Привод ГПМ




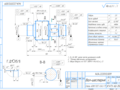
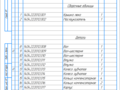
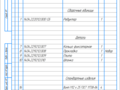
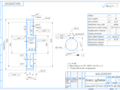
- Добавлен: 24.01.2023
- Размер: 2 MB
- Закачек: 0
Описание
Привод ГПМ
Состав проекта
![]() |
![]() ![]() ![]() |
![]() |
![]() ![]() ![]() ![]() |
![]() |
![]() ![]() ![]() ![]() |
![]() ![]() ![]() ![]() |
![]() ![]() ![]() ![]() |
![]() ![]() ![]() ![]() |
![]() ![]() ![]() ![]() |
![]() |
![]() ![]() ![]() |
![]() ![]() ![]() ![]() |
![]() ![]() ![]() |
![]() ![]() ![]() |
Дополнительная информация
1. Титульный лист.doc
ПОЯСНИТЕЛЬНАЯ ЗАПИСКА
к курсовому проекту по Деталям машин .
(обозначение документа)
вал-шестерня.cdw

Нормальный исходный контур
Коэффициент смещения
кроме места указанного особо.
*Размер обеспечить инструментом.
Общие допуски по ГОСТ 30891.1: Н14;
Сталь 40ХН ГОСТ 4543-71
спецификация Привода.spw

Винт М12 х 25 ГОСТ 11738-84
Винт М16 х 40 ГОСТ 11738-84
Винт А.М10-6gx18 ГОСТ 1478-93
Шайба A.20.37 ГОСТ 11371-78
Шайба 20.37 ГОСТ 11872-89
Шайба 12 ГОСТ 6402-70
Шайба 16 ГОСТ 6402-70
Двигатель асинхронный
Chertezh11111.cdw

Чертеж привода2.cdw

Эл. двигатель АИРС112М4
Потребляемая мощность
Частота вращения вала эл. двигателя
Частота вращения вала
Момент на выходном валу редуктора
Режим работы ГОСТ21354-87 2
Технические требования:
Смещения валов электродвигателя и редуктора не более:
* Размер для справок
Отверстие центровое F М16
Спецификация.spw

Шайба маслоотражательная
Винт А.М6-6gx18 ГОСТ 17473-80
Винт М12-6gX45 ГОСТ 11738-84
Манжета 1.1-35x50-1 ГОСТ 8752-79
Манжета 1.1-50x70-1 ГОСТ 8752-79
Подшипник 107 ГОСТ 8338-75
Подшипник 110 ГОСТ 8338-75
Шайба 6Л ГОСТ 6402-70
Шайба 12 ГОСТ 6402-70
Штифт 2.8*20 ГОСТ 3128-70
Чертеж сборочный.cdw

Вращающий момент на выходном валу
Частота вращения быстроходного вала
Передаточное отношение редуктора.
Режим работы по ГОСТ 21354-84.
Основные параметры зацепления.
Перед сборкой детали промыть
Подшипники освободить от консервации промывкой в
промывочной жидкости;
Монтаж соединений с натягом вести с нагревом охватывающей
детали до температуры 150-200
Установку подшипников качения произвести с нагревом
подшипника в масляной ванне до температуры не более 95
При окончательной сборке плоскость разъема обработать
герметиком УТ-34 ГОСТ 24285-80;
В корпус редуктора залить масло ИГП-49 ТУ 38.101413-97 в
. 1. без нагрузки - 3ч
. 2. при полной нагрузке - 6ч
Температура корпуса не более 70
После обкатки масло слить. Контролировать наличие стружки в
* Размер для справок.
Технические требования.
Техническая характеристика:
Число зубьев шестерни
эпюра.frw

колесо зубчатое.cdw

Нормальный исходный контур
Коэффициент смещения
Сталь40ХН ГОСТ4543-81
Общие допуски по ГОСТ 30893.1: Н14;
* Размер обеспечить инструментом.
