Адаптивное управление станком с ЧПУ с помощью датчика усилия резания



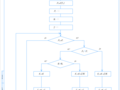
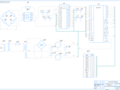
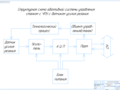
- Добавлен: 24.01.2023
- Размер: 694 KB
- Закачек: 2
Описание
Состав проекта
![]() |
![]() ![]() ![]() |
![]() ![]() ![]() ![]() |
![]() ![]() |
![]() ![]() ![]() ![]() |
![]() ![]() ![]() ![]() |
![]() ![]() ![]() |
Дополнительная информация
Содержание.docx
2 Классификация систем автоматического управления12
Конструкторский раздел16
1. Разработка структурной схемы проектируемой адаптивной
2. Алгоритм работы системы19
3. Измерение усилия резания тензодатчиками22
4. Основные сведения о тензодатчиках29
5. Выбор тензорезисторного датчика31
6. Общие сведения об АЦП33
8. Выбор усилителя36
9. Выбор устройства ввода-вывода39
10. Расчет источника питания41
Список использованной литературы47
Алгоритм..cdw

управления станка с ЧПУ
с датчиком усилия резания
АТС.2011.07АТП1.010.ПАС.
принципиальная схема.cdw

Струк-ная. схема .cdw

станком с ЧПУ с датчиком усилия резания
Схема электрическая структурная
АТС.2011.07АТП1.010.ПАС.
ПЗ.doc
ГОУВПО «Брянский государственный технический университет»
Кафедра «Автоматизированные технологические системы»
«Проектирование автоматизированных систем»
АТС. 07АТП1. 010. ПАС.
В данном курсовом проекте спроектирована адаптивная система управления станком с ЧПУ токарной группы с датчиком усилия резания. Данная система служит для стабилизации усилия резания и управляет скоростью резания. Источником информации об усилии резания является тензодатчик.
Последние 30-40 лет без учета кризисных периодов вся мировая промышленность демонстрирует небывалый для двадцатого века рост. Рост этот прямо пропорционально связан с внедрением и использованием числового программного управления (ЧПУ) на производстве. Сегодня сложно недооценить современные системы автоматизации. В истории индустриального общества подобное влияние на темпы роста производства оказал лишь конвейер изобретенный в начале двадцатого века. Сегодня мировые лидеры отрасли разрабатывают все новые и новые системы управления автоматизацией. Новые системы ЧПУ оказывают огромнейшее влияние на динамику развития не только отдельных отраслей промышленности но и всей мировой промышленности в целом. Уже сложно представить даже небольшое производство где станки не были бы оснащены ЧПУ. [11]
Программное управление станками уже имеет свою собственную историю; и в этой истории существует немало ключевых моментов с которых можно начинать отсчет жизни очередному поколению систем с числовым программным управлением (ЧПУ). Такие ключевые моменты связаны с внедрением в область ЧПУ и адаптацией в этой области (с учетом специфики ЧПУ) концептуальных идей из электроники и вычислительной техники техники автоматического управления приводами и процессами техники автоматизированного проектирования и автоматизированного программирования. Можно насчитать несколько сменивших друг друга а частично сосуществующих поколений (исследователи насчитывают их от четырех до десяти) каждое из которых конечно же оставило свой след в облике современной системы управления.
Однако в истории программного управления станками есть явно выраженная граница (середина 70-х годов) связанная с началом использования микропроцессоров для целей ЧПУ. Специальные электронные аппараты каковыми были устройства ЧПУ прежде уступили свое место специализированным (т. е. проблемно-ориентированным) вычислительно-управляющим машинам. Микропроцессорные устройства ЧПУ не просто отвоевали себе в области управления какую-то часть позиций но победили безоговорочно и полностью.[1]
По своему использованию металлорежущий станок общего назначения укрупненно можно разделить на станки обрабатывающие корпусные детали и детали типа тел вращения а также выделить еще своеобразную группу станков со сложной кинематической структурой - станки для обработки поверхностей зубьев колес червяков реек и др. подобных деталей.
Каждый станок состоит из устройств которые взаимодействуя выполняют или способствуют выполнению той работы для которой предназначен данный станок. Однако можно найти для них общие функциональные черты. По назначению характеристикам и принципам работы а значит и по управлению можно выделить следующие группы исполнительных устройств:
Формообразующие устройства - рабочие органы станка связанные с формообразованием изделий и процессами позиционирования т.е. передвигают заготовку (или инструмент) по программируемым координатам во время обработки или перед обработкой. Отличительным свойством данной группы является то что траекторию и путь движения можно изменять в зависимости от вводимой программы.
