Главный привод токарного станка с ЧПУ


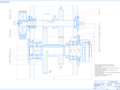
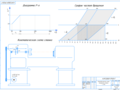
- Добавлен: 25.01.2023
- Размер: 342 KB
- Закачек: 0
Описание
Состав проекта
![]() |
![]() |
![]() ![]() ![]() |
![]() ![]() ![]() |
![]() ![]() ![]() ![]() |
![]() ![]() ![]() ![]() |
Дополнительная информация
Спецификация.doc
Уплотнение лабиринтное
Коробка скоростей токарного станка
Прокладка регулировочная
Жарков.doc
Российской Федерации
Федеральное агентство по образованию
«ИВАНОВСКИЙ ГОСУДАРСТВЕННЫЙ
ЭНЕРГЕТИЧЕСКИЙ УНИВЕРСИТЕТ
Электромеханический факультет
Кафедра технологии автоматизированного машиностроения
Металлорежущие станки
«Главный привод токарного станка с ЧПУ»
Выбор станка аналога
Выбор электродвигателя
Определение числа зубьев колес передач
Выбор материала и термообработки зубчатых колес
Расчет на прочность элементов привода
1 Определение КПД привода и мощности на каждом валу
2 Определение крутящих моментов на валах
3 Определение параметров зубчатых колес
3.2 Определение геометрических параметров зубчатых колес
3.3 Определение межосевого расстояния
4 Расчет клиноременной передачи
5 Расчет действительных частот вращения шпинделя
6.1 Предварительный расчет валов
6.2 Уточненный расчет ведущего вала
6.3 Проверка шлицевых соединений
7 Выбор подшипников качения
Описание разработанной конструкции
Список используемой литературы
Высокие темпы роста выпуска продукции машиностроительной и других отраслей производства требуют разработки и внедрения новейшего высокопроизводительного оборудования различных типов станков-автоматов и автоматических линий.
При реализации поставленных задач важное место занимает проблема улучшения использования действующего металлорежущего оборудования за счет его усовершенствования (повышения скоростей обработки повышение точности и надежности работы увеличение мощности привода применение средств автоматизации и управления рабочим процессом использование приспособлений и устройств расширяющий технологические возможности станков).
Создание металлорежущих станков должно предусматривать их наибольший экономический эффект и высокие тактико-технические и эксплуатационные показатели.
Основные требования предъявляемые к создаваемому станку: высокая производительность надежность технологичность ремонтопригодность минимальные габариты и масса удобство эксплуатации экономичность техническая эстетика. Все эти требования учитываются в процессе проектирования и конструирования.
Выбор электродвигателя
nma nm Pдв = 7(кВт).
Выбирается регулируемый электродвигатель в зависимости от требуемой мощности.
Требованиям удовлетворяет асинхронный электродвигатель с частотным регулированием мод. 2AD100D с параметрами P = 75(кВт) nном = 1500 (обмин)
nmax = 7500 (обмин).
Определяется диапазон регулирования частот вращения привода:
Определяется диапазон регулирования частот вращения двигателя при
постоянной мощности:
Рисунок 1. Диаграмма P-n
Рисунок 2. График частот вращения
Рисунок 3. Кинематика привода.
Разрабатывается график частот вращения.
Для ориентирования используем стандартный ряд частот вращения (φ=125) а каркас графика должен охватывать частоты вращения от nmin = 50 до максимальной частоты вращения в приводе nэmax = 3000.
Определение числа зубьев колес передач
Метод наименьшего общего кратного.
Рисунок 4. Группа передач
Так как межосевое расстояние для всех зубчатых колес группы является величиной постоянной (рисунок 6) и равно
то при одинаковом модуле зубчатых колес должно быть справедливо соотношение
гдеaw – межосевое расстояние групповых передач;
– угол наклона зубьев (=0o);
Sz – сумма чисел зубьев сопряженных колес;
Z и Z – числа зубьев ведущего и ведомого колес.
Передаточное отношение
Наименьшее общее кратное
Для передаточного отношения определим Em
тогда сумма зубьев будет
Выбор материала и термообработки зубчатых колес
Таблица 1. Допускаемые контактные напряжения (Rк) и напряжения на изгиб (Rв)
Материал зубьев шестерни
Допускаемые напряжения
Механические свойства
Расчет на прочность элементов привода
1 Определение КПД привода и мощности на каждом валу
где N – мощность на рассчитываемом валу (кВт);
Nдв. – мощность электродвигателя (кВт);
– КПД кинематической цепи от электродвигателя до вала.
2 Определение крутящих моментов на валах
Определение крутящих моментов действующих на валах производится по формуле
гдеMкр. – крутящий момент (Н*м);
nр – минимальная частота вращения рассчитываемого вала при котором может быть полностью использована мощность электродвигателя.
3 Определение параметров зубчатых колес
Для стальных прямозубых колес модуль определяется:
по напряжениям изгиба
по контактным напряжениям
Из двух значений модуля выбирают большее и округляют до ближайшего большего стандартного значения.
Обозначения и размерности величин в формулах:
знак “+” – соответствует наружному зацеплению;
