Метрология, стандартизация и сертификация вар 1-1




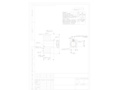
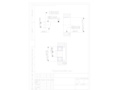
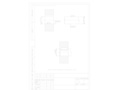
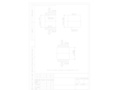
- Добавлен: 24.01.2023
- Размер: 1 MB
- Закачек: 1
Описание
Состав проекта
![]() |
![]() |
![]() ![]() ![]() ![]() |
![]() ![]() ![]() |
![]() ![]() ![]() |
![]() ![]() ![]() ![]() |
![]() ![]() ![]() ![]() |
![]() ![]() ![]() |
![]() |
![]() ![]() ![]() ![]() |
![]() ![]() ![]() |
![]() ![]() ![]() ![]() |
![]() |
![]() ![]() ![]() |
![]() ![]() ![]() |
![]() ![]() ![]() |
![]() ![]() ![]() |
![]() ![]() ![]() |
![]() ![]() ![]() |
Дополнительная информация
D3.dwg

Содержание и летература.doc
1 Соединение гладких валов и отверстий.
2 Контроль размеров цилиндрических поверхностей гладкими
3. Допуски и посадки подшипников качения.
4. Допуски размеров входящих в размерные цепи.
Нормирование точности типовых соединений сложного профиля.
1. Нормирование точности метрической резьбы.
2. Нормирование точности шпоночных и шлицевых соединений.
3. Нормирование точности цидиндрических прямозубых
Выбор универсальных средств измерения.
Используемая литература.
Нормирование точности изделий машиностроения: Учебное пособие
НГТУ; В. Н. Кайнова и др. Н. Новгород 2001.
Расчёт исполнительных размеров гладких калибров: Мтодические
указания НГТУ; В. Н. Кайнова и др. Н. Новгород 1995.
Методические указания к курсовой работе по дисциплине
“Взаимозаменяемость стандартизация и технические измерения”
ГПИ Л.А. Болдин и др. Горький 1989.
Выбор универсальных средств измерения. Кайнова.2000.
1.2 Калибры 1-1.doc
Построить схему расположения полей допусков гладких калибров для контроля отверстия и вала рассчитать исполнительные размеры калибров. Вычертить эскизы калибров.
2.1 Карта исходных данных
Для расчета выбираем соединение «вал - зубчатое колесо» и заполняем карту исходных данных.
Контролируемая поверхность
Контролируемый размер
2.2 Определение размеров допусков на калибры
По ГОСТ 24853-81 найдём допуски на калибры для вала и отверстия [4 с.4 таблица 1]:
Размер сдвига поля допуска проходных калибров внутрь поля допуска детали
Размер выхода допуска на износ за границу поля допуска детали
Размер сдвига поля допуска непроходных калибров внутрь поля допуска детали
Допуск на изготовление калибра
Допуск на изготовление контркалибра
2.3 Расчет калибра - пробки
Исполнительные и действительные размеры пробки согласно схеме расположения полей допусков (рисунок 1.13) подсчитываются по формулам [4 с. 7]:
Размер предельного износа пробки определяется по следующей формуле [4 с. 8]:
Рисунок 1.4 - Схема расположения полей допусков отверстия и калибра-пробки
2.4 Расчет калибра - скобы
Исполнительные и действительные размеры скобы согласно схеме расположения полей допусков (рисунок 1.14) подсчитываются по формулам [4 с. 7]:
Размер предельного износа скобы определяется по следующей формуле [4 с. 8]:
2.5 Расчет контркалибра
Для контроля размеров калибров-скоб используют контркалибры. Исполнительные размеры контркалибров согласно схеме расположения полей допусков (рисунок 1.14) подсчитываются по формулам [4 с. 7]:
Рисунок 1.5 - Схема расположения полей допусков вала калибра-скобы и контркалибров
2.6 Технические требования к калибрам
Допуск цилиндричности (для круглых пробок ) [ 1. 4 ] :
То=13Н= 13*5=167мкм.
Округляем до ближайшего числа из ряда чисел: (08; 1; 2; 25; 3; 4; 5; 6; 8; 10 ) То=2 мкм.
Шероховатость рабочих поверхностей Ra по ГОСТ 2015-84 [4 с. 8]:
КонтркалибрыRa = 0.04 мкм
Шероховатость торцов - Ra= 1.6 мкм фасок - Ra = 08 мкм.
