Основы технологии производства машин




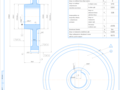
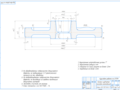
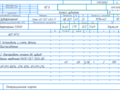
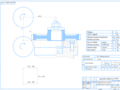
- Добавлен: 24.01.2023
- Размер: 478 KB
- Закачек: 0
Описание
Состав проекта
![]() |
![]() |
![]() ![]() ![]() ![]() |
![]() ![]() ![]() ![]() |
![]() |
![]() ![]() ![]() ![]() |
![]() ![]() ![]() ![]() |
![]() ![]() ![]() ![]() |
![]() ![]() ![]() |
![]() ![]() ![]() ![]() |
![]() ![]() ![]() |
![]() ![]() ![]() ![]() |
![]() ![]() ![]() |
![]() ![]() ![]() ![]() |
![]() ![]() ![]() |
![]() ![]() ![]() ![]() |
![]() ![]() ![]() |
![]() ![]() ![]() ![]() |
![]() ![]() ![]() |
Дополнительная информация
2.cdw

Неуказанные радиусы 4мм
Смещение по линии разьема не более 1
Коробление не более 1
На обрабатываемых поверхностях допускаются
не превышающие 12 фактического
припуска на мех. обработку.
На необрабатываемых поверхностях допускаются
не выходящие за пределы наименьших
допускаемых размеров.
Заготовки очистить от окалины.
Класс точности 4 по ГОСТ7505 - 74
(заготовка штампованная)
Сталь 45Х ГОСТ4543-71
Курсовая работа по ОТ
1.cdw

Курсовая работа по ОТ
Материал-заменитель - сталь 40ХС ГОСТ 1045-87
* Размеры обеспеч. инстр.
Неуказанные предельные отклонения размеров Н14
Покрытие Хим. Фос. прм.
Маркировать Ч шрифтом 6-Пр3 ГОСТ 26.008-85.
Коэффициент смещения
Степень точности по ГОСТ 1643-81
Допуск на колебание длины общей нормали
Допуск на колебание
межосевого расстояния
Допуск на погрешность направления зуба
Радиус развернутости эвольвенты в начале
рабочего участка профиля
Схема сборки.cdw

Операционный эскиз.cdw

Маршрут1.cdw

Код наименование оборудования
Обозначение документа
Сталь 45Х ГОСТ 4543-71
Горизонтально-протяжной 7А250
без КЭ; без ОК; ИОТ N 95
Токарный с ЧПУ 16К20Ф3
без КЭ; без ОК; ИОТ N 65
без КЭ; без ОК; ИОТ N 70
без КЭ; без ОК; ИОТ N 87
Пример2.doc
Курганский государственный университет
Кафедра технологии машиностроения
«Основы технологии производства машин»
Студент: Тупицына Л.В.
Преподаватель: Мосталыгин А.Г.
Анализ служебного назначения изделия и расчет размерной цепи
Разработка схемы сборки
Разработка рабочего чертежа детали
Разработка эскиза заготовки
Проектирование маршрутного технологического процесса
Проектирование технологической операции фрезерования
Список используемых источников
В процессе выполнения данной курсовой работы анализируется предложенный сборочный чертеж задается тип производства. Производится размерный анализ с выявлением размерной цепи и ее решением. Опираясь на сборочный чертеж изделия составляется его схема сборки. Разрабатывается рабочий чертеж предложенной детали. Для данной детали разрабатывается эскиз заготовки из которой в последствии будет изготовлена деталь. Сюда не относится составление маршрутного технологического процесса.
Для обработки конкретных поверхностей для одной операции проектируется операционный технологический процесс. Выполняется операционный эскиз обработки заготовки дается обоснование выбора технологических баз выбора станочного оборудования.
Для обработки и изготовления детали рекомендуется применять современный режущий инструмент станочный парк позволяющий в наибольшей степени оптимизировать технологический процесс обработки а также контроля готового изделия.
АНАЛИЗ СЛУЖЕБНОГО НАЗНАЧЕНИЯ ИЗДЕЛИЯ И РАСЧЕТ РАЗМЕРНОЙ ЦЕПИ
1.Анализ служебного назначения
Редуктор червячный одноступенчатый с внутренним зацеплением предназначен для изменения частоты вращения и крутящего момента в условиях эксплуатации. Редуктор имеет цилиндрический корпус с плоской круглой боковой крышкой. Быстроходный вал - шестерня установлен в конических роликоподшипниках требующих регулировки в осевом направлении. Поэтому для них необходима накладная крышка под которую уложены регулировочные прокладки.
В курсовой работе рассматривается тихоходный вал.
Для изготовления вала необходимо выбрать материал обладающий повышенной износостойкостью и высокой твердостью. Для этих целей выбираем легированную конструкционную сталь марки 20Х с последующим упрочнением поверхностного слоя применив закалку ТВЧ на глубину порядка 2 3 мм. Сердцевина детали изготовленной из хромистой стали имеет изначально высокий предел текучести а закаленный поверхностный слой – высокую твердость.
Общими техническими условиями эксплуатации являются:
-не допускать перегрузок редуктора сверх установленной нормы;
-своевременно менять масло в редукторе и следить за уровнем масла;
-хранить редуктор рекомендуется в полностью собранном состоянии при котором непосредственного допуска к его рабочим поверхностям нет.
2.Расчет размерной цепи
Расчитаем размерную цепь состоящую из трех увеличивающих и семи уменьшающих звеньев по методике изложенной в 2.
Схема размерной цепи
Рисунок 1 – Схема размерной цепи
где А1 А5 монтажная высота конических подшипников
А2 А4 распорные кольца
А6 А8 размер по крышке подшипника
А3 ширина ступицы зубчатого колеса
А7 размер по корпусу редуктора
Замыкающее звено это зазор в подшипниках необходимый для нормальной работы его кинематической пары .
Номинальный размер Ан=03 мм.
Тогда допуск замыкающего звена с учетом что имеется два подшипника
Размерную цепь будем решать методом полной взаимозаменяемости который является простым и обеспечивает 100%-ную взаимозаменяемость.
В данном случае необходимо решить прямую задачу; для ее решения применим способ одного квалитета который используется когда размеры входящие в размерную цепь по своей величине значительно отличаются друг от друга.
Номинальные размеры звеньев: А1=А5=2975 мм; А2= А4 =10 мм;
А3=80 мм; А6= А8 =20 мм; А7=1998 мм;
Для монтажной высоты Т=2975 мм подшипников 7510 ГОСТ 333-71 отклонения по ГОСТ 520-71 равны ±025 мм т.е. ТА1=ТА5=05 мм.
где ам – среднее число едениц допуска в размерах цепи;
- сумма единиц допусков составляющих звеньев в цепи;
m – общее количество звеньев в цепи.
Для А2=10 – А3=80 – А4=10 – А6=20 –
Найденное число единиц допуска близко к 8 квалитету.
Устанавливаем допуски и назначаем отклонения для звеньев цепи:
А2= А4 =10-0027 мм; А3=80-0054 мм; А6=А8=20-0033 мм;
Проверка ТАΔ= 12=1174 т.е. необходимо скоректировать одно из звеньев цепи (А7).
вА7=вА+(нА1 +нА2 +нА3 +нА4 +нА5 +нА6 +нА8)
вА7=06+(-025-0027-0054-0027-025-0033-0033)=-0074 мм.
нА7=нА+(вА1 +вА2 +вА3 +вА4 +вА5 +вА6 +вА8)
нА7=-06+(025+0+0+0+025+0+0)=-0100 мм.
РАЗРАБОТКА СХЕМЫ СБОРКИ
Схема сборки определяет взаимную связь элементов изделия и позволяет установить их последовательность комплектования. Последовательность сборки в основном определяется конструкцией изделия и его отдельных элементов а также методами достижения требуемой точности.
Схема сборки позволяет наглядно представить весь технологический процесс проверить правильность выполнения намеченной последовательности операций.
По заданному сборочному чертежу изделия составим его схему сборки используя методику изложенную в 23.
