Модернизация асфальтосмесительной установки ДС-158



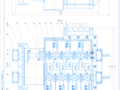
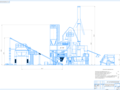
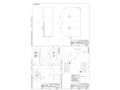
- Добавлен: 24.01.2023
- Размер: 1 MB
- Закачек: 0
Описание
Состав проекта
![]() |
![]() |
![]() ![]() ![]() ![]() |
![]() ![]() ![]() |
![]() ![]() ![]() ![]() |
![]() ![]() ![]() ![]() |
![]() ![]() ![]() |
Дополнительная информация
смеситель сборочный.cdw

Технические требования
Плоскость разъема корпуса смесителя при сборке покрыть слоем
Поверхность крепления герметизирующего рукава к подвижной
емкости и упору при сборке покрыть слоем клея-герметика.
Техническая характеристика
Частота вращения валов смесителя
Наружный диаметр лопастей
Зазор между лопастями и внутренней
частью корпуса смесителя
титульники.docx
УЧРЕЖДЕНИЕ ОБРАЗОВАНИЯ
БЕЛОРУССКИЙ ГОСУДАРСТВЕННЫЙ УНИВЕРСИТЕТ ТРАНСПОРТА
Кафедра «Детали машин путевые и строительные машины»
«Строительные машины и монтажное оборудование»
ассистентстудент группы МС-41
Шебзухов Ю.А.Грабок К.А.
МИНИСТЕРСТВО ОБРАЗОВАНИЯ РЕСПУБЛИКИ БЕЛАРУСЬ
ПОЯСНИТЕЛЬНАЯ ЗАПИСКА
к курсовому проекту по дисциплине:
«Проект модернизации асфальтосмесительной установки ДС-158»
студент группы МС-41
Асфальтосмесительная установка ДС-158 _ КП-12.СМиМО.00.00.00.ВО.cdw

КП-12.СМиМО.00.00.00.
Техническая характеристика
Номинальная производительность
Количество бункеров агрегата питания
Вместимость бункера готовой смеси
Максимальная масса замеса
Тип системы пылегазоочистки - циклоны+скруббер Вентури
Мощность установленного электрооборудования
Масса конструктивная
деталировка.dwg

пояснительная записка.docx
Анализ уровня техники в области асфальтосмесительных установок. Патентная обработка. Выбор прототипа8
Описание конструкции и кинематической схемы привода смесительной установки асфальтосмесителя ДС-1589
Определение основных параметров машины и рабочего оборудования10
1 Расчет длительности смешивания и размеров смесителя10
2 Расчет привода смесительной установки12
2.1 Расчет открытой зубчатой передачи12
2.2 Выбор двигателя и редуктора13
3 Определение параметров лопастей14
5 Расчет валов смесителя20
5.1 Определение нагрузки на валы от подвижной части корпуса20
6 Выбор подшипников25
Эскизное конструирование машины. Обоснование компоновочных решений27
Разработка мероприятий по технике безопасности охране окружающей среды энергоресурсосбережению при работе машины28
1Техника безопасности при эксплуатации асфальтосмесительных установок29
2 Мероприятия по охране окружающей природной среды31
В современных автомобильных дорогах необходимо применение высококачественных дорожно-строительных материалов одним из которых является асфальтобетонная смесь. Производство качественных асфальтобетонных смесей невозможно без применения современных эффективных машин и оборудования реализующих прогрессивные технологии и достижения научно-технического прогресса.
Для получения асфальтобетонных смесей применяют асфальтосмесительные установки. Целью данного курсового проекта является модернизация смесительного агрегата асфальтосмесительной установки с целью повышения производительности установки в целом.
Назначение и краткое описание асфальтосмесительной установки ДС-158
Асфальтосмесительные установки являются полным комплексом технологического оборудования для приготовления асфальтной смеси используемой в строительстве и дорожном хозяйстве. Своевременность технического обслуживания слаженность эксплуатации и возможность ремонта и модернизации делают асфальтосмесительные установки надежным оборудованием способным прослужить долгое время для удовлетворения потребностей дорожно-строительных и подрядных организаций.
Асфальтосмесительная установка состоит из следующего технологического оборудования:
агрегат минерального порошка;
бак топливный объемом 5000 л;
установка кабины оператора;
агрегат смесительный;
бункер готовой смеси вместимостью 32 тонны;
электрооборудование.
