Конструктивные проработки по модернизации козлового контейнерного перегружателя




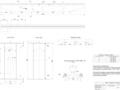
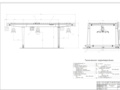
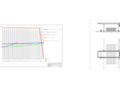
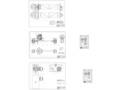
- Добавлен: 25.01.2023
- Размер: 6 MB
- Закачек: 0
Описание
Состав проекта
![]() |
![]() |
![]() |
![]() |
![]() |
![]() |
![]() |
![]() |
![]() ![]() ![]() ![]() |
![]() ![]() ![]() ![]() |
![]() ![]() ![]() |
![]() ![]() ![]() ![]() |
![]() ![]() ![]() ![]() |
![]() ![]() ![]() ![]() |
![]() ![]() ![]() |
Дополнительная информация
графо-аналитическая характеристика+технологическая схема+.dwg

характеристика потерь механизма передвижения перегружателя
характеристика потерь механизма передвижения тележки
Графоаналитическая характеристика
ДП П-0609 00.00.000
характеристика насоса
характеристика предохранительного клапана
общий вид+.dwg

м 3. Высота подъема груза
м 4. Скорость механизма
мс подъема груза передвижения тележки передвижения перегружателя 5. Колея тележки
м 7. Гидромоторы механизма подъема груза: тип МРФ-700025М1 мощность
Канат: ЛК-Р 6×19+Iо.с. диаметр
мм 9. Гидромоторы механизма передвижения тележки: тип МРФ-180025М1 мощность
кВт 10. Гидромоторы механизма передвижения перегружателя: тип МРФ-160025М1 мощность
Козловой контейнерный перегружатель Вид общий
ДП П-0609-01.00.000 ВО
стойка гидромотора+.dwg
ДП П-0609 01 01 001
Сталь 09Г2С ГОСТ 8732-78
Таблица сварных швов
Металлоконструкция+.dwg

ДП-0516-001.01.00 СБ
Металлоконструкция пролетной балки перегружателя Сборочный чертеж
ДП П-0609 01.04.000 СБ
Технические требования: 1) Все элементы продольной балки должны быть изготовлены в соответствии с ГОСТ 380-71 2) Качество сварных швов должно удовлетворять техническим требованиям по ГОСТ 24376-80 (технические условия)
Тип рельса КР70 ГОСТ 6368 - 82 (1:4)
Таблица сварных швов
Обозначение сварного шва
механизм передвижения тележкии+перегружателя + подъема+.dwg

Подшипник 13213 ГОСТ8545-57
Механизм передвижения тележки
Подшипник 13219 ГОСТ8545-57
Рельс крановый ГОСТ 4121-76
Механизм передвижения тележки Сборочный чертеж
Технические условия.
Радиальное смещение валов гидромотора и колеса не более 0.1 мм. 2. Перекос валов гидромотора и колеса не более 0°15'. 3. Проверить величину контакта рабочих поверхностей зубьев.
Техническая характеристика. Скорость передвижения тележки
мс 1.5 Гидромотор МРФ - 180025М1 Колеса ГОСТ 3569 - 74 Dк=400 мм 4 шт.
ДП П-0609 001 03 00 СБ
Наибольшая высота подъема
Техническая характеристика:
Канат ЛК-Р 6 19+I о.с. (ГОСТ 2688-80)
Технические условия: 1. Осевое перемещение валов гидромотора и барабана с подшипниками в пределах 0.4±0.2 мм. 2. Максимально допустимый боковой зазор между зубьями муфты должен составлять 0.55 мм. 3. Муфты заполнить маслом индустриальным И-40 ГОСТ 20799-75 и обкатать механизм без нагрузки в обе стороны. 4. После обкатки проверить величину контакта рабочих поверхностей зубьев.
Механизм подъема Сборочный чертеж
ДП П-0609 01 01 000 СБ
Подшипник 13216 ГОСТ8545-57
Механизм передвижения мостового крана
Техническая характеристика.
Скорость передвижения перегружателя
мм 710 Гидромотор МРФ-160025М1
Радиальное смещение валов гидромотора и колеса не более 0.1 мм. 2. Перекос валов гидромотора и колеса не более 0°15. 3. *- размеры для справок.
Механизм передвижения перегружателя Сборочный чертеж
ДП П-0609 01 02 000 СБ
технологическая схема+.dwg

Козловой контейнерный перегружатель грузоподъемностью 40 тонн.
Груз массой 30 тонн.
Железнодорожная платформа
ДП П-0609 00.00.000 ТС
пояснительная записка.docx
Научно – исследовательская работа
«Анализ способов рекуперации энергии в гидроприводах» ..6
Техническое описание козлового контейнерного перегружателя ..15
Расчет и выбор основных энергетических характеристик приводов перегружателя 17
1. Расчет механизма подъема 17
2. Расчет механизма передвижения перегружателя 25
3. Расчет механизма передвижения тележки перегружателя 31
Описание гидравлической схемы перегружателя 37
Расчет и выбор гидрооборудования перегружателя 41
Построение графо – аналитических характеристик приводов 51
Описание электросхемы управления перегружателем и выбор электродвигателя 55
Прочностной расчет металлоконструкции перегружателя .65
Технология изготовления стойки гидромотора 84
Рассмотрение методики неразрушающего контроля стойки гидромотора ..99
Технологическая схема работы перегружателя 109
Технико – экономический анализ ..115
Экспертиза промышленной безопасности 119
Технологическое обслуживание и ремонт козлового контейнерного перегружателя..147
Предложения по внедрению 162
СПИСОК ИСПОЛЬЗОВАННОЙ ЛИТЕРАТУРЫ 169
Интенсивное развитие перевозок грузов в контейнерах автомобилями железнодорожными составами речным и морским транспортом обусловило создание специальных подъемно-транспортных средств высокой производительности в частности козловых перегружателей на рельсовом ходу способных выполнять операции по перемещению грузов из одного вида транспорта в другой с учетом их взаимного расположения на одной перегрузочной площади.
В последнее время в крановых механизмах все чаще находят свое применение гидроприводы. Наиболее важным их достоинством является возможность бесступенчатого регулирования скорости простота регулирования мощности возможность выполнения механизмов без редукторов и фрикционных тормозов более высокая мощность при той же массе по сравнению с другими типами приводов. Преимуществом так же является возможность рационального размещения его элементов соединенных трубопроводами любой (с точки зрения рациональности) конфигурации возможность питания нескольких гидромоторов одним насосом и одного гидромотора несколькими насосами.
Насосы и гидромоторы характеризуются простотой регулирования и экономичностью регулирования по давлению и скорости малой инерционностью вращающихся частей и возможностью дистанционного и автоматического управления.
Основной показатель гидромотора крутящий момент почти не зависит от частоты вращения а является функцией давления и при нулевой скорости гидромотор имеет полный крутящий момент.
Наиболее широкое распространение получила схема гидропривода с насосом регулируемой подачи с открытой или замкнутой циркуляцией жидкости. Эта схема обеспечивает бесступенчатое изменение скорости работы механизма. Так же используются высокооборотные гидромоторы с редукторами высокомоментные низкооборотные в схемах с непосредственной связью с рабочим органом привода без редуктора.
В приводах козловых перегружателей предпочтительно применяют нерегулируемые радиально-поршневые высокомоментные гидромоторы предназначенные для преобразования энергии потока рабочей жидкости в механическую энергию вращательного движения выходного вала.
Гидрофицирование козлового перегружателя дает возможность использования широкого диапазона скоростей и регулирования мощности снижения «забросов» потребляемой энергии энергосети при пусках электродвигателей приводов насосов крана обеспечивает плавность движения частей крана снижает эксплуатационные расходы.
Модернизация козлового контейнерного перегружателя грузоподъемностью 40 тонн будет заключаться в разработке гидравлического привода (с объемным регулированием) механизмов крана с рекуперацией энергии что снизит ее потребление и эксплуатационные расходы.
В дипломном проекте проводятся необходимые расчеты и конструктивная компоновка механизмов перегружателя и гидросистемы привода.
Для составления и расчета гидросистемы привода необходимо провести расчет основных энергетических характеристик приводов перегружателя и расчет механизмов перегружателя.
Далее проводится расчет металлоконструкций крана. Потом составляется гидравлическая схема перегружателя рассчитывается и выбирается гидроаппаратура. Производится компоновка элементов системы гидрооборудования по элементам крана конструируется насосная станция на которой так же компонуется гидроаппаратура. Затем необходимо построить графо – аналитическую характеристику приводов и насосной станции определить потери давления в линиях приводов механизмов перегружателя характеристику насоса и предохранительного клапана. По ней устанавливаются необходимые уровни давления в линиях приводов для обеспечения нормальной работы механизмов и разгонных характеристик а так же параметры регулирования расхода насоса для обеспечения необходимых скоростей движения приводных элементов крана.
Так же составляется силовая схема электропривода насосной станции схема управления приводом перегружателя с выбором электроаппаратуры.
Далее приводится описание технологии изготовления элемента крана – стойки гидромотора и разрабатывается методика её неразрушающего контроля.
Формируются предложения по внедрению гидрофицированного козлового контейнерного перегружателя описывается схема работы перегружателя и приводятся необходимые экономические расчеты по гидрофицированию перегружателя и его эксплуатации.
В данном дипломном проекте стоит задача: «Конструктивная проработка козлового контейнерного перегружателя грузоподъемностью 40т» где вместо электропривода будет иметь место гидропривод.
НАУЧНО-ИССЛЕДОВАТЕЛЬСКАЯ РАБОТА
«АНАЛИЗ СПОСОБОВ РЕКУПЕРАЦИИ ЭНЕРГИИ В ГИДРОПРИВОДАХ».
Энергосбережение сегодня является одним из важнейших аспектов для большинства потребителей тепловой энергии. Постоянный рост цен на энергоносители делает эту проблему еще острее и актуальнее. В настоящее время рекуперация получила широкое распространение в большинстве европейских стран. Экономическое обоснование применения рекуператоров в условиях относительно сурового российского климата более чем очевидно.
Плюсом рекуперации является экономия энергии и как следствие экономия средств на эксплуатацию системы вентиляции. Иногда когда имеется ограничение в возможном объеме потребляемой энергии и установить мощную обогревательную систему невозможно использование рекуператора является хорошим решением задачи.
Минусом является необходимые дополнительные первоначальные вложения на установку рекуператора.
Рассмотрим несколько изобретений рекуперации энергии:
Изобретение относится к общему машиностроению в частности к объемным гидроприводам и может быть использовано в качестве привода механизмов передвижения машины циклического действия с преимущественным рабочим движением в одном направлении например путевых машин.
Гидропривод передвижения путевых машин содержит гидромотор кинематически связанный с ведущими осями и сообщенный двумя линиями питания через трехпозиционный распределитель с линией нагнетания на которой установлен пневмогидравлический аккумулятор высокого давления.
Недостатками данного привода являются наличие одного аккумулятора для привода нескольких исполнительных механизмов имеющих различные гидравлические параметры; отсутствие рекуперации кинетической энергии машины при торможении (торможение на этих машинах происходит с помощью тормозных колодок прижимаемых к бандажу ведущих колес специальными пневмоцилиндрами) снижает технико-экономические показатели машины; привод не предусматривает выбор зазоров в кинематических передачах связывающих гидромотор с ведущими осями что приводит к динамическим перегрузкам в элементах передачи во время пуско-тормозных операций.
Рисунок 1.1. – Гидрокинематическая схема рекуперации энергии.
Наиболее близким по технической сущности к предлагаемому гидроприводу является гидропривод содержащий реверсивный гидромотор рабочая и тормозная полости которого сообщены через трехпозиционный пятиходовой распределитель с источниками высокого и низкого давления гидравлически управляемый двухпозиционный пятиходовой распределитель связывающий посредством гидролиний рабочую и тормозную гидролинию обратные гидроклапаны гидроаккумулятор малого объема с редукционным клапаном регулируемый дроссель связывающий тормозную магистраль с баком через двухпозиционный распределитель насосы подпитки с предохранительными клапанами распределителем и клапаном автоматической разгрузки.
Известный гидропривод обеспечивает повышение надежности механизма при рекуперации кинетической энергии однако данный гидропривод более сложен вследствие большого числа примененных гидроаппаратов и следовательно менее надежен.
Цель изобретения - повышение надежности привода путем снижения динамических нагрузок при пуске и торможении.
Поставленная цель достигается тем что в гидроприводе содержащем насос сообщенный через обратный клапан с пневмогидроаккумулятором высокого давления и источник низкого давления подключенный через трехпозиционный распределитель рабочей и тормозной гидролиниями с установленным между ними блоком предохранительных клапанов к соответствующим полостям гидромотора двухпозиционный распределитель установленный в тормозной гидролинии и подключенный одним из своих входов к тормозной полости гидромотора а одним из выходов - к сливной гидролинии второй обратный клапан и дроссель двухпозиционный распределитель выполнен четырехлинейным при этом второй вход распределителя сообщен с пневмогидроаккумулятором высокого давления через второй обратный клапан второй выход подключен к трехпозиционному распределителю а дроссель установлен в сливной гидролинии.
2.Способ рекуперации энергии и гидропневмосистема для его осуществления [Автор(ы): Щербаков Виталий Федорович (RU) (73) Патентообладатель(и): Щербаков Виталий Федорович (RU)]
Изобретение относится к области машиностроительного гидропривода и может быть использовано в различных гидропневмосистемах грузоподъемных машин сельскохозяйственных строительно-дорожных и других мобильных машин а также в станкостроении нефтяной (буровых установок) и горнодобывающей промышленности. Способ рекуперации энергии заключается в том что дроссельной гидросистемой на гидравлическом сопротивлении переводят энергию положения груза при его опускании в тепло рабочей жидкости гидросистемы и аккумулируют полученное тепло в тепловом аккумуляторе а затем снимают его теплообменником теплового двигателя и преобразовывают в цикле работы теплового двигателя в механическую энергию для привода грузоподъемных устройств. Гидропневмосистема для осуществления способа содержит дроссельную гидросистему образующую контур циркуляции с теплообменником и тепловой двигатель образующий со своим теплообменником замкнутый контур циркуляции при этом теплообменники гидросистемы и теплового двигателя установлены в тепловом аккумуляторе. Технический результат – перевод энергии положения при опускании груза в тепловую а затем преобразовывание тепловой энергии в механическую для привода грузоподъемных устройств. 2 н. и 3 з.п. ф-лы 1 ил. Изобретение относится к области машиностроительного гидропривода и может быть использовано в различных гидропневмосистемах грузоподъемных машин сельскохозяйственных строительно-дорожных и других мобильных машин а также в станкостроении нефтяной (буровых установок) и горнодобывающей промышленности. Известен способ рекуперации энергии заключающийся в том что тепло рабочей жидкости гидросистемы отводят в тепловой двигатель где преобразовывают в цикле работы теплового двигателя в механическую энергию и через сумматор механической энергии подают к исполнительному механизму (SU 653463 А (МАДИ) 25.03.1979). Недостатком является то что известная гидропередача имеет ограниченную область применения. Общеизвестно что при к.п.д. механизмов равном 1 энергия для подъема груза на высоту Н (где Н высота подъема груза) равна энергии получаемой от груза при опускании с высоты Н. То есть при наличии аккумулирующих устройств в приводе грузоподъемной лебедки на процессы подъема в реальной машине с аккумулированием энергии при опускании требуется только компенсация механических потерь в приводе грузоподъемного механизма. В современных грузоподъемных механизмах механический к.п.д. составляет 06508 (набольший к.п.д. относится к грузоподъемным механизмам на базе симметричного гидроцилиндра работающего в составе гидросистемы с закрытым кругом циркуляции рабочей жидкости). Например US 4819429 A KORDAK 11.04.1989.Таким образом рекуперационная система привода будет требовать установочную мощность в 35 раз меньше мощности существующих приводов грузоподъемных машин. Особенно это существенно для скоростных грузоподъемных устройств большой грузоподъемности к которым можно отнести в первую очередь грузовые лебедки буровых установок. В процессе бурения требуются частые и скоростные процессы подъема и опускания буровой колонны. В процессе бурения требуется наращивать или уменьшать длины буровой колонны и следовательно производить цикличные подъемно-спусковые операции на 818 м (на длину ведущей трубы – квадрата или свечи). Как видно при общей длине буровой колонны сотни метров время на подъем или опускание на одно звено (трубу 89 метров или свечу 1618 м) должно быть минимально а следовательно скорость спуско-подъемных операций и очевидно мощность грузоподъемного механизма в данном случае значительна. Очевидно рекуперационная система цикличного привода (цикл: спуск – подъем) должна включать в свой состав аккумулятор соответствующей энергоемкости. Анализ существующих аккумуляторов (электрических маховичных грузовых пневмогидравлических и т.д.) показал что в данном случае они должны иметь недопустимо большие размеры а их стоимость и затраты на техническое обслуживание недопустимо велики. Наиболее приемлемы в данном случае тепловые аккумуляторы. И наиболее простой из них – теплоизолированная емкость с водой. Таким образом система рекуперации должна переводить энергию положения при опускании груза в тепловую а затем тепловую энергию преобразовывать в механическую для привода грузоподъемных устройств. Это является технической задачей изобретения. Указанная задача решается и технический результат достигается за счет того что способ рекуперации энергии заключается в том что дроссельной гидросистемой на гидравлическом сопротивлении переводят энергию положения груза при его опускании в тепло рабочей жидкости гидросистемы и аккумулируют полученное тепло в тепловом аккумуляторе а затем снимают его теплообменником теплового двигателя и преобразовывают в цикле работы теплового двигателя в механическую энергию для привода грузоподъемных устройств. При этом гидропневмосистема для осуществления способа содержит дроссельную гидросистему образующую контур циркуляции с теплообменником и тепловой двигатель образующий со своим теплообменником замкнутый контур циркуляции при этом теплообменники гидросистемы и теплового двигателя установлены в тепловом аккумуляторе. При этом наилучший результат достигается если дроссельная гидросистема выполнена в виде насосной установки подключенной своим входом к баку а выходом ко входу гидрораспределителя два выхода которого сообщены гидролиниями с баком причем один из них через подпорный клапан при этом первый рабочий отвод гидрораспределителя соединен гидролинией с входом обратимой гидромашины второй – с ее выходом третий – с первым входом теплообменника через дополнительный теплообменник а четвертый – с полостью управления предохранительного клапана непрямого действия вход которого подключен к выходу обратимой гидромашины а выход – ко второму входу теплообменника гидросистемы. При этом наилучший результат достигается если тепловой двигатель выполнен в виде установленных на одном валу компрессора пневмомотора топливного насоса и электростартера при этом выход компрессора и вход топливного насоса подключены к разным входам одной полости калорифера фреона а к разным входам другой полости калорифера фреона подключен вход компрессора и через дроссель – выход пневмомотора вход которого и выход топливного насоса подключены к разным входам теплообменника теплового двигателя причем параллельно топливному насосу установлен дроссель регулировки теплового двигателя. При этом наилучший результат достигается также если тепловой аккумулятор выполнен в виде теплоизолированной емкости.
То есть в этом случае реализуется замкнутая рекуперационная система использующая энергию положения груза а следовательно можно иметь значительно меньшую установочную мощность установки в целом. Формула изобретения 1. Способ рекуперации энергии заключающийся в том что дроссельной гидросистемой на гидравлическом сопротивлении переводят энергию положения груза при его опускании в тепло рабочей жидкости гидросистемы и аккумулируют полученное тепло в тепловом аккумуляторе а затем снимают его теплообменником теплового двигателя и преобразовывают в цикле работы теплового двигателя в механическую энергию для привода грузоподъемных устройств.2. Гидропневмосистема для осуществления способа содержащая дроссельную гидросистему образующую контур циркуляции с теплообменником и тепловой двигатель образующий со своим теплообменником замкнутый контур циркуляции при этом теплообменники гидросистемы и теплового двигателя установлены в тепловом аккумуляторе.3. Система по п.2 отличающаяся тем что дроссельная гидросистема выполнена в виде насосной установки подключенной своим входом к баку а выходом – ко входу гидрораспределителя два выхода которого сообщены гидролиниями с баком причем один из них через подпорный клапан при этом первый рабочий отвод гидрораспределителя соединен гидролинией с входом обратимой гидромашины второй – с ее выходом третий – с первым входом теплообменника через дополнительный теплообменник а четвертый – с полостью управления предохранительного клапана непрямого действия вход которого подключен к выходу обратимой гидромащины а выход – ко второму входу теплообменника гидросистемы.4. Система по п.2 отличающаяся тем что тепловой двигатель выполнен в виде установленных на одном валу компрессора пневмомотора топливного насоса и электростартера при этом выход компрессора и вход топливного насоса подключены к разным входам одной полости калорифера фреона а к разным входам другой полости калорифера фреона подключен вход компрессора и через дроссель – выход пневмомотора вход которого и выход топливного насоса подключены к разным входам теплообменника теплового двигателя причем параллельно топливному насосу установлен дроссель регулировки теплового двигателя.5. Система по п.2 отличающаяся тем что тепловой аккумулятор выполнен в виде теплоизолированной емкости.
3. Гидромеханическая система рекуперации энергии [№341515525-06. 30.03.1983. Е.И. Прочко. Московский автомобильный завод им. И.А. Лихачева. 32-82(088.8)]
Изобретение относится к машиностроительной гидравлике и может найти применение в закрытых гидросистемах мобильных и строительно-дорожных машин.
Известна гидромеханическая система рекуперации энергии содержащая приводной двигатель кинематически связанный с ним насос гидродвигатель сообщенный с насосом гидролиниями которые через обратные клапаны сообщены с насосом подпитки.
В данной системе применяется подача от насоса подпитки во всасывающую магистраль рабочей жидкости в количестве превышающем внутренние утечки гидросистемы. При этом происходит эффективное охлаждение магистралей быстрее обновляется рабочая жидкость в системе выносятся наружу воздух и продукты износа. Излишки рабочей жидкости подаваемой во всасывающую магистраль гидросистемы сливаются в бак через подпорный клапан обеспечивающий поддержание определенного давления во всасывающей магистрали.
Однако с ростом мощности гидросистемы и соответственно расхода рабочей жидкости подаваемой во всасывающую магистраль для подпитки и охлаждения возрастают потери энергии при сливе ее в бак через подпорный клапан так как здесь имеет место перепад давления и следовательно дросселирование потока. При этом энергия выделяемая при работе подпорного (сливного) клапана превращается в тепло и бесполезно рассеивается а также нагревает рабочую жидкость.
Наиболее близкой к предлагаемой по технической сущности является гидромеханическая система рекуперации энергии содержащая приводной двигатель кинематически связанный с ним насос гидродвигатель сообщенный с насосом гидролиниями которые через обратные клапаны сообщены с насосом подпитки и через гидроуправляемый клапан с баком при этом гидроуправляемый клапан выполнен с двумя полостями управления соединенными с гидролиниями.
В данной системе имеет место дросселирование потока и выделяемая при работе подпорного клапана энергия превращается в тепло что снижает КПД.
Цель изобретения - повышение КПД.
Указанная цель достигается тем что гидромеханическая система рекуперации энергии содержащая приводной двигатель кинематически связанный c ним насос гидродвигатель сообщенный с насосом гидролиниями которые через обратные клапаны сообщены с насосом подпитки и через гидроуправляемый клапан с баком при этом гидроуправляемый клапан выполнен с двумя полостями управления соединенными с гидролиниями содержит дополнительный гидродвигатель кинематически связанный с приводным двигателем и включенный в линии связи гидролиний с баком после гидроуправляемого клапана а насос подпитки выполнен переменной подачи. На рис. 1.3 представлена принципиальная схема системы.
