Привод канатного подъемника



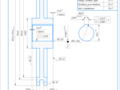
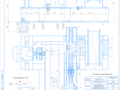
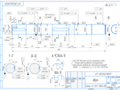
- Добавлен: 24.01.2023
- Размер: 726 KB
- Закачек: 1
Описание
Состав проекта
![]() |
![]() ![]() ![]() ![]() |
![]() ![]() ![]() |
![]() ![]() ![]() ![]() |
![]() |
![]() |
![]() ![]() ![]() ![]() |
![]() |
Дополнительная информация
сборка 1.2.cdw

Передаточное отношение
Смещение валов электродвигателя и редуктора не более:
Открытую передачу смазывать пластической смазкой
литол-24 1 раз в месяц.
В редуктор залить масло И-Г-А-46 5
Техническая характеристика
Технические требования
План фундамента (1:10)
ПЗ по ДМ.doc
Проектирование привода осуществляется на основании технического задания в котором содержится назначение основные характеристики и режим нагружения механизма. Содержание задания приведено на листе технического задания (страница 2).
Привод барабанного кантователя включает в себя: электродвигатель 1 комбинированную муфту 2 редуктор 3-х ступенчатый 3 открытую цепную передачу 4 служащую для передачи мощности от редуктора на исполнительный механизм барабан приводной 5 .
КИНЕМАТИЧЕСКИЙ И СИЛОВОЙ РАСЧЁТЫ ПРИВОДА
Канатного подъёмника. ВЫБОР ЭЛЕКТРОДВИГАТЕЛЯ
Рисунок 1 - Кинематическая схема привода канатного подъемника
1 Определение мощности на валу барабана исполнительного механизма
Мощность на валу барабана P4 кВ определяется по формуле:
где Ft - окружное усилие на барабане Н;
Vt - окружная скорость барабана мс. (см рис.1)
2 Определение расчетной мощности на валу электродвигателя
Расчетная мощность на валу двигателя Р1 кВ определяется с учетом потерь в приводе:
где - общий КПД привода
- КПД открытой цепной передачи 1=093;
- КПД закрытой зубчатой цилиндрической передачи 2=097; [1. табл.1]
При этом Р1== 1442 кВт.
3 Определение частоты вращения вала исполнительного механизма
Частота вращения вала n4 мин-1:
где D - диаметр барабана канатного подъёмника мм; (см рис.1)
4 Определение частоты вращения вала электродвигателя
Частота вращения вала электродвигателя n1 мин-1:
где i - передаточное отношение привода
i1 - передаточное отношение цилиндрического редуктора i1=45 200
Передаточные отношения выбираем средним из интервалов передаточных отношений
i =(45 200). (2 4) =90 800
n1=5732. (90 800)=516 45856 мин-1.
5 Выбор электродвигателя
Рисунок 2 - Электродвигатель АИР80В4УЗ
Типоразмер двигателя выбираем по расчетной мощности P1 и по намеченной частоте
Паспортная мощность двигателя должна быть близка к расчетной мощности P1 при
Выбираем двигатель АИР80В4УЗ (см рис.2)
Pдв =15 кВт nдв=1395 мин-1 nc=1500 мин-1
Тогда условие работоспособности выполняется :
Проверяем условие работоспособности при пуске :
где - кратность пускового момента двигателя;
- кратковременных пиковых перегрузок в приводе;
6 Определение передаточного отношения привода.
6.1Расчёт силовых и кинематических параметров
Уточняем передаточное отношение привода:
Подставляя значения получим:
Вычисляем передаточное отношение ip редуктора:
Выбираем редуктор по вращательному моменту на тихоходном валу (вал 3);
где T3- вращательный момент на тихоходном валу редуктора
Выбираем редуктор Ц3У-200 (см рис.3) с передаточным отношением ip=12939 и с вращательным моментом на тихоходном валу T3=200 (2000) тогда i2=188 ().
7 Определение мощностей вращающих моментов и частот вращения валов
Связь между мощностями и частотами вращения предыдущего и последующего валов:
где P2- мощность на быстроходном валу редуктора кВт;
где n2- частота вращения быстроходного вала редуктора мин-1
где P3- мощность на тихоходном валу редуктора кВт;
где n3-частота вращения тихоходного вала редуктора мин-1
Вращательные моменты на валах определяются по формулам:
где T1-вращательный момент на валу электродвигателя
где T2-вращательный момент на быстроходном валу редуктора
Вращательный момент на тихоходном валу редуктора найден ранее
Результаты расчета по п 1.7 для всех валов сведены в таблицу 1.