Манипулирующие устройства - предназначены для выполнения постоянных команд связанных с автоматическим циклом работы оборудования. Они изменяют режимы резания направления и скорости перемещения механизмов станка управляют охлаждением сменяют режущий инструмент или заготовку закрепляют их транспортируют и складируют. Момент ввода в действие и последовательность их работы могут быть различными. Это определяется программой цикловой автоматики.
Вспомогательные устройства - обслуживают процесс обработки например обеспечивают автоматическую сборку отходов смазывание станка отсос тумана и пыли работу гидро - и пневмосистемы и др. Обычно они имеют автономную систему управления. Наиболее важными и сложными по своему управлению являются первая и частично вторая группа устройств.
Позиционированием называют движения в заранее программируемые точки (позиции) происходящие обычно без обработки т.е. все установочные и делительные движения осуществляемые перед формообразованием а также движения манипулирующих устройств сменяющих инструменты и заготовки и выполняющие другие подобные действия.
Под автоматическим циклом работы станка понимают программируемую последовательность движений основных органов станка а также последовательность всех действий необходимых для нормального функционирования оборудования при изготовлении единицы продукции.
Алгоритмом обозначают точное предписание задающее процесс переработки исходных данных в однозначный результат. Алгоритм управления - предписание о последовательности выполнения операций управления.
При простом формообразовании и позиционировании движения осуществляются поочередно или одновременно но при этом кинематически не взаимосвязаны. Так обработка ступенчатого валика на токарном станке по прямоугольному циклу происходит при поочередных движениях продольной и поперечной кареток суппорта с одновременным но не обязательно взаимосвязанным вращением заготовки.
При сложном движении форма детали зависит от формы направляющих и передаточных отношений между рабочими органами станка которые перемещаются на размеры определяемые командами управления.
Рассмотрим произвольный профиль обрабатываемой поверхности предположим что это или плоский профиль или осевое сечение детали типа тела вращения (см. рис.1.).
Рис.1. Профиль обрабатываемой поверхности.
Такой профиль может быть обработан различным режущим инструментом: резцом 1 с точечной режущей кромкой (если это тело вращения); цилиндрической фрезой 2 с осью расположенной перпендикулярно плоскости заготовки; пальцевой фрезой 3 с осью расположенной в плоскости заготовки.
Однако разнообразие вариантов обработки и возможность использования различного инструмента могут быть получены ограниченным числом формообразующих движений. Возможно лишь три варианта: движение заготовки относительно неподвижного инструмента; движение инструмента относительно неподвижной заготовки и совместное их движение. Выбор варианта происходит при проектировании станка и влияет на разработку его системы управления.
Рассматривая сложное формообразование его можно представить состоящим из простых движений каждое по своим направляющим (координатным перемещениям). Обработка элемента сложной траектории (участок А-Б) произойдет при одновременном перемещении в продольном направлении на расстояние Sz и поперечном на расстояние Sx.
Управление станком можно представить как процесс воздействия на него для обеспечения выполнения требуемого технологического процесса обработки детали с заданными точностью производительностью и себестоимостью обработки. Оно может осуществляться вручную - человеком или без участия человека - системой автоматического управления (САУ).
При управлении станками вручную обеспечиваются большая универсальность и высокая мобильность. Однако управление станком вручную значительно ограничивает возможность повышения производительности обработки а во многих случаях также снижает или делает нестабильной точность обрабатываемых деталей.
При применении САУ управление станком производится на основе заранее разработанной программы воплощенной в программоноситель (кулачках копире перфоленте и др.).
Система автоматического управления (САУ) представляет собой комплекс устройств и средств связи обеспечивающих точное и согласованное во времени взаимодействие рабочих и вспомогательных исполнительных механизмов станка в соответствии с программой управления разработанной на основе принятого технологического процесса обработки. Программа управления - это последовательность команд обеспечивающих заданное функционирование рабочих органов станка. Элемент или комплекс элементов несущих на себе программу управления называется программоносителем.
Варианты исполнения САУ приведены на рис.2. а б в.
При первом варианте исполнения САУ (рис. а) программа управления воплощенная в программоноситель вводится в управляющее устройство которое осуществляет управление рабочими органами станка. САУ в этом исполнении не контролирует как в действительности обрабатывается программа управления.
