Проект предприятия по производству пластиковых аксессуаров для систем вентиляции и кондиционирования методом литья под давлением. Производительностью 100 т/год


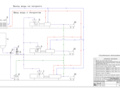
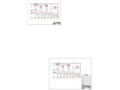
- Добавлен: 25.01.2023
- Размер: 7 MB
- Закачек: 1
Описание
Состав проекта
![]() |
![]() |
![]() |
![]() ![]() ![]() |
![]() ![]() ![]() |
![]() ![]() |
![]() ![]() ![]() |
![]() ![]() ![]() ![]() |
![]() ![]() ![]() ![]() |
![]() ![]() ![]() |
![]() ![]() ![]() |
Дополнительная информация
01 РЕШЕТКа вентиляционная.dwg
Внутренний блок канального типа FDX100 DAIKIN
План кондиционирования воздуха на базе DAIKIN.
Архитектурная мастерская
СХЕМА-ПЛАН 3-ГО ЭТАЖА
Наружный блок RMX140J - 2DAIKIN
Наружный блок R100 DAIKIN
Кабинет 2. Коридор 3. Лифт 4. Лестница 5. Переговорная
Санузел 7. Кухня 8. Венткамера 9. Пост охраны 10. Электрощитовая
Копир 12. Комната уборщиц
Точное месторасположение кондиционера уточняется при монтаже.
Монтаж систем кондиционирования вести в соответствии со СНиП 3.05.01-85.
Монтаж систем кондиционирования вести согласно рекомендациям производителей оборудования
с учетом коммуникаций ВК
электроснабжения и освещения.
После проведения монтажных работ проверить систему отвода дренажа на герметичность.
Уровни прокладки трубопроводов уточняются по месту с учетом существующих коммуникаций.
Отметка установки кондиционера не должна быть ниже отметки точки подключения
указанной на чертеже или предусмотреть установку у кондиционера дренажного насоса.
Коммуникации опускаются на 1 этаж
С О Г Л А С О В А Н О
Решетка вентиляционная пластиковая серия ASGC 1122
Основной вид решетки ASGC 1122
Жалюзи вертикальная (проекция)
Жалюзи горизонтальная
Жалюзи горизонтальная (проекция)
Тяга вертикальная (проекция)
Тяга горизонтальная (проекция)
ЭТО мой ДИПЛОМ вариант № 5.doc
Расчетно-пояснительная записка состоит из следующих частей:
Введение посвященное целям и задачам стоящим перед промышленностью по переработке пластмасс а также целесообразности и перспективам развития малых предприятий как одного из основных направлений развития экономики России.
Технологической части посвященной обоснованию выбора и метода производства разработки технологической схемы производства требованиям предъявляемым качеству выпускаемой продукции входному контролю и подготовке исходного сырья. А также технологическому оборудованию и расчету потребности в нем организации труда включающей в себя информацию об трудовом процессе и условиях труда основным строительным и компоновочным решениям производственных помещений и размещении оборудования в нём расчетам в потребности в электроэнергии освещении отоплении вентиляции водопровода и канализации.
Части по охране среды и безопасности жизнедеятельности посвященной рассмотрению потенциальных опасностей и вредных факторов в процессе производства пожарной безопасности и охране окружающей среды.
Экономической части включающей в себя расчет основных технико-экономических показателей проектируемого предприятия.
Заключение по проекту.
Расчетно-пояснительная записка включает 114 страниц печатного текста 43 таблицы 6 рисунков 25 приложений и 5 графических листов формата А1.
Проект предприятия по производству пластиковых аксессуаров для систем вентиляции и кондиционирования методом литья под давлением. Производительностью 100 тгод.
ТЕХНОЛОГИЧЕСКАЯ ЧАСТЬ11
Задание на проектирование11
1 Основание для проектирования11
2 Район и место расположения проектируемого производства11
3 Номенклатура продукции и мощность производства.12
4 Режим работы предприятия.15
Обоснование выбора и метода16
1 Характеристика способов изготовления изделий.16
1.1 Литье под давлением16
1.3 Пневмо - и вакуумформование18
2 Выбор метода переработки18
3 Технологические особенности литья под давлением19
Разработка технологической схемы28
1 Характеристика сырья28
1.1 Получение сырья и его свойства28
1.2 Обоснование выбора сырья29
1.3 Выбор и обоснование рецепта производства38
1.4 Требования к исходному сырью38
1.5 Входной контроль сырья39
1.6 Методы испытаний сырья на входном контроле40
2 Составление и описание технологической схемы производства45
2.1 Получение сырья48
2.2 Материальный баланс48
2.3 Хранение сырья49
2.4 Растаривание сырья51
2.5 Подготовка сырья51
2.6 Формование изделия литье53
2.7 Контроль качества и упаковка готовой продукции54
2.8 Технические условия ТУ 4863-002-44911369-10 (введены впервые)54
2.9 Хранение готовой продукции и маркировка64
3.1 Переработка отходов64
Выбор технологического оборудования и расчет потребности в нем66
1 Выбор основного технологического оборудования66
1.1 Расчёт потребности в основном технологическом оборудовании67
2. Выбор вспомогательного технологического оборудования71
2.1 Водоохладители ( чиллеры )71
2.2 Вакуумный загрузчик сырья73
1 Трудовой процесс75
2 Разделение труда76
3 Кооперация труда76
4 Организация рабочих мест основного производства77
5 Организация рабочих мест вспомогательных рабочих78
6 Содержание работы литейщика78
7 Организация и обслуживание рабочего места79
9 Численность основных и вспомогательных рабочих80
Основные строительные и компоновочные решения83
1 Планировка помещений83
2 Компоновка технологического оборудования83
3 Основные строительные решения84
Электротехническая часть85
1 Расчёт установленной и потребляемой мощности85
2 Освещение производственных помещений85
3 Заземление и защита от статического электричества88
5 Отопление и вентиляция89
5.1 Расчёт кратности воздухообмена90
5.2 Расчёт расхода теплоты на отопление вентиляцию тепла выделяемого оборудованием91
6 Водопровод и канализация94
7 Расход сжатого воздуха95
БЕЗОПАСНОСТЬ ЖИЗНЕДЕЯТЕЛЬНОСТИ97
Охрана окружающей среды техника безопасности промсанитария и пожарная безопасность.97
1 Охрана окружающей среды97
2 Техника безопасности97
3 Промсанитария и пожарная безопасность98
ЭКОНОМИЧЕСКАЯ ЧАСТЬ99
Расчет технико-экономических показателей проектируемого предприятия99
1 Организация поставок сырья программа производства и режим работы предприятия99
2 Аренда производственных площадей101
3 Стоимость оборудования101
4 Вопросы труда и заработной платы103
4.1 Расчёт фонда заработной платы рабочих103
4.2 Расчёт фонда заработной платы ИТР и МОП104
5 Расчёт заготовительных цен на сырьё материалы и энергию а также себестоимости продукции105
6 Расчёт амортизационных отчислений105
7 Смета расходов предприятия и на содержание и эксплуатацию оборудования106
8 Проектная калькуляция себестоимости продукции107
9 Расчет удельных капитальных вложений и производительности труда110
10 Основные технико-экономические показатели предприятия111
СПИСОК ИСПОЛЬЗОВАННЫХ ИСТОЧНИКОВ114
В настоящее время уровень мировой экономики и экономики отдельных стран всё в большей мере зависит от уровня развития производства и применения полимерных материалов. Потребность самых различных отраслей промышленного производства в пластических массах полуфабрикатов и изделиях из них непрерывно возрастает.
Производство пластмасс и синтетических смол в последние годы остается одним из наиболее динамично развивающихся секторов российского химического комплекса.
В период экономических преобразований падение спроса на полимерные материалы на внутреннем рынке России привело к снижению их производства.
В период с 1990-1996 производство полимерных материалов постоянно снижалось. Объем выпуска сократился в 23 раза достигнув своего критического состояния. С 1996 года начался стабильный рост выпуска пластмасс. В 1998-1999 гг. на российском рынке действовало 148 предприятий. Их общая мощность на 01.01.00 г. достигла 38 млн.т.
Спрос на полимерные материалы определяется с одной стороны наличием перерабатывающей базы ее сбалансированностью с производством полимеров техническим состоянием инвестиционной активностью финансовыми возможностями на приобретение оборотных средств а с другой - платежеспособностью и экономическим состоянием отраслей-потребителей изделий из полимеров развитие которых оказывает косвенное влияние на формирование предложения со стороны продуцентов полимера.
В настоящее время на производстве назрела проблема технического переоснащения в связи с тем что устаревшее оборудование не справляется с задачами производства принято решение об установке нового оборудования на имеющихся площадях и полной автоматизации и механизации процесса изготовления деталей.
Одним из перспективных направлений производства является предприятия по переработке полимерных материалов.
Перспективность развития производств по переработке полимерных материалов заключается в высокой степени автоматизации и механизации безотходность и высокая экологичность производств расширение областей применения и номенклатуры изделий из полимерных материалов.
В этих условиях от отдельных предприятий требуется концентрация усилий на производстве наиболее выгодной продукции а также смене оборудования на современное.
В условиях рыночной экономики и современных коммерческих отношений иногда наиболее целесообразным представляется строительство малых предприятий.
Преимущества малого предприятия состоят в следующем:
- малое предприятие динамичнее крупного оно легче приспосабливается к изменяющимся условиям оперативное отражает изменение потребительского спроса;
- развитие малого предприятия существенно облегчает территориальный и отраслевой перелив рабочей силы и капитала;
- малое предприятие быстрее «впитывает» новые достижения научно-технического прогресса так как они более приспособлены для производства уникальных изделий быстрее и дешевле перевооружаются технически требуют меньших капиталовложений и обеспечивают их быструю окупаемость;
- зачастую само создание малого предприятия реализует попытку коммерческого использования какого-либо новшества;
- малое предприятие улучшает общую структуру производства так как облегчает адаптацию «неповоротливого» крупного производства к изменяющимся условиям к новым требованиям научно-технического прогресса способствует развитию специализации освобождает крупные корпорации от производства мелкосерийной продукции занимается поиском доработкой и освоением новых изделий охотнее идёт на риск.
Развитие малого предпринимательства рассматривается правительствами многих стран как важный фактор обеспечения занятости населения. Политика помощи и поддержки малых предприятий проводится и в России.
Разумеется всё сказанное в пользу малых предприятий ни в коей мере не умаляет значения крупных предприятий располагающих большой научно-технической базой штатами учёных колоссальными финансовыми средствами и мощными производственными возможностями. Будущее химической промышленности не в противопоставлении малых предприятий химическим гигантам а в разумном их сочетании.
Опираясь на вышеизложенное можно сделать вывод что проектируемый нами объект целесообразнее разместить по соседству с другими производственными организациями в виде малого предприятия.
Это сделает производство предприятия более рентабельным и жизнеспособным. Производство изделий из пластмасс не может существовать без некоторых смежных производств. Например инструментального цеха. Находящиеся в эксплуатации машины требуют постоянной и своевременной замены отдельных деталей узлов. Работа предприятия также не возможна без систем отопления канализации энергоснабжения и т. п. Все эти проблемы будут решены если разместить планируемое производство на территории предприятия где все вышеперечисленные условия необходимые для работы предприятия уже имеются.
Таким образом создание малых предприятий по переработке пластических масс – одно из основных направлений развития экономики России.
ТЕХНОЛОГИЧЕСКАЯ ЧАСТЬ
Задание на проектирование
1 Основание для проектирования
Основанием для проектирования является задание на выпускную квалификационную работу утвержденное деканом факультета к.т.н проф Харитоновым Г.И.
2 Район и место расположения проектируемого производства
Краткая характеристика г. Рыбинска :
Расстояние от г. Ярославля – 85 км;
Расстояние от г. Москвы – 330 км;
Расстояние от г. Череповца – 200 км.
Районный центр население 250 тысяч человек. Хорошо развита индустрия (моторостроение приборостроение судостроение).
Есть железнодорожная станция Северной жд;
Автомобильные подъездные пути Федерального значения "Р-151" и "Р-104";
Речной порт (р. Волга).
Существует рынок квалифицированного труда.
3 Номенклатура продукции и мощность производства.
Номенклатура выпускаемой продукции определена исходя из данных маркетингового исследования.
В России строительный бум !
В России ремонтный бум !
В России бум борьбы за организацию жизненного пространства !
Как грибы после дождя появляются новые современные жилые здания в массовом порядке реконструируются гостиницы офисные комплексы производственные помещения. В настоящее время в России можно говорить о настоящем строительном буме и как следствие о высокой востребованности строительно-отделочных материалов.
Одной из высокодоходных товарных групп материалов необходимых при ремонте и отделке как жилых так и офисных помещений являются вентиляционные системы.
Рынок вентиляционных систем вполне можно назвать «новым» поскольку после долгого застоя он успешно возрождается. При этом его объем постоянно увеличивается в связи с «бумом» строительства в России. К тому же контроль за соблюдением санитарных норм по вентиляции помещений становится все жестче в государственных и тем более частных предприятий.
О необходимости вентиляции написано уже множество трактатов. Я не буду повторяться и лишь отмечу что «системы вентиляции являются основным фактором комфортности и необходимым условием увеличения межремонтного периода для жилых и офисных помещений».
По соотношению ценакачество все вентиляционное оборудование представленное на российском рынке можно условно объединить в две группы:
В первую группу входит английское французское немецкое шведское норвежское финское итальянское израильское польское чешское вентиляционное оборудование и часть вентиляционных систем от российских производителей. Этот спектр оборудования на рынке характеризуется хорошим качеством и умеренным ценовым диапазоном.
Вторая группа – это вентиляционная техника из азиатского региона стран СНГ и от некоторых российских производителей. Как правило с уменьшением цены уменьшается и качество продукции хотя здесь большую роль играет стоимость доставки известность и репутация фирмы длительность ее работы на российском рынке.
Основной концепцией предприятия будет являться использование преимуществ технологии изготовления из пластика изделий которые раньше изготавливались из алюминия.
В данном проекте я попытаюсь предложить рынку продукцию пользующуюся огромной популярностью у конечных потребителей благодаря выгодному соотношению ценакачество товаров особым потребительским эксплуатационным и экологическим характеристикам а также технической продуманности изделий.
Конечными покупателями продукции предположительно будут являться:
- Профессионалы. Снабженцы специализированных проектно-монтажных организаций и строительно-монтажных.
Ведь только благодаря такой продукции воздух в Вашем доме или офисе может быть по настоящему чистым увеличение времени между ремонтами в квартире и уникальные потребительские и эксплуатационные свойства продукции - вот некоторые из основных мотивов продвижения продукции частным покупателям и профессионалам.
Оптовые и розничные организации активно смогут продвигать продукцию благодаря ее массовой известности среди конечных потребителей высокой ликвидности и рентабельности а также благодаря отсутствию ярко выраженных сезонных колебаний спроса в течение всего календарного года.
География продаж продукции планируется по всей территории России: от Калининграда до Южно-Сахалинска и от Мурманска до Нальчика; это 55 регионов России (включая Москву и Санкт-Петербург). Также имеется намерение вести активную экспортную политику. В Казахстане Белоруссии Литве и Латвии.
Каталоги буклеты POS-материалы фирменное торговое оборудование методические материалы по результатам маркетинговых исследований совместное участие в региональных выставках - все это и многое другое будет входить в рекламную поддержку партнеров торговой марки.
Опираясь на результаты исследований я считаю что рынок вентиляционных систем на сегодняшний день ограничен лишь пониманием конечного покупателя важности организации грамотной вентиляции
Российский потребитель предъявляет повышенные требования к качеству товаров применяемых при ремонте и отделке жилых и офисных помещений.
Что же будет объединять под собой торговая марка ?
Вентиляционные решетки (область применения):
- декоративное оформление отверстий вентиляционных шахт
- установка в подвесных потолках
- дверная вентиляция
- обеспечение теплообмена при декоративной облицовке радиаторов отопления
Потолочные клапаны (анемостаты) и диффузоры (область применения): предназначены для плавной регулировки объема подачи и (или) вытяжки воздуха и его равномерного распределения.
Пластиковые вентиляционные фасонные изделия – адаптеры (переходы с прямоугольного на круглое сечение) тройники центральные делители потока демпферы (заслонки) ревизионные лючки.
Мощность предприятия по переработке термопластов составляет 100 тгод.
4 Режим работы предприятия.
Работа на проектируемом предприятии планируется в три смены по 8 часов. Количество рабочих дней в году - 250. Номинальные фонды времени работы оборудования приняты по государственным нормам технологического проектирования предприятия машиностроения приборостроения и металлообработки.
Потери времени для оборудования приняты исходя из продолжительности и периодичности планово-предупредительных работ технологических переналадок а также внутрисменных потерь связанных с технологическим обслуживанием оборудования и организационными мероприятиями [1].
Обоснование выбора и метода
1 Характеристика способов изготовления изделий.
Основными методами (способами) переработки полимерных материалов в изделия являются: литьё под давлением; ротационное формование; литьё вспененных изделий; прессование пенопластов; получение профильных изделий экструзия; формование волокна; изготовление плёнок поливом; окунание; прессование; выдувание; каландрование; пневмо – и вакуумформование.
В связи с тем что номенклатура аксессуаров для систем вентиляции и кондиционирования изготавливается из термопластичных материалов то наиболее приемлемыми способами формования изделий являются: литьё под давлением прессование пневмо - и вакуумформование.
Рассмотрим данные методы изготовления изделий.
1.1 Литье под давлением
Литьё под давлением – это основной метод переработки полимерных материалов и получения изделий заключающийся в пластикации гомогенизации полимерного материала в материальном цилиндре и впрыске его в предварительно замкнутую форму которая охлаждается для термопластов и нагревается для реактопластов.
Литьём под давлением изготавливают изделия из термопластичных и термореактивных пластмасс разнообразной конфигурации и массы различающиеся от десятых долей грамма до многих десятков килограмм по толщине стенок – от десятых долей миллиметра до нескольких десятков сантиметров. Причём изделия имеют высокую точность и стабильность размеров.
При литье термопластов расплав заполнивший форму затвердевает при охлаждении после чего форма раскрывается и изделие выталкивается. При формовании реактопластов полимерную композицию впрыскивают в форму которую затем нагревают до температуры отверждения материала. После этого форму открывают и изделие также извлекается.
Переработка пластмасс в изделия сводится к созданию конструкции обеспечивающей заданный комплекс эксплуатационных свойств путем перевода полимерного материала в состояние в котором он легко приобретает требуемую форму с его последующей фиксацией (сохранением).
Литье под давлением имеет ряд преимуществ по сравнению с прессованием и экструзией: хорошая пластикация и гомогенизация продукта; точное дозирование полимерного материала; легко автоматизируемый процесс.
Среди недостатков следует отметить: анизотропию свойств при литье; различную усадку для материалов.
