Привод скоростей сверлильного станка




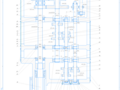
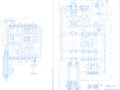
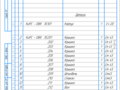
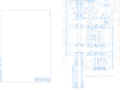
- Добавлен: 25.01.2023
- Размер: 8 MB
- Закачек: 0
Описание
Состав проекта
![]() |
![]() |
![]() ![]() ![]() ![]() |
![]() |
![]() ![]() ![]() ![]() |
![]() ![]() ![]() ![]() |
![]() ![]() ![]() ![]() |
![]() |
![]() ![]() ![]() |
![]() ![]() ![]() ![]() |
![]() ![]() ![]() ![]() |
![]() ![]() ![]() ![]() |
![]() ![]() ![]() ![]() |
Дополнительная информация
Чертеж переделан 11.cdw

Перемещение блоков шестерен при переключении скоростей
должно происходить плавно и без заеданий
Чертеж 88 2.cdw

переключения частот вращения
Спецификация (88).cdw

КиРС - 088 .10.000 СБ
Манжеты ГОСТ 8752-79
Шпонки ГОСТ 23360-78
Подшипники ГОСТ 8338-75
Чертеж3 (88).cdw

88.docx
Знаменатель прогрессии-112
Тип станка – сверлильный
Деталь: Материал - чугун сталь;
Наибольший размер-диаметр 15
Включение передач – на одном блоке муфтой по выбору остальные передвижение блоков
Механизм переключения - однорукояточный с предварительным набором
Привод скоростей – с разгруженным приводом
Положение включения - на минимальную частоту вращения
Сверлильные станки предназначены для сверления глухих и сквозных отверстий рассверливания зенкерования развёртывания растачивания и нарезания резьбы.
Основными формообразующими движениями при сверлильных операциях являются главное движение (вращательное) и движение подачи шпинделя станка.
Кинематические цепи осуществляющие эти движения имеют самостоятельные органы настройки посредством которых устанавливаются необходимая частота вращения инструмента и его подача.
Сверлильные станки подразделяются на вертикально-сверлильные настольные и наклонные радиально-сверлильные для глубокого сверления центровальные многошпиндельные.
РАСЧЕТ РЕЖИМОВ РЕЗАНИЯ
При выборе режимов резания для сверлильных станков следует учитывать особенности выполняемых на них операций: сверление рассверливание зенкерование развертывание и др. Порядок расчета режимов для этих станков является общим независимо от выполняемых операций.
Станок предназначен для сверления рассверливания отверстий поверхностей с максимальным диаметром Dmax=15 мм. В качестве инструмента при наибольшей скорости резания принимаем сверло спиральное с цилиндрическим хвостовиком (ГОСТ 10902-77).
При определении максимальной скорости резания принимаем операцию рассверливание материал заготовки – серый чугун материал режущей части развёртки – быстрорежущая сталь Р6М5.
Расчет режимов резания производим для наиболее энергоемкого перехода – сверления и наиболее точного – развертывания.
1 Расчет режимов резания при сверлении
Подача [2 с. 277 табл.25]:
Определяем период стойкости сверла по [2 табл. 30стр. 279]:
Определяем коэффициенты и показатели степени зависящие от материала изделия и инструмента по [2 табл. 28 стр. 278]:
СV=17.1; q = 0.25 y = 0.4 m = 0.125
Определяем поправочный коэффициент:
КMV = 1 КiV = 13 (для чугуна) КlV = 1
Определяем частоту вращения шпинделя:
Частота вращения шпинделя:
Принимаем нормализованное значение [3 с. 280]:
Фактическая скорость резания
Крутящий момент [2 с. 277]:
гдеCм= 0012; q = 22; y = 08 – при обработке чугуна;
Кp – коэффициент учитывающий механические свойства обрабатываемого (принимаем Кp=1).
