16А20Ф3С39 металлорежущий станок с ЧПУ NC-31





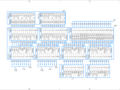
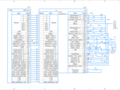
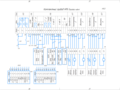
- Добавлен: 25.01.2023
- Размер: 352 KB
- Закачек: 0
Описание
Состав проекта
![]() |
![]() |
![]() ![]() ![]() ![]() |
![]() ![]() ![]() ![]() |
![]() ![]() ![]() ![]() |
![]() ![]() ![]() ![]() |
![]() ![]() ![]() ![]() |
![]() ![]() ![]() |
![]() ![]() ![]() ![]() |
![]() ![]() ![]() ![]() |
![]() ![]() ![]() ![]() |
![]() ![]() ![]() ![]() |
![]() ![]() ![]() |
![]() ![]() ![]() |
![]() ![]() ![]() ![]() |
![]() ![]() ![]() ![]() |
![]() ![]() ![]() ![]() |
![]() ![]() ![]() ![]() |
Дополнительная информация
12.cdw

11.cdw

07.cdw

09.cdw

13.cdw

Ввод и настройка параметров.doc
СТАНОК ТОКАРНЫЙ ПАТРОННО-ЦЕНТРОВОЙ
С ЧИСЛОВЫМ ПРОГРАМНЫМ УПРАВЛЕНИЕМ.
Инструкция по вводу и
настройке параметров.
МЕТОДИКИ ПОДБОРА ПАРАМЕТРОВ6
ЛИСТ РЕГИСТРАЦИИ ИЗМЕНЕНИЙ9
Данная инструкция предназначена для ввода и настройки параметров УЧПУ "Электроника НЦ-31-01" расширенной версии необходимых при запуске станков 16А20ФЗС39 и 16А20ФЗС39РМ или при искажении значении параметров во время эксплуатации станка.
Стандартные значения параметров УЧПУ описаны в:
Описание применения 589.4001008.0004-01 31 01.
Руководство программиста 589.4001008.0004-01 33 01.
Руководство оператора 589.400Ю08.0004-01 34 01.
Руководство оператора и
технолога программиста 589.400Д008.0004-01 90 01.
1. Инициализация параметров.
1.1. Установить режим ввода параметров
1.2. Записать параметр N40 G 1.
1.3. Последовательно нажать клавиши:
Примечание: инициализация параметров проводится всегда после появления кода ошибки 241ХХХ - сбой массива параметров.
2.Ввод и проверка параметров стыковки.
2.1. Установить режим просмотра параметров
и проверить соответствие параметров УЧПУ значениям приведенным в таблице 1.
Номер рабочей зоны архива УП
Номер квадранта программирования.
Скорость быстрых перемещений по оси X в автоматическом режиме (1 дискрета =2мммин).
Скорость быстрых перемещений по оси Z в автоматическом режиме (1 дискрета =2мммин).
Скорость быстрых перемещений по оси X в ручном режиме (1 дискрета =2мммин).
Скорость быстрых перемещений по оси Z в ручном режиме (1 дискрета =2мммин).
Калибровка скорости быстрых перемещений.
После изменения этого параметра необходимо повторно ввести параметры N2P N5P.
Ограничение рабочей подачи в ручном режиме величиной 28ммоб.
Калибровка минутной подачи.
Коэффициент усиления интегральной составляющей главного привода в режимах по функциям M19 и G15.
Калибровка диапазона M38 скорости вращения шпинделя.
Калибровка диапазона M40 скорости вращения шпинделя.
Калибровка диапазона M39 скорости вращения шпинделя.
Снятие маски с сигнала «Бл. ПО».
Для комплектного привода производства НБР дополнительно ввести:
Предельная величина рассогласования в первой зоне по оси Z.
Интенсивность изменения сигнала управления по оси Z.
Зона линейного управления по ошибке скорости по оси Z.
Адресный указатель масштаба коэффициента усиления по оси Z.
* - в таблице приведено максимальное значение параметра. Рабочее значение определяется потребителем.
** - подбирается после ремонта УЧПУ или приводов.
3. Если не используется функция ресурса инструмента по времени ввести следующие параметры.
3.1. Открыть область параметров T отведенных под ресурс инструментов.
N37 S=310 N38 S=2 N39 S=5270.
3.2. Записать в параметры N0 T N12 T число 1.
3.3. Открыть область параметров T отведенных для сопряжения УЧПУ со станком: N37 S=1017 N38 S=100001 N39 S=161.
МЕТОДИКИ ПОДБОРА ПАРАМЕТРОВ.
1. Настройка программы защиты от обрыва обратной связи.
После инициализации параметров параметры для программы защиты настроены для быстрых перемещений по оси Х=75ммин по оси Z=15ммин. Для других значений быстрых перемещений подбираются новые значения параметров.
1.1. Установить режим ввода параметров.
1.2. Снять с параметров группы М защиту ключом М 123456.
Для этого ввести параметр N32 S=1.
1.3. Установить в параметрах N4P и N5P значения быстрых перемещений с которыми будет работать станок в автоматическом режиме.
1.4. Установить режим специальной индикации N15 P=1 N9 M=7 индикация скоростной ошибки по оси X N10 M=10 - индикация скоростной ошибки по оси Z.
1.5.1. В ручном режиме задать ускоренное перемещение суппорта по оси Z в положительном а затем в отрицательном направлении. Запомнить величину и знак показаний индикатора для каждого направления.
1.5.2. Уменьшить значение параметра N15 M на 10 и повторить пункт 3.1.5.1.
1.5.3. Меняя значение параметра N15 М добиться того чтобы скоростная ошибка была минимальной. Параметр N15 М имеет восьмеричное представление. Дискретность изменения параметра равна 1.
1.5.4. Увеличить минимальное значение скоростной ошибки на 10%. Ввести получившуюся величину в параметр N9 F.
1.5.5. Если значение параметра N9 F окажется недостаточно большим то при перемещении на быстром ходу по оси Z движение прекратится и УЧПУ выдаст код ошибки 05XX1X.
1.6. Аналогично подбираются параметры N14 M и N8 F для оси X. При срабатывании программы защиты от обрыва обратно связи УЧПУ дает код ошибки 04XX1X.
1.7. После окончания настройки установить параметра N9 M=3 N10 M=4 N15 P=0 N32 S=100001.
2. Настройка главного привода.
2.1. Снять с параметров группы T защиту ключом M 123456. Для этого ввести параметр N32 S=1.
2.2. Для диапазона М40.
2.2.1. Перейти в ручной режим подать команды M40 M3 S1500.
Замерить тахометром скорость вращения шпинделя.
2.2.2. Если частота вращения шпинделя отличается от заданной величины то перейти в режим ввода параметров и изменить значение параметра N38 Т не меняя значения параметров N98 Т и N22 Т. Диапазон изменения параметра N38 Т от 7000 до 4000 с шагом 10. Представление параметра N38 Т восьмеричное.
2.2.3. Перейти в ручной режим падать команду S1500 и измерить тахометром скорость вращения шпинделя.
2.2.4. Если частота вращения шпинделя отличается от заданной величины повторить п. п. 3.2.2.2. и 3.2.2.3.
2.3. Для настройки диапазонов М38 и М39 значения параметров N22 Т и N38 Т не изменять т. к. они влияют на все три диапазона М38 M39 М40.
2.4. Для диапазона M39.
2.4.1. Перейти в ручной режим подать команды М39 М3 S500. Замерить тахометром скорость вращения шпинделя.
2.4.2. Если частота вращения шпинделя больше (меньше) заданной перейти в режим ввода параметров и уменьшить (увеличить) значение параметра N110 Т. Возможные значения параметра приведены в табл. 2.
2.4.3. Перейти в ручной режим подать команду М39 замерить тахометром скорость вращения шпинделя.
2.4.4. При необходимости повторить п. п. 3.2.4.2 3.2.4.3.
2.5. Для диапазона М38.
2.5.1. Перейти в ручной режим подать команды М38 МЗ S200 измерить тахометром скорость вращения шпинделя.
2.5.2. Если скорость больше (меньше) заданной перейти в режим ввода параметров и уменьшить (увеличить) значение параметра N96 Т. Возможные значения параметра N96 Т приведены в табл. 2.
2.5.3. Перейти в ручной режим подать команду М38 замерить тахометром скорость вращения шпинделя
2.5.4. При необходимости повторить п. п. 3.2.5.2 и 3.2.5.3.