Также в состав установки входят следующие элементы:
система опрыскивания;
разводка теплоносителя.
Асфальтосмесительная установка ДС-158 начала выпускаться в середине 60-х годов прошлого столетия и за это время зарекомендовала себя как надежная и качественная модель. В сереине 90-х годов ее выпуск был прекращен в связи с выходом в свет более новой и более современной на то время асфальтосмесительной установки следующего поколения.
Конструкция асфальтосмесительной установки позволяет выполнять следующие операции технологического процесса:
предварительное дозирование влажных каменных материалов в агрегате питания;
просушивание и нагрев каменных материалов до рабочей температуры в сушильном барабане и подачу их к грохоту смесительного агрегата;
сортировку нагретых каменных материалов на четыре фракции (0-5; 5-10; 10-20; 20-40 мм) временное хранение их в "горячем" бункере дозирование и выдачу их в смеситель;
очистку выходящих из сушильного барабана дымовых газов от пыли в предварительной системе очистки циклонах сухой пылеочистки и в мокром пылеуловителе;
использование уловленной пыли путём подачи её элеватором в "горячий" бункер;
приём минерального порошка из автоцементовозов дозирование и выдачу в смеситель; приём битума из битумовозов (или склада битума) временное хранение и нагрев его в битумной цистерне до рабочей температуры дозирование и подачу его в смеситель;
выдачу смеси в автосамосвал или подачу её скиповым подъёмником в бункер готовой смеси;
обогрев битумных коммуникаций и насосов горячим маслом нагретым в змеевике нагревателя битума.
Управление всей установкой централизовано и осуществляется с пульта управления размещённого в кабине оператора.
Анализ уровня техники в области асфальтосмесительных установок. Патентная обработка
За рубежом установки выпускают фирмы «Паркер» (Великобритания) «Амман» (Швейцария) «Марини» (Италия) «Барбер-Грин» (США) «Миларс» (Великобритания) их производительность до 15 тч. Фирма «Вибау» (Германия) производит специализированные передвижные асфальтосмесительные установки периодического действия четырех видов для литого асфальта с партерной и башенной компоновкой узлов смесительного агрегата. Производительность установок фирмы «Эрмон» (Франция) работающих по турбулентному способу составляет 150-350 и 7-160 тч. Фирма «Цедера-пидс» (США) имеет установки производительностью до 545 тч.
Из отечественных фирм можно выделить фирму «Кредмаш» которая выпускает такие установки как ДС-158 ДС-168 (160 тч) ДС-185 (56 тч) ДС-1857У (64 тч) ДС-185М (56 тч) КДМ 201 (110 тч) КДМ-201М (110 тч).
В приложении А представлены патенты на различные конструкции смесителей.
Известен патент № 1274934 «Лотковый двухвальный смеситель». Достоинством данного смесителя является надежность работы удобство обслуживания а также снижение потерь компонентов смеси. Данный патент невозможно применить в данном курсовом проекте так как лотковые смесители невозможно применять на больших мощностях и объемах смесей.
Известен патент № 778762 «Лопастной смеситель». Достоинством данного смесителя является более интенсивный процесс перемешивания а также уравновешенность перемещаемых потоков смеси что позволяет повысить долговечность смесителя. Данный патент невозможно применить в данном курсовом проекте так как он не соответствует целям данного проекта а также невозможность применения данного смесителя при больших мощностях.
Известен патент № 2077634 «Смеситель». Достоинство данного смесителя в том что он позволяет повысить качество смеси. Недостаток в том что этот смеситель является одновальным. Применим этот патент в данном курсовом проекте но как двухвальный лопастной смеситель. Использование данного патента позволяет снизить время перемешивания смеси при этом не теряя ее качества тем самым подвышая производительность установки что и явлется целью данного курсового проекта.
Прототипом является асфальтосмесительная установка ДС-158.
Описание конструкции и кинематической схемы привода барабана смесительной установки асфальтосмесителя ДС-158
В качестве привода смесителя используется электродвигатель редуктор а также открытая зубчатая передача с передаточным числом равным 1 для передачи крутящего момента на валы смесителя.
Кинематическая схема привода смесителя приведена на рисунке 1.
