Кран стреловой на неподвижной опоре




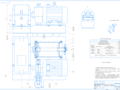
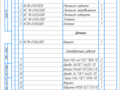
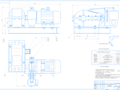
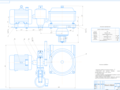
- Добавлен: 25.01.2023
- Размер: 779 KB
- Закачек: 0
Описание
Кран стреловой на неподвижной опоре
Состав проекта
![]() |
![]() |
![]() ![]() ![]() |
![]() |
![]() |
![]() ![]() ![]() ![]() |
![]() ![]() ![]() ![]() |
![]() |
![]() |
![]() |
![]() ![]() ![]() |
![]() ![]() ![]() ![]() |
![]() ![]() ![]() |
![]() ![]() ![]() ![]() |
![]() ![]() ![]() ![]() |
![]() ![]() ![]() |
Дополнительная информация
Спецификация механизм передвижения.doc
Шайба 32 ГОСТ 11371-78
Подшипник ГОСТ 5720-75
Электродвигатель МТН 312-8
Ходовые колеса К2РН-710
общий.cdw

Мех передв мих.cdw

Скорость вращения обмин
Механизм передвижения
Неуказанные предельные отклонения размеров
Подшипниковые узлы заполнить закладной смазкой
долгодействующей МПИ
Защитное заземление электрооборудования произвести согласно
Правил устройства электрооборудования"
Допуск радиального биения рабочей поверхности тормозного
шкива (после установки) относительно оси вращения 0.1мм
Схема запасовки каната
Техническая характеристика
Технические требования
мих.doc
Брянский государственный
технический университет
“Строительная механика”
Расчет металлической конструкции стрелы .3
Расчет металлоконструкции крана по первому расчетному случаю нагрузок 5
Проверка сечения по второму расчетному случаю 7
Расчет сварных швров .10
Расчет металлической конструкции моста
Расчёт металлоконструкции производится на статическую прочность исходя из двух основных расчетных случаев:
) Вертикальные нагрузки на кран при подъеме свободно лежащего груза
) Горизонтальные нагрузки при резком торможении крана с поднятым грузом
Мост сваривается из листов стали ВСт.3 [sи]= 210(МПа).
Основная расчетная зависимость имеет вид
где Ми – изгибающий момент;
γс – коэффициент условий работы
R – сопротивление материала конструкции.
Необходимую высоту балки в зависимости от пролёта определяем по формуле
Принимаем высоту балки H = 600(мм).
Для достижения достаточной жёсткости при кручении ширина балки по осям вертикальных листов выбирается из условий
Принимаем B = 250(мм).
Назначаем остальные размеры сечения:
Исходя из принятых размеров определяем основные расчётные характеристики сечения СТРЕЛЫ крана.
Верхний пояс: F1 = 0.6 25 = 15 см2
Нижний пояс: F2 =06 25 = 15 см2
Вертикальная стенка: F3 =2 06 588 = 7056 см2
Площадь сечения балки: см2
Статический момент элементов сечения относительно оси х (у основания сечения):
Статический момент всего сечения:
Координата центра тяжести
Момент инерции относительно горизонтальной оси х
Общий момент инерции:
Момент сопротивления сечения относительно горизонтальной оси х
Момент инерции относительно вертикальной оси y
Момент сопротивления сечения относительно горизонтальной оси y
Расчет металлоконструкции крана по первому расчетному случаю нагрузок (Вертикальные нагрузки на кран при подъеме свободно лежащего груза).
Нагрузками действующими на мост являются: масса поднимаемого груза масса тележки собственная масса балки и дополнительно силы инерции при подъёме и торможении груза.
Так как мы располагаем данными по массам элементов крана моста тележки механизма передвижения и механизма подъёма то приблизительно подсчитываем эти массы.
Масса моста = 3620кг;
Масса тележки = 700кг;
Масса механизма передвижения= 500кг;
Крюковая подвеска = 214кг;
Динамический коэффициент при подъёме груза с подхватом
где V = 014(мс) – скорость подъёма груза;
x = 15 – поправочный коэффициент учитывающий приближённость расчёта.
где yСТ – статический прогиб моста от веса поднимаемого груза в месте его приложения;
СМ – коэффициент жёсткости моста.