Выбираем исходной деталью на которую монтируем другие корпус редуктора 1 на него прикручиваем крышку 9 болтами 24затем устанавливаем в нишу подшипник 29 на внутреннее кольцо которого накладывается втулка 17в них вставляем вал 4 в предварительно подведенную через поддон шестерню в сборе cо шпонкой 32 затем надеваем еще одну втулку 17поверх одеваем еще один подшипник 29закрываем полученную конструкцию крышкой в сборе и закрепляем болтами 24.
Таким образом спроектированный и изложенный технологический процесс является оптимально технологичным что до минимума уменьшает временны е и материальные затраты на его осуществлен
РАЗРАБОТКА РАБОЧЕГО ЧЕРТЕЖА ДЕТАЛИ
Разработка рабочего чертежа детали производится в соответствии с действующими стандартами ЕСКД.
Подготовительный этап: ознакомление с конструкцией детали указываем на чертеже выбранный ранее материал детали сталь 20Х. Исходя из габаритов и формы детали (вал) располагаем ее на чертеже горизонтально.
Основной этап: выбираем масштаб построения 1:1 для более точного вычерчивания элементов детали. Указание на чертеже отклонений и определение шероховатости производим в экономически и технологически достижимых пределах а также из функционального назначения поверхностей конструктивных особенностей детали условий работы 4.
Строим необходимые виды и разрезы для полного представления о форме детали.
Указываем на чертеже технические требования необходимые для изготовления детали с нужными свойствами.
Составленный рабочий чертеж детали содержит основные данные для выбора формы и размеров заготовки проектирование маршрутного технологического процесса и операционного технологического процесса.
РАЗРАБОТКА ЭСКИЗА ЗАГОТОВКИ
В данном разделе использована методика изложенная в 5.
В нашем случае как и во многих других требуется высокая прочность и плотность заготовки и так перепад диаметров невелик выбираем в качестве заготовки пруток D=60 мм L=285 мм. весом 63 кг
ПРОЕКТИРОВАНИЕ МАРШРУТНОГО ТЕХНОЛОГИЧЕСКОГО ПРОЦЕССА ИЗГОТОВЛЕНИЯ ВАЛА
В данном разделе использована методика описанная в 34.
В результате разработки технологического процесса определяем необходимое оборудование технологическую оснастку и др.
Технологический процесс представляет собой совокупность различных операций в результате выполнения которых изменяется форма размеры осуществляется контроль требований чертежа и технических условий.
Маршрутное описание технологического процесса заключается в сокращенном описании всех технологических операций в последовательности их выполнения без указания переходов и технологических режимов.
В соответствии с чертежем детали разработаем технологический маршрут и оформим его в виде таблицы.
Обрабатываемые поверхности детали
Технологический маршрут
Наименование и краткое содержание операций
Фрезерно – центровальная
фрезеровать поверхности 12
сверлить центровые отверстия
фрезерно – центровальный па МР-71М
точить поверхности 3457
токарный с ЧПУ 16К20Ф3
Продолжение таблицы 1.
точить поверхности 1011
фрезеровать два шпоночных паза (поверхности 1213)
фрезерный с ЧПУ 6Р13РФ3
закалка нагревом ТВЧ
шлифовать поверхности 511
круглошлифовальный с ЧПУ 3М151Ф2
ПРОЕКТИРОВАНИЕ ТЕХНОЛОГИЧЕСКОЙ ОПЕРАЦИИ ФРЕЗЕРОВАНИЯ ШПОНОЧНЫХ ПАЗОВ
1.Расчет режимов резания
Расчет ведется одновременно с заполнением операционных карт технологического процесса: запись данных по оборудованию способу обработки характеристики обработки обрабатываемой детали 6.
Определяем расчетную величину скорости резания:
Выбираем значение стойкости инструмента и значения коэффициентов входящих в формулу: Т=80 мин; Cv=467; q=045; y=05; u=p=01; m=033; при t=16 мм; В=6 мм; Sz=012 мм.
Определим число оборотов шпинделя:
Станок может обеспечить n=250 обмин тогда V=1414 ммин.
Станок может обеспечить такую минутную подачу.
Вычислим величину силы резания:
где CP=682; y=072; u=1; q=086; w=0;
Мощность резания определяется по формуле:
Мощность которую должен обеспечить станок:
где Nдв – мощность электродвигателя привода главного движения кВт; – механический КПД.
2.Технологическое нормирование операций
При обработке в условиях среднесерийного типа производства на станке с ЧПУ определяется штучно – калькуляционное время (Тш-к) состоящее из штучного (Тшт) и подготовительно – заключительного времени на партию деталей (Тп-з) которое определяется по зависимости 4:
Тш-к=Тшт+Тп-з nЗ(6.7)
где nЗ – размер партии деталей запускаемых в производство шт.
Норма штучного времени обработки детали:
Тшт=to+tв+tобс+tп(6.8)
где tо= - основное время на операцию мин; tВ – вспомогательное время мин; tобс – время обслуживания рабочего места мин; tп – время на личные потребности мин.
Основное время на выполнение j – го перехода:
где L – длина обрабатываемой поверхности мм; n – частота вращения шпинделя обмин; S – подача ммоб.
tв=tв.у+tм.в=022+6822500=049 мин.
Времена tобс и tп принимаются в процентном отношении от оперативного времени (tоп):
tоп=0.91+049=14 мин.
(tобс + tп)=012×14=017 мин.
Подготовительно – заключительное время включает в себя:
Tп-з=Tп-з1+Tп-з2+Tп-з3(6.11)
где Tп-з1 – время на приемы вошедшие в комплекс Tп-з1=12 мин; Tп-з2 – время дополнительных работ Tп-з2=23 мин; Tп-з3 – время на пробную обработку детали Tп-з3=5 мин.
Tп-з=12+23+5=40 мин.
Тш-к=0.91+049+017+40600=1.64 мин.
3.Выбор технологических баз и расчет погрешности установки заготовки
Выбор технологических баз имеет первостепенное значение при проектировании технологических процессов. При выборе баз учитывается вид операции точность и производительность обработки и многие другие факторы.
Для выполнения фрезерной операции за технологические базы принимаем обработанные на предыдущих операциях цилиндрические поверхности и торец. Эти технологические базы являются оптимальными т.к. обеспечивают устойчивое положение заготовки относительно станка а также надежное ее закрепление с минимальными деформациями.
Суммарная погрешность установки:
При обработке партии заготовок в одноместном приспособлении на настроенном станке погрешность приспособления вызывает систематическую погрешность обработки и может быть скомпенсирована при наладке (подналадке) поэтому при расчете погрешности установки не учитывается. Тогда учитывая что погрешности Еб и Ез являются случайными величинами можно записать:
Погрешность базирования:
Погрешность закрепления:
где KRZ=0005; KHB=15; m=1; C1=0226; HB=240; Q=2000 H.
4.Выбор средств технологического оснащения
Современное машиностроение на сей день имеет ярко выраженную тенденцию к повышению качества точности обрабатываемых изделий и невозможно будет реализовать спроектированный технологический процесс без соответствующего технологического оснащения. При выборе конкретных моделей станков необходимо учитывать:
-соответствие габаритных размеров заготовки размерам рабочей зоны оборудования;
-требования обеспечения точности и качества обрабатываемых поверхностей;
-технологические возможности станка.
Средствами технологического оснащения были выбраны:
-станок на котором производится обработка детали фрезерный с ЧПУ 6Р13РФ3 что позволяет в значительной степени автоматизировать процесс обработки исключив тем самым частично человеческий фактор довольно сильно влияющий на качество детали;
-фрезерование шпоночных пазов производится специальной фрезой материал рабочей части Р6М5 заданной геометрии.
Анализ служебного назначения изделия позволил максимально уточнить и сформулировать задачу для решения которой предназначено изделие.
Дальнейшим анализом была составлена размерная цепь решение которой было необходимо для разработки чертежей детали. В результате расчета размерной цепи были найдены соответствующие значения параметров всех составляющих звеньев являющиеся экономически достижимыми.
Составленная схема сборки изделия является оптимально технологичной в условиях среднесерийного производства что значительно сокращает затраты на его осуществление.
Составленный рабочий чертеж детали содержит основные данные для выбора заготовки проектирования маршрутного технологического процесса.