знак “-” – соответствует внутреннему зацеплению;
N – мощность передаваемая рассчитываемой шестерни определяется с учетом КПД передачи от электродвигателя до рассчитываемой шестерни кВт;
U – передаточное число пары колес в которой работает рассчитываемая шестерня понимаемое всегда как отношение числа зубьев колеса к числу зубьев шестерни (всегда больше или равно единице);
z – число зубьев рассчитываемой шестерни;
– отношение ширины зуба к модулю;
Rb – допускаемое напряжение изгиба (МПа)
Rк – допускаемое контактное напряжение (МПа);
y – коэффициент формы зуба.
z=20; n=250 (обмин); U=5; N=7125 (кВт)
Предварительно принимаем и =1
z=60; n=250 (обмин); U=1; N=7125 (кВт)
Аналогично принимаем b=30 мм.
Диаметры делительных окружностей
Диаметры окружностей вершин
Диаметры окружностей впадин
3.3 Определение межосевого расстояния
4 Расчет клиноременной передачи
Выбираем сечение ремня УО
b0=10 мм; bp=85 мм; h=8 мм; S=56 мм2; L=6303550 мм
Межосевое расстояние
Определяется длина ремня:
Окончательно межосевое расстояние:
Угол обхвата на малом шкиве:
Коэффициент обхвата на малом шкиве
Начальное напряжение ремней
Усилие действующее на вал
Угол отклонения от линии центров шкивов
Фактическое значение передаточного отношения
5 Расчет действительных частот вращения шпинделя
Рисунок 5. Эпюры изгибающих моментов
Изгибающий момент в сечении:
Окончательный расчет вала на прочность
6.3 Проверка шлицевых соединений
Расчет запаса статической прочности и выносливости проводится по следующим
Момент сопротивления при изгибе для вала со шлицами:
Момент сопротивления при кручении для вала со шлицами:
Определяем коэффициенты запаса
– допускаемый запас выносливости вала.
S [S] следовательно выносливость вала обеспечена.
7 Выбор подшипников качения
Методика расчета подшипников качения основана на ISO и заключается в учете динамической грузоподъемности должно соблюдаться неравенство:
где Стр – требуемая величина динамической нагрузки кН
С – табличное значение динамической нагрузки кН
Величина Стр определяется
n – частота вращающегося кольца подшипника
Lh – долговечность подшипника – 5000ч
где Кд – коэффициент динамичности
Кк – коэффициент учитывающий какое кольцо вращается Кк=1
Q – приведенная нагрузка определяется по радиальной R и осевой А
Подшипники выбираются шариковые радиально-упорные однорядные 2шт по ГОСТ 8338 – 75 исполнение 206.
Описание разработанной конструкции
Коробка передач токарного станка с ЧПУ предназначена для обеспечения главного движения т. е. передачи крутящего момента от двигателя постоянного тока на шпиндель станка и изменения частоты вращения шпинделя.
На ведущем валу установлена муфта посредством которой производится переключение диапазонов частот вращения коробки скоростей.
Асинхронный электродвигатель с частотным регулированием мод. 2AD100D мощностью 75 (кВт) передает вращение через клиноременную передачу на ведущий вал далее через цилиндрические передачи 20100 или 6060 на шпиндель.
Комбинация двигателя с бесступенчатым регулированием и двухступенчатой коробкой скоростей обеспечивает 2 диапазона регулирования от 50 до 3000 (обмин). Коробка скоростей встроена в корпус станка. Для смазки зубчатых колес используют картерный способ. Подвод масла к электромагнитным муфтам осуществляется внутренним или внешним способом. Шпиндель изготовлен полым.
Подшипники шпинделя регулируются с помощью гаек.
В качестве смазки подшипников применяется смазка ЦИАТИМ-201 ГОСТ 6261-69.
В ходе выполнения курсового проекта был проведен анализ назначения и условий работы проектируемого станка наиболее рациональные конструктивные решения с учетом технологических монтажных эксплуатационных и экономических требований; кинематические расчеты; определение сил действующих на детали и узлы; расчеты конструкции на прочность; выбор материалов.
Список используемой литературы
Кочергин А. И. Конструирование и расчет металлорежущих станков и станочных комплексов А. И. Кочергин. – Минск: Высш. шк. 1991.
Колесов М. И. Основы технологии машиностроения: учебник для машиностроительных вузов М. И. Колесов. – М.: Машиностроение1988.
Курсовое проектирование деталей машин: Учебное пособие С. А. Чернавский К. Н. Боков [и др.]. – М.:ООО ТИД «Альянс» 2005.– 416 с.
Шейнблит А. Е. Курсовое проектирование деталей машин: Учеб.пособие.Изд-е 2-е перераб. и дополн. – Калининград: Янтар. Сказ 2002. – 454 с.:ил. черт. – Б.ц.
Жарков 1-й лист.cdw

Допуск радиального биения шпинделя на длине 300 мм
Коническую шейку шпинделя проверить по краске на прилегание.
Пятно контакта не менее 85%.
Радиальный зазор в подшипниках поз. 10
обеспечить гайкой поз. 21.
После сборки обкатать в течение 30 минут при частоте вращения
двигателя 3000 обмин.
Температура в зоне подшипников не выше 50
Уровень шума не более 70 дБ.
Жарков 2-ой лист.cdw

График частот вращения
Кинематическая схема станка