Проект организации службы технической диагностики механического оборудования стана 390




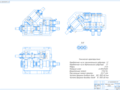
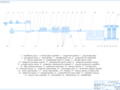
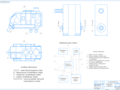
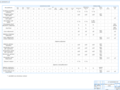
- Добавлен: 25.01.2023
- Размер: 7 MB
- Закачек: 0
Описание
Состав проекта
![]() |
![]() |
![]() |
![]() ![]() ![]() ![]() |
![]() ![]() ![]() |
![]() |
![]() ![]() ![]() ![]() |
![]() ![]() ![]() ![]() |
![]() |
![]() |
![]() |
![]() |
![]() |
![]() ![]() ![]() |
![]() |
![]() |
![]() |
![]() |
![]() ![]() ![]() ![]() |
![]() ![]() ![]() ![]() |
![]() |
![]() ![]() ![]() ![]() |
![]() ![]() ![]() |
Дополнительная информация
Общий вид1.cdw

Диаметр рабочих валков 390 мм
Мощность привода прокатной клети 800 кВт
Температура металла при прокатке
Макссимальный момент прокатки 20
Минимальное усилие прокатки
Прокатная клеть № 16
Верт разрез.frw

Клети.cdw

Передаточное число горизонтального редуктора 1
Передаточное число вертикального редуктора 1
Материал колёс ст.18Х2Н4ВА
Вращательные момент 5748 Нм
Максимальный момент прокатки 20
Частота вращения входного вала 300 1000 обмин
Частота вращения выходных валов 10 1000 обмин
Матрица неисправностей клети.cdw

Ослабление резьбовых
двигателя и редуктора
Несоосность зубчатых
Дефекты электродвигателя
кой части двигателя*
Густая смазка или её
Матрица неисправностей
*- пропадает при отключении питания
Диплом с титулом.doc
ГОСУДАРСТВЕННОЕ ОБРАЗОВАТЕЛЬНОЕ УЧРЕЖДЕНИЕ
ВЫСШЕГО ПРОФЕССИОНАЛЬНОГО ОБРАЗОВАНИЯ
«ДОНЕЦКИЙ НАЦИОНАЛЬНЫЙ ТЕХНИЧЕСКИЙ УНИВЕРСИТЕТ»
КАФЕДРА МЕХАНИЧЕСКОГО ОБОРУДОВАНИЯ ЗАВОДОВ
НАПРАВЛЕНИЕ 15.03.02 ТЕХНОЛОГИЧЕСКИЕ МАШИНЫ И ОБОРУДОВАНИЕ
Заведующий кафедрой МОЗЧМ
ПОЯСНИТЕЛЬНАЯ ЗАПИСКА КЛ 16.00.00.00.000 ПЗ
к бакалаврской работе
«Проект организации службы технической диагностики
механического оборудования стана 390»
АВТОР БАКАЛАВРСКОЙ РАБОТЫ
(Фамилия имя отчество) (Подпись)
РУКОВОДИТЕЛЬ БАКАЛАВРСКОЙ РАБОТЫ
(Должность ученая степень ученое звание фамилия имя отчество) (Подпись)
«Организационная часть» д.т.н. проф. Сидоров В.А.
(наименование раздела должность ученая степень звание фио подпись)
«Экономическая часть» д.т.н. проф. Ченцов Н.А.
«Охрана труда» к.т.н. доц. Курбацкий Е.В.
«Безопасность жизнедеятельности. 1
Гражданская оборона» к.т.н. доц. Ошовская Е.В.
на бакалаврскую работу
Студенту Сокуренко Андрею Анатольевичу 1
(Фамилия имя отчество)
Тема бакалаврской работы:«Проект организации службы диагностики механического оборудования стана 390
Тема бакалаврской работы утверждена приказом № 236-14 от 10.04.2020 г.
Консультанты бакалаврской работы:
(Наименование раздела должность ученая степень звание ФИО)
«Охрана труда» - к.т.н. доц. Курбацкий Е.В. 1
«Безопасность жизнедеятельности. Гражданская оборона» - 1
Содержание пояснительной записки к бакалаврской работе: описание технологической линии и оборудования стана 390; описание конструкции клети № 16; расчётная часть; разработка диагностической модели; выбор диагностических приборов организация службы диагностики; охрана труда; экономическая часть. 1
Перечень графического материала:
Схема стана 390 (А1); Клеть № 16 общий вид (А1); комбинированная и вертикальная клети в разрезе (А1); Диагностическая модель (А1); Точки диагностирования горизонтальной клети (А1); Точки диагностирования вертикальной клети двигателя и информационные потоки (А1). 1
Срок сдачи студентом законченной бакалаврской работы 23.06.2020 г.
выдачи задания на бакалаврскую работу 20.04.2020 г.
(Фамилия имя отчество)(Подпись)
Поиск и анализ информации по теме работы
Описание конструкции установки
Анализ условий эксплуатации и отказов установки
Определение энергосиловых параметров привода
Прочностные расчёты элементов конструкции
Разработка диагностической модели
Выбор диагностических приборов и разработка организации службы диагностики
Охрана труда безопасности жизнедеятельности и гражданской обороны
Выполнение графической части
Оформление пояснительной записки
Руководитель работы: Ошовская Е.В.
Пояснительная записка содержит 83 стр. 21 рисунков 12 таблиц
источников 7 приложений.
Объект исследования: непрерывный сортовой однониточный стан 390 комбинированная клеть № 16.
Цель исследования: организация службы технической диагностики стана в условиях сильного износа (~ 200%) оборудования.
В ходе работы рассмотрена технологическая линия и оборудование стана 390. Описана конструкция комбинированной (горизонтально-вертикальной) клети № 16. Проведены силовые и прочностные расчёты в ходе которых были определены усилие момент и мощность прокатки рассчитаны усилия в зубчатых зацеплениях и реакции на опорах. Выбраны подшипники зубчатых валов и электродвигатель. Разработана диагностическая модель повреждений для неспециалистов. Выбраны диагностические приборы. Разработаны рекомендации для организации службы диагностики стана. На основании заявок цехов и отделов разработан приблизительный график обходов оборудования. Даны рекомендации по охране труда персонала и организации службы гражданской обороны в цехе. Рассчитан экономический эффект организации службы диагностики.
СТАН 390 КОМБИНИРОВАННАЯ ПРОКАТНАЯ КЛЕТЬ СИЛОВОЙ
РАСЧЁТ РЕДУКТОР ПЕРЕДАТОЧНОЕ ЧИСЛО
ТЕХНИЧЕСКАЯ ДИАГНОСТИКА ВИБРАЦИЯ ДИАГНОСТИЧЕСКИЕ
ПРИБОРЫ ОХРАНА ТРУДА ЭКОНОМИЧЕСКИЙ ЭФФЕКТ
ОПИСАНИЕ ТЕХНОЛОГИЧЕСКОГО ПРОЦЕССА СТАНА. 8
ОБОРУДОВАНИЕ СТАНА 390 15
1 Устройство для загрузки заготовок (реечный шлеппер).15
2 Методическая комбинированная нагревательная печь.16
3 Прокатные клети 17
4 Ножницы горячей и холодной резки 19
5 Реечный стеллаж (холодильник) 20
6 Правильная машина 21
7 Водоснабжение стана 22
8 Смазочная станция 23
9 Система жидкого смазывания 24
10 Электромостовые краны 25
ОБОСНОВАНИЕ И ВЫБОР ОБОРУДОВАНИЯ ДЛЯ
1 Исходные данные 33
2 Определение усилия момента и мощности прокатки.34
3 Силовой расчёт усилий в зубчатых зацеплениях и
реакции на подшипниковых опорах 38
4 Выбор и проверка долговечности подшипников..44
РАЗРАБОТКА ДИАГНОСТИЧЕСКОЙ МОДЕЛИ КЛЕТИ № 1648
1 Матрица неисправностей 48
2 Определение информативных частот повреждений..50
3 Определение допустимых значений
диагностических параметров 52
ВЫБОР ДИАГНОСТИЧЕСКИХ ПРИБОРОВ 58
ОРГАНИЗАЦИЯ СЛУЖБЫ ДИАГНОСТИКИ 64
ОХРАНА ТРУДА И ТЕХНИКА БЕЗОПАСНОСТИ.
1 Охрана труда и техника безопасности 72
РАСЧЁТ ЭКОНОМИЧЕСКОГО ЭФФЕКТА ОТ ОРГАНИЗАЦИИ
СЛУЖБЫ ДИАГНОСТИКИ 83
СПИСОК ИСТОЧНИКОВ 87
Техническая диагностика – наука о распознании технического состояния объекта включающая широкий круг проблем связанных с получением и обработкой диагностической информации.
Вибрационная диагностика преимущественно использует весьма ограниченную информацию она производится обычно в процессе эксплуатации и не предусматривает разборку машины ее часто называют безразборной диагностикой.
Методы вибродиагностики направлены на обнаружение и идентификацию таких неисправностей агрегата которые оказывают влияние на его вибрацию: дефектов роторов опорной системы и узлов статора испытывающих либо генерирующих динамические нагрузки.
Целями вибродиагностики являются:
- предупреждение развития дефектов агрегата и сокращение затрат на его восстановление;
- определение оптимальной технологии восстановления работоспособности агрегата если возникший дефект исключает возможность его нормальной эксплуатации.
Основной задачей вибродиагностики является разделение множества возможных технических состояний агрегата на два подмножества: исправных и неисправных.
Следующей задачей является постановка диагноза состоящего в определении характера и локализации одного или группы дефектов соответствующих вибрационному состоянию агрегата.
Одной из задач вибродиагностики является возможное обнаружение дефекта на ранней стадии и прогнозирование его развития во времени.
На основании диагноза определяется оптимальный режим эксплуатации агрегата в условиях возникшей неисправности и технология устранения дефекта и восстановления работоспособности агрегата. Чем надежней и конкретней диагноз тем ниже затраты связанные с восстановлением агрегата.
Также вибродиагностическая служба может взять на себя ещё одну задачу – предотвращение поступления на предприятие некачественных подшипников качения.
Виброналадка – это комплекс работ направленных на поддержание вибрации объекта в пределах установленных норм. Виброналадка оборудования включает два блока работ: определение причин повышенных вибраций и собственно наладочные работы направленные на устранение повышенных вибраций. Виброналадка проводится непосредственно по месту установки объекта и может быть первичной – связанной с первым пуском объекта (после монтажа или ремонта) или эксплуатационной - проводимой во время эксплуатации объекта.
Типовыми источниками повышенной вибрации являются: разбалансировка роторов; расцентровка валов; дефекты соединительных муфт; ослабления креплений и фундамента; автоколебания ротора в опорах вращения; резонансы колебательной системы «фундамент+объект».
Во многих случаях при виброналадке параллельно с измерениями вибрации контролируют и другие физические параметры работы объекта (температура давление ток и т.д.) несущие полезную диагностическую информацию.
Исходя из этих требований служба вибродиагностики и виброналадки предприятия должна обладать оптимальной приборной базой.
ОПИСАНИЕ ТЕХНОЛОГИЧЕСКОГО ПРОЦЕССА СТАНА
Непрерывный сортовой однониточный стан 390 состоит из 18 рабочих клетей дуо с индивидуальным приводом в том числе 8 горизонтальных 4 вертикальных и 6 комбинированных клетей (обеспечивают установку в линию стана рабочей клети либо с горизонтальными либо с вертикальными валками) (рисунок 1.1). Клети установлены последовательно в три группы по шесть клетей в каждой: черновую промежуточную и чистовую.
Рисунок 1.1 – Схема технологической линии стана 390:
– неподвижный упор; 2 – стеллаж брака заготовок; 3 – загрузочная решётка; 4 – рольганговые весы; 5 – опускающийся упор; 6 – сталкиватель; 7 – нагревательная печь; 8 – устройство для гидросбива; 9 – тоннель-термостат; 10 – трайбаппарат перед 1-й клетью; 11 – черновая группа клетей; 12 – кривошипно-рычажные ножницы; 13 – промежуточная группа клетей; 14 – кривошипно- рычажные ножницы; 15 – чистовая группа клетей; 16 – измеритель геометрических размеров; 17 – участок ускоренного охлаждения; 18 – двухсистемные ножницы; 19 – кривошипный крошитель; 20 – реечный стеллаж; 21 – мостовые весы; 22 – вязальная машина; 23 – поперечный транспортёр; 24 – стационарный упор; 25 – накопитель немерных прутков; 26 – цепной транспортёр 1;
– цепной транспортёр 2; 28 – дозатор; 29 – летучие ножницы холодной резки; 30 – правильная машина; 31 – петлерегуляторы; 32 – устройства для смены клетей; 33 – разрывные ножницы; 34 – машина съёма заготовок; 35 – сталкиватель; 36 – бракомоталка; 37 – трайбаппарат
Проектная производительность стана – до 720 тысяч тонн готового проката в год в зависимости от заложенного проката.