Рисунок 1.3- Принципиальная схема гидромеханической системы рекуперации энергии
Система содержит приводной двигатель 1 кинематически связанный с ним насос 2 насос 3 подпитки обратные клапаны 4 и 5 основные гидролинии 6 и 7 гидродвигатель 8 гидроуправляемый клапан 9 дополнительный гидродвигатель 10 связанный валом 11 с приводным двигателем 1. Клапан 9 выполнен с двумя полостями 12 и 13 управления.
Система работает следующим образом.
При работе двигателя 1 насос 2 подает рабочую жидкость в гидролинии 6 или 7 (в зависимости от направления подачи) что приводит в действие гидродвигатель 8. При этом регулируемый насос 3 подпитки подает определенный расход с постоянным давлением для восполнения утечек и для охлаждения а также обновления рабочей жидкости во всасывающую магистраль через обратные клапаны 4 и 5. Излишки рабочей жидкости находящиеся в линии всасывания под давлением (обычно определенной величины) пройдя через клапан 9 поступают к гидродвигателю 10 где происходит выделение механической энергии возвращаемой с помощью вала 11 приводному двигателю 1. При этом баланс подаваемого в систему расхода подпитки и расхода сливаемого через гидродвигатель 10 поддерживается автоматически в результате сетевого объемного регулирования насоса 3 подпитки.
Применение предлагаемого изобретения повышает экономичность системы и ее общий КПД особенно при больших передаваемых мощностях.
Работоспособность надежность и безотказность эксплуатации кранов во многом зависят от состояния в металлических конструкциях. Долговечность работы кранов в основном обуславливаются состоянием металлоконструкции. Динамические нагрузки пагубно влияют на металлоконструкцию крана тем самым сокращая срок его службы. При переходе на гидрокинематическую систему рекуперации энергии снижаются динамические нагрузки на кран повышается его надежность и долговечность.
«ТЕХНИЧЕСКОЕ ОПИСАНИЕ КОЗЛОВОГО КОНТЕЙНЕРНОГО ПЕРЕГРУЖАТЕЛЯ»
В данном дипломном проекте рассматривается козловой контейнерный перегружатель грузоподъемностью 40 тонн который предназначен для вертикального перемещения контейнеров и их транспортировки в продольном и поперечном направлениях.
Контейнерный перегружатель используются для обслуживания крупных перегрузочных пунктов - морских портов контейнерных терминалов железнодорожных станций. Грузозахватным органом контейнерного перегружателя является специальный захват (спредер) с автоматическими зацепами под фитинги и рым-узлы контейнеров.
Козловой перегружатель состоит из следующих частей:
- металлической конструкции;
- главных механизмов;
- вспомогательного оборудования;
- электрооборудования;
- гидрооборудования.
Металлическая конструкция представляет собой мост (пролетное строение) по которому перемещается грузовая тележка и опоры (козлы). К мосту крана крепиться кабина управления механизмами крана.
Главные механизмы перегружателя:
- механизм передвижения тележки вдоль моста;
- механизм передвижения перегружателя по подкрановым путям .
Механизм передвижения перегружателя выполнен с раздельным приводом. На вал приводного колеса через открытую передачу ставится высокомоментный гидромотор который используется без дополнительной установки тормоза и редуктора. Грузовая тележка состоит из сварной рамы с установленными механизмами подъема груза и передвижения. Механизм подъема состоит из высокомоментного гидродвигателя барабана и полиспаста. (Для обеспечения при подъеме - опускании груза только его вертикального перемещения создания равномерной нагрузки на опоры барабана и благоприятных условий для нагружения пролетной части моста устанавливается сдвоенный полиспаст). Гидродвигатель соединен с барабаном при помощи зубчатой муфты. Механизм передвижения тележки выполнен с высокомоментным гидромотором который через открытую зубчатую передачу соединен с приводным колесом. Кабина крана предназначена для размещения аппаратов управления механизмами крана и является рабочим местом крановщика
Гидрооборудование крана состоит из гидромоторов гидронасосов регулирующей и предохранительной гидроаппаратуры бака с гидравлической жидкостью и трубопроводов.
Расчет и выбор основных энергетических характеристик приводов козлового контейнерного перегружателя.
1 Расчет механизма подъема.
Перегружатель козловой контейнерный.
Грузоподъемность () = 40 тонн
Скорость подъема груза () = 06 мc
Высота подъема груза () = 105 м
Группа режима работы (режим) 7М тяжелый [1] Cтр. 82 табл.2 по ГОСТ 25835-83.
1.1. Определение расчетного усилия действующего на канат.
Расчетное усилие в канате () при двух сдвоенных полиспастах в кН:
5 – коэффициент учитывающий неравномерность загрузки лебедок из-за возможного смещения центра массы загруженного контейнера; [3] Стр. 19
грузоподъемность перегружателя кН;
кратность полиспаста ;
; [5] Стр.271 табл.V.2.17.
КПД направляющих блоков
[5] Стр.271 табл.V.2.16.
Расчетное усилие в канате:
Диаметр стального каната определяется по разрывному усилию () в кН.
коэффициент запаса прочности (коэффициент использования каната) зависящий от назначения каната и режима работы.
Группа классификации режима работы механизма по ИСО 43011 М7 [1] стр.164 табл.20
Если кН то принимаем канат ЛК-Р о.с. (ГОСТ 2688-80)
у которого мм а [5] Стр.246 табл.V.2.3.
Канат грузового назначения принимаем правой крестовой свивки из светлой проволоки марки I нераскручивающийся с временным сопротивлением разрыву проволок МПа.
Канат 25 О-Г-I-Н-1568 (160) ГОСТ 2688-80.
ЭСКИЗПрофиль канавок для канатов.
мм мм мм [5] Стр.262 табл.V.2.13.
1.3. Определение диаметров блоков и барабана.
Диаметры блоков и барабана определяются в зависимости от диаметра каната типа грузоподъемной машины и режима ее работы.
Диаметр барабана () в мм по дну канавки:
коэффициент зависящий от типа грузоподъемной машины и режима ее работы.
[1] Стр.169 табл. 23.
Диаметр барабана и блоков округляют до большего десятка.
1.4. Определение длины барабана.
Барабаны применяются с винтовой канавкой и однослойной навивкой каната. Рабочее число витков зависит от высоты подъема груза кратности полиспаста диаметра
Шаг нарезки выбирается в зависимости от диаметра каната.
Длина барабана при двойной нарезке (правой и левой) () в мм.
расстояние между нарезками;
мм – длина ненарезанного участка.
Длина нарезной части () в мм:
рабочее число витков;
число запасных витков: ;
число витков на закрепление каната:
Рабочее число витков:
и диаметр барабана и каната м;
кратность полиспаста.
Длина нарезной части:
1.5. Расчет стенки барабана на прочность.
Напряжение сжатия в МПа
расчетное усилие в канате Н;
толщина стенки и шаг нарезки мм
Допускаемые напряжения можно принимать:
Выбираем Сталь 35ЛII ГОСТ 977—75 . [4] Стр.28 табл. I.1.10.
Напряжения от изгиба:
наибольший изгибающий момент Нм.
момент сопротивления поперечного сечения барабана мм;
внутренний диаметр барабана
Изгибающие напряжения МПа:
Напряжения от кручения МПа:
Полярный момент сопротивления барабана м3:
Напряжения от кручения:
Результирующее напряжение для стальных барабанов:
напряжение от изгиба МПа;
напряжение от кручения МПа.
1.6. Определение частоты вращения барабана.
1.7. Определение угловой скорости барабана.
1.8. Определение крутящего момента на барабане.
1.9. Определение мощность привода.
Статическая мощность привода механизма подъема:
номинальная грузоподъемность перегружателя кН
- скорость подъема мс
Характеристика привода механизма подъема.
Статическая мощность привода кВт
Расчетное усилие в канате кН
Диаметр барабана лебедки мм
Частота вращения барабана обсек
Угловая скорость барабана с
Крутящий момент на барабане Нм
2. Расчет механизма передвижения перегружателя.
Скорость передвижения перегружателя мc
2.1.Сопротивление трения скольжения в цапфах колес и трения качения колес о рельс Н.
сопротивление трения скольжения в цапфах колес и трения качения колес о рельс Н.
масса крана принимая по справочным данным крана аналога кг с корректировкой на измененные параметры.
масса груза и грузозахватного устройства соответствующая номинальной грузоподъемности крана кг.
ускорение свободного падения мс;
коэффициент сопротивления движению:
коэффициент трения качения в цапфах колес.
и диаметр колеса и его цапфы мм
В зависимости от нагрузки в кранах мм и ;
Принимаем [5] Стр. 319 табл. V.2.47.
Крановое двухребордное колесо диаметром мм и шириной катания мм:
К2Р 710×150 ГОСТ 3569 74;
коэффициент учитывающий дополнительные сопротивления в ребордах и ступицах колес при перекосах;
если колеса на подшипниках качения [3] стр.34
2.2. Ветровая нагрузка на кран Н.
динамическое давление ветра;
коэффициент учитывающий изменение динамического давления по высоте;
[4] Стр. 55 табл. I.2.14.
коэффициент аэродинамической силы;
коэффициент перегрузки;
расчетная площадь элемента конструкции;
м[4] Стр. 54 табл. I.2.10.
2.3. Сопротивление вызванное уклоном пути Н.
( плюс движение на подъем минус движение под уклон)
силы тяжести с учетом его подъемной силы Н
Силы тяжести с учетом подъемной силы:
Сопротивление вызванное уклоном пути:
2.4.Сопротивление передвижению крана на прямолинейном рельсовом пути Н.
сопротивление трения скольжения в цапфах колес и трения качения колес о рельс Н;
сопротивление вызванное уклоном пути Н.
ветровая нагрузка на кран Н.
2.5.Расчет необходимого числа ходовых колес в балансирной тележке:
максимальная нагрузка на опору кН;
Допускаемая нагрузка на одно колесо принимается в пределах кН.
грузоподъемность кг;
коэффициент учитывающий неравномерность нагрузки на опоры крана.
2.6.Проверка ходовых колес на отсутствие буксования.
Для отсутствия буксования необходимо чтобы сила сцепления приводных колес с рельсом была больше тягового усилия на их ободе
коэффициент сцепления приводных колес с рельсом;
суммарная нагрузка на приводные колеса. Н:
число приводных колес
число ходовых колес
Суммарная нагрузка на приводные колеса:
Тяговое усилие на ободе приводных колес Н.
сопротивление трения в приводных колесах (холостых) колесах;
сила инерции поступательного движения масс.
Сопротивление трения в приводных (холостых) колесах :
коэффициент сопротивления движения без учета дополнительных сопротивлений от перекоса тележки с приводными колесами.
Коэффициент сопротивления:
скорость передвижения мc;
2.7.Определение мощности двигателя:
число двигателей для кранов Q свыше 5т
2.8. Частота вращения приводного двигателя:
Механизм передвижения перегружателя исполнены без редукторов с высокооборотными гидромоторами.
Крутящий момент на валу двигателя:
Характеристика привода механизма передвижения перегружателя:
Мощность двигателя кВт
Частота вращения вала двигателя обсек
Угловая скорость вала двигателя
3.Расчет механизма передвижения тележки перегружателя.
Грузоподъемность () = 40 тонн.
Скорость передвижения тележки мc
3.1.Сопротивление трения скольжения в цапфах колес и трения качения колес о рельс Н.
масса тележки крана принимая по справочным данным крана аналога кг с корректировкой на измененные параметры.
Принимаем: Диаметр колеса:мм . [5] Стр. 319 табл. V.2.47.
Крановое одноребордное колесо диаметром мм и шириной катания мм:
К1Р 400×100 ГОСТ 3569 74;
3.2. Ветровая нагрузка на тележку.
3.3. Сопротивление вызванное уклоном пути.
Силы тяжести с учетом его подъемной силы:
3.4. Сопротивление передвижению тележки на прямолинейном рельсовом пути Н.
3.5 Расчет необходимого числа ходовых колес в балансирной тележке
Допускаемая нагрузка на одно колесо принимается в пределах кН
коэффициент учитывающий неравномерность нагрузки на опоры тележки.
Максимальная нагрузка на опору:
3.6. Проверка ходовых колес на отсутствие буксования.
суммарная нагрузка на приводные колеса. Н.
число приводных колес
Тяговое усилие на ободе приводных колес Н:
Сопротивление трения в приводных колесах (холостых) колесах:Н
Тяговое усилие на ободе приводных колес:
3.7. Определение мощности двигателя:
3.8 Частота вращения приводного двигателя:
Характеристика привода механизма передвижения тележки перегружателя.
Описание гидравлической схемы перегружателя.
Гидравлическая схема крана состоит из:
– основной регулируемый насос;
– подпиточный насос;
16 – напорные фильтры;
17 20 27 – обратные клапаны;
22 28 – золотниковые распределители с электрогидравлическим управлением;
а-5б 23а-23б 29а-29б – магниты электрогидравлического управления;
– управляемые обратные клапана (гидрозамки);
– гидромотор механизма подъема;
– гидромотор механизма передвижения тележки;
- гидромоторы механизма передвижения крана;
18 – распределитель с управлением от электромагнита с пружинным возвратом;
26 36 – подпорные клапана;
– дроссель (регулятор потока);
– дроссельный регулятор основной скорости опускания;
– напорный золотник;
– аккумулятор гидравлический;
– дроссельный регулятор малой посадочной скорости;
- дроссельный регулятор скорости движения тележки;
32 – делители потока (спаренные гидромоторы);
- дроссельный регулятор скорости;
- дроссельный регулятор с дросселем обеспечивающим установившуюся скорость движения крана;
38 – предохранительные клапана;
I – напорная линия;
II – 1-ая сливная магистраль (подъем);
III - 2-ая сливная магистраль (опускание).
Работа механизма подъема:
Рабочая жидкость подается регулируемым насосом (1) из гидробака (39) к распределителю (4) с электрогидравлическим управлением через фильтр (2) и обратный клапан (3). Ограничение максимального давления в системе осуществляется предохранительным клапаном (37) непрямого действия. При включении распределителя (4) на подъем магнитами (5а-5б) жидкость проходя управляемый клапан (6) и открывая его силой своего давления поступает в гидромотор механизма подъема (7) вращая его. Регулирование скорости подъема осуществляется регулированием подачи насоса. Слив из гидромотора механизма подъема (7) происходит через управляемый клапан (8) открываемый давлением напорной магистрали (I) проходит через распределитель с электрогидравлическим управлением (4) и по 1-ой сливной магистрали (II) через золотниковый распределитель (9) и подпорный клапан (10) сливается в бак. Для обеспечения плавного торможения в конце подъема переключаем распределитель (9) на линию с дросселем (11) в 1-ой сливной магистрали (II). Окончательное торможение и остановка происходит переключением распределителя (4) в среднее положение и запиранием гидрозамков (6 и 8).
Опускание происходит под действием собственного веса груза а заполнение холостой полости гидромотора (7) осуществляется с помощью вспомогательного насоса (15). Слив жидкости из рабочей полости гидромотора (7) под давлением происходит через гидрозамок (6) который принудительно открывается под действием давления жидкости идущей на заполнение холостой полости гидромотора (7) через дроссельный регулятор скорости (12) и напорный золотник (13). При опускании груза то жидкость поступает в гидравлический аккумулятор (14) и заряжает его. Вспомогательный насос (15) включается одновременно с переключением электромагнитов (5а-5б) на распределителе (4) на опускание и через фильтр (16) обратный клапан (17) золотниковый распределитель (18) и обратный клапан (20) рабочая жидкость поступает в полость гидромотора (7).
Как только аккумулятор зарядится срабатывает реле давления (21) переключая напорный золотник (13) и рабочая жидкость движется через золотниковый распределитель (18) обратный клапан (20) заполняя нерабочую полость гидромотора (7).
Торможение и выход на посадочную скорость осуществляется переключением золотникового распределителя (18) на линию с дроссельным регулятором потока (19). Остановка происходит переключением распределителя (4) в среднее положение.
Работа механизма передвижения тележки:
При разгоне: если гидравлический аккумулятор (14) заряжен то рабочая жидкость из него поступает через распределитель с электрогидравлическим управлением (22) в гидромотор (24) определяя требуемое его вращение тем самым осуществляя передвижение тележки. Реверсирование направления движения тележки осуществляется с помощью распределителя (22). Слив из гидромотора идет через дроссельный регулятор скорости (25) настройка которого определяет скорость движения тележки через подпорный клапан (26) в бак. Когда давление в аккумуляторе снизится до отключения реле давления (21) дальнейшее передвижение тележки будет осуществляться с помощью вспомогательного насоса (15) который через фильтр (16) обратный клапан (27) напорный золотник (13) распределитель (22) подает рабочую жидкость в гидромотор (24) или в гидромоторы 30 (12).
Торможение тележки осуществляется просто переключением распределителя (22) в среднее положение а скорость движения настраивается регулятором скорости (25).
Работа механизма движения перегружателя:
Для обеспечения синхронизации движения перегружателя на длинных линиях магистрали требуется синхронизация потоков в напорной и сливной магистралях поэтому устанавливаем два магнитных делителя потока (2 спаренных гидромотора). Если аккумулятор заряжен то рабочая жидкость из него поступает через распределитель с электрогидравлическим управлением (28) и машинный делитель потока состоящий из двух параллельно установленных одинаковых гидромоторов 31 (12) с объединенными валами обеспечивающих синхронную работу гидромоторов 30 (12) тем самым осуществляя движение крана. Реверсирование направления движения крана осуществляется с помощью распределителя (28). Когда давление в аккумуляторе снизится до отключения реле давления (21) дальнейшее передвижение крана будет осуществляться с помощью вспомогательного насоса (15) который через фильтр (16) обратный клапан (27) напорный золотник (13) распределитель (28) машинные делители потока 31(12). Слив происходит через машинные делители потока 32 (12)3 распределитель (28) регулятор потока (33) и подпорный клапан (36).
Дроссельный регулятор скорости потока (33) имеет переход на пониженную скорость с установившейся скорости движения крана с помощью переключения соответствующего из дросселей (34) или (35).
Остановка осуществляется переключением распределителя (28) в исходное (среднее) положение.
В гидросистеме применяется масло ВМГЗ.
Характеристика масла ВМГЗ:
Кинематическая вязкость сСт
при t = 50°С – не менее 10 при t = -50°С - не более 1250
Расчет и выбор гидрооборудования перегружателя.
Для гидроприводов подъемно-транспотных машин выбирают номинальное давление в диапазоне МПа.
В нашей гидросистеме выберем МПа. Перепад давления на гидромоторах устанавливается на 10-20% меньше номинального.
Тогда установим ΔМПа это меньше на 15%.
Определение рабочего объема гидромоторов:
момент сопротивления приведенный к валу гидромтора Нм
момент инерции приведенный к валу гидромотора кгм
масса линейно движущихся частей кг
момент инерции вращающихся частей кгм
скорость линейно движущихся масс мc
угловая скорость вращающихся масс с
угловая скорость звена приведения с
Для механизма подъема:
Грузоподъемность () = 40 тонны.
Угловая скорость барабана
Момент сопротивления кНм на валу приводного двигателя.
Рабочий объем гидромотора:
Для механизма передвижения перегружателя:
Моментами инерции колес и муфт условно пренебрегаем в связи с их незначительностью.
Рабочий объем гидромоторов:
Для механизма передвижения тележки перегружателя:
В соответствии с полученными рабочими объемами по каталогу подбираем следующие гидромоторы радиально-поршневые типа МРФ- 25М1:
Для механизма подъема
Для механизма передвижения перегружателя
Для механизма передвижения тележки перегружателя
Основные технические данные гидромоторов.
Рабочий номинальный объем см
Частота вращения с(обмин)
Расход номинальный лмин
Давление на входе МПа (кгссм)
Давление на выходе МПа (кгссм)
Номинальный перепад давления МПа
Максимальное давление дренажа МПа (кгссм)
Гидромеханический КПД % не менее
Масса (без рабочей жидкости) кг не более
Номинальная мощность кВт
Крутящий момент Нм(кгсм)
Габаритные и присоединительные размеры гидромотора МРФ-160025М1.
Габаритные и присоединительные размеры гидромоторов
Необходимо провести перерасчет давления в соответствии с реальными объемами
подобранных гидромоторов:
Для механизма передвижения тележки:
Расчет расхода жидкости в напорной гидролинии.
Где рабочий объем гидромоторов м
частота вращения вала гидромотора обсек
объемный КПД гидромотора
Расчет и выбор гидравлического аккумулятора.
Максимальный объем жидкости который можно будет «загнать» в аккумулятор при опускании груза с максимальной высоты:
рабочий объем гидромоторов м
число оборотов барабана механизма подъема при опускании груза с максимальной высоты
высота подъема груза м;
кратность полиспаста
диаметр барабана м м
м рабочий объем гидромотора механизма подъема.
Т.к. при проектировании мы используем систему с рекуперацией энергии то энергии накопленной при опускании груза с максимальной высоты должно хватить на перемещение тележки перегружателя и перегружателя.
Объем аккумулятора способного обеспечить поставленное выше условие:
L – путь пройденный тележкой (перегружателем) м;
Vо – суммарный рабочий объем двигателей механизма передвижения тележки (перегружателя);
Dk – диаметр колеса м
Для тележки перегружателя:
По каталогу [6] выбираем аккумулятор АРМ-100.32.
Технические характеристики аккумулятора.
Максимальный расход рабочей жидкости дмс
В гидроприводе перегружателя будем использовать батарею из трех аккумуляторов.
Для механизма подъема и передвижения тележки перегружателя: Расход =960+141=1101 лмин
Выбираем регулируемый аксиально-поршневой насос с механизмом управления типа НАД с регулятором мощности ис постоянным направлением потока масла .
Насос выбираем по каталогу [7] .
Техническая характеристика насоса.
Давление на выходе МПа
Давление на входе МПа
Масса без рабочей жидкости кг
Максимально допустимое давление в дренажной линии 005 МПа
Выбор гидроаппаратуры.
Выбор золотниковых распределителей:
Из [8] выбираем золотниковые распределители типа РН 323 АЛ575А.
Клапана выбираем по номинальному давлению и расходу жидкости в напорной гидролинии.
Выбираем управляемые обратные клапаны (гидрозамки): М2КУ 2032 [7] стр.134.
Выбираем предохранительный клапан: 32-32-2-131 – предохранительный клапан непрямого действия нормально – открытого исполнения с магнитом переменного тока 110В.
Выбор регуляторов потока:
Выбираем регуляторы потока: ПГ 5135 МПГ 5535 МПГ 5536 стр. 174 [7].
Выбор машинных делителей потока:
Машинные делители потока выбирают по расходу жидкости в напорной гидролинии механизма передвижения крана.
Выбираем машинный делитель потока: МГП 160.
Выбираем фильтр 4ФГМ 32-25К стр.312 [7].
Выбор реле давления:
Выбираем реле давления РГ 62 -11.
Построение графоаналитических характеристик приводов.
1.Построение характеристики насоса.
номинальное давление развиваемое насосом МПа.
номинальный расход насоса
Принимаем и из (1) получаем:
Для построения характеристика насоса имеем две точки:
2.Построение характеристики предохранительного клапана.
Откладываем по оси давления от вверх МПа и строим характеристику предохранительного клапана.
3.Построение характеристики потерь.
Где сумма потерь на гидроаппаратуре.
Для механизма подъема.
Для механизма передвижения крана.
Для механизма передвижения тележки.
По полученным значениям в программе Microsoft Excel вычисляем значения давления в зависимости от расхода. Полученные данные заносим в таблиц.
Механизм передвижения перегружателя
Механизм передвижения тележки перегружателя
По полученным значениям строим графики в координатах “P-Q”.
