Дипломный проект-Модернизация системы автоматического управления прошивным станом ТПА-140




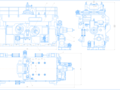
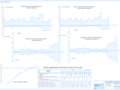

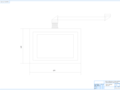
- Добавлен: 24.01.2023
- Размер: 1 MB
- Закачек: 0
Описание
Состав проекта
![]() |
![]() |
![]() ![]() ![]() ![]() |
![]() ![]() ![]() ![]() |
![]() ![]() ![]() ![]() |
![]() ![]() ![]() ![]() |
![]() ![]() ![]() |
![]() |
![]() |
![]() |
![]() ![]() ![]() ![]() |
Дополнительная информация
Блок схема Алгоритма1.cdw

линией прошивного стана ТПА-140
Программа управления
Блок схема алгорритма
Булычев гр. ТЗк-6134с
циклограммаV7.cdw

Программа управления.
Проект модернизации системы управления
линией прошивного стана ТПА-140
экономика прошивнV7.cdw

Функционально-стоимостная диаграмма
(проектируемого варианта)
Эффекты от проектного решения :
Дисконтированный чистый денежный поток средств NCF
Технико-экономические
Проект модернизации системы управления
линией прошивного стана ТПА-140
Булычев гр. ТЗк-6134с
Гафик окупаемости проекта
Таблица формирования денежного потока (в тыс. руб.)
Итого : денежные средства (Cash Flow) от реализации проекта (1-2)
Ликвидационная стоимость активов
Итого : денежные средства (Cash Flow) от инвестиционной деятельности (5-4)
Чистый денежный поток средств (Net Cash Flow) (3+6)
Дисконтированный чистый денежный поток нарастающим итогом
общий вид панели оператораV7.cdw

Проект модернизации системы управления
линией прошивного стана ТПА-140
ПЗ .doc
Итогом работы создан проект системы автоматического управления на безе контроллера S-400 фирмы SIEMENS.
Проект является реальным и реализуемым на производстве.
Обоснование модернизации системы управления линией прошивного агрегата
1 Состав устройства и принцип работы существующей системы управления линией прошивного агрегата
2 Обоснование модернизации системы управления
3 Разработка технического задания на проект
ПРОЕКТИРОВАНИЕКОНСТРУИРОВАНИЕ И МОДЕЛИРОВАНИЕ ТЕХНИЧЕСКИХ СРЕДСТВ
1 Разработка структурной схемы СУ
2 Выбор основных технических средств СУ
3 Разработка и расчет электрической схемы управления линией прошивного агрегата
4 Разработка панели оператора
ПРОГРАММНОЕ ОБЕСПЕЧЕНИЕ СИСТЕМЫ УПРАВЛЕНИЯ
1 Разработка структуры программного обеспечения
2 Разработка алгоритма работы линии
3 Разработка программы управления работой линии
ЭКСПЛУАТАЦИОНАЯ ДОКУМЕНТАЦИЯ
1 Инструкция оператору
ФУНКЦИОНАЛЬНО-СТОИМОСТНОЙ И ЭКОНОМИЧЕСКИЙ АНАЛИЗ ПРОЕКТИРУЕМОЙ СУ
1 Расчет стоимости оборудования и затрат связанных с модернизацией
2 Расчет себестоимости выпускаемой продукции после модернизации
3 Расчет окупаемости и экономическая оценка проекта
БЕЗОПАСНОСТЬ И ЭКОЛОГИЧНОСТЬ ПРОЕКТА
1 Обеспечение безопасности работающих
2 Экологическая безопасность и охрана окружающей среды
Список использованных источников
Данной работой предлагается проект модернизации системы автоматического управления прошивным станом ТПА-140. Проектирование новой системы будет придерживаться главных принципов построения современных систем - модульность и открытость.
В первой части проекта будет изучена действующая в цехе система автоматического управления. Будет описана ее структура и работа составных ее частей.
Вторая часть проекта будет посвящена выбору и обоснованию комплекса технических средств с помощью которых будет реализована будущая система.
В третьей части будет описана разработка программной части системы управления.
Технико-экономическое обоснование будет приведено в четвертой части.
Тема безопасности и экологичности будет раскрыта в последней части проекта.
ОБОСНОВАНИЕ МОДЕРНИЗАЦИИ СИСТЕМЫ УПРАВЛЕНИЯ ЛИНИЕЙ ПРОШИВНОГО АГРЕГАТА.
1 Состав устройство и принцип работы существующей системы управления линией прошивного агрегата.
Трубопрокатные агрегаты с прошивным станом к числу наиболее распространенных для производства бесшовных горячекатаных труб. На таких агрегатах производят свыше 30 % всех горячекатаных труб. Широкое распространение станы подобного типа или различные их модификации получили и в зарубежной практике (США Западная Европа Япония и др.) благодаря ряду технологических достоинств:
высокой маневренности позволяющей в короткий промежуток времени осуществить переход с одного типоразмера прокатываемых труб на другой;
универсальности обеспечивающей производство труб широкого сортамента из разнообразных марок сталей и сплавов (по сравнению с другими способами производства на указанных агрегатах можно прокатывать трубы в наиболее широком диапазоне варьирования отношения диаметра трубы к толщине стенки D 0 S 0 изменяющегося от 4 5 до 40 45);
относительно высокой производительности при удовлетворительном качестве труб (годовой объем производства в зависимости от типа агрегата составляет 150—400 тыс. т а расходный коэффициент металла 106— 115 в зависимости от марочного состава сталей);
высокой степени механизации и автоматизации производственного процесса.
В настоящее время отечественной промышленностью освоено производство труб на ТПА из углеродистых средне- и высоколегированных марок сталей и сплавов в том числе и из коррозионностойких и жаропрочных. В большом объеме производят трубы так называемого нефтяного сортамента (бурильные обсадные насосно-компрессорные) крекинговые заготовки для цехов холодного деформирования и многие другие.
В соответствии с сортаментом выпускаемых труб агрегат ТПА-140 к малым агрегатам для прокатки труб диаметром 40—159 с толщиной стенки 35—30 мм (минимальный диаметр труб определяется технологическими возможностями редукционного стана);
Агрегат имеет в своем составе редукционный и калибровочный стан поэтому оснащен подогревательной индукционной печью.
В состав трубопрокатных агрегатов с автоматическим станом входят:
нагревательная кольцевая печь ;
два стана продольной прокатки;
два обкатных стана ;
подогревательная индукционная печь ;
калибровочный стан ;
Основные технические характеристики агрегата приведены в таблице 1.1
Типоразмер агрегата
Диаметр рабочих валков (максимальный) мм
Частота вращения валков мин -1
Максимальная окружная скорость валков мс
Мощность главного привода кВт
Продольной прокатки
1.1 Назначение и технические характеристики
Настоящая часть предназначена для ознакомления с работой и изучением аппаратуры автоматики системы БАС-54 участка прошивного стана для ее дальнейшей замены. Здесь приведены сведенья о назначении и составе системы о взаимодействии составных частей и описание их работы.
Полное наименование и обозначение системы – Бесконтактная автоматическая система управления технологическим процессом участка прошивного стана трубопрокатного агрегата ТПА-140 цеха Т-2.Сокращенное наименование БАС-54.
БАС-54 предназначена для автоматического управления механизмами прошивного стана. Перечень автоматизируемых механизмов приведен в таблице 1.2.
Система БАС-54 состоит из следующих составных частей (устройств):
В существующей системе используются следующие датчики дающие информацию о положении заготовок гильз механизмов:
Д43-Д52 – фотоэлектрические датчики (фотореле) положения нагретых заготовок и гильз;
И116И121..И152 – индуктивные датчики положения механизмов;
ДН – трансформаторный датчик наличия нагрузки на главный привод;
РД – датчик давления.
1.3.2 Станция управления 4ША (шкаф автоматики).
1.3.3 Пульт управления 5ПА.
1.3.4 Исполнительные механизмы.
Взаимосвязь основных составных частей показана на рисунке 1.1.
Перечень автоматизируемых механизмов и исполнительных устройств
Исполнительные механизмы
Отводящий рольганг пр.115
реле промежуточное U=24в I=1А
Зацентровщик пр.116117118
пневмовентиль U=24в I=1А
Выбрасыватель пр.121
Крышка желоба (перекрыватель) пр.123
Вталкиватель пр.124
Исчезающий упор пр.125
Охлаждение оправки пр.137
Центрователь №1-4 пр.138-141
Выдающие ролики (вращение) ТСУ пр.143
Выдающие ролики (сведение)
Перехват стержня пр.136
Ролики отвода стержня (сведение) пр.149150
Головка упорного механизма пр.151
Замок упорного механизма пр.152
Рисунок 1.1. Взаимосвязь составных частей БАС-54
1.4 Устройство и работа системы
Система БАС-54 использует сигналы датчиков. Чувствительные элементы датчиков устанавливаются на стане а их сигналы преобразуются в стандартные электрические сигналы блоком преобразователей датчиков (БПД). Сигналы дающие информацию о положении заготовок металла гильзы и механизмов поступают в блоки логики которые в соответствии с определенным алгоритмом служат для получения сигналов управления тем или иным механизмом. Блоки логики установленные в станции управления 4ША вырабатывают выходные командные сигналы которые подаются на соответствующие усилители мощности. Используются два типа усилителей мощности: транзисторные (=24В) и тиристорные усилители (=220В). Они так же установлены в шкафу. Выходы через соответствующие избиратели режимов управления воздействуют на исполнительные механизмы стана. Избиратели ( ключи управления ) установлены на пульте управления 5ПА.
