Кинематический анализ поперечно строгольного станка с проектированием режущего инструмента



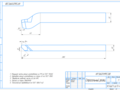
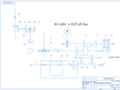
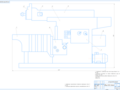
- Добавлен: 25.01.2023
- Размер: 1 MB
- Закачек: 0
Описание
Состав проекта
![]() |
![]() |
![]() |
![]() ![]() ![]() |
![]() ![]() ![]() |
![]() ![]() ![]() |
![]() ![]() ![]() |
![]() ![]() ![]() |
![]() ![]() ![]() |
![]() ![]() ![]() |
![]() ![]() ![]() |
![]() ![]() ![]() |
![]() ![]() ![]() |
![]() |
![]() ![]() ![]() ![]() |
![]() ![]() ![]() ![]() |
![]() ![]() ![]() ![]() |
Дополнительная информация
Введение.docx
Относительно невысокая производительность строгальных станков объясняется потерей времени на холостой ход а также трудностями повышения скоростей главного рабочего движения из-за возрастания инерционных усилий при реверсировании.
В целях повышения производительности станков этой группы многие предприятия прибегают к их модернизации которая осуществляется по трем основным направлениям:
упрощение управления станками;
использование обратного хода для строгания;
расширение технологических возможностей станков.
Однако модернизация строгальных станков весьма затратное мероприятие поэтому в наше время в металлообработке используются фрезерные станки.
В настоящее время строгальные станки нашли широкое применение в деревообработке.
6.docx
Модели станков снабженных гидрофицированными устройствами обеспечивающими плавное (бесступенчатое) регулирование числа двойных ходов и подач являются наиболее совершенными. Гидравлический привод состоит из сдвоенного лопастного насоса типа ЛЗФС производительностью 100 и 50 лмин. гидропанели панели управления обратного клапана золотника подачи золотника включения манометра дросселя подачи и двух цилиндров — главного движения (ползуна) и подачи. Установка длины строгания производится двумя передвижными упорами расположенными в Т-образном пазу планки закрепленной на правой боковой стороне ползуна станка. Расстояние между рисками на упорах определяет длину строгания. Отсчет величины строгания ведется по линейке установленной на Т-образной планке.
2,Расчет базовых элементов станка!.docx
1 Обоснование вида направляющих станка и выбор материала
На верхней части станины имеются плоские горизонтальные направляющие к которым прикрепляются винтами планки создающие форму направляющих типа «ласточкин хвост». По этим направляющим перемещается ползун. Одна из этих направляющих планок регулируется винтами на боковой стенке станины что обеспечивает плотность посадки ползуна на направляющих.
На передней стенке станины расположены плоские направляющие для вертикального перемещения поперечины на которой закреплен стол. Внутри станины находятся коробка скоростей и кулисный механизм для монтажа и наблюдения за которыми в стенках станины имеются отверстия и люки с крышками. На задней стенке станины установлен кронштейн где монтируется электродвигатель. Для отвода масла стекающего с направляющих ползуна на задней стенке станины расположен лоток. Материал направляющих СЧ 15.
2 Обоснование конструкции основных базовых элементов и выбор материала.
Станина представляет собой чугунный литой корпус коробчатой формы расположенный на плите закрепляемой болтами к фундаменту. Внутренние ребра обеспечивают станине необходимую прочность и жесткость. Станина выполнена из СЧ 15.
7.docx
1 Назначение режущего инструмента
В строгальных станках применяются строгальные резцы. Строгальные резцы бывают прямые и изогнутые. Прямые резцы просты в изготовлении но менее виброустойчивы по сравнению с изогнутыми. Поэтому они применяются при малых величинах вылета. В случае работы с большими вылетами рекомендуется пользоваться изогнутыми резцами которые получили широкое распространение в промышленности. В процессе строгания резец под воздействием усилий резания изгибается. При изгибе прямого резца его режущая часть будет углубляться в материал заготовки и резец будет работать с заеданием что снижает качество обработки и дополнительно нагружает инструмент. При изгибе же изогнутого резца его режущая часть будет отходить от заготовки и срезать меньший слой металла. Это обеспечивает более спокойное протекание процесса резания особенно при резких колебаниях усилий резания вызываемых изменениями сечения срезаемого слоя локальными изменениями свойств обрабатываемого материала и т. п.