2.6. Установить защиту ключом М 123456 для параметров группы Т. Для этого ввести параметр N38 S=100001.
3. Настройка функции постоянства скорости резания G96 производится после выполнения п.3.2.
Скорость резания в УЧПУ рассчитывается по формуле:
n - частота вращения шпинделя обмин;
S - скорость резания ммин.
3.2. В режиме привязки инструмента установить значение координаты X равное 19100 мм.
3.3. Перейти в ручной режим подать команды S30 М3 и замерить тахометром скорость вращения шпинделя. Расчетная величина скорости равна 500 обмин.
3.4. Если частота вращения шпинделя больше (меньше) расчетной величины то перейти в режим ввода параметров и уменьшить (увеличить) значение параметра N39 Т. Диапазон изменения от 10000 до 70000 с шагом 10.
3.5. Перейти в ручной режим подать команду S30 и замерить тахометром скорость вращения шпинделя.
3.6. Если частота вращения шпинделя отличается от расчетной величины то повторить п.п. 3.3.4. и 3.3.5.
4Методика ввода параметров коррекции накопленной
погрешности осевых перемещений.
В матобеспечении УЧПУ «Электроника НЦ-31-02» используемых на станках 16А20Ф3С39 предусмотрена возможность коррекции накопленной погрешности осевых перемещений (см. «Руководство оператора и технолога программиста» 589.4001008.0004-01 90 01 раздел 14 «Коррекция кинематики станка»).
Параметры коррекции при необходимости должны вводиться входе эксплуатации станка в энергонезависимую память УЧПУ при отключении станка более чем на 100 часов информация пропадает. Параметры рассчитываются на основе замеров отклонения фактических перемещений от запрограммированных с использованием в качестве отсчетной базы положение суппорта при останове по кулачку фиксированного положения. Кулачек устанавливается наладчиком станка при наладке на определенную группу деталей. При перестановке кулачка после ввода параметров коррекции или при перестановке датчика обратной связи необходимо во избежание ошибок при отработке перемещений аннулировать ранее введенные параметры и при необходимости ввести новые параметры на базе нового фиксированного положения суппорта.
Параметры коррекции на заводе-изготовителе не вводятся.
Для определения параметров коррекции по каждой оси длинна рабочего перемещения разбивается на участки соответственно выбранному шагу коррекции. Замер отклонений перемещения в зависимости от требований к изделию производится по всей длине перемещения. При этом коррекция автоматически отрабатывается только на участке для которого вводился определенный параметр. Для ввода коррекции на следующих участках (в случае если на них не производились отдельные замеры) нужно повторить значение коррекции от последнего предыдущего замеренного участка.
Шаг ввода коррекции задается значениями параметра N 338 T для оси X N 331 T для оси Z. Значения шага выбираются из таблицы 1.
При сбое параметров код ошибки 241ХХХ область Т параметров обнуляется.
Для ввода величины коррекции задаются параметры:
4.1. Определение погрешности перемещения и ввод параметров по оси X следует производить в следующей последовательности (при шаге 4096мкм).
4.1.1. По команде М31 вывести суппорт фиксированное положение.
4.1.2. Нажать на клавишу «Режим привязки» и ввести значение X=0.
4.1.3. На скорости 1ммин вывести суппорт на кулачек ограничения перемещения в направлении –X.
4.1.4. Показание на индикации УЧПУ в этом положении взятые по модулю разделить на 8200(удвоенное для перевода в диаметр и округленное для облегчения расчетов значение шага 4096). Результат обозначим через А. Округлить до целого числа в большую сторону.
4.1.5. По номеру T-параметра равному 335+А в колонке 2 табл.2 найти его десятичный адрес (например: 335+24=359 адрес равен 674) и записать его в параметр N 332 T.
4.1.6. Переместить суппорт по индикации в положение с координатой .
4.1.7. Нажать на клавишу привязки инструмента и ввести значение X равное 0.
4.1.8. Записать управляющую программу для цикла автоматической отработки перемещения с выбранным шагом ввода коррекции.
N02 X –20000выборка люфта
N05G 4*выдержка времени для снятия показаний
N08 P 4096*количество повторений уточняется для
N09P 55конкретного станка
Примечание: перемещения по координатам в программе абсолютные.
4.1.9. Установить измерительный прибор для контроля перемещений и включить отработку программы с нулевого кадра. После отработки кадра N04 определить погрешность перемещения в микронах как разность между показаниями на индикации УЧПУ и показаниями измерительного прибора умноженными на 2(приведенные к значению диаметра).
Погрешность перемещения со знаком + или – заносится в колонку 4 табл.2. Напротив параметров от 334 Т до 339 Т в колонке 4 табл.2 записываются нули.
Первое значение погрешности записывается напротив параметра 340Т. Следующее значение напротив 341Т и так далее.
После отработки кадров N10 и N11 погрешность перемещения записываются в колонку 5 табл.3 в обратном порядке. Первое значение погрешности записываются сразу же после отработки кадров N10 и N11 напротив последней записи в колонке 4 табл.2. Последующие значения погрешности записываются в порядке номера параметра.
Последнее значение погрешности при движении в направлении – Х записывается напротив параметра 339Т.
4.1.10. Для получения достоверного результата наблюдать погрешность перемещения 5 раз.
4.1.11. Заполнить колонку 6 табл.2. В колонку 6 заносится среднее арифметическое значение между соответствующими значениями в колонках 5 и 4 табл.2.
Примечание. Данное вычисление проводится потому что в УЧПУ отработка коррекции не зависит от направления движения суппорта.
4.1.12. Напротив последних параметров в табл.2 для которых не производилось измерение погрешности в колонке 6 повторяется последняя запись.
4.1.13. Ввести в УЧПУ значения параметров от 334Т до 397Т согласно колонке 6.
4.2. Определение и ввод параметров по оси Z.
4.2.1. По команде М32 выйти в фиксированное положение по оси Z.
4.2.2. Установить привязку по оси Z в фиксированном положении Z=0.
4.2.3. На скорости равной 1 ммин вывести каретку на кулачек ограничения перемещения в направлении минус Z.
4.2.4. Показание индикатора по оси Z взятое по модулю поделить на число 8200. Полученный результат округлить до целого в большую сторону.
4.2.5. По номеру Т-параметра равному 399+B из таблицы 3 колонки 2 определить его десятичный адрес и записать этот адрес в параметр 333Т.
4.2.6. Установить по индикации каретку в положение с координатой Z равной
4.2.7. Ввести в том положении привязку по оси Z равную нулю.
4.2.8. Записать управляющую программу:
N02 Z -20000выборка люфта
N05 G 4*выдержка времени для снятия показаний
N08 P 4006*количество повторений числа шагов
N09 P 119ввода коррекции уточняется для конкрет-
N10 Z 20000ного станка
4.2.9. Установить измерительный прибор для контроля перемещений и включить отработку программы с нулевого кадра. После отработки кадра N04 определить погрешность перемещения в микронах как разность между показаниями на индикации УЧПУ и показаниями измерительного прибора.
Погрешность перемещения со знаком + или – заносится в колонку 4 табл.3. Напротив параметров от 398 Т до 403 Т в колонке 4 табл.3 записываются нули.
Первое значение погрешности записывается напротив параметра 404Т. Следующее значение напротив 405Т и так далее.
После отработки кадров N10 и N11 погрешность перемещения записываются в колонку 5 табл.3 в обратном порядке. Первое значение погрешности записываются сразу же после отработки кадров N10 и N11 напротив последней записи в колонке 4 табл.3. Последующие значения погрешности записываются в порядке убывания номера параметра.
Последнее значение погрешности при движении в направлении – Z записывается напротив параметра 403Т.
4.2.10. Для получения достоверного результата наблюдать погрешность перемещения 5 раз.
4.2.11. Заполнить колонку 6 табл.3. В колонку 6 заносится среднее арифметическое значение между соответствующими значениями в колонках 5 и 4 табл.3.
4.2.12. Напротив последних параметров в табл.3 для которых не производилось измерение погрешности в колонке 6 повторяется последняя запись.
4.2.13. Ввести в УЧПУ значения параметров от 398Т до 525Т согласно колонке 6.
4.2.14. Установить десятичное значение параметра 331Т=32733.
Проверить правильность введенных параметров от 334Т до 525Т и установить параметр
После установки параметра N83 отработка будет осуществляться с учетом погрешности перемещения записанных в параметрах 334Т-525Т.
