Нефтеперегонная колонна




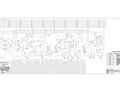
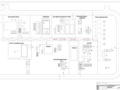
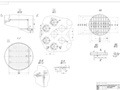
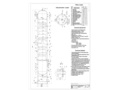
- Добавлен: 04.11.2022
- Размер: 47 MB
- Закачек: 1
Описание
Состав проекта
![]() |
![]() ![]() ![]() |
![]() ![]() ![]() |
![]() ![]() ![]() |
![]() ![]() ![]() |
![]() ![]() ![]() |
![]() ![]() ![]() |
![]() ![]() ![]() |
![]() |
![]() ![]() ![]() ![]() |
![]() ![]() ![]() ![]() |
![]() ![]() ![]() ![]() |
![]() ![]() ![]() ![]() |
![]() ![]() ![]() |
![]() ![]() ![]() |
![]() ![]() ![]() |
![]() ![]() ![]() |
![]() ![]() ![]() |
![]() ![]() ![]() |
![]() ![]() ![]() |
![]() ![]() ![]() |
![]() ![]() ![]() |
![]() ![]() ![]() |
![]() ![]() ![]() |
![]() |
![]() ![]() ![]() |
![]() ![]() ![]() |
![]() ![]() ![]() |
![]() ![]() ![]() |
![]() ![]() ![]() |
![]() ![]() ![]() |
![]() ![]() ![]() |
![]() ![]() ![]() |
![]() ![]() ![]() |
![]() ![]() ![]() |
Дополнительная информация
7.1 Спецификация_приборов.doc
Наименование параметра среды и места отбора импульса
Наименование и характеристика
на трубопроводе подачи нефти
Диафрагма на условное давление 0.6МПа. Материал корпусов сталь 35.
Условный проход 200 мм. Материал диска – сталь Х 17.
Дифманометр бесшкальныйсильфонный с выходным пневматическим унифициро- ванным сигналом 0.2- 1кгссм2 на пре-
дельный перепад давления 0.63кгссм2 . Класс точности 1.
Вторичный показывающий прибор.
Запись и показание величины регули-руемого параметра показание величины
задание и управляющего воздействие переключение системы регулирования
на ручное дистанционное. Класс точ-
«Тепло-прибор» г.Рязань
«Тепло-контроль г.Москва
Продолжение таблицы 3
Температура верха К-1
Термометр сопротивления материал чувствительного элемента платиновый. Градуировка 21. Предел измерения
-50÷150 0С. Материал сталь Х18Н10Т. Инерционность 40 с; Ру=4кгссм2
Автоматический электронный мост с
одним датчиком. Время прохождения
указателем всей шкалы 1с. Количество
измерения 1. Класс точности 0.5; предел измерения 0÷100 0С
«Львов-прибор» г.Львов
Монометр сильфонный самопишущий с пневматическим регулирующим устройством с дистанционной передачей. Класс точности 1. Предел измерений 0-16 кгссм2
Прибор вторичный пневматический показывающий самопищущий со станцией управления. Класс точности 1.Шкала равномерная 0-25 кгссм2
Пневматический Пи-регулятор системы «старт» предел пропорциональности 2-3000% предел интегрирования от 3 с. до 100 мин.
Клапан регулирующий с пневмоприводом для неагрессивных сред.
«Тизприбор» г.Москва
«Киеварматура» г.Киев
Температура верха колонны К-1
Термопреобразователь градуировки хромель-копель предел измерения (0-600)°С материал защитной арматуры: сталь Х18Т10Т монтажная длина 1200 мм. Инерционность 10с. Условное давление 64 кгссм2. Виброустойчивая.
Автоматический потенциометр со встроенным регулятором предназначенный для работы с одним датчиком. Градуировка ХК. Время
прохождения 10с класс точности 05 предел измерения (0–400)°С
Байпасная панель дистанционного управления установленная на щите
Регулирующий клапан с исполнительным мембранным механизмом и пневмоприводом для неагрессивных сред. Dу=50мм. Ру=64МПа
Котельниковский арматурный завод
Температура после холодильника Х-1
Манометр сильфонный самопишущий. Класс точности 1. Предел измерений (0–16) МПа.
Прибор пневматический. Скорость диаграммы 40 ммч. Шкала равномерная (0–16) МПа. Класс точности 1. Исполнение обыкновенное
Манометр электроконтактный показывающий сигнализирующий. Шкала (0016) МПа. Класс точности 1.5
Томский манометровый завод
Уровнемер буйковый со шкальным устройством с унифицированным устройством давления воздуха 02–1 кгс см2. Допускаемое Ризб=4 МПа. Класс точности 15. Предел измерения (0 –16000) мм
Прибор вторичный пневматический показывающий самопишущий со станцией управления. Класс точности 1. Шкала равномерная (0–100)%
Манометр электроконтактный показывающий сигнализирующий. Шкала (0016) МПа. Класс точности 1.5
Пневматический ПИ-регулятор системы «Старт» предел пропорциональ-ности 2-3000% предел интегрирования от 3 с до 100 мин. Класс точности 0.5
Томский манометровый завод
Регулирующий клапан с исполнительным мембранным механизмом и пневмоприводом для неагрессивных сред. Dу=200мм. Ру=64МПа
Температура в колонне К-1
Уровень в кубе колонны К-1
Уровнемер буйковый со шкальным устройством и унифицированным устройством сигнала давления воздуха 02-1кгссм2. Допускаемое избыточное давление 4 мПа. Класс точности 15. Предел измерения 0-16000мм.
Прибор вторичный пневматический показывающий самопищущий со станцией управления. Класс точности 1 шкала равномерная
«Теплоприбор» г. Рязань
Клапан регулирующий с пневмоприводом для неагрессивных сред.Д=250 мм Р=16 МПа
Температура куба колонны К-1
На трубопроводе d=100 мм
Термоэлектрический термометр одинарной градуировки ХА предел измерения 0-420С материал защитной арматуры ХА 18Н10Т монтажная длинна 1200 мм инерционность 10 сек. Ру=64 кгссм2 виброустойчив
Автомат. электр. потенцион. для работы с одним датчиком; град. ХА со встроенным регулятором. Класс точности 05; предел измерения 0-420°C
Панель управления пневматическая предназначена для осуществления перехода с автоматического регулирования на ручное управление исполнительным механизмом и обратно.
Клапан регулирующий с мембран. пневмоприводом для неагрессивных
средств Ду=100 мм; Ру=25 кгссм2.
ТХА-0515-5у2.821730-02
Котельниковский арматурный завод г.Котельни-ков
«Саранский приборостроительный завод»
Температура в колонне К-2
Уровень в кубе колонны К-2
Уровнемер буйковый со шкальным устройством и унифицированным устройством сигнала давления воздуха 02-1кгссм2. Допускаемое избыточное давление 4мПа. Класс точности 15. Предел измерения 0-16000мм.
Температура после холодильника ХВ-1
Термометр сопротивления материал чувствительного элемента платиновый. Градуировка 21. Предел измерения -50÷150 0С. Материал сталь Х18Н10Т. Инерционность 40 с; Ру=4кгссм2
одним датчиком. Время прохождения указателем всей шкалы 1с. Количество измерения 1. Класс точности 0.5; предел измерения 0÷100 0С
Первичный преобразователь для изме-рения расхода установленный по месту Диафрагма на условное давление 0.6МПа. Материал корпусов сталь 35. Условный проход 200 мм. Материал диска – сталь Х 17.
Температура после печи П-2
Температура верха колонны К-3
Температура после холодильника Х-2
Термопреобразователь градуировки хромель-копель предел измерения (0-600)°С материал защитной арматуры: сталь Х18Т10Т монтажная длина 1200 мм. Инерционность 10с. Условное давление 64 кгссм2. Виброустойчивая.
Автоматический потенциометр предназначенный для работы с одним датчиком. Градуировка ХК. Время прохождения 10с класс точности 05 предел измерения (0–400) °С
Пневматический ПИ-регулятор системы «Старт» предел пропорциональ-ности 2-3000% предел интегрирования от 3 с до 100 мин. Класс точности 0.5. Манометр электроконтактный показывающий сигнализирующий. Шкала (0016) МПа. Класс точности 1.5
Температура в колонне К-3
Уровень в кубе колонне К-3
Пневматический Пи-регулятор
системы «старт» предел пропорциональности 2-3000% предел интегрирования от 3 с. до 100 мин.
Температура в кубе колонне К-3
Температура в колонне К-4
Уровень в кубе колонны К-4
Пневматический Пи-регулятор системы «старт» предел пропорциональности 2-3000% предел интегрирования от 3 с. до 100 мин
Введение.docx
Головной установкой НПЗ является установка АВТ. Она предназначена для получения нефтяных фракций которые используется как сырье для последующей переработки или в качестве компонентов товарной продукции. Атмосферная перегонка нефти является начальной стадией переработки нефти. На установке атмосферной перегонки получаются такие продукты как: топливный газ бутан - пентановая фракция прямогонный бензин тяжелый бензин дизельное топливо керосино - газойлевая фракция мазут.
Важность фундаментальной проблемы улучшения экологических и эксплуатационных характеристик моторных топлив определяется мировой тенденцией в изменениях требований к топливам транспортных и стационарных энергетических установок обусловленной все более жесткими нормативами на содержание вредных примесей в продуктах сгорания а так же повышенными требованиями к низкотемпературным свойствам. Основным путем решения этих проблем является развитие методов гидрооблагораживания топлив в том числе и процесса деароматизации.[1 с.4]
Удаление из дизельного топлива ароматических угдеводородов в том числе и полициклического строения позволит получать дизельное топливо удовлетворяющее европейским стандартам (марки Евро 4 Евро 5).
В России ожидается переход на массовую выработку топлив стандарта Евро-4 ориентировочно в 2010 году.
Такого рода работа предстоит и нефтяникам Татарстана в том числе и работникам НГДУ «Елховнефть». С учетом этих требований выполнена данная работа.
Спецификация2.doc
Атмосферная трубчатка
ДП. 2404.26.01.00.000
Колонна отбензинивания
ДП. 2404.26.02.00.000
Колонна атмосферная
ДП. 2404.26.03.00.000
ДП. 2404.26.04.00.000
ДП. 2404.26.05.00.000
ДП. 2404.26.06.00.000
ДП. 2404.26.07.00.000
ДП. 2404.26.08.00.000
ДП. 2404.26.09.00.000
ДП. 2404.26.10.00.000
ДП. 2404.26.11.00.000
ДП. 2404.26.12.00.000
ДП. 2404.26.13.00.000
ДП. 2404.26.14.00.000
ДП. 2404.26.15.00.000
ДП. 2404.26.16.00.000
ДП. 2404.26.17.00.000
ДП. 2404.26.18.00.000
ДП. 2404.26.19.00.000
ДП. 2404.26.20.00.000
Атмосферная трубчатка
Схема общая комбинированная
ДП. 2404.26.21.00.000
ДП. 2404.26.22.00.000
ДП. 2404.26.23.00.000
ДП. 2404.26.24.00.000
ДП. 2404.26.25.00.000
ДП. 2404.26.26.00.000
ДП. 2404.26.27.00.000
ДП. 2404.26.28.00.000
ДП. 2404.26.29.00.000
ДП. 2404.26.30.00.000
ДП. 2404.26.31.00.000
ДП. 2404.26.32.00.000
4 описание тех.схемы.doc
Cырая нефть подается через узел учета нефти на всас насоса Н-1с температурой 25-35 оС.
Насосом Н-1сырая нефть через теплообменники Т-1Т-2и Т-3подается в обессоливатель ЭДГ.
В межтрубном пространстве теплообменников Т-1 сырая нефть подогревается до 59 0С за счет тепла легкого вакуумного газойля подаваемого в трубную часть теплообменников с температурой 145-150 оС.
В межтрубном пространстве теплообменников Т-2 сырая нефть подогревается до 98 0С за счёт тепла дизельного топлива подаваемого в трубную часть теплообменника насосом Н-8с температурой 215-220 оС.
В трубном пространстве теплообменника Т-3 сырая нефть подогревается до 1230С за счет тепла дизельного топлива подаваемого в межтрубную часть теплообменника насосом Н-7с температурой 225-230 оС.
Перед подачей в обессоливатель ЭДГ сырая нефть разбавляется промывочной водой во избежание уменьшения количества солей в сырой нефти.
Вода и нефть тщательно перемешиваются перед поступлением в обессоливатель ЭДГ за счет создания перепада давления на смесительном вентеле. Перепад давления должен находиться в пределах 03 - 10 кгссм2.
Обессоливатель ЭДГ представляет собой емкость с двумя горизонтальными рядами металлических стержней (электродов) расстояние между которыми 19 см. При этом верхний ряд электродов заземлен на корпус сосуда а нижний ряд поддерживается электрическими изоляторами и находится под напряжением 45-55 кВ.
Нефть с температурой 120-125 оС.поступает в обессоливатель ЭДГ через распределительный коллектор расположенный в нижней части аппарата. В обессоливателе происходит раздел фаз нефть - вода.
Увлекаемые нефтью частицы воды под действием электрического поля коагулируют и под действием силы тяжести оседают в нижней части аппарата.
Вода с температурой 115-120 оС.выводится из обессоливателя ЭДГ и отводится в КОС (Кичуйские очистные сооружения) ЦКППН.
Обессоливатель ЭДГ должен эксплуатироваться при полном заполнении нефтью. При снижении уровня нефти менее 97% происходит отключение напряжения на электродегидраторе во избежание образования газовой фазы («шапки») и взрыва из-за оголения электродов находящихся под высоким эл.напряжением.
Обессоленная нефть с температурой 105-115 оС выводится через верхний штуцер обессоливателя ЭДГ и поступает последовательно в:
-трубное пространство теплообменников Т-4 где подогревается за счет тепла циркулирующего дизельного топлива до температуры 140-150 оС;
-Т-5 где подогревается до температуры 170-175 оС за счет тепла циркулирующего атмосферного и тяжелого вакуумного газойля;
-Т-6 где подогревается до температуры 215-220 оС за счет тепла циркулирующего тяжелого вакуумного газойля;
-Т-7 где подогревается до температуры 235-240 оС за счет тепла кубового продукта колонны К-3.
Подогретая до 2390С обессоленная нефть после теплообменников Т-7 под давлением ~80 кгссм2 поступает на 8-ю тарелку стабилизационной колонны К-1.
Для увеличения срока службы и защиты от коррозии оборудования установки применяется ввод щелочных реагентов в сырье.
Паровая фаза колонны К-1 с температурой 65-75оС и давлением 60-65 кгссм2 поступает в конденсатор–холодильник воздушного охлаждения ХВ-1 а затем поступает на охлаждение в водяной холодильник Х-1 откуда с температурой 50-60оС и давлением 60-65 кгссм2 поступает в разделитель жидкости Е-1.
Для защиты от коррозии оборудования конденсатно-холодильного узла верхней части корпуса и тарелок колонны К-1 одновременно с процессом защелачивания нефти подается ингибитор коррозии в количестве 3-6 гтн бензина.
Несконденсировавшиеся углеводородные газы из сепаратора Е-1 направляются на секцию аминовой очистки газов (секция 500) или на факел.
Сепаратор Е-1 снабжен отстойной зоной.
Жидкая фаза углеводородов с сепаратора Е-1 насосом Н-4 направляется на 22-ю тарелку колонны К-1 в качестве орошения.
С 15-ой тарелки колонны К-1 при температуре 109оС и давлении 60-65 кгссм2 выводится боковой погон в отпарную колонну К-2. Обогрев низа колонны К-2 до 119оС осуществляется в подогревателе Т-8 отбензиненной нефтью (Т=271оС. Паровая фаза из отпарной (стриппинг) колонны К-2 возвращаются на 16-ю тарелку колонны К-1.
С низа подогревателя Т-8выводится компонент бензина (фр.НК-85оС) который охладившись в аппарате воздушного охлаждения ХВ-2 от 119оС до 45оС направляется на смешение с товарным бензином поступающим из секции 200 в товарный парк. При необходимости часть компонента бензина может подаваться в линию прямогонного бензина поступающего на гидроочистку (секция 300).
Температура 271оС в кубе колонны К-1 поддерживается за счет горячей струи нефти циркулирующей по схеме:
Циркулирующий поток нефти в печи П-1 нагревается до 265оС. Кубовый остаток – отбензиненная нефть из колонны К-1 с температурой 271оС насосом Н-3 подается по существующей схеме в печь П-2 на атмосферно-вакуумную разгонку для получения нефтепродуктов (бензина диз.топлива гудрона котельного топлива) по технологии фирмы «ПЕТРОФАК».
В печи П-2 отбензиненная нефть подогревается до температуры 335-355оС.
После печи П-2 нефть с температурой 335-355оС подается на 4-ую тарелку ректификационной колонны К-3. Для более полной отпарки легких углеводородов из нефти под 1-ую тарелку колонны подается пар давлением 42 кгссм2 перегретый до 345-360 0С в печи П-2.
Пары прямогонного бензина с температурой 130-145оС с верха колонны К-3 поступают в аппарат воздушного охлаждения ХВ-3 а затем на охлаждение в водяной теплообменник Х-2 где конденсируются и стекают в газосепаратор Е-2.
Несконденсировавшиеся в АВО ХВ-3 газы с температурой 25-40оС из емкости Е-2 отводятся:
-в линию топливного газа печей П-2 через отсекатель ;
-через трехходовой клапан или на факел.
Давление верха колонны К-3 должно быть в пределах 025-035 кгссм2. Газосепаратор Е-2 снабжен отстойной зоной.
Из емкости Е-2 бензин с температурой 25-40оС насосом Н-9 подается на орошение на 23-ю тарелку колонны К-3. Избыток бензина по уровню в емкости Е-2 насосом Н-9 откачивается в секцию гидроочистки бензина.
С 13-ой тарелки колонны К-3 отбирается фракция дизельного топлива с температурой 210-235оС куда поступает и фр. 180-285 отобранная с 16-й тарелки колонны К-3 насосом Н-10 и поступает в верхнюю часть отпарной колонны К-4.
Под 1-ую тарелку отпарной колонны К-4 подается пар давлением 42 кгссм2 перегретый до 345-360 0С. Под действием острого пара стекающий по тарелкам поток дизельного топлива отпаривается от легких углеводородов которые вместе с паром с верха колонны К-4 поступают на 14-ую тарелку колонны К-3.
Из куба отпарной колонны К-4 насосом Н-8 дизельное топливо с температурой 190-215оС прокачивается через трубное пространство теплообменника Т-2 где охлаждается до температуры 65-80оС за счет подогрева сырой нефти затем часть подается в секцию гидроочистки дизельного топлива а часть подается на смешение с дизельным топливом после секции гидроочистки дизельного топлива.
На глухой тарелке К-3 расположенной между 7 и 8 тарелками собирается атмосферный газойль с температурой 300-315оС. Для удаления из атмосферного газойля легких углеводородов под уровень жидкости на глухой тарелке подается пар давлением 42 кгссм2 перегретый до 345-360 0С.
Фракция 285-292 отводится с 15-й тарелки колонны К-3 и используется как компонент мазута флотского.
С глухой тарелки колонны К-3 атмосферный газойль откачивается насосом Н-6:
-Часть атмосферного газойля подается под глухую тарелку колонны К-3.
-Другая часть атмосферного газойля с глухой тарелки поступает в линию тяжелого вакуумного газойля через теплообменник Т-5 с температурой 160-165оС.
Кубовый продукт ректификационной колонны К-3 с температурой 340-345оС насосом Н-5 подается в теплообменники Т-1 Т-7 Т-6. После теплообменника Т-6 мазут смешивается с нефтью или используется как котельное топливо.
Принципиальная технологическая схема АТ приведена на рисунке 4.1.