где E = 21×1011(Па) – модуль упругости каната.
f = 85.5(мм) – площадь поперечного сечения всех проволочек каната;
EK – модуль упругости.
Коэффициент жёсткости моста
Значение коэффициента при экстренном торможении
За расчётную величину принимаем a = 381.
Величина динамического коэффициента
Расчётная нагрузка определяется из формулы
Принимаем что максимальный изгибающий момент будет когда тележка находится краю стрелы.
Расчётная схема стрелы представлена
Рис.1 Расчётная схема стрелы
Максимальный изгибающий момент
Напряжение в расчётном сечении
R = 210 МПа [1 табл. 6.7]
γ1 = 1 – коэффициент учитывающий ответственность рассчитываемого элемента [1 табл. 6.2]
γ2 = 095 – коэффициент учитывающий отклонение в геометрических размерах конструкции влияние коррозии и т.п. [1 табл. 6.3]
γ3 = 085 – коэффициент учитывающий несовершенство расчета [1 табл. 6.5]
Момент сопротивления равен
Для обеспечения устойчивости стенок балки между ними установлены поперечные листы. На среднем участке балки это расстояние проверяем из условия устойчивости стенки по критическим напряжениям.
Проверка сечения по второму расчетному случаю (горизонтальные нагрузки при резком торможении крана с поднятым грузом).
Расчетным для этого случая является нагрузки от массы груза и тележки собственной массы металлоконструкции и сил инерции
Максимальное расчетное напряжение в главной балке
Момент изгибающий колонну
- момент сопротивления трубы
Нам необходимо подобрать такой диаметр трубы что бы выполнялось условие прочности колонны из этой трубы
Толщина стенки трубы
ПринимаемD=300мм значит d=240мм
) Проверяем на кручение при неустановившемся движении
Для толстостенной трубы. Максимальное касательное напряжение с минимальной толщиной стенки
F- площадьохватываемая средней линей замкнутого профиля
Предельное касательное напряжения
Расчёт производим для швов вертикальных стенок нижних и верхних поясов.
Касательные напряжения в швах горизонтальных листов
где Gn – поперечная сила над швом поясов;
b – толщина вертикальной стенки.
Расчет стыков вертикальных листов производим на изгиб при положении тележки над стыком по первой комбинации нагрузок.
Расчётный момент сопротивления определяется по нижним точкам вертикальных швов
Предельное состояние
Курсовое проектирование грузоподъемных машин: Учеб. пособие для студентов машиностр. спец. вузов Под ред. С. А. Казака. -М.: Высш. шк. 1989.-319 с.: ил.
СНиП II-23-81. Стальные конструкции
спец общий вид.cdw

Болт М26 х40 ГОСТ 7805-70
Шайба 26ГОСТ 6402-70
Шпилька М34х60 ГОСТ22043-76
Шайба 34 ГОСТ 6402-70
Гайка М34 ГОСТ 5915-70
Подшипник №3518 ГОСТ 5721-70
Подшипник№8222 ГОСТ7872-89
Шпонка 20х12х60 по ГОСТ 23360-78
Записка.doc
Брянский Государственный
Технический Университет
“Грузоподъёмные машины”
Кран стреловой на неподвижной колонне
Расчет механизма подъёма
1 Выбор кинематической схемы ..4
2 Выбор типа и кратности полиспаста 5
3. Выбор каната ..5
4 Выбор крюковой подвески 5
5 Установка блоков 6
6 Определение параметров барабана 7
7 Выбор электродвигателя 10
8 Выбор редуктора 13
9 Определение времени пуска при неустановившемся режиме движения .14
10 Определение тормозного момента и выбор тормоза 16
12 Крепление концов каната на барабане 18
13 Расчет оси барабана . 19
14 Выбор подшипников оси барабана .21
15 Расчет чистых болтов 24
Расчет механизма передвижения тележки
1. Выбор кинематической схемы .25
2. Максимальные нагрузки на ходовые колеса 25
3. Выбор двигателя и редуктора .27
5. Определение тормозного момента и выбор тормоза ..31
6. Проверочный расчет ..33
7. Расчет ходовых колес .35
Расчет механизма передвижения крана
1. Выбор кинематической схемы 37
2. Статическая нагрузка на колеса .37
3. Сопротивление передвижению крана 38
4. Выбор Электродвигателя и редуктора 40
6. Определение тормозного момента и выбор тормоза 43
7. Проверочный расчет 45
8. Расчет ходовых колес ..47
Список литературы .49
Целью данной работы является проектирование стреловой кран на неподвижной колонне.