Для отключения параметров 334Т-525Т установить параметр
Индикацию действующих на данном интервале значения величин коррекции можно подключить установкой параметров:
В скобках указанны исходные значения параметров которые должны быть установлены для индикации абсолютного положения инструмента.
После окончания ввода величин коррекции в Т-параметры установить параметр N28S=100001.
При выборе шага коррекции больше минимального в управляющей программе перемещения для определения погрешности увеличиваются во столько раз во сколько увеличивается шаг коррекции. При этом количество Т-параметров в которые надо заносить погрешность уменьшается в соответствующее количество раз.
Так как методика ввода коррекции является достаточно сложной и трудоемкой и требует повторения после отключения или переналадки станка то использовать ее следует только в обоснованных случаях повышенных требований к точности обработки деталей.
01.cdw

"С239"-16А20Ф3С239.Э3.2.
Необходимое усилие зажима резцедержки достигается регулировкой тока реле
Питание главного приво-
10.cdw

PRIL2.frw

06.cdw

Руководство по эксплуатации.doc
СТАНОК ТОКАРНЫЙ ПАТРОННО-ЦЕНТРОВОЙ
С ЧИСЛОВЫМ ПРОГРАМНЫМ УПРАВЛЕНИЕМ.
Руководство по эксплуатации
(электрооборудование).
КРАТКАЯ ХАРАКТЕРИСТИКА ЭЛЕКТРООБОРУДОВАНИЯ 4
СВЕДЕНИЯ О СИСТЕМЕ ПИТАНИЯ ЗЛЖТРООВОРУДОВАНИЕ 5
СВЕДЕНИЯ О ПЕРВОНАЧАЛЬНОМ ПУСКЕ 6
УСТРОЙСТВО И ПРИНЦИП РАБОТЫ БЛОКА УПРАВЛЕНИЯ 12
СВЕДЕНИЯ О БЛОКИРОВКАХ СИСТЕМЕ СИГНАЛИЗАЦИИ
МЕРЫ БЕЗОПАСНОСТИ 23
ОВЕДЕНИЯ О РАСЦВЕТКЕ ПРОВОДОВ 24
ХАРАКТЕРНЫЕ НЕИСПРАВНОСТИ И МЕТОДЫ ИХ
ТЕХНИЧЕСКОЕ ОБСЛУЖИВАНИЕ 27
СВЕДЕНИЯ О НАЛИЧИИ ДРАГОЦЕННЫХ МЕТАЛЛОВ 29
Руководство по эксплуатации не отражает незначительных конструктивных изменений в оборудовании внесенных изготовителем после подписания к выпуску в свет данного руководства а также изменений по комплектующим изделиям и документации поступающей с ними.
I. КРАТКАЯ ХАРАКТЕРИСТИКА ЭЛЕКТРООБОРУДОВАНИЯ.
Электрооборудование включает в себя:
устройство числового программного управления УЧПУ) для управления циклом обработки детали;
электропривод асинхронный глубоко регулируемый комплектный для управления приводами подач и приводом главного движения;
электродвигатели для управления приводами резцедержки патрона охлаждения пиноли смазки направляющих смазки шпиндельной бабки транспортера стружкоудаления;
фото импульсные датчики контроля перемещения по осям и резьбонарезания;
аппараты защиты управления и сигнализации;
другие аппараты и устройства осуществляющие коммутацию подсоединение электрических цепей и управление механизмами.
Технические характеристики УЧПУ датчиков электродвигателей
см. 16А20Ф3. РЭ раздел 2.
Электрооборудование станка выполнено в соответствии с требованиями ГОСТ 12. 2. 009-80 и ГОСТ 7599-83 и соответствии схем:
А20Ф3С39. ЭЗ - схема электрическая принципиальная;
А20Ф3. 192501. 000. Э3 - блок управления. Схема электрическая принципиальная;
А20Ф3С39 Э4 - схема электрическая соединений.
Состав основного электрооборудования указан в перечнях элементов: 16А20Ф3С39. ПЭ3 и 16А20Ф3. 192501. 000 ПЭ3 Блок управления.
СВЕДЕНИЯ О СИСТЕМЕ ПИТАНИЯ
ЭЛЕКТРООБОРУДОВАНИЯ.
Электрооборудование станка работает от сети трехфазного переменного тока с напряжением 380В +10% -15% и частотой 50Гц 2% с глухо заземленной нейтралью.
На станке используется переменный и постоянный ток со следующими параметрами:
~50Гц 380В цепи асинхронных электродвигателей питание комплектного электропривода трансформаторов управления.
~50Гц 220В - цепи вводного пускателя УЧПУ вентиляторов.
~50Гц 110В - цепи управления.
~50Гц 24В - цепи местного освещения и сигнализации.
- 24В - цепи управление и сигнализации.
Возможны поставки станка на напряжение и частоту питающей сети в соответствии с заказом.
СВЕДЕНИЯ 0 ПЕРВОНАЧАЛЬНОМ ПУСКЕ.
К обслуживанию электрооборудования станка допускаются лица прошедшие специальный технический инструктаж изучившие работу срабатывания цепей электроавтоматики и направление вращения электродвигателя. Электрооборудования станка. Перед установкой станка необходимо проверить комплектность электрооборудования произвести его внешний осмотр.
1. Установка станка.
Проверить затяжку винтов (крепежных и контактных) и закрепить соединения ослабленные при транспортировке. Особое взимание обратить на контактные винты проводов заземления.
Выполнить монтаж электрооборудования согласно п. 9.
Ввод питающих проводов в шкаф управления выполняется заказчиком через вводное отверстие (фланец Ду=34") на крыше шкафа.
Сечение медных проводов питания и защитного заземления подключаемых заказчиком к вводному клемнику ХТ-50 равны 10 мм.
Заземление станка выполнить согласно требованиям "Правил устройств электроустановок".
Подключить станок к цеховой питающей сети.
2. Первоначальный пуск.
При первоначальном пуске необходимо:
включить автоматический выключатель QF2 в шкафу 1;
подать напряжение на станок при помощи вводного автоматического выключателя QF1 и кнопки SB1.
По наличии сигнала "Готовность УЧПУ" приступить к проверке работы отдельных устройств станка. Работу узлов станка проверить в ручном режиме УЧПУ.
Все команды на включение узлов станка вводятся с пульта оператора УЧПУ. Порядок ввода информации и отработка изложены в "Инструкции по эксплуатации на УЧПУ" и в "Руководстве оператора".
2. 1. Проверка работы насоса охлаждения.
На пульте станка переключатель SA6 "Охлаждение" установить в положение "Вкл.
На пульте оператора УЧПУ ввести команды для включения отработки функции M08. При выходе команды с УЧПУ срабатывает электроавтоматика станка в следующей последовательности: блок управления АЗ пускатель KM10 электродвигатель М9 (насос охлаждения). Правильность работы насоса охлаждения проверяется наличием потока СОЖ. При отсутствии потока проверить наличие выхода сигнала М08 из УЧПУ правильность срабатывания цепей электроавтоматики и направление вращения электродвигателя.
2. 2. Проверка работы системы смазки направляющих.
Электродвигатель смазки направляющих включается автоматически при подаче питания на станок. Цикл смазки направляющих – время смазки 3 сек. время паузы 45 минут - задается УЧПУ. При выдаче команды с УЧПУ срабатывает электроавтоматика станка в следующей последовательности: блок управленияпускатель КМ11 электродвигатель М10. Правильность работы системы смазки проверяется наличием масла в соответствующих точках (см. 16А20Ф3 РЭ) станка.
При отсутствии масла в этих точках проверить правильность
В станке предусмотрен бочковый режим смазки направляющих от кнопки SB7 действующей в любом режиме работы станка.
2. 3. Проверка работы электромеханического патрона.
На пульте станка переключатель SA3 "Работа с зажимными электромеханическими устройствами'' установить в соответствующее положение.
Управление кулачками патрона осуществляется педалью SA4. Прохождение команды от педали возможно только при отключенном шпинделе.
Команды от педали проходят через электроавтоматику станка
в следующей последовательности: "Кулачки к центру" - реле KV7 пускатель KM6 электромеханическая головка М7; "Кулачки от центра" - реле KV6 пускатель КМ7. электромеханическая головка М7.
Правильность работы кулачков патрона определяется перемещением в нужном направлении кулачков. Контроль усилия зажима кулачков контролируется конечным выключателем SQ12 установленным в электромеханической головке.
