Если же НС классифицируется как связанный с работой то он регистрируется актом произвольной формы и по нему не предусматривается возмещение ущерба.
Целью каждого расследования и учета НС является выявление причин приведших к НС и выработка предупредительных мер для устранения этих причин.
Расследованию и учету в порядке предусмотренным «Положением» подлежат НС которые произошли:
- на территории предприятия;
- вне территории предприятия при выполнении пострадавшим трудовых обязанностей задания администрации предприятия руководителя работ (бригадира мастера начальника смены участка и т.д.) например на коммуникациях тепло- и электросети связи на ремонтных работах жилого фонда организации и т.д.
- при следовании на предоставленном предприятием транспорте на работу и с работы;
Расследованию и учету подлежат НС происшедшие как в течение рабочего времени так в течение времени необходимого для приведения в порядок оборудования орудий производства одежды и т.п. перед началом или окончании работы а также при выполнении работ в сверхурочное время выходные и праздничные дни.
НС связанные с работой расследуются комиссией социального страхования профсоюзного комитета с участием представителей администрации в течение 3 суток с момента установления факта НС.
НС связанные с работой могут оформиться актом произвольной формы но лучше по форме БТ. Акт составляется в одном экземпляре подписывается лицами проводившими расследование и хранится с больничным листком или справкой медицинского учреждения. В акте должно быть указано: «Несчастный случай связан с работой».
При выяснении обстоятельств НС должны быть установлены причины время и место происшествия а также состояние пострадавшего в момент получения травмы. Для этого используются объяснения пострадавшего показания свидетелей если они имеются медицинские справки материалы органов милиции ГАИ.
Оформление НС связанных с работой актом установлено формы способствует организации учета расследованию и анализу причин НС связанных с работой особенно тех которые произошли в пути на работу или с работы облегчает разработку мероприятий по предупреждению и снижению травматизма.
При групповых тяжелых и смертельных НС связанных с работой в отличии от НС связанного с производством специальное расследование не проводится.
6 Противопожарная безопасность
Пожар— неконтролируемый процесс горения причиняющий материальный ущерб вред жизни и здоровью людей.
В прокатном цехе имеются следующие средства пожаротушения ППБ-01-93: 1) для тушения электрооборудования - углекислотные огнетушители асбестовые и войлочные полотна; 2) на прокатном участке имеется песок для тушения металлов; 3) для тушения возгорания газа применяют углекислый газ и порошковые огнетушители; 4) меры пожарной безопасности проектируются в соответствии с ГОСТ 12.1.004-91; 5) в пожароопасных местах имеются таблички запрещающие использование открытого огня; 6) в цехе имеется пожарная сигнализация и средства тушения пожара.
Все отделения цеха имеют не менее двух эвакуационных выходов указанных выше. Этого достаточно для эвакуации максимально возможного числа рабочих от наиболее удалённого места работы до ближайшего эвакуационного выхода.
Пути эвакуации освещены в соответствии с требованиями СНиП 23-05.
Высота эвакуационных выходов не менее 2 м. и не менее ширина 0.8 м. Высота эвакуационных путей не менее 2 м. и ширина не менее 1.2 м.
Для предупреждения распространения пожара конструкции зданий снабжают поперечными и продольными противопожарными преградами препятствующими распространению пожара и обеспечивающими защиту от непосредственного распространения огня действия лучистой энергии и передачи тепла.
К противопожарным преградам относятся противопожарные стены и перекрытия а также проемы в этих преградах в которых устанавливают противопожарные завесы ворота двери окна.
Классификация материалов и помещений по пожарной опасности
Ущерб наносимый пожарами в значительной степени определяется разрушением зданий под действием огня. В свою очередь строительные материалы и конструкции реагируют на повышение температуры при пожаре по-разному: одни быстро поддаются воздействию огня а другие – длительное время сохраняют несущую способность. По способности строительных материалов сопротивляться воздействию высокой температуры и сохранять при этом свои эксплутационные функции определяется огнестойкость помещения. В соответствии с нормами технологического проектирования (НПБ-105-95) все производственные и складские помещения подразделяются на категории А (высшая) Б В Г Д. (Приложение К)
В соответствии с НПБ-105-95 противопожарные стены должны иметь минимальные пределы огнестойкости не менее 25 ч противопожарные перекрытия – 1ч а противопожарные перегородки не менее 075 ч.
7Санитарно-бытовые и медицинское обслуживание рабочих
Санитарно-бытовое обслуживаниеработающих является важнейшей частью организации строительной площадки так как особенности строительного производства сказываются и на заболеваемости рабочих.
Мероприятиясанитарно-бытового обслуживанияработающих включают постройку и оборудование комнат для приема пищи буфетов раздевалок-гардеробных сушилок для спецодежды душевых умывальников комнат гигиены женщин помещений для обогрева рабочих осенью и зимой.
7.1Средства индивидуальной защиты
Основными средствами индивидуальной защиты в прокатном цехе являются спецодежда спецобувь каски различные перчатки и рукавицы. Для защиты органов дыхания от пыли применяются респираторы и повязка типа «лепесток». Для защиты рабочих от высоких температур применяются термостойкие защитные щитки термоизоляционные комбинезоны и перчатки. Также в качестве защитных средств применяются различные крема и мази.
Организация труда и система управления предприятием
1.1 График выхода трудящихся
Графики выходов трудящихся приведены в таблице 7.1.
Таблица 7.1-График выходов на работа для годового непрерывного режима работы ( 2 смены 4 бригады)
1.2 Режимы работы прокатного цеха
Режимы работы прокатного цеха приведены в таблице 7.2.
Таблица 7.2-Показатели режима работы металлургического предприятия и его производственных показателей
Подразделения предприятия
Показатели режима работы
Продолжитель-ность смены час
Кол-во рабочих дней в году
График сменности служит дополнением к правилам внутреннего распорядка он утверждается директором предприятия.
1.3 Система заработной платы
Заработная плата оплачивается в соответствии с Законом о труде в РК индивидуальным трудовым и коллективным договорами.