В данной работе проектируем; механизм подъема механизмы передвижения крана и механизм поворота.
Механизм подъема груза включает двигатель редуктор барабан крюковую подвеску муфту и тормоз производим их расчет согласно заданию.
Механизм передвижения тележки принимаем за счет барабана.
Механизм поворота включает червячный редуктор.
МЕХАНИЗМ ПОДЪЕМА ГРУЗА
1 Выбор кинематической схемы механизма.
При проектировании стрелового крана предпочтение можно отдать кинематической схеме механизма подъема груза в которой двигатель соединен с редуктором при помощи зубчатой муфты с промежуточным валом. Роль тормозного шкива выполняет одна из полумуфт. Отсутствуют открытые зубчатые передачи. Концы быстроходного и тихоходного валов редуктора выходят в одну сторону. Механизм подъема располагаем на колонне.
2. Выбор типа и кратности полиспаста.
Тип и кратность полиспаста выбирается на основании конструктивного анализа выбранной схемы механизма в зависимости от типа крана его грузоподъемности и условий работы [4 табл. 2.1].
Выбираем полиспаст сдвоенного типа с характером навивки каната на барабан через направляющие блоки кратностью m = 2
Максимальное натяжение каната Н при подъеме груза равно
a = 2 – для сдвоенного полиспаста ; = 098 – КПД блока установленного на подшипниках качения; m = 2 – кратность полиспаста. Расчет каната по правилам Ростехнадзора проводим по формуле: где Sразр – разрывное усилие каната в целом Н; Zp – коэффициент использования каната зависящий от группы режима работы механизма подъема [3 табл.1]
При группе режима работе М5 выбираем Zp = 4.5
Выбираем канат двойной свивки типа ЛК–Р 6×19(1+6+66)+1о.с. по ГОСТ 2688-80 с диаметром каната dк = 9.9 мм и разрывным усилием каната не менее S = 48.85 кН
4. Выбор крюковой подвески
Крюковую подвеску для кранов общего назначения выбираем по ОСТ 24.191.08-81 в зависимости от грузоподъемности режима работы крана и диаметра каната.
Выбираем по стандарту 1-32-336 [4 прил.1.].
Диаметр барабана выбирают по формуле
Принимаем из стандартного рядамм
Диаметр уравнительного блока рассчитываем
6. Определение параметров барабана
Установка барабана в этом случае представляет собою сборочную единицу-барабан с внешней опорой. В качестве внутренней опоры оси барабана используют конец тихоходного вала редуктора имеющий точку для размещения подшипника.
Число витков нарезки на одной половине барабана под сматываемый канат
Длина нарезки на лдной половине барабана под сматываемый канат
При сдвоенном полиспасте с каждой стороны барабана оставляем под закрепление каната расстояние мм
По Правилам Ростехнадзора длина барабана должна быть такой чтобы при низшем положении груза на барабане оставались навитыми не менее 15 неприкосновенных витков каната не считая витков находящихся под зажимным устройством
Число неприкосновенных витков
Длина витков находящихся под зажимным устройством
Расстояние между правым и левым нарезными полями принимаем согласно расчетам. Необходимо чтобы при крайнем верхнем положении крюковой подвески угол набегания канатов на барабан с крайних блоков подвески не превышал 6°
Расстояние В между вертикальными осями крайних блоков подвески выбирается конструктивно или берется по литературным источникам [2678]. Расстояние hmin выбирается конструктивно в зависимости от типа крана диаметров барабана и блоков высоты тележки и т.д(предворительно можно принимать .
Общая длина барабана равна:
Обычно в краностроении отношение длины барабана к его диаметру рекомендуют в пределах от 15 до 3.
т.е. основной расчет стенки барабана проводим на сжатие
Толщина стенки барабана определяется по формуле:
Материал барабана – Ст3 для него =240 МПа
где п =2 – коэффициент запаса прочности [7 стр. 5]
Скорость каната навиваемого на барабан
где– скорость подъёма груза;– кратность полиспаста.
