Привод ленточного конвейера с двухступенчатым редуктором




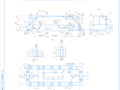
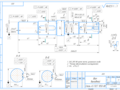
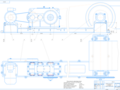

- Добавлен: 24.01.2023
- Размер: 1 MB
- Закачек: 1
Описание
Состав проекта
![]() |
![]() ![]() ![]() ![]() |
![]() ![]() ![]() ![]() |
![]() ![]() ![]() ![]() |
![]() ![]() ![]() ![]() |
![]() ![]() ![]() ![]() |
![]() ![]() ![]() |
![]() ![]() ![]() ![]() |
![]() ![]() ![]() ![]() |
Дополнительная информация
Редуктор-лист1.cdw

Осевой люфт в подшипниках: входного
мм-обеспечить за счет подбора толщины
Валы собранного редуктора должны проворачиваться от руки
без заеданий и стуков.
Сопряженные поверхности корпуса и крышек покрыть тонким
слоем герметика ВГК-18 №2 МРТУ 07-6012-63.
Необработанные поверхности литых деталей
красить маслостойкой эмалью.
Необработанные наружные поверхности редуктора покрыть серой
эмалью ГР. ГФ-20. ЭМ.ПФ-133
литра масла И-30А ГОСТ 20799-88
его при полной нагрузке в течение одного часа
затем заменить масло.
Техническая характеристика
Вращающий момент на выходном валу Т = 336
Частота вращения тихоходного вала n = 161
Общее передаточное число i = 7
Филиал ФГБОУ ВПО УГНТУ
Крышка редуктора.cdw

Сварка ручная дуговая по ГОСТ 5268-80.
Наплавленный металл Э50А ГОСТ 9467-75.
Контроль сварных швов-внешний осмотр и измерения
Базовую плоскость А шлифовать до обработки всех других
Размеры в квадратных скобках обрабатывать совместно с
Неуказанная шероховатость механически обработанных
не рабочих поверхностей: грунтовка ГФ-021
ГОСТ 25129-92. VII. ХЛ3
эмаль ПФ-115 ГОСТ 6465-76
Филиал ФГБОУ ВПО УГНТУ
Вал I.cdw

Филиал ФГБОУ ВПО УГНТУ
Сталь 40 ГОСТ1050-88
Нормальный исходный контур
Направление линии зуба
Привод-вывод-3.cdw

Электродвигатель 4А112M2У3 по ГОСТ19523-81
Мощность электродвигателя 7
Частота вращения барабана 80
Общее передаточное число привода 36
Крутящий момент на барабане 605
Срок службы передачи 15000 часов
Филиал ФГБОУ ВПО УГНТУ
Колесо.cdw

Сталь 45 ГОСТ 1050-88
Филиал ФГБОУ ВПО УГНТУ
Нормальный исходный контур
Направление линии зуба любое
ПЗ.doc
1Общая характеристика ленточных конвейеров
Ленточный конвейер – это непрерывно действующее устройство транспортировки с объединенными грузонесущим механизмом и тяговым механизмом в виде замкнутой гибкой ленты.
Ленточные конвейеры (рисунок 1.1) имеют тяговый орган 2 выполненный в виде бесконечной ленты являющийся одновременно и несущим элементом конвейера привод приводящий в движение приводной барабан 1 натяжное устройство с натяжным хвостовым барабаном 6 и натяжным грузом 7 поддерживающих роликов на рабочей ветви ленты 4 и на холостой ветви ленты 8 (в ряде случаев вместо поддерживающих роликов используется сплошной деревянный или металлический настил) загрузочное устройство 5 и разгрузочное устройство 3 отклоняющий барабан 10 и устройство для очистки ленты 11. Все элементы конвейера смонтированы на металлической раме 9.
Рисунок 1.1 – Ленточный конвейер
Широкое применение ленточные конвейеры получили для межоперационного транспортирования грузов в поточном производстве для транспортирования в литейных цехах (подачи земли) в шахтном хозяйстве для подачи топ-
лива и зерна на элеваторах и т.п.
Ленточные конвейеры могут использоваться при значительной длине транспортирования и отличаются высокой производительностью простотой конструкции малой массой надежностью в работе и удобством в эксплуатации относительно небольшим расходом энергии.
В ленточных конвейерах лента используется в качестве транспортирующего органа осуществляя одновременно и тяговую связь между барабанами конвейера. Поэтому лента должна обладать прочностью гибкостью в продольном (на барабанах) и поперечном (на желобчатых опорах) направлениях высокой сопротивляемостью изнашиванию рабочих поверхностей и расслаиванию при многократных перегибах небольшим упругим и остаточным удлинением малой гигроскопичностью незначительным влиянием влаги на прочность и долговечность ленты.
Конвейерная лента состоит из сердечника воспринимающего тяговые нагрузки и резиновой обкладки рабочей и нерабочей сторон ленты предохраняющей сердечник от механических повреждений и от воздействия на него влаги газов агрессивных сред.
3 Приводы ленточных конвейеров
Назначение привода – приведение в движение тягового органа конвейера и груза. Создание необходимого тягового усилия на тяговом органе ленточного конвейера происходит за счет силы трения возникающей между лентой и поверхностью приводного барабана. Привод (рисунок 1.2) состоит из двигателя 1 редуктора с цилиндрической или червячной передачей 3 барабана 5 а также муфт 2 и 4 соединяющих двигатель с редуктором и редуктор с валом барабана [3].
Рисунок 1.2 – Схема привода конвейера
Выбор двигателя. Кинематический расчет привода
– электродвигатель; 2 – редуктор; 3 – поликлиноременная передача;
– цепная передача; 5 – плита (рама); I II III IV V – обозначения валов
Рисунок 2.1 – Схема привода
Таблица 2.1 – Исходные данные для проектирования
Тяговое усилие ленты F кН
Диаметр барабана D мм
Допускаемое отклонение скорости ленты %
Срок службы привода в годах
Тип корпуса редуктора
2 Определим срок службы привода:
Lh = 365 · Lr · tc · Lc
где Lr = 6 лет – срок службы привода tc = 8 ч – продолжительность смены
Lc = 1смена – число смен.
Подставим значения Lh = 365 · 6 · 8 · 1 = 17520 ч.
От полученного значения Lh следует взять примерно 85% получим:
Lh = 17520 · 085 = 14892 ч.
Окончательно рабочий ресурс привода принимаем
3 Определение номинальной мощности и номинальной частоты вращения двигателя
Определим требуемую мощность рабочей машины
где F – тяговая сила кН;
– линейная скорость мс.
Определим общий коэффициент полезного действия (КПД) привода
где общ – общий КПД привода;
РЕМ – КПД поликлиноременной передачи РЕМ = 095; [ 9 ]
ЗП – КПД косозубой передачи ЗП = 096; [ 7 ]
ЦП – КПД открытой цепной передачи ЦП = 091; [ 10 ]
ПП – КПД пары подшипников ПП = 099. [ 47 ]
Определим требуемую мощность двигателя
где Рдв – требуемая мощность двигателя;
Номинальная мощность двигателя должна быть больше требуемой
где Рном – номинальная мощность двигателя.
Выберем из списка стандартных двигателей ближайший по значению мощности.
