Насадочный абсорбер для улавливания NH3 из газо-воздушной смеси водой


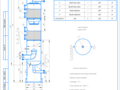
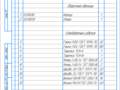
- Добавлен: 04.11.2022
- Размер: 342 KB
- Закачек: 1
Описание
Курсовой проект - Насадочный абсорбер для улавливания NH3 из газо-воздушной смеси водой
Состав проекта
![]() |
![]() ![]() ![]() ![]() |
![]() ![]() ![]() |
![]() ![]() ![]() ![]() |
Дополнительная информация
Насад. абсорбер - Спецификация.spw

Гаика М24 ГОСТ 5915-70
Шайба 20 ГОСТ 11371-78
Шайба 24 ГОСТ 11371-78
Гангнус - Насад. абсорбер - Пояснительная записка.docx
Федеральное государственное бюджетное образовательное учреждение высшего образования
«Пермский национальный исследовательский
политехнический университет»
Факультет химических технологий промышленной экологии и биотехнологий
Кафедра «Оборудование и автоматизация химических производств»
РАСЧЕТНО-ПОЯСНИТЕЛЬНАЯ ЗАПИСКА
к курсовому проекту по дисциплине «Процессы и аппараты нефтегазопереработки»
Тема проекта «насадочный абсорбер для улавливания NH3 из газо-воздушной смеси водой»
(Фамилия имя отчество)
Доцент кафедры ОАХП
(должность Ф.И.О. преподавателя от кафедры)
«Пермский национальный исследовательский политехнический университет
Кафедра «Оборудование и автоматизация химических производств» (ОАХП)
ЗАДАНИЕ НА КУРСОВОЕ ПРОЕКТИРОВАНИЕ
по дисциплине «Процессы и аппараты химической технологии»
студент группа ОНГП-1-1б
Рассчитать и запроектировать: насадочный абсорбер для улавливания NH3 из газо-воздушной смеси водой
Давление: атмосферное
Температура в абсорбере: 33 С
Начальное содержание NH3 в смеси: yН=008 (об.)
Вода поступающая в абсорбер NH3 не содержит: хН=0 (об.)
Расход газо-воздушной смеси при нормальных условиях: 13500 м3час
Степень извлечения NH3: 92%
Пояснительную записку (выбор типа конструкции и краткая характеристика аппарата расчет размеров аппарата расчет материального и теплового балансов расчет гидравлического сопротивления аппарата расчет на прочность основных деталей).
Чертежи аппарата: общий вид и узлы.
Срок выполнения задания
Руководитель проектирования
Описание технологической схемы производства концентрированной аммиачной воды7
Описание технологической схемы процесса абсорбции9
Расчёт насадочного абсорбера11
Масса поглощаемого вещества и расход поглотителя11
Движущая сила массопередачи14
Скорость газа и диаметр абсорбера15
Плотность орошения и коэффициент смачиваемости насадки15
Расчёт коэффициентов массоотдачи16
Коэффициент массопередачи18
Поверхность массопередачи и высота абсорбера18
Гидравлическое сопротивление абсорбера19
Основные результаты расчёта абсорбера19
Проектирование аппарата20
Конструктивный расчёт21
Расчёт диаметра штуцеров21
Разработка чертежа аппарата22
Список используемой литературы23
Пояснительная записка
Абсорбция – это процесс избирательного поглощения газов или паров из газовых или парогазовых смесей жидкими поглотителями (абсорбентами).
При физической абсорбции поглощаемый абсорбтив не взаимодействует химически с абсорбентом. Если же абсорбтив образует с абсорбентом химическое соединение то процесс называется хемосорбцией.
Физическая абсорбция в большинстве случаев обратима. На этом свойстве абсорбционных процессов основано выделение поглощаемого газа из раствора – десорбция.
Сочетание абсорбции с десорбцией позволяет многократно применять поглотитель и выделять поглощаемый компонент в чистом виде. Во многих случаях десорбцию не проводят т.к. абсорбент и абсорбтив представляют собой дешёвые или отбросные продукты которые после абсорбции вновь не используются.
В промышленности процессы абсорбции применяются главным образом для извлечения ценных компонентов из газовой смеси и для очистки этих смесей от вредных примесей.
Абсорбционные процессы широко распространены в химической и пищевой промышленности и являются основной технологической стадией ряда важнейших производств. Например: абсорбция SO3 в производстве серной кислоты абсорбция HCL в производстве соляной кислоты абсорбция аммиака водой в производстве аммиака и аммиачных удобрений.