Расход обеспечивающий требуемые скорости:
Описание электросхемы управления перегружателем и выбор электродвигателя.
1. Выбор электродвигателя.
Построив циклограмму работы перегружателя определили ПВрасч механизма подъема: ПВрасч=83%.
Необходимая мощность электродвигателя для основного насоса :
номинальное давление в гидроприводе;
номинальный расход жидкости;
Мощность электродвигателя для основного насоса:
Расчетная относительная продолжительность включения не соответствует стандартной полученное значение мощности приводится к ближайшему стандартному ПВст.
Выбираем крановый асинхронный двигатель с короткозамкнутым ротором типа MTKF:
Технические характеристики двигателя серии МТКF.
Скорость вращения обмин
Максимальный момент Нм
Момент инерции ротора кгм
Проверка электродвигателя на перегрузочную способность:
- максимальный вращающий момент электродвигателя.
максимально допустимое значение момента сопротивления электродвигателя.
2. Описание электрической схемы управления перегружателем.
В качестве электрической схемы рассмотрим пускатель бесконтактный нереверсивного типа ПБН-160 предназначен для обеспечения плавного нарастания напряжения на обмотке статора электродвигателя и ограничения пускового тока.
2.1Условия эксплуатации
Температура окружающего воздуха – от –10 до +45°С. Окружающая среда невзрывоопасная не содержащая агрессивных паров и газов в концентрациях разрушающих металл и изоляцию и снижающих параметры пускателей в недопустимых пределах не насыщенная токопроводящей пылью и водяными парами.
Требования техники безопасности соответствуют ГОСТ 12.2.007.7-83. Пускатели для стран СНГ соответствуют ТУ16-95 ИЖТП.648300.001 ТУ.
Эксплуатацию пускателя необходимо производить в соответствие с «Правилами технической эксплуатации электроустановок потребителей» и настоящим руководством.
Техническое обслуживание производится при полном отключении пускателя от питающей сети и выполнении организационно-технических мероприятий обеспечивающих безопасность работ.
При обслуживании проверить надежность крепления узлов надежность контактных соединений состояние заземления.
трехфазная с глухозаземленной нейтралью
Время нарастания напряжения с
кнопки «Пуск» и «Стоп»
)пуск – наличие напряжения 220 В
)стоп – отсутствие напряжения
Содержание драгоценных металлов г
2.2 Устройство и принцип работы пускателя
Пускатель представляет собой тиристорный регулятор с цифровой системой управления на интегральных микросхемах обеспечивающий плавное изменение выходного напряжения по принципу фазового регулирования. Плавное изменение (повышение) напряжения позволяет разгонять электродвигатели пониженными пусковыми токами и защищает механические части приводного механизма от ударных моментов.
2.3 Алгоритм работы пускателя
Подается команда «Пуск» на включение пускателя.
Пускатель обеспечивает нарастание пускового напряжения на статорной обмотке двигателя от 108 до 45 с.
По команде «Стоп» снимаются управляющие импульсы с силовых тиристоров тиристоры закрываются.
Останов электродвигателя осуществляется на свободном выбеге (естественное торможение).
2.4 Конструкция пускателя и его составных частей
Конструктивно пускатель выполнен в виде блока одностороннего обслуживания.
Особенностью конструкции является применение общего охладителя на котором размещены:
устройство защиты электродвигателей типа УЗ-ЭД-26ИВ;
трансформатор типа ТПП-288-127220-50;
платы питания и фильтров и силовые тиристорные модули (3 штуки).
На поворотной раме расположена плата управления и плата импульсных трансформаторов. Благодаря наличию поворотной рамы обеспечен доступ ко всем элементам схемы.
Пускатель закрыт кожухом который имеет дверцу.
2.5 Работа пускателя и его составных частей
Рис.7.2.5. Схема подключения
После команды «Пуск» реле КV1 или КV2 замыкает свои контакты и подает 27 В на клемму 2 «зап» (ХТ4:2) платы управления. Начинается процесс пуска. Загорается лампа «Разгон». После отработки заданной команды реле К1 (на плате управления) перебрасывает свой контакт. Поступает команда (+27) на клемму «откр» (ХТ4:1) платы управления. Тиристоры полностью открыты. Загорается лампа «Работа».
Во время запуска работа блока защиты блокирована т.к. может сработать защита «фазировка» из-за прерывистых пусковых токов.
2.6 Технические данные
Электропитание от сети 50 Гц 220 В;
Ток потребления не более 25 мА (активная потребляемая мощность не более 2 Вт);
Переменный ток коммутируемый устройством по цепи управления до 2 А при напряжении от 127 до 380 В;
Кратковременные токовые перегрузки по цепи управления до 4 А;
Диапазон уставок тока срабатывания защиты от 20 до 680 А с шагом 4 А;
Предельная погрешность токов уставки ±5 %;
Диапазон уставок времени срабатывания защиты от 2 до 17 с с шагом 1 с. Параметр нормируется при тридцатипроцентной перегрузке по току (при шестикратной перегрузке время срабатывания в два раза меньше);
Погрешность времени срабатывания защиты от выставленного значения не более ±25 %;
Порог срабатывания защиты по перекосу фаз:
- по току (35±4)% от тока уставки
- по углу (20±3)° при токах уставки;
Порог контроля сопротивления изоляции 500 кОм (на отключение (400±50) кОм на восстановление (500±50) кОм).
Дополнительные поддиапазоны порога 100 кОм и 200 кОм;
Время блокировки сброса фиксации аварийного срабатывания защиты (20±5) с;
Габаритные размеры устройства не более 120х120х55 мм;
Номинальная чувствительность по входу датчиков 03 мВА.
2.7 Устройство защиты электродвигателя
Устройство защиты электродвигателей УЗ-ЭД-26ИВ предназначено для эффективной защиты трехфазных асинхронных электродвигателей (ЭД) мощностью от 10 до 320 кВт. Устройство содержит два выносных малогабаритных датчика тока и обеспечивает:
блокировку включения ЭД при снижении сопротивления изоляции его обмоток ниже установленного порогового значения;
отключение ЭД при механических перегрузках при чрезмерном перекосе фазных токов обрыве фазы изменении чередования фаз;
индикацию пониженного сопротивления изоляции ЭД;
динамическую индикацию токовой перегрузки ЭД;
динамическую индикацию перекоса фазных токов ЭД;
статическую индикацию аварийного срабатывания устройства защиты;
блокировку возможности быстрого повторного пуска ЭД сразу после аварийного срабатывания защиты (задержку сброса фиксации аварии);
возможность переключения порога срабатывания по току для каждой контролируемой фазы независимо (легко позволяет проверить работоспособность фазного канала устройства);
возможность переключения быстродействия защиты;
возможность переключения порога по сопротивлению изоляции;
нормируемые точностные характеристики и простоту монтажа;
долговременную стабильность параметров в широком диапазоне внешних климатических воздействий.
2.8 Плата источника питания
Плата источника питания должна на выходе выдавать стабилизированное напряжение +27±05 В при изменении входного напряжения на ±30 % Uс. Ток нагрузки источника равен 12 А.
С трансформатора питания на клеммник ХТ1 поступает напряжение Uвх = 40 В (см.чертеж «Пускатель типа ПБН. Схема электрическая»). С клеммника данное напряжение поступает на диодный мост VD1. На выходе моста через сглаживающий фильтр (С1 С4 R1 R4 VD2 VD3) напряжение поступает на стабилизатор (DА1 VT1 VT4 VD4 VD6 R6 R11). На выходе платы источника питания находится фильтр (VD7 VD8 L1 C6 C7 R12 R13). С помощью сопротивления R12 выставляется напряжение на выходе равное +27 В. Светодиод VD9 сигнализирует наличие напряжения на выходе платы источника питания.
Схема электрическая платы фильтров состоит из варисторов (RU1 RU3) емкостей (С1 С3) резисторов (R1 R6) и подключается по входу пускателя. С платы фильтров напряжение поступает на схему синхронизации платы управления (А5).
2.10 Плата импульсных трансформаторов
Схема платы импульсных трансформаторов согласует сигналы управления тиристора с входящими а также гальванически их развязывает посредством импульсных трансформаторов.
2.11 Плата управления
Плата управления обеспечивает формирование управляющих импульсов на шесть тиристоров (на положительную и отрицательную полуволну каждой фазы отдельно) по заданному закону. Также плата обеспечивает полное открытие тиристоров включение которых происходит по окончанию разгона. Работа платы возможна в режимах разгона двигателя (плавного увеличения напряжения) и полного открытия тиристоров.
Выходными сигналами платы являются шесть сигналов управления тиристорами (А+ А- В+ В- С+ С-) которые подаются на плату импульсных трансформаторов. Амплитуда выходных импульсов составляет приблизительно 25 В (тип выхода – открытый коллектор) период импульсов заполнения – 128 мкс скважность импульсов заполнения – два. В плате также имеется релейный выход индицирующий окончание разгона. Выход допускает подключение нагрузки напряжением до ~250 В током до 2 А. Состояние выхода индицируется светодиодом VD1 на плате.
Входными сигналами платы являются три сигнала синхронизации (по каждой фазе). Величина напряжения сигналов синхронизации равна приблизительно половине фазного напряжения питания силовой части устройства плавного пуска форма синусоидальная. Также входными сигналами являются логические сигналы «Пуск» и «Открытие тиристоров». По сигналу «Пуск» начинается цикл разгона в конце цикла разгона подается сигнал на полное открытие тиристоров.
Вход «Открытие тиристоров» имеет более высокий приоритет перед входом «Пуск» таким образом если в процессе разгона подать сигнал «Открытие тиристоров» тиристоры будут немедленно полностью открыты. Состояние входов индицируется светодиодами «Пуск» и «Открытие тиристоров» на плате.
Плата управления включает в себя систему импульсно-фазового управления (СИФУ) и устройство формирования характеристики разгона с входной логикой.
Система импульсно-фазового управления платы состоит из трех двухканальных устройств синхронизации выделяющих переход через ноль и полярность напряжения каждой фазы; шести счетчиков угла открытия тиристоров определяющих момент открытия тиристоров относительно перехода через ноль; трех двухканальных модуляторов осуществляющих наложение импульсов высокочастотного заполнения и формирование сигналов полного открытия тиристоров минуя счетчики угла; и шести выходных усилителей обеспечивающих необходимую мощность выходных сигналов для подачи на плату импульсных трансформаторов.
Устройство формирования разгона работает по принципу ступенчатого увеличения угла открытого состояния тиристоров. Полупериод синхронизирующего напряжения разбивается по времени на 128 равных участков (ступеней) таким образом одна ступень приблизительно равна 14 эл.град. (рис.7.2). Разгон производится от начальной ступени (Sнач) до конечной (Sок). На каждой ступени разгон производится в течение определенного времени (времени такта Тm) таким образом полное время разгона составляет Тразг = Тm(Sок – Sнач).
Рис.7.2.11. Кривая U(t)
Начальная ступень разгона определяет напряжение подаваемое на ЭД в начале разгона и подбирается по моменту плавного трогания ЭД без значительной выдержки времени. Оконечная ступень подбирается по выходу ЭД на номинальные обороты до начала колебательных процессов обусловленных характеристикой асинхронного ЭД. При достижении оконечной ступени формируется сигнал на включение шунтирующего контактора и на ступени Sок+1 происходит снятие управляющих импульсов с тиристоров.
В плате предусмотрена возможность оперативного изменения номеров ступеней начала и окончания разгона и времени такта ступени с помощью DIP-переключателей. Изменять положение переключателей допускается без отключения питающего напряжения платы.
При установке всех переключателей переключателя SА3 в положение OFF на выходе пускателя устанавливается напряжение соответствующее углу открытия α на данный момент времени. Угол α при этом в дальнейшем не меняется.
Устройство формирования разгона состоит из генератора с предварительным счетчиком формирующим все необходимые для работы платы частоты в том числе и частоту высокочастотного заполнения выходных импульсов; счетчика номера ступени с переключателями задания начальной и оконечной ступени и времени такта формирующего код номера ступени от начальной до оконечной; генератора частоты для счетчиков угла открытия тиристоров подаваемый на СИФУ и пропорциональный коду номера ступени; входной логики обеспечивающей обработку входных сигналов «Пуск» и «Открытие тиристоров» с необходимыми задержками; выходного усилителя и реле выхода управления К1.
2.12 Порядок работы.
Подключить пускатель согласно схеме подключения. Установить на устройстве защиты следующие параметры:
ток уставки выставлять по номинальному току нагрузки т.к. на блоке защиты установлены шунты рассчитанные на протекание по ним тока равного 20 % от номинального;
время срабатывания устройства;
порог сопротивления изоляции.
Включить RF1 включая лампы HL1 и HL2 расположенные на дверце пускателя.
При импульсном управлении кнопкой S3 включается реле KV1 и подается команда на запуск пускателя. Отключение пускателя осуществляется кнопкой «стоп» – S2.
При потенциальном управлении замыкается тумблер S1. Включается реле KV2 и подает команду на запуск пускателя. Размыкание тумблера равнозначно команде «Стоп».
Прочностной расчет металлоконструкции.
1. Проектирование пролетных (главных) балок моста.
1.1. Выбор генеральных размеров пролетной балки.
Выбираем необходимую высоту балки в среднем сечении из условия :
Высота балки в среднем сечении:
Выбранную высоту Н округляем до стандартной ширины прокатного листа:
Высота продольной балки в месте примыкания ее к концевой балке
Для снижения массы продольной балки на концах делаются скосы длиной С.
Высота стенки балки:
Шаг основных диафрагм:
Высота дополнительных диафрагм:
(но не менее 0004 м )
Толщина верхнего пояса:
Толщина нижнего пояса:
Ширина балки или но не менее 03 м ( по технологическим соображениям) :
Принимаем ширину балки :
Величина свесов (полок):
Ширина балки со свесами:
Рисунок 8.1. – Необходимая высота балки в среднем сечении
Рисунок 8.2. – Дополнительные размеры балки
2. Поверочный расчет на прочность и жесткость балки моста.
2.1. Вычисление геометрических характеристик поперечного сечения балки.
Все геометрические характеристики поперечного сечения балки будем считать в предположении о том что сечение имеет две оси симметрии.
Вычисляем осевой момент инерции сечения относительно центральной оси Z:
Осевой момент сопротивления сечения:
2.2.Определение интенсивности распределенной нагрузки действующей на продольную балку.
Собственная масса продольной балки значительна. Чтобы учесть ее влияние на изгиб балки вычислим интенсивность распределенной нагрузки q.
где сила тяжести продольной балки.
где А — площадь поперечного сечения балки
k=16 — коэффициент учитывающий массу настила диафрагм подтележечного рельса трансмиссии.
удельный вес материала балки.
2.3. Определение расчетной нагрузки на крюке.
В процессе эксплуатации металлоконструкция крана испытывает динамические нагрузки обусловленные работой механизма подъема груза. Этот факт учитывается динамическим коэффициентом . Таким образом динамическая нагрузка на крюке:
Необходимо рассматривать два случая динамического нагружения :
а) Отрыв груза от основания (подъем с подхватом).
b)Случай экстренного торможения механизма подъема.
Динамический коэффициент определяется как:
где коэффициент неполноты расчета ()
скорость подъема груза.
параметр зависящий от жесткости и массы деформируемой конструкции.
Для случая подъема груза:
где статический прогиб балки от массы поднимаемого груза Q.
Здесь коэффициент 2 стоящий в знаменателе учитывает число балок работающих на изгиб.
статическое удлинение канатов при подъеме груза Q.
Где суммарная площадь поперечного сечения проволок каната (учитывает все ветви каната).
модуль упругости каната равный МПа.
может быть выведена из следующего условия:
Учитывая эти условия принимаем .
приведенная масса пролетной части моста.
коэффициент жесткости моста.
Тогда при подъеме груза:
При экстренном торможении:
Для определения расчетной величины динамического коэффициента принимается большее из двух значений т.е. .
Таким образом динамическая нагрузка на крюке:
2.4. Поверочный расчет на прочность при изгибе среднего сечения продольной балки.
Наиболее опасное положение грузовой тележки посредине пролета моста. Распределение нагрузки на колеса тележки принимаем равномерным т.е.
Где динамическая реакция на колесе тележки.
Расчетная схема продольной балки моста:
Для большей ясности эпюры изгибающих моментов от распределенной нагрузки и от сосредоточенных сил построены отдельно.
Наибольший изгибающий момент:
Проверяем условие прочности:
где МПа для материала балки Ст3.
Условие прочности выполняется т.к.
2.5.Поверочный расчет на прочность при сдвиге опорного сечения пролетной балки.
Рассматриваем крайнее положение грузовой тележки (грузовая тележка по конструктивным особенностям не доходит до края балки на 1 1.5 м.) Учтем так же и вес кабины крановщика .
Таким образом расчетная схема в данном случае имеет вид:
Наибольшие касательные напряжения возникнут в сечении балки над опорой А.
Определим сначала величину реакции в этой опоре:
Максимальное значение касательных напряжений имеет место в вертикальных стенках балки на оси Z и определяется по формуле Журавского:
осевой момент инерции опорного сечения главной балки.
статический момент половины сечения.
Максимальное значение касательных напряжений:
Проверяем условие прочности: где .
3.Размещение ребер жесткости.
Ребра жесткости (поперечные основные поперечные дополнительные и продольные) должны обеспечивать геометрическую неизменяемость поперечного сечения балки местную устойчивость стенок и сжатых поясов а при расположении рельса по оси верхнего пояса прочность рельса и пояса при местном воздействии колес тележки.
Расчетными размерами являются:
высота отсека между сжатым поясом и продольным ребром;
расстояние между осями основных и дополнительных поперечных ребер (диафрагм и полу диафрагм);
толщины стенки и ребра жесткости.
При гибкости стенки для малоуглеродистых и для низколегированных сталей местная устойчивость стенки обеспечена если обеспечена ее прочность.
При гибкостях для малоуглеродистых и для низколегированных сталей достаточно устанавливать только основные диафрагмы (рис. 8.3.а)).
При для малоуглеродистых сталей и для низколегированных сталей необходимо устанавливать поперечные и одно продольное ребро жесткости (рис. 8.3.в) г)).
Следовательно: . Необходимо устанавливать поперечные и одно продольное ребро жесткости (соответствует размещению г)).
Рисунок 8.3. варианты установки ребер жесткости:
3.1.Размещение поперечных ребер (диафрагм).
Для отсеков примыкающих к опорам шаг основных диафрагм
В последующих отсеках их шаг можно увеличить до
При высоте балки более 700мм устанавливают диафрагмы (с отверстием).
В этом случае размер диафрагмы принимается равным:
Толщина диафрагмы принимается равной
Шаг диафрагм являющихся опорами для рельса проверяют из условия прочности последнего на изгиб.
Рельс подбираем по максимальной статической нагрузке на колесе.
Максимальная статическая реакция на колесе тележки:
Диаметр колеса: Rk=400мм
По табл. 3 выбираем типоразмер рельса.
Осевой момент сопротивления рельса: Wzp=17810-6 м3
Допустимые напряжения для рельса: p=250106 Па
Из условия прочности рельса:
Изгибающий момент в рельсе если колесо между диафрагмами:
Ширина подошвы рельса:
Длина площадки диафрагмы воспринимающей нагрузку от колеса тележки условно принимается по формуле:
Где ширина подошвы рельса;
Напряжения смятия торца диафрагмы:
Условие прочности на смятие:
Условие выполняется т.к.
3.2. Размещение продольных ребер жесткости.
Продольные ребра жесткости для стенок ставятся на расстоянии от крайней сжатой кромки стенки:
Момент инерции ребра относительно кромки пояса должен быть:
4. Проверка местной устойчивости стенок балки.
Рассмотрим расчет на местную устойчивость панели выделенной из среднего отсека балки.
Рисунок 8.4. – Эпюра на местную устойчивость панели по нормальным напряжениям
Коэффициент запаса устойчивости:
Где наибольшее напряжение от изгиба в центре балки.
нормативный коэффициент запаса местной устойчивости.
Устойчивость стенки балки в концевом сечении проверяют по касательным напряжениям.
Рисунок 8.5. – Эпюра устойчивости стенки балки по касательным напряжениям
Критическое касательное напряжение с учетом защемления стенок у поясов:
5. Проверка местной устойчивости сжатого пояса.
Панели верхнего пояса работают практически в условиях равномерного сжатия.
Критическое напряжение для равномерно сжатой панели в предположении замещения ее по двум сторонам:
6. Расчет сварного шва.
Наиболее нагруженный участок шва соединяющего пояс балки со стенкой расположен у концевого сечения.
Условие прочности имеет вид:
Где подсчитаны ранее.коэффициент зависящий от вида сварки
толщина углового шва принимаемая равной катету вписанного в сечение шва равнобедренного треугольника.
статический момент верхнего пояса балки относительно центра тяжести ее концевого сечения.
Условие прочности сварного шва:
- при однопроходной автоматической сварке:
Проходит 29 МПа 100 МПа
- при однопроходной полуавтоматической сварке:
Проходит 367 МПа 100 МПа
- При ручной или многопроходной автоматической и полуавтоматической сварке:
Проходит 42 МПа 100 МПа
- коэффициент принимаемый равным 1 для однопроходной автоматической сварки 08 – для однопроходной полуавтоматической сварки07- для ручной и многопроходной автоматической и полуавтоматической сварки.-толщина углового шва принимая равной катету вписанного в сечение шва равнобедренного треугольника (рис. 8.7.).
7. Проверка статической жесткости моста.
Допустимый прогиб продольной балки в середине пролета от действия статически приложенной подвижной нагрузки (груз + вес тележки) не должен превышать величины.
Максимальный статический прогиб:
Рисунок 8.8. Расчетная схема моста для определения максимального статического прогиба
8. Проверка динамической жесткости моста.
При резком разгружении крана мост начинает совершать колебательные движения в вертикальной плоскости. Время затухания колебаний ограничивается величиной и для упругой системы определяется по формуле:
Где период частоты собственных колебаний;
Где частота собственных колебаний;
Где приведенная масса моста
прогиб моста под действием единичной силы.
Должно выполняться условие:.
Технология изготовления стойки гидромотора
Для изготовления заготовок листов под стойку гидромотора применим гидроабразивную резку металла. Этот метод позволяет качественно резать не только любые металлы и сплавы включая труднообрабатываемые (нержавеющие и жаропрочные стали твердые и титановые сплавы) но и гранит керамику стекло в т. ч. огнеупорное и пуленепробиваемое резину бумагу войлок композитные и другие материалы.
Последовательность действий при построении технологического процесса.
Процесс вырезания заготовок
При гидроабразивной обработке резка металла производится струей воды смешанной с абразивом. Насос высокого давления подает воду под давлением 4150 атмосфер в режущую головку управляемую от системы ЧПУ. Вода перемешивается с абразивом и выбрасывается через фокусирующую трубку со скоростью 1200 мсек тонкой струей диаметром 1 мм способной разрезать металл толщиной до 300 мм.
Большая мощность струи обеспечивает резание а точнее разрушение твердой структуры на молекулярном уровне.
Резание металла можно производить почти во всех направлениях: оборудование позволяет получать любые контуры внутри и снаружи изделий а также острые углы отверстия и косые разрезы.
Вырезаем листы со следующими размерами:
-2 уголка 340х200х32 мм
При изучении чертежа детали нам необходимо учесть что все размеры выполняются свободно за исключением диаметров под отверстия которые выполняются с допуском 02 мм. А также необходимо чтобы все поверхности имели шероховатость 63 мкм по параметру Ra.
Выбираем заготовку с учетом размеров готовой детали. Выбираем толстолистовой прокат стали Ст5 ГОСТ 19903-74 длиной 1000мм шириной 500мм толщиной 60мм.