В соответствии с чертежом детали также был разработан технологический маршрут обработки поверхностей детали и сведен в таблицу 1.
Проведенные расчеты режимов резания позволяют точно определить уровень технологического оснащения так например мощность станка. Кроме того необходимо создать условия повышающие надежность технологической системы и стабильности процесса обработки.
Было произведено нормирование операции и выбраны базы.
СПИСОК ИСПОЛЬЗУЕМЫХ ИСТОЧНИКОВ
Сборочный чертеж редуктора.
Толмачевский Н.Н. Доможиров А.П. Методы достижения точности сборки: Учебное пособие. – Курган: КМИ 1992 г. – 62 с.
Мосталыгин Г.П. Толмачевский Н.Н. Технология машиностроения. – М: Машиностроение 1990 г. – 288 с.
Справочник технолога – машиностроителя: В 2-х т. Т1 Под ред. А.Г. Косиловой и Р.К. Мещерякова. – М.: Машиностроение 1985 г. – 656 с.
Марфицын В.В. Давыдова М.В. Минин И.А. Выбор способа изготовления заготовок. Методические указания. – Курган.: КГУ 1997 г. – 80 с.
Справочник технолога-машиностроителя В 2-х т. Т2 Под ред. А.Г. Косиловой и РК Мещерекова - М:Машиностроение 1986 г. - 496 с.
Маршрут3.cdw

наименование оборудования
сб.единицы или материала
Обозначение документа
Зубошлифовальный 5Д833Д
без КЭ; без ОК; ИОТ N 51
без КЭ; без ОК; ИОТ N 74
без КЭ; без ОК; ИОТ N 84
без КЭ; без ОК; ИОТ N 91
Обрабатываемые поверхности.cdw

Операционная карта.cdw

Обозначение программы
Сталь 45Х ГОСТ 4543-71
Установить и снять деталь.
Фрезеровать начерно 86 зубьев
Фреза червячная Р6М5 ГОСТ 9324-80
КР-РМ-100%; OTK-10%; KM-PM-2%
Титульный.cdw

Курганский государственный университет
Утверждаю: Зав.кафедрой
на технологический процесс механической обработки
Пример1.doc
Курганский государственный университет
Кафедра технологии машиностроения
«Основы технологии производства машин»
Студент: группы М-4118
Преподаватель: канд. техн. наук доцент
Анализ служебного назначения изделия и расчет размерной цепи4
Разработка схемы сборки7
Разработка рабочего чертежа детали8
Проектирование маршрутного технологического процесса изготовления зубчатого колеса 11
Проектирование технологической операции зубофрезерования 13
Список используемых источников 19
В процессе выполнения данной курсовой работы анализируется предложенный сборочный чертеж задается тип производства. Производится размерный анализ с выявлением размерной цепи и ее решением. Опираясь на сборочный чертеж изделия составляется его схема сборки. Разрабатывается рабочий чертеж предложенной детали. Для данной детали разрабатывается эскиз заготовки из которой в последствии будет изготовлена деталь. Сюда не относится составление маршрутного технологического процесса.
Для обработки конкретных поверхностей для одной операции проектируется операционный технологический процесс. Выполняется операционный эскиз обработки заготовки дается обоснование выбора технологических баз выбора станочного оборудования.
Для обработки и изготовления детали рекомендуется применять современный режущий инструмент станочный парк позволяющий в наибольшей степени оптимизировать технологический процесс обработки а также контроля готового изделия.
АНАЛИЗ СЛУЖЕБНОГО НАЗНАЧЕНИЯ ИЗДЕЛИЯ И РАСЧЕТ РАЗМЕРНОЙ ЦЕПИ
1.Анализ служебного назначения
Редуктор червячно-цилиндрический двухступенчатый с внешним зацеплением предназначен для изменения частоты вращения и крутящего момента в условиях эксплуатации. Редуктор имеет разъёмный корпус с плоской круглой боковой крышкой.
В курсовой работе рассматривается зубчатое колесо.
Для изготовления колеса необходимо выбрать материал обладающий повышенной износостойкостью и высокой твердостью. Для этих целей выбираем легированную конструкционную сталь марки 20ХН2М с последующим упрочнением поверхностного слоя применив закалку. Сердцевина детали изготовленной из хромистой стали имеет изначально высокий предел текучести а закаленный поверхностный слой – высокую твердость.
Общими техническими условиями эксплуатации являются:
-не допускать перегрузок редуктора сверх установленной нормы;
-своевременно менять масло в редукторе и следить за уровнем масла;
-хранить редуктор рекомендуется в полностью собранном состоянии при котором непосредственного допуска к его рабочим поверхностям нет.
2.Расчет размерной цепи
Рассчитаем размерную цепь состоящую из трех увеличивающих и семи уменьшающих звеньев по методике изложенной в 2.
Схема размерной цепи
Замыкающее звено А=10..20 мм. Номинальный размер Ан=15 мм.
Тогда допуск замыкающего звена ТАΔ=10 мм.
Размерную цепь будем решать методом полной взаимозаменяемости который является простым и обеспечивает 100%-ную взаимозаменяемость.
В данном случае необходимо решить прямую задачу; для ее решения применим способ одного квалитета который используется когда размеры входящие в размерную цепь по своей величине значительно отличаются друг от друга.
Номинальные размеры звеньев: А1=А5=39 мм; А2=1105 мм; А3=70 мм;
А4=12 мм; А6=19 мм; А7=2 мм;
А8=306 мм; А9=2 мм; А10=19 мм.
Для монтажной высоты Т=39 мм подшипников 413 ГОСТ 33-71 отклонения по ГОСТ 520-71 равны -015 мм т.е. допуск ТА1=ТА5=015 мм а ТА1+ТА5=0.3мм
где ам – среднее число единиц допуска в размерах цепи;
- сумма единиц допусков составляющих звеньев в цепи;
m – общее количество звеньев в цепи.
Для А2=1105 – А3=70 – А4=12 – А6=19 –
А7=2 – А8=306 – А9=2- A10=19- i=131.
Найденное число единиц допуска близко к 10 квалитету.
Устанавливаем допуски и назначаем отклонения для звеньев цепи:
А2=1105-014 мм; А7= А9=2+004 мм; А3=70-012 мм; А4=12-007 мм;
Рассчитаем величину допуска для 8-го звена:
РАЗРАБОТКА СХЕМЫ СБОРКИ
Схема сборки определяет взаимную связь элементов изделия и позволяет установить их последовательность комплектования. Последовательность сборки в основном определяется конструкцией изделия и его отдельных элементов а также методами достижения требуемой точности.
Схема сборки позволяет наглядно представить весь технологический процесс проверить правильность выполнения намеченной последовательности операций.
По заданному сборочному чертежу изделия составим его схему сборки используя методику изложенную в 23. (Схема сборки приведена в приложении лист 1).
РАЗРАБОТКА РАБОЧЕГО ЧЕРТЕЖА ДЕТАЛИ
Разработка рабочего чертежа детали производится в соответствии с действующими стандартами ЕСКД.
Подготовительный этап: ознакомление с конструкцией детали указываем на чертеже выбранный ранее материал детали сталь 40ХН2М. Исходя из габаритов и формы детали (вал) располагаем ее на чертеже горизонтально.
Основной этап: выбираем масштаб построения 1:2 для более точного вычерчивания элементов детали. Указание на чертеже отклонений и определение шероховатости производим в экономически и технологически достижимых пределах а также из функционального назначения поверхностей конструктивных особенностей детали условий работы 4.
Строим необходимые виды и разрезы для полного представления о форме детали.
Указываем на чертеже технические требования необходимые для изготовления детали с нужными свойствами.
Составленный рабочий чертеж детали содержит основные данные для выбора формы и размеров заготовки проектирование маршрутного технологического процесса и операционного технологического процесса.
1 Разработка эскиза заготовки
В данном разделе использована методика изложенная в 5.
В нашем случае как и во многих других требуется высокая прочность и плотность заготовки поэтому заготовку выбираем для среднесерийного типа производства при массе детали 463 кг изготавливаемую способом штамповки на ГКМ.