При втором исполнении САУ (рис. б) в управляющее устройство поступают не только задающие сигналы программы управления характеризующие требуемое положение рабочих органов станка но и сигналы от датчика обратной связи характеризующие действительное положение рабочего органа станка или от датчиков характеризующих действительные параметры процесса обработки детали (рис.в.). Управляющее устройство перерабатывает получаемую информацию по определенному заложенному в нем алгоритму. Если имеется рассогласование сигналов требуемого и действительного положения на выходе УУ возникает управляющее воздействие подаваемое на приводной двигатель М.[2]
Рис.2. Варианты исполнения САУ
2. Классификация систем автоматического управления
По виду начальной информации включенной в программу управления все САУ можно классифицировать на две группы (см. рис.3.).
Рис.3. Классификация САУ
К первой группе относятся САУ работающие на основе полной заранее рассчитанной программы управления. Главной задачей САУ данной группы является выполнение заданной программы без ее изменения и коррекции на основе получаемых результатов процесса обработки. К данной группе относится большинство САУ станками: системы управления с распределительными валами копировальные системы управления системы циклового программного управления (ЦПУ) и системы числового программного управления (ЧПУ).[3]
Ко второй группе относятся САУ работающие на основе неполной начальной информации которая с целью оптимального управления дополняется и корректируется в процессе обработки на основе использования текущей технологической информации об управляемом процессе получаемой с помощью различных датчиков (см. рис.3.). К данной группе относятся самоприспосабливающиеся (адаптивные) самонастраивающиеся самоорганизующиеся и самообучающиеся системы управления.
В самоприспосабливающихся системах достижение оптимального управления осуществляется изменением только управляющего воздействия.
В самонастраивающихся системах оптимальное управление производится изменением параметров самой системы.
В самоорганизующихся системах оптимальное управление производится изменением структуры системы.
В самообучающихся системах - изменением алгоритма управления.
Наибольшее применение нашли самоприспосабливающиеся (адаптивные) системы управления как более простые.
По наличию обратной связи все САУ делят на две группы: разомкнутые и замкнутые.
В разомкнутых системах (см. рис. а) отсутствует контроль действительного положения рабочего органа станка в которое он устанавливается в результате прохождения и преобразования потока начальной информации вводимой программоносителем. Поэтому точность перемещения рабочего органа а следовательно и точность обработки будут зависеть от точности передаточных механизмов привода подачи. Однако эти системы по сравнению с замкнутыми проще конструктивно надежнее в работе и дешевле. Разомкнутыми системами управления являются системы управления с РВ механические копировальные системы системы ЧПУ построенные на основе применения шаговых электродвигателей.
Замкнутые системы управления можно разделить на две подгруппы:
- системы управления с обратной связью по положению рабочих органов станка (см. рис. б). К этой группе относятся следящие копировальные системы большинство систем ЧПУ замкнутого типа;
- самоприспосабливающиеся системы управления (см. рис. в) в которых использованы датчики измеряющие параметры процесса обработки (силу резания температуру в зоне резания вибрации и др.) для дополнения и коррекции начального потока информации при изменении припуска на заготовке твердости материала и других факторов которые предусмотреть заранее невозможно. Эти системы управления являются самыми сложными но обеспечивают высокую точность обработки оптимальную производительность и минимальную себестоимость обработки.
По характеру управляющих сигналов САУ делят на две группы: непрерывные (аналоговые) и дискретные. Непрерывные сигналы представляют собой величины значения которых являются непрерывными функциями времени. Непрерывные САУ состоят только из звеньев непрерывного действия.
Дискретной САУявляется система содержащая хотя бы одно звено дискретного действия. У такого звена выходная величина изменяется дискретно т.е. скачками даже при плавном изменении входной величины.
В непрерывных системах программа управления задается в виде непрерывного сигнала (профилем кулачка или копира углом сдвига по фазе двух напряжений).
В дискретных системах программа управления задается в виде единичных импульсов (например системы ЦПУ и ЧПУ с шаговым электродвигателем)
Для автоматического управления различных типов станков применяют системы управления с РВ следящие копировальные системы системы ЦПУ и системы ЧПУ. [2]
Конструкторский раздел
1. Разработка структурной схемы проектируемой адаптивной системы
Система управления станками обеспечивающая поиск и поддержание технологических параметров рабочего процесса удовлетворяющих критерию оптимизации и действующим ограничениям получила название адаптивной. Обобщённая структурная схема адаптивного управления показана на рис.4.