Далее осуществляем разметку заготовки для обработки торцевых поверхностей с использованием дисковой фрезы а также разметку отверстий.
Обработка торцевых поверхностей осуществляется дисковой фрезой диаметром и шириной при глубине .
Перед обработкой детали необходимо установить ее на рабочем столе на прокладки толщиной не менее и закрепить универсальными прижимами с трех сторон исключая обрабатываемую сторону.
После выполнения всех подготовительных операций приступаем к выполнению обработки заготовки.
2.Расчет припусков на механическую обработку и определение размеров заготовки.
Общий припуск z0 равен сумме всех промежуточных припусков zi. Поэтому для каждой обрабатываемой детали можно записать:
где - число технологических переходов при обработке детали путем их увеличения или уменьшения на величину общего припуска:
где - номинальный размер детали по чертежу
- общий припуск на обработку
Знак «+» в формуле ставится для охватывающих размеров а знак «-» - для охватываемых.
Запишем припуски на посадочную поверхность изготавливаемой детали:
где 2 – припуск на черновую обработку
– припуск на чистовую обработку
Определим размеры заготовки:
3. Структура технологического процесса.
Основой структуры технологического процесса является технологическая операция. Все технологические операции именуются по роду технологического оборудования на котором они выполняются. Все операции технологического процесса обозначаются номерами кратными пяти.
А. Установить закрепить и снять деталь.
Обработать торцы детали дисковой фрезой диаметром и шириной при глубине до чистовых размеров соответствующих размерам на чертеже.
Используя двуугловую симметричную фрезу диаметром и шириной фрезу снять фаску под сварку под углом 450 с торцевой стороны 1-1.
Сверление отверстий под крепеж осуществляется после выполнения сварочных работ.
По эскизу детали (рис.9.4) с использованием разметочных инструментов делаем разметку отверстий под болты диаметром .
Перед сверлением необходимо обработать торцевую поверхность чтобы торец был перпендикулярен оси и не имел вогнутости или выпуклости.
При изучении чертежа детали нам необходимо учесть что торцевые размеры выполняются свободно кроме стороны 2-2 которую вырезают по радиусу равному R=398мм а также диаметров под отверстия которые выполняются с допуском 02 мм. А также необходимо чтобы все поверхности имели шероховатость 63 мкм по параметру Ra.
Выбираем заготовку с учетом размеров готовой детали. Выбираем толстолистовой прокат стали Ст5 ГОСТ 19903-74 длиной 1000мм шириной 1000мм толщиной 100мм.
Для обработки торцевых поверхностей с использованием дисковой фрезы а также выполнения отверстий осуществляем разметку заготовки.
Обработка торцевых поверхностей выполняется в два прохода (с двух сторон) дисковой фрезой диаметром и шириной при глубине .
Перед обработкой детали необходимо установить ее на рабочем столе на прокладки толщиной не менее и закрепить универсальными прижимами с трех сторон исключая обрабатываемую сторону. После обработки торцов заготовки с одной стороны ее необходимо перевернуть закрепить и обработать вторую сторону аналогичным образом.
Расчет припусков на механическую обработку и определение размеров заготовки.
Запишем припуски на обрабатываемую посадочную поверхность изготавливаемой детали:
Структура технологического процесса.
Обработать торцы детали дисковой фрезой диаметром и шириной при глубине до размеров указанных на эскизе.
Обработка производится с двух сторон; в связи с чем после обработки детали с одной стороны ее необходимо перевернуть на другую сторону и повторить установ А.
Используя двуугловую симметричную фрезу диаметром и шириной снять фаску под сварку под углом 450 с торцевой стороны 3-3. 21>
Обработка производится с двух сторон; поэтому после обработки детали с одной стороны ее необходимо перевернуть на другую сторону закрепить и снять фаску под сварку аналогичным образом.
Используя цилиндрическую фрезу диаметром и длиной обработать торцевую сторону 2-2 по радиусу R=398мм как показано на рис. 7.9.
Используя концевую фрезу с цилиндрическим хвостовиком и длиной хвостовика рассверливаем предварительное отверстие для последующей расточки. 25>
Используя расточный резец с пластинами из твердого сплава с (ГОСТ 18882-73) габаритные размеры которого равны выполняем продольное растачивание сквозного отверстия D=230мм. Обработка осуществляется за 8 проходов. При последнем черновом проходе необходимо выдерживать припуск 25мм. Заключительный чистовой проход необходимо производить при учете припуска на чистовую обработку отверстия.
Шероховатость данной поверхности должна соответствовать 25 мкм по параметру Ra.
Используя расточный резец с пластинами из твердого сплава с (ГОСТ 18882-73) габаритные размеры которого равны выполняем поперечное растачивание глухого отверстия D=450мм. Обработка осуществляется за 4 проходов. Заключительный чистовой проход выполняется продольным растачиванием при учете припуска на чистовую обработку отверстия.
По чертежу детали с использованием разметочных инструментов делаем разметку 20 отверстий под болты диаметром и 6 отверстий под болты диаметром .
При изучении чертежа детали необходимо учесть что все размеры выполняются свободно. Все поверхности должны иметь шероховатость 63мкм по параметру Ra.
Выбираем заготовку с учетом размеров готовой детали. Выбираем прокат стали Ст5 ГОСТ 19903-74 длиной 450мм шириной 400мм толщиной 30мм.
Далее осуществляем разметку заготовки для обработки на фрезерном станке.
Обработка осуществляется дисковой фрезой диаметром и шириной при глубине .
Перед обработкой заготовки необходимо установить ее на рабочем столе на прокладки толщиной не менее и закрепить универсальными прижимами с двух сторон исключая обрабатываемую сторону.
Отрезать заготовку по разметке дисковой фрезой диаметром и шириной при глубине как указано на эскизе.
Отсечь углы на расстоянии 20мм по разметке дисковой фрезой диаметром и шириной при глубине как указано на эскизе.
Используя двуугловую симметричную фрезу диаметром и шириной снять фаску под сварку под углом 450 с торцевых поверхностей. 21>
Обработка осуществляется с двух сторон поэтому после выполнения фрезерных работ с одной стороны детали ее необходимо перевернуть закрепить и обработать вторую сторону аналогично первой.
Сборка узла крепления гидромотора.
Сборка узла осуществляется механизированной электрошлаковой сваркой.
Сборочные работы перед сваркой предусматривают правильное положение соединяемых деталей очистку кромок под сварку разметку временное скрепление деталей. Правильность соединения обеспечивают выверкой. А также необходимо обеспечить защиту всех отверстий путем их закрытия асбестовыми пробками.
Разметка под сварку а также временное скрепление деталей выполняются в соответствии со сборочным чертежом.
Очистку кромок под сварку от загрязнений осуществляют химическим методом: с помощью уайт-спирита ацетона спирта или других соединений удаляющих остатки масла влаги и т. п.
При сборке деталей необходимо обеспечить взаимную перпендикулярность деталей прижатие их друг к другу. Собранные элементы скрепляют прихватами выполненными из порошковой проволоки марки ПП-АН8 которые во время сварки полностью переплавляются.
При скреплении Детали№1 и Детали№2 взаимная перпендикулярность обеспечивается за счет использования в качестве средства крепления угольников. Для удержания деталей во взаимно перпендикулярном положении используют балки которые устанавливают под углом и слегка приваривают к Детали№2 чем обеспечивают устойчивость деталей. Таким образом используя прихваты и угольники мы обеспечиваем взаимную перпендикулярность и возможность сварить детали с внутренней стороны.
При скреплении конструкции состоящей из Детали№1 и Детали№2 и Детали№3 необходимо обеспечить взаимную перпендикулярность которая также обеспечивается за счет использования в качестве средств крепления угольников высотой и балок. Приваривается Деталь№3 сначала с внутренней стороны конструкции.
Выполнение отверстий под крепеж.
После выполнения сварочных работ по эскизам и ранее выполненной разметке учитывая выше указанные требования к выполнению отверстий осуществляем сверление.
А. Устанавливаем закрепляем и снимаем деталь.
Отверстия обрабатывают сверлом .
Так как глубина сверления больше диаметра отверстия то необходимо периодически выводить сверло из обрабатываемого отверстия и очищать канавки сверла и отверстие заготовки от накопившейся стружки.
В связи с тем что сверление производится насквозь то перед выходом сверла из заготовки скорость механической подачи уменьшают и заканчивают обработку вручную.
Отверстия обрабатывают сверлом по диаметру .
Так как глубина сверления больше диаметра отверстия то необходимо периодически выводить сверло из обрабатываемого отверстия и очищать канавки сверла и отверстие заготовки от накопившейся стружки
Разработка методики неразрушающего контроля стойки гидромотора.
В качестве объекта разработки методики проведения неразрушающего контроля задается деталь — стойка гидромотора.
При разработке методике неразрушающего контроля следует уделить особое внимание выбору метода дефектоскопии.
Ультразвуковая дефектоскопия — один из наиболее универсальных способов неразрушающего контроля методы которого позволяют обнаруживать поверхностные и глубинные дефекты — трещины раковины расслоения в металлических и неметаллических материалах (в том числе сварных и паяных швах клеёных многослойных конструкциях) определять зоны коррозии металлов измерять толщину (резонансный метод).
В ультразвуковом диапазоне сравнительно легко получить направленное излучение; он хорошо поддается фокусировке в результате чего повышается интенсивность ультразвуковых колебаний. Так ультразвуковые колебания применяют в неразрушающем контроле. Профессор С. Я. Соколов использовал свойство распространения ультразвука в ряде материалов и предложил в 1928 году новый метод обнаружения дефектов залегающих в толще металла. Ультразвуковой метод скоро получил признание в нашей стране и за рубежом. Это объясняется более высокой чувствительностью по раскрытию на 5 порядков достоверностью в 2 – 25 раза обнаружения дефектов более высокой оперативностью в 15 – 20 раз и производительностью в 2 – 4 раза меньшей стоимостью в 2 – 6 раз и безопасностью в работе по сравнению с другими методами неразрушающего контроля.
1. Классификация акустических методов контроля.
Согласно ГОСТ 23829-79 акустические метода делят на две большие группы: использующие излучение и приём акустических волн (активные методы) и основанные только на приёме (пассивные методы). В каждой из групп можно выделить методы основанные на возникновении в объекте контроля бегущих и стоячих волн или колебаний.
Активные акустические методы в которых применяют бегущие волны делят на две подгруппы использующие прохождение и отражение волн. Применяют как непрерывное так и импульсное излучение.
К методам прохождения относятся следующие:
Теневой метод основанный на уменьшении амплитуды прошедшей волны под влиянием дефекта.
Временной теневой метод основанный на запаздывании импульса вызванном огибанием дефекта.
Зеркально-теневой метод основанный на ослаблении сигнала отраженного от противоположной поверхности изделия (донного сигнала).
Велосиметрический метод основанный на изменении скорости упругих волн при наличии дефекта.
В методах отражения применяют как правило импульсное излучение. К этой подгруппе относятся следующие методы дефектоскопии.
Рисунок 1 – Классификация ультразвуковых методов контроля.
Эхо-метод. Регистрирует эхо-сигналы от дефектов.
Зеркальный эхо-метод основан на зеркальном отражении импульсов от дефектов ориентированных вертикально к поверхности с которой ведётся контроль.
Реверберационный метод предназначен для контроля слоистых конструкций типа металл-пластик. Он основан на анализе длительности реверберации ультразвуковых импульсов в одном из слоёв.
От рассмотренных акустических методов неразрушающего контроля существенно отличается иимпедансный метод основанный на анализе изменения механического импеданса участка поверхности контролируемого объекта с которым взаимодействует преобразователь. На использование стоячих волн основаны следующие методы:
Локальный метод свободных колебаний. Он основан на анализе спектра возбуждённых в части контролируемого объекта с помощью ударов молоточка-вибратора.
Интегральный метод свободных колебаний. Механическим ударом возбуждаются вибрации во всём изделии или в значительной его части.
Локальный резонансный метод. Применяется в тольщиномерии.
Интегральный резонансный метод. Применяют для определения модулей упругости материала по резонансным частотам продольных изгибных или крутильных колебаний изделий простой геометрической формы.
Рисунок 2 – Схемы основных акустических методов контроля.
К методам вынужденных колебаний относят акустико-топографический акустико-эмиссионный метод.
2. Эхо-импульсный метод ультразвуковой дефектоскопии.
Как видно существует огромное количество методов ультразвуковой дефектоскопии но один из наиболее распространённых методов является эхо-импульстный метод ультразвукового неразрушающего контроля. Это объясняется тем что этот метод – в отличии от других – применим при одностороннем доступе к исследуемому объекту и при этом позволяет определить размеры дефекта его координаты характер.
В эхо-импульсном методе ультразвуковой дефектоскопии (УЗД) используются те же принципы что и в радио - и акустической локации.
Современный эхо-метод УЗД основан на излучении в контролируемое изделие коротких импульсов упругих колебаний (длительностью 05 – 10 мксек) и регистрации интенсивности (амплитуды) и времени прихода эхо-сигналов отраженных от дефектов отражателей.
Импульсный эхо-метод позволяет решать следующие задачи дефектоскопии:
Обнаружение и определение координат дефектов представляющих собой нарушения сплошности и расположенных как на поверхности так и внутри металлических и неметаллических изделиях и в сварных соединениях.
Определение размеров дефектов и изделий.
Обнаружение зон крупнозернистости в металлических изделиях и заготовках.
Аппаратура реализующая данный метод позволяет определить характер дефектов идентифицировать их по размерам формам ориентации.
К основным характеристикам метода относятся: чувствительность максимальная глубина прозвучивания минимальная глубина ("мертвая" зона) разрешающая способность точность измерения расстояния производительность контроля[4].
Под чувствительностью понимают минимальный размер дефекта находящийся на максимальной глубине и четко регистрируемый прибором. Количественно ее определяют порогом чувствительности. Для эхо-метода – это минимальная площадь искусственного дефекта типа плоскодонного отверстия который обнаруживается при контроле. Ее можно определить по отражателям другого типа выполняя пересчет на площадь плоскодонного отверстия по формулам акустического тракта. Порог чувствительности ограничивается двумя главными факторами: чувствительностью аппаратуры и уровнем помех. В зависимости от структуры материала будет и изменяться порог чувствительности.
Максимальная глубина прозвучивания определяется максимальным расстоянием от дефекта (отражателя) заданного размера на котором он уверенно выявляется. Она ограничивается условием чтобы сигнал от дефекта был больше минимального сигнала регистрируемого прибором и уровня помех. Она также определяется параметрами аппаратуры. В технических характеристиках прибора в качестве максимальной глубины прозвучивания указывают максимальную длительность развертки дефектоскопа. Достижение максимальной глубины прозвучивания ограничивается теми же факторами которые препятствуют повышению чувствительности.
Минимальная глубина или "мертвая" зона - минимальное расстояние от преобразователя или от поверхности изделия до дефекта на котором он четко выявляется не сливаясь с зондирующим импульсом или импульсом от поверхности ввода ультразвука.
Разрешающая способность - минимальное расстояние между двумя одинаковыми дефектами при котором они регистрируются раздельно. Различают лучевую и фронтальную разрешающую способности метода.
Лучевая разрешающая способность - минимальное расстояние в лучевом направлении при котором сигналы от дефектов видны на экране как два раздельных импульса.
Фронтальная разрешающая способность по перемещению - минимальное расстояние между дефектами в направлении перпендикулярном лучевому.
Точность измерения расстояния до дефекта определяется погрешностью в % от измеряемой величины.
Производительность контроля определяется шагом и скоростью сканирования (перемещения) преобразователя. При оценке времени контроля учитывается и время на исследование дефекта.
2.2 Условия выявления дефектов при эхо-импульсном методе.
Для обеспечения надежного выявления дефектов необходимо выполнение двух условий:
Сигнал от дефекта должен превосходить минимальный сигнал регистрируемый регистратором прибора:
Сигнал от дефекта должен быть больше сигнала помех:
2.3 Условия получения максимального сигнала от дефекта.
Для оптимального выполнения первого условия выявления дефекта величина должна иметь максимальное значение. Где Vд – сигнал от дефекта а V0 – сигнал посылаемый преобразователем.
Также зачастую от правильного выбора частоты ультразвуковых колебаний зависит мощность получения сигнала от дефекта и как следствие точность определения дефекта. Можно сказать что частота является одним из главных параметров от выбора которых зависит выявление. Остановимся подробно на её выборе. Как известно частота зависит от коэффициента затухания. Для большинства материалов в диапазоне частот применяемых в дефектоскопии эта зависимость приближенно выражается формулой:
где и - коэффициенты не зависящие от частоты.
Первый член связан с поглощением второй – с рассеянием ультразвука мелкими зернами (кристаллитами) металла.
При малых расстояниях от преобразователя до дефекта влияние затухания ультразвука невелико поэтому в ближней зоне целесообразно применение высоких частот. В дальней зоне затухание имеет очень большое значение для рационального выбора частоты.
Оптимальная частота ультразвуковых колебаний определяется формулой
С1 – коэффициент связанный с поглощением ультразвука
r – расстояние от преобразователя ультразвуковых волн до дефекта
для мелкозернистых материалов. А для крупнозернистых оптимальная частота находится по формуле:
С2 в зависимости от соотношения λ и равна или (где - средний диаметр кристаллита)
Таким образом в обоих случаях с увеличением толщины изделия следует понижать частоту.
2.4 Виды помех появляющихся при эхо-методе.
При ультразвуковой дефектоскопии материалов и изделий как и при других видов дефектоскопии наблюдается помехи. Их делят на несколько видов:
- помехи усилителя дефектоскопа. Эти помехи препятствуют беспредельному увеличению коэффициента усиления приемного тракта дефектоскопа и определяют граничное значение регистрируемого прибором сигнала ;
- шумы преобразователя возникающие при его работе по совмещенной схеме. Непосредственно после излучения зондирующего импульса чувствительность усилителя резко ослабляется в связи с сильным динамическим воздействием на него мощного сигнала генератора. Вследствие этого в указанной зоне резко возрастает граничное значение регистрируемого прибором сигнала . наличие многократных отражений в протекторе призме преобразователя контактной жидкости создает помехи затягивающие действие зондирующего импульса. Эти помехи быстро исчезают;
- ложные сигналы возникающие в результате отражения от выступов или выточек и других неровностей поверхности. Эти помехи мешают выявлению дефектов на отдельных участках объекта контроля;
- помехи связанные с рассеянием ультразвука на структурных неоднородностях зернах материала т.е. структурной реверберацией. Сигналы от неоднородностей в зависимости от фазы ослабляют или усиливают друг друга. Они носят статистический характер.
Если дефект находиться в дальней зоне то для улучшения выявляемости дефекта в дальней зоне целесообразно увеличивать размеры преобразователя. При увеличении диаметра преобразователя улучшается направленность излучения однако граница ближней зоны удаляется от преобразователя и при дефект попадает в ближнюю зону. В ближней зоне увеличение диаметра преобразователя оказывает отрицательное влияние на отношение сигнал-шум приводит к ухудшению направленности преобразователя.
Одним из путей устранения указанных явлений является применение фокусирующих преобразователей.
2.5 Разрешающая способность эхо-метода.
Как уже говорилось ранее разрешающая способность эхо-метода – минимальное расстояние между двумя одинаковыми дефектами при котором эти дефекты фиксируются раздельно. Различают лучевую и фронтальную разрешающую способности. Первую определяют минимальным расстоянием Δr между двумя раздельно выявленными дефектами расположенными в направлении хода лучей вдоль акустической оси преобразователя. Фронтальную разрешающую способность определяют минимальным расстоянием Δl между одинаковыми по величине точечными раздельно выявляемыми дефектами залегающими на одной глубине.
Всецело разрешающая способность определяет возможность метода судить о форме объекта отражения. О характеристике дефекта судят также по фактуре его поверхности благодаря разной степени рассеяния на ней волн.
Немного познакомимся с лучевой и фронтальной разрешающей способностью:
Достижение максимальной лучевой разрешающей способности ограничивается теми же факторами что и достижение минимальной "мертвой" зоны. Сигнал от дефекта расположенного ближе к преобразователю действует подобно зондирующему импульсу и мешает выявлению дефекта импульс которого приходит позднее.
Конечная величина лучевой разрешающей способности мешает иногда выявлению дефектов вблизи противоположной поверхности изделия на фоне интенсивного донного сигнала. В связи с этим у противоположной поверхности изделия имеется неконтролируемая зона (ее также иногда называют "мертвой") величина которой однако в 2 – 3 раза меньше минимальной глубины прозвучивания.
Рисунок 3 – К оценке фронтальной разрешающей способности.
Основным средством повышения лучевой разрешающей способности служит уменьшение длительности импульса. При контроле изделий большой толщины иногда бывает трудно разделить на экране два близко расположенных импульса. Это ограничение устраняют введением задержанной развертки.
Для теоретической оценки фронтальной разрешающей способности рассчитывают амплитуду эхо-сигнала от двух одинаковых точечных дефектов залегающих на глубине r и расположенных на расстоянии Δ1 друг от друга. На рисунке 3 показаны соответствующие графики. Обращает на себя внимание появление дополнительного (центрального) максимума соответствующего положению преобразователя посередине между отражателями. В этом случае эхо-сигналы от обоих отражателей приходят к преобразователю в одно время и взаимно усиливаются.
Таким образом для улучшения разрешающей способности в дальней зоне следует улучшать направленность преобразователя путем увеличения его диаметра и частоты. В ближней зоне целесообразно применение фокусирующих преобразователей. При контроле наклонным преобразователем фронтальную разрешающую способность определяют по двум дефектам расположенным на одной глубине а не вдоль фронта волны.
2.6.Определение образа выявленного дефекта.
Целью НК является не только обнаружение дефектов но и распознавание их образа для оценки потенциальной опасности дефекта. Методы визуального представления дефектов эффективны когда размеры объектов (дефекта в целом или его фрагментов) существенно превышают длину волны УЗК Кроме того эти методы требуют применения довольно сложной аппаратуры. Вот некоторые из методов определения образа дефекта.
Обегание дефекта волнами [3]. Падающая волна возбуждает волны различного типа распространяющиеся вдоль поверхности дефекта. Например когда на округлый дефект (цилиндр) падает поперечная волна Т (рисунок 4) возникают головные продольные волны L головные поперечные и квазирэлеевские волны. Последние две волны практически неотличимы по скорости и показаны как волна R. Скорость распространения этих волн зависит от диаметра цилиндра и расстояния от его поверхности.
Рисунок 4 – Обегание дефекта волнами
Волны L и R порождают боковые поперечные волны и быстро затухают. Боковые поперечные волны могут быть обнаружены различными способами и использованы для оценки формы и размера дефекта.
Условная ширина Хд и протяженность Lд дефекта определяются расстояниями между такими крайними положениями преобразователя в которых амплитуда эхо-сигнала от дефекта уменьшается до определенного уровня.
Условная высота Hд дефекта определяется как разность показаний глубиномера в положениях преобразователя расстояние между которыми равно условной ширине дефекта. Условные размеры дефектов измеряются двумя способами. При первом способе крайними положениями преобразователя считают такие в которых амплитуда эхо-сигнала от выявленного дефекта уменьшается до значения составляющего определенную часть (обычно 12) от максимальной. При втором способе крайними положениями преобразователя считают такие в которых амплитуда эхо-сигнала достигает величины соответствующей минимальному регистрируемому дефектоскопом значению.
2.7.Ультразвуковой эхо-импульсный дефектоскоп.
Ультразвуковой эхо-дефектоскоп – это прибор предназначенный для обнаружения несплошностей и неоднородностей в изделии определения их координат размеров и характера путем излучения импульсов ультразвуковых колебаний приема и регистрации отраженных от неоднородностей эхо-сигналов. Рассмотрим его составляющие[8].