Частота вращения n мин-1
Таблица 1 Силовые и кинематические параметры привода.
РАСЧЕТ ОТКРЫТОЙ цепной передачи
Принимаем что цепь будет приводная роликовая двух рядная
1. Определим число зубьев ведущей звездочки.
Z1=31-2 i =31-21881=2723827 (округляем до не четного числа) (ист (2) ст.382)
2. Определяем число зубьев ведомой звездочки
Z2= Z1i=271881=5078750(округляем до ближайшего не четного в большую сторону)
3. Уточняем передаточное число цепной передачи
4. Определяем отклонения расчетного передаточного числа от табличного.
Δ i %=[ i цп уточн - iцп табл задан iцп табл]100=(1881-1852)1881=154 %
5. Ориентировочный шаг цепи (втулочно-роликовой приводной цепи)
5.а) Ткр вед зв =Ткр дв = 1143 Нм
5.в) m =2 (двухрядная)
5.г) Кэ - коэффициент учитывающий условия эксплуатации цепной передачи
Кэ = Кд Ка Км Крегулир Ксмазки Кп
5 г-1) Кд - коэффициент учитывающий динамическую нагрузку
5 г-2) Ка - коэффициент учитывающий межосевое расстояние
Ка = 125 (при а =20)
5 г-3) Кн -1 коэффициент учитывающий наклон передачи к горизонту
Км =015b Км =116 (при >45º)
5 г-4) Крег- коэффициент учитывающий способ натяжения цепи
Крег = 125 (при перемещении одной из звездочек)
5 г-5) Ксм - коэффициент учитывающий способ смазки и защиту от загрязнения
Ксм = 13 (при периодической смазке)
5 г-6) Кп - коэффициент учитывающий периодичность работы привода
Кп = 1 (при двух сменной работе)
5 г-7) Кн.р - коэффициент учитывающий неравномерность распределения нагрузки среди рядов многорядной цепи
К н.р =1 (для однорядной)
Кэ = 125 125 1 125 13 1= 254
5.д) [PF] - средне допустимое удельное давление в шарнире цепи
5.д-1) Выбираем из таблицы удельное давление в шарнире цепи при всех шагах и частотах двигателя (nдв=1000 обмин) [2] ст 386
Кz –поправочный коэфициент
Kz = 1 + 001 (Z1 – 17) = 1 + 001 (27-17) = 11
[PF] Z=27 = [PF] Z Kz
Принимаем для расчета ближайший стандартный шаг цепи
6) Проверка выбранной цепи
Определяемые параметры
Площадь опорной поверхности Амм2
Погонная нагрузка qкгм
Разрушающая нагрузка QH
Межосевое расстояние рекомендуемое амм
Межосевое расстояние в шагах аtц ш
Угол наклона ветвей цепи к линии центров γ º
Ориентировочное число звеньев в цепи уориен
до четного числа для соедин. Соедин. звеном
Проверяем условие по частоте вращения ведущей звездочки
781≤400 (ист (5) ст.168)
Проверяем число ударов цепи радс
nдоп.= удсек при шаге цепи = 1905
Смазка непрерывная под давлением.
Окружное усилие Ft Н
Удельная нагрузка шарниров цепи PFt Нмм2
Коэффициент запаса прочности цепи n>[n] доп
а)Q разр=25000 б)Кд=1 в)Ft=5792 г)Fv-усилие от центра сил =qVц2 д)Ff-усилие от провисанья цепи =5qagcos е) Fудар- усилие возникающее от ударов цепи по звездочки при Vц>10 мс =1310-7 n1tц3 Zряд
Уточняем значение межосевого расстояния в шагах по округленной величине ууточн числа звеньев
Расчетное межосевое расстояние аращ мм
Геометрический расчет звездочек
Диаметр делительной окружности звездочек мм
Определяем диаметр нагруженных окружностей
d1=1192 диам ролика цепи
Диаметр окружности впадин
Смещение центров дуг впадин
Высота прямого участка профиля зуба
Наибольшая хорда для контроля звезд с нечетным числом зубьев
КОНСТРУИРОВАНИЕ И РАСЧЕТ ИСПОЛНИТЕЛЬНОГО ОРГАНА
1 Составление схемы определения опорных точек и предварительных размеров
На валу размещают вращающиеся детали такие как звёздочки муфты и т.п. Вал служит той основной деталью с помощью которой вращающий момент передаётся от одной детали к другой. Конструкция нашего приводного вала будет состоять из нескольких ступеней. Образование ступеней на валу связано с необходимостью закрепления деталей на валу. В нашем случае на валу будут крепиться:
Пара подшипников качения
Для определения расстояний между этими деталями составим упрощённую схему приводного вала.