1.5 Устройство и работа составных частей
Система использует несколько типов датчиков. Датчики индицируют положение нагретых заготовок и гильз контролируют положение и состояние исполнительных механизмов стана и определяют наличие напряжения на тех или иных аппаратах связанных со станом.
1.5.1.1 Фотодатчики типа ФГ-13 (Уралчерметавтоматика). Индицирует наличие в своей зоне видимости нагретого тела. Чувствительный элемент датчика фотодиод инфракрасного спектра использует излучение нагретого металла (более 650Со). Системой используется релейный выход данного датчика.
1.5.1.2 Индуктивные датчики типа ИМТ-5. Устанавливаются на тане и индицирует появление металлического шунта над рабочей поверхностью датчика с зазором до 20 мм. Шунт механически связан с механизмом и при перемещениях перекрывает датчик. Системой используется релейный выход данного датчика.
1.5.1.3 Датчик нагрузки. Трансформаторный датчик на выход которого появляется напряжение при наличии тока в цепи главного привода. И дает информацию находиться или нет главный привод в режиме прошивки.
1.5.1.4 Реле давления. Установлено в камере зацентровщика и индицирует наличие повышенного давления в камере что говорит об исходном положении зацентровщика.
1.5.2 Станция управления 4ША (шкаф автоматики)
1.5.2.2 Общие сведения
Станция управления (СУ 4 ША) типа БАС-54 была разработана в соответствии с утвержденным Главэнерго Минчермета СССР ЭЗТМ СКБ «Уралчерметавтоматика» и согласованным с СО ГПИ ТПЭП «Техзаданием на разработку средств и систем автоматизации трубопрокатного агрегата 140» от 25 апреля 1972 г.
СУ 4 ША представляет собой шкаф двухстороннего обслуживания конструкции Калининского завода электроаппаратуры Минэлектропрома. Габаритные размеры шкафа 2000х700х600. В шкафу установлены шесть секций (кассет) являющихся по существу этажами шкафа. В верхних секциях установлены источники питания. В средних секциях установлены блок преобразователей датчиков и блок предохранителей для исполнительных устройств. В нижних секциях установлены блоки логики предназначенные для обработки поступающих на них сигналов преобразователей (датчиков) в соответствии с заложенными в них алгоритмами и для выдачи командных сигналов на управление соответствующими автоматизируемыми механизмами.
Кассеты и шасси блоков выполнены на основе конструктивов единой унифицированной блочной конструкции комплектных устройств автоматики (ЕУБК) разработанных ВНИИЭлектроприводом.
Для внешних подсоединений станции на кассетах установлены по три клеммника каждый из которых имеет 24 изолированных контактных зажима для провода сечением 15 мм2. Электрические соединения выполнены проводом марки МГВ сечением от 035 до 15 мм2. Электрические соединения в блоках выполнены гибким монтажным проводом МГШВ сечением 02 15 мм2. Для цепей питания использован провод сечением 05 и 07515 мм2. Между элементами цепи питания электрические соединения выполнены шинами.
1.5.2.2 Источники питания БПС-1 и БПВ-4
Источники питания обеспечивают станцию следующими напряжениями:
а) стабилизированное напряжение +6В 08А.
б) стабилизированное напряжение -12В 8А.
в) нестабилизированное напряжение -24В 16А.
1.5.2.3 Блоки логики
В блоках на шасси Ш2 может быть установлено до 30 элементов «Логика-Т» наименьшего габарита. В блоках Ш3 и Ш4 может быть установлено до 60 элементов «Логика-Т». Кроме логических элементов в блоках могут устанавливаться резисторы диоды конденсаторы и другие элементы размещаемые на унифицированных монтажных платах. Ручки потенциометров выведены на лицевую панель для возможности изменения оператором временных настроек. Так же на лицевой панели любого блока установлены индицирующие лампы показывающие состояние выходов блока.
На ручке блока установлена табличка с указанием типа (шифра) блока.
Для включения блока в схему станции на задней скобе шасси устанавливается до двух ножевых колодок каждая из которых имеет 30 контактов.
Конструкция блока предусматривает проводной электрический монтаж.
Работа алгоритма преобразования сигналов блоком обеспечивается сбором соответствующих элементов (элементы транзисторные бесконтактные серии «Логика-Т»).
Каждый из блоков логики отвечает за работу определенной группы механизмов и уникален. В случае отказа блок заменяется резервным.
1.5.2.4 Блоки предохранителей.
Блок предохранителей для исполнительных устройств служит для защиты транзисторных усилителей мощности от возможного короткого замыкания. У гнезд предохранителей имеются соответствующие шильдики с наименованием усилителя и включаемого механизма.
1.5.5.4 Блок преобразователей датчиков
Блок преобразователей датчиков необходим для преобразования приходящих сигналов с различных датчиков в стандартные электрические сигналы пригодные для обработки системой. Так же служит для гальванического развязывания электрических цепей датчиков от цепей системы.
1.5.5.5 Усилители мощности УТ-1М
Усилитель мощности тиристорный предназначен для усиливания сигнала полученного с блока логики (=24В) до оперативного напряжения (=220В) необходимого для релейно-контакторной схемы управления приводами.
1.5.3 Пульт управления 5ПА
В системе БАС-54 предусмотрена возможность ручного и автоматического режимов работы механизмов стана. Выбор режимов осуществляется с ключей управления. С этих же ключей производиться и ручное управление механизмами.
В случае управления в ручном режиме питающее напряжение подается непосредственно через шайбы ключей и через предохранитель на обмотки исполняющих устройств а шайба автоматики разомкнута.
При работе в автоматическом режиме замкнута лишь одна шайба автоматики. Через нее управляющий сигнал с усилителей мощности непосредственно управляет механизмом по заданному алгоритму.
2. Обоснование модернизации системы управления
Целями создания системы являются:
- повышение уровня эксплуатационной надежности (сокращение простоев) посредством замены физически и морально устаревшего электрооборудования системы автоматического управления станом продольной прокатки;
- повышение уровня оперативного управления станом за счет обеспечения оператора и технолога стана оперативной информацией о состоянии технологического процесса;
- уменьшение зависимости результатов работы стана от квалификации операторов;
- упрощение обслуживания электрооборудования при помощи постоянной диагностики и контроля состояния оборудования с выдачей удобных для восприятия цифробуквенных сообщений о его текущем состоянии;
- сокращение времени поиска и устранения неисправностей приводов и систем управления станом за счет обеспечения электриков оперативной информацией о состоянии электроприводов и электрооборудования стана;
- повышение культуры управления производством улучшение условий труда и информированности оперативного и производственного персонала;
- создание условий для последующего развития системы (управление цифровыми приводами измерение диаметра толщины стенки температуры длины гильзы);
повышение комфортности работы оператора-технолога быстрая перенастройка системы при смене сортамента.
3. Разработка технического задания на проект
3.1. Наименование и область применения
Настоящее техническое задание распространяется на проект модернизации системы управления прошивным станом трубопрокатного агрегата ТПА-140.
3.2. Основания для разработки
Проект разрабатывается на основании задания на выполнение дипломного проекта и учебного плана по специальности 210200 “Автоматизация технологических процессов и производств (в машиностроении)”.
3.3. Цель и назначение разработки
Объектом проектирования является системы управления прошивным станом трубопрокатного агрегата ТПА-140.
3.4. Источники разработки
-Технологический процесс.
-Действующие схемы существующей системы автоматического управления.
-Техническое описание АСУТП ТПА 140 "Уралчерметавтоматика".
3.5. Технические требования
Вся система САУ-ПС должна являться стандартным программируемым средством автоматизации и предназначена для круглосуточной работы в условиях трубопрокатного производства.
Технические требования к электрооборудованию. Система САУ-ПС должна быть двухуровневой многофункциональной информационно-управляющей системой реального времени реализованной с использованием оборудования и программного обеспечения фирмы Siemens принятого как стандартное средство автоматического управления в цехе Т-2.
Система должна быть открытой допускающей возможность функционального расширения с учетом перспектив развития и адаптации к изменяющимся технологическим условиям.
Система должна включать в свой состав все имеющиеся функции действующей САУ и дополнительные функции - ведения и использования библиотеки программ прокатки обкатного стана; контроля технологических параметров; контроля положения трубы в стане; отображения технологического процесса функции мониторинга отдельных параметров технологического процесса и действий оператора функции генерации сообщений (аварийных предупреждающих и действий оператора) и другое.
3.6. Условия эксплуатации
температура окружающего воздуха в диапазоне (от -12 до 45)
относительная влажность от 10 до 80 %
атмосферное давление от 84 до 107 кПа
запыленность не более 5 мгм3
наличие помех от магнитных полей не должны превышать значения 250 мВбм2
напряжение питания трехфазным переменным током должно быть в пределах:
частота питающей сети должна быть 50±2 Гц
3.7. Режимы работы объекта
Входными параметрами системы управления являются дискретные сигналы с пульта управления сигналы с датчиков. Выходными параметрами являются сигналы управления приводами механизмов станка пускатели а также индикация на пульте оператора.