Частота вращения барабана
7. Выбор электродвигателя
Предварительная мощность двигателя рассчитывается по формуле
где NCT – расчетная статическая мощность кВт;
kT = 13– коэффициент учитывающий режим работы механизма вид управляющего устройства и электропривода [5 Т1 табл. 111.7]
Статическая мощность кВт электропривода при подъеме номинального груза равна
где– скорость подъёма груза
– общий КПД механизма
-КПД узла лебедки между двигателем и барабаном
КПД цилиндрического редуктора
КПД направляющего блока
Мощность двигателя равна
Для рассчитанной мощности N по каталогу выбираем двигатель MTF 112-6 с учетом заданной группы режима работы 5М (а значит и соответствующей относительной продолжительности включения ПВ = 25%). Данные приведены в табл. 2.
Основные технические данные электродвигателя MTH 112-6
Мощность на валу кВт (ПВ=25%)
Расчетная формула для определения мощности электродвигателя по условиям теплового режима имеет вид
где все значения коэффициентов выбираются по литературному источнику [5 Т1 стр. 236.].
кг м2 момент редуктора
кг м2 момент муфты со шкиврм
Здесь и = 081 и 071 соответственно — эквивалентный базовый и эквивалентный КПД зависящие от вида электропривода;
kн = 1.15 — коэффициент учитывающий изменение потерь холостого хода от фактического питающего напряжения;
kЭ = 06 — коэффициент учитывающий степень загрузки электродвигателя (5 Т1 табл. II. 1.8);
k0 = 08 — коэффициент характеризующий изменение потерь холостого хода в зависимости от ПВД;
kp = 1 — коэффициент учитывающий увеличение потерь на регулировочных характеристиках для систем с параметрическим управлением;
kд = 125 — коэффициент учитывающий влияние динамических потерь энергии на нагрев двигателя (5 Т1 табл. II. 1.7).
По условию нагрева выбранный электродвигатель подходит.
Расчетная формула проверки двигателя по условиям обеспечения пуска имеет вид
Kз м = 125 – коэффициент запаса по моменту;
МСТтах Нм – максимально возможный момент статической нагрузки приведенный к валу двигателя;
МД – динамический момент определяемый из условий обеспечения заданного ускорения Нм;
пдв = 915 обмин частота вращения выбранного двигателя;
=5.2кВт– фактическая статическая мощность электродвигателя при подъеме номинального груза с фактической скоростью кВт;
J=0.32 кг м2 – суммарный момент инерции ротора электродвигателя соединительных муфт массы груза кгм2;
J=0.25 – допустимое ускорение при пуске механизма подъема для данного типа крана мс2
По условию пуска выбранный электродвигатель подходит.
Передаточное число равно
По найденному значению передаточного числа выбираем цилиндрический 2-х ступенчатый редуктор типа Ц2 – 300. Данные приведены в табл. 3.
Определим момент на тихоходном валу
Основные параметры и размеры редуктора Ц2-300
Типоразмер редуктора
Межосевое расстояние мм
Номинальное передаточное число
Ном. крутящий момент на тих. валу кНм
Погрешность выбора редуктора равна
Фактическая частота вращения барабана:
Фактическая скорость каната:
Фактическая скорость подъёма груза:
Фактическая статическая мощность при подъёма груза:
9 Определение времени пуска при неустановившемся режиме
- средний пусковой момент выбранного электродвигателя Нм
- момент статического сопротивления груза Нм
- момент инерции вращающихся элементов привода Нм
- момент от сил инерции поступательного движущихся масс Нм
Уравнения приведенных к валу двигателя моментов в развернутом виде
Обычно данное значение находится в диапазоне (1..2)секунды
Фактическое ускорение
Время пуска при опускании груза
11. Определение тормозного момента и выбор тормоза
Тормозной момент рассчитывается по моменту от номинального груза приведённого к валу электродвигателя
где к =175- коэффициент запаса торможения для М5 [4c.33]
MСТ – момент на валу двигателя при подъеме номинального груза
По каталогу выбираем тормоз типа ТКГ-200 (рис.7) отрегулировав его на необходимый тормозной момент. Данные приведены в табл. 4.