Прессование – это технологический процесс сущность которого заключается в пластической деформации полимерного материала при одновременном действии на него тепла и давлении с последующей фиксации формы.
В настоящее время методом прессования перерабатываются только реактопласты.
Данным методом изготавливают: слоистые листовые пластики дозирующие таблетки из пресс-порошков.
Существует компрессионное (прямое) и трансферное (литьевое) прессование.
Компрессионное прессование – процесс при котором материал загружается непосредственно в формующую полость пресс-формы где происходит его формование.
Этот способ отличается невысокой производительностью однако им можно перерабатывать все реактопласты.
Трансферное прессование это способ при котором предварительно подогретый и пластицируемый полимерный материал впрыскивается из загрузочной камеры через литниковые каналы в полость пресс-формы.
Преимущества данного метода - изготовление деталей сложной формы с арматурой; равномерное отверждение изделия.
Недостатками метода являются: сложность автоматизации процесса.
1.3 Пневмо - и вакуумформование
Пневмо - и вакуумформование - это процесс формования изделия из листового полимерного материала переведенного нагревом в высокоэластическое состояние и придание требуемой конфигурации за счет разности давлений под и над листовой заготовкой создаваемой сжатым воздухом или вакуумом.
Это относительно дешевый способ получения крупногабаритных изделий ( ванны корпуса упаковка для пищевых продуктов).
Преимущество данного метода: малая стоимость и металлоемкость оборудования; хорошо поддается автоматизации.
Недостатками метода являются: низкая производительность из-за продолжительности цикла формования; сложность нагрева формования и обрезки листов свыше 3 мм; большое количество отходов до 40%.
2 Выбор метода переработки
При выборе метода переработки будем исходить из проведённого литературного обзора и на основе комплексного анализа следующих показателей:
- вид перерабатываемого материала;
- требования ассортиментной программы (по форме изделия; по предельным значениям толщин стенок; по соотношению габаритных размеров изделия);
- серийность производства;
- требования к качеству изделий.
В нашем случае более подходящим методом переработки полимеров является литьё под давлением так как прессованием перерабатывают как правило реактопласты.
Кроме того литьём под давлением перерабатываются все без исключения термопластичные материалы вид и марки которых выбираются в зависимости от назначения изделий прочности теплостойкости и других свойств. В настоящее время более 30% объёма термопластов перерабатывается этим методом и объемы производства изделий из термопластов методом литья под давлением имеют тенденцию к увеличению. При литье под давлением обеспечивается точность размеров изделий более высокая чистота их поверхности и меньший расход сырья чем при получении изделий другими методами (выдуванием вакуумным и пневматическим формованием).
Стоимость литьевых машин сравнительно небольшая.
Таким образом с учетом проведенных маркетинговых исследований для проектируемого предприятия наиболее удобным и выгодным методом переработки термопластов является литьё под давлением так как он более полно отвечает требованиям задания на проектирование по видам перерабатываемого материала требованиям ассортиментной программы серийности производства и качеству изделий.
3 Технологические особенности литья под давлением
Технологический процесс литья изделий из термопластичных полимеров состоит из следующих операций: плавление гомогенизация и дозирование полимера; смыкание формы; подвод узла впрыска к форме; впрыск расплава; выдержка под давлением и отвод узла впрыска; охлаждение изделия; раскрытие формы и извлечение изделия.
Операции впрыска расплава и выдержки его под давлением сопровождаются тем что цилиндр литьевой машины уже подведён к литьевой форме и сопло соединено с литниковым каналом формы. Шнек под действием поршня узла впрыска перемещается к форме и расплав впрыскивается в формующую полость. Для исключения вытекания расплава из формы даётся выдержка под давлением. Во время охлаждения изделия когда расплав в литнике достаточно охлаждён узел впрыска отводится от формы и начинается дозирование новой порции расплава шнек останавливается. После окончания охлаждения формы происходит её раскрытие и изделие удаляется. Такова общая последовательность технологических операций.
Большинство термопластов не нуждается в предварительной обработке перед загрузкой в литьевую машину если не считать окрашивания в нужный цвет. Полиамиды и поликарбонат способные при хранении увлажняться подвергаются сушке. Повышенная увлажненность материалов приводит к образованию пузырей утяжин серебристости на поверхности изделий. Подсушивание проводят непосредственно перед переработкой.
Литники бракованные изделия и другие отходы переработки термопластов подлежат предварительной разборке очистке и дроблению. После этого они могут быть использованы в качестве добавок к свежему материалу.
Нагревательный цилиндр является основным технологическим узлом машины определяющим её производительность и качество изделий. К нагревательному цилиндру предъявляют следующие требования:
высокий коэффициент теплопередачи от источников нагрева к материалу при небольших разностях температур стенок цилиндра и материала;
равномерный нагрев материала и отсутствие местных перегревов.
Для измерения температуры расплава в различных зонах обогреваемого цилиндра используют термопары.
Режим охлаждения изделия в форме влияет как на производительность машины так и на качество изделий. Интенсивное охлаждение увеличивает производительность машины но может привести к снижению качества изделий из-за появления внутренних напряжений. Чем выше температура затвердевания термопласта тем выше должна быть температура формы.
Температура формы перед заполнением обычно ниже температуры литья на 100-150° С.
Продолжительность цикла складывается из времени смыкания формы впрыска выдержки под давлением и раскрытия формы. Время впрыска зависит от массы отливки формы изделия сечения впускных клапанов текучести термопласта температуры и давления расплава в материальном цилиндре и интенсивности охлаждения изделия в форме. Для различных термопластов при равных условиях длительность впрыска личная и колеблется в пределах от 2-3 с (для полистирола) до 40-60 с (для поламида-54) на 1 мм толщины изделия.
Чем больше масса отливки тоньше стенки изделия и сложнее его форма и чем меньше сечение впускных каналов формы тем больше время впрыска. Чем выше текучесть термопласта давление и температура расплава в материальном цилиндре машины тем меньше продолжительность.
Одним из основных технологических показателей процесса является давление литья. Под давлением материал проходит материальный цилиндр литниковые каналы и заполняет полость форм. Давление под которым находиться расплав в полостях формы всегда меньше давления создаваемого червяком или поршнем [2].
Органической особенностью метода является его цикличность что в общем
сдерживает производительность этого процесса по сравнению с непрерывными технологиями. Принципиально суть технологии литья под давлением состоит в следующем (рис. 2). Расплав полимера подготовлен и накоплен (l = пот) в материальном цилиндре литьевой машины (в данном случае — червячного типа) к дальнейшей подаче в сомкнутую форму (позиция а). Далее материальный цилиндр смыкается с узлом формы а пластикатор (в данном случае — не вращающийся червяк) осевым движением со скоростью Voc перемещает расплав в форму (позиция б). В результате осевого движения червяка форма заполняется расплавом полимерного материала а пластикатор смещается в крайнее левое (на рисунке) положение (позиция в l = 0). Далее расплав в форме застывает (или отверждается — в случае реактопластов) с образованием твердого изделия (позиция г). Материальный цилиндр продолжает оставаться в сомкнутом с системой формы положении. В этой ситуации червяк начинает вращаться с Vч = пот подготавливает и транспортирует расплав в переднюю зону материального цилиндра и при этом отодвигается назад. После накопления требуемого объема расплава (расстояние l = пот) вращение червяка прекращается (Vч = 0). Он занимает исходное к дальнейшим действиям положение. После завершения процесса затвердевания (отверждения) пластмассы форма размыкается и изделие удаляется из нее (позиция д). Для облегчения съема изделия материальный цилиндр может к этому моменту отодвинуться от узла формы. Далее цикл литья под давлением повторяется.
Из изложенного следует ряд принципиальных положений которые определяют не только технологию процесса но и устройство оборудования и оснастки. К ним относятся следующие:
Конструкция литьевой машины обязательно включает: блок подготовки расплава и его подачи в форму (инжекционный узел); блок запирания (и размыкания) формы в виде прессового устройства с ползуном (узел смыкания); блок привода обеспечивающего все виды движения подвижных устройств оборудования и оснастки; устройство управления литьевой машиной реализующее требуемую последовательность взаимодействия блоков силовых и кинематических узлов а также температурные скоростные нагрузочные параметры обеспечивающие оптимальный режим работы оборудования.
Литьевые машины являются сложными и недешевыми устройствами насыщенными современными техническими решениями.
Применение литьевых машин для реализации технологии литья под давлением требует квалифицированного технико-экономического обоснования главные элементы которого: крупнотиражность и геометрическая сложность изделия доступность и достаточность по технологическим физико-механическим и эксплуатационным свойствам полимерного материала выбранного для производства.
Рис. 2. Принципиальная схема процесса литья под давлением
Современные литьевые машины (ЛМ) представляют собой сложные технические устройства оснащенные разнообразными средствами автоматизированного управления параметрами технологического процесса. Нередко их называют термопластавтоматами (ТПА) или реактопластавтоматами (РПА) в зависимости от вида основного перерабатываемого материала.
Конструкции литьевых машин весьма разнообразны. Основными классификационными признаками ЛМ являются усилие запирания формы (кН) то есть смыкания формы создаваемое прессовым блоком и объем впрыска или мощность выражаемая числом кубических сантиметров расплава которые могут быть подготовлены машиной для однократной подачи в литьевую форму. Выпускаемые промышленностью серийные литьевые машины как правило объединены в типоразмерные ряды по двум указанным выше параметрам.
Кроме того ЛМ подразделяются по технологическим и основным конструктивным признакам:
- по способу пластикации – на одно- двухчервячные поршневые и червячно-поршневые;
- по особенностям пластикации – на Л М с совмещенной и раздельной пластикацией (предпластикацией);
- по количеству пластикаторов – с одним двумя и более пластикационными узлами;
- по числу узлов запирания формы (узлов смыкания) – одно- двух- и многопозиционные (ротационные карусельные);
- по конструкции привода – электро- и гидромеханические электрические;
- по расположению оси цилиндра узла пластикации и плоскости разъема литьевой формы - горизонтальные вертикальные угловые (рис. 3.).
Рис. 3. Типы литьевых машин
Б - угловые с вертикальной прессовой частью;
Г - угловые с горизонтальной прессовой частью
Угловые ЛМ используются для литья крупных изделий с затрудненным извлечением из формы. Возможны два типа таких машин:
— с горизонтальным пластикатором и вертикальным разъемом формы;
— с горизонтальным разъемом формы и вертикальным узлом инжекции. Вертикальные ЛМ наиболее удобны при производстве некрупных в том числе армированных деталей (обычно до 05 кг) в съемных формах.
Наибольшее распространение получили горизонтальные одночервячные с совмещенной пластикацией ТПА. Они обеспечивают объемы впрыска от 4 см3 до 70 000 см3 при усилии запирания формы от 25 до 60 000 кН. Принципиальная схема такого ТПА представлена на (рис. 4.).
Все функциональные блоки и устройства ТПА располагаются на жесткой раме (рис. 4 поз. 22). Гранулированный полимерный материал из бункера 1 поступает в материальный цилиндр 2 захватывается вращающимся шнеком 3 и транспортируется в направлении мундштука 8. При этом гранулированный материал нагревается уплотняется в пробку и под действием тепла от трения о поверхность винтового канала червяка и поверхность цилиндра а также за счет тепла от наружных зонных электронагревателей 4 пластицируется то есть расплавляется под давлением и пройдя через обратный клапан 6 накапливается в зоне дозирования материального цилиндра. Под действием возникающего при этом давления червяк отодвигается вправо смещая плунжер 25 и хвостовик с имеющимся на нем (условно) концевым выключателем 26. Установкой ответного выключателя на линейке 27 регулируют отход червяка и следовательно подготовленный к дальнейшим действиям объем расплава в зоне дозирования и мундштука 8. После срабатывания концевых выключателей 26 и 27 вращение червяка прекращается — требуемая доза расплава подготовлена. Далее гидроприводом 5 пластикационный называемый также и инжекционным узел сдвигается влево до смыкания мундштука с литниковой втулкой установленной в стойке 9- К этому моменту завершает смыкание частей прессформы 11 я 12 прессовый узел Л М. Он представляет собой по сути горизонтальный рычажно-гидравлический пресс состоящий из задней 17 и передней 9 плит-стоек соединенных как правило четырьмя колоннами 10 и 14 по которым смещается вправо (смыкание) и влево (размыкание) ползун 13. Ползун приводится в движение от рычажно-гидравлического механизма 15 16.
Рис. 4. Схема термопластавтомата с червячной пластикацией
После приведения всех блоков в исходное состояние создается давление в гидроприводе 25 осевого движения червяка который действуя аналогично поршню инжектирует расплав полимера из материального цилиндра в пресс-форму где и образуется изделие. Наконечник 7 установленный на червяке способствует уменьшению образования застойных зон после впрыска. В период формообразования изделия червяк приводится во вращение для подготовки следующего объема впрыска. После охлаждения расплава до заданной температуры форма раскрывается и изделие с помощью выталкивателей или применением робототехнических устройств удаляется из рабочей зоны литьевой машины.
Все подвижные узлы ЛМ обеспечиваются энергоносителем от главного привода состоящего из электродвигателя 18 насосного блока 19 установленного в маслосборнике и системы трубопроводов высокого 20 и низкого 21 давления. Для вращения червяка в данной схеме служит гидродвигатель 24 с зубчатой передачей 23.
К достоинствам машин описанного типа относят высокую производительность универсальность по видам перерабатываемых материалов удобство управления и обслуживания а также надежность в эксплуатации. Определенный недостаток таких ЛМ впрочем как и всех термопластавтоматов с совмещенной пластикацией состоит в существенных потерях при осевом движении червяка от трения материала о стенки цилиндра что затрудняет достижение высоких скоростей впрыска.
Одночервячные ТПА с усилием запирания от 2500 кН до 4000 кН являются наиболее востребованными машинами. [9].
Разработка технологической схемы
1 Характеристика сырья
1.1 Получение сырья и его свойства
Предполагается что предприятие будет использовать для производства продукции АБС-пластик марки HG-0760AT («Samsung Chemicals» - Южная Корея). Основные физико-химические эксплуатационные и технологические свойства перерабатываемого в проектируемом предприятии полимера указаны в Приложениях 1-3.
Получение: В промышленности АБС-пластик получают методом сополимеризации которая представляет собой процесс образования высокомолекулярных соединений при совместной полимеризации двух или более различных мономеров. Методы получения АБС-пластика основаны на радикальной сополимеризации стирола с акрилонитрилом в присутствии латекса каучука. При соотношении стиролакрилонитрил равном по массе 76:24 получают сополимер такого же состава. При других соотношениях мономеров требуется тщательный контроль однородности образующегося сополимера. Кроме того с увеличением количества акрилонитрила резко повышается вязкость системы. Наибольшее распространение получила двухстадийная эмульсионная сополимеризация по непрерывной или периодической схеме. На первой стадии синтезируют латекс: стирол и акрилонитрил добавляют в полибутадиеновую эмульсию перемешивают и нагревают до 50 °С. На второй стадии прививают к каучуку эмульгированные в латексе мономеры: добавляют растворимый в воде инициатор например персульфат калия и смесь полимеризуется. Полученную в результате суспензию дегазируют фильтруют полимер высушивают и упаковывают. Образующийся порошкообразный АБС-пластик иногда гранулируют.
АБС-пластик с повышенной ударной вязкостью получают обычно в комбинированном процессе который сначала ведут в эмульсии или растворе а затем – в водной суспензии что позволяет вводить дополнительное количество каучука.
Используется также синтез АБС-пластика в массе который включает следующие основные стадии: подготовка сырья и реагентов полимеризация в каскаде реакторов (процесс обрывают при содержании в системе 70-80% АБС-сополимера) удаление не прореагировавших мономеров и растворителя первичное гранулирование и компаундирование упаковка и складирование готовых продуктов.
1.2 Обоснование выбора сырья
Вышеперечисленное сырьё было выбрано исходя из следующего:
- сравнительно низкой стоимости материалов;
- простоты и технологичности его переработки;
- отсутствия при переработке материалов выделения токсичных веществ выше предельно допустимых концентраций;
- универсальности при изготовлении изделий;
- оптимальных физико-химических прочностных и эксплуатационных свойств;
- маркетингового исследования рынка.
Данный АБС-пластик характеризуется высочайшим уровнем экологической безопасности и сертифицирован в России вплоть до контактного применения с пищевыми продуктами. Далее на этапе производства в этот материал путем глубокого компаундирования будут вводяться специальные присадки дающие изделиям уникальные конкурентные преимущества:
- Цвето и светоустойчивость. (Продукция останется неизменно белого цвета на протяжении всего срока службы)
- Температура эксплуатации изделий от -40° до +50° С
- Гарантийный срок службы 2 года
АБС-пластик HG-0760AT предназначен для производства корпусов кондиционеров вентиляторов стиральных машин электропылесосов и т.д. Изделия из него обладают повышенным блеском и улучшенными антистатическими свойствами.
Описание и марки полимеров - АБС-пластик
АБС-пластик (акрилонитрилбутадиеновый пластик) – термопластичный аморфный тройной сополимер акрилонитрила бутадиена и стирола название которого образовано из начальных букв наименований мономеров. Продукт привитой сополимеризации стирола с акрилонитрилом и бутадиеновым каучуком получаемый эмульсионной сополимеризацией стирола с акрилонитрилом в присутствии латекса каучука. Сочетание акрилонитрильных и бутадиеновых звеньев с фрагментами стирола обеспечивает АБС-пластику эластичность и необходимую ударопрочность что делает его одним из самых востребованных пластиков для производства сложных формованных изделий с высокой степенью вытяжки.
АБС-пластик выпускается стабилизированным в виде белых гранул или порошка. Обычное обозначение акрилонитрил-бутадиен-стирольного пластика на российском рынке – АБС-пластик но могут встречаться и другие названия синонимы: ABS (Poly)Acrylonitrile Butadiene Styrene сополимер акрилонитрила бутадиена и стирола АБС-сополимер ABS. В условном обозначении марок АБС-пластика первые две цифры означают величину ударной вязкости по Изоду следующие две – показатель текучести расплава буква в конце марки указывает на метод переработки или на особые свойства.
Пример условного обозначения АБС-пластика с ударной вязкостью 8 кДжм2 показателем текучести расплава – 9 г10 мин с повышенной теплостойкостью: АБС-0809Т. На основе АБС-пластика производятся различные композиции относящиеся к специальным полимерам.
Строение: АБС-пластик является продуктом привитой сополимеризации трех мономеров – акрилонитрила (бесцветная жидкость с резким запахом) бутадиена (бесцветный газ с характерным неприятным запахом) и стирола (бесцветная жидкость с резким запахом) и представляет собой двухфазную систему. Статистический сополимер стирола и акрилонитрила с молекулярной массой 120-180 тысяч образует непрерывную фазу – жесткую матрицу в которой распределены частицы бутадиенстиролъного каучука размером 05-2 мкм образующие дисперсную фазу. Частицы каучука содержат окклюдированные микрочастицы матричного сополимера и привитые к каучуку макромолекулы этого сополимера обеспечивающие межфазное взаимодействие. Доля дисперсной фазы составляет от 15 до 30 % от общей массы пластика.
