Проектирование привода




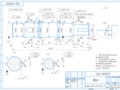
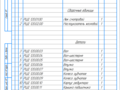
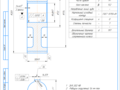
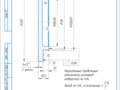
- Добавлен: 04.11.2022
- Размер: 1 MB
- Закачек: 0
Описание
Курсовой проект - Проектирование привода
Состав проекта
![]() |
![]() |
![]() ![]() ![]() |
![]() ![]() ![]() ![]() |
![]() ![]() ![]() ![]() |
![]() ![]() ![]() |
![]() ![]() ![]() ![]() |
![]() ![]() ![]() |
![]() ![]() ![]() ![]() |
![]() |
![]() ![]() ![]() ![]() |
Дополнительная информация
Титульник.docx
Государственное общеобразовательное учреждение высшего профессионального образования
«ТОМСКИЙ ГОСУДАРСТВЕННЫЙ АРХИТЕКТУРНО-
СТРОИТЕЛЬНЫЙ УНИВЕРСИТЕТ»
Кафедра прикладной механики
ПРОЕКТИРОВАНИЕ ПРИВОДА
Расчетно-пояснительная записка к курсовому проекту
по дисциплине “Детали машин”
Руководитель проекта: Глотов С.А.
Спецификация.spw

Маслоуказатель жезловой
Уплотнитель войлочный
Манжеты ГОСТ 8752-79
Подшипник ГОСТ 8338-75
Шпонка ГОСТ 23360-78
Рым-болт ГОСТ 4751-73
Сборочный чертеж.cdw

красный цвет эмалью НЦ-5123 ГОСТ 7462-73
наружные поверхности
красить в серый цвет эмалью ПФ-115 ГОСТ 6465-76.
Плоскость разъема перед сборкой покрыть тонким слоем
герметика УТ-34 ГОСТ 24285-80.
Валы собранного редуктора должны проворачиваться от руки
плавно без заеданий.
Обкатку собранного редуктора производить на стенде по
устанавливаемой техническими условиями.
Допускается эксплуатировать редуктор с отклонением от
горизонтального положения на угол до 5
. При этом должен быть
уровень масла достаточный для смазки зацепления.
Все детали и элементы расположенные снаружи редуктора
должны иметь антикоррозионное покрытие.
Курсовая Работа.docx
Согласно задания требуется разработать привод ленточного конвейера с быстроходной конической зубчатой передачей промежуточной цилиндрической косозубой и тихоходной цилиндрической передачи.
Требуется рассчитать зубчатые передачи спроектировать и проверить пригодность шпоночных соединений подшипников разработать общий вид редуктора разработать рабочие чертежи деталей: выходного вала зубчатого колеса и крышку.
Зубчатые передачи рассчитывается по условиям контактной выносливости зубьев проверяется на изгибную выносливость. Валы проектируются из условия статической прочности (ориентировочный расчет) и проверяются на выносливость по коэффициенту запаса прочности.
Шпоночные соединения проверяются на срез и размеры принимаются в зависимости от диаметра соответствующего участка вала. Пригодность подшипников оценивается долговечностью по динамической грузоподъёмности.
Форма и размеры деталей редуктора определяются конструктивными и технологическими соображениями а также выбором материалов и заготовок.
При расчёте и проектировании ставится цель получить компактную экономичную конструкцию что может быть достигнуто использованием рациональных материалов для деталей передач оптимальным подбором передаточного числа передач использованием современных конструктивных решений стандартных узлов и деталей при проектировании привода.
Кинематический расчет привода
1 Выбор электродвигателя.
Для выбора электродвигателя определяют его требуемую мощность и частоту вращения .
Потребляемую мощность привода (мощность на выходе) определяют по формуле:
гдеКПД муфты; КПД цепной передачи; КПД опор приводного валаКПД зубчатой передачи.
По таблице 1.1 [1. с 6]: ; ; ; ;
Требуемая мощность электродвигателя
Определяем частоту вращения приводного вала :
гдедиаметр барабана (мм).
Требуемую частота вращения вала электродвигателя вычислим по формуле для средние значения передаточных чисел из рекомендуемого диапазона для цепной и двух зубчатых передач примем из рекомендуемого ряда табл. 1.2. [1. Стр. 7]
Принимаем передаточное число цепной передачи
передаточное число тихоходной ступени цилиндрического двухступенчатого редуктора и передаточное число быстроходной ступени.