2 Технические требования предъявляемые к инструменту.
Строгальные резцы как и всякий режущий инструмент должны обладать высокой твердостью которая должна быть выше твердости обрабатываемых материалов. Вместе с тем материал резца должен быть достаточно вязким чтобы режущие кромки не выкрашивались под давлением стружки. Необходимо также чтобы резцы имели высокую износоустойчивость. В процессе резания возникает трение по передней и задней поверхностям инструмента. Стружка истирает Переднюю а деталь точнее ее поверхность резания заднюю поверхность инструмента. Это приводит к затуплению резца а при обработке длинных деталей кроме того сказывается и на размерах последних. Отсюда следует что основным качеством режущих инструментов для их производительной работы должны быть твердость и износоустойчивость. Но этого еще недостаточно. Дело в том что в процессе резания выделяется много теплоты. Часть ее поступает в инструмент и постепенно разогревает его режущие кромки и поверхности. Когда температура резца достигает определенного значения он теряет свою первоначальную твердость и быстро выходит из строя. Резцы изготовленные из различных материалов имеют неодинаковую устойчивость к действию теплоты. Одни теряют свои режущие свойства при температуре 200—250° С а другие способны резать при температуре 1000° С и более. Таким образом третьим требованием предъявляемым к материалам для режущих инструментов является высокая теплостойкость или температуроустойчивостъ. Чем выше теплостойкость резца тем более высокими при прочих равных условиях могут быть режимы резания тем выше производительность при резании.
3 Элементы конструкции и геометрические параметры инструмента.
Основные сведения о резцах. Резец состоит из двух частей: головки (режущей части) и стержня (тела) Служащего для закрепления резца (рис. 3)
На режущей части различают следующие элементы: переднюю поверхность 2 по которой сходит стружка; главную 1 и вспомогательную 6 задние поверхности обращенные к обрабатываемой детали; главную режущую кромку образованную пересечением передней и главной задней поверхностей; вспомогательную режущую кромку 5 образованную пересечением перед ней и вспомогательной задней поверхностей; вершину резца 4 образованную пересечением главной и вспомогательной режущих кромок.
Рисунок 3- Строгальный проходной резец.
Углы резца. Главные углы резца измеряются в главной секущей плоскости (сечение Б-Б на рис.4) К ним относятся: задний угол угол заострения передний угол и угол резания. Обозначаются эти углы буквами греческого алфавита.
Главным задним углом называется угол между главной задней поверхностью резца и плоскостью резания.
Углом заострения называется угол между главной задней поверхностью и плоскостью касательной к передней поверхности резца.
Передним углом называется угол между плоскостью касательной к передней поверхности резца и плоскостью перпендикулярной к плоскости резания проведенной через главную режущую кромку.
Углом резания называется угол между плоскостью касательной к передней поверхности резца и плоскостью резания.
Рисунок 4-Углы заточки строгального резца
Вспомогательным задним углом называется угол между вспомогательной задней поверхностью резца и плоскостью проходящей через вспомогательную режущую кромку перпендикулярно к основной плоскости (сечение В-В на рис. 5)
Главным углом в плане называется угол между проекцией главной режущей кромки на основную плоскость и направлением обратным направлению подачи.
4 Расчет геометрических параметров инструмента.
Выберем строгальный резец по ГОСТ 18887-73.
В ходе выполнения курсового проекта был произведено ознакомление с технологическими возможностями станка устройством и принципом действия станка его кинематической схемой. В ходе курсового проектирования был произведён кинематический анализ поперечно-строгального станка. Также было произведено ознакомление с правилами эксплуатации и технического обслуживания станка и требованиями безопасности при работе не нём.
При выполнении курсового проекта были использованы знания о кинематике станков. При выполнении курсового проекта использовались ГОСТы нормативные документы и справочная литература. А также для разработки чертежей использовалась такая программа как kompas V10.
Глубокий В.И. Металлорежущие станки и промышленные роботы. Ч. 1. Конструирование металлорежущих станков. – Мн. 1988.
Жданович В.В. Техническая эксплуатация технологического оборудования: курсовое и дипломное проектирование В.В. Жданович.- Мн.: «Беларусь» 2006- 278с.:ил.
