Механизм компрессора двухпоршневой горизонтальный




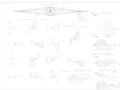
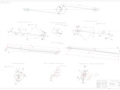
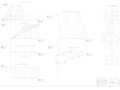
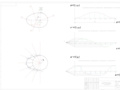
- Добавлен: 24.01.2023
- Размер: 1 MB
- Закачек: 0
Описание
Состав проекта
![]() |
![]() |
![]() ![]() ![]() ![]() |
![]() ![]() ![]() ![]() |
![]() ![]() ![]() |
![]() ![]() ![]() |
![]() ![]() ![]() |
![]() ![]() ![]() ![]() |
![]() ![]() ![]() ![]() |
![]() ![]() ![]() ![]() |
Дополнительная информация
Рдуктор А2.dwg

Карта распределения скоростeй
План угловых скоростей
Нарезание зубцов колеса методом обкатки q*;модуль m=14; угол профиля α=20; диаметр делительной окружности колеса d=126; z=9; x0=6
Угловые скорости зубчатых колес
Кинематический анализ зубчатого механизма
Компрессор А1.dwg

Планы скоростей механизма
Планы ускорений механизма
График скорости ползуна С
График ускорения ползуна С ползуна Д
График поворота шатуна АС ВД
График угловой скорости шатуна СА ВД
График перемещения ползуна
Структурный и кинематический анализы главного механизма
Ведомость курсового.doc
кулачкового механизма
Пояснительная записка
Курсовой проект ТММ .doc
кулачкового механизма
Пояснительная записка
В данном курсовом проекте производится анализ механизма компрессора двух поршневого горизонтального.
В курсовом проекте представлены следующие разделы: структурный и кинематический анализы силовой и динамический анализы механизма компрессора кинематический анализ кулачкового механизма и кинематический анализ сложного зубчатого механизма.
Курсовой проект состоит из пояснительной записки и графической части. В пояснительной записке были детально описаны методы построения планов скоростей ускорений диаграмм для всех разделов.
В состав графической части входят 5 чертежей:
Кинематический анализ механизма компрессора двух поршневого горизонтального (формат А1);
Кинематический анализ кулачкового механизма
Кинематический анализ сложного зубчатого механизма (формат А2):
Силовой анализ механизма компрессора двух поршневого горизонтального (формат А1):
Динамический анализ механизма. Подбор маховика. (формат А1).
Пояснительная записка и чертежи были выполнены согласно всех ГОСТов.
Структурный и кинематический анализ главного механизма
1 Структурный анализ механизмастр.7
2 Построение плана положенийстр.8
3 Построение планов скоростейстр.8
4 Построение планов ускоренийстр.9
5 Кинематический анализ методом построения диаграмм стр.11
6 Сравнение результатов кинематического исследования выполненного графическим и графоаналитическим методамистр.13
Синтез кулачкового механизма
1 Исходные данныестр.14
2 Построение кинематических диаграммстр.14
Кинематический анализ сложного зубчатого механизма
1 Исходные данныестр.15
2 Аналитический методстр.15
3 Нарезание зубцов колеса методом обкаткистр.17
Силовой анализ главного механизма
1 Определение внешних сил сил и моментов инерциистр.19
2 Силовой анализ механизма без учета сил трения стр.20
3 Проверка по теореме Н.Е. Жуковскогостр.21
4 Силовой анализ механизма с учетом сил трениястр.22
Динамический анализ механизма
1 Основные задачи динамического анализастр.24
2 Определение приведенного момента сил сопротивления для всего кинематического цикла главного механизма.стр.24
3 Определение работы сил сопротивления и работы движущих силстр.24
4 Решение уравнения движения машинного агрегатастр.24
5 Определение приведенного момента инерции для 12 положений механизма стр.25
6 Определение момента инерции маховика по методу Витенбауэрастр.25
7 Определение геометрических размеров маховикастр.25
8 Определение угловой скорости после установки маховикастр.26
Список использованной литературыстр.27
Теория механизмов и машин (ТММ) есть одной из основных машиностроительных дисциплин. Она посвящена изучению основных методов изучения механизмов и машин и проектированию их схем.