3. Пояснительная записка.docx
ВЫБОР ОПТИМАЛЬНОГО ВАРИАНТА КОМПОНОВКИ РЕДУКТОРА8
ГЕОМЕТРИЧЕСКИЙ РАСЧЕТ ЗУБЧАТЫХ ПЕРЕДАЧ11
КИНЕМАТИЧЕСКИЙ РАСЧЕТ РЕДУКТОРА13
СТАТИЧЕСКОЕ ИССЛЕДОВАНИЕ РЕДУКТОРА14
1 Моменты на валах и колесах редуктора.14
2 Составляющие полного усилия в зацеплениях быстроходной и тихоходной передач14
3 Определение нагрузок на подшипники промежуточного вала15
РАСЧЕТ ЗУБЧАТОЙ ПЕРЕДАЧИ ТИХОХОДНОЙ СТУПЕНИ18
1 Выбор материала зубчатых колес18
2 Определение допускаемых напряжений18
2.1 Допускаемые контактные напряжения18
2.2 Допускаемые напряжения изгиба20
3 Определение напряжений21
3.1 Определение контактных напряжений в зацеплении передачи21
3.2 Определение напряжений изгиба22
ПОДБОР ПОДШИПНИКОВ ДЛЯ ВАЛОВ24
1 Определение ресурса подшипников промежуточного вала24
ПРОЕКТИРОВОЧНЫЙ РАСЧЕТ ВАЛОВ РЕДУКТОРА26
ПРОЕКТИРОВАНИЕ ЗУБЧАТЫХ КОЛЁС29
1 Основные конструктивные размеры косозубого колеса быстроходной ступени29
2 Основные конструктивные размеры косозубого колеса тихоходной ступени30
ПРОВЕРОЧНЫЙ РАСЧЕТ ПРОМЕЖУТОЧНОГО ВАЛА.31
1 Определение реакций в опорах и построение эпюр внутренних силовых факторов.31
2 Расчёт на статическую прочность.34
Для сечения 1 – 1: ступенчатый переход с галтелью34
3 Проверка промежуточного вала на усталостную прочность36
3.1 Для сечения 1 – 1: ступенчатый переход с галтелью37
3.2 Для сечения 2-2: сечение вала с шпоночным пазом38
РАСЧЕТ СОЕДИНЕНИЙ ПРИЗМАТИЧЕСКИМИ ШПОНКАМИ39
ОПРЕДЕЛЕНИЕ ОСНОВНЫХ РАЗМЕРОВ КОРПУСНЫХ ДЕТАЛЕЙ.39
1 Основные размеры корпуса редуктора39
2 Обоснование выбора конструкции крышек подшипников39
3. Обоснование выбора конструкции манжетных уплотнителей39
4 Определение размеров проушин корпуса редуктора39
5 Конструирование прочих элементов редуктора39
ПРОЕКТИРОВАНИЕ ЧЕРТЕЖА ПРИВОДА39
СПИСОК ИСПОЛЬЗОВАННОЙ ЛИТЕРАТУРЫ39
Приложение А – Эскизы стандартных изделий39
Привод грузоподъемной машины был сконструирован для передачи крутящего момента на барабан который обеспечивает поднятие груза со скоростью 061 мс.
Привод грузоподъемной машины(рис. 1.1) состоит из электродвигателя двух муфт редуктора барабана троса. Электродвигатель и барабан присоединены к редуктору при помощи муфт. Подъем груза осуществляется тросом который наматывается на барабан. Барабан приводится в движение от электродвигателя через редуктор и муфты. Редуктор осуществляет повышение крутящего момента и снижение частоты вращения до требуемой величины.
Рисунок 1.1 Схема привода грузоподъемной машины.
Редуктор состоит из косозубых быстроходной и тихоходной передач. Смазка зубчатых колес и подшипников осуществляется картерным методом т.е. корпус редуктора является резервуаром для масла и в процессе работы колеса вращаясь разбрызгивают масло внутри корпуса.
Для корпуса редуктора была применена современная конструкция. Все выступающие элементы устранены с наружных поверхностей и введены внутрь. Проушины для подъема и транспортировки редуктора отлиты заодно с корпусом.
Для удобства сборки корпус выполняют разъемным. Плоскость разъема проходит через оси валов.
ПОДГОТОВКА ДАННЫХ ДЛЯ ВВОДА В КОМПЬЮТЕР
Определим диаметр каната dk:
Диаметр каната определяется по нормам Госгортехнадзора
dk = 01 = 01 = 85 (мм);
где Fк – сила натяжения троса;
Dб = (е-1) dk ; е = 18
где е – коэффициент установленный Госгортехнадзором для режима работы 4;
Dб = (18-1)·6 = 1445 (мм).
Примем Dб = 145 (мм).
Частота вращения барабана:
где v – скорость наматывания троса;
Для подбора электродвигателя определим:
где =09 – КПД барабана;
= 098 – КПД зубчатого зацепления;
= 099 – КПД подшипника;
=085· 099· 093· 1 2 = 083.
) потребную мощность электродвигателя:
где P – потребляемая мощность электродвигателя;
) передаточное отношение редуктора
где nдвиг – частота вращения вала электродвигателя;
nбар – частота вращения барабана;
Для определения оптимального передаточного отношения составим таблицу значений:
Таблица 2.1 Частоты вращения электродвигателей.
Асинхронный трехфазный
Выберем из таблицы следующие значения:
По таблице 24.9 [2] выбираем электродвигатель 112M41440850:
P=55кВт и п=1440 обмин.
Определим крутящий момент на колесе тихоходной ступни редуктора:
Вращающий момент на барабане:.
где = 1 – КПД муфты;
Принимаем Т2Т = 584 (Н·м).