Упрощённая схема приводного вала
– середина конца вала
– середина левого подшипника
– середины ступиц узла барабана
– середина правого подшипника
Размер с1 предварительно принимаем равным 154 мм. Размеры с2 и с4 принимаем в отношении с2 = с4 = 270 мм.
Также для перечисленных деталей необходимо обеспечить посадочные места на валу.
2 Проектный расчет вала. Определение диаметров вала на отдельных участках
Определяющим размером является диаметр конца вала dвх так как от него будут зависеть диаметры последующих ступеней вала. Диаметр конца вала считается по формуле:
где Т4 – крутящий момент на тихоходном валу.
Концы валов берём стандартные цилиндрические короткого исполнения. Определив диаметр конца вала dвх по ГОСТ 12080 – 66 [2] находим остальные размеры конца вала. На этот конец вала будет крепиться муфта.
Таблица 2 Размеры цилиндрического конца вала
Далее определяем диаметр вала под посадочный диаметр подшипника исходя из условия прочности по максимальным касательным напряжениям:
где tк - касательное напряжение кручения.
[tк] - допускаемое напряжение кручения [tк] = 20 .30 Мпа.
Подставляя в полученное выражение числовые значения получим:
Найденное значение округляем в ближайшую сторону из ряда нормальных линейных размеров
(из ГОСТ 6636-69). Отсюда следует что dП = 80мм.
Для более удобной установки барабана на вал диаметр вала d в этом месте необходимо увеличить. Величину d определим по таблице стандартных чисел [2] значение которой будет равно следующему числу после полученного dП. В нашем случае
Длину ступицы барабана определим по формуле [5]
lСТ = ( 12 15 )×dвх (3.4)
lСТ = ( 12 15 )× 78 120 мм (3.5)
Диаметр ступицы барабана при этом равен
dСТ= ( 12 15 )× d = ( 12 15 )× 85 = 130 мм
Длину посадочной части под ступицу барабана берём на 16 20 мм больше длины ступицы. В нашем случае она равна 140 мм.
3 Расчет вала исполнительного механизма на статическую прочность
3.1 Составление расчетной схемы вала
с1 = 154 мм с2 = 200 мм с4=200 мм Ft = 10 кН = 10000 Н
S1 и S2 – силы натяжения в ветвях каната подъемника – рассчитывается по формулам:
S2 = 025·10000 = 2500 Н
S1 = 10000+2500 = 12500 Н
Q – приведенная сила от действия сил S1 и S2 приложенная к центру барабана рассчитывается по формуле:
Q = 12500+2500 = 15000 Н
Q1 и Q2 – силы приложенные в ступицах узла барабана – рассчитываются по формуле:
Расчетная схема вала показана на рис.4.
3.2 Определение реакции в опорах
Запишем условия равновесия:
Из этой системы уравнений выражаем реакции RA и RB
где = Q1 = Q2 с2=с4
Подставляя числовые значения найдём величины реакций RA и RB
3.3 Построение эпюр изгибающего и крутящего моментов
Определение моментов в различных точках приводного вала:
М3 = RA · c2 = 1005 Н·м
По полученным значениям строим эпюру изгибающего и крутящего моментов (рис.4). Исходя из эпюр моментов устанавливаем опасные сечения вала. В нашем случае это точка 3. Данное сечение подлежит проверке на прочность.
3.4 Статическая прочность вала
При расчете вала на статическую прочность он рассчитывается на совместное действие изгиба и кручения. Прочность характеризуется внутренними механическими напряжениями в деталях.
Прочность – способность сопротивляться разрушению при действии заданных нагрузок. Внутренние силы (межатомные межмолекулярные) действующие на единичной площадке называются внутренними механическими напряжениями. Они появляются при действии внешних сил. Они бывают нормальные и касательные. Нормальные напряжения – напряжения которые действуют перпендикулярно плоскости сечения. Основными материалами для валов служат углеродистые и легированные стали.