автоматический режим – работа стана в автоматическом режиме в соответствии с параметрами установленными на панели оператора;
ручной режим – управление станом осуществляется вручную при помощи кнопок и переключателей
3.8. Стадии и этапы разработки
Получение задания на создание системы управления.
Сбор документации и анализ существующей системы управления.
Разработка структуры системы управления.
Выбор технических средств системы управления.
Разработка схемы подключения устройства управления.
Разработка программного обеспечения.
Оформление расчетно-пояснительной записки.
Оформление графической части дипломного проекта.
ПРОЕКТИРОВАНИЕ КОНСТРУИРОВАНИЕ И МОДЕЛИРОВАНИЕ ТЕХНИЧЕСКИХ СРЕДСТВ
1 Разработка структурной схемы системы управления.
Структурная схема системы управления прошивным станом приведена в графической части проекта.
В соответствии с требованиями технического задания разрабатываем систему на основе современного средства автоматизации – контроллера.
S7-400 имеет следующие особенности:
б) Широкий спектр модулей;
в) CPU в различных классах мощности;
г) Встроенная шина на обратной стороне модулей;
д) Через многоточечный интерфейс (MPI) PROFIBUS и промышленную сеть можно объединить в сеть и многое другое.
Информация о положении заготовки гильзы в стане о положении механизмов будет собираться датчиками. С датчиков дискретные сигналы будут поступать на входные модули контроллера находящегося в 4ША. Контроллер посредством дискретных сигналов через выходные модули согласно заданному в программе алгоритму будит воздействовать на технологический процесс с помощью промежуточных реле которые в свою очередь будут включать и отключать соответствующий пневмо- или электропривода.
В системе будет предусмотрена возможность ручного и автоматического режимов работы механизмов стана. Выбор режимов осуществляется с ключей управления пульта автоматики 5ПА. С этих же ключей производиться и ручное управление механизмами. Дискретные сигналы предлагается передавать в систему с помощью полевой шины ProfibusDP посредством установленного в пульту модуля децентрализованной периферии ЕТ200.
Для ввода значений технологических параметров будет служить панель оператора. С контроллером данная панель будет так же связана с помощью полевой шины ProfibusDP.
2 Выбор основных технических средств системы управления
Контроллер SIMATIC S7-400 применяется во всём мире в различных областях и используется для разнообразных целей. Он построен по модульному принципу причём различные функции автоматизации реализованы в нём с помощью различных модулей. Таким образом можно собрать S7-400 полностью приспособленным к заданным потребностям. Система предлагает богатую палитру устройств программирования диагностики и визуализации. Язык программирования STEP-7 и обширный набор программного обеспечения облегчает работы по программированию.
Программируемый контроллер S7-400 может использоваться для всевозможных промышленных целей. Несмотря на многообразие задач автоматизации S7-400 будет являться оптимальным решением для любой из них будь то простейшее управление или задача комплексного регулирования.
Сердцем любой системы базирующейся на контроллерах является процессор. Поэтому к его выбору должно уделяться большое внимание.
Из линейки процессоров S-400 выбираем CPU 416-2DP. Это центральный процессор с большим объемом памяти программ способный обслуживать разветвленные конфигурации ввода-вывода.
Большая его мощность необходима для возможности расширения функций системы в будущем. К примеру управление вспомогательными приводами или управление главным приводом. Кроме того данный процессор планируется в качестве дополнительной функции «нагрузить» еще и учетом количества и длинны гильз и заготовок.
Рисунок 2.1 Процессор CPU 416 2DP
Технические характеристики: CPU 416 2DP характеризуется следующими показателями:
Память пользователя объемом 16 Мбайт; Расширенный объем памяти загружаемой памяти скоростной памяти для выполнения секций программы. Гибкое расширение; подключение до 32 модулей (4-рядная конфигурация). Встроенный MPI интерфейс позволяет устанавливать одновременно до 4 статических и до 8 динамических связей с S7-300400 или до 4 статических связей с программаторами компьютерами и панелями оператора. Из всех статических соединений одно резервируется для связи с программатором и одно для связи с панелью оператора.
Переключатель режимов работы; переключение режимов может производиться только специальным ключом. Удаление ключа ограничивает доступ к содержимому памяти контроллера.
Парольная защита. Она обеспечивает авторизованный доступ к программе
Диагностический буфер. Он хранит 1024 последних сообщений об отказах и прерываниях которые могут быть использованы для диагностических целей
Необслуживаемое сохранение данных. Центральный процессор способен сохранять данные без использования буферной батареи (NVRAM)
Резервирование программы с помощью карты памяти. Объем карты памяти (FEPROM) может достигать 15 Мбайт
Часы реального времени. Диагностические сообщения центрального процессора могут сопровождаться выдачей даты и времени их формирования.
Встроенные коммуникационные функции;
Стандартные функции S7 связи MPIPROFIBUS
S7 функции связи (только сервер)
2.4 Источники питания
Из трех возможных источников серии PS 407 выбираем самый «слабый» - 4А. Этого тока будет достаточно для питания процессора.
Для питания модулей и снабжением всей системы постоянным напряжением 24В выберем мощный хорошо зарекомендовавший себя источник серии SITOP на 40 А.
Рисунок 2.2 Источник питания PS 407 4А
Системой используются сигналы с 20 различных дискретных датчиков. Поэтому будет достаточного одного 32 разрядного дискретного модуля. SM421. (Рисунок 3.4) Тип входного сигнала DC 24В. Входное напряжение логической единицы: 13 – 30В логического нуля: 0 – 5В. Входной ток при сигнале «1» от 6 до 8 мА. Время задержки ввода 3 мс.
Рисунок 2.3 Модуль ввода SM421
Рисунок 2.4 Модуль вывода SM422
Контроллер будет управлять работой 25 механизмов. Причем двадцать один из них двухпозиционного управления а пять трехпозиционного. Отсюда можем вычислить количество необходимых выходов – 30. Поэтому будет достаточного одного 32 разрядного дискретного модуля SM422. (Рисунок 3.4)
Выходной ток при сигнале «1»:
номинальное значение 05 A;
допустимый диапазон от 5 мА до 06 A.
Максимальная частота включения 100 Гц.
2.7.1 Фотоэлектрические датчики
Снятые с производства датчики ФГ-13 предлагается заменить на ФГ-122 производства того же объединения НПП «УРМА». Опытная эксплуатация этих датчиков проходит в цехе с мая месяца. Кроме того релейный выход датчика не требует дополнительного согласования с модулем.
2.7.2 В качестве индуктивных датчиков предлагается продолжить эксплуатацию датчиков ИМТ-5.
2.8 Усиливающие элементы.
Выхода модулей контроллера могут отдавать в нагрузку токи только до пол ампера. А воздушные вентили ВВ-32 потребляют номинальный ток до 1 ампера. Поэтому существует необходимость в усиливающих элементах. В качестве таких устройств предлагается использовать реле. Кроме того реле развяжут выхода контроллера от силовых цепей.
Современные реле фирмы Finder при своих небольших габаритах позволяют переключать довольно большие нагрузки до 20А. В качестве таких реле выбираем реле с каталожным номером 405 290 24 (ток нагрузки до 10 А). В комплекте с реле поставляется колодка имеющая защитный модуль со светодиодом.
2.9 Пульт автоматики 8ПА
Пульт будет содержать:
а) интерфейсный модуль – модуль децентрализованной периферии предназначенный для связи пульта автоматики с контроллером посредством промышленной сети Profibus-DP. Отказ от электрических связей между шкафом автоматики и пультом посредством кабеля прежде всего связан с тем что при таком виде коммутации наладку оборудования и программы можно произвести вне монтажной зоны. А в условиях ограниченности времени на монтаж новой системы это является главным фактором. Так же упрощается и ускоряется сам монтаж пульта на месте – отпадает необходимость расключения кабелей.
Рисунок 2.5 Станция децентрализованной периферии ЕТ200М
б) Модули ввода необходимые для снятия сигналов с ключей управления и доставки этих сигналов через интерфейсный модуль до процессора.
в) Ключи управления и кнопки с помощью которых оператор воздействует на режимы работы стана и механизмов.
г) Ключ-бирку кнопку-грибок для организации безопасных работ при остановке системы и быстрого отключения работы системы при возникновении аварийных ситуаций.
д) панель оператора через которые меняются настройки технологических параметров программы.
а) В качестве интерфейсного модуля предлагается IM 153-1(ET200M) входящий в линию семейства S-300 соответственно в качестве модулей ввода предлагаются модули SM322 а в качестве местного источника питания- PS307 5A которого хватит и для того что бы запитать входные модули. Модули S-300 по сравнению с модулями S-400 занимают значительно меньшее место и хорошо поместятся вместе со всей профильной шиной в нижней части пульта. Так как системой используются 56 сигналов с ключей управления для станции децентрализованной периферии будет достаточно двух модулей.