На рисунке 5 приведена принципиальная схема импульсного ультразвукового дефектоскопа. Генератор радиоимпульсов 3 возбуждает пьезопластину передающей искательной головки 1. Ультразвуковые колебания распространяются в контролируемой детали отражаются от ее противоположной стенки ("донный сигнал") и попадают на пьезопластину приемной искательной головки 2. Отраженные ультразвуковые колебания возбуждают колебания пьезопластины приемной искательной головки 2. При этом на гранях пьезопластины возникает переменное напряжение которое детектируется и усиливается в усилителе 4 а затем поступает на вертикальные отклоняющие пластины электронно-лучевой трубки (ЭЛТ) 5 осциллографа. Одновременно генератор горизонтальной развертки 6 подает пилообразное напряжение на горизонтальные отклоняющие пластины ЭЛТ 5. Генератор радиоимпульсов 3 возбуждает пьезопластину передающей
Рисунок 5 – Блок схема импульсного ультразвукового дефектоскопа
искательной головки 1 короткими импульсами между которыми получаются продолжительные паузы. Это позволяет четко различать на экране ЭЛТ 5 сигнал начального (зондирующего) импульса I сигнал от дефекта III и донный сигнал II. При отсутствии дефекта в контролируемом участке детали на экране осциллографа импульс III будет отсутствовать. Перемещая передающую и приемную искательные головки по поверхности контролируемой детали обнаруживают дефекты и определяют их местоположение. В некоторых конструкциях ультразвуковых дефектоскопов имеется только одна совмещенная искательная головка которая используется как для передачи так и для приема ультразвуковых колебаний. Места прилегания искательных головок к контролируемой детали смазывается тонким слоем трансформаторного масла или вазелина для обеспечения непрерывного акустического контакта искательных головок с поверхностью контролируемого изделия.
Разработка технологии производства перегрузочных работ.
Рельсовые перегружатели являются оборудованием исключительно зоны складирования. Они используются в сочетании с тягачами-трейлерами (или реже с автоконтейнеровозами) осуществляющими перевозку между зоной складирования и причальной зоной складом комплектации и прочие терминальные операции. Тягачи передвигаются по специальным транспортным коридорам обычно под консолью вне колеи портала. Сам перегружатель перемещает контейнеры к штабелю и от него а также перемещает контейнеры в штабеле при выборке нужного. Контейнерный перегружатель установлен на контейнерном терминале. Площадка имеет склад железнодорожные и автомобильные пути. На территорию терминала подаются контейнеры на платформах. Контейнер захватывается спредером. Включается механизм подъема перегружателя на подъем далее включается механизм передвижения тележки. Груз совершает перемещение вдоль моста крана к концу пролета под которым находится местный транспорт терминала. По завершении необходимого перемещения до продольной оси транспорта (края пролета) выключается механизм передвижения тележки. Механизм подъема совершается опускание груза на трейлер после чего производят отпуск. Затем включается одновременно механизмы передвижения тележки и перегружателя. Кран перемещается к следующей платформе а тележка в исходное положение под платформой и операция начинается заново.
Характеристика перегрузочного оборудования:
Козловой контейнерный перегружатель грузоподъемностью 40 тонн.
Скорость подъема груза –06мс
Скорость передвижение тележки –1мс
Скорость передвижения крана – 15мс
Характеристика груза:
Контейнер – крупнотоннажный 40-футовый с угловыми фитингами
Обозначение типоразмера – 1А
Масса брутто т – Rном=30т
Внутренний объем – 613 м3
Размеры дверных проемов мм
Варианты: Вагон-Склад; Склад-Автомобиль
Железнодорожный транспорт.
Контейнеры устанавливаются на специализированные платформы для перевозки крупнотоннажных контейнеров так чтобы упорные головки расположенные на платформах и предварительно приведенные в рабочее (вертикальное) положение вошли в отверстия фитингов расположенные снизу контейнеров. После установки контейнеров необходимо проверить правильность расположения упорных головок в рабочем положении.
Таблица 11.1.1 – Параметры железнодорожной платформы
статическая осевая кН(тс)
Скорость конструкционная кмч
по осям сцепления автосцепок
по концевым балкам рамы
Ширина максимальная мм
Высота от уровня верха головок рельсов мм:
Модель 2-осной тележки
Наличие переходной площадки
Наличие стояночного тормоза
Удельная площадь м²т
Количество упоров для крепления контейнеров шт.:
Год постановки на серийное производство
Возможность установки буфера
Рисунок 11.1.1 - Железнодорожная платформа
Автомобильный транспорт
Полуприцеп СЗАП-99051 позволяет перевозить все типы большегрузных контейнеров 20 ft 40 ft
Таблица 11.1.2. -Технические характеристики прицепа:
- перевозимого груза
- снаряженного полуприцепа
Габаритные размеры (мм):
Дорожный просвет (мм)
Рисунок 11.1.2. - Полуприцеп
2.Грузозахватное приспособление для козлового контейнерного перегружателя Спредеры фиксированной длины поворотные
Грузоподъёмность (т)
Автоматический электрический
Поворотные автоматические спредеры имеют собственное устройство вращения и могут быть применены на контейнерных козловых и мостовых кранах. Зацеплениеотцепление контейнера осуществляется по команде оператора из кабины.
3. Технология перегрузочных работ.
Вариант: Вагон - Склад
Технологическая схема: Вагон – перегружатель (автоматический захват)– склад
Описание технологического процесса по операциям:
Вагонная – перегружателем развернуть автоматический захват в положение удобное для захвата контейнера на высоте 300-400 мм над контейнером. Опустить спредер на контейнер таким образом чтобы штыки спредера вошли в отверстия верхних фитингов контейнера и произвести захват груза с последующим подъемом. При подъеме контейнер должен быть сначала приподнят на высоту 0 3м для проверки правильности захвата груза и надежности действия тормозов.
Внутрипортовая – ход с грузом (выполняется перемещение перегружателем контейнера на склад).
Складская – при опускании контейнера перегружателем на высоте 300-400 мм над местом установки развернуть контейнер в положение удобное для установки опустить и произвести отдачу груза на склад (таким образом чтобы штыки спредера вышли из отверстий фитингов контейнера).
Вариант: Склад - Автомобиль
Технологическая схема: Склад – перегружатель (автоматический захват) – автомобиль
Складская операция - перегружателем развернуть автоматический захват в положение удобное для захвата контейнера на высоте 300-400 мм над контейнером. Опустить спредер на контейнер таким образом чтобы штыки спредера вошли в отверстия верхних фитингов контейнера и произвести захват груза с последующим подъемом. При подъеме контейнер должен быть сначала приподнят на высоту 0 3м для проверки правильности захвата груза и надежности действия тормозов.
Внутрипортовая – ход с грузом (выполняется перемещение перегружателем контейнера в зону загрузки автотранспорта).
Автомобильная операция – при опускании контейнера перегружателем на высоте 300-400 мм над местом установки развернуть контейнер в положение удобное для установки опустить и произвести отдачу груза на трейлер (таким образом чтобы штыки спредера вышли из отверстий фитингов контейнера).
4 Схема механизации.
Складирование производим под пролетом перегружателя в 3 яруса. Под консолями перегружателя организуем зону загрузки автомобилей и выгрузки вагонов.
Расстояние от головки рельса до склада – не менее 15 м.
При размещении крупнотоннажных контейнеров с применением спредера по их периметру оставляются технологические зазоры 04м [17].
В темное время суток зона производства перегрузочных работ должна быть освещена в соответствии с действующими санитарными нормами.
Под кареткой причального контейнерного перегружателя имеется прожектор который перемещается вместе с тележкой и управляется из кабины оператора. Прожектор должен быть выбран с учетом того что он должен освещать груз и зону безопасности (по 5 м по периметру груза).
На складе организуем освещение на вышках по всей площади склада таким образом чтобы весь склад был освещен в соответствии с действующими нормами.
Технико – экономический анализ.
Оценка капиталовложений
Приведем цены на гидрооборудование козлового контейнерного перегружателя грузоподъемностью 40 тонн:
Гидромотор МРФ – 7000 25М1 – 300 000 рублей.
Гидромотор МРФ – 1600 25М1 – 160000 рублей.
Гидромотор МРФ – 1800 25М1 – 170000 рублей.
Насос НАД 250 35 - 95000 рублей.
Насос НАД 125 35 - 75 500 рублей.
Предохранительный клапан 32-32-2-131 – 1600 рублей.
Подпорный клапан ПГ54-32М – 1400 рублей.
Обратный клапан 20-32-1-11 20-32-1-11 – 1500 рублей.
Гидрозамок М2КУ 20 32 – 2000 рублей.
Гидрозамок М2КУ 32 32 – 3100 рублей.
Аккумулятор АРМ – 100.32. – 4080 рублей.
Дроссель ПГ – 77 – 12 – 1900 рублей.
Регулятор расхода МПГ 55 13А - 1700 рублей.
Регулятор расхода МПГ 55 14 – 1700 рублей.
Регулятор расхода МПГ 55 15 - 1700 рублей.
Распределитель Р202 АЛ45МР3Н – 12 500 рублей.
Распределитель Р203 АЕ514АМР3Н – 24 450 рублей.
Распределитель Р122 AF514AMP3H – 35 000 рублей.
Делитель потока МГП 160 – 1310 рублей.
Реле давления ВПГ62 – 11 – 805 рублей.
Напорный золотник РН – 323 – 12 500 рублей.
Напорный золотник АГ 573 – 4400 рублей.
Фильтр напорный ГОСТ18026-80 D32 – 3950 рублей.
Стоимость трубопроводов примем 10% от общей стоимости гидроаппаратуры.
Общая стоимость гидропривода механизмов козлового крана:
Приведем цены на электрооборудование контейнерного перегружателя грузоподъемностью 40 тонн.
Электродвигатель MTH 611 – 10 – 210500 рублей.
Электродвигатель MTF 412 – 6 – 90000 рублей.
Электродвигатель MTF 311 – 6 – 80000 рублей.
Редуктор Ц2 – 750 – 250000 рублей.
Редуктор ВКУ –965 – 200 000 рублей.
Редуктор ВКУ – 765 – 190 000 рублей.
Тормоз ТКГ – 500 – 30000 рублей.
Тормоз ТТ – 400 – 18 000 рублей.
Муфты: МУВП – 1000 – 13000 рублей.
МУВП – 500 – 10000 рублей.
МУВП – 710 – 11000 рублей.
Общая стоимость электропривода механизмов козлового контейнерного перегружателя:
Капиталовложение в подъемно – транспортное оборудование определяют в зависимости от его количества типа сроков службы и стоимости машины.
Где капиталовложение в i-ю машину
коэффициент приведения равномерных затрат к началу расчетного срока.
Е = 015 – нормативный коэффициент эффективности капиталовложений.
По оценке срока службы козловых контейнерных перегружателей примем что уменьшение динамических нагрузок на металлоконструкцию крана увеличит срок его службы на 5 лет так как основанием запрещения эксплуатации крана является состояние его металлоконструкции. Однако главным критерием оценки гидрофицированного крана является его более высокая надежность по сравнению с кранами имеющими электропривод механизмов.
Расчет коэффициентов приведения равномерных затрат.
Перегружатель с электроприводом:
Перегружатель с гидроприводом:
Расчет капиталовложений в перегружатель:
Перегружатель с электроприводом руб.
Перегружатель с гидроприводом руб.
Оценка эксплуатационных расходов:
Расходы на электроэнергию:
коэффициент использования мощности двигателя;
коэффициент одновременной работы двигателей принимаемый для машин периодического действия при перегрузке грузов;
руб. - стоимость 1 энергии по тарифу для промышленных предприятий по одноставочному тарифу;
ч.год – продолжительность работы машины за расчетный период;
– суммарная мощность основных электродвигателей машины кВт;
кВт – для гидрофицированного крана;кВт – для модернизируемого крана с электроприводом;
Вывод: проанализировав и сравнив результаты экономических показателей для козлового контейнерного перегружателя с электроприводом и такого же перегружателя с гидроприводом делаю вывод что перегружатель с гидроприводом выходит более выгодным по капитальным вложениям а также по эксплуатационным расходам а именно по расходам на электроэнергию - абсолютная эффективность.
Экспертиза промышленной безопасности.
Процент техногенных катастроф в мире неуклонно растет несмотря на ужесточающиеся экологические ограничения и технологические нормативы пополняющиеся все новыми стандартами безопасности. Причина этого кроется не только в устаревании технической базы промышленности или в желании некоторых собственников сэкономить на мониторинге угроз намного более частой причиной различных аварий является элементарная неосведомленность собственника о износе оборудования зданий сооружений или любых других составляющих материально-технической базы предприятия.
Казалось бы как такое возможно ведь с этим оборудованием ежедневно работает соответствующий персонал техническое состояние зданий и сооружений тоже находится в постоянном поле зрения да и сервисное обслуживание производится регулярно. Между тем крупное оборудование вроде стрелового крана доменной печи или участка магистрального трубопровода хоть и находится у всех на виду но дать точное заключение о их технической исправности неспециалисту крайне затруднительно.
Исправное состояние (ГОСТ 27.002-89) – это состояние крана при котором он соответствует всем требованиям нормативных и конструкторских (проектных) документов.
Для того чтобы получить точное заключение необходима экспертиза промышленной безопасности.
Экспертиза промышленной безопасности (РД 10-528-03) – это оценка соответствия объекта экспертизы предъявляемым к нему требованиям промышленной безопасности результатом которого является заключение. Она производится группой специалистов которые оценивают состояние тех или иных материально-технических средств и выносят на основании этого заключение о технической безопасности оборудования коммуникаций зданий и сооружений.
Серьёзной проблемой крупных промышленных комплексов является неизбежная выработка проектного ресурса оборудования дальнейшая эксплуатация которого может привести к крупной аварии и даже к техногенной катастрофе.
Ресурс (ИСО 11994) – это суммарная наработка изделия от начала его эксплуатации или ее возобновления после ремонта до перехода в предельное состояние.
Немаловажную роль при решении этой задачи играет вопрос проведения экспертизы промышленной безопасности на опасных производственных объектах. Повышение качества экспертизы является основой выхода на научно обоснованный прогноз безопасности таких объектов что позволит повысить эффективность превентивных мер по предупреждению аварийности и травматизма.
Качество проведения экспертизы зависит от многих факторов. В качестве основных можно выделить:
- выполнение лицензионных требований;
- своевременность проведения экспертизы;
- правильность оценки объёма работ и совокупности объектов проведения экспертизы;
- организация проведения экспертизы;
- компетентность уровень квалификации и правильный подбор состава экспертной группы;
- полнота и точность проведения инструментального контроля использование современного контрольно-диагностического оборудования при проведении экспертизы;
- полнота использования действующих нормативно-технических документов при проведении экспертизы;
- правильность оформления заключения экспертизы.
Экспертиза промышленной безопасности (экспертиза) проводится в соответствии с законом «О промышленной безопасности опасных производственных объектов» ФЗ-116 от 21.07.97г. постановлением Правительства РФ «О мерах по обеспечению промышленной безопасности опасных производственных объектов на территории Российской Федерации» №241 от 28.03.01г. на основании предписаний органов Ростехнадзора.
Целью экспертизы является установление фактического технического состояния и условий эксплуатации объекта экспертизы их соответствия действующим Нормам и Правилам промышленной безопасности с установлением возможности параметров и срока дальнейшей безопасной эксплуатации объекта экспертизы.
Экспертиза выполняется специализированной экспертной организацией имеющей соответствующую лицензию на право проведения работ и имеющей в своём штате экспертов аттестованных установленным порядком.
Согласно Положению по проведению экспертизы промышленной безопасности опасных производственных объектов на которых используются подъемные сооружения (РД 10-528-03) экспертное обследование (техническое диагностирование) ГПМ рекомендуется проводить в следующих случаях:
- по окончании срока службы;
- после аварии грузоподъемной машины (при необходимости ее восстановления);
- при выявлении в процессе эксплуатации грузоподъемной машины дефектов вызывающих сомнение в прочности конструкции или дефектов причину которых установить затруднительно.
Экспертное обследование - оценка соответствия грузоподъемной машины требованиям нормативных технических и эксплуатационных документов результатом которой является заключение о возможности или невозможности ее дальнейшей эксплуатации.
Техническое диагностирование - оценка технического состояния объекта (ГОСТ 20911-89) является составной частью экспертного обследования.
Срок службы ГПМ устанавливается заводом-изготовителем и указывается в ее паспорте. Срок службы ГПМ исчисляется с даты ее выпуска. При отсутствии в паспорте ГПМ сведений о сроке службы машины рекомендуется руководствоваться справочным приложением 2 руководящего документа РД 10-112-1-04.
Предусматриваются следующие виды экспертного обследования ГПМ с истекшим сроком службы:
Первичное экспертное обследование ГПМ проводится после выработки срока службы установленного изготовителем и занесенного в паспорт крана.
Повторное экспертное обследование ГПМ проводится в сроки установленные экспертной организацией и внесенные в заключение.
Внеочередное экспертное обследование ГПМ может проводиться вне зависимости от срока эксплуатации крана:
- по требованию ФСТН или по заявлению заказчика;
- в случаях выявления опасных дефектов в металлоконструкциях грузоподъемной машины вызывающих переход ее в предельное состояние;
- при подготовке дубликата паспорта;
- после модернизации реконструкции ремонта монтажа аварии.
Количество повторных обследований определяется типом назначением и условием эксплуатации ГПМ и может быть ограничено либо ее техническим состоянием и требованиями безопасности либо экономической целесообразностью.
Период на который продляется срок службы ГПМ устанавливается экспертной организацией в соответствии с рекомендациями нормативной документации ФСТН. Периодичность обследования зависит от:
- технического состояния ГПМ на момент экспертизы;
- соответствия фактического режима эксплуатации ГПМ паспортному (в случае превышения паспортного режима ГПМ требуется дополнительная проверка (расчет) ее металлоконструкции на сопротивление усталости);
- степени агрессивности окружающей среды;
- количества и качества ремонтов базовых конструкций;
- величины износа в том числе коррозии элементов конструкции;
- наличия остаточных деформаций несущих металлоконструкций;
- результатов расчета остаточного ресурса и др.
Перечисленные факты могут служить основанием для сокращения периодичности обследований рекомендованной нормативной документацией.
Оценка остаточного ресурса по балльной системе проводится для всех ГПМ отработавших нормативный срок службы.
Расчет базовых конструкций ГПМ на сопротивление усталостным разрушениям для определения возможности и срока дальнейшей эксплуатации ее с паспортными (или измененными) характеристиками выполняет специализированная организация имеющая специалистов III уровня по технической диагностике. В целях обеспечения гарантии безопасной эксплуатации ГПМ расчет остаточного ресурса требуется выполнять для ГПМ:
срок службы которых после установленного заводом-изготовителем (или рекомендованного приложением 2 РД 10-112-1-04) превышает: 20 лет-для спецкранов и кранов-перегружателей; 15 лет-для кранов общего назначения мостового типа портальных кранов; 10 лет-для кранов стрелового и башенного типа подъемников и вышек строительных подъемников;
техническое состояние базовых конструкций которых требует капитального ремонта или замены элементов;
режимы работы которых превышают паспортные;
если окружающая среда эксплуатации агрессивна;
которым требуется проводить реконструкцию или модернизацию под новые технологии.
Расчет остаточного ресурса ГПМ может быть выполнен и вне зависимости от срока ее эксплуатации для любых обстоятельств требующих данных о технических возможностях ГПМ.
По результатам расчетов остаточного ресурса ГПМ отработавшей нормативный срок службы экспертная организация может продлить срок ее эксплуатации. Запись о продлении срока службы вносится в паспорт ГПМ на основании заключения экспертной организации.
Экспертному обследованию должны подвергаться ГПМ находящиеся в рабочем состоянии.
Экспертное обследование на предмет продления срока службы рекомендуется совмещать с перемонтажом ГПМ проведением текущего ремонта или технического освидетельствования желательно в летний период времени. В этих целях сроки до начала проведения обследований ГПМ установленных на открытом воздухе или в неотапливаемых помещениях могут увеличиться до 3 месяцев.
Экспертному обследованию подлежат ГПМ импортного производства вне зависимости от даты их выпуска в целях:
установления соответствия их конструкции и технической документации нормам и требованиям НТД России;
внесения изменений и дополнений в части безопасной эксплуатации ГПМ (в случае необходимости);
подготовки (корректировки) эксплуатационной документации согласно требованиям ФСТН;
получения разрешения на эксплуатацию импортной техники на территории России.
Экспертное обследование импортной техники выполняют специализированные организации имеющие в своем составе специалистов-экспертов по ПС и рекомендации ФСТН на право проведения этих работ.
Срок службы импортной ГПМ соответствует записи сделанной в паспорте заводом-изготовителем. В случае отсутствия такой записи срок службы ГПМ оценивается согласно приложению 2 РД 10-112-1-04.
С момента регистрации в органах ФСТН импортная ГПМ отработавшая свой нормативный срок службы подлежит технической диагностике согласно данным Рекомендациям. Контроль за соблюдением периодичности и качества экспертных обследований ГПМ осуществляется на предприятиях лицами по надзору за безопасной эксплуатацией ГПМ и территориальными органами ФСТН.
Заключения по экспертному обследованию ГПМ отработавших нормативный срок службы подлежат регистрации в территориальных органах ФСТН.
Экспертные организации и владельцы ГПМ при подготовке и проведении экспертных обследований ГПМ должны руководствоваться Правилами государственными и международными стандартами положениями методическими указаниями данными Рекомендациями и другими документами утвержденными в установленном порядке (см. приложение 1 РД 10-112-1-04).
Экспертная организация проводящая обследование ГПМ должна:
иметь статус юридического лица;
иметь полномочия включающие наличие лицензии на проведение экспертизы объектов повышенной опасности ФСТН;
быть независимой чтобы персонал не подвергался какому-либо административному финансовому или другому виду давления со стороны владельца ГПМ или контролирующих органов способных повлиять на технические решения;
обладать квалифицированным кадровым персоналом способным оценить работоспособность ГПМ качество выполненного ремонта и уровень безопасности работ при ее дальнейшей эксплуатации;
обладать необходимыми техническими средствами для проведения обследования и оценки технического состояния ГПМ до и после ремонта;
иметь в пользовании учтенные и другие нормативные документы относящиеся к обследованию конкретных типов ГПМ.
Экспертная организация может проводить экспертное обследование при наличии специалистов и экспертов прошедших подготовку и аттестацию согласно Рекомендациям по подготовке и аттестации специалистов и экспертов осуществляющих экспертизу промышленной безопасности подъемных сооружений (см. приложение 1 РД 10-112-1-04).
Экспертная организация перед началом обследования издает приказ о назначении экспертной комиссии по обследованию конкретного объекта в котором назначается председатель комиссии и члены комиссии ответственное лицо за ТБ на объекте указываются сроки проведения обследования (согласно договору) количество и типы ГПМ. Форма приказа по экспертной организации приведена в приложении 3 РД 10-112-1-04.
В комиссию должно входить не менее трех специалистов. Председателя комиссии рекомендуется назначать из числа лиц имеющих II или III уровень (и выше) квалификации по технической диагностике ГПМ членов комиссии-из числа специалистов I или II уровня. Все члены комиссии помимо аттестации по технической диагностике ГПМ должны иметь удостоверения о подготовке и проверке знаний правил по промышленной безопасности и как лицо ответственное за безопасное производство работ ГПМ.
Приборы и инструменты используемые в ходе обследования должны пройти метрологическую поверку.
Средства неразрушаюшего контроля применяемые при экспертизе должны соответствовать требованиям изложенным в РД 03-606-03.