По таблице 24.9 [1. с 417]: выбираем двигатель серии АИР-100L2ТУ16-525.564-84:
2 Уточнение передаточных чисел привода.
После выбора определяем общее передаточное число привода :
где – передаточное отношение всех ступеней редуктора;
По формулам из табл. 1.3 [1.Стр. 8-9] имеем:
3 Определение вращающих моментов на валах привода.
Частота вращения вала шестерни быстроходной ступени:
Частота вращения вала шестерни тихоходной ступени (вала колеса быстроходной ступени двухступенчатого редуктора):
Частота вращения вала колеса тихоходной ступени:
Частота вращения приводного вала:
Вращающий момент (Нм) на приводном валу:
Момент на валу колеса тихоходной ступени редуктора:
Вращающий момент на валу шестерни тихоходной ступени (на валу колеса быстроходной ступени редуктора):
Момент на валу быстроходной шестерни быстроходной ступени:
Момент от электродвигателя:
Расчёт зубчатых передач
1. Выбор материала колес и расчет допускаемых напряжений.
Выбираем для изготовления колеса сталь марки 35ХМ и шестерни сталь марки 40Х.Табл.2.1. [1 с.11]
Термообработка - улучшение и закалка ТВЧ
твердость поверхности 45 50 HRC
твердость в сердцевине 269 302 НВ
Термообработка - улучшение
твердость поверхности 235 262 HB
твердость в сердцевине 235 262 НВ
2.Расчёт цилиндрической зубчатой передачи (тихоходная ступень).
2.1 Определение допускаемых контактных напряжений.
Определим допускаемые контактные напряжения для шестерни и колеса по формуле [1 с.13]:
где - предел контактной выносливости.
В соответствии с табл.2.2 [1 с.13]:
SH – коэффициент запаса прочности принимаем в соответствии с
рекомендациями [1 с.13] SH2=11 SH1=12;
ZR– коэффициент учитывающий влияние шероховатости сопряженных
поверхностей зубьев. Принимаем ZR=09 в соответствии с
рекомендациями [1 с.14] и [2 с.27](при 9 степени точности
шероховатость поверхности Ra=3.2 6.3мкм).
ZV –коэффициент учитывающего влияние окружной скорости.
ZN – коэффициент долговечности учитывающий влияние ресурса.
Производим предварительный расчёт межосевого расстояния aw' мм:
где К – коэффициент поверхностной твёрдости в соответствии с
рекомендациями [1 с.17] принимаем K=8.
Определим окружную скорость v мс:
По полученным данным примем степень точности зубчатой передачи примем 9 класс точности применяемый для передач пониженной точности. Табл.[1 с.17]
Так как окружная скорость = 13 мс меньше чем 5мс принимаем ZV=10 в соответствии с рекомендациями
где NHG – число циклов соответствующее перелому кривой усталости
определяют по формуле:
Nk – ресурс передачи в числах циклов перемены напряжения определяют по
параметры принимаем в соответствии с рекомендациями [1 с.13]
эквивалентное число циклов:
гдекоэффициент эквивалентности:
Так как принимаем ZN1=1 и ZN2=1 в соответствии с рекомендациями.
[]H=045([]H1+[]H2)≥ []Hmin=[]H2
[]H≤125[]Hmin=12546391=57989 МПа.
2.2 Определение допускаемых напряжений изгиба
Определим допускаемое напряжение изгиба по следующей формуле[1с.14]:
где YN – коэффициент долговечности учитывает влияние ресурса
где и - для закаленных и поверхностно упрочненных зубьев.
и - для улучшенных зубчатых передач.
Число циклов соответствующее перелому кривой усталости NFG=4106 NК1=738108 NК2=168108.
YR – коэффициент учитывающий влияние шероховатости переходной поверхности между зубьями принимаем YR=1 в соответствии с рекомендациями Табл.3.2.5[2 с.29].
YA – коэффициент учитывающий влияние двустороннего приложения
нагрузки принимаем YA=1 в соответствии с рекомендациями
[1 с.15] т.к. приложение нагрузки является односторонним.