Заработная плата рабочих начисляется по сдельно-премиальной системе и определяется их личными результатами и проводится в зависимости от конечных результатов работы коллектива.
Заработная плата выплачивается не реже одного раза в месяц и подразделяется на: сдельный заработок; поощрительный фонд; индивидуальные выплаты.
Сдельный заработок начисляется по тарифной расценке.
При выполнении условленных показателей работы на сдельный заработок смен и отдельных рабочих начисляется премия. Премирование производится в пределах образованного фонда заработной платы путем соответствующей корректировки размера премии установленного Положением об оплате труда на заводе.
Индивидуальные выплаты (доплата за работу в ночную смену праздничные дни и др.) производится в соответствии с трудовым законодательством другими нормативными актами и специальными постановлениями дирекции завода. Расчет фонда оплаты труда рабочих выполняется на основе списочной численности рабочих.
1.4 Расчет заработной платы
Заработная плата определяется исходя из баланса рабочего времени и тарифа.(Приложение Л)
Тарифная ставка соответственно часовая и тарифная для рабочего первого разряда определяется по соотношению:
Тгод – количество рабочих часов одного рабочего за год чгод;
Nд. год – количество рабочих дней за год сут.год.
Тарифные ставки других разрядов (Чтсi) рассчитываются на основе тарифной ставки рабочего первого разряда (Чтс1) и соответствующих этим разрядам тарифных коэффициентов (kтi):
При помесячной (окладной) системе учета расчет заработной платы осуществляется по формулам:
где Тф Nф –фактический отработанное время ч сут.;
Тпл Nпл – плановый фонд времени ч сут.
Рабочим промышленных предприятий кроме оплаты труда производятся различные доплаты к заработной плате под которыми понимаются – суммы денежных средств начисляемые для компенсации трудности работ в связи с выполнением дополнительной функции не входящих в прямые обязанности отклонением от нормальных условий труда а так же с целью сохранения за работником части заработной платы в случае ее уменьшения не по его вине.
Размер доплат устанавливается законодательством коллективным договором и другими соглашениями предприятий с профсоюзными организациями.
Премия за выполнение плана может быть учтена как доплата к прямой заработной плате и входит в состав основной заработной платы и соответственно в себестоимость. Общий размер премии за выполнение и перевыполнение плана по объему производства не может превышать определенного процента прямого заработка (4060 %).
Доплаты не освобожденным бригадирам из числа рабочих за руководство бригадой производится в зависимости от численности бригады. Размер доплат при численности бригады 5 10 человек составляет 710 % тарифной ставки а при численности более 10 человек – 1015 %.
Фонд дополнительной заработной платы исчисляется обычно в процентах к дневному или тарифному фонду и складывается из оплаты очередных и дополнительных отпусков прочих выплат из фонда дополнительной заработной платы (оплата времени затраченного на выполнение государственных и общественных обязанностей; оплата льготных часов подросткам и перерывов матерям для кормления детей; выходные пособия). При этом оплата за отпуска (dо) и за выполнение государственных и общественных обязанностей (dгоо) начисляется в процентах от основного дневного заработка рабочего а остальные доплаты (dпр) - от тарифного. Поэтому дополнительная заработная плата за один день работы может быть условно выражена формулой:
а годовой фонд дополнительной заработной платы определяется по формуле:
где tм – количество дней работы в течение года рабочего места сут.;
tраб – количество дней работы в году одного рабочего сут.
Процент оплаты очередных и дополнительных отпусков определяется исходя из дней отпуска и числа рабочих дней по формуле:
где Фопт – число дней очередного и дополнительного отпуска сут.
Фраб – число рабочих дней в году без учета основного и
дополнительного отпусков сут.
Таблица 7.4-Расчет фонда оплаты труда
Тарифная ставка тенгесм
Прямая зарплата тенгегод·чел.
Доплаты тенгегод·чел
Основная зарплата тенгегодл·чел
Дополн-ая зарплата тенгегод·чел
Фонд оплаты труда тенгегод·чел
Общий фонд оплаты труда тенгегод
Коэфф. спис-го состава kcc
рабочего времени сут.чел.
Участники трудового процесса поощряются за добросовестный труд и достигнутые производственные и экономические результаты.
2.1 Материальные формы поощрения
-В объединении применяются сдельная повременная и другие системы оплаты труда.
-Оплата труда производится на основании утвержденных тарифных ставок и должностных окладов.
-Для работников особо дефицитных профессий высокой квалификации применяются контрактная форма договора (дополнение к ИТД).
-При совмещении профессий (должностей) выполнении работ с меньшей численностью персонала выполнении обязанностей временно отсутствующих работников производятся доплаты к тарифным ставкам (должностным окладам).
-Работникам труд которых связан с особым режимом работы и условиями устанавливаются компенсационные выплаты.
-При выполнении производственных показателей выплачивается премия за месяц квартал.
-За выполнение особо важных срочных заданий выплачивается разовая премия.
-За разработку и внедрение изобретений рационализаторских предложений работникам выплачивается вознаграждение.
-По итогам хозяйственной деятельности за год выплачивается вознаграждение.
-За достижение призовых мест в соревновании при различных видах морального поощрения - при объявлении благодарности присвоения звания и т.д. выплачивается денежная премия.
Другие формы материального поощрения.
-Работникам оплачиваются дополнительные дни отпуска за работу во вредных и опасных условиях труда.
-Производится единовременная выплата при увольнении в связи с выходом на пенсию по возрасту или инвалидности.
-Многодетным семьям оказывается материальная помощь.
-Нуждающимся выделяется ссуда на лечение жилье обучение.
-Выплачивается единовременное пособие на погребение умерших работников и пенсионеров.
-Оказывается материальная помощь пенсионерам.
-Приобретаются новогодние подарки детям работников.
-Выделяются льготные путевки в лечебно-оздоровительный центр.