Нагрев исходных заготовок сечением 150×150 мм и 125×125 мм длиной до 120 м осуществляется в нагревательной печи с водоохлаждаемыми балками с боковой подачей и боковой выгрузкой заготовок с помощью внутрипечных роликов.
Стан оборудован холодильником линиями для регулируемого охлаждения и термоупрочнения готового проката механизированным участком отделки в потоке.
Максимальная скорость прокатки на стане – 18 мс расчетная рабочая – от 23 до 17 мс в зависимости от прокатываемого профилеразмера сортовой стали.
Стан оснащен автоматизированными системами регулировки и управления режимами прокатки и работой технологических агрегатов механизмов и устройств а также промышленными телекамерами обзора невидимых оператору зон и участков технологической линии мониторы которых установлены на соответствующих постах управления. Прокатка на стане осуществляется с минимальным натяжением в черновой и промежуточной группах клетей и с петлерегулированием в чистовой группе.
Непрерывный стан 390 предназначен для производства в прутках крупного среднего и мелкого сортового проката.
Оборудование стана и технология прокатки обеспечивают производство сортового проката повышенной точности с предельными отклонениями размеров профиля согласно требованиям соответствующих стандартов и технических условий.
Прокатный стан 390 производит следующий сортамент продукции из углеродистых и легированных сталей:
- прокат стальной горячекатаный круглый;
- прокат стальной горячекатаный квадратный;
- прокат стальной горячекатаный шестигранный;
- уголки стальные горячекатаные равнополочные;
- прокат горячекатаный для армирования железобетонных конструкций;
- прокат арматурный для железобетонных конструкций;
- сталь арматурная термомеханически упрочненная для железобетонных конструкций;
- прокат стальной горячекатаный для рессор;
- уголки стальные горячекатаные неравнополочные;
- полоса для накладок к железнодорожным рельсам узкой колеи.
Подготовленные для прокатки на стане заготовки поплавочно в соответствии с заказами подаются пратцен-кранами со склада заготовок или из железнодорожных вагонов и укладываются в один слой на одну из двух загрузочных решеток откуда кулачками реечного шлеппера транспортируются к перекладывающему устройству.
Перекладывающим устройством заготовки передаются на подводящий рольганг которым транспортируются к нагревательной печи. На третьей секции подводящего рольганга заготовки взвешиваются на рольганговых весах. Фиксированное положение заготовки на участке весов обеспечивается опускающимся упором.
Бракованные заготовки подводящим рольгангом подаются в противоположную от печи сторону к стационарному упору и сталкивателем передаются на решетку-стеллаж.
Нагрев заготовок до температуры прокатки производится в методической комбинированной печи с водоохлаждаемыми балками с боковой подачей и разгрузкой заготовок с помощью внутрипечных роликов.
При аварийной ситуации на стане связанной с прекращением процесса прокатки или в случае необходимости разгрузки печи нагретые заготовки с рольганга выгрузки транспортируются по отводящему рольгангу в противоположную от стана сторону к стационарному упору и сталкивателем передаются на стеллаж откуда после охлаждения убираются пратцен-краном.
Заготовка поступает в тоннель-термостат (обеспечивает минимальное падение и выравнивание по сечению температуры заготовки перед первой клетью) откуда трайбаппаратом подается в первую клеть.
Перед первой клетью установлены разрывные ножницы маятникового типа которые при производственной необходимости или в аварийных ситуациях выполняют делительный рез и предотвращают дальнейшую подачу заготовки в черновую группу. При этом перемещение верхнего и нижнего ножей из исходного положения до контакта с гранями заготовки осуществляется пневмоприводом а дальнейшее внедрение их в металл до завершения делительного реза – за счет тянущего усилия первой клети.
Прокатка сортовых профилей на стане осуществляется в трех группах клетей:
- черновой состоящей из одной горизонтальной (№ 1) и одной вертикальной (№ 2) клетей 600 двух горизонтальных (№ 3 5) и двух вертикальных (№ 4 6) клетей 440;
- промежуточной состоящей из трех горизонтальных (№ 7 8 9) и двух комбинированных (№ 11 12) клетей 390 и одной вертикальной (№ 10) клети 390;
- чистовой состоящей из двух горизонтальных № 13 14) и четырех комбинированных (№ 15 16 17 18) клетей 390.
Число проходов и следовательно количество используемых клетей зависят от прокатываемого на стане профилеразмера сортовой стали.
В черновой и промежуточной группах прокатка ведется без кантовки раската с минимальным натяжением его между клетями которое автоматически поддерживается системой регулирования минимального натяжения.
На кривошипно-рычажных ножницах после черновой и промежуточной групп производится обрезка передних и при необходимости задних концов раската а также аварийная порезка на мерные части.
Из промежуточной группы в чистовую раскат транспортируется с минимальным натяжением или без натяжения с петлерегулированием – в зависимости от прокатываемого профиля сортовой стали.
В чистовой группе прокатка осуществляется без натяжения раската с петлерегулированием. Величина петли поддерживается автоматически петлерегуляторами с использованием импульсов от фотоэлектрических датчиков положения петли.
При производстве арматурной стали № 10 № 12 № 14 № 16 № 18 по технологии сдвоенной прокатки в чистовой группе стана ведется формирование раската сдвоенного или счетверённого профиля валками клетей №№ 15 и 16 и последующая двух- или четырёх-ручьевая прокатка в клетях № 17 и № 18.
При прокатке винтовой арматурной стали чистовые клети № 16 и № 18 (в зависимости от прокатываемого профилеразмера) используются в вертикальном варианте где на конических механизмах привода шестеренных валков предусмотрена осевая регулировка на одном косозубом шестеренном валке для обеспечения требуемой точности винтового профиля готового проката.
Рабочие клети по программе неиспользуемые в процессе прокатки из потока стана удаляются а на их место устанавливаются специальные желоба.
Готовый прокат периодического профиля после контроля геометрических размеров транспортируется через установку ускоренного охлаждения которая обеспечивает снижение вторичного окалинообразования и повышение прочностных свойств металла.
При производстве профилей не подвергающихся ускоренному охлаждению вместо секций охлаждающих труб в линию стана вводятся соответствующие секции рольганга.
Термоупрочненный или горячекатаный прокат подается трайбаппаратом к двухсистемным стоп-стартовым ножницам на которых производится раскрой его на штанги заданной длины транспортируемые на холодильник подводящим рольгангом.
Торможение полос готового проката осуществляется на приемном рольганге холодильника системой двойных подъемных клапанов (разделительных перегородок и клапанов). Эффективность торможения ускоренно-охлажденного проката повышают за счет использования отдельных тормозных клапанов с электромагнитами питание которых включается циклически при подъеме клапанов из исходного нижнего в верхнее положение.
Полосы проката охлаждаются при перемещении в поперечном направлении по реечному стеллажу. При этом производится выравнивание укладки полос проката по передним концам с помощью двух рольгангов установленных в неподвижной системе реек стеллажа.
Прокат после реечного стеллажа поступает на передаточное устройство на собирательных цепях которого формируются слои проката с определенным для каждого профилеразмера количеством штанг и шагом раскладки которые с помощью подъемных тележек передаются на отводящий рольганг холодильника.
На отводящем рольганге слой фасонного проката торцуется по передним концам с помощью опускающегося упора и подается к многоручьевой правильной машине. В процессе правки головная часть слоя проката после правильной машины поступает по рольгангу к летучим ножницам холодной резки на которых производится обрезка передних концов и раскрой прутков проката на готовые длины с использованием профильных ножей при этом правильная машина и летучие ножницы холодной резки работают в синхронном скоростном режиме.
При производстве простых профилей не требующих правки правильная машина выводится из потока и на ее место вводится секция рольганга. В этом случае слой проката (с шаговой раскладкой или уплотненный) с отводящего рольганга подается непосредственно к летучим ножницам холодной резки. Обрезка концов слоя проката и раскрой на ножницах холодной резки при непрерывном движении проката производится в автоматическом режиме – аналогично раскрою фасонного проката при этом в зависимости от профилеразмера проката используют либо плоские либо профильные ножи.
Слои прутков готовой длины после порезки на летучих ножницах холодной резки транспортируются в потоке на участок отделки по одному из трех технологических маршрутов:
Пакетирование или штабелирование готового проката на первом участке поперечной транспортировки со сбором пакетов круглого поперечного сечения или штабелей прямоугольного поперечного сечения на сборных решетках 1 и 2.
Пакетирование или штабелирование готового проката на втором участке поперечной транспортировки со сбором пакетов или штабелей на сборных решетках 2 и 3.
Пакетирование или штабелирование готового проката на первом и втором участках поперечной транспортировки со сбором пакетов или штабелей на всех трех сборных решетках.
В случае раскроя пакета на мерные длины с образованием остатка проката укороченной длины последний транспортируется рольгангом за ножницами под упор и сбрасывается в карман.
Слои прутков с участка поперечной транспортировки передаются скоростным передаточным устройством на цепной транспортер 1; затем после укладки следующего слоя удвоенное количество прутков перекладывается на рольганг для выравнивания концов с использованием стационарного упора и поступает на цепной транспортер 2.
Передвижные вязальные машины обвязывают пакет в заданных местах концы которой увязываются.
При работе в режиме штабелирования для укладки в перевязку прутки фасонных профилей с цепного транспортера 2 собираются дозаторами в слои с заданным количеством прутков которые в определенной последовательности с использованием магнитов поворотных (кантующих) устройств поступают на промежуточный стол откуда перекладываются на подъемный стол укладочного устройства. Подъемный стол по мере увеличения высоты штабеля опускается. Дальнейшая последовательность технологических операций обработки штабеля аналогична пакетированию с той лишь разницей что штабели снимаются с тележки в положение обвязки не цепями а горизонтальными рычагами вертикального транспортера.
Пакет или штабель готового проката со сборной решетки передается цеховым краном на склад готовой продукции или на погрузку в вагон.
ОБОРУДОВАНИЕ СТАНА 390
1 Устройство для загрузки заготовок (реечный шлеппер)
Реечный шлеппер (рисунок 2.1) служит для перемещения заготовок в поперечном (относительно линии прокатки) направлении и подачи их на рольганг для транспортировки в нагревательную печь.
Рисунок 2.1 – Реечный шлеппер (а) и устройство опрокидывающегося кулачка (б)
Скорость транспортирования015 мс;
Количество решёток2 шт.
2 Методическая комбинированная нагревательная печь
Печь (рисунок 2.2) служит для нагрева заготовок до нужной температуры и перемещения их в поперечном (относительно линии прокатки) направлении и подачи их на рольганг для дальнейшей прокатки.
Режим работы непрерывный. Нагрев заготовок производится газовыми горелками в печи с шагающими водоохлаждаемыми балками (таблица 2.1). Рабочая температура прогрева заготовок 1240 °С.
Рисунок 2.2 – Принципиальная схема механизма шагания печи:
– гидроприводы перемещения; 2 – балка горизонтального перемещения;
– рама вертикального перемещения; 4 – неподвижная балка
Таблица 2.1 - Характеристика горелок и расход природного газа в печи
Номинальный расход газа м3ч
Количество горелок шт
Максимальная производительность одной горелки м3ч
производительность печи тч
производительность м3ч
Основное рабочее оборудование стана – прокатные клети. Для стана 390 это клети трёх типов: вертикальные горизонтальные и комбинированные.
Комбинированная клеть содержит в себе элементы вертикальной и горизонтальной клетей. Устройство прокатных клетей рассмотрим на её примере (рисунок 2.3). Технические характеристики клетей приведены в таблицах 2.2 – 2.4.
Рисунок 2.3 – Комбинированная клеть прокатного стана 390:
– комбинированный горизонтально-вертикальный редуктор; 2 – наклонный вал; 3 – вертикальный редуктор; 4 – вертикальные валы; 5 – прокатная клеть;
– прокатные валки; 7 – фундамент; 8 – гидростопор клети; 9 – горизонтальные валы; 10 – опоры вертикального редуктора; 11 – приводной электродвигатель
Таблица 2.2 - Вертикальные клети
Возможный диаметр валков
Межосевое расстояние валков
Допустимая осевая регулировка верхнего валка
Минимальное усилие прокатки
Максимально число оборотов на входе
Число оборотов валка
Макс момент прокатки
Таблица 2.3 - Горизонтальные клети
Максимальное число оборотов на входе
Таблица 2.4 - Комбинированные клети
Максммальное число оборотов на входе
4 Ножницы горячей и холодной резки
По линии прокатки расположены пять ножниц:
- разрывные (перед первой прокатной клетью);
- четверо кривошипно-рычажных (рисунок 2.4): после черновой и промежуточной групп клетей; после участка термоупрочнения и пакетные летучие ножницы холодной резки после холодильника (таблица 2.5).