Основные параметры тормоза ТКГ
Т.к. разница между номинальным моментом и тормозным более 10% то необходимо отрегулировать тормоза на момент равный 96.25 Нм [4.с.34]
Время торможения при спуске груза определяется по формуле: с
где SJТ=SJ – суммарный момент инерции ротора электродвигателя соединительных муфт массы груза кг×м2 ;rб – радиус барабана измеренный по оси сечения каната м; Vср – скорость опускания груза мс
Время торможения при подъёме груза
В механизме подъема груза расчетный момент муфты определяем по формуле
где K1 = 13 – коэффициент учитывающий степень ответственности соединения [5 т.2 табл.V.2.36];
K2 = 1.1 – коэффициент режима работы [5 т.2 табл.V.2.37];
K3 = 1 – коэффициент углового смещения [5 т.2 табл.V.2.38];
– номинальный момент электродвигателя.
Подбираем муфту упругую втулочно-пальцевую соединяющую электродвигатель с редуктором с тормозным шкивом соответствующим по диаметру выбранному тормозу. Данные приведены в табл. 5
Основные размеры и параметры втулочно-пальцевой муфты с тормозным шкивом.
Номинальный вращающий момент Mk Hм
13 Крепление концов каната на барабане.
По Правилам Ростехтехнадзора канаты к барабану должны крепиться надежным способом допускающим возможность замены каната. В случае применения прижимных планок количество их должно быть не менее двух. Длина свободного конца каната от последнего зажима на барабане должна быть не менее двух диаметров каната. Изгиб свободного конца каната под прижимной планкой или на расстоянии от пленки составляющем менее трёх диаметров канат не разрешается.
Вариант крепления каната планками к барабану шпильками изображен на рис. 1.
Рис.1 Крепление каната на барабане.
Охват барабана 15 разгружающими витками каната соответствует углу a= 3p в связи с чем при минимальном коэффициенте трения между канатом барабаном и накладкой усилие в канате под накладками равно:
Усилие прижатия накладок определяем по формуле:
где j = 035 040 – коэффициент сопротивления каната при зажиме накладками.
Внутренний диаметр резьбы шпильки равен
где =2 – число болтов; =360 МПа – предел текучести стали 45;
- Коэффициент запаса прочности.
Минимальный внутренний диаметр резьбы шпилек для каната dk = 9.9 мм равен 10мм. Поэтому принимаем d = 10мм
14 Расчет оси барабана
Барабан закрепляем на сплошных осях опирающихся на сферические подшипники качения что компенсирует смещение и перекосы вызываемые неточностью изготовления и монтажа а так же деформациями металлоконструкции.
. Во вращение барабан приводится с помощью встроенной зубчатой муфты. В этом случае левый подшипник располагается внутри полости выполненной на конце тихоходного вала редуктора а правый подшипник устанавливается в подшипниковом корпусе закрепленном на раме тележки. Зубчатый венец представляющий одно целое с валом редуктора и зубчатая ступица барабана имеющая внутренние зубья образуют встроенную в барабан зубчатую муфту. Зубчатая ступица соединяется с обечайкой барабана «чистыми болтами». При этом соединении левый подшипник выполняет лишь роль сферической опоры («плавающая» опора) т.к. при вращении барабана оба его конца вращаются с одинаковой угловой скоростью и этот подшипник выбирается по статической нагрузке.
Ось барабана изготавливается из стали 45 (ГОСТ 1050-88) и она испытывает напряжение изгиба от действия усилий двух ветвей каната при сдвоенном полиспасте а также от собственного веса барабана.
Рис.10 Схема нагружения оси барабана.
Принимаем a= 100 мм b = 120 мм l = 600 мм.
Определяем реакции в опорах:
Строим эпюру изгибающих моментов
Для оси барабана выберем материал Сталь45.
Диаметр оси под ступицей в зависимости от изгибающего момента определяем по формуле
- допускаемое напряжение
где Т = 360 МПа – предел текучести для стали 45;
к=15 – коэффициент запаса прочности.