Рисунок 1 – Кинематическая схема привода смесительной:
– пружина; 2 – подвижная часть корпуса; 3 – неподвижная часть корпуса; 4 – открытая зубчатая передача; 5 – редуктор; 6 - электродвигатель
Привод валов смесителя осуществляется от электродвигателя через редуктор и открытую зубчатую передачу с передаточным числом равным 1. Загрузка происходит через загрузочное отверстие в верхней части корпуса смесителя а разгрузка через разгрузочное отверстие в нижней части корпуса. Во время работы смесителя происходит движение подвижной части корпуса за счет винтового соединения между подвижной частью и валом. За половину оборота вала подвижная часть отводится в сторону после чего резко возвращается в исходное положение с помощью пружины сжатия.
Определение основных параметров машины и рабочего оборудования
1 Расчет длительности смешивания и размеров смесителя
Расчет длительности смешивания будем вести в соответствии с методикой изложенной в [1 с 83–85].
где П–производительность установки тч;
–коэффициент использования смесителя по времени = 085;
– длительность цикла с
где –время загрузки смесителя = 5 с;
–длительность смешивания с;
– время разгрузки = 5 с.
Тогда из формулы (4.1) с учетом (4.2) длительность смешивания с
Радиус корпуса смесителя м
где –коэффициент характеризующий форму корпуса смесителя = 085;
–коэффициент заполнения корпуса смесителя материалом = 1;
–плотность смеси = 1650 кгм3
Межцентровое расстояние валов м
Ширина корпуса смесителя м
Длина корпуса смесителя м
Площадь поперечного сечения рабочей части корпуса смесителя м2
Действительная частота вращения лопастных валов обмин
Фактическая длительность смешивания с
где –относительная концентрация компонента в зоне одного из лопастных валов для неблагоприятного случая = 0;
–коэффициент характеризующий поперечный обмен = 005
2 Расчет привода смесительной установки
2.1 Расчет открытой зубчатой передачи
Допускаемые напряжения изгиба [2 с. 140] МПа
где –предел выносливости зубьев по напряжениям изгиба для стали 40Х с твердостью 300 HB = 540 МПа;
–коэффициент безопасности = 175;
–коэффициент учитывающий влияние двухстороннего приложения нагрузки = 1;
–коэффициент долговечности предполагая длительный срок службы примем = 1
Модуль открытой зубчатой передачи из условия прочности зубьев по напряжениям изгиба [2 с. 141]
Преобразовав формулу (4.12) получим
где –крутящий момент на валу привода Нм
где –мощность необходимая для привода лопастных валов смесительного агрегата [1 с. 87] Вт
–коэффициент нагрузки согласно [2 рис. 8.15] = 102;
–коэффициент формы зуба = 412
–согласно рекомендациям [2 табл. 8.5] = 30
Округляем полученное значение модуля до стандартного 9 мм.
Количество зубьев одного колеса
2.2 Выбор двигателя и редуктора
Согласно [3 с. 115] мощность приводного двигателя кВт
где –КПД муфты = 098;
–КПД редуктора = 096;
–КПД зубчатой передачи = 092;
–КПД пар подшипников = 099
Из [3 табл. III.3.1] принимаем электродвигатель защищенный обдуваемый 4A225M6Y3 мощностью =37 кВт с частотой вращения nдв=980 обмин момент инерции ротора 0735 кгм2.
Из [3 табл. III.4.2] принимаем редуктор цилиндрический горизонтальный двухступенчатый Ц2-500 с фактическим передаточным числом равным u=1241.
С учетом выбранных электродвигателя и редуктора уточняем частоту вращения лопастного вала смесителя и время смешивания смеси в смесителе.
Фактическая частота вращения лопастного вала смесителя обмин
Фактическое время смешивания по (4.10) с
3 Определение параметров лопастей
Определение параметров лопастей будем вести в соответствии с методикой изложенной в [1 с. 85–87].
Число парных лопастей на одном валу
где –зазор между крайней лопастью и торцовой стенкой смесителя = 10 мм;
–угол наклона лопастей к оси вала = 4427°;
–зазор между боковыми кромками соседних лопастей = 50 мм
Расчет пружины будем вести в соответствии с методикой изложенной в [5 с. 195–204].
Для толкания подвижной части смесителя будут использоваться две пружины сжатия. Чтобы подвижная часть могла двигаться она должна преодолеть ряд сопротивлений: сопротивление от трения подвижной части о герметичные уплотнения и сопротивление смеси. Силой сопротивления от трения подвижной части о герметизирующие уплотнения пренебрегаем из-за ее малости в отношении к силе сопротивления смеси.