Таблица 2.5 - Параметры пакетов сортового проката подлежащих порезке летучими ножницами холодной резки
Количество прутков в пакете шт
Рисунок 2.4 – Общий вид (а) и механизм резания (б) кривошипно-рычажных ножниц:
– серьга; 2 – жёсткий рычаг; 3 – водило; 4 – зубчатое колесо; 5 – шестерня; 6 – приводной вал; 7 – подшипники
5 Реечный стеллаж (холодильник)
Перемещение проката производится посредством эксцентриков связанных с рейками холодильника и установленных на приводном валу (рисунок 2.5).
Рисунок 2.5 – Общий вид (а) и механизм перемещения проката (б) реечного холодильника
Основные характеристики
Расстояние между рейками:
- неподвижными500 мм;
- подвижными2501000 мм;
Макс. нагрузка на решётку800 кН.
Правильная машина предназначена для правки в потоке пакетов фасонного проката с шаговой укладкой прутков поступающих с отводящего рольганга холодильника. Состоит из правильного девятивалкового блока передвижной рамы и приводной линии.
скорость правки075 20 мс;
скорость заправки прутков075 мс;
правильный момент12 кН×м;
расстояние между осями правильных валков400 мм;
- полезная ширина590 мм;
количество правильных валков:
- нижних (приводных)5 шт.;
- верхних (неприводных)5 шт.;
перемещение (ход) правильных валков:
- вертикальное150 мм;
скорость перемещения правильных валков:
- вертикального02 04 ммс;
перемещение установки при выводе из линии1235 мм;
скорость вывода из линии60 ммс.
7 Водоснабжение стана
В состав комплекса стана 390 входят объекты:
- «чистого» оборотного цикла производительностью 980 м3ч;
- оборотного цикла установки термоупрочнения производительностью 900 м3ч;
- «грязного» оборотного цикла (становой воды) производительностью 524 м3ч.
Для перекачки воды используются насосы:
- центробежный секционный насос VKF и Mult
- центробежный насос К-200-150-250 (18 шт.) с производительностью 315 м3ч и напором 20 м;
- центробежный насос ГРаТ35040П-16 (4 шт.) с производительностью 400 м3ч и напором 50 м;
- центробежный насос ТР200-3904 А-F-A (4 шт.) с производительностью 149 м3ч и напором 35 м;
- центробежный насос ТР100-2004 (4 шт.) с производительностью 135м3ч и напором 10 м;
- центробежный насос ХП-28042б-Е-Щ (2 шт.) с производительностью 280 м3ч и напором 20 м;
- центробежный насос ГНОМ 10-10 (2 шт.) с производительностью 10м3ч и напором 10 м.
Общий вид центробежного насоса показан на рисунке 2.6.
Рисунок 2.6 – Центробежный консольный насос
Смазочная станция применяется в качестве закрытой транспортной единицы для работы двухпроводниковой централизованной установки для пластичной смазки (таблица 2.6). Она состоит из двух насосов для централизованной смазки ZP 35080 (рисунок 2.7) реверсивного клапана VUD и сигнального датчика SG 40I в качестве управляющего приспособления двухпроводниковой установки.
Рисунок 2.7 – Насос централизованной смазки ZP 35080. Общий вид
Характеристики насоса:
номинальное давление280 бар;
максимальное рабочее давление350 бар;
пропускаемый объём350 см3мин
вместительность бака 80 л;
предельные рабочие температуры5 50 °С.
Таблица 2.6 - Расход пластичной смазки на смазывание оборудования
Кол-во циклов в сутки
Кол-во рабочих суток
Рольганги холодильника
Привалковая арматура клетей для арматуры 32
Опоры клетей для арматуры 32
Внутрипечные рольганги
Трайб перед клетью 1
Рольганг термоупрочнения
Рольганг перед холодильником
9 Система жидкого смазывания
На рисунке 2.8 приведена схема подачи смазки к элементам редуктора. Для создания рабочего давления в системе смазки используются трёхвинтовые маслонасосы IMO ACF-1104 (рисунок 2.9) со следующими техническими характеристиками:
максимальное давление на выходе - 16бар.;
производительность - 310-2900лмин.;
максимальная температура +90°С.
Рисунок 2.8 – Схема подачи смазки к элементам редуктора:
– запорный клапан; 2 – фланец; 3 – уплотнение; 4 10 – гайки; 5 8 11 15 – болты; 6 – резьбовое трубное соединение; 7 – подкладка; 9 16 – хомут;
– скоба; 13 – дроссель; 14 – держатель; 17 – зажимная муфта; 18 – цапфа;
– прокладочное кольцо; 20 – манометр
Рисунок 2.9 – Общий вид (а) и устройство (б) трёхвинтовогой маслонасоса
10 Электромостовые краны
В состав оборудования стана входят мостовые краны разной грузоподъемности (таблица 2.7).
Таблица 2.7 - Список кранов и их основные характеристики
Рисунок 2.10 – Тележка пратцен-крана с лапами на траверсе:
– лапы; 2 – кабина машиниста; 3 – механизм управления лапами; 4 – механизм подъёма; 5 – поворотное кольцо; 6 7 – механизм поворота; 8 – колонна; 9 – электромагнит
ОБОСНОВАНИЕ И ВЫБОР ОБОРУДОВАНИЯ
ДЛЯ ДИАГНОСТИРОВАНИЯ
В качестве объекта диагностирования выбрана прокатная клеть № 16.
Клеть №16 расположена в чистовой группе клетей и представляет собой комбинированную клеть с двумя вертикальными и двумя горизонтальными рабочими валками.
Для привода валков используется комбинированный редуктор представляющий собой комбинацию в одном корпусе редуктора и шестеренной клети. При чем таких редукторов два – горизонтальный и вертикальный. Горизонтальный редуктор – двухступенчатый и используется для привода горизонтальных валков а также имеет наклонный вал и коническую передачу при помощи которой может передавать момент на редуктор привода вертикальных валков. В зависимости от производственной программы комбинированный редуктор клети №16 приводит во вращение вертикальные или горизонтальные валки.
Прокатная клеть №16 задействована практически во всех производственных программах прокатка в ней может вестись сразу в двух ручьях.
Привод прокатной клети №16 состоит из двух комбинированных редукторов – вертикального и горизонтального.
Горизонтальный редуктор предназначен для привода горизонтальных рабочих валков а также для передачи крутящего момента посредством конической передачи вертикальному редуктору для чего в его конструкции предусмотрена переключающая муфта.
Последовательно рассмотрим конструкции обоих редукторов.
Комбинированный редуктор (рисунок 3.1) прокатной клети представляет собой совокупность цилиндрического редуктора и шестеренной клети собранных в одном корпусе. Такое конструктивное решение позволяет снизить количество оборудования общую длину валопроводов и следовательно ведет к уменьшению стоимости оборудования и облегчению его эксплуатации.
Горизонтальный редуктор состоит из одной цилиндрической косозубой передачи и передачи состоящей из двух шестеренных валков. Момент передается от двигателя через муфту на входной вал редуктора затем на переключающую муфту которая передает момент на промежуточный вал после чего крутящий момент передается на вал шестеренного валка. В последней передаче крутящий момент разделяется пополам. На хвостовиках шестеренных валков закрепляются муфты шпиндельного соединения при помощи которого момент передается на рабочие валки.
Рисунок 3.1 – Кинематическая схема комбинированного редуктора:
21 – коническое колесо; 2 – самоустанавливающийся роликоподшипник;
8 11 15 – конические роликоподшипники; 4 – ведомый вал; 5 – цилиндрический роликоподшипник; 6 – вал нижнего шестерённого вала; 7 - вал верхнего шестерённого вала; 9 12 14 18 – цилиндрическое колесо; 10 16 – радиальные шарикоподшипники; 13 – муфта переключения; 17 – приводной вал; 19 – промежуточный вал
Корпус редуктора сварной и состоит из трех частей: верхней средней и нижней. Части соединены между собой при помощи болтовых соединений центрирование осуществляется при помощи штифтов.
Валы опираются на прецизионные подшипники качения номинальный срок службы которых составляет не менее 50 тыс. часов (при максимальном моменте прокатки). Горизонтальные цапфы валов уплотнены бесконтактно.
В данном случае горизонтальный комбинированный редуктор предназначен как для привода горизонтальных рабочих валков так и для передачи крутящего момента на вертикальный редуктор.
Привод вертикальных рабочих валков осуществляется за счет вертикального комбинированного редуктора (рисунок 3.2).
Рисунок 3.2 – Кинематическая схема вертикального редуктора
– шестеренный валок 1; 20 – шестеренный валок 2; 21 – промежуточный вал; 29 – приводной вал; 30 – коническое колесо; 31 – коническое колесо; 80 – самоустанавливающийся роликоподшипник; 81 – цилиндрический роликоподшипник; 82 – конический роликоподшипник; 83 – конический роликоподшипник; 84 – конический роликоподшипник
Редуктор состоит из одной конической передачи и двух цилиндрических косозубых передач.
Крутящий момент передается от горизонтального редуктора когда муфта переключение установлена в положение «V». От входного вала горизонтального редуктора через муфту включения и коническую передачу момент передается на шпиндельное соединение при помощи которого осуществляется привод входного вала вертикального редуктора.
Затем крутящий момент передается на два шестеренных валка в которых он разделяется пополам и посредством шпинделей передается рабочим валкам.
Корпус редуктора сварной состоит из двух боковых частей с вертикальным разъемом. Части соединяются при помощи болтов и центрируются штифтами.
Валы опираются на прецизионные подшипники качения срок службы которых составляет при максимальном моменте прокатки не менее 50 тыс. часов работы полной нагрузки.
Наклонный приводной вал (от горизонтального редуктора к вертикальному) и вертикальные шестеренные валки уплотнены бесконтактно.
Во время эксплуатации стана 390 после реконструкции были зафиксированы такие отказы:
Сбои в работе автоматики управления нагревательной печи.
Обрывы стяжных шпилек на комбинированном редукторе клети №10.
Разрушение конического зацепления в вертикальном редукторе клети №18 из-за отсутствия смазки.
Ослабление резьбовых соединений в комбинированном редукторе клети №14 после прокатки холодного металла после чего повысилась вибрация – устранено обтяжкой резьбовых соединений.
Износ вкладышей шпиндельного устройства соединения вертикальных шестеренных и рабочих валков проявляющийся в виде увеличения вибрации после выхода заготовки из клети и увеличения токовых характеристик двигателя – устранено при помощи замены вкладышей.
Повышение осевой составляющей вибрации на подшипниках электродвигателя и зубчатого вала первой ступени редуктора клети № 9 из-за отсутствия планового ежегодного ТО с заменой смазки и заклинивания зубчатой соединительной муфты. Проблема решена промывкой частей муфты и заменой смазки.
Разрушение сепаратора роликового двухрядного сферического подшипника на шестерённом валу редуктора № 11 из-за повышенных ударных нагрузок (в момент захвата заготовки) и повышенной осевой нагрузки на подшипник. Подшипник заменён проблема конструктивная и решению не подлежит.
Разрушение подшипника № 2 электродвигателя клети № 11 из-за отказа смазывать их «по состоянию» и продолжения смазывания по инструкции. Проблема в отсутствии планового ежегодного ТО с заменой смазки в подшипниках. Смазывание проводится «по состоянию» проблема с ТО не решена.
Регулярное разрушение валков клети № 1 из-за недопустимого искривления заготовки поступающей с Алчевского металлургического завода. Проблема не решена.
К отказам можно добавить регулярно выявляемые дефекты при осмотрах и диагностике:
- износ подшипников;
- ослабление резьбовых соединений;
- дефекты зубчатых зацеплений;
- дефекты соединительных муфт;
- проблемы со смазыванием подшипников;
- другие характерные для роторного оборудования работающего с ударно-переменными нагрузками в тяжёлых условиях.
Из всего вышеперечисленного можно сделать вывод что прокатная клеть № 16 является объектом включающим в себя большинство возможных проблем возникающих на оборудовании прокатного стана 390. И именно её можно рассматривать в качестве объекта исследования при выполнении дипломного проекта.