Каждому значению номинальной мощности Рном соответствует в большинстве не одно а несколько типов двигателей с различными синхронными частотами вращения – 3000 1500 1000 750 обмин. Выбор оптимального типа двигателя зависит от типов передач входящих в привод кинематических характеристик рабочей машины и производится после определения передаточного числа привода и его ступеней.
Выбираем электродвигатель серии 4А по ГОСТ 19523-81 с номинальной мощностью 75 кВт применив для расчета четыре варианта типа двигателя см. таблицу 2.2 [4с.390].
Таблица 2.2 – Технические данные двигателей
Номинальная мощность Рном кВт
Частота вращения обмин
при нормальном режиме
4 Определение передаточного числа привода и его ступеней
Определим частоту вращения выходного вала V рабочей машины
где – скорость тягового органа мс;
D – диаметр барабана мм.
Определим передаточное число привода для всех приемлемых вариантов типа двигателя при заданной номинальной мощности
где nном – номинальная частота вращения электродвигателя.
Предварительно задаем наиболее рекомендуемые передаточные отношения см. литературу [ 478]:
– для поликлиноременной передачи uрем = 2;
– для цепной передачи uцеп = 2.
Тогда передаточные отношения закрытой передачи (двухступенчатого редуктора) для четырех вариантов электродвигателей будут:
Рекомендуемые передаточные отношения для двухступенчатых редукторов общего назначения лежат в диапазоне 7 30.
Поэтому выбираем первый вариант электродвигателя с nном = 2925 обмин.
Передаточное число редуктора разбивается по передачам так:
Рекомендуется использовать стандартные передаточные числа (ГОСТ 2185-66):
uред.б = 315 uред.т = 25
тогда uред = uред.б · uред.т = 315·25 = 7875 .
Далее уточняем передаточные числа:
– для цепной передачи uцеп = 2;
тогда для поликлиноременной передачи
uрем = u (uред · uцеп ) = 3635 (7875 · 2) = 23;
Фактическое значение общего передаточного отношения передач
uфакт = uрем · uред · uцеп = 23 · 7875·20 = 36225.
Отклонение фактического передаточного отношения от требуемого
Δu = (uфакт - u) u ·100% = (36225-3635) 3635·100% = 03%
меньше 1% что приемлемо.
5 Определение мощностей угловых скоростей и вращающих моментов на валах привода
Мощности на валах привода:
Р2 = Р1 · РЕМ · ПП = 669 095 · 099 = 6292 кВт
Р3 = Р2 ЗП · ПП = 6292 096 · 099 = 5980 кВт
Р4 = Р3 ЗП · ПП = 5980 096 · 099 = 5683 кВт
Р5 = Рpм = Р4 ЦП · ПП = 5683 091 · 099 = 5120 кВт.
Частоты вращения и угловые скорости валов привода:
n1 = nДВ = 2925 обмин;
n2 = n1 uрем = 2925 23 = 12717 обмин;
n3 = n2 uред.б = 12717 315 = 4037 обмин;
n4 = n3 uред.т = 4037 25 = 1615 обмин;
n5 = n4 uцеп = 1615 2 = 8075 обмин;
Вращающие моменты на валах:
Результаты расчетов сведем в таблицу 2.3
Таблица 2.3 – Мощности угловые скорости и вращающие моменты на валах привода
Расчет внешней цепной передачи привода
(используем литературу [10])
– крутящий момент на меньшей звездочке равен: Т4 = 3363 Н·м;
– частота вращения меньшей звездочки n4 = 1615 обмин;
– передаточное число цепной передачи uЦЕП = 20;
Так как скорость цепи гораздо меньше 10мс (16мс) то выбираем цепь втулочную однорядную тогда коэффициент учитывающий рядность цепи mр= 10;
Определяем приближенное значение шага цепи
Выбираем стандартную роликовую цепь
ПР – 3175 – 8850 ГОСТ13568-75
Шаг цепи Р = 3175 мм;
Площадь проекции опорной поверхности шарнира цепиА = 2622 мм2
Разрушающая нагрузка Fразр= 885 кН;
Масса одного метра цепиq = 38 кгм
Число зубьев звездочек:
Z1 = 29 – 2 uЦЕП = 29 – 2 2 = 25; Принимаем Z1 = 23;
Задаем межосевое расстояние
апред= (30 50) Р = (30 50) · 3175 = 9525 15875мм;
Принимаем а = 1000мм.
Уточняем межосевое расстояние
Делительные диаметры звездочек:
Оценка долговечности цепи по частоте ударов звена цепи о звездочки:
U = Z1 n4 30 z0 = 23 1615 30 98 = 126 с-1;
U = 126 с-1 [U] = 12 с-1
Долговечность цепи обеспечивается. Окружная сила на малой звездочке:
Ft = 2 Т4 d1 = 2 336300 2333 = 2883 Н;
Коэффициент эксплуатации цепи
Кэ=К1 К2 · К3 · К4 · К5 · К6
где К1 =1 – коэффициент динамичности нагрузки;
К2 =1 – коэффициент учитывающий способ натяжения цепи;
К3 =1 – коэффициент учитывающий величину межосевого расстояния;
К4 =1 – коэффициент учитывающий наклон передачи;
К5 =1 – коэффициент учитывающий способ смазки цепи;
К6 =125 – коэффициент учитывающий влияние сменности работы передачи;
После подстановки числовых значений получаем
Допускаемое давление в шарнире цепи из условия износостойкости
шарнира цепи при n4 = 1615 обмин и Р = 3175 мм [p] = 290 Нмм2;
Расчетное давление в шарнире цепи:
p = Ft Kэ А = 2883 125 2622 = 137 Нмм2 [p] = 290 Нмм2;
износостойкость шарнира цепи обеспечивается.
Общее натяжение цепи:
Fобщ = Ft К1 + Ff + Fv
где Ff – натяжение от собственного веса цепи
Ff = q · a · g · Kf = 38 · 095 · 98 · 6 = 224 Н;
Kf = 6 – коэффициент зависящий от положения линии центров звездочек;
Fvнатяжение цепи от действия центробежных сил;
Fv = q · V2 = 38 202 = 147 Н
Fобщ = 2883 1 + 224 + 147 = 3122 Н;
Прочность цепи на разрыв обеспечивается.
Нагрузка на валы от цепной передачи:
Fв = Ft · Kb = 2883 · 115 = 3316 H.
где Kb = 115 – коэффициент нагрузки;
Расчет внешней поликлиноременной передачи
(используем литературу [9])
Рисунок 4.1 – Схема и основные размеры поликлиновой передачи
– передаваемая мощность РДВ = 669 кВт;
– передаваемый момент на меньшей звездочке ТДВ = 218 Н·м;
– частота вращения меньшей звездочки nДВ = 2925 обмин;
– передаточное число передачи передачи uРЕМ = 23;
Рисунок 4.2 – Параметры поперечного сечения поликлиновых ремней
Таблица 4.1 – Размеры и параметры поперечных сечений поликлиновых ремней
Выбираем из табл.4.1[9] минимально допустимый диаметр ведущего шкива d1 = 80 мм профиль ремня Л.
Определим диаметр ведомого шкива
d2 = d1 · uРЕМ· (1 – ) = 80· 23·(1 – 0015) = 1812мм
где – коэффициент проскальзывания принимаем =0015.
Определим фактическое передаточное число
Проверим отклонение Δ u фактического передаточного числа от заданного
Определим ориентировочное межосевое расстояние
Определим расчетную длину ремня
Примем по ТУ 38 105763-84 длину ремня L = 1120 мм.