2.3 Моральные формы поощрения
В качестве поощрения в объединении используются:
-объявление благодарности;
-награждение Почетной грамотой;
-занесение на Доску почета подразделения объединения города;
-награждение ценным подарком;
-признание победителем в разных формах трудовых соревнований;
-проведение конкурсов профессионального мастерства среди молодых рабочих;
-публикации в периодических изданиях показ по ТВ;
-присвоение почетных званий;
-представление к награждению почетным знаком ЕПА;
-представление к награждению отраслевыми почетными знаками;
-представление к награждению государственными наградами РК.
3 Система управления предприятием
Производственная структура представляет собой совокупность относительно самостоятельных частей (цехов участков служб) которые связаны между собой отношениями производственной кооперации.
Все внутриструктурные подразделения предприятия должны быть подразделены по назначению и видам производства на:
- основные производственные цехи и участки производящие работы так или иначе связанные с основным видом производства;
- вспомогательные подразделения участвующие в производстве обеспечивая работу основных цехов;
- обслуживающие подразделения (Складское хозяйство АХО Служба охраны Участок по содержанию зданий и сооружений Служба обслуживающего автотранспорта).
Состав управленческих подразделений их подчиненность связи и разделение функций между ними образуют структуру аппарата управления. Отдел создается при численности не менее 5 человек включая руководителя. Если численность меньше то создается объединенный отдел с суммированием количества работников и соответствующим расширением функций.
Структура аппарата управления как правило имеет многоуровневую структуру управления (президент объединения - начальник структурного подразделения - начальник участка или цеха – старший мастер - мастер). В не больших структурных подразделениях используются структура управления при которой мастер подчиняется непосредственно начальнику структурного подразделения (бесцеховая или участковая структура управления).
Основными структурными (производственными) единицами являются цех и участок (с правами цеха) для управления которыми создаются специальные аппараты управления.
Система руководства рудоуправлением может состоять из 4 уровней:
- начальник предприятия (главный инженер);
- начальник участка (цеха);
- старший мастер (начальник смены);
Для определения организационной структуры управления структура аппарата управления дополняется связями с производственными подразделениями.
В состав системы оперативного управления предприятий входит диспетчерская служба обеспечивающая достижение согласованной работы всех подразделений в соответствии с графиками работы. Диспетчерская служба подчиняется главному инженеру и осуществляется старшими мастерами горными диспетчерами диспетчерами по транспорту телефонистами операторами.
1 Архитектурно-строительные решения
Данное здание запроектировано простой прямоугольной формы. Размер здания по осям 84х30 м.
1.1 Каркас промышленного здания.
Колонны - вертикальные элементы служащие для опирания на них несущих конструкций покрытия восприятия крановых и технологических нагрузок.
В качестве каркаса использованы железобетонные двухветвевые колонны с проходом в уровне крановых путей сечением 500х400 мм.
Для проходов в шейке колонны устроены лазы размером 400х2200мм.
Шаг крайних колонн 6 м. Шаг средних колонн 6 м.
Колонны снабжены закладными элементами для распалубки и крепления инвентарных монтажных приспособлений опирания стальных или железобетонных подкрановых балок и стропильных конструкций опирания и навески стеновых панелей и крепления стальных связей.
В торцах здания для крепления стеновых панелей устанавливаются колонны торцевого фахверка размером 400х400 мм. Колонны изготовляются из бетона марок М200 и выше и арматура из горячекатаной стали периодического профиля класса А-III. Серия 460-75.
В поперечном направлении устойчивость зданий обеспечивается жесткостью заделанных в фундамент колонн и жестким диском покрытия в продольном направлении - дополнительно стальными связями устанавливаемыми по всем рядам между колоннами и опорами стропильных конструкций.
Межколонные стальные связи располагаются в среднем шаге температурного блока в здании с опорными кранами в пределах высоты подкрановой части колонн. При шаге колонн 6 м. используются крестовые связи. Рядовые колонны соединяются со связевыми колоннами подкрановыми балками.
1.2 Фундаменты и фундаментные балки
Колонны каркаса опирают на отдельные железобетонные фундаменты с подколонниками стаканного типа а стены – на фундаментные балки (бетон М200 арматура А-III серия 1.415-1).
В проекте используют унифицированные монолитные фундаменты имеющие ступенчатую конструкцию с подколонником и стаканом для заделки колонн. Для их изготовления применяют бетон М200 и выше и арматуру в виде сеток из стали классов А-I и А-II.Серия 1.412-177.
Стены каркасных зданий опирают на железобетонные фундаментные балки укладываемые между подколонниками фундаментов на бетонные стяжки сечением 300·600 мм.
В местах устройства ворот для проезда автомобильного транспорта фундаментные балки не предусматривают. Участки стены в пределах этого шага колонн и рамы ворот опирают на бетонную подготовку. По фундаментным балкам для гидроизоляции стен укладывают два слоя рулонного материала на мастике. От деформации при пучении грунтов снизу и с их боков делают подсыпку из шлака.
1.3 Стеновое ограждение и проверочный расчет тепловой защиты
Наружные стены предусмотрены самонесущие панельные толщиной 350мм что вполне обеспечивает необходимый температурно-влажностный режим помещения. Стеновые панели (бетон М100арматура А-II и А-III серия 1.432-12) при правильном конструктивном выполнении полностью отвечают требованиям предъявляемым к ограждающим конструкциям. Они хорошо противостоят атмосферным воздействиям не допускают проникания влаги внутрь конструкции воспринимают нагрузки от собственной массы вышележащих конструкций и от напора ветра действующего на поверхность панели; они также хорошо противостоят воздействиям возникающим в процессе эксплуатации технологического оборудования и внутрицехового транспорта в том числе и воздействиям агрессивного характера.
1.4 Покрытия и перекрытия
Покрытие промышленного здания определяет долговечность здания в целом характер внутреннего пространства.