При отсутствии перемещения кулачков патрона проверить исправность цепей электроавтоматики и работу электродвигателя проверить соответствие движения кулачков по нажатию педали в выбранном направлении.
2. 4. Проверка работы электромеханической пиноли.
На пульте станка переключатель SA3 "Работа с зажимными
электромеханическими устройствами" установить в соответствующее
Подвод и отвод пиноли осуществляется педалью SA5. Прохождение команды от педали возможно только при отключенном шпинделе.
Команды от педали проходят через электроавтоматику в следующей последовательности: "Подвод пиноли" - реле KV2 пускатель KM8 электромеханическая головка M8 "Отвод пиноли" - реле KV4 пускатель KM9 электромеханическая головка M6.
Правильность работы пиноли определяется перемещением пиноли
в нужном направлении. Контроль усилия поджима пиноли контролируется микро выключателем SQ13 установленным в электромеханической головке.
При отсутствии перемещения пиноли проверить исправность
цепей электроавтоматики и работу электродвигателя проверить соответствие движения пиноли по нажатию педали в выбранном направлении.
2.5. Проверка работы смазки шпиндельной бабки.
Цикл работы смазки непрерывный. При подаче питания на станок блок управления АЗ выдает команду в электроавтоматику станка в следующей последовательности: пускатель KM2 электродвигатель М11.
Правильность работы системы смазки проверяется по вращению турбинки со стрелков в "Глазке" шпиндельной бабки. При отсутствии масла в шпиндельной бабке проверить правильность срабатывания цепей электроавтоматики и направление вращения электродвигателя.
2.6. Проверка работы автоматической резцедержки.
На пульте оператора УЧПУ ввести необходимые команды для смены позиции резцедержки.
При выходе команды с УЧПУ срабатывает электроавтоматика станка в следующей последовательности: блок управления АЗ пускатель KM4 электродвигатель М6. Происходит поворот резцедержки до заданной позиции. Контроль совпадения позиций осуществляет датчик положения SQ10 встроенный в резцедержку сигнал от которой поступает в блок управления АЗ где формируется команда на реверс и выдается в электроавтоматику станка в следующей последовательности: пускатель КМ5 электродвигатель М6. Окончание реверса и
зажима резцедержки контролируется микропереключателем SQ11 и токовым реле КА1 команда от которых поступает в блок управленияи далее в УЧПУ.
Если резцедержка не поворачивается то необходимо проверить наличие выходных сигналов с УЧПУ правильность срабатывания цепей электроавтоматики.
2.7. Проверка работы приводов подач.
Перед проверкой работы приводов подач установить кулачки для воздействия на конечные выключатели ограничения хода и аварийного отключения каретки SQ4 SQ5 суппорта SQ3.
Запрещается задавать перемещения суппорта каретки при отсутствии кулачков во избежание поломки инструмента или станка.
Включить привода нажатием кнопки SB5.1 после чего должна загореться лампа встроенная в кнопку.
В процессе работы необходимо:
проверить действие кнопки аварийного отключения SB2 действие конечных выключателей ограничения перемещений и аварийного останова SQ3 SQ4
проверить управление механизмами перемещений осуществляемых при помощи регулируемых электроприводов. Для правильного пуска электроприводов ознакомиться с техдокументацией на них;
на пульте оператора УЧПУ ввести необходимые команды для отработки перемещения с заданной скоростью. Порядок ввода информации и отработка изложены в "Руководстве оператора";
на небольших скоростях перемещения провести проверку срабатывания конечных выключателей SQ3 SQ4 SQ5 ограничения перемещения и аварийного отключения по осям X и Z;
проверить работу схемы съезда с конечных выключателей SQ3 SQ4 SQ5 ограничения перемещения заданием противоположного направления;
проверить схему отвода суппорта и каретки из положения наезда на конечные выключатели аварийного отключения заданием противоположного направления и удержания кнопки SB5 в нажатом положении.
При отсутствии перемещения проверить цепи электроавтоматики работу электропривода руководствуясь техдокументацией на электропривод.
2.8. Проверка работы привода главного движения.
Перед проверкой главного привода проконтролировать срабатывание микропереключателей SQ7 SQ8 диапазона частоты вращения шпинделя.
При совпадении заданного от УЧПУ диапазона скоростей с выбранным от микропереключателей логическая часть схемы электроавтоматики разрешает включить вращение шпинделя. При несовпадении – следует проверить правильность срабатывания цепей электроавтоматики и правильность установки кулачка диапазона.
На пульте оператора УЧПУ ввести необходимые команды вращения шпинделя. Порядок ввода информации и ее отработка изложены в "Инструкции по эксплуатации УЧПУ" и "Инструкции по программированию" 16А20ФЗС39.ИП. Для правильного пуска главного привода необходимо ознакомиться с техдокументацией на электропривод. В станке управление приводом главного движения осуществляется при помощи регулируемого электропривода.
При выдаче с УЧПУ команд о направлении вращения и величине скорости шпинделя через преобразователь электропривода включаются соответствующие направление и скорость вращения двигателя.
При отсутствии вращения привода главного движения проверить соответствующие цепи электроавтоматики и работу электропривода руководствуясь техдокументацией на привод.
На станке предусмотрен толчковый режим работы шпинделя от кнопки SB3. Данный режим срабатывает только при отсутствии команд от УЧПУ на вращение шпинделя и выполняется после окончания торможения.
На станке имеется возможность останова шпинделя переключателем SA1. При возвращении переключателя в первоначальное положение вращение восстанавливается. При резьбонарезании контроль синхронности вращения двигателя главного движения и скорости перемещения по координатам контролируется датчиком резьбонарезания BV2.
После окончания проверки всех функциональных узлов станка можно приступить к работе станке в покадровом и автоматическом режимах.
Для выключения станка необходимо рукоятку привода вводного выключателя QF1 установить в положение "Выключено".
При этом следует учитывать что в соответствии с "Инструкцией по эксплуатации" УЧПУ (0.170.000 ИЭ) подзарядку аккумуляторов нужно производить 1 раз в 5 суток.
29. Работа транспортера стружкоудаления.
Для работы транспортера со станка подаются напряжения:
цепей управления 24В постоянного тока или ~ 110В. (в зависимости от типа).
Управление транспортером производится от органов управления расположенных на шкафу управления транспортером.
Работа транспортера описана в техдокументации на транспортер.
УСТРОЙСТВО И ПРИНЦИП РАБОТЫ БЛОКА УПРАВЛЕНИЯ.
При изучении работы блока управления (в дальнейшем - БУ) 16А20Ф3.192501.000 необходимо дополнительно пользоваться схемой принципиальной электрической 16А20Ф3С39.33 (станок токарный программный с оперативной системой управления).
Блок управления собран на интегральных микросхемах серии К511 предназначенной для работы в устройствах промышленной электроавтоматики в условиях сильных электрических помех.
Через разъем XI на БУ поступает информация от УЧПУ которая контролируется по светодиодам HL1-HL12.
Резисторы R1-R12 R25. R41 служат нагрузкой для выходных оптронов УЧПУ.
Через разъем Х2 на УЧПУ поступает информация со станка. Сигналы от микросхем на УЧПУ подаются через оптроны V3 V6-V8 V11-V13 и контролируются по светодиодам HL-13 HL15-HL18 HL20.
Сигнал от УЧПУ "Готовность ЧПУ" уровнем лог.1 сбрасывает три триггеры резцедержки (D18.1-D17.3) главного привода (D 29.2-D31.3). Смазочно-охлаждающей жидкости (СОЖ) (D15.3 - D16.3) блокирует импульсный сигнал от УЧПУ "Импульс смазки" и сигнал включения приводов подач (светодиоды HL14 и HL19 погашены) а также через микросхему D22.2 размыкает герконовое реле K5.
Сигнал "Готовность ЧПУ" уровнем лог. «0» снимает блокировку с сигнала "Импульс смазки" переводит в проводящее состояние оптроны V5 и V2 (светодиоды HL14 и HL9 загораются после срабатывания пускателей KV5 и KV1 соответственно) и замыкает герконовое рале K5. Геркон K5 управляет пускателем KM2 который включает двигатель смазки шпиндельной бабки.