Уточним межосевое расстояние при стандартной длине
Определим угол обхвата ремнем ведущего шкива
Определим скорость ремня
Определим частоту пробегов ремня
Определим допускаемую передаваемую мощность поликлиновым ремнем
[Рп]= ([Р10]·Сα·СL+ΔPF )·Ср (4.1)
где [Р10] – допускаемая приведенная мощность передаваемая поликлиновым ремнем с десятью клиньями [Р10]= 70 кВт табл. 3.5 [ 9 ] ;
Сα – коэффициент угла обхвата на меньшем шкиве:
Сα= 1– 0003·(180º– α) = 1– 0003·(180º– 1638º) = 095;
СL – коэффициент влияния отношения расчетной длины ремня к базовой:
СL = 094 при LL0 = 11201600=07
ΔPF – поправка к мощности учитывающая влияние изгиба на меньшем шкиве:
ΔPF =10-4 ·Δ ТF · n1 = 10-4 ·5 · 2925 = 146 кВт;
где Δ ТF = 5 Н·м – поправка на передаточное число к крутящему моменту на быстроходном валу табл. 3.5 [ 9 ];
Ср = 12 – коэффициент динамичности и режима нагрузки табл. 2.5 [ 9 ] ;
Подставим значения в формулу (4.1):
[Рп]= (7 · 095 · 07 + 146 ) · 12 = 73 кВт.
Определим количество клиньев поликлинового ремня
округляем до четного: z = 8.
Вш = (z – 1) ·t + 2·s = (8–1) ·48+2·55 = 446мм
Сила предварительного натяжения
Определяем нагрузку на валы от ременной передачи
Расчет внутренних передач редуктора
Ниже приняты следующие индексы:
- относящийся к шестерне первой передачи редуктора (колесу с меньшим числом зубьев);
- относящийся к колесу первой передачи редуктора;
- относящийся к шестерне второй передачи редуктора
- относящийся к колесу второй передачи редуктора
1 Выбор материалов зубчатых колес закрытых передач редуктора
При выборе материала зубчатых колес и варианта термообработки учитываем следующее:
) высокотвердые материалы (Н>350 НВ) плохо прирабатываются поэтому они требуют повышенной точности изготовления повышения жесткости валов и опор. Нарезание зубьев при высокой твердости затруднено поэтому тер-
мообработку выполняют после нарезания.
Некоторые виды термической обработки (объемная закалка цементация) сопровождаются короблением зубьев. Для исправления формы зубьев требуются дополнительные трудоемкие операции: шлифовка притирка обкатка и т.п. Эти трудности проще преодолеть в условиях крупносерийного и массового производства когда окупаются затраты на специальное оборудование инструменты и приспособления. Мастерские предприятий нефтяного профиля оснащены как правило только универсальным металлорежущим оборудованием;
) нарезание зубьев колес невысокой твердости (H350 НВ) возможно и после термообработки. При этом можно получить высокую точность без применения дорогих отделочных операций. Колеса из таких материалов хорошо прирабатываются и не подвержены хрупкому разрушению при динамических нагрузках. Для лучшей приработки зубьев твердость шестерни рекомендуется назначать больше твердости колеса на 30-40 НВ. Технологические преимущества материала при Н350 НВ обеспечили ему широкое применение в условиях индивидуального и мелкосерийного производства в мало- и средненагруженных передачах а также в передачах с большими колесами термическая обработка которых затруднена.
Исходя из вышеизложенного выбираем марку сталей одинаковую для шестерни и колеса: сталь 45 ГОСТ 1050-88 термообработка шестерни – улучшение до средней твердости Н1=285НВ термообработка колеса – улучшение до средней твердости Н2=248 НВ.
Ориентировочное значение допускаемого контактного напряжения при расчете на выносливость (при коэффициенте долговечности ZN=1)
2 Расчет закрытой цилиндрической косозубой передачи первой ступени редуктора из условия сопротивления контактной усталости поверхности зубьев
–вращающий момент на шестерне Т1 = 473 Н·м;
–частота вращения шестерни n1 = 12717 обмин;
–передаточное число зубчатой передачи u = 315;
–принимаем делительный угол наклона линии зуба = 120 ;
Определяем допускаемые контактные напряжения не вызывающие опасной контактной усталости материалов колес:
ZN – коэффициент долговечности;
NHE – эквивалентное число циклов изменения контактных напряжений;
qH – показатель степени кривой контактной усталости;
где j – число вхождений рассчитываемой стороны зуба в зацепление за один оборот колеса;
н – коэффициент учитывающий форму циклограммы нагружения при постоянном режиме нагружения н = 1.
NHE1 = 60Lh n1 j1 н = 60 15000 12717 1 1 = 11445106 циклов;
NHE2 = 60Lh n2 j2 н = 60 15000 4037 1 1 = 3633106 циклов;
так как NHE12 > NHl
[SH] – минимальный коэффициент запаса прочности;
ZR – коэффициент учитывающий влияние исходной шероховатости сопряженных поверхностей зубьев;
Zv – коэффициент учитывающий влияние окружной скорости колес;
Z При проектировочном расчете ZR Zv Z
Вычисляем допускаемые контактные напряжения подставляя численные значения в формулу (5.1):
Расчетное допускаемое напряжение
Т.к. значение выходит за пределы 1 123 принимаем
2.2 Определяем ориентировочное значение межосевого расстояния передачи:
где Ка – вспомогательный коэффициент [5 с.9 ];
КH B - коэффициент учитывающий неравномерность распределения нагрузки по длине контактных линий [5 с.10 ];
Yba- предварительное значение коэффициента ширины венца относительно межосевого расстояния:
где Ybd - предварительное значение коэффициента ширины венца относительно диаметра.
При несимметричном относительно опор расположение колес и Н1 2 350 НВ задаемся Y bd = 10 ; bm = 30 [5 с.9 ] тогда
Вычисляем предварительное межосевое расстояние по формуле (5.2):
Определяем числа зубьев колес
Проверяем отсутствие подрезания зубьев колес:
где Х = 0 – коэффициент смещения исходного контура
αt – делительный угол профиля зубьев в торцевом сечении; т.к. коэффициент смещения исходного контура Х12 = 0 то αtw = αt = 2040;
где α = 200 – угол профиля исходного контура.
Так как Z1 и Z2 > Z min подрезания зубьев колес не будет.
Уточняем значение передаточного числа:
Δu = (uфакт - u)u ·100% = (3166-315)315·100% = 05%
Делительный нормальный модуль зубьев
αtW = αW при Х12 = 0
Модуль округляем до ближайшего стандартного m = 20 мм.
Уточняем межосевое расстояние передачи при стандартном модуле зубьев
Уточняем значение коэффициента ширины венца
Рабочая ширина венца зубчатой передачи
принимаем bw = 35 мм.
2.3 Геометрические и кинематические параметры
– делительные (начальные) диаметры шестерни и колеса
Находим окружную скорость колес
Назначаем степень точности передачи 8 так как V1 = V2 = 41 м с
меньше 10 м с [5 с.12].
