Проект лопастного смесителя




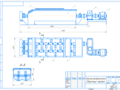
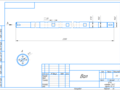
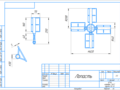
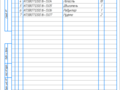
- Добавлен: 25.01.2023
- Размер: 1 MB
- Закачек: 2
Описание
Проект лопастного смесителя
Состав проекта
![]() |
![]() |
![]() |
![]() ![]() ![]() ![]() |
![]() ![]() ![]() ![]() |
![]() |
![]() |
![]() ![]() ![]() ![]() |
![]() ![]() ![]() ![]() |
![]() ![]() ![]() |
Дополнительная информация
Сборочный чертеж.cdw

Спецификация.spw

Вал2.cdw

Лопасть.cdw

Курсовой проект.docx
Основы теории и расчета лопастного смесителя непрырывного действия
Расчет конструктивных и технологических параметров лопастного смесителя непрерывного действия
Список использованной литературы
История развития механизации литейного производства. Механизация литейнего производства в мировой практике насчитывает всего каких-нибудь 50-70 лет. Началась она с создания примитивных формовочных машин если не считать применявшихся в еще ранее время простых подъемных кранов на формовке и лифтов для подъема шихты на колошниковую площадку вагранок.
В начале ХХ века механизация литейного производства во всех странах была на низком уровне. Литейные цехи работали на ступенчатом режиме работы. Характерным в этот период было применение формовочных машин с ручной набивкой а также изредка гидравлических прессовых машин. Для приготовления формовочных материалов использовались простейшие машины ( бегуны сита дезинтеграторы) а для очистки отливок пескоструйные аппараты.
В 20-х годах появились и быстро распространились пневматические встряхивающие формовочные машины. Усложнялось и усовершенствовалось смесеприготовительное оборудование появились пневматические выбивные устройства оборудование для очистки отливок совершенствовалась механизация транспорта шихтовых и формовочных материалов отливок. Создавались и внедрялись в производство литейные конвейеры и поточный метод работы.
В нашей стране механизация литейного производства получила свое развитие в годы Советской власти начиная с первой пятилетки индустриализации страны.
Процесс развития механизации литейного производства в нашей стране можно разделит на следующие периоды.
Первоначальный период (с 1927 до 1941 г.). В этот период происходит невиданный для прежней России рост промышленности создаются ее новые отрасли строятся крупнейшие механизированные заводы. Строятся и пускаются литейные цехи работающие на поточном режиме с высокой степенью механизации с конвейерами с годовым выпуском до 100 тыс. т литья.
Паралельно с коренным перевооружением и механизацией литейного производства в СССР в этот период развертывается и узучение новой техники. Проводятся научно- исследовательские работы разрабатываются теории рабочих процессов и методов расчета литейного оборудования главным оброзом прессовых и встряхивающих формовочных машин. Начинает формироваться советская научная школа Московского высшего технического училища основанная и возглавляемая доктором технических наук профессор Н. П. Аксеновым. Им же в рассматриваемый период впервые создается и в дальнейшем развивается курс оборудования литейных цехов как специальная дисциплина в машиностроительных вузах Советского Союза.
Период Великой Отечественной войны и послевоенного восстановления промышленности (1941-1950гг.). В этот период советское литейное машиностроение становится самостоятельной отраслью промышленности. Восстановление заводов после войны было связано с большими работами по модернизации расширению и дальнейшей механизации литейных цехов. Модернизируются старые и создаются новые типы и конструкции советских машин литейного производства. Укрепляется база для серийного изготовления таких машин.
Период после 1950г. Происходит дальнейшее развитие и рост механизации литейного производства в стране пояляются новые методы литья с целью получения отливок повышенной точности. Проектируются и создаются новые усовершенствованные машины литейного производства. Ставится и реально осуществляется задача создания машин-автоматов и автоматизированных участков и цехов. Углубляется и расширяется разработка теории и методов расчета машин литейного производства.
В 70-е годы интенсивно повышается уровень механизации отечественного литейного производства путем введения новейшего и кординального обновления существующего парка оборудования.
Значение механизации литейного производства - развитие и усовершенствование машиностроительной промышленности неизменно сопровождается прогрессивным уменьшением трудоемкости изготовляемых изделий. Поэтому важнейшей задачей задачей на производстве является обеспечение систематического роста производительности труда.
