Дипломная работа по модернизации гидропривода оборудования




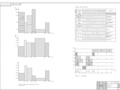
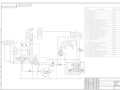
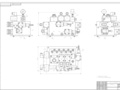
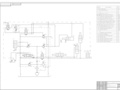
- Добавлен: 24.01.2023
- Размер: 744 KB
- Закачек: 3
Описание
Состав проекта
![]() |
![]() |
![]() ![]() ![]() |
![]() |
![]() ![]() ![]() |
![]() ![]() ![]() ![]() |
![]() ![]() ![]() |
![]() ![]() ![]() |
![]() ![]() ![]() |
![]() ![]() ![]() ![]() |
![]() ![]() ![]() |
![]() ![]() ![]() |
![]() ![]() ![]() |
![]() ![]() ![]() |
![]() ![]() ![]() |
![]() ![]() ![]() |
![]() ![]() ![]() |
![]() ![]() ![]() |
![]() ![]() ![]() |
![]() ![]() ![]() |
![]() ![]() ![]() |
![]() ![]() ![]() |
![]() ![]() ![]() |
![]() ![]() ![]() |
![]() ![]() ![]() ![]() |
![]() ![]() ![]() |
![]() ![]() ![]() |
![]() ![]() ![]() |
![]() ![]() ![]() |
![]() ![]() ![]() |
![]() ![]() ![]() |
![]() ![]() ![]() |
![]() ![]() ![]() ![]() |
![]() ![]() ![]() |
![]() |
![]() ![]() ![]() |
![]() ![]() ![]() |
![]() ![]() ![]() |
![]() ![]() ![]() |
![]() ![]() ![]() |
![]() ![]() ![]() |
![]() ![]() ![]() |
![]() ![]() ![]() |
Дополнительная информация
13 Охрана труда.doc
Охрана труда представляет собой систему правовых социально-экономических организационных технических санитарно-гигиенических и лечебно-профилактических мероприятий и средств по обеспечению безопасности и сохранению здоровья и работоспособности человека в процессе труда. [4]
Правовой основой организации работы по охране труда в республике является Конституция Республики Беларусь (ст. 41 45 46) которая гарантирует права граждан на здоровье и безопасные условия труда право на отдых охрану здоровья и право на благоприятную окружающую среду.
Положение Конституции конкретизированы в Трудовом кодексе Республики Беларусь а также в постановлениях приказах распоряжениях государственных органов министерств и ведомств.
Для обеспечения охраны труда существуют также Закон РБ «Об основах государственного социального страхования» Закон РБ «О санитарно-эпидемическом благополучии населения» от 23.11.1993 г. №2583-XII (в редакции Закона от 23.05.2000 г. №397-З с изм. и доп. от 29.06.2003 г. №217-З) Закон РБ «Об оценке соответствия требованиям технических нормативных правовых актов в области технического нормирования и стандартизации» от 05.01.2004 г. №269-З Закон РБ «О техническом нормировании и стандартизации» от 05.01.2004 г. №262-З Закон РБ «О пожарной безопасности» от 15.06.1993 г. Закон РБ «О промышленной безопасности опасных производственных объектов» от 10.01.2000 г. Закон о коллективных договорах и соглашениях.
По сфере действия все нормы и правила по охране труда подразделяются на единые и отраслевые.
Единые нормы и правила закрепляют одинаковые для всех отраслей хозяйства требования охраны труда. К ним относятся Строительные нормы и правила (СНиП) Санитарные правила и нормы (СанПиН) Правила устройства электроустановок (ПУЭ) Нормы радиационной безопасности (НРБ) и др.
Отраслевые нормы и правила действуют в отдельной отрасли хозяйства и содержат требования по охране труда специфические только для данной отрасли.
К должностным лицам по охране труда можно отнести руководителя главного инженера главного механика главного энергетика других главных специалистов руководителей структурных подразделений мастеров.
Главный инженер руководит разработкой и осуществлением планов работы по охране труда организует исполнение указаний вышестоящих органов проверяет состояние техники безопасности и санитарно-гигиенических условий труда в цехах и структурных подразделениях принимает оперативные меры по устранению выявленных недостатков. В его обязанности входят также организация разработки и утверждение инструкций по охране труда для всех профессий работников и выполняемых работ осуществление пропаганды охраны труда и обеспечение работников инструкциями и правилами по охране труда.
Главный технолог предприятия обеспечивает разработку и внедрение рациональных и безопасных технологических процессов приспособлений инструмента а также соблюдение технологических инструкций.
Главный конструктор обеспечивает разработку безопасных конструкций изготовляемых предприятием станков машин оборудования приспособлений установок и другой продукции.
Главный механик и главный энергетик предприятия обеспечивают своевременное проведение технического обслуживания и ремонтов оборудования грузоподъемных машин и механизмов паровых и водогрейных котлов аппаратов и устройств работающих под давлением компрессорных установок электротехнических установок и устройств а также вентиляционных и отопительных систему.
Служба эксплуатации зданий и ее персонал осуществляют технический надзор за безопасным состоянием производственных зданий и сооружений.
Мастер организовывает и создает безопасные условия труда на рабочих местах следит за состоянием и правильной эксплуатацией оборудования приспособлений ограждений средств сигнализации и автоматики.
Мастер проводит инструктаж по охране труда на рабочем месте принимает участие в обучении рабочих по охране труда ведет журналы регистрации инструктажей на рабочем месте.
О происшедших несчастных случаях мастер немедленно докладывает начальнику цеха обеспечивает участок средствами наглядной агитации и пропаганды охраны труда (инструкции памятки плакаты).
Согласно ГОСТ 12.0.004—90 проводятся следующие виды инструктажей: вводный первичный на рабочем месте повторный внеплановый целевой.
Вводный инструктаж по охране труда проводится при поступлении на постоянную или временную работу службой охраны труда предприятия. Этот инструктаж обязаны пройти все вновь поступающие на предприятие а также командированные учащиеся прибывшие на практику.
Вводный инструктаж проводит инженер по охране труда или специалист организации на которого возложены эти обязанности.
Первичный инструктаж на рабочем месте проводится для всех вновь принятых на предприятие перед первым допуском к работе (в том числе командированные учащиеся прибывшие на практику) а также при переводе из одного подразделения в другое.
Все рабочие после первичного инструктажа на рабочем месте должны пройти в течение 2—14 смен стажировку под руководством лица назначенного приказом (распоряжением) по цеху (участку и т.п.). Рабочие допускаются к самостоятельной работе после стажировки проверки знаний и приобретенных навыков безопасных способов работы.
Повторный инструктаж проводится не реже одного раза в полугодие а для работ повышенной опасности — раз в квартал по программе первичного инструктажа на рабочем месте или по инструкциям по охране труда для профессий и видов работ.
Внеплановый инструктаж проводится:
– при изменении технологических процессов замене или модернизации оборудования и других факторов влияющих на охрану труда;
– при перерывах в работе на 60 календарных дней а для работ к которым предъявляются дополнительные (повышенные) требования безопасности более чем на 30 дней;
– при нарушениях работниками нормативных технических правовых актов по охране труда которые привели или могли привести к аварии несчастному случаю на производстве и другим тяжелым последствиям;
– при перерывах в работе по профессии (в должности) более 6 месяцев;
– при поступлении информационных материалов об авариях и несчастных случаях происшедших в однопрофильных организациях;
– по требованию органов надзора.
Целевой инструктаж проводят:
– при выполнении разовых работ не связанных с прямыми обязанностями по специальности (погрузочно-разгрузочные работы уборка территории и т.п.);
– при ликвидации последствий аварий стихийных бедствий и катастроф;
– при производстве работ на которые оформляется наряд-допуск; проведении экскурсий в организации; организации массовых мероприятий с учащимися (экскурсии походы спортивные соревнования и др.).
2 Санитарно-гигиенические требования
В производственных условиях вредные вещества поступают в организм человека в основном с вдыхаемым воздухом. Токсичность вредных веществ определяется прежде всего их концентрацией в воздухе рабочей зоны. Устанавливаются предельно допустимые значения — ПДК мгм3 на содержание вредных веществ в воздухе рабочей зоны. Эти значения определены в ГОСТ 12.1.005—88 и СанПиН 11—19—94.
Для того чтобы человек испытывал состояние комфорта необходимо обеспечить благоприятный микроклимат производственного помещения в соответствии с ГОСТ 12.1.005-88 нормируются значения приведенные в таблице 16.
Таблица 16 – Нормируемые значения
Все выше перечисленные параметры обеспечиваются вентиляцией и системой отопления.