Рассчитаем эквивалентное время работы в часах:
LHE = Lh· Н = 16·0125·1000 = 200ч
ВЫБОР ОПТИМАЛЬНОГО ВАРИАНТА КОМПОНОВКИ РЕДУКТОРА
Произведем расчет 3 вариантов компоновки редуктора с целью нахождения наиболее оптимального из них.
Рисунок 3.1 - Схема редуктора
Данный вид расчета осуществляется по следующим формулам:
L =(05*dw1 Б+ mn)+aw Б +aw Т+(05*dw1 Т+ mn);
=885мм примем a=9 мм;
где – коэффициент пропорциональности.
А- высота редуктора;
В- ширина редуктора;
V – объем корпуса редуктора;
bwТ – ширина венца тихоходной ступени;
bwБ – ширина венца Быстроходной ступени;
dw1Б – диаметр шестерни быстроходной ступени;
dw2Б – диаметр колеса быстроходной ступени;
dw2Т – диаметр колеса тихоходной ступени;
awБ – межосевое расстояние быстроходной ступени;
awТ – межосевое расстояние тихоходной степени;
a – зазор между корпусом и вращающимися деталями передач (колесами) (одно значение для всех вариантов).
L =(05*dw1 Б+ mn)+aw Б +aw Т+(05*dw1 Т+ mn)=(05*3555+ 150)+85 +140+(05*23119+ 25)=36237 (мм);
A =dw2 Т +2mn=23119+2*25=23619 (мм);
B =25a +bwТ + bwБ =25*88+271+44=931(мм);
V = ABL= 2361910 -293110 -23623710 -2=797 (л);
L =(05*dw1 Б+ mn)+aw Б +aw Т+(05*dw1 Т+ mn)=(05*3385+ 150)+90 +135+(05*21857+ 25)=35521 (мм);
A =dw2 Т +2mn=21857+2*25=22357 (мм);
B =25a +bwТ + bwБ =25*88+296+46=976(мм);
V = ABL= 2235710 -297610 -23552110 -2=775 (л);
L =(05*dw1 Б+ mn)+aw Б +aw Т+(05*dw1 Т+ mn)=(05*3505+ 2)+100 +130+(05*20337+ 25)=35371 (мм);
A =dw2 Т +2mn=20337+2*25=20837 (мм);
B =25a +bwТ + bwБ =25*88+275+439=934(мм);
V = ABL= 2083710 -293410 -23537110 -2=6884 (л);
Оптимизацию по критериям минимального объема и массы зубчатых колес проведем построением графика зависимости V и m от количества вариантов:
Рисунок 3.2 – График объемов и масс редуктора для трёх вариантов
Из Рисунка 3.2 можно сделать вывод о том что наилучшая компоновка редуктора достигается в третьем случае т.к. при этом редуктор обладает оптимальными параметрами (объемом и массой).
ГЕОМЕТРИЧЕСКИЙ РАСЧЕТ ЗУБЧАТЫХ ПЕРЕДАЧ
Геометрический расчет выполняется в минимальном объеме. Определению подлежат: делительные d1 и d2 и начальные dw1 и dw2 диаметры колес; коэффициенты смещения X1 и диаметры окружностей вершин da1 и угол зацепления w; коэффициент торцевого перекрытия ; коэффициент осевого перекрытия для косозубых колес. Все колеса нарезаются реечным инструментом или долбяком с исходным контуром по ГОСТ 13755-81 с параметрами: угол профиля = 20; коэффициентом головки (ножки) зуба ; коэффициент радиального зазора с* = 025.
Выполним расчет для быстроходной шевронной передачи:
Коэффициенты смещения колес равны нулю т.к. суммарный коэффициент смещения X = X1 + X2 = 0.
СледовательноW = =20
– делительные диаметры приводятся в распечатке:
–начальные диаметры:
- коэффициент торцового перекрытия:
- коэффициент осевого перекрытия:
- суммарный коэффициент перекрытия:
Выполним расчет для тихоходной косозубой передачи:
Коэффициенты смещения колес равны нулю т.к. суммарный коэффициент смещения
КИНЕМАТИЧЕСКИЙ РАСЧЕТ РЕДУКТОРА
Определение крутящих моментов и частот вращения зубчатых колес:
Частота вращения быстроходного вала
n1 = nдвиг = n1Б = 1440 (обмин);
Частота вращения промежуточного вала
n2 = n2Б = n1Т = = 30573 (обмин)
где uб = 471 - передаточное число быстроходной ступени;
Частота вращения тихоходного вала
n3 = n2Т = nБ = = 8516 (обмин)
где uТ = 359 - передаточное число тихоходной ступени;
Окружная скорость в зацеплении быстроходной передачи
V = dw1Б n1 (610 4) = 3505 1440 (610 4)=26 (мс);
Окружная скорость в зацеплении тихоходной передачи
V = dw1Т n1Т (610 4) = 5663 30573 (610 4)=09 (мс).