Передача редуктора общая:
Возможный диаметр валков мм:
Межосевое расстояние валков по оси прокатки мм:
Допустимая осевая регулировка верхнего валка мм ..±3
Скорость прокатки мс:
Минимально существующее усилие прокатки кН..74
Соответствующее число оборотов валка (макс) обмин.4591
Максимальное число оборотов на входе обмин.10001100
Число оборотов валка обмин:
- с максимальной нагрузкой 4253
Максимальный момент прокатки кНм 2027
Часть крутящего момента на каждую цапфу
Мощность двигателя кВт:
Калибровка клети № 16 для прокатки круга 28 мм по ГОСТ 2590-88
Диаметр заготовки на входе мм 480
Высота металла мм 282
Ширина металла мм 282
Площадь металла мм2 423
Коэффициент вытяжки 127
Средний диаметр валка по буртам:
- минимальный мм 340
- максимальный мм 390
Катающий диаметр валка:
- минимальный мм 321
- максимальный мм 371
Частота вращения двигателя:
- минимальные обмин 431
- максимальные обмин 498
Частота вращения валков:
- минимальные обмин 360
- максимальные обмин 417
Скорость прокатки мс 70
Температура прокатки °С 1000
Предел текучести стали 25Г2С т МПа
- при нормальных условиях 785
- при температуре прокатки 50
2 Определение усилия момента и мощности прокатки
Момент прокатки определяется по формуле
где Р – усилие прокатки;
R – катающий радиус валка (рисунок 4.1).
Рисунок 4.1 – Схема обжатия при прокатке
Горизонтальная проекция дуги захвата
где рср – среднее давление прокатки;
F = 423 мм2 = 0000423 м2 – площадь металла.
Среднее давление прокатки
где γ – коэффициент влияния среднего нормального напряжения в очаге деформации γ = 115;
n – коэффициент напряжённого состояния;
ф – фактическое сопротивление деформации от скорости деформации и (с учётом материала температуры и скорости прокатки) определяется по диаграмме (рисунок 4.2) ф = 113 МНм2.
Рисунок 4.2 – Зависимость фактического сопротивления деформации от скорости деформации для стали 25Г2С при степени обжатия:
– 10% 2 – 20% 3 – 40% [6 стр. 374]
Коэффициент напряжённого состояния
где nш – коэффициент учитывающий ширину заготовки;
nт – коэффициент внешнего трения;
nвз – коэффициент внешних зон nвз =1;
nн – коэффициент натяжения nн = 08 10.
Для коэффициент учитывающий ширину заготовки
Коэффициент внешнего трения для
Тогда среднее давление прокатки
Так как расчётный момент прокатки на валках Мпр = 226 кНм отличается от фактического М = 2027 кНм на 111% дальнейший расчёт будем проводить по фактическому моменту прокатки.
В работе будем рассчитывать горизонтальную часть редуктора.
Редуктор двухступенчатый общее передаточное число i = 12.
Определяем максимальную мощность на выходном валу
Определяем максимальную мощность двигателя
где мех – КПД механизма:
где ред – КПД редуктора по ГОСТ Р 50891;
Выбираем ближайший подходящий по заданным и рассчитанным параметрам двигатель независимого возбуждения типа 4П-450-38-800 - УЗ с параметрами:
Проверяем условия запуска двигателя под нагрузкой:
Условие выполняется.
3 Силовой расчёт усилий в зубчатых зацеплениях и реакции на подшипниковых опорах
Выбор материала валов.
Исходные данные для расчёта:
- материал: ст. 18Х2Н4ВА;
Режим работы передачи принимаем нереверсивный постоянный.
Срок службы L = 5 лет количество смен z = 3 по 8 часов коэффициент использования по времени Kz = 09.
Расчёт производим для второй ступени (цилиндрическая прямозубая).
Приближённое определение модуля передачи
где Тном1 – номинальный вращательный момент
Число циклов напряжения для зубьев колеса второй ступени
где Lh – номинальное время работы
Так как то Т1 = Тном1.
Согласно ГОСТ 9563-60 из стандартного ряда выбираем мм.
Выбор материала для зубчатых колёс определение допустимых напряжений.
Диаметр вершин колеса и шестерни второй ступени при числе зубьев z’1 = z’2 = 47:
Материал для колёс примем ст. 18Х2Н4ВА закалка ТВЧ со свойствами:
- твёрдость поверхности 404 НВ;
- твёрдость сердцевины 220 280 НВ;
- предел прочности В =1050 МПа;
- предел текучести Т = 800 МПа;
- предел контактной прочности Hl
- предел общей прочности Flim = 750 МПа.
Так как термообработкой выбрана закалка то будем проводить прочностной расчёт на изгиб. Допустимые напряжения:
где [S]F – коэффициент запаса прочности по напряжениям на изгиб при закалке [S]F = 17 ;
КFC – коэффициент учитывающий характер изменения напряжений изгиба для нереверсивных передач КFC = 10;
KFL – коэффициент долговечности учитывающий повышение предельных напряжений при числе циклов напряжения меньше базового KFL = 1.
Проектный расчёт передачи на прочность зубьев при изгибе
где YF – коэффициент формы зуба YF = YF1 = YF2 = 412;
К – коэффициент расчётной нагрузки К = 13;
m – коэффициент ширины колеса при Н 350 НВ m = 18.
Согласно ГОСТ 9563-60 из стандартного ряда выбираем шп= 8 мм. Определяем основные размеры колеса.
Делительный диаметр мм.
Межосевое расстояние aw = a = d = 376 мм.
Ширина зубчатого венца:
Значение b округляем до ближайшего стандартного из ряда Ra40 по ГОСТ 6636-69:
b2 = 120 мм; b1 = 125 мм.
Проверочный расчёт прочности зубьев.
Окружная скорость зубчатого колеса:
Напряжение изгиба в опасном сечении должно быть не больше допустимого:
Фактическое напряжение
где Ftp – расчётное окружное усилие
Фактическое напряжение изгиба в опасном сечении зуба колеса:
Проверка прочности []F = 4412 МПа F2 = 1791 МПа.
Проверочный расчёт прочности выходного вала.
Расстояние между центрами подшипников (рисунок 4.3) у = 165мм (рисунок 4.3).
Нагрузки действующие на вал:
- окружное усилие Ftp = 397461 H;
Fr = Ftp · tgα = 397461 · tg20° = 144676 H
где α = 20° – угол зацепления цилиндрической прямозубой передачи.
Реакции опор в вертикальной плоскости
Изгибающий момент в вертикальной плоскости:
Mu = RуА · y = 67671 · 0165 = 11657 H·м.
Реакции опор в горизонтальной плоскости:
Изгибающий момент в горизонтальной плоскости:
Mux = RxA · y = 185909 · 0165 = 30675 H·м.
Суммарный изгибающий момент:
Опасное сечение расположено по середине ступицы колеса. Диаметр вала рядом с колесом равен d = 220 мм.
Выполним расчет на статическую прочность.
Вычисляем момент сопротивления поперечного сечения оси изгибу и площадь поперечного сечения:
где е’ = 09 и еF = 097 – поправочные коэффициенты.
Строим эпюры изгибающего и приведенного моментов (рисунок 4.3).
Рисунок 4.3 – Эпюры моментов к расчёту вала
Находим нормальные напряжения от изгиба
и касательные напряжения от кручения
Определяем с учетом размеров сечения масштабный коэффициент е = =072 (рисунок 4.4).
Рисунок 4.4 – Масштабный коэффициент е в зависимости от диаметра вала
Определяем пределы текучести при растяжении и кручении для материала вала (сталь 18Х2Н4ВА) с учетом масштабного коэффициента ет = 072 пределы текучести образца ’т = 1050 МПа ’ m = 800 МПа.
Находим запасы прочности по нормальным и касательным напряжениям:
Определим запас прочности при совместном действии нормальных от изгиба и касательных напряжений:
Условие прочности выполняется.
4 Выбор и проверка долговечности подшипников
Определим фактическую долговечность подшипников выходного вала
где С – динамическая грузоподъёмность кН;
Рприв – приведенная нагрузка кН;
ρ = 3.33 – коэффициент тела качения для роликового подшипника.
Полученное значение должно быть в диапазоне Lв Lhфакт где Lв – потребная долговечность.
Вал будет установлен на двухрядный конический подшипник 2097144 и роликовый цилиндрический двухрядный подшипник 426944 (таблица 4.1).
Таблица 4.1 - Параметры подшипников
Суммарная реакция опор:
Для подшипника 426944.
Расчетная нагрузка на подшипник
где kб – коэффициент безопасности для редукторов прокатных клетей
Так как подшипники работают при переменном режиме нагрузки то необходимо определить эквивалентную нагрузку действующую на них:
где Fr = RА – радиальная нагрузка на подшипник;
Fa = 0 – осевая нагрузка на подшипник;
Х = 1 Y = 0 – коэффициенты приведения для данного подшипника;
km = 1 – коэффициент температурного режима.
Определяем фактическую долговечность подшипника
Согласно ГОСТ 16162—85 долговечность подшипника должна составлять Le= 10000 час.
Le = 10000 Lhфакт = 1395871 час.
Условие долговечности выполняется.
Для подшипника 2097144.
где Fr = RВ – радиальная нагрузка на подшипник;
Le = 10000 Lhфакт = 8845039 час.
РАЗРАБОТКА ДИАГНОСТИЧЕСКОЙ МОДЕЛИ КЛЕТИ № 16
1 Матрица неисправностей
Следует отметить что во время работы стана исходя из норм безопасности условно доступны для диагностирования только приводной двигатель и комбинированный редуктор находящиеся на нулевой отметке. Для них и разработаем матрицу неисправностей.
Клети характерны регулярно выявляемые дефекты при осмотрах и диагностике:
- расцентровки валов;
- электрические дефекты приводных двигателей.
Данная матрица позволит эксплуатационному персоналу и малоопытному специалисту по диагностике на месте осмотра примерно определять причины неполадок с целью принятия решений и дальнейшим действиям.
Таблица 5.1 - Матрица неисправностей
Органолептические методы
Ослабление резьбовых соединений
Разрушение зубьев соед. муфты
Отсутствие смазки в соед. муфте
Заклинивание соед. муфты
Расцентровка валов двигателя и редуктора
Дефекты сепаратора подшипника
Износ поверхностей качения подш.
Дефекты зубчатых зацеплений
Отсутствие смазки зубч. зацеплений
Выкрашивание зубьев зубч. зацеплений
Несоосность зубч. колёс
Отсутствие смазки подшипников
Дефекты электродвигателя
Дефекты электрич. части двигателя*
Густая смазка или её отсутствие
* - пропадают при отключении питания
2 Определение информативных частот повреждений
В настоящее время одним из самых распространенных методов представления данных о вибрации является представления вибрационного сигнала разложенного в спектр при помощи быстрого преобразования Фурье.
Такое представление сигнала позволяет оценивать состояние отдельных элементов оборудования за счет того что в результате измерения получается совокупность значений характеризующих амплитуды параметров вибрации на конкретных частотах.
Если измерение общего уровня вибрации позволяет нам судить лишь о состоянии оборудования в целом то спектральный анализ вибрации позволяет распознавать изменение технического состояния отдельных его элементов. Это возможно за счет того что повреждения полученные элементами оборудования проявляются на заранее известных частотах которые называются информативными.
Обобщив можно сказать что информативной называется такая частота в спектре вибрации на которой проявляются повреждения элементов оборудования.
Для эффективного анализа спектра важно изначально знать значения этих частот что позволит нам быстро и точно находить поврежденные элементы.
Для расчета необходимы следующие исходные данные:
Знание конструкции исследуемого механизма его конструктивных элементов таких как: зубчатые колеса муфты подшипники турбины крыльчатки и т.д. То есть необходимы чертежи оборудования с которых берутся данные.
Параметры конструктивных элементов.
- для зубчатого колеса муфты колеса вентилятора: количество зубьев (лопаток лопастей рабочего колеса и т.д.);
- для подшипника: диаметр тел качения угол контакта число тел качения внешний и внутренний диаметры подшипника;
- для муфты – число соединительных элементов: пальцев зубьев шариков и др.;
Оборотная частота в оборотах в минуту.
Формулы по которым ведется расчет:
- переводим единицы измерения оборотной частоты из оборотов в минуту в герцы путём деления исходного значения на 60;
- для зубчатого колеса муфты рабочего колеса с лопатками: умножаем оборотную частоту на число элементов: fповр = z×fвр. Для выходного вала-шестерни fповр = 47 · 7088 = 33314 Гц;
- для подшипников используем (определим информативные частоты для роликового цилиндрического двухрядного подшипника 426944):
- повреждения наружного кольца:
- повреждения внутреннего кольца:
- повреждения тел качения:
- повреждения сепаратора: fс = 05×fвр×(1 - d×cos b D)
где fвр – частота вращения вала (оборотная) fвр = 4253 обмин = 7088 Гц;
z – число тел качения z = 26 шт.;
d – диаметр тел качения d = 28 мм;
b – угол контакта b = 0;
D – диаметр окружности проходящей через центры тел качения D = 296 мм;
- ослабление посадки подшипников в корпусе определяется наличием субгармоник которые рассчитывают делением оборотной частоты на 2 3 4:
fсб = [fвр2 fвр3 fвр4].