Вентиляцию производственных помещений разделяют на основную аварийную естественную искусственную смешанную приточную местную и др. но любая вентиляция должна удалять из помещения загрязнения и подавать в рабочую зону свежий чистый воздух обеспечивая требуемый в соответствии с санитарно-гигиеническими требованиями микроклимат.
Не мало важным является и освещение рабочих мест которое тоже подразделяется на естественное искусственное местное аварийное эвакуационное дежурное и тд. Нормирование естественного освещения осуществляется с помощью коэффициента естественной освещенности КЕО % минимальная величина которого определяется разрядом работ. При недостатке освещенности от естественного света используют искусственное освещение создаваемое электрическими источниками.
Согласно СНБ 2.04.05-98 «Естественное и искусственное освещение. Нормы проектирования» для ремонтных работ гидросистемы определим разряд зрительных работ значения сведем в таблицу 17.
Таблица 17 – Нормируемые значения освещения
Разряд зрительных работ
Подразряд зрительных работ
Искусственное освещение освещенность лк
Естественное освещение КЕО %
При работе человек сталкивается с еще одним вредным фактором – шум.
Источниками шума являются электрические машины и оборудование стационарные и нестационарные процессы в жидкостях соударения деталей трения и тд. Шум до 30 45 дБ привычен для человека и не беспокоит его.
В соответствии с СанПиН 2.2.42.1.8.10—32—2002 предельно допустимые уровни шума нормируются по двум категориям норм шума: ПДУ шума на рабочих местах и ПДУ шума в помещениях жилых общественных зданий и на территории жилой застройки.
Классификация средств и методов защиты от шума приведена в ГОСТ 12.1.029-80 ССБТ «Средства и методы защиты от шума. Классификация» СНиП II-12-77 «Защита от шума» которые предусматривают защиту от шума путем установки звукопоглощающих конструкций и экранов применение глушителей создание шумозащитных зон и т.д.
Вибрация не должна превышать значений установленных ГОСТ 12.1.012-90 «ССБТ. Вибрационная безопасность» и СН 9-89 РБ 98 «Вибрация производственная общая. Предельно допустимые уровни».
3 Техника безопасности
В соответствии с ГОСТ 12.0.003—2003 все опасные и вредные производственные факторы (ОВПФ) по природе действия подразделяются на физические химические биологические и психофизиологические.
Для обеспечения защиты машин механизмов инструмента используют:
– оградительные устройства (постоянные временные ручные и т.д.) предназначенные для предотвращения случайного попадания человека в опасную зону. Они применяются для изоляции движущихся частей машин зон обработки станков штампов прессов и т.д.;
– стационарные ограждения обычно предпочтительнее чем другие виды ограждений поскольку они отличаются прочностью и простотой конструкции.
– устройства аварийного отключения. К ним относятся: органы ручного аварийного выключения штанги чувствительные к изменению давления; устройства аварийного отключения с отключающим стержнем; провода или кабели аварийного отключения.
4 Электробезопасность
В отношении опасности поражения людей электрическим током помещения классифицируют как помещения с повышенной опасностью особо опасные помещения помещения без повышенной опасности.
Проходя через организм человека электрический ток оказывает следующие воздействия: термическое (нагревает ткани кровеносные сосуды нервные волокна и внутренние органы вплоть до ожогов отдельных участков тела); электролитическое (разлагает кровь плазму); биологическое (раздражает и возбуждает живые ткани организма нарушает внутренние биологические процессы).
Для защиты от поражения током предусмотрены организационно-технические мероприятия включающие в себя:
– подготовку (обучение) повышение квалификации и проверку зананий работников по вопросам охраны труда;
– инструктаж по безопасным методам работы на рабочих местах;
– допуск к работам по нарядам;
– назначение лиц ответственных за безопасность работ;
– включение в проект производства работ решений по созданию условий для безопасного и безвредного производства работ по санитарно-гигиеническому обслуживанию работающих и освещению рабочих мест;
– внедрение передового опыта работы по предупреждению производственного травматизма;
– организацию кабинетов по технике безопасности.
5 Пожарная безопасность
Обеспечение пожарной безопасности осуществляется в соответствии с Законом РБ «О пожарной безопасности».
Пожарная безопасность обеспечивается совместной работой всех противопожарных средств а также рядом мероприятий проводимых для обеспечения пожарной безопасности.
Огнестойкость здания и сооружения подразделяется на восемь степеней огнестойкости: I II III IIIa IIIб IV IVa и V. С возрастанием номера категории уменьшается предел огнестойкости конструкции.
Производственные здания и склады по взрывной взрывопожарной и пожарной опасности подразделяются на следующие категории: А Б В1-В4 Г1 Г2 Д (НПБ 5-2000 «Нормы пожарной безопасности Республики Беларусь. Категорирование помещений зданий и наружных установок по взрывопожарной и пожарной безопасности»; СНиП 2.09.02-85* «Производственные здания»; СНБ 2.02.03-03 «Ограничение распространения пожара в зданиях и сооружениях. Объемнопланировачные и конструктивные решения»).
Пожар может возникнуть вследствие курения в запрещенных местах аварии отсутствия надежных устройств молниезащиты неисправности электрооборудования электросетей электроаппаратуры и неправильной их эксплуатации нарушения правил пожарной безопасности.
К средствам пожаротушения относятся различного рода огнетушители автоматические спринклеры и дренчерные установки ящики с песком пожарные краны и т.д.
Эвакуация людей при пожаре производится через эвакуационные (пожарные) выходы.
8 Расчет основных параметров гидропривода. 8.3 Определение КПД.doc
КПД гидравлической системы гидропривода определяется как отношение полезной работы к затраченной:
гс = ΣΔPj Qpj tj [Pк Qн tц]; (13)
где ΔPj Qpj tj – полезный перепад давления рабочий расход рабочей жидкости время работы исполнительного органа в течение цикла; Pк – давление настройки предохранительного клапана; Qн – подача насоса; tц – время цикла.
Разжим подъем материала и подвод упора:
гс1=(1960012+1967018+0764005+21110017)(3221018)=032
гс2=29126007(3221007)=055
гс3=(2791008+21108015)(3221015)=053
Ускоренная подача и отвод упора:
гс4=(0824501+270890017)(322101)=030
гс5=324303(322103)=020
Отвод бабки пильного диска:
гс6=2712601(322101)=051
Рассчитываем общий КПД гидросистемы:
гс=((1960012+1967018+0764005+21110017)+(29126007)+(2791 ·008+21108015)+(0824501+270890017)+(324303)+(27126·01)) (322109)=035
Таблицы и графики.dwg

подъем материала и подвод упора
Ускоренная подача и отвод упора
Рисунок 2 - Циклограмма
Таблица 1-Рабочая таблица
Рисунок 1-Графические зависимости Q
ΔР и от времени цикла
3 Применяемая рабочая жидкость. 3.2 Заменители рабочей жидкости.doc
В некоторых случаях не всегда возможно применение требуемых для данного гидропривода масел поэтому можно воспользоваться их заменителями. Заменителями называются масла которые имеют схожие свойства с применяемыми маслами и их применение не может привести к ухудшению работы гидропривода. К заменителям отечественного производства относятся такие масла как «Турбинное 22Б» Т22 или «ВНИИ НП-412». Для гидросистем экспортируемого оборудования возможно применение масел иностранных фирм: Shell Tellus Oil 27 Shell Turbo Oil 27 Shell Turbo Oil 29 также помимо приведенных сортов могут быть использованы взаимозаменяемые сорта других фирм например: ESSO Mobil Oil British Petroleum (BP) и др.
6 Составление циклограммы работы гидропривода.doc
Для того чтобы быстро и наиболее точно определить последовательность действий работающих органов системы составляем циклограмму представляющую собой цепочку событий которая должна быть реализована гидросистемой. Циклограмму работы данного автомата на автоматическом цикле представим графически как показано на рисунке 1.
Рисунок 1 – Циклограмма работы гидропривода
При включении автоматического цикла срабатывают цилиндры вертикального Ц5 и горизонтального Ц4 зажима цилиндр подъема материала и цилиндр подачи упора; происходит разжим материала его подъем и подвод упора. Далее срабатывает гидромотор Г который подает материал после которого происходит зажим материала и опускание цилиндра Ц6. После того как материал будет зажат осуществляется отвод упора и быстрый подвод диска. За быстрым подводом следует рабочая подача и отвод диска. Цикл повторяется.
Составление рабочих таблиц
1 Описание процесса управления
Процесс управления работой гидропривода автомата представлен в рабочей таблице 3 согласно гидросхеме ДП 2-360107 02 ГС.
Такт 0 – Исходное положение. Кнопка управления находится в свободном положении без сигнала на обмотках электромагнитов 1Э и 2Э распределителей Р1 и Р2 соответственно нет тока поэтому они находятся в крайних правых положениях распределитель Р4 находится в левом положение сигналов на выключателях нет цилиндры находятся в состоянии покоя а клапаны давления закрыты.