СТАТИЧЕСКОЕ ИССЛЕДОВАНИЕ РЕДУКТОРА
Рисунок 6.1 – Схема усилий в зацеплении
1 Моменты на валах и колесах редуктора.
Момент на шестерне тихоходной ступени и на колесе быстроходной ступени:
Момент на шестерне быстроходной ступени:
2 Составляющие полного усилия в зацеплениях
быстроходной и тихоходной передач
Окружная сила на шестерне тихоходной ступени:
Радиальная сила на шестерне тихоходной ступени:
Осевая сила на шестерне тихоходной ступени:
Окружная сила на шестерне быстроходной ступени:
Радиальная сила на шестерне быстроходной ступени:
Осевая сила на шестерне быстроходной ступени:
где – угол наклона зубьев (указан в распечатке);
w – угол зацепления.
Окружная сила на колесе быстроходной ступени:
Радиальная сила на колесе быстроходной ступени:
Осевая сила на колесе быстроходной ступени:
Окружная сила на колесе тихоходной ступени:
Радиальная сила на колесе тихоходной ступени:
Осевая сила на колесе тихоходной ступени:
3 Определение нагрузок на подшипники промежуточного вала
Рассмотрим промежуточный вал а также действующие на него нагрузки:
Этот рисунок не подходит надо исправить
Рисунок 6.2 – Действующие нагрузки на промежуточный вал
Рассчитаем расстояние между колесами и шестернями:
Определим нагрузки на подшипники от сил в зацеплении.
Сумма моментов относительно опоры 3:
Сумма моментов относительно опоры 4:
Определим радиальные и осевые реакции опор:
РАСЧЕТ ЗУБЧАТОЙ ПЕРЕДАЧИ ТИХОХОДНОЙ СТУПЕНИ
1 Выбор материала зубчатых колес
При выборе материалов для зубчатых колес необходимо обеспечить прочность зубьев на изгиб стойкость поверхностных слоев зубьев и сопротивление заедания. Материалы и термообработку зубчатых колес выбираем по справочнику [1] таблица 8.9.
Шестерня - материал сталь 35ХМ;
Твердость поверхности зубьев 48 56 Н
Термообработка Улучшение и закалка ТВЧ.
Колесо - материал Сталь 45;
Твердость поверхности зубьев 260 320НВ;
Термообработка - улучшение.
2 Определение допускаемых напряжений
2.1 Допускаемые контактные напряжения
Допускаемые контактные напряжения рассчитаем по формуле:
где – допускаемые контактные напряжения для шестерни тихоходной ступени;
- допускаемые контактные напряжения для колеса тихоходной ступени;
где - предел длительной прочности соответствующий базовому числу циклов;
SH – коэффициент безопасности.
ZN – коэффициент долговечности.
По таблице 89[1] определяем
=1750+200=1050 (МПа);
Коэффициент долговечности.
где NHG1 = 8010 6;по рисунку 8.40 [1].
NHE1 – эквивалентное число циклов соответствующее
NHE1 = NH H = 60 nw n1 Lh H =601305731600025=73410 6;
где nw – число зацеплений в которое входит шестерня или колесо за один оборот в нашем случае nw = 1;
n1 – соответствующая частота вращения;
Lh – ресурс привода;
H – коэффициент режима определяемый по табл. 8.10 [1] в зависимости от категории режима.
Рассчитаем коэффициент долговечности:
Допускаемые контактные напряжения:
По таблице 89[1] определяем:
=2·290+70=650 (МПа);
Коэффициент долговечности определяем по формуле 861[1].
где NHG2 =2310 6 по рис 8.4 [1];
NHE2 – эквивалентное число циклов соответствующее
NHE2 = NH H = 60 nw n1 Lh H =60185161600025=20410 6;
Рассчитаем допускаемые контактные напряжения:
2.2 Допускаемые напряжения изгиба
Допускаемое напряжение изгиба определим по формуле:
YА – коэффициент учитывающий влияние двустороннего приложения нагрузки (при односторонней нагрузке KFC=1);
YR – коэффициент учитывающий шероховатость переходной кривой.(YR = 1 при шероховатости RZ 40 мкм);
YN – коэффициент долговечности;
SF – коэффициент безопасности;
Рассчитаем пределы выносливости для колеса и шестерни (табл.8.9 [1]);
Flim2 = 18НВ = 18290 = 522 (МПа).
Принимаем значение коэффициентов безопасности для шестерни и колеса
SF = 175 (табл.8.9 [1]);
Коэффициент долговечности определим по формуле :
где NFG = 410 6 – базовое число циклов;
NFE – эквивалентное число циклов;
Эквивалентное число циклов определим по формуле:
где F – коэффициент эквивалентности (табл.8.10 [1])
для шестерни: F = 01;
для колеса: F = 0143;
Nк – число циклов перемены напряжений за весь срок службы;
где с – число зацеплений зуба за один оборот колеса;
п – частота вращения;
NFE1 =F1 Nк1 = 60сп1LH F1 = 6013057316000.143 = 4110 6;
NFE2 =F2 Nк2 = 60сп2LH F2 = 601851616000.1 = 08210 6;
Допускаемые изгибные напряжения равны:
3 Определение напряжений
3.1 Определение контактных напряжений в зацеплении передачи
Выполним проверочный расчет по контактным напряжениям.
