Модернизация бурового оборудования (клин-отклонитель)




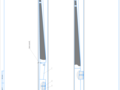
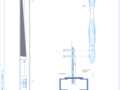
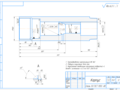
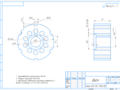
- Добавлен: 04.11.2022
- Размер: 3 MB
- Закачек: 4
Описание
Состав проекта
![]() |
![]() |
![]() ![]() ![]() |
![]() |
![]() ![]() ![]() ![]() |
![]() |
![]() ![]() ![]() ![]() |
![]() ![]() ![]() |
![]() |
![]() |
![]() |
![]() ![]() ![]() |
![]() |
![]() |
![]() |
![]() ![]() ![]() ![]() |
![]() ![]() ![]() |
![]() |
![]() ![]() ![]() |
![]() |
![]() ![]() ![]() |
![]() ![]() ![]() |
![]() |
![]() |
![]() ![]() ![]() |
![]() |
![]() ![]() ![]() |
![]() ![]() ![]() |
![]() |
![]() ![]() ![]() ![]() |
![]() |
![]() |
![]() ![]() ![]() |
![]() ![]() ![]() |
![]() ![]() ![]() |
![]() ![]() ![]() |
![]() ![]() ![]() |
![]() ![]() ![]() |
![]() ![]() ![]() |
![]() ![]() ![]() |
![]() ![]() ![]() |
![]() ![]() ![]() |
Дополнительная информация
Введение.docx
Один из методов повышения нефтеотдачи месторождений получивший повсеместное распространение это восстановление старого фонда скважин путём бурения боковых стволов из обсадных колонн.
Его «привлекательность» во многом определяется простой и эффективной операцией «зарезки» бокового ствола базирующейся на использовании клина-отклонителя.
При правильной ориентации отклоняющей плоскости клина и направления действия отклонителя (НДО) перфорация «окна» в обсадной колонне и последующая «зарезка» бокового ствола будет производиться в проектном направлении. Именно это обстоятельство во многом определяет эффективность клина-отклонителя и его популярность у буровиков.
Поскольку клин-отклонитель устанавливается внутри обсадной колонны для его ориентации обычно используется гироскопический инклинометр.
Вместе с тем простота методики ориентирования клина и «прозрачность» этой операции для всестороннего контроля позволяет уверенно предположить что неконтролируемое изменение азимута происходит не в процессе ориентирования а на последующих этапах при неконтролируемом (т.е. в отсутствии измерительных средств) углублении ствола скважины.
Тем не менее поскольку ориентирование является всё же основополагающим этапом обеспечивающим «попадание» ствола скважины в заданное направление всестороннее изучение дополнительных факторов влияние которых может сказаться на результатах ориентирования представляется важным и актуальным.
Использование предложенных в дипломном проекте решений на месторождениях западносибирского региона несет реальную прибыль предприятиям нефтяной отрасли.
88.cdw

44.cdw

55.cdw

Неуказанные фаски в дет. ВЧ 2х45
111.cdw
Схема сборки и компоновки
Монтажная схема сборки ОКС и КФРМ
99.cdw
клина-отклонителя (состояние
Положение клина-отклонителя
подготовленного к спуску
Схема транспортировки
и подготовки к спуску
3. 3 лист. Диск.cdw
Радиусы скруглений 16мм max
Неуказанные предельные отклонения отверстий +t
остальных +t2 по ГОСТ 25670-83
Сталь 50Л ГОСТ 1050-80
3. 3 лист. Корпус.cdw
Радиусы скруглений 16мм max
Неуказанные предельные отклонения отверстий +t
остальных +t2 по ГОСТ 25670-83
Сталь 50 ГОСТ 1050 -80
3. 3 лист. Шток.cdw

радиусы скруглений 16мм max
Неуказанные предельные отклонения отверстий +t
остальных +t2 по ГОСТ 25670-83
Сталь 50 ГОСТ 1050-80
77.cdw
Остальные технические требования по ГОСТ 7360-75.
Раздел 5.docx
1 Общие требования безопасности
К физическим факторам действующим на территории предприятия можно отнести: ударные волны и осколочные поля возникающие вследствие взрывов скопившегося газа; тепловые и световые излучения в результате возгорания горючих жидкостей в емкостях технологических аппаратах; электрический ток высокого напряжения на трансформаторах и на приводах силовых установок; движущиеся машины и механизмы подъемного оборудования; виброакустические факторы – шум вибрация – источниками являются электродвигатели компрессоры ударные процессы и т.д.
