Проектирование технологической оснастки для обработки детали на металлорежущем станке




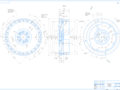
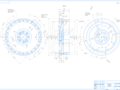
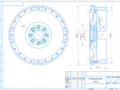
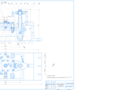
- Добавлен: 04.11.2022
- Размер: 1009 KB
- Закачек: 0
Узнать, как скачать этот материал
Подписаться на ежедневные обновления каталога:
Описание
Курсовой проект - Проектирование технологической оснастки для обработки детали на металлорежущем станке
Состав проекта
![]() |
![]() ![]() ![]() |
![]() ![]() ![]() |
![]() ![]() ![]() |
![]() ![]() ![]() ![]() |
![]() ![]() ![]() ![]() |
![]() ![]() ![]() |
Дополнительная информация
Контент чертежей
Пояснительная записка 2015.doc
1 Техническое задание 4
2 Операционного технологического процесса обработки заданной поверхности 5
3 Выбор схемы базирования на операции 5
Классификация проектируемого станочного приспособления и выбор металлорежущего станка 7
1 Классификация проектируемого станочного приспособления 7
2 Выбор металлорежущего станка 7
Выбор и обоснование применяемого режущего инструмента 10
Расчет сил резания 11
Расчет необходимой точности обработки и выбор базирующих и координирующих устройств 13
Расчет погрешности базирования 14
Расчет сил закрепления 16
Расчет погрешности закрепления 18
Расчет погрешности установки 19
Описание работы обслуживания и контроля наладки 22
Список используемых источников 23
Интенсификация производства в машиностроении неразрывно связана с техническим перевооружением и модернизацией средств производства на базе применения новейших достижений науки и техники. Техническое перевооружение подготовка производства новых видов продукции машиностроения и модернизация средств производства неизбежно включают процессы проектирования средств технологического оснащения и их изготовления.
В общем объеме средств технологического оснащения примерно 50% составляют станочные приспособления. Применение станочных приспособлений позволяет:
надежно базировать и закреплять обрабатываемую деталь с сохранением ее жесткости в процессе обработки;
стабильно обеспечивать высокое качество обрабатываемых деталей при минимальной зависимости качества от квалификации рабочего;
повысить производительность и облегчить условия труда рабочего в результате механизации приспособлений;
расширить технологические возможности используемого оборудования.
В зависимости от вида производства технический уровень и структура станочных приспособлений различны. Для массового и крупносерийного производства в большинстве случаев применяют специальные станочные приспособления. Специальные станочные приспособления имеют одноцелевое назначение для выполнения определенных операций механической обработки конкретной детали. Эти приспособления наиболее трудоемки и дороги при исполнении. В условиях единичного и мелкосерийного производства широкое распространение получила система универсально-сборных приспособлений (УСП) основанная на использовании стандартных деталей и узлов. Этот вид приспособлений более мобилен в части подготовки производства и не требует значительных затрат.
Создание любого вида станочных приспособлений отвечающих требованиям производства неизбежно сопряжено с применением квалифицированного труда. В последнее время в области проектирования станочных приспособлений достигнуты значительные успехи. Разработаны методики расчета точности обработки деталей в станочных приспособлениях созданы прецизионные патроны и оправки улучшены зажимные механизмы и усовершенствована методика их расчета разработаны различные приводы с элементами повысившими их эксплуатационную надежность.
Описание и анализ оснащаемой технологической операции
1 Техническое задание
Спроектировать технологическую наладку для обработки детали на металлорежущем станке. Исследовать спроектированную наладку для операции «Программная» на точность выполнения размеров.
На данной операции производиться сверление отверстий растачивания отверстий фрезерование поверхностей нарезание резьбы в отверстиях на станке модели ИС-800 в условиях серийного производства;
-геометрические параметры:
-Точность выполняемой операции в мм:
на данной операции производиться получение поверхностей следующих классов точности IT6 IT 7 IT 9 IT 10 IT 14 .
Способ обеспечения заданной точности по предварительной настройке станка
Годовая программа выпуска всех типоразмеров Nг = 5000шт
Рисунок 1.1 Операционный эскиз рассматриваемой операции
2 Операционного технологического процесса обработки заданной поверхности
- Установить деталь и закрепить.