Локтева С. Е. Станки с программным управлением: Учебн. Пособие для машиностроительных техникумов. – М.: Машиностроение 1979.- 288 с.ил.
Копылов Р.Б. Работа на строгальных и долбежных станках Учебн. Пособие для машиностроительных техникумов. – М.: Машиностроение 1979.- 392 с.ил
Чернов Н.Н. Металлорежущие станки: Учебник для машиностроительных техникумов.-3-е изд. перераб. и доп.- М.: «Машиностроение»1978-389 с. ил.
Черпаков Б. И. Альперович Т. А. «Металлорежущие станки» Москва ACADEMIA 2004 г.
ГОСТ 12.1.030-81. Система стандартов безопасности труда. Электробезопасность. Защитное заземление зануление. – Москва: Госстандарт: Межгос. совет по стандартизации метрологии и сертификации 1982.
ГОСТ 12.2.009-99. Система стандартов безопасности труда. Станки металлообрабатывающие. Общие требования безопасности. – Минск: БелГИСС: Межгос. совет по стандартизации метрологии и сертификации 1999.
Титульный лист.doc
УЧРЕЖДЕНИЕ ОБРАЗОВАНИЯ
«БАРАНОВИЧСКИЙ ГОСУДАРСТВЕННЫЙ УНИВЕРСИТЕТ»
студент (факультет курс группа)
фамилия имя отчество
ученое звание ученая степень должность
(фамилия имя отчество)
содержание.docx
1Анализ конструкции современных металлорежущих станков . 6
2Назначение и принцип работы станка . ..7
3Технические характеристики станка . .7
4Основные узлы станка 8
5Органы управления станком 9
6Конструктивные особенности станка .9
Расчет базовых элементов станка 10
1Обоснование вида направляющих станка и выбора материала 10
2Обоснование конструкции основных базовых элементов выбор материала ..10
Кинематический анализ станка 11
1Описание кинематической схемы станка 11
1.1Движение резания 11
1.2Движение подачи 11
Указания по эксплуатации и обслуживанию станка 12
Требования техники безопасности и экологии при работе на станке.16
Обоснование экономической эффективности станка 20
Режущий инструмент 21
1Назначение режущего инструмента .21
2Технические требования предъявляемые к инструменту .21
3Элементы конструкции и геометрические параметры инструмента 22
4Расчет геометрических параметров инструмента 23
пункт 4 5!!!.docx
Долговечность работы станка в значительной мере зависит от условий его эксплуатации. Во избежание повреждений станков при транспортировке следует соблюдать правила упаковки перевозки и переноски станков.
Качество работы станка зависит от правильной его установки на фундаменте. Без фундамента разрешается установка станка только на бетонированном полу достаточной толщины (200—300 мм). В остальных случаях для достижения спокойной и точной работы необходимо подготовить бетонный фундамент. Установку станка на фундамент производят после полного затвердевания раствора цемента. В отверстия основания станины закладывают фундаментные болты с навинченными гайками и при установке станка на фундамент опускают болты в заранее подготовленные колодцы. Выверку правильности положения станка производят при помощи точных уровней которые устанавливают на обработанные горизонтальные или вертикальные плоскости станка (направляющие стола и т. п.). Для придания станку правильного положения применяют стальные клинья или регулируемые башмаки которые устанавливают по периметру станины на определенных расстояниях друг от друга. После выверки станка по уровню в продольном и поперечном направлениях производят заливку основания станка раствором цемента.
Каждый станок находящийся в цехе имеет паспорт выданный заводом-изготовителем и хранящийся в отделе главного механика завода. Паспорт станка является основным техническим документом содержащим полную характеристику станка.
В паспорте даны сведения характеризующие тип станка модель завод-изготовитель год выпуска заводской номер место установки дату пуска в эксплуатацию и т. п.; помещена фотография станка со спецификацией органов управления. В разделе «Основные данные станка» приведены сведения характеризующие габарит и массу станка основные размеры стол направляющие станины шпиндель хобот и серьгу принадлежности и приспособления для настройки и обслуживания станка прилагаемые к станку сведения о ремонте комплект поставки и др.