К основным вопросам которые изучает ТММ относятся:
- изучение строения (структуры) механизмов;
- определение положений механизмов и траекторий описуемых отдельными точками;
- определение скоростей и ускорений отдельных точек;
- анализ и проектирование разных механизмов (зубчатых кулачкових);
- определение разных сил (внешних реакций трения инерции) действующих на механизм;
- изучение энергетического баланса машин ( к.п.д.);
- изучение действительного закона движения машин под действием заданных сил;
- изучение способов регулирования скорости хода машины;
- изучение способов уравновешивания сил инерции в машинах и т. д.
Относительно этих вопросов теория механизмов и машин это наука которая изучает строение кинематику и динамику механизмов и машин.
Механизмы которые входят в состав машины разные. По функциональному назначению механизмы машины делятся на следующие виды:
а) механизмы двигателей и преобразователей:
механизмы двигателей выполняют преобразование разных видов энергии в механическую работу;
механизмы преобразователей выполняют преобразование механической работи в другие виды работы;
б) передаточные механизмы которые выполняют передачу движения от двигателя к технологической машины или рабочего органа;
в) рабочие механизмы которые непосредственно влияют на обрабатываемую среду или объект;
г) механизмы управления контроля и регулирования выполняя управление технологическим процессом контроль и т.п.;
д) механизмы автоматического счета взвешивания и упаковывания установлены в машинах которые выпускают массовую штучную продукцию.
Академик И.И.Артоболевский класифицируя механизмы разного назначения разделил их по структурним признакам на следующие виды: весы зубчатые червячные фрикционные кулачковые винт-гайка и др. отдельно комбенированные.
Механизмы бывають плоские и пространственные. В основном применяют плоские механизмы все точки которых двигаются в одной или нескольких параллельных плоскостях.
Зубчатые механизмы используются для изменения параметров вращательного движения а также для преобразования вращательного движения в прямолинейное.
Рис.1 Кинематическая схема компрессора
Кинематический анализ главного механизма
1 Структурный анализ механизма
Рис.2 Структурная схема механизма
Степень подвижности механизма
Где количество звеньев =6; количество низших пар =7; количество высших пар =0.
Механизм двухпоршневого насоса состоит из 6 звеньев:
кривошип ОА и ОВ; шатуны АС и ВД; ползуны (поршни Д и С); стойка.
Звенья 1-5 –подвижные 6- неподвижное звено.
Звенья механизма образуют 7 кинематических пар из которых 5 вращательных и 2 поступательные. На рис.2 изображена структурная схема механизма с разбитием на структурные группы Асура и начальный механизм. Стойка 6 и кривошип 1 – 1-го класса.
Две группы Ассура – шатун 2 ползун 4 и шатун 32 ползун 5.
Структурная формула насоса.
II (2 – 4) I (6 - 1) II (3 – 5)
Механизм относится к механизмам II класса по классификации И.И.Артоболевского.
2 Построение планов положений
В курсовом проекте рекомендуется план положений изображать в масштабе М 1:1 следовательно масштабный коэффициент будет равен:
Начальное положение механизма (А0В0) затем поворачивая кривошип по часовой стрелке на 300 (строится 12 положений) обозначаются точки А1 А2 и т. д. и откладывается эксцентриситет е на направляющих находим положение поршня В1 В2 и т. д. Соединяя точки А1 с центром О и с точками В1 получаем план положений.
3Построение плана скоростей:
Находим скорость точки А:
От произвольной точки P откладываем отрезок РА=42 мм перпендикулярно кривошипу ОА в сторону вращения. Масштабный коэффициент плана скоростей равен:
где параллелен направляющим а АС
Проводя через полюс Р прямую параллельную направляющим а через точку А – прямую перпендикулярную шатуну АС на их пересечении получаем точку c. В построении показываем векторы и . Изображаем вектор скорости центра тяжести шатуна АC (вектор РS) где S середина АC(AS=SC).