Flim– предел выносливости при нулевом цикле нагружения
принимаем в соответствии с табл.2.3 [1 с.14]:
SF – коэффициент запаса прочности принимаем в соответствии с
рекомендациями [1 с.15] SF=17.
Расчет тихоходной цилиндрической передачи
Уточним предварительно найденное значение межосевого расстояния:
где Ka= 410 МПа для косозубых колёс.
ba – коэффициент ширины принимаем в соответствии со
стандартным рядом чисел и рекомендаций [1 с.17] ba=04.
КН – коэффициент нагрузки в расчётах на контактную прочность:
где– коэффициент учитывающий внутреннюю динамику
нагружения определяем методом экстрополяции табл. 2.6 [1 с.18] ;
KH- коэффициент неравномерности распределения нагрузки по
длине контактных линий в соответствии с [1 с.18]:
где KH0 – коэффициент неравномерности распределения
нагрузки в начальный период работы в соответствии с
табл. 2.7 [1 с.19] KH0=1127.
KHw – коэффициент учитывающий приработку зубьев определим методом интерполяции табл. 2.8 [1 с.19] KHw= 0255.
KH - коэффициент распределения нагрузки между зубьями
определяем по формуле:
где KH0 – начальное значение коэффициента распределения
нагрузки между зубьями KH0=15:
KH0=1+А(nст-5) при условии 1≤ KH0≤16
где А=025 - для зубчатых колес с твердостью Н1 ≥ 350 HB и Н2 ≤ 350 НВ
nст- степень точности 7.
Уточняем предварительно найденное значение межосевого расстояния:
Учитывая стандартный ряд величин межосевых расстояний принимаем aw = 125 мм [2с.47].
Предварительно определим основные размеры.
Определяем делительный диаметр:
Определим ширину колеса:
Определим модуль передачи для этого определим максимальное и минимальное значение модуля:
где Km =28103- для косозубых передач.
KF – коэффициент нагрузки при расчёте по напряжениям изгиба:
где КFv – коэффициент учитывающий внутреннюю динамику
нагружения определим методом интерполяции КFv=1052 по табл. 2.9 [1 с.20];
КF – коэффициент неравномерности распределения
напряжений у основания зубьев по ширине зубчатого
КFα – коэффициент учитывающий влияние погрешностей
изготовления шестерни и колеса на распределение
нагрузки между зубьями причём КFα= КHα0=15.
Принимаем значение модуля в соответствии с рядом размеров m = 2 мм.
Определение суммарного числа зубьев и угла наклона.
Определим минимальный угол наклона зубьев косозубых колес:
Определим суммарное число зубьев по формуле:
где – угол наклона зубьев принимаем =9.2°.
Полученное значение zs округляем в меньшую сторону до целого числа и определяем действительное значение угла наклона зуба:
=arccos[1232(2125)]=1026°
Определяем число зубьев шестерни:
Определяем число зубьев колеса:
Фактическое передаточное число [1с.29]:
Рассчитываем отклонение
Определяем делительные диаметры:
Определяем диаметры окружностей вершин и впадин колес: [1с.22]
где х1 и х2 – коэффициенты смещения у шестерни и колеса (х1=0 и
y – коэффициент воспринимаемого смещения (у=0).
Размеры заготовок рассчитываем по формуле [1 с.22]:
шестерни:Dзаг=da+6=57+6=63 мм ≤ Dпр=125 мм
колеса:Sзаг=8m=82=16 мм ≤ Sпр=125 мм
3.1 Проверим зубья колеса по контактным напряжениям.
Расчётное значение контактного напряжения определяем по формуле:
где Z =8400 MПа12 для косозубых колёс.
Расчет отклонения расчетного контактного напряжения от допускаемого:
значит ранее принятые параметры передачи принимаем за окончательные.
Определяем силы в зацеплении.
Fa =392tg1026°=07 кН.
3.2 Проверочный расчет зубьев по напряжениям изгиба.
где YFS2 – коэффициент учитывающий форму зуба в соответствии с
zv2 = z2cos=97cos31026°=1018
Y- коэффициент учитывающий угол наклона зуба в косозубой передаче вычисляем по формуле: Y=1-100 при условии Y≥07.