2.7 Конструктивные размеры пробки
Конструктивные размеры калибра-пробки [4 с. 14 таблица 8] указаны в таблице 1.6:
Пробка проходная по ГОСТ 14815
Пробка непроходная по ГОСТ 14816
Рисунок 1.6 - Эскиз пробки
а) – проходная пробка- 8136-0001 Н8 ГОСТ 14815-69
б) – непроходная пробка- 8136-0101 H8 ГОСТ 14816-69
2.8 Конструктивные размеры скобы
Конструктивные размеры калибра-скобы (4 с.10 таблица 8.4) указаны в таблице 1.7:
Условное обозначение скобы (рисунок 1.8): Скоба 8113-0141. ГОСТ 18360-93.
Рисунок 1.8 - Эскиз скобы 8113-0141 g7 ГОСТ 18360-93
D 1.dwg

Зубчатое.dwg

Степень точности по ГОСТ 1643
Обозначение чертежа сопряженного колеса
2.2.1 Шпоночное соед 1-1.doc
и шлицевых соединений
2.1 Нормирование точности шпоночного соединения
Для шпоночного соединения с призматической (или сегментной) шпонкой подобрать посадки шпонки в пазы вала и отверстия исходя из условий работы; вычертить эскизы поперечных сечений вала отверстия и самой шпонки; изобразить на схеме посадки шпонки по ширине в пазы вал и отверстия.
2.1.1 Карта исходных данных
Наименование исходных данных
Значение исходных данных
Диаметр соединения d мм
Ширина и высота шпонки (ГОСТ 23360) b x h мм
Количество шпонок в соединении:
Расположение нескольких шпонок в соединении под углом:
2.1.2 Определение параметров шпоночного соединения [3 с.69 таблица 3.1]:
d =24 мм- диаметр вала
b = 8 мм- ширина шпонки
h = 7мм - высота шпонки
Smin = 0.25 мм - фаска
S1 max = 0.25 мм- фаска
r = 0.25 мм - радиус закругления
l = 18..90 мм - интервал длин
t1 = 4.0+0.2 мм - глубина шпоночного паза с отклонением на валу
t2 = 33+0.2 мм - глубина шпоночного паза с отклонением во втулке
2.1.3 Выбор посадок шпонки.
Предельное отклонение по ГОСТ 23360-78 [3 с.70]:
Поля допусков пазов [3 с.72 таблица 3.2.]:
Поля допуска по длине шпонки l: h14
Поля допуска по длине паза под шпонку L:H15
Рисунок 2.1 - Схема расположения полей допусков на размер b и шпоночное соединение
Рисунок 2.2 - Эскиз шпоночного соединения
Подшипник.dwg

1.3 Подшипник 1-1 .doc
Для колец заданного подшипника назначить посадку на вал и в корпус. Расшифровать условное обозначение подшипника. Построить схемы полей допусков. Вычертить эскизы подшипникового узла и посадочных поверхностей вала и корпуса под подшипник.
3.1 Карта исходных данных
Наименование исходных данных
Значение исходных данных
Условное обозначение подшипника
№ позиции по чертежу
Радиальная нагрузка Fr кН
Режим работы подшипника перегрузки %
перегрузка до 150% толчки и вибрации умеренные режим работы –нормальный.
Конструкция вала (по чертежу)
Конструкция корпуса (по чертежу)
Соседние с подшипником детали
Наличие стакана (СТ): нерегулируемого
Наличие крышки (КР):
- фланцевой глухой (КФ)
- то же с отверстием под вал и гнездом под манжету (КФМ)
- закладной глухой (КЛ)
- то же с отверстием под вал и гнездом под манжету (КЛМ)
Наличие втулки (ВТ):
Наличие кольца на валу (КЦ):
3.2 Условное обозначение подшипника
Расшифровка подшипника по ГОСТ 8338:
Радиальный шарикоподшипник однорядный.
код диаметра отверстия внутреннего кольца- 05
серия по диаметру - 3
тип подшипника- 0 – радиальный шариковый
конструктивное исполнение- 0 – однорядные
3.3 Конструктивные размеры подшипника
Основные размеры подшипника по ГОСТ 8338:
Внутренний диаметр подшипника d = 25 мм
Внешний диаметр подшипника D = 62 мм
Ширина внутреннего кольца B = 17-012 мм
Радиусы скругленийr = 20 мм
Рисунок 1.9 - Эскиз подшипника ГОСТ 8338
3.4 Определение отклонений на посадочные размеры колец подшипника
Класс точности подшипника – 6.
По ГОСТ 520-89 определим нижние отклонения на посадочные размеры коле подшипника:
внутренне кольцо подшипника мкм
внешнее кольцо подшипника мкм
3.5 Определение вида нагружений колец подшипника
Вращающаяся деталь - вал следовательно внутренне кольцо подшипника испытывает циркуляционную нагрузку наружное кольцо испытывает местное нагружение.