Приложение А библиография.doc
Сарданашвили А.Г. Львова А.И. Примеры и задачи по технологии переработки нефти и газа-М.: Химия 1996-256 с.
Смидович Е.В. Технология переработки нефти и газа ч. 1-М.: Химия 1993-328 с.
Гариева Ф.Г. Караванов А.А. Снигирёв С.В Гаврилов В.И. Компьютерный расчёт процесса ректификации.- Учебное пособие-Казань 2006- 83 с.
Танатаров М.А. Ахметшина М.Н. и др. Технологические расчеты установок переработки нефти.- М.: Химия 1989-325 с.
Кузнецов А.А. Кагерманов С.М. Судаков Е.И. Расчеты процессов и аппаратов нефтеперерабатывающей промышленности. М.: Химия 1989-344 с.
Гусейнов ДА. Спектор Ш.Ш. Вайнер Л.З. Технологические расчеты процессов переработки нефти.-Л.: Машиностроение 1992-380 с.
Павлов К.Ф. Примеры и задачи по курсу процессов и аппаратов химической технологии К.Ф.Павлов П.Г.Романков А.А. Носков.- М.: Химия 1976. – 551 с.
Лащинский А.А. Конструирование сварных химических аппаратов. Справочник А.А. Лащинский.- М.: Машиностроение 1981. – 381 с.
Рабинович Г.Г Рябых П.М. Хохряков П.А.справочник Расчеты основных процессов переработки нефти. -М.: Химия1989-568 с.
Кошарский П.Д. Аналитические приборы регуляторы и вычислительные системы. Л.: Машиностроение1986-380 с.ю
Долин А.М. Основы техники безопасности в электроустановках –М.: энергия 1989-408 с.
Правила устройства электроустановокМинэрго СССР-62 изд. Переработанное и дополненное. –М.: Энергоиздат.
Пожарная опасность веществ и материалов применяемых веществ в химической промышленности.: Справочник Под ред. И.В. Рябова -М.: Химия1999-568 с.
Вредные вещества в промышленности.: Справочник Под ред. А.Н. Лазарева -М.: Химия 1996-590 с.
СНиП II-4-79 Естественное и искусственное освещение.
Кулиев В.П. Орлов Г.Г.: Охрана труда в нефтеперерабатывающей и в нефтехимической промышленности. -М.: Химия1993-380 с.
Средства защиты в машиностроении. Расчет и проектирование Под ред. С.В. Белова- М.: Машиностроение1999-380 с.
Экономическое обоснование дипломных и курсовых проектов: методические указания сост. В.И. Вольперт [и др.]; Казан. гос. технол. ун-т.– Казань 1996. – 53 с.
Методические указания по экономическому обоснованию проектов по специальностям. Сост. Н.В.Лыжина.: КГТУ-Казань 1998-102 с.
5 расчеты.doc
1 Расчет электродегидратора
Таблица 5.1 Материальный баланс электрообесоливания.
)Обезвоженная нефть в т.ч.
)Обессоленная нефть в т.ч.
Производительность по нефти составляет 545058 кг ч из таблицы 5.1 обводненность 2%.
В ходе расчета блока обессоливания определяют:
-критическую напряженность в межэлектродном пространстве
-температуру процесса обессоливания
-скорость осаждения дисперсной фазы
-производительность одного электродегидратора
-расчет числа электродегидраторов
Температура в аппарате 700С
Вязкость при этой температуре 911 сСт
Плотность нефти при температуре 700С 897 кгм3
Плотность воды 1150 кгм3
Плотность эмульсии при температуре 200С 927.61 кгм3
Давление в аппарате 65 атм.
Выбираем стандартный электродегидратор: объём аппарата V=150м3 длина L=12.2 м диаметр D=3.4м
Время пребывания эмульсии в аппарате
коэффициент межфазного натяжения мНм
диэлектрическая проницаемость эмульсии
коэффициент пропорциональности зависящий от обводненности эмульсии
Критическая напряженность в межэлектродном пространстве ( ) вычисляется по формуле:
Реальная напряженность поля ():
Плотность эмульсии ():
Найдем производительность (V) в м3ч
Температура процесса в электродегидраторе равна 70 0С и вязкость при этой температуре будет равна Па*с.
Скорость осаждения капель воды (Vо) находим по формуле Стокса:
где динамическая вязкость Па*с
Так как ввод потока в аппарат осуществляется через нижний коллектор тогда скорость движения потока снизу вверх (Vn) определяется по формуле:
D-диаметр аппарата м [5 с.18] (5.4)
Фактическая скорость движения (Uf) эмульсии мс:
Площадь горизонтального сечения (S) м2:
Производительность одного аппарата (Q) м3ч:
Найдем необходимое количество электродегидраторов (n):
Согласно расчетам принимаем 1 электродегидратор объемом 150м3 . На действующей установке производительностью 440000 тнгод имеется один электродегидратор объемом 150м3 .
2 Расчет колонны К-1
2.1 Расчет доли отгона на тарелке питания колонны К-1
Расчет колонны сводится к определению доли паровой и жидкой фаз получаемых в результате однократного испарения температуры верхней и кубовой частей рабочего числа тарелок и размеров аппарата. Поскольку колонна К-1 служит для отбензинивания нефти верхним ее продуктом является бензиновая фракция с пределами кипения нк - 1800С. Нижний продукт - отбензиненная нефть которая направляется в колонну К-3.
Исходные данные для расчета К-1:
- количество сырья F = 523024 кгч;
- давление в точке ввода сырья на 8-ой тарелке колонны S= 80 атм;
- температура ввода сырья Tp= 2390С.
Переводим состав нефти из % массовых в массовые доли по формуле
где ci - массовая доля каждого компонента нефти
xi – массовый состав каждого компонента в %мас.
Рассчитываем мольный состав компонентов нефти ci:
где Ci – мольная доля компонента нефти
ci - массовая доля каждого компонента нефти
Mi – молекулярная масса каждого компонента.
Расчёт давления насыщенных паров углеводородов производим по формуле:
Для расчета мольной доли отгона определяются давления насыщенных паров по формуле Ашворта и константы фазового равновесия компонентов:
где Po – давление насыщенных паров компонентоватм
Tp – температура однократного испарения К
Тk – температура кипения углеводородной фракции К.
Мольная доля отгона определяем по формуле:
Ki - константы фазового равновесия определяемые по зависимости
где Pi - парциальные давления компонентов
S – давление на тарелке питания атм
Мольную доля отгона определяем графически
Определённая мольная доля отгона в точке ввода сырья
Массовая доля отгона в точке ввода сырья emac0н = 014421
Определяем количество жидкого потока в кМоль ч
Определяем количество парового потока кМоль ч
Количество жидкого потока в месте ввода сырья кгч
Количество парового потока кгч
Подробный расчет приведен в приложении В.
В таблице 5.1 приведен состав нефти.
Таблица 5.1 – Состав нефти
Массовая концентрация
Продолжение таблицы 5.1
Расчёт тарелки бокового погона
Боковой погон направляется в стриппинг секцию колонну К-2
Давление в месте отбора т.е. с 15-ой тарелки S1 = 796 атм
Температура в месте отбора To=1200C
Мольный состав отгона cdtmi находим по формуле:
где Cdti – массовая концентрация
Температурная функция уравнения Ашворта XT1 рассчитывается по формуле:
Где: Т01 - температура на тарелке бокового отбора
Где: XT1 X21i – температурные функции.
Среднюю молекулярную массу Ms1 определяем по формуле:
Где: Cdti – массовый состав компонентов
Константы фазового равновесия определим по формуле:
Количество сырья в месте отбора в Кмольчас L1 = 14955465
Мольную долю отгона определим по формуле:
Определяем мольную долю отгона в месте вывода боковой фракции графичеки
Определяем массовую долю отгона
Количество жидкости в месте вывода кМольч
Количество паровой фазы кМольч
Количество жидкого потока кгч
Количество парового потока кгч
Общее количество бокового погона кгч
Расчёт стриппинг секции (колонны К-2)
Температура в стриппинге 1190С давление 788 атм
При этих параметрах определяем долю отгона в стриппинг секции по приведённой ранее методике.
Средняя молекулярная масса Ms2 = 512
Определённое значение мольной доли отгона графически
Уточнённое значение мольной доли отгона аналитически
Массовая доля отгона emac02 = 009463
Количество жидкого потока кМольч Lg2=1209
Количество парового потока кМольч Lo2 = 152
Определяем количество жидкого потока в стриппинг секции кгчас
Определяем количество парового потока возвращаемого в колоннукгчас
Общее количество потоков в стриппинг секциикгч R2+ N2 = 69647
Количество парового потока возвращаемое в колонну кгч 12368
Подробный расчет представлен в приложении В.
1.2Расчёт рефлюксной ёмкости Е-1
Давление в рефлюксной ёмкости принимаем Sv = 75 атм
Температуру в рефлюксной ёмкости принимаем Tv = 318К
Определяем среднюю молекулярную массу
Константы фазового равновесия
P3 i - давление паров углеводородов атм.
Определяем мольную долю отгона по формуле:
Мольную долю C3m i определяем графически.
Определённая мольная доля отгона
Определяем массовую долю отгона emac03 = 0075
Количество жидкого потока в сепараторе (рефлюксной ёмкости)
Газовая отдувка кгч 935
Согласно проведенным расчетам составляем материальный баланс колонны К-1 приведенный в таблице 5.2.
Таблица 5.2 – Материальный баланс колонны стабилизации К-1
1.3 Расчет минимального и рабочего флегмового числа
Определяем коэффициент относительной летучести компонентов по отношению к тяжёлому ключевому компоненту в точке ввода питания αsri по формуле:
где K2i K22 – константы фазового равновесия
Минимальное флегмовое число определяем графически по функциональной зависимости
где αsri - коэффициент относительной летучести компонентов по отношению к тяжёлому ключевому компоненту в точке ввода питания.
Определённое значение параметра f =134
Минимальное флегмовое число Rmin определяем по формуле:
Определённое значение минимального флегмового числа
Рабочее флегмовое число определяем по зависимости
Количество флегмы определяем по уравнению
Температуру в рефлюксной ёмкости определяем по функциональной зависимости графически:
где РК – давление конденсации компонентов в рефлюксной ёмкости;
Уi – содержание легколетучих компонентов в дистилляте колонны
ТЕ – температура в рефлюксной ёмкости.
Определённое значение РЕ = 805 ат
Давление верха с учётом гидравлических потерь принимаем РV = 79 ат
Температуру низа колонны определяем по функциональной зависимости
Где: PV – давление на верху колонны.
Определённое значение температуры верха колонны TV = 38604К.
Расчёт температуры низа колонны производим по функциональной зависимости:
Определённая температура низа колонны TN = 546К.
Расчёт числа тарелок колонны.
Минимальное количество тарелок в укрепляющей части колонны NminU определим по формуле:
где YLK – концентрация легкокипящего компонента (фр.170-1800С) в верхнем продукте
YTK– концентрация тяжелокипящего компонента (фр.180-1900С) в верхнем продукте
CTK CLK – концентрации тяжелокипящего и легкокипящего компонентов в сырье соответственно.
αsr1 – коэффициент относительной летучести легколетучих компонентов
αsr1 - коэффициент относительной летучести тяжелолетучих компонентов
Минимальное количество тарелок в отгонной части колонны NminO определим по формуле:
Определённое количество тарелок в отгонной части колонны NminO = 1201
Оптимальное количество тарелок NoptU принимаем по формуле:
Для клапанных тарелок коэффициент полезного действия принимаем по таблице 4 [3 c.42] = 035
Рабочее число тарелок определим по формуле:
NrabU = 13.71786NrabO = 8.14786
Общее количество рабочих тарелок Nтар :
Количество тарелок в колонне К-1на действующей установке – 23. Следовательно реконструкция не требуется.
Более полный расчет флегмового числа и числа тарелок приведен в приложении В.
1.4 Расчет диаметра колонны К-1
Диаметр колонны Du определяется по формуле:
где W – секундный объем паров м3с
u – линейная скорость движения паров мс.
Секундный объем паров W определяется по формуле:
Где: Dmol – количество паров уходящих с верха колонны кмольч
z – коэффициент сжимаемости (определяется в зависимости от температуры и давления)
Tkv – температура верха колонны;
Pkv – давление на верху колонны атм.
Определённое значение объёмной скорости м3сW = 014612
Линейная допустимая скорость движения паров принята по таблице
Таким образом при значениях линейной скорости движения паров
u = 01 мс и секундного объема паров V = 014612 м3с диаметр колонны
Диаметр действующей колонны - 1400 мм следовательно реконструкция колонны не требуется.
1.5 Расчет высоты колонны К-1
Высота колонны зависит от числа и типа тарелок в колонне а также от расстояния между ними. Фактическая высота колонны складывается из следующих величин:
где h1 – высота от верхнего днища до первой ректификационной тарелки мм:
h2 – высота укрепляющей части колонны мм:
где NY – число тарелок в укрепляющей части
r – расстояние между тарелками равное 500 мм.
h3 – высота отгонной части колоннымм:
где NX – число тарелок в отгонной части
h4 – высота места ввода сырья мм:
h5 – высота от нижней тарелки до зеркала жидкости в кубе колонны мм принимается по практическим данным 1000 мм.
h6 – высота от нижней тарелки до днища 2500 мм
h7 – высота зависящая от запаса остатка кубового продукта на 600с:
где Gn – количество кубового продукта необходимого для нормальной работы насоса в течении 600с кгс
Fk – площадь сечения колонны мм2.
Общая высота колонны H = 19.6 м.
Высота действующей колонны равна 19685 мм следовательно реконструкция колонны не требуется.
1.6 Расчет теплового баланса колонны
Для расчета теплового баланса колонны необходимо определить количество тепла выносимого из колонны отбензиненной нефтью парами бензина и флегмы а также вносимое в колонну сырьем и флегмой и определить количество тепла которое необходимо подвести «горячей струей». В тепловом балансе учитывается все количество тепла вносимого и выносимого из колонны потоками в паровом и жидком состоянии. Составляем тепловой баланс колонны и определяем количество тепла которое необходимо подвести «горячей струей»:
Количество компонентов участвующих в переносе тепла
Расход питания F = 52302.4 кгч
Расход флегмы F1 = 722.4 кгч
Раcход паровой фазы с верха колонны F2 = 1236.7 кгч
С паровой фазой со стриппинг секции F4 = 959.1кгч
С кубовой жидкостью F6 = 44759.9 кгч
С боковым погоном в стриппинг секцию F5 = 6964.7 кгч
Количество теплоты вносимое сырьём в колонну Q1 определяем по формуле:
Q1 = FJn (1- emas0н) + FJж emas0н
Где: Jn Jж – энтальпия паров и жидких углеводородов притемпературе ввода сырья Jж = 53927 кДжкг; Jп = 7981123 – энтальпия жидкой фазы при температуре ввода Температура ввода Т = 512 К приложение 2[5 с.328]
Определённы составляющие теплового баланса потерями тепла пренебрегаем.
Q6 = 2934445649 кДжQ2 = 1090970 кДж
Q3 = 9166871 кДж Q4 = 40047345 кДж
Рассчитанные значения энтальпий и тепловых эффектов приведены в таблице 5.3. Подробный расчет теплового баланса приведен в приложении В.
Таблица 5.3 – Расчетные параметры теплового баланса.
Стабильная нефть с куба
тепло в стрипинг секцию
Пар со стрипинг секции
Тепло с паром верха колонны
Необходимое количество тепла с горячей струёй
2 Расчет колонны К-3
2.1 Расчет доли отгона в точке ввода сырья
Доля отгона в атмосферной колонне рассчитываем при температуре 350оС в зоне питания колонны и при температуре 360оС в отгонной части колонны. Расчет будет производиться при давлении в точке ввода сырья т.е. на 4-ой тарелке Рк1 = 2.5 атм. Подробно вследствие аналогичности будет описываться второй режим как наиболее перспективный расчетные данные первого режима будут приводиться для сравнения.
Мольную долю отгона при выбранных условиях находим методом постепенного приближения для отгонной части колонны:
z – количество водяного пара кмоль ч;
L – количество сырья кмоль ч;
Рк – давление в колонне атм ;
е – мольная доля отгона.
Для этого пересчитываем массовые доли компонентов в мольные по формуле (5.3).
Константы фазового равновесия в точке ввода сырья находятся по формуле (5.6) и в отгонной части колонны по формуле:
где Pi - давление насыщенных паров компонентов атм
Pкol - давление в системе атм
Давления насыщенных паров рассчитываются по формуле 5.14.
Средние молекулярные масса по формуле (5.10)
жидкого потока кгч R = 24388.2
Масса парового потока Ym = 16783.1
Полный расчет доли отгона приведен в приложении Г.
2.2 Расчет составов жидкой и паровой фаз
Массовые составы жидкой и паровой фаз находятся по формулам (5.26) (5.27).
Состав продуктов указан в таблице 5.4
Таблица 5.4 - Состав продуктов
2.3 Расчет флегмового числа
Для определения минимального флегмового числа используется формула 5.18. Относительная летучесть определяется по формуле (5.29).
Минимальное флегмовое число Rmin = 1.2.
Рабочее флегмовое число определяется по формуле (5.30).
Определяем количество флегмы FL по формуле (5.31).
Число ректификационных тарелок в колонне в основном зависит от требуемой четкости ректификации; разности температур кипения разделяемых фракций; количества подаваемого в колонну орошения.
Основными методами расчета являются тарельчатый расчет аналитический и графический и все они дают примерно одинаковые результаты. В ходе расчета определяются минимальное число тарелок (Nmin). Для проведения расчета разбиваем колонну сверху вниз на 5 секций характеризующихся своей степенью разделения.
2.4 Расчет температуры верха колонны и вывода боковых фракций
При расчете температуры верха колонны необходимо учитывать количество водяного пара подаваемого вниз колонны. Температуру верха колонны и определяем методом постепенного приближения при помощи уравнения изотермы паровой фазы (5.37).
Константа фазового равновесия находится по формуле (5.38)
где pi – давление наверху колонны равное 22 атм.
Температуры вывода боковых фракций определяем методом постепенного приближения при помощи уравнения изотермы жидкой фазы( 5.39).
Данные необходимые для расчета температур верха колонны и вывода боковых фракций представлены в таблице 5.5.
Таблица 5.5 – Расчет парциального давления паров углеводородов
Молекулярная масса М кгкмоль
Парциальное давление Рb атм
Путем экстраполяции зависимости ΣXFi Кi где XFi – мольная доля компонента Кli – константа фазового равновесия компонента от температуры верха при Σ = 1 находим температуру верха колонны которая равна 119оС. (392К)
Температуру вывода боковых фракций задаем такой при которой изотерма жидкой фазы равняется единице.
Константа фазового равновесия находится по формуле:
Рb – парциальное давление углеводородов атм.
Парциальное давление углеводородов Pb находим по формуле:
где Nv – количество фракций проходящих через верх колонны кмольч
Npar – количество водяного пара проходящего через верх колонны кмольч
Pv – давление верха колонны атм.
Уравнение изотермы жидкого потока:
Где: X6i – мольный состав продукта
Температуры вывода боковых фракций равны:
Фр.292-360 - 325 оС.
Полный расчет температуры верха и температур вывода боковых фракций приведен в приложении Г.
2.5 Тепловой баланс колонны
Тепловой баланс колонны учитывает все тепло вносимое в колонну и выносимое из нее. Согласно закону сохранения энергии можно записать (без учета потерь тепла в окружающую среду):
Σ Qвх = Σ Qвых [ 4 с.70] (5.47)
Где: Qвх – количество тепла входящее в колонну кДжч;
Qвых – количество тепла выходящее из колонны кДжч.
