Технология сварки сепаратора НГС




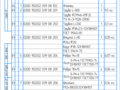
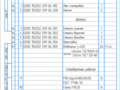
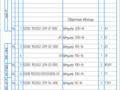
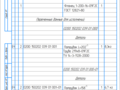
- Добавлен: 04.11.2022
- Размер: 6 MB
- Закачек: 3
Описание
Состав проекта
![]() |
![]() |
![]() |
![]() ![]() ![]() ![]() |
![]() ![]() ![]() |
![]() ![]() ![]() ![]() |
![]() |
![]() |
![]() |
![]() |
![]() ![]() ![]() |
![]() ![]() ![]() |
![]() |
![]() |
![]() |
![]() |
![]() |
![]() |
![]() |
![]() ![]() ![]() |
![]() |
![]() |
![]() ![]() ![]() ![]() |
![]() ![]() ![]() ![]() |
![]() |
![]() |
![]() |
![]() |
![]() |
![]() |
![]() |
![]() ![]() ![]() |
![]() |
![]() ![]() ![]() |
![]() ![]() ![]() ![]() |
![]() ![]() ![]() ![]() |
![]() |
![]() |
![]() |
![]() |
![]() |
![]() ![]() ![]() |
![]() ![]() ![]() |
![]() |
![]() ![]() ![]() |
![]() |
![]() ![]() ![]() |
![]() |
![]() ![]() ![]() |
![]() ![]() ![]() |
![]() ![]() ![]() ![]() |
![]() ![]() ![]() |
![]() |
![]() ![]() ![]() |
![]() |
![]() |
![]() ![]() ![]() |
![]() ![]() ![]() |
![]() |
![]() |
![]() |
![]() |
![]() |
![]() |
![]() |
![]() ![]() ![]() |
![]() ![]() ![]() |
![]() ![]() ![]() |
![]() ![]() ![]() |
![]() ![]() ![]() |
![]() ![]() ![]() |
![]() ![]() ![]() |
![]() ![]() ![]() |
![]() ![]() ![]() |
![]() ![]() ![]() |
![]() ![]() ![]() |
Дополнительная информация
0200.150202.039.06.000 СБ (Отбойник).cdw

Гайки поз.12 прихватить по трем граням к нижней полки поз.5.
Отверстия под болты на люке смотровом поз.1 и стенке нижней поз.3 выполнить
Антикоррозионное покрытие на люк смотровой поз.1 нанести отдельно.
Внутренную резьбу гаек поз.13
при нанесении внутреннего антикоррозионного покрытия
Прокладку поз.8 приклеить к люку смотровому поз.1.
* Размеры для справок.
0200.150202.039.09.006 (Плита опорная).cdw

0200.150202.039.00.002 (Лист опорный).cdw
* Размеры для справок.
Длина развертки (1508
Допускается изготовление из 2-х частей. Сварка по
ГОСТ 14771-76-C21-УП. Сварочная проволока Св-08Г2С
ГОСТ 2246-70.наплавенного металла 0
Контроль сварного шва: визуальный осмотр и измерение.
Допускаемый сварной шов зачистить заподлицо со стороны
приварки опорного листа к корпусу.
0200.150202.039.09.000 СБ (Опора неподвижная).cdw
* Размеры для справок.
Технические требования по ОСТ 26-2091-93.
Место для заземления нанести на опору яркой несмываемой
) привязать проволокой к отверстию плиты
Маркировать: М42. Маркировку производить яркой
несмываемой краской.
Чертеж разработан на основании ОСТ 26-2091-93.
0200.150202.039.00.000 СБ (Сепаратор нефтегазовый НГС-II-1,0-1200-1-И).cdw

Минимально-допустимая
отрицательная температура
Категория взрывоопсности
по ГОСТ Р 51330.11-99
Группа взрывоопасности
по ГОСТ Р 51330.05-99
Прибавка на коррозию
Расчетный срок службы
Число циклов нагружения аппарата за весь
Группа аппарата по ПБ 03-576-03
Таблица 2 - Таблица штуцеров
Покрытие всех наружных поверхностей сепаратора:
Грунт ФЛ-03К ГОСТ 9109-81 в один слой
Площадь покрытия F=33 м
Покрытие всех внутренних поверхностей сепаратора:
Грунт «ЦИНОТАН» ТУ 2312-017-12288779-2003 (в два слоя
толщина каждого слоя 40 60 мкм);
Антикоррозионная композиция «ФЕРРОТАН» ТУ
12-036-12288779-2003 (в два слоя
толщина каждого слоя
100 мкм.) Общая толщина покрытия 250 320 мкм.
Площадь покрытия F=30 м
Обработанные неокрашенные поверхности покрыть смазкой
Т55-5 ГОСТ 19537-83. F = 1 м
Шпатлевка автомобильная марки "Мобихел".- 0
Шероховатость поверхностей в местах реза деталей без
чертежа должна быть
Позиционное отклонение (в радиусном измерении) осей
штуцеров и люков должно быть не более
Каждая труба из стали 09Г2С по ТУ 14-3-1128-2000 должна
Сталь 09Г2С по ГОСТ 19281-89 с содержанием серы и
Отклонение обечайки от прямолинейности должно быть не
Маркировать места строповки
бокового положения горизонтального аппарата на фундаменте
надписи "Место для заземления"
места клейма сварщика
маркировки отверстий "М42" на опорной плите
несмываемой краской отличительной от цвета аппарата. F = 1 м
Дополнительные технические требования
не прикладываемые к паспорту аппарата
Схема расположения строповых устройств
центра масс и мест крепления стропов аппарата (1:40)
(Остальное условно не показано)
Остальное не показано
Методы контроля сварных швов
ГОСТ 8713-79-С29-АФф
ГОСТ 14771-79-С21-УП
ГОСТ 14771-76-Н1-УП-
Сепаратор нефтегазовый
*Размеры для справок.
Сепаратор подлежит ведению Ростехнадзора.
На сепаратор распространяются требования ПБ 03-576-03
"Правила устройства и безопасной эксплуатации сосудов
работающих под давлением.
испытания и приёмку сепаратора производить в
соответствии с требованиями ПБ 03-576-03
ГОСТ Р 52630-2006 и ТУ 3615-016-88138445-2009.
Неуказанные предельные отклонения размеров механически
обработанных поверхностей - H14
; для поверхностей без
механической обработки
а также между обработанной и
необработанной до 500 мм - H17
; свыше 500 до 3150 мм
; свыше 3150 мм - H15
Острые кромки внутренних элементов должны быть
закруглены. Все внутренние элементы не должны иметь резких
подрезов и острых кромок.
Внутренние кромки патрубков скруглить радиусом 5
Антикоррозионная композиция «ФЕРРОТАН»
ТУ 2312-036-12288779-2003 (в два слоя
На период транспортировки и хранения сепаратор
герметизировать транспортными заглушками.
Требования по пожарной безопасности на объекте
устанавливается настоящее оборудование
соответствовать ГОСТ 12.1.004-91.
Общие требования по взрывобезопасности на объекте
устанавливается настоящий сепаратор
должны соответствовать
остановку и испытание на герметичность аппарата в
зимнее время проводить в соответствии с "Регламентом
Класс герметичности аппарата 5-ый по ОСТ 26.260.14-2001.
Испытание на герметичность в процессе гидроиспытания.
Направление горизонтальной оси аппарата в плане для
выверки положения на фундаменте смотри на схеме строповки.
Расчетный срок службы при скорости проникновения коррозии
мм в год - не более 20 лет.
Сепаратор теплоизолировать на монтаже.
0200.150202.039.04.000 (Штуцер 50-16).spw

Обечайка ВО.dwg
Сепаратор нефтегазовый
*Размеры для справок.
Сепаратор подлежит ведению Ростехнадзора.
На сепаратор распространяются требования ПБ 03-576-03
"Правила устройства и безопасной эксплуатации сосудов
работающих под давлением.
испытания и приёмку сепаратора производить в
соответствии с требованиями ПБ 03-576-03
ГОСТ Р 52630-2006 и ТУ 3615-016-88138445-2009.
Неуказанные предельные отклонения размеров механически
обработанных поверхностей - H14
; для поверхностей без
механической обработки
а также между обработанной и
необработанной до 500 мм - H17
; свыше 500 до 3150 мм
; свыше 3150 мм - H15
Острые кромки внутренних элементов должны быть
закруглены. Все внутренние элементы не должны иметь резких
подрезов и острых кромок.
Внутренние кромки патрубков скруглить радиусом 5
Покрытие всех наружных поверхностей сепаратора:
Грунт ФЛ-03К ГОСТ 9109-81 в один слой
Покрытие всех внутренних поверхностей сепаратора:
Грунт «ЦИНОТАН» ТУ 2312-017-12288779-2003 (в два слоя
толщина каждого слоя 40 60 мкм);
Антикоррозионная композиция «ФЕРРОТАН»
ТУ 2312-036-12288779-2003 (в два слоя
толщина каждого слоя
100 мкм.) Общая толщина покрытия 250 320 мкм.
На период транспортировки и хранения сепаратор
герметизировать транспортными заглушками.
Требования по пожарной безопасности на объекте
устанавливается настоящее оборудование
соответствовать ГОСТ 12.1.004-91.
Общие требования по взрывобезопасности на объекте
устанавливается настоящий сепаратор
должны соответствовать
остановку и испытание на герметичность аппарата в
зимнее время проводить в соответствии с "Регламентом
Класс герметичности аппарата 5-ый по ОСТ 26.260.14-2001.
Испытание на герметичность в процессе гидроиспытания.
Направление горизонтальной оси аппарата в плане для
выверки положения на фундаменте смотри на схеме строповки.
Расчетный срок службы при скорости проникновения коррозии
мм в год - не более 20 лет.
Сепаратор теплоизолировать на монтаже.
Чертеж разработан на основании технического проекта
Таблица 1 - Техническая характеристика
Минимально-допустимая
отрицательная температура
Категория взрывоопсности
по ГОСТ Р 51330.11-99
Группа взрывоопасности
по ГОСТ Р 51330.05-99
Прибавка на коррозию
Расчетный срок службы
Число циклов нагружения аппарата за весь
Группа аппарата по ПБ 03-576-03
Таблица 2 - Таблица штуцеров
Площадь покрытия F=33 м
Антикоррозионная композиция «ФЕРРОТАН» ТУ
12-036-12288779-2003 (в два слоя
Площадь покрытия F=30 м
Обработанные неокрашенные поверхности покрыть смазкой
Т55-5 ГОСТ 19537-83. F = 1 м
Шпатлевка автомобильная марки "Мобихел".- 0
Шероховатость поверхностей в местах реза деталей без
чертежа должна быть
Позиционное отклонение (в радиусном измерении) осей
штуцеров и люков должно быть не более
Каждая труба из стали 09Г2С по ТУ 14-3-1128-2000 должна
Сталь 09Г2С по ГОСТ 19281-89 с содержанием серы и
Отклонение обечайки от прямолинейности должно быть не
Маркировать места строповки
бокового положения горизонтального аппарата на фундаменте
надписи "Место для заземления"
места клейма сварщика
маркировки отверстий "М42" на опорной плите
несмываемой краской отличительной от цвета аппарата. F = 1 м
Дополнительные технические требования
не прикладываемые к паспорту аппарата
Схема расположения строповых устройств
центра масс и мест крепления стропов
(Остальное условно не показано)
Остальное не показано
Методы контроля сварных швов
ГОСТ 8713-79-С29-АФф
ГОСТ 14771-79-С21-УП
ГОСТ 14771-76-Н1-УП-
00 150202 039 39 000 ВО
0200.150202.039.04.000 СБ (Штуцер 50-16).cdw
Сварка электродом Э 50А ГОСТ 9467-75. Масса
наплавленного металла - 0
кг. Корень шва подварить в среде
аргона неплавящимся электродом сварочной проволокой Св-08Г2С
ГОСТ 2246-70.наплавленного металла - 0
Контроль шва : визуальный осмотр и измерения
0200.150202.039.09.000 (Опора неподвижная).spw

0200.150202.039.11.000 (Ушко траспортировочное).spw

Б-ПН-О-10 ГОСТ19903-74
Ст3сп4-св ГОСТ14637-89
Б-О-ПН-10 ГОСТ19903-74
Х18Н10Т-М2б ГОСТ7350-77
0200.150202.039.11.000 СБ (Ушко траспортировочное).cdw
*Размеры для справок.
**Радиус «R» выбирается по наружному диаметру
Шероховатость поверхностей в местах реза детали БЧ
Подкладку поз. 2 применять при толщине аппарата менее
0200.150202.039.01.000 СБ (Штуцер 200-16).cdw
Сварка электродом Э 50А ГОСТ 9467-75. Масса
наплавленного металла - 0
Контроль шва : визуальный осмотр и измерения
Допускается сварка по ГОСТ 14771-76-С21-УП сварочной
проволокой Св-08Г2С ГОСТ 2246-70.
0200.150202.039.08.200 СБ (Каплеуловить).cdw
Сварка по ГОСТ 5264-80
электродом Э-50А ГОСТ 9467-75.
Антикоррозионное покрытие нанести до сборки.
0200.150202.039.08.200 (Каплеуловитель).spw

0200.150202.039.00.000 (Сепаратор нефтегазовый НГС-II-1,0-1200-1-И).spw
Пояснительная записка
Короб каплеуловителей
Ушко транспортировочное
Бобышка 1-2-G 12-50
Скоба для крепления
Б-ПН-0-10 ГОСТ 19903-74
5-09Г2С-6 ГОСТ 19281-89
Б-ПН-0-4 ГОСТ19903-74
Фланцы ГОСТ 12821-80
Заглушки АТК 24.200.02.90
Прокладки ГОСТ 15180-86
Гайки ОСТ 26-2038-96
Шпильки ОСТ 26-2040-96
0200.150202.039.00.000 ВО.dwg
Сепаратор нефтегазовый
*Размеры для справок.
Сепаратор подлежит ведению Ростехнадзора.
На сепаратор распространяются требования ПБ 03-576-03
"Правила устройства и безопасной эксплуатации сосудов
работающих под давлением.
испытания и приёмку сепаратора производить в
соответствии с требованиями ПБ 03-576-03
ГОСТ Р 52630-2006 и ТУ 3615-016-88138445-2009.
Неуказанные предельные отклонения размеров механически
обработанных поверхностей - H14
; для поверхностей без
механической обработки
а также между обработанной и
необработанной до 500 мм - H17
; свыше 500 до 3150 мм
; свыше 3150 мм - H15
Острые кромки внутренних элементов должны быть
закруглены. Все внутренние элементы не должны иметь резких
подрезов и острых кромок.
Внутренние кромки патрубков скруглить радиусом 5
Покрытие всех наружных поверхностей сепаратора:
Грунт ФЛ-03К ГОСТ 9109-81 в один слой
Покрытие всех внутренних поверхностей сепаратора:
Грунт «ЦИНОТАН» ТУ 2312-017-12288779-2003 (в два слоя
толщина каждого слоя 40 60 мкм);
Антикоррозионная композиция «ФЕРРОТАН»
ТУ 2312-036-12288779-2003 (в два слоя
толщина каждого слоя
100 мкм.) Общая толщина покрытия 250 320 мкм.
На период транспортировки и хранения сепаратор
герметизировать транспортными заглушками.
Требования по пожарной безопасности на объекте
устанавливается настоящее оборудование
соответствовать ГОСТ 12.1.004-91.
Общие требования по взрывобезопасности на объекте
устанавливается настоящий сепаратор
должны соответствовать
остановку и испытание на герметичность аппарата в
зимнее время проводить в соответствии с "Регламентом
Класс герметичности аппарата 5-ый по ОСТ 26.260.14-2001.
Испытание на герметичность в процессе гидроиспытания.
Направление горизонтальной оси аппарата в плане для
выверки положения на фундаменте смотри на схеме строповки.
Расчетный срок службы при скорости проникновения коррозии
мм в год - не более 20 лет.
Сепаратор теплоизолировать на монтаже.