Для косозубых передач Y=065 [1 с.24]
Для зубьев шестерни:
где YFS1 – коэффициент учитывающий форму зуба в соответствии с табл. 2.10 [1 с.25].
zv1 = z1cos3=26cos31026°=271
Принимаем YFS1=3829 после экстраполяции данных из таблицы [1 с. 24].
Проверим зубья на прочность при действии пиковой нагрузки:
Для предотвращения остаточных деформаций или хрупкого разрушения поверхностного слоя:
где - контактное напряжение при действии номинального момента Т;
- коэффициент перегрузки характеризующий режим нагружения =22 в соответствии с табл. 24.9 [1 с.417];
- допускаемое контактное напряжение
где - предел текучести выбираем в соответствии с табл. 2.1 [1 с.11]
4.Расчёт цилиндрической зубчатой передачи (быстроходная ступень).
4.1 Определение допускаемых контактных напряжений.
Определим допускаемые контактные напряжения для шестерни и колеса:
Принимаем ZR=09 (при 9 степени точности шероховатость поверхности Ra=3.2 6.3мкм).
Так как окружная скорость = 372 мс меньше чем 5мс принимаем ZV=10 в соответствии с рекомендациями.
4.2 Определение допускаемых напряжений изгиба
Число циклов соответствующее перелому кривой усталости NFG=4106 NК1=4202108 NК2=738108.
Принимаем YR=1 в соответствии с рекомендациями Табл.3.2.5[2 с.29].
YA=1 в соответствии с рекомендациями [1 с.15] т.к. приложение нагрузки является односторонним.
Расчет быстроходной цилиндрической передачи
табл. 2.7 [1 с.19] KH0=1215.
KHw – коэффициент учитывающий приработку зубьев определим методом интерполяции табл. 2.8 [1 с.19] KHw= 031.
Учитывая стандартный ряд величин межосевых расстояний принимаем aw = 100 мм [2с.47].
нагружения определим методом интерполяции КFv=11369 по табл. 2.9 [1 с.20];
Принимаем значение модуля в соответствии с рядом размеров m = 15 мм.
где – угол наклона зубьев принимаем =8.62°.
=arccos[13115(2100)]=107°
шестерни:Dзаг=da+6=37+6=43 мм ≤ Dпр=125 мм
колеса:Sзаг=8m=815=12 мм ≤ Sпр=125 мм
5.1 Проверим зубья колеса по контактным напряжениям.
Fa =125tg107°=024 кН.
5.2 Проверочный расчет зубьев по напряжениям изгиба.
zv2 = z2cos=109cos3107°=11497
Расчет гибкой передачи. Расчет цепной передачи.
Расчет мощности на входной звездочке:
где - угловая скорость определяем по формуле:
- вращающий момент колеса тихоходного вала .
Примем =5270 Вт =527 кВт.
n1 = n2T = 152 мин-1.
Цепь приводная роликовая типа ПР.
Условия работы и размещение передачи:
- передача работает от асинхронного электродвигателя
- работа в три смены
- режим нагружения -средний равномерный режим (СР)
- угол наклона передачи к горизонту (=0).
Число зубьев ведущей звездочки z1=f(u) определяем по табл.13.2.4[2c.360]
Граничная вытяжка цепи при эксплуатации [t]=3%.
Число зубьев ведомой звездочки:
Принимаем z2=78 z2 ≤ zmax (100 200).
Действительное передаточное число передачи:
Расчетный момент на ведущей звездочке:
где =12 - коэффициент учитывающий динамичность нагружения передачи определяем по таблице 13.2.6[2 с.361].
Предварительное значение средних удельных давлений в шарнирах цепи табл.13.2.15[2 с.360]
Предварительно задаемся числом рядов цепи (=1-коэффициент рядности)
Расчет предварительного шага цепи:
где - коэффициент интенсивности нагрузки при расчете на износ для режима СР.
Выбираем цепь с шагом t =254.
Тип цепи ПР-254 – 60 ГОСТ 13568-97
Fp=60000 H; Aoп=179 мм2; q=26 кгм2; табл.13.2.6[2 с.356]
Условие ограничения частоты вращения ведущей звездочки n1
Для t = 254 мм [n1]=700 мин-1 (табл.13.2.8[2 с.361])
n1=152 мин-1 [n1]=700 мин-1.