Рис. 4. Обобщённая структурная схема адаптивного управления.
Блок (модуль) адаптивного управления в данном курсовом проекте является частью ЧПУ и реализуется программными средствами. Из рисунка понятно что устройство ЧПУ управляет технологическим процессом лишь косвенно: через приводы подачи главного движения автоматики. Таким образом только адаптивное управление способно снизить отрицательное влияние действующих на технологический процесс возмущений а также отрицательные последствия несовершенной управляющей программы ЧПУ.
Измеряемые параметры зависят от искомых технологических; обычно измеряют силу резания мощность износ инструмента и т.п. К параметрам настройки относятся коэффициенты уравнений определяющих математическую модель. Ограничения составляют систему неравенств каждое из которых устанавливает пределы варьирования измеряемых и искомых параметров. Математическая модель связывает критерий оптимальности искомыми технологическими и измеряемыми параметрами. Блок оптимизации действуя в соответствии с некоторым постоянным или выбираемым алгоритмом находит такие значения искомых технологических параметров которые обеспечивают критерию оптимальности максимум или минимум. При этом учитываются необходимые ограничения.[3]
Получить математическую модель чисто теоретическим путём удаётся далеко не всегда. По этой причине при разработке модели эффективны методы теории планирования эксперимента. Информационно-измерительная система сама является непрерывно работающим экспериментатором а вычислительный блок оптимизации способен сам выполнять расчёты требуемые при построении модели методами планирования эксперимента В связи с этим блок оптимизации может автоматически вносить необходимые коррекции в математическую модель а в принципе и синтезировать такую модель.
На основании общих данных об адаптивных системах спроектируем систему адаптивного управления станком с датчиком температуры. На рис.5. представлена разработанная структурная схема.
Рис.5. Разработанная структурная схема
2. Алгоритм работы системы
Информация о мощности резания через блок коррекции поступает на блок сравнения где сравнивается с сигналом от задатчика. Блок коррекции учитывает особенности каждого нового заменяемого инструмента в соответствии с его кодом передаваемым устройством ЧПУ. Сигнал с выхода блока сравнения управляет регулируемым приводом главного движения. При этом номинальное значение скорости главного движения устанавливается в исходной программе. В процессе регулирования режима резания важно сохранить постоянство оборотной подачи которая связана с частотой вращения шпинделя обратно пропорциональной зависимостью. Для этого на шпинделе установлен фотоэлектрический датчик угла поворота частотная последовательность с которого поступает к дешифратору блока задания скорости. Дешифратор устанавливает такую кратность выходного делителя блока задания скорости которая и соблюдает упомянутую обратно пропорциональную зависимость.
Положительным эффектом подобного управления процессом резания является увеличение стойкости инструмента повышение производительности сохранение постоянной чистоты обработки. Пусть для увеличения эффективности токарной обработки повышения производительности поставлена задача стабилизации величины силы резания на уровне определяемом из условий прочности станка или инструмента. В качестве регулируемого параметра в этом случае наиболее удобно принять оборотную подачу. Как правило в устройствах ЧПУ есть выходной делитель позволяющий вручную регулировать запрограммированную скорость подачи с кратностью 01—10.
Алгоритм автоматического управления представлен на рис.6. Исходными данными являются заданные сила Рз мощность Nз максимальная оборотная подача S. В каждый эта информация перерабатывается и в (i +1)-й момент времени устанавливается новая подача выбором коэффициента ki+1 в формуле Si+1 = kiхS1. Автоматическое изменение подачи осуществляется до тех пор пока не будет достигнуто равенство фактического и заданного значений силы резания при соблюдении условия ограничения по мощности. Если ограничение по мощности вступает в силу раньше чем достигнуто Рф=Рз то дальнейшее увеличение подачи блокируется.
Рис.6. Алгоритм работы адаптивной системы управления.
3. Измерение усилия резания тензодатчиками
Одним из направлений дальнейшего совершенствования парка современного металлорежущего оборудования с ЧПУ является оснащение его адаптивными системами управления которые позволяют учитывать параметры и факторы технологического процесса механической обработки. Одним из элементов таких систем является датчик мгновенных значений усилий резания.
Датчик состоит из совокупности измерительных преобразователей рис.7.
Рис.7. Структура датчика обратной связи
Задача измерительного преобразователя – переводить одну физическую величину в другую. В каждом измерительном преобразователе используется какая-либо физическая закономерность функционально связывающая одну физическую величину с другой. Для такой связи используют различные физические явления:
тензорезистивный эффект;
пьезоэлектрический эффект;
эффект изменения электрической емкости;
эффекты которые основаны на электромагнитных явлениях;
эффект изменения частоты колебания струн;
эффект наведения электрического заряда.