Тепло вводимое в колонну:
с сырьем при температуре 239 оС
Энтальпию жидкой нефти определяем по формуле:
Где: d – плотность нефтяного потока
ρ – плотность исходного нефтяного потока при нормальных условиях
Энтальпию паровой фазы определяем по уравнению:
Количество вводимого тепла определяем по формуле
Qs = 42952849.7 кДжчас
Где: F – количество сырья кг ч;
еmac – массовая доля отгона;
p g – энтальпия сырья в паровом и жидком состоянии соответственно кДж кг; при температуре 239оС
Тепло вводимое с флегмой при температуре 40 оС
где FL – количество флегмы кг ч;
f – энтальпия флегмы кДж кг; if = 76.16
Qf = 353683.7 кДж чac
Тепло вносимое с перегретым водяным паром
Qpvp = W pvp [ 4 с. 71] (5.54)
где W – количество водяного пара кг ч;
pvp – энтальпия перегретого водяного пара кДж кг;
Потери тепла принимаются в количестве 5% от статьи приход кДжч
Тепло выводимое из колонны:
с верхним продуктом колонны
Энтальпия верхнего продукта:
Qv = 15420825 кДж чac
где D – количество дистиллята кг ч;D = 10728
v – энтальпия верхнего продукта кДж кг;
с боковыми погонами
Qb = G b [ 4 с. 71] (5.58)
Где: G – количество бокового погона кг ч;
b - энтальпия бокового погона кДж кг;
0-285 Qb1 = 5346473 кДж чac
5-292 Qb2 = 7278288 кДж чac
2-360 Qb4 = 21733857 кДж чac
Количество тепла выносимое насыщенным водяным паром
Qnvp = 670840 кДж чac
тепло выводимое с кубовым остатком определим по формуле
Qn= (Qs +Qpvp +Qf)- (Qv + Qp + Qb1 +Qb2+ Qb4) [ 4 с. 71] (5.59)
Количество кубового остатка кгч W = 27220.36
Qn = 36262104 кДж чac
Данные по расчёту материального баланса сводим в таблицу 5.6.
Таблица 5.6 – Расчетные параметры теплового баланса.
Тепло с верха колонны
С насыщенным водяным паром Qnbp
Потери в окружающее пространство 5% Qp
По формуле определяем критерий:
d = 0.9952ρn 0.00806
Критерий а определяем по формуле:
Температура низа колонны Т = 3450С
2.6 Расчёт числа тарелок в укрепляющей и отгонной частях колонны
Минимальное число тарелок в укрепляющей (выше точки ввода сырья) части колонны рассчитываем по формуле:
Где: YLK – концентрация ЛКК в верхнем продукте;
YTK - концентрация ТКК в верхнем продукте;
XLK - концентрация ЛКК в жидкой фазе;
XTK - концентрация ТКК в жидкой фазе;
aLK – коэффициент относительной летучести ЛКК;
aTK - коэффициент относительной летучести ТКК.
Коэффициент относительной летучести находится по формуле 5.20.
Рассчитываем количество тарелок в районах ввода сырья в колонну вывода фракций 185-285 285-292 285-360 и верхнего погона.
NminU = 5.506 NminO = 3.634
Оптимальное и рабочее число тарелок находим по формулам 5.25 5.26.
Коэффициент полезного действия тарелки с учетом износа принимаем равным 055.
Практическое число тарелок находится по формуле:
Найденное количество тарелок подходит т. к. в действующей колонне К-3 установлено 23 тарелок. Более полный расчет флегмового числа и числа тарелок приведен в приложении Г.
2.7 Расчет диаметра колонны К-3
Диаметр колонны dk определяется по формуле:
где V – секундный объем паров м3с
Секундный объем паров Vv определяется по формуле:
где D – количество паров уходящих с верха колонны кгч
rrab – рабочее флегмовое число;
Mmv – средняя молекулярная масса паров
Pk = 2.2 – давление на верху колонны атм.
Количество водяного пара подаваемого в колонну 881 кгч
Молекулярная масса воды m =18
Tkv – температура верха колонны
где Ym – количество паров в отгонной части колонны
Линейная скорость движения паров Uv рассчитывается по формуле:
где K – коэффициент зависящий от расстояния между тарелками и условий ректификации (для колонны отбензинивания равна 310)
ρav – абсолютная плотность жидкости кгм3
ρgv –плотность паров кгм3 которая находится по формуле:
Tkv = 1190С – температура верха
Р0 – атмосферное давление
Диметр колонны определяем отдельно для укрепляющей и отгонной части.
Диаметр действующей колонны равнен 1800 мм значит реконструкция не требуется.
2.8 Расчет высоты колонны К-3
r – расстояние между тарелками равное 500 мм
h4 – высота места ввода сырья мм [5 с.59]:
h5 – высота от нижней тарелки до зеркала жидкости в кубе колонны мм принимается по практическим данным 800 мм.
h6 – высота от нижней тарелки до днища 1500 мм
h7 – высота зависящая от запаса остатка кубового продукта на 600 с:
где Gn – количество кубового продукта необходимого для нормальной работы насоса в течении 600 с кгс
Общая высота колонны H = 19.47 м.
Высота действующей колонны равна 19500 мм значит ее реконструкция не требуется
3 Расчет теплообменного оборудования
3.1 Расчет теплообменника Т-8
Теплообменник служит для подогрева нефти перед входом в колонну К-1.
Расход нефти пред входом в колонну G1= 523024 кгчас
Второй поток – теплоноситель мазут из колонны К-3. Расход мазута
Нефть нагревается с температуры t1 =2150С до температуры t2 = 2390С
Мазут из колонны К -3 выходит с температурой t3 = 3450C
охлаждается до температуры t4 = 2500C. Нефть направляем в трубное пространство мазут в межтрубное.
Расчет тепловой нагрузки аппарата
Количество тепла отдаваемое мазутом кДжч
гдеilt1 ilt2 – энтальпия нефти (первого потока)
Среднелогарифмический температурный напор
где Δt= t3 – t1 – средняя температура потока нефти 0С
Δt = t4 - t2 - средняя температура потока мазута 0С .
Расчёт теплоёмкости нефти при средней температуре потока кДжкг
где t1cp = (t1+ t2)2
Теплопроводность нефти при средней температуре потока ВтмК
Критерий Рейнольдса для трубного пространства
где U – скорость нефти по трубному пространству мс
d – наружный диаметр трубы м
s - толщина стенок аппарата м
где ρ41 – плотность нефти
λ – теплопроводность нефти при средней температуре потока
Разность между средней температурой стенки потока и температурой потока
где tcten – средняя температура стенки.
где - коэффициент расширения нефти.
Расчёт теплоёмкости мазута при средней температуре потока:
где ρ151 – плотность нефти с температурной поправкой на плотность
Теплопроводность стенки при средней температуре потока λcten:
Критерии Нуссельта для трубного пространства
Коэффициент теплоотдачи:
Площадь сечения аппарата Fob определяем по формуле м2
Общая площадь сечения труб м2
Расчёт теплоёмкости мазута при средней температуре потока
Критерий Рейнольдса для межтрубного пространства
Критерий Нуссельта для межтрубного пространства
Коэффициент теплоотдачи для межтрубного пространства
где Deff – эффективный диаметр аппарата равный 0287 м2.
Коэффициент теплопередачи Втм2К
где λct – теплопроводность стали Втм2К
Необходимая площадь теплообмена м2
Площадь теплообмена выбранного аппарата м2
где L – длина труб м
N – количество труб.
Необходимое количество теплообменников
где F – необходимая площадь теплообмена м2
f – площадь теплообмена выбранного аппарата м2
Подробный расчет приведен в приложении Д.
К установке принимаем два горизонтально установленных теплообменника с поверхностью теплообмена F = 42 м2
Наружный диаметр аппарата D = 0.406 м
Трубки диаметром 9 * 216 * 6000 мм
Количество трубок n = 58
Полный расчёт теплообменника приведён в приложении Д.
Остальные теплообменники рассчитываются аналогичным методом. Спецификация теплообменного оборудования приведена в таблице 5.7.
Таблица 5.7 - Спецификация теплообменного оборудования
Расчётная поверхност
Техническая характеристика
Количество трубок 58
Количество трубок 204
Холодильник воздушный
Корпус 3550*4150*8340
Количество трубок 268
Электродвигатель ВАСО 30-14У1
Количество трубок 45
Корпус 321*2175*9000
Количество трубок 219
4Технологический расчёт печи П-2
Печь предназначена для нагрева перед входом в колонну К-3.
Производительность печи по нагреваемой нефти G = 487995кгчас.
Печь обогревается попутным нефтяным газом который состоит из метана этана пропана бутана углекислоты и азота.
Определяем состав топливного газа в мольных долях по формуле:
где cmi – массовый состав топливного газа %масс
MMi – молекулярная масса компонента кгмоль.
4.1Расчёт процесса горения
Низшую теплоту сгорания топлива определяем по формуле кДжкг:
где cm0cm1cm2cm3 – теплоемкость СН4С2Н6С3Н8С4Н10 соотв.
Теоретическое количество воздуха необходимое для сгорания газа определим по формуле кг возкг газа:
Коэффициент избытка воздуха принимаем α = 106
Действительное количество воздуха Ld кгкг (м3кг)
где L0 – теоретическое количество воздуха кг возд.кг сырья
Определим количество продуктов сгорания образующихся при сжигании 1 кг топлива кгкг по формуле:
где С Н N – количество атомов углерода водорода азота в данном компоненте топлива соотв.
Объёмное количество продуктов сгорания (в м3) на 1 кг топлива определяем по формуле:
Суммарный объём продуктов сгорания м3кг
Энтальпию дымовых газов определяем по графику кДжкг
Количество тепла переданного сырью в камере радиации кДжчас
где В – тепловой расход топлива кгч
Количество теплоты Вт
Низшая теплота сгорания топлива кДжкг: Qнp = 408313
Полезное тепло печи определяем по формуле:
Полную тепловую нагрузку печи определяем по формуле кДжкг:
Часовой расход топлива кгчас:
В = 658542 [5 c.159] (5.96)
4.2 Расчёт радиантной поверхности печи
Поверхность нагрева ридиантных труб определяем по формуле м2 :
Принимаем поверхность радиантных труб Нр = 144 м2
Рабочая длина радиантных труб Lp при наружном диаметре труб 159 мм м
Число радиантных труб Np определим по формуле:
По существующим нормам принимаем шаг размещения экранных (радиантных) труб S = 025 м
Тогда расстояние между вертикальными рядами радиантных труб S1:
По данным ВНИИНефтемаша расстояние от излучающих стен до трубного пучка должно быть от 06 м до 10 м принимаем это расстояние at = 1
В каждом вертикальном ряду экрана разместим по 17 труб. Тогда высота радиантной камеры (топки) составит при условии: расстояние от нижних и верхних труб вертикального ряда соответственно от пола и потолка печи
Объём камеры радиации определим по формуле:
Для обеспечения равномерного обогрева каждой трубы экрана по окружности и по длине принимаем для проектируемой печи газовые горелки типа ГБП2 теплопроизводительностью qg:
Количество горелок qv определим по формуле:
qv = 107.039 [5 c.162] (5.102)
Так как в действующей на установке печи 108 горелок - для каждой из излучающих стен топки по 54 горелки (9 горелок по длине излучающей стены и 6 горелок по высоте) то замена печи не требуется.
4.3 Расчёт конвективной поверхности печи
Количество тепла передаваемого сырью в конвективных трубах Qk кДжчас:
Перевод с кДЖ в кВт Qkв = 6470
Коэффициент теплоотдачи конвекцией от дымовых газов к трубам принимаем равной
α1 = 18 Втм2 К[5 c.169]
Коэффициент теплоотдачи излучением от трёх атомных газов к трубам принимаем равной
α2 = 12 Втм2 К[5 c.169]
Суммарный коэффициент теплопередачи определим по формуле Вт м2К:
Среднелогарифмический температурный напор: [5 c.169] (5.105)
Поверхность конвекционных труб Нк определим по формуле:
Принимаем поверхность конвекционных труб Нк = 131 м2
Полезная длина конвекционных труб при диаметре труб Lk = 6 м
Число конвективных труб Nk
Принимаем к установке 6 труб
4.4 Расчёт поверхности теплообмена паровых труб
Количества пара вводимого в колонну К- 3 определено в расчёте колонны
Количества тепла необходимого для подогрева пара Вт
Средняя разность температур на входе и выходе из камеры
Коэффициент теплоотдачи дымовых газов к перегретому пару Вт(м2К)
Поверхность теплоотдачи паровых труб Нп м2
Принимаем поверхность теплоотдачи паровых труб Нп = 101 м2
Стандартная длина труб диаметром 889 мм Lk = 6 м
Принимаем число паровых труб Nk = 6 труб.
Более подробный расчет представлен в приложении Е.
Реферат.docx
АТМОСФЕРНАЯ ТРУБЧАТКА КОЛОННА РАСЧЕТ.
Объектом проектирования является установка АТ ЕНПУ НГДУ «Елховнефть».
Цель проекта – провести проверочный расчет установки ЭЛОУ-АТ с увеличенной загрузкой по сырью 450000тнгод
В процессе проектирования произведен расчет установки ЭЛОУ-АТ.
Также была обоснована система контроля и регулирования основных параметров процесса.
В проекте разработаны мероприятия по охране труда технике безопасности и пожарной профилактике.
В экономическом расчете проекта была определена производственная себестоимость 1 тонны калькулируемой продукции которая составляет 46572 рубт.
Ген.план.dwg

Блок по по производству серы
Блок окисления битума
Блок гидроочиски дизельного топлива
Блок каталитического
Печной и реакторный блок
Установка перегонки нефти.
ТС с КИПом.A2x3 dwg.dwg

Наименование среды в трубопроводе
Легкий вакуумный газойль
Тяжелый вакуумный газойль
Установка перегонки нефти.
Схема общая комбинированная
Модули ввода аналоговые
Модули вывода аналоговые
Модули ввода дискретные
Модули вывода дискретные
Приборы и аппараты по месту
Панели аппаратуры и
Атм.колонна.dwg

Аппарат предназначен для ректификации нефти
Рабочее давление в аппарате - 0
Рабочая температура в аппарате - 240 °C
Характеристика рабочей среды - ЛВЖ
днище по ГОСТ 5520-79 - Сталь 09Г2С
Прибавка на коррозию - 2 мм
Тип контактных устройств - тарелки клапанные прямоточные
Технические требования
ным индикаторным покрытием по ОСТ 26-11-14-88;
валиком сварного шва - 1мм; 3) гидравлический с люминесцет-
дефектоскопию-шереховатость Ra=6
контроль: 1) радиационный метод по ГОСТ 7512-82; 2) цветную
Поверхность сварных швов и околошовных зон подготовить под
Контроль и оценку качества сварных швов производить согласно:
) ГОСТ 23055-78 класс чувствительности 2 ГОСТ 7512-82;
) для УЗД-согласно технологической инструкции 015725203010
Сварные швы испытать пневматическим давлением 0
Коэффициент прочности сварных швов 1
Габаритные размеры:
Схема расположения штуцеров
Класс герметичности по ОСТ 26-11-14-88 - 5 класс
Группа аппарата по ОСТ 26 291-94 - 1 группа
испытании и поставке аппарата должны
выполняться требования:
а) ГОСТ 12.2.003-74 " Оборудование производственное. Общие
требования безопасности
б) ОСТ 26-291-79 "Сосуды и аппараты стальные сварные.
Аппарат испытать на прочность и плотность гидравлически
) ультразвуковой метод по ОСТ 26-2044-83
Прокладки из паронита ПОН-1 ГОСТ 481-71
Не указанный вылет штуцеров - 150 мм
Производительность - 57200 кгч
Вывод дизельной фракции
Выход кубового продукта
Для регулятора уровня
Ввод паров из стрипинг колонны
Вывод атмосферного газойля
Ввод атмосферного газойля
Срок службы - 12 лет
Ввод дизельной фракций
Ввод перегретого водяного пара
Установка перегонки нефти.
Колонна атмосферная.
Тарелка клапанная.dwg

1_Патентная_проработка.doc
Предмет поиска: «Способы получения дизельного топлива».
Глубина поиска 10 лет.
Целью патентных исследований является установление уровня развития техники и анализ применимости прогрессивных решений в дипломном проекте.
Перечень и номера охранных документов имеющих отношение к теме приведены в таблице 1.1.
Таблица 1.1 – Список охранных документов
Номер охранных документов (11) или (21)
Дата публикации (43) или (46)
Страна выдачи патента (19)
Название изобретения (54)
Способ переработки нефтяного сырья
C10G35095 C10G4512 C10G4702 B01J29076 B01J2922 B01J2948 B01J2985 B01J2986 B01J2987 B01J2988
Способ переработки углеводородного сырья (варианты)
Способ получения зимнего дизельного топлива
Способ получения бензина и дизельного топлива (варианты)
Продолжение таблицы 1.1
Способ получения моторных топлив
Атмосферно-вакуумная установка получения топливных фракций из углеводородного сырья
Способ получения дизельного топлива
C10G700 C10G706 C10G3302 C10G6710 C10G5312
C10G700 C10G706 C10G3302 C10G6710
C10G900 C10G3302 C10G700 C10G1902
Способ получения дизельного и реактивного топлива
После предварительного ознакомления с сущностью изобретений для анализа выписывается краткая техническая характеристика отобранных изобретений.
(54) Способ переработки нефтяного сырья
(72) Хавкин В. А. Галиев Р. Г. Школьников В. М. Гуляева Л. А. Соляр Б. З. Капустин В. М. Шуверов В. М.
(57) Изобретение относится к области нефтепереработки в частности к способу переработки нефтяного сырья с получением дизельных топлив отвечающих современным требованиям уровня качества (Евро-4 и Евро-5). Предлагается способ переработки нефтяного сырья включающий стадии гидрогенизационного облагораживания нефтяного сырья и каталитического крекинга остатка полученного из продуктов гидрогенизационного облагораживания дизельный дистиллат стадии гидрогенизационного облагораживания смешивают с дизельным дистиллатом стадии каталитического крекинга и подвергают совместной гидроочистке в соотношении соответственно от 15:85 до 60:40% мас.
(51) C10G35095 C10G4512 C10G4702 B01J29076 B01J2922 B01J2948 B01J2985 B01J2986 B01J2987 B01J2988
(54) Способ переработки углеводородного сырья (варианты)
(72) Степанов В. Г. Пословина Л. П. Снытникова Г. П. Ионе К. Г.
(57) Группа изобретений относится к области нефтехимии - к способам переработки углеводородного сырья имеющего температуру конца кипения от 140 до 400 °С и предназначено для получения топливных фракций бензиновых керосиновых иили дизельных фракций при помощи твердых катализаторов. Первый вариант способа переработки углеводородного сырья осуществляют путем его контактирования при давлении 01-4 МПа температуре 250-500 °С и массовой скорости подачи сырья до 10 ч-1 с регенерируемым катализатором содержащим кристаллический силикат или цеолит со структурой ZSM-5 или ZSM-11 общей эмпирической формулы (002-035) Na_ 2 O·Эл_2 O_3 ·(27-300)SiO_2 ·kH_ 2 O где Эл - по меньшей мере один элемент из ряда Al Ga В Fe a k – соответствующий влагоемкости коэффициент или с катализатором содержащим силикат или цеолит указанного состава и по меньшей мере один элемент или соединение элемента I-VIII групп в количестве 001-100% мас. разделения продуктов контактирования после их охлаждения путем сепарации или ректификации на фракцию(и) углеводородных газов бензиновую керосиновую иили дизельную фракции регенерацию катализатора осуществляют кислородсодержащим газом при температуре 350-600 °С и давлении 01-4 МПа причем в качестве сырья используют углеводородные фракции выкипающие до 400°С и содержащие изопарафины и нафтены в суммарном количестве 54-581% мас. ароматические углеводороды - 84-127% мас. парафины и н-парафины - остальное до 100% мас. или в качестве сырья используют углеводородные фракции выкипающие до 400°С и выбранные из группы имеющей следующие интервалы выкипания фракций °С: 43-195 151-267 130-364 168-345 26-264 144-272. Второй вариант способа переработки углеводородного сырья в присутствии водорода при мольном отношении H_2углеводороды - 01-10 осуществляют путем его контактирования при избыточном давлении температуре 250-500 °С массовой скорости подачи сырья до 10 ч-1 с регенерируемым катализатором содержащим цеолит и возможно содержащим металлы или их соединения разделения продуктов контактирования после их охлаждения путем сепарации или ректификации на фракцию(и) углеводородных газов бензиновую керосиновую иили дизельную фракции регенерацию катализатора осуществляют кислородсодержащим газом при температуре 350-600 °С и давлении 01-6 МПа причем катализатор содержит цеолит со структурой ZSM-12 иили (бета) иили (омега) иили цеолит L (эль) или морденит иили кристаллический элементоалюмофосфат а также он содержит по меньшей мере один элемент иили соединение элемента I-VIII групп в количестве 005-200% мас. а в качестве сырья используют углеводородные фракции выкипающие до 400°С. Достигается увеличение гибкости процесса при расширении ассортимента используемого сырья и получаемых целевых продуктов.