Действие вредных веществ применяемые вспомогательные материалы нефть и ее фракции а также предельные углеводородные газы сероводород. В бурения скважин промышленно – производственный персонал низшего производственного звена – бурильщики и помощники бурильщиков подвергаются воздействию неблагоприятных метеорологических условий выделяющихся в атмосферу легких фракций газов. Такое загрязнение воздушной среды может привести к интоксикации организма.
Физические и нервно - психические перегрузки человеческого организма напряжения отдельных органов нерациональная рабочая поза неблагоприятные условия труда приводят к переутомлению. Источниками шума и вибрации являются: двигатели внутреннего сгорания электродвигатели компрессоры пневмооборудование лебедки.
На буровых на кустовых площадках скважин на строительных площадках и прочих производственных объектах обязательно пользуйтесь защитной каской которая должна быть застегнута подбородочным ремешком.
Передвигаясь по объекту будьте внимательны к указателям и предупреждающим надписям. Спускаясь или поднимаясь по лестницам или рабочим площадкам на высоте держитесь за перила и будьте осторожны ступая на ступеньки – они могут быть скользкими от пролитого или неубранного своевременно масла нефти или льда в зимнее время.
Запрещается находиться в производственных помещениях технологических установок лицам не связанным с производством работ.
На объектах запрещается курение которое возможно только в специально отведенных местах обозначенных указателем.
2 Безопасность работы персонала
В процессе трудовой деятельности на человека могут воздействовать опасные (вызывающие травмы) и вредные (вызывающие заболевания) производственные факторы.
Эти факторы разделяются на четыре группы: физические химические биологические и психофизические.
К опасным физическим факторам относятся: движущиеся механизмы и машины подъемно-транспортные устройства и перемещаемые грузы незащищенные вращающиеся части и детали оборудования отлетающие частицы обрабатываемого материала и инструмента электрический ток повышенная температура поверхности оборудования обрабатываемых материалов высокое давление.
Шум инфразвук и ультразвук относят к акустическим колебаниям которые могут быть как слышимыми так и неслышимыми. Акустические колебания в диапазоне 16 Гц – 20 кГц воспринимаемые человеком с нормальным слухом называют звуковыми; колебания с частотой менее 16 Гц – инфразвуковыми а с частотой выше 20 Гц – ультразвуковыми.
Распространяясь в пространстве звуковые колебания создают акустическое поле. Интенсивное шумовое воздействие на организм человека неблагоприятно влияет на протекание нервных процессов способствует развитию утомления изменениям в сердечнососудистой системе и появлению шумовой патологии среди многообразных проявлений которой ведущим клиническим признаком является медленно прогрессирующее снижение слуха по типу кохлеарного неврита.
В производственных условиях источниками шума являются работающие станки и механизмы ручные механизированные инструменты электрические машины компрессоры кузнечнопрессовое подъемно-транспортное вспомогательное оборудование
Нормируемые параметры шума на рабочих местах определены ГОСТ 12.1.003-83 с дополнениями 1989 года и Санитарными нормами СН 2.2.42.1.8.562-96 «Шум на рабочих местах в помещениях жилых общественных зданий и на территории жилой застройки». Документы дают классификацию шумов по спектру на широкополосные и тональные а по временным характеристикам – на постоянные и непостоянные. Для нормирования постоянных шумов применяют допустимые уровни звукового давления в девяти октавных полосах частот в зависимости от вида производственной деятельности. Для ориентировочной оценки в качестве характеристики постоянного широкополосного шума на рабочих местах допускается принимать уровень звука определяемый по шкале шумомера с коррекцией низкочастотной составляющей по закону чувствительности органов слуха и приближением результатов объективных измерений к субъективному восприятию.
Средства и методы защиты от шума.
Для защиты от шума применяют:
уменьшение шума в источнике возникновения;
звукопоглощение и звукоизоляцию;
установку глушителей шума;
рациональное размещение оборудования;
применение средств индивидуальной защиты.
Для уменьшения механического шума своевременно проводят ремонт оборудования заменяют ударные процессы на безударные применяют принудительное смазывание трущихся поверхностей применяют балансировку вращаюшихся частей.
Средствами индивидуальной защиты от шума являются ушные вкладыши наушники шлемофоны. Эффективность индивидуальных средств защиты зависит от используемых материалов конструкции силы прижатия правильности ношения.
2.2 Защита от вибрации
Воздействие вибрации на человека классифицируют:
по способу передачи колебаний;
по направлению действия вибрации;
по временной характеристике вибрации.
По временной характеристике различают: постоянную вибрацию для которой контролируемый параметр за время наблюдения изменяется не более чем в два раза; непостоянную вибрацию изменяющуюся по контролируемым параметрам более чем в два раза.