Мощность резания [2 стр. 280]:
Осевая сила [2 с. 277]:
гдеCр= 42; q= 12; y = 075 – для чугуна [2 с. 281 табл. 32];
2 Расчет режимов резания при развертывании
Расчет режимов резания при развертывании производим для чугуна т.к. при обработке деталей из этого материала допускаются более высокие подачи.
Глубина резания равна припуску на сторону. Наибольший припуск - при развертывании по 7-му квалитету для отверстия диаметром 15 мм h = 025 мм.
Подача: при НВ 200 S = 2.6 ммоб [2 c. 278 табл. 2].
Значения коэффициентов в формуле резания: СV=156;q=02; y=05; m=03 [2 с. 279 табл. 29].
Период стойкости: Т = 60 мин[2 с. 280 табл. 30].
Принимаем нормализованное значение (приложение 3 стр. 280 [3]):
где Cр= 42; q= 12; y = 075 – для чугуна [2 с. 281 табл. 32];
Определение диапазона регулирования частот вращения (стр.108[1]): .1355
Определение числа ступеней частот вращения шпинделя (стр.108[2]): 24
КИНЕМАТИЧЕСКИЙ РАСЧЕТ
1 Построение структурной сетки
Определяем требуемые числа оборотов шпинделя из геометрического ряда для φ = 112 (стр.280[1]) обмин:
Рисунок 1 – Структурная сетка
Из структурной сетки получаем следующие отношения для передаточных чисел: i1 : i2 = φ3 = 1123 = 1405
i3 : i4 : i5 = φ = 112 (1)
i6 :i7 : i8 = φ6 = 1126 = 1974
2 Построение графика чисел оборотов
Для построения графика чисел подач необходимо из соотношения (1) выбрать одно передаточное число тогда определятся и все остальные значения. Притом во избежание больших диаметров колес должно соблюдаться условие: (2)
В соответствии с полученными передаточными отношениями строим график чисел оборотов (рисунок 2).
Рисунок 2 — График чисел оборотов
Принимаем электродвигатель с синхронной частотой вращения nс = 1500 обмин.
Асинхронная частота: nа = (1-005) nс = (1-005)·1500 = 1425 обмин [3 стр.27]. Вал II вращается с частотой nII = 1000 обмин (рисунок 2).
Тогда передаточное число: i0 = 14251000= 1425.
3 Определение числа зубьев зубчатых колес
Числа зубьев определяем по [табл. 3 стр.121 4]. При этом находим Σz такую чтобы для каждой передачи zmin ≥ 18 межосевое расстояние должно быть одинаковым для всех передач одной группы т. е. сумма зубьев сцепляющихся пар должна быть одинаковой модули для пар одной группы тоже одинаковы. Данные в таблице 1.
Таблица 2.1 – Определение чисел зубьев.
Определяем действительные значения частот вращения шпинделя с учетом конкретных чисел зубьев колес на каждом валу и сравниваем их со стандартными значениями (рис.2). Отклонение действительных величин от геометрического ряда не должно отличаться более чем на = ± 10(φ – 1) % т. е. = ± 10*(112 – 1) % = ± 1.2 %.
Данные расчета сводим в таблицу 2.2.
Во всех случаях величина отклонения не превышает предельно допустимой величины max = ± 1.2 %.
Таблица 2.2 – Расчет действительных значений частот вращения шпинделя
Частота вращения обмин
СИЛОВОЙ РАСЧЕТ КОРОБКИ СКОРОСТЕЙ
1 Определение мощности электродвигателя
Определяем КПД привода (стр.344[5]):
где а b – число зубчатых передач находящихся в зацеплении число пар подшипников;
– средние значения КПД зубчатых передач и подшипников.
а = 4 – в зацеплении одновременно находятся 4 зубчатых пары;
b = 5 – количество пар подшипников (5 валов – 5 пар подшипников).
Требуемая мощность электродвигателя:
Выбираем электродвигатель: закрытый обдуваемый асинхронный фланцевого исполнения IM3081 типа 4А100L4У3 с синхронной частотой вращения nс = 1500 обмин мощностью Nдв = 40 кВт. Габаритные и присоединительные размеры – табл.24.9[5] стр.379.