В разделе «Механика станка» приведены данные по механике главного движения (число оборотов шпинделя в минуту мощность на шпинделе) и по механике подачи (подачи стола в мммин — продольная поперечная и вертикальная ускоренные подачи стола). Кроме паспорта к каждому станку прилагают руководство по эксплуатации которое хранится у цехового механика или на рабочем месте. В руководстве кроме сведений имеющихся в паспорте приведены рекомендации по транспортировке и распаковке установке станка на фундамент подготовке станка к первоначальному пуску смазке станка охлаждению фрез при резании. В руководстве имеется также кинематическая схема станка со спецификацией зубчатых и червячных колес червяков и реек описание конструкции станка и его узлов рекомендации по настройке наладке и режимам работы регулированию и эксплуатации электрооборудования и др. В конце руководства прилагают чертежи быстроизнашивающихся деталей.
Регулирование станков
Регулирование зазора между ходовым винтом и гайкой. В процессе эксплуатации станков возникает необходимость в регулировании отдельных узлов и элементов с целью восстановления их нормальной работы. Между ходовым винтом и гайкой имеется небольшой зазор (люфт). Поэтому как указывалось ранее при точных перемещениях необходимо маховичок ручного перемещения стола вращать в одном направлении чтобы выбирать мертвый ход. Если некоторая доля оборота маховичка происходит без перемещения стола то это означает что между ходовым винтом и гайкой винт-гайка имеется зазор (мертвый ход). Если мертвый ход превышает % оборота рукоятки надо сообщить об этом мастеру. При наличии зазора в ходовом винте продольного перемещения стола нельзя производить строгание по подаче.
Для регулирования зазора между ходовым винтом и гайкой стола консольно-фрезерных станков № 2 и 3 серии «Р» необходимо ослабить контргайку 1 и вращая валик 2 произвести подтягивание гайки ходового винта. Выбор люфта необходимо производить до тех пор. пока люфт ходового винта проверяемый поворотом маховичка продольного хода окажется не более 3—5J и пока при перемещении стола вручную не произойдет заклинивание винта на каком-либо участке необходимом для рабочего хода.
После регулирования затягивают контргайку 1 фиксируя валик 2 в установленном положении.
Регулирование клиньев стола и салазок. Зазор в направляющих стола и салазок консольно-фрезерных станков № 2 и 3 серии «Р» выбирается клиньями. Регулирование клина 1 стола (132) производится при ослабленных гайках 2 и 4 подтягиванием винта 3 отверткой. После проверки регулирования ручным перемещением стола гайки надежно затягиваются. Зазор в направляющих салазок регулируется клином 6 при помощи винта 5. Степень регулирования проверяется при перемещении салазок вручную.
В процессе эксплуатации кроме указанных элементов регулируются:
зазор в переднем подшипнике:
пружины фиксатора лимба скоростей и лимба подач:
предохранительная муфта коробки подач и др.
Смазка станков. Основное назначение смазки сводится к уменьшению потерь на трение повышению износостойкости трущихся поверхностей и обеспечению допустимой температуры. От правильности смазки станка зависит срок службы станка и надежность его работы.
Для смазки этих станков рекомендуется масло «индустриальное 30».
Охлаждение в процессе фрезерования. Смазочно-охлаждающую жидкость (СОЖ) следует подавать непосредственно в зону резания. Подвод СОЖ в нужную зону обеспечивается маневренностью системы подвода сопла. Приведена схема подвода СОЖ к режущему инструменту для станков № 2 и 3 серии «Р». Если отвернуть гайку то сопло можно поворачивать под любым углом и устанавливать по высоте. Для перемещения сопла вдоль скосов хобота необходимо также ослабить гайку 3 со стороны противоположной соплу. При изменении направления фрезерования вся система может быть перенесена на другую сторону хобота. Регулятором подачи требуемого количества СОЖ является кран 2 расположенный сверху сопла. Этим краном разрешается пользоваться так же как краном-выключателем СОЖ. если время выключения не превышает 10 мин. На более продолжительное время отключение эмульсии необходимо производить выключением насоса с помощью переключателя на дверке электрониши.