В литейных цехах эта задача решается двумя путями:
) применением новых технологических процессов либо дающих непосредственное уменьшение трудоемкости изготовления отливок либо позволяющих получить более точные отливки что даст возможность уменьшит объем и следовательно трудоемкость и стоимость механической оброботки литых заготовок в механосборочных цехах; однако примение новых технологических процессов в литейных цехах (под давлением кокильного центробежного в оболочковые формы по выплавляемым моделям выжиманием и др.) ограничено по номенклатуре отливок и вцелом по машиностроению может охватиь лишь максимум 20-25 всего литья;
) механизацией литейного производства являющейся основным средством уменьшения трудоемкости получения отливок применимым для наиболее широкой номенклатуры отливок. Кроме повышения производительности труда механизация дает повышение точности и качества отливок и коренное улучшение условий труда.
Связь механизации литейных цехов с производительностью труда можно иллюстрировать например построенной на основании статистических данных. Как видно средниий уровень производительности труда Р выражающийся в выпуске годных отливок (тгод) на одного списочного работающего возрастает с увеличением мощности цеха и одновременно степени механизации М становясь для крупных высокомеханизированных.
Поэтому в передовых индустриальных странах делают большие капиталовложения в механизацию и оборудование литейных цехов что окупается увеличением производительности труда (экономией на трудозатратах) а также повышением точности отливок ( экономией на сокращении объема механической обработки).
Основная доля трудоемкости изготовления отливок а именно от 50 до 70 приходится на формовку ( с приготовлением формовочных смесей) и изготовление стержней. Следовательно большое значение имеет механизация и автоматизация этих основных участков литейного цеха. Кроме того в связи с тяжелыми санитарно-гигиеническими условями труда первоочередной задачей является также механизация и автоматизация участков выбивки и очистки отливок.
КЛАССИФИКАЦИЯ СМЕШИВАЮЩИХ УСТРОЙСТВ
Технологическое свойства формовочных смесей зависят от равномерности распределения связующегопо объему смеси а также от того насколько равномерно зерна песка покрыты оболочкой связующего. Чем равномернее составляющие распределены в смеси по ее объему тем более высокими технологическими свойствами обладает формовочная смесь. Равномерность распределения составляющих смесей и создание оболочек связующего вокруг зерен песка достигаются в процессе смешивания.
Процесс смешивания формовочных материалов условно можно разделить на два этапа: смешивания составляющих смеси и обволакивание зерен песка связующим.
В процессе смешивания механизм смесителя создает по всему объему оргонизованный поток составляющих смесей. Внутри этого потока отдельные частицы соударясь движутся беспорядочно. При таком движении отдельные составляющие смеси распределяются между собой более или менее равномерно в зависимости от времени смешивания конструкции смесителя скорсти их движения и т.д.
В смешивающих бегунах при движении катков и плужков происходит не только перемещение смешиваемых компонентов относительно друг друга но и уплотнение смеси под катками и последующее разрушение уплотненных слоев что создает обволакивание зерен песка связующим.
Большое значение для обволакивания зерен песка связующим имеет проскользывание катков относительно днища чаши что создает деформации сдвига в уплотненной зоне. Последовательное уплотнение и разрушение вследствие сдвига уплотненных структур с последующим разрыхлением смеси и перебрасывание ее плужками смесителя способствуют равномерному нанесению слоя связующего на зерна песка повышению прочности смеси ее пластичности и форму емкости.
В каждой смесеприготовительной установке основным агрегатом является смеситель. По характеру работы смесители подразделяют на периодического действия и непрерывного действия.
В смесителях периодического действия материал смешивается отдельными порциями (замесами). Каждая новая порция может быть загружена в смеситель лишь после выгрузки из него предыдущего замеса. В смесителях непрерывного действия загрузка смешивание и выгрузка готовой смеси ведутся одновременно и непрерывно. Эти машины более производительны и экономичны по сравнению со смесителями периодического действия. Такие смесители наиболее полно отвечают требованием полной автоматизации процесса приготовления смеси.
По конструктивным признакам смесители подразделяют на катковые центробежные лопастные барабанные. Для получения песчано-глинистых смесей наиболее часто применяют катковые (бегуны с вертикальными катками) и центробежные смесители. Для получения холоднотвердеющих смесей чаще используют лопастные или шнековые смесители.
По конструктивным признакам смесители можно подразделить на:
а. С вертикально расположенными катками
б. С горизонтально расположенными катками (центробежные).
Лопастные (шнековые) смесители.