3.6 Расчет интенсивности радиальной нагрузки
Вращающееся кольцо подшипника испытывает циркуляционный вид нагружения что требует обеспечения неподвижного соединения с сопрягаемой деталью. Величина минимального натяга зависит от интенсивности радиальной нагрузки определяемой по формуле:
где - интенсивность радиальной нагрузки кНм;
Fr- радиальная реакция опоры в подшипнике кН;
B - ширина подшипника мм;
r и r1 - радиусы закруглений внутреннего кольца подшипника мм
К1 - динамический коэффициент посадки зависящий от допустимой перегрузки.
(K1=1 при перегрузке до 150% когда толчки и вибрации умеренные);
К2 - коэффициент учитывающий ослабление посадочного натяга при пониженной жесткости вала или корпуса (для жесткой конструкции К2=1);
К3 - коэффициент неравномерности распределения радиальной нагрузки между рядами тел качения в двурядных роликоподшипниках и сдвоенных шарикоподшипниках при наличие осевой нагрузки на опору (для однорядных подшипников К3=1).
3.7 Выбор полей допусков
Для циркуляционно-нагруженного кольца подберем посадку в зависимости от диаметра интенсивности радиальной нагрузки и класса точности.
Посадка для внутреннего кольца подшипника:
Для местно-нагруженного кольца подберем посадку в зависимости от диаметра и класса точности.
Посадка для наружного кольца подшипника:
3.8 Геометрические параметры посадки
Внутреннее кольцо подшипника: мм
Минимальный натяг: мм
Максимальный натяг: мм
Рисунок 1.10 - Расположения полей допусков внутреннего кольца подшипника и вала
3.9 Геометрические параметры посадки
Отверстие корпуса: мм
Внешнее кольцо подшипника: мм
Минимальный зазор: мм
Максимальный зазор: мм
Рисунок 1.11 - Расположения полей допусков внешнего кольца подшипника и отверстия
3.10 Технические требования на рабочие чертежи деталей.
Значение шероховатости поверхностей сопрягаемых деталей [3 с.42 таблица 2.2]:
Допуск круглости и профиля продольного сечения [3 с. 97 таблица 4.13]:
для отверстия:мкм мкм
Допуски торцевого биения заплечиков: [3 с. 97 таблица 4.13]
Эскизы деталей показаны на рисунках 1.21 1.22 1.23.
D2.dwg

2.3 зубчатая передача 1-1.doc
По заданным степени точности и виду сопряжения прямозубой b = 0 и некорригированной х = 0 цилиндрической зубчатой передачи назначить контрольные параметры для проверки её годности. Определить их допустимые значения. В соответствии с ЕСКД вычертить эскиз зубчатого колеса.
3.1. Карта исходных данных Таблица 2.3.1
Наименование исходных данных
Значение исходных данных
Сведения о зубчатой передаче и колесе
Вид изделия (автомобиль пресс специальный станок)
№ позиции по чертежу
Межосевое расстояние а мм
Модуль зубчатой передачи m мм
Коэффициент смещения исходного контура
Окружная скорость V мс
3.2 Определение параметров зубчатого колеса
Диаметр делительной окружности d = m z = 4 25 = 100 мм
Диаметр окружности вершин d а = d + 2 m = 100 + 2 4 = 108 мм
Ширина зубчатого венца В = 10 m = 10 4 = 40 мм
3.3 Определение степени точности
Передача является скоростной.
По заданной окружной скорости согласно [3 с.124 таблица 6.3]:
Степень точности по нормам плавности - 6.
С технологической точки зрения нормы плавности могут быть не более чем на одну- две степени грубее норм кинематической точности. Степень точности по нормам контакта принимается равной степени плавности или на одну степень грубее норм плавности для кинематических и скоростных передач или точнее на одну степень для силовых передач.
[3 с.125]. Таким образом получаем:
Степень кинематической точности - 7.
Степень точности по нормам контакта - 6.
3.4 Определим вид сопряжения
Вид сопряжения определим по минимальному гарантированному боковому зазору
j n1 = 0.03 · 4 = 0.12 мм
Боковой зазор соответствующей температурной компенсации определяется по формуле:
j n2 = 0.684 · а · (а1 · (t1 – 20°) – а2 · (t2 – 20°))
где а – межосевое расстояние;
а1 и а2 – коэффициенты линейного расширения для материалов зубчатых колес и корпуса
t1 и t2 – предельные температуры для которых рассчитывается боковой зазор для зубчатых колес и корпуса соответственно.