После появления сигнала "Готовность ЧПУ уровнем лог. «0» с УЧПУ подается импульсный сигнал "Импульс смазки" который замыкает герконовое рале К1. Геркон К1 управляет пускателем КМ1 который включает двигатель смазки направляющих. Длительность и период повторения сигнала "Импульс смазки" определяется параметрами УЧПУ (параметры N20Т и N21Т). Включение двигателя смазки направляющих возможно также через вход Х6:В22 («Толчок смазки направляющих» от кнопки на станке).
На рис.1 .приведена диаграмма выдачи информации от УЧПУ на БУ.
Цикл обращения к БУ начинается с установки в лог. "0" сигнала БСМ или БСТ. После этого в течение времени t1 ответный сигнал на УЧПУ РВК (разрешение ввода кадра) должен установиться в лог."0".
Если этого не будет то на этом цикл обращения к БУ прекращается и УЧПУ выдает сообщение об ошибке. Через время t1 (величина t1 определяется параметром N21S) УЧПУ устанавливает восьмиразрядный двоично-десятичный код на шинах данных. Затем устанавливается в лог. "0" сигнал от УЧПУ "Считывание". Через время t2 сигнал БСМ (БСТ) устанавливается в состояние лог. "1". Через следующий временной интервал (величина t2 определяется параметром N19М) сигнал "Считывание" устанавливается в состояние лог. "1". Код на шинах данных снимается после того как сигнал РВК установится в состояние лог. "1". Если сигнал РВК не будет установлен в состояние дог. "1".после окончания интервала t3 то УЧПУ снимает код с шин данных и выдает на ПО сообщение об ошибке (код ошибки XXXXIXX). Длительность интервала t3 определяется параметром N29М.
В БУ передний фронт РВК формируется микросхемой D37 на входы которой подаются сигналы БСМ и БСТ. Светодиод HL17 светится когда на УЧПУ выдается сигнал РВК уровнем лог. "1". Длительность сигнала РВК определяется временем срабатывания исполнительных устройств в станке и формируется схемами сравнения (D19.2-D19.4 D21.1- D21.3 D23.1- D23.3 D33.3-DЗ3.3) триггером резцедержки (D17.3-D18.1). Если подаваемая от УЧПУ М-команда не отрабатывается на станке то длительность сигнала РВК равна длительности сигнала БСМ.
В БУ дешифрируются следующие команды:
ТО Т12 - смена инструмента (Т0 и Т1 выполняются одинаково);
М3 М4 - включение привода главного движения;
М5 - отмена команд М3 М4;
М8 - включение двигателя СОЖ;
М9 - отмена команды М8;
М30 - отмена команд М3 М4 М8;
М35 - пуск робота по первой программе;
М40М38 М39 - контроль положения редуктора шпиндельной бабки;
М45 - пуск робота по второй программе.
На микросхеме D3 дешифрируются четыре старших разряда кода команды. На микросхемах D5 D6.1D7 дешифрируются сигналы с микросхемы D3 и буквенные подадреса (БСМ БСТ). Этими сигнала ми стробируются по выводу питания дешифраторы D8 - D12. На входы D8 - D12 подаются четыре младших разряда кода команды. Дешифрированный сигнал с выхода D8-D12 уровнем лог. "0" подается на соответствующий триггер. Ложные импульсы на выходах дешифраторов D8-D12 возникающих во время переходных процессов при стробировании дешифраторов блокируются конденсаторами С1-С8.
М - команды по которым производится управление устройствами станка запоминаются в БУ по остальным М - командам в УЧПУ выдается только ответный сигнал РВК.
Алгоритм работы БУ построен таким образом что прежде чем будут отработаны любые М (Т) - команды триггеры диапазонов (D15.1 - D16.1 D15.3 - D16.2) должны быть установлены одной из команд М36 М39 М40 в состояние соответствующее выбранному положению редуктора шпиндельной бабки. Контроль положения редуктора осуществляется через входы БУ 'Контакт Д1" и "Контакт Д2".
На лог. элементах D19.2 - D19.4 и D21.1 - D21.3 собраны схемы выполняющие лог. функцию сложение по модулю два. На выходах этих схем устанавливается уровень лог. "1" в том случае если на вход поступают сигналы одинакового лог. уровня. Уровнем лог. "0'' блокируется сигнал РВК.
В таблице 1 приведены состояния триггеров диапазонов после отработки команд контроля положения редуктора шпиндельной бабки.
Команды М38 М39 дешифрируются микросхемой D9 а команда М40 - микросхемой D10.
Команда М8 дешифрируется микросхемой D88 и запоминается на триггере СОЖ (D15.3 - D16.3). С выхода триггера СОЖ сигнал через элемент D16.4 поступает на элемент D22.1 который нагружен на обмотку горконового реле К2. Геркон К2 вызывает срабатывание пускателя КМ10. На входы схемы сравнения (D23.1- D23.3) подаются сигналы о лог. элемента D22.1 и через вход "Ответ М8" с контактов пускателя КМ10. Включение двигателя СОЖ возможно также от кнопки на станке через вход "Толчок охлаждения".
Сигнал с триггера СОЖ может быть заблокирован с помощью лог. элемента D16.4 через вход "Стоп шпинделя" от кнопки на станке.
Команды МЗ М4 дешифрируются микросхемой D8 и запоминаются на триггере главного привода (D31.3 - D29.2). С выхода триггера главного привода сигнал через триггер ограждения (D29.3 - D38.2) поступает на элемент D35.1 который нагружен на обмотку герконового реле К6. Геркон К6 управляет пускателем KV1. После срабатывания KV1 загорается светодиод HL19. На входы схемы сравнения (D33.1 – D33.3) подаются сигналы с элемента D35.1 и через вход
Ответ МЗ М4" с контактов пускателя KVI.
Сигнал с триггера главного привода может быть заблокирован от кнопки на станке через вход "Стоп шпинделя". Сигнал "Стоп шпинделя" без задержки подается на вход УЧПУ "Блокировка главного привода" (светодиод HL16 гаснет). По этому сигналу УЧПУ задает на привод нулевую скорость. Чтобы обеспечить торможение шпинделя электрическим полем сигнал "Стоп шпинделя" задерживается на RC - цепочке. Величина задержки определяется временем разряда конденсатора C15 через резистор R76. После этого блокируется
сигнал с триггера главного привода. К этому моменту на входе "Nф=Nз" появляется сигнал который поддерживает пускатель KV1 включенным до тех пор пока шпиндель не остановится. Сигнал "Nф=Nз" (заданная скорость равна фактической) поступает из привода нормально разомкнутыми контактами. Сигнал "Готовность привода" блокирует сигнал "Nф=Nз" при неисправности приводов.
Через элемент D35.2 подключается индикаторная лампа установленная на пульте управления станком. Постоянное свечение лампы свидетельствует о том что главный привод включен.
Триггер ограждения (D29.3-D38.2) блокирован во всех режимах работы УЧПУ кроме автоматического поэтому на отработку команд МЗ М4 не влияет.
При автоматическом режиме работы УЧПУ на входе "Автоматический режим" устанавливается сигнал уровнем лог. "0". При этом снимается блокировка с триггера ограждения и с сигнала контроля положения ограждения на входе "Ограждение".
При подключении переключателя режима контроля ограждения к входу БУ в "Режиме наладка" возможны два режима контроля ограждения:
Переключатель режима контроля ограждения на пульте управления находится в положении наладки (на входе БУ "Режим наладки" лог. "0").
В этом случае команда МЗ (М4) запоминается на триггере главного привода но сигнал с него не проходит через триггер ограждения до тех пор пока ограждение остается открытым (на входе "Ограждение" лог. "1"). Когда ограждение будет закрыто (на входе "Ограждение" лот. "0") триггер ограждения пропустит сигнал с триггера главного привода. Если вновь ограждение открывается то состояние триггера ограждения не изменяется до отработки команды М5.
Переключатель режима контроля ограждения в рабочем положении (на входе БУ "Режим наладки" лог. "1"). В этом случае необходимо закрыть ограждение раньше чем на пульте оператора УЧПУ будет нажата кнопка автоматического режима. Если ограждение будет открыто во время выполнения управляющей программы то сигнал "Ограждение" будет передан в УЧПУ как сигналы "Прерывание подачи" и "Блокировка главного привода" (светодиоды HL15 HL16 гаснут) на вход УЧПУ будет подан импульсный сигнал "Готовность станка'' (при этом на пульте оператора УЧПУ появится код 77X1XX) в БУ будут сброшены триггеры СОЖ и главного привода.