Физические основы смесеприготовления
Процесс приготовления смесей заключается в смешивании твердых и жидких составляющих. При перемешивании составляющих на поверхности частиц песка образуются пленки связывающие между собой смежные зерна. Связывание разрозненных зерен песка в единую систему (смесь) обусловлено возникновением сил сцепления между поверхностью зерен и пленкой связующего а также наличием сил связи между молекулами самого связующего вещества.
Применительно к условиям приготовления формовочных смесей процесс смесеобразования может быть условно разделен на собственно перемешивание и обволакивание которые в зависимости от режима работы смесителя могут совершаться последовательно или одновременно.
Смесеобразованию обычно сопутствуют важные в технологическом отношении физико – химические явления. Так при смешивании песка с водой молекулы воды ориентируются определенным образом по отношению к ионам расположенным на поверхности зерен кварца покрывая их слоем «жесткой» воды.
При сближении увлажненных зерен песка водные оболочки вступают в электростатическое взаимодействие связывая между собой эти зерна. Однако прочность такой смеси будет незначительна т.к. площадь контакта зерен чрезвычайно мала.
Повысить прочность смеси можно путем создания вокруг зерен деформируемых оболочек из глины или другого связующего. Глинистые частицы покрываясь слоем воды с несколько иной ориентацией молекул чем на поверхности зерен кварца при сближении с этими зернами прочно связывают их. При этом часть глинистых агрегатов удерживается на поверхности зерен а остальная часть располагается в порах между песчинками.
Очевидно для прочного связывания зерен между собой необходимо распределить глинистые агрегаты по всей их поверхности что возможно при сближении зерен и перекатывании их в среде глинистого вещества. В идеальном случае смешивание должно быть таким чтобы каждое зерно песка было окружено оболочкой связующего вещества.
Интенсивность обволакивания определяется физико-химическими свойствами компонентов конструкцией рабочих органов смесителя и числом уплотнений и разуплотнений каждого элемента смеси в единицу времени.
Лопастной смеситель представляет собой корытообразный корпус внутри которого вращаются один или два горизонтальных вала с насаженными на них лопастями. При вращении валов винтообразные лопасти захватывают материал и перемещают его как по окружности так и вдоль корпуса смесителя. Благодаря этому а также трению о стенки корыта частицы материала перемещаются. При перемешивании материал разрезается внедряющимися в него лопастями и перебрасывается ими. Однако смесь перетирается и уплотняется при этом очень мало и следовательно полного обволакивания зерен песка глинистой оболочкой не получается. По этой причине лопастной смеситель применяется при приготовлении наполнительных смесей при приготовлении ЖСС и ХТС.
Однако у лопастного смесителя есть и ряд положительных свойств: простота конструкции надежность в работе небольшой расход энергии и высокая производительность.
У двухвального лопастного смесителя (рис. 2.1) корпус представляет сварное корыто 4 из листовой стали облицованное внутри плитами из износостойкого материала. В корпусе встречно вращаются два вала 1 с попарно насаженными на них рычагами 3. Каждая пара рычагов повернута относительно соседней на угол который у смесителей периодического действия обычно равен 90 (крестообразно) а у смесителей непрерывного действия 45 60 и реже 90.
Рис. 2.1 – Схема лопастного смесителя: 1 – вал; 2 – лопасть; 3 – рычаг; 4 – корпус
Каждая лопасть представляет собой рычаг один коней которого укреплен на валу а другой несет на себе лопатку (лопасть). Плоскость лопатки повернута относительно плоскости вала на угол называемый углом атаки и чаще всего равный 45. Лопасти располагаются на валу так что образуют прерывистую винтовую линию. Это необходимо для перемешивания материала и перемещения его вдоль корпуса смесителя.
В зависимости от вида связующего вещества а также от физико – механических свойств получаемой смеси угол установки лопастей можно изменять в результате чего изменяется шаг винтовой линии и скорость перемещения материала вдоль смесителя а следовательно и продолжительность перемешивания (в смесителях непрерывного действия). В этих же смесителях несколько последних пар лопастей повернуты так чтобы создать встречное движение материала вызывающее подпор смеси и поддерживающее нужную высоту слоя материала в корыте смесителя.
В смесителях периодического действия перемешивание производится в течение определенного времени при этом материал вдоль корыта не перемещается а поднимается лопастями вверх. Замес выгружается либо путем поворота корыта либо через открываемое днище корыта.