Делительные диаметры звездочек :
Окружное усилие на ведущей звездочке:
Номинальное удельное давление в шарнирах цепи:
Проверим условие стойкости шарниров цепи против изнашивания.
Допускаемое давление в шарнирах цепи :
где =267 - базовое удельное давление
-поправочные коэффициенты учитывающие параметры передачи и условия ее эксплуатации:
- долговечность передачи
=Lh15000=24571815000=164
где Lh=245718 - время работы передачи
- частоту вращения ведущей звездочки
- относительную норму износа цепи .
- режим работы передачи
- параметры передачи (
где - коэффициент числа зубьев.
- условия эксплуатации передачи :
горизонту табл.13.2.9[2 с.161]
коэффициент учитывающий способ натяжения ветвей цепи (натяжение цепи перемещением опор валов) .
коэффициент учитывающий способ смазывания передачи (класс смазывания -2 условия работы - запыленное).
Расчетные удельные давления в шарнирах цепи:
Условие стойкости шарниров цепи против изнашивания:
Условие прочности цепи на разрыв .
Максимальное натяжение цепи:
где натяжение цепи от действия центробежных сил .
где коэффициент учитывающий наклон оси центров звездочек к горизонту табл.13.2.13[2 с.361].
ориентировочное межосевое расстояние.
Запас прочности цепи :
Условие прочности цепи на разрыв : S=1577 ≥ [S];
Минимальные значения [S]=7 8.
Число звеньев цепи :
Расчетное межосевое расстояние передачи:
Межосевое расстояние с учетом провисания ведомой ветви цепи:
Сила нагружающая валы передачи
где для горизонтальной передачи.
Разработка эскизного проекта [1 с.42]
Предварительные значения диаметров различных участков стальных валов редуктора определяем по формулам:
Для быстроходного (входного) вала:
Принимаем d = 22 мм.
Диаметр под манжету:
tцил – высота заплечика [1 c. 42]
Диаметр под подшипник
Диаметр под буртик подшипника
r-координаты фаски подшипника [1 c. 42]
Диаметр под манжету :
Выбираем муфту упругую втулочно-пальцевую.
Муфта 63-22-1 ГОСТ 21424-93.
Определяем окружную силу передаваемую элементами соединяющими полумуфты:
Сила нагружающая вал от муфты:
Выбираем тип и марку подшипников.
Для быстроходного вала применим подшипник:
Подшипник 305 ГОСТ 8338-75
Статическая грузоподъемность
Динамическая грузоподъемность
Внутренний диаметр подшипника
Наружный диаметр подшипника
Для промежуточного вала применим подшипник:
Подшипник 306 ГОСТ 8338-75
Для тихоходного вала применим подшипник:
На входном валу используем уплотнительную манжету по:
ГОСТ 8752-79 типа: 1.1-25x42-1
Конструктивные размеры корпуса редуктора
Компоновка редуктора.
Для редукторов толщину стенки корпуса отвечающую требованиям технологии литья необходимой прочности и жёсткости корпуса вычисляем по формуле:
Так как при условии ≥80 мм примем = 80 мм.
Расстояние от стенки корпуса редуктора до боковой поверхности вращающейся части:
Расстояние от стенки корпуса редуктора до боковой поверхности подшипника качения:
Расстояние в осевом направлении между вращающимися частями смонтированными на:
одном валу: примем мм
Радиальный зазор между зубчатым колесом одной ступени и валом другой ступени (min):
Радиальный зазор от поверхности вершин зубьев:
- до внутренней поверхности стенки редуктора
- до внутренней нижней поверхности стенки корпуса (величину определяет также объем масляной ванны)
Расстояние от боковых поверхностей элементов вращающихся вместе с валом до неподвижных наружных частей редуктора примем
Ширина фланцев S соединяемых болтом диаметром:
Толщина стенки крышки:
Болт М16 z1=4 h1=16.
Болт М6х25 z4=4h1=6.
Размеры боковых и передней крышки.
Передняя крышка для быстроходного вала.
Диаметр болтов крепления крышки к корпусу и их количество :
Диаметр установки болтов :
Наружный диаметр фланца :
Толщина фланца крышки :
Толщина цилиндрической части крышки:
Толщину цилиндрической части Н крышки выбираем конструктивно.
Длину цилиндрической части крышки L мм (конструктивно).
Крышка боковая для промежуточного вала.