Контактные напряжения определяются по формуле:
Коэффициент расчетной нагрузки:
где KH - коэффициент концентрации нагрузки;
KHV - коэффициент динамической нагрузки;
KH - коэффициент распределения нагрузки между зубьями.
Коэффициент распределения нагрузки между зубьями KH=107 (табл. 8.7 [1]).
Коэффициент ширины шестерни относительно диаметра:
Коэффициент концентрации нагрузки при постоянной нагрузке при bd = 0775 примем KH = 111 (по рис.8.15 для графика II [3]).
Коэффициент динамической нагрузки при v = 09мс определим по табл.8.3[1]:
Коэффициент расчетной нагрузки
KH = KHKHVKH= 111102107 = 121.
Eпр – приведенный модуль упругости. Для стальных колес и шестерен
Т1 – момент на шестерни передачи;
dw1 – начальный диаметр шестерни;
bw – ширина зубчатого венца колеса;
w – угол зацепления;
u – передаточное число передачи .
Коэффициент ZH определяется по формуле:
где – коэффициент торцевого перекрытия;
– угол наклона зубьев на делительном диаметре.
Величина контактного напряжения
условие прочности выполняется.
3.2 Определение напряжений изгиба
Напряжения в основании зубьев колес определяются по формулам:
гдеYF – коэффициент формы зуба;
Эквивалентное число зубьев:
где z – число зубьев
Коэффициент формы зуба (по рис.8.20 [1]):
ZF – коэффициент вычисляемый по формуле
KF – коэффициент учитывающий распределение нагрузки между зубьями равный 122 (табл. 8.7 [1]);
Y – учитывает работу зуба как пластины (а не балки) и определяется равенством
Y = 1 –140=1-13795140=0901;
ZF = KFY=12209011645=0668
Коэффициенты расчетной нагрузки
Коэффициент распределения нагрузки между зубьями (по табл.8.7[1]):
Коэффициент концентрации нагрузки (по рис 8.15 [1]):
Коэффициент динамической нагрузки (по табл.8.3[1]):
F1 = YF1ZFFtKF(bwm)=40206685862156(56325)=1745 (МПа);
F2 = F1 YF2 YF1.=1745 374402=1623 (МПа).
Условия прочности для шестерни и колеса выполняются.
Рассмотренная ступень редуктора обеспечит необходимую долговечность и ресурс в заданных условиях нагружения.
ПОДБОР ПОДШИПНИКОВ ДЛЯ ВАЛОВ
Для быстроходного вала-шестерни выберем по ГОСТ 8338-75 роликовые радиальные подшипники с короткими цилиндрическими роликами 208.
Внутренний диаметр подшипников быстроходного вала определим по формуле:
где r=15 (мм) – переходной радиус( по табл.19[3]);
Примем dП = 35 мм. По ГОСТ 8338-75 выбираем шариковый радиальный однорядный подшипник 107 (легкая серия).
Определим внутренний диаметр подшипников промежуточного вала:
Примем мм. По ГОСТ 8338-75 выбираем шариковый радиальный однорядный подшипник 107 (особо легкая серия).
Внутренний диаметр подшипников тихоходного вала:
(мм) примем d=45 мм.
Примем dП = 50 мм. В соответствии с требуемой грузоподъемностью (1911 кН) выбираем подшипник 210 (легкая серия).
1 Определение ресурса подшипников промежуточного вала
Рассчитаем подшипник по динамической грузоподъемности по формуле:
где а1 = 1 – коэффициент надежности;
а2 = 1 – обобщенный коэффициент совместного влияния качества металла и условий эксплуатации;
α = 3 (для шариковых подшипников);
n – частота вращения;
– эквивалентная нагрузка;
X Y – коэффициенты радиальной и осевой нагрузок (по табл.16.5 [1])
V – коэффициент вращения зависящий от того какое кольцо вращается (при вращении внутреннего кольца V = 1);
k – коэффициент безопасности учитывающий характер нагрузки ( при умеренных толчках k = 13)
kT – температурный коэффициент (при температуре до 100 С 0 kT = 1).
Для подшипника 107 по ГОСТ 8338-75 определим параметры подшипника:
Динамическая грузоподъемность С = 159 (кН);
Статическая грузоподъемность С0 = 85 (кН).
е = 030 (табл.16.5 [1]);
Эквивалентная нагрузка:
Lh LHE исходя из этого делаем вывод о работоспособности подшипника.