Такт 1 – Разжим подъем материала и подвод упора. С нажатием кнопки управления на электромагнит 2Э поступает сигнал и распределитель Р2 занимает левое положение что приводит в движение гидроцилиндры Ц3 Ц4 Ц5 Ц6. Бабка пильного диска нажимает на выключатель 3пв.
Такт 2 – Подача материала. Цилиндр Ц5 опустившись вниз нажимает на выключатель 5пв который подает сигнал на обмотку 4Э распределителя Р3 и он занимает крайнее левое положение. Гидромотор начинает вращаться против часовой стрелки и падает материал вперед.
Такт 3 – Зажим материала. После того как заготовка дойдет до упора она нажмет на выключатель 4пв который пошлет сигнал на электромагнит 1Э распределителя Р1 и он займет левое положение отключится электромагнит 2Э и распределитель Р2 займет правое положения. Гидромотор остановится цилиндры Ц5 и Ц4 зажмут заготовку и в следующем такте участвовать не будут цилиндр подъема материала Ц6 опустится вниз.
Такт 4 – Ускоренная подача и отвод упора. По достижению необходимого давления клапан давления КД2 откроется и цилиндр бабки пильного диска Ц2 начнет движение влево (шток будет выдвигаться) цилиндр упора Ц3 опустится вниз. Клапан давления КД3 будет нести функцию предохранительного в данный момент давление в системе будет превышать давление настройки клапана и он откроется.
Такт 5 – Рабочая подача. Отвод упора завершен и поршень цилиндра Ц3 без движения. Продолжая двигаться бабка пильного диска наезжает на управление распределителем Р4 и он занимает правую позицию. Рабочая жидкость пойдет через регулятор потока и уже в меньшем объеме. Часть рабочей жидкости продолжает сливаться через клапан давления КД3.
Такт 6 – Отвод бабки. В конце обработки бабка пильного диска нажимает на выключатель 2пв который отключает электромагнит 1Э и распределитель Р1 занимает правую позицию. Шток цилиндра бабки пильного диска Ц2 начнет вдвигаться. В начале цикла распределитель Р4 будет находиться в правом положении но когда пильный диск выйдет из заготовки он переключится в левую что сохраняет инструмент и обеспечивает безопасную работу.
Такт 7 – Повтор цикла. Данный такт включается в рабочую таблицу ввиду того что если остановку произвести после такта 6 – деталь останется зажатой. Такт аналогичен такту 1 только электромагнит 2Э распределителя Р2 включается от выключателя 3пв. Выключатель падает сигнал на электромагнит когда бабка пильного диска завершит обратный ход.
Такт 8 – Остановка. Аналогично исходному положению.
Определенные состояния элементов гидропривода в рабочей таблице записаны следующим образом:
Кнопка управления (КУ):
– без сигнала (клавиша в свободном положении)
– импульсный сигнал (после нажатия и освобождения клавиши данный сигнал сохраняется)
– сигнал отсутствует
– сигнал присутствует
Распределители Р1 и Р2:
+1 – правое положение
-1 – левое положение
для трехпозиционного распределителя Р3 среднее положение – 0
для распределителя Р4 изменение положения в течение такта – +1-1
+1 – движение штока из цилиндра
-1 – движение штока в цилиндр
+1 – движение по часовой стрелке
-1 – движение против часовой стрелки
Р1(+1)Р2(+1) Р3(0)Р4(-1) КУ(0)Ц1(0) Ц2(0)Ц3(0) Ц4(0)Ц5(0) Ц6(0)Г(0) 1пв(0)2пв(0) 3пв(0)4пв(0) 5пв(0)КД2(0) КД3(0)
Разжим подъем материала и подвод упора
КУ(10)Ц3(+1)Ц4(-1)Ц5(-1) Ц6(+1) Р2(-1)
Ц3(0)Ц4(0) Ц5(0)Ц6(0) Г(-1)Р3(-1) 5пв(1)
Ц4(+1)Ц5(+1) Ц6(-1)Г(0) Р1(-1) Р2(+1) Р3(0)5пв(0)
Ускоренная подача и отвод упора
Ц2(+1)Ц3(-1) Ц4(0)Ц5(0) Ц6(0)4пв(0) КД2(1)КД3(1)
Ц2(-1)Р1(+1) 2пв(1) Р4(+1-1) КД3(0)
Ц2(0)Ц3(+1)Ц4(-1) Ц5(-1) Ц6(+1) Р2(-1) Р4(-1) 2пв(0) 3пв(1)
Таблица 3 – Процесс управления гидроприводом
7 Составление рабочих таблиц. 7.1 Описание процесса управления.doc
1 Описание процесса управления
Процесс управления работой гидропривода автомата представлен в рабочей таблице 3 согласно гидросхеме ДП 2-360107 00.02 ГС.
Такт 0 – Исходное положение. Кнопка управления находится в свободном положении без сигнала на обмотках электромагнитов 1Э и 2Э распределителей Р1 и Р2 соответственно нет тока поэтому они находятся в крайних правых положениях распределитель Р4 находится в левом положение сигналов на выключателях нет цилиндры находятся в состоянии покоя а клапаны давления закрыты.
Такт 1 – Разжим подъем материала и подвод упора. С нажатием кнопки управления на электромагнит 2Э поступает сигнал и распределитель Р2 занимает левое положение что приводит в движение гидроцилиндры Ц3 Ц4 Ц5 Ц6. Бабка пильного диска нажимает на выключатель 3пв.
Такт 2 – Подача материала. Цилиндр Ц5 опустившись вниз нажимает на выключатель 5пв который подает сигнал на обмотку 4Э распределителя Р3 и он занимает крайнее левое положение. Гидромотор начинает вращаться против часовой стрелки и падает материал вперед.
Такт 3 – Зажим материала. После того как заготовка дойдет до упора она нажмет на выключатель 4пв который пошлет сигнал на электромагнит 1Э распределителя Р1 и он займет левое положение отключится электромагнит 2Э и распределитель Р2 займет правое положения. Гидромотор остановится цилиндры Ц5 и Ц4 зажмут заготовку и в следующем такте участвовать не будут цилиндр подъема материала Ц6 опустится вниз.
Такт 4 – Ускоренная подача и отвод упора. По достижению необходимого давления клапан давления КД2 откроется и цилиндр бабки пильного диска Ц2 начнет движение влево (шток будет выдвигаться) цилиндр упора Ц3 опустится вниз. Клапан давления КД3 будет нести функцию предохранительного в данный момент давление в системе будет превышать давление настройки клапана и он откроется.
Такт 5 – Рабочая подача. Отвод упора завершен и поршень цилиндра Ц3 без движения. Продолжая двигаться бабка пильного диска наезжает на управление распределителем Р4 и он занимает правую позицию. Рабочая жидкость пойдет через регулятор потока и уже в меньшем объеме. Часть рабочей жидкости продолжает сливаться через клапан давления КД3.
Такт 6 – Отвод бабки. В конце обработки бабка пильного диска нажимает на выключатель 2пв который отключает электромагнит 1Э и распределитель Р1 занимает правую позицию. Шток цилиндра бабки пильного диска Ц2 начнет вдвигаться. В начале цикла распределитель Р4 будет находиться в правом положении но когда пильный диск выйдет из заготовки он переключится в левую что сохраняет инструмент и обеспечивает безопасную работу.
Такт 7 – Повтор цикла. Данный такт включается в рабочую таблицу ввиду того что если остановку произвести после такта 6 – деталь останется зажатой. Такт аналогичен такту 1 только электромагнит 2Э распределителя Р2 включается от выключателя 3пв. Выключатель падает сигнал на электромагнит когда бабка пильного диска завершит обратный ход.
Такт 8 – Остановка. Аналогично исходному положению.