Боковая крышка для тихоходного (выходного) вала.
Конструктивные размеры стакана.
Длину стакана L мм выбираем конструктивно.
Диаметр болтов крепления стакана к корпусу:
Диаметр установки болтов:
Высота расположения осей редуктора
Расчет валов на прочность.
Расчет быстроходного (входного) вала.
Материал вала-шестерни сталь марки 40Х:
Реакции опор лежащих на вертикальной плоскости:
Крутящий момент: T1Б = 1881 Нм.
Общий коэффициент запаса прочности по пределу текучести определим по формуле 10.3 [1 с. 166]:
где ST и ST частные коэффициенты запаса прочности по нормальным и касательным напряжениям 10.2 [1 с. 166]:
где T и Т пределы текучести материала.
и – это максимальные напряжения в рассматриваемом сечении:
W – момент сопротивления сечения вала при расчете на изгиб;
где WK – момент сопротивления сечения вала при расчете на кручение;
- минимально допустимое значение общего коэффициента запаса текучести.
Условие выполняется.
Расчет вала на сопротивление усталости.
Минимально допустимое значение запаса прочности
Коэффициент запаса по нормальным напряжениям :
Предел выносливости вала для симметричного нагружения
a – амплитуда цикла напряжения в опасном сечении.
Предел выносливости гладких образцов при симметричном цикле изгиба и кручения по табл. 10.2 [1с.170];
Коэффициент влияния качества поверхности по таблице 10.8[1с.170];
Коэффициент влияния поверхностного упрочнения по таблице 10.9[1с.170];
Для оценки концентрации напряжений в местах установки на валу деталей с натягом определим методом интерполяции отношения табл.10.13 [1 с.171].
Коэффициент запаса по касательным напряжениям :
Предел выносливости вала
Для оценки концентрации напряжений в местах установки на валу деталей с натягом табл.10.13 [1 с.170].
Коэффициент влияния поверхности упрочнения по таблице 10.9[1с.170];
Коэффициент влияния асимметрии цикла :
Коэффициент чувствительности материала к асимметрии цикла напряжений по таблице 10.2[1с.165];
Сопротивление усталости обеспечено.
2 Расчет промежуточного вала.
Материал вала сталь марки 40Х:
Реакции опор сил лежащих на вертикальной плоскости:
Крутящий момент: T1Т = 899 Нм.
3 Расчет тихоходного (выходного) вала.
Реакции опор сил лежащих на вертикальной плоскости :
Крутящий момент: T1Т = 3324 Нм.
Проверка долговечности подшипников
KT = 1 – температурный коэффициент [1 с. 107];
KБ = 14 – коэффициент безопасности табл. 7.4 [1 с. 107];
Lh = 20000 ч – требуемый ресурс долговечности;
Подшипник шариковый радиальный однорядный 306 ГОСТ 8338-75 средней серии со следующими параметрами:
d = 25 мм – диаметр вала (внутренний посадочный диаметр подшипника);
D = 62 мм – внешний диаметр подшипника;
C = 225 кН – динамическая грузоподъёмность;
С0 = 114 кН – статическая грузоподъёмность;
Находим е – параметр осевого нагружения с помощью экстраполяции по табл. 5.5.2. [2 с. 165]:
Расчет эквивалентной динамической нагрузки:
Расчетная долговечность работы подшипника.
d = 30 мм – диаметр вала (внутренний посадочный диаметр подшипника);
D = 72 мм – внешний диаметр подшипника;
C = 281 кН – динамическая грузоподъёмность;
С0 = 146 кН – статическая грузоподъёмность;
Подшипник шариковый радиальный однорядный 309 ГОСТ 8338-75 средней серии со следующими параметрами:
d =45 мм – диаметр вала (внутренний посадочный диаметр подшипника);
D = 100 мм – внешний диаметр подшипника;
C = 527 кН – динамическая грузоподъёмность;
С0 = 30 кН – статическая грузоподъёмность;
Элементы соединения вал-ступица.
Крутящий момент Т1Б = 1881 Нм.
Диаметр вала dвал = 22 мм.
Выбираем шпонку призматическую:
Условия работы kА = 1 табл.3.3.3[2 с.47].
Размеры поперечного сечения b×h =8×7 мм; t1 = 4 мм (табл. 7.1.1).