Химическая формула: (C8H8 · C4H6 · C3H3N)x
Свойства: АБС-пластик – ударопрочный материал относящийся к инженерным пластикам. Обладает более высокой стойкостью к ударным нагрузкам по сравнению с полистиролом общего назначения ударопрочным полистиролом и другими сополимерами стирола. Превосходит их по механической прочности и жесткости. Износостоек. Выдерживает кратковременный нагрев до 90-100 °С. Максимальная температура длительной эксплуатации: 75 – 80 °С. АБС-пластик пригоден для нанесения гальванического покрытия для вакуумной металлизации а также для пайки контактов. Хорошо сваривается. Рекомендуется для точного литья. Имеет высокую размерную стабильность. Дает блестящую поверхность. Имеются специальные марки с повышенным и пониженным блеском. Стоек к щелочам смазочным маслам растворам неорганических солей и кислот углеводородам жирам бензину. Растворяется в ацетоне эфире бензоле этилхлориде этиленхлориде анилине анизоле. Не стоек к ультрафиолетовому излучению. Характеризуется ограниченной устойчивостью против атмосферных воздействий и пониженными электроизоляционными свойствами по сравнению с полистиролом общего назначения и ударопрочным полистиролом.
Применениe: АБС-пластик обладает оптимальным сочетанием эластичности и ударопрочности что в сочетании с отличной размерной стабильностью делает его одним из самых востребованных пластиков для производства сложных формованных изделий с высокой степенью вытяжки и точности изготовления. Области применения АБС-пластика обусловлены комплексом уникальных свойств которые позволяют использовать его в тех деталях где ранее нельзя было обойтись без применения цветных металлов реактопластов и резин керамики бетона или дерева.
АБС-пластик перерабатывается всеми известными способами но наибольшее применение находит переработка АБС-пластика литьем под давлением и экструзией (вследствие повышенной вязкости расплава необходимо применять более высокие температуры и напряжения чем при переработке ударопрочного полистирола перед переработкой АБС-пластик рекомендуется сушить). Хладотекучесть пластика позволяет также формовать его при высоких давлениях ниже температуры стеклования. В производстве изделий из АБС-пластика применяют тиснение печатание и гальванизацию поверхности. Его используют также как наполнитель повышающий ударопрочность и улучшающий перерабатываемость композиций на основе поливинилхлорида поликарбонатов полистирола.
В России широкое распространение получили следующие типы специализации переработки АБС-пластика: применение непосредственно АБС-грануляра и композиций на основе АБС-пластика и изготовление листов толщиной от 1 до 7 мм для изготовления изделий технического назначения. Кроме того применяется вспенивание АБС-пластика (при этом плотность снижается обычно на 25-40%) или наполнение его высокодисперсными веществами. Обобщенное применение АБС-пластика дает следующую картину. Из АБС-пластика изготавливаются: детали интерьера и экстерьера автомобиля включая крупногабаритные корпусные детали; панели приборов и другие детали салона;
решетки радиатора автомобиля; колпаки автомобильных колес; корпусные детали работающие в помещении: корпуса телевизоров радиоприемников магнитофонов видеомагнитофонов пылесосов кофеварок пультов управления телефонов факсовых аппаратов компьютеров мониторов принтеров калькуляторов другой бытовой и оргтехники; металлизированные детали бытовой техники и оргтехники; конструкционные детали электротехнического назначения; выключатели переключатели; корпуса электроинструмента; канцелярские изделия; настольные принадлежности; игрушки; детские конструкторы; чемоданы; контейнеры; дверные ручки; металлизированные сантехнические изделия: вентили душевые рассекатели мойки поддоны сливные бачки; металлизированные украшения; мебельную фурнитуру; фитинги; детали медицинского оборудования и медицинские принадлежности; смарт-карты.
В переложение на различные отрасли народного хозяйства применение АБС-пластика выглядит следующим образом.
В автомобильной промышленности на основе АБС-пластика и его композиций производятся детали интерьера и экстерьера автомобиля. Сюда относятся панели каркасы щитки панели приборов обрамление окон облицовка дверей и другие детали салона решетки радиатора колпаки колес корпуса фонарей и наружных зеркал горловина воздухозаборника облицовка дверей бампер. Относительно широкое применение в автомобильной промышленности нашла композиция на основе АБС-пластика – АБСПК.
В приборостроении АБС-пластик применяют как конструкционный материал для изготовления корпусов электроприборов электроинструментов аккумуляторов. При этом можно отдельно выделить использование АБС-пластика для производства корпусных деталей электроприборов работающих в помещении. Сюда можно отнести корпуса таких приборов как телевизоров радиоприемников магнитофонов видеомагнитофонов пылесосов кофеварок пультов управления телефонов факсовых аппаратов компьютеров мониторов принтеров калькуляторов другой бытовой и оргтехники. Также на основе АБС-пластика могут быть изготовлены части электрических и электронных приборов: гибкие диски CD-ROM вставки DVD. АБС-пластик широко применяется для изготовления деталей холодильников.
В производстве ТНП АБС-пластик применяется для производства таких видов товаров народного потребления как: хозяйственные товары для домашнего обихода – товары для ванной и туалетной комнаты садово–огородный инвентарь; спортивные товары – шлемы щиты; детские товары и игрушки включая детские конструкторы; настольные канцелярские принадлежности.
В пищевой промышленности АБС-пластик находит применение в качестве посуды для питания на воздушном железнодорожном и водном транспорте: чашки тарелки боксы изготавливаемые из марок АБС-пластика разрешенных к использованию с горячими пищевыми продуктами.
Кроме того на основе АБС-пластика изготавливаются дорожные знаки элементы часовых механизмов оптические инструменты. В медицине АБС-пластик используется для производства деталей медицинского оборудования медицинских чемоданов. Также АБС-пластик применяется при изготовлении профилей для торгового оборудования. В мебельной промышленности АБС-пластик и композиции на его основе применяются для производства мебельной фурнитуры. Свойства АБС-пластика можно изменять в широких пределах посредством модификации исходного материала. На основе АБС-пластика создаются композиционные полимерные материалы имеющие улучшенные эксплуатационные характеристики по сравнению с собственно АБС-пластиком. Наиболее известные из них:
Другие обозначения: ABS+PC ABSPC PCABS. Ударопрочный аморфный материал. Имеет большую теплостойкость чем АБС-пластик которая повышается при увеличении содержании поликарбоната. Выдерживает кратковременный нагрев без нагружения до 130-145 °С с нагружением до 100-110 °С (стеклонаполненные марки до 130-140 °С). Максимальная температура длительной эксплуатации: 60-95 °С. Температура хрупкости: -50 °С. Повышение содержания поликарбоната увеличивает ударопрочность и морозостойкость. Композит АБСПК имеет хорошую химическую стойкость. Стоек к спиртам воде растворам солей и маслам. Может растрескиваться при действии щелочей алифатических углеводородов хлорированных углеводородов. Лучше перерабатывается по сравнению с поликарбонатом. Имеет высокую размерную стабильность. Рекомендуется для точного литья. Отличается малым короблением. Хорошо сваривается трением горячей плитой ультразвуком.
Другие обозначения: ABS+PVC PVC + ABS ABSPVC PVCABS. Смесь АБС-пластика и поливинилхлорида представляет собой аморфный ударопрочный материал. Выдерживает кратковременный нагрев до 90-97 °С. Композит АБСПВХ имеет большую атмосферостойкость чем AБС. Стоек к старению. Хорошо перерабатывается.
Другие обозначения: ABS+PBT ABSPBT PBTABS. Смесь АБС-пластика и полибутилентерефталата – жесткий ударопрочный аморфный или кристаллизующийся материал. Отличается высокой размерной стабильностью при повышенных температурах. Повышение содержания полибутилентерефталата увеличивает теплостойкость. Выдерживает кратковременный нагрев при нагружении до 85-150 °С (для стеклонаполненных марок – до 150-200 °С). Имеет хорошие диэлектрические свойства и высокую химическую стойкость. Устойчив к алифатическим углеводородам бензину маслам и смазкам разбавленным кислотам и щелочам детергентам. Хорошо перерабатывается. Повышение содержания АБС снижает усадку и увеличивает размерную точность.
Другие обозначения: ABSPA ABSPA PAABS. Смесь АБС-пластика и полиамида – ударопрочный аморфный или кристаллизующийся материал. В основном выпускается смесь АБС+ПА6. Смесь АБС+ПА6 выдерживает температуру кратковременно до 180 °С АБС+ПА66 – до 250 °С. Температура длительной эксплуатации смеси АБС+ПА6 без ударных нагрузок до 80-110 °С; с ударными нагрузками – до 60-65 °С. Повышение содержания полиамида увеличивает ударопрочность. Имеет высокую износостойкость. Отличается низкой плотностью по сравнению с АБС+ПБТ AБС+ПК. Характеризуется хорошими диэлектрическими свойствами. Имеет хорошую химическую стойкость. Стоек к растрескиванию. Имеет хорошую перерабатываемость хорошо воспроизводит текстуру. Характеризуется высоким качеством спаев: высокая прочность невидимые линии спая. Усадка меньше чем у ПА. Имеет лучшую размерную стабильность по сравнению с ПА6.
Композиты АБС-пластика и эластомеров. Взятые в различных соотношениях термопластичные эластомеры (термополиуретан термопластэластомеры) и АБС-пластик образуют сплавы которые имеют хорошие свойства недостижимые для отдельно взятых полимеров. Соэкструзия АБС с термопластичными эластомерами удорожает материал но повышает его атмосферо- и морозостойкость жесткость и стойкость к действию окислителей и алифатических углеводородов. Основные характеристики АБС-пластиков приведены в таблице 3.1.1.
Физико-механические свойства АБС-пластика.
Наименование показателя
Насыпная плотность кгм3.
Прочность при растяжении МПа.
Прочность при изгибе МПа.
Прочность при сжатии МПа.
Относительное удлинение %.
Усадка (при изготовлении изделий) %.
Модуль упругости при растяжении при 23о С МПа
Ударная вязкость по Шарли (с надрезом) кДжм2.
Твердость по Бринеллю МПа.
Теплостойкость по Мартенсу °С.
Температура размягчения °С.
Максимальная температура длительной эксплуатации °С.
Диапазон технологических температур °С.
Диэлектрическая проницаемость при 106 Гц
Тангенс угла диэлектрических потерь при 106 Гц
Удельное объемное электрическое сопротивление Омм.
Электрическая прочность МВм.
Температура самовоспламенения °С.
1.3 Выбор и обоснование рецепта производства
АБС-пластик марка HG-0760AT («Samsung Chemicals» - Южная Корея)
1.4 Требования к исходному сырью
Для получения качественных изделий сырьё должно отвечать следующим требованиям:
содержание влаги – не более 05%;
содержание вторичного сырья – не более 20%;
размер гранул должен быть не более 4 мм в диаметре;
содержание посторонних включений должно быть в норме.
Задание требований обусловлено следующим: при высоком содержании влаги в полимерном материале впрыск расплава в матрицу становится затруднительным. Материал не впрыскивается струёй а распрыскивается каплями что затрудняет процесс формования.
Выпускаемые изделия должны быть прочными и эластичными что не достигается при содержании в сырье выше установленной нормы инородных тел и частично денатурированного материала. Инородные тела способствуют засорению литниковых каналов.
Основной источник инородных тел – измельчитель бракованных изделий так как в бункер измельчителя иногда по различным причинам попадает мелкий мусор.
1.5 Входной контроль сырья
Входной контроль сырья осуществляется по следующим документам:
гигиенический сертификат от центра санитарно-эпидемиологического надзора;
сертификат качества сырья.
В соответствии с выданным предприятию гигиеническим сертификатом на сырьё предприятие сможет производить изделия предназначенные для контакта с пищевыми продуктами.
В соответствии с сертификатом качества по заключению лаборатории производства сырья качество полимерных материалов должно соответствовать требованиям ГОСТ 12271-76.
Приёмка сополимеров стирола производится партиями. За партию принимают количество сополимера стирола полученного за одну операцию смешения сопровождаемое одним документом о качестве.партии должна быть не менее 05 т.
Для проверки качества сополимеров стирола на соответствие требованиям настоящего стандарта отбирают точечные пробы от 5 % едениц продукции но не менее чем от трех.
Контроль внешнего вида показателей чистоты поверхности диска массовой доли влаги и летучих веществ текучести расплава проводят на каждой партии сополимеров. Изготовитель определяет массовую долю остаточного мономера стирола температуру размягчения по Вика ударную вязкость периодически не реже одного раза в месяц а напряжение при изгибе и электрические характеристики – не реже одного раза в год.
Контроль гигиенических показателей проводят на каждой партии сополимеров стирола предназначенных для изготовления изделий контактирующих с пищевыми продуктами и детских игрушек.
Каждая партия сополимера стирола должна сопровождаться документом удостоверяющим ее качество. Документ должен содержать следующие данные:
- условное обозначение материала;
- номер партии и количество единиц продукции;
- дату изготовления;
- результаты проведения испытаний или подтверждение соответствия продукта требованиям настоящего стандарта.
При получении неудовлетворительных результатов испытания хотя бы по одному из показателей по нему проводят повторное испытание на удвоенном количестве единиц продукции взятых от той же партии. Результаты повторных испытаний распространяются на всю партию.
1.6 Методы испытаний сырья на входном контроле
Точечные пробы отбирают совком или щупом с продольным вырезом или щупом для порошкообразных продуктов по ГОСТ 2517-85 в равных количествах от каждой отобранной в выборку упаковочной единицы.
Из каждого мягкого контейнера берут не менее трех проб щупом с разных уровней.
Точечные пробы соединяют тщательно перемешивают и отбирают объединенную пробу массой не менее 2 кг.
Объединенную пробу помещают в чистую сухую плотно закрывающуюся банку или во влагонепроницаемый мешочек. На банку наклеивают а в мешочек вкладывают этикетку с обозначением предприятия-изготовителя наименования продукта марки номера партии даты отбора проб.
Образцы для физико-механических и электрических испытаний а также для определения гигиенических показателей изготавливают по ГОСТ 12019-66 литьем под давлением по режимам указанным в табл. 3.1.3 на червячных литьевых машинах с объемом впрыска не более 63 см3.
Эскиз формы для изготовления образцов дан в рекомендуемом приложении к госту.
Температуру расплава замеряют игольчатой термопарой диаметром не более 2 мм которую вводят до середины толщины стренги материала непосредственно у сопла литьевой машины сразу после окончания впрыска. Термопара не должна касаться поверхности сопла. Допускается производить замер температуры расплава термометром.
Режимы литья образцов для физико-механических и электрических испытаний .
Сополимеры стирола марок
Температура литьевой массы °С
Время выдержки под давлением в форме с
Время выдержки под охлаждением в форме с
Давление литья Нмм2 (кгссм2)
Температура литьевой формы °С
Перед литьем сополимер подсушивают до содержания влаги не более 01 % при 70 - 80 С.
Остаточную влагу рекомендуется определять по ГОСТ 11736-78.
Образцы перед испытанием кондиционируют по ГОСТ 12423-66 не менее 3 ч.
Для электрических испытаний образцы кондиционируют по ГОСТ 6433.1-71 не менее 4 ч при температуре 15 - 35 С и относительной влажности 45 - 75 %.
Внешний вид гранул сополимера определяют визуально без увеличительных приборов на пробе отобранной по методу отбора разовых проб описанному выше
Размер гранул сополимеров стирола определяют измерением максимального размера гранул.
Максимальный размер гранул взятых из (200 ± 1) г объединенной пробы отобранной по методу отбора разовых проб определяют штангенциркулем по ГОСТ 166-89 или линейкой по ГОСТ 427-75.
Максимальные размеры отобранных для испытания гранул должны находиться в диапазоне от 2 до 5 мм.
Чистоту поверхности диска определяют визуально без применения увеличительных приборов в отраженном свете на трех дисках диаметром (50 ± 1) мм толщиной (3 ± 02) мм или (2 ± 02) мм изготовленных по методу изготовления образцов для физико-механических и электрических испытаний .
Поверхность диска должна быть однородной по цвету. Цвет определяют сравнением с контрольным образцом утвержденным в установленном порядке.
Массовую долю остаточного мономера определяют по ГОСТ 15820-82 методом газожидкостной хроматографии.
Определение массовой доли влаги летучих веществ
Образцы отбирают по по методу отбора разовых проб
- стаканчик для взвешивания типа СН-3412 или СН-6014 по ГОСТ 25336-82;
- эксикатор с любым осушающим веществом;
Проведение испытания
В высушенный и взвешенный с погрешностью не более 00002 г стаканчик помещают 15 - 20 г сополимера и вновь взвешивают с той же погрешностью.
Стаканчик с навеской помещают в сушильный шкаф и выдерживают при 105 - 110 °С. Продолжительность сушки сополимеров марок МСН и МСН-Л - 25 ч. Затем стаканчик охлаждают в эксикаторе и взвешивают.
Массовую долю влаги и летучих веществ (X) в процентах вычисляют по формуле
где т - масса стаканчика с сополимером стирола до сушки г;
т1 - масса стаканчика с сополимером стирола после сушки г;
m2 - масса сополимера стирола г.
За результат испытания принимают среднее арифметическое значение двух параллельных определений допускаемые расхождения между которыми не должны быть более 0005 %.
Показатель текучести расплава определяют по ГОСТ 11645-73 при температуре (200 ± 05) С и нагрузке (9810 ± 025) Н [(10000 ± 0025) кгс] на экструзионном пластометре с диаметром капилляра (2095 ± 0005) мм после выдержки материала под давлением в течение (100 ± 05) мин. Перед определением материал подсушивают в сушильном шкафу при температуре (75 ± 5) С в течение 3 ч. Допускается измерять температуру введением термометра в экструзионную камеру пластометра.
Температуру размягчения по Вика определяют по ГОСТ 15088-83 при нагрузке (50 ± 1) Н [(50 ± 10) кгс] на образцах размером (80 ± 2)(10 ± 05)(4 ± 02) мм изготовленных по методу изготовления образцов для физико-механических и электрических испытаний. Скорость подъема температуры (120 ± 10) °С за час.
Ударную вязкость определяют по ГОСТ 4647-80 при скорости движения маятника мс на образцах без надреза размером (50 ± 1)×(6 ± 02)×(4 ± 02) мм изготовленных по методу изготовления образцов для физико-механических и электрических испытаний. Испытание проводят при комнатной температуре на 5 образцах.