(54) Способ получения зимнего дизельного топлива
(72) Котов С.В. Шабалина Т.Н. Шафранский Е.Л. Олтырев А.Г. Ясиненко В.А. Кривцов И.А. Новикова О.А.
(57) Изобретение относится к нефтепереработке в частности к способу переработки сернистых нефтей. Сущность: проводят ректификационное разделение сернистой нефти с получением фракций 96% которых выкипает в
пределах 140(280-290) 0С и 305(390-405) 0С. Фракцию 140(280-290) 0С подвергают гидроочистке и смешивают с фракцией 305(390-405) 0С в массовом соотношении от 75:25 до 95:5. В полученное базовое топливо вводят депрессорную присадку - сополимер этилена с винилацетатом с молекулярной массой 1000-500000 взятой в количестве 001-005% мас. Технический результат: повышение выхода топлива и улучшение его низкотемпературных свойств.
(51) C10G35095 C10G5902
(54) Способ получения бензина и дизельного топлива (варианты)
(72) Климов О.В. Аксенов Д.Г. Коденев Е.Г. Ечевский Г.В. Мегедь А.А. Корсаков С.Н. Тлехурай Г.Н.Аджиев А.Ю.Кильдяшев С.П.
(57) Использование: нефтепереработка и нефтехимия. Сущность: проводят превращение углеводородного сырья в присутствии пористого катализатора при температуре 250-500 °С давлении не более 25 МПа массовых расходах смеси углеводородов не более 10 ч-1 при этом в качестве исходного
сырья используют углеводородные дистилляты различного происхождения с концом кипения не выше 400 °С а в качестве катализатора используют различные цеолиты алюмосиликатного состава либо галлосиликаты галлоалюмосиликаты железосиликаты железоалюмосиликаты хромсиликаты
хромалюмосиликаты с введенными в структуру на стадии синтеза различными
элементами. Образовавшиеся в ходе реакции углеводороды C_1 -С_5 отделяют
от бензина и дизельного топлива в сепараторе и подают во второй реактор заполненный пористым катализатором в котором из этих углеводородов образуется концентрат ароматических углеводородов с суммарным содержанием ароматических соединений С_9 -С_9 не менее 95% мас. В других вариантах изобретения на выходе из второго реактора продукты разделяют на газ и высокооктановую фракцию которою смешивают либо с бензиновой фракцией выделенной из продуктов первого реактора либо с прямогонной бензиновой фракцией отогнанной от исходного сырья. Технический результат: увеличение среднего выхода жидких продуктов.
(51) C10L108 C10L118
(54) Дизельное топливо
(72) Булкатов А.Н. Капустин В.М. Митусова Т.Н. Мкртычев А.А. Ткачев И.И. Рудяк К.Б.
(57) Настоящее изобретение относится к области нефтепереработки и нефтехимии конкретно к дизельному топливу предназначенному для использования в быстроходных дизелях в зимних условиях и в условиях Крайнего Севера. Дизельное топливо содержит смесь прямогонной нефтяной фракции выкипающей в интервале 110-140 0С и прямогонной нефтяной фракции выкипающей в интервале 200-360 0С взятых в соотношении 2:1-6: 1 соответственно и сополимерную присадку. В качестве присадки дизельное топливо содержит сополимер этилена винилацетата и алкилметакрилата в количестве 0005-005% мас. Предлагаемое дизельное топливо обладает улучшенной стабильностью при длительном хранении в условиях низких температур.
(51) C10G6512 C10G6902
(54) Способ получения моторных топлив
(72) Демьяненко Е.А. Санников А.Л. Дружинин О.А. Твердохлебов В.П. Бирюков Ф.И. Хандархаев С.В. Каминский Э.Ф. Мелик-Ахназаров Талят Хосров оглы Лощенкова И.Н. Хавкин В.А. Гуляева Л.А. Бычкова Д.М.
(57) Изобретение относится к области нефтепереработки конкретно к способу получения моторных топлив а также тяжелых дистиллятов являющихся компонентами остаточных топлив и сырьем для каталитических процессов. Сущность: из сырья выделяют фракцию выкипающую в интервале температур 140-370 oС и фракцию выкипающую в интервале температур 250-500 oС которую затем подвергают двухстадийной гидрогенизационной переработке в присутствии катализатора до степени обессеривания на первой стадии 50-60% и степени деструкции сырья 5-10% и до степени обессеривания на второй стадии 90-95% и степени деструкции сырья 15-40% выделенную из гидрогенизата среднедистиллятную фракцию смешивают с фракцией 140-370 oС выделенной из исходного сырья в соотношении 40: 60-95: 5 соответственно. Предлагаемый способ позволяет получить моторные топлива соответствующие перспективным требования на дизельное топливо.
(51) C10G700 B01D300
(54) Атмосферно-вакуумная установка получения топливных фракций из углеводородного сырья
(72) Жвачкин С.А. Емешев В.Г. Соловьев В.А. Митяй С.С. Кириленко В.Н. Брулев С.О.
(57) Атмосферно-вакуумная установка получения топливных фракций из
углеводородного сырья относится к нефтепереработке получению моторных
топлив на малотоннажных установках из местных сырьевых ресурсов для покрытия потребности в нефтепродуктах потребителей прилегающих районов. Целью изобретения является создание эффективной экологически безопасной надежной и простой в эксплуатации установки получения топлива из углеводородного сырья благодаря исключению взрывопожароопасного огневого нагрева сырья в трубчатых печах и разделение сырья на топливные фракции в ректификационных колоннах. Новыми техническими решениями обеспечивающими требуемый запас качества по четкости разделения получаемых топливных фракций является интенсивное разделение диспергированного нагревом парожидкостного потока на криволинейной поверхности в центробежном поле фазового разделителя которое многократно превышает земное тяготение; ступенчатое длительное отпаривание жидкой фазы от низкокипящих углеводородов в испарителе перегретыми парами отбираемой фазы в течение 05-15 ч.
(51) C10G6914 C10G6514
(54) Способ получения дизельного топлива
(72) Курганов В.М. Мелик-Ахназаров Талят Хосров оглы Фалькевич Г.С. Хавкин В.А. Каминский Э.Ф. Гуляева Л.А. Виленский Л.М.
(57) Использование: нефтепереработка. Сущность: из нефтяного сырья выделяют фракции выкипающие в интервале (260-290 0С) - (340-370 0С) и (340-370 0С) - (530-560 0С) первую из которых подвергают каталитической гидродепарафинизации с последующей гидростабилизацией вторую - гидроочистке с последующим каталитическим гидрокрекингом полученные гидрогенизаты совместно подвергают ректификации с выделением ензиновой фракции легкой дизельной фракции тяжелой дизельной фракции а также остатка который возвращают в процесс и подвергают каталитическому гидрокрекингу совместно со второй фракцией. Технический способ позволяет получить компоненты низкозастывающего дизельного топлива (зимнего и арктического) которые могут после смешения непосредственно (или после введения депрессорной присадки) использоваться как товарные дизельные топлива.
(51) C10G700 C10G706 C10G3302 C10G6710 C10G5312
(72) Шевченко Н. С. Степанишин Ф. М.
(57) Изобретение относится к получению дизельного топлива из нефтей с различным содержанием серы. Нефть подвергают электрообессоливанию и обезвоживанию в электродегидраторах с системой сетчато или ячеисто расположенных электродов с последующей атмосферной или атмосферно-вакуумной перегонкой обессоленной нефти в колоннах атмосферной перегонки снабженных пакетами перекрестно-точных насадок размещенными с высотным или высотно-угловым смещением адекватно температурным зонам конденсации паров. При этом осуществляют вывод дизельной фракции с температурой кипения 240-350 °С или разделенной дизельной фракции 240-300 °С и 300-350 °С с последующим защелачиванием полученных дизельных фракций и их компаундированием с соответствующими фракциями. В качестве теплоносителя используют пар получаемый в парогенераторах путем нагрева воды за счет сжигания в последних газообразного или жидкого топлива. Образующийся конденсат по крайней мере частично рециркулирует в системе. Пар-теплоноситель по крайней мере частично получают при перегреве воды за счет сжигания содержащегося в нефти попутного газа иили газа образующегося за счет термодеструктивных процессов нефтепереработки. Газ подают в сеть с температурой 50-70 °С и давлением 3-5 кгсм2 подогревают его до температуры не ниже 100 °С и 60-85% подают на сжигание для получения пара в технологических процессах а 15-40% газа подают на сжигание в парогенератор. Нагретую химически очищенную сырую воду добавляют в количестве необходимом для возмещения потерь конденсата. Для подогрева сырой воды или исходной нефти используют также остаточную теплоту отработанного пара. В результате увеличивается глубина переработки нефти повышается выход дизельных фракций с высокими эксплуатационными показателями а также снижается расход пара-теплоносителя за счет рекуперации тепла парового конденсата и отводимых технологических потоков.
(51) C10G700 C10G706 C10G3302 C10G6710
(72) Шевченко Н. С. Соболев Б. К.
(57) Изобретение относится к нефтепереработке конкретно к получению
дизельного топлива. Дизельное топливо получают из малосернистых или сернистых или высокосернистых нефтей включая термические и термодеструктивные технологические процессы. Электрообессоливание и обезвоживание ведут путем пропускания потока нефти через систему сетчато или ячеисто расположенных электродов в электродегидраторах с различно ориентированной продольной осью корпуса. Далее способ включает атмосферную иили атмосферно-вакуумную перегонку обессоленной нефти гидроочистку дизельных фракций защелачивание части полученных дизельных
фракций с последующим компаундированием фракций. На указанных стадиях в
качестве теплоносителя используют пар получаемый в парогенераторе с образованием конденсата который по крайней мере частично возвращают на стадию получения пара. Используемый пар по крайней мере частично получают путем перегрева воды за счет сжигания содержащегося в нефти попутного газа иили газа термических процессов иили термодеструктивных процессов процессов нефтепереработки. Газ подают в сеть с температурой 50-70 0С и давлением 3-5 кгсм2 подогревают его до температуры не ниже 100 °С и 60-85% подают на сжигание для получения пара используемого в виде теплоносителя а 15-40% газа подают на сжигание в парогенератор для получения пара из возвратного парового конденсата в который добавляют нагретую химически очищенную сырую воду в необходимых количествах. Теплота от сжигания газа также используется для подогрева химически очищенной сырой воды иили исходной нефти. При этом рекуперируют остаточную теплоту отработанного в технологических процессах пара или парового конденсата. На стадии перегонки нефти предпочтительно используют ректификационные колонны оборудованные пакетами перекрестно-точных насадок а гидроочистку дизельного топлива проводят с использованием алюмокобальтовых или алюмомолибденовых катализаторов. Защелачивание полученных дизельных фракций ведут 3-5% мас. водным раствором едкого натра при объемном соотношении дизельная фракция: раствор едкого натра = 05-20. Предпочтительно проводят компаундирование дизельной фракции с прямогонной керосиновой фракцией или с прямогонными вакуумными соляровыми компонентами. В результате достигают повышение экономических показателей процесса улучшение экологии.
(72) Езунов И.С. Гебель Л.Г. Савинков А.К. Кузьмин В.Н. Селиванов Н.П.
(57) Изобретение относится к нефтепереработке в частности к способу получения дизельного топлива. Сущность изобретения состоит в электрообессоливании различных нефтей в электродегидраторе с системой электродов расположенных в двух уровнях при градиенте высоты между ними 005-01 условного отрезка пути совпадающего со средним вектором перемещения потока нефти в зоне наибольшего миделя. Поток нефти после обессоливания поступает в колонну атмосферной перегонки с пакетом насадок и двумя патрубками тангенциально расположенными в корпусе колонны. Колонна снабжена внутренним цилиндрическим отражателем потока диаметр которого соотносится с диаметром корпуса в зоне питания как (059-075) : 1 а высотный диапазон ввода потока нефти составляет 021 - 028 высоты колонны от низа днища. Вывод дизельной фракции 240 – 350 0С ведут в высотном интервале колонны составляющем 032 - 062 от низа днища. Полученную дизельную фракцию защелачивают 3 - 5% раствором NaOH в двух реакторах в две стадии. Первую стадию ведут инжектированием щелочи полученную смесь вводят в придонный слой NaOH и ведут вторую стадию с использованием маточника. Компаундирование дизельного топлива ведут в две стадии смешивания с прямогонными или гидроочищенными керосиновыми фракциями.
(51) C10G6900 C10G3302 C10G700 C10G1902
(54) Способ получения дизельного и реактивного топлива
(72) Селиванов В.Н. Селиванов С.Н. Баланюк А.А. Селиванов Н.П.
(57) Изобретение относится к нефтепереработке в частности к способу получения дизельного и реактивного топлива из нефти. Сущность изобретения состоит в электрообессоливании различных нефтей в электродегидраторе с системой электродов расположенных в двух уровнях при градиенте высоты между ними 005-01 условного отрезка пути совпадающего со средним вектором перемещения потока нефти в зоне наибольшего миделя при этом поток нефти после обессоливания поступает в колонну атмосферной перегонки с пакетом насадок и двумя патрубками тангенциально расположенными в корпусе колонны снабженной внутренним цилиндрическим отражателем потока диаметр которого соотносится с диаметром корпуса в зоне питания как (059-075):1 а высотный диапазон ввода потоков нефти составляет 021-028 высоты колонны от низа днища колонны причем вывод керосиновой фракции 140-240 °С ведут в высотном интервале колонны составляющем 058-081 считая от низа днища колонны а выделенную керосиновую фракцию делят на 3 потока третий поток в смеси с 30-35% мас. остаточной керосиновой фракции после вторичной перегонки бензина подают на гидроочистку и в полученный продукт вводят 0007-0008% мас. концентрата смеси присадок нафтеновых кислот и ионола при этом дизельную фракцию подают на блок защелачивания куда направляют также прямогонную керосиновую фракцию и целевое дизельное топливо получают компаундированием дизельной фракции отводимой из блока защелачивания и фракций отводимых с различных стадий процесса.
Патентные исследования показали что тема хорошо разработана. Пик активности приходится на 2009 год. В таблице представлены технические решения относящиеся к «способу» и «устройство» как объектам изобретений. Всего в таблице 12 изобретений. Внимание разработчиков к данной теме достаточно равномерно по годам. Однако в 2002 г. 2001 г. 2003г. 2004 г. подобные изобретения не обнаружены. Изобретения в основном касаются разработок по схеме атмосферной перегонки нефти.
Для анализа отобрано 3 изобретений имеющих отношение к исследуемой теме. Согласно сущности выбранных патентов в них разработаны способы повышения отбора дизельных фракций и получения дизельных топлив отвечающим современным стандартам.
Наиболее перспективным процессом для получения дизельных топлив из рассмотренных является изобретение 2205200 сущность заключается выделении из сырья фракции 140-370 0С и смешение ее с фракцией 250-500 0С после гидрогенизационного облагораживания.
Для дизельного топлива с улучшенной стабильностью в условиях низких температур является изобретения 2205201 смесь прямогонной фракций 110-140 0С и прямогонной фракций 200-360 0С с добавлением сополимерной присадки.
Более новым в техническом решении в получении топливных фракций является изобретения 2211853 благодаря исключения трубчатых печей и ректификационных колонн. Разделение происходит в центробежном поле фазового разделителя при помощи поступающего перегретого пара. Данный процесс экологический безопасный надежный и простой в эксплуатаций.
9.1 Затраты.doc
Расчет переменных и постоянных затрат представлен в таблице 9.9.
Таблица 9.9 – Расчет переменных и постоянных затрат на производство бензина
Годовая норма расхода
Вспомогательные материалы:
Зарплата осн. рабочих
Отчисления на социальное страхование ЕСН осн.
Продолжение таблицы 9.9
Амортизация зданий и сооружений
Амортизация оборудования
Отчисления на социальное страхование (ЕСН ИТР и МОП)
Расходы на содержание и эксплуатацию оборудования
зарплата всп. рабочих
отчисления на социальное страхование ЕСН всп.
Прочие расходы (1% от Σ п. 12345)
Аннотация.docx
Хазиахметова К.И. руководитель Фахрутдинов Р.З.
Спроектирован блок АТ предусмотрена деароматизация дизельного топлива путем отбора дополнительной фракции 285-292 в которой обнаружено повышенное содержание ароматических углеводородов. При этом рассчитанная себестоимость составляет 4657 руб.
6 Аналитический контроль технологического процесса.doc
Аналитический контроль технологического процесса приведены в таблице 6.1
Таблица 6.1 - Аналитический контроль технологического процесса
Наименование процесса
Контролируемые показатели
Методы контроля. Методика анализа ГОСТ или ОСТ
Трубопровод сырой нефти перед подачей воды
плотность при 200С кгм3
содержание серы % вес.
содержание солей мгл
содержание воды % об.
содержание механических примесей %
Трубопровод после ЭДГ
фракционный состав 0С
Компонент бензина фракции НК-85оС
Трубопровод после Т-8
плотность при 20 0С кгм3
диапазон температур кипения 0С
содержание серы % масс
Бензин после колонны К – 3 (прямогонный)
Трубопровод после Е-2
Продолжение таблицы
Дизельное топливо после колонны К – 3
Трубопровод после К – 4
температура вспышки в закрытом тигле 0С
содержание серы % вес
Трубопровод воды из Е-12
Трубопровод после Т-5
Рабочий раствор щелочи
Рабочий раствор ингибитора
Рабочий рас-твор аммиака
массовая доля серы %
температура застывания вспышки0C
плотность при 200C кгм3
по требованию в период вывода мазута в Е-41-4
2 Аналитический обзор.doc
Нефть представляет собой сложную жидкую смесь близко кипящих углеводородов и высокомолекулярных углеводородных соединений. В ней растворены газообразные (до 4 %) и твердые углеводороды. Углеводороды с числом атомов углерода от 1 до 4 т.е. метан этан пропан бутан и изобутан - газообразные углеводороды. Углеводороды С5 - С15 при нормальных условиях находятся в жидком состоянии. Углеводороды С16 - С34 и выше являются твердыми углеводородами они образуют парафины и церезины. Их содержание в нефти составляет до 5 % иногда до 12 %. В нефти содержатся также в небольших концентрациях не углеводородные соединения органические кислоты и некоторые другие вещества.
По химическому составу углеводороды нефти относятся к следующим классам соединений: парафиновые нафтеновые и ароматические. Ненасыщенных углеводородных соединений в нефти мало но они в большом количестве образуются при термической обработке нефти.