2 Определение расчетной частоты вращения валов
В коробках скоростей универсальных станков в качестве расчетного числа оборотов берут не по nmin а расчетную определяемую по формуле (стр.119[4]):
где Rn – диапазон регулирования.
Принимаем nр = 250 обмин.
Тогда по графику чисел оборотов (рис.2) частота вращения каждого вала составит:
nI = nдв = 1425 обминnIV = 500 обмин
nII = 1250 обминnV = 250 обмин
3 Определение мощности на валах
Определяем мощность на каждом валу по формуле:
где – КПД передач (подшипников зубчатых передач ).
4 Определение крутящих моментов на валах
Определяем крутящие моменты на каждом валу по формуле (стр.273[6]):
5 Определение модуля зубчатых зацеплений
В коробках скоростей размер шестерен определяется контактными напряжениями т. е. усталостью поверхностных слоев. Поэтому определяем модуль mпов а не межосевое расстояние и проверяем на изгиб по формулам (стр.150[7]):
где пов и изг – допускаемые напряжения по усталости поверхностных слоев и на изгиб Нсм2.
пов = 2000 · 60 = 120000 Нсм2;
изг = 800 Нмм2 = 80000 Нсм2
N – номинальная передаваемая мощность рассчитываемой шестерни кВт;
n – минимальное число оборотов шестерни при котором передается полная мощность обмин;
у – коэффициент формы зуба (при z = 20 60 у = 0243 0268);
z – число зубьев шестерни;
i – передаточное число.
К = Кд · Кк · Кр = 1 · 13 · 1 = 13 – коэффициент нагрузки который учитывает изменение по сравнению с номинальной от действия различных факторов.
Для валов I – II – колеса z1 и z2 с i0=2637=0.85 NI = 387 кВт nI = 1425 обмин:
Для валов II – III – колеса z5 и z6 с i = 1.405 NII = 381 кВт nII = 1000 обмин:
Для валов III – IV – колеса z11 и z12 с i = 1.405 NIII = 376 кВт nIII = 500 обмин:
Для валов IV – V – колеса z17 и z18 с i = 395 NIV = 37 кВт nIV = 315 обмин:
Полученные значения округляем до стандартных: mI–II = mII–III = mIII–IV = 1 мм; mIV–V = 25 мм.
Чтобы диаметры впадин зубьев не были меньше диаметров валов (они рассчитываются по крутящему моменту) увеличим модули до следующих стандартных значений mI–II = 15 мм; mII–III = 15 мм.
РАСЧЕТ ЭЛЕМЕНТОВ КОРОБКИ СКОРОСТЕЙ
1 Расчет геометрических параметров зубчатых колес
По формулам (стр.175[6] табл.3):
) делительный диаметр ;
) диаметр вершин зубьев ;
) диаметр впадин зубьев ;
) межосевое расстояние .
Данные заносим в таблицу 4.1.
Таблица 4.1 – Расчет параметров зубчатых колес
Ширина венцов колес (стр.151[7]): откуда b = 10m тогда для m = 15: b = 10·25 = 25 мм.
Степень точности колес определяется в зависимости от назначения (стр.373 табл.22[5]). Для силовых кинематических целей (коробок скоростей) со скоростью (линейной) V ≤ 10 мс – 7-я степень точности.
Выполняем предварительную эскизную компоновку коробки по рекомендациям на стр.189[8].
2 Предварительный расчет диаметров валов
Предварительный расчет диаметров валов проводим по (стр.273[6]).
Определяем диаметр вала из условия прочности на кручение при пониженных допускаемых напряжениях:
где Т – крутящий момент Н·мм;
[] – допускаемое условное напряжение при кручении.
[] = 10 15 Нмм2 – для промежуточных валов;
[] = 20 25 Нмм2 – для входных и выходных валов.
Тогда для входного и выходного валов (вал I и вал V – шпиндель):
Принимаем dI = 20 мм
Принимаем dV = 35 мм
принимаем dII = 25 мм;
Принимаем 25 шлицевое соединение 6 x 21 x 25.