Чертеж разработан на основании технического проекта
Таблица 1 - Техническая характеристика
Минимально-допустимая
отрицательная температура
Категория взрывоопсности
по ГОСТ Р 51330.11-99
Группа взрывоопасности
по ГОСТ Р 51330.05-99
Прибавка на коррозию
Расчетный срок службы
Число циклов нагружения аппарата за весь
Группа аппарата по ПБ 03-576-03
Таблица 2 - Таблица штуцеров
Площадь покрытия F=33 м
Антикоррозионная композиция «ФЕРРОТАН» ТУ
12-036-12288779-2003 (в два слоя
Площадь покрытия F=30 м
Обработанные неокрашенные поверхности покрыть смазкой
Т55-5 ГОСТ 19537-83. F = 1 м
Шпатлевка автомобильная марки "Мобихел".- 0
Шероховатость поверхностей в местах реза деталей без
чертежа должна быть
Позиционное отклонение (в радиусном измерении) осей
штуцеров и люков должно быть не более
Каждая труба из стали 09Г2С по ТУ 14-3-1128-2000 должна
Сталь 09Г2С по ГОСТ 19281-89 с содержанием серы и
Отклонение обечайки от прямолинейности должно быть не
Маркировать места строповки
бокового положения горизонтального аппарата на фундаменте
надписи "Место для заземления"
места клейма сварщика
маркировки отверстий "М42" на опорной плите
несмываемой краской отличительной от цвета аппарата. F = 1 м
Дополнительные технические требования
не прикладываемые к паспорту аппарата
Схема расположения строповых устройств
центра масс и мест крепления стропов
(Остальное условно не показано)
Остальное не показано
Методы контроля сварных швов
ГОСТ 8713-79-С29-АФф
ГОСТ 14771-79-С21-УП
ГОСТ 14771-76-Н1-УП-
Категория взрывоопасной
Таблица 1. Таблица штуцеров
Наклон ячеек просечно-
общей толщиной 250-320мкм:
** Массу аппарата уточнить по выпуску конструкторской документации завода-изготовителя.
Заземление аппарата согласно ПУЭ.
- цинотан (в два слоя
толщина каждого слоя 40-60мкм);
- ферротан (в два слоя
толщина каждого слоя 85-100мкм).
В перегородке из просечно-вытяжного листа выполнить переходный люк (дверь) 600х600.
Конструкцию антизавихрителя штуцера Д1 и пропарочного трубопровода выполнить по
испытание и поставка аппарата производятся в соответствии с
Обеспечить внутреннее антикоррозионное покрытие аппарата и всех внутренних устройств
ОСТ26-291-94 "Сосуды и аппараты сварные. Общие технические условия"
ПБ 03-576-03 "Правила
Группа взрывоопасной
Технические требования
Фланцы штуцеров - по ГОСТ 12821-80.
На аппарате предусмотреть крепления для теплоизоляции.
Опоры выполнить согласно ОСТ 26-2091-93.
Днища корпуса эллиптические выполнить по ГОСТ 6533-78.
работающих под давлением" ПБ 03-576-03.
устройства и безопасной эксплуатации сосудов
работающих под давлением".
Расчетный срок службы сосуда
Масса сепаратора. кг
Аппарат расположен на открытой площадке. Сейсмичность района 9 баллов.
Ответные фланцы и заглушки должны быть укомплектованы прокладками и крепежом.
Аппарат подлежит действию "Правил устройства и безопасной эксплуатации сосудов
Прибавка для компенсации коррозии
листа повернутые относительно
Перегородки из просечно-вытяжного
Расчетная температура стенки
Абсолютная минимальная температура
Наименование рабочей среды
Рабочая температура среды
Таблица 1. Техническая характеристика
Рукав сетчатый 3рулона
00 150202 039 00 000 ВО
Сеппаратор нефтегазовый
0200.150202.039.07.000 СБ (Антизавихритель).cdw
Сварку произвести электродом типа Э 50А ГОСТ 9467-75
масса наплавленного металла- 0
Контроль сварного шва: визуальный осмотр и измерения.
1 ОПИСАНИЕ ИЗДЕЛИЯ И УСЛОВИЯ ЕГО ЭКСПЛ.doc
1 Описание и назначение сепараторов нефтегазовых типа НГС
Сепараторы нефтегазовые типа НГС используются для очистки попутного газа для дегазации непенящихся нефтей а также для подготовки продукции нефтяных месторождений в установках сбора. Нефтегазовый сепаратор НГС также применяется для входных промежуточных и концевых ступеней в промысловых установках для подготовки нефти и газа.
Нефтегазовые сепараторы представляю собой емкостные устройства необходимые для очистки нефтяной эмульсии от попутного газа. Также сепараторы очищают сам газ удаляя взвешенные капли жидких углеводородов частички пыли технические загрязнения и пары катализаторных ядов. Надо сказать что сепараторы представляют собой аппараты первичной очистки. Продукт на выходе недостаточно чистый для катализируемых реакций. Между тем нефтегазовые сепараторы совершенно незаменимы так как сырой газ может повредить тонкие фильтры вторичной очистки.
Существуют различные типы и виды нефтегазовых сепараторов. Они различаются рядом конструктивных особенностей накладывающих ограничения по чистоте и свойствам сырья. Прежде всего нефтегазовые сепараторы различаются по наличию или отсутствию депульсатора – то есть специального штуцера обеспечивающего предварительный отбор газа. Также важным является наличие или отсутствие пеногасящей насадки позволяющей сепарировать нефтяные пены.
Техническое описание нефтегазового сепаратора обязательно включает в себя указание основных технических характеристик инструкцию по эксплуатацию и рекомендуемую сферу применения.
Изготовление нефтегазовых сепараторов требует точного соблюдения технологии. От работоспособности этих аппаратов напрямую зависит работоспособность всей технологической линии а возможно и всего предприятия. Именно поэтому качество изготовления сепараторов приобретает такое большое значение.
В качестве исходного материала используется листовая сталь. Обычно применяется малолегированная сталь стойкая к механическим воздействиям и высокому давлению. С помощью автоматизированного оборудования стальному листу придают форму цилиндра и затем – резервуара. После этого идет монтаж дополнительного оборудования и перегородок. Сепарирующие сетки изготавливаются из металлической проволоки которая в свою очередь изготавливается из другого вида стали. Этот сорт стоек к коррозии не боится традиционных примесей нефти и высоких температур.
Завод по производству нефтегазовых сепараторов несет полную ответственность за качество своей продукции. Именно поэтому каждый аппарат тщательно проверяется. Его тестируют на герметичность способность работать в граничных условиях и при сверхвысоких нагрузках. Также проверяется соответствие эксплуатационных показателей заявленным. Нефтегазовые сепараторы как и вся продукция подобных предприятий обязательно сертифицируются по отечественным и международным стандартам.
2 Конструкция и технические характеристики НГС-II-10-1200-1-И
Сепаратор нефтегазовый НГС представляют собой горизонтально расположенный металлический аппарат с эллиптическими днищами внутри которого имеется уголковый отбойник для первичного разделения потока рабочей жидкости. Чтобы поток внутри имел равномерную скорость сепараторы нефтегазовые оснащаются вертикальной перегородкой состоящей из просечно-вытяжных листов и струнным каплеуловителем. Система штуцеров обеспечивает подачу и выход жидкости в различных режимах работы. Необходимыми элементами оснащения являются контрольно-измерительные приборы и аппаратура управления а специальная насадка называемая пеногаситель препятствует образованию пены внутри устройства. Конструкция сепаратора полностью исключает возможность утечки нефтепродуктов.
Рисунок 1.1 – Сепаратор нефтегазовый типа НГС
Работа сепараторов заключается в следующем: в секцию ввода поступает нефть с газом. Там происходит предварительное разделение свободного газа от нефти. Дальше при поступлении в зону осаждения и отстоя (перфорированные распределяющие успокаивающие перегородки) газ частично очищается от крупных капель жидкости т. е. происходит дегазация нефти. Там же происходит выделение растворенного газа. Струнные каплеуловители на выходе завершают процесс очищения газа.
Рисунок 1.2 – Сепаратор нефтегазовый НГС-II-10-1200-1-И
Объем аппарата расчетное давление материальное исполнение и другие определяющие технические характеристики подбираются в соответствии с условиями эксплуатации: производительность по жидкой и газовой среде рабочее давление климатические условия коррозионная активность среды и другие. Основные технические характеристики аппарата НГС-II-10-1200-1-И представлены в таблице 1.1.
Таблица 1.1 – Основные технические характеристики
Абсолютная минимальная
Газ нефть пластовая вода
Класс опасности ГОСТ 12.1.007-76
Категория и группа взрывоопасной смеси по ПУЭ
Группа аппарата по ПБ 03-576-03
Прибавка для компенсации коррозии мм
Расчетный срок службы сосуда лет
Для изготовления обечайки данного аппарата использована листовая сталь Б-ПН-0-10 ГОСТ 19903-74 из стали марки 09Г2С-6 ГОСТ 19281-89.
Список литературы.doc
ГОСТ Р 52857.1-2007. Сосуды и аппараты. Нормы и методы расчета на прочность. Общие требования.
ГОСТ Р 52857.5-2007. Сосуды и аппараты. Нормы и методы расчета на прочность. Расчет обечаек и днищ от воздействия опорных нагрузок.
Лащинский А.А. Конструирование сварных химических аппаратов А.А. Лащинский. Под редакцией к.т.н. А.Р. Толчинского. – М.: Машиностроение 1981. – 752 с.
Фетисов Г.П. Материаловедение и технология металлов. Учебник для вузов Г.П. Фетисов – М.: Высшая школа 2000. – 638 с.
Марочник сталей и сплавов Под общ. редакцией А.С. Зубченко – М.: Машиностроение 2003. - 784 с.
Шарафиев Р.Г. Основы проектирования цехов по изготовлению нефтегазового оборудования Р.Г. Шарафиев – Уфа: Изд-во УГНТУ 2012. – 265 с.
Климов А.С. Роботизированные технологические комплексы и автоматические линии в сварке А.С. Климов Н.Е. Машнин – С.-Петербург: Лань 2011. – 234 с.
Николаев Г.А. Сварные конструкции. Расчёт и проектирование Г.А. Николаев В.А. Винокуров. Под редакцией академика Г.А. Николаева – М.: Высшая школа 1990. – 446 с.
Прох Л.Ц. Справочник по сварочному оборудованию Л.Ц. Прох Б.М. Шпаков Н.М. Яворская – М.: Техника 1978. – 207 с.
Фролов В.В. Теория сварочных процессов В.В. Фролов – М.: Высшая школа 1988. – 559 с.
Дальский А.М.Технология конструкционных материалов: Учебник для студентов машиностроительных специальностей вузов А. М. Дальский Т. М. Барсукова Л. Н. Бухаркин и др.; Под общей ред. А. М. Дальского – 5-е изд. исправленное – М.: Машиностроение 2003. – 512 с.
Технология металлов и сварка: Учебник для вузов Под ред. П.И. Полухина – М.: ЭКОЛИТ 2011. – 464 с.
Дунаев П.Ф. Детали машин и основы конструирования П.Ф. Дунаев О.П.Леликов – М.: Высшая школа 2008. – 447 с.
Безопасность производственных процессов: Справочник. Под общей редакцией С.В.Белова – М.: Машиностроение 2005. – 448с.
МалышевБ.Д.Безопасность труда при выполнении сварочных работ в строительстве: Учебник Б.Д. Малышев И.Г. Гетия – М.: Стройиздат 1988. – 88с.
РЕФЕРАТ.doc
Пояснительная записка содержит 125 страниц включая 35 рисунков 24 таблицы 55 формул 15 литературных источников.
Работа состоит из введения 7 разделов заключения.
Во введении отражена актуальность задачи и описаны основные требования к проекту.
В первом разделе произведено описание выбранного оборудования (сепаратор нефтегазовый типа НГС) и условий его эксплуатации.
Во втором разделе приводится обзор современных методов изготовления обечаек.
В третьем разделе произведено обоснование выбора материала и марки стали для изготовления обечайки нефтегазового сепаратора произведены технологические расчеты режимов сварки а также предложен способ совершенствования выбранного способа сварки.
В четвертом разделе проведены механические расчеты на прочность сварных швов расчеты на прочность и устойчивость обечайки сепаратора.
В пятом разделе проведена калькуляция изготовления нефтегазового сепаратора проведен расчет показателей экономической эффективности.
Шестой раздел посвящен вопросам обеспечения безопасности на производстве и охраны труда работников.
В седьмом разделе отражены вопросы обеспечения экологичности проекта.
Заключение включает основные выводы по работе.
5 Экономическая часть.docx
Целью экономического раздела является расчет себестоимости изготовления нефтегазового сепаратора прибыли предприятия-изготовителя и экономической эффективности.
Экономический раздел начинается с расчета затрат на эксплуатацию машин и оборудования. Затем составляется калькуляция стоимости из расчета на одну тонну массы металлоконструкции. В ней отдельно рассматривается стоимость основных и вспомогательных материалов для изготовления составных частей сепаратора. Затем вычисляется полная себестоимость изготовления продукции его оптовая цена прибыль и затраты на 1 рубль товарной продукции.
1 Расчет затрат на эксплуатацию машин и оборудования
Затраты на эксплуатацию машин и оборудования определяются по формуле
где: Тоб. – время в течении которого используется оборудование ч;
См-ч. - стоимость машино-часа эксплуатации оборудования руб.
В таблице 5.1 приведен расчет затрат на эксплуатацию машин и оборудования из расчета на одну тонну металлоконструкций. В таблице приведены наименования работ по изготовлению. По каждому наименованию работ представлены механизмы используемые в данном виде работы с объемом машино-часов стоимости машино-часа работы механизма из расчета на одну тонну металлоконструкции.
Стоимость машино-часа работы механизма представляет собой затраты на эксплуатацию электроэнергию топливо из расчета на изготовление одной тонны металлоконструкции без учета заработной платы рабочего персонала.
Нормы машино-часов приняты на основании ГЭСНм-2001-38 «Изготовление технологических металлических конструкций в условиях производственных баз».
Таблица 5.1 – Результаты расчета затрат на эксплуатацию машин и оборудования из расчета на одну тонну металлоконструкций
Наименование работ и механизмов
На одну тонну металлоконструкций
Стоимость единицы См-ч руб.
Стоимость затрат Сэк. руб.
Изготовление обечайки днищ и опор
Аппарат для газовой сварки и резки
Машины шлифовальные электрические
Ножницы листовые гильотинные
Прессы гидравлические
Изготовление площадок и лестниц для обслуживания оборудования
Пресс-ножницы комбинированные
Изготовление люков-лазов патрубков и молниеприёмников
Прессы листогибочные
Машины специальные (вальцы)
Изготовление внутренних устройств
Контроль сварных соединений просвечиванием рентгеновскими установками
Аппарат рентгеновский
Огрунтовка металлических поверхностей грунтовкой ГФ-021
Лебёдка электрическая 5 т
Агрегат окрасочный ВД Р=1 кВт
Итого сумма затрат на эксплуатацию машин и оборудования из расчета на одну тонну металлоконструкций:
Сэк. = 169724 +254447 + 349519 + 155148 +1551 + 142 = 931809 руб.
2 Калькуляция стоимости из расчета на одну тонну массы металлоконструкций
2.1 Калькуляция изготовления обечайки днищ и опор сепаратора
Результаты расчета сведены в таблице 5.2.
Таблица 5.2 – Калькуляция изготовления обечайки днищ сепаратора и опор из расчета на одну тонну массы металлоконструкций
Основные материалы (09Г2С)
Вспомогательные материалы:
Рентгеновская пленка
Заготовительно-складские расходы (2% от п.1+п.2)
Зарплата производственных
Эксплуатация машин и оборудования
ИТОГО производственная себестоимость
Внепроизводственные расходы
Итого полная себестоимость
изготовления продукции
ИТОГО оптовая цена изготовления продукции
2.1.1 Основные материалы.
Основной материал вычисляется по формуле (4.3)
где РОМ - стоимость тонны основного материала (09Г2С) руб.;
6 – коэффициент принятый для пересчета стоимости материала на 2014 г.
Основным материалом стенки днища опор люков-лазов люков смотровых патрубков и молниеприемников является сталь 09Г2С. Основным материалом площадок для обслуживания оборудования является сталь 20.
2.1.2 Вспомогательные материалы.
При изготовлении сепаратора основными операциями являются резка сварка грунтовка и рентгеноскопия сварных швов. Вспомогательными материалами при данных операциях являются электроды сварочные проволоки кислород пропан-бутан грунт флюс рентгеновская пленка проявитель фиксаж уайт-спирит.
Затраты на вспомогательные материалы вычисляются по формуле (5.4)
где- цена одной единицы
- объем или количество
Рэл. Vэл. – цена и количество электрода
Рсв. пр.. Vсв. пр. – цена и количество сварочной проволоки
Рк Vк. – цена и количество кислорода
Рпр.-б. Vпр.-б – цена и количество пропан-бутана
Ргр. Vгр. – цена и количество грунта
Рфл. Vфл. – цена и количество флюса
Рр. пл. Vр. пл. – цена и количество рентгеновской пленки
Рпр. Vпр. – цена и количество проявителя
Рф. Vф. – цена и количество фиксажа
РУ-с. VУ-с. – цена и количество Уайт-спирита.