Аппараты в которых осуществляется абсорбционные процессы. Называют абсорберами. Как и другие процессы массопередачи абсорбция протекает на поверхности раздела фаз поэтому абсорберы должны иметь развитую поверхность соприкосновения между жидкостью и газом. По способу образования этой поверхности абсорберы можно условно разделить на следующие группы: 1) поверхностные и пленочные; 2) насадочные; 3) барботажные (тарельчатые); 4) распылительные.
Широкое распространение в химической и пищевой промышленности в качестве абсорберов получили колонны заполненные насадкой – твердыми телами различной формы. В насадочной колонне насадка устанавливается на опорные решетки имеющие отверстия или щели для прохождения газа и стока жидкости.
Жидкость с помощью распределителя равномерно орошает насадочные тела и стекает вниз. По всей высоте слоя насадки равномерного распределения жидкости по сечению колонны обычно не достигают что объясняется пристенным эффектом – большей плотностью укладки насадки в центре сечения колонны чем у её стенок. Вследствие этого жидкость имеет тенденцию растекаться от центра колонны к её стенкам. Поэтому для улучшения смачивания насадки в колоннах большего диаметра насадку укладывают слоями (секциями) высотой 2-3м и под каждой секцией кроме нижней устанавливают перераспределители жидкости в виде перераспределительных тарелок.
В насадочной колонне жидкость течет по элементу насадки главным образом в виде тонкой пленки поэтому поверхностью контакта фаз является в основном смоченная поверхность насадки.
В тарельчатых абсорберах контакт между газом и жидкостью обеспечивается специальными устройствами – тарелками которые в зависимости от скоростей их движения работают в различных гидродинамических условиях: пузырьковом или струйном.
Наибольшее распространение в тарельчатых колонных аппаратах нашли колпачковые сетчатые клапанные и пластинчатые тарелки.
Все тарельчатые колонные аппараты могут быть с переливными устройствами или без них (провальными).
В промышленности абсорбция широко применяется для выделения из газовых смесей ценных компонентов для очистки технологических и горючих газов от вредных примесей для санитарной очистки газов и т.д.
При переходе из газовой фазы в жидкую энергия молекул распределяемого компонента уменьшается. Поэтому процесс абсорбции сопровождается выделением тепла и повышением температуры системы. Кроме того объем системы в процессе абсорбции уменьшается за счет уменьшения объема газовой фазы. Следовательно согласно принципу Ле-Шателье растворимость газа в жидкости увеличивается при повышении давления и уменьшении температуры процесса. Статика процесса абсорбции описывается уравнением Генри а кинетика – основными уравнениями массопередачи.
При абсорбции процесс массопередачи протекает на поверхности соприкосновения фаз. Поэтому в аппаратах для поглощения газов жидкостями (абсорберах) должна быть создана развитая поверхность соприкосновения между газом и жидкостью. По способу образования этой поверхности абсорбционные аппараты можно разделить на поверхностные барботажные и распыливающие.
В абсорберах поверхностного типа поверхностью соприкосновения фаз является зеркало жидкости или поверхность стекающей пленки.
Насадочные колонны представляют собой колонны загруженные насадкой – твердыми телами различной формы; при наличии насадки увеличивается поверхности соприкосновения газа и жидкости.
Эффективность работы насадочного абсорбера во многом зависит не только от гидродинамического режима но и от типа выбранной насадки. Разнообразие применяемых насадок объясняется множеством предъявляемых к ним требований: большая удельная поверхность и свободный объем малое гидравлическое сопротивление газовому потоку равномерное распределение абсорбента хорошая смачиваемость коррозионная стойкость малая насыпная плотность и низкая стоимость.
В барботажных абсорберах поверхность соприкосновения фаз развивается потоками газа распределяющегося в жидкости в виде пузырьков и струек. Такое движение газа называемое барботажем осуществляется в тарельчатых колоннах с колпачкаовыми ситчатыми или провальными тарелками. Особенностью тарельчатых колонн является ступенчатый характер проводимого в них процесса (в отличие от непрерывного процесса в насадочных колоннах) газ и жидкость последовательно соприкасаются на отдельных ступенях (тарелках) аппарата.
В распыливающих абсорберах поверхность соприкосновения создается путем распыления жидкости в массе газа на мелкие капли. Такие абсорберы изготовляются обычно в виде колонн в которых распыление жидкости производится сверху а газ движется снизу вверх.