принимаем dIII = 25 мм;
мм принимаем dIV = 32 мм
Принимаем 32 шлицевое соединение 6 х 26 х 32.
Для передачи крутящего момента от электродвигателя к входному валу коробки скоростей применяется муфта упругая втулочно-пальцевая которая передает крутящий момент со смягчением ударов посредством упругих резиновых втулок надетых на пальцы.
Расчетный момент передаваемый муфтой (стр.378[8]):
где М – момент на первом валу (МI = 2579 Н·м);
k – коэффициент режима (табл.16.1 стр.497[9])
k = 15 25 – для станков с возвратно-поступательным движением.
Мр = 2579 ·15 = 387 Н·м.
По табл. 16.11 стр.512[9] исходя из расчетного момента диаметра валов электродвигателя (dдв = 28 мм) и входного вала коробки (d = 20 мм) принимаем типоразмер муфты:
Муфта МУВП1 – 20 – 28 МН2096 – 64 со следующими конструктивными размерами и параметрами:
D = 100 мм – наибольший диаметр муфты;
Lma D1 = 71 мм – диаметр центров пальцев;
z = 6 – число пальцев; dдв = 28 мм; dI = 20 мм.
При вычерчивании остальные конструктивные элементы из таблицы 16.11 [9].
Конструктивная форма шпинделя определяется типом и назначением станка требованиями к его точности способом крепления инструмента и т. д.
Конфигурацию переднего конца шпинделя выбирают в зависимости от способа крепления инструмента или заготовки (стр. 210 [10]) т. к. для их крепления применяют стандартные приспособления то передние концы шпинделей большинства станков стандартизированы. Так для сверлильных станков применяется ГОСТ 24644 – 81 (стр. 143 [11]) по которому центрирование оправки инструмента осуществляется конусом 7:24 передача крутящего момента – торцевыми шпонками затяжка инструмента – шомполом. Типоразмер конуса определяем в процессе проектирования.
Тип опор шпинделя определяющий форму посадочных мест выбирают на основании требований к точности обработки и быстроходности величин нагрузок действующих на опоры. Наибольшее применение (более 50%) в качестве опор шпинделя получили подшипники качения (стр.211[10]). Схемы расположения опор и их конструктивное исполнение весьма разнообразны. Для шпинделей воспринимающих значительную осевую нагрузку (к ним относятся сверлильные фрезерные станки) находят применение упорные подшипники.
Поэтому в передней опоре по рекомендациям на стр.82 [10] 234 [12] устанавливаем радиальный двухрядный роликоподшипник воспринимающий только радиальную нагрузку в средней - 2 радиальных шарикоподшипника воспринимающих радиальную и осевую нагрузку. В задней опоре устанавливаем 1 радиальный роликоподшипник причем ролик имеет возможность осевого перемещения вдоль оси шпинделя относительно наружного кольца что исключает осевую нагрузку на шпиндель при температурной деформации шпинделя вдоль оси.
Радиальный предварительный натяг роликоподшипника осуществляется с помощью деформации внутреннего кольца подшипника путем его осевого перемещения на конусе 1:12 посредством промежуточной втулки. Ограничение осевого перемещения внутреннего кольца подшипника до требуемой величины осуществляется компенсационным кольцом выполненным из двух частей которые удерживаются пружинным кольцом. Плотный прижим наружного кольца роликоподшипника производится фланцем за счет компенсатора.
Защиту подшипников от воздействия внешней среды (грязи воды пыли) у шпинделей работающих при малых и средних оборотах и для исключения вытекания смазки из шпинделя используем армированную манжету.
Ориентировочные размеры конструктивное оформление узла шпинделя определяем эскизным прочерчиванием с учетом общей компоновки коробки.
1 Проверка шпинделя на точность
Так как сверлильный станок испытывает в процессе резания значительные осевые нагрузки то выбор точности подшипников шпинделя будет определяться их максимальным осевым биением от которого будут зависеть параметры шероховатости обрабатываемой детали.
За допускаемое осевое биение подшипников в машиностроении принято брать одну треть от допустимого биения шпинделя (стр.184 [11]).