Общая вибрация вызывает изменения в сердечно-сосудистой и центральной нервной системах появление болей в отдельных органах.
Локальные вибрации влияют на центральную нервную систему повышая кровяное давление вызывают сужение капилляров в кончиках пальцев приводят к потери их чувствительности.
Действие вибрации на человека становится опасным когда частота колебаний рабочего места приближается к частоте собственных колебаний органов тела человека.
Основным нормативным документом в области вибрации является ГОСТ 12.1.012-90.
В нем нормируются значения виброскорости и виброускорения а также их логарифмические уровни.
Вибрацию воздействующую на человека нормируют отдельно для каждого направления учитывая для общей вибрации ее категорию а при локальной вибрации – время действия.
Для снижения вибрации широко используют эффект вибродемпфирования – превращение энергии механических колебаний в другие виды энергии чаще всего в тепловую.
С этой целью в конструкции деталей через которые передается вибрация применяют материалы с большим внутренним трением – специальные сплавы пластмассы резины вибродемпфирующие покрытия.
Для предотвращения общей вибрации используют установку вибрирующих машин и оборудования на самостоятельные виброгасящие фундаменты.
Для ослабления передачи вибрации от источников ее возникновения полу рабочему месту сиденью рукоятке и т.п. широко применяют методы виброизоляции. Для этого на пути распространения вводят дополнительную упругую связь в виде виброизоляторов из резины пробки войлока асбеста стальных пружин.
В качестве средств индивидуальной защиты работающих используют специальную обувь на массивной резиновой подошве.
Для защиты рук служат рукавицы перчатки вкладыши и прокладки которые изготавливают из упругодемпфирующих материалов.
Освещенность которую необходимо поддерживать на площадке предусмотрена в соответствии со СНиП 23-05-95 «Естественное и искусственное освещение».
Площадки оборудуются светильниками повышенной надежности против взрыва с лампами накаливания мощностью 300 Вт.
Работы с различением объектов от 015 до 03 мм относятся современными нормами (СНиП 23-05-95) ко II разряду зрительной работы (очень высокой точности) и при системе общего освещения лампы накаливания требуются в зависимости от контраста объекта различения с фоном и светлоты фона освещенности от 200 до 300 лк. Работы с различением объектов от 03 до 05 мм (III разряд – работы высокой точности) требуют освещенности от 150 до 300 лк.
Анализ выше перечисленных факторов изображен в таблице 5.1.
Таблица 5.1 – Итоговая таблица по оценке условий труда работника по степени вредности и опасности
Классы условий труда
Общая оценка условий труда Вредный 2 степени
3 Электробезопасность и молниезащита
Электронасыщенность современного производства формирует электрическую опасность источником которой могут быть электрические сети электрифицированное оборудование и инструмент вычислительная и организационная техника работающая на электричестве. Электротравматизм по сравнению с другими видами производственного травматизма составляет небольшой процент однако по числу травм с тяжелым и особенно летальным исходом занимает одно из первых мест.
3.1 Основные требования по предупреждению электротравматизма
Технические методы и средства защиты для обеспечения электробезопасности подбираются в соответствии с ГОСТ 12.1.009-76 «ССБТ Электробезопасность. Общие требования»
Двигатели необходимо снабдить защитой от короткого замыкания от перегрузки минимального напряжения замыканий на землю асинхронного хода.
Кроме того предусмотреть защиту действующую при повышении давления нагнетания понижении давления всасывания понижении давления масла в коллекторе понижении уровня масла в маслоотделителе повышение температуры подшипников электродвигателя повышении концентрации взрывоопасной смеси пожаре перегрузке электродвигателя насоса.
Насосный агрегат устанавливается на месте которое не является постоянным рабочим местом для обслуживающего персонала управление насосным агрегатом – дистанционное с помощью комплекта контрольно-измерительных приборов и автоматики.
Согласно ГОСТ 12.1.019-79 «Электробезопасность» для обеспечения электробезопасности на промышленных предприятиях необходимо принимать следующие методы.
К работе с электрооборудованием должны допускаться лица прошедшие инструктаж и обучение безопасным методам труда проверку знаний правил безопасности и инструкций в соответствии с занимаемой должностью применительно к выполняемой работе с присвоением соответствующей квалификационной группы по технике безопасности и не имеющие медицинских противопоказаний установленных Министерством здравоохранения РФ.
Монтаж и эксплуатация согласно нормативно-технической документации на электрооборудование предоставленной заводом-изготовителем.
Периодическая проверка технического состояния электрооборудования согласно ГОСТ Р 50669-94.