3 Определение допустимых значений диагностических параметров
Виброскорость v - производная виброперемещения по времени. Этот параметр характеризует мощность колебатель-ного (вибрационного) процесса направленного на разрушение деталей и характеризует энергетическое воздействие на узлы объекта контроля (энергия колебания E=m×V22). Виброскорость – это скорость перемещения контролируемой точки оборудования. Виброскорость одновременно учитывает перемещение контролируемой точки и частоту колебаний вы-звавших вибрацию. Виброскорость измеряется в миллиметрах на секунду - ммсек. Виброскорость измеряют в частотном диапазоне 10 1000 Гц.
Допустимые значения вибрации определяются согласно ГОСТ ИСО 10816-1-97 «Вибрация. Контроль состояния машин по результатам измерений вибрации на невращающихся частях. Общие требования»
В нём рассматриваются критерии двух видов распространяющиеся на эксплуатационный контроль и приемочные испытания и предназначенные для оценки уровней вибрации машин различных типов. Критерий 1 связан со значениями измеряемых параметров вибрации а критерий 2 - с изменениями этих значений (независимо от направления изменений).
Нас интересует критерий 1. Критерий 1 связан с определением границ для абсолютного значения параметра вибрации соответствующих допустимым динамическим нагрузкам на подшипники и допустимой вибрации передаваемой вовне через опоры и фундамент. Максимальное значение полученное в результате измерения на каждом подшипнике или опоре сравнивают с границами четырех зон установленных исходя из международного опыта проведения исследований и эксплуатации. Данные зоны предназначены для качественной оценки вибрационного состояния машин и принятия решения о необходимых мерах.
Зона А. В эту зону попадают как правило новые машины только что введенные в эксплуатацию.
Зона В. Машины попадающие в эту зону обычно считают пригодными для дальнейшей эксплуатации без ограничения сроков.
Зона С. Машины попадающие в эту зону обычно рассматривают как непригодные для длительной непрерывной эксплуатации. Обычно данные машины могут функционировать ограниченный период времени пока не появится подходящая возможность для проведения ремонтных работ.
Зона D. Уровни вибрации в данной зоне обычно рассматривают как достаточно серьезные для того чтобы вызвать повреждение машины.
Предельные уровни вибрации
Как правило для машин предназначенных для длительной эксплуатации устанавливают предельные уровни вибрации превышение которых в установившемся режиме работы машины приводит к подаче сигналов ПРЕДУПРЕЖДЕНИЕ или ОСТАНОВ:
ПРЕДУПРЕЖДЕНИЕ - для привлечения внимания к тому что вибрация или изменения вибрации достигли определенного уровня когда может потребоваться проведение восстановительных мероприятий. Как правило при появлении сигнала ПРЕДУПРЕЖДЕНИЕ машину можно эксплуатировать в течение некоторого периода времени пока исследуют причины изменения вибрации и определяют комплекс необходимых мероприятий.
ОСТАНОВ - для индикации уровня вибрации при превышении которого дальнейшая эксплуатация может привести к повреждениям. При достижении уровня ОСТАНОВ следует принять немедленные меры к снижению вибрации или же остановить машину.
Согласно этого же ГОСТа машины делятся на классы по мощности и варианту установки:
Класс 1. Отдельные части двигателей и машин соединенные с агрегатом и работающие в обычном для них режиме (серийные электрические моторы мощностью до 15 кВт являются типичными машинами этой категории).
Класс 2. Машины средней величины (типовые электромоторы мощностью от 15 до 875 кВт) без специальных фундаментов жестко установленные двигатели или машины (до 300 кВт) на специальных фундаментах.
Класс 3. Мощные первичные двигатели и другие мощные машины с вращающимися массами установленные на массивных фундаментах относительно жестких в направлении измерения вибрации.
Класс 4. Мощные первичные двигатели и другие мощные машины с вращающимися массами установленные на фундаменты относительно податливые в направлении измерения вибрации (например турбогенераторы и газовые турбины с выходной мощностью более 10 МВт).
Как видно из определения клеть № 16 соответствует Классу 3 и определять допустимые значения вибрации будем согласно вышеозвученных определений (таблица 5.2).
Таблица 5.2 - Примерные границы зон для машин различных классов
Для клети рекомендуемые значения:
Зона А – виброскорость до 18 ммс;
Зона В – виброскорость в диапазоне 18 45 ммс;
Зона С – виброскорость в диапазоне 45 112 ммс;
Зона D – виброскорость выше 112 ммс.
Настоящий стандарт является базовым документом для разработки руководств по измерению и оценке вибрации машин. Критерии оценки для машин конкретных типов должны быть установлены в соответствии с условиями работы каждого механизма.
Учитывая сложную конструкцию большое количество зубчатых колёс различных узлов и деталей рекомендуется распределение зон выполнить следующим образом:
Зоны А и В – без изменений;
Зона D – свыше 71 ммс.
Виброускорение а – производная виброскорости по времени. Параметр характеризует силу инерции которая воздействует на объект при вибрации. Виброускорение характеризует силовое динамическое взаимодействие элементов агрегата. Виброускорение измеряется в метрах на секунду в квадрате – мсек2. Виброускорение измеряется при наличии вибрации в широкой полосе частот от 50 до 10000 Гц и более (чаще всего полосу обрезают до 50-4000 Гц). Эти измерения актуальны при виброакустической диагностике для оценки силы ударов и раннего обнаружения повреждений в подшипниках качения и зубчатых передачах.
Согласно ГОСТ 12.1.012-2004 «Система стандартов безопасности труда (ССБТ). Вибрационная безопасность. Общие требования» установлены следующие значения вибрации (виброускорения и виброскорости) (таблица 5.3).
Таблица 5.3 - Примерные границы зон для виброускорения
Для клети № 16 верхней границей виброускорения будет значение
Пик-фактор виброускорения
Суть метода Пик-фактора состоит в том что наличие даже зарождающихся дефектов либо отсутствие смазки при износе поверхностей качения в подшипнике приводит к появлению высокочастотных ударных импульсов и следовательно к увеличению уровней пиков амплитуд в высокочастотном сигнале вибрации при этом его среднеквадратичные уровни в общем случае могут даже оставаться неизменными.
Пик-фактор – это отношение пикового значения виброускорения к его среднеквадратичному значению:
В случае отсутствия ударных импульсов величина пик-фактора высокочастотной вибрации подшипника качения меньше 3-5 а при наличии ударных импульсов этот показатель может быть даже выше 10.
Контроль температуры является важным аспектом оценки технического состояния механического оборудования. До 95% всех форм энергии создаваемой и передаваемой машинами прямо или частично превращается в тепловую энергию. Параметром теплового диагностирования является температура отражающая протекание рабочего процесса и развитие целого ряда неисправностей оборудования.
Контроль температуры позволяет получить следующие диагностические параметры: 1) абсолютное значение в локальных точках; 2) разность температур масла или жидкости на выходе и входе; 3) интенсивность нарастания температуры при запуске; 4) определение цветов побежалости. Первые три параметра могут быть определены при эксплуатации механизма а последний – при остановке на осмотр.
Повышение температуры корпуса свыше 60°С зимой и 70°С летом говорит о проблемах в узлах.
ВЫБОР ДИАГНОСТИЧЕСКИХ ПРИБОРОВ
Прокатный стан состоит не только из оборудования включённого в линию прокатки но и дополнительного обеспечивающего его работу например насосы вентиляторы и пр. Также не на всё оборудование стана целесообразно ставить стационарную систему вибромониторинга. Кроме вибрации необходимо контролировать температуру уточнять состояние оборудования находящегося на контроле стационарной системы поэтому служба технической диагностики должна быть оснащена переносными приборами.
Стационарная система вибромониторинга
Рисунок 6.1 - Структура СВД «Корунд»:
6 – измерительные блоки; 2 – магистральный коммутатор; 3 – серверная стойка; 4 5 – удалённые рабочие места; 7 – клеммная коробка
Система вибродиагностики предназначена для мониторинга технического состояния и автоматической диагностики клетей по вибрации температуре току и другим технологическим параметрам и представляет собой совокупность первичных преобразователей соединенных кабельными линиями с блоком связи и далее с серверным рабочим местом оператора. Данные от первичных преобразователей поступают на измерительные блоки для первичной обработки конвертации и передачи по стандартному протоколу TCP на серверное рабочее место. Сбор математическую обработку отображение и хранение производят на серверном автоматизированном рабочем месте (АРМ) оператора с помощью программного обеспечения сборщика данных (рисунок 6.1).
Система непрерывного мониторинга прокатного оборудования обеспечивает наблюдение за техническим состоянием механизмов в режиме реального времени. Автоматическая диагностика агрегатов осуществляется с интервалом времени меньшим чем период развития возможных неисправностей. В защитном мониторинге оборудования используются предельные пороговые значения вибрации установленные на основе анализа инцидентов произошедших на конкретных агрегатах. Данный подход обеспечивает своевременное обнаружение неисправностей отслеживание их развития и оперативное оповещение обслуживающего персонала о необходимости проведения ремонтных мероприятий.
Программное обеспечение СВД представляет собой комплекс программных средств работающий во взаимодействии с аппаратными модулем СМ-8 предназначенным для оперативной оценки технического состояния оборудования и выявления вероятных дефектов и неисправностей в процессе эксплуатации.
Система диагностирования работает в автоматическом («Сервер АРМ») и интерактивном (диалог с оператором — «Диагностика АРМ») режимах. Диалог с системой осуществляется через систему меню.
Анализ данных в приложении «Сервер АРМ» осуществляется в автоматическом режиме четыре раза в сутки работает независимо от приложения «Диагностика АРМ» [7–14]. На автоматизированном рабочем месте диагноста можно выбрать любую клеть и выполнить внеочередную проверку нажатием клавиши «Определение состояния». В приложении «Диагностика АРМ» представлены все диагнозы для выбранной клети выполненные системой за прошедший период времени.
В диагнозе отражены: виды и степень развития обнаруженных дефектов для каждого подшипника иили зубчатой передачи; соответствие уровня вибрации клети установленным нормативным требованиям как в процессе прокатки так и в режиме холостого хода; эксплуатационный ресурс. Диагноз формируется в автоматическом режиме по результатам диагностирования прямого спектра и спектра огибающей расчета эксцесса пик-фактора в соответствии с решающими правилами. Результаты диагностирования и актуальные уровни вибрации учитываются при определении эксплуатационного ресурса узлов и клети в целом.
В программе используется алгоритм автоматического слежения за скоростью вращения оборудования и оперативного выбора участков во временном сигнале (с минимальным отклонением оборотов 1 %) для преобразования в спектр. Для инженеров-диагностов предусмотрены дополнительные функции ручного анализа: 13-октавный спектр вейвлет-анализ кепстр взаимный спектр разнообразные виды статистической обработки. Приложение «Отчет» формирует текстовый документ о текущем техническом состоянии оборудования по результатам диагностики с указанием актуальных уровней вибрации схемы агрегата обнаруженных дефектов или неисправностей допустимого эксплуатационного ресурса клети и рекомендации по устранению обнаруженных неисправностей или дефектов.
Данные приборы должны совмещать в себе удобство (небольшой вес возможность обслуживания одной рукой удобный экран отсутствие избыточных функций) малогабаритный и удобный в установке датчик вибрации и иметь возможность гибкого изменения настроек для предварительной диагностики (частотный диапазон количество линий и пр.).
Прибор данного типа должен проводить замеры с выводом на экран и сохранением в памяти:
- скз и пик виброскорости (в диапазоне 2 4 000 Гц (число и спектр);
- скз и пик виброперемещения в диапазоне 2 400 Гц (число и спектр);
- скз и пик виброускорения в диапазоне 10 10 000 Гц (число и спектр);
- получение временного сигнала (спектр);
- работать в режиме виброметра.
Остальные характеристики для предварительной диагностики непринципиальны и их наличие зависит от пожеланий специалиста либо руководителя службы.
Одним из лучших приборов отвечающим всем вышеперечисленным требованиям является виброметр с анализатором спектра вибрации 795MC911 производства компании ПП "НПП ОНТЕСТ" (Украина):
- 2 канала измерения вибрации (виброускорения виброскорости виброперемещения);
- 1 вход таходатчика предусмотрена возможность подключения лазерных измерительных головок для центровки механизмов.
- от 2 до 18000 Гц в двухканальном режиме;
- от 2 до 36000 Гц в одноканальном режиме.
- Разрешение анализатора линий- 100 200400800160032006400.
Программа динамической балансировки механизмов. Тестер подшипников и тахометр. Память – встроенный диск 2 МБ и сменные карты SD до 1 GB (micro SD). Стандартная файловая система. Интерфейс USB
Анализатор спектра вибрации 795С911 – малогабаритный автономный микропроцессорный виброизмерительный анализатор с двойным питанием – от внутренних аккумуляторов или от сетевого блока питания. Предназначен для измерения и спектрального анализа параметров вибрации балансировки и наладки механизмов роторного типа.
Анализатор позволяет измерять динамические сигналы с последующей их записью в энергонезависимую память просматривать анализировать и передавать их в базу данных на персональный компьютер (ПК).