2.4 Проверочный расчет на сопротивление контактной усталости
активных поверхностей зубьев
Расчетное контактное напряжение в полюсе зацепления
где Z E – коэффициент учитывающий механические свойства материалов колес
для стальных колес Z E = 190 [5 с.13 ];
Z H – коэффициент учитывающий форму сопряженных поверхностей зубьев
в полюсе зацепления;
Z – коэффициент учитывающий суммарную длину контактных линий;
где α – коэффициент торцового перекрытия;
F t – окружная сила на делительном цилиндре в торцовом сечении;
K H – коэффициент нагрузки при расчете по контактным напряжениям;
KH = KA· KHV · KH Kα = 1 · 107 · 108 · 135 = 156
где KA – коэффициент учитывающий внешнюю динамическую нагрузку (за пределами зацепления) КA = 1 [5 с.13 ];
V – коэффициент учитывающий динамическую нагрузку возникающую в
где WHV – удельная окружная динамическая сила Н мм ;
где = 002 – коэффициент учитывающий влияние твердости поверхностей зубьев [5 с.14];
g0 = 56 – коэффициент учитывающий влияние разности шагов зубьев шестерни и колеса [5 с.14].
– коэффициент учитывающий неравномерность распределения нагрузки по длине контактных линий; при Ybd = b w d 1 = 35 6135 = 057
H1 и H2 350 HB и несимметричном расположении обоих колес относительно опор KH = 108 [5 с.10].
α – коэффициент учитывающий неравномерность распределения нагрузки между зубьями из-за погрешности изготовления α = 135 [2 с.13].
Подставляем числовые данные параметров в формулу (5.2.3)
Уточненное значение расчетного допускаемого контактного напряжения
где ZR = 10 [2 с.7] при Ra = 063 125;
ZV = 10 [2 с.7] т.к. V1 = V2 = 41 м с 5 м с ;
ZX = 10 [2 с.7] т.к. d 2 700 мм .
Проверка сопротивления активных поверхностей зубьев контактной усталости
= 407 МПа 105 [] P ут = 105 442 = 464 МПа .
Сопротивление зубьев контактной усталости обеспечивается.
Усталостного выкрашивания зубьев не будет.
2.5 Проверочный расчет на сопротивление усталости зубьев при изгибе
Напряжения изгиба в опасных сечениях на переходных поверхностях зубьев шестерни и колеса
где KF – коэффициент нагрузки при расчете на изгиб;
KF = KA· KFV · KF · KF α = 1 · 12 · 117 · 135 = 189;
где KFV – коэффициент учитывающий внутреннюю динамическую нагрузку
возникающую в зацеплении при расчете на изгиб
где WFV – удельная окружная динамическая сила при расчете на изгиб
где F = 006 – коэффициент учитывающий влияние вида зубчатой передачи для косозубых [5 с.15].
KFb–коэффициент учитывающий неравномерность распределения нагрузки по длине контактных линий;
KFα – коэффициент учитывающий распределение нагрузки между зубьями.
При Yb d = bw d1 = 35 6135 = 057
KF α = 135 – для косозубых [5 с.15].
(для колеса b1 = bw = 35мм; для шестерни b2 = bw+4 мм =35+4=39 мм;)
YF – коэффициент учитывающий форму зуба.
При X1 = 0 и числе зубьев эквивалентного колеса Z n 1 = Z1 cos 3 =
= 30 cos3 12º = 30 09783 = 32 YF1 = 364.
При X2 =0 и Zv2 = 95 cos3 12º = 95 09783 = 1016 YF2 =36 [5 с.16];
Y – коэффициент учитывающий влияние наклона зубьев;
= 1 – (b 120°) = 1 – 116 (12º 120º) = 088
где коэффициент осевого перекрытия
где осевой шаг зубьев
Y – коэффициент учитывающий влияние перекрытия зубьев.
Так как >1 = 1 α = 1 178 = 056;
Вычисляем напряжения изгиба по формуле (5.4):
Допускаемое напряжение изгиба не вызывающее усталостной поломки зуба
F lim В2 = 175 · H2 = 175 · 248 = 434 MПa .
[SF] – минимальный коэффициент запаса прочности;
[SF ]12 = 17 [5 с.5].
YN – коэффициент долговечности при изгибе ;
где q F = 6 для стальных колес с нешлифованной переходной поверхностью
– базовое число циклов напряжений;
и при постоянном режиме нагружения так как
m F = m H = 1 [5 с.7] .
YR – коэффициент учитывающий шероховатость переходной поверхности;
YR =1 – для неполированных зубьев [5 с.17 ];
YХ – коэффициент учитывающий размеры зубчатого колеса;
Yх1= 105 – 0000125·d 2 =105 – 0000125·6135 = 1042;
Yх2 = 105 – 0000125·d 1 =105 – 0000125·19427 = 1026;
YА – коэффициент учитывающий влияние двустороннего приложения нагрузки;
YА = 1 – при одностороннем приложении нагрузки к зубу.
YZ – коэффициент учитывающий способ получения заготовки зубчатого
YZ = 1 – для поковок и штамповок;
Yg – коэффициент учитывающий влияние шлифования переходной поверхности зубьев;
Yg = 1 – если переходная поверхность зубьев не шлифуется;
Yd – коэффициент учитывающий влияние деформационного упрочнения
переходной поверхности;
Yd = 1 – если переходная поверхность зубьев не подвергается деформационному упрочнению или электрохимической обработке;
Вычисляем по формуле (5.5)
Проверяем сопротивление зубьев на усталость при изгибе
F2 = 74 MПа = 262 Ma.
Сопротивление зубьев усталости при изгибе обеспечивается. Усталостной поломки зубьев в пределах расчетного срока службы не будет.
3 Расчет закрытой цилиндрической косозубой передачи второй ступени редуктора из условия сопротивления контактной усталости поверхности зубьев
–вращающий момент на шестерне Т3 = 1417 Н·м;
–частота вращения шестерни n3 = 4037 обмин;
–частота вращения колеса n4 = 1615 обмин;
–вращающий момент на колесе Т4 = 3363 Н·м;
–передаточное число зубчатой передачи u = 25;
Выбираем марку сталей одинаковую для шестерни и колеса: сталь 45 ГОСТ 1050-88 термообработка шестерни – улучшение до средней твердости Н1=285НВ термообработка колеса – улучшение до средней твердости Н2=248 НВ.
3.1 Определение допускаемых контактных напряжений
NHE3 = 60Lh n3 j3 н = 60 15000 4037 1 1 =3633 106 циклов;
NHE4 = 60Lh n4 j4 н = 60 15000 1615 1 1 =1454 106 циклов;
так как NHE34 > NHl
ZR –коэффициент учитывающий влияние исходной шероховатости сопряженных поверхностей зубьев;
3.2 Определение ориентировочного значение межосевого расстояния передачи
При несимметричном относительно опор расположение колес и Н1 2 350 НВ задаемся Y bd = 06 ; bm = 20 [5 с.9 ] тогда
Так как Z3 и Z4 > Z min подрезания зубьев колес не будет.
Модуль округляем до ближайшего стандартного m = 30 мм.
принимаем bw = 50 мм.
3.3 Геометрические и кинематические параметры
Назначаем степень точности передачи 8 так как V3 = V4 = 21 мс
меньше 10 мс [5 с.12].
3.4 Проверочный расчет на сопротивление контактной усталости
Z H – коэффициент учитывающий форму сопряженных поверхностей зубьев в полюсе зацепления;
KH = KA· KHV · KH Kα = 1 · 1034 · 106 · 135 = 148
V – коэффициент учитывающий динамическую нагрузку возникающую в зацеплении
– коэффициент учитывающий неравномерность распределения нагрузки по длине контактных линий; при Ybd = b w d3 = 50 9816 = 051
H1 и H2 350 HB и несимметричном расположении обоих колес относительно опор KH = 106 [5 с.10].