а1 = 12·10-6 – для стали; t1 = 35°
а2 = 23·10-6 – для силумин; t2 = 30°
j n2 = 0.684 · 160 · (12·10-6 · (35° – 20°) – 23·10-6 · (30° – 20°)) = 0.005472 мм
j n min = j n1 + j n2 = 0.12 + 0.005472 = 0.125472мм
Для заданного межосевого расстояния и значению минимального гарантированного бокового зазора определяем [3 с.130 таблица 6.9]:
Вид сопряжения - C ( jmin=100 мкм)
Класс отклонения межосевого расстояния - IV
Полное обозначение степени точности:
3.5Выбираем контрольные показатели норм точности и вида сопряжения:
Выбираем третий контрольный комплекс; т.к. производство серийное степени точности 7 и 6:
- для кинематической точности: F
- для плавности работы – fi’ и ff
- для степени контакта: суммарное пятно контакта в % по длине и высоте зуба а также fx и fy для зубчатой передачи.
- для бокового зазора: Ews и а также для передачи с нерегулируемым расположением осей [3 таблица 6.14]
3.6 Определим числовые значения допусков.
Допуск на колебание измерительного межосевого расстояния за один оборот колеса Fi
Допуск на колебание длины общей нормали Fvw:
Fvw = 22 мкм [3 с.127 таблица 6.6]
Погрешность профиля зуба ff:
Допуск на колебание измерительного межосевого расстояния на одном зубе fi
для 6-степени fi"= 18 мкм
для 7-степени fi"= 25 мкм
Кинематическая точность при комбинировании степеней точности:
(Fi")комб = [ Fi" - fi" ]F + [fi"]f = (56 - 25) +18 = 49 мкм
Относительный размер суммарного пятна контакта [3 с.130 таблица 6.8]:
по высоте зуба - 50%
Допуск параллельности осей fx
Допуск параллельности осей fy [3 с.130 таблица 6.8]
Для оценки вида сопряжения необходимо определить длину общей нормали и предельные отклонения для нее:
Номинальное значение длины общей нормали:
W= m(1476(2Zw-1)+0.014Z)= 4·(1.476(23-1)+0.01425)= 3092 мм [3 с.118 таблица 6.1]
Zw = 0.111Z+0.5=0.11125+0.5= 3275 округляем до Zw= 4 ( [3] табл. 61)
Верхнее отклонение длины общей нормали - Ewms:
= 60 мкм для 6-ой степени точности при виде сопряжения C [3 с.131 таблица 6.10]
= 11 мкм [3 с.133 таблица 6.11]
Допуск на длину общей нормали:
Тw- зависит от вида сопряжения и допуска на радиальное биение (Fr) зубчатого колеса
Fr = 45 мкм [3 с.127 таблица 6.5]
Тw = 80 мкм [3 с.133 таблица 6.11]
Исполнительная длина общей нормали:
Предельные отклонения межосевого расстояния
[3 с.130 таблица 6.4]
Наименование контролируемого
Допускаемое значение мм
Применяемые средства измерения
Колебание длины общей нормали
Колебание измерительного межосевого расстояния
межцентромер для контроля измерительного межосевого расстояния
Суммарное пятно контакта %
Погрешность направления зуба
Нижнее отклонение длины общей нормали
Верхнее отклонение длины общей нормали
Отклонение от параллельности осей
3.7 Определение требований к точности заготовки зубчатого колеса:
В зависимости от степени точности по нормам плавности точность диаметра вершин зубьев по 8-му квалитету 108h8()
Допуск на радиальное биение по диаметру вершин
F da = 0.16 · d + 10 = 0.16 · 108 + 10 = 2728 мкм.
Расчётное значение допуска округляем [3 с.52 таблица 2.8] до F da = 30 мкм.
Допуск на торцевое биение:
торцовое биение базового торца на диаметре 0.75 d = 0.75 108 = 81 мм
Расчётное значение допуска округляем [3 с.53 таблица 2.9] до F Т = 10 мкм.
2.2.2 Шлицевое соед 1-1.doc
Для шлицевого призматического соединения по заданным условиям работы и наличию или отсутствию термообработки у втулки выбрать способ центрирования и назначить посадки по ГОСТ 1139. Построить схемы полей допусков по трем элементам (d D b) соединения. Вычертить эскизы поперечных сечений поверхностей шлицевого соединения в сборе вала и втулки.
2.2.1 Карта исходных данных
Наименование исходных данных
Значение исходных данных
Соединение работает:
с вращением в одну сторону
Вращение в одну сторону
Соединение вдоль оси:
Шлицы в отверстии втулки:
2.2.2 Определение параметров шлицевого соединения
z = 6-количество шлиц
d = 28 мм-внутренний диаметр шлиц
D = 32 мм-наружный диаметр шлиц
b = 7.0 мм-ширина шлиц
c = 0.4+0.2 мм-фаска
r = 0.2 мм-радиус закруглений
d1=26.7 мм - внутренний диаметр шлиц
Шлицевое соединение 6 x 28 x 32 относится к легкой серии ГОСТ 1139.