Парафиновые углеводороды нефти представлены соединениями как с неразветвлённой цепью (нормального строения) так и с разветвленной цепью (изостроения) например н-бутан и изобутан:
СН3 СН2 СН2 СН3 СН3 СН СН3
Парафиновых углеводородов нормального строения в нефти значительно больше чем углеводородов изостроения. Однако целью ряда процессов переработки нефти является получение именно изомеров поскольку их наличие значительно улучшает эксплуатационные характеристики топлива. Так с увеличением содержания углеводородов изостроения в автомобильных бензинах повышается их октановое число но с удалением парафинов снижается цетановое число поэтому оно должно быть оптимальным особенно для дизельных топлив.
Из нафтеновых углеводородов в качестве примера можно назвать циклопентан С5Н10 и циклогексан С6Н12.
Наличие нафтеновых углеводородов в реактивных и дизельных топливах положительно сказывается на их эксплуатационных свойствах. Нафтеновые углеводороды обладают большей термической стойкостью чем парафиновые; они менее склонны к нагарообразованию в двигателях чем ароматические углеводороды.
Ароматические углеводороды содержание которых в нефти незначительно образуются из нафтеновых углеводородов в процессе каталитического риформинга. Ароматические углеводороды входящие в состав бензинов также повышают их октановое число в то же самое время наличие их в дизельном топливе не желательно в связи с жесткими экологическими требованиями.
Кислород сера азот и хлор входят в состав нефти в виде отдельных соединений. Присутствие в нефти и топливах соединений серы нежелательно так как они приводят к коррозии аппаратов трубопроводов и двигателей а также являются ядом для катализаторов ряда процессов нефтепереработки. [2 с.23]
1.1 Электрообессоливание нефти
В нефти поступающей на установку содержание воды должно быть не более 05% солей - не более 40 мгл.
Содержащаяся в нефти вода с растворенными в ней солями преимущественно хлоридами является не только ненужной примесью но вызывает сильную коррозию оборудования и ухудшает качество топлив.
Растворенные в воде и находящиеся в нефти соли ведут себя по разному. Хлористый натрий почти не гидролизуется. Хлориды кальция и магния гидролизуются с образованием хлористого водорода даже при низкой температуре:
Для удаления солей вся нефть подвергается обессоливанию. С этой целью нефть интенсивно смешивается с пресной водой а образовавшаяся эмульсия воды в нефти разрушается и расслаивается в электрическом поле электродегидратора. Наиболее быстрое и полное разрушение нефтяных эмульсий достигается при подогреве нефти с применением эффективных реагентов - деэмульгаторов в нейтральной и слабощелочной среде регулируемой подачей щелочи. [2 с.45]
1.2 Процесс ректификации и ректификационные колонны
На производстве НГДУ «Елховнефть» разделение нефти на фракции осуществляется в атмосферной колонне.
Разделение нефти на фракции путем перегонки (дистилляции) основано на различии температур кипения ее компонентов. При нагревании компоненты с более низкой температурой кипения переходят в пары а компоненты с высокой температурой кипения остаются в жидкости. Пары после конденсации образуют дистиллят неиспарившаяся жидкость - остаток. Такой процесс называется простой перегонкой.
Для более четкого разделения сложной смеси каковой является нефть применяют перегонку с ректификацией. Процесс ректификации проводится в ректификационных колоннах при взаимодействии на тарелках двух встречных потоков: газового - снизу вверх и жидкостного - сверху вниз. В средней части колонны (зона эвапорации) вводится сырье. Выше ввода сырья находится концентрационная зона колонны а ниже - отгонная зона. С верха концентрационной части колонны получают продукт необходимой чистоты - ректификат а с низа отгонной части - остаток. Для работы ректификационной колонны необходимо чтобы с тарелки на тарелку непрерывно стекала орошающая жидкость - флегма. Она образуется за счет возвращения в колонну части готового продукта называемого орошением. Изменением подачи флегмы регулируется температура верха колонны тем самым определяется качество получаемого дистиллята.
При перегонке нефти в результате термического разложения сернистых соединений образуется сероводород который в сочетании с хлористым водородом является причиной сильной коррозии аппаратуры.
В присутствии воды и при повышенных температурах сероводород реагирует с металлом аппаратов образуя сернистое железо.
Для подавления хлористо-водородной коррозии аппаратуры АТ и отбензинивания нефти предусматривается подача 1%-го щелочного раствора и 1-2% содо-щелочной раствор в поток нефти перед подачей ее в колонну поз.К-1 1% раствора аммиачной воды 2-5%-го раствора ингибитора коррозии в шлемовые трубы колонн К-1 К-3.
Сульфиды выводятся с дренажной водой из рефлюксных емкостей Е-1 Е-2 колонн К-1 К-3 соответственно. [2 с.83]
2 Гидрооблагораживание топлив.
Для улучшения экологических показателей топлива развиваются методы гидрооблагораживания топлив. При этом снижаетя содержание прежде всего бензола в продуктах сгорания бензина ограничение на концентрацию которого сейчас ужесточается почти на порядок уменьшая дымность топлива а кроме того нафтены образующиеся при полном гидрировании ароматики являются желательными компонентами дизельных топлив повышая их цетановое число. Основные требования к ДТ приведены в таблице 2.1
Таблица 2.1 -- Основные требования к ДТ
Наименование основных показателей качества дизельного топлива
Содержание серы мгкг не более
Цетановое число не менее
Содержание полициклических ароматических углеводородов
Диаметр пятна износа мкм не более
Методы гидрооблагораживания топлив делятся на:
- химические (гидрогенизация)
- физические (избирательная очистка экстракция ректификация)
Гидрогенизация требует дополнительных затрат: требуются дополнительные реакторы источник Н2 процесс должен проходить при высоких температурах и давлении.
Процессы экстракционной деароматизации протекают при относительно
низких температуре и давлении и наряду с рафинатом – компонентом
дизельного топлива с пониженным содержанием аренов позволяют получать
экстракт - концентрат аренов который может быть использован в качестве
нефтехимического сырья.
Процессы экстракционной деароматизации бензиновых и масляных
фракций хорошо исследованы и успешно реализованы в промышленности. Для
разработки технологии экстракционной деароматизации дизельных фракций с
получением компонента экологически чистого дизельного топлива актуальным
и практически значимым является проведение работ по выбору эффективного
экстрагента и исследованию закономерностей процесса экстракционной
деароматизации дизельных фракций.
Экстракция связана с применением и дальнейшей экстракцией растворителя которая конечно связана с дополнительными капиталовложениями. [2 с.120]
Ректификация - наиболее простой метод. Можно выделять не только нежелательные ароматические углеводороды но и высокоплавкие парафиновые углеводороды.
3рекомендуемые к внедрению на установке АТ ЕНПУ с целью повышения качества дизельного топлива.
В настоящее время на установке АТ ЕНПУ принята установка с предварительным испарением (двукратное испарение) со стадией отбензинивания нефти.
Дизельное топливо выделяется в атмосферной колонне в виде бокового погона. Из этой же колонны предусмотрено выделение следующих фракций: 85-180 180- 285 285-292 292-360 360 - >.
В летнее время атмосферный газойль смешивается с дизельным топливом с получением товарного дизельного топлива.
В зимнее время атмосферный газойль используется как компонент котельного топлива.
В настоящий момент на установке не предусмотрены мероприятия по ограничению содержания ароматических углеводородов. В связи с введением новых стандартов в которых ограничивается содержание полициклических ароматических углеводородов необходимо предусмотреть меры по их снижению.
Приведенные выше патентные исследования и аналитический обзор указывают на необходимость удаления ароматики что связано с дополнительными затратами. Поэтому мы рекомендуем выделять из широкой дизельной фракции фракцию где концентрируются бициклические ароматические углеводороды. Анализ состава нефтей на ЕНПУ показал что бициклическая ароматика концентрируется в фракции 285-292.
Эта же фракция содержит парафины нормального строения таким образом выделение этой фракции позволит снизить температуру застывания дизельной фракции.
Возможное снижение цетанового числа из-за удаления высокоплавких парафинов будет компенсироваться удалением бициклической ароматики имеющей пониженное цетановое число.
В данном проекте предложена реконструкция атмосферной колонны К-3 позволяющей реализовать эти предложения.
9 экономика.doc
Елховский нефтепрерабатывающий завод НГДУ «Елховнефть» является основным нефтеперерабатывающим заводом в республике Татарстан. Расположенный на территории Кичуйского товарного парка завод перерабатывает Новоелховскую нефть добываемую нефтяниками НГДУ «Елховнефть».
Производительность установки по сырью 440 000 тг.
Товарный баланс установки АВТ приведен в таблице 9.1.
Таблица 9.1 – Товарный баланс установки (аналог)
Компонент ДТ 290-350
В т.ч. калькулируемая продукция
Материальный баланс установки АВТ приведен в таблице 9.2.
Таблица 9.2 – Материальный баланс установки (проект)
1 Расчет капитальных затрат на здания и сооружения
Расчет капитальных вложений состоит из расчета объема капитальных затрат на здания и сооружения которые приведены в таблице 9.3.
Таблица 9.3 – Расчет капитальных затрат на здания и сооружения
Амортизационные отчисления
здание насосной пенотушения
2 Расчет капитальных затрат и амортизационных отчислений на оборудование
Стоимость и амортизация оборудования по проекту приведены в таблице 9.4.
Таблица 9.4– Расчет капитальных затрат на оборудование по аналогу и по проекту
Наименование оборудования
Сметная стоимость руб
Колонна отбензинивания К-1
Колонна отпарная К-2К-4
Теплообменник Т-1 – Т-7
Электродегидратор ЭДГ
Колонна атмосферная К-3
Аппараты воздушного охлаждения
Неучтенное оборудование
Электросиловое оборудование
Сводная смета капитальных затрат и структура основных фондов по аналогу и проекту приведены в таблице 9.5.
Таблица 9.5 – Сводная смета капитальных затрат и основных фондов
Элементы основных фондов
3 Расчет численности и фонда заработной платы персонала
- производство непрерывное;
- длительность рабочей смены 8 часов;
- невыходы на работу предусмотрены;
- в балансе рабочего времени отпуск 24 дня прочие невыходы 8 дней.
Примерный баланс рабочего времени одного рабочего:
- календарный фонд рабочего времени 365 дней;
- выходных дней 91;
- праздничных дней 13;
- эффективный фонд рабочего времени составляет 233 дня;
- эффективный фонд рабочего времени 1864 часов.
Расчет годового фонда заработной платы основных рабочих приведена в таблице 9.6
Таблица 9.6 - Расчет годового фонда заработной платы основных и вспомогательных рабочих
Наименова-нии профессии
вая тариф-ная ставка
Годовой фонд заработ
Вспомогательные рабочие
Слесарь по ремонту КИП и А
Зтар = 50 4 1864 = 372800 руб.
Здоп=372800 033 = 123024 руб.
Зпр. = 372800 0.6 = 223680 руб.
Згод. = Зтар. + Здоп.+ Зпр = 372800 + 123024 + 223680 = 719504 руб.
Дополнительная заработная плата в размере 10% для основных рабочих :
Здоп. = Згод. 10% (9.1)
где Здоп. - дополнительная заработная плата в размере 10% руб;
Згод. - годовой фонд заработной платы основных рабочих руб.
Здоп.= 2647775 10% = 2647776 руб.
Фонд оплаты труда основных рабочих рассчитывается по формуле:
Фо.т = Згод. + Здоп. (9.2)
Ф о.т.= 2647775 + 264778 = 2912553 руб.
Дополнительная заработная плата в размере 10% для вспомогательных рабочих :
Здоп. = Згод. 10% (9.3)
Згод. - годовой фонд заработной платы вспомогательных рабочих руб.
Здоп.= 1801639 10% = 180164 руб.
Фонд оплаты труда вспомогательных рабочих рассчитывается по формуле:
Фо.т = Згод. + Здоп. (9.4)
Ф о.т.= 1801639 + 180164 = 1981803 руб.
Расчет численности и фонда заработной платы труда ИТР и МОП приведены в таблице 9.7.
Таблица 9.7 – Численность и оплата труда ИТР и МОП
Наименование должности
Оплата за месяц руб.
Годовой фонд оплаты труда руб.
Уборщик произв. помещении
4 Расчет среднегодовой заработной платы одного списочного рабочего и специалиста а также производительности труда
Среднегодовая заработная плата одного списочного рабочего рассчитывается по формуле:
Зср.год.= (Фо.т.осн + Фо.твсп ) ( rосн. + rосн). (9.5)
где Фо.т.осн – годовой фонд заработной платы основных рабочих руб.;
Фо.твсп - годовой фонд заработной платы вспомогательных рабочих руб.;
rосн. – численность основных рабочих чел.;
rосн..- численность вспомогательных рабочих чел.
Зср.год.= (2912 553 +1981 803) 16+12 = 174 798 руб.
Среднегодовая зарплата одного списочного работающего:
Зср.год.1= ( Фо.т.итр. + Фо.т.осн + Фо.твсп)( rосн.+ rвсп +rитр.) (9.6)
где Фо.т.итр. – годовой фонд заработной платы работающих руб.;
Фо.т.осн – годовой фонд заработной платы основных рабочих руб.;
rвсп.- численность вспомогательных рабочих чел.;
rитр. – численность работающих чел.
Зср.год.1= (1972 884+2912 553 +1981 803)16+12+10=180717 руб.
Производительность труда одного списочного рабочего:
где Вг – годовой объем тгод;
rосн. – численность основных рабочихчел.;
rвсп.- численность вспомогательных рабочих чел.
ПТосн. = 430 760 28 = 153843 тчел – по проекту и по аналогу.
ПТосн. = 440 550 28 = 157339 тчел – по проекту и по аналогу
Производительность труда одного списочного работающего:
где Вг – годовой объем м3;
rитр. – численность работающих чел.;
ПТитр = 430 760 38 = 113358 тчел – по проекту и по аналогу
ПТитр = 440 550 38 = 115934 тчел – по проекту и по аналогу
5 Расчет отчислений в социальный фонд
ЕСНосн. = 0.26 2912553= 757264 руб.
ЕСН.всп. = 0.26 1981803 = 515269 руб.
ЕСНитр. = 0.26 1972884 = 512950 руб.
6 Расчет годового расхода электроэнергии
Расчет годового расхода электроэнергии на двигательные цели представлен в таблице 9.8.
Таблица 9.8 – Расчет годового расхода электроэнергии при Тэф = 8160 ч.
Единичная мощность кВт
Суммарная мощность кВт
Потребность годовая кВтч
Расчет годового расхода электроэнергии на двигательные цели:
где Этеор. – потребность в электроэнергии;
Кспр. – коэффициент спроса;
Кэл.с. – коэффициент потерь в электрической цепи;
Кдв. – коэффициент потерь в двигателе.
Э = 3880080 08 098 085 = 3726 367 кВт. – по проекту и по аналогу
Себестоимость 1 тонны продукции определяется по формуле:
где Зат. - затраты руб.
V –объем готовой продукции т г
Сс – себестоимость 1 тонны продукции руб.т.
Сс = 2006514 691 430 760= 46581 руб.т.- по аналогу
Сс = 2006130 092440550= 45537руб.т – по проекту
Валовая прибыль рассчитывается по формуле:
ВП = (Ц – Сс)· V [19c.10] (9.11)
где Ц –отпускная цена руб.;
Сс – себестоимость 1 тонны продукции руб.т.;
V- объем готовой продукции тг.
Расчет ВП осуществляется по ДТ:
ВП = (11 000 – 46581) · 116 160= 736919 040 руб.- по аналогу
ВП = (13 000 –45537) · 115 280= 973689 464 руб.- по проекту
Чистая прибыль рассчитывается по формуле:
ЧП = ВП (1 -0.24) [19c.10] (9.12)
где ВП – валовая прибыль руб.;
ЧП – чистая прибыль руб.
ЧП = 736919040 (1 - 0.24) = 560058 470 руб. – по аналогу
ЧП = 973689 464 (1 - 0.24) = 740003993 руб.- по проекту
Рентабельность продаж по аналогу и проекту определяется по формуле:
где ВВ – валовая выручка (V*Ц) руб.;
ЧП – чистая прибыль руб.;
Рпр - рентабельность продаж %.
Рпр = (560058470 1277760 000) х 100 = 44% - по аналогу
Рпр = (740003 993 1498640000) х 100 = 49% - по проекту
Рентабельность продукции определяется по формуле:
Рпродукт = [19c.12] (9.14)
где Ц –отпускная ценаруб.;
Р продукт – рентабельность продукции%.
Рпродукт = (11 000 – 4656) 4656 х100 = 136% - по аналогу
Рпродукт = (13 000 - 4657) 4657 х100 = 179 % - по проекту
ОС- оборотные средства руб.
ОС = (2006130092 – 1440694 – 7408829) 7 365 = 38 304 – по аналогу и проекту руб.
Фондоотдача по аналогу и проекту определяется по формуле:
где ВВ - валовая выручка руб.;
КЗ- капитальные затраты руб.;
ФО – фондоотдача руб1руб.
ФО = 1277760000 116174210 = 11 руб.1руб - по аналогу
ФО = 1498640000 116174 210 = 129 руб.1руб - по проекту
Экономический эффект определяется по формуле:
Э = (ЧПп – ЧПа) – доп.кв. [19c.13] (9.17)
где ЧПп – чистая прибыль по проекту руб.;
ЧПа – чистая прибыль по аналогу руб..
доп.кв. дополнительные инвестиции руб.
Э = (730936068 - 560058 470) – 20000 = 170857 598 руб.
8 Технико-экономические показатели
Технико-экономические показатели представлены в таблице 9.10.
Таблица 9.10 – Технико-экономические показатели
Наименование показателя
Объем товарной продукции
в т.ч. в основные фонды
в оборотные средства
Среднегодовая зарплата:
Производительность труда (по ТП) :
Cебестоимость 1 тонны продукции
Валовая прибыль (по ДТ)
Чистая прибыль (по ДТ)
Рентабельность продаж
Экономическая эффективность
колонна.docx
1 Расчет колонны К-1
1.1 Расчет доли отгона на тарелке питания колонны К-1
Расчет колонны сводится к определению доли паровой и жидкой фаз получаемых в результате однократного испарения температуры верхней и кубовой частей рабочего числа тарелок и размеров аппарата. Поскольку колонна К-1 служит для отбензинивания нефти верхним ее продуктом является бензиновая фракция с пределами кипения нк - 1800С. Нижний продукт - отбензиненная нефть которая направляется в колонну К-3.
Исходные данные для расчета К-1:
- количество сырья F = 523024 кгч;
- давление в точке ввода сырья на 8-ой тарелке колонны S= 80 атм;
- температура ввода сырья Tp= 2390С.
Переводим состав нефти из % массовых в массовые доли по формуле
где ci - массовая доля каждого компонента нефти
xi – массовый состав каждого компонента в %мас.
Рассчитываем мольный состав компонентов нефти ci:
где Ci – мольная доля компонента нефти
ci - массовая доля каждого компонента нефти
Mi – молекулярная масса каждого компонента.
Расчёт давления насыщенных паров углеводородов производим по формуле:
Для расчета мольной доли отгона определяются давления насыщенных паров по формуле Ашворта и константы фазового равновесия компонентов:
где Po – давление насыщенных паров компонентоватм
Tp – температура однократного испарения К
Тk – температура кипения углеводородной фракции К.
Мольная доля отгона определяем по формуле:
Ki - константы фазового равновесия определяемые по зависимости
где Pi - парциальные давления компонентов
S – давление на тарелке питания атм
Мольную доля отгона определяем графически
Определённая мольная доля отгона в точке ввода сырья
Массовая доля отгона в точке ввода сырья emac0н = 014421
Определяем количество жидкого потока в кМоль ч
Определяем количество парового потока кМоль ч
Количество жидкого потока в месте ввода сырья кгч
Количество парового потока кгч
Подробный расчет приведен в приложении В.