Допускаемое напряжение
- коэффициент учитывающий конструкцию детали
- допускаемый коэффициент запаса прочности
Общее число нагружений оси [9 c. 24]
час – число часов работы детали (таб12)
расчетное число подъемов в год
- число нагружений за подъем
Коэффициент приведения к расчетному числу нагружений
коэффициент использования крана при работе с грузом
от Q до 0.75 Q(таб15)
коэффициент использования крана при работе с грузом
коэффициент поправочный
Расчетное число нагрузки оси
Предел выносливости соответствует расчетному числу нагружений
базовое число циклов
показатель степени усталостной кривой
15 Выбор подшипников оси барабана
Учитывая возможную неточность монтажа на оси барабана располагаем двухрядные радиальные самоустанавливающиеся сферические роликоподшипники.
Подшипник опоры А вставляем в выточку тихоходного вала редуктора имеющую следующие размеры: диаметр наружного кольца подшипника и его ширину. Подшипники устанавливаемые в опорах А и В работают в разных условиях. Расчет подшипника в опоре А производят по статической нагрузке равной RA . Подшипник в опоре В производят по динамической нагрузке.
Выбор производим по статической грузоподъемности из условия что
коэффициент условия работы(5 Т2.таб.V.1.67.)
Выбираем двухрядный радиальный самоустанавливающийся сферический роликоподшипник №3508 . ГОСТ 28428-90 тип 1000
Подшипник в сечении В работает при переменном режиме
- суммарное число оборотов оси при каждом из приведенных нагружений
Приведенные нагружения
- радиальная нагрузка в Н
- осевая нагрузка в Н
- коэффициент радиальной и осевой нагрузки для радиального самоустанавливающегося сферического роликоподшипника
номинальный угол наклона
е – коэффициент осевого нагружения зависящий от угла контакта
Внутреннее кольцо относительно направления нагружения V=1
температурный коэффициент
С учетом графика загрузки [ 5 .c.50]
Режим работы М5 выбираем следующие режимы
Приведенные нагрузки
часов - ресурс подшипника
Динамическая грузоподъемность определяется по
Динамическая грузоподъемность подшипника
Для опоры В принимаем тотже подшипник
16 Расчет чистых болтов.
Барабан крепится к зубчатой полумуфте с помощью болтов поставленных в отверстие без зазора. В этом случаи расчет болтов ведется на срез. Напряжения среза определяем по формуле:
Допускаемые напряжения среза болта
К1 =1.3 – коэффициент безопасности
К2 =1.1 – коэффициент нагрузки
Задавая число болтов
Для стали 45 =280МПа
МЕХАНИЗМ ПЕРЕДВИЖЕНИЯ ТЕЛЕЖКИ
Выбираем тележку с канатной тягой.и габариты грузовой тележки с канатной тягой резко уменьшаются из-за установки механизма подъема и передвижения вне тележки.
2 Сопротивление передвижению самоходной тележки.
Масса тележки с канатной тягой обычно принимается в пределах кг
Коэффициент реборд для тележек с канатной тягой принимаем в пределах
Таким образом для преодоления всех сопротивлений движению тележки к ней необходимо приложить усилие F
- КПД барабана механизма передвижения
- КПД обводного блока
Сопротивление разности усилий в подъемных канатах определяется по формуле
а - количество ветвей каната на которых подвешен груз
Сопротивление от провисания тягового каната определяется по формуле
м – максимальная длина свободно висящего тягового каната
м – допускаемое провисание тягового каната
– сопротивление создаваемое уклоном подтележечного пути:
=0.002 – уклон рельсового пути для тележки [4 с.41];
Максимальная нагрузка Н на ходовое колесо грузовой тележки составляет
где – грузоподъемность крана кг;
КТ – коэффициент толчков.
где– скорость движения грузовой тележки ммин;
а – коэффициент равный 0001 при заваренных стыках на рельсах или при их отсутствии и 0002 при открытых стыках на рельсах [5 т.1 с. 63].
Зная максимальную статическую нагрузку на одно приводное колесо определяем диаметр колеса и тип рельса [5 т.2 табл. V.2.47].
При от 30 до 50 кH диаметр дорожки катания колеса = 200 мм тип рельса – Р 24 (ГОСТ 6358-82).