Анализатор может работать как автономный анализатор и как коллектор данных в системе прогнозируемого обслуживания оборудования совместно с программным обеспечением.
Рисунок 6.2 – Виброметр с анализатором спектра вибрации 795MC911
Технические характеристики:
Единицы измерения частоты Гц
Минимальный диапазон рабочих частот2.0
Максимальный диапазон рабочих частот10000.0
Минимальный диапазон измерения ускорения2.0 (мс²)
Максимальный диапазон измерения ускорения10000.0 (мс²)
Минимальный диапазон измерения скорости2.0 (ммс)
Максимальный диапазон измерения скорости1000.0 (ммс)
Минимальный диапазон измерения смещения2.0 (мкм)
Максимальный диапазон измерения смещения1000.0 (мкм)
Количество каналов измерения2
В несомненные достоинства прибора следует включить гибкую систему настроек позволяющую производить измерения в любом доступном их сочетании (в отличие от большинства приборов других производителей).
Так же для регулярного контроля необходимо иметь возможность контроля температуры оборудования.
Тепловизор – прибор достаточно дорогой капризный и в большинстве случаев ненадёжной тепловизионной матрицей. Для удешевления конструкции производитель закупает матрицы на базе диодов из аморфного кремния которые не переносят высокотемпературных объектов (в том числе прямых солнечных лучей). Поэтому я бы рекомендовал не скупиться а приобрести тепловизор с матрицей основанной на базе диодов из оксида ванадия. Такие (по заверению производителя) выпускает компания FLUKE. Например тепловизор FLUKE TIS40 обладающий куда более высокой стойкостью (до 30 минут направления на Солнце).
Рисунок 6.3 – Тепловизор FLUKE TIS40
Некоторые характеристики:
- диапазон измерения температуры: от -20 °C до +350 °C;
- 35 дюйма ЖК-дисплей 320
- цифровая камера промышленного уровня с разрешением 5 мегапикселей;
- 4 ГБ внутренней памяти и 4 ГБ на дополнительной карте памяти;
- возможность съёмки видео.
Есть ещё ряд приборов и устройств которые необходимы предприятию и службе диагностики но для начального этапа становления службы достаточно этого базового набора.
ОРГАНИЗАЦИЯ СЛУЖБЫ ДИАГНОСТИКИ
Учитывая то что обслуживание отдельного стана – лишь частный случай то служба технической диагностики предприятия должна организовываться на базе межцеховой или надцеховой службы. Идеальным вариантом является отдел главного механика (ОГМ) предприятия как служба. контролирующая состояние оборудования и обеспечивающая подготовку и проведение ремонтов.
Для обслуживания оборудования стана и контроля состояния его оборудования на начальном этапе становления службы достаточно одного грамотного специалиста.
Это должен быть инженер с профильным образованием и опытом диагностики и наладки роторного оборудования не менее десяти лет годный по состоянию здоровья.
В случае расширения службы требования к вновь принятым в плане опыта могут быть существенно снижены вплоть до его отсутствия. Важно наличие базового образования. Так же возможен приём на должность специалиста по диагностике человека со средне-техническим образованием. но со стажем работы в ремонте и наладке роторного оборудования не менее десяти лет.
Специалист по диагностике подчиняется непосредственно Главному механику (начальнику ОГМ) для ускорения передачи информации о состоянии оборудования исключения её искажения или сокрытия и возможности оперативного вмешательства в производственный процесс для предотвращения аварийных ситуаций.
В обязанности специалиста входят:
- регулярный обход оборудования с выполнением замеров и осмотров получение информации о неполадках от дежурного персонала и стационарной системы диагностики.
- доведение текущего состояния до руководителей участков цехов и подразделений.
- обработка полученной информации определение состояния оборудования локализация проблемных узлов и диагностирование причин неполадок.
- составление технических отчётов с численными значениями вибрации их расшифровкой указанием проблем и выдачей рекомендаций по их устранению.
- составление предписаний на устранение проблем или остановку оборудования с передачей их Главному механику (начальнику ОГМ) для их передачи в цеха и отделы заведующие проблемным оборудованием.
- контроль выполнения работ по выданным рекомендациям в отчётах и предписаниях.
- выполнение внеплановых работ по диагностике и наладке оборудования не включённого в график обходов.
- участие в наладке оборудования где квалификация ремонтного персонала недостаточна.
Графики обхода составляются в зависимости от заявок цехов и возможности персонала службы диагностики обеспечивать контроль заявленного объёма оборудования (таблица 7.1).
Так же следует отметить что не всё оборудование возможно контролировать из соображений безопасности и особенностей конструкции. Так вертикальные редукторы комбинированных клетей во время работы недоступны для персонала из-за непосредственной близости лестниц к прокатываемой заготовке. Часть насосов конструктивно выполнены так что корпусные детали на которые необходимо устанавливать датчики для контроля расположены под внешним корпусом. Подшипники редукторов клетей расположенные со стороны обращённой к прокатным клетям расположены рядом с промежуточными валами и недоступны с точки зрения обеспечения безопасности. Часть оборудования включается краткосрочно (5-15 с) и приборный контроль их состояния крайне затруднён.
Для стана 390 в условиях Макеевского металлургического завода список и периодичность контроля оборудования выглядит следующим образом.
Оборудование цеха прокатного передела (ЦПП).
Виброакустическая диагностика:
- Прокатные клети 1-18 – приводные двигатели и
подшипники редуктора со стороны двигателя..1 разнед.
- Вентиляторы нагревательной печи 2 шт ежедневно
- Насосы К200-150-400 9 шт 1 разнед.
- Насосы ГРАТ 35040-II-16 4 шт 1 разнед.
- Насосы WKF насосной ТЗУ 4 шт ежедневно
Акустический контроль:
- Приводы БПУ линии 100 и линии 200 2 размес.
- Электродвигатели реечного стеллажа 2 шт 2 размес.
- Электродвигатели клапанов перегородок 2 шт 2 размес.
- Электродвигатель цепей и передающего
устройства холодильника 2 шт 2 размес.
- Электродвигатель подъёма передающего
устройства холодильника 2 размес.
-Электродвигатели ножниц 51 52 53 55 6 шт 2 размес.
- Редуктора приводов оборудования участка
холодильника: приводы шиберов и перегородок..2 размес.
- Привода секций реечного стеллажа редуктора качания реек2 размес.
- Редуктора приводов передаточного устройства холодильника2 размес.
Оборудование цеха энергообеспечения (ЦЭО).
Участок оборотного цикла стана 390 насосная станция "Батман
- Насосы LS 150-500 S1NL1-16004 6 шт 2 размес.
- Насосы LS 125-500 S1NL1-9004 6 шт 2 размес.
- Насосы LS 125-500 S1NL1-13204 5 шт 2 размес.
- Насосы L 150-315 U1NN-3004 5 шт 2 размес.
- Насосы L 125-315 U1-2204 5 шт 2 размес.
Таблица 7.1 - ОБРАЗЕЦ ГРАФИКА проведения мониторинга и диагностики состояния оборудования с помощью портативного виброизмерительного прибора
и акустического контроля в цехах Филиала № 3 ММЗ на июнь 2020 г.
Наименование оборудования
Прокатные клети 1-18
Вентиляторы нагревательной печи 2 шт.
Насосы К200-150-400 9 шт.
Насосы ГРАТ 35040-II-16 4 шт.
Насосы WKF насосной ТЗУ 4 шт.
Приводы БПУ линии 100 и линии 200
Электродвигатели реечного стеллажа 2 шт.
Электродвигатели клапанов перегородок 2 шт.
Электродвигатель цепей и передающего устройства холодильника 2 шт.
Электродвигатель подъёма передающего устройства холодильника
Электродвигатели ножниц 51 52 53 55 6 шт.
Редуктора приводов оборудования участка холодильника: привод шиберов и перегородок
Привода секций реечного стеллажа редуктора качания реек
Редуктора приводов передаточного устройства холодильника
ЦЭО участок оборотного цикла стана 390 "Батман
Насосы LS 150-500 S1NL1-16004 6 шт.
Насосы LS 125-500 S1NL1-9004 6 шт.
Насосы LS 125-500 S1NL1-13204 5 шт.
Насосы L 150-315 U1NN-3004 5 шт.
Насосы L 125-315 U1-2204 5 шт.
в – вибродиагностика; а – акустический контроль.
Принципы обработки информационных потоков.
Информационный поток – это совокупность циркулирующих в логистической системе между логистической системой и внешней средой сообщений необходимых для управления анализа и контроля логистических операций. Информационный поток может существовать в виде бумажных и электронных документов (носителей).
Информационными потоками называют физические перемещения информации от одного сотрудника предприятия к другому или от одного подразделения к другому.
Любая логистическая система состоит из совокупности элементов-звеньев между которыми установлены определенные функциональные связи и отношения. Непосредственно рабочим звеном информационной системы может быть автоматизированное рабочее место управленческого персонала информационное подразделение системы управления организацией или обособленная группа управленческих работников объединенных общностью выполняемых информационных функций.
Используемое на предприятии информационное обеспечение можно разделить на первичное и вторичное.
К первичным функциям относятся следующие: организация массивов информации; организация потоков информации; организация процессов и средств сбора хранения обработки и транспортировки информации.
При организации потоков информации выполняются следующие управленческие процедуры:
Определение источников и потребителей информации в соответствии со специальными функциями и задачами управления. Источник информации – результаты осмотров и диагностики оборудования в ходе плановых обходов специалиста по диагностике и дежурного персонала стана.
Определение состава информации периодичности её циркуляции и форм представления. Состав информации – техническое состояние оборудования определённое в результате обработки ранее полученной информации.
Разработка документооборота. Этот этап стоит в стороне от предыдущих и выполняется различными специалистами: инженером по диагностике и специалистами цехов и отделов в ведении которых находится контролируемое оборудование.
Использование комплекса технических средств для организации потоков информации. Сюда входят диагностические комплексы приборы и приспособления для сбора информации персональный компьютер для её обработки и и оформления в виде документов принтер для печати готовых документов и средства электронной коммуникации для передачи этих документов заинтересованным лицам.
Установление порядка составления оформления регистрации согласования и утверждения документов. Для этого разрабатываются Положения и Инструкции включающие в себя пункты по распределению обязанностей между участниками информационного потока.
Вторичными функциями подсистемы информационного обеспечения является обеспечение управленческого персонала научно-технической информацией о новейших отечественных и зарубежных достижениях науки техники экономики технологии производства передовом отечественном и зарубежном опыте в области управления.
Для этого должны организовываться посещения различных учебных мероприятий организуемым ВУЗами и производителями современного оборудования.
В настоящее время возможны три варианта организации подсистемы информационного обеспечения на предприятиях: централизованный; децентрализованный; специализированный.
При централизованном способе организации вся деятельность по информационным технологиям сосредоточена в одном управлении (подразделении) и подчиняется непосредственно высшему руководству компании ответственному за информационные системы и технологии.
Преимуществом централизованного способа организации является обеспечение высокой эффективности работы по внедрению новых информационных систем и технологий. К недостаткам можно отнести высокие затраты на содержание аппарата управления.
При децентрализованном способе организации подсистемы информационного обеспечения специалисты разных функциональных подразделений выполняют функции управления информационными системами каждый в своем направлении.
Преимуществом такого способа организации является высокий уровень знаний предметной области менеджера по информационным системам недостатком – дублирование однотипных задач и функций в разных подсистемах.
При специализированном способе организации отсутствует подразделение по информационным системам (технологиям). При необходимости внедрения автоматизированной системы данные организации обращаются в специализированные фирмы и выполняют работы на договорной основе. Это характерно для небольших организаций которые не могут иметь собственных специалистов в области информационных технологий занятых полный рабочий день и прибегают к услугам консультантов.
Преимуществом данного способа организации подсистемы информационного обеспечения является высокий уровень научных и методических разработок недостатком – сложность учета всех специфических особенностей объекта.
Для эффективного функционирования службы технической диагностики более всего подходит централизованный способ но с подчинением не руководителю предприятия а Главному механику (начальнику ОГМ). Так как именно он занимается непосредственным обеспечением безаварийной работы и от его решений эта работа зависит.
Примерную организацию информационных потоков службы диагностики применительно к её организации для обслуживания стана 390 Макеевского металлургического завода можно посмотреть на иллюстрации ниже (рисунок 7.1).
Цеха и отделы выдают заявки на контроль оборудования.
Инженер по диагностике составляет график согласовывает его с Главным механиком (начальником ОГМ) и руководителями заинтересованных подразделений.
Главный механик (начальник ОГМ) выдаёт задание инженеру по диагностике.
Инженер проводит регулярные обходы оборудования со сбором диагностической информации.
По результату обхода устно сообщает руководителям участков информацию о состоянии оборудования.
Составляет технические отчёты и предписания (при необходимости).