Степень сложности – С2
Конфигурация поверхности разъема штампа – П (плоская)
Исходный индекс – 14
Основные припуски на размеры:
толщина 70 мм и Ra=63 мкм – 20 мм
диаметр 310 мм и Ra=63 мкм – 27 мм
диаметр 70 мм и Ra=63 мкм – 20 мм
Дополнительные припуски учитывающие: смещение по поверхности разъема штампа – 04 мм; изогнутость отклонение от плоскостности и прямолинейности – 05 мм.
толщина 70+(20+04+05)*2=768 мм; принимаем 77 мм
диаметр 310+(27+04+05)*2=3172 мм; принимаем 317 мм
диаметр 70-(20+04+05)*2=638 мм; принимаем 64 мм
Радиус закругления наружных углов – 30 мм внутренних –7 мм.
Штамповочный уклон - 5º.
Допускаемые отклонения размеров:
Допускаемая величина смещения по поверхности разъема штампа – 10 мм.
2 Расчет себестоимости изготовления заготовки
Себестоимость заготовки определяется по формуле:
Значения коэффициентов берутся из справочника 7: C KT=1; KM=1.15; KC=0.87; KB=0.8; KП=1 (KП=092 для КГШП); SОТХ=285.
Экономический эффект от применения нового метода получения заготовки можно определить по формуле:
ПРОЕКТИРОВАНИЕ МАРШРУТНОГО ТЕХНОЛОГИЧЕСКОГО ПРОЦЕССА ИЗГОТОВЛЕНИЯ ВАЛА-ШЕСТЕРНИ
В данном разделе использована методика описанная в 34.
В результате разработки технологического процесса определяем необходимое оборудование технологическую оснастку и др.
Технологический процесс представляет собой совокупность различных операций в результате выполнения которых изменяется форма размеры осуществляется контроль требований чертежа и технических условий.
Маршрутное описание технологического процесса заключается в сокращенном описании всех технологических операций в последовательности их выполнения без указания переходов и технологических режимов.
В соответствии с чертежом детали разработаем технологический маршрут и оформим его в виде таблицы.
Рис. 5.1. Обрабатываемые поверхности
Технологический маршрут
Наименование и краткое содержание операций
Заготовительная - ГКМ
расточить на черно и на чисто поверхность 3;
точить поверху поверхность 4;
протянуть шпоночный паз поверхности 2;
фрезеровать зубья (поверхность 4)
закалка в масле+отпуск
шлифовать зубья (поверхность 4)
шлифовать отверстие (3) и торец (1)
шлифовать другой торец 5
ПРОЕКТИРОВАНИЕ ТЕХНОЛОГИЧЕСКОЙ ОПЕРАЦИИ ЗУБОФРЕЗЕРОВАНИЯ
1.Расчет режимов резания
Расчет ведется одновременно с заполнением операционных карт технологического процесса: запись данных по оборудованию способу обработки характеристики обработки обрабатываемой детали 6.
Определяем расчетную величину подачи:
Выбираем значение подачи и значения коэффициентов входящих в формулу: SH=2.8; KM=0.8; Kb=0.9; KX=1; KНАПР=1.
Определим скорость резания:
Выбираем значение скорости резания и значения коэффициентов входящих в формулу: vH=29; KM=0.9; Kb=1.0; KX=1; KНАПР=1; КИ=1; КТ=105.
Определим частоту вращения шпинделя:
Станок может обеспечить n=100 обмин тогда V=314 ммин.
Вычислим величину силы резания:
где CP=682; S=2; t=3; m=5; v=31.4; K10=1.6; KM=0.95
Мощность резания определяется по формуле:
Мощность которую должен обеспечить станок:
где Nдв – мощность электродвигателя привода главного движения кВт; – механический КПД.
2.Технологическое нормирование операций
При обработке в условиях среднесерийного типа производства на станке с ЧПУ определяется штучно – калькуляционное время (tш-к) состоящее из штучного (tшт) и подготовительно – заключительного времени на партию деталей (tп-з) которое определяется по зависимости 4:
tш-к=tшт+tп-з nЗ(6.7)
где nЗ – размер партии деталей запускаемых в производство шт.
Норма штучного времени обработки детали:
tшт=to+tв+tобс+tп(6.8)
где tо= - основное время на операцию мин; tВ – вспомогательное время мин; tобс – время обслуживания рабочего места мин; tп – время на личные потребности мин.
Основное время на выполнение j – го перехода:
где b – длина обрабатываемой поверхности мм; z – число зубьев; n – частота вращения шпинделя обмин; S – подача ммоб; K- число заходов червячной фрезы.
Вспомогательное время определяем по справочнику 8:
Времена tобс и tп принимаются в процентном отношении от оперативного времени (tоп):
tоп=1692+125=1817 мин.
tобс = tп=004×1817=0725 мин.
tшт=16.92+1.25+0.725+0.725=19.62 мин.
Подготовительно – заключительное определяем по справочнику 10:
tш-к=19.62+29833=1962 мин.
3.Выбор технологических баз и расчет погрешности установки заготовки
Выбор технологических баз имеет первостепенное значение при проектировании технологических процессов. При выборе баз учитывается вид операции точность и производительность обработки и многие другие факторы.
Для выполнения зубофрезерной операции за технологические базы принимаем обработанные на предыдущих операциях цилиндрические поверхности и торец. Эти технологические базы являются оптимальными т.к. обеспечивают устойчивое положение заготовки относительно станка а также надежное ее закрепление с минимальными деформациями.
Суммарная погрешность установки:
При обработке партии заготовок в одноместном приспособлении на настроенном станке погрешность приспособления вызывает систематическую погрешность обработки и может быть скомпенсирована при наладке (подналадке) поэтому при расчете погрешности установки не учитывается. Тогда учитывая что погрешности Еб и Ез являются случайными величинами можно записать:
Погрешность базирования зависит от величины радиального зазора оправки но т.к. деталь садится на оправку с натягом то:
Погрешность закрепления для жёсткой оправки с креплением по торцу:
Общая погрешность установки:
Схема установки приведена на рис. 6.3.1:
Рис 6.3.1 Схема установки
4.Выбор средств технологического оснащения
Современное машиностроение на сей день имеет ярко выраженную тенденцию к повышению качества точности обрабатываемых изделий и невозможно будет реализовать спроектированный технологический процесс без соответствующего технологического оснащения. При выборе конкретных моделей станков необходимо учитывать:
-соответствие габаритных размеров заготовки размерам рабочей зоны оборудования;
-требования обеспечения точности и качества обрабатываемых поверхностей;
-технологические возможности станка.
Средствами технологического оснащения были выбраны:
-станок на котором производится обработка детали зубофрезерный 53А30П;
-зубофрезерование производится червячной фрезой материал рабочей части Р6М5 заданной геометрии.
Анализ служебного назначения изделия позволил максимально уточнить и сформулировать задачу для решения которой предназначено изделие.
Дальнейшим анализом была составлена размерная цепь решение которой было необходимо для разработки чертежей детали. В результате расчета размерной цепи были найдены соответствующие значения параметров всех составляющих звеньев являющиеся экономически достижимыми.
Составленная схема сборки изделия является оптимально технологичной в условиях среднесерийного производства что значительно сокращает затраты на его осуществление.
Составленный рабочий чертеж детали содержит основные данные для выбора заготовки проектирования маршрутного технологического процесса.
В соответствии с чертежом детали также был разработан технологический маршрут обработки поверхностей детали и сведен в таблицу 5.1.
Проведенные расчеты режимов резания позволяют точно определить уровень технологического оснащения так например мощность станка. Кроме того необходимо создать условия повышающие надежность технологической системы и стабильности процесса обработки.
Было произведено нормирование операции и выбраны базы.
СПИСОК ИСПОЛЬЗУЕМЫХ ИСТОЧНИКОВ
Сборочный чертеж редуктора.
Толмачевский Н.Н. Доможиров А.П. Методы достижения точности сборки: Учебное пособие. – Курган: КМИ 1992 г. – 62 с.
Мосталыгин Г.П. Толмачевский Н.Н. Технология машиностроения. – М: Машиностроение 1990 г. – 288 с.
Справочник технолога – машиностроителя: В 2-х т. Т1 Под ред. А.Г. Косиловой и Р.К. Мещерякова. – М.: Машиностроение 1985 г. – 656 с.