Определенные состояния элементов гидропривода в рабочей таблице записаны следующим образом:
Кнопка управления (КУ):
– без сигнала (клавиша в свободном положении)
– импульсный сигнал (после нажатия и освобождения клавиши данный сигнал сохраняется)
– сигнал отсутствует
– сигнал присутствует
Распределители Р1 и Р2:
+1 – правое положение
-1 – левое положение
для трехпозиционного распределителя Р3 среднее положение – 0
для распределителя Р4 изменение положения в течение такта – +1-1
+1 – движение штока из цилиндра
-1 – движение штока в цилиндр
+1 – движение по часовой стрелке
-1 – движение против часовой стрелки
Р1(+1)Р2(+1) Р3(0)Р4(-1) КУ(0)Ц1(0) Ц2(0)Ц3(0) Ц4(0)Ц5(0) Ц6(0)Г(0) 1пв(0)2пв(0) 3пв(0)4пв(0) 5пв(0)КД2(0) КД3(0)
Разжим подъем материала и подвод упора
КУ(10)Ц3(+1)Ц4(-1)Ц5(-1) Ц6(+1) Р2(-1)
Ц3(0)Ц4(0) Ц5(0)Ц6(0) Г(-1)Р3(-1) 5пв(1)
Ц4(+1)Ц5(+1) Ц6(-1)Г(0) Р1(-1) Р2(+1) Р3(0)5пв(0)
Ускоренная подача и отвод упора
Ц2(+1)Ц3(-1) Ц4(0)Ц5(0) Ц6(0)4пв(0) КД2(1)КД3(1)
Ц2(-1)Р1(+1) 2пв(1) Р4(+1-1) КД3(0)
Ц2(0)Ц3(+1)Ц4(-1) Ц5(-1) Ц6(+1) Р2(-1) Р4(-1) 2пв(0) 3пв(1)
Таблица 3 – Процесс управления гидроприводом
Гидросхема до модернизации, с рамкой на А2.dwg

Гидроклапан давления БГ54-22
Гидроклапан редукционный Г57-12
Манометр МТ60* 60c ГОСТ8625-65
Насос лопастной Г12-32
Гидрораспределитель 54БПГ73-11
Гидрораспределитель 44БПГ73-11
Гидрораспределитель Г74-22
Гидромотор подачи материала
Цилиндр подачи бабки пильного диска
Цилиндр горизонтального зажима
Цилиндр вертикального зажима
Цилиндр подъема материала
Гидрораспределитель 54БПГ73-24
Гидроклапан давления ПГ54-22
Содержание.doc
Назначение и анализ гидросистемы входящей в состав оборудования 7
Применяемая рабочая жидкость 8
1 Характеристика рабочей жидкости 8
2 Заменители рабочей жидкости 9
Обоснование модернизации10
Техническое обеспечение модернизации11
Составление циклограммы работы гидропривода12
Составление рабочих таблиц13
1 Описание процесса управления13
2 Описание направления потоков рабочей жидкости17
Расчет основных параметров гидропривода20
1 Определение требуемых давлений20
2 Определение требуемых расходов25
3 Определение коэффициента полезного действия (КПД)28
4 Обоснование выбора насоса29
Содержание технического обслуживания гидропривода оборудования30
Причины возможных отказов гидросистемы и методы их устранения32
Запуск гидропривода в эксплуатацию после модернизации34
Экономическая часть35
1 Расчет режима работы и фондов времени для оборудования и рабочих35
2 Расчет трудоемкости работ до проекта38
3 Расчет трудоемкости работ по проекту41
4 Расчет заработной платы до проекта43
Заключение.doc
3 Применяемая рабочая жидкость. 3.1 Характеристикарабочей жидкости.doc
1 Характеристика рабочей жидкости
Основная функция рабочих жидкостей для гидравлических систем – передача механической энергии от ее источника к месту использования с изменением значения или направления приложенной силы. Поэтому для нормального функционирования гидроприводов необходимо правильно подобранное масло которое должно обладать хорошими смазочными свойствами инертностью по отношению к применяемым для гидропривода материалам малой способностью к растворению воздуха малой токсичностью. Масло должно иметь оптимальную вязкость с незначительным ее изменением в широком диапазоне температур большой модуль упругости сопротивляемость к вспениванию высокую температуру кипения и малую плотность. Также применяемая рабочая жидкость должна быть безопасной в пожарном отношении т. е. негорючей иметь хорошие диэлектрические свойства и самое главное – длительное время сохранять свои свойства в условиях хранения и эксплуатации. В данном гидроприводе используется масло «Турбинное 22С» или «ВНИИНП-403» характеристика применяемых масел представлена в таблице 2.
Таблица 2 – Характеристика масел
Кинематическая вязкость при температуре +40 0С мм2с
Индекс вязкости не менее
Плотность ρ при 20 0С кгм3
Кислотное число мг КОНг не более
вспышки в открытом тигле не ниже
2 Заменители рабочей жидкости
В некоторых случаях не всегда возможно применение требуемых для данного гидропривода масел поэтому можно воспользоваться их заменителями. Заменителями называются масла которые имеют схожие свойства с применяемыми маслами и их применение не может привести к ухудшению работы гидропривода. К заменителям отечественного производства относятся такие масла как «Турбинное 22Б» Т22 или «ВНИИ НП-412». Для гидросистем экспортируемого оборудования возможно применение масел иностранных фирм: Shell Tellus Oil 27 Shell Turbo Oil 27 Shell Turbo Oil 29 также помимо приведенных сортов могут быть использованы взаимозаменяемые сорта других фирм например: ESSO Mobil Oil British Petroleum (BP) и др.
Содержание_продолжение.doc
6 Расчет расходов на содержание и эксплуатацию оборудования до проекта 46
7 Расчет расходов на содержание и эксплуатацию оборудования по проекту 50
8 Экономическое обоснование целесообразности модернизации оборудования 52
1 Правовые и организационные вопросы охраны труда 53
2 Санитарно-гигиенические требования 56
3 Техника безопасности 58
4 Электробезопасность 59
5 Пожарная безопасность 60
Список литературы 62
Используемые ГОСТы 63
8 Расчет основных параметров гидропривода. 8.4 Обоснование выбора насоса.doc
Выбранный насос должен иметь подачу не меньше наибольшей подачи Qн=202 лмин и развивать давление больше чем то значение на которое настраивается предохранительный клапан Pк=32 МПа.
Исходя из этого выбираем пластинчатый насос модели Г12-32М характеристика насоса представлена в таблице 4.
Таблица 4 – Характеристика насоса
Подача не менее лмин
Давление на выходе МПа:
Частота вращения обмин:
Номинальная мощность кВт
КПД при номинальном режиме работы:
Ресурс при номинальном режиме работы ч не менее
8 Расчет основных параметров гидропривода. 8.2 Определение требуемых расходов.doc
Исходной формулой для расчета расхода рабочей жидкости в полости силового гидроцилиндра возвратно-поступательного движения является:
где Q – расход рабочей жидкости в полости цилиндра лмин; S – рабочая площадь в полости цилиндра мм2; v – скорость движения поршня силового цилиндра ммин.
Скорость перемещения штока гидроцилиндра можно определить по формуле:
где t – время прохождения рабочего хода мин.
Цилиндр подачи бабки пильного диска:
Vраб.ход=01503=05 ммин
Vотвод=03501=35 ммин
Цилиндр подачи упора:
Vотвод=Vподвод=0012 0017=07 ммин
Цилиндр горизонтального зажима:
Vразжим=015012=125 ммин
Vзажим=015008 =19 ммин
Цилиндр вертикального зажима:
Vразжим =025018=14 ммин
Vзажим=025015=17 ммин
Цилиндр подъема материала:
Vподъем=005005=1 ммин
Vопуск.=00502=025 ммин
Определяем расход рабочей жидкости для напорных полостей гидроцилиндров.
Qподвод=122656·21000=245 лмин
Qраб.ход=86546·051000=43 лмин
Qотвод=3611·351000=126 лмин
Qподвод=15896·071000=11 лмин
Qотвод=12756·071000=089 лмин
Qразжим=47689·1251000=60 лмин
Qзажим=47689·191000=91 лмин
Qразжим=47689·141000=67 лмин
Qзажим=63585·171000=108 лмин
Qподъем=63585·11000=64 лмин
Расход рабочей жидкости необходимый для сообщения выходному валу гидромотора соответствующей частоты вращения определяется по формуле:
где Q – расход жидкости для обеспечения требуемой частоты вращения выходного вала лмин; q – рабочий объем гидромотора см3; n – частота вращения выходного вала мин-1.
Q = 18 · 700103 = 126 лмин
Определяем необходимую наибольшую подачу рабочей жидкости:
где Qн– наибольшая подача рабочей жидкости; Qi – сумма подач рабочей жидкости для исполнительных гидравлических органов при сочетании их работы требующей наибольшей подачи насоса.
Qн=11+ 6 + 67 + 64= 202 лмин
Литература.doc
Методическое пособие по курсовому и дипломному проектированию специальности 2-360107 “Гидропневмосистемы мобильных и технологических машин”. МГАК. Минск 2008.
Методическое пособие для выполнения экономической части дипломного проекта (при модернизации элементов гидросистемы оборудования) специальности 2-360107 “Гидропневмосистемы мобильных и технологических машин”.
Усов А.А. Свешников В.К. «Станочные гидроприводы» Москва “Машиностроение” 1982г.
К.М. Великанов «Расчеты экономической эффективности новой техники». Справочник. «Машиностроение» 1989 г.