Длина шпонки L = 40 мм (табл.7.1.2)
Крутящий момент Т1Б = 899 Нм.
Диаметр вала dвал = 32 мм.
Размеры поперечного сечения b×h =10×13 мм; t1 = 10 мм (табл. 7.1.1).
Длина шпонки L = 32 мм (табл.7.1.2)
Крутящий момент Т1Б = 3324 Нм.
Диаметр вала dвал = 48 мм.
Размеры поперечного сечения b×h 14×9 мм; t1 = 55 мм (табл. 7.1.1).
4 Выходной вал (соединение со звездочкой)
Крутящий момент Т1Б = 39888 Нм.
Диаметр вала dвал = 35 мм.
Размеры поперечного сечения b×h 10×8 мм; t1 = 5 мм (табл. 7.1.1).
Длина шпонки L = 36 мм (табл.7.1.2)
Для уменьшения потерь мощности на трение снижение интенсивности изнашивания трущихся поверхностей их охлаждения и очистки от продуктов износа а также для предохранения от заедания задиров коррозии должно быть обеспечено надежное смазывание трущихся поверхностей. [1 стр. 172]
Для смазывания передач широко применяют картерную систему. В корпус редуктора или коробки передач заливают масло так чтобы венцы колес были в него погружены. Колеса при вращении увлекают масло разбрызгивая его внутри корпуса. Масло попадает на внутренние стенки корпуса откуда стекает в нижнюю его часть. Внутри корпуса образуется взвесь частиц масла в воздухе которая покрывает поверхность расположенных внутри корпуса деталей. [1 стр. 172]
Картерное смазывание применяют при окружной скорости зубчатых колес и червяков от 03 до 125 мc. При более высоких скоростях масло сбрасывает с зубьев центробежная сила и зацепление работает при недостаточном смазывании. Кроме того заметно возрастают потери мощности на перемешивание масла повышается его температура. [1 стр. 172]
Окружная скорость зацепления:
Картерная система смазывания подходит для проектируемой передачи.
Выбор смазочного материала основан на опыте эксплуатации машин.
Преимущественное применение имеют масла. Принцип назначения сорта масла следующий: чем выше окружная скорость колеса тем меньше должна быть вязкость масла и чем выше контактные давления в зацеплении тем большей вязкостью должно обладать масло. Поэтому требуемую вязкость масла определяют в зависимость от контактного напряжения о окружной скорости колес. [1 табл. 11.1]
Для предельного контактного напряжения 57989 МПа и окружной скорости 13 мс выбираем рекомендованное значение кинематической вязкости масла 32 мм2c.
Выбирают марку масла для смазывания зубчатых и червячных передач. [1 стр. 172]
Для рекомендуемой вязкости 32 мм2c выбираем масло индустриальное И-Г-А-32.
Уровень погружения должен быть таким чтобы в масло были погружены венцы зубчатых колес обоих ступеней т.к. скорость в зацеплении меньше 1 мс.
Технология сборки редуктора
Перед сборкой внутреннюю полость корпуса редуктора тщательно очищают и покрывают маслостойкой краской. Сборку производят в соответствии с чертежом общего вида редуктора начиная с узлов валов.
На валы закладывают шпонки и напрессовывают элементы передач редуктора. Подшипники следует насаживать предварительно нагрев в масле до 80-100 градусов по Цельсию последовательно с элементами передач. Собранные валы укладывают в основание корпуса редуктора и надевают крышку корпуса покрывая предварительно поверхности стыка крышки и корпуса спиртовым лаком. Для центровки устанавливают крышку на корпус с помощью двух конических штифтов; затягивают болты крепящие крышку к корпусу. После этого в подшипниковые камеры закладывают смазку ставят крышки подшипников с комплектом металлических прокладок регулируют тепловой зазор. Перед постановкой сквозных крышек в проточки закладывают манжетные уплотнения. Проверяют проворачиванием валов отсутствие заклинивания подшипников (валы должны проворачиваться от руки) и закрепляют крышку винтами. Затем ввертывают пробку маслоспускного отверстия с прокладкой и жезловый маслоуказатель. Заливают в корпус масло и закрывают смотровое отверстие крышкой с прокладкой закрепляют крышку болтами. Собранный редуктор обкатывают и подвергают испытанию на стенде по программе устанавливаемой техническими условиями.