б) Ключи управления кнопки ключ-бирку кнопку-грибок выбираем из стандартных средств SIMENS серии 3SB. Дальнейшее каталожное обозначение элементов будет зависеть от тех технических функций которые они выполняют. К примеру кнопка грибок красного цвета с поворотным расклиниванием будет заказываться под каталожным номером 3SB3500-1HA20. Кроме того при выборе ключей управления учитывается то что в цехе эксплуатируются ключи с «пистолетной» рукояткой.
2 Разработка и расчет электрической схемы
Для питания системы используется трехфазное переменное напряжение 380 Вольт поданное с 12КТП на вводный автомат QF. Далее этим напряжением запитывается через автомат SF2 и контакты пускателя KM1 источник питания G1.
Шкаф автоматики 4ША.
Данный источник постоянного тока вырабатывает стабилизированное напряжение 24 Вольта и способен отдавать в нагрузку до 40 А. Его напряжением через автоматы SF4SF5SF6 запитываются входныевыходные модули датчики и контакты реле через которые исполняющие устройства подключаются к этому же напряжению.
Для питания процессора CPU416-2DP используется свое стабилизированное напряжение от источника A1 – PS 407 A. Он запитан однофазным переменным напряжением 220 Вольт через автомат SF1.
Розетка XS1 запитывается через автомат SF3 и служит для возможности работы с программатором в шкафу автоматики.
Сигналы с фотодатчиков D43-D52 поступают на модуль ввода A4 c адресом в системе от Е0.0 до Е1.2. Адреса до Е2.0 оставляем в качестве резервных так как существует возможность установки дополнительных фотодатчиков.
Сигналы от остальных датчиков подаются на адреса c Е2.0.
С модуля выводауправляющий сигнал соответствующего адреса подается на обмотку коммутирующего реле K1-K32. Своими контактами реле подключает исполнительное устройство через предохранительный клеммник XF1 к напряжению плюс 24В. Исполняющие устройства другой своей стороной обмотки «посажено» на минус 24 В. Обмотки коммутирующих реле обвязываются диодом и светодиодом размещенных в одном модуле который идет вместе с поставкой реле. Светодиод служит для индикации подачи на обмотки реле напряжения а диод служит для защиты транзисторного выхода модулей вывода от возникающих обратных токов в обмотках реле. Обмотки исполнительных устройств также обвязываются диодами с помощью специальных клеммников XV1.
Пульт управления 5ПА
Компоненты пульта управления 5ПА питаются стабилизированным постоянным напряжением 24 вольта. Это напряжение обеспечивается источником А1 входящим в состав станции децентрализованной периферии ЕТ200М. С этого источника запитаны через автомат SF2 модули вводаА4 ключи управления SA кнопки SB интерфейсный модуль IM153-1 A2 и панель оператора OP1 через автомат SF3.
Шайбы ключей управления и контакты кнопок с одной стороны находятся под напряжением +24 Вольта. И при замыкании шайб ключей и контактов кнопок это напряжение попадает на входы модулей ввода. Тем самым система определяет положение ключей управления.
4. Разработка панели оператора.
В качестве панели оператора выбираем OP270 SMATIC HMI. Выбор данной панели прежде всего обусловлен тем что данные панели уже эксплуатируются в цехе и хорошо себя зарекомендовали со всех сторон. Так же при заказе данной панели не потребуется заказа резервной так как резервная панель OP270 уже имеется в цехе. Кроме того данная панель соответствует всем предъявляемым требованиям по защищенности (IP65 с лицевой стороны) так как место ее установки непосредственно пульт управления где содержание железосодержащей пыли и агрессивных веществ в воздухе повышено. Рисунок 2.6
Рисунок 2.6 Панель оператора OP270
В качестве монтажных элементов предлагается остановиться на продукции фирмы RITTAL. В ее арсенале присутствуют все необходимые монтажные конструктивы. От составных пультов до зажимных кабельных профилей.
В качестве шкафа автоматики выбираем шкаф защищенного исполнения IP65 800x1800x400 в комплекте с монтажной панелью. Шкаф будет оснащен обзорной передней дверью с резиновыми уплотнителями.
Пульт автоматики предлагается собрать из составного пульта защищенного исполнения IP65 состоящего из: тумбы 1200х670х400 пульта 1200х200х400 крышки 1200х200.
В заявке требуется заказать необходимое количество кабельных зажимов две профильные рейки для крепления кабеля.
РАЗРАБОТКА ПРОГРАММНОГО ОБЕСПЕЧЕНИЯ
1.1 Основы проектирования с помощью STEP 7
При решении задачи автоматизации с помощью STEP 7 появляется ряд основных задач. Следующий рисунок показывает задачи которые должны быть решены для большинства проектов и ставит им в соответствие базовые процедуры.
Краткое описание шагов
- Планирование концепции использования вашего контроллера.
Перед началом работы со STEP 7 планируется решение задачи автоматизации от деления процесса на отдельные задачи до создания диаграммы конфигурации.
Рисунок 3.1 Задачи решаемые при автоматизации с помощью STEP 7
- Проектирование структуры программы
Преобразуются задачи описанные в эскизном проекте вашего контроллера в структуру программы используя блоки имеющиеся в STEP 7.
- Запускается STEP 7
STEP 7 запускается из пользовательского интерфейса Windows 9598NT
- Создается структура проекта
Проект похож на папку в которой все данные хранятся в виде иерархической структуры и доступны вам в любое время. После создания проекта все остальные задачи выполняются в этом проекте.
- Конфигурируется станция
При конфигурировании станции указывается какой программируемый контроллер будет использоваться; например SIMATIC 300 SIMATIC 400 SIMATIC S5
- конфигурируется аппаратура
При конфигурировании аппаратуры указывается в конфигурационной таблице какие модули будут использоваться для решения задачи автоматизации и какие адреса должны быть использованы для доступа к модулям из программы пользователя. Модулям также могут быть назначены свойства с помощью параметров.
- Проектируются сети и коммуникационные связи
Основой для коммуникаций является предварительно спроектированная сеть. Для этого вам нужно будет создать подсети необходимые для ваших задач автоматизации установить свойства подсетей и установить свойства сетевых подключений и всех коммуникационных связей требуемых для сетевых станций.
- Определите символы
Вы можете определить в таблице символов локальные или совместно используемые символы имеющие более наглядные имена для использования вместо абсолютных адресов в своей пользовательской программе.
- Разрабатывается программа
Используя один из доступных языков программирования создается программа связанная с модулями или независимая от модулей и сохраняется в виде блоков исходных файлов или схем.
- Генерируются и анализируются справочные данные
Вы можете использовать эти справочные данные для облегчения отладки и модификации программы пользователя
- Проектируются сообщения
Сообщения относящиеся к блокам создаются например с помощью их текстов и атрибутов. Используя передающую программу вы переносите созданные данные о конфигурации сообщений в базу данных системы взаимодействия с оператором (SIMATIC WinCC SIMATIC ProTool).
- Проектируются переменные для управления и наблюдения оператором
Вы создаете переменные для управления и наблюдения оператором один раз в STEP 7 и назначаете им требуемые атрибуты. Используя передающую программу вы переносите созданные переменные для управления и наблюдения оператором в базу данных системы взаимодействия с оператором WinCC.
- Загружается программа в программируемый контроллер
После завершения конфигурирования назначения параметров и программирования задач можно загрузить всю свою пользовательскую программу или отдельные боки из нее в программируемый контроллер. CPU уже содержит операционную систему.
Для тестирования или отображения значения переменных из своей пользовательской программы или CPU которые хотим отображать или присваивать значения переменным необходимо создать таблицу для переменных.
- Диагностика аппаратуры
Причина неисправности модуля определяется отображением информации о модуле в режиме online. Причины ошибок в обработке программы пользователя определяются с помощью диагностического буфера и содержимого стеков. Также можно проверить может ли программа пользователя исполняться на конкретном CPU.
1.2 Создание конфигурации контроллера и проектирование структуры программы.
Первым этапом проектирования в STEP 7 является создание проекта и конфигурирование контроллера в Hardware.
При создании проекта в мастере указываем необходимый процессор CPU 416-2DP и назначаем название проекту. Проект называем «Прошивной стан».
Далее запускаем инструмент HW config в котором начинаем сначала конфигурировать аппаратуру.
Под конфигурированием понимается размещение стоек модулей устройств децентрализованной периферии и интерфейсных модулей в окне станции. Стойки представляются с помощью конфигурационной таблицы которая как и стойка допускает определенное число устанавливаемых модулей. В конфигурационной таблице STEP 7 автоматически присваивает каждому модулю адрес. Вы можете изменить адреса модулей станции если CPU допускает свободное присвоение адресов. Вы можете как угодно часто копировать конфигурацию в другие проекты STEP 7 при необходимости их модифицировать и загрузить в одну или несколько существующих установок. При запуске системы автоматизации CPU сравнивает заданную конфигурацию созданную с помощью STEP 7 с фактической конфигурацией установки. Благодаря этому возможные ошибки немедленно распознаются и сигнализируются.
В окне для выбора аппаратуры в папке S-400 выбираем источник питания PS407 4A и переносим его мышкой в первую строчку стойки контроллера. Процессор должен уже находиться в стойке. Далее таким же образом устанавливаем модули ввода и вывода SM421 DI32х24V и SM422 DO32х24V0.5A.