α – коэффициент учитывающий неравномерность распределения нагрузки между зубьями из-за погрешности изготовления α = 135 [5с.13].
Подставляем числовые данные параметров в формулу (5.3)
где ZR = 10 [5 с.7] при Ra = 063 125;
ZV = 10 [5 с.7] т.к. V1 = V2 = 21 м с 5 м с ;
ZX = 10 [5 с.7] т.к. d 2 700 мм .
= 3854 МПа 105 [] P ут = 105 458 = 481 МПа .
3.5 Проверочный расчет на сопротивление усталости зубьев при изгибе
KF = KA· KFV · KF · KF α = 1 · 11 · 115 · 135 = 17;
При Yb d = bw d1 = 50 9816 = 051
(для колеса b1 = bw = 50мм; для шестерни b2 = bw+4 мм =50+4= 54 мм;)
При X3 = 0 и числе зубьев эквивалентного колеса Z n 3 = Z3 cos 3 =
= 32 cos3 12º = 32 09783 = 342 YF3 = 384.
При X4 =0 и Zv4 = 80 cos3 12º = 80 09783 = 855 YF4 =360 [5 с.16];
= 1 – (b 120°) = 1 – 110 (12º 120º) = 089
где q F = 6 для стальных колес с нешлифованной переходной поверхностью [5 с.17].
и при постоянном режиме нагружения так как m F = m H = 1 [5 с.7] .
Yх3= 105 – 0000125·d3 =105 – 0000125·9816 = 104;
Yх4 = 105 – 0000125·d4 =105 – 0000125·24540 = 102;
Вычисляем допускаемое напряжение изгиба по формуле (5.5)
F3 = 626 MПa = 3053
F4 = 587 MПа = 2604 Ma.
Расчет корпуса редуктора
Определим толщину стенок сварного корпуса
= 0025 · а + 1 5 мм = 0025 · 17178 + 5 = 93 мм примем = 9 мм.
Толщина стенки крышки корпуса редуктора
= 002· а + 1 5 мм1 = 00217178 + 5 = 84 мм примем 1 = 8 мм.
Определим толщину верхнего пояса корпуса редуктора
S = 15 = 15 9 = 135 мм.
Определим толщину пояса крышки редуктора
S1 = 15 1 = 15 8 = 12 мм ;
Определим толщину нижнего пояса корпуса редуктора
t = (2 25)· = 25 9 = 225 мм;
Определим диаметр фундаментных болтов
dф = (15 25) = 2 9 = 18 мм принимаем dф= М18.
Определим ширину нижнего пояса корпуса редуктора
К2 21 dф = 21 18 = 378 мм;
Определим диаметр болтов соединяющих корпус с крышкой редуктора
d4 = (05 06) dф = 06 18 = 108 мм принимаем dк.р= М12.
Определим ширину пояса соединения корпуса и крышки редуктора около подшипников К = 3 d4= 3 108 = 324 мм ;
Определим диаметр болтов соединяющих крышку и корпус редуктора около подшипников
dк.п = 075 dф= 075 18 = 135 мм принимаем dк.п= М14.
Диаметр болтов для крепления крышек подшипников к редуктору зависят от их посадочных диаметров то есть от наружных диаметров подшипников которые будут определены ниже.
Определим диаметр винтов для крепления крышки смотрового отверстия
dк.с= 6 10мм принимаем dк.р= М6.
Определим диаметр резьбы пробки маслосливного отверстия
dк.р19 9 = 171 мм принимаем dк.р= М18
Проектировочные (ориентировочные) расчеты валов
Валы предполагается изготовить из стали 45 с термообработкой «Улучшение»
В = 880 МПа [кр]ст45 = 130 МПа;
Ориентировочный минимальный диаметр вала
где [кр]'ст45II = 25 Н мм – допускаемое напряжение кручения вала заниженное в 5 6 раз для учета влияния изгибающих моментов;
Тi – вращающий момент на i-том валу.
Вычислим диаметры по формуле (7.1):
Принимаем: для II вала dпод подшипниками = 25 мм;
dпод шкивом = 22 мм;
dпод шестерней = 30 мм;
для III вала dпод подшипниками = 30 мм;
dпод колесом = 34 мм;
dпод шестерней = 34 мм;
для IV вала dпод подшипниками = 40 мм;
dпод колесом = 45 мм.
dпод звездочкой = 38 мм;
Определение ориентировочных длин валов
1 Определение конструктивных размеров ступеней вала II рисунок 8.1.
При определении диаметров и длин используем ряды Ra 5 Ra 40.
Учитывем ширины венцов шестерен и расстояние до внутренних стенок
редуктора принимаем Δ = 10мм.
Рисунок 8.1 – Эскиз вала II
2 Определение конструктивных размеров ступеней вала III рисунок 8.2.
Рисунок 8.2 – Эскиз вала III
3 Определение конструктивных размеров ступеней вала IV рисунок 8.2.
Рисунок 8.3 – Эскиз вала IV
Приближенные расчеты валов
Предварительно принято (см.рис. 8.1):
a = 40 мм; b = 45 мм; c = 110 мм;
– окружная сила на шестерне
Ft1 = 2 · Т2 d1 = 2 · 47300 6135 = 1542 H;
– радиальная сила раздвигающая шестерню и колесо
Fr1 = Ft1 · tg 20º = 1542 · 0364 = 561 H;
Fа1 = Ft1 · tg = 1542 tg 120 = 1542 02126 = 328 Н;
нагрузка на вал от ременной передачи
б) Горизонтальная плоскость:
– определение опорных реакций
МBY = RDY· (b+c) + Q· a Fr1· b Fa1· d 12 = 0;
RDY = (Fr1· b + Fa1· d 12 Q· a) (b+c) = (561· 45+ 328· 6135 2 675· 40)(45+110) = 54 H;
МDY = Fr1 · c + RBY· (b+c) + Fa1· d12 Q· (a+b+c) = 0;
RBY=(Fr1 c Fa1d12+Q·(a+b+c))(b+c) =
= (561 110 32861352+675·(40+45+110))(45+110) = 1182H.
– построение эпюры изгибающих моментов
MBY = Q·a = 675 · 004 = 27 Нм;
MCYправ = RDY · c = 54 · 011 = 6 Нм;
MCYлев = RBY · b Q · (a+b) = 1182 ·0045 675 ·(004+0045) = 4 Нм.