В таблице 5.1 приведен состав нефти.
Таблица 5.1 – Состав нефти
Массовая концентрация
Продолжение таблицы 5.1
Расчёт тарелки бокового погона
Боковой погон направляется в стриппинг секцию колонну К-2
Давление в месте отбора т.е. с 15-ой тарелки S1 = 796 атм
Температура в месте отбора To=1200C
Мольный состав отгона cdtmi находим по формуле:
где Cdti – массовая концентрация
Температурная функция уравнения Ашворта XT1 рассчитывается по формуле:
Где: Т01 - температура на тарелке бокового отбора
Где: XT1 X21i – температурные функции.
Среднюю молекулярную массу Ms1 определяем по формуле:
Где: Cdti – массовый состав компонентов
Константы фазового равновесия определим по формуле:
Количество сырья в месте отбора в Кмольчас L1 = 14955465
Мольную долю отгона определим по формуле:
Определяем мольную долю отгона в месте вывода боковой фракции графичеки
Определяем массовую долю отгона
Количество жидкости в месте вывода кМольч
Количество паровой фазы кМольч
Количество жидкого потока кгч
Количество парового потока кгч
Общее количество бокового погона кгч
Расчёт стриппинг секции (колонны К-2)
Температура в стриппинге 1190С давление 788 атм
При этих параметрах определяем долю отгона в стриппинг секции по приведённой ранее методике.
Средняя молекулярная масса Ms2 = 512
Определённое значение мольной доли отгона графически
Уточнённое значение мольной доли отгона аналитически
Массовая доля отгона emac02 = 009463
Количество жидкого потока кМольч Lg2=1209
Количество парового потока кМольч Lo2 = 152
Определяем количество жидкого потока в стриппинг секции кгчас
Определяем количество парового потока возвращаемого в колоннукгчас
Общее количество потоков в стриппинг секциикгч R2+ N2 = 69647
Количество парового потока возвращаемое в колонну кгч 12368
Подробный расчет представлен в приложении В.
1.2Расчёт рефлюксной ёмкости Е-1
Давление в рефлюксной ёмкости принимаем Sv = 75 атм
Температуру в рефлюксной ёмкости принимаем Tv = 318К
Определяем среднюю молекулярную массу
Константы фазового равновесия
P3 i - давление паров углеводородов атм.
Определяем мольную долю отгона по формуле:
Мольную долю C3m i определяем графически.
Определённая мольная доля отгона
Определяем массовую долю отгона emac03 = 0075
Количество жидкого потока в сепараторе (рефлюксной ёмкости)
Газовая отдувка кгч 935
Согласно проведенным расчетам составляем материальный баланс колонны К-1 приведенный в таблице 5.2.
Таблица 5.2 – Материальный баланс колонны стабилизации К-1
1.3 Расчет минимального и рабочего флегмового числа
Определяем коэффициент относительной летучести компонентов по отношению к тяжёлому ключевому компоненту в точке ввода питания αsri по формуле:
где K2i K22 – константы фазового равновесия
Минимальное флегмовое число определяем графически по функциональной зависимости
где αsri - коэффициент относительной летучести компонентов по отношению к тяжёлому ключевому компоненту в точке ввода питания.
Определённое значение параметра f =134
Минимальное флегмовое число Rmin определяем по формуле:
Определённое значение минимального флегмового числа
Рабочее флегмовое число определяем по зависимости
Количество флегмы определяем по уравнению
Температуру в рефлюксной ёмкости определяем по функциональной зависимости графически:
где РК – давление конденсации компонентов в рефлюксной ёмкости;
Уi – содержание легколетучих компонентов в дистилляте колонны
ТЕ – температура в рефлюксной ёмкости.
Определённое значение РЕ = 805 ат
Давление верха с учётом гидравлических потерь принимаем РV = 79 ат
Температуру низа колонны определяем по функциональной зависимости
Где: PV – давление на верху колонны.
Определённое значение температуры верха колонны TV = 38604К.
Расчёт температуры низа колонны производим по функциональной зависимости:
Определённая температура низа колонны TN = 546К.
Расчёт числа тарелок колонны.
Минимальное количество тарелок в укрепляющей части колонны NminU определим по формуле:
где YLK – концентрация легкокипящего компонента (фр.170-1800С) в верхнем продукте
YTK– концентрация тяжелокипящего компонента (фр.180-1900С) в верхнем продукте
CTK CLK – концентрации тяжелокипящего и легкокипящего компонентов в сырье соответственно.
αsr1 – коэффициент относительной летучести легколетучих компонентов
αsr1 - коэффициент относительной летучести тяжелолетучих компонентов
Минимальное количество тарелок в отгонной части колонны NminO определим по формуле:
Определённое количество тарелок в отгонной части колонны NminO = 1201
Оптимальное количество тарелок NoptU принимаем по формуле:
Для клапанных тарелок коэффициент полезного действия принимаем по таблице 4 [3 c.42] = 035
Рабочее число тарелок определим по формуле:
NrabU = 13.71786NrabO = 8.14786
Общее количество рабочих тарелок Nтар :
Количество тарелок в колонне К-1на действующей установке – 23. Следовательно реконструкция не требуется.
Более полный расчет флегмового числа и числа тарелок приведен в приложении В.
1.4 Расчет диаметра колонны К-1
Диаметр колонны Du определяется по формуле:
где W – секундный объем паров м3с
u – линейная скорость движения паров мс.
Секундный объем паров W определяется по формуле:
Где: Dmol – количество паров уходящих с верха колонны кмольч
z – коэффициент сжимаемости (определяется в зависимости от температуры и давления)
Tkv – температура верха колонны;
Pkv – давление на верху колонны атм.
Определённое значение объёмной скорости м3сW = 014612
Линейная допустимая скорость движения паров принята по таблице
Таким образом при значениях линейной скорости движения паров
u = 01 мс и секундного объема паров V = 014612 м3с диаметр колонны
Диаметр действующей колонны - 1400 мм следовательно реконструкция колонны не требуется.
1.5 Расчет высоты колонны К-1
Высота колонны зависит от числа и типа тарелок в колонне а также от расстояния между ними. Фактическая высота колонны складывается из следующих величин:
где h1 – высота от верхнего днища до первой ректификационной тарелки мм:
h2 – высота укрепляющей части колонны мм:
где NY – число тарелок в укрепляющей части
r – расстояние между тарелками равное 500 мм.
h3 – высота отгонной части колоннымм:
где NX – число тарелок в отгонной части
h4 – высота места ввода сырья мм:
h5 – высота от нижней тарелки до зеркала жидкости в кубе колонны мм принимается по практическим данным 1000 мм.
h6 – высота от нижней тарелки до днища 2500 мм
h7 – высота зависящая от запаса остатка кубового продукта на 600с:
где Gn – количество кубового продукта необходимого для нормальной работы насоса в течении 600с кгс
Fk – площадь сечения колонны мм2.
Общая высота колонны H = 19.6 м.
Высота действующей колонны равна 19685 мм следовательно реконструкция колонны не требуется.
1.6 Расчет теплового баланса колонны
Для расчета теплового баланса колонны необходимо определить количество тепла выносимого из колонны отбензиненной нефтью парами бензина и флегмы а также вносимое в колонну сырьем и флегмой и определить количество тепла которое необходимо подвести «горячей струей». В тепловом балансе учитывается все количество тепла вносимого и выносимого из колонны потоками в паровом и жидком состоянии. Составляем тепловой баланс колонны и определяем количество тепла которое необходимо подвести «горячей струей»:
Количество компонентов участвующих в переносе тепла
Расход питания F = 52302.4 кгч
Расход флегмы F1 = 722.4 кгч
Раcход паровой фазы с верха колонны F2 = 1236.7 кгч
С паровой фазой со стриппинг секции F4 = 959.1кгч
С кубовой жидкостью F6 = 44759.9 кгч
С боковым погоном в стриппинг секцию F5 = 6964.7 кгч
Количество теплоты вносимое сырьём в колонну Q1 определяем по формуле:
Q1 = FJn (1- emas0н) + FJж emas0н
Где: Jn Jж – энтальпия паров и жидких углеводородов притемпературе ввода сырья Jж = 53927 кДжкг; Jп = 7981123 – энтальпия жидкой фазы при температуре ввода Температура ввода Т = 512 К приложение 2[5 с.328]
Определённы составляющие теплового баланса потерями тепла пренебрегаем.
Q6 = 2934445649 кДжQ2 = 1090970 кДж
Q3 = 9166871 кДж Q4 = 40047345 кДж
Рассчитанные значения энтальпий и тепловых эффектов приведены в таблице 5.3. Подробный расчет теплового баланса приведен в приложении В.
Таблица 5.3 – Расчетные параметры теплового баланса.
Стабильная нефть с куба
тепло в стрипинг секцию
Пар со стрипинг секции
Тепло с паром верха колонны
Необходимое количество тепла с горячей струёй
2 Расчет колонны К-3
2.1 Расчет доли отгона в точке ввода сырья
Доля отгона в атмосферной колонне рассчитываем при температуре 350оС в зоне питания колонны и при температуре 360оС в отгонной части колонны. Расчет будет производиться при давлении в точке ввода сырья т.е. на 4-ой тарелке Рк1 = 2.5 атм. Подробно вследствие аналогичности будет описываться второй режим как наиболее перспективный расчетные данные первого режима будут приводиться для сравнения.
Мольную долю отгона при выбранных условиях находим методом постепенного приближения для отгонной части колонны:
z – количество водяного пара кмоль ч;
L – количество сырья кмоль ч;
Рк – давление в колонне атм ;
е – мольная доля отгона.
Для этого пересчитываем массовые доли компонентов в мольные по формуле (5.3).
Константы фазового равновесия в точке ввода сырья находятся по формуле (5.6) и в отгонной части колонны по формуле:
где Pi - давление насыщенных паров компонентов атм
Pкol - давление в системе атм
Давления насыщенных паров рассчитываются по формуле 5.4.
Средние молекулярные масса по формуле (5.10)
жидкого потока кгч R = 24388.2
Масса парового потока Ym = 16783.1
Полный расчет доли отгона приведен в приложении Г.
2.2 Расчет составов жидкой и паровой фаз
Массовые составы жидкой и паровой фаз находятся по формулам (5.16) (5.17).
Состав продуктов указан в таблице 5.4
Таблица 5.4 - Состав продуктов
2.3 Расчет флегмового числа
Для определения минимального флегмового числа используется формула 5.18. Относительная летучесть определяется по формуле (5.19).
Минимальное флегмовое число Rmin = 1.2.
Рабочее флегмовое число определяется по формуле (5.20).
Определяем количество флегмы FL по формуле (5.21).
Число ректификационных тарелок в колонне в основном зависит от требуемой четкости ректификации; разности температур кипения разделяемых фракций; количества подаваемого в колонну орошения.
Основными методами расчета являются тарельчатый расчет аналитический и графический и все они дают примерно одинаковые результаты. В ходе расчета определяются минимальное число тарелок (Nmin). Для проведения расчета разбиваем колонну сверху вниз на 5 секций характеризующихся своей степенью разделения.
2.4 Расчет температуры верха колонны и вывода боковых фракций
При расчете температуры верха колонны необходимо учитывать количество водяного пара подаваемого вниз колонны. Температуру верха колонны и определяем методом постепенного приближения при помощи уравнения изотермы паровой фазы (5.27).
Константа фазового равновесия находится по формуле (5.28)
где pi – давление наверху колонны равное 22 атм.
Температуры вывода боковых фракций определяем методом постепенного приближения при помощи уравнения изотермы жидкой фазы( 5.29).
Данные необходимые для расчета температур верха колонны и вывода боковых фракций представлены в таблице 5.5.
Таблица 5.5 – Расчет парциального давления паров углеводородов
Молекулярная масса М кгкмоль
Парциальное давление Рb атм
Путем экстраполяции зависимости ΣXFi Кi где XFi – мольная доля компонента Кli – константа фазового равновесия компонента от температуры верха при Σ = 1 находим температуру верха колонны которая равна 119оС. (392К)
Температуру вывода боковых фракций задаем такой при которой изотерма жидкой фазы равняется единице.
Константа фазового равновесия находится по формуле:
Рb – парциальное давление углеводородов атм.
Парциальное давление углеводородов Pb находим по формуле:
где Nv – количество фракций проходящих через верх колонны кмольч
Npar – количество водяного пара проходящего через верх колонны кмольч
Pv – давление верха колонны атм.
Уравнение изотермы жидкого потока:
Где: X6i – мольный состав продукта
Температуры вывода боковых фракций равны:
Фр.292-360 - 325 оС.
Полный расчет температуры верха и температур вывода боковых фракций приведен в приложении Г.
2.5 Тепловой баланс колонны
Тепловой баланс колонны учитывает все тепло вносимое в колонну и выносимое из нее. Согласно закону сохранения энергии можно записать (без учета потерь тепла в окружающую среду):
Σ Qвх = Σ Qвых [ 4 с.70] (5.39)
Где: Qвх – количество тепла входящее в колонну кДжч;
Qвых – количество тепла выходящее из колонны кДжч.
Тепло вводимое в колонну:
с сырьем при температуре 239 оС
Энтальпию жидкой нефти определяем по формуле:
Где: d – плотность нефтяного потока
ρ – плотность исходного нефтяного потока при нормальных условиях
Энтальпию паровой фазы определяем по уравнению:
Количество вводимого тепла определяем по формуле
Qs = 42952849.7 кДжчас
Где: F – количество сырья кг ч;
еmac – массовая доля отгона;
p g – энтальпия сырья в паровом и жидком состоянии соответственно кДж кг; при температуре 239оС
Тепло вводимое с флегмой при температуре 40 оС
где FL – количество флегмы кг ч;
f – энтальпия флегмы кДж кг; if = 76.16
Qf = 353683.7 кДж чac
Тепло вносимое с перегретым водяным паром
Qpvp = W pvp [ 4 с. 71] (5.44)
где W – количество водяного пара кг ч;
pvp – энтальпия перегретого водяного пара кДж кг;
Потери тепла принимаются в количестве 5% от статьи приход кДжч
Тепло выводимое из колонны:
с верхним продуктом колонны
Энтальпия верхнего продукта:
Qv = 15420825 кДж чac
где D – количество дистиллята кг ч;D = 10728
v – энтальпия верхнего продукта кДж кг;
с боковыми погонами
Qb = G b [ 4 с. 71] (5.48)
Где: G – количество бокового погона кг ч;
b - энтальпия бокового погона кДж кг;
0-285 Qb1 = 5346473 кДж чac
5-292 Qb2 = 7278288 кДж чac
2-360 Qb4 = 21733857 кДж чac
Количество тепла выносимое насыщенным водяным паром
Qnvp = 670840 кДж чac
тепло выводимое с кубовым остатком определим по формуле
Qn= (Qs +Qpvp +Qf)- (Qv + Qp + Qb1 +Qb2+ Qb4)[ 4 с. 71] (5.49)
Количество кубового остатка кгч W = 27220.36
Qn = 36262104 кДж чac
Данные по расчёту материального баланса сводим в таблицу 5.6.
Таблица 5.6 – Расчетные параметры теплового баланса.
Тепло с верха колонны
С насыщенным водяным паром Qnbp
Потери в окружающее пространство 5% Qp
По формуле определяем критерий:
d = 0.9952ρn 0.00806
Критерий а определяем по формуле:
Температура низа колонны Т = 3450С
2.6 Расчёт числа тарелок в укрепляющей и отгонной частях колонны
Минимальное число тарелок в укрепляющей (выше точки ввода сырья) части колонны рассчитываем по формуле:
Где: YLK – концентрация ЛКК в верхнем продукте;
YTK - концентрация ТКК в верхнем продукте;
XLK - концентрация ЛКК в жидкой фазе;
XTK - концентрация ТКК в жидкой фазе;
aLK – коэффициент относительной летучести ЛКК;
aTK - коэффициент относительной летучести ТКК.
Коэффициент относительной летучести находится по формуле 6.20.
Рассчитываем количество тарелок в районах ввода сырья в колонну вывода фракций 185-285 285-292 285-360 и верхнего погона.
NminU = 5.506 NminO = 3.634
Оптимальное и рабочее число тарелок находим по формулам 5.25 5.26.
Коэффициент полезного действия тарелки с учетом износа принимаем равным 055.
Практическое число тарелок находится по формуле:
Найденное количество тарелок подходит т. к. в действующей колонне К-3 установлено 23 тарелок. Более полный расчет флегмового числа и числа тарелок приведен в приложении Г.
2.7 Расчет диаметра колонны К-3
Диаметр колонны dk определяется по формуле:
где V – секундный объем паров м3с
Секундный объем паров Vv определяется по формуле:
где D – количество паров уходящих с верха колонны кгч
rrab – рабочее флегмовое число;
Mmv – средняя молекулярная масса паров
Pk = 2.2 – давление на верху колонны атм.
Количество водяного пара подаваемого в колонну 881 кгч
Молекулярная масса воды m =18
Tkv – температура верха колонны
где Ym – количество паров в отгонной части колонны
Линейная скорость движения паров Uv рассчитывается по формуле:
где K – коэффициент зависящий от расстояния между тарелками и условий ректификации (для колонны отбензинивания равна 310)
ρav – абсолютная плотность жидкости кгм3
ρgv –плотность паров кгм3 которая находится по формуле:
Tkv = 1190С – температура верха
Р0 – атмосферное давление
Диметр колонны определяем отдельно для укрепляющей и отгонной части.
Диаметр действующей колонны равнен 1800 мм значит реконструкция не требуется.
2.8 Расчет высоты колонны К-3
r – расстояние между тарелками равное 500 мм
h4 – высота места ввода сырья мм [5 с.59]:
h5 – высота от нижней тарелки до зеркала жидкости в кубе колонны мм принимается по практическим данным 800 мм.
h6 – высота от нижней тарелки до днища 1500 мм
h7 – высота зависящая от запаса остатка кубового продукта на 600 с:
где Gn – количество кубового продукта необходимого для нормальной работы насоса в течении 600 с кгс
Общая высота колонны H = 19.47 м.
Высота действующей колонны равна 19500 мм значит ее реконструкция не требуется
Доклад.docx
Процессы перегонки нефти осуществляют на так называемых атмосферных трубчатых (АТ) и вакуумных трубчатых (ВТ) или атмосферно-вакуумных трубчатых (АВТ) установках.
На установках АТ осуществляют неглубокую перегонку нефти с получением топливных (бензиновых керосиновых дизельных) фракций и мазута.
В связи с ужесточением прежде всего экологических и технических требований к топливным фракциям должен меняться и подход к их выделению из нефти.
Топливные фракции полученные на этих установках перерабатывают с помощью сложных процессов включающих как правило гидрогенолиз то есть разложение с помощью Н2 в частности в литературе наблюдается именно такой подход в вопросах содержания серы t0 застывания и снижения содержания ароматики в особенности бициклических соединений.
В нашем проекте мы предлагаем более простой дешевый и технологически не сложный прием облагораживания дизельной фракции.
Технологическая схема.
Схема с предварительным отбензиниванием.
Сырая нефть с 02% воды и 2% соли отправляется на 8-ую тарелку колонны отбензинивания К-1.Паровая фаза колонны фракция НК-35 сконденсировавшись отводится в емкость Е-1.
Несконденсировавшиеся углеводородные газы из Е-1 направляются на секцию аминовой очистки газов. Жидкая фаза углеводородов с Е-1 направляется на 22-ю тарелку колонны К-1 в качестве орошения. С 15-ой тарелки колонны К-1 выводится боковой погон (35-85) в отпарную колонну К-2. Обогрев низа осуществляется в подогревателе Т-8 отбензиненной нефтью колонны К-2.