От окна станции будет отходить ветка – шина Profibus-DP. Именно на нее перетаскиваем интерфейсный модуль IM 153-1. После в появившееся окно добавляем два модуля SM421 DI32х24V. Так сконфигурируем станцию децентрализованной периферии ЕТ200М. Сохраняем и закрываем окно HW config. Параметризацию модулей оставляем по умолчанию.
В главном окне SIMATIC Manager вставляем панель оператора OP. Откроется пакет ProTool в котором выберем интересующую панель OP270. На данном этапе пакет ProTool закрываем
В итоге конфигурации получаем промышленную сеть работающую по протоколу Profibus-DP и состоящую из контроллера S-400 панели оператора OP270 и станции децентрализованной периферии ЕТ200М.
1.3 Определение символов
Для облегчения чтения своей программы и упрощения поиска неисправностей с помощью символьной таблицы назначим абсолютным адресам символические имена. Каждому входу и выходу присваиваем символическое имя. В символьном имени ставим префикс «D» для фотодатчиков и «I» для индуктивных далее номер датчика. Для входов снимающих сигналы с ключей управления в имени ставим обозначение элемента на схеме. Для выходов в имени указываем цеховой номер привода. Символьную адресацию сопровождаем разъясняющими комментариями в
1.4 Определение структуры программы.
Блоки программы пользователя в STEP 7 изначально можно поделить на несколько частей выполняющих разные функции.
1.4.1 Определение условий для перезапуска в CPU.
Так как системе не требуется инициализации сигналов с определенным значением при запуске или рестарте блоки обработки рестарта можно не программировать.
1.4.2 Определение реакции на прерывания.
Для того что бы программа имела возможность запрограммированного реагирования на возникновение программных и аппаратных ошибок программируем блоки обработки прерываний по ошибке.
В каждом из организационных блоков обрабатывающих ошибки программы будет устанавливаться в «1» определенный меркер. Далее уже в основной программе при установке в «1» такого меркера соответствующее сообщение будет отослано на панель оператора после меркер здесь же будет сброшен в «0». Таким образом будет обработано прерывание по ошибке и персонал будет проинформирован о возникшей неисправности.
Программируем следующие организационные блоки:
OB80 – блок обрабатывающий временную ошибку
OB81 – блок обрабатывающий ошибка по питанию
OB82 – блок обрабатывающий диагностическое прерывание
OB83 – блок обрабатывающий ошибку установки модуля
OB84 – блок обрабатывающий аппаратную неисправность CPU
OB85 – блок обрабатывающий ошибку класса приоритета
OB86 – блок обрабатывающий неисправность стойки
OB87 – блок обрабатывающий ошибку связи
OB 121 – блок обрабатывающий ошибку программирования
OB 122 – блок обрабатывающий ошибку доступа
1.4.3 Обработка данных процесса.
К этому типу блоков относятся блоки решающие технологическую задачу – обработку входных сигналов с датчиков и генерирование выходных сигналов управляющих механизмами по определенному алгоритму.
Предлагается разделить управление механизмами по определенным функциональным блокам. Каждому механизму или группе механизмов будет соответствовать свой блок. Нумерацию начнем со ста. Первые номера функций оставляют для системных и прикладных задач.
Создаем функцию за функцией в соответствии с блоками старой системы. При этом параллельно присваивая каждому блоку символьное имя.
В итоге получится пятнадцать функциональных блоков:
«FC101_ОТВОДЯЩИЙ_РОЛЬГАНГ» – программный блок для управления отводящим рольгангом;
«FC102_ЗАЦЕНТРОВЩИК» – программный блок для управления зацентровщиком;
«FC103_ВЫБРАСЫВАТЕЛЬ» – программный блок для управления выбрасывателем;
«FC104_КРЫШКА_ЖЕЛОБА» – программный блок для управления крышкой желоба;
«FC105_ВТАЛКИВАТЕЛЬ» – программный блок для управления вталкивателем;
«FC106_ИСЧЕЗАЮЩИЙ УПОР» – программный блок для управления исчезающим упором;
«FC107_ГОТОВНОСТЬ_МЕХ._ВЫХ._СТ.» – программный блок формирования готовностей устройств на выходе стана;
«FC108_ПЕРЕХВАТЧИК» – программный блок для управления перехватчиком;
«FC109_ОХЛАЖДЕНИЕ_ОПРАВКИ» – программный блок для управления охлаждением оправки;
«FC110_ЦЕНТРОВАТЕЛИ» – программный блок для управления центрователями;
«FC111_ВЫДАЮЩИЕ РОЛИКИ-ВРАЩЕНИЕ» – программный блок для управления вращением выдающих роликов;
«FC112_ВЫДАЮЩИЕ РОЛИКИ-СВЕДЕНИЕ» – программный блок для управления сведением выдающих роликов;
«FC113_УПОРНЫЙ_МЕХАНИЗМ» – программный блок для управления упорным механизмом;
«FC114_РОЛИКИ_ОТВОДА_СТЕРЖНЯ» – программный блок для управления роликами отвода стержня;
«FC115_ЗАМЕНА_ОПРАВКИ» – программный блок для замены оправки.
1.5 Организация цикла выполнения программы пользователя
Из организационного блока OB1 организуем последовательный вызов всех вышеперечисленных функций. Программа последовательно будет обрабатывать каждый функциональный блок. После обработки последнего программа начнет обработку цикла сначала. Так будет организован цикл выполнения программы пользователя.
1.6 Организация обмена данных с панелью оператора
В процессе работы программа будет обрабатывать таймеры которые должны реализовывать различные технологические задержки. Значения этих задержек должны изменяться технологическим персоналом с панели оператора. Кроме того существуют некоторые различия в режимах работы механизмов. Например срабатывание механизма с задержкой но с задержкой от различных датчиков.
Для этих целей в теле программы организуется блок данных DB20 похожий на массив. Таймер для получения своего задания обращается к соответствующему полю блока. В свою очередь поля блока данных изменяются с панели оператора. Каждое поле окошка панели оператора жестко связано с соответствующим полем блока данных.
Таким образом технологический персонал с помощью панели оператора может оперативно задавать технологические параметры и режимы работы механизмов. Главным достоинством такого метода задания параметров является его «жесткость» так все переменные вводятся в цифровом виде.
Еще одним важным моментом является необходимость в обеспечении ремонтного персонала сообщениями о возникших неисправностях. Такой обмен реализуется тоже с помощью блока данных состоящего из битов каждый из которых в свою очередь связан с определенной ошибкой. С возникновением ошибки программа взводит этот бит и на панели оператора появляется сообщение о конкретной неисправности. Данное сообщение не исчезнет до тех пор пока оператор не нажмет кнопку «квитирование сообщений». При программировании панели указывается этот блок данных область отвечающая за сообщения.
2 Разработка алгоритма работы линии.
Прошивной стан трубопрокатного агрегата ТПА-140 предназначен для горячей прошивки сплошной заготовки в полую гильзу методом поперечно-винтовой прокатки с целью получения гильзы для последующей ее прокатки в трубу. Общий вид района стана представлен в приложении.
Нагретая в кольцевой печи заготовка укладывается машиной выгрузки на отводящий рольганг пр.115 который включается по сигналу фотореле Д43. По сигналу фотореле Д44 отводящий рольганг c выдержкой времени отключается. Выдержка времени выбирается так чтобы заготовка плавно подошла к зацентровщику пр.116 117118. По сигналу фотореле Д45 (засвечен) и отсутствии заготовки в желобе Д46 (не засвечен) включается выбрасыватель пр.121. При работе с зацентровщиком (режим выбирается с панели оператора) по сигналу Д45 с выдержкой времени включается механизм подъёма конца заготовки пр.116. По датчику верхнего положения механизма 116И формируется сигнал "Выстрел" - включение ударника пр.117 по сигналу датчика давления ударник отключается и включается эжектор пр.118 (возврат ударника) одновременно опускается механизм подъема. Заготовка зацентровалась.
Зацентрованная заготовка выбрасывателем пр.121 (исходное положение индицируется датчиком 121И) передается на решетку перед прошивным станом и скатывается по ней в желоб (верхнее положение индицируется датчиком 123И). При наличии заготовки в желобе (Д46 засвечен) если есть "Готовность стана" и главный привод включен через регулируемую выдержку времени включается вталкиватель пр.124. При засвечивании Д47 перекрыватель пр.123 опускается. Одновременно отключается охлаждение оправки пр.137 которое включается после пропадания сигнала с датчика нагрузки (ДН).
Заготовка попадает в валки стана появляется сигнал с датчика статической нагрузки ДН при этом вталкиватель возвращается в исходное положение перекрыватель через выдержку времени открывается.
На рольганг пр.115 подается следующая заготовка зацентровывается (при работе с зацентровщиком) и если Д46 не засвечен выбрасывателем пр.121 передается на решетку перед станом и скатывается в желоб засвечивая датчик Д46.
Если прошивка предыдущей заготовки закончилась (ДН нет Д48А не засвечен) а "Готовности стана" нет опускается исчезающий упор пр.125 (опущенное положение упора индицируется датчиком 125И) после чего вталкиватель толкает заготовку до упора. Как только появляется "Готовность стана" исчезающий упор поднимается и заготовка подается в стан.