Напряжение при изгибе при заданной величине прогиба равной 15 толщины образца определяют по ГОСТ 4648-71 на образцах размером (80 ± 2)×(10 ± 05)×(4 ± 02) мм изготовленных по по методу изготовления образцов для физико-механических и электрических испытаний.
Удельное электрическое сопротивление определяют по ГОСТ 6433.2-71 при комнатных условиях на дисках диаметром (100 ± 1) мм; толщиной (2 ± 02) мм изготовленных по методу изготовления образцов для физико-механических и электрических испытаний после выдержки их в течение 2 ч при температуре (20 ± 2) °С и относительной влажности (65 ± 15) %.
Испытание проводят на любой аппаратуре позволяющей измерять удельное электрическое сопротивление до 1016 Ом см при постоянном напряжении 1000 В и имеющей электроды из отожженной алюминиевой фольги по ГОСТ 618-73 или оловянной фольги толщиной 001 - 002 мм.
Размеры электродов следующие:
- измерительный электрод диаметром (50 ± 02) мм;
- охранный кольцевой электрод внутренним диаметром (54 ± 02) мм шириной 10 мм;
- высоковольтный электрод диаметром 75 мм.
Контакт электрода с образцом осуществляется давлением 00098 Нмм2 (100 гссм2).
Тангенс угла диэлектрических потерь при частоте 106 Гц определяют по ГОСТ 22372-77 на дисках диаметром (50 ± 05) мм толщиной (2 ± 02) мм изготовленных по методу изготовления образцов для физико-механических и электрических испытаний. Электроды из отожженной алюминиевой фольги по ГОСТ 618-73 или оловянной фольги должны иметь форму и размеры испытуемого образца.
Электрическую прочность определяют по ГОСТ 6433.3-71 при комнатной температуре на дисках диаметром (100 ± 1) мм толщиной (2 ± 02) мм изготовленных по методу изготовления образцов для физико-механических и электрических испытаний после выдержки их в течение 2 ч при (20 ± 2) °С и относительной влажности (65 ± 5) %. Электрическую прочность при переменном напряжении и частоте 50 Гц определяют в трансформаторном масле с применением цилиндрических электродов из нержавеющей стали или латуни при плавном подъеме напряжения. Диаметр электродов должен быть равен (25 ± 05) мм радиус закругления - 25 мм высота - не менее 25 мм.
Запах привкус и концентрацию мономеров в водных вытяжках сополимеров стирола определяют по ГОСТ 22648-77 на бруске размером (50 ± 1)×(6 ± 02)(4 ± 02) мм изготовленном по методу изготовления образцов для физико-механических и электрических испытаний.
2 Составление и описание технологической схемы производства
В проектируемой технологической схеме производства предусматривается автоматический режим работы основного оборудования. Графическое изображение данной схемы приведено в Приложении 26.
Технологическая схема производства литьевых изделий состоит из следующих операций:
- растаривание сырья;
- формование изделий;
- контроль и упаковка;
- хранение готовой продукции;
- переработки отходов.
Рассмотрим содержание каждой стадии технологической схемы более подробно.
Блок-схема технологического процесса производства пластиковых аксессуаров для систем вентиляции и кондиционирования методом литья под давлением представлена на Рис. 5
Рис. 5. Блок-схема технологического процесса производства пластиковых аксессуаров для систем вентиляции и кондиционирования методом литья под давлением
Материал в гранулированном виде поступает на завод в автофургонах в контейнерах по 500 кг или полиэтиленовых мешках по 25-30 кг. Выгрузка из вагона производится с помощью электропогрузчика (автокрана). Сырье из контейнеров растаривается и подается пневмотранспортом в складские емкости. Сырье в мешках укладывается партиями на поддоны и межцеховым транспортом перевозится на склад предприятия. При приеме сырья в любой упаковке обязательным условием является учет прибывшего сырья для чего предусматриваются железнодорожные и автомобильные весы.
2.2 Материальный баланс
Нормативные коэффициенты представляют собой отношение массы потерь или отходов к массе готовых изделий. При изготовлении изделий из термопластов методом литья под давлением существуют технологические потери а также возвратные (используемые) и безвозвратные отходы.
Величина потерь и отходов определяются нормативными коэффициентами.
Нормативные коэффициенты представляют собой отношение массы потерь или отходов к массе готовых изделий. Значения коэффициентов для весовых диапазонов и групп сложности изделий определяются техническим бюро проектируемого предприятия. Схема материального баланса проектируемого предприятия представлена на рис 3.1.
Используя эти данные рассчитываем количество возвратных и безвозвратных отходов и технологические потери.
В результате переработки 1025 тгод сырья будет получено 100 тгод готовых изделий. Технологические потери составляют 05 % т.е. 05 тгод перерабатываемого материала; возвратные отходы составляют 25 % или 25 тгод перерабатываемого материала; безвозвратные отходы 2 % или 2 тгод
Рис. 6. Схема материального баланса
Сырьевой склад проектируется из расчёта сорока суточного запаса сырья.
Основная масса сырья хранится в емкостях отдельно расположенного склада и с помощью пневмотранспорта подается в емкости расположенные внутри предприятия. Из складских емкостей предприятия сырье подается к литьевым машинам при помощи пневмотранспорта включающегося автоматически по вызову от литьевой машины при понижении уровня сырья в бункере машины.
Часть сырья поступающего в мешках храниться партиями стеллажным способом на поддонах.
Расчет размеров бункеров для хранения текущих запасов сырья
Расчет размеров бункеров.
При расчете бункеров учитываем только те их части которые представляют собой параллелепипеды.
Расчет производим исходя из формулы:
V – объем исходного запаса компонента в бункере м3;
a b и h – соответственно длина ширина и высота бункера м;
k – коэффициент заполнения бункера (085-095);
m – исходный запас компонента в бункере кг;
γнас. – насыпная плотность компонента кгм3;
Если принять что a = b и h = 2a то:
АБС-пластик – десятисуточный исходный запас.
Объем бункера для АБС-пластик V=a*b*h= 15*15*3=675 м3
Выбираем ближайший V=8 м3 15х15х3.55
Коэффициент запаса составляет K=V бункера V необход = 8675=1185
2.4 Растаривание сырья
Гранулированное сырьё в мешках массой 25 кг в приёмный бункер объёмом 675 м³. Под бункером установлен шлюзовой питатель который сохраняет вакуум в бункере и является дозатором гранулированного сырья. Транспортирующая среда – воздух. На бункере для контроля заполнения установлены датчики верхнего и нижнего уровня сырья. Управление системой пневмотранспорта производится с дистанционного пульта. Из приёмного бункера сырьё пневмотранспортом подаётся в бункера литьевых машин.
Сырье поступающее на предприятие в любой упаковке сопровождается соответствующим документом (паспортом) в котором указывается его основные характеристики и соответствие требованиям государственных стандартов или технических условий.
Для определения параметров перерабатываемости сырья а также соответствия характеристик значениям указанным в сопроводительном документе проводится так называемый входной контроль. При этом определяется однородность материала в партии и показатель текучести расплава.
Определение основных технологических и физико-механических показателей сырья при необходимости проводится в цеховой лаборатории имеющей отделения технологических физико-механических и химико-аналитических испытаний.
2.5 Подготовка сырья
Подготовка сырья выполняется в зависимости от его свойств и требований к качеству готовой продукции. Как правило для получения продукции высокого качества и точности необходимо сырье подвергать сушке и гомогенизации. В связи с этим в сушильных бункерах будут выполняться операции сушки сырья. Влажность сырья является одним из важных параметров влияющих на качество литьевых изделий. При повышенной влажности изделия имеют плохой внешний вид (серебристость утяжины) а также ухудшение механических свойств.
В связи с этим термопласты перед переработкой рекомендуется сушить горячим воздухом с температурой 60-800С. Для этого у литьевой машины устанавливают дополнительный бункер с вентилятором электрическим нагревателем распределителем воздуха и системы контроля и управления -"бункер-сушилка".
Предполагается что на предприятии будет использоваться бункер-сушилка производства "Shini" (Тайвань) cерия SHD 20-U "EURO
Бункер-сушилка (осушитель сырья) серии SHD 20-U сконструирован в соответствии с европейскими стандартами. Отличительной особенностью данного осушителя сырья является система нисходящей подачи горячего воздуха. Особая конструкция позволяет добиться равномерного распределения воздушного потока что обеспечивает поддержание постоянной температуры и повышает эффективность осушения. Корпус бункера выполнен из нержавеющей стали. Для контроля за температурой используется микропроцессор. Бункер-сушилка снабжен двойной системой защиты от перегрева. Блок управления осушителя оснащен цифровой системой контроля с LED индикатором таймером запускаостановки переключателем системы контроля регулятором подачи питания. Технические характеристики приведены в таблице 3.2.1.
Технические характеристики бункер-сушилки производства "Shini" (Тайвань) cерия SHD 20-U "EURO
Мощность нагревателя кВт
Мощность вентилятора Вт
Габаритные размеры бункера ДхШхВ мм
Габаритные размеры установочной рамы ДхШхВ мм
Высота комплекса "бункер на установочной раме" мм
2.6 Формование изделия литье
Для формования изделий методом литья под давлением применяются шнековые литьевые машины. Конструкция литьевых машин и их техническое оснащение обеспечивают переработку практически всех термопластичных материалов.
Технологический цикл в литьевой машине при изготовлении изделий обеспечивается за счёт слаженной работы трёх узлов: узла смыкания и запирания форм узла пластикации и впрыска механизма подвода и отвода узла пластикации и впрыска.
Цикл литья изделий из термопластов состоит из следующих операций и выполняется в такой последовательности: перемещение подвижной плиты; запирания формы; перемещения механизма впрыска к форме и впрыск раслава в форму; выдержка материала в форме под давлением; охлаждение изделия в форме; раскрытие формы; подача материала в материальный цилиндр пластикация его и гомогенизация за счёт энергии вращения червяка и тепла подводимого из вне; раскрытие формы и удаление изделия из формы.
Процесс литья под давлением характеризуется технологическими параметрами: давление литья температура материального цилиндра время (продолжительность) цикла температура формы и т.п.
Режимы литья контролируются программным управлением с измерительными приборами (КИП).
За изготовлением изделия следует следующая стадия - механическая обработка изделий. Механическая обработка изделий в большинстве случаев заключается в отделении изделии от литников. После того как изделие с помощью выталкивателей извлекается из пресс- формы отрезаются литники. Эта операция осуществляется непосредственно на рабочем месте вручную с помощью ножа.
2.7 Контроль качества и упаковка готовой продукции
Детали изготовленные методом литья под давлением должны соответствовать требованиям стандартов (ГОСТ ОСТ) техническим условиям на данную продукцию. По внешнему виду изделия должны соответствовать образцам (эталонам).
Контроль качества осуществляется контролером непосредственно на месте изготовления деталей или на столе контролера.
Упаковка изделий может осуществляться централизованно (на столе упаковки) и децентрализовано - непосредственно у литьевых машин.
2.8 Технические условия ТУ 4863-002-44911369-10 (введены впервые)
Настоящие технические условия распространяются на пластиковые аксессуары для систем вентиляции и кондиционирования (далее аксессуары) изготавливаемые методом литья под давлением.
Пластмассовые аксессуары предназначены для установки на вытяжных приточных вентиляционных каналах жилых общественных зданий и вспомогательных зданий промышленных предприятий.
Применение аксессуаров в условиях их возможного нагрева свыше +500 С не допускается.
Перечень оборудования и приборов приведен в приложении 23.
Перечень ссылочных документов приведен в приложении 25.
Условное обозначение пластмассовой вентиляционной решетки должно состоять из обозначения типа решетки и обозначения настоящих технических условий.
Пример условного обозначения решетки типа ASGC 1530 состоящей из рамки с посадочными размерами 150х300 мм вертикальными и горизонтальными поворотными жалюзи:
ASGC 1530 ТУ 4863-002-44911369-10
Пример условного обозначения решетки типа ARGWF 1144 состоящей из решетчатой вставки с наклонно расположенными направляющими жалюзи шаг 19 мм под углом 300 по направлению вниз размер 110х440 мм рамки с фиксирующими элементами и листа оконной сетки:
ARGWF 1144 ТУ 4863-002-44911369-10
Пример условного обозначения решетки типа ARGWO 1133 состоящей из трех цельнолитых деталей которые соединены между собой посредством шипового соединения тип "шип-паз" с посадочными размерами 110х330 мм :
ARGWO 1133 ТУ 4863-002-44911369-10
Пример условного обозначения тройника типа ATE 160160160 состоящего из двух цельнолитых деталей которые соединены между собой посредством шипового соединения тип "шип-паз" с присоединительными размерами воздуховодов d= 3х160 мм:
ATE 160160160 ТУ 4863-002-44911369-10
Пример условного обозначения адаптера типа AADS 110х330160 цельнолитая деталь которая имеет присоединительный размер к решетке 110х330 мм и присоединительный размер для воздуховодов d= 160 мм:
AADS 110х330160 ТУ 4863-002-44911369-10
Пример условного обозначения демпфера модульного типа DM200 состоящего из двух цельнолитых деталей которые соединены между собой посредством шипового соединения тип "шип-паз" с присоединительными размерами воздуховодов d=200 мм и поворотной заслонки зафиксированной между двумя внешними деталями демпфера:
DM 200 ТУ 4863-002-44911369-10
Технические требования.
Вентиляционные пластмассовые аксессуары должны соответствовать требованиям настоящих технических условий и комплектам конструкторской документации (КД) указанным в приложениях № 16 17 18 19 20 21 и 22.
2 Типы решеток тройников адаптеров и демпферов должны соответствовать данным указанным в приложении № 16
3 Основные размеры параметры и обозначения решеток типа ASGC должны соответствовать данным указанным в приложении № 17
4 Основные размеры параметры и обозначения решеток типа ARGWF должны соответствовать данным указанным в приложении № 18
5 Основные размеры параметры и обозначения решеток типа ARGWO должны соответствовать данным указанным в приложении № 19
6 Основные размеры параметры и обозначения тройников типа ATE должны соответствовать данным указанным в приложении № 20
7 Основные размеры параметры и обозначения адаптеров типа AADS должны соответствовать данным указанным в приложении № 21
8 Основные размеры параметры и обозначения демпферов модульных типа DM должны соответствовать данным указанным в приложении № 22
9 Аксессуары и входящие в них детали не должны иметь видимых дефектов; на поверхности деталей не должно быть «апельсиновых корок» вздутий гратов; поверхность не должна быть волнистой иметь царапин видимых на расстоянии 1 метра от поверхности аксессуара; трещин. Литники и облои не допускаются. Следы от среза литников и выталкивателей не должны превышать по глубине или высоте 02 мм.
10 Наличие дефектов на внешней поверхности аксессуаров после сборки: сколов вмятин царапин трещин не допускается.
ПРИМЕЧАНИЕ: Допускаются дефекты с внутренней стороны изделия (царапины небольшие пятна разводы) общей площадью не более 1% от внутренней поверхности.
11 Наличие дефектов листа оконной сетки (разрывов вырывов) не допускается.
12 Смещение листа оконной сетки относительно решетки с выступлением за её края не допускается.
13 Наличие следов клея на поверхности решетки не допускается.
14 Цвет деталей должен соответствовать цвету эталонных образцов.
15 Решетки должны быть теплостойкими. При нагревании решеток до температуры +50°С конструкция решеток не должна меняться (клеевое крепление листа оконной сетки к решетке не должно разрушаться входящие детали должны сохранять форму и размеры).
16 Покупные изделия должны иметь документ подтверждающий их соответствие стандартам техническим условиям или другой документации утвержденной в установленном порядке.
17 Маркировка аксессуаров наносится на этикетки или бирки на которых должно быть указано: наименование изделия наименование страны изготовителя наименование и адрес предприятия-изготовителя область применения условия хранения краткие технические характеристики решетки обозначение технических условий.
18 Каждый аксессуар должен быть индивидуально упакован в термоусадочную пленку по ГОСТ 25951 с вложенной этикеткой или с биркой скрепленной с пленкой упаковки. Допускается в качестве упаковки использовать полиэтиленовый пакет по ГОСТ 10354 или ему подобный.
19 Индивидуально упакованные аксессуары с бирками или этикетками укладывают в ящики из гофрированного картона по ГОСТ 7376; ящики должны быть заклеены лентой клеевой по ГОСТ 18251 или ей подобной.
20 Маркировка транспортной тары должна производиться по ГОСТ 14192 с нанесением манипуляционного знака «Хрупкое. Осторожно» и следующих дополнительных данных: наименование и адрес предприятия – изготовителя или его товарный знак; обозначение и число решеток масса брутто.
. Требования безопасности и охраны окружающей среды.
1 При изготовлении аксессуаров содержание вредных веществ в воздухе рабочей зоны не должно превышать установленных предельно-допустимых концентраций указанных в ГОСТ 12.1.005.
2 Технологические процессы изготовления аксессуаров должны соответствовать требованиям ГОСТ 12.3.002.
3 Вентиляционные системы помещений для производства аксессуаров должны соответствовать требованиям ГОСТ 12.4.021.
4 Производственное оборудование должно соответствовать требованиям ГОСТ 12.2.003.
5 При изготовлении и хранении аксессуаров пожарная безопасность должна быть обеспечена в соответствии с требованиями ГОСТ 12.1.004.
6 Детали не должны выделять во внешнюю среду вредные вещества в количествах превышающих допустимые уровни (ДУ) утвержденные Минздравом РФ. Концентрацию вредных веществ выделяющихся из аксессуаров и их санитарно-гигиеническую оценку определяют в соответствии с “Методическими указаниями по санитарно-гигиеническому контролю полимерных строительных материалов предназначенных для применения в строительстве жилых и общественных зданий” утвержденными Минздравом СССР № 2158-80 от 28 марта 1980 г.
1 Для проверки соответствия аксессуаров требованиям технических условий предусматриваются следующие виды испытаний:
2 Приемо-сдаточные испытания .
2.1 Приемо-сдаточные испытания проводят для определения соответствия аксессуаров техническим условиям при их выпуске.
2.2 Испытания проводит отдел технического контроля перед сдачей на склад. На испытания аксессуары должны предъявляться партиями. Партией считают количество аксессуаров одного типа изготовленных в течение смены выдержавших производственный контроль предусмотренный технологическим процессом изготовления и оговоренный в технологической документации.
2.3 Для испытания от партии отбирают 15 аксессуаров из которых 5 подвергают испытаниям а 10 оставляют на случай повторных испытаний.
Объем испытаний должен соответствовать таблице 6.
2.5 Результаты приемо-сдаточных испытаний оформляют в соответствии с п.6.6 ГОСТ 15.309.
2.6 В сопровождающем документе по п.5.2 на партию аксессуаров прошедших испытания с положительными результатами должна быть отметка отдела технического контроля.
2.7 При неудовлетворительных результатах проверки хотя бы по одному показателю по этому показателю проводят повторную проверку удвоенного числа аксессуаров.