Рассматривая физические процессы во всех известных измерительных преобразователях можно в каждом случае установить связь между входной и выходной величинами:
Отношение изменения выходной величины к изменению входной получило название – чувствительность измерительного преобразователя:
Чувствительность датчика в этом случае:
В машиностроении хорошие рекомендации имеют тензорезисторные преобразователи . Тензодатчик (тензорезисторный датчик)- преобразователь силы измеряющий массу методом преобразования измеряемой величины (массы) в другую измеряемую величину (выходной сигнал) с учетом влияния силы тяжести и выталкивающей силы воздуха действующих на взвешиваемый объект.
Основой тензорезисторных датчиков является тензоэфект: при изменении длинны проволоки (проволочный тензорезистор) или фольги (ленточный фольговый тензорезистор) изменяется ее сопротивление. (рис. 8)
Рис.8. Структура тензорезистора
Известно что особенностью датчиков силы является малые величины деформации порядка 01-02% и для этих приделов погрешность тензорезисторов гистерезис нелинейность становятся минимальными это позволяет повышать чувствительность датчиков.
Структурная схема любого тензорезисторного датчика силы представляет собой последовательность соединений трех измерительных преобразователей рис.9.
Рис.9. Структурная схема тензорезисторного датчика силы
Особый интерес представляет собой механическая часть датчика – упругий элемент а в особенности его место расположения в объекте управления (исследования).
Применительно к адаптивным системам управления станками с ЧПУ расположить упругий элемент в близи зоны резания (т.е. инструментальной головки) не предоставляется возможным. Особенность работы резцедержки такова что при повороте инструментальной головки будет менять свое положение и измерительная часть датчика. В этом случае конструкция датчика требует использование токосьемника который внесет нестабильность работы адаптивной системы управления из-за переменного сопротивления подвижных частей токосьемника.
Одним из путей решения вопроса эффективного использования тензодатчика является размещение его упругого элемента на стыке узлов резцедержки и ее корпуса. В частном случае при оснащении адаптивными системами токарных станков семейства 16К20 с ЧПУ в качестве упругого элемента датчика может служить правая полумуфта которая неподвижно закреплена на корпусе резцедержки рис.10.
Рис. 10. Правая сцепная полумуфта резцедержки
Левая полумуфта узла привода поворотной резцедержки сцепляется с правой полумуфтой при действии силы резания возникает крутящий момент левая полумуфта давит на правую зубья правой полумуфты испытывают напряжения изгиба этот изгиб изменяет сопротивление тензорезистора.
Наиболее простым решением по конструкции упругого элемента является правая полумуфта с прорезью в зубе на щеку которой приклеен тензорезистор рис.11. Это решение ведет к зависимости точности изготовления зубьев муфты и достоверности датчика а именно конструкция работает при условии что все зубья муфты находятся в зацеплении это соответствует высокой точности изготовления зубьев. В производстве такое решение обойдется большими затратами.
Рис. 11. Схема установки тензорезистора на щеку прорези зуба правой полумуфты
Изменяем конструкцию правой полумуфты как показано на рис.12
Рис. 12. Правая полумуфта резцедержки используемая в качестве упругого элемента датчика
Наклейка тензорезисторов будет производиться на прорези корпуса правой полумуфты как показано на рис.13.
Рис. 13. Схема установки тензорезисторов на прорези корпуса правой полумуфты
Предлагаемое решение позволяет исключить зависимость точности изготовления зубьев муфты и достоверности датчика.
Измерения с помощью тензодатчиков требуют регистрации очень малых изменений сопротивления. Например относительное изменение сопротивления вызываемое относительным растяжением 00005 при тензорезистивном коэффициенте равном 2 составит 01% что для тензодатчика сопротивлением 120 Ом эквивалентно сопротивлению всего лишь 012 Ом. Чтобы измерять столь малое изменение сопротивления и скомпенсировать температурную погрешность тензодатчики практически всегда используют в мостовой схеме (мост Уитстона рис. 14) подключенной к источнику напряжения или тока (источнику питания моста).