8 Расчет основных параметров гидропривода. 8.1 Определение требуемых давлений.doc
1 Определение требуемых давлений
Исходной формулой для расчетов параметров гидроцилиндра является выражение силы давления рабочей жидкости на поршень в полости цилиндра
где F – сила давления рабочей жидкости Н; P – давление рабочей жидкости МПа; S – рабочая площадь поршня мм2;
Если исполнительным двигателем является одноштоковый цилиндр то рабочие площади полостей напора и слива не равны.
Площади рабочей поверхности поршня определяется по формуле:
Sн= Sс= (D2 – d2) 4 (2)
где S – площадь рабочей поверхности поршня мм2; D – диаметр поршня;
d – диаметр штока мм;
Если исполнительным двигателем является двухштоковый цилиндр и рабочие площади полостей напора и слива равны т.е. SH = Sс = S то
Sн= Sс= (D2 – d2) 4 (3)
Рассчитаем рабочие площади бесштоковых и штоковых полостей одноштоковых цилиндров.
Цилиндр включения гидромуфты Ц1:
Sб= 314·6524=33166 мм2
Sш=314(652-322)4=25128 мм2
Цилиндр подачи бабки пильного диска Ц2:
Sб= 314·12524=122656 мм2
Sш=314(1252-1052)4=3611 мм2
Цилиндр подачи упора Ц3:
Sб= 314·4524=15896 мм2
Sш=314(452-202)4=12756 мм2
Цилиндр вертикального зажима Ц5:
Sб= 314·9024=63585 мм2
Sш=314(902-452)4=47689 мм2
Цилиндр подъема материала Ц6:
Sш=314(902-752)4=19429 мм2
Рассчитаем рабочие площади полостей напора и слива у двухштокового цилиндра горизонтального зажима Ц4:
Sн= Sс=314(902-452)4=47689 мм2
Определим давления при работе гидроцилиндров в соответствии с циклограммой. Так как работа гидропривода в норме то расчетом давления у цилиндра гидромуфты можно пренебречь.
Из исходной формулы (1) можно выразить давление в полости гидроцилиндра:
Цилиндр подачи бабки пильного диска:
Рподвод=9000122656=07 МПа
Рраб.ход=2500086546=29 МПа
Ротвод=90003611=25 МПа
Цилиндр подачи упора:
Рподвод=300015896 =19 МПа
Ротвод=300012756 =24 МПа
Цилиндр горизонтального зажима:
Рзажим=1200047689 =25 МПа
Рразжим=800047689 =17 МПа
Цилиндр вертикального зажима:
Рзажим=1200063585 =19 МПа
Цилиндр подъема материала:
Рподъем=400063585 =06 МПа
Ропуск.=300012756 =24 МПа
Требуемый полезный перепад давления в гидроцилиндре можно найти по формуле:
где Р – давление в полости гидроцилиндра МПа; M – механический КПД гидроцилиндра M=085 095 [ 1].
ΔРподвод=0709=08 МПа
ΔРраб.ход=2909=32 МПа
ΔРподвод=1909=21 МПа
ΔРразжим=1709=19 МПа
ΔРподъем=0609=07 МПа
ΔРопуск.= 2409=27 МПа
Исходной формулой для расчета параметров гидромотора является выражение крутящего момента на его выходном валу:
М = q Δp м ( 2 ) (6)
где М – крутящий момент на выходном валу гидромотора Н·м; q – рабочий объем гидромотора см3; Δp – полезный перепад давления на гидромоторе МПа; м – механический КПД гидромотора м=09 [ 1].
При известном крутящем моменте на выходном валу гидромотора и его рабочем объеме можно определить полезный перепад давления:
ΔР= 2 · 75 · 314 (09 · 18) =29 МПа
По расчетному давлению настраивается с запасом предохранительный клапан т.е.
Рк = (110 115)Рр (8)
1 Назначение и техническая характеристика оборудования 2.doc
Автомат отрезной круглопильный модели 8В66А предназначен для разрезания сегментными пильными дисками черных металлов с временным сопровождением до 6В=120 кгмм2 круглого профиля на автоматическом цикле квадратного швеллерного и двутаврового профилей на простом цикле. Разрезка производится под углом 900 к оси разрезаемой заготовки.
Автомат предназначен для применения в заготовительных цехах машиностроительных заводов при крупносерийном и массовом производстве.
Техническая характеристика автомата представлена в таблице 1.
Таблица 1 – Техническая характеристика автомата
Габариты (длина×ширина×высота) мм
Наибольший диаметр пилы мм
Длина отрезаемой по упору заготовки мм
на автоматическом цикле
Наибольшее перемещение бабки пильного диска мм
Вертикальный ход зажима мм
Горизонтальный ход зажима мм
Пределы величин подач мммин
11 Запуск гидропривода в эксплуатацию поле модернизации.doc
После установки на фундаменте тщательно необходимо очистить станок от скопившейся пыли и грязи и выполнить его смазку согласно схеме смазки.
Перед запуском станка необходимо:
- Заполнить маслобак маслом соответствующей марки до требуемого уровня. Перед заливкой рабочей жидкости рекомендуется промыть бак чистым маслом для удаления загрязнений.
- Убедиться в правильности монтажа всей системы проверить наличие в гидросистеме контрольно-измерительной аппаратуры.
- Проверить соостность установленного вала насоса и приводного двигателя обеспечить жесткую относительно гильзы фиксацию штока гидоцилиндра а так же прочно закрепить цилиндр. При этом должен быть обеспечен удобный доступ к цилиндру для его техобслуживания и наблюдения за его работой.
- Настроить предохранительный клапан на нулевое давление.
- Открыть все воздухоспускные устройства для удаления воздуха из гидросистемы.
- Кратковременным включением электродвигателей удостовериться в правильности вращения и всасывании рабочей жидкости. Кратковременное включение продолжается до полного заполнения системы рабочей жидкостью.
- Установить минимальное давление в системе и привести гидропривод в действие на холостых режимах следя за удалением воздуха из системы.
- Закрыть воздухоспускные устройства и затянуть трубные соединения и сделать несколько рабочих циклов убедившись при этом что воздух из системы удален.
- Настроить на требуемое давление ПК.
- При обнаружении утечек – устранить их и весь пуск повторить сначала.
- Проверить уровень масла в баке и при необходимости произвести доливку.
7 Составление рабочих таблиц. 7.2 Описание направления потоков рабочей жидкости.doc
Движение рабочей жидкости происходит согласно тактам работы гидропривода и выглядит следующим образом:
Б Н 1 Ф 16 КО 17 Р2 4 Ц4Ц4 Ц6
Разжим подъем материала и подвод упора:
КД1 Ц1 8 КР КД2 Ц3Ц3 7 Р1
Б Н 1 Ф 16 КО 17 Р2 5 Ц4Ц4
Р3 18 Д Ц6 Ц5Ц5 4 Р2 13 Б
Аналогично такту «Исходное положение».
Ускоренная подача и отвод упора:
Б Н 1 Ф 16 КО 17 Р2 4 Ц4Ц4 Ц6
Р3 18 Д Ц5Ц5 5 Р2 13 Б
Аналогично такту «Разжим подъем материала и подвод упора».
Такт «Исходное положение». Рабочая жидкость из бака всасывается насосом Н и поступает в трубопровод 1 где разделяется на два потока. Один поток поступает в магистраль 15 далее в переключатель манометра ПМ и из него в магистраль 16 а второй поток походит через фильтр Ф и тоже попадает в магистраль 16 где соединяется со вторым потоком. Давление в системе не превышает давление настройки предохранительного клапана КД1 и поэтому слив через него не происходит. Через обратный клапан КО рабочая жидкость попадает в магистраль 17 и распределяется следующим образом:
а)через дроссель Д по трубопроводу 18 к распределителя Р3 который находясь в среднем положении не пропускает жидкость далее;
б)далее по трубопроводу 17 к клапану давления КД2 который закрыт и жидкость через него не идет и к редукционному клапану КР через который по трубопроводу 8 попадает в штоковую полость цилиндра Ц1;
в)через распределитель Р2 по трубопроводу 4 в бесштоковую полость цилиндра Ц5 и в левую полость цилиндра Ц4;
Из правой полости цилиндра Ц4 штоковой полости цилиндра Ц5 и бесштоковой полости цилиндра Ц6 жидкость по трубопроводу 5 через распределитель Р2 и трубопроводу 13 сливается в бак.
Такт «Разжим подъем материала и подвод упора». При включении электромагнита 2Э распределитель Р2 занимает левую позицию и жидкость из трубопровода 17 попадает в трубопровод 5 и далее в правую полость цилиндра Ц4 в штоковую полость цилиндра Ц5 и бесштоковую полость цилиндра Ц6 происходит разжим и подъем материала. Поступая в бесштоковую полость цилинадра Ц3 жидкость не вызывает его перемещения так как цилиндр уже отведен до упора.