Покрытия устраивают бесчердачным. Состоит оно из несущих и ограждающих конструкций. Несущие конструкции покрытия устраивают в виде стропильных ферм (бетон М300 арматура А-III серия ПК-01-12968) которые поддерживают ограждающую часть. Ограждающая часть покрытия кроме защиты помещений от атмосферных воздействий вместе с несущими конструкциями обеспечивают зданиям пространственную жесткость.
Предусмотрен внутренний водоотвод с покрытий: состоит из водоприемных воронок водосточных труб стояков подвесных трубопроводов и выпусков.
Внутренние перегородки отделяют помещения в которых располагаются технологические процессы с особо шумными процессами с повышенными требованиями к производственному комфорту а также как противопожарные преграды. Так как в данном производственном здании нет подобных процессов которые необходимо отделять друг от друга то перегородки не проектируем.
Покрытие полов в производственных цехах - цементно-песчаные. Верхний слой – бетон высотой 100 мм непосредственно подвергающегося всем эксплуатационным воздействиям. Прослойка - цементно-песчаный раствор толщина слоя 15 мм. Гидроизоляция - препятствует проникновению через пол сточных вод и других жидкостей устраивают из материалов на основе битумов и выполняют в два слоя. Основанием под пол является грунт. В грунт вдавливают щебень на глубину 40мм.
1.7 Окна. Двери. Ворота
Применяются стальные оконные панели из листового стекла со стальными переплетами. В данном проекте применяются коробки панелей размером 6x18м. и 6х12м.
Ворота распашные двухпольные (серия ПР-05-36). Воротный проем обрамляется сборной железобетонной рамой вписывающейся по внешним размерам в принятую разрезку панельной стены. В одном из воротных полотен устраивается калитка.
В промышленных зданиях в основном применяют кровли из рулонных материалов с битумной пропиткой. Основанием для кровли служит стальной профилированный настил с высотой волны 60мм. Гофрированные профили выполняются из стального оцинкованного и покрытого слоями пластика листа толщиной до 1мм. Профили поставляются длиной от 2 до 12 м в комплекте с самонарезающими болтами служащими для крепления настила к стальным прогонам и комбинированными заклепками предназначенными для соединения листов между собой. Рубероидную кровлю составляют:
- защитный слой гравия толщиной 15мм фракцией 5-15мм утопленный в битумную мастику. Защитный слой гравия исключает механические повреждения при хождении по кровле и сбрасывании снега.
- 3-слойный водоизоляционный рубероидный ковер толщиной 30мм наклеенный кровельной битумной мастикой подогретой до 160-190 градусов.
- защитный из цементно-песчаной стяжки толщиной 20 мм.
- теплоизоляционный слой из пенополиуретана толщиной 60мм.
- пароизоляция выполняется из слоя рубероида толщиной 1мм на битуме марки БНК- 5.
Служебные лестницы устраивают для сообщения с рабочими площадками с которых рабочие обслуживают технологические агрегаты и осматривают ответственные строительные конструкции.
Служебные лестницы монтируют из маршей и переходных площадок. Уклон маршей к горизонту принимаем 60 градусов ширину - 1000 мм. Шаг проступней 200 мм. Марш имеет ограждения с поручнями.
Пожарные лестницы в зданиях делаем вертикальными. У лестниц предусматриваем ограждения. Размещаем такие лестницы напротив глухих участков стен.
1.10 Наружная и внутренняя отделка
Внутри и снаружи производственных помещений нужна дополнительная отделка. Стеновые панели зачищаются затем наносится цементно-песчаный раствор для выравнивания поверхности и заделки стыковых соединений стеновых панелей после чего производится побелка всех производственных помещений. Ворота и двери окрашиваются краской.
2 Отопление вентиляция и кондиционирование
Отопление водяное теплоноситель – вода температурой 95-70оС.
Вентиляция – приточно-вытяжная с механическим побуждением.
Системы вентиляции и кондиционирования воздуха проектируются согласно СНиП II-33-75 и сведены в Приложение М
3 Водоснабжение и канализация
В проектируемом прокатном цехе предусматриваются следующие системы водоснабжения: хозяйственно-противопожарная; производственная свежей воды; производственная оборотной воды.
В производственных и вспомогательных зданиях предусматривается установка приборов для учета расхода свежей оборотной воды. Расходомеры устанавливаются как на вводах так и у отдельных потребителей.
В проектируемом прокатном цехе предусматриваются следующие системы канализации: производственная бытовая и дождевая.
Список использованной литературы
Иванченко Ф. К. и др. Расчеты грузоподъемных и транспортирующих машин. Киев: "Вища школа" 1978.
Овсянников К. М.. Основы расчета вакуумных систем применяемых в литейном производстве. М.: Машиностроение 1971.
Минаев А. А.. Вакуумная формовка. М.: Машиностроение 1984.
Васильев В. А.. Физико-химические основы литейного производства. М.: МВТУ им. Н. Э. Баумана 1994.
Фролов Е. С. и др. Вакуумная техника. Справочник. М.: Машиностроение 1992.
Дорошенко В. С. Шинский И. О. Бердыев К. Х. Оборудование непрерывного действия для литья по газифицируемым моделям Процессы литья – 2009.- №2. – С. 56 – 61.
Дорошенко В. С. Бердыев К. Х. Шинский И. О. Структура цеха литья по газифицируемым моделям и особенности его проектирования Металл и литье Украины. – 2010.- №4 . – С. 8 –16.
Дорошенко В. С. Бердыев К.Х. Шинский И.О. Обобщение опыта изготовления пенополистироловых литейных моделей. Металл и литье Украины. – 2010.- №5. – С. 14 – 19.
Бердыев К. Х. Дорошенко В. С. Проходное оборудование для получения пенопластовых литейных моделей. Станочный парк. – Санкт-Петербург. -2010. -№1-2.- С. 36-37.
Дорошенко В. С. Шинский И. О. 3D-технологии при литье по газифицируемым моделям Металл и литье Украины. – 2009.- № 4-5. – С. 30 – 33
Дорошенко В. С. Шинский И. О. Бердыев К. Х. Структура цеха литья по газифицируемым моделям и особенности его проектирования. Металл и литье Украины. – 2010.- №4. – С. 8 – 16.