- Сверлить последовательно 8 отверстий Ф14 мм;
- Зенковать последовательно 8 отверстий Ф14 мм для получения фаски;
3 Выбор схемы базирования на операции.
Анализируя техническое задание эскиз детали под выполняемую операцию из ГОСТ 21495-76 выбираем теоретическую схему базирования и из ГОСТ3.1107-81 возможные схемы практической реализации.
Практическая схема базирования детали "Маховик в сборе" для операции ХХХ ''Программная''.
Рисунок 1.1 - Схема базирование детали на операции
Базирование детали производиться по внутреннему предварительно обработанному отверстию Б Ф8444 мм (цилиндрический палец) и плоскости детали А. Закрепление детали производиться по цилиндрической поверхности В.
Классификация проектируемого станочного приспособления и выбор металлорежущего станка
1 Классификация проектируемого станочного приспособления
Классификация по группам станков.
В нашем случае приспособление которое проектируется относиться к группе приспособлений для многооперационных станков так как предполагается обработка на станках данной группы.
Классификация степени специализации.
По степени специализации наше приспособление относится к неразборным специальным приспособлениям.
2 Выбор металлорежущего станка
Данный вид поверхности можно обработать на следующих видах оборудования:
- Радиально сверлильный станок модели 2Н55;
- Горизантально-расточной станок модели 2А620;
- Координатно-расточной станок модели 2Е450;
- Горизонтально обрабатывающий центр ИС-800.
Критерием выбора являлось вид обрабатываемой поверхности габариты детали точность получаемых размеров программа выпуска.
Из приведенных видов станков наибольший интерес представляет горизонтальный обрабатывающий центр ИС-800 так как на данном станке можно обработать наибольшее количество поверхностей детали «Маховик в сборе».
Горизонтальный обрабатывающий центр ИС-800 - одна из самых распространённых моделей обрабатывающих центров на территории бывшего СССР позволяющая производить фрезерование и расточку и сверление корпусных деталей небольших и средних размеров.
Горизонтальный обрабатывающий центр ИС-800предназначен для фрезерования сверления и выполнения расточных работ заготовок любых форм и из любых материалов - от чугуна до сплавов цветных металлов пластмасс. Широкие диапазоны частот вращения шпинделя и скоростей подач наличие поворотного стола высокая степень автоматизации вспомогательных работ расширяют технологические возможности станков и позволяют использовать их в составе гибких производительных систем. Дискретный стол станка ИС-800 (число позиций 120 х 3о) габариты стола 800 х 800 мм система ЧПУ фирм «BOSCH» или «FANUC».
Технические характеристики
Размеры рабочей поверхности стола мм
Наибольшая масса обрабатываемого изделия кг
Частота вращения поворотного стола (с круговой подачей) мин-1
Количество позиций поворота стола
Индексируемый поворот стола угл. с
Точность автоматической установки поворота стола
Конус для крепления инструмента в шпинделе
Частота вращения шпинделя мин-1
Мощность электродвигателя привода вращения шпинделя кВт
Величина перемещения стола (поперечное) мм
Величина перемещения бабки (вертикальное) мм
Величина перемещения стойки (продольное) мм
Время смены столов-спутников с
Количество столов-спутников в накопителе шт
Рабочие подачи стола шпиндельной бабки стойки мммин
Скорость быстрых установочных перемещений мммин
Емкость инструментального магазина шт.
Время смены инструмента с
Наибольший диаметр рядом стоящих инструментов мм
Наибольший диаметр инструмента при свободных соседних гнездах мм
Точность линейного одностороннего позиционирования стола мкм
Точность линейного одностороннего позиционирования стойки шпиндельной бабки мкм
Постоянство положения рабочей поверхности стола-спутника при повороте на 30° мкм
Габаритные размеры станка (Д х Ш х В) мм
Выбор и обоснование применяемого режущего инструмента.
При обработке используется спиральное сверло из быстрорежущей стали
диаметром 65 мм с цилиндрическим хвостовиком ГОСТ 10903 – 77.
Диаметр сверла D = 14 мм
Длина сверла L = 189 мм
Длина рабочей части l = 108 мм
Материал режущей части: P6М5
Материал хвостовика: 40Х
Геометрические параметры:
α=12º ; = 40º ; 2φ = 118º ;
Рисунок 3.1 - Спиральное сверло
Измерительный инструмент: калибр-пробка Ф14 ПР НЕПР
Расчет сил резания.