Насос подачи СОЖ смонтирован за одно целое со своим электродвигателем и расположен в нише основания под кожухом электродвигателя главного движения. Наибольшая производительность насоса — 22 л мин. Включение -и выключение насоса охлаждения происходит при установке переключателя на дверке левого электрошкафа в положение «Охлаждение включено» или «Охлаждение выключено». Для периодической очистки основания и замены СОЖ в основании имеется пробка 4 а в фундаменте — приямок для слива СОЖ. В передней части основания имеется решетчатая крышка через которую СОЖ стекает с верхней поверхности во внутреннюю полость. Эта крышка задерживает стружку тряпки грязь и т. д. Снятие ее недопустимо так как приводит к порче насоса и загрязнению всей системы.
Систему охлаждения следует периодически (через 6 месяцев) демонтировать и промывать под давлением. При смазке станков других моделей нужно пользоваться рекомендуемыми схемами и режимами смазки аналогичными приведенным.
Ремонт станков. Система планово-предупредительного ремонта (ППР) предусматривает выполнение ряда мероприятий по уходу надзору и ремонту станков.
Основными мероприятиями в системе ППР являются межремонтное обслуживание и периодические плановые ремонты. Межремонтное обслуживание предусматривает ежедневный осмотр станков и устранение обнаруженных недостатков; периодический плановый осмотр в установленные сроки; периодическую плановую проверку станков на точность. Периодические плановые ремонты подразделяют на малый средний и капитальный.
На каждый станок должен быть заведен журнал в котором отмечают осмотры ремонты аварии переделки мероприятия по модернизации и т. п.
общие сведение о мрс.docx
1 Анализ конструкции современных металлорежущих станков
На данный момент современные поперечно-строгальные станки имеют гидравлический привод. Однако поперечно-строгальные станки из-за своих недостатков применяются редко. На их смену пришли многосторонние строгальные станки которые серьезна отличаются конструктивно применяемым режущим инструментом. Эти станки не имеют гидравлический привод. На них легко устанавливается система ЧПУ. Большое применение эти строгальные станки получили в деревообработке.
2Назначение и принцип работы станка
Станок предназначен для обработки сравнительно небольших по размерам деталей. Наибольшее применение он находит в инструментальных и ремонтных цехах а так же в основных цехах с индивидуальным и мелкосерийным характером производства. В серийном производстве используются при обработки деталей типа планок узких и протяженных поверхностей а так же при обработке пазов и канавок.
Как главное движение (возвратно-поступательное перемещение ползуна) так и горизонтальная и вертикальная подачи осуществляются здесь с помощью гидравлической системы.
Гидравлический привод состоит из сдвоенного лопастного насоса типа ЛЗФС производительностью 100 и 50 лмин. гидропанели панели управления обратного клапана золотника подачи золотника включения манометра дросселя подачи и двух цилиндров — главного движения (ползуна) и подачи.
Масло от сдвоенного лопастного насоса 1 (рис. 1) поступает к золотнику 4 переключения ступеней скоростей панели управления а затем через канал промежуточной плиты — в гидропанель. Золотник имеет четыре положения. При первых трех положениях масло поступает в гидропанель от одного или другого насоса либо же от обоих насосов одновременно а при четвертом положении золотник соединяет рабочую 9 и штоковую 10 полости цилиндра ползуна.
Рисунок 1-Гидравлическая схема станка модели 7М36
1Технические характеристики станка
Наименьшая и наибольшая длина хода ползуна (вылет) в мм 150-700
Наибольшее расстояние от опорной поверхности резца до станины в мм.840
Размер горизонтальной рабочей поверхности стола в мм;
Наибольшее горизонтальное поперечное перемещение стола в мм 700
Наибольшее вертикальное перемещение стола в мм .320
Наибольшее вертикальное перемещение резцовой головки в мм .200
Наибольшая эффективная мощность главного движения кВт 70
Наибольший крутящий момент на шпинделе кгссм 7100
Наибольшее усилие подачи кгс 2000
Масса станка кг 3200
2Основные узлы станка
На рис.3 показан общий вид гидрофицированиого поперечно-строгального станка модели 7М36: 1— стол; 2 —суппорт; 3 —механизм механической подачи суппорта; 4-станина; 5 — ползун; 6 — коробка подач; 7 — гидропривод; 8 — электрооборудование.
Рисунок 3- Общий вид гидрофицированиого поперечно-строгального
3Органы управления станком
Управление гидрофицированным поперечно-строгальным станком производится при помощи кнопочной станции и соответствующих рукояток.