С помощью плана скоростей находим :
Для положения Р4 и Р7 находим:
Проставляем на чертеже для положения Р4 направление . Для этого вектор мысленно переносим в точку С и относительно точки А имеем направление против хода часовой стрелки.
4 Построение плана ускорений для положений Р4 и Р7
Находим ускорение точки А:
От произвольной точки p4 откладываем отрезок (р4а) = 42 мм параллельно кривошипу в направлении от А к О. Тогда масштабный коэффициент плана ускорения будет равен:
Ускорение поршня С определяется выражением:
где параллельно направляющим
параллельно СА (от точки С к точке А)
Отрезок изображающий это ускорение будет равен:
Решаем уравнение (1) на плане ускорений для чего от точки а откладываем =151 мм для положения Р4 и для положения Р7 - =453мм в направлении от С к А (параллельно шатуну АС) к концу которого проводим линию перпендикулярную шатуну АС а через полюс р1 проводим прямую параллельную направляющим. В точке пересечения этих прямых будет находиться точка С. Проставляем стрелки векторов уравнения (1).
С помощью построенного плана ускорений находим:
=258.9 042=616.4 с-2
На чертеже проставим направление для чего вектор мысленно перенесем в точку С и относительно точки А получаем направление (против хода часовой стрелки).
Результаты расчета сводим в таблицу:
5 Кинематический анализ методом построения диаграмм
Диаграммы строятся для 12 положений механизма которые были изображены на плане положений. Полный оборот кривошипа ОА соответствует одному кинематическому циклу.
Рассмотрим построение диаграммы перемещений ползуна С S=f(φ). Проводим координатные оси S и φ. На оси φ откладываем 12 равновеликих отрезков 0-1 1-22-3 и т.д. соответствующих углу поворота кривошипа на 112 часть оборота (300). Через точки 1 2 3 и т.д. проводим ординаты и откладываем на них отрезки равные координатам точки С – SС в соответствующих положениях отсчитываемых от крайнего левого положения точки С. Соединяя полученные точки плавной кривой линией изображаем диаграмму SС= f(φ). В этой же координатной системе строим диаграмму SД= f(φ) отсчитывая перемещение ползуна Д тоже от крайнего правого положения.
При равномерном вращении кривошипа угол его поворота φ пропорционален времени. Поэтому полученная диаграмма S=f(φ) является одновременно диаграммой зависимости перемещения ползуна от времени S= f(t). Разница будет лишь в масштабах по оси абсцисс.
Масштаб перемещений S =0002 ммм масштабу плана положений механизма l потому что отрезки изображающие перемещение перенесены с плана без изменений.
Масштаб углов φ равен
где - отрезок (мм) по оси φ изображающий полный оборот кривошипа ОА (2).
Масштаб времени t диаграммы равен:
где T – период одного оборота кривошипа который определяется по формуле:
Таким образом для получения масштаба времени t достаточно помножить масштаб угла поворота φ на величину обратную угловой скорости кривошипа 1=100 (с-1).
Построение кривых V=f(φ) и а=f(φ) выполняется способом графического дифференцирования (методом хорд). При этом масштабные коэффициенты диаграмм определяются по формулам:
где Н и Н1 – полюсные расстояния диаграмм соответственно мм. Принимаем Н=22150мм Н1=11075 мм.
=0002*7000523*22150=012 м*с-1мм
=012*7000523*11075=14.5 м*с-2мм
Далее следует построить диаграмму угловых перемещений шатунов АЕ и АВ. Угловое перемещение измеряют в градусах отсчитывая его от направляющих ОЕ и ОВ. Масштабный коэффициент удобнее представлять в воспользовавшись для перевода из градусов в радианы известной формулой : 1 рад = . Принимаем α=00174.
Так как то достаточно выполнить графическое дифференцирование предыдущей диаграммы =f(t) используя при этом метод хорд. Масштабный коэффициент определится по формуле:
где Н2 – полюсное расстояние диаграммы принимаем Н2=22150 мм.