Общепринятого стандарта для питания моста не существует. Типовыми являются напряжения 3В и 10В. [4]
Рис. 14. Мост Уитстона
4. Основные сведения о тензодатчиках
Тензорезисторный датчик обычно представляет собой специальную упругую конструкцию с закреплённым на нейтензорезистороми другими вспомогательными деталями. После калибровки по изменению сопротивления тензорезистора можно вычислить степеньдеформации которая будет пропорциональна силе приложенной к конструкции. [5]
Основные характеристики тензодатчиков:
Наибольший предел измерения (НПИ). НПИ- это максимальное усилие которое может воспринимать тензодатчик. Фактически датчик имеет дополнительный запас прочности но при выборе тензодатчика номинальная нагрузка на него не должна превышать НПИ. Для особо ответственных конструкций рекомендуется выбирать НПИ тензодатчика с дополнительным запасом.
Конструкция тензодатчика. Наиболее распространенные конструкции тензодатчиков: балочный мостовой сильфонный одноточечный (single point) колонный шайбовый S - образный. Выбор типа конструкции обуславливается назначением весовой системы в которой используется датчик веса и конструктивными особенностями места его установки.
Схема подключения тензодатчика. Самая распространенная это так называемая "четырехжильная" схема подключения такая схема применяется в обычных случаях. В случаях когда имеется существенная разница сопротивлений кабелей смежных тензодатчиков используется "шестижильная" схема подключения такая схема позволяет компенсировать электрическое сопротивление кабелей тензодатчиков.
Класс точности тензодатчика. В соответствии с OIML R 60 классы точности датчиков распространяются в очень широком диапазоне но в реальности классы точности тензодатчиков соответствуют от D1 до С6. Наибольшее применение нашел класс точности C3 что приблизительно соответствует комбинированной погрешности 0.02%. Использование более точных датчиков требует обоснования. Также определяет точность весовой индикатор.
Материал тензодатчика. Чаще всего датчики изготавливаются из легированной стали нержавеющей стали и алюминия. Обычно одноточечные (single point) датчики производятся из алюминия а остальные из легированной стали. Нержавеющая сталь дороже и предлагается как опция чаще применяется в пищевых производствах.
Другие характеристики тензодатчиков. Также при выборе тензодатчика необходимо обратить внимание на: рабочий диапазон температур рабочий коэффициент передачи (РКП) рекомендуемое и максимальное напряжение питания класс защиты входное и выходное сопротивление длину и диаметр кабеля.[6]
5. Выбор тензорезисторного датчика
Рис.15. Общий вид тензорезистора 2ФКП-5400.
Электрическое сопротивление 400 ± 035%Ом
Диапазон измеряемых деформаций - ± 3000 млн.-1
Ток питания не более - 25 мА.
Напряжение питания – 10В
Диапазон рабочих температур эксплуатации от –50°С до +70°С.
Категория точности - 005 %.
Чувствительность – 21
С моста снимается сигнал равный 21 мВ.
Рис. 16. Габаритно-присоединительные размеры (мм) 2ФКП-5400
Для наклейки тензорезисторов рекомендуется применять клеи ВС-10Т иEP-310S (фирмы HBM Германия). Клей поставляется позаявкам потребителей.
В2005 году реализована программа технических инноваций тензорезисторов врезультате чего:
—внедрено применение импортной константановой фольги при производстве тензорезисторов;
—внедрена технология наклейки тензорезисторов клеем EP-310S фирмы HBM (Германия). [7]
6. Общие сведения об АЦП
В электронной аппаратуре одинаково широко используются сигналы представленные как в виде непрерывных переменных так и в виде дискретных двоичных сигналов. Для взаимодействия электронных устройств обрабатывающих непрерывные (аналоговые) сигналы с устройствами оперирующими дискретными двоичными (цифровыми) сигналами применяют цифро-аналоговые (ЦАП) и аналого-цифровые преобразователи (АЦП).
Распространение цифровой вычислительной техники особенно активное в последние годы благодаря выпуску микропроцессорных БИС и однокристальных микро-ЭВМ потребовало выпуска отечественной промышленностью БИС ЦАП и АЦП. Это объясняется тем что большинство переменных информационных величин (ток напряжение скорость температура давление освещенность и т. д.) представляется в аналоговой форме. Непосредственная обработка этих величин цифровыми устройствами невозможна без предварительного представления их в виде цифрового N-разрядного слова. Эту операцию осуществляют АЦП. В свою очередь для точного управления изменениями аналоговых величин по результатам обработки цифрового слова в микро-ЭВМ необходимо преобразовывать цифровую информацию в аналоговую с помощью ЦАП.