Результаты повторной проверки считают окончательными и распространяют на всю партию.
3 Периодические испытания.
3.1 Периодические испытания проводят с целью подтверждения качества аксессуаров ранее установленным требованиям.
3.2 Испытания проводят 1 раз в 6 месяцев.
3.3 Для периодических испытаний отбирают 15 аксессуаров от выдержавшей приемо-сдаточные испытания партии из которых 5 подвергают испытаниям а 10 оставляют на случай повторных испытаний.
3.4 Объем испытаний должен соответствовать Приложению № 23. Результаты проведения испытаний оформляются актом по п. 7.7. ГОСТ 15.309.
3.5 При неудовлетворительных результатах проверки хотя бы по одному показателю проводят повторную проверку удвоенного числа аксессуаров. При неудовлетворительных результатах повторных испытаний испытуемые аксессуары бракуют отгрузку готовых и приемку новых аксессуаров временно прекращают.
После анализа выявленных дефектов и устранения причин брака возобновляют отгрузку готовых и приемку новых аксессуаров.
4 Типовые испытания.
4.1 Типовые испытания проводятся при изменении материалов или технологического регламента. Объем типовых испытаний должен определятся характером изменений материалов или изменений вносимых в технологию изготовления.
Вопрос о необходимости проведения и объем типовых испытаний решается техническим директором по представлению подразделения предлагающего изменения.
4.2 Типовые испытания проводят по программе разработанной подразделением предлагающим изменения и утвержденной в установленном порядке.
4.3 Для типовых испытаний изготавливают 15 аксессуаров с предлагаемыми изменениями 5 из них подвергают испытаниям а 10 хранят на случай повторных испытаний.
4.4 При несоответствии аксессуаров хотя бы по одному требованию программы испытаний проводят повторные испытания удвоенного количества аксессуаров
4.5 При неудовлетворительных результатах повторных испытаний аксессуаров предлагаемые изменения не вносятся в документацию.
5 Потребитель имеет право проводить контрольную проверку аксессуаров соблюдая при этом приведенный порядок отбора образцов и применяя указанные ниже методы контроля.
6 Условия проведения приемо-сдаточных периодических и типовых испытаний: температура окружающего воздуха от плюс 15°С до плюс 35°С при относительной влажности до 80%.
1 Покупные изделия (п.1.14) проверяются внешним осмотром и сличением сертификатов соответствия или другой сопроводительной документации с маркировкой транспортной тары и упаковкой.
2 Проверку конструкции аксессуаров их деталей на соответствие требованиям КД (п.1.6) проводят в процессе изготовления деталей при операционном контроле и ее сборке.
3 Проверку геометрических размеров (п.1.3;1.4;1.5) и чистоты поверхности (п.1.7) проводят в процессе настройки технологического оборудования.
3.1 Размеры детали проверяют штангенциркулем по ГОСТ 166 с погрешностью 01мм.
3.2 Отклонение от плоскостности нелицевой поверхности плоских деталей проверяют щупом по ТУ2-034-0221197-011-91 с погрешностью 01мм. Измеряют величину наибольшего зазора по периметру детали уложенной на поверочную плиту по ГОСТ 10905. Перечень оборудования и приборов указаны в таблице 3.2.10
4 Качество аксессуаров по показателям внешнего вида (п.п.1.7;1.8;1.11) проводят визуально с расстояния 1 м при освещенности не менее 200 лк.
5 Проверку качества оконной сетки (п.1.91.10) проводят визуально.
6 Цвет аксессуаров (п.1.12) определяют сличением с эталонным образцом.
7 Для проверки теплостойкости решетки (п.1.13) ее помещают в лабораторный сушильный шкаф с терморегулятором и выдерживают при температуре (50±3)°С в течение 20 мин. Затем решетку вынимают и на 30 мин оставляют на воздухе при температуре (20±2)°С. После этого проверяют конструкцию клеевое крепление листа оконной сетки к решетке геометрические размеры и плоскостность.
8 Проверка маркировки аксессуаров сводится к проверке наличия и качества маркировки в соответствии с требованием п.1.15 настоящих технических условий.
9 Упаковку аксессуаров проверяют на соответствие требованиям п.1.16 1.17.
10 Проверка маркировки транспортной тары заключается в проверке наличия манипуляционных знаков и надписей мест их расположения и качества маркировки тары в соответствии с требованиями п.1.18 настоящих технических условий и ГОСТ 14192.
Транспортирование и хранение.
1 Аксессуары транспортируют любым видом транспорта при условии защиты их от воздействия атмосферных осадков и сохранения целостности упаковки.
2 Предприятие – изготовитель должно сопровождать каждую отгружаемую партию аксессуаров документом установленной формы в котором указывают: наименование и адрес предприятия –изготовителя или его товарный знак; условное обозначение аксессуаров по настоящим техническим условиям; номер партии и дату изготовления; число аксессуаров; гарантийный срок хранения; отметку упаковщика; отметку ОТК предприятия-изготовителя.
3 Аксессуары следует хранить в упакованном виде в закрытом сухом помещении при температуре не ниже минус 40°С на расстоянии не менее 1 м от отопительных приборов.
4 Аксессуары поступающие к потребителю при температуре наружного воздуха ниже 0°С следует распаковывать и выдерживать в помещении не менее суток при соблюдении правил хранения согласно п.5.3.
Указания по эксплуатации.
1 Крепление аксессуаров на предварительно подготовленном месте: места должны быть очищены от строительного мусора и т.п.
2 При креплении аксессуаров не допускается их механическое повреждение.
3 Загрязнения с поверхности аксессуаров следует удалять мягкой тканью смоченной теплой водой или мыльным раствором.
Гарантии изготовителя
1 Изготовитель гарантирует соответствие аксессуаров требованиям настоящих технических условий при соблюдении условий транспортирования и указаний по эксплуатации. Гарантийный срок хранения и эксплуатации аксессуаров – 2 года с момента изготовления.
2.9 Хранение готовой продукции и маркировка
Готовая продукция в упакованном виде временно хранится на складе предприятия. Далее на тару с готовой продукцией наклеивается ярлык с указанием вида продукции количества изделий даты упаковки и т.п.
3.1 Переработка отходов
Предполагается что на предприятии переработка отходов будет производиться производится на дробилке для пластика c системой пневматической транспортировки серия XFS-180G-A ("Shini" Тайвань) технические характеристики которого приведены в таблице 3.2.2. Дроблёное вторичное сырьё перерабатывается в гранулы. Переработанные отходы добавляются к первичному сырью [4].
Технические характеристики дробилки XFS-180G-A
Мощность привода кВт
Количество ротационных ножей шт
Количество стационарных ножей шт
Диаметр ячеи сетки-экрана мм
Размеры приемной горловины мм
Частота вращения ротора обмин
Производительность кгчас
Выбор технологического оборудования и расчет потребности в нем
1 Выбор основного технологического оборудования
Выбор основного технологического оборудования должен соответствовать выбранной технологической схеме с учётом особенностей переработки того или иного вида термопластов. К основному оборудованию относятся оборудование оказывающее непосредственное воздействие на материал в процессе получения готовых изделий. Таким оборудованием являются литьевые машины.
Для производства изделий методом литья под давлением выбираются наиболее эффективные литьевые машины одноцилиндровой конструкции со шнековой пластикацией в которой шнек совершает вращательные и поступательные движения.
В производстве изделий из термопластов наиболее распространены литьевые машины с гидравлическим приводом из-за ряда преимуществ: они наиболее просты и удобны в эксплуатации; долговечны; легко регулировать основные параметры процесса литья (скорость впрыска давление литья).
Оборудование для литья под давлением производят в нашей стране и за рубежом. В связи с номенклатурой изделий выпускаемых на проектируемом предприятии выбираем однопозиционные термопластавтоматы с числовым программным управлением и объемом впрыска от 276 см3 до 1314 см3 ими являются модели типа SANDRETTO NOVE HP 750900 (Италия) SANDRETTO HP 13001650 (Италия) SANDRETTO HP 23003000 (Италия). Тип и типоразмер литьевых машин выбраны исходя из массы и размеров изделия площади литья материала изделий тиражности отношения толщины изделия к его длине гнёздности формы конструктивных особенностей изделий требований к точности изготовления и чистоте поверхности изделия. Марки и технологические характеристики выбранных машин указаны в Приложении 4.
1.1 Расчёт потребности в основном технологическом оборудовании
Произведём расчёт потребности в оборудовании по заданной ассортиментной программе.
Производительность литьевых машин по заданной ассортиментной программе рассчитывается по формуле:
где Q – производительность оборудования кгч;
m – масса изделия г;
T – число гнёзд в форме;
t – продолжительность цикла с.
Производительность по вертикальной и горизонтальной жалюзи для вентиляционной решетки двойной регулировки с посадочной высотой 110 мм (Qвертгор 110) соответственно:
Qвертгор 110 = 36*7*650 = 3 кгч;
Производительность по рычагам для вентиляционных решеток двойной регулировки с различной посадочной высотой (Qрычаг ) соответственно:
Qрычаг = 36*10*650 = 432 кгч;
Производительность по тягам для вентиляционных решеток двойной регулировки с различной посадочной высотой (Qтяг ) соответственно:
Qтяг = 36*3*640 = 162 кгч;
Производительность по частям корпуса для сборки вентиляционных решеток двойной регулировки с различной посадочной высотой (Qкорпус) соответственно:
Qкорпус = 36*138*260 = 1656 кгч;
Производительность по адаптерам с различными посадочными размерами среднее (Qадаптеры ) соответственно:
Qадаптеры = 36*929*160 = 5574 кгч;
Производительность по тройникам с различными посадочными размерами среднее (Qтройники ) соответственно:
Qтройники = 36*793*160 = 4758 кгч;
Производительность по демпферам с различными посадочными размерами среднее (Qдемпферы ) соответственно:
Qдемпферы = 36*1007*160 = 6042 кгч;
Производительность по заслонкам для демпферов с различными посадочными размерами среднее (Qзаслон ) соответственно:
Qзаслон = 36*70*260 = 84 кгч;
Производительность по частям корпуса для сборки переточных вентиляционных решеток с различной посадочной высотой (Qкорпус переточн) соответственно:
Qкорпус переточн = 36*762*160 = 4572 кгч;
Определим затраты времени необходимые для выполнения годовой программы по каждому изделию по формуле:
где Т – затраты времени необходимые для выполнения годовой программы по изделию ч;
Пт – годовая программа по изделию кгч;
Q – производительность работы литьевой машины по данному изделию кгч;
m – масса одного издели кг;
Твертгор 110 =3233990*00073= 7546 (ч)
Трычаг =213980*001432= 495 (ч)
Ттяг=427960*0003162=7925 (ч)
Ткорпус=302740*01381656=2523 (ч)
Тадаптеры =8550*09295574=1425 (ч)
Ттройники=4320*07934758=72 (ч)
Тдемпферы=37800*10076042=630 (ч)
Тзаслон=18900*00784= 1575 (ч)
Ткорпус переточн =74610*07624572=1244 (ч)
Если сложить время необходимое для выполнения годовой программы по каждому изделию то получится фонд времени выполнения всей программы производства при работе одной литьевой машины:
Тобщее = Твертгор 110 + Трычаг + Ттяг + Ткорпус + Тадаптеры + Ттройники + Тдемпферы + Тзаслон + Ткорпус переточн = 7546+495+7925 +2523+1425 +72+630+1575 +1244= 136025 (ч)
Рассчитаем количество литьевых машин которое обеспечит выполнение предприятием программы производства по формуле:
где Чм – количество необходимых машин;
Тобщее – фонд времени выполнения всей программы производства при эксплуатации одной литьевой машины ч;
Фд – действительный годовой фонд времени работы основного оборудования предприятия при работе предприятия в полуавтоматическом режиме в 3 смены составляет 5400 часов
К =093– коэффициент учитывающий потери времени на обслуживание рабочего места и оборудования подготовительно-заключительное время время на отдых и личные надобности.
Чм = 136025(5400*093) = 27
Таким образом количество оборудования необходимого для выполнения всей программы производства равно 3 машин.
2. Выбор вспомогательного технологического оборудования
К вспомогательному оборудованию относится холодильное оборудование (чиллер) а также вакуумный загрузчик сырья.
2.1 Водоохладители ( чиллеры )
Используются для охлаждения воды используемой в различных технологических процессах в том числе для охлаждения различных узлов и агрегатов промышленного оборудования. Использование чиллеров положительно сказывается как на долговечности промышленного оборудования так и на качестве изготовляемых изделий.
Использование холодной воды позволяет существенно снизить время цикла при изготовлении изделий методом литья под давлением. Порой эта разница составляет 50% если вместо холодной воды используют оборотную воду охлажденную с помощью градирен. Тем самым использование чиллера позволяет увеличить выпуск готовой продукции на 20% и более.
Почему используют чиллеры с воздушным охлаждением конденсаторного блока? Легкий и быстрый запуск. Нет необходимости в применении громоздких градирен.
Предполагается что на проектируемом предприятии будет использоваться чиллер производства "Shini" (Тайвань) модель XC-05ACI. Технические характеристики которого приведены в таблице 4.2.1. Использование чиллеров для охлаждения молдингов позволяет получать изделия с высокоглянцевой поверхностью и минимальными внутренними напряжениями Этот фактор способствует свободному извлечению готовых изделий без их механических повреждений. Охладители данной марки производятся по лицензии компании COPELAND (США). Оборудование обладает высокой надежностью а также простотой в эксплуатации и обслуживании. Использование электронных терморегуляторов обеспечивает высокоточное поддержание рабочей температуры в диапазоне от 5 до 35°C.
Защитные системы: защита от перегрузки компрессора и помпы датчики высокогонизкого давления защита от замерзания защита от короткого замыкания отключения фазы индикатор неисправностей
Использование импортных комплектующих производства Тайваня США Дании Японии гарантирует долгую безотказную работу.
Технические характеристики чиллера XC-05ACI
Производительность ккалч
Производительность насоса на охлаждение молдинга лмин
Диаметр трубопровода охлаждения кондесаторного блока дюймы
Мощность охлаждающего вентилятора кВт
Габаритные размеры мм
Емкость резервуара с водой л
2.2 Вакуумный загрузчик сырья
Предполагается что на проектируемом предприятии будет использоваться вакуумный загрузщик полимерного сырья "Shini" производства (Тайвань) серия SAL "EURO" модель SAL-1.5U. Технические характеристики которого приведены в таблице 4.2.2. Вакуумные загрузчики сырья серии SAL "EURO" сконструированы в соответствии с европейскими стандартами и отличаются высокой надежностью простотой установки и эксплуатации.
Корпус загрузчиков изготовлен из нержавеющей стали.
Звукоизолирующий колпак двигателя снижает уровень шума при работе загрузчика.
Положение бункера и основы легко регулируются.
Микропроцессорная система управления простота обслуживания и контроля. Цифровой дисплей.
Съемная контрольная панель позволяет организовать дистанционное управления загрузчиком.
Функция плавного запуска двигателя система контроля состояния ротора.
Возможность настройки для работы загрузчика в комплексе с миксером двухкомпонентного сырья для пропорционального добавления вторичного гранулята.
В базовую комплектацию загрузчика входит тканный фильтр. Имеется возможность оснащения системой автоочистки фильтра и воздушным аккумулятором для повышения эффективности работы загрузчика и упрощения его обслуживания.
Для контроля за уровнем сырья используются высокочувствительные датчики - микропереключатели и фотосенсоры (зависит от модели бункера).
Высокоэффективный электродвигатель с фазным ротором отличается высокой скоростью работы с поддержанием оптимально высокого давления.
Технические характеристики вакуумного загрузчика SAL-1.5U
Производительность кгч
Объем сырьевого бункера л
Диаметр подающих шлангов мм
Система автоочистки фильтра
Воздушный аккумулятор
Вес главного контроллера кг
В соответствии с инструкцией СН 202-76 в каждом проекте должен содержаться раздел по организации труда включающий следующие основные разделы: трудовой процесс; разделение труда; кооперация труда; организация и обслуживание рабочих мест; нормы труда и обоснование потребности в кадрах; численность персонала; условия труда; трудовые затраты и производительность труда; карты организации труда [6].
Трудовой процесс разработан в виде баланса рабочего времени за смену по каждому рабочему месту. Баланс рабочего времени составлен из функциональной занятости в течение оперативного времени в смену (время оперативной работы); подготовительно-заключительного времени; времени обслуживания рабочего места; времени на отдых и личные надобности.
Функциональная занятость по отдельным профессиям установлена путём определения объёма работ подлежащих выполнению рабочими в течение смены с учётом механизации и автоматизации процесса соответствующих современному уровню организации производства на данном участке.
При работе литьевых машин (в полуавтоматическом режиме) оператор выполняет в основном контрольные функции в течение всей смены производя обход обслуживаемого им оборудования через определённые промежутки времени. Наиболее существенными факторами влияющими на занятость литейщика является конструкция оснастки и место упаковки готовой продукции. Под конструкцией оснастки подразумевается конструкция литьевых систем. Наибольшее распространение получили безлитниковые формы формы с отрывом литника при размыкании и формы с пальчиковым литником.
Перечень элементов оперативного времени литейщика при работе литьевых машин в полуавтоматическом режиме в зависимости от конструкции литьевой формы и с учётом упаковки у литьевых машин приведён в Приложении 5.
Для производства изделий методом литья под давлением рассматривается в основном функциональное разделение труда.
По принципу функционального разделения труда выделяются следующие взаимосвязанные группы работающих: производственные рабочие деятельность которых связана непосредственно с предметом труда и направлена на его изменение и придание ему товарного вида; вспомогательные рабочие обеспечивающие нормальное функционирование основного производства к этой категории работающих также относятся уборщики производственных помещений; инженерно-технические работники (ИТР) деятельность которых обеспечивает организацию производства и управление им; младший обслуживающий персонал (МОП) обеспечивающий уборку конторских помещений сюда также относятся уборщики бытовых помещений. Внутри технологических групп предусмотрено разделение труда в соответствии с квалификационным уровнем выполняемых работ. Типовой профессионально-квалификационный состав рабочих производства литьевых изделий приведён в Приложении 6. Наименование профессий рабочих и тарифные разряды указаны согласно единому тарифно-эксплуатационному справочнику (ЕТКС) 1970 г. [7].
Для осуществления кооперации труда использована бригадная форма организации труда. Возможны две основные формы производственных бригад – специализированные и комплексные. Выбраны комплексные бригады. Они формируются из рабочих различных профессий и специальностей. Распределение работ в бригаде осуществляется в зависимости от профессии квалификации и состава работ подлежащих выполнению. При этом имеются различные варианты совмещения профессий позволяющие улучшить организацию труда и более рационально использовать рабочее время.
4 Организация рабочих мест основного производства
На предприятии имеется одно рабочее место основного производства состоящее из двух литьевых машин.