Для работы с роботом в этом режиме на разъеме Х7 предусмотрен вход "Блокировка ограждения". Т.к. УЧПУ при совместной работе с роботом всегда работает в автоматическом режиме то прежде чем робот откроет ограждение он должен подать сигнал блокировки ограждения (уровнем дог. "0").
В данном варианте станка переключатель режима контроля ограждения подключен параллельно конечнику ограждения поэтому первый режим контроля ограждения не осуществляется.
Включение привода главного движения возможно через вход "Кнопка толчок шпинделя" от кнопки на станке. При этом на УЧПУ подается сигнал "Толчок шпинделя'' для отработки программы толчковой кнопки. Для работы с роботом аналогичный вход предусмотрен на разъеме Х7 - "Толчок шпинделя".
Сигнал "ППВ" (привода подач включены) уровнем дог. "1" подается с привода после включения приводов подач от кнопки на станке. Блокировка приводов подач осуществляется через вход "Стоп подачи" от переключателя на станке (при этом светодиод HL15 погашен).
Сигнал "Аварийный стоп" блокирует работу УЧПУ с приводами с помощью сигналов "Прерывание подачи" и ''Блокировка главного привода". Через выход "Включение приводов подач" обеспечивается быстрое отключение приводов что исключает неконтролируемое кратковременное движение по координатах X и Z в момент выключения станка. Для обеспечения торможения шпинделя при выключении станка по аварийной кнопке сигнал "Аварийный стоп" поддерживает включенным пускатель KM1 пока не будет блокирован сигналом с привод
ППВ" уровнем лог. "0".
Если в процессе работы станка УЧПУ снимет сигнал "Готовность ЧПУ" то отключение приводов производится аналогично отработка сигнала "Аварийный стоп".
Команда М35 дешифрируется микросхемой D910 и запоминается на триггере D24.1 - D31.1. Одновременно с сигналом с микросхемы D910 на вход этого триггера поступает сигнал сброса БСМ но т.к. сигнал БСМ пропадает раньше сигнала с микросхем D910 то триггер запоминает команду М35. При подаче любой другой М - команды этот триггер будет сброшен. С выхода триггера сигнал подается на робот через выход "Запрос 1" и на УЧПУ через выход "Пуск ЧПУ" (при этом светодиод HL13 светится). Сигнал "Пуск ЧПУ подается на вход ЧПУ "Флажок условного перехода по внешнему событию". В управляющей программе УЧПУ организуется циклический опрос этого входа.
Сигнал от робота через вход "Пуск станка" (уровнем лог. "0") сбрасывает триггер D24.1 - D31.1.
Команда М45 дешифрируется микросхемой D1010 и запоминается на триггере D24.2 - D31.2. С выхода триггера сигнал подается на робот через выход "Запрос 2" и на УЧПУ через выход "Пуск ЧПУ". Сброс триггера осуществляется через вход "Пуск станка".
Т - команды отрабатываются следующим образом.
При совпадении сигналов от УЧПУ "БСТ" и "Считывание" перебрасывается триггер D8.1- D17.3. Сигнал с триггера через лог. элементы D19.1 и D20.2 замыкает герконовое реле К4 и сблокирует ответный сигнал РВК. Геркон К4 управляет пускателем КМ4 который включает двигатель резцедержки. Также сигнал с триггера включает через лог. элемент D7 один из дешифраторов D11 или D12. Код номера инструмента на входах этих дешифраторов должен сохраняться до завершения смены инструмента. Выходы дешифраторов через разъем Х4 подаются на герконовые датчики в резцедержке. По мере вращения резцедержки герконы поочередно подключают выводы дешифраторов к входу "Совпадение позиции". Как только на входе "Совпадение позиции" будет подан дешифрированный сигнал уровнем лог. "0" прохождение сигнала через лог. элемент D19.1 блокируется и размыкается герконовое реле К4. Сигнал лог. "0" с выхода элемента D17.4 через элемент D20.1 замыкает герконовое реле КЗ. Геркон КЗ управляет пускателем КМ5 который осуществляет реверс двигателя резцедержки. Когда механизм резцедержки встанет в рабочее положение то с конечника будет подан через контакты токового реле КА1 сигам лог. "0'' на вход "Ответ Т". Обмотка токового реле КА1 включена в цепь обмотки двигателя резцедержки и срабатывает при достижении двигателем резцедержки определенного усилия. Сигнал "Ответ Т" проходит через RC - цепочку служащую для подавления импульсных помех.
При наличии сигнала на входе ''Ответ Т' триггер D17.3 - D18.1 сбрасывается и выключается дешифратор (D11 или D12). С выхода триггера через D37 на УЧПУ подается обменный сигнал РВК.
На элементах D26 D27 D28 D34 собран узел контроля зажима пиноли и патрона. Входы "Установка счетчика пиноли" и "Установка счетчика патрона" служат для обнуления счетчиков D27 и D28. С выходов счетчиков информация передается на робот через выходы "Патрон зажат" "Пиноль зажата" и на УЧПУ через выход "Блокировка ПО" (светодиод HL18 погашен). При этом импульсы
с генератора (VT3 VT4) через элемент D35.2 подастся на индикаторную лампу на пульте управления станком.
Мигание этой лампы свидетельствует о том что деталь не зажата пинолью или в патроне. Частота генератора около 1 Гц.
На входы "Пн. раб. " и "Пн. раб." подаются парафазные импульсы с конечников при достижении двигателем пиноли определенного усилия зажима. После поступления на счетчик D28 восьми импульсов его счетный вход блокируется снимается сигнал блокировки пульта оператора и прекращается мигание индикаторной лампы.
Аналогично построен узел контроля зажима детали в патроне.
С помощью входов "Блок контр. пн." и "Блок контр. пт." выбирается режим контроля зажима детали только пинолью или в патроне или одновременный контроль что определяется переключателем на станке.
Питание микросхем осуществляется от стабилизатора с выходным напряжением 15В. Входное напряжение 27В подается на стабилизатор через резистор гашения от блока питания УЧПУ "Электроника НЦ-31-02" БПС 18-1-1. Стабилизатор собран по схеме компенсационного типа на микросхеме А39 (КР142ЕН2Б). Стабилитроны VD8 VD9 служат для защиты от перенапряжения. Выходное напряжение устанавливается с помощью подстроечного резистора R115.
Для расширения возможности станка через разъем Х7 выводятся все сигналы поступающие от УЧПУ. К этому разъему возможно подключение устройства аналогично данному БУ.
Для формирования сигнала РВК от внешнего устройства предусмотрен вход "Выполнено". В частном случае через разъем Х7 подключается блок измерения для автоматической привязки инструмента и блок связи с роботом.
1. Наладочный режим.
Наладочный (ручной) режим предназначен для проверки и настройки всех узлов станка для уточнения режимов резания и размеров получаемых на детали в результате обработки.
В этом режиме управление станком производится со станочного пульта управления и с пульта оператора УЧПУ которые выполнены в одном корпусе а также с панели управления станка.
Перечень органов управления пультов и панели их назначение и способы использования см. 16А20Ф3.РЭ раздел 7.
2. Автоматический и по кадровый режим.
Порядок ввода программы в этих режимах изложен в технической документации на устройство ЧПУ инструкции по программированию (16А20Ф3С39.ИП) и инструкции по вводу параметров (16А20ФЗС39.ИП10).
В этом случае последовательность работы электроавтоматики определяется отработкой программы и схемой электрической принципиальной станка.
1.В станке выполнены следующие блокировки:
нулевая защита станка осуществляется блок контактами пускателя КМ1 (см.16А20Ф3С39.Э3). После восстановления напряжения для продолжения работы необходимо нажать кнопку
ограничение перемещения по координатам и аварийное отключение приводов подач от блоков микропереключателей SQ3 SQ4
исключение возможности работы приводов патрона и пиноли при включенном приводе главного движения;
запрещение включения электродвигателя главного привода при работающих приводах патрона и пиноли;
запрещение пуска программы в автоматическом режиме при открытом ограждении зоны резания (контроль микропереключателем SQ6);
запрещение включения электродвигателя резцедержки одновременно в прямом и обратном направлениях;
исключается постороннее вмешательство в программу с помощью блокировки пульта оператора от переключателя
запрещение включения электродвигателя главного привода при не зажатой заготовке в патроне или при -отсутствии поджима заготовки пинолью;
запрещение включения электродвигателя главного привода при отсутствии смазки шпиндельной бабки.
Защита электрооборудования от коротких замыканий осуществляется автоматическими выключателями QF1 QF2 и предохранителями FU1 FU5.