Заготовительно-складские операции вычисляются по формуле (5.5):
где - затраты на основной материал руб.;
- затраты на вспомогательные материалы руб.
Заработная плата производственных рабочих вычисляется по формуле (5.6)
где - средняя часовая заработная плата производственных рабочих руб.;
- количество отработанных часов ч.
Накладные расходы вычисляются по формуле (5.7)
где - заработная плата производственных рабочих руб.;
- коэффициент зависимости накладных расходов от заработной платы производственных рабочих.
Итого производственная себестоимость
где СОМ – стоимость основных материалов;
СВМ – стоимость вспомогательных материалов;
СС-З – затраты на заготовительно-складские операции;
СЭМ – затраты на эксплуатацию машин;
СЗ – затраты на заработную плату;
СОМ – накладные расходы.
К внепроизводственным расходам относится разработка чертежей и проекта на сумму равную 1100 рубт согласно калькуляции составленного на основании ГЭСНм-2001 «Изготовление металлических конструкций в условиях производственных баз».
Итого полная себестоимость составит по формуле (5.8)
СПС= 5792005+1100 = 5902005 руб.
Плановые накопления рассчитывают по (5.9)
Рентабельность вычисляют по формуле (5.10)
СР= СПС · 20% (5.10)
СР= 5902005. · 02 = 1180401руб.
Итого цена изготовления продукции без НДС
НДС находят по формуле (5.11)
СНДС = СИт. без НДС · 18% (5.11)
СНДС = 7566918 · 018 = 1362045 руб.
Итого оптовая цена изготовления продукции с НДС
СОПТ = СНДС + СИт. без НДС (5.12)
СОПТ = 1362045+ 7566918= 8928963 руб.
2.2 Калькуляция изготовления площадок и лестниц для обслуживания оборудования.
Результаты расчетов сведены в таблицу 5.3.
Таблица 5.3 – Калькуляция изготовления площадок для обслуживания оборудования из расчета на одну тонну массы металлоконструкций
Вспомогательные материалы
Заготовительно-складские расходы (2% от суммы осн. мат. и вспом. мат.)
Зплата производственных
Внепроизводственые расходы
2.2.1 Основные материалы.
Основной материал вычисляется по формуле (5.3)
где - стоимость тонны основного материала (сталь 20) руб.;
- объем или количество основного материала;
2.2.2 Вспомогательные материалы.
Вспомогательными операциями при данных операциях являются Электроды кислород пропан-бутан грунт.
Затраты на вспомогательные материалы вычисляются по формуле
Рк Vк. – цена и количество кислорода
Ргр. Vгр. – цена и количество грунта.
Заготовительно-складские операции вычисляются по формуле
Заработная плата производственных рабочих вычисляется по формуле
Накладные расходы вычисляются по формуле
СВМ – стоимость вспомогательных материалов;
СЭМ – затраты на эксплуатацию машин;
К внепроизводственным расходам относится разработка чертежей и проекта на сумму равную 1100 рубт согласно калькуляции составленного на основании ГЭСНм-2001. Изготовление металлических конструкций в условиях производственных баз.
Итого полная себестоимость составит
СП.С.= 4649572+1100 = 4759572 руб.
Рентабельность вычисляют по формуле
СР.= 4759572. · 02 = 951914 руб.
Итого оптовая цена изготовления продукции с НДС НДС=18%
СОПТ = СИт. без НДС ·118
СОПТ = 6199046·118 = 7314874 руб.
2.3 Калькуляция изготовления люков-лазов патрубков и молниеприёмников
Результаты расчетов сведены в таблицу 5.4.
Таблица 5.4 – Калькуляция изготовления люков-лазов патрубков и молниеприемников из расчета на одну тонну массы металлоконструкций
Заготовительно-складские расходы
2.3.1 Основные материалы.
где - стоимость тонны основного материала (09Г2С) руб.;
2.3.2 Вспомогательные материалы.
Вспомогательными операциями при данных операциях являются электроды кислород пропан бутан.
Заготовительно-складские операции вычисляются по формуле:
СС-З – затраты на заготовительно-складские операции;
СП.С.= 5265732+1100 = 5375732 руб.
Плановые накопления:
СР.= 5375732. · 02 = 1075146 руб.
НДС находят по формуле (4.11)
СНДС = СИт. без НДС · 18%
СНДС = 6799878 · 018 = 1223978 руб.
СОПТ = СНДС + СИт. без НДС
СОПТ = 1223978+ 668824 = 8023856 руб.
2.4 Калькуляция изготовления внутренних устройств
Результаты расчета сведены в таблице 5.5.
Таблица 5.5 – Калькуляция изготовления внутренних устройств из расчета на одну тонну массы металлоконструкций
2.4.1 Основные материалы.
2.6.2 Вспомогательные материалы.
Вспомогательными операциями при данных операциях являются электроды кислород пропан-бутан.
Рпр.-б. Vпр.-б – цена и количество пропан-бутана.
Заготовительно-складские операции вычисляются по формуле (5.5)
Итого производственная себестоимость:
где СОМ – стоимость основных материалов;
СЗ – затраты на заработную плату;
Итого полная себестоимость по формуле (5.8) составит
СП.С.= 4938681+1100 = 5048681руб.
Плановые накопления (5.9)
СР.= 5048681 · 02 = 1009736 руб.
Итого цена изготовления продукции без НДС:
СОПТ = 118 · 6345831 = 748808 руб.
3 Расчет показателей экономической эффективности
Полная себестоимость изготовления сепаратора вычисляется по формуле:
СП.С= ΣCп.с.i · mi (5.13)
где mi – масса калькулируемых деталей сепаратора тонн.
В таблице 5.6 приведены массы калькулируемых деталей сепаратора.
Таблица 5.6 – Массы калькулируемых деталей сепаратора
Обечайка днище и опоры
Площадки и лестницы для обслуживания
Люки-лазы патрубки и молниеприемники
Внутренние устройства
Полная себестоимость изготовления сепаратора:
СП.С.=25·5902005 + 03·4759572 + 02·5375732 + 04·5048681 =
Общая оптовая цена изготовления сепаратора по всем видам калькуляций составит:
СОПТ. = ΣCоптi · mi (5.14)
Итого оптовая цена изготовления сепаратора массой 3400 кг составляет:
СОПТ.= 8928963·25+7314874·03+8023856·02+ 748808·04 = 29116873 руб.
Страховые платежи составляют 30% от стоимости изготовления аппарата:
ЗСТРАХ=03· СОПТ (5.15)
где ЗСТРАХ – затраты на страховые платежи.
ЗСТРАХ=030·29116873=8735062 руб.
Учет уральского коэффициента(15% от оптовой цены изготовления сепаратора):
СУРАЛ=015· СОПТ (5.16)
СУРАЛ=015·29116873=4367531 руб.
Итого общая оптовая цена изготовления сепаратора с учетом страховых платежей и уральского коэффициента:
СОПТ.+СТРАХ= СОПТ.+ ЗСТРАХ+СУРАЛ (5.17)
СОПТ.+СТРАХ=29116873+8735062+4367531=42219466 руб.
Чистая прибыль завода-изготовителя сепаратора определяется по формуле:
ЧП = Σmi·CР.i (5.18)
mi – масса калькулируемых деталей сепаратора тонн.
ЧП = 25· 11804.01 + 03 · 951914 + 02 · 1075146 + 04 · 1009736 = 4715617 руб
Затраты на 1 рубль товарной продукции вычисляются по формуле:
З1 руб = Σ mi·Сп.с. i СИт.без НДС. i (5.19)
З1руб=25·59020057566918+03·47595726199046+02·53757326799878+
+04·50486816345831=266 рубруб.
Сп.с. i – полная себестоимость изготовления по видам калькуляций руб.
Таким образом общая оптовая цена изготовления сепаратора с учетом страховых платежей и уральского коэффициента составила 422 19466 рублей. Чистая прибыль от продажи сепаратора составит 47 15617 рублей.
4 МЕХАНИЧЕСКАЯ ЧАСТЬ.doc
1 Расчет на прочность сварного соединения
Расчеты прочности сварных конструкций и их отдельных элементов сводятся к определению напряжений в опасных (самых нагруженных) сечениях деталей и узлов.
Механические свойства материалов определяют их способность воспринимать заданные нагрузки.
Они в значительной степени характеризуют величину массы материала изделий и оказывают непосредственное влияние на их стойкость.
К основным механическим свойствам как правило относят [3]:
Предел прочности называемый нередко временным сопротивлением в представляющий собой отношение максимального усилия Р испытуемого при разрыве к первоначальной площади поперечного сечения испытуемого образца. Для стали 09Г2С в = 440 МПа
Предел текучести т - максимальное напряжение при котором деформации переходят из упругой в пластическую область. Ввиду того что при испытании различных материалов в том числе и сталей отсутствует четкая граница перехода в пластическую область т определяют как величину напряжений 02 вызывающую остаточную пластическую деформацию 02% при испытаниях образцов стандартной формы. Для стали 09Г2С т = 295 МПа.
Относительное удлинение при разрыве 5 определяемое на образцах стандартной величины.
Ударная вязкость ан характеризующаяся сопротивлением ударным воздействиям стандартных образцов с надрезами имеющими различную остроту.
Существует два основных метода расчета конструкций: по допускаемым напряжениям и по предельному состоянию [13].
При расчете по допускаемым напряжениям условие прочности должно соответствовать т = [] для низкоуглеродистых низколегированных сталей примерно равно 0.9 т т.е.
5 МПа х 09 = 2685 МПа
где т - напряжение в опасном сечении изделия;
[] - допускаемое напряжение которое составляет некоторую часть от предела текучести с учетом запаса прочности n то есть [] = т n.
n – коэффициент запаса прочности принимаемый равным 2.
Для конструкций с разным назначением коэффициент запаса прочности различен и принимается от 15 до 6.
При расчете конструкции по предельному состоянию условие прочности должно соответствовать:
где N – расчетное усилие;
F – площадь сечения;
R – расчетное сопротивление материала кгсмм2;
m - коэффициент условий работы который учитывает степень ответственности конструкции жесткость узла.
Сварные швы на прочность рассчитываются по формуле:
где N — расчетная продольная сила действующая на соединение кг;
Rcвс – расчетное сопротивление сварного стыкового соединения растяжения или сжатия кгсмм2;
S – толщина металла стыкового соединения;
Угловые швы рассчитываются по формуле:
Коэффициент 07 учитывает длину опасного сечения в угловом шве так как шов разрушается не но катету а по опасному сечению.
Зона I-I предполагаемого разрушения короче чем катет К а длина этой зоны составляет примерно 07 от К.
В расчетах прочности усиление швов во внимание не принимается.
Рисунок 4.1 – Тавровое соединение
Рисунок 4.2 – Стыковое соединение
Так как обечайка варится по средством стыкового шва рассчитаем для него растягивающее усилие:
Толщина пластаны S = 10 мм;
Длина шва L = 1500 мм
R расчетное сопротивление равно 2600 кгссм2.
Определяем расчетное растягивающее усилие (предельное состояние):
2 Расчет обечайки сепаратора на прочность и устойчивость
Исходные данные для расчета обечайки на прочность и устойчивость представлены в таблице 4.1.
Таблица 4.1 – Исходные данные для расчета
Суммарная прибавка мм
Коэфф. прочности сварного шва
Полученные эпюры сил и моментов представлены на рисунках 4.3-4.5.
Рисунок 4.3 – Эпюра продольных перемещений
Рисунок 4.4 – Эпюра поперечных усилий
Рисунок 4.5 – Эпюра изгибающего момента
Прибавка для компенсации коррозии и эрозии c1:
Прибавка для компенсации минусового допуска c2:
Прибавка технологическая c3:
Сумма прибавок к расчётной толщине стенки c:
Коэффициенты прочности сварных швов:
Расчёт в рабочих условиях
Расчётная температура T:
Расчётное внутреннее избыточное давление p:
Расчётный изгибающий момент M:
Расчётное поперечное усилие Q:
Расчётное осевое растягивающее усилие F:
Расчёт на прочность и устойчивость по ГОСТ Р 52857.2-2007
Допускаемые напряжения для материала 09Г2С при температуре T = 60 °C (рабочие условия):
Модуль продольной упругости для материала 09Г2С при температуре T = 60 °C:
Гладкая обечайка нагруженная внутренним избыточным давлением.
Расчётная толщина стенки с учётом прибавок:
= (105 * 1200)(2 * 1865 * 1 - 105) + 25
Заключение: Условие работоспособности выполнено.
Допускаемое давление:
* 1865 * 1 * (10 – 25) (1200 + 10 - 25)
Заключение: Условие прочности выполнено.
Минимальное расстояние между “одиночными” штуцерами:
= 2 * (1200 * (10 – 25))12
Обечайка нагруженная осевым растягивающим усилием.
Допускаемое осевое растягивающее усилие:
42* (1200 + 10 – 25) * (10 - 25)* 1865*1
Заключение: Условие прочности и устойчивости выполнено.
Обечайка нагруженная изгибающим моментом.
Допускаемое осевое сжимающее усилие из условия прочности:
42* (1200 + 10 - 25) * (10 - 25) * 1865
Допускаемый изгибающий момент из условия прочности со стороны сжатия:
Допускаемое осевое сжимающее усилие из условия местной устойчивости:
= 310 * 10-6 * 195105 * 12002 (24) * (100*(10 - 25) 1200 )2.5
Допускаемый изгибающий момент из условия устойчивости в пределах упругости:
Допускаемый изгибающий момент:
9106 (1 + (159106 384106 )2)12
7106 Н м ≥ 1247106 Н м
Заключение: Условие прочности и устойчивости выполнено
Обечайка нагруженная поперечным усилием.
Допускаемое поперечное усилие из условия прочности:
25 * 3142 * 1200 * (10 - 25) * 1865
Расчётная длина для расчёта от действия давления:
Расчётная длина для расчёта от действия поперечной силы:
Допускаемое поперечное усилие из условия устойчивости:
4 * 195105 * (10 – 25)224 * (0.18 + 3.3*1200 * (10 - 25) 5.4103) 2
Допускаемое поперечное усилие:
106 (1 + (13106 623107 )2)12
Обечайка работающая под совместным действием нагрузок.
Обечайка работающая под совместным действием наружного давления осевого сжимающего усилия изгибающего момента и поперечного усилия.
Проверка условия устойчивости:
= 0 0 + 0 0 + 1247106 147107 + (6843105 13 106 )2
Заключение: Условие устойчивости выполнено.
Допускаемый изгибающий момент из условия прочности со стороны растяжения:
Обечайка работающая под совместным действием внутреннего давления осевого растягивающего усилия и изгибающего момента.
Проверка условия прочности:
= (3587+ 105* 3142 * 12002 4) 53106 +1247106 147107
Заключение: Условие прочности выполнено
Для расчёта обечайки от действия седловых опор:
=min1.0 9.45 * 3400 2173104*(3400 (100 * (20 -28)))12
Допускаемое наружное давление из условия устойчивости:
8 * 10-6 * 195105 * 1200 (24 * 1 * 5.4103 ) * (100*(10 - 25) 1200 )2.5
Допускаемое наружное давление из условия прочности:
* 1865 * (10 – 25) (1200 + 10 - 25)
17 (1 + (2317 0116)2)12
Допускаемое наружное давление: [p] = 0116 МПа
Обечайка нагруженная осевым сжимающим усилием.
Допускаемое осевое сжимающее усилие:
106 (1 + (53106 112106 )2)12
Допускаемый изгибающий момент из условия устойчивости:
Расчётная длина для расчёта cедловых опор:
4 * 195105 * (10 – 25)224 * (0.18 + 3.3*1200 * (10 - 25) (3103 )2)
2106 (1 + (132106 201106 )2)12
2 СОВРЕМЕННЫЕ МЕТОДЫ ИЗГОТОВЛЕНИЯ ОБЕЧАЕК.doc
При изготовлении сосудов приходится выполнять прямолинейные кольцевые и круговые стыковые швы. В зависимости от толщины стенок приемы выполнения каждого из них имеют свои особенности; разнообразна и применяемая оснастка [6].