Рассылает их в электронном виде Всем заинтересованным сторонам.
Печатает отчёты и предписания.
Предписания передаёт Главному механику (начальнику ОГМ) для дальнейшей передачи их руководителям цехов и отделов.
Отчёты подписывает у руководителей цехов и отделов для дальнейшего их архивирования.
Рисунок 7.1 – Организация информационных потоков службы диагностики стана 390:
– заявки от цехов и отделов; 2 – задание инженеру по диагностике;
– получение диагностической информации и её обработка;
– устный отчёт руководителям участков о состоянии оборудования;
– готовые отчёты и предписания в электронном виде; 6 – бумажные отчёты;
– бумажные предписания на устранение замечаний
ОХРАНА ТРУДА И ТЕХНИКА БЕЗОПАСНОСТИ.
1 Охрана труда и техника безопасности
Стан разделён на участки по выполняемым операциям:
- склад заготовок с загрузочными решётками и рольгангами для подачи заготовки в печь;
- нагревательная печь;
- участок прокатки с прокатными клетями и ножницами горячей резки;
- участок термического упрочнения;
- участок холодильника с рольгангами правильной машиной и ножницами холодной резки;
- адьюстаж с пакетир-машинами и складом готовой продукции.
На всех этих участках есть как общие вредные и опасные факторы присущие всему производству так и индивидуальные. присущие конкретным выполняемым операциям.
Опасные и вредные производственные факторы прокатного производства подразделяются на три группы: физические химические и психофизиологические.
К физическим опасным производственным факторам в прокатном производстве относятся:
- подвижные машины и механизмы; подвижные части оборудования; движущиеся изделия заготовки материалы (валки шпиндели муфты станов выбросы петли прокатываемого материала осколки прокатываемого металла отлетающие окалина и шлаки);
- повышенная температура поверхностей;
- повышенное значение напряжения в электрической сети;
- острые кромки заусеницы и шершавость на поверхностях заготовок инструментов и оборудования;
- высокая вероятность возможности возгорания.
К физическим вредным производственным факторам относят:
- повышенную запыленность воздуха;
- повышенные температуру и влажность воздуха рабочей зоны;
- сниженную подвижность воздуха;
- повышенный уровень инфракрасной радиации;
- повышенный уровень шума инфразвукових колебаний ультразвука и вибрации;
- повышенный уровень электрических магнитных и электромагнитных излучений;
- недостаточную освещенность рабочей зоны повышенную яркость света и сниженную контрастность.
Химические производственные факторы.
Выделение вредных веществ в воздух (токсичной пыли газов) происходит при проведении технологических процессов проката металла и проведении работ связанных с применением химических веществ и материалов (смазка техническое масло и др.). При прокате металла наиболее возможное проникновение в организм веществ в виде пара и пыли через органы дыхания (около 95 % всех отравлений).
Наиболее характерными психофизиологическими факторами для прокатного производства является высокая скорость технологических процессов и интенсивность грузопотоков которая обуславливает в свою очередь высокую интенсивность работы персонала. Это приводит к большому умственному утомлению которое связано с ошибками в управлении механизмами и возникновение опасных ситуаций т.е. преобладают нервно-психические перегрузки.
Рассмотрим наиболее важные производственные факторы прокатного производства.
Пыль является наиболее распространенным неблагоприятным фактором производственной среды. В металлургическом производстве преобладает пыль которая содержит оксиды железа кремния марганца фтористые соединения и др. В воздухе у станов горячей прокатки металла содержание пыли окислов железа достигает 2400–4400 мгм3.
Микроклимат в прокатных цехах определяется наличием чрезмерного конвекционного и лучистого тепла в связи с чем они относятся к группе горячих цехов. Источниками тепла являются прокатываемый металл нагретые оборудование механизмы и коммуникации открытые отверстия или крышки нагревательных устройств горючие газы.
Лучистая энергия на расстоянии 1 м от проката составляет до 4-5 калл см2в минуту. Двигаясь по цеху прокат на своем пути нагревает все металлическое оборудование при этом нагретые предметы сами становятся источником тепла и быстро нагревают воздуха.
Метеорологические условия в прокатных цехах характеризуются также наличием участков с высокой и низкой влажностью воздуха что отрицательно влияет на самочувствие и здоровье человека.
В прокатных цехах к шумоопасному оборудованию относятся рабочие клети машины огневой зачистки металла ножницы для резания металла маятниковой дисковые пилы правильные машины; моталки шлепперы рольганги и др.
Основным источником шума является прокатный стан в котором находится огромное количество металлических механизмов. Основной шум прокатного цеха лежит в области частот до 1000 Гц и имеет значение звукового давления в пределах 75–95 дБ и может достигать 110 дБ.
Инфразвук возникает за счет тех же процессов что и шум слышимых частот. Прокатные станы (конструкции с плоскими поверхностями большой площади и малой жесткости) создают условия для генерации инфразвука. Инфразвук при прокате металла имеет постоянный характер.
Максимальные уровни низкочастотных акустических колебаний от промышленных источников в прокатном цехе достигают 100–110 дБ.
В условиях прокатного производства наблюдается местная (локальная) и общая вибрации. Прокатные станы (система механизмов) при своей работе создают общую вибрацию которая заключается в отклонении рабочих мест от положения равновесия на малую величину.
Длительное воздействие вибрации высоких уровней на организм человека приводит к развитию преждевременного утомления снижению производительности труда росту заболеваемости и нередко к возникновению профессиональной патологии – вибрационной болезни.
В прокатном производстве применяется огромное количество разнообразного электрооборудования оказывающего опасное воздействие на работников (электрические поля промышленной частоты и электромагнитные поля высокой частоты).
Длительное воздействие электрического поля на организм человека может вызвать нарушение функционального состояния нервной и сердечно-сосудистой систем. Это выражается в повышенной утомляемости снижении качества выполнения рабочих операций болях в области сердца изменении кровяного давления и пульса. Длительное воздействие токов высокой частоты на различные системы организма человека по последствиям имеют многообразные проявления.
Правильное освещение рабочих мест прокатных цехов имеет большое значение для создания безопасных условий работы: неудовлетворительное освещение негативно влияет на зрение работников может стать причиной травматизма. Равномерное распределение яркости в условиях прокатного производства не достигается. Вследствие образования огромного количества пыли наблюдается ухудшение видимости и уменьшается обзор. Чрезмерная ослепительная яркость металлических деталей нарушает условия комфортного зрения ухудшает контрастную чувствительность.
Пожарная и взрывная опасность прокатного производства определяется следующими факторами:
- наличием широко развитой сети кабельного хозяйства большого количества масла в масло-эмульсионных подвалах сети масляных гидроприводов;
- применением горючих (взрывоопасных) газов в нагревательных печах и колодцах при резании металла взрывоопасный водород образовывается в травильных ваннах при обработке металла взрывоопасного защитного газа при отжиге металла в безкислородной среде.
Для защиты от этих факторов разрабатываются и применяются коллективные и индивидуальные меры защиты.
Коллективные меры защиты
Главной мерой коллективной защиты является автоматизация и механизация процессов позволяющая сократить число работников подвергающихся воздействию вредных и опасных факторов. А так же внедрение следующих мер защиты.
К мерам коллективной защиты работающих относятся меры которые конструктивно или функционально связаны с производственным процессом или оборудованием. Они как правило предназначены для защиты любого работника находящегося в рабочей зоне.
Методы защиты от шума:
- уменьшение шума машин у его источника;
- внедрение новых технологических бесшумных процессов;
- дистанционное управление шумными машинами и механизмами;
- внедрение звукоизолирующих кожухов кабин укрытий;
- блокировка выключающая генератор шума при нарушении звукоизоляции;
- установка акустических экранов;
- звукопоглощение методом перехода шумовой энергии в тепловую;
- применение способов индивидуальной защиты;
- выбор рационального режима работы и отдыха сокращение времени пребывания работающих в шумных условиях;
- лечебно-профилактические меры.
Для защиты органов дыхания работников от пыли в рабочей зоне на промышленных предприятиях можно применить:
- очистку воздуха рабочей зоны механической вентиляцией;
- подачу в рабочую зону очищенного воздуха;
- использование местной вытяжной вентиляции дистанционное управление технологическим процессом;
- монтаж у источника пыли вододушевой установки (экрана);
- применение средств индивидуальной защиты.
Для защиты от вибрации.
- применение приспособлений для гашения колебаний при вибрации оборудования до гранично-допустимого;
- дистанционное управление вибрирующими машинами оборудованием;
- улучшение статической и динамической балансировки движущихся частей;
- замена металлических частей машин пластмассовыми;
- укрытие вибрирующих поверхностей материалами с очень большим внутренним трением (резиной битумом поролоном и т.д.);
- установка оборудования на специальные виброизоляторы;
- виброизоляция рабочего места;
- применение средств индивидуальной зашиты.
Так же к коллективным средствам безопасности относят оградительные предохранительные тормозные устройства оградительные устройства устройства автоматического контроля и сигнализации дистанционного управления знаки безопасности.
Индивидуальные меры защиты.
Средства индивидуальной защиты (СИЗ) средства используемые работником для предотвращения или уменьшения воздействия вредных и опасных производственных факторов а также для защиты от загрязнения. Применяются в тех случаях когда безопасность работ не может быть обеспечена конструкцией оборудования организацией производственных процессов архитектурно-планировочными решениями и средствами коллективной защиты.
В зависимости от назначения СИЗ подразделяют на классы:
- костюмы изолирующие;
- средства защиты органов дыхания;
- одежда специальная защитная;
- средства защиты ног;
- средства защиты рук;
- средства защиты головы;
- средства защиты лица;
- средства защиты глаз;
- средства защиты органа слуха;
- средства защиты от падения с высоты и др. предохранительные средства;
- средства дерматологические защитные;
- средства защиты комплексные.
Учитывая разнообразие вредных и опасных факторов на стане в различных случаях применяются все вышеперечисленные СИЗ.
Гигиена труда устанавливает нормы и требования выполнение которых необходимо для создания здоровых условий труда и рассматривает вопросы устройства оборудования и содержания производственных помещений и предприятий в целом. Применительно к производственным помещениям производственная санитария разрабатывает требования к отоплению освещению вентиляции и т. д.
Рабочее место организуют с учетом вида выполняемых работ. На рабочем месте должны быть предусмотрены устройства и приспособления для работы хранения инструмента посуды приборов материалов запасных частей – верстаки стеллажи этажерки тумбочки. Для работы с тяжелыми предметами рабочее место оборудуют подъемно-транспортными устройствами. В случае выполнения операций сопровождающихся выделением пыли паров газов рабочее место оборудуется общей или местной вентиляцией: вытяжные шкафы приспособления для местного отсоса пыли газов.
Чтобы легче было распознавать опасные объекты используют предохранительные цвета. Так опасные детали машин окрашивают в черный цвет с желтыми полосами внутренние поверхности опасных зон окрашивают в красный цвет. Кнопки управления оборудованием например «Пуск» окрашивают в зеленый цвет а кнопку остановки «Стоп» – в красный.
Для сохранения здоровья и работоспособности работников важное значение имеет режим отдыха и питания. В течение рабочего дня (смены) работнику предоставляется перерыв для отдыха и питания продолжительностью 30 минут который в рабочее время не включается. На работах где по условиям производства (работы) предоставление перерыва для отдыха и питания невозможно работодатель обеспечивает работнику возможность отдыха и приема пищи в рабочее время. Перечень таких работ а также места для отдыха и приема пищи установлены правилами внутреннего трудового распорядка.
Работникам работающим в холодное время года на открытом воздухе или в закрытых необогреваемых помещениях а также грузчикам занятым на погрузочно-разгрузочных работах и другим работникам в необходимых случаях предоставляются специальные перерывы для обогревания и отдыха которые включаются в рабочее время. Работодатель обязан обеспечить оборудование помещений для обогревания и отдыха работников.
На работах с вредными условиями труда работникам выдаются бесплатно по установленным нормам молоко.
На предприятии по установленным нормам оборудуются санитарно-бытовые помещения помещения для приема пищи помещения для оказания медицинской помощи комнаты для отдыха в рабочее время и психологической разгрузки; создаются санитарные посты с аптечками укомплектованными набором лекарственных средств и препаратов для оказания первой медицинской помощи; устанавливаются аппараты (устройства) для обеспечения работников горячих цехов и участков газированной соленой водой и др.
К медико-профилактическим и санитарно-гигиеническим мероприятиям относятся также медицинские осмотры имеющие целью не допустить к работе лиц которым работа с вредными условиями по медицинским показаниям запрещена (больные склонные к аллергическим заболеваниям перенесшие хирургическую операцию и т. д.).
Стирка ремонт и обезвреживание спецодежды должны производиться централизованно.
На производствах где возможно загрязнение спецодежды пылью должны предусматриваться устройства для ее обеспыливания исключающие поступление пыли в окружающую среду а также на внутреннюю поверхность спецодежды и кожу работающих.