4 Обоснование модернизации.doc
Модернизация автомата а в частности гидропривода производится для улучшения ремонтопригодности замены устаревшей гидроаппаратуры (в настоящее время промышленностью не выпускается) на современную новую и установки ее за пределы станка. Связи с чем изготавливается разделительная панель для последующей установки на ней гидроаппаратуры и выносится гидростанция за пределы станка. Вследствие этого уменьшится время затрачиваемое на монтаждемонтаж аппаратуры а значит и время простоя автомата. А также уменьшатся затраты на ремонт и обслуживание гидропривода.
Маршрутная карта (Приложение1).doc
ТУУ21.1-00191164-60-2003-350×240 Сталь 45 ГОСТ 1050-88
Код наименование операции
Обозначение документа
Код наименование оборудования
01 005 4285 Отрезная ИОТ№69
Г662 резчик 3 н 1 1 1 1
01 010 4261 Фрезерная ИОТ№67
Р12 фрезеров. 4 н 1 1 1 1
01 015 4133 Шлифовальная ИОТ№76
Д732 шлифов. 4 н 1 1 1 1
01 020 4223 Расточная ИОТ№68
21 сверлов. 4 н 1 1 1 1
01 025 4214 Сверлильная ИОТ№75
Н125 сверлов. 4 н 1 1 1 1
01 030 0260 Контрольная ИОТ№91
Контрольный стол контролер 4 н 1 1 1 1
Гидросхема после модернизации, с рамкой.dwg

Гидроклапан давления ПБГ54-32М
Гидроклапан редукционный МКРВ-10
Гидроклапан обратный 1МКО-10
Манометр МТП-601-60-2
Насос пластинчатый НПл S256
Переключатель манометра ПМ2-2-С320
Регулятор потока МПГ55-22
Гидрораспределитель ВЕ10.574А.Г24Н
Гидрораспределитель ВЕ10.44.Г24Н
Гидрораспределитель ВМР10.574
Гидромотор подачи материала
Цилиндр подачи бабки пильного диска
Цилиндр горизонтального зажима
Цилиндр вертикального зажима
Цилиндр подъема материала
5 Техническое обеспечение модернизации.doc
Проводя модернизацию устанавливаем следующую новую гидроаппаратуру: дроссель ПГ77-12 гидроклапаны давления ПБГ54-32М гидроклапан редукционный МК РВ-10 гидроклапан обратный 1МКО-10 переключатель манометра ПМ2-2-С320 регулятор потока МПГ55-22 два гидрораспределителя ВЕ10.574А.Г24Н гидрораспределитель ВЕ10.44.Г24Н гидрораспределитель ВМР10.574 фильтр 2ФГМ16-10 и пластинчатый насос НПл .
Изготавливаем гидропанель представленную на чертеже ДП 2-360107 04 для монтирования на ней аппаратуры. Для этого нам понадобится следующее оборудование: отрезной круглопильный автомат 8Г662 вертикально-фрезерный станок 6Р12 плоскошлифовальный станок 3Д732 координатно-расточной станок 2421 и вертикально-сверлильный станок 2Н125.
Маршрут изготовления гидропанели показан в приложении 1.
Введение.doc
Гидравлические приводы подач технологического оборудования обеспечивают перемещение рабочих органов технологического оборудования со скоростью подачи. Цикл работы гидравлических приводов подач несколько отличается и может включать быстрые подводы рабочего органа рабочие подачи выстой на упоре быстрые отводы в исходное положение и др. Скорости движения рабочего органа для указанных элементов цикла работы отличаются и регулирование их независимое.
Применение гидропривода дает возможность бесступенчато регулировать скорости в широких пределах плавно реверсировать движущие органы станка автоматически предохранять его от перегрузки легко обеспечивать смазывание возможность любого разветвления мощности и т.п. Недостатками гидроприводов являются утечка рабочей жидкости через уплотнения и зазоры что загрязняет окружающую среду проникновение воздуха в рабочую жидкость изменение свойств рабочей жидкости в зависимости от температуры и времени.
Для сведения недостатков к минимуму и повышения технического уровня выпускаемой продукции в конструкцию гидропривода вносятся некоторые изменения т.е. гидропривод модернизируют. Также модернизация может производиться в связи со снятием с производства устаревшей гидроаппаратуры и заменой ее на новую.
СПЕЦИФИКАЦИЯ.doc
Гидроклапан обратный
Гидродроссель ПГ77-12
Гидроклапаны давления
Гидроклапан редукционный
Переключатель манометра
2 Назначение и анализ гидросистемы, входящей в состав оборудования.doc
Гидросхема автомата приведена на чертеже ДП 2-360107 02 ГС.
Гидропривод автомата обеспечивает быстрый подвод рабочий и обратный ход бабки пильного диска продвижение материала до упора зажим и разжим материала а также подвод и отвод упора.
Гидропривод автомата состоит из пластинчатого насоса Н цилиндра подъема Ц6 цилиндра подачи бабки пильного диска Ц2 цилиндра вертикального зажима Ц5 цилиндра горизонтального зажима Ц4 цилиндра гидромуфты Ц1 цилиндра упора Ц3 гидромотора подачи материала Г и золотников управления. Насос нагнетает рабочую жидкость в систему которая воздействует на поршни гидроцилиндров и за счет того что жидкость несжимаема в системе создается давление. На штоках гидроцилиндров образуются необходимые усилия. Передвижения штоков гидроцилиндров осуществляются согласно циклограмме управление этими движениями обеспечивается распределителями Р1 Р2 Р3 Р4 и клапаном давления КД3. Для плавного перемещения бабки пильного диска при изменении силы резания предусмотрен регулятор потока РП. Защита гидросистемы от перегрузки обеспечивается гидроклапаном давления КД1 а клапан давления КД2 обеспечивает блокировку системы при не зажатой заготовке. В обеспечении безопасной работы участвует и гидромуфта которая подает команду на отвод бабки пильного диска при превышении максимально допустимого момента на шпинделе. Чтобы из системы не осуществлялся слив масла установлен обратный клапан КО. Очистку рабочей жидкости от загрязняющих частиц обеспечивает фильтр Ф.
При автоматическом цикле все движения совершаются последовательно автоматически вплоть до остановки автомата для загрузки следующего прутка.
9 Содержание технического обслуживания нидропривода оборудования.doc
Для обеспечения нормальной работы гидропривода должно быть налажено качественное обслуживание станка должен производиться контроль над всеми механизмами станка.
Замену масла в баке производить в следующем порядке:
- первая замена - после одного месяца работы
- вторая замена - после трех месяцев работ
- третья и последующие замены - не реже одного раза в шесть месяцев работы.
Испытания трубопроводов производить не реже одного раза в 8 лет осмотры трубопроводов должны производиться не реже одного раза в год.
Проверка манометров и их опломбирование должно производиться не реже одного раза в 12 месяцев. Кроме того не реже одного раза в 6 месяцев предприятием должна производиться дополнительная проверка. А так же:
- узлы вращающихся деталей должны быть заполнены смазкой;
- необходимо следить чтобы не было ударов и вибраций;
- один раз в неделю производить смазку вращающихся деталей узлов;
- покупные механизмы обслуживать согласно инструкции на них (ЭД; Электроаппаратура).
Заменять узлы гидропривода следует после их наработки до предельного состояния которое характеризуется допустимым изменением одного из основных параметров технической характеристики. Для насосов обычно регламентируется снижение объемного КПД для распределителей — утечки для дросселей — минимальный расход масла для предохранительных клапанов (клапанов давления) — изменение давления настройки во всем диапазоне потоков масла. Таким образом реальная долговечность узлов определяется не только их износом но и допустимым для конкретного гидропривода изменением параметра соответствующим предельному состоянию.
Поскольку стоимость узлов гидропривода сравнительно невелика производить их трудоемкий ремонт чаще всего нецелесообразно проще заменить узел новым. Однако замена быстроизнашиваемых деталей и узлов (шарики предохранительных клапанов пружины уплотнения электромагниты микровыключатели и т. п.) позволяющая в несколько раз увеличить срок службы широко применяется в практике эксплуатации гидроприводов.
В состав ТО входят очистные моечные крепежные монтажно-демонтажные заправочные регулировочные контрольные диагностические и др. операции.