а) Вертикальная плоскость:
– определение опорных реакций
МВZ = Ft1 · b RDZ · (b+c) = 0;
RDZ = Ft1· b (b+c) = 1542 · 45 (45+110) = 448 H;
МDZ = Ft1· c RBZ· (b+c) = 0 ;
= RBZ· b = 1094 · 0045 = 49 Н;
Построение эпюры суммарных изгибающих моментов
Построение эпюры эквивалентных моментов
Вал предполагается изготовить из стали 45 с термообработкой «Улучшение». в = 880 МПа. Допускаемое напряжение изгиба при симметричном цикле изменения напряжений:
Предварительно принимаем минимальные значения диаметров (учитывая ориентировочные расчеты валов на кручение и выполнение шпоночных пазов)
Принимаем: для II вала dпод шкивом = 16 мм;
dпод подшипниками = 20 мм;
dпод шестерней = 25 мм;
Предварительно принято (см.рис. 8.2):
a = 45 мм; b = 64 мм; c = 45 мм;
– окружная сила на колесе первой передачи
Ft2 = Ft1 = 1542 H;
– окружная сила на шестерне второй передачи
Ft3 = 2 · Т3 d3 = 2 · 141700 9816 = 2887 H;
Fr3 = Ft3 · tg 20º = 2887· 0364 = 1051 H;
Fа3 = Ft3 · tg = 2887 tg 120 = 2887 02126 = 614 Н;
а) Горизонтальная плоскость:
МАY = RDY· (a+b+c) Fr3· (a+b) Fa2· d 22+ Fr2· a Fa3· d 32 = 0;
RDY = ( Fr3· (a+b) + Fa2· d 22 Fr2· a + Fa3· d 32) (a+b+c) =
= ( 1051·(0045+0064)+328·0097 561· 0045 + 614· 0049) (0045+0064+0045) = 982 H;
МDY = RAY· (a+b+c) + Fr3· c Fa2· d 22 Fr2· (b+c) Fa3· d 32 = 0;
RAY = ( Fr3· c + Fa2· d 22 + Fr2· (b+c) + Fa3· d 32) (a+b+c) =
= ( 1051· 45 + 328· 97 + 561· (64+45) + 614· 49) (45+64+45) = 492 H.
MBYлев = RAY ·a = 492 · 0045 = 22 Нм;
MBYправ = RAY ·a+ Fa2· d 22 = 492·0045 +328· 0097 = 10 Нм;
MCYправ = RDY · c = 982 · 0045 = 44 Нм;
MCYлев = RDY · c Fa3· d 32 = 982 · 0045 614· 0049 = 14 Нм.
б) Вертикальная плоскость:
МAZ = Ft2 · a + RDZ · (a+b+c) Ft3 · (a+b) = 0;
RDZ = ( Ft2 · a + Ft3 · (a+b)) (a+b+c) = (1542· 45 + 2887·(45+64)) (45+64+45) = 1593 H;
МDZ = Ft2 · (b+c) RAZ · (a+b+c) Ft3 · c = 0 ;
RAZ = ( Ft2 · (b+c) Ft3 · c) (a+b+c) = (1542·(64+45) 2887· 45) (45+64+45) =248 H;
= RDZ·c = 1593· 0045 = 72 Н·м;
= RAZ·a = 248· 0045 = 11 Н·м;
Вал предполагается изготовить из стали 45 с термообработкой «улучшение». в = 880 МПа.
Допускаемое напряжение изгиба при симметричном цикле изменения напряжений:
Принимаем: для III вала dпод подшипниками = 25 мм;
dпод колесом = 32 мм;
dпод шестерней = 32 мм;
Предварительно принято (см.рис. 8.3):
a = 100 мм; b = 50 мм; c = 55 мм;
– окружная сила на колесе
Ft4 = – Ft3 = 2887 H;
Fr4 = – Fr3 = 1051 H;
Fа4 = – Fа3 = 614 Н;
d 4 2 = 2454 2 = 1227 мм;
нагрузка на вал от цепной передачи
Горизонтальная плоскость:
МAY = RCY· (a+b) – FB· (a+b+c) Fr4· a + Fa4· d 42 = 0;
RСY = (FB· (a+b+c) + Fr4· a – Fa4· d 42) (a+b) =
= (3316· (100+50+55) + 1051· 100 – 614· 1227) (100+50) = 4730 H;
МСY = RАY· (a+b) – FB· c + Fr4·в + Fa4· d 42 = 0;
RАY=(FB· c – Fr4·в– Fa4· d 42) (a+b) = (3316·55– 1051·50 – 614·1227) (100+50) = 363 Н;
MBYЛЕВ = RАY ·a = 363·01 = 363 Нм;
MВYПРАВ = – RСY · в + FВ· (в+с) = – 4730 · 005+ 3316· (005+0055) = 112 Нм.
MCY = FВ · c = 3316 · 0055 = 182 Нм;
Вертикальная плоскость:
МАZ = Ft4 · а RСZ · (а+в) = 0;
RСZ = Ft4· а (а+в) = 2887· 100 (100+50) = 1925 H;
МСZ = Ft4·в RАZ· (а+в) = 0 ;
RАZ = Ft4· в (а+в) = 2887 · 50 (100+50) = 962 H;
= RАZ· а = 962 · 01 = 962 Н;
Вал предполагается изготовить из стали 45 с термообработкой «улучшение» в = 880 МПа.
Принимаем: для IV вала dпод звездочкой = 36 мм;
dпод подшипниками = 40 мм;
dпод колесом = 45 мм;
Выбор и расчет подшипников
Исходные данные для подбора подшипников на II вал:
Fa1 = 328 Н ; dпод подшипниками = 20 мм; n II = 12717 обмин; Lтребh = 15000 ч.
Предполагается установка конических роликовых подшипников
№7304 ГОСТ 333-79 d = 20 мм; D = 52 мм; В=1625; C = 26000 H;
коэффициент осевого нагружения подшипника e = 03;
Определяем внутренние осевые усилия возникающие из-за наклона беговых дорожек см. рисунок 10.1.
SВ = 083 e RВ = 083 03 1611 H = 401 H;
SD = 083 03 RD = 083 03 451= 112 H;
Рисунок 10.1– Расчетная схема подшипников вала II
Определяем осевые нагрузки:
Fa1 + SB = 328 + 401 = 729 H > SD= 112 H
то есть вал упрется в опору D тогда
FaD = SB + FA1 = 729 H;
Определяем эквивалентные радиальные динамические нагрузки:
при этом FaB V RB = 401 1 1611 = 025 e
тогда XB = 1; YB = 0;
FaD V RD = 729 1 451 = 161 > e тогда XD = 04; YD = 06 e = 06 03 = 20;
РB = (V XB RB + YB FaB) Кб Kt КЕ = (1 1 1611+0 401) 13 1 1 = 2094 Н;
РD = (V XD RD + YD FaD) Кб Kt КЕ = (1 04 451 + 20 729) 13 1 1 =
где Кб = 13 – коэффициент безопасности;
Kt = 1 – коэффициент учитывающий влияние температуры на долговечность;
КЕ = 1 – коэффициент эквивалентности нагрузки при постоянном режиме нагружения;
Большая эквивалентная динамическая нагрузка на подшипник:
Долговечность более нагруженного подшипника
Долговечность предложенного подшипника в часах
Lhфакт = Lфакт 106 60 nII = 2697 106 60 12717 = 35300 часов > Lhтреб = 15000 часов
долговечность подшипника обеспечивается.
Исходные данные для подбора подшипников на III вал:
Fa2 = 328 Н; Fa3 = 614 Н; dпод подшипниками = 25 мм; n II = 4037 обмин; Lтребh = 15000 ч.
№7205 ГОСТ 333-79 d = 25 мм; D = 52 мм; В=1625; C = 24000 H;
коэффициент осевого нагружения подшипника e = 036;
Определяем внутренние осевые усилия возникающие из-за наклона беговых дорожек см. рисунок 10.2.