С низа подогревателя Т-8 выводится компонент бензина (фр.35-85оС) который охладившись в аппарате воздушного охлаждения направляется на смешение с товарным бензином.
Кубовый остаток – отбензиненная нефть из колонны К-1 с температурой 270оС подается по существующей схеме в печь П-2 на атмосферную разгонку для получения нефтепродуктов. В печи П-2 отбензиненная нефть подогревается до температуры 350 оС.
После печи П-2 нефть подается на 4-ую тарелку ректификационной колонны К-3. Из колонны К-3по аналогу отбирают следующие фракции: сверху – 85-180 2 боковые фракции: с 13-ой тарелки – дизельная фракция с глухой тарелки – фр. атмосферного газойля.
Мы-же отбираем дополнительную фракцию 285-292 в которой концентрируется бициклическая ароматика. эту фракцию в дальнейшем рекомендуем использовать как компонент мазута флотского. Для реализации этого проектом предусматриваются 2 дополнительные тарелки.
Пары прямогонного бензина с верха колонны К-3 конденсируются и стекают в газосепаратор Е-2. Несконденсировавшиеся в АВО газы из емкости Е-2 отводятся в линию топливного газа печей.
Из емкости Е-2 бензин подается на орошение на 23-ю тарелку колонны К-3.
С 16-ой тарелки колонны К-3 отбирается фракция 292-360 которая совместно с фракцией 180-285 отобранной с 13-ой тарелки поступает в верхнюю часть отпарной колонны К-4.
Фракция 285-292 отводится с 15-й тарелки колонны К-3 и используется как компонент мазута флотского.
Под 1-ую тарелку вниз отпарной колонны К-4 подается пар. Под действием острого пара стекающий по тарелкам поток дизельного топлива отпаривается от легких углеводородов которые вместе с паром с верха колонны К-4 поступают на 14-ую тарелку колонны К-3.
Из куба отпарной колонны К-4 дизельное топливо подается в секцию гидроочистки дизельного топлива а часть подается на смешение с дизельным топливом после секции гидроочистки дизельного топлива.
На глухой тарелке К-3 расположенной между 7 и 8 тарелками собирается атмосферный газойль. Часть атмосферного газойля подается под глухую тарелку колонны К-3. Другая часть атмосферного газойля с глухой тарелки поступает в линию тяжелого вакуумного газойля.
Колонна. На плакате 2 изображен основной аппарат - атмосферная колонна К 3. Диаметр колонны составляет 18 мм. Высота колонны составляет – 195 м. В колонне используется клапанные тарелки. Колонна снабжена штуцерами для ввода и вывода продуктов переработки штуцерами для монтажа приборов контроля и регулирования а также люк-лазами.
Печь. На плакате 4 изображена печь П-2. Поверхность теплообмена змеевиков: радиантного – 1446 м2 конвекционного – 131 м2 парового – 102 м2. Размеры труб змеевиков: радиантного - 1143*602 мм конвекционного - 1143*602 мм парового - 889*55 мм.
КиП и А. В данном проекте подобрана система контрольно-измерительных приборов и автоматизации «Старт».
Оборудование расположено в соответствии с нормами. Предусмотрены все меры по обеспечении безопасности обслуживающего персонала. Основной аппарат – колонна расположена на открытой площадке без навеса.
План расположения оборудования выполнен в соответствии с нормативными документами. Выдержаны расстояния между зданиями и сооружениями. Блок разделен на зоны каждая из которых доступна с разных сторон для свободного доступа техники и пожарных к месту возгорания. На установке предусмотрена автоматическая система сигнализации в случае загазованности. Предусмотрены средства пожаротушения используются пены распыленная вода хладоны порошки класса ВСЕ объемное тушение и флегматизация газовыми составами порошки вода для охлаждения оборудования. Обслуживающий персонал обеспечивается средствами индивидуальной и коллективной защиты в соответствии с нормативными требованиями.
Установка АТ относится к наружным установкам категории Бн.
Экономика. В проекте проведен расчет ТЭП представленных в таблице себестоимость одной тонны калькулируемой продукции составляет 4 657 рубт.
Спецификация4.doc
ДП. 2404.26.02.01.000
ДП. 2404.26.02.02.000
ДП. 2404.26.02.03.000
ДП. 2404.26.02.04.000
ДП. 2404.26.02.05.000
ДП. 2404.26.02.04.001
Крепление перегородки
ДП. 2404.26.02.04.002
ДП. 2404.26.02.04.003
Крепление листа тарелки
Шайба 12 ГОСТ11371-68
ДП. 2404.26.02.00.000.ВО
Атмосферная трубчатка
Атмосферная колонна
3 Характеристика сырья.docx
Характеристика сырья материалов полупродуктов и энергоресурсов представлена в таблице 3.1
Таблица 3.1 -- Характеристика сырья материалов полупродуктов и энергоресурсов
Наименование сырья материалов полупродуктов
Нормативно-техническая документация
Показатели по стандарту обязательные для проверки
Регламентируемые показатели
плотность при 20 0С кгм3 не более
содержание серы % вес. не более
содержание солей мгл не более
содержание воды % об. не более
содержание воды %об. не более
содержание С5 и выше % мас.не более
Компонент. бензина (фр.НК-85оС)
содержание С5 и выше не более
содержание С6 % мас. не более
Бензин после колонны К-3 (прямогонный)
плотность при 20 0С кгм3 не выше
диапазон температур кипения 0C
содержание серы % масс не более
Дизельное топливо после колонны К-4
плотность при 20 0C кгм3 не выше
% перегоняется при температуре 0C не выше
температура вспышки в закрытом тигле 0C не ниже
Атмосферный газойль (комп. мазута флотского)
плотность при 200C кгм3 не выше
температура вспышки в закрытом тигле 0C
Вода подтоварная с Е-12
содержание Fe мгм3 не более
плотность при 25 0С кгм3
плотность при 15 0С кгм3
Щелочной раствор NaOН
Концентрация % не более
Содощелочной раствор (Na2CO3+ NaOH в соотн. 3:1)
Готовая товарная продукция на секции:
Топочный мазут марки М-40 или М-100 (ГОСТ 10585 «Мазут»). Внешний вид: вязкая масса черного цвета.
Характеристика мазута приведена в таблице 3.2.
Таблица 3.2 -- Характеристика мазута
вязкость при 800C не более
масс. доля серы для высокосернистого % не более
содержание.docx
1.1 Электрообессоливание нефти
1.2 Процесс ректификации и ректификационные колонны
2 Гидрооблагораживание топлив
Характеристика сырья продуктов и материалов.
Описание технологического процесса
Технико-технологические расчеты
1 Расчет колонны К-1
1.1 Расчет доли отгона в колонне К-1
1.2 Расчет флегмового числа и числа тарелок
1.3 Расчет температуры верха колонны
1.4 Расчет температуры низа колонны
1.5 Расчет теплового баланса колонны
1.6 Расчет диаметра колонны К-1
1.7 Расчет высоты колонны К-1
2 Расчет колонны К-3
2.1 Расчет доли отгона в точке ввода сырья
2.2 Расчет составов жидкой и паровой фаз
2.3 Расчет флегмового числа
2.4 Расчет температуры верха колонны и вывода боковых фракций
2.5 Тепловой баланс колонны
2.6 Расчёт числа тарелок в укрепляющей и отгонной частях колонны
2.7 Расчет диаметра колонны К-3
3Расчет теплообменного оборудования
3.1 Расчет теплообменника Т-8
4Технологический расчёт печи П-2
4.1Расчёт процесса горения
4.2 Расчёт радиантной поверхности печи
4.3 Расчёт конвективной поверхности печи
4.4 Расчёт поверхности теплообмена паровых труб
Аналитический контроль производства
Контрольно-измерительные приборы и автоматизация производства
1 Цель и назначение автоматизации
2 Анализ статического и динамических характеристик объектов регулирования
3 Обоснование выбора приборов контроля и регулирования
4 Регулирование температуры
5 Регулирование давления
6 Регулирование уровня
7 Автоматический контроль производства
8 Измерение и регулирование расхода
9 Контроль и регулирование параметров в случае аварийных ситуации
10 Контроль выбросов в воздушный и водный бассейн
10.1 Технические данные
10.2 Лабораторный контроль
11 Спецификации приборов регулирования
Безопасность и экологичность проекта
1 Общая характеристика объекта
2 Основные физико-химические токсические взрыво- и пожароопасные характеристики веществ и материалов обращающихся в производстве.
3 Категорирование производственных помещений и наружных установок по взрывопожароопасности
4 Опасные и производственные факторы проектируемого объекта
5 Индивидуальные средства защиты
7 Вентиляция и отопление
8 Производственное освещение
10 Электробезопасность
11 Защита от статического электричества и молниезащита.
13 Пожарная профилактика и средства пожаротушения
Экономическое обоснование проекта
1 Расчет капитальных затрат на здания и сооружения
2 Расчет капитальных затрат и амортизационных отчислений на оборудование
3 Расчет численности и фонда заработной платы персонала
4 Расчет среднегодовой заработной платы одного списочного рабочего и специалиста а также производительности труда
5 Расчет отчислений в социальный фонд
6 Расчет годового расхода электроэнергии
7 Расчет себестоимости продукции
8 Технико-экономические показатели
Приложение А Библиография
Приложение Б Спецификация
1.doc
План расположения оборудования
Колонна атмосферная.
Установка перегонки нефти
Спецификация3.doc
Гайка М12 ГОСТ 5916-70
Шайба 12 ГОСТ 11371-68
Установка перегонки нефти.
2.doc
Емкость разделительная
Установка перегонки нефти.
Схема общая комбинированная
7 КИП и автоматизация.doc
1 Цель и назначение автоматизации
Автоматизация современного производства – это один из главных направлений совершенствования технологического процесса предприятий. При автоматизации повышается производительность труда улучшается качества продукции равномерно используется энергетические и сырьевые ресурсы.
Автоматизации позволяет повысить уровень условия труда обеспечить безопасность ведения работ сократить численность обслуживающего персонала.
Развитие автоматизации химической промышленности характеризуется мощностью скоростью и многообразием операции и оборудования. Управлением такими производствами возможно лишь при широком использовании методом и средств автоматизации.
Развитии автоматизации химической промышленности связано с вопросами взрыво- и пожароопасности перерабатывающего сырья агрессивностью и токсичностью продуктов полупродуктов необходимостью предотвращения вредных выбросов в окружающую среду.
Указанные особенности высокая чувствительность к нарушению технологического режима а так же необходимо своевременного и сопутствующего воздействия на процессе в случае отключения от заданных по регламенту условий не позволяет даже опытному оператору обеспечить качественного ведения процесса в ручную. Поэтому в настоящее время эксплуатация процессов переработки без автоматизации является немыслимо.
Основной целью автоматизации является безопасное ведения процесса при оптимальных условиях в связи с чем увеличивается эффективность производства.
2 Анализ статического и динамических характеристик объектов регулирования
Система автоматического регулирования процесса переработки нефтидинамическая система так как отключения регулируемого параметра изменяется во времени.
Основными факторами влияющими на качество нефти является температура давления в аппарате количество добываемой нефти и добавляемого в него деэмульгатора.
Объект регулирования давления характеризуется самовыравниванием. Если в какой-то момент времени в колонне повышалось давление в результате чего уменьшилось доля отгона легколетучих компонентов нефти то повышение давления произведет воздействие на регулирующий клапан который находится на трубопроводе выхода паровой фазы клапан открывается и давление понижается. В этом и заключается явление саморегулирования.
Объекты регулирования температуры и расхода деэмульгатора характеризуется запаздыванием то есть изменением регулируемого параметра начинается не одновременно с регулирующим воздействием а с запаздыванием на 05 часа.
3 Обоснование выбора приборов контроля и регулирования
При выборе приборов для контроля и регулирования параметров надо учитывать что:
-Прибор должен обеспечивать необходимое измерение должен быть достаточно быстродействие и надежным;
-Приборы установленные по методу и месту должны быть легкодоступными для наблюдения контроля и обслуживания.
Для контроля и регулирования применяют приборы системы ''Старт''. Они просты по устройству и надежны.
4 Регулирование температуры
Температура верха колонны измеряются термометром сопротивления с электрическим выходом сигнала. Этот сигнал во вторичном преобразованием типа ТП-ТП-68 где преобразуется в стандартный электрический сигнал затем в преобразователе ЭПП-63 преобразуется в пневматический показывающий сигнал поступает во вторичный пневматический показывающий прибор ПВ-10.17 который связан с регулятором системы ''Старт''. Сигнал от регулятора подается на клапан на орошения.
5 Регулирование давления
Производится также с помощью системы ''Старт'' состоящей из датчика сильфонного манометра МСП-2 вторичного прибора ПВ.10.1Э Пи-регулятора ПР3.31 и Регулирующего клапана 25ч. 30нж.
6 Регулирование уровня
Уровень регулируется в бензосепараторе и в колонне с помощью буйковых уровнемеров УБПВ прибора ПВ.10.1Э Пи-регулятора ПР.3.31 и регулирующего клапана 25ч. 30нж регулирующего рсход бензина и нефти.
Основные аппараты регулируемые параметры приведены в таблице 7.1.
Таблица 7.1 – Основные аппараты и регулируемые параметры
Характеристика автоматизированных процессов приведена в таблице 7.2.
Таблица 7.2 - Характеристика автоматизированных процессов
Величина параметра и размерность
7 Автоматический контроль производства
На НГДУ ''Елховнефть'' существует автоматический контроль за производством – это система программного обеспечение СН-1800.
Носитель рабочей программы является гибкий магнитный диск.
Программа работает в информационном режиме. Вся обработанная информация выдается на экран дисплея. Опрос технологических датчиков с аналоговыми сигналами производится через каждую минуту. Опрос датчиков с числоимпульсами сигналами производится через 2 минуты. Опрос декретными сигналами производится через 1 минуту.
К системе заложено 115 параметров из них 100-аналоговые 1-число-импульсный и 14-дискретные.
Однако при корректировке конфигураций системы любой параметр можно произвольно настраивать на нужный тип сигнала.
Функции вычислительного комплекса СН-1800:
-периодический съем сигналов с первичным датчиком
технологических параметров;
-обработка сигналов инфикация на экране дисплея текущих значений технологических параметров;
-сравнение полученных значений технологического параметра допустимыми границами;
-индикация установок технологических и аварийных параметров при выходе за предел границ а также индикация знака аварии (АН АВ) или выход за технологическую границу (ТНТВ) на экране дисплея. При этом АН – аварийная нижняя граница АВ – аварийная верхняя граница ТН(В) – технологическая нижняя (верхняя) граница;
-звуковая сигнализация при появлении аварийных параметров которая сопровождается после каждого опроса процессора до исчезновения аварийных параметров;
-выдача на печать один раз в смену номеров и значений параметров вышедших за аварийные границы а также их время выхода и входа в предел установок.
8 Измерение и регулирование расхода
Измерение и регулирование расхода осуществляется с помощью камерой диафрагмы ДК-80 ДК6-80 и дифманометра сильфоного ДС-П3 с выходным пневматическим унифицированным сигналом который поступает на вторичный пневматический показывающий и самопишущий прибор ПВ10.1Э и одновременно на пневморегулятор ПР3-31 выходной сигнал пневморегулятора поступает на регулирующий клапан 25ч.32нж установленный на трубопроводе подаче питающего раствора в колонну.
9 Контроль и регулирование параметров в случае аварийных ситуации
Все параметры процесса контролируется и регулируются системой ''Старт''. В производстве предусмотрена световая и звуковая сигнализация. В операторной при отключении датчиков параметра от заданного отключении вентиляционных систем загазованность в помещениях на линии подачи сырья в аппарат установлены системы автоматической блокировки защиты и сигнализации.
Все аппараты работающие под давлением имеют контролирующий манометр и предохранительный клапан ПМК-4 который срабатывают при повышении давлении на 15% выше рабочего. Для слива продуктов при повышении его уровня в аппаратах предусмотрены заглубленные аварийные емкости.
10 Контроль выбросов в воздушный и водный бассейн
Для контроля за выбросами существуют специальные сигнализаторы СТМ-10 СВК-3М1.
Сигнализатор СВК-3М1 представляет собой стационарно непрерывно действующий прибор предназначенный для автоматической сигнализации при наличии в воздухе закрытых помещений горючих газов относящихся по взрывоопасности к 123 категории группы А – четвертая категория по классификации ''Правел изготовления взрывозащитного оборудования'' издания 1993 года. Нормальная работа сигнализатора обеспечивается при температура от 5 до 50°С для блока датчика от 5 до 40°С для блока электропитания относительной влажности от 3 до 90°С при температуре 20°С атмосферном давлении от 008 до 00107МПа (от 600до 800мм.рт.ст.).
В анализируемой среде не должно быть агрессивных веществ являющихся ядами для катализаторов платиновой группы: хлор- серо- фосфор- цианосодержащих соединений и других в концентрациях превышающих санитарный номер. Содержание механических примесей в контролируемой среде и воздухе поступающим в датчик при контроле не должно быть более 0001гм2.
10.1 Технические данные
Сигнализируемые концентрации от нижнего предела взрываемости (НПВ):
-горючих газов паров и их смесей 30±25%(от 5 до 50)
-водородовоздушный смеси 125±75% (от 5 до 20)
Основная погрешность сигнализации:
-горючих газов паров и их смесей 19±24% НПВ при 30% НПВ;
-водородовоздушных смесей ±65% НПВ при 125% НПВ.
Инерционность сигнализатора не более 30с.
Потребление тока не более 02А.
Напряжение питания 220±23В.
Частота питания 50±1Гц.
Давление линии сжатого воздуха от 196до 580кПа (кгссм2).
Расход сжатого воздуха не более 150 nчас.
Температура анализируемой смеси на входе в прибор 50-150°С.
-блок электропитания не более 8кг;
-блок датчика не более 65кг;
Габаритные размеры не более:
-блока электропитания 332х160х275мм;
-блок датчиков 285х240х240мм
Сигнализатор СГМ-10 общетехнического применения предназначены для непрерывного контроля до взрывоопасных концентраций в воздухе помещений и открытых пространств горючих газов паров и их смесей.
Содержание механических агрессивных примесей в окружающий и контролируемой среде отравляющих каталитических активные элементы датчика не должно превышать санитарные нормы.
10.2 Лабораторный контроль
Контроль воздушной среды: приборы – переносные газоанализаторы трех типов: ПГФ-2м1 ЭТХ-1 УГ-2.
Углеводороды – применяются ЭТХ-1 ПГФ-2м1 а для бензола толуола аммиака Н2S – применяются УГ-2.
Отбор по графику: по технологической площадке – ежедневно а насосные – ежемесячно.
Анализ на содержания хлористых солей через каждый 4 часа методом титрования.
Содержание воды после электродегидратора через каждые 4 часа разгонкой на аппарате.
11 Спецификации приборов регулирования
Спецификация приборов и средства автоматизации представлена в таблице 7.3.
Заключение.docx
В ходе расчета проектируемого блока были рассчитаны:
- материальные балансы колонн
- тепловые балансы колонн с целью определения температуры выходящего из него потока
- основные размеры колонн
- рассчитан теплообменник и его размеры
- рассчитана печь процесс горения рассчитана радиантная и конвективная поверхность печи рассчитана поверхность теплообмена паровых труб .
Подобраны приборы автоматизации и регулирования основных параметров системы « Старт».
В проекте разработаны основные мероприятия по предупреждению и ликвидации аварийных ситуаций а также защита обслуживающего персонала.
8 Безопасность и экологичность проекта исправление1.doc
1 Общая характеристика объекта
Атмосферно-вакуумная трубчатка установка для первичной перегонки сырой нефти с получением нефтяных фракций.
Нагрев нефти топливных газов в печи П-1 до 360°С при температуре в печи 400°С и давлении Р=232кгссм2.