Марфицын В.В. Давыдова М.В. Минин И.А. Выбор способа изготовления заготовок. Методические указания. – Курган.: КГУ 1997 г. – 80 с.
Справочник технолога-машиностроителя В 2-х т. Т2 Под ред. А.Г. Косиловой и РК Мещерекова - М:Машиностроение 1986 г. - 496 с.
Мосталыгин Г.П. Орлов В. Н. Проектирование технологических процессов обработки заготовок. Учебное пособие. – Свердловск 1991 г. – 112 с.
Общемашиностроительные нормативы времени и режимов резания для многоцелевых станков фрезерно- сверлильно- расточной группы: - М.
ВНИИТЭМР 1986. – 159 с.
Инструментальная наладка.cdw

зубофрезерной операции
Курсовая работа по ОТ
Предельные отклонения измерительного
межосевого расстояния
Пояснительная.doc
Курганский государственный университет
Кафедра технологии машиностроения
«Основы технологии производства машин»
Анализ служебного назначения изделия и расчет размерной цепи4
Разработка схемы сборки7
Разработка рабочего чертежа детали9
Проектирование маршрутного технологического процесса изготовления зубчатого колеса 12
Проектирование технологической операции зубофрезерования 14
Библиографический список 20
В процессе выполнения данной курсовой работы анализируется предложенный сборочный чертеж задается тип производства. Производится размерный анализ с выявлением размерной цепи и ее решением. Опираясь на сборочный чертеж изделия составляется его схема сборки. Разрабатывается рабочий чертеж предложенной детали. Для данной детали разрабатывается эскиз заготовки из которой в последствии будет изготовлена деталь. Сюда не относится составление маршрутного технологического процесса.
Для обработки конкретных поверхностей для одной операции проектируется операционный технологический процесс. Выполняется операционный эскиз обработки заготовки дается обоснование выбора технологических баз выбора станочного оборудования.
Для обработки и изготовления детали рекомендуется применять современный режущий инструмент станочный парк позволяющий в наибольшей степени оптимизировать технологический процесс обработки а также контроля готового изделия.
АНАЛИЗ СЛУЖЕБНОГО НАЗНАЧЕНИЯ ИЗДЕЛИЯ И РАСЧЕТ РАЗМЕРНОЙ ЦЕПИ
1.Анализ служебного назначения
Цилиндр тормоза используется в качестве силового привода тормозных устройств. Цилиндр состоит из корпуса в котором перемещается плунжер. Рабочий ход плунжера происходит при подаче тормозной жидкости через имеющийся в цилиндре штуцер. Обратный ход осуществляется усилием пружины.
В курсовой работе рассматривается изготовление зубчатого колеса.
Для изготовления колеса необходимо выбрать материал обладающий повышенной износостойкостью и высокой твердостью. Для этих целей выбираем легированную конструкционную сталь марки 45Х с последующим упрочнением поверхностного слоя применив закалку. Сердцевина детали изготовленной из хромистой стали имеет изначально высокий предел текучести а закаленный поверхностный слой – высокую твердость.
2.Расчет размерной цепи
Рассчитаем размерную цепь состоящую из трех увеличивающих и шести уменьшающих звеньев по методике изложенной в 2.
Схема размерной цепи
Номинальный размер замыкающего звена АΔ=128мм. Допуск замыкающего звена ТАΔ=04 мм.
Размерную цепь будем решать методом полной взаимозаменяемости который является простым и обеспечивает 100%-ную взаимозаменяемость.
В данном случае необходимо решить прямую задачу; для ее решения применим способ одного квалитета который используется когда размеры входящие в размерную цепь по своей величине значительно отличаются друг от друга.
Номинальные размеры звеньев: А1= 6 мм; А2=40 мм; А3=А4 =4 мм;
А5=10 мм; А6=18 мм; А7= А8=5 мм;
где ам – среднее число единиц допуска в размерах цепи;
- сумма единиц допусков составляющих звеньев в цепи;
m – общее количество звеньев в цепи.
Для А1=6– А2=40– А3=4– А4=4– A5=10– i=090
А6=18 – А7=5 – А8=5– A9=200– i=290.
Найденное число единиц допуска близко к 9 квалитету.
Устанавливаем допуски и назначаем отклонения для звеньев цепи:
А1=6-003 мм; А2=40-0062 мм; А3=А4=4-003 мм; А5=10-0036 мм;
А6=18-0043 мм; А7=A8=5+003 мм; А9=200+0115 мм;
Проверка ТАΔ= 04=0346 т.е. необходимо скоректировать одно из звеньев цепи (А9).
Рассчитаем величину допуска для 9-го звена:
РАЗРАБОТКА СХЕМЫ СБОРКИ
Схема сборки определяет взаимную связь элементов изделия и позволяет установить их последовательность комплектования. Последовательность сборки в основном определяется конструкцией изделия и его отдельных элементов а также методами достижения требуемой точности.
Схема сборки позволяет наглядно представить весь технологический процесс проверить правильность выполнения намеченной последовательности операций.
По заданному сборочному чертежу изделия составим его схему сборки используя методику изложенную в 23.
РАЗРАБОТКА РАБОЧЕГО ЧЕРТЕЖА ДЕТАЛИ
Разработка рабочего чертежа детали производится в соответствии с действующими стандартами ЕСКД.
Подготовительный этап: ознакомление с конструкцией детали указываем на чертеже выбранный ранее материал детали сталь 45Х. Исходя из габаритов и формы детали (зубчатое колесо) располагаем ее на чертеже горизонтально.
Основной этап: выбираем масштаб построения 1:1 для более точного вычерчивания элементов детали. Указание на чертеже отклонений и определение шероховатости производим в экономически и технологически достижимых пределах а также из функционального назначения поверхностей конструктивных особенностей детали условий работы 4.
Строим необходимые виды и разрезы для полного представления о форме детали.
Указываем на чертеже технические требования необходимые для изготовления детали с нужными свойствами.
Составленный рабочий чертеж детали содержит основные данные для выбора формы и размеров заготовки проектирование маршрутного технологического процесса и операционного технологического процесса.
1 Разработка эскиза заготовки
В данном разделе использована методика изложенная в 5.
В нашем случае как и во многих других требуется высокая прочность и плотность заготовки поэтому заготовку выбираем для среднесерийного типа производства при массе детали 33 кг изготавливаемую способом штамповки на КГШП.
Степень сложности – С2
Конфигурация поверхности разъема штампа – П (плоская)
Исходный индекс – 13
Основные припуски на размеры:
толщина 40 мм и Ra=32 мкм – 17 мм
толщина 78 мм и Ra=32 мкм – 18 мм
диаметр 78 мм и Ra=25 мкм – 18 мм
диаметр 354 мм и Ra=25 мкм – 25 мм
Дополнительные припуски учитывающие: смещение по поверхности разъема штампа – 08 мм; отклонение от плоскостности и прямолинейности – 08 мм.
толщина 40+(17+08)*2=45 мм; принимаем 45 мм
толщина 78+(18+08)*2=832 мм; принимаем 83 мм
диаметр 7776-(18+08)*2=7256 мм; принимаем 73 мм
диаметр 354+(25+08)*2=3606 мм; принимаем 360 мм
Радиус закругления углов – 40 мм;
Штамповочный уклон поверхностей : наружных – 4º.
Допускаемые отклонения размеров:
Допускаемая величина смещения по поверхности разъема штампа – 12 мм.
2 Расчет себестоимости изготовления заготовки
Себестоимость заготовки определяется по формуле:
Значения коэффициентов берутся из справочника 7: C KT=1; KM=0.87; KC=1.13; KB=0.73; KП=1; SОТХ=28.
ПРОЕКТИРОВАНИЕ МАРШРУТНОГО ТЕХНОЛОГИЧЕСКОГО ПРОЦЕССА ИЗГОТОВЛЕНИЯ ВАЛА-ШЕСТЕРНИ
В данном разделе использована методика описанная в 34.
В результате разработки технологического процесса определяем необходимое оборудование технологическую оснастку и др.