Описание технологической схемы производства концентрированной аммиачной воды
Слабая аммиачная вода из напорного бака НБ через теплообменник Т в котором она нагревается до 50-60 поступает в диссоциатор Д. Диссоциатор представляет собой тарельчатую колонну на нижних тарелках которой расположены нагревательные устройства обогреваемые глухим паром. Эти тарелки не имеют колпачков но снабжены переливными трубами для жидкости. Нагрев в диссоциаторе производится до 96-98%; при этом происходит разложение карбоната и сульфида аммонии. Верхние тарелки представляют собой обычные барботажные колпачковые тарелки на которых выходящие из нижней части диссоциатора газы промываются поступающей аммиачной водой. Чтобы уменьшить потери NH3 с газами из диссоциатора подогретую слабую аммиачную воду подают на одну из средних тарелок верхней части диссоциатора а на верхнюю тарелку подают холодную аммиачную воду (около 10% от всего количества) направляемую в обход теплообменника. Газы выходят из диссоциатора с температурой 45; с ними уходит до 80% всего СО2 и до 50% H2S содержащихся в слабой аммиачной воде. Потери NH3 с газами из диссоциатора обычно не превышают 5% от содержания его в слабой аммиачной воде; для улавливания этого аммиака газы из диссоциатора пропускают через орошаемый водой скруббер.
Из диссоциатора аммиачная вода в значительной степени освобожденная от СO2 и H2S и подогретая до 96—98 поступает сверху в дестилляционную колонну ДК представляющую собой обычную колонну с колпачковыми тарелками. В дестилляционной колонне происходит десорбция летучего аммиака путем его отгонки с подаваемым снизу в колонну острым паром. Освобожденная от аммиака вода выходит из нижней части колонны и направляется в теплообменник Т для подогрева слабой аммиачной воды.
Газы из колонны имеющие температуру 100 - 102 и содержащие кроме аммиака еще пары HsO СО2 и H2S поступают в дефлегматор ДФ-1 где охлаждаются до 89—92; при этом часть водяных паров конденсируется в конденсате растворяется некоторое количество аммиака и эта жидкость стекает обратно в колонну как флегма. Из дефлегматора смесь паров соответствующая по составу концентрированной аммиачной воде поступает в конденсатор К из которого выводят готовую концентрированную аммиачную воду.
При описанном методе работы (так называемый круговой метод) отработанная вода выпускаемая из дестилляционной колонны и содержащая нелетучий аммиак после охлаждения в градирне Г возвращается на абсорбцию аммиака в скрубберах. По мере накопления в ней нелетучих соединений аммония часть циркулирующей таким образом выводят из оборота и заменяют свежей. Выведенная из оборота вода подается на известковую колонну ИК в нижнюю часть которой подается также известковое молоко (с содержанием 45 - 75 г СаО в 1 л воды). Газы из колонны поступают в дефлегматор ДФ-2 аналогичный дефлегматору ДФ-1 а жидкость из нижней части колонии направляется в приколонок ПК в котором происходит взаимодействие аммиачной воды с известковым молоком.
Получаемая при описанном процессе концентрированная аммиачная вода содержит 18—20% NН3 и небольшое количество примесей — СO2 и H2S.
В соответствии с заданием на проектирование необходимо выполнить расчет насадочного абсорбера.
Целью расчета абсорберов будем считать определение их габаритных размеров (высоты и диаметра) и гидравлического сопротивления по газовому потоку.
Описание технологической схемы процесса абсорбции
Газовоздушная смесь с помощью газодувки ГД подается в насадочный абсорбер А. В верхнюю часть абсорбера центробежным насосом Н подается вода. Вода стекает по насадке вниз а навстречу ей движется газовоздушная смесь. При взаимодействии фаз аммиак растворяется в воде и воздух очищается. Вода насыщенная аммиаком самотеком поступает в приемную емкость ПЕ а очищенный воздух выбрасывается в атмосферу.
Все перечисленные типы абсорберов имеют свои достоинства и недостатки. Поверхностные абсорберы малоэффективны и имеют ограниченное применение главным образом для абсорбции небольших количеств хорошо растворимых газов.