При выполнении курсового проекта по “Деталям машин” были закреплены знания полученные за прошедший период обучения в таких дисциплинах как: теоретическая механика сопротивление материалов материаловедение.
Целью данного проекта является проектирование привода ленточного конвейера который состоит как из простых стандартных деталей так и из деталей форма и размеры которых определяются на основе конструкторских технологических экономических и других нормативов.
В ходе решения поставленной передо мной задачей была освоена методика выбора элементов привода получены навыки проектирования позволяющие обеспечить необходимый технический уровень надежность и долгий срок службы механизма.
Опыт и навыки полученные в ходе выполнения курсового проекта будут востребованы при выполнении как курсовых проектов так и дипломного проекта.
Можно отметить что спроектированный редуктор обладает хорошими свойствами по всем показателям.
По результатам расчета на контактную выносливость действующие напряжения в зацеплении меньше допускаемых напряжений.
По результатам расчета по напряжениям изгиба действующие напряжения изгиба меньше допускаемых напряжений.
Расчет вала показал что запас прочности больше допускаемого.
Необходимая динамическая грузоподъемность подшипников качения меньше паспортной.
При расчете был выбран электродвигатель который удовлетворяет заданные требования
СПИСОК ИСПОЛЬЗОВАННОЙ ЛИТЕРАТУРЫ
Конструирование узлов и деталей машин: Учебное пособие для машиностроительных спец. Вузов П.Ф.Дунаев О.П.Леликов. -7-е изд. перераб. и доп.-М.:Высш. шк. 2001-447 с. ил.
Конструирование узлов и деталей машин: Справочное учебно-методическое пособие Л.В. Курмаз О.Л. Курмаз.- М.: Высш. шк. 2007-455 с. ил.
Колесо.cdw

Неуказанные пред. откл. размеров:
Направление линий зуба
Сталь 40Х ГОСТ 4543-71
Содержание.docx
1 Выбор электродвигателя .. .6
2 Уточнение передаточных чисел привода .. ..7
3 Определение вращающих моментов на валах привода 7
Расчёт зубчатых передач .. 8
1. Выбор материала колес и расчет допускаемых напряжений .. ..8
2.Расчёт цилиндрической зубчатой передачи (тихоходная ступень) .. .9
2.1 Определение допускаемых контактных напряжений .. 9
2.2 Определение допускаемых напряжений изгиба . 11
2.3 Расчёт передачи . 13
3.1 Проверим зубья колеса по контактным напряжениям . .17
3.2 Проверочный расчет зубьев по напряжениям изгиба . ..18
4.Расчёт цилиндрической зубчатой передачи (быстроходная ступень) . 20
4.1 Определение допускаемых контактных напряжений . ..20
4.2 Определение допускаемых напряжений изгиба . 22
4.3 Расчёт передачи. Расчет быстроходной цилиндрической передачи .. ..23
5.1 Проверим зубья колеса по контактным напряжениям . . 27
5.2 Проверочный расчет зубьев по напряжениям изгиба . . .28
Расчет гибкой передачи. Расчет цепной передачи . .29
Разработка эскизного проекта . .34
Конструктивные размеры корпуса редуктора . ..39
Расчет валов на прочность . 43
1 Расчет быстроходного вала . 43
2 Расчет промежуточного вала . .49
3 Расчет тихоходного (выходного) вала . ..56
Проверка долговечности подшипников .61
1 Быстроходный вал 61
2 Промежуточный вал . ..62
3 Тихоходный вал . ..63
Элементы соединения вал-ступица . .64
2 Промежуточный вал 64
4 Выходной вал (соединение со звездочкой) 65
Выбор сорта масла ..66
Технология сборки редуктора 67
СПИСОК ИСПОЛЬЗОВАННОЙ ЛИТЕРАТУРЫ .69
Приложение А Спецификация цилиндрического редуктора.
Крышка.cdw

Вал.cdw

Размер обеспеч. инстр.
Неуказанные предельные
отклонения размеров:
Сталь 40Х ГОСТ4543-71
ТВЧ h 0.8 1.0;40 50 HRC
Рекомендуемые чертежи
- 25.10.2022
- 04.06.2015
- 22.04.2022
- 26.10.2015