Аналого-цифровые преобразователи (АЦП) применяются в измерительных системах и измерительно-вычислительных комплексах для согласования аналоговых источников измерительных сигналов с цифровыми устройствами обработки и представления результатов измерения.[8]
Выбираем АЦП марки ADS7811. (рис.17.)
Микросхема ADS7811 представляет собой 16-разрядный АЦП рассчитанный на входное напряжение 25 В. Питание данного аналого-цифрового преобразователя осуществляется напряжением ±5 В. Питающие электроды соединены с землёй через параллельно соединённые конденсаторы (керамический и танталовый). Вывод CAP необходим для подключения конденсаторной компенсации. Используется параллельная комбинация керамического конденсатора 0.1 мФ и танталового конденсатора 2.2 мФ. Выводы D0-D15 для формирования 16-ти разрядного кода аналогового напряжения.
- чтениепреобразование.
Рис. 17. Аналого-цифровой преобразователь ADS 7811.
При =1 и переходит в 0 то доступны биты выходных данных если не выполняется преобразование. При =0 и переходит в 0 то запускается преобразование если оно не выполняется в это время.
Падает в 0 когда запущено преобразование и остаётся в 0 пока преобразование не завершится.
При =0 =1 и =1 то выходные данные доступны и заперты т. е. не изменяются. [9]
Сведем параметры АЦП в таблицу 1.
D623 - недорогой инструментальный усилитель с однополярным питанием и уровнем сигналов от питания-до питания. AD623 имеет разводку стандартную для 8-контактного корпуса. Его коэффициент передачи устанавливается с помощью одного внешнего резистора. Величина коэффициента передачи может меняться в пределах от G=1 до G=1000. ( рис.18.)
медицинское оборудование низкого потребления;
обработка сигналов первичных преобразователей;
усилители сигналов с термопар;
системы промышленного управления;
системы сбора информации малого потребления;
дифференциальные усилители.
Параметры данного прецизионного микромощного инструментального усилителя:
Набор устанавливаемых коэффициентов передачи
Коэффициент подавления синфазной помехи
Малое время установления (до 001%)
Малое напряжение смещения
Малый дрейф напряжения смещения
Низкий уровень шумов (f=1кГц)
Низкое потребление при однополярном питании
Широкий диапазон питающих напряжений
Промышленный диапазон температур
Корпус 8-контактный для всех модификаций
Рис.18. Измерительный преобразователь AD623.
Микросхема представляет собой микромощный инструментальный усилитель общего применения обладающий прекрасными точностными параметрами. Гибкая структура из трёх операционных усилителей и малый размер делают его идеальным для множества применений. Единственный внешний резистор устанавливает любое усиление от1 до 10000. Внутренние цепи защиты входного каскада выдерживают напряжение до ±40 В без повреждения прибора. Усилитель сохраняет работоспособность при напряжении питания ±135 В. [9]
Сведем параметры усилителя в таблицу 2.
С тензодатчика поступает сигнал равный 20 мВ.
Напряжение от измерительного преобразователя которое необходимо подать на вход АЦП составляет 25 В.
Выходное напряжение:
Откуда коэффициент усиления реализуемый преобразователем:
Выберем в соответствии с рядом Е 192 значение сопротивления равное 806Ом 05 %.
Осуществим пересчет выходного напряжения для новых условий усиления:
9. Выбор устройства ввода-вывода
Ввод и вывод информации в МП-системах осуществляется как правило с помощью специальных БИС. Одной из наиболее употребляемых микросхем ввода — вывода является БИС параллельного периферийного адаптера на рис. 19 —это микросхема типа WDCW65C21S.
х 8-разрядный двунаправленный порт ввода вывода с индивидуальным контролем направления данных
Автоматический контроль передачи данных
выхода прерывания с программным управлением
контактов Dip Пластиковые и 44 в выводной пластмассовой PLCC версии
Совместимость с 65xx и 68xx семейства микропроцессоров
Замена для MotorolaFreescale Rockwell AMI MOS Technology MOSTEK HITACHI ST Microelectronics GTE CMD 6520 6521 6820 6821 PIAs
Параметры приведены в таблице 3.
Рис.19. Микросхема порта W65C21S
К портам А и В могут быть присоединены различные источники и приемники информации например аналого-цифровые и цифро-аналоговые преобразователи.
10. Расчет источника питания
Расчет источника питания проводится на основании требований по качеству питания электрической схемы.
Определим наиболее энергоемкие элементы схемы и сведем их в таблицу 4:
Характеристики потребителей по энергопотреблению.