Сила сопротивления смеси кН
где –вместимость = mз = 0649 т;
–коэффициент динамичности = 25
Для обеспечения движения подвижной части корпуса смесителя сила пружины при рабочей деформации должна быть Силу пружины при рабочей деформации примем равной F2=20 кН. Рабочую деформацию пружины из конструктивных соображений принимаем равной s2=200 мм. Выносливость пружины примем равной NF=1107 циклов. Согласно [6] наружный диаметр пружины D1 = 280 мм.
Сила пружины при максимальной деформации Н
Сила пружины при предварительной деформации Н
Относительный инерционный зазор пружины сжатия
По значению относим пружину к I-му классу 4-му разряду пружин сжатия. Диаметр проволоки согласно [7] d = 32 мм. Жесткость одного витка пружины согласно [6] c1 = 6737 Нмм.
Минимальная деформация одного витка пружины мм
где –наибольший прогиб одного витка согласно [6] = 29690 мм
Согласно [7] максимальное касательное напряжение примем равным 3=480 Нмм2.
Критическая скорость пружины мс
где –модуль сдвига = 785104 Нмм2
–динамическая плотность материала = 8103 Нс2м4
Жесткость пружины Нмм
Число рабочих витков пружины
Полное число витков пружины
где –число опорных нерабочих витков пружины = 15
Средний диаметр пружины мм
Предварительная деформация пружины мм
Максимальная деформация пружины мм
Длина пружины при максимальной деформации мм
где –число обработанных витков = 15
Длина пружины в свободном состоянии мм
Длина пружины при предварительной деформации мм
Длина пружины при рабочей деформации мм
Шаг пружины в свободном состоянии мм
Напряжение в пружине при предварительной деформации Нмм2
Напряжение в пружине при рабочей деформации Нмм2
Коэффициент учитывающий кривизну витка пружины
Длина развернутой пружины мм
Внутренний диаметр пружины мм
5 Расчет валов смесителя
5.1 Определение нагрузки на валы от подвижной части корпуса
Сторона квадрата сечения вала в месте крепления лопастей согласно [3 с. 121] см
где –сила приложенная к лопасти при заклинивании кг
где –коэффициент динамичности = 12
l1и l2–расстояние от опор вала до центра крепления ступицы l1=737 см l2=954 см
–коэффициент учета уменьшения момента инерции для валов квадратного сечения со снятыми фасками = 12;
–модуль упругости = 2106 кгсм2;
–длина вала = 1691 см
Примем что после обработки участки вала под посадку лопастей будут иметь размер 90×90 мм диаметр вала примем равным d = 86 мм.
Сила воздействующая на вал от подвижной части корпуса Н
Динамическая сила воздействующая на вал Н
где –динамические напряжения [8 с. 176] МПа
где –статические напряжения МПа
где –площадь поперечного сечения вала м2
–динамический коэффициент [8 с. 177]
где –прогиб от статической нагрузки [8 с. 27] мм
Для дальнейших расчетов силу действующую на вал со стороны подвижной части корпуса примем равной динамической силе = = 4590 Н.
5.2 Определение реакций опор
Расчетная схема вала смесителя с действующими на него нагрузками и эпюрами изгибающих моментов приведена на рисунке 2.
Рисунок 2 – Эпюры изгибающих моментов
При установившемся режиме все лопасти испытывают нагрузку от сил сопротивления движению при перемешивании.
Распределенная нагрузка [3 с. 120] Нм
Крутящий момент на валу [3 с. 120] Нм
Реакции моментов определим через уравнения моментов относительно опор вала.
Определение реакций опор в горизонтальной плоскости.
Определение реакций опор в вертикальной плоскости.
Выбор подшипников будем вести в соответствии с методикой изложенной в [9 с. 140–142].
Рисунок 3 – Расчетная схема для выбора подшипников
Предварительно принимаем подшипник [10 табл. 24.16] роликовый конический однорядный 7315А ГОСТ 27365-87 с базовой динамической грузоподъемностью =2290 кН и расчетными параметрами e=035 =17. Радиальные нагрузки подшипников принимаем равными реакциям опор валов ==1874454 Н ==2387107 Н.