атмосферная перегонка в колонне К-1 при t=100-350°С и Р=012 МПа с получением фракции бензина дизельного топлива мазута.
Технологическое оборудование (колонны емкости печи) расположены на открытой площадке. Насосная операторная и компрессорная находятся в помещении двух этажного здания.
Колонна представляет собой вертикальный аппарат с аксиальным движением реакционного потока сверху вниз. Расчетная температура - 399 оС ; расчетное давление – 35 кгссм2 ; объем - 50 м3 ; диаметр - 1800 мм ;высота - 19500 мм.
Основное технологическое оборудование расположено на открытой площадке в помещении находятся насосная компрессорная и операторная.
Характеристика помещения операторной: длина – 18 м ширина – 8 м высота – 4 м.
Основные опасности производства.
-высокое давление в колоннах обуславливает возможности пропускание через не герметичности в арматуре фланцевых соединениях. В местах пропусков нефтепродуктов при высокой температуре а также при переливе продуктов из емкостей возможно возгорание и взрыв продуктов.
-при работе на высоких лестницах возможны падения людей.
-Возникновение искры и пламени нагретые поверхности электрооборудования могут стать источником воспламенения окружающей пожаро- и взрывоопасной среды.
-Вследствие разгерметизации вакуумной колонны возможно подсасывания воздуха и самопроизвольная эндотермическая реакция окисления и самовозгорания паров внутри колонны.
Отравление токсичными веществами (нефть нефтяной газ деэмульгатор ДиН-и бензин) в случае разгерметизации аппаратов.
В зависимости от мощности от условий технологического процесса характера и количества выделяемых в окружающую среду вредных веществ в соответствии с СанПиН 2.2.12.1.1.567-96 производство относится к 1 классу с шириной санитарно-защитной зоны 2000 м т.к. связано с переработкой нефти и нефтепродуктов.
Категорирование и классификация наружных установок и помещений приведена в таблице 8.1.
Таблица 8.1- Классификация наружных установок и помещений
Наименование помещений и наружных установок
Категорирование взрывоопасности по НПБ 105-03
Класс взрывоопасной зоны
Категория и группа взрывоопасной среды
Наружная установка (колонны емкости печи)
2 Основные физико-химические токсические взрыво- и пожароопасные характеристики веществ и материалов обращающихся в производстве.
Характеристика применяемых и получаемых веществ приведена в таблице 8.2.
Таблица 8.2 - Характеристика применяемых и получаемых веществ
Общая хар-ка (агрегат
Нефть (жидкость пар)
(парожидкостная смесь)
3 Категорирование производственных помещений и наружных установок по взрывопожароопасности
Наружные технологические установки по пожарной опасности категорируются в соответствии с НПБ 105-03 «Определение категорий помещений зданий и наружных установок по взрывопожарной и пожарной опасности».
Категория пожарной опасности наружных установок определяется исходя из вида находящихся в наружных установках горючих веществ и материалов их количества и пожароопасных свойств особенностей технологических процессов.
Расчет избыточного давления взрыва ΔР в зоне наружной установки производится по формуле:
r Р = Ро(08Мпр033r+3Mпр066r2+5Mпрr3) (8.1)
где Ро - атмосферное давление равное 101 кПа
r – расстояние от геометрического центра газопаровоздушного облака 30м
Мпр – приведенная масса пара или газа кг.
Мпр = Нт М z02210-3 кг (8.2)
где Нт - удельная теплота сгорания газа
М – масса жидкости поступившей в результате разгерметизации в окружающее пространство кг.
z – коэффициент участия горючего газа в горении z = 01.
Величина избыточного давления взрыва Р развиваемого при сгорании газопаровоздушных смесей составляет 1959 кПа что превышает 5 кПа и Твсп> 28 ºС следовательно согласно НПБ 105-03 наружная установка по пожарной опасности относится к категории Бн по ПУЭ-99 установка относится к классу В-1Г.
4 Опасные и производственные факторы проектируемого объекта
Технологический процесс осуществляется по непрерывной схеме полностью автоматизированный параметры процесса: Р-давление Т-температура L-уровень F-расход регулируются контролируются приборами системы «Старт»
Контролирование давления температуры уровня в колоннах К1 К2 осуществляется приборами системы «Старт». Приборами автомат. контроля регистрируют параметры технологического процесса и подают сигнал о их нарушениях.
Регулирование температуры в колонне-увеличенных осуществляется за счет расхода флегмы. (Температура падает подача флегмы увеличивается.
Регулирование уровня в колоннах осуществляется путем изменение отбора кубовой жидкости. (Уровень в колонне увеличивается в следствии этого отбор кубовой жидкости увеличивается)
Все оборудование герметично при изготовлении которого использовалась сталь марок ст.3 Х18 Н 10 Т.
Герметичность всех оборудований обеспечивается применением сварных аппаратов с малым числом разъемных деталей. Герметичность разъемных соединений обеспечивается применением прокладок из поронина фланцевых соединений- прокладок из асбеста.
На крышах ректификационных колонн для К1 Р=012 мПа для К2 Р=060 кПа устанавливаются предохранителные клапана пружинные которые срабатывают при Р крит. >Р раб. На 15%.
Предохранительный клапан сбрасывает продукт в закрытую емкость с последующим сжиганием на факеле.
При повышенной допустимого уровня емкости перелив происходит в аварийной емкости. При заполнении емкости больше 75-80% автоматически срабатывает сигнализация открывается клапана и перелив происходит в аварийной емкости.
Ректификационные колонны и емкости оборудованные стационарными площадками и лестницами; ширина площадок 15-40м высота перил- 1м уклон лестницы 45° ширина 1м шаг ступеней 025м их ширина 015м.
Термоизоляцию колонны производят матами из стекловолокна с последующим покрытием аллюминиевами листами.
Все запорные приспособления для аппаратов и трубопроводов (задвижки на трубопроводах для перекачки жидкости; краны на газотрубопроводах).
5 Индивидуальные средства защиты
Весь обслуживающий персонал обеспечивается индивидуальными средствами защиты [19 с.59]:
-спецодежда из хлопчатобумажной ткани костюм. В зимнее время ватные штаны телогрейки;
-обувь поГОСТ12.4103-83 – кожаные ботинки резиновые сапоги галоши а в зимнее время валенки на токопроводящей основе;
-для защиты рук – рукавицы хлопчатобумажные перчатки комбинированные резиновые перчатки;
-защитная фибровая каска с подшлемником;
-прорезиненные фартуки предназначены для защиты рабочих от нефти масел бензина и др.;
-фильтрующие противогазы марки БКФ(ГОСТ12.4.121-83) при работе по ремонту оборудования применяются шланговые противогазы ПШ-1 ПШ-2;
-защитные очки (ОЗО – открытые ОЗЗ – закрытые) маска из органического стекла щитки с прозрачным экраном;
-для защиты органов слуха от шума применяются противошумные наушники марки "А" [19 с.90].
В соответствии с ГОСТ 12.10005 – 88 выполняемые работы аппаратчика относятся к работам II а категории средней тяжести так как связаны с ходьбой перемещением и переноской мелких (до 1 кг) изделий или предметов в положении стоя или сидя и требующие определенного физического напряжения (энергозатраты одного человека от 151 до 200 ккалч или 175÷232 Вт).
В таблице 8.3 приведены параметры микроклимата воздуха рабочей зоны согласно СНиП2.04.05-91.
Таблица 8.3 – Оптимальные значения параметров микроклимата воздуха рабочей зоны по ГОСТ12.1.005-88
Относительная влажность %
Скорость движения мс
Допустимая на рабочих местах постоян-ных и непостоянных не более
Допустимая на рабочих местах постоянных и непостоянных
Средней тяжести- IIа
Для категории работ II а предусмотрены допустимые нормы температуры относительной влажности и скорости движения воздуха в рабочей зоне.
7 Вентиляция и отопление
Для обеспечения нормируемых параметров метеоусловий и снижение концентрации вредных веществ на складе реагентного хозяйства в операторной насосной и компрессорной предусмотрены естественная и искусственная вентиляция. Естественная вентиляция осуществляется через вентиляционные короба искусственная вентиляция – общеобменная приточно-вытежная.
В насосной и компрессорной предусмотрено аварийная вентиляция с восьмикратным воздухообменом совместно с рабочей которая приводится в действие автоматически когда концентрация углеводородного газа в воздухе на 20% меньше чем нижний концентрационный предел его воспламенения.[13 с.3]
Воздуховоды изготовлены из не искрящего и нержавеющего материала и заземлены.
Предусмотрены технологические разрывы между оборудованием для естественного проветривания и исключения застойных зон в которых могут скапливаться пары и газы.
В соответствии со СНиП2.04.05-91 предусмотрено воздушное отопление совмещенное с приточной вентиляцией.
8 Производственное освещение
Освещение является необходимым условием безопасного ведения технологического процесса. В операторной предусмотрено общее искусственное освещение и боковое.
В таблице 8.4 приведена характеристика освещения производственного помещения.
Таблица 8.4 - Характеристика освещения производственного помещения
Разряд зрительных работ
ЛБ-40 мощность 40 Вт
Для естественного освещения рассчитывается площадь световых проемов :
где S0 – площадь окон м2;
lН– нормированное значение КЕО = 15%
Н0 - световая характеристика окна = 115
КЗАП – коэффициент запаса = 12
t0– общий коэффициент светопропускания = 07
t1– коэффициент учитывающий отражение света от стен = 15
КЗД – коэффициент учитывающий затемнение окон противостоящим зданием = 1
Согласно расчетам S0 = 28м2. Предусматриваем площадь окон в операторной равной 28 м2
Для искусственного рассчитывается световой поток:
где К – коэффициент запаса учитывающий снижение освещенности ламп в процессе эксплуатации К=12;
Z – поправочный коэффициент светильника = 13;
h = 055 - коэффициент использования светового потока
Е –освещенность Е=200 лк.
Согласно расчетам F = 3120 лм.
Для искусственного освещения выбираем для операторной люминесцентные лампы типа ЛБ мощностью 40 Вт. (ЛБ-40) с световым потоком 3120 лм в количестве 32 штуки. В качестве светильников выбираем люминесцентные светильники прямого света типа ОДОР-80 с экранирующей решеткой в количестве 8.
Предусматривается аварийное освещение для обеспечения минимальной освещенности на случай внезапного отключения рабочего освещения. Источником питания служит аккумулятор. Норма аварийного освещения 5 % от рабочего.
Источником шума и вибрации на установке являются насосные вентиляционные системы печи компрессоры.
В соответствии с ГОСТ 12.1.003-88 уровень звукового давления не должен превышать 85дБ при частоте 1000Гц. [11 с.8]
Мероприятия по снижению шума:
- систематическая смазка трущихся частей оборудования;
- звукоизоляция приводов шумных машин кожухами;
- тщательная балансировка и центровка вращающихся частей при сборке;
- изолирование вентиляционных камер кирпичной стенкой в насосной и операторной.
- в помещении стены облицованы звукопоглощающих материалом-пористой штукатуркой;
-оборудование (колонны) устанавливающихся на массивный фундамент с малой амплитудой собственных колебаний.
Фундаменты под тяжелое оборудование вызывающее значительные вибрации делают заглубленные и изолируют со всех сторон войлоком асбестом.
-для уменьшения вибрации между вентилятором и его основанием устанавливаются виброизоляторы из резины.[12 с.3]
10 Электробезопасность
Согласно ПУЭ-99 по насосу опасности поражения электрическим током установка относится к классу - помещениям повышенной опасности. Наружная установка – к классу особой опасности. Она характеризуется наличием химически активной среды. Помещение операторной - без повышенной опасности т.к в нем отсутствуют условия создающие повышенную опасность или особую опасность. Безопасное напряжение для ручных светильников – 12В для переносных электроприемников номинальное напряжение – 36В.
В взрывоопасных зонах В–1а и В-1г электрооборудование взрывозащищенное с маркировкой 2ЕхdIIAT3.
Для защиты людей от поражения электрическим током предусмотрено защитное заземление R3=4Ом приводов насосов корпуса электроустановок оболочка кабелей корпуса трансформаторов.
Изоляция проводов выполнена из поливинилхлорида а сверху покрыт свинцовой оболочкой. Сопротивление изоляции не ниже 05106Ом. Для защиты от перегрузок и короткого замыкания устанавливается автомат.
11 Защита от статического электричества и молниезащита.
Заряды статического электричества образуются при движении нефти по трубопроводу при заполнении резервуаров. Согласно ГОСТ 12.10.18-79 установка относится к 3 классу электростатической искробезопасности - сильная электризация (объекты с заземленным электропроводным оборудованием где перерабатываются вещества и материалы с rv более 108Ом×м )
Для предотвращения накопления зарядов статического электричества предусмотрены следующие меры:
Заземления корпусов аппаратов не менее чем в двух трубопроводы находящихся на расстоянии 10см друг от друга через каждые 10-15м соединяются металлическими перемычками и заземляются.
Транспортировка жидкости со скоростью не более 10мс при d=50см.
Слив и налив жидких продуктов осуществляется так чтобы сливная труба опускалась на дно и струя стекала со скоростью 05-07мс.
Для защиты людей применяются: токопроводимый бетонный пол толщиной 3мм; обувь на токопроводящий подошве (резиновая с медными заклепками) спецодежда из хлопчатобумажной ткани ручной инструмент изготовлен из не искрящих материалов.
Согласно ПУЭ наружная установка имеет класс зоны В-Iг относится к зоне защиты Б и II категории молниезащиты. Ожидаемое число поражении молний в год рассчитывается по формуле:
где n =2 удельная плотность ударов молнии в землю
hx =195 м - высота аппарата м.
Ожидаемое количество поражений в год наружной установки не оборудованной молниезащитой по расчетным данным N=0.0215следовательно тип зоны защиты Б.
Установки отнесенные ко второй группе должны быть защищены от прямых ударов молний электростатической и электромагнитной индукции через наземные и подземные металлические коммуникации. Выбираем одиночный стержневой молниеотвод .Величина сопротивления заземлителя R3 зависит от удельного сопротивления грунта Rг. R3 = 5 – 50 Ом при Rг не менее 104 Ом·м.
Защита от прямых ударов молнии осуществляется при помощи стержневых молниеотводов установленных непосредственно на колонне. Для защиты от вторичных проявлений молнии (электростатической электромагнитной индукции) предусмотрено заземление металлических частей оборудования Rз=10 ом.
Зона защиты одиночного стержневого молониеотвода приведена на рисунке 8.1
-граница зоны защиты на уровне земли; 2- граница зоны защиты
Рисунок 8.1 – Зона защиты одиночного стержневого молониеотвода
Рассчитывается высота молниетвода Н:
H = (rx + 163hx)15 м (8.6)
hx = 195 м высота аппарата.
Н = 2239м - высота молниеотвода м
h0 = 2082м – высота зоны защиты над землей.
r0 = 3356м - радиус зоны защиты на уровне земли
Согласно расчету высота молниеотвода составляет 3356м.
13 Пожарная профилактика и средства пожаротушения
По степени пожароопасности производственные помещения относятся к пожаро-взрывоопасным категории Б. Здания двух этажное кирпичное с бетонными покрытиями. Степень огнестойкости здания II. Предел огнестойкости основных строительных конструкции:
-колонны стены – 2 часа;
-лестничные площадки – 1 час;
-наружные стены – 05 часа;
-перегородки – 025 часа;
-плиты и настилы – 075 часа;
-несущие конструкции – 025 часа;
Количество эвакуационных выходов два. Расстояние до эвакуационного выхода 75 м.
В воздуховодах и трубопроводах применяют огнепреградители В-3Г. Предусмотрены ЭПС с тепловыми извещателями в производственных помещениях АТМ-3 кнопочными на наружной установке типа ПКИП-9.
В целях недопущения пожаров и загорания в отделении предусмотрены следующие мероприятия:
-использованный обтирочный материал складываются в специальные металлические ящики расположенные за пределами помещения с последующей вывозкой за территорию объединения и уничтожением;
-для обогревания замёрзших трубопроводов и арматуры используются только пар и горячая вода.
Для тушения пожара применяется следующие средства.
-ящики с песком кошма лопата асбест;
-огнетушители пенные ОХП-10 ОХП – 15 и углекислотные ОУ – 2 ОУ – 8 расположенные в операторной насосной компрессорной.
-стационарные пенные установки ОВПС – 250 расположенные в насосной и компрессорной;
-внутренний пожарный кран расположен на высоте Н-135м от пола на лестничных клетках у входа в каридор.
На наружной установке:
-пожарные гидранты установлены на наружной водопроводной сети цеха с интервалом 8 – 100м;
-на верху колонны оросительные кольца;
-наружный пожарный водопровд.
Все средства пожаротушения располагаются в доступных безопасных местах. Класс пожара Б и С поэтому рекомендуемы средства тушения: распыленная вода пена порошки аэрозольные огнетушащие составы.
В зависимости от класса пожара применяется различные методы тушения пожара приведенные в таблице 8.5.
Таблица 8.5 - Класс пожара и средства его тушения
Класс пожара характеристика
Пены распыленная вода хладоны порошки класса ВСЕ
С при горении горючих газообразных веществ
Объемное тушение и флегматизация газовыми составами порошки вода для охлаждения оборудования
Твердые и жидкие отходы в производстве отсутствуют.
Нефтяной газ содержащий H2S и СО2 идет на сжигание на факел или на собственные нужды в печь нагрева нефти.
Вода от промывки и пропарки оборудования вода используемая в дефлегматоре для охлаждения реакционных паров стоки от атмосферных осадков и смыва полов поступают в очистные сооружения ЦКППН где проходят механическую обработку и возвращается в систему оборотного водоснабжения.
В целях защиты воздуха от загрязнения сброс нефтяного газа предусматривается через дренажную емкость на факел для зажигания.
Вентиляционные выбросы содержащие СО пыль удаляются в атмосферу на высоту 38м от конька к крышке
Спецификация_1.doc
Пояснительная записка
ДП 2404.26.00.00.000.С6
ДП. 2404.26.02.00.000.ВО
ДП. 2404.26.02.01.000.СБ
Атмосферная колонна
ДП. 2404.26.16.00.000.ВО
ДП. 2404.26.00.00.000.С7
ДП. 2404.26.00.00.000.ТП
Атмосферная трубчатка
Ведомость технологического проекта
Хамидуллин Р.Ф. Р.Ф.
Приложение Б – Спецификация на технический проект (Обязательное)
Порядок условных обозначений.doc
В дипломном проекте приняты следующие условные обозначения:
АТ- атмосферная трубчатка
10 Стандартизация.doc
ГОСТ 2.1-84 Описание производственной печати.
ГОСТ 2.793-79 Графические элементы и устройства машин
И аппаратов химического производства.
ГОСТ 12.4.103-83 Одежда специализированная защитная
Средства индивидуальной защиты рук и ног.
ГОСТ 12.1.011-78 Смеси взрывоопасные. Классификация и методы
ГОСТ 12.1.018-86 Пожарная безопасность. Электрическая
ГОСТ 3900-85 Нефтепродукты. Методы определения
ГОСТ 2084-77 Нефтепродукты. Методы определения
фракционного состава.
ГОСТ 1756-82 Нефтепродукты. Методы определения
давления насыщенных паров.
ГОСТ 33-82 Нефтепродукты. Методы определения
кинематической вязкости.
ГОСТ 6365-75 Нефтепродукты. Методы определения
температуры вспышки.
ГОСТ 5066-91 Нефтепродукты. Методы определения
температуры помутнения.
ГОСТ 20287-91 Нефтепродукты. Методы определения
температуры застывания.
ГОСТ 12.1.005-88 Общие санитарно технические требования
к воздуху рабочей зоны.
ГОСТ 12.2.020-76 Электрооборудование во взрывоопасных зонах.