Так как жёсткость вала является определяющим параметром и для её обеспечения диаметр вала должен быть большим материалом для изготовления вала выбираем Сталь 45 прошедшую термическую обработку нормализацию.
где sи - действующее нормальное напряжение изгиба
tк - касательное напряжение кручения
[s] – допускаемое эквивалентное напряжение.
где [sи] – допускаемое напряжение изгиба
Кр – коэффициент режима работы Кр = 2.
где sТ – напряжение соответствующее пластической деформации металла для материала Ст. 45
[n] – коэффициент запаса прочности [n] = 3 4
Ми – момент изгибающий действующий в сечении вала (Н×м2)
В точке 3: МПа 100 Мпа.
Вывод: вал данную статическую нагрузку выдерживает.
4 Подбор стандартной шпонки. Расчет выбранной шпонки на прочность
Для передачи вращающего момента чаще всего применяют призматические или сегментные шпонки. В нашем случае будем применять высокие призматические шпонки прямоугольного сечения со скругленными концами. Стандарт предусматривает для каждого диаметра вала определённые размеры поперечного сечения шпонки. Используя диаметр конца вала dK определяем по ГОСТ 10748 – 68 [2] основные размеры шпонки.
Таблица 3 Размеры высокой призматической шпонки
Рабочие грани шпонок будем проверять на смятие
где Ар – площадь смятия мм2; мм (3.20)
- длина шпонки =125 мм
Ft – окружное усилие на валу Н;
Условие (3.19) выполняется следовательно шпонка способна передавать требуемый крутящий момент. В сечении 3 и 4 (рис.6) расчёт не проводим так как при одном и том же крутящем моменте диаметр вала сечения 3 и 4 больше следовательно шпонка выдержит.
5 Выбор типа подшипника и его размеров. Проверка подшипников на ресурс
Подшипники служат опорами для валов и вращающихся осей. Они воспринимают радиальные и осевые нагрузки приложенные к валу и сохраняют заданное положение оси вращения вала. Подшипники качения классифицируют по форме тел качения и по направлению воспринимаемой нагрузки. В нашем случае будем использовать шариковые радиальные сферические двухрядные подшипники по ГОСТ 28428 – 90 [2]. Первоначально назначим подшипники легкой серии. Размеры подшипника определяем по посадочному диаметру на вал dП. В нашем случае dП = 80 мм следовательно обозначение нашего подшипника 1216.
Крыша глухая будет: крыша 22-140 ГОСТ 18511-73
Корпус подшипника сквозной неразборный : корпус ШМ 140 ГОСТ 13218.1-80
Таблица 4 Основные размеры подшипника
Во избежание установки подшипника с перекосом вследствие малого отношения l d (l = B – ширина кольца подшипника d – посадочный диаметр подшипника на вал l d = 0353) для точности базирования подшипника на валу необходимо предусмотреть заплечник к торцу которого при сборке будет поджиматься подшипник. Высота заплечника должна образовывать достаточную опорную поверхность для торца кольца подшипника. Диаметр в этой части вала назовём диаметром буртика dБП. Величину dБП определим из условия:
Из стандартного ряда ([4] стр.410) выбираем (мм)
где r – фаска подшипника
Так как используемые подшипники одного типа и одного размера то расчёты будем проводить в наиболее нагруженной опоре которой является опора 2 (рис.6). Подшипники будем проверять на заданный ресурс.
L - долговечность подшипника;
Р – эквивалентная нагрузка;
С – динамическая грузоподъемность подшипника;
к - показатель степени к = 3 – для шариковых подшипников;
- коэффициент долговечности;
- коэффициент характеризующий совместное влияние на долговечность особых свойств металла деталей подшипника.