Осевая составляющая радиальной нагрузки подшипника Н
Осевая нагрузка на первую опору ==544529 Н. Осевая нагрузка на вторую опору Н
Условие правильности выбора подшипников
где –расчетная динамическая грузоподъемность Н
где –эквивалентная динамическая нагрузка Н
где –коэффициент радиальной нагрузки = 04;
–коэффициент осевой нагрузки = 17;
–коэффициент вращения = 1;
–коэффициент безопасности = 17;
–температурный коэффициент = 1
m–показатель степени m=33;
–показатель надежности = 1;
–коэффициент учитывающий влияние качества подшипника и качества его эксплуатации = 07
–требуемая долговечность подшипника 5000 ч
Условие (4.70) выполняется следовательно выбранный подшипник пригоден для конструирования подшипниковых узлов.
Эскизное конструирование машины. Обоснование компоновочных решений
Для увеличения производительности смесительной установки в ее конструкцию вводится подвижная емкость. Из-за этого увеличиваются габаритные размеры установки. Так как подвижная емкость двигается на расстояние 200 мм то увеличивается длина валов смесителя. Вводится конструкция упора для пружин сжатия что также увеличивает длину валов смесителя. В результате ввода в конструкцию смесителя подвижной емкости и упора расстояние между опорами вала становится 2068 мм. Также увеличивается нагрузка на опоры вала из-за динамической составляющей. Воспринимать эти нагрузки будут конические роликовые подшипники.
Для передвижения подвижной емкости по валу при его вращении на участке вала на половине его диаметра нарезается упорная резьба. Для возвращения подвижной емкости в исходное положение используются две пружины сжатия. В соответствии с рекомендациями [5 с. 241] данные пружины сжатия должны работать в направляющей гильзе. Направляющие гильзы входят в состав конструкции упора для пружин сжатия. Для уменьшения нагрузки на вал со стороны силы тяжести подвижной емкости а также предотвращения перекосов ее перекосов вводим опорные ролики по которым подвижная емкость будет перекатываться. Местами для опоры на ролики предусмотрены в конструкции подвижной емкости.
Разработка мероприятий по технике безопасности охране окружающей среды энергоресурсосбережению при работе машины
1 Техника безопасности при эксплуатации асфальтосмесительных установок [11 с. 177]
Во время работы асфальтосмесительной установки НЕ ДОПУСКАЮТСЯ:
любые операции связанные с обслуживанием в т. ч.: чистка регулировка ремонт подтяжка резьбовых соединений трубопроводов (топлива битума теплоносителя воздуха) трубопроводной арматуры насосов редукторов и т. п.;
техническое обслуживание электроприемников находящихся под напряжением;
нахождение людей под навесными битумопроводами наклонным конвейером смесителем бункером готовой смеси скипом и затвором бункера излишков;
снятие решетки с бункеров агрегата питания нахождение в бункерах и под ними;
нахождение посторонних в кабине оператора на площадках обслуживания агрегатов;
При работающей установке проход под эстакадой скипового подъемника должен быть закрыт ограждением с запрещающими знаками «ПРОХОД ВОСПРЕЩЕН».
При отборе проб асфальтобетонной смеси из кузова автотранспорта нельзя находиться под бункером готовой смеси и под смесителем.
Пробу следует отбирать с уже загруженной машины отъехавшей от места загрузки (согласно ГОСТ 12801-98).
допуск к работе лиц не прошедших специального обучения для работы на уста-новке не прошедших инструктажа по технике безопасности и противопожарного инструктажа и не получивших соответствующих квалификационных удостоверений;
запуск установки без продувки сушильного агрегата;
работа при неисправных контрольно-измерительных приборах;
оставлять без присмотра работающую установку или отдельные агрегаты;
работа с неизолированными обогреваемыми трубопроводами при отсутствии защитных кожухов на фланцевых соединениях битумопроводов и топливопроводов;
заполнять битумные цистерны более чем на 80 % их объема;
работа при неисправных поплавковых указателях уровня в битумной цистерне и топливной емкости;
работа оборудования при снятых перилах кожухах ограждениях установленных над подвижными вращающимися механизмами;
работа при незакрепленных люках битумной цистерны топливной емкости люках на газоходах;
заносить огонь на площадку смотровых люков и вовнутрь цистерн;
включать в работу битумные насосы без прогрева теплоносителем;
включать вибраторы при незагруженных бункерах агрегата питания.