Сопротивление передвижению тележки с номинальным грузом Н при установившемся режиме работы равно:
где– диаметр цапфы колеса [5 т.2 табл. V.2.43];
– диаметр ходового колеса выбранный по максимальной нагрузке;
– коэффициент трения в опоре вала колеса [4 табл. 2.14];
– коэффициент трения качения колеса по рельсу [4 табл. 2.13];
– коэффициент реборд определяемый в основном трением реборд о головку рельса и трением элементов токосъемного устройства [1 табл. 2.15];
– сопротивление создаваемое ветром учитывать не будем поскольку кран установлен в помещении.
Сопротивление передвижению тележки равно:
Натяжение тягового каната на барабане равно
В данном механизме передвижения принимаем приводной барабан насаженный на выходной конец редуктора и на который навито несколько витков тягового каната. В этом случае при натяжении ветвей каната окружное усилие равно
3 Выбор Электродвигателя и редуктора
Двигатель механизма передвижения обычно выбирается серии МТКF МТКН таким образом чтобы отсутствовала пробуксовка ведущих колес незагруженной тележки а коэффициент запаса сцепления должен быть не менее 12.
Мощность двигателя кВт равна
где =0.08– заданная скорость грузовой тележки;
– общий КПД механизма передвижения [5 т.2 с.423]
Для рассчитанной мощности по каталогу выбираем двигатель MTKF 011-6 (рис.13) с учетом заданной группы режима работы М5 (а значит и соответствующей относительной продолжительности включения ПВ = 25%). Данные приведены в табл. 6.
Основные технические данные электродвигателя MTKF 011-6
Частота вращения колес с-1
Передаточное число редуктора
По найденному значению передаточного числа выбираем цилиндрический 2-х ступенчатый редуктор типа Ц2-250Данные приведены в табл. 7.
Основные параметры и размеры редуктора
Так как расчетная величина передаточного числа редуктора не совпадает с передаточным числом фактического редуктора то фактичес0кая частота вращения ходового колеса равна
Фактическая скорость передвижения грузовой тележки равна
Погрешность выбора скорости передвижения тележки
Погрешность выбора скорости передвижения тележки не превышает допустимых 15%.
Требуемая мощность электродвигателя кВт определяется по формуле
При пуске электродвигателя максимальное допустимое ускорение ненагруженной тележки при котором обеспечивается заданный запас сцепления ходового колеса с рельсом без пробуксовки равно:
где – число приводных колес грузовой тележки;
– общее число колес грузовой тележки;
– коэффициент сцепления ходовых колес с рельсом [6 с. 393];
– ускорение свободного падения м с .
Время пуска при максимальном ускорении:
где– максимальный момент электродвигателя Нм
В механизме передвижения грузовой тележки расчетный момент муфты определяем по формуле
K2 = 11 – коэффициент режима работы [5 т.2 табл.V.2.37];
K3 = 1 – коэффициент углового смещения [5 т.2 табл.V.2.38].
Подбираем муфту упругую втулочно-пальцевую соединяющую электродвигатель с редуктором с тормозным шкивом соответствующим по диаметру выбранному тормозу. Данные приведены в табл. 8
Основные размеры и параметры втулочно-пальцевой муфты с тормозным шкивом
5 Определение тормозного момента и выбор тормоза
При подъеме или опускании груза появляются силы которые стремятся сдвинуть тележку с места. Для того.чтобы удержать тележку в неподвижном состоянии механизм передвижения снабжают тормозом
Усилие натяжения нижней ветви тягового органа механизма передвижения при удержании тележки в неподвижном состоянии равно
Крутящий момент возникающий на барабане механизма передвижения при подъеме или опускании
По расчетному тормозному моменту выбираем тормоз ТКГ-200 (рис.7) с максимальным тормозным моментом МТ = 250 Нм. Данные приведены в табл. 9.
МЕХАНИЗМ ПОВОРОТА КРАНА
Место расположения механизма на поворотной части.Данная схема срдержит двигатель муфтутормозредуктор и пару «шестерня- венец».
Расстояние между опорами
Вес крана можно определить по удельной металлоемкости
- вес поворотной части крана
Вес противовеса определяем из равенства моментов
Находим реакцию в верхней части колонны
Диаметр колонны имеющей круглое сплошное сечение принимаем по формуле
3 Определение момента сопротивлению поворота
Момент сопротивления повороту крана действующий в период разгона равен сумме моментов
Момент сил трения в верхней опоре
Момент сил трения в нижней опоре
Момент ветровой нагрузки рабочего состояния
4 Выбор Электродвигателя и редуктора
Двигатель механизма передвижения обычно выбирается серии МТКF МТКН таким образом чтобы отсутствовала пробуксовка ведущих колес разгруженного крана а коэффициент запаса сцепления должен быть не менее 12.