C – это такая нагрузка на подшипник радиальная для радиально - упорных подшипников или осевая для упорных упорно- радиальных при действии которой подшипник вырабатывает без дополнительного выкрашивания металла на телах качения или беговых дорожках 1 млн. оборотов с вероятностью 90. С берем из таблицы 24.12([4] стр. 419) то есть С=39.7 кН
Эквивалентная нагрузка на подшипник вычисляется по следующей формуле
где Fr– радиальная нагрузка Н
X- коэффициент учитывающий Fr
Y- коэффициент учитывающий Fa
Kб– коэффициент безопасности
Kт– коэффициент температуры
V – коэффициент вращения кольца V=1 (при вращении внутреннего кольца подшипника относительно направления радиальной нагрузки)
Из таблицы 24.11 ([4] стр. 419) выбираем X=1
Из таблицы 7.4 ([4] стр. 107) выбираем Кб =1.8
Из [4] стр. 107 выбираем Кт= 1
Из таблицы 7.5([4] стр. 108) выбираем
Из [4] стр. 108 выбираем
Кроме того известно что к =3 Fr = 4125 Н Fa =0
L переводим в Ln (часов)
где n – частота вращения вала
ПРОЕКТИРОВАНИЕ КОМбенированной МУФТЫ
1 Проектный расчет зубчатой полумуфты
Диаметр отверстия под вал dК = 80 мм;
Диаметр ступицы D2 = 90 мм;
Диаметр крышки D1 = 200 мм;
Диаметр фланца полумуфты D = 280 мм;
Ширина зубчатого венца b = 25 мм;
Модуль зацепления m = 3;
Число зубьев z = 48.
2 Проверочный расчет зубчатой полумуфты по напряжениям смятия рабочих поверхностей зуубьев
Условие прочности определяется формулой:
где – коэффициент динамичности режима нагрузки (= 2.288)
T4 – крутящий момент на начальной окружности зубчатого сопряжения
Условие прочности по данному критерию прочности выполнено.
3 Проектный расчет комбинированной муфты
Материал пар трения сталь закаленная - асбест
Диаметр отверстия под вал dR = 60 мм;
Диаметр ступицы D3 = 100 мм;
Наружный диаметр кольца контакта дисков DН = (35)dВАЛ (4.2)
Внутренний диаметр кольца контакта дисков DВ = (0506)DН (4.3)
DВ = 625 75 = 65 мм;
Средний диаметр кольца контакта дисков: мм; (4.4)
Допускаемое давление [p] = 025Мпа;
Коэффициент трения f = 015..018.
Требуемое число пар трения вычисляется по формуле:
Сила сжатия дисков определяется следующим соотношением:
4Расчет пружины фрикционной полумуфты
Для передачи вращающего момента диски фрикционной муфты должны сжиматься силой F = 16785 Н. По окружности можно расположить 6 цилиндрических винтовых пружин при условии что наружный диаметр Dнар 40 мм.
При включении муфты пружины дополнительно сжимаются на 3 мм причем приращение усилия F не должно превышать 20% от F.
Усилие приходящееся на одну пружину при включенной муфте
где zпр – количество пружин.
Строим характеристику пружины с учетом увеличения осадка пружины на 3 мм при возрастании силы от F1 до F2 (рис.13).
Рисунок 9 – Пружина сжатия
Определяем из подобия треугольников АОВ и СОЕ:
Т.к посадка витка на виток недопустима то предельная нагрузка не должна превышать F2 при зазоре между витками Sp = 01d.
Выбираем для пружин стальную углеродистую проволоку 2 класса по ГОСТ 9389 - 75
выбираем предел прочности при растяжении пружинной проволоки в и вычисляем допускаемое касательное напряжение []:
[] =04в=041450=580 МПа
Задаемся индексом пружины с = =6 и вычисляем коэффициент учитывающий влияние кривизны витков и поперечной силы k:
Учитывая формулу (4.10) вычисляем диаметр проволоки d:
Принимаем d=56 мм и вычисляем средний диаметр пружины D0 по формуле: D0=сd= 656=336 мм.
Число рабочих витков пружины z определяется по формуле:
где – G – модуль сдвига; для стали в среднем G=8104 МПа;
Полное число витков z1 вычисляется по формуле:
Шаг пружины t мм определяется как выражение:
Высота пружины при полном сжатии витков Н3 мм вычисляется по формуле:
Высота свободной пружины Н0 мм определяется выражением:
Н0= Н3+z(t-d) (4.16)
Н0=42+6(916-56)=6336 мм
Проверка пружины на устойчивость:
Условие выполнено ≤26 (18826).
Смазка зубчатых соединений редуктора осуществляется за счет окунания большего колеса в масло которое залито в корпус а так же за счет разбрызгивания масла.