=00174 *7000523*22150=105 с-1мм
6Сравнение результатов кинематического исследования выполненного графическим и графоаналитическими методами
В ходе кинематического исследования с помощью диаграмм были получены значения скоростей ускорений и угловых скоростей ползунов С и Д. Эти же кинематические параметры были определены с помощью планов. Поэтому целесообразно сравнить их и сделать вывод о правильности и точности проведения анализа. Результаты сравнения сводим в таблицу.
Расхождение результатов не превышает 5%.
Кулачковый механизм – это механизм состоящий из ведущего звена криволинейной формы (кулачка) и выходного звена (толкателя) которые образуют между собой высокую кинематическую пару. Поэтому при помощи кулачкового механизма можно легко выполнить любой заранее заданный закон движения ведомой цепи. Это основное преимущество механизма. Недостатком данных конструкций является необходимость замыкать кинематичные пары (кулачок - толкатель). Недостатком является сложность изготовления кулачка.
На формате А2 изображаем кинематическую схему кулачкового механизма.
Используя метод инверсии (метод обратного движения) построил закон движения толкателя S=f(φ) график S=f(φ) с масштабным коэффициентом =1 мммм. Этот метод заключается в том что вокруг неподвижного кулачка вращается весь механизм со стойкой. Точка вращения – ось вращения кулачка. Угловая скорость равна угловой скорости кулачка но с противознаком ( = - '). В данном проекте рассмотрен кулачек с плоским толкателем.
2 Построение кинематических диаграмм
Таблица перемещения толкателя.
Методом графического дифференцирования построил графики скорости =58651мм*смм и ускорения =34399 мм*с2мм толкателя.
Кинематический анализ зубчатого механизма
2 Аналитический метод
Определяем радиусы делительных окружностей по формуле:
Строим кинематическую схему зубчатого механизма с масштабным коэффициентом l=1мммм.
Строим картину распределения скоростей с масштабным коэффициентом
где =r6*6; [Р5`6Р'5`6]=2.26 мм.
=45502.26=2013 мм*с-1мм
Строим план угловых скоростей с масштабным коэффициентом =[OH]*l=20131*30=67.1 радс.
Определяем погрешность расчета
=(70-69784)70=0003 %
Определяем передаточное отношение редуктора i18. Для определения передаточного отношения планетарного редуктора используем формулу Виллиса:
- передаточное отношение от колеса 5` к колесу 8 при неподвижном колесе 7.
- - передаточное отношение от колеса 5` к колесу 7 при неподвижном колесе 8.
3 Нарезание зубцов колеса методом обкатки
модуль m=14; угол профиля α=20; диаметр делительной окружности колеса d=126
Метод обкатки – наиболее распространенный способ производства эвольвентных профилей зубчатых колес. Сущность метода обкатки заключается в том что в процессе нарезания зубцов имитируется зацепление заготовки колеса с режущим инструментом. Основное преимущество метода обкатки – возможность нарезания зубчатых колес с разными геометрическими параметрами и разным числом зубцов одним инструментом определенного модуля. Благодаря прямобочному профилю режущего ребра рейки достигается высокая точность изготовления ее и колес упрощается переточка режущих граней рейки. Точность обработки профилей зубцов обеспечивает стойкость работы зацепления.
МПР – модульная прямая инструментальной рейки – средняя прямая на которой толщина зуба равна ширине впадин и составляет половину шага.
ДПР – делительная прямая рейки – прямая касательная к делительной окружности колеса.
Делительная окружность колеса – окружность на котором шаг зацепления равен шагу инструментальной рейки.
Шаг рейки постоянный для любой прямой которая параллельна модульной прямой в зоне прямолинейного профиля зуба поэтому заготовку можно установить так чтобы делительная окружность колеса касалась к одной из таких прямых которая и будет делительной.
Если делительная окружность колеса касается модульной прямой рейки (МПР) то профиль зуба будет нормальным (нулевым или некорректированным). У такого колеса высота головки зуба равна модулю а толщина зуба (по делительной окружности) равна ширине впадин и одновременно половине шага рейки.