При прошивке заготовки на выходной стороне стана засвечивается датчик Д48А. Через регулируемую выдержку времени открывается центрователь №1 пр.138 затем засвечивается фотодатчик Д48 и открывается центрователь №2 пр.139. Далее при засветке Д49 разводится центрователь №3 пр.140 либо центрователь №3 открывается по датчику Д48 после сведения первой пары выдающих роликов - при короткой гильзе. Центрователь №4 пр.141 открывается через регулируемую выдержку времени при подходе гильзы к фотодатчику Д50.
По окончании прошивки исчезает сигнал с датчика нагрузки открывается замок формируется импульсное включение сведения выдающих роликов №1 пр.144. (длительность регулируется). Существует режим сведения роликов №1 по исчезновению нагрузки или открытию замка. Происходит проброс гильзы из зоны перехвата. В зависимости от массы гильзы при пробросе могут подключаться выдающие ролики №2 №3. После сведения роликов №1 с регулируемой выдержкой срабатывает перехватчик стержня пр.136 либо перехватчик сводится после схода гильзы с фотодатчика Д48А. По сигналу наличия напряжения на вентиле перехватчика поднимается упорная головка и с регулируемой выдержкой времени сводятся выдающие ролики №2 №3 №4 №5 №6. Ролики начинают стягивать гильзу с оправки.
- с Д49 разводятся выдающие ролики №2;
- с Д50 разводится выдающие ролики №3;
- с Д51 разводятся выдающие ролики №4;
- с Д52 закрывается центрователь №4 и разводятся выдающие ролики №5 №6.
После закрытия центрователя №4 с регулируемой выдержкой времени закрывается упорная головка. По закрытию головки сводятся центрователи №1-№3 и закрывается замок. По появлению сигналов "головка опущена" "замок закрыт" разводится перехватчик и появляется сигнал "Готовность". Стан готов к прокатке следующей заготовки.
3 Разработка программы управления линии
3.1 Программирование контроллера
Действующая система автоматического управления работает по алгоритмам реализованным на элементах «логики-Т». Работа блоков логики описывается принципиальными электрическими схемами состоящими из элементов булевой логики. На основании этих схем создаем программу на языке FBD. Этот язык тоже использует для программирования булеву логику. Каждый блок логики со своей принципиальной схемой будет соответствовать функциональному блоку со своей программой в FBD. Простейшие элементы И ИЛИ НЕ в FBD рисуются один к одному. Память в блоках логики реализованная двумя элементами И в FBD рисуется триггером. Задержки реализованные на элементах Т-303 в FBD рисуются таймерами. Если задержка является регулируемой в блоке данных DB20
отводится переменное поле с типом S5TIME. Адрес этого поля указывается в задании соответствующего таймера.
В конечном итоге количество блоков логики в шкафу автоматики БАС-54 будет совпадать с количеством функциональных блоков в программе STEP 7.
После программу написанную в FBD переводим на язык более понятный ремонтному персоналу LAD(это сокращение международного термина Ladder Logic - логическая схема). Это делаем в связи с тем что на участке в качестве языка для программирования контроллеров принято использовать контактный план. Синтаксис команд этого языка похож на коммутационную схему поэтому LAD позволяет легко проследить поток сигнала между токовыми шинами через входы выходы и команды что сокращает время наладки и поиска неисправностей при дальнейшей эксплуатации.
3.1 Программирование панели оператора
Программа или проект для панели оператора создается с помощью пакета ProTool. Проект ProTool состоит главным образом из экранных форм при помощи которых можно осуществлять контроль и управление объектом автоматизации. Кроме того будут использоваться дополнительные объекты такие как сообщения. Связь с контроллером устанавливается посредством тегов. Операторский терминал осуществляет отображение значений получаемых от контроллера и может использоваться для ввода значений с клавиатуры. Еще одной функцией использования панели является визуализация технологического процесса. Визуализация осуществляется так же при помощи экранных форм. На экранной форме оператору представляется информация о текущем состоянии технологическ5их параметров в виде числовых данных. Текущий этап технологического процесса будет отображаться посредством динамических объектов.
В начале создания проекта определимся с окнами (экранами) которые нам необходимы.
Самое первое окно будет называться «главным». Оно будет содержать перечень всех окон и из него нажатием необходимой кнопки можно будет вызвать все остальные экраны.
Второе окно будет служить для просмотра и изменения технологических параметров. Экран будет содержать таблицу с названиями технологических задержек слева и полями для просмотра и изменения справа. Оператор направив курсор на нужное поле с цифровой клавиатуры может изменить нужное значение. Каждое из полей будет связано с тегом который в свою очередь привязывается к соответствующему полю блока данных контроллера DB20. Теги описываются параллельно созданию поля на экране.
За визуализацию технологического процесса будет отвечать третье окно. На нем будет изображен район прошивного стана с вырисовкой всех механизмов и датчиков. Этот экран будет в динамике показывать положение трубы в стане состояние датчиков и механизмов.
Четвертое окно предназначается ремонтному персоналу и будет заниматься диагностической функцией. Данное окно будет показывать состояние всех входов и выходов системы состояние модулей и периферии.
Кроме создания экранных форм необходимо запрограммировать обработку сообщений. В системных настройках панели указываем блок DB21 как блок отвечающий в PLC за сообщения.
После того как проект для S-400 и для OP270 будет готов приступаем отладке системы. Отладка программной части контроллера производится после внутреннего монтажа шкафа и пульта управления. То что проект предусматривает связь пульта управления с контроллером без кабельных соединений позволяет проводить проверку работы основных частей системы в лабораторных условиях вне монтажной зоны.
Основным инструментом для отладки является персональный компьютер с установленным на него необходимым программным обеспечением.
Для начала стендовой проверки монтированного шкафа автоматики и пульта управления остается только запитать шкаф пульт панель оператора.
Далее сразу же проверяем правильность подачи напряжения на источники питания в шкафу их выхода правильность распределения питания 24 вольта при запитке модулей и датчиков. Таким же образом проверяем правильность монтажа пульта управления и станции ЕТ200.
После проверки правильности распределения питающих напряжений следует смонтировать сетевое оборудование для работы Profibus. Посредством специальных разъемов и кабеля соединяем между собой контроллер S-400 панель оператора OP270 и станцию.
Загружаем проекты в контроллер и панель оператора.
Как правило на данном этапе первыми проблемами являются различные ошибки при задании сетевых настроек таких как несогласование скорости передачи несогласование адресации в проектах для панели и контроллера.
Следующим этапом проверяем соответствие полей на экранах OP необходимым таймерам в программе. Включив режим динамики Online изменяем значение задержек на экранах. Задание для соответствующих таймеров должно равняться значению на панели. При этом проверяем работу ключей управления их правильность монтажа и правильность использования в программе. Любое изменение положения ключа должно отображаться в работе программы.
Установив все ключи управления в положение «автоматика» начинаем проверку работы технологической программы.
Суть проверки работы программы будет сведена к имитации сигналов датчиков в технологической последовательности и проверка правильной реакции выходов системы. При этом в программе открывается интересующий нас функциональный блок и опять же в динамике просматривается работа программы. Кроме стандартной последовательности сигналов задается аварийная последовательность. Реакция системы должна быть четкой. В зависимости от типа аварии на экране панели оператора должна появиться соответствующее мигающее сообщение а выхода контроллера должны быть отключены. Для имитации работы датчиков используется пульт собранный посредством тумблеров. Данный пульт подключается к шкафу через клеммники с помощью которых после посредством кабеля будут подключены настоящие датчики.
Такая комплексная стендовая проверка позволяет проверить не только работу программы но и правильность электрического монтажа.
После такой проверки при монтаже такой несложной системы на месте как правило больших трудностей не возникает.
ЭКСПЛУАТАЦИОННАЯ ДОКУМЕНТАЦИЯ
1 Инструкция оператору
Перечень экранов панели оператора – технолога приведены в приложении 1 данной записки.
Экран панели оператора – технолога состоит из трех областей:
В обзорной области экранов панели оператора – технолога отображена следующая информация:
Количество прокатанных за смену труб
Режим работы САУ (ручнойавтоматический).
В области кнопок отображены пиктограммы кнопок с указаниями экранов доступных для перехода из данного экрана.
Рабочая область содержит непосредственно сам экран. Описание экранов приведено ниже.
На рисунке 4.1 приведен стартовый экран. На данном экране размещены следующие кнопки управления:
кнопка перехода на экран просмотра и ввода программ прокатки;
кнопка перехода на экран контроля текущего состояния системы;
кнопка перехода на экран просмотра параметров главных приводов;
кнопка перехода на экран временных задержек транспортной автоматики;
кнопка перехода на экран просмотра технологических параметров прошитых гильз;
кнопка перехода на экран текущих параметров вспомогательных приводов;
кнопка перехода на экран диагностики органов управления;
кнопка перехода на экран изменения паролей и уровней доступа.
На рисунке 4.2 приведен экран просмотра и ввода теоретических и практических программ прокатки. Данный экран позволяет загружать из контроллера и сохранять в контроллере программы прокатки как практические (для операторов-технологов) и как теоретические (по паролю). Также на экране изображены текущие значения параметров программы (из текущей программы прокатки). В качестве параметров программы прокатки могут быть заданы следующие величины:
номер программы прокатки;
диаметр готовой трубы;
толщина стенки готовой трубы;
толщина стенки гильзы;
расстояние между валками;
положение верхней линейки;
положение каретки УРМ;
коэффициент вытяжки.