Для передней опоры – 4-ый класс точности;
Для задней опоры – 5-ый класс точности;
Для упорных подшипников – 5-ый класс точности.
Предполагаем наиболее неблагоприятный случай когда биения подшипников ΔА в передней опоре ΔВ в задней направлены в противоположные стороны (рис. 5.1).
Рисунок 5.1 – Схема к расчёту шпинделя на точность
Так как передняя опора шпинделя нагружена больше задней и её погрешность в большей степени влияет на точность обрабатываемой детали то в переднюю опору устанавливаем подшипники более точные.
Биения в точках А и В должны быть меньше допустимого биения шпинделя равного мм и мм соответственно.
2 Расчет шпинделя на жесткость
Шпиндели как правило не рассчитываются на прочность (кроме тяжелонагруженных станков) а производится расчет на жесткость (стр. 444[5]).
Прежде всего определяем допускаемые значения параметров жесткости для проектируемого шпинделя. Согласно данным (стр.136 [11]) допускаемая минимальная жесткость конца шпинделя для продукционных станков составляет 200 Нмкм.
Составляем расчетную схему в которой на шпиндель действует только сила резания Р.
Рисунок 5.2 – Расчётная схема
С учетом зацепляющего момента в передней опоре перемещение переднего конца шпинделя (стр.180[11]):
а = 59 мм = 0059 м – вылет переднего конца шпинделя;
jA и jВ – жесткость подшипников передней и задней опор которую определим по графику (рис.7.2 стр.218[12]):
jA = 100 кгмкм = 1·109 Нм;
jВ = 40 кгмкм = 04·109 Нм;
= 0.45 – коэффициент защемления (табл.6.22 стр.178[11]);
Е = 2.1·1011 Па – модуль упругости материала шпинделя;
G = 8·1010 Па – модуль сдвига материала шпинделя;
S1 и S2 – площади сечения переднего конца и межопорной части шпинделя:
J1 J2 – среднее значение осевого момента инерции сечения консоли и сечения шпинделя в пролете между опорами.
Для кольцевого сечения:
Фактическая жесткость переднего конца шпинделя:
jф = Нмкм > 200 Нмкм т. е. жесткость шпинделя обеспечена.
РАСЧЕТ МЕХАНИЗМА УПРАВЛЕНИЯ
Изменение частот вращения шпинделя осуществляется введением в зацепление различных пар зубчатых колес. Механизм управления предназначен для включения требуемой частоты вращения шпинделя получаемой в результате определенного взаимного расположения в зацеплении зубчатых колес.
При перемещении колес возникают различного рода силы сопротивления (силы трения блоков зубчатых колес и деталей механизма управления перекосы осей колес и т. д.). Требуется определить эти силы и рассчитать длину рукоятки механизма переключения с учетом того чтобы сила приложенная к ней не превышала 40 Н.
1 Определение массы блоков зубчатых колес и перемещающихся деталей
Массы блоков колес и вспомогательных деталей определяем по справочнику [14]:
) Двойной блок mII = 24 кг (вал II);
) Тройной блок mIII = 35 кг (вал III);
) Двойной блок mIV = 4.8 кг (вал IV);
Масса диска переключения mд = 09 кг.
Массы вилок переключения принимаем 3 кг каждая т. е. mв = 4·3 = 12 кг.
2 Производим расчет потребного усилия пружины для развода дисков переключения
Усилие пружины для развода дисков должно преодолеть силу трения дисков в шлицевом соединении т. е. Fпр > Fтр где Fтр = fmg где f = 015 – коэффициент трения в шлицевом зацеплении (стр.464[5]).
mg = 09 · 10 = 9 Н – масса дисков в Н.
Fтр = 015 · 9 = 135 Н.
С учетом двух дисков Fтр = 135 · 2 = 27 Н.
Принимаем Fпр = 3 Н – сила пружины при разведенных дисках.
Сила пружины (которую нужно преодолеть рукояткой механизма переключения) при максимальной деформации (стр.102[5]):
= 025 – относительный инерционный зазор.