2.2.3 Выбор вида центрирования назначение посадок
В зависимости от условий работы механизма (отсутствие реверса) и закалки шлиц выбираем вид центрирования шлицевого соединения и назначаем посадки по ГОСТ 1139-80 [3 с.75].Выбираем центрирование по D
Центрирование по D применяется для незакаленных неподвижных соединений.
Соединение вдоль оси неподвижное назначаем посадки на элементы шлицевого соединения
по внутреннему диаметру d: - посадка предпочтительная
по внешнему диаметру D: - посадка предпочтительная
по ширине b: - посадка предпочтительная
Таким образом условная комплексная запись шлицевого соединения будет иметь вид:
2.2.4Схема расположения полей допусков в посадках:
d = - нецентрирующий элемент
Рисунок 2.3 - Схема расположения полей допусков по внутреннему диаметру
D=- центрирующий элемент
Рисунок 2.4 - Схема расположения полей допусков по внешнему диаметру D
b =-элемент дополнительного центрирования
Рисунок 2.5 - Схема расположения полей допусков по ширине b
Рисунок 2.6 - Эскиз шлицевого соединения.
3 Выбор унив. средств измерения 1-1.doc
Для одной детали (вал или отверстие) из соединений назначенных в разделе «Соединение гладких валов и отверстий» требуется выбрать средство измерения. По относительной точности изготовления (ITs тех) определить параметры разбраковки. Решить вопрос о значениях приёмочных границ и показать их на схеме полей допусков.
1 Карта исходных данных
Наименование исходных данных
значение исходных данных
Точность изготовления ITsтех
Исполнительный размер мм
Допуск на контролируемый размер мкм
Контролируемая поверхность
2 Выбор средств измерения и их анализ
Допуск на изготовление (IT) и допускаемая погрешность измерения () согласно [6 с.8 таблица 1]
Выбираем возможное измерительное средство [6 с.9-10 таблица 2]:
Головка пружинная микрокатор 5 ИГП (±015) КМД-3 кл ГОСТ28798
Предел измерения: 180 мм
Цена деления отсчётного устройства: 0.0005 мм
Предельная погрешность измерительного средства: D = 30 мкм
3 Оценка влияния погрешностей измерения
Относительная точность метода измерения [6 с.6]:
sмет = D2 = 32 =15 мкм – среднее квадратичное отклонение погрешности
измерения принятого средства измерения
4 Параметры разбраковки
Определяем следующие значения параметров разбраковки [6 с.11 рисунок 1]:
Необнаруженный брак (риск заказчика) m = 14 %
Ложный брак (риск изготовителя): n = 63 %
Вероятностная величина выхода размера за каждую границу поля допуска у неправильно принятых деталей:
с IT = 012 c = 012· IT = 012 · 13 = 156 мкм
Величины m (риск заказчика) и n (риск изготовителя) недопустимы необходимо ввести производственный допуск Тпр.
5 Расчет производственного допуска Тпр:
Тпр = IT – 2 · c = 13 – 2 · 156 = 988 мкм
6 Определение предельно допустимых размеров с учетом производственного допуска:
D min пр= 239935 + 0.00156 = 2399506 мм.
Рисунок 3.1 - Приемочные границы
7 Выбор средств измерения для арбитражной проверки
Средство измерения для арбитражной перепроверки производиться в зависимости от допускаемой погрешности при арбитражной проверки арб.
арб= 03 . = 0.3 · 4= 12 мкм.
Выбираем измерительное средство [6 с.9-10 таблица 2]:
Вертикальный оптиметр ИКВ (±01 по шкале) КМД-3 кл
Цена деления устройства: 0.0001 мм
Предельная погрешность измерительного средства: D =10 мкм
Метод измерения: относительный бесконтактный прямой.
1.1 Гладкое соединение 1-1.doc
На рис. представлен механизм привода вращательного движения
звеньев манипулятора промышленного робота. Он выполнен в виде комбинированного червячно-зубчатого редуктора.
Параллельно работающие зубчатые передачи из колес 20 и 12 соединены с шестерней 15 которая выполнена заодно со ступицей червячного колеса и установлена на вал 5 с гарантированным зазором по D3. Величина зазора оговорена заданием.