В проектируемом предприятии предусмотрены литьевые машины с встроенными электрошкафами.
Количество машин – 3 штуки.
Основными параметрами характеризующими рабочие места для литьевых машин являются: расстояние между осями машин в зоне обслуживания (а) расстояние между осями машин с тыльной стороны (в) габаритные размеры рабочего места – длина (с) и ширина (св).
Расстояние между осями машин со стороны рабочей зоны (а) ограничивается шириной прохода в зону обслуживания и прохода в зоне обслуживания (k) (не менее 800 мм) а также расстоянием между рабочими столами или столом и термостатирующим агрегатом в зоне обслуживания (е) (не менее 1200 мм). Расстояние между осями машины с тыльной стороны определяются шириной прохода между шкафами или термостатами и литьевой машиной (m) и между пневмопогрузчиками (n) (не менее 700 мм) а также удобством прокладки коммуникаций и выполнении работ при ремонтах осмотрах и наладке. Габаритные размеры рабочего места определяются: ширина – расстоянием между осями машин; длина – суммой длины оборудования половины ширины прохода и половины ширины проезда.
Ширина проезда может быть различной в зависимости от вида средств механизации и их но она не должна быть меньше 2500 мм для одностороннего проезда и 3500 мм для двустороннего. Ширина прохода может быть также разной но не менее 800 мм. Для рабочих мест из трёх литьевых машин при обслуживании которых литейщик в течение рабочего времени должен ходить по проходу ширина прохода должна быть увеличена на 600 мм.
5 Организация рабочих мест вспомогательных рабочих
Для организации рабочих мест вспомогательных рабочих необходимо предусматривать: производственную мебель для размещения и хранения приспособлений инструмента измерительных приборов вспомогательных материалов сменных частей. А также специально выделенные места для хранения резервного оборудования; удобную тару для материалов проводов кабелей; инструмент измерительные приборы; планшеты для хранения электрических схем справочных материалов; доски для схем плакатов инструкций; приспособления для ухода за машиной для уборки рабочего места; средства механизации вспомогательных работ при подъёме тяжестей и их перемещении. Для транспортировки пресс-форм и грузов массой более 25 кг на предприятии предусмотрена потолочная подвесная кран-балка грузоподъёмностью Q = 23 т.
6 Содержание работы литейщика
Литьё под давлением на литьевых машинах в автоматическом режиме.
Работа литейщика (оператора литейной машины) содержит следующий ряд основных операций: участие в настройке всех механизмов машины на заданный режим литья; разогрев машины по зонам; установление технологической последовательности и режимов литья по технологической карте и смазка литьевых форм. А также наблюдение за установленным режимом литья по контрольно-измерительным приборам; вставка в гнёзда форм арматуры и оформляющих знаков; разборка форм съём изделий заделка раковин; устранение неполадок в работе литьевой машины; упаковка изделий [1]. Затраты времени литейщика на выполнение некоторых основных операций (укрупненные нормы) указаны в таблице 5.1.
Затраты времени литейщика
Наименование затрат времени
Продолжительность мин.
Подготовительно-заключительное время
Время обслуживания рабочего места
Время оперативной работы литейщика пластмасс
Время на отдых и личные надобности
7 Организация и обслуживание рабочего места
Организация рабочего места изображена в Приложении 8.
Технологическая оснастка: литьевая форма приспособления.
Инструменты: мерительный режущий слесарно-монтажный.
Документация: инструкция по ТБ карта технологическая карта организации труда чертёж изделия.
Карта обслуживания рабочего места приведена в Приложении 7.
Основные характеристики условий труда приведены в таблице 5.2.
Факторы санитарно-гигиенические
Средства защиты от неблагоприятных условий
Температура воздуха °С
Общеобменная вениляция. Местный отсос от каждой машины в зоне выделения летучих. Регулирование температуры приточного воздуха за счёт совмещения вентиляции с отоплением.
Относительная влажность воздуха %
Скорость движения воздуха мс
9 Численность основных и вспомогательных рабочих
Численность рабочих занятых на ненормируемых работах может быть расчитана по нормам обслуживания по числу рабочих мест и по нормативам численности рабочих.
Расчитаем норму обслуживания литьевых машин (количество единиц оборудования Нобсл обслуживаемых одним человеком).
Расчёт рекомендуется производить по формуле:
Нобсл = (Тсм - Т'пз – Тот – Тл) (Т"пз + Тобсл + Топ) (5.1.)
где Тсм – продолжительность смены;
Т'пз – подготовительное время нормируемое на одного человека в смену;
Тот – время на отдых в зависимости от оперативного времени в смену;
Тл – время на личные надобности нормируемое на одного человека в смену;
Т"пз – подготовительно-заключительное время нормируемое на единицу оборудования в смену;
Тобсл – время обслуживания нормируемое на единицу оборудования в смену;
Топ – время оперативной работы на единицу оборудования в смену.
Тсм = 480 мин.; Т'пз = 2 мин.; Тот = 20 мин.; Тл = 5 мин.; Т"пз = 7 мин.; Тобсл = 5 мин. для полуавтоматического режима работы оборудования согласно нормативам НИИ труда.
Время оперативной работы на единицу оборудования в смену определяется по формуле:
где а1 – доля оперативного времени расходуемая на отдых.
Для полуавтоматического режима работы оборудования а1 = 005.
Норма обслуживания литьевых машин составляет:
Топ =20005 = 400 мин.
Нобсл = (480 – 2 –20 – 5)(7 + 5 + 400) = 102
На обслуживание единицы оборудования приходится один человек.
На предприятии имеется три литьевых машины. Предприятие работает в три смены.
Производим расчёт численности литейщиков по нормам обслуживания по формуле:
Ч = (n*с*Ксп)Нобсл (5.3.)
где Ч – численность рабочих (списочный состав) чел.;
n – число единиц однотипного оборудования;
Ксп – коэффициент определения списочного состава;
Нобсл – норма обслуживания.
Списочная численность литейщиков составит:
Ч = (3*3*114)1 = 1026 (чел.)
Списочная численность литейщиков 10 человек.
Для обеспечения бесперебойной работы предприятия необходимы следующие кадры:
ИТР (главный механик начальник производства предприятия и электронщик);
вспомогательные рабочие (электрик слесарь контролёр наладчик (начальник смены) грузчик (дробильщик));
МОП (кладовщик уборщик).
Итого ИТР – 2 чел. вспомогательные рабочие – 8 чел. МОП – 2 чел. основных рабочих – 10 чел.
На основании приведённых расчётов составлен плановый график работы МОП ИТР и рабочих смен приведённый в Приложении 8
Основные строительные и компоновочные решения
1 Планировка помещений
Помещения производства делятся на помещения основного производства складские вспомогательные и обслуживающие (бытового социального назначения).
К производственным площадям предприятия относятся площади занятые производственным оборудованием заготовками деталями у рабочих мест и у оборудования проходами между оборудованием.
К вспомогательным площадям относятся площади инструментального и ремонтного хозяйства; складов предприятия и кладовых; помещений ОТК; прочих вспомогательных помещений: пожарных и магистральных проездов.
Исходя из состава помещения и строительных норм определены основные размеры строения (длина – 24 м ширина – 12 м высота – 72 м). Планировка помещений предприятия приведена в Приложении 9.
2 Компоновка технологического оборудования
При размещении оборудования необходимо учитывать следующие технологические требования: удобство обслуживания оборудования его демонтажа и ремонта; наиболее эффективное использование производственной площади и объёма; рациональное решение внутрицехового транспорта.
При планировке оборудования необходимо соблюдать строительные нормы правила техники безопасности и охраны труда санитарные и противопожарные нормы [7].
В соответствии с приведёнными нормами и требованиями произведена компоновка технологического оборудования которая приведена в Приложении 9.
3 Основные строительные решения
Устанавливаемые эксплуатационные качества здания санитарно-технический режим и пожарная безопасность должны обеспечивать максимально возможную экономичность проектных решений (СН и П 11-90-61 «Производственные здания промышленных предприятий. Нормы проектирования»).
Согласно СН и П 11-2-80 «Противопожарные нормы проектирования зданий и сооружений» помещения по переработке пластмасс в изделия относятся к категории В а по переработке отходов – к Б.
Согласно правилам устройства электроустановок (ПЭУ-78) класс основных помещений принимается П-IIа а переработки отходов – В-IIа.
При строительстве здания планируется применить унифицированные пролёты с сеткой колонн 6х6 метров и с высотой до низа несущей конструкции фермы 72 м.
Согласно СН 245-71 в состав бытовых помещений для производства по переработке пластмасс (класс IIn с улучшенной отделкой) входят гардеробные блоки душевые умывальные помещения и устройства местного обслуживания (санузлы устройства питьевого водоснабжения) с соответствующим оборудованием по числу рабочего персонала [8].
Электротехническая часть
1 Расчёт установленной и потребляемой мощности
Определим установленную мощность проектируемого электрооборудования и предприятия в целом.
Для расчёта потребления электроэнергии на технологические нужды (электропривод и электрообогрев) по соответствующим таблицам выбора оборудования определим мощность электродвигателей и нагревателей. Таким образом мы определим установленную мощность.
Исходными данными для расчёта потребляемой электроэнергии является:
N – общая установленная мощность электродвигателей и нагревателей (в кВт);
К – коэффициент загрузки электродвигателей и нагревателей (К = 07-08);
m – коэффициент полезного действия электродвигателей (m = 085);
Тэф – эффективный фонд времени работы оборудования ч.
Годовой расход электроэнергии Qгод (кВт·ч) определяется по формуле:
Qгод = N*Тэф*К*m (7.1.)
Qгод = N*Тэф*07*085 = N*Тэф*0595. (7.2.)
Результаты расчёта приведены в Приложении 11.
2 Освещение производственных помещений
В проектируемом предприятии предусматривается естественное и электрическое освещение.
Расчёт естественного освещения ведётся методом световой площади и глубины освещённости.
где Sо – площадь окон м²;
Sп – площадь пола м²;
F – световая площадь м² ( Sо : Sп = 16 значит Sо = Sп6.);
Общая площадь производственных помещений составляет 288 м².
Размеры выбранного окна ПГ-44 составляют 150х170 см значит площадь окна Fок = 255 м².
Тогда количество окон составит:
n = SоFок = 48255 = 188
Проектируем 19 окон.
Расчёт искусственного освещения ведём методом светового потока.
F = (Е*k*S*Z) (7.4.)
где F – световой поток каждой лампы лм;
Е – количество номинальной освещённости (Е = 25 лк);
k – коэффициент запаса (k = 13);
S – площадь помещений м²;
Z – отношение средней освещённости к минимальной (Z = 12).
Коэффициент даётся для различных светильников в функции отражения стен и потолка Sс и Sп и индекса помещений i. Sс и Sп = 50%
Индекс помещений вычисляется по формуле:
= i = S(n*(А + В)) (7.5.)
= i = 288(35*(15 + 115)) = 31 (7.6.)
Отсюда F = (25*13*288*12)31 =3623 лм.
По ГОСТ 2239-75 выбираем лампу ЛДЦ-80 со световым потоком Fп=266 лм.
Количество светильников составит:
n = FFп = 3623266 = 136
Годовой расход энергии на освещение 1 м² равен 15 кВт.
Отсюда Руст = Sп *15 = 288*15 = 4320 кВт (7.7.)
С учётом коэффициента запаса k = 15 установленная мощность составит:
Руст = 4320*15 = 6480 кВт
Количество светильников тогда будет:
N = n*15 = 136*15 = 204 20(7.8.)
С учётом коэффициента спроса по мощности k = 07 потребляемая мощность составит:
Рпотр = Руст*k = 6480*07 = 4536 кВт. (7.9)
Учитывая косинус угла φ и электрических потерь (соs φ = 095):
Рпотр = Рпотр095 = 4536095 = 47747 кВт. (7.10.)
Согласно СН и П II-А.8-72. На предприятии предусматривается аварийное освещение обеспечивающее безопасность эвакуации людей из помещений в случае аварии. Питание аварийного освещения осуществляется от независимого источника питания.
Годовой расход электроэнергии на аварийное освещение напряжением 36 В исходит из 15 Вт на 1 м² площади включая служебные и бытовые помещения.
3 Заземление и защита от статического электричества
Сопротивление заземляющих устройств должно быть не более 4 Ом.
В качестве заземляющих проводников и заземления используются строительные элементы здания.
Контуры заземления выполняются из полосовой стали.
Отвод зарядов статического электричества осуществляется путём заземления оборудования.
Согласно СН 305-69 проектируемое предприятие (здание предприятия) относится по молниезащите ко II категории для которой расчитывается зона защиты молниеотвода R и потребное количество молниеотводов n [7].
где hm – высота молниеотвода hm = 12*h м;
h – высота строения м;
L – длина строения м.
R = 15*12*9 = 162 м² ;
n = 24(2*162) = 07 1.
Проектируем один молниеотвод с зоной защиты 162 м².
5 Отопление и вентиляция
Отопление и вентиляция проектируемого предприятия рассчитывается в соответствии с СН и П II-33-76 по чертежам теплотехническим данным источника теплоснабжения количеству газо- пыле- и тепловыделения ПДК вредных веществ (СН245-71) метеоусловиям места расположения производства (СН и П II-А.6-72).
Для города Рыбинска : tпо – расчётная температура для проектирования отопления tпо = минус 25°С;
tпоср – средняя температура за отопительный период tпоср = минус 5°С;
tпв – расчётная температура для проектирования вентиляции tпв = минус 25°С;
n – продолжительность отопительного периода n = 198 сут.;
tср – средняя температура наружнего воздуха жаркого месяца tср =25°С.
5.1 Расчёт кратности воздухообмена
Процесс производства литьевых изделий сопровождается загрязнением воздушной среды производственных помещений предприятия вредными выделениями.
Негативно на самочувствии человека в жаркие месяцы сказывается повышенное теплообразование.
В процессе переработки полимеров выделяются окись углерода и непредельные углеводороды. Кроме того образуется пыль в результате дробления бракованных изделий.
Так как в год выделение летучих составляет 002 % от всего объёма перерабатываемого сырья (002 т.) то в рабочее время за один час будет выделяться 00000023 кг летучих.
Кратность воздухообмена определяется по формуле:
где W – объёмный расход воздуха отсасываемого из помещений м³ч.;
Vп – объём помещения м³.
W = g (Cg – Co) (7.14)
где g – количество вредных веществ выделяющихся в рабочее время за 1 час;
Cg – содержание вредных веществ в засасываемом воздухе;
Co – предельнодопустимая концентрация вредных веществ в воздухе Co = 0006 кг м³.
Cg Co Cg = 00000023(288*72) = 11*109
Следовательно для удаления вредных веществ вентиляцию проектировать нецелесообразно. Однако учитывая что средняя температура наружного воздуха жаркого месяца tср = 25°С объём помещения 20736 м³ и энергия тепла отдаваемая оборудованием составляет 81*104 кДж берём кратность воздухообмена К = 1.
Данный воздухообмен обеспечит благоприятную для работы температуру в помещениях максимально удалит вредные вещества из помещений. Согласно СН и П-33-76 к каждому материальному цилиндру литьевых машин должен быть проведён местный отсос.
На предприятии для подачи приточного воздуха применяется коллекторная система позволяющая осуществить равномерную раздачу воздуха по всей площади помещения.
5.2 Расчёт расхода теплоты на отопление вентиляцию тепла выделяемого оборудованием
Расчётный поток теплоты на отопление определяется по формуле:
Фот = о*Vн* (tвн – tпо) (7.16.)
где о – удельная относительная характеристика здания о = 06-11 Втм³;
Vн – наружный строительный объём здания м³;
tвн – проектируемая температура воздуха в помещениях tвн = 20°С;
tпо – расчётная температура для проектирования отопления tпо = минус 25°С.
Толщина наружных стен здания 05 м; высота фермы 18 м тогда наружный объём здания:
Vн = 25*13*9 = 2925 м³;
Фот = 1*2925*(20 – (–25)) = 131625 Вт.
Средний поток теплоты определяется по формуле:
Фотср = Фот*(tвн - tпоср )(tвн - tпо) (7.17.)
где tпоср – средняя температура отопительного сезона tпоср = минус 5°С для Рыбинска.
Фотср = 131625*(20 – (–5))(20 –(–25)) = 73125 Вт
Годовой расход теплоты на отопление определяется по формуле:
Qотг = 36*Фотср*m*((n – a)(2 *106)) (7.18.)
где n – продолжительность отопительного сезона в сутках;
а – сумма выходных и праздничных дней приходящихся на отопительный сезон а = 40 дней;
m – продолжительность работы предприятия в сутки m = 24 час.
Qотг = (36*73125*21*198)(2*106) = 6255 ГДжг = 1424 Гкалг
Расчётный поток теплоты на вентиляцию определяется по формуле:
Фв = q*Vвн*(tвн – tпв) (7.19.)
где q – удельная относительная характеристика здания q = 03-3 Вт м³;
Vвн – внутренний объём здания м³;
tпв – расчётная температура для проектирования вентиляции tпв = минус 25°С.
Фв = 25*20736*(2 – (–25)) = 139968 Вт
Фвср = Фв*(tвн – tпоср )(tвн – tпв) (7.20.)
Фвср = 139968*(20 – (–5))(20 – (–25)) = 1574640 Вт
Годовой расчёт теплоты на вентиляцию определяется по формуле:
Qвг = 36*Фвср*m*(n – a)(2 *106) (7.21.)
Qвг = (36*1574640*24*198)(2*106) = 134689 ГДжг = 3606 Гкалг
Мощность обогревателей основного оборудования Роб = 22500 Вт.
Годовой расход теплоты основным оборудованием определим по формуле:
Qобг = 36*Р*m*(n – a)(2*106) (7.22.)
где Р – мощность обогревателя Вт.
Qобг = (36*22500*24*198)(2 *106) = 1923 ГДжг
Количество тепла необходимое для поддержания оптимальной температуры на предприятии составит
Qнеобхг = Qотг + Qвг – Qобг (7.23.)
Qнеобхг = 6255 + 134689 – 1923 = 13902 ГДжг = 2048 Гкалг
Qнеобх = 139023234 = 42 ГДжг = 063 Гкалг
В качестве теплоносителя для отопления принимаем водяной пар: прямая линия - +15°С обратная - +70°С.
Для обеспечения обогрева приточного воздуха применим кондиционер КТЦ-3А-315 вырабатывающий 07 Гкал теплоты в час и создающий расход воздуха 4000 м³ч.
6 Водопровод и канализация
Внутренний водопровод здания проектируется в соответствии с СН и П II-170 а внутренняя канализация в соответствии с СН и П II 4-70.
Проектом предприятия предусматриваются внутренние магистрали водопровода и канализации предприятия.
Вода расходуется на санитарно хозяйственные производственные и противопожарные нужды.