SA = 083 e RA = 083 036 551 H = 165 H;
SD = 083 03 RD = 083 036 1871= 559 H;
Рисунок 10.2– Расчетная схема подшипников вала III
Fa2 + SD = 328 + 559 = 887 H > Fa3 + SA = 614 + 165 = 779 H
то есть вал упрется в опору A тогда
FaA = Fa2 + SD = 887 H;
при этом FaA V RA = 887 1 551 = 161 > e
тогда XA = 04; YA = 06 e = 06 036 = 167;
FaD V RD = 559 1 1871 = 03 e тогда XD = 1; YD = 0;
РA = (V XA RA + YA FaA) Кб Kt КЕ = (1 04 551+ 167 887) 13 1 1 = 2212 Н;
РD = (V XD RD + YD FaD) Кб Kt КЕ = (1 1 1871 + 0 559) 13 1 1 = 2432 Н;
Lhфакт = Lфакт 106 60 nII = 1337 106 60 4037 = 55200 часов > Lhтреб = 15000 часов
Исходные данные для подбора подшипников на IV вал:
Fa4 = 614 Н; dпод подшипниками = 40 мм; n III = 1615 обмин; Lтребh = 15000 ч.
№2007108 ГОСТ 333-79 d = 40 мм; D = 68 мм; В=18; C = 40000 H;
коэффициент осевого нагружения подшипника e = 033;
Определяем внутренние осевые усилия возникающие из-за наклона беговых дорожек см. рисунок 10.3.
SA = 083 e RA = 083 033 1028 H = 282 H;
SC = 083 033 RC = 083 033 5107= 1399 H;
Рисунок 10.3 – Расчетная схема подшипников вала IV
Fa4 + SC = 614 + 1399 = 2013 H > SA= 282 H
FaA = Fa4 + SC = 2013 H;
при этом FaA V RA = 2013 1 1028 = 196 > e
тогда XA = 04; YA = 06 e = 06 033 = 182;
FaC V RC = 1399 1 5107 = 027 e
тогда XC = 1; YC = 0;
РA = (V XA RA + YA FaA) Кб Kt КЕ = (1 04 1028+ 182 2013) 13 1 1 = 5297 Н;
РC = (V XC RC + YC FaC) Кб Kt КЕ = (1 1 5107 + 0 1399) 13 1 1 = 6639 Н;
Lhфакт = Lфакт 106 60 nIII = 262 106 60 1615 = 27000 часов > Lhтреб = 15000 часов
Расчеты шпоночных соединений
Предполагается установка шпонок призматических по ГОСТ 23360-78
Таблица 11.1– Данные для расчета шпонок
вал IIIпод шестерней
вал IVпод звездочкой
Рисунок 11.1– К расчету шпонок
Материал шпонок – сталь 45 нормализованная МПа . [4 с.168 170]
Все шпонки работоспособны.
Проверочный (уточненный) расчет валов на сопротивление усталости (раздел выполнен по литературе [57])
Напряжения в сечениях вала изменяются:
а) напряжения изгиба по III циклу;
б) напряжения кручения по II циклу так как предполагаются частые пуски и остановы редуктора.
Коэффициент запаса прочности:
где –коэффициент запаса прочности по нормальным напряженям
Для случая шпоночного паза:
-1 = 380 МПа –предел выносливости материала по изгибу при симметричном цикле
К = 175 – коэффициент концентрации напряжений при изгибе;
= 085 – масштабный фактор;
= 1 – коэффициент поверхностного упрочнения;
И – напряжение изгиба в сечении МПа;
Вычислим общий коэффициент для случая шпоночного паза:
MИ – суммарный изгибающий момент в сечении H мм;
W= 01 d3 – b t (d –t)2 2 d – осевой момент сопротивления изгибу
при наличии шпоночного паза в сечении мм3.
Коэффициент запаса прочности по касательным напряжениям:
-1 =230 МПа –предел выносливости материала при кручении при симметричном цикле
К = 15 – коэффициент концентрации напряжений при кручении;
= 08 – масштабный фактор;
= 005 – коэффициент асимметрии цикла при кручении;
Вычислим общий коэффициент для случая шпоночного паза:
где KP – напряжение кручения в сечении МПа;
где Wρ = 02 d3 – b t (d –t)2 2 d – полярный момент сопротивления сечения кручению при наличии шпоночного паза в сечении мм3;
где d – диаметр вала; t – глубина шпоночного паза; b – ширина шпоночного паза.
Вал II cечение А концентратор – шпоночный паз:
Wρ = 02 d3 – b t (d –t)2 2 d =02 183 – 64 (18 – 4)2 2 18 = 1036 мм3;
KP = 47300 1036 = 457 МПа;
S = 230 457 096 = 52;
Сопротивление усталости сечения А выполняется так как 52 > [15].
Сечение В концентратор-насаженный подшипник. Посадка – 20L0k6.
Wρ = 02 d3 = 02 203 = 1600 мм3;
KP = 47300 1600 = 296 МПа;
W =01 d3 = 01 203 = 800 мм3 ;
ИС =27000 800 = 34 МПа;
Сопротивление усталости сечения В выполняется так как 36 > [15] .
Вал III cечение B концентратор – шпоночный паз:
W =01 d3 – b t (d –t)2 2 d = 01 343 – 10 5 (34 – 5)2 2 34 = 3312 мм3;
И =24600 3312 = 74МПа;
Wρ = 02 d3 – b t (d –t)2 2 d = 02 343 – 10 5 (34 – 5)2 2 34 =7242 мм3;
KP = 141700 7242 = 196 МПа;
S = 230 196 096 = 122;
Сопротивление усталости сечения B выполняется так как 110 > [15].
Сечение C концентратор – шпоночный паз.
И =84000 3312 = 254 МПа;
Wρ = 02 d3 – b t (d –t)2 2 d = 02 343 – 10 5 (34 – 5)2 2 34 = 7242 мм3;
S = 230 196 096 = 122 ;
Сопротивление усталости сечения C выполняется так как 63 > [15].
Вал IV сечение С концентратор-насаженный подшипник. Посадка – 40L0k6.
W – осевой момент сопротивления изгибу мм3;
W = 01 d3 = 01 403 = 6400 мм3;
Wρ = 02 403 = 12800 мм3;
KP = 336300 12800 = 263МПа;
Сопротивление усталости сечения С выполняется так как 34 > [15] .
Назначение посадок деталей
Внутренние кольца подшипников насаживаем на валы с натягом значения которых соответствуют полю допуска k6 а наружные кольца в корпус – на переходной посадке значение которой соответствует полю допуска Н7.
Для ступицы детали насаживаемой на выходной конец вала и для ступицы зубчатого колеса принимаем посадки с натягом значение которой соответствует полю допуска g6 и Н7р6.
Выбор способа и типа смазки редуктора
Для уменьшения потерь мощности на трение и снижения интенсивности износа трущихся поверхностей а также для предохранения их от заедания задиров коррозии и лучшего отвода теплоты трущиеся поверхности деталей должны иметь надежную смазку.
В настоящее время в машиностроении для смазки применяют картерную систему смазки. В корпус редуктора заливают масло так чтобы венцы колес были в него погружены. При их вращении масло увлекается зубьями разбрызгивается попадает на внутренние стенки корпуса откуда стекает в нижнюю его часть. Внутри корпуса образуется взвесь частиц масла в воздухе.