Циклограмма.dwg

Используемые ГОСТы.doc
ГОСТ 2.104-68 «ЕСКД. Основные надписи»
ГОСТ 2.105-95 «ЕСКД. Общие требования к текстовым документам»
ГОСТ 2.109-73 «ЕСКД. Основные требование к чертежам»
ГОСТ 2.780-96 «ЕСКД. Обозначения условные графические. Кондиционеры рабочей среды емкости гидравлические и пневматические»
ГОСТ 2.781-96 «ЕСКД. Обозначения условные графические. Аппараты гидравлические и пневматические устройства управления и приборы контрольно-измерительные»
ГОСТ 2.782-96 «ЕСКД. Обозначения условные графические. Машины гидравлические и пневматические»
ГОСТ 3.1105-84 «ЕСТД. Формы и правила оформления документов общего назначения»
Панель_ Сборочный чертеж.dwg

Размеры для справок. 2. Течь масла не допускается.
10 Причины возможных отказов гидросистемы и методы их устранения.doc
Одними из причин отказа гидросистемы являются неисправности в работе гидронасоса и гидроцилиндра:
)Во время работы насоса может возникать повышенный шум. Существует две причины: кавитация во всасывающем трубопроводе и несоосность или излом осей валов насоса и приводного двигателя. В первом случае необходимо снизить частоту вращения насоса либо промыть всасывающий фильтр либо проверить засорение всасывающего трубопровода либо нагреть рабочую жидкость. Во втором – проверить и установить соостность осей не более 02 мм и угол излома осей не более 30 мин.
)Еще одна неисправность – насос подсасывает воздух. Причина – низкий уровень рабочей жидкости в баке нарушение герметичности соединений на всасывающем трубопроводе повреждение уплотнений вала насоса пенообразование в маслобаке. Для устранения необходимо долить требуемое количество рабочей жидкости в бак проверить всасывающий трубопровод и подтянуть все соединения заменить уплотнения устранить источник пенообразования или заменить масло на другое с антиприсадкой соответственно.
)Также может возникать стук и вибрация из-за износа или повреждения качающихся узлов насоса (поршней шестерни пластин и т.д.) износа или повреждения подшипников износа соединительной муфты ослабления крепежных винтов. Соответственно заменить или отремонтировать насос заменить подшипники заменить муфту подтянуть крепежные винты насоса и приводного электродвигателя.
)При работе насос если он неисправен может развивать недостаточное давление или не развивать его вообще. Причиной недостаточного давления служит загрязненность рабочей жидкости (метод устранения: замена рабочей жидкости предварительно промыв гидросистему) неисправность предохранительного клапана (заменить ПК) засорение ПК (промыть ПК) неправильная настройка ПК (настроить ПК на требуемую величину давления). Причиной последнего является низкий уровень рабочей жидкости в баке (долить жидкость в бак) неправильное направление вращение вала насоса (установить направление вращения вала насоса в соответствии с инструкцией) не работает приводной двигатель (выявить причину и запустить двигатель) сломан вал насоса (заменить или отремонтировать вал) предохранительный клапан заклинен в верхнем положении (промыть ПК и настроить его на требуемое давление).
)При работе гидроцилиндра возможно отсутствие рабочего давления в его поршневой полости из-за износа и разрушения уплотнительных узлов (метод устранения: заменить уплотнения) медленное перемещение штока и подтеки масла по штоку из-за износа уплотнений (заменить уплотнения).
)Также может возникать нагрев штока и его направляющих неравномерное с вибрацией движение штока или его защемление; причина – ослабление крепления гидроцилиндра (обеспечить соостность штока и приводного механизма) наличие недопустимых радиальных нагрузок (проверить надежность крепления и при необходимости восстановить его).
)Еще одной неисправностью является неравномерное с рывками перемещение штока и повышенный шум и вибрация из-за наличия воздуха в цилиндре (удалить воздух из цилиндра и устранить возможность подсоса воздуха по присоединениям трубопроводов и уплотнению штока).
12.2 Расчет трудоемкости работ до проекта.doc
Расчет годовой трудоемкости работ по техническому обслуживанию гидросистемы станка необходимо выполнять исходя из периодичности выполнения каждой операции а также трудоемкости восстановления работоспособности оборудования.
2.1 Расчёт i-го вида операций в год:
где – количество – периодичность выполнения операции i-го вида час.
mmmi15=3623 60 = 604
2.2 Расчёт трудоёмкости выполнения операции (работ) i-го вида в год:
где – трудоёмкость выполнения операции – продолжительность выполнения операции i-го вида час.
ТрТрТрi15=604*0005=03 ч.
2.3 Определение общей трудоёмкости работ по обслуживанию и ремонту оборудования
Для определения общей годовой трудоёмкости работ по обслуживанию оборудования составляем график планово-предупредительного ремонта (ППР).
График ППР до проекта представлен в таблице 7.
Таблица 7 – График ППР до проекта
Содержание работ по техническому обслуживанию и ремонту
Трудоёмкость работ по разрядам часы
Проверить уровень масла
Проверить температуру масла в баке
Проверить степень засорения фильтра по манометру или индикатору
Проверить уровень давления в напорной линии и других точках гидросистемы по манометрам
Проверить визуально наружные утечки
Проверить шум и вибрации при работе (на слух); при необходимости заменить неисправные элементы
Проверить нагрев приводного электродвигателя (на ощупь)
Проверить наличие пены на поверхности
масла в баке а также мутность масла
Проверить состояние заделок гибких
Произвести настройку регулирующих аппаратов
Определить величину утечек в сливную линию при неработающих гидродвигателях
Определить максимальную
подачу нерегулируемых насосов
Взять пробу масла на анализ; при отрицательном результате очистить бак и заменить масло
Проверить надежность закрепления гидроагрегатов; при необходимости подтянуть крепежные элементы
продолжение таблицы 7
Проверить расход масла через дренажную линию
Общая трудоемкость работ по обслуживанию и ремонту оборудования часы
2.4 Определение численности обслуживающего персонала до проекта:
где – численность обслуживающего персонала до проекта; – общая годовая трудоёмкость работ до проекта; – коэффициент выполнения норм.
Рассчитаем численность обслуживающего персонала до проекта:
12.3. Расчет трудоемкости работ по проекту.doc
3.1 Расчёт i-го вида операций в год:
3.2 Расчёт трудоёмкости выполнения операции (работ) i-го вида в год:
ТрТрТрi15=48*0005=024 ч.
3.3 Определение общей трудоёмкости работ по обслуживанию и ремонту оборудования
График ППР по проекту представлен в таблице 8.
Таблица 8 – График ППР по проекту
Содержание работ по техническому обслуживанию и ремонту
Трудоёмкость работ по разрядам часы
Проверить уровень масла
Проверить температуру масла в баке
Проверить степень засорения фильтра по манометру или индикатору
Проверить уровень давления в напорной линии и других точках гидросистемы по манометрам
Проверить визуально наружные утечки
продолжение таблицы 8
Проверить шум и вибрации при работе (на слух); при необходимости заменить неисправные элементы
Проверить нагрев приводного электродвигателя (на ощупь)
Проверить наличие пены на поверхности
масла в баке а также мутность масла
Проверить состояние заделок гибких
Произвести настройку регулирующих аппаратов
Определить величину утечек в сливную линию при неработающих гидродвигателях
Определить максимальную
подачу нерегулируемых насосов
Взять пробу масла на анализ; при отрицательном результате очистить бак и заменить масло
Проверить надежность закрепления гидроагрегатов; при необходимости подтянуть крепежные элементы
Проверить расход масла через дренажную линию
Общая трудоемкость работ по обслуживанию и ремонту оборудования часы
3.4 Определение численности обслуживающего персонала по проекту:
12.4 Расчет заработной платы до проекта.doc
4.1 Определение основной заработной платы обслуживающего персонала по каждой операции i-го вида:
где – основная заработная плата обслуживающего персонала соответствующего разряда руб; – часовая тарифная ставка выполняемых работ соответствующего разряда руб; – трудоёмкость выполняемых работ по соответствующему разряду ч; – коэффициент премий.
ЗПосн2= 3098·214007·14= 9281912 руб.
ЗПосн3= 13475·249060·14= 46985169 руб.
ЗПосн4= 225·289648·14= 9123912 руб.
ЗПосн5= 518·319166·14= 231459183 руб.
ЗПосн6= 10·350529·14= 4907405 руб.
Общая величина основной зарплаты определяется как сумма:
ЗПосн= 9281912 +46985169 +9123912+231459183+4907405=80816131 руб.
4.2 Определение дополнительной зарплаты обслуживающего персонала
где – дополнительная зарплата руб; – процент дополнительной зарплаты %.
ЗПдоп= 16·80816131 100= 12930581 руб.
Общая величина зарплаты определяется как сумма:
ЗПобщ= 80816131 + 12930581 = 93746712 руб.
4.3 Определение отчислений в социальные фонды:
где – отчисления в социальные фонды руб; – норматив отчислений в социальные фонды %.