Технологический процесс представляет собой совокупность различных операций в результате выполнения которых изменяется форма размеры осуществляется контроль требований чертежа и технических условий.
Маршрутное описание технологического процесса заключается в сокращенном описании всех технологических операций в последовательности их выполнения без указания переходов и технологических режимов.
В соответствии с чертежом детали разработаем технологический маршрут и оформим его в виде таблицы.
Рис. 5.1. Обрабатываемые поверхности
Технологический маршрут
Наименование и краткое содержание операций
Технологические базы приспособления
Заготовительная- КГШП
Расточить на черно и на чисто отверстие 1; подрезать торцы 3456; снять фаски 78
Наружная цилиндрическая поверхность 9 .
патрон трехкулачковый самоцентрирующийся
точить поверху поверхность 9; снять фаски 1011
Цилиндрическая поверхность 1 и торец 3.
Приспособление: патрон трехкулачковый самоцентрирующийся
протянуть шпоночный паз поверхности 2;
Торец 3 и цилиндрическая поверхность 1.
Приспособление: адаптер
Приспособление контрольное с установкой детали на оправку
фрезеровать зубья (поверхность 9)
Цилиндрическая поверхность 1 и торец 4.
Приспособление зубофрезерное
закалка в масле + отпуск
шлифовать зубья (поверхность 9)
Приспособление: оправка
ПРОЕКТИРОВАНИЕ ТЕХНОЛОГИЧЕСКОЙ ОПЕРАЦИИ ЗУБОФРЕЗЕРОВАНИЯ
1.Расчет режимов резания
Расчет ведется одновременно с заполнением операционных карт технологического процесса: запись данных по оборудованию способу обработки характеристики обработки обрабатываемой детали 6.
Определяем расчетную величину подачи:
Выбираем значение подачи и значения коэффициентов входящих в формулу: SH=2.0; KM=1; Kb=1; KX=1; KНАПР=1.
Определим скорость резания:
Выбираем значение скорости резания и значения коэффициентов входящих в формулу: vH=305; KM=1; Kb=1; KX=1; KНАПР=1; КИ=1; КТ=1.
Определим частоту вращения шпинделя:
Станок может обеспечить n=100 обмин тогда V=282 ммин.
Вычислим величину силы резания:
где CP=47; y=072; u=1; q=086; w=0;
Мощность резания определяется по формуле:
Мощность которую должен обеспечить станок:
где Nдв – мощность электродвигателя привода главного движения кВт; – механический КПД.
2.Технологическое нормирование операций
При обработке в условиях среднесерийного типа производства на зубофрезерном станке определяется штучно – калькуляционное время (tш-к) состоящее из штучного (tшт) и подготовительно – заключительного времени на партию деталей (tп-з) которое определяется по зависимости 4:
tш-к=tшт+tп-з nЗ(6.7)
где nЗ – размер партии деталей запускаемых в производство шт.
Норма штучного времени обработки детали:
tшт=to+tв+tобс+tлп(6.8)
где tо= - основное время на операцию мин; tв – вспомогательное время мин; tобс – время обслуживания рабочего места мин; tлп – время на личные потребности мин.
Основное время на выполнение j – го перехода:
где z – число зубьев; n – частота вращения шпинделя обмин; S – подача ммоб; K- число заходов червячной фрезы.
Вспомогательное время определяем по справочнику 8:
tв=tуст+tпер+tизм (6.10)
где tуст – вспомогательное время на установку и снятие детали мин; tпер – вспомогательное время связанное с переходом мин; tизм – вспомогательное время на контрольное измерение мин.
tв=1+02+055=175 мин.
Времена tобс и tлп принимаются в процентном отношении ( 4..8% ) от оперативного времени (tоп) :
tоп=1462+175=1637 мин.
tобс = tлп= 4% tоп (6.12)
tобс = tп=004×1637=066 мин.
tшт=14.62+1.75+0.66+0.66=17.69 мин.
Подготовительно – заключительное определяем по справочнику 10:
tш-к=17.69+325500=1776 мин.
3.Выбор технологических баз и расчет погрешности установки заготовки
Выбор технологических баз имеет первостепенное значение при проектировании технологических процессов. При выборе баз учитывается вид операции точность и производительность обработки и многие другие факторы.
Для выполнения зубофрезерной операции за технологические базы принимаем обработанные на предыдущих операциях цилиндрические поверхности и торец. Эти технологические базы являются оптимальными т.к. обеспечивают устойчивое положение заготовки относительно станка а также надежное ее закрепление с минимальными деформациями.
Определим величину радиального биения зубчатого колеса при установке на специальное зубофрезерное приспособление. Суммарная величина биения складывается из погрешности обработки торца зубчатого колеса а также погрешности обработки внутреннего отверстия:
В соответствии с рабочим чертежом детали определим допускаемые (максимальные) значения составляющих и :
– принимаем значение равным допускаемому биению торца относительно внутреннего отверстия колеса: = 01 мм;
– значение принимаем равным допуску отверстия по соответствующему квалитету: = 0046 мм.
Находим величину радиального биения:
= 01 + 0046 = 0146 мм.
Схема установки приведена на рис. 6.3.1:
Рис 6.3.1 Схема установки
4.Выбор средств технологического оснащения
Современное машиностроение на сей день имеет ярко выраженную тенденцию к повышению качества точности обрабатываемых изделий и невозможно будет реализовать спроектированный технологический процесс без соответствующего технологического оснащения. При выборе конкретных моделей станков необходимо учитывать:
-соответствие габаритных размеров заготовки размерам рабочей зоны оборудования;
-требования обеспечения точности и качества обрабатываемых поверхностей;
-технологические возможности станка.
Средствами технологического оснащения были выбраны:
-станок на котором производится обработка детали зубофрезерный 53А50;
-зубофрезерование производится червячной фрезой материал рабочей части Р6М5 заданной геометрии.
Анализ служебного назначения изделия позволил максимально уточнить и сформулировать задачу для решения которой предназначено изделие.
Дальнейшим анализом была составлена размерная цепь решение которой было необходимо для разработки чертежей детали. В результате расчета размерной цепи были найдены соответствующие значения параметров всех составляющих звеньев являющиеся экономически достижимыми.
Составленная схема сборки изделия является оптимально технологичной в условиях среднесерийного производства что значительно сокращает затраты на его осуществление.
Составленный рабочий чертеж детали содержит основные данные для выбора заготовки проектирования маршрутного технологического процесса.
В соответствии с чертежом детали также был разработан технологический маршрут обработки поверхностей детали и сведен в таблицу 5.1.
Проведенные расчеты режимов резания позволяют точно определить уровень технологического оснащения так например мощность станка. Кроме того необходимо создать условия повышающие надежность технологической системы и стабильности процесса обработки.
Было произведено нормирование операции и выбраны базы.
БИБЛИОГРАФИЧЕСКИЙ СПИСОК
Сборочный чертеж цилиндра тормоза.
Толмачевский Н.Н. Доможиров А.П. Методы достижения точности сборки: Учебное пособие. – Курган: КМИ 1992 г. – 62 с.
Мосталыгин Г.П. Толмачевский Н.Н. Технология машиностроения. – М: Машиностроение 1990 г. – 288 с.
Справочник технолога – машиностроителя: В 2-х т. Т1 Под ред. А.Г. Косиловой и Р.К. Мещерякова. – М.: Машиностроение 1985 г. – 656 с.
Марфицын В.В. Давыдова М.В. Минин И.А. Выбор способа изготовления заготовок. Методические указания. – Курган.: КГУ 1997 г. – 80 с.
Справочник технолога-машиностроителя В 2-х т. Т2 Под ред. А.Г. Косиловой и РК Мещерекова - М:Машиностроение 1986 г. - 496 с.
Мосталыгин Г.П. Орлов В. Н. Проектирование технологических процессов обработки заготовок. Учебное пособие. – Свердловск 1991 г. – 112 с.
Общемашиностроительные нормативы времени и режимов резания для многоцелевых станков фрезерно- сверлильно- расточной группы: - М.
ВНИИТЭМР 1986. – 159 с.
Общемашиностроительные нормативы времени вспомогательного на обслуживание рабочего места и подготовительно-заключительного на работы выполняемые на металлорежущих станках. Среднесерийное и крупносерийное производство: -М: НИИ труда 1984 г. – 476 с.