Диаметр сверла 14 мм; глубина сверления 34; подача S = 0.05 ммоб; Материал режущей части инструмента Р6М5
Глубину сверления принимаем по формуле
Скорость резания рассчитывается по эмпирическим формулам
Кv=Кмv×Киv×КLv=1×1×1=1
где Кмv - поправочный коэффициент учитывающий влияние физико-механических свойств обрабатываемого материала на скорость резания. В нашем случае данный коэффициент составит Кмv=1
К иv =1 (без корки) поправочный коэффициент учитывающий влияние состояния поверхности заготовки на скорость резания.
КLv=1 - поправочный коэффициент учитывающий глубину обрабатываемого отверстии
Коэффициенты и показатели степени в формуле скорости резания
Сv=7; q=04; у=07; m=02;Т=60 мин;
Принимаем n = 1600 обмин.
Фактическая скорость:
Коэффициенты и показатели степени в формуле скорости резания СМ=003; q=2; у=08; КР = 096
МКР = 10×003×142×00508×096 = 513 Н×м
Коэффициенты и показатели степени в формуле скорости резания Ср=68; q=1; у=07; КР = 096
Р0 = 10×68×141×00507×096 = 1122 Н
Что намного меньше действительной мощности применяемого станка.
Расчет необходимой точности обработки и выбор базирующих и координирующих устройств
Выбор конструкции корпуса приспособления
Корпусом приспособления служит металлический корпус выполненный литьем из стали 10 имеющая параметры 780х890х285 мм которая обеспечит достаточную жесткость приспособления так же имеет достаточную толщину для закрепления на ней составных частей приспособления.
Выбор установочных зажимных и вспомогательных элементов приспособления
В качестве установочных элементов приняты кронштейн на который закреплены два регулировочных опоры и один палец (цилиндрический) ГОСТ 12195-66. Размер цилиндрического пальца по справочным данным принимаем Ф84 f 7. Зажимными элементами в данном приспособление служат два зажима с гидравлическим приводом. Применение гидравлического зажима связано с тем что данное приспособление и оборудование в основном используется для серийного производства.
Расчет погрешности базирования
Базирующими элементами приспособлений называются детали и механизмы обеспечивающие правильное и однообразное расположение заготовок относительно инструмента.
оснастка приспособние отверстие деталь
Рисунок 6.1 - Схема для расчета погрешности базирования
Определение погрешности сводиться к решению чисто геометрических задач.
Так как установка осуществляется на жесткий палец с зазором то погрешность базирования б рассчитывается по формуле
б = 2 · e - 1 + 2 + 2 · Δ
где e - эксцентриситет наружной поверхности относительно отверстия;
- допуск на диаметр отверстия Ф8444+IT142: где верхние отклонение +0435 а нижнее отклонение -0435;
- допуск на диаметр пальца Ф8444 f7: где верхние отклонение -0036 а нижнее отклонение -0071;
Δ - минимальный радиальный зазор при посадке заготовки на палец.
В нашем случае e = 0.45 мм по справочным данным
= 0.435+0.435= 0.87 мм
=0071-0036= 0035 мм
Δ =(8444-0435)-(8444-0036)=0.399 мм.
б = 2 · 0.45 – 087 + 0035 + 2х0.399 = 0.85 мм.
Расчет сил закрепления
Деталь прижимается планкой которая надета на ось и закреплена на оси при помощи гайки.
По справочной литературе можно выбрать следующую схему закрепления детали.
Рисунок 5.1 - Расчетная схема расчета силы закрепления
Определение усилия зажима Pз
где f – коэффициент трения по рабочим поверхностям зажимов для гладких поверхностей f1 =015
K – коэффициент запаса.