3 Усилие для преодоления действия силы фиксатора блока колес
Рассчитываем усилие необходимое для преодоления действия силы фиксатора блока колеса расположенного на 3-х вилках переключения Р0.
Т. к. оси перемещаемых зубчатых блоков расположены горизон-тально а осевые силы во время вращения зубчатых колес отсутствует (зубчатые зацепления прямозубые) то силу фиксации (сила пружины) принимаем равной Рпр = 10 Н для всех зубчатых блоков колес.
Рисунок 6 - Расчетная схема
Усилие пружины (стр.464[5]):
Рпр = Р0 · [tg (α - φ) – fn]
где α – угол наклона касательной в точке контакта шарика с рабочей поверхностью (α = 45о);
φ – угол трения между шариком и поверхностью контакта (φ = 6о – стр.465[5]);
fn – приведенный коэффициент трения между шариком и стенками отверстий при осевом перемещении шарика (fn = 015).
При количестве блоков 3суммарное усилие ΣР0:
ΣР0 = 15 · 3 = 45 Н.
4 Усилие для перемещения вилок переключения на штангах
Усилие которое необходимо преодолеть для перемещения вилок переключения на штангах при их количестве 3составит:
Fвил = mв · g · f = 12 · 10 · 015 = 18 Н.
Определяем суммарное усилие необходимое для преодоления сил трения от массы блоков зубчатых колес перемещаемых на шлицевом соединении.
Суммарная масса блоков в Н:
ΣМбл = (mII +mIII +mIV)g = (24 + 35 + 4.8) · 10 = 107 Н.
Тяговая сила на вилках переключения для перемещения блоков колес составит:
FT = ΣМбл · f = 107· 015 = 16.05 Н.
6 Мощность холостого хода
Определяем мощность холостого хода по формуле (стр.194[10]):
где d – средний диаметр шеек под подшипники всех промежуточных валов
d0 – диаметр шеек шпинделя
Σn – сумма частот вращения всех промежуточных валов
Σn =500+900+1250=2650 обмин
n0 – частота вращения шпинделя n0 =1425 обмин;
К1 = 15 – коэффициент учитывающий повышение за счет предварительного натяга потери в узле;
К2 = 3 – коэффициент учитывающий совершенство системы смазывания.
Момент на первом валу от мощности холостого хода:
Окружная сила на колесе:
Необходимая осевая сила на шестерне для преодоления силы Рt:
Тогда сила сопротивления повороту зубчатого колеса при введении во впадину зуба при несовпадении зуба и впадины:
Р0 = 69.6 · sin 30o = 34.8Н.
Рисунок 7 – Схема усилий на рукоятке управления
7 Составляем расчетную схему и определяем усилие на рукоятке управления. При этом условно показываем на схеме один блок.
7.1 Суммарное усилие на дисках переключения которое необходимо приложить для передвижения блоков:
FΣ = Fсп + Fтр + ΣР0 + Fвил + Fт + Р0
FΣ = 4+27+45+18+16.05+348=120.55 Н.
7.2 Момент на рукоятке:
где Рр = 40 Н – максимальное усилие на рукоятке.
Мрук = FΣ · r = мм где r – радиус сектора.
Для удобства переключения длину рукоятки принимаем равной 110 мм.
ОПИСАНИЕ КОНСТРУКЦИИ КОРОБКИ СКОРОСТЕЙ
Механизм коробки скоростей расположен в корпусе отлитом из чугуна. Вращение на первый вал коробки передается через упругую втулочно-пальцевую муфту. Коробка состоит из 5-ти валов причем выходной вал является шпинделем. На 1-м валу консольно насажена цилиндрическая шестерня находящаяся в постоянном зацеплении с колесом на 2-м валу. На промежуточных валах насажены зубчатые колеса и блоки шестерен осуществляющих передачу движения от входного вала на шпиндель. Причем зубчатые колеса шпиндельного вала выполнены в виде блока колес и передают вращение на шпиндель посредством шлицевого зацепления.
На конце шпинделя имеются отверстия для установки и закрепления поворотной планшайбы.
Для монтажа зубчатых колес и блоков шестерен предусматриваются в корпусе коробки специальные окна затянутые болтами.