Швы тонкостенных сосудов как правило выполняют в среде защитных газов. Сборку рекомендуется производить с помощью зажимных приспособлений — надежное прижатие свариваемых кромок к подкладке позволяет выполнять одностороннюю сварку в приспособлении без прихватки. При сборке и сварке прямолинейных швов между листами и продольных швов обечаек равномерное и плотное прижатие кромок к подкладке осуществляется зажимными приспособлениями клавишного типа. Усилие прижатия обычно составляет 300—700 Н на 1 см длины шва и создается гидравлическим или пневматическим устройством (рисунок 2.1). На верхнем основании жесткого каркаса закреплен ложемент 6 с подкладкой 5. Прижим свариваемых кромок осуществляют раздельно для каждого листа через набор клавиш 3 укрепленных на балках 1. Давление на клавиши передается пневмошлангами 2 и регулируется редуктором. Установка и прижатие листов производятся в такой последовательности: поворотом эксцентрикового валика 7 из подкладки выдвигаются фиксаторы 4 после чего до упора в них (справа по рисунку) заводится листовая заготовка и зажимается подачей воздуха в шланг. Затем фиксаторы убираются и до упора в кромку заготовки устанавливается другая заготовка и зажимается подачей воздуха в шланг 2.
Рисунок 2.1 – Приспособление для сборки и сварки прямолинейных стыков тонколистовых элементов
При сборке и сварке продольных стыков обечаек основание приспособления выполняют в виде консоли прижимные балки с клавишами закрепляют к ним одним концом жестко а другим концом — посредством откидных болтов.
Рисунок 2.2 – Характер деформаций обечайки от продольного шва
Продольные швы вызывают нарушение прямолинейности образующих тонкостенных обечаек и уменьшение кривизны в зоне шва в поперечном сечении (рисунок 2.2). Для исправления таких сварочных деформаций широко используют прокатку роликами. При выполнении кольцевых стыков тонкостенных сосудов из материалов мало чувствительных к концентрации напряжений используют остающиеся подкладные кольца которые облегчают центровку кромок и их одностороннюю сварку. Для ряда высокопрочных материалов такой прием оказывается неприемлемым. В этом случае кольцевые стыки собирают и сваривают на съемных подкладках разжимных колен. Однако надо учитывать что из-за подогрева кромок впереди сварочной дуги они расширяются и отходят от подкладного кольца в радиальном направлении что может приводить к смещению кромок или образованию домика. В тонкостенных сосудах работающих под давлением смещение кромок в стыковом шве — опасный концентратор и при изготовлении необходимо принимать меры по их предотвращению или устранению. Для прижатия кромок можно применять наружные стяжные ленты однако их приходится располагать на некотором расстоянии от оси стыка и перемещения предотвращаются лишь частично. Более эффективно оказывается прижатие кромок к подкладкам роликом перекатывающимся по поверхности стыка непосредственно перед сварочной дугой. Прижим не дает возможности кромкам оторваться от поверхности подкладного кольца в месте образования сварного соединения. Приспособление для прижатия кромок обечаек (рисунок 2.3) закреплено на консоли сварочной головки. Прижимные ролики опираются на обе свариваемые кромки выравнивая их и прижимая к подкладному кольцу с помощью пружины.
Для сварки стыка обечаек можно использовать также схему при которой стык выполняется изнутри обечайки. В этом случае зона кольцевого шва охватывается жестким бандажом вращающимся при сварке вместе с изделием а сварка первого прохода выполняется изнутри обечайки. Напряжения сжатия возникающие в зоне нагрева стремясь увеличить длину свободной кромки стыка прижимают ее к наружному кольцу бандажа.
Деформации от кольцевого шва для большинства материалов уменьшают диаметр обечайки. Такое сокращение зоны шва хорошо поддается исправлению прокаткой роликами. При сварке алюминиевых сплавов диаметр обечайки в зоне кольцевого шва выполненного на подкладном кольце может оказаться не только не меньше но даже больше первоначального размера. Рассмотренный выше прием прижатия кромок к подкладному кольцу роликом расположенным перед сварочной головкой (рисунок 2.3) позволяет практически полностью предотвратить такое увеличение диаметра при сварке стыков обечаек из алюминиевых сплавов.
– прижимные ролики; 2 – присадочная проволока
Рисунок 2.3 – Схема приспособления для прижатия кромок к подкладному кольцу перед сварочной головкой
Особое внимание приходится уделять конструктивному оформлению и технологии выполнения замыкающего кольцевого шва сосуда. При наличии лазовых отверстий или патрубков значительного размера внутрь сосуда можно ввести разборное разжимное кольцо. В этом случае одностороннюю сварку замыкающего шва выполняют на съемной подкладке по обычной технологии. Задача усложняется если размеры отверстий патрубков малы. Если остающееся подкладное кольцо является слишком резким концентратором и его использовать нельзя то приходится осуществлять одностороннюю сварку на весу.
Соединение элементов арматуры (фланцы штуцера) со стенкой сосуда обычно делают стыковым допуская соединение угловыми швами или рельефной сваркой только для материалов мало чувствительных к концентрации напряжений. Стыковые круговые швы выполняют односторонней сваркой на подкладке с канавкой. Вид сборочно-сварочной оснастки и конструктивное оформление стыка определяются необходимостью плотного прижатия кромок к подкладке предотвращения их перемещений в процессе сварки и устранения сварочных деформаций приводящих к местному искажению формы оболочки в зоне шва. В зависимости от формы поверхности стенки сосуда (сферической или цилиндрической) материала и толщины свариваемых элементов конструктивно-технологические решения могут быть различными. Так например при вварке фланца в сферический сосуд из алюминиевого сплава АМг6 целесообразно использовать соединение с буртиком показанное на рисунок 2.4. Технологический буртик предназначен для передачи усилия прижатия фланца на оболочку обеспечения их соосности и повышения жесткости кромки фланца. Наличие буртика позволяет упростить прижимное приспособление так как усилие прижатия прикладывается только к фланцу и предотвратить смещение кромок в процессе сварки а также уменьшить местные искажения формы оболочки возникающие в результате усадки кругового шва.
Рисунок 2.4 – Сборка фланца с оболочкой при наличии технологического буртика на фланце
При небольших размерах сосуда или того элемента в который вваривается деталь арматуры сварку кругового шва целесообразно осуществлять неподвижной сварочной головкой при вращении приспособления с закрепленным свариваемым стыком. При вварке арматуры в узел значительных размеров круговой шов более удобно выполнять сварочной головкой перемещающейся по поверхности элемента оболочки закрепленного неподвижно.
В крупносерийном производстве тонкостенных сосудов (тормозные резервуары пропановые баллоны) для выполнения сборочно-сварочных операций применяют специальные полуавтоматические установки. В них для сборки и сварки продольного стыка обечайки необходимо выполнять следующие операции: приемку обечайки ориентирование стыка прижатие его к подкладке симметрично относительно формующей проплав канавки выполнение шва освобождение обечайки от зажатия и ее сброс.
Наиболее сложной для автоматизации операцией является ориентирование. Если эту операцию выполняет рабочий то установка значительно упрощается и это является причиной отказа от применения полностью автоматизированных устройств.
а – схема установки; б – расположение обечайки на позиции сборки; в – расположение обечайки на позиции сварки
Рисунок 2.5 – Полуавтоматическая установка для сборки продольного стыка обечайки
На такой установке (рисунок 2.5) сборочную и сварочную операции можно выполнять на разных позициях связанных транспортирующим устройством например планшайбой 1 с шаговым поворотом на которой закреплены консольные балки 2 6 9 несущие сварочную подкладку. От обечаек расположенных на наклонном накопителе 5 отсекателем 7 отделяется одна и окатывается на приемное место 10 тележки 8. При движении этой тележки обечайка надвигается на консоль 6 планшайбы находящейся в положении приема опускается на нее а тележка отходит в исходное положение. Оператор ориентирует одну из кромок вдоль оси канавки 12 подкладки и фиксирует ее вакуумными присосками 13 вторую кромку устанавливают впритык к первой. Сборочная операция завершается установкой заходных планок (если это необходимо) и нажатием кнопки снимающей ограничение автоматического включения шагового поворота. Точная установка стыка под сварочную головку обеспечивается конусным фиксатором 4 который одновременно используется для поддержания конца консольной балки 2 при зажатии кромок обечайки клавишными прижимами 11 балки портала 3. Операция сварки в этом случае может осуществляться без участия оператора. По ее окончании клавишные прижимы и фиксатор отходят и поворот планшайбы 1 (рисунок 2.5а) переносит сваренную обечайку на позицию съема где она подхватывается приемным устройством тележки.
Сосуды со стенками средней толщины (до 40 мм) из низкоуглеродистых и низколегированных сталей изготовляют преимущественно с помощью автоматической сварки под флюсом. Сосуды работающие в агрессивных средах изготовляют из хромоникелевых и хромистых сталей цветных металлов и их сплавов автоматической сваркой под флюсом а также аргонодуговой сваркой. В целях экономии дорогостоящих и дефицитных материалов часто применяют двухслойные листы.
Цилиндрические сосуды обычно собирают из нескольких обечаек и двух полусферических или эллиптических днищ. Обечайки вальцуют из одиночного листа или из сварной карты при расположении швов вдоль образующей. Днища либо сваривают из отдельных штампованных лепестков либо штампуют целиком из листа или из сварной заготовки. Сборку и сварку цилиндрической части сосуда производят на роликовом стенде. Продольный стык обечайки собирают на прихватках с помощью простейших стяжных приспособлений. Сборка кольцевого стыка между обечайками является более трудоемкой операцией. Для ее механизации роликовый стенд можно оборудовать установленной на тележке 5 скобой 1 (рисунок 2.6). Тележка передвигается вдоль стенда по рельсовому пути 7. Настройка скобы в вертикальной плоскости осуществляется тягой 4. Последовательность операций при сборке в этом случае такова. На роликовый стенд 6 краном подают две обечайки. Скобу продвигают так чтобы опора 13 гидроцилиндра 10 оказалась в плоскости собираемого стыка и закрепляют на первой обечайке включением гидроцилиндра 11. После того как торцовый гидроцилиндр 2 придвигая вторую обечайку к первой установит требуемый зазор в стыке гидроцилиндром 10 выравнивают кромки и ставят прихватку. Поворот собираемых обечаек на некоторый угол для постановки других прихваток требует не только отвода прижимов гидроцилиндров 10 и 11 но и опор 12 и 13. Последнее осуществляется путем небольшого поворота скобы 1 вокруг оси 3 под действием штока поршня гидроцилиндра 10.
Рисунок 2.6 – Установка для механизированной сборки кольцевых стыков цилиндрических сосудов
Шток 9 при движении вниз встретив неподвижную регулируемую опору 8 поднимает цилиндр поворачивая скобу 1.
Сварка продольных и кольцевых швов сосудов со средней толщиной стенки выполняется как правило с двух сторон. Выполнение первого слоя на весу требует тщательной сборки и ограничения размера зазора по всей длине шва. Поэтому роликовые стенды обычно оборудуют флюсовыми подушками позволяющими производить сварку первого слоя шва без жесткого ограничения зазора в стыке. Флюсовая подушка для продельных швов представляет собой жесткий короб закрепленный на тележке. Пневмоцилиндры поднимают короб до упора в изделие. Плотное прижатие флюса к стыку создается подачей сжатого воздуха в шланг. Поджатие флюса при сварке кольцевых швов может осуществляться с помощью подушки ременного типа (рисунок 2.7). Движение ремня и подача флюса к месту горения дуги происходит вследствие сил трения. Другая конструкция флюсовой подушки для кольцевых швов представлена на рис. 2.8. При подаче воздуха в пневмоцилиндр 4 диск флюсовой подушки 2 поднимается до упора в изделие а сам цилиндр благодаря пружинной подвеске опускается и упирается траверсой 7 в рельсы фиксируя положение тележки 1. При вращении изделие увлекает за собой диск 2 с ложементом 5 и поворачивая его вокруг наклонной оси 3 прижимает резиновую камеру 6 с флюсом к стыку.
Рисунок 2.7 – Схема флюсоременной подушки для сварки кольцевых швов
Рисунок 2.8 – Флюсовая подушка с эластичным лотком для сварки кольцевых швов
Первый слой выполняют изнутри обечайки а второй сваривают снаружи по ранее уложенному первому с полным проплавлением всей толщины стенки. При толщине стенки сосуда более 25 мм автоматическая сварка под флюсом обычно выполняется в несколько слоев.
При серийном изготовлении сосудов днища часто выполняют штамповкой целиком причем листовая заготовка может быть сварной. В мелкосерийном и индивидуальном производстве днища обычно собирают и сваривают из отдельных штампованных элементов.
При изготовлении толстостенных сосудов (свыше 40 мм) широко используют электрошлаковую сварку обеспечивающую надежное проплавление всего сечения за один проход. Продольные швы толстостенных обечаек как правило выполняют электрошлаковой сваркой. В зависимости от размеров сосуда листовую заготовку гнут в нагретом состоянии вдоль длинной или вдоль короткой кромки листа. В первом случае обечайка получается длинной и меньше число кольцевых швов в сосуде. Однако для сосудов большого диаметра длина короткой кромки листа может оказаться недостаточной тогда обечайку составляют из двух корыт с двумя продольными швами. Во втором случае обечайка получается более короткой но с одним продольным швом. Второй прием представляется менее целесообразным так как кольцевые швы более трудоемки по сравнению с продольными. Обечайку с одним продольным швом можно получить вальцовкой.после обрезки нагревают до 1000—1050°С и вальцуют до замыкания стыка оставляя недовальцованными плоские участки шириной 100—150 мм (рисунок 2.9). После остывания обечайки стык закрепляют приваркой скоб 1 и тепловой резкой вырезают зазор 2 под электрошлаковую сварку.
Рисунок 2.9 – Свальцованная обечайка с одним продольным стыком
Методом вальцовки трудно получить обечайки длиной более 3500 мм и толщиной стенок более 100 мм. Гибка на мощном прессе таких ограничений не имеет особенно если обечайка образуется из двух корыт. Сборку обечайки под электрошлаковую сварку в этом случае (рисунок 2.10) выполняют с помощью скоб постоянства зазора в стыке достигают постановкой прокладок удаляемых перед сваркой. После приварки выходных планок и кармана для наведения шлаковой ванны собранную под сварку обечайку устанавливают вертикально. Если обечайка имеет два продольныхшва их целесообразно выполнять одновременно двумя сварочными аппаратами.
При сварке гнутых под прессом корыт обечайка получается достаточно правильной цилиндрической формы и последующая калибровка необязательна. Напротив обечайки получаемые вальцовкой требуют как правило правки. Калибровку производят при температуре 1000— 1050°С и при охлаждении обечайки на воздухе она одновременно проходит процесс нормализации.
Рисунок 2.10 – Сборка обечайки с двумя продольными стыками
Кольцевые швы выполняют многослойными сваркой под флюсом или электрошлаковой сваркой в один проход. Полное проплавление при многослойной сварке обеспечивают укладкой в разделку нескольких подварочных слоев 1 с внешней стороны (рисунок 2.11) зачисткой корня шва с помощью пневматического зубила или резака и наложением внутреннего подварочного шва 2. После этого производят многослойное заполнение внешней разделки 3.
Рисунок 2.11 – Форма разделки кольцевого стыка под многослойную сварку
Сборка кольцевого шва под электрошлаковую сварку должна быть достаточно точной так как местная депланация криволинейных кромок свыше 3 мм может привести к нарушению уплотнения и вытеканию шлаковой ванны. Поэтому перед сборкой обычно внешнюю и внутреннюю поверхности каждой из обечаек протачивают на ширину 70—100 мм от торца (рисунок 2.12). Так же осуществляют подготовку стыка обечайки с днищем. Собирают стык с помощью планок которые устанавливают «на ребро» поперек кольцевого шва и приваривают к поверхности обечаек. Если в качестве внутреннего формирующего устройства используют медные охлаждаемые подкладки изогнутые по радиусу свариваемого изделия то внутри обечайки дополнительно устанавливают скобы временного крепления. Подкладки 1 (рисунок 2.13) заводят в отверстия скоб 2 и закрепляют клиньями 3 или винтовыми прижимами.
Рисунок 2.12 – Обработка торцов обечайки
Рисунок 2.13 – Кольцевой стык собранный под электрошлаковую сварку
Рисунок 2.14 – Схема электрошлаковой сварки кольцевых швов
Электрошлаковую сварку кольцевого шва начинают на вспомогательной пластинке вваренной в зазоре стыка (рисунок 2.14а).