В смесителе непрерывного действия загружаемые материалы и смесь непрерывно перемещаются вдоль корыта причем твердые компоненты загружаются в голове смесителя (зона сухого перемешивания) жидкие на среднем участке (зона увлажнения) а окончательное перемешивание происходит на самом длинном участке смесителя в его конце (зона влажного перемешивания).
Для изготовления стержней и форм из холоднотвердеющих (ХТС) и жидких (ЖСС) самотвердеющих смесей применяют лопастные (шнековые) смесители моделей 4727 47314732 4737 АМД -15.
Смеситель мод. 4727 (рис. 4.2) представляет собой станционарную установку с пультом управления 1. Сухой кварцевый песок из основного стационарного бункера расположенного над установкой поступает в приемный бункер 6 машины откуда через шиберный дозатор 5 кварцевого песка в шнековый смешивающий механизм 2 с индивидуальным приводом 7. В шнеке песок смешивается с катализатором который подается насосом 8 из специальной емкости расположенной в нижней части станины 9 по одному из шлангов 10 через разбрызгивающую трубку 4. Одновременно из емкости также расположенной в нижней части станины аналогичным образом подается смола в шнек через разбрызгивающие трубки 3. По мере вращения лопастного механизма все компоненты смеси смешиваются и перемещаются к разгрузочному патрубку 11 откуда попадают в стержневой ящик.
Рис. 2.2. Лопастной смеситель
Обычно такой смеситель может работать как индивидуально так и в комбинации с пескометом Так сочетание лопастного (шнекового) смесителя непрерывного действия подающего приготовленную смесь в пескометную голвку с 12-позиционной каруселью и механизмом - разборки ящиков и выдачи rotoBix стержней позволяет использовать полуавтоматическую непрерывного действия машину для изготовления стержней массой до 40 кг. Если для технологического процесса требуется применение разных смесей (ХТС ЖСС и др.) с различными физико-механическими свойствами то применяют не шнековый смеситель где шаг винта постоянный а лопастный в котором возможно изменение угла установки лопастей а следовательно и скорости перемещения материала вдоль смесителя. Непрерывность действия смесителей позволяет легко автоматизировать весь комплекс смесеприготовительных операций.
Лопастные смесители другой разновидности рассмотрим на примере автоматизированной установки для приготовления жидкостекольных смесей (рис. 4.3). Установка состоит из двух независимых узлов для приготовления смеси каждый из которых имеет лопастный смеситель 13. Кроме того установка имеет сдвоенный бункер 3 для песка с питателями 16 бункера 5 со шнековыми питателями для древесного песка бункера 6 для отвердителя дозаторы 10 связующего общие конвейеры 1 15 для подачи сухого песка и транспортирования стержневых ящиков (форм) 14 а также общий промежуточный бак 12 для связующего. Оба узла смешивания имеют единый узел подготовки связующего на основе жидкого стекла в состав которого входят баки 9 для жидкого стекла распределители 11 баки 78 для поверхностно- активных веществ и соды с дозаторами 10 и бак - мешалка 12. Жидкая композиция приготовленная в баке-мешалке 12 через промежуточный бак 2 и дозатор 4 поступает в лопастный смеситель 13 в который подается и твердая композиция - песок из бункера 3 и пек из бункера 5. После смешивания жидкая самотвердеющая смесь заливается в стержневые ящики путем поворота смесителя на некоторый угол. Конвейер 15 бывает реверсивным или замкнутым. Диаметр смесителя d=600÷800 мм длина 1000мм. Скорость вращения вала n=05 с-1. Время замеса 2-3 мин.
ОСНОВЫ ТЕОРИИ И РАСЧЕТА ЛОПАСТНОГО СМЕСИТЕЛЯ НЕПРЫРЫВНОГО ДЕЙСТВИЯ
Производительность смесителя периодического действия определяется по формуле:
где Z – число замесов в час;
G – вес одного замеса т.
Число замесов в час может быть найдено из выражения:
Продолжительность загрузки и выгрузки зависит от конструкции машины а время перемешивания определяется видом приготавливаемой смеси.
Весовая емкость смесителя зависит в основном от его геометрических размеров степени заполнения корыта смесью.
Порядок определения геометрических размеров можно принять следующий:
а. По заданной теоретической производительности смесителя Q (тч) определяют его весовую (кг) или объемную () емкость;
б. Задавшись коэффициентом заполнения смесителя и числом парных лопастей на каждом валу определяют радиус корпуса смесителя R.