Нормы потребления воды:
расход воды на санитарно-хозяйственные нужды qc-х = 45 л(чел*ч);
расход питьевой воды qпв = 2 м³(чел*ч);
расход воды на душевую сетку qдс = 666 л(чел*ч);
расход горячей воды qгв = 1 м³(чел*ч);
бытовая канализация qртех = 4 м³ч;
расход воды на внутреннее пожаротушение из пожарных гидрантов для производственных и бытовых помещений qпж = 10 лс.
Максимальный часовой расход на пожаротушение составит:
qрпож = 001*3600 = 36 м³ч.
Расход воды на технические нужды определяется из расчёта водопотребления технологическим оборудованием.
На основании этих данных расход воды на технические нужды составил:
Суммарный максимальный расход воды за час по предприятию составит:
qобщ = qc-х + qпв + qдс + qгв + qрпож + qртех + qрбк (7.24.)
qобщ = 0045 + 2 + 0666 + 1 + 36 + 17 + 4 = 45411 м³ч.
В соответствии с этим суточный расход воды составит 1089864 м³ годовой расход составит 272466 м³ (22266 м³ без учёта qрбк и qрпож и qртех).
В соответствии с требованиями к качеству воды и её количеству на предприятии предусматриваются три системы водоснабжения: водопровод хозяйственно-противопожарный водопровод производственный водопровод обратной воды.
Сеть производственной канализации грязных стоков отводит сточные воды по трём выпускам: по одному – в хозяйственно-фекальную по двум другим – в производственно-ливневые наружные сети канализации. Присоединение выпусков к городским сетям канализации осуществляется через масло- жиро- улавливатели.
7 Расход сжатого воздуха
Сжатый воздух необходим для обдувки пресс-форм во время работы основного оборудования.
На основании данных на единицу основного оборудования (литьевую машину) требуется 6 м³ воздуха в час при давлении 06 МПа .
Следовательно на литьевое производство предприятия необходимо 18 м³ч.
Годовая потребность в сжатом воздухе составляет 108000 м³ при давлении 06 МПа.
Таким образом определены основные санитарные электротехнические данные проектируемого предприятия. Потребляемая мощность предприятия составляет 476637 кВтч. Отопление воздушное совмещено с приточной вентиляцией. Расход воды в год составляет 22266 м³. Расход сжатого воздуха в год составляет 108000 м³.
БЕЗОПАСНОСТЬ ЖИЗНЕДЕЯТЕЛЬНОСТИ
Охрана окружающей среды техника безопасности промсанитария и пожарная безопасность.
1 Охрана окружающей среды
Воздух удаляемый при помощи системы местных отсосов и общеобменной вентиляции из отделений литья и переработки отходов содержит вредные пары и газы (формальдегид уксусная кислота оксид углерода).
Однако в связи с большими объёмами удаляемого воздуха и низкой концентрации в нём вредностей в большинстве случаев проектирование очистки нерационально. Загрязнения содержащиеся в вентиляционных выбросах рассеиваются в атмосфере. Выхлопные трубы систем местных отсосов должны быть подняты выше зоны аэродинамической тени и снабжены устройствами для создания факельного выброса.
Воздух удаляемый от станков механической обработки отходов изделий перед выбросом в атмосферу должен подвергаться очистке. Воздух удаляемый от токарных фрезерных сверлильных и других станков очищается в сухих циклонах; от полировальных станков – в сетчатых фильтрах. Вместо батарейных циклонов могут быть применены рукавные фильтры.
На предприятии имеется канализация благодаря которой не загрязняются почва и грунтовые воды [4].
2 Техника безопасности
Основные опасности при работе на литьевом предприятии: электроопасность термоопасность опасность механического травмирования.
На предприятии должен быть организован трёхступенчатый контроль техники безопасности.
На предприятии должны быть инструкции по охране труда для работников предприятия.
Для профилактики травм и защиты труда литейщиков на производстве должны быть приняты следующие меры: регулярно проводится технические осмотры машин работающий на предприятии персонал должен иметь спецодежду спецобувь.
Литьевые машины оборудованы специальными устройствами обеспечивающими безопасность работы при соблюдении правил их эксплуатации (дверцы защитные клапаны заземление и др.).
3 Промсанитария и пожарная безопасность
На производстве имеются: душевое отделение туалет кухня бытовая комната. Есть отопление. Все помещения убираются уборщиком.
Вблизи от огнеопасных объектов должны быть оборудованы пожарные щиты укомплектованные огнетушителями ящиками с песком лопатами вёдрами и другими необходимыми инструментами. Кроме пожарных щитов на предприятии должны быть пожарные гидранты [6].
Расчет технико-экономических показателей проектируемого предприятия
Основными задачами данной части проекта являются расчёт технико-экономических показателей установление экономической целесообразности и хозяйственной необходимости организации предприятия расчёт эффективности его действия.
Решение этих задач осуществляется путём расчёта программ производства арендных ставок на используемые здания и сооружения стоимости используемого оборудования сырья и материалов топлива и энергии затрат и отчислений на социальное страхование амортизацию оборудования расходов предприятия [1].
1 Организация поставок сырья программа производства и режим работы предприятия
Предполагается что поставка АБС-пластика марки HG-0760AT («Samsung Chemicals» - Южная Корея) на предприятие будет производиться через Компанию "ЮМСК" г.Москва. Поставка сырья на предприятие осуществляется начальником снабжения предприятия по заявке начальника производства предприятия. Стоимость сырья указана в таблице 9.5. Прибывшее сырьё складируется на территории склада готовой продукции.
Согласно заданию на проектирование годовая мощность предприятия литья пластмасс составляет 100 тонн изделий в год.
График переработки сырья литьевыми машинами приведён в таблице 9.1.
График переработки сырья литьевыми машинами чгод.
Порядковый номер машины
Вертикальные и горизонтальные жалюзи
Режим работы предприятия:
- рабочая неделя с двумя выходными;
- количество смен в сутки – 3 по 8 часов;
- средняя продолжительность рабочей недели – 40 час;
- номинальный фонд рабочего времени составляет 250 рабочих дней;
- количество праздничных и выходных дней – 115.
2 Аренда производственных площадей
Предполагается что проектируемое предприятие заключит договор аренды – договор по которому арендодатель (наймодатель) обязуется предоставить арендатору (нанимателю) имущество за плату во временное владение и пользование или во временное пользование.
Таким образом общая стоимость аренды производственных площадей проектируемого предприятия составит 1200 руб х 288 м2 =345600 рубгод.
3 Стоимость оборудования
Договорная цена на основное технологическое оборудование расчёт его общей стоимости приведены в Приложении 13.
Суммарная стоимость оборудования составляет 3745725 руб.
Общая величина затрат на технологическое оборудование определяется как сумма затрат на основное технологическое оборудование КИП и средства автоматизации прочее оборудование.
К сметной стоимости оборудования суммируются транспортные расходы заготовительно-складские затраты стоимость запчастей. Эти затраты определяются суммарно в размере 5 % от стоимости всего оборудования и составляют 187286 рублей.
Проект стоимости монтажа оборудования и КИП спецработ по укрупнённым нормативным показателям в процентах от стоимости оборудования транспортных заготовительно-складских затрат затрат на запчасти приведён в таблица 9.3.1.
Стоимость монтажа оборудования КИП и пусконаладочных работ
Норма от стоимости оборудования %.
Стоимость работ руб.
Монтаж оборудования и КИП
Пусконаладочные работы
На основании приведённых расчётов определяется общая итоговая стоимость оборудования. Расчёт приведён в таблице 9.3.2.
Итоговая стоимость оборудования
Прейскурантная стоимость
Транспортные заготовительно-складские расходы на запчасти
Стоимость монтажных и пусконаладочных работ
Общие капитальные затраты по проектируемому предприятию определяются затратами на строительные работы и приобретение оборудования расчёт суммы данных затрат приведён в таблице 9.3.3.
Капитальные затраты по предприятию литья пластмасс
Наименование расходов
Стоимость аренды производственных площадей в год
Итого капитальные затраты
4 Вопросы труда и заработной платы
4.1 Расчёт фонда заработной платы рабочих
Расчёт фонда заработной платы для основных и вспомогательных рабочих производится отдельно в связи с тем что заработная плата основных производственных рабочих учтена в прямых затратах а вспомогательных рабочих связанных с обслуживанием технологического оборудования – в смете затрат на содержание текущий ремонт и эксплуатацию оборудования.
Вспомогательных рабочих подразделяют на две группы:
рабочие по уходу и надзору за технологическим оборудованием (контролёр водитель-грузчик наладчик) заработная плата которых включена в одну смету расходов по содержанию и эксплуатации оборудования;
рабочие по текущему ремонту оборудования (слесарь электрик) заработная плата которых входит в состав расходов по текущему ремонту оборудования.
ИТР и МОП заработная плата данных рабочих учтена в смете затрат расходов предприятия.
Тарифный фонд заработной платы определяется по формуле:
Зт = Зтч*Чсп*Тэф (9.1.)
где Зтч – часовая тарифная ставка рабочего;
Чсп – списочная численность рабочих;
Тэф – эффективный фонд рабочего времени.
Дополнительная заработная плата взята в размере 12% от суммы тарифной зарплаты. Расчёт годового фонда заработной платы рабочих приведён в Приложении 12.
Годовой фонд заработной платы основных рабочих составляет 1900800 руб. рабочих по уходу и надзору за оборудованием 948816 руб. рабочих по текущему ремонту оборудования 340560 рублей.
4.2 Расчёт фонда заработной платы ИТР и МОП
Расчёт фонда заработной платы ИТР и МОП производится на основании схемы должностных окладов по отраслям промышленности. Согласно схемы предприятие литья пластмасс относится к первой группе по оплате труда ИТР и МОП.
Расчёт фонда заработной платы персонала предприятия приведён в Приложении 12 и составляет 957600 рублей.
5 Расчёт заготовительных цен на сырьё материалы и энергию а также себестоимости продукции
Оптовые цены за сырьё материалы и энергию
Сырьё материалы энергия
Теплота (водяной пар)
Масло гидравлическое
Проектная себестоимость продукции определяется по калькуляции на основании расчётов в предыдущих разделах данного проекта.
Исходными данными для расчёта являются:
капитальные затраты по проектируемому предприятию;
нормы расхода сырья и материалов энергии и планово-заготовительные цены;
годовой фонд заработной платы работающих;
сметы расходов предприятия и расходов на содержание и эксплуатацию оборудования.
6 Расчёт амортизационных отчислений
Отчисления на амортизацию здания включается в смету расходов предприятия отчисления на амортизацию оборудования – в смету расходов на содержание и эксплуатацию оборудования. Расчёт амортизационных отчислений на здание и оборудование приведён в таблице 9.6.
Расчёт амортизационных отчислений по основным фондам литьевого предприятия
Стоимость основных фондов руб.
Сумма амортизации руб.
Примечание: 1. стоимость оборудования берём с учётом стоимости монтажа; 2. Нормы амортизации взяты по данным действующих предприятий.
7 Смета расходов предприятия и на содержание и эксплуатацию оборудования
Смета расходов предприятия приведена в таблице 9.7.1.
Смета расходов предприятия
Заработная плата ИТР и МОП (с учётом премий)
Отчисления на соцстрахование (8 % от статьи 1)
Расход на охрану труда (5% от заработной платы)
Итого по статьям 1-3
Прочие расходы предприятия (5% от расходов статей1-6)
Итого расходы предприятия
Смета расходов на содержание эксплуатацию оборудования приведена в таблице 9.7.2.
Смета расходов на содержание и эксплуатацию оборудования
Расходы на содержание и эксплуатацию оборудования:
зарплата рабочих по уходу и надзору за оборудованием
смазочные и обтирочные материалы
Текущий ремонт оборудования
зарплата рабочих по текущему ремонту оборудования
текущий ремонт оборудования (5% от его стоимости)
Амортизация оборудования
8 Проектная калькуляция себестоимости продукции
Калькуляцию себестоимости продукции ведём из расчёта на 1 тонну готовой продукции.
Калькуляция себестоимости приведена в Приложении 14.
Анализ структуры себестоимости продукции показывает что основные затраты приходятся на сырьё и материалы то есть производство является материалоёмким.
Оценка экономической эффективности проектируемого предприятия ведётся по - следующим основным показателям:
- уровень рентабельности производства;
- срок окупаемости капитальных вложений;
- коэффициент эффективности капитальных вложений;
- удельные капитальные вложения.
Цена за 1 тонну изделий из АБС-пластика HG-0760AT ЦАБС = 13820457 р.т.;
Условно годовая прибыль предприятия определяется по формуле:
П = (Ц – С) * В (9.2.)
где П – прибыль руб.;
Ц – цена продукции руб.т.;
С – себестоимость продукции р.т.;
В – количество выпускаемой продукции в год т.
ПАБС=(186500-13820457)*100=4830000 руб
Общую прибыль предприятия составляет ПАБС=4830000 руб
Налог от прибыли составляет 18%. Чистая прибыль предприятия:
Пч = 4830000 *082 = 3960600 руб.
Уровень рентабельности проектируемого производства определяется по формуле:
R = 100%*Пч(Сопф + Соб) (9.3.)
где Сопф – стоимость основных производственных фондов руб.;
Соб – стоимость оборотных фондов руб.
R = 3960600 *100(4830000 + 3960600) = 4505%
Срок окупаемости капитальных вложений определяется по формуле:
Т = 44882683960600= 113 лет
Коэффициент общей эффективности капитальных вложений являются обратной срока окупаемости и определяется по формуле:
Экп = 39606004488268 = 088
Фондоотдача предприятия определяется по формуле:
Ф = СпродСопф (9.5.)
где Спрод – стоимость годовой программы выпускаемой продукции руб.
Ф = 39606004830000= 082 руб.руб.
9 Расчет удельных капитальных вложений и производительности труда
Удельные капитальные вложения (УКВ) определяются по формуле:
где Кп – капитальные затраты на промышленное строительство руб;
Мп – проектная мощность т.
УКВ = 4488268100 = 4488268 руб.т.
Расчет производительности труда приведен в таблице 9.8.1
Расчет производительности труда
Производственная программа
Производительность труда
В натуральном выражении т.
В стоимостном выражении руб.
На одного работающего
10 Основные технико-экономические показатели предприятия
На основании расчётов приведённых в технологической и экономической частях проекта составляется сводная таблица основных технико-экономических показателей проектируемого предприятия. Данные приведены в Приложении 27.
Разработана технологическая часть эскизного проекта предприятия по производству пластиковых аксессуаров для систем вентиляции и кондиционирования методом литья под давлением мощностью 100 тонн в год.
Произведён выбор номенклатуры выпускаемой продукции (решетки тройники адаптеры демпферы) рассчитаны производственная программа и потребное количество материалов для ее выполнения (АБС-пластик).
Произведены обоснование и выбор способа изготовления изделий (литьё под давлением).
Разработана технологическая схема производства литьевых изделий. Основное оборудование работает в полуавтоматическом режиме.
Произведён выбор технологического оборудования и расчёт потребности в нём. На предприятии установлены литьевые машины марки Sandretto Nove HP 750900 Sandretto Nove HP 13001650 и Sandretto Nove HP 23003000 итальянского производства а также вспомогательное оборудование:
- измельчитель типа ИПР-150М отечественного роизводства
- чиллер производства "Shini" (Тайвань) модель XC-05ACI
- вакуумный загрузщик полимерного сырья производства "Shini" (Тайвань) серия SAL "EURO" модель SAL-1.5U.
- бункер-сушилка производства "Shini" (Тайвань) cерия SHD 20-U "EURO
Списочная численность рабочих и персонала предприятия составляет: основных рабочих - 10 человек вспомогательных – 7 человек ИТР – 4 человека МОП – 2 человека.
Произведена планировка помещений и компоновка технологического оборудования. Здание занимает площадь 288 м² и объём 20736 м³.
Годовой расход электроэнергии на предприятии составляет 6758792 кВт·ч; воды – 272466 м³; сжатого воздуха (06 МПа) – 144000 м³; тепла на отопление и вентиляцию – 2048 Гкал.
Ориентировочные капитальные вложения составляют 4488268 руб. Годовая прибыль предприятия равна 3960600 руб. Уровень рентабельности предприятия 4505% срок окупаемости капитальных вложений составляет 113 лет. Коэффициент эффективности капитальных вложений 088.
СПИСОК ИСПОЛЬЗОВАННЫХ ИСТОЧНИКОВ
Оленев В. А. Мордкович Е. Н. Проектирование производств по переработке пластмасс- М.: Химия 1982 - 334 с.
Торнер Р. В. Оборудование заводов по переработке пластмасс–М.: Химия 1986 - 464 с.
Бортников В. Г. Основы технологии переработки пластических масс- Л.: Химия 1983 – 304 с.
Завгородний В.К. Оборудование предприятия по переработке пластмасс- Л.: Химия 1987 – 596 с.
Кацнельсон М. Ю. Балаев Г. А. Пластические массы. Свойства и применение Справочник - М.: Химия 1978 – 567 с.
Стандарт предприятия ОТП-1-82- Саратов.: СВВИУХЗ 1983 – 120 с.
Общесоюзные нормы технологического проектирования производств по переработке пластмасс- М.: Гипропласт 1985 – 167 с.
Каталог справочник по технологической оснастке- М.: НИИТЭ 1968 – 245 с.
"Производство изделий из полимерных материалов" Профессия 2004
ЭТО ПРИЛОЖЕНИЯ для варианта № 5.doc
Наименование показателя
Прочность при растяжении МПа
Прочность при изгибе МПа
Модуль упругости МПа
Ударная вязкость по Изоду 14" (надрезом) Джм
Ударная вязкость по Изоду 18" (надрезом) Джм
Твердость по Роквеллу R-шкала
Термические свойства АБС-пластика марки HG-0760AT ГОСТ 12271-76
Температура начала деформации при 182 МПа °С
Температура размягчения по Вика при 5 кгсм2 °С
Физические свойства АБС-пластика марки HG-0760AT ГОСТ 12271-76
Плотность при 23 °С гсм3
Водопоглощение за 24 ч в воде при 23 °С %
Показатель текучести расплава при 220 °С г10 мин
Степень стойкости к горению
Технические характеристики литьевых машин
Давление впрыска кгсм2
Теоретический объем впрыска см3
Масса впрыска (Полистирол) г
Скорость впрыска см3сек
Скорость вращения шнека обмин
Усилие смыкания тонн
Размер между колоннами мм
Максимальное раскрытие плит мм
Минимальная высота пресс-формы мм
Максимальная высота пресс-формы мм
Усилие эжектора тонн
Мощность нагревателей кВт
Мощность электромоторов кВт
Общее энергопотребление кВт
Сухая масса машины тонн
Размеры машины (дл.шир.выс.) мм
Прохождение воды лмин
Перечень элементов оперативного времени операторов (литейщиков) при работе оборудования в автоматическом режиме
Элементы оперативного времени
Повторяемость в смену
Форма с отрывом литника при размыкании
Форма с пальчиковым литником
Общее наблюдение за работой оборудования
Контроль параметров технологического процесса
Контроль качества изделий
Совмещён с удалением литника
Контроль количества сырья в бункере машины и подключение местного пневмотранспорта
Удаление литников вручную
Удаление литников и контроль качества изделий
Счёт укладка изделий в тару (при укладке в насыпь)
Подготовка тары для упаковки
Счёт и укладка изделий в тару (при упорядоченной укладке)
Прокладка рядов изделий бумагой
Подготовка прокладочной бумаги
Заполнение сертификата и укладка его в тару
Вынос упакованной продукции к месту отбора
Перемещение литейщика при обслуживании одной машины
Примечания: 1. n1- число циклов в смену; n2- число едениц тары в смену; T1- затраты времени на удаление литников и контроль качества изделий; Т2- то же на счёт и укладку изделий в тару; 2. значения n1 n2 T1 и Т2 определяются для каждого конкретного изделия; 3. приведены затраты времени на прокладку рядов изделий бумагой приходящиеся на еденицу тары.