Общемашиностроительные нормативы режимов резания для технического нормирования работ на металлорежущих станках. В 2-х ч. – М:Машиностроение 1974 г.
Маршрут2.cdw

наименование оборудования
сб.единицы или материала
Обозначение документа
без КЭ; без ОК; ИОТ N 84
без КЭ; без ОК; ИОТ N 91
141.00001; 60141.00001; ИОТ N 73
без КЭ; без ОК; ИОТ N 87
Пояснительная1.doc
Курганский государственный университет
Кафедра технологии машиностроения
«Основы технологии производства машин»
Студент: гр. Т-4110 Штундер В.А.
Преподаватель: Михалев А.М.
Анализ служебного назначения изделия и расчет размерной цепи4
Разработка схемы сборки7
Разработка рабочего чертежа детали9
Проектирование маршрутного технологического процесса изготовления зубчатого колеса 12
Проектирование технологической операции зубофрезерования 14
Библиографический список 20
В процессе выполнения данной курсовой работы анализируется предложенный сборочный чертеж задается тип производства. Производится размерный анализ с выявлением размерной цепи и ее решением. Опираясь на сборочный чертеж изделия составляется его схема сборки. Разрабатывается рабочий чертеж предложенной детали. Для данной детали разрабатывается эскиз заготовки из которой в последствии будет изготовлена деталь. Сюда не относится составление маршрутного технологического процесса.
Для обработки конкретных поверхностей для одной операции проектируется операционный технологический процесс. Выполняется операционный эскиз обработки заготовки дается обоснование выбора технологических баз выбора станочного оборудования.
Для обработки и изготовления детали рекомендуется применять современный режущий инструмент станочный парк позволяющий в наибольшей степени оптимизировать технологический процесс обработки а также контроля готового изделия.
АНАЛИЗ СЛУЖЕБНОГО НАЗНАЧЕНИЯ ИЗДЕЛИЯ И РАСЧЕТ РАЗМЕРНОЙ ЦЕПИ
1.Анализ служебного назначения
Цилиндр тормоза используется в качестве силового привода тормозных устройств. Цилиндр состоит из корпуса в котором перемещается плунжер. Рабочий ход плунжера происходит при подаче тормозной жидкости через имеющийся в цилиндре штуцер. Обратный ход осуществляется усилием пружины.
В курсовой работе рассматривается изготовление зубчатого колеса.
Для изготовления колеса необходимо выбрать материал обладающий повышенной износостойкостью и высокой твердостью. Для этих целей выбираем легированную конструкционную сталь марки 45Х с последующим упрочнением поверхностного слоя применив закалку. Сердцевина детали изготовленной из хромистой стали имеет изначально высокий предел текучести а закаленный поверхностный слой – высокую твердость.
2.Расчет размерной цепи
Рассчитаем размерную цепь состоящую из трех увеличивающих и шести уменьшающих звеньев по методике изложенной в 2.
Схема размерной цепи
Номинальный размер замыкающего звена АΔ=128мм. Допуск замыкающего звена ТАΔ=04 мм.
Размерную цепь будем решать методом полной взаимозаменяемости который является простым и обеспечивает 100%-ную взаимозаменяемость.
В данном случае необходимо решить прямую задачу; для ее решения применим способ одного квалитета который используется когда размеры входящие в размерную цепь по своей величине значительно отличаются друг от друга.
Номинальные размеры звеньев: А1= 6 мм; А2=40 мм; А3=А4 =4 мм;
А5=10 мм; А6=18 мм; А7= А8=5 мм;
где ам – среднее число единиц допуска в размерах цепи;
- сумма единиц допусков составляющих звеньев в цепи;
m – общее количество звеньев в цепи.
Для А1=6– А2=40– А3=4– А4=4– A5=10– i=090
А6=18 – А7=5 – А8=5– A9=200– i=290.
Найденное число единиц допуска близко к 9 квалитету.
Устанавливаем допуски и назначаем отклонения для звеньев цепи:
А1=6-003 мм; А2=40-0062 мм; А3=А4=4-003 мм; А5=10-0036 мм;
А6=18-0043 мм; А7=A8=5+003 мм; А9=200+0115 мм;
Проверка ТАΔ= 04=0346 т.е. необходимо скоректировать одно из звеньев цепи (А9).
Рассчитаем величину допуска для 9-го звена:
РАЗРАБОТКА СХЕМЫ СБОРКИ
Схема сборки определяет взаимную связь элементов изделия и позволяет установить их последовательность комплектования. Последовательность сборки в основном определяется конструкцией изделия и его отдельных элементов а также методами достижения требуемой точности.
Схема сборки позволяет наглядно представить весь технологический процесс проверить правильность выполнения намеченной последовательности операций.
По заданному сборочному чертежу изделия составим его схему сборки используя методику изложенную в 23.
РАЗРАБОТКА РАБОЧЕГО ЧЕРТЕЖА ДЕТАЛИ
Разработка рабочего чертежа детали производится в соответствии с действующими стандартами ЕСКД.
Подготовительный этап: ознакомление с конструкцией детали указываем на чертеже выбранный ранее материал детали сталь 45Х. Исходя из габаритов и формы детали (зубчатое колесо) располагаем ее на чертеже горизонтально.
Основной этап: выбираем масштаб построения 1:1 для более точного вычерчивания элементов детали. Указание на чертеже отклонений и определение шероховатости производим в экономически и технологически достижимых пределах а также из функционального назначения поверхностей конструктивных особенностей детали условий работы 4.
Строим необходимые виды и разрезы для полного представления о форме детали.
Указываем на чертеже технические требования необходимые для изготовления детали с нужными свойствами.
Составленный рабочий чертеж детали содержит основные данные для выбора формы и размеров заготовки проектирование маршрутного технологического процесса и операционного технологического процесса.
1 Разработка эскиза заготовки
В данном разделе использована методика изложенная в 5.
В нашем случае как и во многих других требуется высокая прочность и плотность заготовки поэтому заготовку выбираем для среднесерийного типа производства при массе детали 33 кг изготавливаемую способом штамповки на КГШП.
Степень сложности – С2
Конфигурация поверхности разъема штампа – П (плоская)
Исходный индекс – 13
Основные припуски на размеры:
толщина 40 мм и Ra=32 мкм – 17 мм
толщина 78 мм и Ra=32 мкм – 18 мм
диаметр 78 мм и Ra=25 мкм – 18 мм
диаметр 354 мм и Ra=25 мкм – 25 мм
Дополнительные припуски учитывающие: смещение по поверхности разъема штампа – 08 мм; отклонение от плоскостности и прямолинейности – 08 мм.
толщина 40+(17+08)*2=45 мм; принимаем 45 мм
толщина 78+(18+08)*2=832 мм; принимаем 83 мм
диаметр 7776-(18+08)*2=7256 мм; принимаем 73 мм
диаметр 354+(25+08)*2=3606 мм; принимаем 360 мм
Радиус закругления углов – 40 мм;
Штамповочный уклон поверхностей : наружных – 4º.
Допускаемые отклонения размеров:
Допускаемая величина смещения по поверхности разъема штампа – 12 мм.
2 Расчет себестоимости изготовления заготовки
Себестоимость заготовки определяется по формуле:
Значения коэффициентов берутся из справочника 7: C KT=1; KM=0.87; KC=1.13; KB=0.73; KП=1; SОТХ=28.
ПРОЕКТИРОВАНИЕ МАРШРУТНОГО ТЕХНОЛОГИЧЕСКОГО ПРОЦЕССА ИЗГОТОВЛЕНИЯ ВАЛА-ШЕСТЕРНИ
В данном разделе использована методика описанная в 34.
В результате разработки технологического процесса определяем необходимое оборудование технологическую оснастку и др.
Технологический процесс представляет собой совокупность различных операций в результате выполнения которых изменяется форма размеры осуществляется контроль требований чертежа и технических условий.
Маршрутное описание технологического процесса заключается в сокращенном описании всех технологических операций в последовательности их выполнения без указания переходов и технологических режимов.
В соответствии с чертежом детали разработаем технологический маршрут и оформим его в виде таблицы.