Экспертная организация проводит в установленном законодательством порядке страхование своей ответственности на случай возникновения аварии (поломки трещин изгиба требующих выполнения ремонта или замены) несущих элементов металлических конструкций в период на который продлен срок службы ГПМ. Страхование ответственности на случай возникновения аварий несущих элементов металлических конструкций должно проводиться на основании положений (правил) страхования.
Владелец ГПМ подлежащей экспертному обследованию перед началом экспертизы издает приказ по предприятию о передаче на обследование (первичное повторное или внеочередное) данной ГПМ или группы ГПМ о назначении ответственных лиц за технику безопасности на объекте за организацию и контроль качества проведения работ при обследовании ГПМ. Форма приказа по предприятию приведена в приложении 4 РД 10-112-1-04.
Владелец ГПМ должен подготовить к обследованию:
ГПМ испытательные грузы а также выделить опытного крановщика (машиниста оператора) на период проведения обследования;
оборудование и средства для обследования металлических конструкций и механизмов на высоте (при необходимости);
акт сдачи-приемки кранового пути в эксплуатацию и предыдущий акт нивелировки путей (для грузоподъемных машин перемещающихся по наземным или надземным рельсовым путям) в соответствии с требованиями нормативных документов;
акт проверки сопротивления изоляции и заземления;
документы акты проведенного ремонта (реконструкции) а также сертификаты металла использованного при проведении ремонта реконструкции (если эти работы проводились);
справку о характере работ выполняемых ГПМ;
журнал технических обслуживаний (либо вахтенный журнал) с записями о проведенных технических обслуживаниях и текущих ремонтах;
паспорт руководство по эксплуатации и другие эксплуатационные и проектно-конструкторские документы (при необходимости);
акты и экспертное заключение ранее проведенных экспертных обследований (техническое диагностирование) ГПМ.
По результатам обследования ГПМ экспертная организация составляет заключение экспертизы и передает его владельцу ГПМ для регистрации в территориальном органе ФСТН. Заключение после регистрации является неотъемлемой частью паспорта ГПМ.
Экспертное обследование проводится на основании заявки владельца ГПМ или других документов в соответствии с согласованными экспертной организацией и заказчиком условиями. Документы на проведение экспертного обследования ГПМ составляются после согласования договаривающимися сторонами:
типов ГПМ и их количества;
технических характеристик и условий эксплуатации ГПМ;
перечня информации необходимой для проведения экспертного обследования в соответствии с действующей НТД;
требований обязательных для проведения экспертизы;
сроков проведения работ по экспертному обследованию и передачи заключения владельцу ГПМ;
других организационно-технических вопросов.
Экспертное обследование ГПМ следует проводить в соответствии с программой выполнения работ разработанной экспертной организацией на основании НТД ФСТН с учетом типа конструкции назначения и условий эксплуатации ГПМ согласованной с заказчиком.
Программа экспертного обследования как правило предусматривает 3 этапа выполнения работ:
Подготовительный этап включает:
подбор нормативно-технической и справочной документации требуемой для технической диагностики ГПМ;
ознакомление с сертификатами (на канаты крюки металл электроды и т.п.) с эксплуатационной ремонтной проектно-конструкторской и другой документацией на данную ГПМ;
подготовку выписок из паспорта ГПМ;
составление карты осмотра ГПМ (при необходимости);
проверку на соответствие справки о характере работы ГПМ;
проверку условий и организации работ по подготовке места проведения экспертного обследования и испытаний ГПМ;
подготовку технических средств и приборов для обследования;
проведение инструктажа по технике безопасности членов комиссии.
Рабочий этап включает:
обследование технического состояния металлоконструкций;
обследование механического оборудования;
обследование канатно-блочной системы;
обследование гидро- и пневмооборудования;
обследование электрооборудования;
обследование приборов безопасности;
обследование состояния крановых путей и тупиковых упоров подтележечных путей (в объеме Рекомендаций);
проведение геодезических замеров конструкции;
взятие контрольных образцов из элементов металлоконструкций ГПМ для определения химического состава и механических свойств металла (при необходимости);
расчет фактического режима работы ГПМ;
проведение приборного контроля металлоконструкций и сварных соединений методами неразрушающего контроля (по решению комиссии);
проведение испытаний (статических динамических специальных).
Если по результатам обследования комиссией установлено что требуется произвести ремонт до испытания ГПМ то после ремонта производится проверка отремонтированного узла после чего обследование ГПМ осуществляется в той же последовательности что и до ремонта.
Заключительный этап включает:
сбор и анализ результатов обследования;
составление ведомости дефектов;
оценку остаточного ресурса ГПМ (балльная система);
оформление актов (визуально-измерительного контроля; проверки сопротивления изоляции и заземления; химического анализа и механических свойств металла; грузовых испытаний ГПМ) и др.;
проверочные расчеты несущей способности элементов конструкции крепежа сварных соединений (при необходимости и согласовании с заказчиком);
расчет остаточного ресурса ГПМ (при необходимости);
выработку решения о возможности и целесообразности продления срока эксплуатации ГПМ;
рекомендации по обеспечению безопасной эксплуатации ГПМ;
оформление акта обследования;
оформление заключения экспертного обследования;
передачу заключения владельцу ГПМ для регистрации в органах ФСТН.
При проведении внеочередного обследования объем экспертных работ определяется комиссией с учетом причин этого обследования.
В процессе выполнения работ по экспертному обследованию комиссии необходимо ознакомиться с имеющимися:
сертификатами на канаты крюки металл электроды крепеж и т.п.;
паспортами на ГПМ крюки тормоза двигатели и др.;
инструкциями по ТО и эксплуатации ГПМ;
журналами: сменными вахтенными учета проверки знаний персонала инструктажей техники безопасности квалификационными данными обслуживающего персонала; осмотра технического обслуживания и ремонта ГПМ и крановых путей; ремонтной документацией (в комплекте);
чертежами и расчетами выполненными при реконструкции или модернизации ГПМ;
материалами последнего полного технического освидетельствования;
предыдущими заключениями поданной ГПМ;
справкой о характере работы ГПМ (форма справки приведена в приложении 5 РД 10-112-1-04);
документами по крановым рельсовым путям (генплан сертификаты на элементы пути паспорта на пути и тупики геодезические замеры - планово-высотные съемки сведения о зданиях территориях установки путей и др.);
актами проверки сопротивления изоляции и заземления;
актами проверки приборов безопасности и измерительных приборов;
предписаниями органов ФСТН и службы технического надзора организации.
По результатам ознакомления с документацией делаются выписки из паспортов составляется рабочая карта осмотра ГПМ дается оценка:
наличия и комплектности документации;
соответствия имеющегося оборудования и его технических данных паспортным и сертификационным документам;
наличия системы и контроля проверки знаний правил промышленной безопасности а также соблюдения квалификационных требований к персоналу;
соблюдения предписаний органов контроля и экспертных комиссий;
уровня технического обслуживания ГПМ и соответствия ТО требованиям инструкций;
соответствия ремонтной документации требованиям ГОСТ и НТД ФСТН.
Место установки ГПМ на период ее обследования должно быть ограждено с соответствующими предупредительными знаками освещено и доступно для установки дополнительных подъемных средств используемых при обследовании. На рубильнике включающем ГПМ должна быть табличка с надписью: «Не включать работают люди».
В зоне обследования владельцем ГПМ должны быть подготовлены контрольные грузы для испытаний ГПМ.
ГПМ должна быть очищена от грязи смазки оледенения и т.п. кожуха-сняты люки вскрыты кран обесточен.
Лестницы перила ограждения люки должны быть исправны и отвечать требованиям ТБ.
На ГПМ должны быть таблички с указанием регистрационного номера ГПМ ее грузоподъемности и даты испытания. Надписи на табличке должны быть хорошо различимы с земли (с пола) и соответствовать данным в паспорте ГПМ.
Следует обратить внимание на расположение рубильника подающего напряжение на ГПМ наличие свободного доступа к нему устройства для запирания рубильника в отключенном положении наличие на нем надписи «Крановый» заземление корпуса рубильника.
В зоне действия ГПМ должны отсутствовать помещения в которых могут находиться люди. При наличии таких помещений необходимо проверить достаточность мер принятых администрацией для обеспечения безопасного производства работ по перемещению грузов.
Зона обследования ГПМ должна находиться вне зоны воздушных линий электропередачи.
Проверка состояния металлоконструкций ГПМ - основной по объему и значимости вид работ при экспертном обследовании. Она включает:
внешний осмотр несущих элементов металлических конструкций;
проверку элементов металлических конструкций одним из видов неразрушающего контроля;
проверку качества соединений элементов металлических конструкций (сварных болтовых шарнирных и др.);
измерение остаточных деформаций балок стрел ферм и отдельных поврежденных элементов;
оценку степени коррозии несущих элементов металлических конструкций.
Перед обследованием металлические конструкции особенно места их возможного повреждения должны быть очищены от грязи коррозии снега избытка влаги и смазки. Внешний осмотр следует проводить с применением простейших оптических средств и переносных источников света при этом особое внимание должно уделяться следующим местам возможного появления повреждений:
участкам резкого изменения сечений;
участкам прорезанным шпоночными или шлицевыми канавками а также имеющим нарезанную резьбу;
местам подвергшимся повреждениям или ударам во время монтажа и перевозки;
местам где при работе возникают значительные напряжения коррозия или износ;
участкам имеющим ремонтные сварные швы.
При проведении внешнего осмотра необходимо обращать особое внимание на наличие следующих дефектов:
трещин в основном металле сварных швах и околошовной зоне косвенными признаками наличия которых являются шелушение краски местная коррозия подтеки ржавчины и т.п.;
механических повреждений;
расслоения основного металла;
некачественного исполнения ремонтных сварных соединений;
люфтов шарнирных соединений ослабления болтовых и заклепочных соединений.
При обнаружении механических повреждений металлической конструкции (вмятин изгиба разрывов и т.п.) замеряются их размеры (длина ширина высота или глубина). Затем размеры повреждения следует сравнить с предельными размерами подобного дефекта для металлической конструкции ГПМ данного типа и в случае превышения нормативных значений повреждения зафиксировать в ведомости дефектов форма которого приведена в приложении 6 РД 10-112-1-04.
Контроль состояния болтовых и заклепочных соединений ГПМ рекомендуется производить согласно Инструкции по оценке технического состояния болтовых и заклепочных соединений грузоподъемных кранов (РД 10-197-98) и других нормативных документов.
Контроль соединительных элементов металлической конструкции (осей пальцев и т.п.) следует начинать с осмотра состояния фиксирующих элементов свидетельствующих о наличии осевых или крутящих усилий в соединении ось (палец) демонтируют и замеряют. Аналогичному осмотру и замерам при этом следует подвергать и посадочные гнезда осей.
Наличие люфтов в шарнирных соединениях предварительно определяют визуально а в процессе эксплуатации крана по характерным признакам (толчки резкие удары болтанка и т.п.). При наличии характерных признаков точную количественную оценку люфта и его допустимости в сомнительных случаях устанавливать путем измерений.
При обследовании металлоконструкций следует учитывать что усталостные трещины возникают в первую очередь в зонах концентраторов местных напряжений а именно в:
узлах крепления раскосов стоек косынок к поясам; элементах с резким перепадом поперечных сечений; местах окончания накладок ребер;
зонах отверстий с необработанными прожженными или заваренными кромками;
местах пересечения сварных швов;
зонах перепадов толщины стыкуемых листов (соединений);
местах повторной заварки трещин в сварочных швах и др.
При обнаружении трещин в металлоконструкциях ГПМ или в сварном шве зоны их образования подвергаются дополнительной проверке одним из видов неразрушающего контроля согласно НТД ФСТН.
Выбор вида неразрушающего контроля для конкретной ГПМ определяет экспертная комиссия.
При оценке деформации металлоконструкций необходимо обращать внимание на дефекты приводящие к снижению несущей способности конструкции:
отклонение от прямолинейности (башен стрел пролетных строений стоек элементов ферменных конструкций);
скручивание (пролетных конструкций опор стрел и др.);
несоосность соединений (секций стрел башен и др.);
наличие остаточных прогибов пролетных балок кронштейнов консолей и т.п.;
искажение формы моста элемента в плане.
Результаты измерений деформаций геометрических параметров металлоконструкций оформляются в виде схем и таблиц с указанием и координацией мест замеров и дефектов (приложение 7 РД 10-112-1-04).
Возможными местами появления коррозии являются:
замкнутые пространства (коробки) ходовых рам кольцевых балок пояса и стойки порталов;
опорные узлы стрел башен;
зазоры и щели образующиеся вследствие неплотного прилегания элементов;
сварные соединения выполненные прерывистым швом и др.
Степень коррозионного износа определяется с помощью измерительного инструмента или средствами неразрушающего контроля.
Зоны коррозии наносятся на схемы металлоконструкций с указанием размеров повреждений и координат местонахождения.
Особое внимание следует обратить на соответствие паспортных значений марок стали из которых изготовлены несущие металлоконструкции ГПМ фактическим (особенно если были ремонты металлоконструкций) согласно требованиям НТД по температурным возможностям их использования.
Работы по проверке состояния узлов и механизмов включают:
оценку соответствия установленного оборудования эксплуатационным документам;
внешний осмотр в целях анализа общего состояния работоспособности и необходимости проведения дальнейших измерений;
проведение необходимых измерений.
Перед проведением обследования механизмы и другие подвергаемые осмотру узлы ГПМ должны быть очищены от грязи коррозии снега избытка влаги и смазки кожуха и крышки редукторов-сняты обеспечен доступ к осмотру каждого узла.
При внешнем осмотре выявляют:
наличие и общее состояние всех механизмов наличие повреждений их отдельных узлов и деталей;
отсутствие деформаций коррозии и необходимость их устранения;
отсутствие вытекания смазки;
наличие и качество затяжки элементов крепления механизмов;
соответствие установки узлов механизмов (например тормозов механизма передвижения и т.п.) требованиям эксплуатационной и нормативной документации;
наличие и техническое состояние предохранительных устройств (кожухов крышек и т.п.).
Необходимость разборки механизмов при осмотре определяет комиссия.
Повреждения близкие к предельным выявленные в результате внешнего осмотра должны быть измерены. Результат измерения сравнивают либо с размером где дефект практически отсутствует либо с размером указанным в чертеже.
Необходимость измерений может быть определена в ходе обкатки и испытаний по косвенным признакам (шум течь смазки повышение температуры узла и т.п.).
Наличие смазки в редукторах проверяется с помощью щупа маслоуказательных пробок глазков либо через люк в крышке. Уровень масла должен находиться между верхней и нижней отметками маслоуказателя.
При проверке механизмов следует обратить внимание на:
трещины в кожухах редукторов рычагах тормозов шкивах колодках;
поломку тормозных пружин;
износ зубчатых зацеплений;
износ ходовых колес и их позиционирование;
муфты в шарнирных и шпоночных соединениях;
комплектность и крепление болтовых соединений особенно опорно-поворотных устройств;
правильность установки тормозов муфт барабанов и т.п.;
перекос опорно-поворотного устройства.
Основные дефекты и нормы выбраковки механизмов приведены в рекомендациях по каждому конкретному типу крана.
Проверку работоспособности механизмов рекомендуется совмещать со статическими и динамическими испытаниями ГПМ. При этом проверяются: на плавность срабатывания и надежность удержания тормоза механизмов подъема и передвижения отсутствие биения шкивов блоков и барабанов опорно-поворотного устройства характер шума и температура в редукторах двигателях правильность установки колес на рельсах забеги опор и т.п.
Дефекты выявленные в ходе обследования вносятся в ведомость дефектов с указанием места дефекта и сроков устранения. Комиссия может дать свои рекомендации по устранению дефектов.
Для канатно-блочных систем характерны следующие повреждения:
трещины и сколы реборд блоков;
износ по ручью или реборде блоков и барабанов;
отсутствие (течь) смазочного материала в подшипниках;
отсутствие (повреждение) стопорной планки в крюковой подвеске;
смещения в установке блоков полиспастной системы;
отклонения в запасовке и заделке концов каната.
Опасными местами являются места возможного появления коррозии-это места скопления влаги и где канат редко перемещается по блокам.
Участки каната интенсивно работающие проходящие по наибольшему числу блоков подвержены износу и обрыву проволок деформации.
Контролю подлежат места крепления канатов на барабанах и на конструкциях ГПМ (обратить внимание на количество соответствие типоразмеров затяжку крепежных элементов).
Крюки и другие грузозахватные органы должны соответствовать паспортным характеристикам и иметь соответствующие маркировки заводов-изготовителей. В процессе испытания ГПМ грузозахватные органы (грейферы захваты электромагниты) подвергаются специальным испытаниям. Результаты этих испытаний вносятся в акт испытаний ГПМ.
Канаты блоки барабаны и крюки следует проверять используя предельные нормы браковки элементов ГПМ приведенные в эксплуатационной документации а при их отсутствии-приведенные в Правилах и НТД ФСТН.
Несущие и вантовые канаты следует проверять согласно рекомендациям Методических указаний по магнитной дефектоскопии стальных канатов. Основные положения (РД 03-348-00).
В ходе статических и динамических испытаний ГПМ канатно-блочная система проверяется на:
правильность запасовки каната; наличие биения блоков и барабанов;
правильность намотки каната на барабан;
надежность удержания контрольного груза с последующей проверкой состояния каната и узлов крепления его к барабану или металлоконструкции ГПМ.
Обследование электрооборудования должно проводиться при полностью снятом с ГПМ напряжении.
Предварительно необходимо проверить наличие и соответствие паспортным данным:
пускорегулирующие резисторы;
пульт управления и монтажный пульт;
тормозные электромагниты и электродвигатели электрогидравлических толкателей;
Внешний осмотр электрооборудования зависит от конкретного типа ГПМ типа электропривода и рода питающего электрического тока. При данном виде осмотра проверяют:
наличие и комплектность электрооборудования токоподводящей системы и системы управления и защиты ГПМ;
целостность корпуса клеммных коробок зон крепления в местах установки электрооборудования;
отсутствие влаги внутри корпуса и в клеммных коробках ящиках сопротивления;
исправность щеток коллекторов (контактных колец) контактных реле пускателей электромагнитов электрогидротолкателей приборов и аппаратуры управления;
правильность установки и подключения к питающей сети в соответствии с паспортной документацией.
При осмотре кабеля проводов проводят замер сопротивления изоляции. Проверяют правильность разводки а также состояние и крепление коробов предохранительных рукавов (труб) распределительных коробок и др.
При осмотре электрического освещения отопления и сигнализации проверяют исправность электрической аппаратуры приборов осветительных ламп.
Проверке подлежит система заземления ГПМ в соответствии с требованиями технической документации и Правилами установки электрооборудования промышленных установок.
По результатам внешнего осмотра и изменений производится проверка работоспособности электрооборудования под напряжением без нагрузки ГПМ при статических и динамических грузовых испытаниях.
Результаты измерений сопротивления изоляции электрических цепей оформляются в виде таблицы по форме представленной в приложении 8 РД 10-112-1-04.
Обследование приборов и устройств безопасности включает:
внешний осмотр приборов и устройств безопасности;
контрольную проверку их работоспособности.
При внешнем осмотре приборов и устройств безопасности необходимо выполнить проверку:
наличия приборов и соответствия их паспортным данным;
наличия пломб на электронных (релейных) блоках приборов.
Контрольная проверка их работоспособности включает проверку:
надежности срабатывания и соответствия показаний индикаторов ограничителей грузоподъемности нормативным данным;
работы концевых выключателей ограничивающих перемещение груза тележки ГПМ и т.п.;
работы систем блокировок и срабатывания защит установленных на ГПМ и приведенных в ее паспорте;
точности показаний контрольно-измерительных приборов.
Методы проверки конкретных приборов и устройств безопасности приведены в других рекомендациях.
При отсутствии приборов безопасности дальнейшая эксплуатация ГПМ должна быть приостановлена до согласования с органами ФСТН.
Приборы и устройства безопасности в ГПМ импортного производства проверяются на соответствие российским нормам и правилам и согласуются с ФСТН.
Результаты проверки работоспособности приборов и устройств безопасности оформляются в виде таблиц одна из которых приведена в приложении 9 РД 10-112-1-04.
При обследовании ГПМ установленных на рельсовых путях проверке подлежит участок рельсовых путей находящийся в зоне обследования ГПМ протяженностью не менее трех баз крана. Остальные рабочие рельсовые пути на которых согласно технологии работает данная ГПМ проходят периодическую комплексную проверку и являются самостоятельным видом работ согласно Комплексному обследованию крановых путей грузоподъемных машин. Часть 1. Общие положения. Методические указания (РД 10-138-97).
Проверка состояния крановых путей рельсов и монорельсов грузовых тележек включает:
ознакомление с документацией по устройству рельсового пути паспортом кранового пути актами нивелировки и проверки сопротивления заземления рельсового пути ранее выполненными планово-высотными съемками путей;
проверку комплектности и соответствия рельсового пути типовому проекту и требованиям эксплуатационной документации;
визуально-измерительный контроль всех элементов пути включая заземление сопоставление замеров с нормами ФСТН;
проведение планово-высотной съемки крановых путей на участке установки ГПМ с выдачей рекомендаций по его рихтовке при несоответствии отклонений путей нормативам;
оценку состояния верхнего и нижнего строения рельсовых путей наземного ориентирования;
оценку общего состояния подкрановых балок и несущих строительных конструкций (для ГПМ передвигающихся по надземным рельсовым путям).
Планово-высотная съемка подтележечных рельсов (монорельсов) проводится в случаях неудовлетворительной работы механизма передвижения тележки (шум повышенная вибрация наличие значительного износа колес тележки и т.п.).
Низкое качество рельсовых путей и отсутствие надлежащего ухода за ними может служить одним из оснований для уменьшения срока обследования ГПМ назначаемого комиссией.
По результатам обследования крановых и подтележечных путей составляются таблицы замеров и схемы планово-высотной съемки.
Статические и динамические испытания должны выполняться в соответствии с указаниями эксплуатационной документации (при отсутствии этих указаний-в соответствии с Правилами и рекомендациями ФСТН) комиссией с участием инженерно-технических работников по надзору за безопасной эксплуатацией ГПМ предприятия-владельца.
ГПМ может быть подвергнута статическим и динамическим испытаниям только после устранения дефектов установленных комиссией и перевода ее в работоспособное состояние.
Испытаниям на работоспособность подвергаются грузозахватные органы (грейферы захваты электромагниты и др.).
ГПМ специального назначения для металлургического производства проходят испытания согласно рекомендациям РД 10-112-06-03.
Результаты грузовых испытаний оформляются в виде протокола (приложение 10 РД 10-112-1-04).
Дефекты выявленные по результатам обследования ГПМ их металлических конструкций механизмов и отдельных узлов приборов безопасности гидро- и электрооборудования крановых и подтележечных путей должны быть занесены в ведомость дефектов форма которой приведена в приложении 6 РД 10-112-1-04. Ведомость дефектов передается владельцу крана для согласования мероприятий по устранению замечаний комиссии. Форма документа по согласованию мероприятий приведена в приложении 11 РД 10-112-1-04.
Ведомость дефектов является официальным документом для направления ГПМ в ремонт.
Необходимость определения химического состава и (или) механических свойств металла возникает в следующих случаях:
если в паспорте ГПМ отсутствуют данные о металле из которого изготовлены несущие элементы металлических конструкций;
при работе ГПМ в условиях агрессивной среды;
если температурный режим эксплуатации ГПМ не соответствует режиму для данной марки стали;
при внеочередном обследовании (при необходимости);
при отсутствии сертификатов на металл используемый при ремонтах ГПМ.
Порядок отбора проб для проверки химического состава и анализа механических свойств металла следует осуществлять в соответствии с требованиями приведенными в других рекомендациях.