Рабочая площадка на которой смонтирована асфальтосмесительная установка должна иметь освещение для обслуживания установки в ночное время. Трубопроводы битума топлива (мазута) разводки жидкого теплоносителя должны быть теплоизолированы и окрашены опознавательной краской.
Пожароопасные места (склады топливосмазочных материалов и поверхностно-активных добавок битумохранилища битумоплавильные агрегаты асфальтобетонные смесители) должны быть оснащены щитами с противопожарным оборудованием огнету-шителями ящиками с сухим песком. Тушение загоревшихся топливосмазочных материа-лов поверхностно-активных добавок битума производится огнетушителями-пеногонами песком. Для тушения источника огня можно применять брезент или кошму.
Разрывы и проходы между установками завода должны быть не менее 3 м чтобы обеспечить беспрепятственный подъезд пожарным машинам к любой установке завода и в любое время дня и года. Сооружения и сгораемые строения завода необходимо располагать от пожароопасных мест не менее чем на 50 м.
Битумный дозатор по массе должен быть всегда плотно закрыт крышкой предохраняющей от разбрызгивания горячего битума. Рабочие места машиниста и форсунщика должны быть оснащены огнетушителями-пеногонами.
В качестве разжижителя битума можно использовать лигроин керосин или дизельное топливо. Разжижать битум можно под руководством ответственного лица и в дневное время. Оборудование для разжижения битума должно располагаться не ближе 30 м от битумохранилища и битумоплавильного агрегата. Подогрев разжиженного битума осуществляется только теплоносителями с температурой от 100 до 300 °С.
Разжижитель подают непосредственно в массу битума а не на его поверхность чтобы разжижитель не загорелся. Рабочим занятым разжижением битума целесообразно находиться с наветренной стороны от оборудования и применять индивидуальные средства защиты в том числе респираторы и очки.
Штабеля песка и щебня располагаемые над течками конвейерных галерей должны быть ограждены надписями «Вход в штабель воспрещен под штабелем течка».
Асфальтобетонный смеситель разрешается пускать в работу только после подачи предупредительного звукового сигнала; установления исправности машины выявленной путем тщательного внешнего осмотра; проверки исправности проводки и узлов автоматики механизмов и местного пуска отдельных механизмов наличия соответствующего давления сжатого воздуха в системе пневмопривода; опробования вхолостую всех узлов и агрегатов смесителя пробного пуска битумного насоса подающего битум от битумоплавильного агрегата к смесителю и обратно; установки транспортного средства под погрузку на АБЗ где отсутствует накопительный бункер готовой смеси (при наличии накопительного бункера проверяют вхолостую открытие и закрытие затворов бункера работу скипового подъемника).
При отсутствии автоматической системы розжига основной форсунки сушильного барабана розжиг и регулировка форсунки должны производиться форсунщиком находящимся сбоку топки. Запрещается стоять против форсунки во время розжига и ее работы.
При неисправности топок форсунок или газовых горелок работа сушильного барабана запрещается. Все сушильные барабаны асфальтобетонных смесителей должны быть оборудованы двух- или трехступенчатой системой пылеулавливания.
По окончании работы асфальтобетонного завода пульт управления пусковые приспособления необходимо отключить и запереть чтобы исключить возможность пуска смесителя или машины посторонними людьми.
Осмотр и ремонт внутренних частей сушильного барабана «горячего» элеватора грохота «горячего» бункера дозаторов по массе мешалки пылеулавливающего оборудования а также накопительного бункера готовой смеси где они имеются разрешается проводить только после их остывания.
Магистральные теплопроводы для подачи жидкого топлива в форсунки битумоплавильных агрегатов могут располагаться не ближе 2 м от форсунок. Подводящие топливопроводы к каждой форсунке должны иметь самостоятельные краны расположенные в удобных для использования местах.
Применять открытый огонь для разогрева битумопроводов перед началом работы запрещается. В случае возгорания битума в котле битумоплавильного агрегата необходимо плотно закрыть крышкой горловину котла и отключить форсунку.
Запрещается оставлять битумоплавильные агрегаты без присмотра при включенной электроэнергии пользоваться металлическими приспособлениями для замера или перемешивания битума. Электронагреватели должны быть полностью погружены в битум.