После заварки примерно половины окружности стыка (рисунок 2.14б) сварщик резаком удаляет из зазора начало шва до полного устранения непровара и придает торцу шва наклонный срез облегчающий выполнение замыкания шва (замка) (рисунок 2.14б). Усадочную раковину либо выводят в специальный прилив в наружном ползуне или в медный кокиль либо выплавляют и заваривают вручную.
Перспективной является однопроходная сварка толстостенных сосудов электронным лучом в вакууме. Экспериментально показано что при использовании сварки горизонтальным лучом можно выполнить продольные и кольцевые швы металла толщиной 250 мм и более при скорости сварки 25—5 мч. Однако для производственного применения этого перспективного метода еще требуется отработка ряда технологических вопросов а также создание вакуумных камер больших размеров.
По завершении сварки корпуса сосуда вырезку отверстий для вварных штуцеров производят или механическим путем или тепловой резкой. Особенно большой объем таких работ выполняется при изготовлении барабанов котлов и коллекторов. Чтобы сократить подгоночные работы на монтаже при сборке коллекторов и барабанов с блоками экранных труб к точности установки штуцеров предъявляют жесткие требования. Приварку большого числа штуцеров необходимо автоматизировать. Применяемые для этой цели специализированные автоматы и полуавтоматы обычно центрируются по верхней части ввариваемого штуцера.
Варианты конструктивного оформления соединений штуцеров с оболочками большой толщины разнообразны. Наиболее целесообразны те которые позволяют получить надежное проплавление всей стенки штуцера исключая возможность образования и роста трещины от непровара. Для этой цели можно использовать формующую подкладку удаляемую после сварки (рисунок 2.15). Другой вариант соединения показан на рисунке 2.16. В оболочке 2 в центре установки трубчатого переходника сверлят центровочное отверстие d в которое вставляют заготовку 1 переходника с разделкой кромок под сварку. После сварки просверливают отверстия диаметром D (рисунок 2.16а).Окончательно соединение имеет вид показанный на рисунок 2.16б. В нем присутствует концентрация напряжений вследствие резких изменений сечения на внешней поверхности трубы и оболочки но качество поверхности металла во внутренней полости хорошее.
Рисунок 2.15 – Конструкция штуцерного соединения: а – до сварки; б – после сварки
Рисунок 2.16 – Соединение штуцера с оболочкой с последующим удалением корня шва высверловкой
6,7 БЕЗОПАСНОСТЬ И ЭКОЛОГИЧНОСТЬ ПРОЕКТА.doc
1 Общие вопросы безопасности при выполнении сварочных работ
Инструкция по охране труда является нормативным документом устанавливающим требования безопасности при выполнении рабочими и служащими (далее по тексту — работающими) работ в произволе помещениях на территории предприятия на строительных площадках и в иных местах местах где работающие выполняют порученную им работу или служебные обязанности.
Требования инструкцийявляютсяобязательными для работающих. Невыполнение этих требований должно рассматриваться как нарушение производственной дисциплины.
Постоянный контроль за выполнением инструкций работающими возлагается на администрацию — руководителей предприятия учреждения организации (далее предприятия) и его структурных подразделений (служб) руководителей цехов (участков) мастеров на службу охраны труда (отдел бюро инженера) а также на бригадиров и профсоюзный комитет предприятия.
Целью при проектировании и эксплуатации предприятий со сварочным производством является необходимость принять меры по профилактике производственного травматизма и профессиональных заболеваний в первую очередь по уничтожению вредных и опасных производственных факторов а если ликвидация опасных и вредных факторов затруднена технически или экономически по их нейтрализации и защите от них [14].
Задача которая ставится перед нами в данной работе это нейтрализация или снижение влияния вредных веществ на организм сварщика за счет организации приточно-вытяжной вентиляции рабочего места а так же обеспечение электробезопасности.
Опасными и вредными производственными факторами для сварки являются [14]:
-движущиеся машины и механизмы передвигающиеся изделия заготовки и материалы;
-повышенная запыленность и загазованность воздуха рабочей зоны;
-повышенная температура воздуха рабочей зоны;
-Повышенный уровень электромагнитных излучений;
-повышенное значение напряжения в электрической цепи замыкание которой может произойти через тело человека;
-повышенная яркость света;
-недостаточная освещенность рабочей зоны;
-повышенный уровень ионизирующих излучений в рабочей зоне;
-пожаро-взрывоопасность;
-недостаточная освещенность рабочего места;
-химические факторы (сварочные аэрозоли);
-психофизиологические факторы;
-нервнопсихические перегрузки.
Непосредственно на исследуемом рабочем месте сварщика при сварке корпуса сепаратора идентифицированы следующие вредные и опасные факторы:
-повышенный уровень электромагнитных излучений;
-пожаро-взрывоопасность в сварочном производстве.
2 Вентиляция рабочих мест
Для снижения концентрации вредных веществ на рабочих местах до предельно допустимой концентрации необходимо прежде всего применять местные отсосы при ручной сварке штучными электродами с покрытием полуавтоматической и автоматической сварке в защитных газах плавящимся электродом порошковой проволокой и под флюсом контактной точечной шовной и рельефной сварке гальванопокрытых и цветных металлов контактной стыковой сварке оплавлениемпри ручной и машинной термической резке металла.
Расход воздуха удаляемого отсосами определяют по формуле [14]:
где F0 - площадь всасывающего отверстия отсоса м2;
v0 - скорость воздуха в этом отверстии мс.
Площадь отсоса Fo и его форму выбирают в зависимости от вида сварки или резки используемого оборудования и т. д. Скорость v находят исходя из условий обеспечения заданной скорости воздуха vx в зоне сварки или резки на расстоянии х (м) от центра всасывающего отверстия.
При ручной сварке v в углекислом газе - не более 05мс; в инертньгх газах - не более 03 мс; при газовой и плазменной резке титановых сплавов и низколегированных сталей - соответственно не менее 1 мс и 14 мс; при плазменной резке алюминиево-магниевых сплавав и высоколегированных сталей - не менее 18 мс при плазменном напылении - не менее 13 мс при заточке торированых вольфрамовых электродов - не менее 13 мс.
Для точечного стока за который приближенно можно принять всасывающее отверстие малого диаметра по сравнению с расстоянием до него:
для сферического стока
для полусферического стока
Для отсосов простейшей формы скорость v определяют следующим образом:
для круглых квадратных отверстий без экрана
где d - диаметр круглого отверстия или гидравлический диаметр квадратного отверстия м.
Для прямоугольного отверстия щелевидной формы шириной 1:
Формулы (6.4) и (6.5) можно применять при х > 05d а (6.6) – при более близком расположении отсосов к зоне сварки а также при использовании отсосов сложной формы для определения скорости пользоваться графиками рис. 6.1. На этом рисунке приведены спектры относительных скоростей всасывания (%). В этих случаях
Для щелевых и круглых отверстий расположенных вблизи ограничивающих поверхностей полученное по формуле (6.6) значение v нужно разделить на коэффициент (рисунок 6.1e):
а) для круглого отверстия без экрана; б) для кольцевого отверстия шириной b0=(005-01)d0 при расположении экрана на расстоянии hd0=05 10; в) для прямоугольного щелевидного отверстия с соотношением сторон 1:10; г) то же но лежащего на плоскости; д) для наклонной панели (сплошные линии - панель без козырька пунктирные - с козырьком); е) - зависимость от хh (1 - щелевое отверстие; 2 - круглое отверстие)
Рисунок 6.1 – Спектры относительных скоростей всасывания V
Ручная сварка покрытыми электродами. На стационарных сварочных постах используют вытяжные устройства в виде боковых панелей обеспечивающих отклонение факела вредных выделений от лица сварщика.
Для ручной и полуавтоматической сварки мелких изделий применяют сварочные столы со встроенными отсосами выпускаемые в двух вариантах: со встроенным вентиляционным агрегатом (рисунок 6.2) и для присоединения к цеховой системе местной вытяжной вентиляции. Столы ССН-1 и ССН-3 оборудованы радиальными вентиляторами ЦЧ-70 № 21 2 (L=1500 м3ч) и присоединяются к воздуховодам для выброса загрязненного воздуха в атмосферу за пределы помещения а стол ССН-2 подсоединяется к цеховой системе вентиляции. В столах новой конструкции С100.20 и С 100.21 С100.40 и С100.41 размеры рабочих решеток составляют соответственно 800х800 мм и 1250x800 мм а встроенный вентилятор Ц14-46 № 2 обеспечивает удаление воздуха с расходом 2000 и 2700 мЗч.
Рисунок 6.2 – Сварочный неповоротный стол
Наиболее распространенными конструкциями вытяжных панелей является наклонная панель равномерного всасывания А.С.Чёрнобережского (рисунок 6.3 а) и панель конструкции ГПИ «Сантехпроект» (рисунок 6.3 б). Скорость воздуха в живом сечении (25% от плошади панели) решетки всасывающего отверстия панели А.С. Чернобережского принимается равной 3-4 мс а иногда (для высокоопасных веществ) до 6-8 мс. Расход воздуха может быть определен по удельному расходу воздуха равному 3300 мЗч на 1 м2 площади панели При сварке изделий до 2-3 м длиной используют подъемно-поворотные воздухоприемники типа ЛИОТ-1 (рисунок 6.3 в) и ЛИОТ-2 (рисунок 6.3 г). Расход удаляемого воздуха равен соответственно 4000 и 2000 м3ч.
a) панель А. С. Чернобережского; б) панель ГПИ «Сантехпроект»; в) двусторонний поворотный воздухоприемник ЛИОТ-1; г) поворотно-подъемный воздухоприемник ЛИОТ-2: 1-свариваемое изделие; 2-воздухоприемная панель; 3-воздуховод; 4-поворотный кронштейн.
Рисунок 6.3 – Вытяжные панели
При сварке крупногабаритных изделий отсосы для манипуляторов и позиционеров могут быть выполнены в виде подвижного воздухоприемника укрепленного на шарнирно соединенных воздуховодах.
Автоматическая и полуавтоматическая сварка. Обычно отсосы ветра в сварочные горелки. При сварке под флюсом шланговым полуавтомат ПШ 5-у отсос щелевидной формы крепится к сварочной головке и перемещается сварщиком. В зависимости от силы сварочного тока расход составляет 70-140 мЗч. Для сварочных тракторов типа АДС-100-2 применяют щелевой (рисунок 6.4а) или воронкообразный воздухоприемник (рисунок 6.4б) всасывающее отверстие которого нужно располагать на высоте 40-50 мм над поверхностью флюса. Расход воздуха удаляемого щелевым воздухоприемником (м3ч):
где I – сила сварочного тока А.
Для воронкообразного воздухоприемника количество воздуха нужно увеличить на 10%.
– кольцо; 2 – хомутик; 3 – планка; 4 – конфузор; 5 – патрубок; 6 – щель равномерного всасывания; 7 – воздухоприемник.
Рисунок 6.4 – Щелевой (а) и воронкообразный (б) воздухоприемник
При сварке в защитных газах недопустимо нарушать газовую защиту сварочных швов что может произойти при близком расположении всасывающего патрубка (воздухоприемника) от среза сопла подающего защитный газ. Схемы воздухоприемников к горелкам при полуавтоматической сварке в СО2 даны на рисунке 6.5. В выполненном по схеме рисунок 6.5а отсосе ЦНИИТС (рисунок 6.5а) расход воздуха 60 мЗч. Патрубок отсоса в держателе должен быть несколько удален от сварочной головки с тем чтобы не было перетекания защитного газа в отсос.
а) кольцевой симметричный; б) кольцевой асимметричный; в) конический дырчатый; г) конусно-щелевой (НИИСТ Киев)
Рисунок 6.5 – Схемы воздухоприемников к горелкам для полуавтоматической сварки в С02
Особенностью отсосов выполненных по схеме рисунка 6.5б является удаление основного количества загрязненного воздуха над сварочной дугой (рисунки 6.5бв). В отсосах изготовленных по схеме рисунка 6.6в воздух удаляется через перфорированный насадок (рисунок 6.5г) с расходом который может быть определен в зависимости от силы сварочного тока.
Побудителями движения в рассмотренных отсосах чаще всего являются водокольцевые вакуум-насосы типа ВВН. При разрежении 25 кПа производительность ВВН-12 равна 500 мЗч ВВН-25 – 1100 м3ч ВВН-50 – 2200 м3ч.
– воздухоприеммик; 2 – патрубок; 3 – сопло; 4 – трубка; 5 – патрубок для подвода защитного газа; 6 – мундштук
Рисунок 6.7 – Местные отсосы для сварочных полуавтоматов
3 Обеспечение электробезопасности
Все электрооборудование сварочных и сборочно-сварочных цехов и участков должно соответствовать «Правилам устройства электроустановок ПУЭ-76». Общие требования его эксплуатации – «Правилам технической эксплуатации электроустановок потребителей и правилам техники безопасности при эксплуатации электроустановок потребителей». Кроме того необходимо выполнять указания по эксплуатации и безопасному обслуживанию электросварочных установок имеющиеся в инструкциях заводов-изготовителей.
Присоединение и отсоединение от сети электросварочных установок а также наблюдение за их исправным состоянием в процессе эксплуатации производятся электротехническим персоналом данного предприятия. К проведению электросварочных работ допускаются электросварщики с квалификационной группой по технике безопасности не ниже второй.
Неправильная эксплуатация электрического оборудования создает опасность поражения электрическим током. Основными причинами поражения электрическим током являются: воздействие электрического тока проходящего в сварочной цепи касание открытых токоведущих частей и проводов (случайное не вызванное производственной необходимостью или из-за ошибочной подачи напряжения во время ремонтов и осмотров) касание токоведущих частей через предметы с низким сопротивлением и прикосновение к металлическим частям оборудования случайно оказавшимися под напряжением и др.
Электрический ток проходя через организм вызывает ожоги отдельных участков тела нагрев кровеносных сосудов нервов и других тканей что приводит к раздражению живых тканей организма. Это сопровождается непроизвольными судорожными сокращениями мышц. В результате могут возникнуть различные нарушения в организме в том числе нарушение и даже полное прекращение деятельности органов дыхания и кровообращения.
Корпус электросварочной установки заземляется.
Защитным заземлением называется преднамеренное электрическое соединение с землей или ее эквивалентом металлических нетоковедущи частей.
Условие применения защитного заземления:
Рисунок 6.8 – Схеманапряжение сети переменного тока 380 В независимо возможного поражения от категории помещения.
В таблице 6.1 приведены максимально допустимые значения сопротивления заземления [15].
Таблица 6.1 – Максимально допустимые значения сопротивления заземления.
Дополнительное сопротивление заземления Ом
Рабочее заземление нейтрали
Защитное заземление при больших токах короткого замыкания на массу (>500А)
Повторное заземление N провода
Защитное заземление применяют в сетях напряжением до 1000 В с изолированной нейтралью и в сетях напряжением свыше 19000 В как с изолированной так и с заземленной нейтралью.
С помощью защитного заземления уменьшается напряжение на корпусе относительно земли до безопасного значения следовательно уменьшается сила тока протекающего через тело человека. Напряжение приложенное к телу человека в случае прикосновения к оборудованию можно снизить уменьшая сопротивление заземляющего устройства. Согласно ПУЭ сопротивление заземления в электроустановках до 1000 В не должно превышать 4 Ом.
В случае использования установки для сварки рабочий ток 170 А номинальное рабочее напряжение 30В первичная мощность 21 кВА.
В случае выносного заземления ток через человека определяется по следующей формуле [15]:
Получаем при Iз=170А rз=82 Oм а =1 Rch =1000 Ом ток через человека Ih = 05 мА – ниже порога пропускания.
Сварочные установки защищают предохранителями или автоматами со стороны питающей сети.
Проведём расчёт заземления.
Сначала согласно ПУЭ выбирается допустимое сопротивление заземляющего устройства Rзд = 4 Ом.
После этого определяется расчётное удельное сопротивление (ρ):
где ρr - удельное сопротивление грунта Ом·м;
- климатический коэффициент в зависимости от вида грунта и степени влажности. В учебных расчётах можно применять = 1.
Удельное сопротивление грунта ρr составляет: для глины - 60 Ом·м; для
супеска - 500 Ом·м; для гравия и щебня - 2000 Ом·м; для сухого песка – 2500 Ом·м; для каменистой почвы - 4000 Ом·м.
В данном расчёте будем принимать для сухого песка ρr = 500 Ом·м.
ρ = 500 · 1 = 500 Ом·м.
Следующий этап расчёта определение сопротивления заземлителей (Ом).