Преимуществом распылительных абсорберов является их простота и дешевизна низкое гидравлическое сопротивление а недостатками – дополнительные затраты энергии на распыление жидкости большая плотность орошения и трудность регулирования подачи большого количества жидкости
Преимуществом барботажных абсорберов является хороший контакт между фазами и возможность работы при любом в том числе и низком расходе жидкости кроме того в барботажных абсорберах легко осуществить отвод теплоты. Основной недостаток барботажных абсорберов сложность конструкции и высокое гидравлическое сопротивление.
Насадочные колонны – наиболее распространенный тип абсорберов. Преимуществом их является простота устройства особенно важная при работе с агрессивными средами так как в этом случае требуется защита от коррозии только корпуса колонны и поддерживающих насадку решеток насадка же может быть выполнена из химически стойкого материала. Важным преимуществом насадочных колонн более низкое чем в барботажных абсорберах гидравлическое сопротивление. Однако насадочные колонны малопригодны при работе с загрязненными жидкостями при малых расходах жидкости и при больших тепловыделениях.
В результате абсорбции аммиака водой образуется щелочной раствор являющийся коррозионно-активным поэтому выбираем насадочный тип абсорбера с керамической насадкой кроме того при работе под атмосферным давлением гидравлическое сопротивление насадочного абсорбера будет меньше чем у барботажного.
Расчёт насадочного абсорбера
Степень извлечения NH3 92%
поглощаемого вещества и расход поглотителя
1 Пересчёт мольных долей в относительные массовые доли:
кгкг – начальная концентрация аммиака в газе
кгкг – конечная концентрация аммиака в газе
2 Нахождение конечной концентрации аммиака в поглотителе: строим график равновесной и рабочей линии. Данные для равновесной линии берём из таблицы 6.4 [1] при этом необходимо пересчитать значения X и Y* в и * по следующим формулам: = * X; * = * Y*
Полученные данные занесём в таблицу:
Для построения рабочей линии при минимальном расходе воды проведём прямую через точки (Xн1 = 0; Yк1 = 0.004) и (Xmax=0.018 и Yн1 = 0.051).
3 Найдём минимальный удельный расход воды:
Действительный удельный расход воды примем:
4 Получим уравнение действительной рабочей линии:
Строим действительную рабочую линию через точки ( к = 0.014; н = 0.051) и ( н = 0; к = 0.004).
Графики представлены на рисунке 1.
5 Определим расход инертной части газа
Пересчитаем концентрацию аммиака. Из уравнения 5.3 [2] н = находим yн = 0.0584 кгм3
кгм3 – средняя плотность воздуха при нормальных условиях
Определим объёмную долю аммиака в газовоздушной смеси:
Расход инертной части газа:
6 Производительность абсорбера по поглощаемому компоненту:
7 Расход поглотителя (воды) равен:
Удельный расход поглотителя (соотношение расходов фаз):
Что соответствует предыдущему способу расчёта (пункт 1.3).
Движущая сила массопередачи
По графику определим Yxн и Yхк – концентрации аммиака в газе равновесные с концентрациями в жидкой фазе соответственно на входе и выходе из абсорбера.
Yxн = 0 кгкг (т.к. н = 0)
Определим большую и меньшую движущие силы на входе потоков в абсорбер и на выходе из него:
Δб = н - Yхк = 0.051 – 0.026 = 0.025 кгкг
Δм = к - Yxн = 0.004 – 0 = 0.004 кгкг
Определим движущую силу по формуле 5.7 [2]
Скорость газа и диаметр абсорбера
В качестве насадки выберем керамические кольца Рашига размером 15×15×2 мм. Удельная поверхность насадки а = 330 м2м3; свободный объём = 0.7 м3м3; эквивалентный диаметр dэ = 0.009 м; насыпная плотность ρ = 690 кгм3 (стр. 196 [2]).