Определение коэффициента запаса [1 с. 199-207]:
где - гарантированный коэффициент запаса; =15;
- для чистовой обработки; =10; - коэффициент учитывающий увеличение сил резания из-за прогрессирующего затупления режущего инструмента =16;
- коэффициент учитывающий увеличение силы резания при прерывистом резании; =10;
- коэффициент учитывающий постоянство силы зажима при использовании пневматического зажима =10;
- при удобном расположении рукоятки; =10
-коэффициент учитываемый только при наличии крутящих моментов стремящихся повернуть заготовку; =10;
В связи с тем что в нашем приспособление предусмотрено два зажимных устройства то на каждый приходиться следующая сила закрепления =105182=52593Н
Расчет погрешности закрепления
В приспособление погрешность закрепления для диаметральных размеров а именно для межосевого расстояния Ф142 мм будет равна нулю Так как соблюдается следующее условие при приложение силы закрепления размер который необходимо выдержать будет перемещаться в той же плоскости в которой будет действовать сила закрепления.
Расчет погрешности установки
Погрешность установки EУ
где eБ – погрешность базирования;
e3 – погрешность закрепления;
e3И – погрешность формы поверхности контакта установочного элемента в результате износа;
eИ – погрешность определяемая прогрессирующим изнашиванием установочных элементов;
eУС – погрешность изготовления и сборки приспособления;
eС – погрешность установки и фиксации приспособления на станке.
eПР - погрешность положения заготовки
Если систематические погрешности eУС и eС можно полностью устранить то
Если погрешности eИ и e3И зависящие от износа можно регулярно компенсировать поднастройкой инструмента то
Погрешность положения заготовки возникает в результате погрешностей изготовления приспособления погрешность установки и фиксации приспособления на станке и износа опор :
Точность изготовления опор и других стандартных деталей приспособления. Допуски ответственных размеров нестандартных деталей приспособления обычно составляет 10 – 30 % допуска на соответствующий размер обрабатываемой детали. Как правило
Составляющая возникает в результате перемещений и перекосов корпуса приспособления на столе планшайбе или шпинделя станка. При рациональных условиях схемы приспособления и при правильном выборе зазоров в сопряжениях величину можно снизить до 001..002 мм.
Тогда общая погрешность составит:
где - погрешность базирования
- погрешность закрепления
- погрешность формы поверхности контакта установочного элемента в результате износа
- погрешность определяемая прогрессирующим изнашиванием установочного элемента
- погрешность изготовления и сборки приспособления
- погрешность установки и фиксации приспособления на станке.
где- погрешность положения.
Тогда погрешность установки составит:
В результате можно сделать заключение что приспособление используемое при обработке будет обеспечивать требуемую точность так как погрешность наладки составит +04375 мм а допуск на получаемы размер составит +05 мм. Следовательно точность получаемых размеров находиться в пределах допуска.
Описание работы обслуживания и контроля наладки.
Рисунок 10.1 - Станочное приспособление
Приспособление состоит из основания 22 на которое крепятся все остальные элементы приспособления. Опорная плита крепиться на основание 5 при помощи винтов 11. Деталь на приспособление базируется при помощи цилиндрического пальца 19. Деталь закрепляется на приспособление при помощи двух прижимных планок 28. Закрепление осуществляется при помощи штоков 12. Закрепление детали производиться при помощи цилиндров 4и 5. Приспособление закрепляется на столе станка при помощи болтов 45.
Список используемых источников.
Справочник технолога-машиностроителя: В 2 т. Под ред. А.Г. Косиловой и Р.К. Мещерякова. - М.: Машиностроение 1985. -Т.1.-656 с.
Справочник технолога-машиностроителя: В 2 т. Под ред. А.Г. Косиловой и Р.К. Мещерякова. - М.: Машиностроение 1985. -Т.2. - 496 с.
Взаимозаменяемость стандартизация и технические измерения: Учеб. А.И. Якушев Л.Н. Воронцов Н.М. Федотов. - М.: Машиностроение 1987. - 352 с.
Ансеров М.А. Приспособления для металлорежущих станков.Л.: Машиностроение 1966. - 652 с.
А.Горошкин АС Приспособления для металлорежущих станков: Справ. - М.: Машиностроение 1979. - 303 с.
Справочник конструктора инструментальщика; Под ред. В.И. Баранчикова. - М.: Машиностроение 1994. - 560 с.
Справочник инструментальщика Под ред. И.А. Ординар-цева. - Л.: Машиностроение: Ленингр. отд-ние 1987. - 846 с.
Чертеж Маховик в сборе.cdw

Чертеж.cdw

Неуказанные предельные отклонения размеров по H14
Рекомендуемые чертежи
- 14.06.2023
Свободное скачивание на сегодня
Обновление через: 8 часов 14 минут