Электродвигатель базируется на отъемной литой крышке.
Смазка подшипников шпинделя – консистентная а зубчатых зацеплений и подшипников промежуточных валов – жидкая. Подача жидкой смазки к местам зацеплений колес и к подшипникам производится с помощью металлических трубочек (на чертежах не показываем) порциями поршневым насосом (насос не показан). Привод насоса осуществляется от 2-го вала с помощью кулачка. Защита от утечек масла из коробки и смазки из шпинделя осуществляется с помощью прокладок круглых резиновых колец и манжет.
Управление переключением передач осуществляется одндорукояточным селективным механизмом переключения частот вращения позволяющим подготовить следующее включение частоты вращения (не нарушая предыдущей) и в нужный момент с помощью рукоятки быстро производить переключение.
Предварительный выбор частоты вращения производится поворотом лимба. Лимб при помощи конической передачи поворачивает сдвоенные диски. Рукоятка переключений (перемещение блоков) при помощи зубчатых секторов и рычагов сдвигает диски которые через штыри передвигают ползуны с вилками входящими в пазы передвижных блоков шестерен. Фиксация блоков осуществляется с помощью подпружиненных шариков.
Разработанная коробка скоростей отвечает следующим показателям эффективности:
– наряду с одиночными зубчатыми колесами применены блоки колес что снижает себестоимость;
– применена бочкообразная форма закругления зуба что приводит к повышению долговечности передачи;
– количество деталей сведено к минимуму что повышает надежность коробки;
– повышается производительность станка за счет применения преднабора уменьшающего потери на вспомогательное время переключения скоростей;
– органы управления расположены с максимальным удобством для рабочего их конструкция проста и надежна.
СПИСОК ИСПОЛЬЗОВАННЫХ ИСТОЧНИКОВ
Тарзиманов Г. А. Проектирование металлорежущих станков М. Машиностроение 1972.
Справочник технолога-машиностроителя т.2 под ред. Косиловой А. Г. М. Машиностроение 1986.
Кузьмин А. В. и др. Курсовое проектирование деталей машин ч.1 Мн.: Выш. школа1982.
Проников А. С. Расчет и конструирование металлорежущих станков М. Высшая школа 1962.
Колев Н. С. и др. Металлорежущие станки М. Машиностроение 1980.
Детали машин в примерах и задачах под ред. Ничипорчика С. Н. Мн.: Выш. школа 1981.
Атлас конструкций деталей машин под ред. Решетова Д. Н. М. Машиностроение 1979.
Чернин М. М. Расчеты деталей машин Мн.: Выш. школа 1974.
Металлорежущие станки под ред.Пуша В.Э.М.Машиностроение1985.
Кочергин А. И. Конструирование и расчет металлорежущих станков и станочных комплексов. Курсовое проектирование Мн.: Выш. школа 1991.
Детали и механизмы металлорежущих станков т.2 под ред. Решетова Д. Н. М. Машиностроение 1972.
Перель Л. Я. Подшипники качения. Справочник М. Машиностроение 1983.
Поливанов П. М. Таблицы для подсчета массы деталей и материалов М. Машиностроение 1980.
Дунаев П.Ф. Леликов О.П. Детали машин. Курсовое проектирование. М. Высш. школа 1990.
Анурьев В.И. Справочник конструктора – машиностроителя Т2 М. Машиностроение 1978
Крупнова В.А. Общемашиностроительные укрупнённые нормативы времени. М. НИИ Маш 1982
Чертеж.cdw

переключения частот вращения
Шпиндель А2.cdw

Сталь 40Х ГОСТ 4543-71
Неуказанные пред. откл. размеров: валов -t
Чертеж переделан.cdw

Перемещение блоков шестерен при переключении скоростей
должно происходить плавно и без заеданий
Чертеж A0 1.cdw

должно происходить плавно и без заеданий
вертикально-сверлильного
Рекомендуемые чертежи
- 07.06.2021
Свободное скачивание на сегодня
Другие проекты
- 29.08.2014
- 01.07.2014