Шинский О. И. Газогидродинамика и технология литья железоуглеродистых и цветных сплавов по газифицируемым моделям. К.: Автореф. дисс. д. т. н. 1997. 43 с.
Шуляк В. С. Литье по газифицируемым моделям. – СПб.: НПО «Профессионал» 2007.- С. 200.
Барский В. Т. Производство литых заготовок методом вакумно-пленочной формовки. - М.: ЦНИИЕЭстроймаш 1985. – С. 9.
Дорошенко В. С. Бердыев К.Х. Современные тенденции конструирования опочной оснастки для ЛГМ. Металл и литье Украины. – 201 .- № . – С. – .
Дорошенко В. С. Бердыев К. Х. Болюх В. А. Вакуумные системы формовочно-заливочных участков цехов ЛГМ. Металл и литье Украины. – 2010.- №7. – С. 32 – 37.
ГОСТ 2.301-68. ЕСКД – форматы на чертежи пояснительную записку;
ГОСТ 2.302-68. ЕСКД – масштабы;
ГОСТ 2.303-68. ЕСКД – линии;
ГОСТ 2.304-81. ЕСКД – шрифты чертежные
Рыбаков С. А. Инновационные возможности литья по газифицируемым моделям состояние и перспективы этого метода в России Литейщик России. № 4 2009 с. 44-45.
Рахимов З. Р. Методические указания к экономической части дипломной работы для студентов специальности 050709 – «Металлургия» всех форм обучения. – Рудный: РИИ 2007. – 25 с.
СНиП II-89-90 «Генеральные планы. Нормы проектирования»;
СНиП II-92-76 «Вспомогательные здания и помещения промышленных предприятий»;
Отчет по преддипломной практике 2011.
СНиП II-4-79 «Естественное и искусственное освещение»;
Ахлюстин В.К. Электрификация ОФ.-М.: Недра 1973.
Сперанский Б. С. Туманский Б. Ф. Охрана окружающей среды в литейном производстве. – Киев; Донецк: Вища шк. Головное изд-во 1985. – 80 с.
Гринин А. С. Новиков В. Н. Промышленные и бытовые отходы: хранение утилизация переработка. – М.: ФАИР-ПРЕСС 2002. – 336с.
Экологический паспорт предприятия.
Воскобойников В.Г Кудрин В.А. A.M. Якушев. «Общая металлургия». М.: ИКЦ "Академкнига". 2002г.
ГОСТ 12.1.005-76 «ССБТ Воздух рабочей зоны»;
СНиП II-2-80 «Противопожарные нормы»;
ГОСТ 12.1.004-85 «Пожарная безопасность»;
СНиП II-90-81 «Производственные здания»;
СНиП 245-71 «Санитарные нормы проектирования промышленных зданий»;
Трепененков Р.И. Альбом чертежей конструкций и деталей промышленных зданий: Учеб. пособие для вузов. – 3-е изд. перераб. и доп. – М.: Стройиздат 1980. – 284с.
СНиП II-33-75 «Отопление вентиляция и кондиционирование воздуха»;
Разрез А- А лит цех.cdw

Мостовой кран груз. Q = 10 тн.
Гидроизоляция 1 слой толя 3
Железобетонный настил 30
-х слойный рулонный ковер 20
Цементно-песчаная стяжка 10
Спец часть Современные тенденции конструирования опочной оснастки для лгм.doc
Опочная оснастка для ЛГМ обладает рядом конструктивных особенностей которые описаны в статье. Эту оснастку используют в действующих литейных цехах. Модернизация литейного производства при переходе на качественно новую ступень технологического использования науки и экологической культуры чем является ЛГМ в вакуумируемые формы из песка без связующего востребует эти отечественными техническими разработки.
Ключевые слова: опока литейный контейнер ЛГМ конструирование вакуум.
В последних публикациях технической прессы России литейной тематики по мере выхода из экономического кризиса усилилось внимание к проблемам модернизации литейного производства. Среди формовочных процессов предпочтение отдается новым видам песчано-глинистой сырой формовки и ХТС. Объем выпуска отливок способом ВПФ прогнозируется в районе 3%. При этом практически не уделяется внимание процессу литья по газифицируемым моделям (ЛГМ - процесс). Многолетний опыт изготовления отливок развесом 01-12000 кг. постоянное совершенствование технологии ЛГМ и организация ряда цехов с поставкой для них полного комплекта оборудования производительностью 500 – 20 000 тонн отливок в год свидетельствует о значительном неиспользуемом потенциале ЛГМ. Последние работы проведенные компанией по литью крупных стальных отливок массой до 6 т. для ремонта МНЛЗ разновидностью ЛГМ-процесса (называемой Full Mold Process) с использованием холоднотвердеющих в т.ч. жидкоподвижных - ЖСС смесей [1] показали что сфера действия ЛГМ может охватывать почти всю традиционную песчаную формовку.
Кроме того быстро прогрессируя ЛГМ-процесс достиг высокой гибкости технологии изготовления моделей из пожалуй наиболее легко обрабатываемого среди современных твердых промышленных материалов – пенополистирола (ППС) которая включает четыре взаимодополняющих варианта: на 3D-фрезерах в пресс-формах на полуавтоматах или в автоклавах а также на столах с нагретой струной. Короткая продолжительность формовки состоящая в засыпке сухим песком моделей в контейнерных опоках с виброуплотнением до двух минут соответствует этой тенденции гибкости независимо от того индивидуальное это производство отливок или крупносерийное. Тому же способствует ускоряющая технологическую подготовку практика использования программного проектирования и производства литой алюминиевой модельной оснастки способом ЛГМ для серийного производства отливок этим же способом.