Защита электродвигателей резцедержки патрона пиноли охлаждения. смазки направляющих и шпидельной бабки от перегрузок осуществляется тепловыми реле КК1 КК6.
Все металлические части станка (станина корпуса электродвигателей каркасы шкафов пульт управления и т.д.) которые могут оказаться под напряжением выше 42В - заземлены. Схему заземления см. 16А20ФЗС39.Э4 л.6.
Для контроля наличия напряжения между любыми из трех линейных проводов и шиной заземления служит светосигнальное устройство H1 установленное в шкафу 1. Это устройство работает только при открытой двери шкафа и показывает включенное состояние вводного автоматического выключателя QF1.
На пульте управления установлен сигнализатор заземления А26 который осуществляет контроль состояния изоляции проводов в цепях управления переменного тока 110В. Одновременное горение двух тиратронов при подача напряжения на станок показывает нормальное состояние цепей управления. При подаче напряжения на привода или включение вспомогательного оборудования (резцедержка смазка и т.п.) тиратроны могут гаснуть что не говорит о нарушении цепи управления. Горение одного из тиратронов в любом состоянии станка сигнализирует о замыкании цепи управления на землю.
В станке выполнена следующая сигнализация:
лампа HL1 наличия напряжения на станке;
лампа HL2 контроля смазки шпиндельной бабки.
После установки станка до подключения его к цеховой сети необходимо произвести замеры электрического сопротивления цепи заземления измеренного между узлом заземления станка ХТ11 и магистральной цеховой шиной заземления. Сопротивление цепи заземления не должно превышать 0.1 Ома.
Строго соблюдать меры безопасности указанные в сопроводительной документации комплектующих изделий.
Работа станка с открытыми дверями шкафов категорически запрещается.
На шкафу 1 около рукоятки привода вводного автоматического выключателя QF1 установлено специальное запирающее устройство при помощи которого можно запирать привод вводного выключателя в отключенном состоянии а следовательно исключить возможность подключить станок к источнику питания. Запирающее устройство допускает установку до трех висячих замков скобами диаметром 9 мм.
Токоведущие части электрооборудования остающиеся под напряжением при отключенном вводном автоматическом выключателе закрыты изоляционными крышками.
Пульт управления имеет степень защиты 1Р44 шкафы управления 1Р54 по ГОСТ 14254-80.
Верхние контакты вводного автоматического выключателя постоянно находятся под напряжением. Случайное прикосновение с ними ОПАСНО для жизни.
СВЕДЕНИЯ О РАСЦВЕТКЕ ПРОВОДОВ.
Монтаж электрооборудования выполнен проводами со следующими
силовая цепь переменного или постоянного тока - черный (цвет обязательный);
цепь управления переменного тока - красный (допускается замена);
цепь постоянного тока управления и сигнализации – синий (допускается замена);
цепь заземления - зелено-желтый (цвет обязательный).
Монтаж устройств педали патрона пиноли SA4 SA5 транспортер стружкоудаления A33 демонтированных для транспортировки провести по схеме соединений 16А20Ф3С39.Э4 и таблице соединений 16А2Ф3С39.ТЭ4.
При раздельной поставке транспортера стружкоудаления и станка необходимо установить разъемы на жгутах 29 и 58 в соответствии с рис.2 используя детали из ЗИПа станка и подключить жгуты в шкафу и транспортеру по таблице соединения 16А20Ф3С39.ТЭ4.
Разъемы поз.1 поставляются с транспортером.
Детали поз.3 установлены на жгутах.
ХАРАКТЕРНЫЕ НЕИСПРАВНОСТИ И МЕТОДЫ ИХ УСТРАНЕНИЯ.
Характерные неисправности электрооборудования станка и методы их устранения приведены в пунктах раздела 6 по проверке работы механизмов и в табл.2.
Не горит лампа HL1 "Наличие напряжения" при включенном вводном выключателе QF1.
1. Перегорела плавкая вставка одного из предохранителей QF1 QF3.
2. Перегорела лампа HL1.
3. Сгорела одна из обмоток трансформатора TV1.
Заменить плавкую вставку предохранителя.
Заменить трансформатор.
Не подается питание на станок нажатием кнопки SB1.
Исчезло питание цепей управления – 24В.
Исчезло питание цепей управления ~110В.
1. Перегорела плавкая вставка одного из предохранителей FU1 FU2 FU4.
2. Сгорела катушка пускателя КМ1.
3. Кнопка аварийного останова SB2 в нажатом
4. Сгорела одна из обмоток трансформатора TV1.
1. Сгорели диоды выпрямителя А11.
2. См. Причины п.1.1.и п.1.3.
1. Сработала отсечка максимального тока выключателя QF2.
2. Сгорела одна из обмоток трансформатора TV2.
3. Сгорела плавкая вставка предохранителя FU5.
Вытянуть толкатель кнопки.
ТЕХНИЧЕСКОЕ ОБСЛУЖИВАНИЕ.
При уходе за электрооборудованием необходимо периодически проверять состояние пусковой и релейной электроаппаратуры. Все детали электроаппаратов должны быть свободными от пыли и грязи.
Нагар образующийся на силовых контактах должен быть удален при помощи бархатного напильника. Поверхность контакта сердечника с якорем магнитного пускателя во избежание появление ржавчины рекомендуется периодически смазывать машинным маслом с последующим обязательным удалением его сухой тряпкой (от залипания якоря сердечника).
При осмотрах аппаратуры особое внимание следует обращать на надежное замыкание и размыкание контактных мостиков.
Систематически производить технический осмотр и профилактический ремонт электродвигателей.
Периодичность технических осмотров устанавливается в зависимости от производственных условий но не реже одного раза в два месяца.
При технических осмотрах контролируется состояние выводных проводов обмотки статора производится наружная чистка электродвигателя от загрязнения проверяется надежность заземления.
Периодичность профилактических ремонтов устанавливается также в зависимости от производственных условий но не реже одного раза в год при этом должна производиться разборка электродвигателя внутренняя и наружная чистка и замена смазки подшипников.
Смазку подшипников при нормальных условиях работы следует производить через 4000 часов работы а при работе электродвигателей в пыльной и влажной среде - чаще по мере необходимости.
Перед набивкой свежей смазки подшипники должны быть тщательно промыты бензином. Камера заполняется смазкой на 23 ее объема.
Рекомендуемая смазка подшипников электродвигателей - ЦИАТИМ-203 ГОСТ 8773-73.
Профилактический осмотр автоматических выключателей необходимо производить не режа одного раза в шесть месяцев а также после каждого короткого замыкания в том числе и повторного.
При осмотре нужно очистить выключатель от копоти и нагара металла проверить затяжку винтов целостность пружин и состояние контактов.
Шарниры механизма выключателя следует смазывать приборным вазелином примерно через 2000-3000 включений.
Магнитный расцепитель автоматического выключателя тарируется на заводе-изготовителе дополнительная регулировка может нарушить работу и вызвать аварийный режим работы станка.
Сведения по техническому обслуживанию приводов подач и УЧПУ приведены в технической документации на них.
Инструкция по програмированию.doc
СТАНОК ТОКАРНЫЙ ПАТРОННО-ЦЕНТРОВОЙ
С ЧИСЛОВЫМ ПРОГРАМНЫМ УПРАВЛЕНИЕМ.
Инструкция по программированию.
ТЕХНОЛОГИЧЕСКИЕ ВОЗМОЖНОСТИ СТАНКА 4
Настоящая инструкция определяет программирование с учетом технологических возможностей станка 16А20Ф3С39 по используемым функциям и командам.
Остальной порядок программирования изложен в:
Руководство программиста589.4001008.0004-01 33 01;
Руководство оператора
и технолога программиста 589.4001008.0004-01 90 01.
ТЕХНОЛОГИЧЕСКИЕ ВОЗМОЖНОСТИ СТАНКА.
1. Станок отрабатывает следующие технологические команды:
М0 - останов выполнения УП в автоматическом режиме и выключение
привода главного движения. В ручном режиме отрабатывается аналогично команде М5. Величина скорости вращения шпинделя запоминается в УЧПУ. При включении привода главного движения после команды М0 скорость шпинделя восстанавливается.
М2 - останов выполнения УП в автоматическом режиме выключение
провода главного движения. В ручном режиме отрабатывается аналогично команде М5. Величина скорости вращения шпинделя не запоминается. При включении привода главного движения после команды М2 необходимо задавать величину скорости вращения шпинделя.