Корректированными или выправленными называют зубчатые колеса которые нарезаны смещенной инструментальной рейкой. При этом размеры и конфигурация зубцов эвольвентного профиля отличается от нормальных. Корректирование зубчатых колес выполняется с целью уменьшения габаритов улучшения качества зацепления устранения подреза ножки зуба увеличения коэффициента перекрытия уменьшение износа повышения крепости зуба и с целью получения требуемого межосевого расстояния.
Сдвиг рейки от центра колеса называют положительным сдвигом а в направлении к центру – негативным.
Количество нарезаемых зубцов:
Для устранения подрезания зубцов находим относительный сдвиг:
Радиус делительной окружности
Радиус основной окружности
Радиус окружности выступов
Радиус окружности впадин
=43962+2*0*036=2198мм
=43962+2*7*036=2702мм
=43962+2*10*036=2918мм
=43962+2*(-10)*036=1478мм
Кинетостатический (силовой) анализ механизма
Задачей силового исследования является определение реакций в кинематических парах механизма находящегося под действием внешних сил. Закон движения при этом считается заданным. Для того чтобы ведущее звено двигалось по заданному закону необходимо к нему приложить уравновешивающую силу (или уравновешивающий момент) которая уравновесит все внешние силы и силы инерции. Определение уравновешивающей силы или уравновешивающего момента наряду с определением реакций в кинематических парах также является задачей силового исследования механизма.
Для осуществления силового расчета кинематической цепи необходимо чтобы она была статически определенной т. е. чтобы число уравнений которое можно составить для кинематической цепи было равно числу неизвестных. Такой статически определимой цепью является группа Ассура – кинематическая цепь с нулевой подвижностью.
Силовой расчет ведется в порядке обратном кинематическому исследованию т. е. сначала ведется расчет группы Ассура наиболее удаленной от ведущего механизма.
1.Определение внешних сил и сил моментов инерции.
1.1.Определяем массу звеньев и их вес:
Погонная единица массы q =15 кгм
G1 = m1 * g = 1.8*10 =18 H;
G2 = m2 * g = 6.3*10 =63 H;
G3 = m3 * g = 6.3*10 =63 H;
Коэффициент массы поршня с = 1.5
m4 = c * m2 = 1.5*6.3= 9.45 кг;
G4 = m4 * g = 9.45*10 =94.5 H;
m5 = c * m3 = 1.5*6.3= 9.45 кг;
G5 = m5 * g = 9.45*10 =94.5 H;
1.2. Определяю силы и моменты инерции:
Fu2 = m2 * as2 = 6.3 * 186.9= 1177.47 H
Fu3 = m3 * as3 = 6.3 * 186.9= 1177.47 H
Fu4 = m4 * a4 = 9.45 * 126 = 1190.7 H
Fu5 = m5 * a5 = 9.45 * 126 = 1190.7 H
MU2 = = 6.3 * 0422 * 616.4 12 = 57.08 Н*м;
MU3 = = 6.3 * 0422 * 616.4 12 = 57.08 Н*м;
Изображаю MU2 дуговой стрелкой противоположной и MU3 дуговой стрелкой противоположной 3.
1.3.Нахожу силу полезного сопротивления:
С4 = 0.0867 м – перемещение поршня в четвертом положении.
Fпс = В * С4 = 400000 * 0.0867= 34680 Н
2.Силовой анализ механизма без учета сил трения.
2.1.Силовой анализ группы Асура звеньев 2 и 4.
– * AC * + G2*hG2* – MU2 – FU2*hFu2* = 0
= (– G2*hG2* + MU2 + FU2*hFu2*)АС;
= (-63*104.3*0002+57.08 +1177.47 *80.6*0002)042 = 556.53 H
Знак « + » указывает на правильное направление вектора
Принимаю масштабный коэффициент F= 100 Hмм
От точки О откладываю все известные силы последовательно. Через начальную точку О провожу прямую параллельную а через конечную точку - прямую параллельную реакции . Там где закончится - начнется . Проверяю – силовой многоугольник должен быть замкнутым.