Слабое внедрение ЛГМ в отечественное производство (и стран СНГ) можно объяснить недостаточной осведомленностью литейщиков и промышленников о несложных принципах регулирования газового давления на границе металл-форма по законам газодинамики и гидравлики о наличии достаточно простого преимущественно отечественного оборудования для модельного и формовочного производства. Недопонимание физики пока еще малопопулярного в производстве СНГ процесса ЛГМ включая принцип «работы» вакуумируемой опочной оснастки дает предпочтение знакомой традиционной формовке со связующим при выборе технологических процессов для модернизации цехов тем более при обильной рекламе импортеров оборудования для ХТС даже при том что в последующем при эксплуатации выясняется что стоимость смоляной связующей композиции доходит до 500 на тонну литья. Применение смесей со связующим сопровождается неблагоприятной экологией литейного цеха и малопривлекательностью труда в нем если его не переводят на качественно новый уровень экологической культуры.
Применению вакуума в форме при ЛГМ предшествовало то что газы от деструкции ППС модели отводились через перфорации опок и проколы в песчаном наполнителе в атмосферу цеха что по сегодняшним меркам просто недопустимо. Дальнейшие исследования физико-химии технологии ЛГМ гидродинамики процесса с подвижным фронтом газификации модели как химического и фазового источника газовыделения теории фильтрации песка при применении вакуума дали новые положительные результаты для получения качественных отливок и повышения экологии производства. Проведенные специалистами научно-исследовательские и опытно-конструкторские работы определили параметры необходимого вакуума в формах в процессе заполнении их металлом включая саморегулирующее действие на заливаемый металл давления продуктов газификации с учетом заданного режима фильтрации этих продуктов вглубь вакуумируемого песка что привело к созданию ряда новых разновидностей этого способа литья и соответствующего технологического оборудования стабильно обеспечивающего целостность литейной формы при заливке при получении точных и отливок с качественной поверхностью.
При ЛГМ технологические операции определяющие получение отливок с наименьшими трудовыми и материальными затратами обычно выполняют в такой последовательности: 1) проектирование технологии литья с выбором положения модели в форме вида и размеров литниково-питающей системы (ЛПС); 2) получение моделей; 3) формовка; 4) плавка металла нужной марки и заливка им формы. Анализ работы цехов и участков ЛГМ показывает что качество отливок обычно зависит: до ~50% от качества модели собранного модельного блока его покрытия специальной краской (т.е. от соблюдения технологии изготовления модели); до ~25% от положения модельного блокакуста в литейных контейнерах качества формовочного материала – песка степени его виброуплотнения и герметизации (т.е. от режима формовки); до ~25% - от работы вакуумной системы при отсосе газов деструкции ППС во время заливки температуры и качества жидкого металла от поддержания заданной скорости заливки в правильно подобранной ЛПС. Две последние группы факторов касаются правильного выбора для каждого типажа моделей контейнерной опочной оснастки и ее функционирования.
Технологические особенности получения моделей из ППС описаны в статье [2]. Затраты на изготовление модели в среднем составляет до 20% и более при единичном изготовлении от всей стоимости отливки. Подробнее рассмотрим цикл формовки который при ЛГМ включает следующие технологические операции:
) подача очищенного и обеспыленного формовочного материала – огнеупорного наполнителя в контейнер (с содержанием пылевидных частиц до 8% и с температурой ниже 40 С);
) создание песчаной "постели" в литейном контейнере;
) контроль формовщиком моделимодельного блока (куста) с ЛПС на отсутствие отслоений противопригарного покрытия щелей в местах склейки частей модели стояка питателей прибылей и др.;
) установка моделиблока на "постель" в контейнере;
) послойная засыпка контейнера с виброуплотнением для заполнения песком полостей модели (которые в традиционных формах со связующим изготовленных по постоянным моделям выполняют стержнями).
) герметизация контейнера с установкой литейной чаши а также засыпки защитного слоя песка на герметизирующую пленку от прожога каплями жидкого металла при заливке;
) транспортирование контейнерной формы на заливочный плац и подключение ее к рукаву вакуумной системы с последующим включением вакуумного насоса лишь на период заливки с выдержкой 05-5 мин. после нее для затвердевания отливки.
При литье деталей мелкого развеса на кусте могут быть десятки моделей. При неправильном составлении куста часть моделей могут подвергнуться серьезной термодеформации от теплоты ранее залившихся отливок на этом кусте. Кроме этого нарушение равномерности эвакуации газов - продуктов деструкции моделей приводит к таким видам брака как недолив газовые раковины ужимины пригар и т.д.
Требования к вакуумным системам участков ЛГМ описаны в работе [3]. Поддерживать заданный режим вакуумирования на границе металл-форма а также быть емкостью для удобного засыпания-высыпания удержания и уплотнения песка литейной формы фиксирующего фасонную поверхность отливки и служащего опорой для жидкого металла твердеющего в отливку есть функции опочной оснастки. Ее еще можно рассматривать как продолжение вакуумной системы литейного участка в виде герметичной ячейки. Очевидно что вместе оснастка уплотненный песок и модель составляют литейную форму. Задачей конструирования такой оснастки является обеспечение указанных функций с минимальными затратами. Ранее конструкции вакуумируемой оснастки рассматривались прежде всего для ВПФ [4] описания таких контейнеров для ЛГМ авторам не известны.
За время внедрения ЛГМ-процесса в литейных цехах компании и других предприятиях созданы вакуумируемые литейные контейнеры (ЛК) различных форм и конструкций. Приводим их описания и достоинства по опыту эксплуатации ЛГМ разной серийности на различных предприятиях в различных странах.
Первые конструкции ЛК были без средств вакуумирования для чего использовали традиционные опоки [1] либо герметично сваренные ящики. Спустя два десятилетия для форм из песка без связующего в 80-х годах прошлого века стали применять вакуумирование что стабилизировало прочность формы стало обязательным фактором для получения высококачественных отливок а также кардинально улучшило экологию литья.