На рисунке 4.3 приведен экран диагностики состояния системы. На данном экране размещена следующая информация и кнопки управления:
подача напряжения на устройства в шкафу 4ША;
готовность электрооборудования участка стана;
подача напряжения на устройства в пульте 5ПУ;
подача напряжения на устройства в шкафу приводов ШП3;
готовность систем измерения;
готовность приводов настройки стана;
кнопка перехода в стартовый экран.
На рисунке 4.4 приведен экран энергосиловых параметров стана. На данном экране размещена следующая информация и кнопки управления:
скорости двигателей левого и правого валков стана в цифровом и в графическом виде;
токи якоря двигателей левого и правого валков стана в цифровом и в графическом виде;
напряжение якоря двигателей левого и правого валков стана в цифровом и в графическом виде;
моменты двигателей левого и правого валков стана в цифровом и в графическом виде;
токи возбуждения двигателей левого и правого валков стана в цифровом и в графическом виде;
На рисунке 4.5 изображен экран временных параметров системы. В качестве параметров можно задать следующие величины:
задержки на включениеотключение механизмов;
время работы механизма;
условия срабатывания некоторых механизмов;
задание количества заготовок для смены оправки.
На рисунке 4.6 изображен экран технологических параметров гильз. На данном экране размещена следующая информация:
номер прошитой гильзы;
температура заготовки на выходе из печи;
температура гильзы на выходе из стана;
диаметр гильзы на выходе из стана;
длина гильзы на выходе из стана.
На рисунке 4.7 приведен экран параметров электроприводов настройки стана. На данном экране размещена следующая информация и кнопки управления:
скорости двигателей вспомогательных приводов;
токи двигателей вспомогательных приводов;
кнопка перехода в экран настройки параметров стана;
кнопка перехода в экран калибровки датчиков положения механизмов настройки стана;
На рисунке 4.8 приведен экран настройки параметров стана. На данном экране размещена следующая информация и кнопки управления:
выбор режима работы приводов установки левого и правого валков (совместнораздельно);
заданные значения положений механизмов настройки стана;
фактические значения положений механизмов настройки стана;
поля ввода для задания значения скорости приводов в ручном режиме;
кнопка перехода в экран параметров электроприводов настройки стана;
На рисунке 4.9 приведен экран калибровки датчиков положения. На данном экране размещена следующая информация и кнопки управления:
текущее значение датчиков положения в миллиметрах;
текущее значение датчиков положения в двоичном коде;
поля ввода для измеренных опытным путем значений положения механизмов;
кнопки «ЗАДАТЬ» для задания измеренных опытным путем значений;
На рисунке 4.10 приведен экран диагностики входныхвыходных сигналов. Данный экран предназначен для ускорения процесса поиска неисправностей. Экран имитирует внешний вид станции распределенного вводавывода ЕТ200М. При срабатывании какого-либо входа или выхода на экране зажигается соответствующий сигнал.
На рисунке 4.11 приведен экран настройки прав доступа. Этот экран предназначен для ввода новых пользователей и задания уровня доступа. Вход в этот экран возможен только при наличии прав полного доступа. На данном экране размещена следующая информация и кнопки управления:
таблица пользователей с указанием их паролей и уровня доступа;
кнопка для выхода из сети текущего пользователя;
ФУНКЦИОНАЛЬНО-СТОИМОСТНОЙ И ЭКОНОМИЧЕСКИЙ АНАЛИЗ ПРОЕКТА
1. Функционально-стоимостной анализ (ФСА) базового проекта
В данном разделе обоснована экономическая целесообразность модернизации системы автоматического управления прошивного стана. Для этого используется функционально-стоимостной анализ старой системы управления. С использованием корректирующей формы функционально-стоимостного анализа производится анализ базового варианта технической системы подвергающийся инновационным преобразованиям. В результате данного анализа в базовом варианте обнаруживаются функциональные и структурные элементы системы обладающие экономической несостоятельностью или функциональной недостаточностью. Именно эти элементы должны быть рационализированы. При этом кроме технических эффектов от разработки появляются экономические социальные экологические и иные эффекты.
Построение структурной модели.
Структурная модель (СМ) - это упорядоченное представление элементов объекта и отношений между ними дающее представление о составе материальных составляющих объекта их основных взаимосвязях и уровнях иерархии. Структурная модель базового варианта стенда для приемо-сдаточных испытаний арматуры высокого давления представлена на рис. 8.
Построение функциональной модели объекта.
Функциональная модель (ФМ) - это логико-графическое изображение состава и взаимосвязей функций объекта получаемое по средствам их формулировки и установления порядка подчинения. ФМ базового варианта пары труботрезных станков на рис. 9.
Построение совмещенной функционально-стоимостной модели (ФСМ) объекта.
В данном пункте производится функционально-стоимостной анализ базового варианта стенда для приемо-сдаточных испытаний арматуры высокого давления. ФСМ объекта пригодна для выявления ненужных функций и элементов в объекте (бесполезных и вредных); определения функциональной достаточности и полезности материальных элементов объекта; распределения затрат по функциям; оценки качества исполнения функций; выявления дефектных функциональных зон в объекте; определения уровня функционально-структурной организации изделия.
Построение ФСМ осуществляется путем совмещения ФМ и СМ объекта .
ФСМ системы управления базового варианта стенда для приемо-сдаточных испытаний арматуры высокого давления представлена в таблице 10.
Оценка значимости функции ведется последовательно по уровням ФМ (сверху вниз) начиная с первого. Для главной и второстепенной т.е. внешних функций объекта при оценке их значимости исходным является распределение требований потребителей (показателей качества параметров свойств) по значимости (важности).
Нормирующим условием для функции является следующее:
n - количество функций расположенных на одном уровне ФМ и относящихся к общему узлу вышестоящего уровня.
Для внутренних функций определение значимости ведется исходя из их роли в обеспечении функций вышестоящего уровня.
Определение относительной важности функции R.
Учитывая многоступенчатую структуру ФМ наряду с оценкой значимости функций по отношению к ближайшей вышестоящей определяется показатель относительной важности функции любого i-го уровня Rij по отношению к изделию в целом:
где G - количество уровней ФМ.
В случае если одна функция участвует одновременно в обеспечении нескольких функций верхнего уровня ФМ ее значимость определяется для каждой из них отдельно а относительная важность функции для объекта в целом рассчитывается как сумма значений Rij по каждой ветви ФМ (от iго уровня до первого) проходящей через эту функцию.
Оценка качества исполнения функций Q.
Обобщенный (комплексный) показатель качества варианта исполнения функций оценивается по формуле:
где bn - значимость nго потребительского свойства;
Pnv - степень удовлетворения nго свойства в vом варианте;
m - количество свойств.
Важным элементом качества исполнения функций является функциональная организованность изделий которая определяется следующими показателями.
Показатель актуализации функций определяется коэффициентом актуализации:
где Fп - необходимые функции;
Fоб - общее количество действительных функций;
Показатель сосредоточения функций определяется коэффициентом сосредоточения:
где Fосн - количество основных функций;
Fоб - общее количество функций.
Показатель совместимости функций определяется коэффициентом совместимости:
где Fс - функции согласования;
Показатель гибкости функций определяется коэффициентом гибкости:
где FP - количество потенциальных функции;
FП - количество необходимых функций.
Качество выполнения функций будет иметь вид:
Определение абсолютной стоимости функций.
Функционально необходимые затраты - минимально возможные затраты на реализацию комплекса функций объекта при соблюдении заданных требований потребителей (параметров качества) в условиях производства и применения (эксплуатации) организационно- технический уровень которых соответствует уровню сложности спроектированного объекта.
Абсолютная стоимость реализации функций Sабс определяется по формуле:
Sабс=Sизг+Sэкспл+Sтр+Sэн+Sпроч
где Sизг - затраты связанные с изготовлением (приобретением) материального носителя функции. В состав этих затрат входят: затраты на проектирование изготовление (модернизацию) пуско-наладочные работы обучение персонала:
Sэкспл - эксплуатационные затраты;
Sтр - затраты связанные с трудоемкостью реализации функции;
Sэн - энергозатраты на реализацию функции;
Sпроч - прочие затраты на реализацию функции .
Определение относительной стоимости реализации функций
Относительная стоимость реализации функций SотнF определяется по формуле:
где Sабс - суммарная абсолютная стоимость функционирования объекта.
SабсFij - абсолютная стоимость реализации jой функции iго уровня ФМ.
Построение функционально-стоимостных диаграмм (ФСД) и диаграмм качества исполнения функций (КИФ).
Данные диаграммы строятся для базового и проектного варианта исследуемого объекта. Они имеют целью выявления зон диспропорции т.е. зон избыточной затратности реализации функции а также определение зон функциональной недостаточности (низкого качества исполнения функций).
Диаграммы ФСД и КИФ строятся для базового варианта (до принятия проектного решения) и проектного варианта. Они вынесены на графическую часть проекта и изображены на листе 9 (технико-экономические показатели проекта иллюстрация).