Мощность двигателя NCT кВт равна
где wк = 0.29 обс – заданная скорость поворота крана;
= 07 085 - общий КПД механизма передвижения [5 т.2 с.423]
Для рассчитанной мощности NСТ по каталогу выбираем двигатель MTF 111-6 мощностью 4.1 кВт. Данные приведены в табл. 9.
Основные технические данные электродвигателя MTF – 111-6
Выбираем редуктор РЧ-200
Так как расчетная величина передаточного числа редуктора не совпадает с передаточным числом фактического редуктора то фактическая частота вращения ходового колеса равна
Фактический средний пусковой момент электродвигателя равен:
K2 = 12 – коэффициент режима работы [5 т.2 табл.V.2.37];
K3 = 1.3 – коэффициент углового смещения [5 т.2 табл.V.2.38].
Подбираем муфту упругую втулочно-пальцевую соединяющую электродвигатель с редуктором с тормозным шкивом (соответствующим по диаметру выбранному тормозу. Данные приведены в табл. 10
6 Определение тормозного момента и выбор тормоза
Расчетный тормозной момент. При работе крана на открытом воздухе определяем уравнением
Здесь -КПД механизма при торможении. Он может существенно отличаться от КПД механизма при разгоне и установившемся движении так как в механизме использована червячная передача.
Выбираем тормоз ТКГ- 200
Анурьев В. И. Справочник конструктора-машиностроителя. Т.1. Т.2. Т.3. – 8-е изд. перераб. и доп. Под ред. И.Н. Жестковой. – М.: Машиностроение 2001. Т.1. – 920с. Т.2. – 912с. Т.3. – 864с.
Блейшмидт Л.И. Расчет и выбор стальных проволочных канатов для грузоподъемных машин: Метод. указания. – Брянск: БГТУ 2001. – 18с.
Курсовое проектирование грузоподъемных машин: Учеб. пособие для студентов машиностр. спец. вузов Под ред. С. А. Казака. -М.: Высш. шк. 1989.-319 с.: ил.
Справочник по кранам Под общ. ред. М. М. Г о х б е р г а. — Л.: Машиностроение. Ленингр. отд-ние 1988. Т.1 — 536 с. Т.2 – 559 с.
Александров М.П. Грузоподъемные машины.-М.; МГТУ Баумана- Высшая школа 2000 -552с.
Федоренко В.И. Расчет механизма подъема: Метод. указания. - Брянск: БГТУ2002.- 16 с.
Федоренко В.И. Расчет механизмов передвижения: Метод. указания. – Брянск: БГТУ 2002.- 19 с.
Павлов Н.Г. Примеры расчета кранов.Л. Машиностроение1976.- 320с.
Подъемно-транспортные машины. Атлас конструкций Под ред. М.П. Александрова Д.Н. Решетова. – М.: Машиностроение 1987. – 122 с.
Подъем Мих.cdw

Продолжительность включения
Скорость подъема груза
Скорость вращения обмин
Канат ЛК-Р 6Х19 (1+6+66) + 1 о.с. ГОСТ 2688-80 d=19
Неуказанные предельные отклонения размеров
Запасовка каната в механизм подъема производить по схеме
Подшипниковые узлы тележки заполнить закладной смазкой
долгодействующей МПИ
Защитное заземление электрооборудования тележки
произвести согласно
Правил устройства электрооборудования"
Допуск радиального биения рабочей поверхности тормозного
шкива (после установки) относительно оси вращения 0.1мм
Технические требования
Техническая характеристика
Схема запасовки каната
поворот.cdw

Скорость вращения обмин
Неуказанные предельные отклонения размеров
Подшипниковые узлы заполнить закладной смазкой
долгодействующей МПИ
Защитное заземление электрооборудования произвести согласно
Правил устройства электрооборудования"
Допуск радиального биения рабочей поверхности тормозного
шкива (после установки) относительно оси вращения 0.1мм
Техническая характеристика
Технические требования