Перед пуском станка нужно включить блок пакетного выключателя и тем самым подать к станку напряжение. Затем нажатием кнопки включают в работу насос (при наличии последнего) и лишь после этого включением кнопки «пуск» сообщают движение ползуну станка.
Установка длины строгания производится двумя передвижными упорами расположенными в Т-образном пазу планки закрепленной на правой боковой стороне ползуна станка. Расстояние между рисками на упорах определяет длину строгания. Отсчет величины строгания ведется по линейке установленной на Т-образной планке.
Для поворота суппорта на необходимый угол нужно отжать квадрат зажима его поворотной части а после поворота суппорта снова зажать его.
Перед началом подъема или опускания стола надо открепить гайки зажима стойки стола и поперечины а после окончания подъема или опускания— зажать их. Механическая подача суппорта и вертикальная или горизонтальная подача стола производятся установкой маховичка в положение указанное в табличках прикрепленных на станке.
4Виды движений в станке
Возвратно-поступательное движение ползуна управление цилиндром подачи стола (автоматическая горизонтальная подача) переключение с горизонтальной подачи стола на вертикальную осуществляется рукояткой
ручная вертикальная подача может быть получена и путем вращения винта.
5Конструктивные особенности станка
Узлы гидрофицированного станка конструктивно отличаются от узлов поперечно-строгального станка с кривошипно-кулисным механизмом. Внутренняя часть станины поперечно-строгального станка модели 7М36 является емкостью для масла; в верхней части станины смонтирован гидроцилиндр перемещения ползуна. Гидропанель закреплена на правой боковой стенке станины. В нижней части станины располагаются гидронасосы. В коробке подач смонтированной на правой боковой поверхности стола размещаются гидроцилиндр горизонтальной и вертикальной подач и электродвигатель ускоренных перемещений. В ползуне закреплен шток гидроцилиндра главного рабочего движения.
3кинематика.docx
1 Описание кинематической схемы станка.
1.1 Главное движение. Возвратно-поступательное движение ползуна осуществляется гидропанелью при помощи реверсивного золотника 18. Он подает масло поочередно в рабочую и штоковую полости цилиндра ползуна при этом поршень перемещается и производятся рабочий и холостой (обратный) ходы ползуна. Управляет переключением реверсивного золотника гидропанели золотник управления 23 приводимый в действие упорами закрепленными на ползуне. Бесступенчатое регулирование скорости рабочего хода ползуна в пределах каждой ступени производится дросселем 14 с регулятором 13 подключенным параллельно с рабочей полостью цилиндра ползуна. Регулирование скорости рабочего хода осуществляется за счет частичного слива в бак масла подаваемого насосами.
1.2 Движение подачи. При переключении ползуна на рабочий ход масло от насоса через золотник 4 переключения ступеней скоростей и золотник подачи 29 поступает в цилиндр подачи 30. и толкает его поршень вверх. Шток поршня соединен с рейкой. Перемещая ее вверх он вращает сцепленное с ней зубчатое колесо 7 от которого через зубчатую муфту с колесом 6 колеса 5 7 8 и 10 движение передается на винт 11 и далее через гайку 12 скрепленную со столом. При этом происходит поперечная подача стола. Вертикальная подача стола осуществляется через зубчатые колеса 5 и 7 8 и 9 червячную пару 13 и 14 на винт 15. Переключение с горизонтальной подачи стола на вертикальную осуществляется рукояткой которая переводит подвижное зубчатое колесо 8 в зацепление с колесом 10; при зацеплении колеса 8 с колесом 10 производится горизонтальная подача.
Кинематика1.cdw

Режущий инструмент.cdw

Державка резца изготовлена из стали 45 по ГОСТ 1050
Твердость рабочей части 63 66 НРС
Припой из марки ПЖ60НХБ
Технические требования по ГОСТ 10047-62
Общий вид станка.cdw

Наибольшее расстояние от опорной поверхности резца до
Рамер горизонтальной рабочей поверхности стола
Наибольшее горизонтальное поперечное перемещение стола
Наибольшая эффективная мошность электродвигателя
Рекомендуемые чертежи
- 25.01.2023
- 24.01.2023