М3 - включение привода главного движения по часовой стрелке.
М4 - включение привода главного движения против часовой стрелки.
М5 - выключение привода главного движения.
М8 - включение привода СОЖ.
М9 - выключение привода СОЖ.
М10 - реверс вращения шпинделя.
М19 - ориентированный останов шпинделя по нулевой метке датчика
М30 - выключение привода СОЖ и главного движения. Останов выполнения УП с обнулением счетчика номера кадра и регистра кода скорости вращения шпинделя.
М31 - выход в фиксированную точку по оси Х (движение до кулачка осуществляется в направлении +Х).
М32 -выход в фиксированную точку по оси Z (движение до кулачка осуществляется в направлении +Z).
М38 - команда контроля положения редуктора шпиндельной бабки и задания 1-го диапазона частот вращения шпинделя от 20 до 200 обмин.
М39 - команда контроля положения редуктора шпиндельной бабки и задания 2-го диапазона частот вращения шпинделя от 60 до 830 обмин.
М40 - команда контроля положения редуктора шпиндельной бабки и задания 3-го диапазона частот вращения шпинделя от 185 до 2500 обмин.
Т1 Т12 - установка позиции автоматической поворотной резцедержки.
2 Команды зеркальной отработки М37 и М38 по осям X и Y на станке не используются.
3. После включения станка перед подачей любых технологических команд (М и Т) необходимо отработать команду выбора диапазона частот вращения шпинделя (М38 М39 или М40) соответственно положению рукоятки переключения диапазонов. В противном случае от электроавтоматики станка к УЧПУ не будет поступать сигнал о выполнении технологических команд (код ошибки XXXIXX).
4. Если возникает необходимость программирования в одной УП скоростей шпинделя находящихся в разных диапазонах то перед командой смены диапазона (М38 МЗ9 или М40) в УП записать команду МО. После команды смены диапазона - МЗ (М4) и величину скорости вращения шпинделя по адресу S. После того как выполнение УП будет остановлено по команде МО рукояткой переключения диапазонов установить соответствующий диапазон и продолжить выполнение УП нажав кнопку «Пуск».
5. Если команда выхода в фиксированную точку (М31 или М32) отрабатывается в ручном режиме то после выполнения команды для осуществления перемещения от клавиши ручного управления необходимо выйти из ручного режима в любой другой а потом снова установить ручной режим.
6. Для устранения отключения двигателя резцедержки в случае задания номера позиции инструмента более 12 в схеме станка предусмотрена установка инструмента в первую позицию. Причем остановка произойдет после того как на цифровом индикаторе появится код ошибки ХХ1ХХ (нет ответа от электроавтоматики). При этом будет сбой привязки для инструмента в первой позиции. Привязка будет восстановлена при вызове инструмента в первую позицию по команде Т1.
7. Запрещается отрабатывать на станке команду ТО. После выполнения этой команды инструмент будет установлен в первую позицию с потерей привязки.
8. При программировании перемещений надо иметь в виду что задание на перемещение допускается задавать с дискретностью 1 мк (одна дискрета задания соответствует 1 мк) а перемещение исполнительных органов осуществляется при задании не менее 2 мк.
9. Диапазон программируемых перемещений 999 999 мм.
10. Диапазон программируемых рабочих подач:
Оборотных М38 0 01 40 00 МинутныхМ381 4000
ммобМЗ9 0 01 3200 ммминМЗ91 3200
М40 0 01 16 00М401 1600.
11.Максимальная скорость рабочей подачи мммин:
12.Максимальная скорость быстрых ходов ммин:
13.Пределы шагов нарезаемых резьб:
14.Номограмма для определения воздушного минимального зазора по оси Z при нарезании резьбы.
где n - частота вращения шпинделя в обмин.
F - шаг нарезаемой резьбы в мм.
tр = 0 2сек - время разгона (торможения) электродвигателя привода.
- скорость продольного перемещения суппорта при нарезании резьбы.
При значении скорости продольного перемещения суппорта равной 2000 мммин получаем:
При значении скорости более 2000 мммин время разгона увеличивается до 03сек.
14.1.Наиболее сложный режим работы привода это разгон и торможение. Ввиду того что электродвигателю привода необходимо определенное время и путь для достижения максимальной скорости быстрого хода не рекомендуется при программировании перемещений на скоростях быстрых ходов близких к 15000 для оси Z и 7500 для оси X (мммин) задавать повторяющиеся перемещения меньше 50 мм по оси Z и 12 5 мм по оси X. В противном случае привод будет работать в режиме постоянного разгона торможения что снижает его долговечность и не приводит к желаемому увеличению производительности. (Длины 50 мм оси Z и 12. 5 мм оси X определены как суммарный путь который проходит рабочий орган станка при разгоне и торможении максимальной скорости быстрого хода).
15. При отработке УП в автоматическом режиме в электроавтоматике станка организованы два режима работы с подвижным экраном
15. 1. Если вставить ключ в замок блокировки ограждения на пульте управления станком и повернуть его вправо то устанавливается наладочный режим. В этом режиме производится отладка УП в автоматическом режиме без резания с открытым подвижным экраном.
15. 2. Если извлечь ключ из замка то устанавливается режим контроля подвижного экрана. При этом если кнопка установки автоматического режима на пульте оператора УЧПУ будет нажата до закрытия подвижного экрана или открыть подвижной экран после установки автоматического режима то выполнение УП будет остановлено и появится код 77Х1ХХ (нет готовности станка) а в электроавтоматике будут отключены приводы СОЖ и главного движения. Для продолжения работы на станке выполнить следующие действия:
Установить ручной режим открыть подвижной экран до упора нажать кнопку сброс [] отработать команду М5. Если подвижной экран был открыт во время перемещения инструмента то по командам М31 и МЗ2 выйти в фиксированную точку для восстановления привязки. Закрыть подвижной экран установить автоматический режим и запустить выполнение УП с нулевого кадра.
16. Особенности привязки сверл и метчиков.
На представленном рисунке показана схема привязки-метчиков и сверл. Отличием от привязки резцов является введение в память при привязке по оси Х суммы предварительно проточенного диаметра заготовки d1 и диаметра метчика (сверла) d2. При привязке по оси Z и по оси Х метчик (сверло) лишь касается предварительно проточенных диаметра и торца.
Предварительно проточен Ф40 мм подрезан торец - размер Z0 = 60 мм.
Инструмент - метчик для резьбы М10 - Т5.
Вызываем в рабочую позицию метчик нажимаем для этого клавиши «Т» «5» (даже если в станке нет автоматической смены инструмента).
Включаем шпиндель и в режиме «Ручной» метчик подводим к образующей Ф40 мм.
Переходим в режим «Маховичек» касаемся Ф40 мм вдоль образующей.
Останавливаем шпиндель замеряем соответственно диаметр проточки и диаметр метчика. Получили размер 5008 мм.
Переходим в режим «Привязка инструмента» нажимаем клавиши: «Х» «5» «0» «0» «8» «0» (индикация адреса и числа гаснет).
Включаем шпиндель нажимаем клавишу режима «Ручной» подводим метчик к торцу детали.
Переходим в режим «Маховичек» касаемся проточенного торца заготовки торцовой частью метчика.
Отводим метчик по оси X останавливаем шпиндель переходим в режим «Привязка инструмента».
Нажимаем клавиши: «Z» «6» «0» «0» «0» «0».
17. Сведения о режимах работа УЧПУ.
В УЧПУ "Электроника НЦ31-02" имеется возможность стыковки с перфоратором; фотосчитывающим устройством или с ЭВМ верхнего уровня. Сведения изложены в документации УЧПУ альбом № 8: "Ячейка АМТ Техническое описание 3.056.018-01" "Руководство оператора и технолога-программиста 589.4001008.00004-01 90 01" и "Пояснительная записка 589.4001008.00004-01 81 01- лу они предназначены для потребителей станков как исходные с целью организация подключения УЧПУ к необходимым внешним устройствам.
02.cdw

Флаж. условн перехода
Блок. главн. привода
Перегрев вент. смазки
Прер. резьбонар. (G 36)
Блок. пульта оператора
Флаж. условн. перехода
Фиксиров. точка по X
Запрет. пульта операт.
PRIL1.frw

08.cdw

03.cdw

Реле потока смазки шпинделя
Рекомендуемые чертежи
- 24.01.2023
- 24.01.2023