Qmax.– определяется габаритами корпуса (внутренними размерами) чтобы обеспечить высоту масла в которую опускается зуб большего колеса (на всю высоту).
Из характеристики редуктора – Qmax= 6 л.
Из рекомендаций для червячных редукторов выбираем марку масла: масло Цилинаровое 52 ГОСТ 6411-76.[1табл.3]
Все подшипники смазываем смазкой ЛИТОЛ–24 ГОСТ 21150-75. Этой же смазкой смазываем и цепь.
Устиновский Е.П. Шевцов Ю.А. Яшков Ю.К. и др. Многовариантное проектирование зубчатых цилиндрических конических и червячных передач с применением ЭВМ: Учебное пособие к курсовому проектированию по деталям машин. – Челябинск: ЧГТУ 1995. – 102с.
Курсовое проектирование деталей машин: учеб. пособие для учащихся машиностроительных специальностей техникумов С.А. Чернавский К.Н. Боков И.М. Чернин и др. – 2-е изд. перераб. и доп. – М.: Машиностроение 1988. – 416 с.:ил.
Анурьев В.И. Справочник конструктора-машиностроителя: В 3-х т. – 6-е изд. перераб. и доп. – М.: Машиностроение 1992. – Т. 1. – 729 с. – Т. 2. – 783 с. – Т. 3. – 732 с.
Ряховский О.А. Иванов С.С. Справочник по муфтам. – Л.: изд. Политехника 1991. – 384 с.: ил.
Сохрин П.П. Оптимальное проектирование и расчет механизмов: Учебное пособие к выполнению заданий по курсу детали машин. Челябинск ЧПИ 1980. – 43 с.: ил.
Проектирование механических передач: Учебно-справочное пособие для вузов С.А. Чернавский Г.А. Снесарев Б.С. Козинцов и др. – 5-е изд. перераб. и доп. – М.: Машиностроение 1984.–560с.: ил.
МИНЕСТЕРСТВО ОБРАЗОВАНИЯ РОССИЙСКОЙ ФЕДЕРАЦИИ
ЮЖНО-УРАЛЬСКИЙ ГОСУДАРСТВЕННЫЙ УНИВЕРСИТЕТ
Кафедра «Теоретическая механика и основы проектирования машин»
Тема проекта: Привод привод канатного подъемника
Пояснительная записка к курсовому проекту по курсу
«Детали машин и основы конструирования»
НормоконтролерРуководитель
студент группы: АТ-351
Техническое задание ..2
КИНЕМАТИЧЕСКИЙ И СИЛОВОЙ РАСЧЁТЫ ПРИВОДА. ВЫБОР ЭЛЕКТРОДВИГАТЕЛЯ 4
1Определение мощности на валу исполнительного механизма .4
2Определение расчётной мощности на валу электродвигателя ..5
3Определение частоты вращения вала приводного барабана .5
4Выбор электродвигателя 5
5Определение передаточного отношения привода. Расчёт силовых и кинематических параметров привода 7
ПРОЕКТИРОВАНИЕ ОТКРЫТОЙ ЦЕРНОЙ ПЕРЕДАЧИ 11
1Расчёт открытой передачи 11
2 Конструкция цепной передачи ..13
3 Конструктивные размеры звёздочек ..14
РАСЧЕТ УПРУГО-ПРЕДОХРАНИТЕЛЬНОЙ МУФТЫ ..14
1 Выбор стандартной упругой полумуфты ..14
3Расчёт пружины сжатия . 15
КОМПОНОВКА ВАЛА БАРАБАНА КАНТОВАТЕЛЯ 18
1 Предварительный расчет вала 18
2 Ориентировочный выбор подшипников 19
3 Выбор крышек и корпуса подшипников 20
4 Дополнительные конструктивные размеры барабана .21
5 Линейные размеры вала 23
6 Проверка работоспособности шпоночных соединений вала барабана .25
7 Проверка ресурса работы подшипников .25
РАСЧЕТНАЯ СХЕМА ВАЛА БАРАБАНА 25
1 Определение опорных реакций 25
2Проверка работоспособности вала барабана .28
звездочка1.cdw

Радуисы скруглений 2
Сталь 45 ГОСТ 1050-88
вал1.2.cdw

* Размер обеспечивается инструментом.
Неуказанные предельные отклонения размеров:
Сталь 45 ГОСТ 1050-88