Цеха должны обеспечиваться банями.
Эффективность внедрения мероприятий может выражаться инженерно-техническими социальными социально-техническими социальными социально-экономическими и экономическими показателями.
Социальная эффективность мероприятий по охране труда позволит:
- увеличить количество работающих для которых условия труда соответствуют нормативным требованиям;
- снизить травматизм и заболеваемость;
- сократить текучесть кадров из-за неудовлетворительных условий труда.
Некоторые социальные показатели могут быть выражены в данной форме а также через рабочее время. Такие показатели называются социально-экономические.
Экономические результаты мероприятий по охране труда выражаются в экономии живого или общественного труда:
- снижение потерь связанных с утратой трудоспособности по травматизму и заболеваемости
- прибыль полученную увеличением производительности труда связанной с улучшением медико-биологических и технических условий
- снижение потерь за счет уменьшения текучести кадров
- снижение издержек связанных с обеспечением льгот для работающих во вредных условиях
- снижение расходов на ликвидацию аварий пожаров.
Гражданская оборона на промышленном объекте организуется с целью защиты персонала объекта и населения проживающего вблизи от него от чрезвычайных ситуаций природного техногенного и военного характера.
Основными задачами ГО на объекте являются:
- защита персонала объекта и населения от ЧС;
- повышение устойчивости функционирования объекта в ЧС;
- проведение аварийно-спасательных и других неотложных работ в очагах поражения и зонах катастрофического затопления.
Организационные мероприятия предусматривают разработку и планирование действий руководящего командно-начальствующего состава отдела по делам ГОЧС служб и формирований ГО по защите персонала объекта проведению аварийно-спасательных и других неотложных работ.
Инженерно-технические мероприятия ГО – это комплекс мероприятий осуществляемых инженерно-техническими методами и средствами и направленных на предотвращение или уменьшение возможных потерь и разрушений повышение устойчивости работы объекта в чрезвычайных ситуациях.
Экономические мероприятия предусматривают такой подход к выполнению всего комплекса работ который обеспечил бы их эффективность при минимальных капитальных затратах.
Экологические мероприятия представляют собой продолжение комплекса работ данного направления которые должны вестись каждым объектом с целью максимально возможного уменьшения вредного воздействия продуктов технологического цикла на окружающую среду.
За организацию защиты персонала объекта и населения от ЧС отвечает система гражданской обороны объекта.
Начальником гражданской обороны объекта является его руководитель. Он подчиняется ведомству а в оперативном отношении начальнику гражданской обороны города на территории которого расположен объект.
На крупных промышленных объектах как правило есть штатный заместитель начальника гражданской обороны который в мирное время является основным организатором всех подготовительных мероприятий по гражданской обороне.
Заместителем начальника гражданской обороны по рассредоточению и эвакуации персонала назначается обычно заместитель руководителя объекта по общим вопросам. Он разрабатывает план рассредоточения работающего персонала и их семей организует подготовку мест в загородной зоне перевозку туда людей.
Заместителем начальника ГО по инженерно-технической части назначается главный инженер предприятия который непосредственно руководит службами а также осуществляет техническое руководство аварийно-спасательными и другими неотложными работами.
Заместителем начальника ГО по материально-техническому снабжению назначается заместитель руководителя объекта по этим вопросам руководящий службой материально-технического снабжения.
На всех объектах как правило создаются отделы по делам ГО и ЧС которые комплектуются из должностных лиц. Для решения задач возлагаемых на ГО на объектах располагающих соответствующей базой создаются следующие службы:
- оповещения и связи;
- охраны общественного порядка;
- аварийно-техническая;
- энергетики и светомаскировки;
- радиационной и химической защиты;
РАСЧЁТ ЭКОНОМИЧЕСКОГО ЭФФЕКТА
ОРГАНИЗАЦИИ СЛУЖБЫ ДИАГНОСТИКИ
Экономический эффект представляет собой конечный экономический результат который получен от внедрения определенного мероприятия. Мероприятия должны вызывать улучшение определенной работы предприятия. Результат представляет собой абсолютный показатель и может быть измерен в денежных единицах. В целом получатель эффекта предполагает первоначально осуществить определенные затраты впоследствии получить дополнительный доход от проведенных мероприятий.
Исходные данные (цены по данным на 2018 год простои – 2016 год):
Объём произведенной продукции V т 606400
Себестоимость продукции S тыс. рубт 26548
Стоимость простоя стана sпр тыс. рубчас 140
Количество аварийных простоев Т часгод 136
простой по причине разрушения подшипника
электродвигателя клети № 9 Т1 час 6
простои по причине разрушения валков клети № 1Т2 час..15
простои по причине разрушения подшипников насосов* Т3 час.52
простои по причине разрушения ножей ножниц
холодной резки Т4 час 12
простой по причине разрушения зубчатого вала
ножниц холодной резки Т5 час 10
редуктора клети № 11 Т6 час 6
простои по причине нарушения технологии Т7 час 35
* - большое количество аварий вызвано запредельным износом оборудования
Затраты на ликвидацию аварий Zав:
Стоимость изготовления вала насоса S2тыс. руб 145
Количество изготовленных валов n1 шт 8
Стоимость изготовления разрушенной
секции насоса S3 тыс. руб 23
Количество изготовленных секций n1 шт 1
Стоимость подшипника QJ330 N2MA
электродвигателя S4 тыс. руб 1239
Количество приобретённых подшипников n1 шт..1
Затраты на организацию службы диагностики Zсл:
Оклад инженера по тех. диагностике
категории Sо тыс. рубмес 115
Среднемесячная премия Sпр % к окладу 123
Стоимость приобретения и установки стационарной
системы диагностики «КОРУНД» SК тыс. руб 950
Стоимость приобретения виброанализатора
5С911 Sвиб тыс. руб 95
Стоимость приобретения тепловизора
FLUKE TIS40 Sтеп тыс. руб 55
Срок эксплуатации приборов лет 10
Из всех простоев стана служба диагностики предотвращает простои Т1 Т3 Т6 Т7 и все перечисленные затраты на ликвидацию аварий.
Для оценки экономической эффективности рассчитаем экономический эффект от затрат на приобретение оборудования введения новой штатной единицы (инженера по тех. диагностике 1 категории) и предотвращения части аварий.
Годовая себестоимость произведенной продукции:
Р = S * V = 26548 * 606400 = 16098707200 руб. = 160987 млн. руб.
Потери из-за простоев предотвращаемых службой диагностики:
Zпр = (Т1 + Т3 + Т6 + Т7) * sпр = (6 + 52 + 6 + 35) * 140 = 13860 тыс. руб.год
Затраты на ликвидацию аварий:
Zав = Sn*nn = 145 * 8 + 23 * 1+ 1239 * 1 = 2629 тыс. руб.год
Общая сумма потерь от аварий предотвращаемых службой диагностики:
Zпот = Zпр + Zав = 13860 + 2629 = 141229 тыс. руб.год
Затраты на организацию службы диагностики.
ФЗП инженера по технической диагностике 1 категории:
Sфзп = (Sо + Sо·Sпр100) * 12 = (115 + 115 * 0123) * 12 = 154974 тыс. руб.
Годовая cтоимость эксплуатации нового оборудования:
SП = (SК + Sвиб + Sтеп)Тэ= (950 + 95 + 55) 10 = 110 тыс. руб.
Годовые затраты на службу диагностики:
SД = Sфзп + SП = 154974 + 110 = 254974 тыс. руб.
Годовой экономический эффект от предотвращения аварий:
ЭГ = Zпот – SП = 141229 – 254974 = 13867926 тыс. руб.
Для предприятия с изношенным оборудованием организация службы диагностики почти ничего не стоит но приносит гигантский экономический эффект.
В работе рассматривались проблемы организации службы диагностики непрерывного сортового однониточного стана 390.
Описан технологический процесс стана с краткой характеристикой участков и выполняемых работ. Описано оборудование участков по группам с перечислением основных характеристик и схемами (где необходимы).
Приведено обоснование выбора оборудования для диагностирования по универсальности критичной важности для процесса производства. Приведены типовые отказы их причины и способы их исправления.
В расчётной части определены усилия моменты и мощность прокатки рассчитаны усилия в зубчатых зацеплениях и реакции на подшипниковых опорах выбраны подшипники и проведен расчёт их долговечности.
Разработана диагностическая модель неисправностей. Составлена матрица неисправностей приведена методика определения информативных частот повреждений обоснованы допустимые значения диагностических параметров.
Для вновь создаваемой службы диагностики выбран необходимый минимум диагностических приборов количество и квалификационные требования к персоналу перечислено диагностируемое оборудование частота его диагностики и составлен приблизительный график обходов. Составлена схема взаимодействия и информационных потоков.
Перечислены вредные и опасные факторы на производстве и требования к комплексным и персональным мерам защиты для соблюдения требований охраны труда и техники безопасности. Перечислены необходимые требования норм санитарной гигиены. Приведены основные нормы организации гражданской обороны.
В экономической части приведен расчёт экономического эффекта от внедрения службы диагностики и предотвращения аварий в условиях запредельного износа оборудования.
Паспорт клети № 16 стана 390 ПС-390-РК-16-1996.
Бедарев С.А. Механическое оборудование прокатных цехов: курс лекций; ГОУВПО «ДОННТУ». – Донецк 2018.
Машиностроение. Энциклопедия. Под ред. Фролова К.В. – т. IV-5 Машины и агрегаты металлургического производства – М.: Машиностроение 2000. – 912 с.
Целиков А.И. Машины и агрегаты металлургических заводов А.И. Целиков П.И. Полухин и др. Учебник для вузов. –Т. 3 – М.: Металлургия 1987. - 440 с.
Королев А.А. Конструкция и расчет машин и механизмов прокатных станов: Учеб пособие для вузов. – М.: Металлургия 1985. - 376 с.
Сидоров В.А. Техническая диагностика механического оборудования: учебник; ГОУВПО «ДОННТУ». – Донецк 2018. – 253 с.
ГОСТ ИСО 10816-1-97. Контроль состояния машин по результатам измерений вибрации на невращающихся частях. Межгосударственный стандарт
Санитарные правила для предприятий черной металлургии № 2527-82 от 20 июня 1982 г.
Ченцов Н.А. Экономика для дипломного проекта Методические рекомендации. – Донецк: ГОУВПО «ДОННТУ» 2020.
КЛ 16.00.00.000 ВО Общий вид 1
КЛ 16.01.00.000 ПЛ1 Редукторы клети
КЛ 16.02.00.000 ПЛ2 Матрица неисправн
КЛ 16 03.00.000 ПЛ3 Точки диагностирования
КЛ 16.04.00.000 ПЛ4 Точки диагностирования
КЛ 16.05.00.000 ПЛ5 Схема стана 1
Точки диагностирования горизонтального редуктора.cdw

8 - номер диагностируемой опоры
В - вертикальная составляющая замера
П - поперечная составляющая замера
О - осевая составляющая замера
С3 С8 - места установки датчиков
стационарной системы
Точки диагностирования
Схема стана.cdw

- опускающийся упор; 6 - сталкиватель; 7 - нагревательная печь; 8 - устройство для гидросбтва;
- тоннель-термостат; 10 - трайбаппарат перед 1-й клетью; 11 - черновая группа клетей;
- кривошипно-рычажные ножницы; 13 - промежуточная группа клетей; 14 - кривошипно-рычажные ножницы;
- чистовая группа клетей; 16 - измеритель геометрических размеров; 17 - участок ускоренного охлаждения;
- двухсистемные ножницы; 19 - кривошипный крошитель; 20 - реечный стеллаж; 21 - мостовые весы;
- вязальная машина; 23 - поперечный транспортёр; 24 - стационарный упор; 25 - накопитель номерных прутков;
- цепной транспортёр 1; 27 - цепной транспортёр 2; 28 - дозатор; 29 - летучие ножницы холодной резки;
- правильная машина; 31 - петлерегуляторы; 32 - устройства для смены клетей; 33 - разрывные ножницы;
- машина съёма заготовок; 35 - сталкиватель; 36 - бракомоталка; 36 - трайбаппарат.
Точки диагностирования вертикального редуктора.cdw

12 - номер диагностируемой опоры
В - вертикальная составляющая замера
П - поперечная составляющая замера
О - осевая составляющая замера
С9 С12 - места установки датчиков
стационарной системы
- заявки от цехов и отделов;
- задание инженеру по диагностике;
- получение диагностической информации
- устный отчёт руководителям участков
о состоянии оборудования;
- готовые отчёты и предписания в
- готовые отчёты в бумажном виде;
- готовые предписания в бумажном виде.
Точки диагностирования
вертикального редуктора
Информационные потоки
Разрез.frw

Рекомендуемые чертежи
- 09.06.2022
- 13.05.2023