Типовой профессионально-квалификационный состав рабочих производств литьевых изделий
Распределение рабочих по разрядам
Производственные рабочие
Аппаратчик смешивания
Вспомогательные рабочие
Наладчик литьевых машин
Слесарь-электрик по ремонту электрооборудования
Слесарь по КИП и автоматике
Уборщик производственных помещений
Карта обслуживания рабочего места
Функции обслуживания средств труда и предмета труда
Исполнители функций обслуживания
Виды самообслуживания
Производственно - подготовительная
Главный механик слесарь электрик
Телефонная и личная связь
Наладчик слесарь электрик
Ремонтно-инструментальный цех
Устранение неполадок
Транспортно-складская
Хозяйственно-бытовая
Энергетическая служба
Плановый график работы ИТР МОП и рабочих предприятия
Наименование профессии
Количество в первую сменучел.
Количество во вторую смену чел.
Количество в треью смену чел
Явочная численность чел.
Списочная численность чел.
Инженерно-технические работники
Начальник производства
Зам. начальника производва
Младший обслуживающий персонал
Расчёт установленной мощности электрооборудования
Наименование оборудования
Количество по проекту
Суммарная мощность нагревателей кВт
Суммарная мощность электродвигателей кВт
Эффективный фонд времени работы оборудования ч
Годовой расход электроэнергии кВт·ч
Sandretto Nove HP 750900
Sandretto Nove HP 13001650
Sandretto Nove HP 23003000
Измельчитель XFS-180G-A
Вакуумный загрузчик SAL-1.5 U
Упаковочная машина “Унилак-Рапид”
Станок мех. Обработки
Газодувка пневмотранспорта
Расчёт стоимости строительства зданий
Строительная площадка
Стоимость строительных работ
Стоимость санитарно-технических и электромонтажных работ тыс. руб.
Общая стоимость сантехнических и электромонтажных работ тыс. руб.
Сметная стоимость строительства здания тыс. руб.
Отопление и вентиляция тыс. руб
Водопровод и канализация тыс. руб.м²
Электромонтаж тыс. руб.м²
Производ-ственный корпус
Расчёт фонда заработной платы рабочих
Продолжительность рабочего дня ч
Списочная численность
Часовая тарифная ставка руб.ч.
Тарифный фонд заработной платы руб.
Фонд дополнительной заработной платы руб.
Годовой фонд заработной платы руб.
Вспомогательные рабочие по Т.Р.
Вспомогательные рабочие по уходу и надзору за оборудованием
Водитель-резчик (дробильщик)
Стоимость оборудования
Единицы оборудования руб.
Проектного количества оборудования руб.
Подвесная кран-балка
Бункер для хранения сырья
Станок мех. обработки
Упаковочная машина “Унипак-Рапид”
Вентилятор для вытяжной вентиляции
Калькуляция себестоимости 1 т. отливок изделий из АБС-пластика марки HG-0760AT
Цена за единицу руб.
Расход по статье на 1 т. литьевых изделий
Гидравлическое масло
–сжатый воздух (06 МПа)
Затраты на оснастку пресс-форм
Зарплата основных рабочих
Расходы на содержание и эксплуатацию оборудования
Итого себестоимость предприятия
Себестоимость предприятия за вычетом затрат на материалы
Общие расходы с ПМ (10% от статьи 8)
Итого себестоимость ПМ
Внепроизводственные расходы (2% от статьи 10)
Налоги (356% от ФЗП)
Полная себестоимость
Стоимость сырья материалов и энергоресурсов.
Сырьё материалы энергия
Теплота (водяной пар)
Масло гидравлическое
Типы решеток тройников адаптеров и демпферов по ТУ 4863-002-44911369-10
Конструктивные характеристики решетки
Пластмассовая вентиляционная решетка состоящая из рамки в которой фиксируются вертикальные и горизонтальные поворотные жалюзи
Пластмассовая вентиляционная решетка состоящая из решетчатой вставки с наклонно расположенными направляющими жалюзи шаг 19 мм под углом 300 по направлению вниз рамки с фиксирующими элементами и листа оконной сетки
Пластмассовая вентиляционная решетка состоящая из цельнолитых деталей с наклонно расположенными направляющими жалюзи шаг 19 мм под углом 300 по направлению вниз которые соединены между собой посредством шипового соединения тип "шип-паз
Пластмассовый вентиляционный тройник состоящий из двух цельнолитых деталей которые соединены между собой посредством шипового соединения тип "шип-паз
Пластмассовый адаптера для вентиляционных решеток типа представляет собой цельнолитую деталь которая имеет присоединительный размер к решетке и присоединительный размер для воздуховодов
Пластмассовый вентиляционный модульный демпфер состоящий из двух цельнолитых деталей которые соединены между собой посредством шипового соединения тип "шип-паз" и поворотной заслонки зафиксированной между двумя внешними деталями демпфера
Основные размеры параметры и обозначения решеток типа ASGC соответствующих ТУ 4863-002-44911369-10
Примечания: 1. Коэффициент “живого сечения” - отношение свободной площади проема решетки для прохода воздуха к габаритной площади проема.
Основные размеры параметры и обозначения решеток типа ARGWF соответствующих ТУ 4863-002-44911369-10
Масса (справочная) кг
Основные размеры параметры и обозначения решеток типа ARGWO соответствующих ТУ 4863-002-44911369-10
Основные размеры параметры и обозначения тройников типа ATE соответсятвующих ТУ 4863-002-44911369-10
Присоединительные размеры мм
Основные размеры параметры и обозначения адаптеров типа AADS соответствующих ТУ 4863-002-44911369-10
Присоединительные размеры воздуховода d=мм
Основные размеры параметры и обозначения демпферов модульных типа DM соответствующих ТУ 4863-002-44911369-10
Присоединительные размеры d=мм
Перечень оборудования и приборов используемых для контроля качества продукции согласно ТУ 4863-002-44911369-10
Технические характеристики
Стандарты или технические условия
ТУ 2-034-0221197-011-91
Объем испытаний проводимых согласно ТУ 4863-002-44911369-10
Необходимость проведения испытаний (проверки)
При приемо-сдаточных испытаниях
При периодических испытаниях
Проверка конструкции на соответствии КД
Проверка качества внешнего вида
Проверка качества оконной сетки
Испытание на теплостойкость
Проверка индивидуальной упаковки
Проверка маркировки транспортной тары
Примечание: Знак “+” означает что испытания (проверки) проводятся знак “-” - не проводятся.
Перечень нормативных документов на которые даны ссылки в технических условиях ТУ 4863-002-44911369-10
№ пункта ТУ в котором
ССБТ. Общие санитарно-гигиенические требования к воздуху рабочей зоны.
ССБТ. Процессы производственные. Общие требования безопасности.
ССТБ. Системы вентиляционные. Общие требования.
ССБТ. Оборудование производственное. Общие требования безопасности.
ССБТ. Пожарная безопасность. Общие требования.
Система разработки и постановки продукции на производство. Испытания и приемка выпускаемой продукции.
Штангенциркули. Технические условия.
Картон гофрированный. Общие технические условия.
Плиты поверочные и разметочные. Технические условия.
Лента клеевая на бумажной основе.
Пленка полиэтиленовая термоусадочная. Технические условия.
«Методические указания » Минздрав СССР №2158-80 от 28.04.80
Расчёт фонда заработной платы управленческого и обслуживающего персонала
Категория работающих
Количество работающих
Полный годовой фонд заработной платы руб.
Зам. начальника производства
Основные технико-экономические показатели предприятия.
Годовой выпуск продукции
в натуральном выражении т.
в стоимостном выражении руб.
Полная себестоимость всей продукции руб.
Списочная численность работающих
Ориентировочные капитальные вложения руб.
Себестоимость 1 т. изделий руб. из АБС-пластика :
Съём продукции с 1 м² производственной площади руб.
Выпуск продукции на одного работающего
в в стоимостном выражении руб.
Удельные капитальные вложения на 1 т. руб.
Удельные нормы расхода на единицу мощности (1 т.)
сжатый воздух (06 МПа) м³
Годовая прибыль цеха руб.
Уровень рентабельности %
Срок окупаемости капитальных вложений лет
Коэффициент общей эффективности капитальных вложений
Термопластавтомат. Основные узлы и детали.
СПЕЦИФИКАЦИЯ ОБОРУДОВАНИЯ
НАИМЕНОВАНИЕ ОБОРУДОВАНИЯ
Подшипники линейного скольжения
Заглушка колонны зажима
Поршень выталкивателя
Поршень впрыска (шпиндель)
Кожух цилиндра экструдера
Опора цилиндра экструдера
Шнек с вращательно-поступательным движением
Ленточные нагревательные элементы
Задвижка бункера питателя
Запорный клапан сопла (опция)
Технологическая схема производства пластиковых аксессуаров для систем вентиляции и кондиционирования методом литья под давлением
Бункер для гранул АБС-пластика
Пропорциональный дозатор двухкомпонентного сыоья (дозирующий миксер двойной смеситель пропорциональный клапан) модель SPV-15
Вакуумный автозагрузчик сырья модель SAL-1.5U
Бункер-сушилка модель SHD 20-U "EURO
Термопластавтомат SANDRETTO модель NOVE HP 7509000
Термопластавтомат SANDRETTO модель NOVE HP 13001650
Термопластавтомат SANDRETTO модель NOVE HP 23003000
Дробилка модель XFS-180G-A
Водоохладитель (чиллер) для молдингов модель XC-05ACI
Бункер-тележка для транспортировки готовой продукции
Решетка вентиляционная пластиковая серия ASGC 1122
СПЕЦИФИКАЦИЯ ОБОРУДОВАНИЯ
Основной вид решетки ASGC 1122
Жалюзи вертикальная (проекция)
Жалюзи горизонтальная
Жалюзи горизонтальная (проекция)
Тяга вертикальная (проекция)
Тяга горизонтальная (проекция)
Компоновка оборудования цеха по производству пластиковых аксессуаров для систем вентиляции и кондиционирования методом литья под давлением.
Отдел отбраковки сборки комплектациии упаковки продукции
Склад готовой продукции
Ремонтно-механическая мастерская
Приточно-вытяжная вентиляционная установка с рекуперацией
02 ТЕХНОЛОГИЧЕСКАЯ СХЕМА ПРОИЗВ.dwg

СПЕЦИФИКАЦИЯ ОБОРУДОВАНИЯ
Ввод воды с молдингов
Выход воды на молдинги
Бункер-тележка для транспортировки готовой продукции
НАИМЕНОВАНИЕ ОБОРУДОВАНИЯ
Бункер для гранул АБС-пластика
Пропорциональный дозатор двухкомпонентного сыоья (дозирующий миксер
пропорциональный клапан) модель SPV-15
Вакуумный автозагрузщик сырья
модель SHD 20-U "EURO"
Термопластавтомат SANDRETTO
модель NOVE HP 7509000
модель NOVE HP 13001650
модель NOVE HP 23003000
Водоохладитель (чиллер) для молдингов
04 ЦЕХ компоновка оборудования.dwg

Внутренний блок канального типа FDX100 DAIKIN
План кондиционирования воздуха на базе DAIKIN.
Архитектурная мастерская
СХЕМА-ПЛАН 3-ГО ЭТАЖА
Наружный блок RMX140J - 2DAIKIN
Наружный блок R100 DAIKIN
Кабинет 2. Коридор 3. Лифт 4. Лестница 5. Переговорная
Санузел 7. Кухня 8. Венткамера 9. Пост охраны 10. Электрощитовая
Копир 12. Комната уборщиц
Точное месторасположение кондиционера уточняется при монтаже.
Монтаж систем кондиционирования вести в соответствии со СНиП 3.05.01-85.
Монтаж систем кондиционирования вести согласно рекомендациям производителей оборудования
с учетом коммуникаций ВК
электроснабжения и освещения.
После проведения монтажных работ проверить систему отвода дренажа на герметичность.
Уровни прокладки трубопроводов уточняются по месту с учетом существующих коммуникаций.
Отметка установки кондиционера не должна быть ниже отметки точки подключения
указанной на чертеже или предусмотреть установку у кондиционера дренажного насоса.
Коммуникации опускаются на 1 этаж
С О Г Л А С О В А Н О
Компоновка оборудования цеха по производству пластиковых аксессуаров для систем вентиляции и кондиционирования методом литья под давлением
Термопластавтомат SANDRETTO NOVE HP 13001650
Термопластавтомат SANDRETTO NOVE HP 750900
Термопластавтомат SANDRETTO NOVE HP 23003000
Сушильный бункер с автозагрузщиком
комплектациии упаковки продукции
Склад готовой продукции
Ремонтно-механическая мастерская
Приточно-вытяжная вентиляционная установка с рекуперацией
Вакуумный автозагрузщик сырья
03 ТПА термопластавтомат.dwg
Внутренний блок канального типа FDX100 DAIKIN
План кондиционирования воздуха на базе DAIKIN.
Архитектурная мастерская
СХЕМА-ПЛАН 3-ГО ЭТАЖА
Наружный блок RMX140J - 2DAIKIN
Наружный блок R100 DAIKIN
Кабинет 2. Коридор 3. Лифт 4. Лестница 5. Переговорная
Санузел 7. Кухня 8. Венткамера 9. Пост охраны 10. Электрощитовая
Копир 12. Комната уборщиц
Точное месторасположение кондиционера уточняется при монтаже.
Монтаж систем кондиционирования вести в соответствии со СНиП 3.05.01-85.
Монтаж систем кондиционирования вести согласно рекомендациям производителей оборудования
с учетом коммуникаций ВК
электроснабжения и освещения.
После проведения монтажных работ проверить систему отвода дренажа на герметичность.
Уровни прокладки трубопроводов уточняются по месту с учетом существующих коммуникаций.
Отметка установки кондиционера не должна быть ниже отметки точки подключения
указанной на чертеже или предусмотреть установку у кондиционера дренажного насоса.
Коммуникации опускаются на 1 этаж
С О Г Л А С О В А Н О
СПЕЦИФИКАЦИЯ ОБОРУДОВАНИЯ
Термопластавтомат. Основные узлы и детали.
НАИМЕНОВАНИЕ ОБОРУДОВАНИЯ
Подшипники линейного скольжения
Заглушка колонны зажима
Поршень выталкивателя
Поршень впрыска (шпиндель)
Кожух цилиндра экструдера
Опора цилиндра экструдера
Шнек с вращательно-поступательным движением
Ленточные нагревательные элементы
Задвижка бункера питателя
Запорный клапан сопла (опция)
Выступление.doc
Выбор темы для моего дипломного проекта не случаен. В настоящее время в России можно говорить о настоящем строительном буме и как следствие этого и о высокой востребованности в строительно-отделочных материалах.
Одной из высокодоходных товарных групп материалов необходимых при ремонте и отделке как жилых так и офисных помещений являются вентиляционные системы.
В данном проекте я попытаюсь предложить рынку продукцию пользующуюся огромной популярностью как у конечных потребителей так и у профессионалов. (снабженцев специализированных проектно-монтажных организаций и строительно-монтажных).
благодаря выгодному соотношению ценакачество товаров особым потребительским эксплуатационным а также технической продуманности изделий.
Одна из выпускаемых номенклатурных позиций показана на чертеже
Размещение производства
Предполагается что проектируемое производство будет размещено на имеющихся площадях одного из предприятий г.Рыбинска Ярославской области исходя из следующих предпосылок:
- наличие на предприятии энергоснабжения
- электро- и водоснабжения
- близость федеральных трасс и наличие железнодорожной ветки
Выбор метода производства и сырья
В связи с тем что номенклатура аксессуаров изготавливается из термопластичных материалов то наиболее приемлемым способом формования изделий является: литьё под давлением
Литьё под давлением – это один из основных метод переработки полимерных материалов и получения изделий заключающийся в пластикации и гомогенизации полимерного материала в экструдере впрыске его в предварительно замкнутую форму которая затем охлаждается расплав заполнивший форму затвердевает после чего форма раскрывается и изделие выталкивается из формы при этом мы получаем практически готовую деталь..
Причём с достаточно высокой точностью и стабильностью размеров.
Предполагается что предприятие будет использовать для производства продукции АБС-пластик марки HG-0760AT («Samsung Chemicals» - Южная Корея).
Данное сырьё было выбрано исходя из:
- сравнительно низкой стоимости
- простоты его переработки;
- отсутствия при переработке выделения токсичных веществ выше предельно ПДК
- универсальности при изготовлении изделий;
- оптимальных физико-механических прочностных и эксплуатационных свойств;
Данный АБС-пластик характеризуется высочайшим уровнем экологической безопасности и сертифицирован в России вплоть до контактного применения с пищевыми продуктами.
Конкурентными преимуществами также являютя:
- Цвето и светоустойчивость. (Продукция останется неизменно белого цвета на протяжении всего срока службы)
- Температура эксплуатации изделий от -40° до +50° С
Данный АБС-пластик предназначен для производства корпусов кондиционеров вентиляторов стиральных машин электропылесосов и т.д.
Схема технологического процесса производства состоит из следующих основных стадий.
- растаривание сырья;
- формование изделий;
- контроль и упаковка;
- хранение готовой продукции;
- переработки отходов.
На предприятии планируется организовать как общеобменную приточно-вытяжную вентиляцию так и местные вытяжные зонты непосредственно над ТПА.
Кроме основного производственного помещения и склада будут предусмотрены : комната отдыха Кухня-столовая СУ Ремонтно-механическая мастерская лаборатория кабинет ИТР Склад форм. Это показано на графическом приложении
Технико-экономические показатели предприятия отражены в таблице.
Благодарю вас за внимание. Готов отвечать на все ваши вопросы.
Рекомендуемые чертежи
- 30.03.2024
- 24.01.2023
- 25.01.2023