Картерную смазку применяют при окружной скорости зубчатых колес от 03 до 125 мс. При более высоких скоростях масло сбрасывается с зубьев центробежной силой и зацепление работает при недостатке смазки. Кроме того заметно увеличиваются потери мощности на перемешивание масла и повышается его температура.
Выбор смазочного материала основан на опыте эксплуатации машин. Принцип назначения сорта масла следующий: чем выше контактные давления в зубьях – тем большей вязкостью должно обладать масло чем выше окружная скорость колеса – тем меньше должна быть вязкость масла. Поэтому требуемую вязкость масла определяют в зависимости от контактного напряжения и окружной скорости колес.
Окружная скорость колеса быстроходной передачи 1-2 V1 = V2 = 41 м с
окружная скорость колеса быстроходной передачи 3-4 V3 = V4 = 21 мс.
Т.к. V4 12мс для смазки зубчатой передачи применяем картерную систему смазки–окунанием колес в масло.
При скорости V4 = 21 мс и контактных напряжениях 3854 МПа рекомендуемая вязкость масла равна 28·10-6 м2с. [4 с.253]
Такой вязкостью обладает масло Индустриальное И-30А ГОСТ 20799-88.
При смазывании окунанием обьем масляной ванны редуктора определяется из расчета 035 – 05 л масла на 1кВт передаваемой мощности [347].
В нашем случае обьем масляной ванны необходим в диапазоне от
5лкВт ·67кВт 23 л до 05лкВт · 67кВт 33 л.
Смазка подшипников – масляным туманом который образуется при окружных скоростях больших 1 мс .
При длительной работе в связи с нагревом масла и воздуха повышается давление внутри корпуса. Это приводит к просачиванию масла через уплотнения и стыки. Чтобы избежать этого внутреннюю полость корпуса сообщают с внешней средой путем установки отдушины в его верхней точке.
Порядок сборки привода
Перед началом сборки устанавливают соответствие имеющихся узлов и деталей а также проверяют их целостность. Внутреннюю полость корпуса редуктора тщательно очищают. Сборку производят в соответствии с чертежом общего вида редуктора начиная с узлов валов.
На ведущий вал насаживают мазеудерживающие кольца и подшипники предварительно нагретые в масле до 60 – 100 С.
В ведомый вал закладывают шпонки и напрессовывают зубчатые колеса до упора в бурт вала. Затем надевают распорную втулку мазеудерживающие кольца и устанавливают подшипники предварительно нагретые в масле.
После этого на валы надевают распорные кольца в подшипниковые камеры закладывают пластичную смазку ставят крышки подшипников с комплектом металлических прокладок для регулировки. Перед постановкой сквозных крышек в проточки закладывают манжеты резиновые армированные.
Собранные валы укладывают в основание корпуса редуктора и надевают крышку корпуса покрывая предварительно поверхности стыка крышки и корпуса спиртовым лаком. Для центровки устанавливают крышку на корпус с помощью двух конических штифтов затягивают болты крепящие крышку к корпусу.
Проверяют проворачиванием валов отсутствие заклинивания подшипников (валы должны проворачиваться от руки). Затем ввертывают пробку маслоспускового отверстия с прокладкой и устанавливают жезловый маслоуказатель.
Заливают в корпус масло и закрывают крышку смотрового отверстия крышкой с прокладкой закрепляют крышку болтами.
Собранный редуктор обкатывают и подвергают испытанию на стенде по программе устанавливаемой техническими условиями.
Сборка привода осуществляется следующим образом: на фундаменте при помощи специальных болтов устанавливается рама представляющая собой литую чугунную плиту; на раме устанавливается электродвигатель. На выходном конце вала электродвигателя устанавливается шкив поликлиноременной передачи. Затем на раме при помощи болтовых соединений крепится редуктор. На входном валу редуктора при помощи шпоночного соединения крепится шкив поликлиноременной передачи. На выходном валу редуктора крепится звездочка цепной передачи.
В курсовом проекте спроектирован привод ленточного конвейера на основе двухступенчатого редуктора открытая поликлинноременная передача открытая цепная передача. Произведены проектный и проверочные расчеты открытых передач.
В результате кинематического расчета привода был выбран двигатель с номинальной мощностью 75 кВт и номинальной частотой вращения 2925 обмин определены передаточное отношение.
Подобрана сталь 40 улучшенная для колес и шестерен.
Определены силы действующие в зацеплении проведен проверочный расчет на контактную и изгибную выносливость зубьев.
При расчете зубчатых передач определены главные параметры – межосевые расстояния подобран материал и произведены проверочные расчеты.
При проведении проектного расчета валов определены геометрические параметры валов произведен предварительный выбор подшипников и определены реакции опор.
В результате подбора подшипников качения определили динамическую грузоподъемность подшипников и их базовую долговечность. При сравнении этих параметров с базовой грузоподъемностью и требуемой долговечностью была определена пригодность подшипников.
Подобраны шпонки и назначены посадки деталей.
Определен способ смазки зубчатого зацепления и подшипников. Смазка осуществляется разбрызгиванием масла в полости редуктора. Назначен тип масла Индустриальное И - 30А ГОСТ 20799-88.
Разработан порядок сборки привода.
СПИСОК ИСПОЛЬЗОВАННОЙ ЛИТЕРАТУРЫ
Оформление пояснительных записок при курсовом проектировании и выполнении расчетно-графических работ.: Учебно-методическое пособие.сост.А.С.Сулейманов.–Уфа:Изд-во УГНТУ. 2011.–18с.
Александров М.П. Подъемно-транспортные машины. – М.: Высшая школа 1979. – 558 с.
Дьячков В.К. Машины непрерывного транспорта. – М.: Гостоптехиздат 1961. – 352 с.
Расчет зубчатых передач на прочность : Учебно-методическое пособие Сост. А.С. Сулейманов Э.А. Щеглов .- Уфа : Изд-во УГНТУ. 2004.–30 с.
ГОСТ 21354-87. Передачи зубчатые цилиндрические эвольвентные: Расчет на прочность . – М.: Изд-во стандартов 1988 . – 127 с.
Пример выполнения расчетной части проекта привода. Учебно-методическое пособиеСост. А.С.Сулейманов–Уфа: Изд-во УГНТУ2002.-30с.
Дунаев П.Ф. Леликов О.П. Конструирование узлов и деталей машин : Учеб. пособие для студ. техн. спец. вузов. - М. : Издательский центр «Академия» 2003 - 496 с.
Ременные передачи : Учебно-методическое пособие Сост. А.А. Комлев О.Г. Полканова . – Уфа : Изд-во УГНТУ 2004. – 25 с.
Расчет цепных передач.: Учебно-методическое пособиеСост. Митюрев Е.Д. Хлесткина В.Л.Сулейманов А.С.–Уфа: Изд-воУфим.нефт.техн.унив.2001.–19с.
Подшипники качения: Справочник – каталог Под ред . В.Н. Нарышкина
Р.В.Коросташевского . – М. – Машиностроение 1992. – 608 с. ил.
Допуски и посадки.: Методическое пособие.Сост.Митюрев Е.А. и др.–Уфа: Изд-во УГНТУ. 2007.–28с.
Вал III.cdw

Филиал ФГБОУ ВПО УГНТУ
5 285 НВ кроме места
*Размер обеспечивается инструментом
Редуктор-лист2.cdw

Рекомендуемые чертежи
- 24.01.2023
- 24.01.2023
Свободное скачивание на сегодня
Другие проекты
- 24.01.2023