Рис. 5.1. Обрабатываемые поверхности
Технологический маршрут
Наименование и краткое содержание операций
Технологические базы приспособления
Заготовительная- КГШП
Расточить на черно и на чисто отверстие 1; подрезать торцы 3456; снять фаски 78
Наружная цилиндрическая поверхность 9 .
патрон трехкулачковый самоцентрирующийся
точить поверху поверхность 9; снять фаски 1011
Цилиндрическая поверхность 1 и торец 3.
Приспособление: патрон трехкулачковый самоцентрирующийся
протянуть шпоночный паз поверхности 2;
Торец 3 и цилиндрическая поверхность 1.
Приспособление: адаптер
Приспособление контрольное с установкой детали на оправку
фрезеровать зубья (поверхность 9)
Цилиндрическая поверхность 1 и торец 4.
Приспособление зубофрезерное
закалка в масле + отпуск
шлифовать зубья (поверхность 9)
Приспособление: оправка
ПРОЕКТИРОВАНИЕ ТЕХНОЛОГИЧЕСКОЙ ОПЕРАЦИИ ЗУБОФРЕЗЕРОВАНИЯ
1.Расчет режимов резания
Расчет ведется одновременно с заполнением операционных карт технологического процесса: запись данных по оборудованию способу обработки характеристики обработки обрабатываемой детали 6.
Определяем расчетную величину подачи:
Выбираем значение подачи и значения коэффициентов входящих в формулу: SH=2.0; KM=1; Kb=1; KX=1; KНАПР=1.
Определим скорость резания:
Выбираем значение скорости резания и значения коэффициентов входящих в формулу: vH=305; KM=1; Kb=1; KX=1; KНАПР=1; КИ=1; КТ=1.
Определим частоту вращения шпинделя:
Станок может обеспечить n=100 обмин тогда V=282 ммин.
Вычислим величину силы резания:
где CP=47; y=072; u=1; q=086; w=0;
Мощность резания определяется по формуле:
Мощность которую должен обеспечить станок:
где Nдв – мощность электродвигателя привода главного движения кВт; – механический КПД.
2.Технологическое нормирование операций
При обработке в условиях среднесерийного типа производства на зубофрезерном станке определяется штучно – калькуляционное время (tш-к) состоящее из штучного (tшт) и подготовительно – заключительного времени на партию деталей (tп-з) которое определяется по зависимости 4:
tш-к=tшт+tп-з nЗ(6.7)
где nЗ – размер партии деталей запускаемых в производство шт.
Норма штучного времени обработки детали:
tшт=to+tв+tобс+tлп(6.8)
где tо= - основное время на операцию мин; tв – вспомогательное время мин; tобс – время обслуживания рабочего места мин; tлп – время на личные потребности мин.
Основное время на выполнение j – го перехода:
где z – число зубьев; n – частота вращения шпинделя обмин; S – подача ммоб; K- число заходов червячной фрезы.
Вспомогательное время определяем по справочнику 8:
tв=tуст+tпер+tизм (6.10)
где tуст – вспомогательное время на установку и снятие детали мин; tпер – вспомогательное время связанное с переходом мин; tизм – вспомогательное время на контрольное измерение мин.
tв=1+02+055=175 мин.
Времена tобс и tлп принимаются в процентном отношении ( 4..8% ) от оперативного времени (tоп) :
tоп=1462+175=1637 мин.
tобс = tлп= 4% tоп (6.12)
tобс = tп=004×1637=066 мин.
tшт=14.62+1.75+0.66+0.66=17.69 мин.
Подготовительно – заключительное определяем по справочнику 10:
tш-к=17.69+325500=1776 мин.
3.Выбор технологических баз и расчет погрешности установки заготовки
Выбор технологических баз имеет первостепенное значение при проектировании технологических процессов. При выборе баз учитывается вид операции точность и производительность обработки и многие другие факторы.
Для выполнения зубофрезерной операции за технологические базы принимаем обработанные на предыдущих операциях цилиндрические поверхности и торец. Эти технологические базы являются оптимальными т.к. обеспечивают устойчивое положение заготовки относительно станка а также надежное ее закрепление с минимальными деформациями.
Определим величину радиального биения зубчатого колеса при установке на специальное зубофрезерное приспособление. Суммарная величина биения складывается из погрешности обработки торца зубчатого колеса а также погрешности обработки внутреннего отверстия:
В соответствии с рабочим чертежом детали определим допускаемые (максимальные) значения составляющих и :
– принимаем значение равным допускаемому биению торца относительно внутреннего отверстия колеса: = 001 мм;
– значение принимаем равным допуску отверстия по соответствующему квалитету: = 0046 мм.
Находим величину радиального биения:
= 001 + 0046 = 056 мм.
Схема установки приведена на рис. 6.3.1:
Рис 6.3.1 Схема установки
4.Выбор средств технологического оснащения
Современное машиностроение на сей день имеет ярко выраженную тенденцию к повышению качества точности обрабатываемых изделий и невозможно будет реализовать спроектированный технологический процесс без соответствующего технологического оснащения. При выборе конкретных моделей станков необходимо учитывать:
-соответствие габаритных размеров заготовки размерам рабочей зоны оборудования;
-требования обеспечения точности и качества обрабатываемых поверхностей;
-технологические возможности станка.
Средствами технологического оснащения были выбраны:
-станок на котором производится обработка детали зубофрезерный 53А50;
-зубофрезерование производится червячной фрезой материал рабочей части Р6М5 заданной геометрии.
Анализ служебного назначения изделия позволил максимально уточнить и сформулировать задачу для решения которой предназначено изделие.
Дальнейшим анализом была составлена размерная цепь решение которой было необходимо для разработки чертежей детали. В результате расчета размерной цепи были найдены соответствующие значения параметров всех составляющих звеньев являющиеся экономически достижимыми.
Составленная схема сборки изделия является оптимально технологичной в условиях среднесерийного производства что значительно сокращает затраты на его осуществление.
Составленный рабочий чертеж детали содержит основные данные для выбора заготовки проектирования маршрутного технологического процесса.
В соответствии с чертежом детали также был разработан технологический маршрут обработки поверхностей детали и сведен в таблицу 5.1.
Проведенные расчеты режимов резания позволяют точно определить уровень технологического оснащения так например мощность станка. Кроме того необходимо создать условия повышающие надежность технологической системы и стабильности процесса обработки.
Было произведено нормирование операции и выбраны базы.
БИБЛИОГРАФИЧЕСКИЙ СПИСОК
Сборочный чертеж цилиндра тормоза.
Толмачевский Н.Н. Доможиров А.П. Методы достижения точности сборки: Учебное пособие. – Курган: КМИ 1992 г. – 62 с.
Мосталыгин Г.П. Толмачевский Н.Н. Технология машиностроения. – М: Машиностроение 1990 г. – 288 с.
Справочник технолога – машиностроителя: В 2-х т. Т1 Под ред. А.Г. Косиловой и Р.К. Мещерякова. – М.: Машиностроение 1985 г. – 656 с.
Марфицын В.В. Давыдова М.В. Минин И.А. Выбор способа изготовления заготовок. Методические указания. – Курган.: КГУ 1997 г. – 80 с.
Справочник технолога-машиностроителя В 2-х т. Т2 Под ред. А.Г. Косиловой и РК Мещерекова - М:Машиностроение 1986 г. - 496 с.
Мосталыгин Г.П. Орлов В. Н. Проектирование технологических процессов обработки заготовок. Учебное пособие. – Свердловск 1991 г. – 112 с.
Общемашиностроительные нормативы времени и режимов резания для многоцелевых станков фрезерно- сверлильно- расточной группы: - М.
ВНИИТЭМР 1986. – 159 с.
Общемашиностроительные нормативы времени вспомогательного на обслуживание рабочего места и подготовительно-заключительного на работы выполняемые на металлорежущих станках. Среднесерийное и крупносерийное производство: -М: НИИ труда 1984 г. – 476 с.
Общемашиностроительные нормативы режимов резания для технического нормирования работ на металлорежущих станках. В 2-х ч. – М:Машиностроение 1974 г.
Рекомендуемые чертежи
- 08.06.2016