Предельную скорость газа выше которой наступает захлёбывание абсорбера найдём из уравнения 5.9 [2]
lg × × ) = A – B × ×
x = 0.76×10-3 Па*с – вязкость поглотителя (воды) при температуре в абсорбере (табл.XXXIX [1])
в = 10-3 Па*с – вязкость воды при 20 (табл.XXXIX [1])
A и B – коэффициенты зависящие от типа насадки
А = -0.073 B = 1.75 (стр.197 [2])
ρx = 1000 кгм3 – плотность воды (табл.XXXIX [1])
ρy – плотность газовоздушной смеси при условиях в абсорбере:
ρy = ρ0y × = 1.2041 × × 1 = 1.074 кгм3
Подставим значения в формулу 5.9 и найдём из него значение предельной скорости газа: Wпр = 3.147 мс
Рабочую скорость W примем 0.8 Wпр (6.37 [1])
W = 0.8* Wпр = 2.52 мc
Диаметр абсорбера найдём из уравнения расхода:
Выбираем стандартный диаметр обечайки абсорбера d = 1.4 м (стр.197 [2])
Действительная рабочая скорость газа в колонне:
W = 2.52*(1.461.4)2 = 2.74 мс
Плотность орошения и коэффициент смачиваемости насадки
U = Lρx*S = 13.4321000*0.785*1.42 = 87.8*10-4 м3м2*с (5.11 [2])
Где S – площадь поперечного сечения абсорбера м2 S = 0.785*d2
Umin = a*qэф = 330*0.022*10-3 = 72.6*10-4 м3м2*с
qэф – эффективная линейная плотность орошения м2с
qэф = 0.022*10-3 м2с (стр. 198 [2])
Коэффициент смачиваемости насадки :
= 0.122(U*ρx)13dн-12-m = 0.122*(87.8*10-4*1000)13*0.01512*0.0708-1.086 = 0.538
dн = 0.015 м – диаметр насадки
m=0.133* dн-0.5 = 0.133*0.015-0.5 = 1.086 – вспомогательный коэффициент (стр. 198 [2])
= 0.0708 кгс2 – вязкость воды при температуре в абсорбере (табл.XXXIX [1])
Расчёт коэффициентов массоотдачи
Коэффициент массоотдачи y можно найти из уравнения:
Nuy = 0.407Rey0.665*Pry 0.33 где Nuy = y* dэDy
Dy – коэффициент диффузии аммиака в газовоздушной смеси (5.20 [2])
NH3 и возд – мольные объёмы аммиака и воздуха см3моль (25.8 и 29.9 соотв.) [3]
MNH3 и Mвозд – мольные массы аммиака и воздуха гмоль (17 и 29 соотв.) [3]
Rey = – критерий Рейнольдса
y = 0.0181*10-3 Па*с – вязкость воздуха (табл. V [1])
Pry = – диффузионный критерий Прандтля
Подставив численные значения получим:
Выразим в необходимой размерности:
y = 0.134(1.074 – ) = 0.139 кгм2*с
Коэффициент массоотдачи в жидкой фазе найдём из уравнения 5.22 [2]
x = 0.0021(Dxпр) Rex0.75*Prx0.5
Dx – средний коэффициент диффузии аммиака в воде
пр = 13 – приведённая толщина стекающей плёнки жидкости
Rex = 4*U*ρxa*x – модифицированный критерий Рейнольдса для стекающей по насадке плёнке жидкости
Dx = 7.4*10-12*(*Mвод)0.5*T(x*NH30.6)
= 2.6 – коэффициент учитывающий ассоциацию молекул в воде
Mвод = 18 гмоль – мольная масса воды
Подставив числовые значения получим:
x = 1*10-4*(1000-0.0008) = 9.9*10-2 кгм2*с
Коэффициент массопередачи
Коэффициент массопередачи Ky находят по уравнению аддитивности фазовых диффузионных сопротивлений:
m – коэффициент распределения кгкг
Найдём m по данным из таблицы (пункт 1.2)
m = (*к - *н)(к - к) = (0.056-0)(0.0244-0) = 2.29 кгкг
Подставив числа получим
Поверхность массопередачи и высота абсорбера
Поверхность массопередачи определим по формуле 5.1 [2]
F = M Ky* Δср = 0.186(0.033*0.0115) = 490 м2
Высоту насадки необходимую для создания этой поверхности массопередачи рассчитаем по формуле:
H = F(0.785a*d2*) = 490(0.785*330*1.42*0.538) = 1.8 м
Расстояние между днищем абсорбера и насадкой Zн определяется необходимостью равномерного распределения газа по поперечному сечению колонны. Расстояние от верха насадки до крышки абсорбера Zв зависит от размеров распределительного устройства для орошения насадки и от высоты сепарационного пространства. Согласно [3] примем эти расстояния равными соответственно 2.5 и 2.0 м. Тогда общая высота одного абсорбера:
Ha = H + Zв + Zн = 1.8 + 2.5 + 2.0 = 6.3 м
Гидравлическое сопротивление абсорбера
Рассчитывают по формуле 5.25 [2]
ΔPc – гидравлическое сопротивление сухой насадки Па
U – плотность орошения м3м2*с
b – вспомогательный коэффициент [3]
Гидравлическое сопротивление сухой насадки определяют по следующему уравнению:
ΔPc = λ*(Hdэ)*(W22)*ρy
Где λ = 16Rey0.2 = 1620900.2 = 3.47 – коэффициент сопротивления беспорядочно насыпанных насадок при турбулентном режиме
Н – высота насадки м
Подставив значения получим
ΔPc = 3.47*(1.80.009)*(2.7422)* 1.074 = 4440 Па
ΔP = ΔPc*10184*0.00878 = 185 кПа
Основные результаты расчёта абсорбера
Производительность абсорбера по поглощаемому компоненту
U = 87.8*10-4 м3м2*с
x = 9.9*10-2 кгм2*с
Проектирование аппарата
Разделим насадку на равные слои между которыми выберем конструктивно высоту h3. Она будет складываться из высоты тарелки и расстояния между тарелкой и нижней насадкой:
Тогда H= 6300 + 1300 = 7600 мм
Между слоями насадки устанавливаем перераспределительную тарелку
ТСН-II над верхним слоем насадки устанавливаем распределительную
Техническая характеристика тарелок:
Fс – свободное сечение тарелки;
Fт – рабочее сечение тарелки;
Fсл – сечение слива;
U – максимальная допустимая нагрузка по жидкости;
n – число отверстий слива жидкости.