ПРОЕКТИРОВОЧНЫЙ РАСЧЕТ ВАЛОВ РЕДУКТОРА
Рис. 9.1 Конструкции валов редуктора
Проектный расчет валов носит ориентировочный характер и имеет цель определить основные размеры и форму вала связанные с нагрузками и назначением его основных элементов.
Диаметры участков валов:
– для быстроходного вала
Полученный размер согласуем с диаметром вала электродвигателя d1
d=(08 12)d1=(08 12)32=256 384 (мм) примем d=32 (мм).
– для промежуточного вала диаметр в месте установки зубчатых колес
Полученный диаметр согласуем со стандартным числовым рядом следовательно dК = 40 (мм);
– для тихоходного вала
Полученный диаметр согласуем со стандартным числовым рядом следовательно d = 45 (мм);
Диаметр буртика для упора кольца подшипника и колеса:
dБП = dП + 3 r=35+3 15= 395 (мм)
– для промежуточного вала
dБК = dК + 3 f=40+312=436 (мм)
dБП = dП + 3 r=50+325=575 (мм)
dБК = dК + 3 f= 56+316=608 (мм)
Значения переходных радиусов и заплечиков приведены в табл. 1.9[3]
Консольные участки входного и выходного вала выполнены коническими по ГОСТ 12081-72. Конический конец входного вала выполнен с наружной резьбой (Рисунок 6) а конец выходного вала выполнен с внутренней резьбой (Рисунок. 7).
Размеры выходного вала определяются по справочнику табл.24.27 [2].
Рисунок 9.2 – Конструкция консольного участка
Отверстие центровое F М16
Рисунок 9.3 – Конструкция консольного
участка выходного вала.
ПРОЕКТИРОВАНИЕ ЗУБЧАТЫХ КОЛЁС
1 Основные конструктивные размеры косозубого колеса быстроходной ступени
lСТ =(0.8 1.5)d ([2] стр. 68)
где d – диаметр посадочного отверстия
lСТ =(0.8 1.5) 40=32 60 мм
Ширина зубчатого венца
Диаметр ступицы колеса ([2] стр. 68)
для стали dСТ =(1.5 1.55)d=(1.5 1.55) 40=60 62 мм;
Принимаем dСТ =60 мм;
Ширина торца зубчатого венца
S=2.2m+0.05bw =2.22+0.0524=56 мм;
На косозубых колесах при твердости рабочих поверхностей менее 350 HB
выполняют фаску под углом 450.
Толщина диска: ([2] стр. 68)
C=(0.35 0.4)bw=(0.35 0.4) 24=84 96 мм;
Принимаем С=10 мм для облегчения механической обработки колеса.
Рис. 10.1 Эскиз колеса быстроходной ступени
2 Основные конструктивные размеры косозубого колеса тихоходной ступени
lСТ =(0.8 1.5) 56=448 84 мм.
Принимаем lСТ=56 мм.
для стали dСТ =(1.5 1.55)d=(1.5 1.55) 56=84 868 мм;
Принимаем dСТ =84 мм;
S=2.2m+0.05bw =2.225+0.0538=74 мм;
C=(0.35 0.4)bw=(0.35 0.4) 38=133 152 мм;
Рис. 10.2 Эскиз колеса тихоходной ступени
ПРОВЕРОЧНЫЙ РАСЧЕТ ПРОМЕЖУТОЧНОГО ВАЛА.
1 Определение реакций в опорах и построение эпюр внутренних силовых факторов.
Вал изображён на рис. 7.1. Материал – сталь 40ХМ имеющая следующие характеристики:5
Предел текучести при изгибе
Предел текучести при кручении
Предел выносливости при изгибе
Предел выносливости при кручении
Коэффициенты чувствительности к асимметрии цикла
Из расчётов зубчатых передач редуктора:
максимальный крутящий момент ;
силы в зацеплении ; ;
из чертежа редуктора: .
Реакции в опорах ищем из условий и .
Определение реакций в опорах в плоскости XZ:
Рис 11.1 Расчетная схема с обозначением всех активных и реактивных сил действующих на вал.
Проверка правильности определения реакций:
Определение реакций в опорах в плоскости YZ:
Построение эпюр. Значения изгибающих моментов в характерных сечениях вала:
Значения изгибающих моментов в характерных сечениях вала:
Значения суммарных изгибающих моментов в характерных сечениях вала:
Анализ эпюр внутренних силовых факторов и несущей способности сечений вала показал что опасными сечениями являются сечения:
-1 – место перехода от шестерни к валу;
-2 – место шпоночного соединения вала с колесом и соединение с натягом.
2 Расчёт на статическую прочность.
Для сечения 1 – 1: ступенчатый переход с галтелью
Определение геометрических характеристик опасных сечений вала:
Определение действующих напряжений:
Значение общего коэффициента запаса прочности в сечении 1-1 > значит статическая прочность в сечении 1-1 обеспечена.