Обслуживать и ремонтировать элементы электронагревателей разрешается только при отсутствии в них тока. Все металлические элементы битумоплавильных агрегатов должны быть заземлены. Очистка обслуживание и ремонт оборудования для разогрева и приготовления битума возможны только после их полного остывания.
Очистку котлов битумоплавильных агрегатов должны выполнять два человека: один спускается вниз а другой - страхует его привязанной к предохранительному поясу веревкой. Для освещения внутренних деталей котла необходимо использовать переносную лампу напряжением не выше 12 В во взрывобезопасном исполнении.
Поверхностно-активные вещества содержащие воду могут вводиться в битум если его температура не выше 95 °С. Помещения в которых приготавливаются активированные асфальтобетонные смеси должны обеспечиваться приточно-вытяжной вентиляцией.
Попавшие на кожу водорастворимые поверхностно-активные добавки (катапин катамин) должны быть немедленно смыты сильной струей воды и вымыты нейтральным не содержащим соду мылом. Поверхностно-активные вещества высших алифатических аминов (диамин БП-2 БП-3 эвазин и т. п.) сначала снимают растворителями (керосин бензин) не втирая в кожу а затем смывают водой с нейтральным мылом.
Анионактивные поверхностно-активные вещества типа высших карбонов кислот (госсиполовая смола второй жировой гудрон окисленные петролатум или рисайкл и др.) удаляются с поверхности кожи так же как и высшие алифатические амины. Хлорное железо попавшее на кожу работающего смывают водой с нейтральным мылом а поврежденные участки смазывают жиром.
2 Мероприятия по охране окружающей природной среды [11 с. 180]
Проектирование генеральных планов асфальтобетонных заводов (АБЗ) с точки зрения соблюдения санитарно-гигиенических требований предусматривает расположение предприятий по отношению к жилым районам сельскохозяйственным угодьям и другим экологически чувствительным зонам с учетом преобладающего движения воздушных масс (розы ветров) то есть с подветренной стороны.
Размеры санитарно-защитных зон непосредственно от источника загрязнения на АБЗ до границ жилой застройки принимаются в соответствии с требованиями СН-245-71 и составляют: для АБЗ стационарного типа - 300 м (III класс по санитарной классификации); для инвентарного - 500 м (II класс по санитарной классификации).
Территория санитарно-защитных зон должна быть благоустроена газоустойчивыми породами деревьев и кустарников по проектам благоустройства. При этом следует иметь в виду что запыленность березы в 25 раза а запыленность хвойных пород в 30 раз больше запыленности осины. Лучше пыль задерживают деревья с шероховатыми листьями на листовой поверхности таких деревьев осаждается до 70 % пыли из атмосферного воздуха.
Древесные насаждения значительно уменьшают концентрацию вредных газов например: концентрация окислов азота проходя через зеленые насаждения снижается в 5 и более раз. В очистке воздуха от токсичных газов наиболее эффективны лиственные насаждения по сравнению с хвойно-лиственными и хвойными.
Эксплуатация предприятий по производству дорожно-строительных материалов сопровождается значительным выделением загрязняющих веществ в окружающую среду. При этом не только теряется значительная часть дефицитного сырья но и возникают условия для нарушения экологических требований и санитарно-гигиенических норм.
Источники загрязнения окружающей природной среды подразделяются на источники выделения и источники выбросов вредных веществ в атмосферу.
Источником выделения вредных веществ на АБЗ является технологический агрегат установка устройство аппарат и др. выделяющие в процессе эксплуатации вредные вещества.
Источником выбросов вредных веществ является устройство (труба аэрационный фонарь вентиляционная шахта) посредством которого осуществляются выбросы вредных веществ в атмосферу.
Выбросы вредных веществ подразделяются на организованные и неорганизованные.
Организованными выбросами являются выбросы отводимые от мест выделения системой газоотводов что позволяет применять для их улавливания различные системы и оборудование.
Неорганизованными выбросами являются выбросы возникающие за счет негерметичности технологического оборудования газоотводных устройств резервуаров открытых мест пыления и испарения.
Инвентаризация должна проводиться как для организованных так и неорганизованных выбросов.
Высокие и постоянно растущие экологические требования предъявляемые к АБЗ предопределяют расширение внедрения организационных технических и технологических мероприятий направленных на снижение вредных воздействий на окружающую природную среду.