Первые контейнеры цилиндрической или прямоугольной формы имели каналы различной формы или перфорированные профили с закрывающими их сетками для защиты от проникновения песка. Использовали сетки с мелкими ячейками или более крупные в несколько слоев. Мелкие частицы песка уносимые газами деструкции попадая в каналы вместе с конденсацией газообразных продуктов ППС со временем резко уменьшают проходное сечение. Конструкция первых контейнеров с сетчатыми стенками приведена на рис. 1.
– Корпус с перфорацией; 2 – Сетка; 3 – Рамка прижимная
Рис. 1. Контейнер с вентилируемыми стенками без вакуумирования.
Для предотвращения ухудшения условий откачки регулярно разбирали и очищали каналы сетки. По этой причине также типы ЛК хотя просты конструктивно и недороги при изготовлении но в эксплуатации более трудозатратны. Основным недостатком ЛК такой конструкции является разноудаленность различных частей модели от сетчатого фильтра что приводит к неравномерности эвакуации газов деструкции модели. Особенно очень сложно осуществить оптимальный вывод газов когда отливка крупная сложной конфигурации и с отверстием и полостями в середине. С целью устранения этого недостатка в середину ЛК установили перфорированную обтянутую сеткой прямоугольную трубу (рис. 2). В ЛК такой конструкции условия получения отливок при ЛГМ более приближены к требуемым.
– Корпус; 2 – Стойки; 3 – Сетка; 4 – Узел (штуцер) вакуумирования
Рис. 2. ЛК с фигурной системой вакуумирования.
Работы по усовершенствования конструкций ЛК проведенные конструкторами и технологами привели к использованию стандартных гибких спиральных труб имеющих перфорацию или межвитковые щели. Они укладываются по высоте в несколько слоев по бортам ЛК в специальные перфорированные профили а их концы соединены в общий короб с патрубком к которому подсоединяется вакуумная система. Расстояние между слоями спиральных труб не превышает 800 мм. Используемые ЛК такой конструкции оказались более эффективными. Дальнейшая модификация привела к отказу укладки гибкого трубопровода в перфорированные угольники трубы гнутые П-образные профили а навеска его на специальные крюки из круга или листа. Это позволяет легко снимать гибкие трубы и укладывать их вокруг и внутри модели на требуемых расстояниях. Увеличивается откачиваемость газов что определяет выход качественных отливок (брак 2-3%) без науглероживания и газовых раковин. Эти ЛК можно использовать для получения отливок различного развеса со сложными формами. Основание (дно) контейнера из толстого листа обеспечивает равномерный контакт с плитой вибростола а также использование рольгангов приводных и бесприводных для перемещения между технологическими площадками формовочно-заливочного участка.
Последние модели ЛК имеют донную разгрузку при помощи рычажного механизма. Их удобно перемещать они высокоэффективны для литья с вакуумированием в процессе выполнения технологических операций легко перемещаются по замкнутой конвейерной рольганговой системе (с приводом или без) литейного цеха в количестве до нескольких десятков штук быстро высыпаются без опрокидывания что улучшает санитарно-гигиенические условия из-за устранения запыленности воздуха на участке выбивки. Такая конструкция ЛК приведена на рис. 3. Опыт эксплуатации этих ЛК в цехе ЛГМ производительностью до 5 000 т. отливокгод показал их высокую универсальность и надежность.
– дно; 2 – донная часть; 3 – узел выгрузки; 4 – стойки; 5 – боковые стенки; 6 – гибкие рукава; 7 – защитные профили; 8 – усилительные ребра; 9 – узел вакуумирования
Рис.3 ЛК с донной разгрузкой: а) вид сбоку б) фото сверху ЛК с 4-мя рядами гибких рукавов.
Для серийного получения крупногабаритных пространственных отливок например боковых рам тележек вагонов валков прокатных станов трубчатых элементов скважинной запорной арматуры корпусов («улиток») насосов часто делают специальные литейные контейнеры а для разовых отливок могут применять различные металлические ящики навесив на их стенки гибкие трубчатые фильтры и загерметизировав пленкой возможные щели на стенках (например челюстных контейнеров). В этих случаях делать элементы донной разгрузки не всегда возможно и не целесообразно. Элементы вакуумной системы гибкие спиральные трубы и соединения рассчитываются исходя из объема газов деструкции. Они должны обеспечивать равномерность откачки быть равноудаленными от стенок моделиотливки. Конструкция ЛК должна быть жесткой т. к. в отличие от традиционного способа литья в песчано-глинистые формы ЛГМ-процесс позволяет разделение технологических площадок (участков) – формовки заливки выбивки очистки и др при перемещении формы в ЛК между которыми (например с плаца формовки на заливочный плац) модели из ППС особенно ажурные и тонкостенные при деформации стенок ЛК могут повредиться а ЛПС отломаться.
На предприятиях где отливки цилиндрической формы составляют значительную часть производственной программы обычно применяют ЛК цилиндрической формы высота которых должна превышать максимальную длину детали. Получение крупногабаритных отливок со сквозными или глухими полостями в теле представляют определенную трудность из-за опасности обрушения песка при заливке или искривления модели при формовке или перемещении контейнера вдоль плаца. В таких случаях усиливают жесткость ППС модели установкой металлических стержней в песке рядом или в полости модели заполненной песком. Технологи-формовщики разработали ряд различных способов повышения жесткости моделей с габаритами 2 и более метров что позволяет получать стабильно качественные крупногабаритные сравнительно тонкостенные отливки массой до 1-15 т. без опасности их коробления.
Как указано выше получение качественных отливок методом ЛГМ аналогично всем литейным технологиям зависит от многих технологических факторов. Поскольку фактор качества модели при ЛГМ является определяющим а стоимость модели особенно при индивидуальном литье может существенно влиять на стоимость отливки следует тщательно выполнять операции формовки и заливки чтобы зря не испортить модель. Это часто зависит от конструкции применяемого оборудования и оснастки. С учетом вышеприведенной аргументации конструкция ЛК должна удовлетворять следующим требованиям: 1) жесткость 2) герметичность 3) равномерность вакуумирования по поверхности модели или по объему песка (подробнее см. [4]) 4) удобство эксплуатации включая требования безопасности труда и экологии 5) ремонтопригодность 6) долговечность при эксплуатации и вибровоздействии а также невысокая стоимость.