Для сечения 2-2: сечение вала со шпоночным пазом
Определение геометрических характеристик:
Значение общего коэффициента запаса прочности в сечении 2-2
значит статическая прочность в сечении 2-2 обеспечена.
3 Проверка промежуточного вала на усталостную прочность
Опасными сечениями являются сечения 1 – 1 и 2 – 2.
Для каждого из установленных предположительно опасных сечений вала вычисляем общий коэффициент S запаса прочности:
где и – коэффициенты запаса по нормальным и касательным напряжениям определяемые по зависимостям:
где и – коэффициенты снижения предела выносливости; и – пределы выносливости материала вала; и – коэффициенты чувствительности материала к асимметрии цикла нагружений для рассматриваемого сечения.
3.1 Для сечения 1 – 1: ступенчатый переход с галтелью
Концентратором напряжений является ступенчатый переход с галтелью. Расчёт ведём с использованием табличных данных:
Концентратором напряжений является ступенчатый переход с галтелью:
Значения эффективных коэффициентов концентрации напряжений для ступенчатого перехода с галтелью принимаем по графикам 4: ;
Значения коэффициентов влияния абсолютных размеров поперечного сечения 5:
Значения коэффициентов влияния качества поверхности при шероховатости :
Значение коэффициента влияния поверхностного упрочнения 5:
Значения коэффициентов снижения предела выносливости:
Амплитуды напряжений и среднее напряжение цикла:
Коэффициенты запаса:
Значение общего коэффициента запаса прочности в сечении 1-1 > значит усталостная прочность в сечении 1-1 обеспечена.
3.2 Для сечения 2-2: сечение вала с шпоночным пазом
В сечении 2-2 источником концентрации напряжений являются шпоночный паз выполненный концевой фрезой и натяг при установке колеса на вал.
Значения эффективных коэффициентов концентрации напряжений для шпоночного паза 5 таб. 41:
Значения коэффициентов влияния абсолютных размеров поперечного сечения 5 таб. 44:
Значения коэффициентов влияния качества поверхности при шероховатости Ra=32 мкм для шпоночного паза 5 таб. 45:
Значения коэффициентов и для соединения с натягом 5 таб. 43:
Значения коэффициентов влияния качества поверхности при шероховатости Ra=08 мкм для соединений с натягом принемаем по таблице 5 таб. 45:
Значения коэффициентов снижения предела выносливости для шпоночного паза:
Значения коэффициентов снижения предела выносливости для соединения с натягом:
Из полученных значений коэффициентов снижения выносливости в сечении 2-2 выбираем для расчета коэффициенты с наибольшими значениями и .
Значение общего коэффициента запаса прочности в сечении 2-2 > значит усталостная прочность в сечении 2-2 обеспечена.
РАСЧЕТ СОЕДИНЕНИЙ ПРИЗМАТИЧЕСКИМИ ШПОНКАМИ
Подбор шпонок произведем по таблицам
стандартов ГОСТ23360-78 для соединений типа
вал-ступица. Принимаем величину допускаемых
напряжений смятия [см] = 120 (МПа).
Определим рабочую длину шпонки:
)Для колеса быстроходного вала:
l1 = lр1 + b=156+12=276 (мм) Рисунок 12.1 – Шпоночное соединение
согласуем со стандартным
числовым рядом l=28 (мм).
где Т – вращающий момент на колесе тихоходной ступени;
) Для колеса тихоходного вала:
l3 = lр3 + b=309+16=469 (мм)
согласуем со стандартным числовым рядом l=50 (мм).
) Для входного вала:
l4 = lр4 + b=62+6=122 (мм)
l4=(06 065)lк=(06 065)·58=(348 377)
где lк- длина концевого участка вала
согласуем со стандартным числовым рядом l=36 (мм).
) Для выходного вала:
l5 = lр5 + b=529+12=649 (мм)
согласуем со стандартным числовым рядом l=70 (мм).
ОПРЕДЕЛЕНИЕ ОСНОВНЫХ РАЗМЕРОВ КОРПУСНЫХ ДЕТАЛЕЙ.
1 Основные размеры корпуса редуктора
Основные размеры определяющие внешние очертания корпуса находят в функции толщины стенки вычисляемой по формуле:
Толщина крышки редуктора 1
= (08 09)=(56 63)=6 (мм);
Ширина фланца разъема корпуса f
f = (2 22)=(2 22)7=(14 154)=15 (мм);
Диаметр d резьбы винта соединяющего крышку и основание корпуса
Диаметр df фундаментных винтов
df = 125d=12512=15 (мм)
2 Обоснование выбора конструкции крышек подшипников
Торцевые крышки предназначены для герметизации подшипников качения осевой фиксации подшипников и восприятию осевых нагрузок. В данной работе применим закладные крышки не требующие крепления винтами или болтами что в свою очередь упрощает конструкцию и процесс сборки.