Ос.ф= 367·93746712 100= 344050433 руб.
4.4 Годовой фонд заработной платы с отчислениями до проекта:
ЗПгод= 93746712 + 344050433 = 1281517553 руб.
Полученные результаты расчетов занесем в таблицу 9.
Таблица 9 – Заработная плата обслуживающего персонала до проекта
Дополнительная заработная
12.1 Расчет режима работы и фондов времени для оборудования и рабочих.doc
1 Расчёт режима работы и фондов времени для оборудования и рабочих
1.1 Расчет номинального и действительного фонда времени для оборудования
Для оборудования рассчитывается номинальный и действительный фонды времени.[3]
Номинальный фонд времени рассчитывается по формуле:
Fн=(Дк-Двых)×S×Тсм-Дсокр×Тсокр×S (14)
где Дк-количество календарных дней в году; Двых-количество выходных и праздничных дней в году; S-количество смен; Дсокр-количество дней в году с сокращённой длительностью рабочей смены дня; Тсокр-величина сокращения ч.
Рассчитаем номинальный фонд времени и результат занесем в таблицу 5.
Fн=(366-112)×2×8-8×1×2=4048
Действительный фонд времени работы оборудования определяется по формуле:
Fд.о.=Fн×(1- α 100) (15)
где α -процент потерь времени на ремонт
Рассчитаем действительный фонд времени работы оборудования и результат занесем в таблицу 5.
Fд.о.=4048×(1-105100)=3623
Таблица 5 – Действительный фонд времени работы оборудования
Простой оборудования из-за ремонта
Годовой фонд времени оборудован
1.2 Расчет фонда времени для рабочих
Для рабочих рассчитывается номинальный и действительный фонды времени. [3]
Номинальный фонд времени для рабочих рассчитывается по формуле:
Fн.р=Др×Тсм - Дсокр×Тсокр (16)
где Др –количество рабочих дней в году.
Рассчитаем номинальный фонд времени для рабочих и результат занесем в таблицу 6.
Fн.р=254×8 - 8·1=2024
Действительный фонд времени рабочего:
Fд.р=Fн.р×(1- α 100) Тсм (17)
где α –процент плановых потерь рабочего времени α= 12%.
Рассчитаем действительный фонд времени для рабочих и результат занесем в таблицу 6.
Fд.р=2024×(1-12100)=1781
Таблица 6 – Действительный фонд времени рабочего
Число рабочих дней в году
Плановые потери рабочего времени
Годовой фонд времени рабочего
12.8Экономическое обоснование целесообразности модернизации оборудования.doc
Проект может быть признан экономически обоснованным в том случае если проведенные мероприятия по модернизации гидросистемы станка улучшают параметры работы и эксплуатации последнего. Это выражается положительным значением годового экономического эффекта от указанной модернизации. Годовой экономический эффект от указанной модернизации:
где – сумма годового экономического эффекта от мероприятий по модернизации; – производственная себестоимость работ по обслуживанию и эксплуатации оборудования соответственно до и после проекта; – коэффициент эффективности капитальных вложений (для РБ=015) [3]; К – единовременные затраты связанные с модернизацией;
Эг = (5476229514-5221194537) – 015 · 2939170 = 210947427 руб.
12.7 Расчет расходов на содержание и эксплуатацию оборудования до проекта.doc
7.1 Расчёт стоимости силовой электроэнергии
Сэ.э= 1866 ·10 ·3623 ·09 ·1 = 60844662 руб.
7.2 Расчёт амортизации оборудования
Са = 17040000 ·11 ·10 ·1100 = 1874400 руб.
7.3 Расчёт вспомогательных материалов
Свсп = 19959871 ·1 = 19959871 руб.
7.4 Определение расходов на содержание и эксплуатацию оборудования
Рсод = 17040000 ·1 ·001 = 170400 руб.
7.5 Определение расходов на текущий ремонт
Ртек.р = 17040000 ·1 ·0005 = 85200 руб.
7.6 Расходы на содержание малоценных инструментов и приспособлений
Ризн.ин = 71285252·1 = 71285252руб.
Таблица 14 – Смета расходов на содержание и эксплуатацию оборудования по проекту
Силовая электроэнергия
Амортизация основных средств
Вспомогательные материалы
Содержание оборудования
Износ содержание и ремонт малоценных инструментов и приспособлений
Покупные комплектующие за вычетом стоимости неисправных
Изготовление дополнительных деталей
Рц = 263 ·71285252100 = 1874802128 руб.
7.8 Общезаводские расходы
Робщ = 1164 ·71285252100 = 829760333 руб.
Таблица 15 – Калькуляция себестоимости работ по проекту
Основная зарплата обслуживающего персонала
Дополнительная зарплата обслуживающего персонала
Отчисления в социальные фонды
Расходы на содержание и эксплуатацию оборудования
Цеховая себестоимость
Общезаводские расходы
Производственная себестоимость
12.6 Расчет расходов на содержание и эксплуатацию оборудования до проекта.doc
6.1 Расчёт стоимости силовой электроэнергии
Таблица 11 – Стоимость оборудования
Модель станка наименование оборудования
Свободная отпускная цена руб
Установленная мощность кВт
Автомат отрезной круглопильный модели 8В66А
где – стоимость одного киловатт-часа электроэнергии руб.
где – общий расход электроэнергии для работы оборудования кВт; – установленная мощность оборудования; – коэффициент спроса учитывающий недогрузку оборудования по мощности; – доля занятости станка обработкой детали.*В случае модернизации – равен 1.[3]
Сэ.э= 1866 ·10 ·3623 ·09 ·1 = 60844662 руб.
6.2 Расчёт амортизации оборудования
где – балансовая стоимость оборудования руб; – норма амортизации %.
где 11 – коэффициент учитывающий затраты на доставку и установку оборудования [3]; – отпускная цена оборудования.
Са = 17040000 ·11 ·10 ·1100 = 1874400 руб.
6.3 Расчёт вспомогательных материалов
где – затраты на вспомогательные материалы на один универсальный станок.
Свсп = 2262852 ·1 = 2262852 руб.
6.4 Определение расходов на содержание и эксплуатацию оборудования
Принимаем приближенный норматив расхода средств на эти цели равным 1% от стоимости оборудования. [3]
Рсод = 17040000 ·1 ·001 = 170400 руб.
6.5 Определение расходов на текущий ремонт
Принимаем приближенный норматив расхода средств на эти цели равным 05% от стоимости оборудования. [3]
Ртек.р = 17040000 ·1 ·0005 = 85200 руб.
6.6 Расходы на содержание малоценных инструментов и приспособлений
где – расходы на эту статью на один станок в год руб.
Ризн.ин = 80816131·1 = 80816131 руб.
Таблица 12 – Смета расходов на содержание и эксплуатацию оборудования до проекта
Силовая электроэнергия
Амортизация основных средств
Вспомогательные материалы
Содержание оборудования
Износ содержание и ремонт малоценных инструментов и приспособлений
где – процент цеховых расходов.
Рц = 263 ·80816131100 = 2125464245 руб.
6.8 Общезаводские расходы
где – процент общезаводских расходов.
Робщ = 1164 ·80816131100 = 940699765 руб.
Таблица 13 – Калькуляция себестоимости работ до проекта
Основная зарплата обслуживающего персонала
Дополнительная зарплата обслуживающего персонала
Отчисления в социальные фонды
Расходы на содержание и эксплуатацию оборудования
Цеховая себестоимость
Общезаводские расходы
Производственная себестоимость
12.5 Расчет заработной платы по проекту.doc
5.1 Определение основной заработной платы обслуживающего персонала по каждой операции i-го вида:
ЗПосн2= 23319·214007·14= 6986601 руб.
ЗПосн3= 11482·249060·14= 40035897 руб.
ЗПосн4= 1665·289648·14= 6751695 руб.
ЗПосн5= 518·319166·14= 231459183 руб.
ЗПосн6= 9·350529·14= 4416665 руб.
Общая величина основной зарплаты:
ЗПосн= 6986601 +40035897 +6751695+231459183+4416665=71285252 руб.
5.2 Определение дополнительной зарплаты обслуживающего персонала:
ЗПдоп= 16·71285252 100= 1140564 руб.
Общая величина зарплаты:
ЗПобщ= 71285252 + 1140564= 82690892 руб.
5.3 Определение отчислений в социальные фонды:
Ос.ф= 367·82690892 100= 303475574 руб.
5.4 Годовой фонд заработной платы с отчислениями по проекту:
ЗПгод= 82690892 + 303475574 = 1130384494 руб.
Полученные результаты расчетов занесем в таблицу 10.
Таблица 10 – Заработная плата обслуживающего персонала по проекту
Дополнительная заработная
Рекомендуемые чертежи
- 05.12.2023