Основной технологический фактор формовки при ЛГМ – газовое разрежение Р в порах песчаного наполнителя которое не только влияет на прочность формы но и на качество отливок появление дефектов. Вопросы оптимизации вакуумирования для получения отливок из цветных и черных сплавов рассмотрены в статьях [3 и 5]. Необходимость жесткой конструкции обусловлена тем что на вакуумируемый контейнер при эксплуатации действуют силы внешнего атмосферного давления а также вибро-транспортные воздействия и возможен контакт с расплавом металла. При заливке усилия действующие на ЛК состоят из: 1) газового давления 3070 кПа на наружную поверхность от разницы атмосферного давления и вакуума; 2) сил термического расширения формовочного песка и его веса; 3) веса заливаемого металла.
На поверхность контейнера размерами 06х06 м и высотой 05 м сжимающая сила при вакуумировании составляет 4711 т а в сумме элементы конструкции ЛК воспринимают значительные силы – сжатия растяжения изгиба и комбинированные. В условиях компании проводится анализ эксплуатации ЛК и постоянно модернизируется их конструкция. При формовке для заполнения полостей в моделимодельных кустов песком ЛК с песком вибрируют увеличивая текучесть и создавая эффект псевдожидкости. Большинство имеющихся виброустановок имеют однонаправленное вибрирующее усилие которое может не обеспечивать полноту заполнения полостей модели. При разработке нового вибростола были учтены потребности формовки сложных пустотелых ППС моделей и он имеет 3-х осевое направление колебательных сил что вызывает необходимость полного соприкосновения дна ЛК с плоскостью стола. Этим вызвано изготовление из толстой листовой стали основания контейнера.
Боковые стенки ЛК изготавливают из листов толщиной 2540 мм и усиливают уголками. Донный разгрузочный узел с вакуумным уплотнением облегчает разгрузку ЛК (рис. 3) и дает возможность встроить операцию выбивки в единый транспортный поток или конвейер а также упрощает конструкцию вытяжных вентиляционных систем. Нижняя внутренняя часть такого ЛК имеет вид усеченной пирамиды. При вибрации из-за разложения вынуждающих сил в 3-х осевом направлении частицы песка могут перемещаться винтообразно и полностью заполняют пустоты и каналы по конфигурации модели. Уклон стенки донной части дает песку легко высыпаться однако придание нижней части профиля ломаной линии с горизонтальной и пирамидальной частью позволяет сохранять часть песка для постели под модель и уменьшает объем песка участвующего в пескообороте.
Описанные конструкции ЛК для ЛГМ служат в литейных цехах где освоена эта перспективная технология. Модернизация литейных цехов с традиционной формовкой со связующим неизбежно востребует их при переходе на качественно новую ступень технологического использования науки и экологической культуры чем является ЛГМ в вакуумируемые формы из песка без связующего а приведенная информация будет полезна технологам и конструкторам желающим воспользоваться отечественными техническими достижениями.
Список использованных источников :
Дорошенко В. С. Чичкань И. П. Регулирование газового режима формы из ЖСС при получении крупных отливок по ЛГМ-процессу Металл и литье Украины. – 2008.- № 11-12. – С. 35 – 38.
Дорошенко В. С. Бердыев К. Х. Шинский И. О. Обобщение опыта изготовления пенополистироловых литейных моделей Металл и литье Украины. – 2010.- № . – С. .
Дорошенко В. С. Бердыев К. Х. Болюх В. А. Вакуумные системы формовочно-заливочных участков цехов ЛГМ Металл и литье Украины. – 2010.- № . – С. .
Дорошенко В. С. Шейко Н. И. Критерии выбора конструкций опок для вакуумно-пленочной формовки Литейное производство. –1988. - №7. – С. 25-26.
Иванов В. В. и др. Влияние геометрии внутренних стенок опоки на разряжение в ВПФ Литейное производство.- 2006.- № 8.- С. 12-13.
Шинський .О. к.т.н. Дорошенко В.С. к.т.н. Шинський О.Й. д.т.н. Бердиєв К.Х. дипл. інженер
Сучасні тенденції конструювання опочної оснастки для ЛГМ.
Опочна оснастка для ЛГМ має ряд конструктивних особливостей які описані в статті. Цю оснастку використовують у діючих ливарних цехах. Модернізація ливарного виробництва при переході на якісно новий щабель технологічного використання науки і екологічної культури чим є ЛГМ в вакуумовані форми з піску без сполучного затребує ці вітчизняні технічні розробки.
Ключові слова: опока ливарний контейнер ЛГМ конструювання вакуум.
I.O. Shinsky V.S. Doroshenko O.I. Shinsky K.H. Berdyev
Current trends of designing the molding boxes for Lost Foam process.
Molding boxes for Lost Foam Process has a number of design features that are described in the article. This snap is used in the existing foundries. Modernization of foundry during the transition to a qualitatively new level of technological application of science and environmental culture what is the Lost Foam Process in the evacuated molds of sand without binder will claim these domestic technological developments.
Keywords: casting-box casting container Lost Foam construction vacuum.
Виброопока 2000х2000х1800 12.cdw

План цеха А1.cdw

Бронеплита приклиновая ЦМ - 166..m3d

Генеральный план.cdw

тротуаров и замещений
Козловой кран Q - 15 тн.
Условные обозначения
- автомобильные дороги
- линии электропередач
- трансформатор силовой
- проектируемое здание
- существующее здание
Административно-бытовой комплекс
Склад временного хранения
Компресорная станция
Экспликация зданий и сооружений
Коэффициент озеленения
Коэффициент застройки
Протяженность автомобильных дорог
Коэффициент используемой территории
Технико-экономические показатели
Рекомендуемые чертежи
- 25.01.2023
- 24.01.2023