Структурная модель базового варианта
Функциональная модель базового варианта стенда
Функционально-стоимостная модель базового варианта стенда
Наименование функции
Материальный носитель функции
Придача вращения валкам
Двигатель гл. привода
Регулировка и настройка стана
Подача силового напряжения на двигателя
Обеспечение защиты главных и вспом. приводов
Преобразование частоты
Преобразователи частоты
Траснпортировка заготовки к выбрасывателю
Перемещение заготовки к вталкивателю
Задача заготовки в валки
Удерживание заготовки на оси прокатки
Перемещение гильзы вдоль оси прокатки
Вертикальное удерживание гильзы
Обеспечение соосности основных узлов стана
Перемещение заготвки вдоль стержня
Центровка гильзы на выходной стороне
Формирование внутреннего диаметра
Удерживание заднего конца стержня
Удерживание переднего конца стержня
Включение выключение устройств
Индикация режимов работы
Реализация алгоритма посредством элементов
Обеспечение системы стабилизированным питанием
Обеспечение электрической совместимости сигналов с датчиков и команд
Блоки развязки и усиления
Реализация управления
Управление работой станка согласно заданному алгоритму
Преобразование электрической энергии в механическую
F1= f1.1+ f1.2+ f1.3+ f1.4
Транспортировка заготовки
F2= f2.1+ f2.2+ f2.3+ f2.4+ f.2.5
F3= f3.1+ f3.2+ f3.3+ f3.4+ f.3.5
Транспортировка гильзы
F4=f4.1+ f4.2+ f4.3+ f4.4
Управление работой прошивного стана
2. Функционально-стоимостной анализ проектируемого варианта
Структурная модель (СМ) - это упорядоченное представление элементов объекта и отношений между ними дающее представление о составе материальных составляющих объекта их основных взаимосвязях и уровнях иерархии . Структурная модель проектируемого варианта стенда для приемо-сдаточных и исследовательских испытаний арматуры высокого давления представлена на рис. 10.
Функциональная модель (ФМ) - это логико-графическое изображение состава и взаимосвязей функций объекта получаемое по средствам их формулировки и установления порядка подчинения. ФМ проектируемого варианта стенда для приемо-сдаточных и исследовательских испытаний арматуры высокого давления представлена на рис. 11.
В данном пункте производится функционально-стоимостной анализ проектируемого варианта стенда для приемо-сдаточных и исследовательских испытаний арматуры высокого давления. ФСМ объекта пригодна для выявления ненужных функций и элементов в объекте (бесполезных и вредных); определения функциональной достаточности и полезности материальных элементов объекта; распределения затрат по функциям; оценки качества исполнения функций; выявления дефектных функциональных зон в объекте; определения уровня функционально-структурной организации изделия.
Построение ФСМ осуществляется путем совмещения ФМ и СМ объекта . ФСМ проектируемого варианта стенда для приемо-сдаточных и исследовательских испытаний арматуры высокого давления представлена в таблице 11.
Оценка значимости функции ведется последовательно по уровням ФМ (сверху вниз) начиная с первого. Для главной и второстепенной т.е. внешних функций объекта при оценке их значимости исходным является распределение требований потребителей (показателей качества параметров свойств) по значимости (важности).
Sабс=Sизг+Sэкспл+Sтр+Sэн+Sпроч
Определение относительной стоимости реализации функций.
Структурная модель проектируемого варианта
Функциональная модель проектируемых гидравлической пневматической систем стенда
Выбор режимов и управляющие воздествия
Управление электроприводом
Упрвление пневмоприводом
Програмное управление
Обеспечение системы стаб. питанием
Организация ввод и вывод сигналов контроллера
Реализация сбора информации и испонения команд
Датчики и исполнительные устройства
Програмное управление работой станка
Диаграммы ФСД и КИФ строятся для базового варианта (до принятия проектного решения) и проектного варианта. Они имеют целью выявления зон диспропорции т.е. зон избыточной затратности реализации функции а также определение зон функциональной недостаточности (низкого качества исполнения функций).
3. Расчет окупаемости и экономическая оценка проекта
Экономическая оценка проекта осуществляется с использованием следующих показателей:
) чистая приведенная величина дохода (Net Present Value - NPV).
NPV представляет собой разность между приведенным к началу реализации проекта поступлениями от реализации проекта и инвестиционными затратами т.е. сумму дисконтированного чистого денежного потока за период реализации проекта:
где Т – продолжительность реализации проекта;
t – порядковый номер года реализации проекта;
NCFt – чистый денежный поток года t;
PV – коэффициент дисконтирования в году t;
) коэффициент дисконтирования (PV – фактор) для года t определяется по формуле:
где r – ставка дисконта;
) внутренняя норма доходности (Internal Rate of Return - IRR).
Внутренняя норма доходности (IRR) – это значение ставки дисконтирования при котором сумма дисконтированных поступлений денежных средств равна сумме дисконтированных платежей или чистая приведенная величина дохода (NPV) обращается в ноль. Таким образом значение внутренней нормы доходности определяется из соотношения:
) периодом окупаемости проекта или периодом возврата инвестиций (Discounted Payback Period - DPP) называется период времени за который дисконтированные поступления от результатов внедрения проектных решений покроют инвестиции т. е. значение периода окупаемости определяется из соотношения:
где CFt – поступление денежных средств от эффектов связанных с внедрением проекта;
IN – инвестиционные затраты.
Наименование показателей
Эффект от проектного решения:
Итого: денежные средства (Cash Flow) от реализации проекта (1-2)
Ликвидационная стоимость активов
Итого: денежные средства (Cash Flow) от инвестиционной деятельности (5-4)
Чистый денежный поток средств (Net Cash Flow) (3+6)
Дисконтированный чистый денежный поток средств NCFt*PVt
Дисконтированный чистый денежный поток нарастающим итогом
Таблица формирования денежного потока (в рублях)
Исходя из приведенных расчетов (табл. ) можно сделать вывод о том что проект является эффективным т.к. чистая приведенная величина дохода положительна внутренняя норма доходности больше ставки дисконтирования проект окупается за 2 года.
ГОСТ 2.105 – 95. ЕСКД. Общие требования к текстовым документам. - изд. 1995.
ГОСТ 2.106 – 96. ЕСКД. Текстовые документы. - изд. 1995.
ГОСТ 7.32 – 91. ЕСКД. Отчет о НИР. - изд. 1991.
ГОСТ 2.301 – 68. ЕСКД. Форматы. - изд. 1991.
ГОСТ 2.104 – 68. ЕСКД. Основные надписи. - изд. 1995.
ГОСТ 7.1 – 84. ЕСКД. Библиографическое описание документа. Общие требования и правила составления. - изд. 1987.
ГОСТ 8.417 – 81. ЕСКД. Единицы физических величин. - изд. 1981.
ГОСТ 19.701 – 90. ЕСКД. Схемы алгоритмов программ данных и систем. - изд. 1994.
ГОСТ 2.004 – 88. ЕСКД. Общие требования к выполнению конструкторских и технологических документов на печатающих и графических устройствах вывода ЭВМ. - изд. 1995.
Методические указания к выполнению дипломного проекта для студентов специальности 210200 Курган - изд. 2001.
АСУТП ТПА 140 БАС-54 Участок прошивного стана: Техническое описание Уралчерметавтоматика. – изд. 1975
АСУТП БАС-5 Подсистема БАС-54 Участок прошивного стана Станция управления 4ША: Техническое описание Уралчерметавтоматика. – изд. 1975
АСУТП БАС-5 Подсистема БАС-54 Участок прошивного стана Пульт управления 5ПА: Техническое описание Уралчерметавтоматика. – изд. 1975
SIMATIC Программируемые контроллеры S-400: Справочное руководство SIMENS AG. – изд. 1998.
SIMATIC HMI Панель оператора OP270: Справочное руководство SIMENS AG. – изд. 1998.
SIMATIC HMI Среда программирования ProTool: Руководство пользователя SIMENS AG. – изд. 1998.
SIMATIC LAD для S-400S-300 Программирование : Справочное руководство SIMENS AG. – изд. 1998.
SIMATIC Конфигурирование аппаратуры и проектирование соединений в STEP 7: Руководство пользователя SIMENS AG. – изд. 1998.
SIMATIC Программирование в STEP 7: Руководство пользователя SIMENS AG. – изд. 1998.
Общий видV7.cdw

Механизм перехвата стержня.
Механизм перемещения валка.
Привод поворота барабана.
Механизм запирания крышки.
ТЕХНИЧЕСКИЕ ТРЕБОВАНИЯ
Размеры для справок.
Разводку трбной проводки выполнить по месту.
Стан заземлить согласно требований эксплуатации
Стан покрасить в соответвии с правилами и нормами.
Проект модернизации системы управления
линией прошивного стана ТПА- 140
Булычев гр. ТЗк-6134с
Производительность стана - до 170в час
Минимальный диаметр заготовки - 88 мм.
Максисмальный диаметр заговки - 120 мм.
Максимальная длинна гильзы - 7500 мм.
Количество технологического персонала - 2 человека
ТЕХНИЧЕСКАЯ ХАРАКТЕРИСТИКА
Рекомендуемые чертежи
- 09.03.2022