Конструктивный расчёт
= D*P(2*д* – P) + Ск = 1.4*1(2*183*1 – 1) + 0.001 = 0.0048 м
где д = 183 МНм2 – допускаемое напряжение;
= 10 – коэффициент ослабления из-за сварного шва
Ск = 0001 м – поправка на коррозию
Принимаем толщину обечайки = 8 мм.
Наибольшее распространение в химическом машиностроении получили эллиптические отбортованные днища по ГОСТ 6533 – 78
Толщину стенки днища принимаем = 10 мм.
Расчёт диаметра штуцеров
Рассчитаем по формуле:
Штуцер входа и выхода поглотителя (воды)
d12 = (13.4320.785*1*1000)0.5 = 0.130 м
Принимаем d12 = 200 мм
Штуцер входа и выхода газовоздушной смеси
d34 = (3.9660.785*12*1.074) = 0.358 м
Принимаем d34 = 400 мм
Разработка чертежа аппарата
Проведение предыдущих расчётов необходимо для проектирования аппарата (насадочного абсорбера) для работы в заданных условиях. Основные параметры (высота абсорбера насадки толщина обечайки и др.) необходимы для разработки чертежа насадочного абсорбера.
В ходе данного курсового проекта был рассчитан и запроектирован насадочный абсорбер для улавливания аммиака из газо-воздушной смеси водой работающий при температуре 33 атмосферном давлении и при расходе газо-воздушной смеси 13500 м3ч. Был выбран тип конструкция и рассчитаны размеры проектируемого аппарата. Полностью произведён расчёт насадочного абсорбера рассчитаны следующие характеристики: масса поглощаемого вещества и расход поглотителя; движущая сила массопередачи; коэффициент массопередачи; коэффициенты массоотдачи; скорость газа и диаметр абсорбера; плотность орошения и активная поверхность насадки; расчёт коэффициентов массоотдачи; поверхность массопередачи и высота абсорбера; гидравлическое сопротивление абсорбера. Также был произведён расчёт основных узлов и деталей абсорбера.
Список используемой литературы
Павлов К.Ф. Романков П.Г. Носков А.А. Примеры и задачи по курсу процессов и аппаратов химической технологии Под ред.П.Г. Романкова. – 10-е изд. перераб. и доп. - Л.: Химия 1987. - 510 с.
Дытнерский Ю.И. Борисов Г.С. Брыков В.П. и др. Основные процессы и аппараты химической технологии: Пособие по проектированию 2-е изд. - М.: Химия 1991. - 496с.
Рамм В.М. Абсорбция газов Изд. 2-е перераб. и доп. - М.: Химия 1976 г. - 650 с.
Касаткин А.Г. Основные процессы и аппараты химической технологии: Учеб. для студ. хим. – технол. спец. вузов. – 9-е изд; испр. - М.: Химия 1971. - 784 с.
Рамм В.М. Абсорбционные процессы в химической промышленности М.: Госхимиздат 1951 г. - 351 с.
Насад. абсорбер - Чертёж.cdw

Давление в колонне-атмосферное.
Расход инертного газа - 13500 м
Среда в аппарате - токсичная.
Тип колонны - насадочная.
Технические характеристики