в. Находят все размеры корпуса выраженные через . Емкость смесителя в весовых единицах:
где – коэффициент заполнения корпуса смесью ();
F – площадь смесителя занятая смесью (заштрихованная площадь)
– плотность разрыхленной смеси ;
– угол наклона лопастей к горизонту ();
– число парных лопастей на обоих валах принимается обычно для смесителей периодического действия для смесителя непрерывного действия ;
R – радиус днища смесителя м.
Рис. 3.1 – Схема к расчету конструктивных параметров смесителя
Из рис. 3.1 видно что расстояние между осями валов таким образом общая ширина корпуса смесителя:
Длина корпуса смесителя зависит от числа парных лопастей на каждом валу и может быть определена по формуле:
Высота корпуса зависит от длины лопастей радиуса R и от степени заполнения смесителя. Так у смесителя периодического действия:
У смесителя непрерывного действия: ;
Площадь одной лопасти у смесителя периодического действия у смесителей непрерывного действия .
Большую роль при конструировании лопастных смесителей играет выбор числа оборотов валов в минуту. С увеличением скорости вращения увеличивается эффективность перемешивания однако растет потребляемая мощность. Поэтому увеличение скорости вращения валов целесообразно только до некоторого предела после которого заметного повышения эффективности не наблюдается.
Для определения числа оборотов можно воспользоваться приближенной эмпирической формулой:
где G – весовая емкость смесителя кг.
Мощность двигателя определяется таким же методом как и для катковых смесителей. Так при перемещении лопаток двухвального смесителя:
При этом имеется в виду что число погруженных в смесь лопастей равно половине их общего числа.
В числе прочих элементов лопастного смесителя рассчитываются: валы рычаги лопаток приводные зубчатые колеса и др.
Задание. Определить основные конструктивные параметры двухвального смесителя для приготовления наполнительной формовочной смеси.
Исходные данные. Прочность сырой смеси =035 кгсм2 производительность смесителя Q=10 тч технологически необходимое время перемешивания t=3 мин.
Весовая емкость смесителя:
Объемная емкость смесителя:
где 0 удельный вес разрыхленной смеси кгм3;
Радиус корпуса смесителя:
iкоп общее количество пар лопастей (принимаем равным 20)
Ширина корпуса смесителя:
B =2*02(0707+1)=068 м
Рабочая длина корпуса:
Lраб =012*18*068=146 м
С учетом длины мест загрузки и выгрузки принимаем L=2 м;
.Высота корпуса смесителя:
Выполняем кинематический расчет смесителя:
а) Валы должны вращаться встречно при этом число их оборотов в минуту должно составлять:
принимаем nв=73 обмин
б) Передаточное число редуктора при nв=1450 (1мин)
Мощность двигателя смесителя:
где к.п.д. редуктора и передач (= 0.85);
угловая скорость вращения валов
=2*314*119=747 (1сек)
где h ширина лопасти (принята 5 см).
Выполняем силовой расчет смесителя:
а) Крутящий момент на каждом валу:
б) Окружное усилие или сила изгибающая вал:
где R максимальный радиус вращения лопатки см;
в) Наибольший изгибающий момент действующий по середине вала:
г) Расчетный момент:
Диаметры валов смесителя:
Выбираем двигатель с мощностью Nдв=82 кВт. Принимаем стандартный двигатель с мощностью 13 кВт модели А2-61-4.
Тогда передаточное число редуктора:
Выбираем редуктор модели Ц2-20-1983-4Л.
Технологический процесс приготовления смеси
Загрузка песок + отбивная смесь
Ввод в смесь глины в виде суспензии + Н2О
Список использованной литературы:
В.Я.Сафронов "Справочник по литейному оборудованию" - М. Машиностроение 1985-320 с.
П.Н. Аксенов "Оборудование литейных цехов" - М. Машиностроение 1977-510 с.
В.Л.ЛехтмецА.А.Чернышева " Механическое оборудование литейных цехов промышленные роботы и манипуляторы" методическое указание к практическим занятиям и к курсовому проектированию.Темиртау2012-74с.
М.П.Александров "Подъемно-транспортные машины" Учебник для машиностроительных спец. вузов- 6-е издание переработанное - М. Высшая школа.1985-520с.
А.И.Горский "Расчет машин и механизмов автоматических линий литейного производства" - М. Машиностроение 1978-552 с.
А.О.Спиваковский В.К.Дьяченко "Транспортирующие машины" Учебное пособие для машиностроительных вузов 3-е издание переработанное- М.Машиностроение 1983-487с
Рекомендуемые чертежи
- 04.02.2024
- 24.01.2023
- 24.01.2023