При использовании искусственных заземлителей вначале выбирают материал тип и размеры заземлителей. Чаще всего применяют угловые и трубчатые металлические электроды размещаемые в земле вертикально и соединяемые горизонтальной металлической полосой.
а) трубчатый стержневой; б) уголковый
Рисунок 6.9 – Схематическое изображение заземлителей
При использовании в качестве искусственного заземлителя вертикально расположенного уголка с размерами представленными на рисунке 6.9б Rиз составит:
(при условии что t0 ≥ d).
При использовании горизонтально расположенной полосы длиной 1 со стороной сечения b заглублённой оси относительно поверхности земли t величине:
Общее сопротивление вертикальных электродов:
где в – коэффициент использования вертикальных заземлителей.
Если вертикальные электроды (заземлители) расположены в ряд то величина в при n=4 составляет 073.
С учётом коэффициента использования соединительной полосы заземляющего устройства n расчётное значение сопротивления искусственного заземлителя должно быть:
Результирующее сопротивление заземляющего устройства при использовании естественных и искусственных заземлителей должно соответствовать требованиям:
Данные расчетов по вентиляции и электробезопасности были сопоставлены с предельно допустимыми значениями. Общие рекомендации по безопасности были сопоставлены с мероприятиями предпринятыми в проекте. В результате можно считать что предпринятые мероприятия в достаточной степени обеспечивают безопасность рабочего персонала.
Экологичность проекта
Машиностроительные предприятия изготавливающие такие изделия как нефтегазовые сепараторы оказывают негативное воздействие на окружающую среду. Машиностроительное производство включает в себя заготовительные и кузнечнопрессовые цеха цеха термической и механической обработки металлов цеха покрытий и литейные цехи сварочные цеха.
1 Загрязнение атмосферы
Основной физической характеристикой примесей атмосферы является концентрация – масса (мг) вещества в единице объёма (м3) воздуха при нормальных условиях. Концентрация примесей определяет физическое химическое и другие виды взаимодействия веществ на человека и окружающую среду и служит основным параметром при нормировании содержания примесей в атмосфере.
ПДК – это максимальная концентрация примеси в атмосфере отнесённая к определённому времени осреднения которая при периодическом воздействии или на протяжении всей жизни человека не оказывает ни на него ни на окружающую среду в целом вредного воздействия. В таблице 7.1 приведены ПДК некоторых наиболее характерных веществ загрязняющих атмосферный воздух.
Таблица 7.1 – ПДК веществ загрязняющих атмосферный воздух в процессе сварки
Предельно допустимые концентрации (мгм3)
Максимальная разовая
На участках сварки и резки металла состав и масса выделяющихся вредных веществ зависит от вида и режимов технологического процесса свойств применяемых сварочных и свариваемых материалов. Наибольшие выделения вредных веществ характерны для процесса ручной сварки покрытыми электродами. При расходе 1кг электродов в процессе ручной дуговой сварки стали образуется до 40 г пыли 2 г фтористого водорода 15 г оксидов углерода и азота.
К мероприятиям по защите атмосферы относится ограничение количества загрязняющих окружающую среду выбросов путем улавливания пылегазовыделений выбрасываемых в атмосферу с помощью местных отсосов.
2 Загрязнение гидросферы
На территории промышленных предприятий образуются сточные воды трех видов: бытовые поверхностные и производственные. При выборе способов и технологического оборудования для очистки сточных вод от примесей необходимо учитывать что заданные эффективность и надёжность работы любого очистного устройства обеспечивается в определённом диапазоне значений концентрации примесей и расходов сточной воды. Большинство цехов машиностроительных предприятий характеризуется постоянством расхода и состава сточных вод однако в некоторых технологических процессах имеют место кратковременные изменения что может существенно уменьшить эффективность работы очистных устройств или вывести их из строя.
В термическом цехе частицы пыли окалины и масла являются основными примесями сточных вод используемых для охлаждения технологического оборудования поковок гидросбива металлической окалины и обработки помещения.
В механическом цехе для приготовления смазочно-охлаждающих жидкостей промывки окрашиваемых изделий используется вода. Основными примесями сточных вод является пыль металлические и абразивные частицы сода масла растворители мыло краски.
Очистка сточных вод от твёрдых частиц в зависимости от их свойств концентрации и фракционного состава на машиностроительных предприятиях осуществляется методами процеживания отстаивания отделения твёрдых частиц в поле действия центробежных сил и фильтрования.
Процеживание – первичная стадия очистки сточных вод – предназначено для выделения из сточных вод крупных нерастворимых частиц размером до 25мм а также более мелких волокнистых загрязнений которые в процессе дальнейшей обработки стоков препятствуют нормальной работе очистного оборудования. Процеживание осуществляется пропусканием воды через решётки и волокноуловители.
Отстаивание основано на особенностях процесса осаждения твёрдых частиц в жидкости. При этом может иметь место свободное осаждение неслипающихся частиц сохранивших свои формы и размеры и осаждение частиц склонных к коагулированию и изменяющих при этом свою форму и размеры. Закономерности свободного осаждения частиц практически сохраняются при объёмной концентрации осаждающихся частиц до 1% что соответствует их массовой концентрации не более 26 кгм3.
Отделение твёрдых примесей в поле действия центробежных сил осуществляется в открытых или напорных гидроциклонах и центрифугах.
Фильтрование сточных вод предназначено для очистки от тонкодисперсных твёрдых примесей с небольшой концентрацией. Процесс фильтрования применяется также после физико-химических и биологических методов очистки так как некоторые из этих методов сопровождаются выделением в очищаемую жидкость механических загрязнений.
Твердые отходы машиностроительного производства содержат амортизационный лом (модернизация оборудования оснастки инструмента) стружки и опилки металлов древесины пластмасс и т. п. шлаки золу шламы осадки и пыль (отходы систем очистки воздуха и РД). Количество амортизационного лома зависит от намеченного списания в лом изношенного оборудования и имущества а также от замены отдельных деталей в планово-предупредительном ремонте. На машиностроительном предприятии 55% амортизационного лома образуется от замены технологической оснастки и инструмента. Безвозвратные потери металла вследствие истирания и коррозии составляют 25% от общего количества амортизационного лома. В основном машиностроительные предприятия образуют отходы от производства проката (обрезки обдирочная стружка опилки окалины и т. п.) производства литья (высечки обрезки стружки и др.). В небольших количествах промышленные отходы могут содержать ртуть.
К мероприятиям по защите почвенного покрова относится вывоз отходов с территории предприятия в специальные цеха по утилизации и переработке промышленных отходов. Наибольшее распространение получили складирование на полигоне сжигание переплавка биотермическое компостирование.
содержание.doc
1Описание и назначение сепараторов нефтегазовых типа НГС7
2Конструкция и технические характеристики НГС-II-10-1200-1-И 8
Современные методы изготовления обечаек 12
Технологическая часть 27
1Обоснование выбора материала обечайки и его характеристика 27
2Оценка свариваемости материала и анализ способов получения неразъемных соединений33
3Выбор способа сварки и его обоснование 36
4Расчет режимов сварки 39
4.1 Ручная дуговая сварка39
4.2 Полуавтоматическая сварка в углекислом газе проволокой сплошного сечения46
4.3 Автоматическая сварка под флюсом проволокой сплошного сечения48
5Совершенствование технологии сварки 52
Механическая часть 59
1Расчеты на прочность сварных швов 59
2Расчет обечайки сепаратора на прочность и устойчивость60
Экономическая часть68
1Расчет затрат на эксплуатацию машин и оборудования68
2Калькуляция стоимости из расчета на одну тонну массы металлоконструкций 72
2.1 Калькуляция изготовления обечайки днищ и опор сепаратора72
2.2 Калькуляция изготовления площадок и лестниц для обслуживания оборудования77
2.3 Калькуляция изготовления люк-лазов патрубков и молниеприемников82
2.4 Калькуляция изготовления внутренних устройств87
3Расчет показателей экономической эффективности92
Безопасность проекта95
1Общие вопросы безопасности при выполнении сварочных работ95
2Вентиляция рабочих мест97
3Обеспечение электробезопасности104
Экологичность проекта105
1Загрязнение атмосферы105
2Загрязнение гидросферы107
3Загрязнение почвы113
СПИСОК ИСПОЛЬЗОВАННЫХ ИСТОЧНИКОВ115
ЗАКЛЮЧЕНИЕ.doc
Для подбора оптимальной технологии были проработаны вопросы выбора и обоснования основного материала оценки свариваемости стали произведены расчеты режимов сварки с выбором наиболее оптимального способа. В результате расчетов была выбрана автоматическая сварка под слоем флюса которая обеспечивает большую производительность в сравнении с базовым проектом.
Был предложен способ совершенствования технологии сварки под слоем флюса который решает задачу повышения прочности сварных обечаек за счет повышения прочности сварных швов. В качестве подтверждения были представлены расчеты на прочность сварных швов и расчеты обечайки на прочность и устойчивость.
Также в данном проекте представлено обоснование экономической эффективности применяемой технологии.
В разделах безопасность и экологичность был рассмотрен цикл мероприятий по обеспечению вентиляции и электробезопасности труда которые позволяют предупредить производственный травматизм и уменьшить риск возникновения профессиональных заболеваний что способствует повышению защищенности работников а также мероприятия по защите окружающей среды.
3 ТЕХНОЛОГИЧЕСКАЯ ЧАСТЬ.doc
1 Обоснование выбора материала обечайки и его характеристика
Обечайка работает в условиях умеренно холодного климата при температуре окружающей среды до минус 40 градусов. Рабочей средой являются слабокоррозионные среды (нефть газ пластовая вода сероводород отсутствует).
Исходя из назначения и условий эксплуатации оборудования к материалу корпуса сепаратора нефтегазового предъявляется ряд эксплуатационных и технологических требований.
К эксплуатационным требованиям относится прежде всего хладостойкость и коррозионная стойкость в области рабочих температур стойкость к воздействию абразивного поверхностного трения.
К технологическим требованиям относятся требования предъявляемые к технологии изготовления изделия и технологии получения неразъемных соединений. Главное технологическое требование – хорошая свариваемость материала из которого изготавливается обечайка.
Выбор материала основывается на трёх требованиях [8]:
Соответствие материала условиям эксплуатации изделия;
Свариваемость материала;
Стоимость и дефицитность материала.
С учётом условий эксплуатации наиболее рациональной группой материалов для изготовлений изделия являются низколегированные стали.
По принятой квалификации низколегированной называется сталь легированная одним или несколькими элементами если содержание каждой из них не превышает 2% а суммарное содержание легирующих не превышает 5%. Низколегированные стали применяемые для изготовления сварных конструкций делятся на три основные группы: низколегированные низкоуглеродистые конструкционные стали низколегированные теплоустойчивые стали и низколегированные среднеуглеродистые стали.
Низколегированныенизкоуглеродистые конструкционные стали предназначенные для сварных конструкций поставляют в основном в горячекатаном или нормализованном состоянии. Ряд сталей применяют в термоулучшенном состоянии (после закалки и отпуска) что дает возможность повысить их прочность и стойкость против хрупкого разрушения. Содержание углерода в низколегированных углеродистых конструкционных сталях не превышает 023%. Стали этого типа легируют рядом элементов например марганцем хромом кремнием ванадием и другими что приводит к некоторому повышению их прочности. Поэтому их часто называют низколегированными сталями повышенной прочности.
В зависимости от легирования стали рассматриваемого типа подразделяют намарганцовистые кремнемарганцовистые хромокремнемарганцовистые и другие. Расширяется применение стали повышенной прочности на основе нитридного упрочнения например с ванадием и азотом (стали 15Г2АФ 18Г2АФ) а также стали дополнительно легированные небольшим количеством (002-004%) ниобия (сталь 10Г2Б).
Перспективно применение для сварных полуспокойных сталей с нитридным упрочнением типа 18Г2АФпс.
Низколегированные конструкционные стали повышенной прочности должны обладать высокой устойчивостью против перехода в хрупкое состояние и быть недорогими и экономичными в производстве. Состав стали должен предопределять возможность ее сварки без усложнения технологий и обеспечивать высокую стойкость против образования трещин в металле шва.
Использование дефицитных и дорогих легирующих элементов например никеля и молибдена ограничивается требованием низкой стоимости и экономичности производства. Поэтому в применяемых низколегированных сталях (сталях 15ХСННД и 10ХСНД) содержание никеля невелико.
Необходимость обеспечения высокой стойкости против перехода в хрупкое состояние и хорошей свариваемости ограничивает применение легирующих элементов которые способствуя повышению прочности стали в то же время снижают ее стойкость против перехода в хрупкое состояние и образования кристаллизационных трещин (например углерода и кремния).
Для изготовления обечайки целесообразней применить сталь 09Г2С которая не представляет особых технологических трудностей при сварке.
Сталь конструкционная низколегированная для сварного изделия «обечайка» обладает свариваемостью без ограничений дуговой сваркой автоматической сваркой под флюсом и в среде углекислого газа.
Химический состав стали должен соответствовать ГОСТ 19281-89.
Таблица 3.1 – Химический состав
Таблица 3.2 – Механические свойства
Термообработка состояние поставки
Сортовой и фасонный прокат
Листы и полосы (образцы поперечные)
Листы и полосы (образцы поперечные)
Листы после закалки отпуска (образцы поперечные)
Листы после закалки отпуска (образцы поперечные)
Листы горячекатаные
Таблица 3.3 – Механические свойства при повышенных температурах
Нормализация 930 – 950 °C
Таблица 3.4 – Механические свойства в зависимости от температуры отпуска
Листы толщиной 34 мм в состоянии поставки НВ 112-127 (образцы поперечные)
Таблица 3.5 – Технологические свойства
Начала 1250 конца 850.
Сваривается без ограничений. Способы сварки: РДС АДС под флюсом и газовой защитой ЭШС.
Обрабатываемость резанием
В нормализованном отпущенном состоянии при sB = 520 МПа Ku тв.спл. = 16 Ku б.ст. = 10.
Склонность к отпускной способности
Флокеночувствительность
Таблица 3.6 – Температура критических точек
Таблица 3.7 – Ударная вязкость
Ударная вязкость KCU Джсм2
Состояние поставки термообработка
ГОСТ 19281-73. Сортовой и фасонный прокат сечением 5-10 мм
ГОСТ 19281-73. Сортовой и фасонный прокат сечением 10-20 мм
ГОСТ 19281-73. Сортовой и фасонный прокат сечением 20-100 мм
ГОСТ 19282-73. Листы и полосы сечением 5-10 мм
ГОСТ 19282-73. Листы и полосы сечением 10-160 мм
ГОСТ 19282-73. Листы после закалки отпуска (Образцы поперечные) сечением 10-60 мм
Таблица 3.8 – Предел выносливости
Таблица 3.9 – Предел текучести
Температура испытания °C s02
Таблица 3.10 – Физические свойства
Температура испытания °С
Коэффициент линейного расширения (a 10-6 1°С)
2 Оценка свариваемости материала и анализ способов получения неразъёмных соединений
Свариваемость – это способность материалов и сплавов образовывать соединения с помощью сварки без трещин пор и других дефектов [4].
Под свариваемостью в основном понимают склонность сварного соединения к образованию трещин закалочных структур и других структурных изменений в ЗТВ. Свариваемые металлы должны иметь близкие физические механические термические химические свойства близость коэффициентов термического линейного расширения металлов в стыке. Критерием хорошей свариваемости является способность сохранения специальных физических механических свойств равнопрочности жаропрочности коррозионнойстойкости антифрикционности прочности вязкости и т.д. Для образования качественного сварного соединения важно предупредить возникновение в сварном токе различных дефектов: пор непроваров трещин. А это в свою очередь зависит от степени легирования металла содержания примесей наибольшее влияние на свариваемость оказывает углерод.
Свариваемость различных металлов и сплавов неодинакова.
Углерод увеличивает твердость и уменьшает пластичность приводит к закаливаемости ЗТВ и к появлению трещин вызывает большое количество газовых пор в процессе окисления при сварке так как не превышает предела 0.25%
Кремний - до 1% вводится как раскислитель и не влияет на свариваемость. Но при содержании кремния более 25% свариваемость ухудшается так как образуются тугоплавкие оксиды ведущие к появлению шлаковых включений повышается прочность и твердость а вместе с этим и хрупкость.
Марганец - при содержании до 1% не ухудшает свариваемость и не затрудняет сварку. Как хороший раскислитель он способствует уменьшению содержания кислорода в стали. При содержании более 25% свариваемость ухудшается так как повышается твердость стали появляются закалочные структуры ухудшающие прочность пластические свойства и коррозионную стойкость стали.