Рисунок 13.1 – Крышка подшипника
Толщина стенки крышки
=6 (мм);([2] стр.169)
S = (09 1)=(09 1)6=54 6=6 (мм);
3. Обоснование выбора конструкции манжетных уплотнителей
Резиновые армированные однокромочные манжеты с пружиной предназначены для уплотнения валов. Манжеты работают в минеральных маслах воде дизельном топливе при избыточном давлении до 005 МПа скорости до 20 мс и температуре от -60 до 170 С. Что удовлетворяет нашим условиям работы
Манжету обычно устанавливают открытой стороной внутрь корпуса.
К рабочей кромке манжеты в этом случае обеспечен хороший доступ смазочного масла.
Рисунок 13.2 – Манжета
4 Определение размеров проушин корпуса редуктора
Для подъема и транспортировки крышки корпуса и собранного редуктора применяют проушины (рисунок 15) отливая их заодно с крышкой. В данном случае проушина выполнена в виде ребра с отверстием.
Рисунок 13.3 – Проушина
5 Конструирование прочих элементов редуктора
Для наблюдения за уровнем масла в корпусе устанавливают маслоуказатели жезловые (щупы).
При длительной работе в связи с нагревом воздуха повышается давление внутри корпуса. Это приводит к просачиванию масла через уплотнения и стыки. Чтобы избежать этого внутреннюю полость корпуса сообщают с внешней средой путем установки отдушин в его верхних точках.
Крышку фиксируют относительно корпуса штифтами. Штифты предотвращают взаимное смещение деталей при растачивании отверстий под подшипники обеспечивают точное расположение деталей при повторных сборках.
Люк в верхней части крышки используют не только для заливки масла но и для осмотра зацепления колес. Размеры его приняты по возможности большими форма - прямоугольной.
Люк закрывают крышкой. В данном проекте используется штампованная крышка объединенная с отдушиной и фильтром. Крышка состоит из плоской верхней пластины на которой выдавлены гофры через которые внутренняя полость редуктора соединяется с атмосферой. В нижней штампованной части имеются 6 отверстия диаметром 5 мм. Эта часть крышки по периметру окантована про вулканизированной резиной. Фильтр состоящий из тонкой медной проволоки заполняет пространство между верхней и нижней частями крышки. Крышка крепится винтом М6.
Рисунок 13.4 – Крышка люка редуктора
Для замены масла в корпусе предусмотрено сливное отверстие закрываемое пробкой с конической резьбой. Коническая резьба создает герметичное соединение поэтому дополнительного уплотнения не требуют.
Рисунок 13.5 – Маслосливная пробка.
ПРОЕКТИРОВАНИЕ ЧЕРТЕЖА ПРИВОДА
При монтаже привода состоящего из электродвигателя и редуктора должны быть выдержаны определенные требования точности относительного положения узлов. Для этого узлы привода устанавливают на плиту.
Конфигурацию и размеры плиты определяют тип и размеры редуктора и электродвигателя.
Для создания базовых поверхностей под двигатель и редуктор на плите размещают платики в виде узких полос. Ширину и длину платиков принимают большими чем ширина и длина опорных поверхностей электродвигателя и редуктора.
В ходе выполнения курсовой проекта был спроектирован привод грузоподъемной машины. Для этого был разработан редуктор с рациональными показателями массы размеров и себестоимости отвечающий требованиям по безотказной работе и ресурсу. К редуктору были подобраны двигатель и муфта. А также разработана конструкция плиты.
СПИСОК ИСПОЛЬЗОВАННОЙ ЛИТЕРАТУРЫ:
Задания на курсовой проект: методические указания к курсовому проектированию по дисциплине «Детали машин и основы конструирования» Сост.: Прокшин С.С. Сидоренко А.А. Федоров В.А. Минигалеев С.М. – Уфа: УГАТУ 2006. – 34 с. ил.
Дунаев П.Ф. Леликов О.П. «Конструирование узлов и деталей машин» - М.: Высшая школа 1985 - с.416.
Иванов М.Н. «Детали машин»- М.: Высшая школа 1991 - с.383.
Анурьев В.И. «Справочник конструктора - машиностроителя» том 1. - М.: Машиностроение 1978 - с. 728.
Анурьев В.И. «Справочник конструктора - машиностроителя» том 2. - М.: Машиностроение 1979 - с. 559.
Решетов Д.Н. «Детали машин» - М.: Машиностроение1989 - с. 496.
М.Ш. Мигранов и др. Расчёт и конструирование одноступенчатого зубчатого редуктора. Учебное пособие УГАТУ – 2003 г.
Приложение А – Эскизы стандартных изделий
Подшипник ГОСТ 8328-75
Обозначение подшипника
Манжета ГОСТ 8752-79
Шпонка ГОСТ 23360-78
Двигатель асинхронный АИР 112L4
Рекомендуемые чертежи
Свободное скачивание на сегодня
Другие проекты
- 20.09.2021