Расчет остаточного ресурса выполняется по рекомендациям (методикам) согласованным с ФСТН.
Исходными данными для определения остаточного ресурса являются:
результаты обследования ГПМ в соответствии с настоящими и другими рекомендациями;
данные характеризующие использование ГПМ за весь срок ее эксплуатации (число циклов распределение транспортируемых грузов по массам степень агрессивности среды и т.п.);
данные о химическом составе и механических свойствах металла расчетных элементов металлических конструкций в момент выполнения оценки остаточного ресурса;
данные о геометрии расчетных элементов металлической конструкции с учетом фактической коррозии ремонтов реконструкций;
руководящие документы и стандарты по оценке остаточного ресурса по расчету металлических конструкций данного типа в том числе на усталостную прочность (при наличии);
результаты тензометрирования и методов неразрушающего контроля оцениваемых металлических конструкций (при необходимости);
расчет металлической конструкции на прочность и сопротивление усталостным разрушениям.
Расчет остаточного ресурса передается владельцу ГПМ. Расчет должен содержать заключение о возможности и условиях дальнейшей эксплуатации ГПМ.
По результатам обследования и испытаний ГПМ оформляется акт обследования форма которого приведена в приложении 13 РД 10-112-1-04. В случае проведения внеочередного обследования форма акта не регламентируется.
Акт после его подписания всеми членами комиссии утверждается руководителем организации проводившей экспертное обследование.
Для ГПМ находящейся при завершении экспертного обследования в работоспособном состоянии комиссия устанавливает в акте срок на время которого рекомендуется продление их дальнейшей эксплуатации.
Одновременно с актом может оформляться отчет о проведенном обследовании (по произвольной форме). Допускается отчет о проведенном обследовании делать сводным на группу обследованных ГПМ одной организации (участка цеха и т.п.). Отчет является внутренним документом организации выполнявшей экспертное обследование к заключению не присоединяется и владельцу ГПМ не передается.
Итогом экспертного обследования является заключение экспертизы промышленной безопасности ГПМ форма и содержание которого рекомендованы письмом Госгортехнадзора России от 10.01.03 № 12-0126.
В заключении даются оценка технического состояния ГПМ (исправное или неисправное) рекомендации (или нет) к дальнейшей ее эксплуатации и указывается (в случае положительного решения) срок следующего обследования крана (приложение 14 РД 10-112-1-04).
Заключение подписывается экспертной комиссией и руководителем экспертной организации заверяется печатью прошивается с указанием количества сшитых страниц и передается владельцу ГПМ.
Владелец ГПМ передает заключение в территориальные органы ФСТН для рассмотрения и утверждения в установленном порядке.
Итоговое заключение о возможности продления срока безопасной эксплуатации ГПМ подписывается руководителем экспертной организации заверяется печатью прошивается с указанием количества страниц и передается заказчику который передает заключение экспертизы в ФСТН.
Решения принятые в заключении являются обязательными для владельца ГПМ. Заключение экспертизы является неотъемлемой частью эксплуатационной документации ГПМ.
Члены комиссии участвующие в обследовании должны соблюдать требования безопасности и охраны труда в соответствии с требованиями правил и инструкций по охране труда разработанными и утвержденными в установленном порядке.
Перед выходом на объект в экспертной организации для членов комиссии проводится инструктаж по технике безопасности в соответствии с инструкцией по технике безопасности для экспертов промышленной безопасности при проведении обследования подъемных сооружений согласованной в установленном порядке.
Для обеспечения безопасности труда в процессе проведения обследования ГПМ на предприятии члены комиссии должны пройти инструктаж по ТБ с учетом конкретных условий производства где находится объект. Владелец ГПМ должен выдать наряд-допуск на ГПМ и назначить лицо ответственное за безопасное ведение работ.
Запрещается проводить обследование ГПМ во время грозы снегопада гололеда тумана сильного дождя в темное время суток на открытом воздухе на высоте при скорости ветра более 10 мс.
Некоторые приложения к рекомендациям по экспертному обследованию грузоподъемных машин (РД 10-112-1-04):
Перечень нормативно-технических документов использованных в ходе экспертизы
Федеральный закон «О промышленной безопасности опасных производственных объектов» от 21.07.97 № 116-ФЗ (Собрание законодательства Российской Федерации. 1997. № 30. Ст. 3588).
Федеральный закон «О лицензировании отдельных видов деятельности» от 08.08.01 № 128-ФЗ.
Федеральный закон «О техническом регулировании» от 27.12.02 № 184-ФЗ.
Указ Президента Российской Федерации «О системе и структуре федеральных органов исполнительной власти» от 09.03.04 № 314.
Положение по проведению экспертизы промышленной безопасности опасных производственных объектов на которых используются подъемные сооружения (РД 10-528-03) Промышленная безопасность при эксплуатации грузоподъемных кранов-манипуляторов: Сборник документов. М: Федеральное государственное унитарное предприятие «Научно-технический центр по безопасности в промышленности» 2005. Сер. 10. Вып. 22.
Правила проведения экспертизы промышленной безопасности (ПБ 03-246-98) с Изменением № 1 [ПБИ 03-490(246)-02] утвержденным постановлением Госгортехнадзора России от 01.08.02 № 48 Экспертиза промышленной безопасности: Сборник документов. М.: Федеральное государственное унитарное предприятие «Научно-технический центр по безопасности в промышленности» 2006. Сер. 26. Вып. 2.
Положение о порядке продления срока безопасной эксплуатации технических устройств оборудования и сооружений на опасных производственных объектах (РД 03-484-02). М.: Федеральное государственное унитарное предприятие «Научно-технический центр по безопасности в промышленности» 2005. Сер. 03. Вып. 21.
Инструкция по надзору за изготовлением ремонтом и монтажом подъемных сооружений (РД 10-08-92) с изменением № 1 [РДИ 10-175(08)—98] утвержденным постановлением Госгортехнадзора России 09.01.98 № 1.
Положение о порядке утверждения заключений экспертизы промышленной безопасности (РД 03-298-99) с Изменением № 1 [РДИ 03-530(298)-03] утвержденным постановлением Госгортехнадзора России от 09.04.03 № 12 Экспертиза промышленной безопасности: Сборник документов. М.: Федеральное государственное унитарное предприятие «Научно-технический центр по безопасности в промышленности» 2006. Сер. 26. Вып. 2.
Методические указания по обследованию грузоподъемных машин с истекшим сроком службы. Часть 1. Общие положения (РД 10-112-96).
Рекомендации по подготовке и аттестации специалистов и экспертов осуществляющих экспертизу промышленной безопасности подъемных сооружений.
Положение о порядке подготовки и аттестации работников организаций осуществляющих деятельность в области промышленной безопасности опасных производственных объектов подконтрольных Госгортехнадзору России (РД 03-444-02).
Рекомендации по проведению испытаний грузоподъемных машин (РД 10-525-03).
Правила устройства и безопасной эксплуатации грузоподъемных кранов (ПБ 10-382-00).
Общие правила промышленной безопасности для организаций осуществляющих деятельность в области промышленной безопасности опасных производственных объектов (ПБ 03-517-02).
Правила устройства и безопасной эксплуатации подъемников (вышек) (ПБ 10-611-03).
Правила устройства и безопасной эксплуатации строительных подъемников (ПБ 10-518-02).
Правила устройства и безопасной эксплуатации кранов-трубоукладчиков (ПБ 10-157-97) с изменением № 1 [ПБИ 10-371(157)-00] утвержденным постановлением Госгортехнадзора России от 21.07.00 №43.
Правила устройства и безопасной эксплуатации грузоподъемных кранов-манипуляторов (ПБ 10-257-98).
Руководящий документ по оценке остаточного ресурса кранов мостового типа (РД 24-112-5Р).
Оценка остаточного ресурса грузоподъемных кранов. Методические указания (МУ 22-28-05-99).
Комплексное обследование крановых путей грузоподъемных машин. Часть 1. Общие положения. Методические указания (РД 10-138-97) с изменением № 1 [РДИ 10-349(138)-00] утвержденным постановлением Госгортехнадзора России от 30.03.00 № 12.
Пути наземные рельсовые крановые. Проектирование устройство и эксплуатация (СП 12-103-03).
Конструкция устройство и безопасная эксплуатация рельсовых путей башенных кранов (РД 22-28-35-99).
Временные рекомендации по устройству и безопасной эксплуатации наземных крановых путей (ВРД 50:48:0075.01.02).
Временные рекомендации по устройству и безопасной эксплуатации надземных крановых путей (ВРД 50:48:0075.03.02).
Стропы грузовые общего назначения. Требования к устройству и безопасной эксплуатации (РД 10-33-93) с изменением № 1 (РД 10-231-98) утвержденным постановлением Госгортехнадзора России от 08.09.98 № 57.
Инструкция по визуальному и измерительному контролю (РД 03-606-03).
Подъемно-транспортные машины. Материалы для сварных металлических конструкций (РД 24.090.52-90).
Правила устройства электроустановок (извлечения). М.: Федеральное государственное унитарное предприятие «Научно-технический центр по безопасности в промышленности» 2005.
Правила технической эксплуатации электроустановок потребителей. М.: Федеральное государственное унитарное предприятие «Научно-технический центр по безопасности в промышленности» 2005. Сер. 17. Вып. 7.
Межотраслевые правила по охране труда (правила безопасности) при эксплуатации электроустановок (ПОТ РМ-016-2001) (РД 153-34.0-03.150-00). Си доп. 2003 г. М.: Федеральное государственное унитарное предприятие «Научно-технический центр по безопасности в промышленности» 2005. Сер. 17. Вып. 6.
ГОСТ 25546-82*. Краны грузоподъемные. Режимы работы.
ГОСТ 25835-83*. Краны грузоподъемные. Классификация механизмов по режимам работы.
ГОСТ 28609-90. Краны грузоподъемные. Основные положения расчета.
ГОСТ 29266-91 (ИСО 9373-89). Краны грузоподъемные. Требования к точности измерений параметров при испытаниях.
ГОСТ 22045-89*. Краны мостовые электрические однобалочные опорные. Технические условия.
ГОСТ 27584-88*. Краны мостовые и козловые электрические. Общие технические условия.
ГОСТ Р 51248-99. Наземные рельсовые крановые пути. Общие технические требования.
Постановлением Ростехнадзора № 4 от 07.02.2001 г. вводится в действие РД 10-397-01 «Положение по проведению экспертизы промышленной безопасности (ЭПБ) подъемных сооружений». Этот документ устанавливает требования к порядку проведения экспертизы промышленной безопасности оформления и утверждения заключений экспертизы подъемных сооружений требования к экспертным органам.
Положение разработано в соответствии с требованиями:
-Федерального закона «О промышленной безопасности опасных производственных объектов» от 21.07.1997 г. № 116 ФЗ;
-Федерального закона «О лицензировании отдельных видов деятельности» от 25.09.1998 г. №158 ФЗ;
-Постановлением Правительства РФ от 25.07.1998 г. № 1540 «О применении технических устройств на опасных производственных объектах»;
-Правила проведения экспертизы промышленной безопасности (ПБ 03-246-98) утвержденных постановлением Ростехнадзора от 06.11.1998 г. № 64;
-Правил устройства и безопасной эксплуатации подъемных сооружений (ПБ 10-382-00) и других нормативно-технических документов регламентирующих цикл подъемных сооружений.
Экспертиза промышленной безопасности подъемного сооружения - это оценка соответствия подъемного сооружения предъявляемым к нему требованиям промышленной безопасности результатом которого является заключение.
Подъемные сооружения подвергаются экспертизе в случаях:
-исчерпания нормативного срока службы или наступления предельного состояния или по другим нормативным характеристикам;
-аварии подъемных сооружений или в случае их падения в условиях чрезвычайных ситуаций;
-выявление в процессе эксплуатации подъемных сооружений дефектов вызывающих сомнение в прочности конструкции или дефектов причину которых установить невозможно а также в случаях эксплуатации подъемных сооружений с отступлениями от паспортных характеристик.
Экспертные организации осуществляют экспертизу промышленной безопасности подъемных сооружений в соответствии с действующим законодательством правилами безопасности нормативно-правовыми документами РФ и Положением по проведению экспертизы промышленной безопасности подъемных сооружений.
Для каждого типа кранов разработаны руководящие документы на проведение ЭПБ например:
- РД 10-112-2-97 «Методические указания по обследованию грузоподъёмных машин с истекшим сроком службы. Часть 2. Краны стреловые самоходные общего назначения» ;
- РД 10-112-4-97 «Методические указания по проведению обследования портальных кранов с целью определения возможности их дальнейшей эксплуатации»
- РД 10-112-5-97 «Методические указания по обследованию грузоподъёмных машин с истёкшим сроком службы Часть 5 . Краны мостовые и козловые».
Процесс проведения ЭПБ состоит из этапов:
Предварительный этап (переговоры о порядке проведения экспертизы и др.);
Разработка документов устанавливающих условия проведения ЭПБ (срок проведения не должен превышать 3-х месяцев с момента получения комплекта необходимых материалов и документов в полном объеме в соответствии с действующей нормативно-технической документацией).
Процесс экспертизы (назначение экспертов сбор проектной конструкторской ремонтной эксплуатационной и др. документации для проведения ЭПБ) в общем случае включает в себя:
-анализ соответствия эксплуатационной документации требованиям нормативных документов;
-проведение необходимых расчетов включая определение остаточного ресурса;
-визуальный контроль с проведением проверки исправности механизмов и приборов безопасности;
-техническое диагностирование и контроль неразрушающими методами;
-проведение грузовых испытаний с учетом требований международных стандартов на которые имеются ссылки в нормативных документах.
Оформление и выдача заключения экспертизы.
При проведении ЭПБ крана необходимо рассмотреть следующие документы:
-паспорт и инструкцию по эксплуатации крана;
-документы об организации безопасной эксплуатации крана;
-документы об аттестации и проверке знаний обслуживающего персонала;
-графики технических обслуживании и ремонтов крана;
-протоколы по наладке и настройке приборов безопасности;
- технологические карты погрузочно-разгрузочных работ и складирования груза.
При обследовании крана необходимо дать (установить):
-оценку ведения эксплуатационной документации;
-оценку состояния технического обслуживания и надзора;
-наличие аттестованных кадров связанных с эксплуатацией крана;
-оценку исполнения требований технологических карт погрузоразгрузочных работ и складирования груза;
-общее состояние крана;
-состояние контролируемых параметров основных несущих элементов металлоконструкции крана;
-состояние механического оборудования;
-состояние гидрооборудования;
-состояние приборов и устройств безопасности.
На основании обследования технического состояния крана необходимо сделать расчетную оценку фактической группы классификации (режима нагружения) по отечественной (ГОСТ 22827) или международной (ИСО43011) методике.
В отчете по ЭПБ необходимо представить документы:
- справку о характере работы крана;
-выписку из паспорта крана;
-выписку из паспорта о проведенных ранее ремонтов крана;
-карту возможных повреждений металлоконструкции крана;
-ультразвуковой контроль сварных швов металлоконструкции;
-ультразвуковая толщинометрия металлоконструкции;
-акт обследования (по требуемой форме);
-протокол статических и динамических испытаний крана;
-расчет остаточного ресурса крана.
Проверка состояния металлоконструкции крана
Обследование состояния металлоконструкции включает следующие этапы:
- внешний осмотр состояния несущих и вспомогательных элементов а также сварных соединений
- дополнительную проверку элементов металлоконструкции и сварных соединений подозреваемых на наличие трещин
- измерение деформаций балок
- определение химического состава и химических свойств металла несущих и вспомогательных элементов
- составление заключения о результатах обследования
Таблица 13.1. - Элементы металлоконструкции козлового крана подвергаемые контролю.
Листовые балочные конструкции
Места соединения опор с пролетным строением козловых кранов и опор с ходовыми тележками
Трещины в металле и сварных швах
Техническое обслуживание и ремонт козлового контейнерного перегружателя.
Техническое обслуживание — комплекс операций по поддержанию работоспособности или исправности крана при использовании по назначению хранении и транспортировке.
Условия эксплуатации подъемно-транспортных машин (ПТМ) в значительной степени определяют срок службы механизмов узлов деталей.
Надежность и безотказность работы этих машин повышается при высокой культуре их эксплуатации и качестве ремонтов. Учет реальных условий эксплуатации ПТМ позволяет правильно определять меры необходимые для организации ремонта и других видов обслуживания например создание парка запасных частей и узлов разработку инструкции по обслуживанию и ремонту прогрессивные методы организации ремонтов.
1. Система планово-предупредительного ремонта.
В настоящее время на промышленных предприятиях транспортных и в строительстве ремонт подъемно-транспортных машин ведется в основном по единой системе применение которой при рациональной эксплуатации технологического оборудования машиностроительных предприятий обеспечивает работоспособное состояние оборудование при котором уменьшается его износ производится своевременная подготовка к ремонтам и сокращается время их проведения.
Системой планово-предупредительного ремонта (ППР) машин называют совокупность мероприятий обеспечивающих планово-предупредительный характер выполняемых работ ремонтов чередование и периодичность которых определяются назначением машины его конструктивными и ремонтными особенностями габаритными размерами и условиями эксплуатации.
Система ремонта является предупредительной потому что направлена на предупреждение остановки машины вследствие износа его узлов и деталей. Машины охваченные системой ППР останавливаются для ремонта по заранее составленному графику. Ремонт ПТМ должны компенсировать износы в течение периода времени предшествовавшего данному ремонту.
Основные положения направлений по ремонту машин и оборудования основные положения ремонтной практики и методы работы ремонтных служб предприятий систематизированы в книге: «Единая система ПТР и рациональной эксплуатации технического оборудования машиностроительных предприятий».
Системой ППР предусматривается проведения следующих мероприятий:
- ежемесячное техническое обслуживание выполняемое в течение рабочей смены (ЕО);
- периодическое техническое обслуживание выполняемое после отработки машинной определенного количества часов (ТО);
- текущие ремонты (Т);
- капитальные ремонты (К);
Текущие и капитальные ремонты различаются объемами работ. При текущем ремонте производят частичную разработку машин устранение неисправностей в агрегатах и узлах возникающих в процессе работы машин и препятствующих их нормальной эксплуатации замену отдельных агрегатов узлов и деталей (кроме базовых) новыми или заранее отремонтированными. При капитальном ремонте механической части ПТМ производят подетальную разработку и промывку всех узлов и механизмов обмоток электродвигателей и валов ротора переработку контактных колец а также производят испытания двигателей под нагрузкой и выполняют другие необходимые работы.
Капитальный ремонт является наиболее сложным техническим мероприятием в системе ППР и осуществляется он в том случае когда все другие виды ремонта не могут обеспечить работоспособное состояние.
2. Техническое обслуживание козлового контейнерного перегружателя состоит из:
ТО-1 которое включает в себя все виды обслуживания с периодичностью менее месяца а именно: сменное ежесуточное еженедельное. Эти виды обслуживания проводятся во время приема и сдачи смены в период отсутствия грузовых работ а также с выводом машины из эксплуатации но не более чем на 8 часов (одна дневная смена);
При ТО - 1 портовыми рабочими крановщиками и членами ремонтно-наладочных бригад выполняются следующие осмотры и проверки:
) Грузозахватного органа находящегося на кране;
)Подъемных канатов и их креплений;
)Наличия напряжений и соответствия его норме по вольтметру;
)Плавности и легкости хода штурвалов и рукояток контроллеров и командоконтроллеров;
)Работа тормозов и фрикционов;
)Действия аварийных выключателей (кнопок «Стоп») сигнализации конечных выключателей и нулевой блокировки (защит);
)Системы заземления визуально;
)Уборочные работы (подметание пола в кабине удаление с него масла; очистка поверхностей электродвигателей от пыли и грязи протирка смотровых стекол кабины).
)Плотности затяжки болтовых соединений механизма подъема механизма передвижения талей и кранов;
)Плотности затяжки болтовых соединений механизмов передвижения кранов;
)Состояния металлоконструкции крана;
)Очистка и протирка механизмов находящихся на открытом воздухе.
ТО-2 - периодическое техническое обслуживание крана включает обязательные работы и по потребности:
) Механизмы подъема и передвижения.
Обязательные работы:
проверка состояния всех болтовых соединений и стопорных устройств механизмов (контр гайки пружинные шайбы шплинты); зазоров разъемных подшипников; всех смазочных устройств и очистка засоренных маслопроводных каналов; проверка и регулировка отхода лент и колодок всех тормозов и фрикционов; проверка углубления головок заклепок тормозных и фрикционных обкладок; состояния всех канатов и их крепления и крюковой подвески; канатных блоков и устройств защищающих канат от схода с блоков; предохранительных ограждений движущихся частей; ограничителя грузоподъемности и концевых выключателей.
Работы по потребности:
замена отдельных крепежных болтов; отдельных
подшипников качения и вкладышей подшипников скольжения отдельных канатов поврежденных блоков и блочных осей; обкладок отдельных тормозов регулировка положения отдельных валов открытых зубчатых передач при резком нарушении правильности работы зубчатых пар; пальцев и втулок отдельных эластичных муфт; установка отдельных масленок и ниппелей; правка отдельных тяг и рычагов ручного управления; устранение задиров шеек отдельных валов и осей; поверхностная смазка всех канатов.
) Металлоконструкции.
проверка состояния заклепочных болтовых сварных соединений металлоконструкций крана наиболее часто повреждаемых; прямолинейности ответственных стержней металлоконструкций; крепление трапов и настилов (площадок).
правка отдельных стержней металлоконструкций; вырубка и подварка поврежденных швов в узлах смена ослабших заклепок; рихтовка и восстановление отдельных участков настилов и ограждений трапов; устранение водотечности крыши кабины и исправление ее окон и дверей.
ТО - 2 кранов должно выполняться через часов работы определяющих время занятости крана на перегрузочных работах.
-коэффициент имеющий следующие значения: крана на грейферной работе – ; 50% времени кран на грейферной работе – ; кран с крюком – .
Превышение регламентируемого планом-графиком периода между ТО - 2 допускается не больше одной недели. Плановое время простоя крана на ТО - 2 не должно превышать для береговых кранов - 2 суток.
Таблица 14.1. - Типовой регламент по техническому обслуживанию и ремонту гидроприводов
Содержание работ по техническому обслуживанию
Вид технического обслуживания
Проверить уровень масла в баке; при необходимости восстановить
Проверить температуру масла в баке (на ощупь); при необходимости проверить работу устройств разгрузки и охлаждения
Проверить степень засорения фильтра по индикатору или манометру; засоренные фильтроэлементы промыть и заменить
Проверить уровень давления в напорной линии и других точках гидросистемы по манометрам; при необходимости произвести регулировку клапанов
Проверить визуально наружные утечки; при необходимости устранить течи
Проверить уровень шума и вибрации при работе (на слух); при необходимости заменить неисправные элементы
Проверить расход масла через дренажную линию (визуально при наличии прозрачного трубопровода)
Проверить наличие пены на поверхности масла в баке а также мутность масла; при необходимости устранить возможность попадания воздуха и воды в масло
Проверить давление зарядки аккумулятора (если он имеется) по манометру; при необходимости аккумулятор подзарядить
Проверить состояние заделок гибких металлорукавов; при необходимости заменить рукава
Произвести настройку регулирующих аппаратов (при необходимости): дросселей тормозных устройств клапанов реле давления
Определить мощность холостого хода регулируемых насосов (по силе тока в фазе приводного электродвигателя) а также максимальную подачу (по скорости движения рабочих органов); при необходимости насос заменить
Определить максимальную подачу нерегулируемых насосов (по скорости движения рабочих органов); при необходимости насос заменить
Определить величину утечек в сливную линию при неработающих гидродвигателях; при необходимости заменить дефектные узлы
Проверить срабатывание аварийных блокировок (зажим патрона датчики давления блокировки движений систему диагностики); при необходимости произвести дополнительную регулировку
Взять пробу масла на анализ; при отрицательном результате очистить бак и заменить масло
Очистить воздушный фильтр и магнитные патроны (если имеются) в баке
Проверить надежность закрепления гидроагрегатов; при необходимости подтянуть крепежные элементы
Содержание работ по ремонту
Выполнить при необходимости операции по ТО указанные выше
Очистить от пыли и грязи радиаторы воздушного охлаждения
Заменить унифицированные узлы и детали отработавшие ресурс
Проверить внутреннюю полость бака; при наличии коррозии зачистить до металлического блеска и окрасить
Отремонтировать специальные узлы гидропривода с последующим испытанием на стендах
*В скобках указано время необходимое для восстановления работоспособности (периодичность -при необходимости).