Из плана сил нахожу:
Геометрическая сумма и = .
2.2.Силовой анализ группы Асура звеньев 3 и 5.
* lВД * – G3*hP3* – MU3 – FU3*hRu3* = 0
= (G3*hG3* + MU3 + FU3*hFu3*)ВД;
= = (63*104.3*0002+57.08 +1177.47 *80.6*0002)042 = 619.11 H
Знак « + » указывает на правильное направление вектора .
Принимаю масштабный коэффициент сил= 100 Hмм
От точки О откладываю все известные силы последовательно.
Через начальную точку О провожу прямую параллельную а через конечную точку – прямую параллельную реакции . Там где закончится – начнется . Проверяю – силовой многоугольник должен быть замкнутым.
2.3.Силовой анализ начального механизма:
На отдельно взятый кривошип прикладываю известные силы (G1 R21 R31) и неизвестные (FУР и R61). Силу FУР прикладываю перпендикулярно кривошипу в сторону его вращения. Силы R21 R31 одинаковы по величине и обратные по направлению соответствующим силам R12 и R13.
Уравнение моментов сил действующих на кривошип относительно точки О.
План сил ведущего звена начинаю от произвольной точки О откладываю последовательно векторы сил FУР G1 R21 R31. соединив вектор R31 с точкой О получил неизвестную реакцию R61.
3.Проверка по теореме Н.Е. Жуковского.
Для определения FУР методом Жуковского строю повернутый на 90 план скоростей и загружаю его в соответствующих точках силами инерции силами веса и движущей силой.
Момент сил инерции представляю в виде пары сил приложенных в точках А С Д и В и этими силами загружать рычаг Жуковского. Величина сил определяется по формуле:
Составляю уравнение моментов всех сил относительно полюса повернутого плана скоростей:
Размеры плеч измеряю в «мм» непосредственно с чертежа рычага Жуковского.
Сравним величину движущей силы найденной по методу Жуковского и по методу разбиения на группы Асура:
По методу Жуковского:
Определяем погрешность:
4.Силовой анализ механизма с учетом сил трения.
Выполняется аналогично только каждая группа Ассура и начальный механизм дополнительно нагружаются силами и моментами трения. Величины сил трения определяются по формуле:
где коэффициент трения в поступательной паре зависит от пары работающих материалов состояния поверхности условий смазки и проч;
- реакция в поступательной паре предварительно определенная без учета сил трения
Сила трения направлена в сторону противоположную относительному движению звена.
Возникающий во вращательной паре момент трения рассчитываю по формуле:
где r - радиус цапфы мм;
Прикладываю найденные моменты в направлениях противоположных относительному вращению звеньев.
– * AC * + G2*hG2* – MU2 – FU2*hFu2* –Мтр24 – Мтр21 = 0
= (– G2*hG2* + MU2 + FU2*hFu2* + Мтр24 + Мтр21)АС;
= (-63*104.3*0.002+57.08 +1177.47 *80.6*0.002+89.4+87.3)0.42 = 977.2 H
Так как сила трения мала тогда ей можно пренебречь следовательно можно принять:
* lВД * – G3*hG3* – MU3 – FU3*hFu3* – Мтр31 – Мтр35 = 0
= (G3*hP3* + MU3 + FU3*hRu3*+Мтр31 + Мтр35)ВД;
= = (63*104.3*0002+57.08 +1177.47 *80.6*0002+87.683+89.66)042 = 1041.35 H
Динамический анализ механизма. Подбор маховика.
1. Основные задачи динамического анализа
В ходе динамического анализа определяем приведенные моменты сил сопротивления и движущих сил приведенные моменты инерции а также решается основное уравнение движения и определяем момент инерции маховика по методу Витенбауэра.
Исходными данными являются кинематические параметры определенные в ходе кинематического исследования.
2. Определение приведенного момента сил сопротивления для всего кинематического цикла главного механизма.
Находим Мпс для 12 положений и результаты заносим в таблицу 1.