Медь - в сталях до 1% улучшат свариваемость
Сера - не ухудшает свариваемость стали так как не превышает 0055%.
Молибден - в сталях от 05 до 3% в сильной степени увеличивает прочность и ударную вязкость стали: но ухудшает свариваемость повышением склонности к образованию трещин в шве и переходной зоне.
Азот - растворяется в расплавленном металле попадая в сварочную ванну из окружающей среды воздуха. Азот повышает прочность и твердость значительно снижает пластичность стали.
В нашем конкретном случае применяется сталь 09Г2С которая не представляет особых технологических трудностей при сварке.
О свариваемости стали учитывая химический состав следует судить по эквивалентному содержанию углерода:
Сэк= С + Mn 20 + Ni15 = 012 + 1720 + 0315 = 0225025 %
Сталь 09Г2С относится к 1 группе свариваемости так как у нее Сэк025 %. Эта сталь при обычном виде сварки не требует последующей термической обработки. Получаются сварные соединения высокого качества. Следовательно сталь 09Г2С хорошо свариваемая сталь. Эта сталь под действием обычного цикла сварки не закаляется.
Под технологической свариваемостью подразумевают совокупность свойств основного металла определяющих чувствительность его к термическому циклу сварки и способность при данной технологии сварки образовывать сварное соединение надлежащего качества по прочности и вязкости без применения специальных технологических приемов (подогрева отжига и т.д.).
Вывод: данная марка стали 09Г2С свариваетсябез ограничения ручной дуговой сваркой полуавтоматической и автоматической сваркой в защитных газах автоматической сваркой под флюсом.
Очевидными недостатками ручной дуговой сварки являются:
Неравномерное проплавление основного металла по толщине;
Непостоянство термического цикла сварки;
Необходимость частых повторных зажиганий дуги которые приводят к нежелательному тепловому воздействию на металл появлению склонности к коррозии.
Благодаря ряду преимуществ дуговая сварка под флюсом в настоящее время стала наиболее распространенным видом механизированной дуговой сварки металлов.
Сварка под флюсом успешно применяется при изготовлении аппаратуры конструкций и изделий самого ответственного назначения которые должны надежно работать и в условиях глубокого холода и под действием высоких температур давлений агрессивных жидких и газовых сред и т.д.
3 Выбор способа сварки и его обоснование
Способы сварки при изготовлении различных узлов отличаются по степени механизации и по способу защиты металла в зоне сварки [3].
Сварочные материалы должны иметь сертификаты и соответствовать требованиям стандартов или технических условий на их поставку.
Таблица 3.11 Сварочные материалы
Автоматическая сварка под флюсом
Полуавтоматическая сварка в среде защитного газа
При полуавтоматической сварке в среде защитного газа теплофизические свойства защитных газов оказывают большое влияние на технологические свойства дуги и форму швов. Широкий диапазон используемых защитных газов обладающих значительно различающимися теплофизическими свойствами обусловливает большие технологические возможности этого способа как в отношении свариваемых металлов (практически всех) так и их толщин (от 01 мм до десятков миллиметров). Сварку в защитных газах можно выполнять используя также неплавящийся (угольный вольфрамовый) или плавящийся электрод.
По сравнению с другими способами сварка в защитных газах обладает рядом преимуществ: высокое качество сварных соединений на разнообразных металлах и сплавах различной толщины; возможность сварки в различных пространственных положениях; возможность визуального наблюдения за образованием шва что особенно важно при полуавтоматической сварке; отсутствие операций по засыпке и уборке флюса и удалению шлака; высокая производительность и легкость механизации и автоматизации; низкая стоимость при использовании активных защитных газов.
К недостаткам способа сварки в защитных газах по сравнению со сваркой под флюсом относится необходимость применения защитных мер против световой и тепловой радиации дуги.
При сварке под флюсом плавление электродного и основного металлов осуществляется под флюсом надежно защищающим расплавленный металл от действия кислорода и азота воздуха. Флюс обладая плохой теплопроводностью замедляет процесс затвердевания металла шва что способствует выделению газов растворенных в расплавленном металле шва и предохраняет металл шва от выгорания основных легирующих элементов (марганец и кремний). При нейтральных флюсах металл шва по химическому составу близок к основному металлу а при марганцево-кремнистых флюсах происходит дополнительное легирование металла шва марганцем и кремнием вследствие чего улучшается его качество. Флюс способствует получению чистого и плотного металла шва без пор и включений с ровной однообразной внешней поверхностью с плавным переходом к основному металлу и высокими механическими свойствами сварного соединения. Потери на угар и разбрызгивание при сварке под флюсом практически отсутствуют.
При сварке под флюсом по сравнению с ручной сваркой применяются значительно большие токи обеспечивающие глубокое проплавление основного металла что позволяет производить сварку металла значительной толщины без скоса кромок. А при большой толщине суммарный угол разделки кромок можно уменьшить до 30-45° и следовательно можно уменьшить сечение шва а значит и количество электродного металла необходимого для заполнения разделки кромок. Высокая скорбеть однопроходной сварки легкая отделяемость шлаковой корки и отсутствие брызг экономят время и труд.
Применение больших токов обеспечивает повышенную скорость плавления электродной проволоки. Потери на угар и разбрызгивание практически отсутствуют. Коэффициент наплавки для наиболее часто применяемых токов 400-1200 А при сварке электродной проволокой диаметром 5 мм колеблется от 12 до 17 гА ч. При сварке электродной проволокой диаметром 2 мм на токах 400-700 А он составляет 20- 28 гАч.
Наличие мощной ванны расплавленного металла под слоем плохо проводящего тепло флюса является весьма благоприятным фактором способствующим стабильному горению дуги. Сварка обычно производится на переменном токе поэтому отсутствует явление магнитного выдувания дуги.
Дуга горит под толстым покровом флюса и невидима для оператора и окружающих лиц вследствие чего не требуется специальных устройств для защиты глаз.
4 Расчет режимов сварки
4.1 Ручная дуговая сварка
При ручной дуговой сварке угол разделки шва образованный двумя состыкованными кромками (рисунок 3.1д) составляет 55±3° (при этом зазор b3 и притупление кромок hп для листов толщиной >3 мм изменяются в пределах 0 – 3 мм). Такую подготовку кромок применяют при сварке листов толщиной до 18 – 20 мм. При большей толщине свариваемых элементов целесообразнее применять двухстороннюю Х-образную разделку кромок (рисунок 3.1е) с углами скоса также 55±3°. Сварку листов толщиной до 3 мм выполняют без скоса кромок (так называемая I-образная разделка) – рисунок 3.1а. Зазор между свариваемыми листами — 0 – 2 мм.
Тонкие швы (стыковые при толщине листов до 6 – 8 мм а угловые при катете шва до 6 – 8 мм) сваривают как правило за один проход (слой). При выполнении более толстых стыковых и угловых швов сварку (заполнение разделки шва) ведут за несколько проходов (слоев) – рисунок 3.1д. При этом сварку всех проходов стремятся выполнить при одних и тех же параметрах режима. Исключением является первый проход который рекомендуется выполнять электродами диаметром 3 – 4 мм (применение электродов большего диаметра затрудняет проплавление корня шва).
Сечение первого слоя (прохода) не должно превышать 30 – 35 мм2 и может быть определено по формуле: [11]
F1 =(6 – 8) dэ (3.1)
а последующих слоев (проходов) – по формуле
Fс =(8 – 12) dэ (3.2)
Общее число слоев (проходов) включая первый (сварка корня шва)
n = ((Fн - F1)Fc) + 1 (3.3)
где Fн - общая площадь наплавленного металла (шва).
При ручной дуговой сварке к параметрам режима сварки относятся: диаметр электрода сила сварочного тока скорость перемещения электрода вдоль шва (скорость сварки) род тока его полярность и др.
а) б) то же с металлической (остающейся) подкладкой (1); в) г) К-образный стыковой шов с подваркой (2) корня шва; д) V-образный многопроходной стыковой шов (цифры указывают номер прохода слоя); е) Х-образный двусторонний стыковой шов; з) расположение валиков при наплавке (наплавленный металл заштрихован пунктиром показана первоначальная разделка кромок соединяемых элементов)
Рисунок 3.1 – Размеры и форма подготовки кромок сварного шва
Диаметр электрода выбирается в зависимости от толщины свариваемых элементов типа сварного соединения и положения шва в пространстве. Для выбора диаметра электрода можно использовать ориентировочные данные:
В нашем случае толщина стенки обечайки сепаратора НГС-II-10-1200-1-И составляет 10 мм. Диамет электрода dэ принимаем 5 мм.
n = ((70 - 30)40) + 1 = 2.
При выборе типа и марки электрода необходимо исходить прежде всего из требований предъявляемых к качеству сварных швов или наплавки.
В настоящее время для сварки широко применяются высокопроизводительные электроды в том числе содержащие в составе обмазки железный порошок. В таблице 3.12 приведены данные о некоторых марках электродов в том числе и высокопроизводительных.
При выборе электродов рекомендуется ознакомиться с ГОСТ 9466 – 75 (классификация общие технические требования размеры правила приема методы испытания и др.) ГОСТ 9467 – 75 (электроды для сварки углеродистых низколегированных и легированных конструкционных и теплоустойчивых сталей) ГОСТ 10052 – 75 (электроды для сварки высоколегированных сталей с особыми свойствами: коррозионно- жаропрочные и др.) ГОСТ 10051 – 75 (электроды для наплавки слоев с особыми свойствами: износостойкие коррозионностойкие и др.).
Для оценки производительности электродов необходимо сравнивать значения коэффициента наплавки αн. Из группы электродов обеспечивающих заданные механические свойства металла шва или наплавки следует выбрать те которые имеют более высокий коэффициент наплавки и следовательно обеспечивают при прочих равных условиях большую производительность.
Таблица 3.12 - Характеристики сварочных и наплавочных электродов
Обозначение типов сварочных электродов расшифровывается так: Э – электрод; цифры стоящие за буквой – гарантированное значение предела прочности в кгсмм2.
В наплавочных электродах следующие за буквой Э цифры и буквы показывают среднее содержание углерода и легирующих элементов в наплавленном металле. В марках электродов цифры указывают твердость НВ. Например металл наплавленный электродами типа Э12Г4 (марка ОЗН-350У) содержит в среднем 012 % С и 40 % Мn; твердость его равна 350 НВ.
Силу сварочного тока выбирают на основании рекомендаций помещенных в паспортах электродов и справочных таблицах или рассчитывают по эмпирическим формулам.
При ручной дуговой сварке стальными электродами диаметром 1 – 6 мм можно пользоваться формулой:
где К — коэффициент равный 25 – 60;
dэ — диаметр электрода мм.
Коэффициент К в зависимости от диаметра электрода dэ принимается равным:
Принимаем К равным 45.
Силу сварочного тока рассчитанную по этой формуле следует скорректировать с учетом толщины свариваемых элементов типа соединения и положения сварки в пространстве. Так если толщина листов S >= 3 dэ то значение Iсв следует увеличить на 10—15%. Если же S = 15 dэ то сварочный ток уменьшают на 10—15%. При сварке угловых швов и наплавке значения Iсв должно быть повышено на 10 – 15%. Если сварка производится в вертикальном или потолочном положении значение сварочного тока должно быть уменьшено на 10 – 15%.
Iсв = (11-115)·225 = 2475 - 25875 А
Принимаем Iсв=250 А.
Выбирая род тока следует учитывать экономические и эксплуатационные преимущества переменного тока перед постоянным. Однако могут быть положения при которых использование переменного тока не допускается или не рекомендуется например при сварке электродами УОНИ-13. Так характер наплавочных работ обусловливает необходимость получения слоя наплавленного металла за счет возможно большего количества электродного металла при минимальной глубине проплавления основного металла. Поэтому для наплавочных работ следует предпочесть постоянный ток и вести наплавку на той полярности на которой электродный металл плавится быстрее.
Для ориентировочного определения длины дуги lд мм можно пользоваться формулой
lд = (05 – 11) dэ (3.5)
где dэ – диаметр электрода мм.
Длина дуги влияет на качество наплавленного металла и геометрическую форму шва. При длинной дуге ухудшается защита сварочной ванны и металл шва интенсивно насыщается кислородом и азотом воздуха. С увеличением длины дуги увеличивается разбрызгивание металла и в шве могут появиться поры. Принимаем lд равным 25 мм.
Для определения напряжения дуги Uд используют справочные данные или рекомендации сертификатов которыми сопровождается каждая марка электрода (в технологической документации Uд не регламентируется).
Для большинства марок электродных покрытий используемых при сварке углеродистых и легированных конструкционных сталей напряжение дуги Uд = 22 – 28 В.
Расчет скорости сварки (скорость перемещения электрода при укладке одного слоя валика многослойного шва) мч производится по формуле
Vсв= αнIсв100Fн(с)ρ (3.6)
где αн – коэффициент наплавки г(А ч);
Fн(c) – площадь поперечного сечения шва Fн при однопроходной сварке (или одного слоя валика Fн(c) при многослойном шве) см2;
ρ – плотность металла электрода гсм3 для стали ρ = 78 гсм3.
Vсв= 10·250100·07·78 = 46 мч
Коэффициент наплавки αн выбирается в зависимости от марки электрода по таблице 3.12.
Масса наплавленного металла определяется по справочнику или рассчитывается по формуле
где Fн – площадь наплавки (поперечное сечение разделки шва включая его усиление) см2; L — длина шва см;
Gн = 07·540·78 = 2948 г;
t = 294810·250 = 118 ч.
Приближенно полное время сварки Т ч можно определить по формуле:
где t – время горения дуги ч;
Кп – коэффициент использования сварочного поста который можно принять для ручной сварки 05 – 055 а для механизированных способов сварки и наплавки – 06 –07.
Расход электродов для ручной сварки и наплавки можно определить воспользовавшись данными помещенными в таблицу 3.12.
Расход электроэнергии А кВт-ч на сварку заданной детали можно найти установив по справочным материалам расход электроэнергии на 1 кг наплавленного металла. Более точно его можно рассчитать по формуле:
где Uд – напряжение дуги В (при сварке покрытыми электродами принять 22 – 28 В);
– КПД источника тока;
– мощность расходуемая источником тока при работе на холостом ходу кВт;
t и Т – соответственно время горения дуги и полное время сварки ч.
Данные для определения значений и 0 помещены в таблицу 3.13.
4.2 Полуавтоматическая сварка в углекислом газе проволокой сплошного сечения
При сварке в углекислом газе применяют следующие виды подготовки кромок свариваемых элементов [12]:
) при толщине листов 1 – 2 мм – I-образную (без скоса кромок) зазор в стыке 0 – 1 мм сварка односторонняя;
) при толщине листов 3 – 12 мм – I-образную зазор в стыке 0 – 15 мм сварка двухсторонняя;
) при толщине листов 14 – 24 мм — V-образная под углом 40±5° притупление кромок 2 – 3 мм зазор в стыке 0 – 15 мм; сварка многопроходная с подваркой корня шва.
В нашем случае толщина стенки обечайки сепаратора НГС-II-10-1200-1-И составляет 10 мм.
В основу выбора диаметра электродной проволоки положены те же принципы что и при выборе диаметра электрода при ручной дуговой сварке:
Сварка в углекислом газе выполняется легированной проволокой сплошного сечения (чаще всего кремнемарганцовистой: Св-08ГС Св-10Г2С и др.).
Расчет сварочного тока А при сварке проволокой сплошного сечения производится по формуле: [11]
где а – плотность тока в электродной проволоке Амм2 (при сварке в СО2 а = 110 – 130 Амм2);
dэ – диаметр электродной проволоки мм.
Принимаем Iсв равным 380 А.
Механизированные способы сварки позволяют использовать значительно большие плотности тока по сравнению с ручной сваркой. Это объясняется меньшей длиной вылета электрода.
Процесс сварки в углекислом газе на постоянном токе прямой полярности отличается меньшей глубиной проплавления основного металла но при этом заметно снижается устойчивость дуги и возрастает склонность наплавленного металла к образованию пор. Поэтому наплавку в углекислом газе предпочтительно вести на обратной полярности.