U=5 B; Р=2652.875 мВт; I=530.575 мА
U=-5 B; Р=50 мВт; I=10 мА
На основании полученных данных выбираем в качестве стабилизаторов напряжения интегральные стабилизаторы напряжения КР1157ЕН8В и 79L05 позволяющие существенно сократить общее количество элементов блока питания при этом обеспечив высокие технологические характеристики.
Основные характеристики выбранных стабилизаторов напряжения представлены в таблице 5.
Характеристики стабилизаторов.
Максимальный ток нагрузки
Максимальная рассеиваемая мощность
Схема подключения интегральных стабилизаторов типовые и представлены на рис. 20:
Рис.20 Схема электрическая принципиальная блока питания
Конденсаторы С1 С2 и С5 выбираются в зависимости от потребляемого тока. Емкость выходных конденсаторов можно определить по упрощенному соотношению: 1000 мкФ на 1 A в цепи. Следовательно выбираем:
С9 - К50-35-16B-470 мкФ ОЖО.461.031. ТУ
С10 - К50-35-16B-150 мкФ ОЖО.461.031. ТУ
С11 С12- К50-35-16В-100 мкФ ОЖО. 464.214 ТУ
Выбираем диодный мост VD1 у которого значение выпрямленного тока и допустимого обратного напряжения равно или превышает расчетные. В качестве диодного моста VD1 выбираем диодную сборку. Диодную сборку выбираем с учетом номинальных токов потребления интегральных стабилизаторов. Диодную сборку выбираем по самой нагруженной цепи т.е. Iвх=500мА и принимаем КЦ405Е. Основные характеристики сборки приведены в таблице 6.
Характеристики диодной сборки КЦ405Е
Среднее прямое напряжение короткого замыкания
Средний обратный ток холостого хода при Uобр. = Uобр.max
Обратное максимально-допустимое напряжение Uобр.
С учетом падения напряжения на интегральных стабилизаторах а так же на диодной сборке определяем минимально допустимое значение напряжения вторичной обмотки трансформатора:
Из расчётов видно что для получения двухполярного напряжения +5В и -5В на вторичной обмотке трансформатора необходимо иметь две обмотки на напряжение не менее 87В т.к. используется двухполупериодная схема выпрямителя со средней точкой которая получается путём последовательного соединения двух обмоток с одинаковым напряжением.
С учётом потерь в обмотках трансформатора а также нестабильностью сетевого напряжения питания увеличиваем напряжение на вторичной обмотке на 10%. Принимаем напряжения на вторичной обмотке:
Далее выбираем трансформатор по максимальному току нагрузки Iн = 0.15А необходимому напряжению Uн = 5 В и габаритной мощности
Выбираем универсальный трансформатор для питания полупроводниковых приборов ТПП235 на 50Гц 127220В мощностью 9Вт ток первичной обмотки 017501А. Технические характеристики вторичных обмоток приведены в таблице 7.
Определим ток потребляемый от сети:
Для определения параметров плавкой вставки увеличим ток потребляемый от сети 23 раза:
Предохранитель FU1 выбираем с учетом тока срабатывания защиты в первичной обмотке следовательно - FU1 - ВП1-1 025-250.
Тумблер выбираем по допустимому напряжению и с учетом малого тока в первичной цепи трансформатора по механической прочности – П2Т-1-1.
С целью получения необходимых напряжений питания +5В и -5В соединяем последовательно следующие вторичные обмотки трансформатора ТПП235: 12-13 14-15. Получаем обмотку с выводом от средней точки и напряжением U2=20В что и требовалось по расчётам для получения необходимых уровней напряжений..
В ходе выполнения курсового проекта была спроектирована адаптивная система управления токарным станком с ЧПУ с датчиком усилия резания. Была спроектирована электрическая структурная и электрическая принципиальная схемы.
В дальнейшем адаптивная система может быть модернизирована в связи с развитием интегральной электроники.
В.Л. Сосонкин О.П. Михеев «Программное управление станками» - М.: Машиностроение 1981. – 398 с. ил.
В.Л. Сосонкин Ю.Е. Михеев «Системы автоматического управления станками» - М.: Машиностроение 1978. – 264 с. ил.
Федорков Б.Г. Телец В.А. Микросхемы ЦАП и АЦП их функционирование параметры применение. – М.: Энергоатомиздат 1990. – 320 с.: ил.
Рекомендуемые чертежи
- 17.03.2024
- 25.01.2023
- 19.10.2023