К числу этих мероприятий в первую очередь следует отнести:
совершенствование контроля за соблюдением технологических режимов и правил;
строительство новых и повышение эффективности существующих очистных установок;
совершенствование технологических процессов приготовления асфальтобетонных смесей.
К первому направлению относятся постоянный контроль за агрегатами и узлами АБЗ являющимися источниками выброса загрязняющих веществ и регулярное проведение технического обслуживания очистных устройств. Особое наблюдение должно быть установлено:
за состоянием уплотнения между обечайкой вращающихся сушильных барабанов и торцами неподвижно закрепленных загрузочных и разгрузочных коробок асфальтосмесительных установок;
за пыленепроницаемостью кожухов горячих элеваторов грохотов и смесителей и наличием отсоса воздуха из-под кожухов с целью исключения выделения при работе механизмов;
за герметичностью газоотводов;
за бесперебойной работой всех пылегазоочистных систем;
за соблюдением температурных режимов.
Ресурсосбережение можно повысить за счет:
применение герметичных бункеров и силосов для минерального порошка а также пневмотранспорта для его перемещения к асфальтобетонной установке;
использование минеральных заполнителей отвечающих требованиям соответствующих государственных стандартов по содержанию в них пылевидных и глинистых частиц;
применение совершенных топочных устройств установку газоанализаторов и кислородомеров для подбора оптимального режима сжигания топлива;
оснащение асфальтобетонных установок устройствами для непрерывного контроля эффективности пылеулавливания;
разработка новых технологичных способов приготовления асфальтобетонных смесей отличающихся от принятой технологии меньшим пылеобразованием.
Также в качестве ресурсосберегающих мероприятий можно использовать ограничение потребления тепловой энергии административными и производственными зданиями в нерабочее время и выходные дни проведение режимно-наладочных испытаний паровых и водогрейных котлов горелочных устройств сушильных барабанов асфальтосмесительных установок внедрение топочных установок работающих на местных видах топлива внедрение энергосберегающих светильников экономичных ламп и приборов регулирования теплоснабжения и ряд других.
В данном курсовом проекте была модернизирована асфальтосмесительная установка ДС-158. Была повышена ее производительность до 60 тч. В результате модернизации также возросли габаритные размеры смесителя его вес. Модернизировав данную установку повысили ее производительность не потеряв качества смеси.
Довгяло В.А. Бочкарев В.И. Мартиновский В.А. Машины и оборудование для производства асфальтобетонных смесей: Пособие. – Гомель: УО «БелГУТ» 2005. – 91 с.
Иванов М.Н. Детали машин: Учеб. для студентов втузов. – М.: Высш. шк. 2000. – 383 с.: ил.
Севров К.П. Камчатнов Л.П. Установки для приготовления асфальтобетонных и битумоминеральных смесей. – М.: Машиностроение 1971. – 129 с.
Кузьмин А.В. Марон Ф.Л. Справочник по расчетам механизмов подъемно-транспортных машин. 2-е изд. перераб. и доп.Мн.: Высш. шк. 1983.350 с. ил.
Анурьев В.И. Справочник конструктора-машиностроителя: в 3-х т. Т.3. – 9-е изд. перераб. и доп. – М.: Машиностроение 2006. – 928 с.
ГОСТ 13776–86 Пружины винтовые цилиндрические сжатия III класса разряда 3 из стали круглого сечения.
ГОСТ 13764–86 Пружины винтовые цилиндрические сжатия и растяжения из стали круглого сечения.
Старовойтов Э.И. Сопротивление материалов: Учеб. пособие для студентов технических вузов. – Гомель: БелГУТ 1999. – 219 с.
Шейнблит А.Е. Курсовое проектирование деталей машин: Учеб. пособие. Изд-е 2-е перераб. и дополн. – Калининград: Янтар. сказ. 2002. – 454 с.: ил. черт. – Б. ц.
Дунаев П.Ф Леликов О.П. Конструирование узлов и деталей машин учеб. пособие для техн. спец. вузов. – М.: Высш. шк. 1998. – 447 с.
Силкин В.В. Лупанов А.П. Асфальтобетонные заводы: Учебное пособие. - М.: Экон-Информ 2008 г. - 266 с и 20 с. ил.
Рекомендуемые чертежи
- 22.08.2014
- 22.08.2014
- 22.08.2014
- 22.08.2014
- 22.08.2014