Напряжение дуги и расход углекислого газа выбираются в зависимости от силы сварочного тока [12]:
U=30 – 32 В QCO2 = 18 – 20 лмин
Скорость подачи электродной проволоки Vпр мч выбирается по справочным материалам или рассчитывается по формуле:
где αр – коэффициент расплавления проволоки г(А-ч);
Для сварки в углекислом газе значение αр может быть рассчитано по формуле:
Скорость полуавтоматической сварки или скорость перемещения электрода при укладке отдельного слоя (валика) многослойного шва смс определяется по формуле (3.6). При этом
где – коэффициент потерь металла на угар и разбрызгивание. При сварке в СО2 = 010 – 015.
Массу наплавленного металла время горения дуги и время сварки – по формулам (3.7–3.9); при этом Кп принимается равным 06 – 07.
t = 2948164·380 = 047 ч;
Расход электродной проволоки сплошного сечения Qпр кг можно рассчитать по формуле
Qпр = Gн(+ 1) (3.15)
Qпр = 2948(01+ 1) = 324 кг
Расход электроэнергии – по формуле (3.10):
4.3 Автоматическая сварка под флюсом проволокой сплошного сечения
При автоматической сварке под флюсом чаще всего применяют следующие виды подготовки кромок [12]:
) I-образная (без скоса кромок) – применяют при однопроходной и двухпроходной сварке. При однопроходной сварке чаще всего сварку выполняют на остающейся стальной подкладке (рисунок 3.1 б) или по ручной подварке при соединении листов толщиной до 10 – 12 мм. Зазор bз между кромками 2 – 3 мм. При двухпроходной сварке листов толщиной 14 – 60 мм сварку ведут по зазору bз между кромками 3 – 11 мм который увеличивается с толщиной свариваемых листов.
) V-образная со скосом кромок под углом 60±5° (рисунок 3.1 г) применяется для листов толщиной 14 – 30 мм. Сварка выполняется по ручной подварке. Притупление кромок и зазор между ними 0 – 3 мм.
) Х-образная со скосом кромок под углом 60±5° (рисунок 3.1 е) применяется для листов толщиной 20 – 60 мм и более.
В нашем случае выбираем I-образную подготовку без скоса кромок.
Для сварки стали применяют сварочную проволоку по ГОСТ 2246-70 (Св08 Св08ГА Св10Г2 Св08ГС Св18ХГС Св08ХМ Св08ХГ2С Св08ХНМ).
Расчет силы сварочного тока по формуле (3.11).
Плотность тока при автоматической сварке под флюсом изменяется в достаточно широком диапазоне (табл. 3.14). Рекомендуется при сварке для более глубокого проплавления использовать высокие значения плотности тока в электродной проволоке (α>= 40 – 50 Амм2). Диаметр электродной проволоки желательно выбирать таким чтобы он обеспечил максимальную производительность сварки при требуемой глубине проплавления. В таблице 3.14 приведено влияние силы сварочного тока и его плотности на глубину проплавления.
Таблица 3.14 – Влияние силы и плотности сварочного тока на глубину проплавления
Примечание. В числителе – сила сварочного тока А; в знаменателе – потность тока в электродной проволоке Амм².
Зависимость напряжения дуги от силы сварочного тока (флюс АН-348А) следующая:
Сила сварочного тока А 180-300 300-400 500-600 600-700 700-850 850-1000
Напряжение дуги В 32-34 34-36 36-40 38-40 40-42 41-43
Принимаем Iсв равным 800 А. Uд=40 В.
Расчет скорости подачи электродной проволоки см. формулу (3.12).
Коэффициент расплавления электродной проволоки сплошного сечения при сварке под флюсом для постоянного тока прямой полярности
Расчет скорости сварки Vсв (скорости перемещения электродной проволоки при укладке отдельного валика многопроходного шва) определяется по формуле (3.6). При этом принять для расчета αн значение = 002 – 003.
αн=161(1-002) = 1578;
Марка флюса выбирается в зависимости от химического состава основного металла и требований предъявляемых к свойствам наплавленного металла. Наиболее часто употребляются флюсы АН-348А или ОСЦ-45 в сочетании с проволокой марки Св08А.
Толщина слоя флюса зависит от силы сварочного тока:
Расчет массы наплавленного металла время горения дуги и время на сварку производится по формулам (3.7-3.9) при этом Кп =06 – 07.
t = 29481578·800 = 023 ч;
Расчет расхода проволоки сплошного сечения по формуле (3.15):
Расчет расхода электроэнергии по формуле (3.10):
5 Совершенствование технологии сварки обечайки
Изобретение относится к нефтяной и нефтеперерабатывающей промышленности и может найти применение при изготовлении оборудования для переработки нефти в частности при сборке крупноразмерных металлических резервуаров типа сепараторов отстойников емкостей для хранения и подготовки нефти. Способ включает сварку металлических листов встык под флюсом с принудительной подачей флюса сверху и снизу сварного шва. Затем осуществляют вальцевание из сваренных листов цилиндров. Далее сваривают стык вдоль цилиндров с принудительной подачей флюса сверху и снизу сварного шва с получением цилиндрических обечаек. Размещают цилиндрические обечайки на роликах торцевыми поверхностями друг к другу. Ведут сварку встык по торцам цилиндрических обечаек с принудительной подачей флюса сверху и снизу сварного шва. При этом заполняют зону сварки флюсом между обечайками путем подачи флюса изнутри обечаек. Сварку осуществляют при вращении свариваемых обечаек. Техническим результатом изобретения является повышение прочности сварных обечаек за счет повышения качества сварных швов.
Задача решается способом изготовления крупноразмерных металлических обечаек включающим сварку металлических листов встык под флюсом с принудительной подачей флюса сверху и снизу сварного шва из сваренных металлических листов вальцеванию цилиндра сварку металлических листов встык вдоль цилиндра с формированием цилиндрической обечайки с принудительной подачей флюса сверху и снизу сварного шва размещение цилиндрических обечаек на роликах торцевыми поверхностями друг к другу сварку встык по торцам цилиндрических обечаек с одновременным вращением двух обечаек с принудительной подачей флюса сверху и снизу сварного шва при сварке листов встык для принудительной подачи флюса снизу сварного шва под сварным швом размещают ванну с гибким днищем наполненную флюсом и поджимают гибкое днище и объем флюса снизу к сварному шву при сварке встык по торцам цилиндрических обечаек для принудительной подачи флюса снизу сварного шва под сварным швом размещают чашеобразную емкость с эластичными бортами способную свободно вращаться на оси с осью на шарнире и с возможностью перемещаться по вертикали размещают чашеобразную емкость под обечайками в зоне сварного шва с наклоном оси чаши к вертикали под углом 10-15 град. и контактированием борта чашеобразной емкости с днищем одной из обечаек заполняют сварочным флюсом чашеобразную емкость и пополняют флюс при его расходовании заполняют зону сварки между обечайками изнутри обечаек вращают обечайки с передачей вращения чашеобразной емкости.
Сущность изобретения.
При изготовлении крупноразмерных т.е. более 1 м в диаметре металлических обечаек особое внимание уделяют качеству сварных швов. Сварку металлических листов производят встык с небольшим зазором между листами. При электросварке под флюсом не вызывает особых трудностей подача флюса сверху в зону сварки. Но при этом происходит просыпание флюса между металлическими листами и оголение сварного шва. В результате сварной шов получается ослабленным имеют место непровары прожоги основного металла. Применение ванны с флюсом под сварным швом также не решает эту проблему т.к. флюс в ванне оседает и зона сварки остается без флюса. К тому же эффекту приводит и расход флюса на сварку. Существующие технические решения или не решают эту проблему или решают ее лишь частично. В предложенном изобретении решается задача повышения прочности сварных обечаек за счет повышения качества сварных швов. Задача решается следующим образом.
При сварке крупноразмерных металлических обечаек выполняют электросварку металлических листов встык под флюсом с принудительной подачей флюса сверху и снизу сварного шва. Из сваренных металлических листов вальцуют цилиндры изгибанием листов в цилиндры на трехвалковой листогибочной машине. Вдоль цилиндра производят электросварку металлических листов встык с формированием цилиндрической обечайки. Электросварку ведут в полуавтоматическом режиме с принудительной подачей флюса сверху и снизу сварного шва. Полученные цилиндры размещают на роликах торцевыми поверхностями друг к другу. Производят электросварку встык по торцам цилиндрических обечаек с одновременным вращением двух обечаек с принудительной подачей флюса сверху и снизу сварного шва после сварки получают крупноразмерную металлическую обечайку. При необходимости к обечайке приваривают одно или два днища или переход или какое-либо другое продолжение в зависимости от конкретного применения на производстве.
Рисунок 3.2 – Ванна с флюсом с системой поджатия флюса к сварному шву
При сварке металлических листов встык для принудительной подачи флюса снизу сварного шва под сварным швом размещают ванну с гибким днищем наполненную флюсом. На рисунке 3.2 показана ванна с флюсом с системой поджатия флюса к сварному шву. Под металлическими листами 1 размещена ванна 2 с резиновым днищем 3 под которым расположена асбестовая прокладка 4 и рукава 5 типа пожарных способные раздуваться и увеличиваться в диаметре что способствует плотному прилеганию флюса снизу сварного соединения. Флюс 6 размещен под металлическими листами 1 над резиновым днищем 3.
При сварке подают сжатый воздух по рукавам 5 которые увеличиваются в диаметре и поджимают резиновое днище 3 и флюс 6 к металлическим листам 1 обеспечивая наличие флюса 6 в зоне сварки между листами 1. Асбестовая прокладка 4 предохраняет рукава 5 от воздействия повышенной температуры возникающей при сварке.
Такую же ванну используют при электросварке встык металлических листов отформованных в цилиндрическую форму. Вдоль цилиндра производят электросварку металлических листов встык с формированием цилиндрической обечайки.
Рисунок 3.3 – Оборудование для принудительной подачи флюса снизу сварного шва
При сварке встык по торцам цилиндрических обечаек для принудительной подачи флюса снизу сварного шва в зоне сварки размещают оборудование представленное на рисунке 3.3.
На рисунке 3.3 чашеобразная емкость 7 с эластичными бортами 8 из резины заполнена флюсом 6. Емкость 7 установлена на оси 9 с возможностью свободно вращаться на оси 9. Ось 9 закреплена на шарнире 10. Емкость 7 размещена под обечайками 11 со смещением оси 9 относительно зоны сварки (сварного шва) 12 вдоль металлических обечаек 11 на угол α. Обечайки поставлены на роликовые опоры 13 с возможностью вращения на роликовых опорах 13. Внутри обечаек размещен бункер для подачи флюса 14 с флюсом 15 и сварочная головка 16 на консоли 17. Ось 9 закреплена через шарнир 10 на пневмоцилиндре 18 с возможностью вертикального перемещения под действием пневмоцилиндра 18.
Чашеобразную емкость 7 размещают под обечайками 11. Пневмоцилиндр 18 поджимает чашеобразную емкость 7 к сварному шву 12 обечаек 11 что способствует плотному прилеганию флюса 6 снизу к сварному шву 12 между обечайками 11. В зоне сварки 12 организуют смещение оси 9 относительно сварного шва 12 вдоль металлических обечаек 11. Для этого чашеобразную емкость 7 располагают с наклоном оси 9 в сторону смещения под углом α=10-15 градусов к вертикали и контактированием эластичного борта 8 чашеобразной емкости 7 с днищем одной из обечаек 11.
Чашеобразную емкость 7 заполняют флюсом 6. При электросварке сварочную головку 16 направляют в зону сварки 12 внутри обечаек 11 также внутри обечаек 11 в зону сварки 12 подают флюс 15 из бункера 14. Снизу от обечаек 11 флюс 6 подают в зону сварки 12 из чашеобразной емкости 7. При вращении обечаек 11 за счет контактирования эластичного борта 8 чашеобразной емкости 7 с обечайкой 11 вращение передается от обечайки 11 к расположенной наклонно и касающейся обечайки 11 чашеобразной емкости 7. Эластичный борт 8 чашеобразной емкости 7 отгибается и флюс 6 касается зоны сварки 12. С другой стороны чашеобразной емкости 7 отстоящей от обечайки 11 подсыпают флюс 6 обеспечивая пополнение флюса 6 при его расходовании. Производят сварку встык по торцам обечаек 11.
В результате получают качественно выполненные сварные швы.
Пример конкретного выполнения
Изготовляют крупноразмерную металлическую обечайку диаметром 1200 мм длиной 5400 мм и толщиной стенки 10 мм. Электросварку ведут в полуавтоматическом режиме с применением сварочной проволоки марки СВ-08ГА с напряжением электрического тока 38-40 вольт и силой тока 700-750 ампер.
Выполняют электросварку металлических листов толщиной 10 мм встык под флюсом марки АН-47. При электросварке выполняют принудительную подачу флюса сверху и снизу сварного шва. Сверху сварного шва выполняют подсыпку флюса а для подачи флюса снизу используют приспособление и выполняют работу приспособления показанного на рисунке 3.2. Получают листы с размерами 3773×1500 мм каждый.
Из сваренных металлических листов формуют цилиндры изгибанием листов в цилиндры на трехвалковой листогибочной машине. Получают 2 цилиндра наружным диаметром 1200 мм и длиной 1500 мм. Вдоль каждого цилиндра производят электросварку металлических листов встык с формированием цилиндрической обечайки.
Полученные обечайки размещают на роликах торцевыми поверхностями друг к другу. Производят электросварку встык по торцам цилиндрических обечаек с одновременным вращением двух обечаек с принудительной подачей флюса сверху и снизу сварного шва. При электросварке выполняют принудительную подачу флюса сверху и снизу сварного шва. Сверху сварного шва выполняют подсыпку флюса а для подачи флюса снизу используют приспособление и выполняют работу приспособления показанного на рис.3.3.
После сварки получают крупноразмерную металлическую обечайку с качественно выполненными сварными швами. В швах отсутствует разнотолщинность непровары прожоги.
Применение предложенного способа позволит повысить прочность сварных обечаек за счет повышения качества сварных швов.
Способ изготовления крупноразмерной металлической обечайки состоящей по крайней мере из двух металлических обечаек включающий сварку металлических листов встык под флюсом с принудительной подачей флюса сверху и снизу сварного шва вальцеванием из них цилиндров сварку стыка вдоль цилиндров с принудительной подачей флюса сверху и снизу сварного шва с получением цилиндрических обечаек размещение цилиндрических обечаек на роликах торцевыми поверхностями друг к другу и сварку их встык по торцам цилиндрических обечаек отличающийся тем что при сварке металлических листов встык принудительную подачу флюса снизу сварного шва обеспечивают путем размещения под сварным швом ванны выполненной с гибким днищем и наполненной флюсом и поджатия ее гибкого днища с флюсом снизу к сварному шву сварку встык по торцам цилиндрических обечаек осуществляют с принудительной подачей флюса сверху и снизу сварного шва причем принудительную подачу флюса снизу сварного шва обеспечивают путем размещения под сварным швом чашеобразной емкости с эластичными бортами с возможностью контактирования борта чашеобразной емкости с днищем одной из обечаек причем чашеобразную емкость закрепляют на оси с возможностью вращения которая закреплена шарнирно на пневмоцилиндре с возможностью перемещения по вертикали и наклона оси чаши к вертикали под углом 10-15° при этом чашу заполняют сварочным флюсом в процессе сварки заполняют зону сварки флюсом между обечайками путем подачи флюса изнутри обечаек сварку осуществляют с вращением свариваемых обечаек.
Введение.doc
Современное оборудование подготовки нефти характеризуется высокой сложностью и ответственностью. Актуальность проблемы подготовки нефти обусловлена двумя основными причинами. Во-первых в связи с совершенствованием технологии переработки нефти превращение прежних нефтеперерабатывающих заводов вырабатывающих различное топливо и смазочные масла в комплексные нефтехимические комбинаты производящие новые виды химической продукции значительно изменились требования к качеству нефти. Если раньше на технологические установки НПЗ шла нефть с содержанием 100-500 мгл минеральных солей то в настоящее время требуется более глубокое обессоливание а в дальнейшем и полное удаление солей из нефти перед ее переработкой. Во-вторых наша страна являясь крупным экспортером нефти поставляет ее во многие государства. При этом требования к качеству поставляемой нефти довольно жестки - содержание солей не должно превышать 25-40 мгл при содержании воды до 01%.
Сепараторы нефтегазовые типа НГС являются основным видом оборудования в составе установок подготовке нефти. При их изготовлении используются самые разные способы и методы сварки поэтому важнейшая роль принадлежит технологии сварочного производства и сварочной технике.
В данной работе рассмотрены задачи стоящие при проектировании и изготовлении нефтегазового сепаратора типа НГС. В частности это технология сварки обечаек ее совершенствование.
Рекомендуемые чертежи
- 23.03.2021