Обод червячного колеса 17 точно сцентрирован по D2 относительно ступицы колеса 15 закреплен болтами и двумя коническими штифтами. Передача крутящих моментов на валы 2 (или 14) производится через шлицевые соединения. Шлицы в отверстиях зубчатых колес 20 и 12 не закалены.
По D1 шестерня 4 имеет температуру окружающей среды +25ºС установлена на конце вала 2 по плотной посадке со шпонкой и закреплена шайбой с винтом.
Зубчатое колесо 12 связано с шестернёй 9 через торсион 14 который одним концом жёстко закреплён в отверстии вала. При монтаже редуктора производится закрутка торсиона 14 с последующей фиксацией его гайкой 8 которая соединена со ступицей шестерни 9.Гайка 8 имеет резьбу с мелким шагом и короткой длиной свинчивания. Зубчатая передача тихоходная но требуется обеспечить точность угла поворота. Зубчатые колёса стальные закаленные нагреваются до +35 ºС корпус выполнен из силумина и может нагреваться до +30 ºС.
Подшипники качения (поз.3;7;10;18) установленные на опорных шейках валов допускают перегрузку до 150% толчки и вибрации умеренные режим работы – нормальный.
Закладные фланцевые крышки (поз.6; 16 и др.) установлены в корпус 1 с гарантированным зазором и закреплены болтами с потайными головками (поз.13; 19; и др.). Резьба нормальной длины свинчивания.
Между торцами подшипника 7 и крышкой 6 предусмотрен гарантированный зазор необходимый для компенсации температурных деформаций (тепловой зазор). Величина заданного зазора обеспечивается расчетом размерной цепи.
Перечислим звенья размерной цепи:
A1 и A4 – монтажная высота (ширина) подшипников;
A2 – длина ступицы зубчатого колеса 15;
A3 – высота буртика вала;
A5 и A9 – высота буртиков крышек;
A6 и A8 – толщина прокладок;
A7 – размер корпуса 1.
Привод манипулятора промышленного робота.
Исходные данные к рисунку 1
Гладкие цилиндрические соединения
Шпоночное соединение
Условное обозначение
Резьбовое соединение
Размерная цепь размеры в мм
Нормирование точности гладких соединений
1 Соединение гладких валов и отверстий
Для гладких соединений номинальные размеры которых указаны в чертежах таблицах к чертежам и пояснениях назначить посадки по ГОСТ-25347 (с соблюдением предпочтительности) построить схемы полей допусков с указанием предельных отклонений предельных и средне вероятных зазоров (натягов). Для одного из заданных сопряжений рассчитать посадку по указанным в таблице предельным зазором (натягом). Назначение посадки указать на сборочном чертеже. Выполнить эскизы деталей входящих в соединения.
1.1 Подбор посадки методом подобия для соединения по D1
1.1.1Карта исходных данных Таблица 1.1
Наименование исходных данных
Значение исходных данных
Номинальный размер соединения и его значение
Название деталей входящих в соединение
Зубчатое колесо 4 и вал 2
Заданные характеристики
(для расчетного метода назначения посадок)мкм
Требования предъявляемые к работе соединения (из описания к чертежу)
зубчатое колесо 4установленно на конце вала 2 по диаметру D1 по плотной посадке со шпонкой
1.1.2 Назначение на соединение системы вала или отверстия
В соединение входит вал 2 и зубчатое колесо 4. Т.к. внутренние поверхности более сложны в обработке выбираем основное отверстие зубчатого колеса и соответственно систему отверстия СН.
1.1.3 Определение типа посадки
Соединение неподвижное (зубчатое колесо 4 установленное по плотной посадке) таким образом тип посадки – переходная.
1.1.4 Подбор вида сопряжения
Методом подобия назначаем посадку [3 с.26 таблица 1.6].
1.1.5 Выбор точности посадки
Рассматривая конструкцию и условия работы данного соединения назначаем посадку .Более вероятен зазоров чем натяг. Обеспечивает легкую сборку и разборку и точное центрирование. Применяется для сменных деталей которые требует дополнительного крепления.[1 с.31 таблица 1.6].
1.1.6 Расчет характеристик посадки
Расчет характеристик заключается в определении предельных размеров отверстия и вала [3с.8] определении величин зазоров (натягов) [3 с. 20].