По результатам табл.1 строим график зависимости приведенного момента сил сопротивления от угла поворота кривошипа Мпс=f(j)
mj = 0035 радмм ; mм = 40
3. Определение работы сил сопротивления и работы движущих сил.
Определяем работу сил сопротивления методом графического интегрирования
mА=mмmj[ОН] Джмм. mА= 40 · 0035 · 50 = 70 Джмм
Приняв момент движущих сил постоянным учитывая что при установившемся режиме работы машинного агрегата в начале и в конце цикла работа движущих сил равна работе сил сопротивления. На построенном графике работы сил сопротивления строим график работы движущих сил.
Мдв=[ОР] mм = 253 · 40 = 1012 Н·м
4. Решение уравнения движения машинного агрегата.
5 Определение приведенного момента инерции для 12 положений механизма
Результаты вычислений заносим в табл 2.
Строим график зависимости приведенного момента инерции как функция от угла поворота кривошипа.
6. Определение момента инерции маховика по методу Витенбауэра.
Строим с использованием графиков DТ как функция от j и пр как функция от j кривую Витенбауэра т.е. зависимость DТ=f (пр).
Опреляем тангенсы углов наклонов касательных соответственно max и min угловым скоростям ведущего звена.
7. Определение геометрических размеров маховика.
Учитывая что маховик представляет собой колесо с массивным ободом его момент инерции :
Предварительно задаемся Дср конструктивно:
Дср=5rкрив.= 5 012 =06 м
Пренебрегая массой ступицы и спиц определяем массу через размеры маховика:
m=gbh Дср где g=7·103кгм3-удельный вес
Задаемся соотношением b и h
Проверяем не получился ли у нас маховик слишком толстым или слишком вытянутым в диаметральном направление.
b=(13÷15) Дср= (02÷012)м
Условие выполняется.
h=075 b = 075 0158 = 0118м.
8. Определение угловой скорости после установки маховика.
Реальную угловую скорость кривошипа определяем для 12 положений по формуле:
где: Iмах= 2212 кгм2
w2 max=wср2(1+)= 702 (1+129) = 506897
DТ max- координаты точки касания прямой проведенной под углом ymax с кривой Витенбауэра
Результаты определения угловой скорости заносим в таблицу
По результатам расчетов строим график изменения w кривошипа: mw = 1
Список использованной литературы.
Артоболевский И.И. Теория механизмов и машин. – М.: Наука. 1975. – 638 с.
Теория механизмов и машин: Учебн. для Вузов. Под. ред. К.В. Фролова М.: Высш. шк. 1987. – 496 с.: ил.
Методичні вказівки до виконання курсового проекту з дисципліни «Теорія механізмів і машин» (для студентів заочної форми навчання спеціальності 7.090220 «Обладнання хімічних виробництв і підприємств будівельних матеріалів»). Уклад.: О.Г. Архипов Е.М. Кравцова Н.. Галабурда. – Сєвєродонецьк: Вид-во СТ 2006. – 12 с.
Титульный лист.doc
Восточноукраинский национальный университет
имени Владимира Даля
ПОЯСНИТЕЛЬНАЯ ЗАПИСКА
к курсовому проекту по дисциплине "Теория механизмов и машин
тема проекта: Механизм компрессора
двух поршневой горизонтальный
Силовой анализ А1.dwg

Планы скоростей механизма
Планы ускорений механизма
График скорости ползуна С
График ускорения ползуна С ползуна Д
График поворота шатуна АС ВД
График угловой скорости шатуна СА ВД
План ускорения механизма
Проверка по теореме Жуковского
План сил начального механизма
Кинематический анализ главного механизма
Динамический анализ А1.dwg

Планы скоростей механизма
Планы ускорений механизма
График изменения кинетической энергии
График приведенного момента инерции
График угловой скорости
Структурный и кинематический анализы главного механизма
Кулачок А2.dwg

Кинематическая диаграмма скоростeй толкателя
Кинематическая диаграмма ускорений толкателя
Кинематический анализ кулачкового механизма