П р и м е ч а н и е. ЕО - ежедневное обслуживание; ТО - технический осмотр; Т- текущий ремонт; С - средний ремонт; К - капитальный ремонт.
Если грузоподъемная машина по техническому состоянию не требует капитального ремонта ранее установленного графиком срок до капитального ремонта может быть продлен комиссией предприятия-владельца не более чем на 25 процентов межремонтного цикла с учетом результатов обследования машины оценки надежности работы ее металлоконструкций узлов и механизмов.Результаты работы комиссии и ее предложения оформляются актом.
Предприятия организации граждане(предприниматели)производящие ремонт грузоподъемных машин с применением сварки или их реконструкцию в заводских условиях или на месте их установки должны иметь лицензию технадзора на этот вид деятельности.
На проведение капитального ремонта конкретной модели крана предприятие имеющее лицензию должно получить разрешение технадзора в порядке установленном "Инструкцией по надзору за изготовлением подъемных сооружений" (кроме лифтов эскалаторов) на предприятиях подконтрольных технадзору.
Предприятия организации и граждане(предприниматели) производящие ремонт грузоподъемных машин с применением сварки или их реконструкцию в заводских условиях или на месте их установки должны иметь лицензию технадзора на этот вид деятельности.
Если ремонт с применением сварки производится по заказам других владельцев грузоподъемных машин то указанные предприятия граждане должны иметь собственные лаборатории по контролю качества сварки металла.
На проведение капитального ремонта конкретной модели крана предприятие имеющее лицензию должно получить разрешение органа технадзора в порядке установленном"Инструкцией по надзору за изготовлением подъемных сооружений" (кроме лифтов эскалаторов) на предприятиях подконтрольных органу технадзора.
Ремонт (реконструкция) крана с изменением длины моста крана если возможность таких изменений не предусмотрена паспортом крана или инструкцией по его эксплуатации другие работы связанные с изменением конструкции или паспортных данных крана должны производиться по проекту разработанному специализированной организацией. При разработке проекта должно быть учтено фактическое состояние крана (степень износа наличие повреждений и пр.).
Предприятие производящее ремонт и реконструкцию грузоподъемных кранов должно отразить в паспорте крана характер произведенной работы и внести в него сведения о примененном материале (сталь сварочные материалы и т.п.) с указанием номера сертификата. Документы подтверждающие качество примененного материала и сварки должны храниться на предприятии производившем работы.
При выполнении капитального ремонта крана отработавшего нормативный срок службы ремонтное предприятие выполненным объемом и качеством работ должно обеспечить продление срока службы крана не
менее чем на 20 процентов от нормативного. Сведения о продлении срока эксплуатации должны быть записаны ремонтным предприятием в паспорт крана.
Результаты осмотров и технических обслуживаний сведения о ремонтах грузоподъемных машин должны записываться в журнал. Сведения о ремонтах вызывающих необходимость внеочередного технического освидетельствования машины заносятся в ее паспорт.
Вывод крана в ремонт должен производиться специалистом ответственным за содержание грузоподъемных машин в исправном состоянии в соответствии с графиком ремонта утвержденным владельцем.
Использование крана для работы во время его ремонта не разрешается.
Разрешение на работу крана после ремонта кроме случаев выдается специалистом ответственным за содержание грузоподъемных машин в исправном состоянии с записью в вахтенном журнале.
Для правильного обслуживания грузоподъемных кранов владелец обязан обеспечить крановщиков их помощников слесарей электромонтеров и стропальщиков инструкциями определяющими их права обязанности порядок безопасного производства работ и ответственность.
Руководитель предприятия-владельца грузоподъемной машины или гражданин (предприниматель) в процессе эксплуатации должны обеспечить правильное ведение и хранение паспортов и технической документации на грузоподъемные машины съемные грузозахватные приспособления тару и крановые пути а также журналов периодической проверки знаний персонала сформулированы его конкретные обязанности и права.
3. Технология ремонта.
3.1. Материалы применяемые при ремонте козлового крана
Все материалы применяемые для ремонта металлоконструкций по своим механическим и качественным характеристикам должны отвечать требованиям соответствующих стандартов технических условий указанных в рабочих чертежах завода-изготовителя или в ремонтных чертежах.
Соответствие материалов подтверждается сертификатами заводов-поставщиков или данными дополнительных лабораторных испытаний.
Применение материалов без проверки их на соответствие требованиям указанных документов путем проведения входного контроля качества не допускается службой технического контроля ремонтного подразделения.
Стальной прокат поступивший на склад хранится в условиях не допускающих снижения его качества. На поверхности проката не допускается наличия трещин расслоений неметаллических включений закатов. Дефекты устраняются пологой вырубкой или зачисткой с шириной вырубки или зачистки не менее пятикратной глубины дефектов.
Запрещается заварка или заделка указанных дефектов.
На поверхности стального проката допускается: тонкий слой окалины или коррозии не препятствующий выявлению поверхностных дефектов отдельные раковины риски волосовины вмятины рябизна и пр.
Марки сталей для ремонта основных и вспомогательных элементов металлоконструкций кранов всех типов (в том числе кранов северного исполнения и зарубежного производства) должны соответствовать или быть равноценными маркам. Замена марки осуществляется только по согласованию с разработчиком проекта с оформлением соответствующего документа.
Химический состав прокатных малоуглеродистых сталей предназначенных для ремонта металлоконструкций по содержанию примесей должен соответствовать требованиям стандартов на эти стали. Верхний предел углерода не должен превышать 022%.
Для несущих сварных металлоконструкций эксплуатируемых при температуре ниже – 20С применяются низколегированные стали.
В случае сильноагрессивной атмосферы следует применять более коррозионно-стойкую сталь марок 10ХСНД 15ХСНД.
При заказе сталей для ремонта несущих элементов металлоконструкции в заказе-наряде должно быть оговорено требование поставки с перспективными характеристиками по прочности выносливости и ударной вязкости.
При выборе марки стали для ремонта следует учитывать экономическую и производственную целесообразность её применения:
- углеродистую сталь ВСт3пс5 следует применять в листовом фасонном и широкополосном прокате толщиной до 10мм включительно и в сортовом;
- до 16мм включительно для кранов общего назначения при температурах эксплуатации до -30С;
- сталь ВСт3сп5 следует применять в листовом фасонном и широкополосном прокате толщиной более 10мм и в сортовом – более 16мм при температуре эксплуатации ответственных крановых конструкций до -40С;
- профильный и листовой прокат из сталей ВСт3сп ВСт3пс толщиной до 10мм рекомендуется для применения в крановых конструкциях эксплуатируемых до температуры - 40С;
- недопустимо применение в сварных конструкциях кипящей стали ВСт3кп; указания сталь может быть применена в малонагруженных сварных элементах не участвующих в работе конструкций (настилы ограждения лестницы кожухи обшивки кабины и пр.);
- допускается применения низколегированных сталей (09Г2 09Г2С 14Г2) для ремонта сварных конструкций изготовленных из Ст3 которую не рекомендуется использовать для сварных конструкций из низкоуглеродистых сталей.
Одним из наиболее характерных способов ликвидации трещин в металлоконструкции является сварка.
3.2. Сборка и подготовка к сварке элементов металлоконструкций
Прежде всего необходимо проверить соответствие предельных размеров отклонений формы деталей и зазоров чертежам с требованиями ГОСТ 5264-80.
Свариваемые кромки и прилегающие к ним зоны металла шириной не менее 20мм должны быть очищены от ржавчины грязи масла влаги.
В стыковых соединениях должны быть предусмотрены выводные планки размеры которых: длина – не менее толщины сварных элементов.
Принудительная прогонка деталей к элементам нарушающим конструктивные формы предусмотренные чертежами запрещается.
При сборке деталей под сварку допускаются следующие отклонения от проектного расположения деталей:
а) в стыковых соединениях:
- смещение свариваемых кромок относительно друг друга при толщине стыкуемых деталей не более 4мм – 05 мм при толщине от 4 до 10мм;
- до 1мм при толщине свыше 10мм – 01 толщины стыкуемых деталей но не более 3мм;
- уступ кромок в плоскости соединения для полок элементов и свободных по ширине деталей – не более 3мм для деталей шириной от 400 мм и более;
- уступ кромок в соединениях замкнутого контура – не более 2мм по всему периметру;
б) в шаровых соединениях отклонения полки от заданного по чертежу положения – не более 1:100.
Дефектные элементы (участки) удаляют разделительной резкой или механическим путем. При удалении дефектного участка рез должен проходить по телу удаляемого элемента без захвата основного металла. Место реза должно быть зачищено.
Трещины проходящие по телу элементов металлоконструкций разделываются в конце их выполняется засверловка диаметром не менее 15мм для ограничения границ трещины затем они завариваются. Отверстия ограничивающие трещину не завариваются.
3.3. Сварка элементов металлоконструкций
Сварка металлоконструкций проводится в соответствии с требованиями технологического процесса утверждённого специализированной организацией.
К сварке расчетных несущих металлоконструкций и их элементов допускаются сварщики аттестованные в соответствии с правилами аттестации сварщиков утвержденными Ростехнадзором.
В удостоверениях сварщиков выполняющих сварку в различных пространственных положениях должна иметься соответствующая отметка.
Сварные соединения несущих элементов металлоконструкций должны иметь клеймо.
Сварочные работы выполняются согласно требованиям техники безопасности действующим на предприятии картам технологического процесса и ГОСТ12.3.003-86.
Перед сваркой сварочную проволоку отчищают от грязи и ржавчины. Электроды и флюс просушивают прокаливают согласно режимам указанным в паспортах на эти материалы.
Сварка металлоконструкций преимущественно выполняется высокопроизводительными способами (автоматическая и полуавтоматическая под флюсом в среде углеродистого газа порошковой проволокой).
Во избежание создания в металлоконструкциях при сварке реактивных напряжений выполняют в свободном состоянии стыковые швы расположенные перпендикулярно силовому потоку затем остальные стыковые швы и в последнюю очередь - угловые и тавровые швы. Положения свариваемых металлоконструкций должны обеспечивать наиболее удобные и безопасные условия для работы сварщика и получения швов высокого качества.
Сварку металлоконструкций производят в положениях исключающих влияние неблагоприятных атмосферных условий на качество соединений.
Допускается выполнение сварочных работ на открытом воздухе при условии применения соответствующих приспособлений для защиты мест сварки а также свариваемых поверхностей металлоконструкций от попадания атмосферных осадков от ветра влияния отрицательных температур.
При двусторонней сварке швов стыковых сварных соединений а также угловых и тавровых сварных соединений с разделанными кромками со сквозным проплавлением перед выполнением шва с обратной стороны очищают корень шва до чистого бездефектного металла.
По окончании сварки очищают швы и прилегающие к ним зоны от шлака брызг и натеков металла а выводные планки удаляют. Удаление выводных планок производят кислородной резкой или механическим путем после чего торцы швов зачищают. Удаление выводных планок ударами молотка или кувалды запрещается.
3.4. Контроль качества сварных соединений
Контроль качества сварных соединений производят любым из следующих методов:
- внешним осмотром и замером шва ГОСТ 3242-79;
- за сверловкой или вскрытием воздушно-дуговой выплавкой;
- радиографическим ГОСТ 7512-82;
- ультразвуком ГОСТ 14782-86 при согласовании с Ростехнадзором и специализированной организацией;
- механическим испытанием контрольных образцов ГОСТ 6996-86.
3.5. Защитные покрытия металлоконструкций
Окраску металлоконструкций после ремонта выполняют согласно конструкторской документации завода-изготовителя на конкретный кран где в соответствии устанавливаются требования к цветовым сочетаниям применяемым маркам красок лаков а также с учетом требований Ростехнадзора.
Защита металлоконструкций крана от коррозии выбор схемы защиты зависит от условий эксплуатации и соответствуют требованиям СНиП 3.04.03.-85 и СНиП 2.03.11.-85.
Подготовку поверхности и окраску производят в отапливаемом вентилируемом помещении при температуре не ниже 18°С и относительной влажности не более 75%. Допускается при необходимости выполнение этих работ на открытом воздух при температуре не ниже 10°С влажности не более 75% и отсутствии запыленности. Помещения должны быть соответствовать требованиям ГОСТ 9.402-80.
Защита металлоконструкций осуществляется путем нанесения лакокрасочных покрытий класс покрытия 1У или УП по ГОСТ 9.032-74.
Цвета сигнальные и знаки безопасности на кранах должны соответствовать ГОСТ 12.4.026-76. Требование к цветовому обозначению частей крана опасных при эксплуатации по ГОСТ 12.2.060-81.
Работы по нанесению лакокрасочных покрытий следует проводить согласно общим требованиям безопасности по ГОСТ 12.3.005-75. Операция по нанесению защитных покрытий осуществляют в следующей последовательности:
- снять старую краску и продукты коррозии;
- провести обезжиривание;
Грунтование под эмалевое покрытие производят на сухие поверхности не позднее чем через 10 часов после окончания очистки. Для грунтования поверхностей применяют грунтовки ГФ-021 по ГОСТ 25.1290-82 ФЛ-ОЗЖ по ГОСТ 9109-81.
Все недоступные для окраски щели и углубления в которые может проникнуть влага а также местные неровности подлежат шпаклеванию с толщиной слоя не более 15мм. Применяют шпаклевку ПФ-002 по ГОСТ 10277-90 наносят и применяют шпаклевку в соответствии с ГОСТ10277-90.
Окраску элементов металлоконструкций производят в два слоя только после полного высыхания грунтовки и шпаклевки.
Лакокрасочные покрытия должны быть однотонными; наносят их равномерным слоем без подтеков трещин пузырей оспин отслоений.
Консервации подлежат все незащищенные лакокрасочными покрытиями поверхности металлоконструкций.
Операции по подготовке поверхностей для их консервации выполняют согласно требованиям ГОСТ 9.014-78.
Для консервации применяют смазку АМС-3 по ГОСТ 2712-75. Толщина наносимого слоя – от 05 до 15 мм.
Данные о консервации оформляют свидетельством о консервации.
4. Смазка механизмов крана.
Смазка должна производится в соответствии со схемой смазки и таблицей смазки.
При отсутствии масел и смазок указанных в таблице смазки допускается применение других масел и смазок предназначенных для тех же целей. Перед смазкой тщательно очистить от пыли и грязи место смазки. После смазки во избежание прилипания пыли и грязи необходимо тщательно вытереть выступающую наружу смазку. При смазке шарниров и осей смазка подается до тех пор пока не будет выходить свежая смазка из мест стыков деталей подвергающихся смазке. Не допускается попадание смазки на обмотку двигателя при смазке его подшипников.
Карты смазки. В каждой инструкции по эксплуатации крана имеется карта смазки крана включающая схему крана.
На схеме указываются смазываемые точки и их номера; в карте приводятся номера смазываемых точек наименование механизма или детали подлежащих смазке способ смазки режим и количество смазки в смену на каждую смазываемую деталь наименование смазки и расход ее в течение года. В табл. 14.2 приведен пример карты смазки крана БКСМ-3. При эксплуатации крана следует строго придерживаться указаний содержащихся в карте смазки. Несвоевременная смазка приводит к быстрому износу машины и повышенному расходу энергии. Обильная смазка так же вредна как и недостаточная.
Новый кран следует смазывать обильнее чем кран бывший в работе. Так например масленки заправляемые обычно одич раз в сутки в первые 10—15 дней следует заправлять два раза в смену.
Спустя 10—15 дней следует перейти на обычный режим смазки указанный в карте смазки.
Способы смазки. При смазке механизма необходимо принимать меры предотвращающие попадание в смазочные материалы посторонних загрязняющих примесей. Пыль песок и другие вредные примеси попадая между трущимися деталями вызывают быстрый износ деталей что ухудшает их эксплуатацию и приводит к преждевременному ремонту.
Смазку наносят на трущиеся поверхности различными способами. Жидкую смазку подают посредством масленок и колец непрерывно по фитилям или каплями из бачка через определенные промежутки времени (фитильная и капельная смазка) под давлением от насоса особого устройства или заливают в корпус редуктора.
Густую смазку подают под давлением с помощью шприца намазывают на открытые передачи или вручную набивают в корпусы подшипников лопаточками.
При смазке следует руководствоваться следующими основными правилами.
Перед нанесением новой смазки очищать смазываемую де таль от грязи и старой смазки и промывать керосином после чего насухо вытирать.
При подаче густой смазки под давлением проверять дошла ли смазка до трущихся поверхностей; при этом сначала под давлением должно выходить старое масло темного цвета а потом новое — светлого цвета. Если этого не наблюдается необходимо прочистить весь маслопровод от грязи и старой смазки.
Проверять качество смазочного материала на отсутствие воды и других примесей. Консистентные мази кроме того не должны содержать комков и посторонних примесей что проверяется растиранием смазки на пальцах. Жидкие масла перед употреблением желательно профильтровать.
Хранить смазочные материалы в закрытой чистой посуде отдельно по видам и сортам.
Не производить смазку на ходу машины.
Экономно использовать смазочные материалы и не расходовать их сверх установленной нормы.
Канаты смазывают перед первоначальной установкой их на кран а также всякий раз при новом монтаже крана. Лучший способ смазки каната — погружение его перед установкой на сутки в бак с минеральным маслом.
Предложения по внедрению.
Сегодня козловой контейнерный перегружатель является основным подъемным средством для перегрузки средне- и крупнотоннажных контейнеров различных типов и грузоподъемности. Одной из важнейших особенностей контейнерных козловых перегружателей является возможность перекрывать большие перегрузочные и складские площади по которым проложены подъездные пути разных видов транспорта например автомобильного и железнодорожного. Поэтому данный перегружатель предлагается использовать в складских зонах в настоящее время активно развивающихся контейнерных терминалах с большим грузооборотом и темпом обработки контейнеров железнодорожных автомобильных морских речных а также на контейнерных площадках промышленных предприятий и складов.
Предполагается оснащать гидроприводом выходящие из капитального ремонта краны или вновь выпускаемые.
Снижение динамических нагрузок повышает надежность механизмов и металлоконструкций грузоподъемных машин. Поэтому предполагается так же использовать гидрофицированные козловые перегружатели в тех производственных районах в которых отказы работы крана сопряжены с прекращением производства работ и большими экономическими потерями из-за простоя оборудования и т.п. так как такие перегружатели имеют большую надежность по сравнению с электроприводными.
В дипломном проекте разработан гидрофицированный козловой контейнерный перегружатель грузоподъемностью 40 тонн. Металлоконструкция перегружателя аналогична перегружателю с электрическим приводом механизмов. Приводы всех механизмов оснащены высокомоментными гидромоторами питающимися от одной насосной станции с двумя аксиально-поршневыми насосами.
Применение гидропривода позволяет обеспечить глубокое и бесступенчатое регулирование скорости исполнительных звеньев простоту регулирования мощности приводов возможность выполнения механизмов без редукторов и фрикционных тормозов более высокую мощность при той же массе по сравнению с другими типами приводов возможность использования широкого диапазона скоростей снижения динамических нагрузок на металлоконструкцию и механизмы в периоды неустановившегося движения упрощение схемы управления. Вместе с этим применение гидропривода повышает надежность козлового крана из-за снижения динамических нагрузок и упрощения кинематических и электрических схем приводов механизмов.
Привод механизма подъема оснащен высокомоментным гидромотором. Который через зубчатую муфту расположенную в барабане передают крутящий момент на барабан лебедки. Гидролиния механизма подъема оснащена обратными управляемыми клапанами (гидрозамками) которые в случае утечек рабочей жидкости по поршню гидромотора смогут обеспечить удержание груза. Опускание груза осуществляется под действием его веса а заполнение холостой полости гидромоторов происходит с помощью подпиточного насоса. Жидкость вытесняемая из рабочей полости гидромотора идет на зарядку аккумулятора. Настройка скоростей подъема и опускания выполняется регулированием механизма изменения подач насоса и дроссельных регуляторов расхода.
Приводы механизмов передвижения тележки и крана оснащены высокомоментными гидромоторами передающими крутящий момент непосредственно на ходовые колеса крана через муфты. Механизмы передвижения не имеют редукторов и фрикционных тормозов. Как было сказано выше гидромоторы обеспечивают плавный разгон и торможение а так же выбор любой скорости передвижения в диапазоне от нулевой до номинальной.
Время разгона механизмов определяется уровнем давления в гидросистеме и настройкой дросселей регулятора подачи насоса и дросселей регулирующих время срабатывания золотника гидрораспределителя.
В дипломном проекте рассчитаны и скомпонованы все механизмы перегружателя составлена гидравлическая схема перегружателя выбрана гидроаппаратура. Составлена графоаналитическая характеристика привода. Выполнен прочностной расчет металлоконструкции козлового контейнерного перегружателя. Разработана технологическая схема работы перегружателя в складской зоне контейнерного терминала. Проведена оценка капиталовложений по кранам с электроприводом механизмов и гидрофицированным приводом. Внесены предложения по внедрению контейнерного перегружателя.
СПИСОК ИСПОЛЬЗОВАННОЙ ЛИТЕРАТУРЫ.
[1] — Александров М. П. Подъемно-транспортные машины. – М.; Высшая школа 1985 г.
[2] — Александров М. П. Подъемно-транспортные машины. Атлас конструкций.- М. ”Машиностроение” 1987 г.
[3] — Киселев В.А.Захарцев В. П. Методические рекомендации по курсовому по курсу “Портовые подъемно-транспортные машины”- М.; 2002 г.
[4] — Гохберг М. М. Справочник по кранам. Т.1”Машиностроение” 1988 г.
[5] — Гохберг М. М. Справочник по кранам. Т.2”Машиностроение” 1988 г
[6] — Каталог. Людиновское производственное объединение “Агрегатный завод” 1987 г.
[7] — Паспорт. Гидромоторы высокомоторные радиально-поршневые типа МРФ.
[8] — Свешников В. К. Станочные гидроприводы. Справочник. -М.;2004 г.
[9] — Баржанский Е. Е. Методические указания.”Приводы перегрузочных машин”- М.; 2000г.
[10] — Замолотчиков А.М. Методические указания. “Технология и механизация перегрузочных работ”.-М.; 2002 г.
[11] — Кузнецов А.Л. Оборудование контейнерных терминалов.- С.; 2001 г.
[12] — Галабурда М. А.”Металлоконструкции ПТМ”. Методическое пособие. М.;
[13] — Руководство по проектированию речных портов
[14] — Единые комплексные нормы выработки и времени на перегрузочные работы выполняемые в речных портах и на пристанях. Часть 12 Москва 1988
[15] — Нормативы времени на перегрузочные работы выполняемые в речных портах и на пристанях М.Транспорт 1990 112 с.
[16] — А. П. Казаков Технология и организация перегрузочных работ на речном транспорте М. Транспорт 1984 415 с.
[17] – Технические условия размещения в судах и на складах тарно-штучных грузов.