Предельные размеры отверстия: мм
Предельные размеры вала: мм
Максимальный натяг: мм
Максимальный зазор: мм
Рисунок 1.1 - Схема расположения полей допусков вала и отверстия посадки
1.1.7 Технические требования на рабочие чертежи деталей
Значение шероховатости поверхностей сопрягаемых деталей определяем методом подобия. Для соответствующих квалитетов при нормальном уровне относительной геометрической точности (А) :
для вала: мкм округляем до стандартного мкм
для отверстия:мкм округляем до стандартного мкм
Донуск формы поверхности- цилиндричности назначаем по [1 таблица 2.3 и 2.9]:
для вала: мкм округляем до стандартного мкм
для отверстия: мкм округляем до стандартного мкм
Эскизы деталей показаны на рисунках
1.2 Подбор посадки методом подобия для соединения по D2
1.2.1Карта исходных данных
Обод червячного колеса 17 и ступица колеса 15
(для расчетного метода назначения посадок) мкм
Обод червячного колеса 17 точно сцентрировано по D2 относительно ступицы колеса 15 закреплен болтами и двумя штивтами
1.2.2 Назначение на соединение системы вала или отверстия
Втулка соед с валом по D2 и они закреплены коническими штифтами и болтами. Т.к. внутренние поверхности более сложны в обработке выбираем основное отверстие корпуса и соответственно систему отверстия СН.
1.2.3Определение типа посадки
Соединение неподвижное тип посадки –переходная посадка.
1.2.4 Подбор вида сопряжения
1.2.5 Выбор точности посадки
Рассматривая конструкцию и условия работы данного соединения назначаем посадку. Более вероятен зазоров чем натяг. Обеспечивает легкую сборку и разборку и точное центрирование. Применяется для сменных деталей которые требует дополнительного крепления.[1 с.31 таблица 1.6].
1.2.6 Расчет характеристик посадки
Выбранная посадка с отклонениями [3 с. 12-14 таблица 1.1-1.2]:
Предельные размеры вала: мммм
Рисунок 1.2 - Схема расположения полей допусков вала и отверстия посадки
1.2.7 Технические требования на рабочие чертежи деталей
Допуск формы поверхности- цилиндричности назначаем по [1 таблица 2.3 и 2.9]:
1.3 Назначение посадки расчетным методом для D3
Назначение посадки расчетным методом производится в следующей последовательности [3с.23].
1.3.1Карта исходных данных
Требования предъявляемые к работе соединения
(из описания к чертежу)
Устанавливается с гарантированным зазором по D3
1.3.2 Назначение на соединение системы вала или отверстия
В соединение входит шестерня 15 установленная на вал 5 по диаметру D3 выбираем основное отверстие корпус и соответственно систему отверстия СН.
1.3.2Расчет допуска посадки в соединении
1.3.4 Расчет относительной точности посадки
По номинальному размеру находим число единиц допуска [3 с. 12 таблица 1.1]:
Находим среднюю точность детали по числу единиц допуска посадки:
1.3.5 Определение квалитета вала и отверстия
Исходя из того что принимаем .что соответствует соответственно 8 квалитету для отверстия и 8 квалитету для вала.
1.3.6 Расчет характеристик посадки
Выбранная посадка с отклонениями [3 с. 12-14таблица 1.1-1.2]:
Расчет характеристик заключается в определении предельных размеров отверстия и вала [3 с.8] определении величин зазоров (натягов) [3 с. 20].
Минимальный зазор: мм
Проверка правильности расчета и подбора посадки:
Рисунок 1.3 - Схема расположения полей допусков вала и отверстия посадки
1.3.7 Технические требования на рабочие чертежи деталей
Эскизы деталей показаны на рисунках
2.1 Резьбовое соед 1-1.doc
1 Нормирование точности метрической резьбы
Расшифровать условное обозначение резьбы определить ряд предпочтительности заданной резьбы. Назначить посадку на резьбовое соединение. Построить номинальный профиль и схемы расположения полей допусков болта. По значениям погрешностей размеров элементов цепи определить приведённый средний диаметр дать для него схему и сделать заключение о годности резьбы.
1.1 Карта исходных данных
Наименование исходных данных
Значение исходных данных
Условное обозначение резьбы
№ позиции по чертежу
Наименование деталей
входящих в соединение
Исходные данные к расчёту годности резьбы:
d 2 изм = 5.3 мм Р n = 12 мкм a пр 2 = +10 мин a лев 2 = +12 мин
1.2 Определение ряда предпочтительности шага резьбы и степени точности
Резьба метрическая с номинальным диаметром болта d = 6 мм.
Шаг крупный Р = 1 мм.
По ГОСТ 8724 [3 с.103 таблица 5.1] определяем: ряд предпочтительности – первый.
Определим поля допусков резьбы по ГОСТ 16093 [3 с.110 таблица 5.8]
С учётом того что класс точности по ГОСТ 16093 резьбы средний (получил наибольшее распространение в машиностроении) и длина свинчивания нормальная то выбираем предпочтительные поля допусков:
Поле допуска резьбы болта: 6g
Поле допуска резьбы гайки: 6Н
1.3 Определение номинальных размеров резьбы
По ГОСТ 24705 [3 с.104 таблица 5.2] определяем основные размеры профиля:
Наружный диаметр резьбы: d = 6 мм
Внутренний диаметр: D1= d 1 = d – 2 + 0.917 = 6– 2 + 0.917 = 4.917 мм
Средний диаметр: D2 = d 2 = d – 1 + 0350 = 6 - 1 + 0350 = 5.350 мм
Диаметр по дну впадин: d 3 = d – 2 + 0773 = 6 - 2+0773 = 4.773 мм
Теоретическая высота витка: Н = 0.866 · Р = 0.866 · 1 = 0.866 мм
Рабочая высота витка: Н 1 = 0.541 · Р = 0.541 · 1 = 0.541 мм
Радиус закругления впадин: R = 0.14 · Р = 0.14 · 1 = 0.14 мм
Рис.2.1.1 - Профиль резьбы
1.4 По ГОСТ 16093 определяем поля допусков и значение отклонений
1.5 Определение приведённого диаметра резьбы:
По заданным значениям шага Р и угла наклона a2 боковых сторон профиля подсчитываем приведённый средний диаметр резьбы.
d 2 прив. = d 2 изм. + f a + f p
Погрешность половины угла профиля:
Диаметральная компенсация погрешностей половины угла профиля f a
f a = 0.36 Р a2 = 0.36 1 11 = 3.96 мкм.
Диаметральная компенсация погрешностей по шагу на длине свинчивания f p
f p = 1.732 Рn = 1.732 12 = 20.784 мкм.
d 2 прив. = d 2 изм. + f a + f p = 5.3+ 0.00396 + 0.020784 = 5.314744 мм.
1.6 Заключение о годности:
Условие годности резьбы по среднему диаметру для болта
Таким образом резьба по среднему диаметру для гайки годна
Рисунок 2.1.2 - Расположения полей допусков по среднему диаметру болта
Рисунок 2.1.3 - Расположение полей допусков по профилю резьбы болта
Рисунок 2.1.4 - Расположение полей допусков резьбы гайки
1.4 Размерные цепи 1-1.doc
Для сборочной единицы заданного варианта размерной цепи решить "прямую задачу" по методу максимума-минимума (методу полной взаимозаменяемости) т.е. по заданным предельным размерам замыкающего звена назначить предельные отклонения на составляющие звенья номинальные размеры которых установлены.
4.1 Исходные данные и результаты поэтапных и окончательных расчетов представлены в табличной форме
мм - максимальное значение замыкающего звена.
мм - минимальное значение замыкающего звена.
Таблица 1.9 - Сводная таблица к расчету прямой и обратной задачи
Обозначение размеров размерной цепи A j
Номинальный размер звена мм
Принятые значение звеньев размерной цепи
назначения полей допусков по расчетному значению am
после согласования величин допусков звеньев
4.2 Схема размерной цепи
Составляем схему размерной цепи а также определяем увеличивающие и уменьшающие звенья методом замкнутого потока.
Рисунок 1.12 - Схема размерной цепи
- уменьшающие звенья
- увеличивающие звенья.
4.3 Определение номинального размера замыкающего звена.
4.4. Определение допуска замыкающего звена
4.5. Определение отклонений замыкающего звена
4.6. Определение среднего квалитета размеров без допусков
Принимаем 13 квалитет для вала и отверстия табличные значения которых равны: IT13 =250.
Если то на одном из звеньев уменьшаем квалитет на единицу.
Если то на одном из звеньев увеличиваем квалитет на единицу.
Результаты расчётов сводим в таблицу смотри таблицу 1.9.
Назначение стандартных полей допусков
Для размеров охватывающих поверхностей отклонения назначаем как для основного отверстия (Н) т.е. в плюс; для размеров охватываемых поверхностей отклонения назначаем как для основного вала (h) т.е. в минус; для остальных назначаем симметричные отклонения т.е. ±IT2
4.7 Определение допуска замыкающего звена
4.8 Определение верхнего отклонения замыкающего звена
4.9 Определение нижнего отклонения замыкающего звена
Предельные отклонения замыкающего звена по расчётам не соответствуют заданным:
Существует не соответствие в значение расчётных отклонений замыкающего звена над заданными поэтому для согласования этих значений вводим корректировочное отклонение звена звена компенсатора т.е. определение его отклонения из условия мм.
4.10 Определение нижнего отклонения звена компенсатора
4.11 Определение верхнего отклонения звена компенсатора
4.12 Отклонение звена А8 приводим к стандартному виду
Рекомендуемые чертежи
- 01.07.2014