При проведении работ со снятием напряжения в действующих электроустановках или вблизи них: отключение установки (части установки) от источника питания электроэнергией; механическое запирание приводов отключенных коммутационных аппаратов снятие предохранителей отсоединение концов питающих линий и другие мероприятия обеспечивающие невозможность ошибочной подачи напряжения к месту работы; наложение заземлений (включение заземляющих ножей или наложение переносных заземлений); ограждение рабочего места и установка предписывающих знаков безопасности (по ГОСТ 12.4.026).
При проведении работ на токоведущих частях находящихся под напряжением и вблизи них: выполнение работ но наряду не менее чем двумя лицами с применением электрозащитных средств под непрерывным надзором с обеспечением безопасного расположения работающих и используемых механизмов и приспособлений.
3.2 Средства предотвращения электротравматизма
С целью обеспечения электробезопасности предусмотрены различные средства защиты от поражения электрическим током.
Средства индивидуальной защиты от поражения электрическим током включают в себя: спецодежда (по ГОСТ 12.1.029-80) галоши и боты диэлектрические – используются при работе в закрытых электроустановках и в открытых (при отсутствии дождя или мокрого снега) по ГОСТ 13385-78 перчатки резиновые диэлектрические бесшовные – одно из основных защитных средств от поражения постоянным или переменным электрическим током напряжением не выше 1кВ и дополнительное средство защиты при напряжении свыше 1кВ (по ГОСТ 12.4.183-91) ковры резиновые диэлектрические – представляют собой резиновую пластину с рифленой лицевой поверхностью и предназначены для защиты рабочего от поражения электрическим током воздействия электромагнитных полей. Применяются при работе на электроустановках напряжением до 1кВ.
При защите от случайного прикосновения к токоведущим частям:
защитные оболочки (по ГОСТ 14254-96);
защитные ограждения (временные или стационарные);
безопасное расположение токоведущих частей;
изоляция токоведущих частей (рабочая дополнительная усиленная двойная); защитное отключение;
предупредительная сигнализация блокировка знаки безопасности (по ГОСТ 12.4.026).
4 Взрывопожаробезопасность объекта
К пожарам взрывам и авариям на производстве приводит:
курение в не отведенных и не оборудованных местах;
неосторожность обращения с огнем;
неисправность и неправильная эксплуатация электросети электрооборудования и электронагревательных приборов;
неисправность и неправильная эксплуатация газосварочных установок;
нарушения правил пожарной безопасности при электросварочных работах;
нарушения технологического режима на производстве;
неисправность или неправильная эксплуатация технологического оборудования;
неправильное применение горючих и легковоспламеняющихся жидкостей;
некачественная чистка вентиляционных систем;
самовозгорание промасленной рабочей одежды и обтирочного материала;
Согласно СНиП 11-90-81 производства подразделяются по взрывной взрывопожарной и пожарной опасностям на категории А Б В Г Д Е.
Во всех производственных административных складских и вспомогательных помещениях на видных местах должны быть вывешены таблички с указанием номера телефона вызова пожарной охраны.
Правила применения на территории предприятий открытого огня проезда транспорта допустимость курения и проведения временных пожароопасных работ устанавливаются объектовыми инструкциями о мерах пожарной безопасности.
На каждом предприятии приказом (инструкцией) должен быть установлен соответствующий их пожарной опасности противопожарный режим в том числе:
определены и оборудованы места для курения;
определены места и допустимое количество единовременно находящейся в помещениях готовой продукции;
установлен порядок уборки горючих отходов и пыли хранения промасленной спецодежды;
определен порядок обесточивания электрооборудования в случае пожара и по окончании рабочего дня;
порядок проведения временных огневых и других пожароопасных работ;
порядок осмотра и закрытия помещений после окончания работы;
действия работников при обнаружении пожара;
определен порядок и сроки прохождения противопожарного инструктажа и занятий по пожарно-техническому минимуму а также назначены ответственные за их проведение;
определен порядок проведения планово-предупредительных ремонтов автоматических систем пожаротушения пожарной сигнализации систем электроснабжения вентиляции и первичных средств пожаротушения.
Согласно НПБ 105-95 среда в которой работает турбобур относится к взрывоопасной категории «А».
По ПУЭ относится к классу взрывоопасности В – 1г (зона I радиусом 5 метров зона II R=5÷75 м).
Категория и группа взрывоопасных смесей: нефть относится к категории IIА и группе взрывоопасных смесей Т3 согласно таблице 5.2.
Таблица 5.2 – Классификация производственной среды
Категория производст-ва по НПБ 105-95
Класс взрыво-опасности ПУЭ
Категория и группа взрывоопасной смеси по ПУЭ
Краткая характеристика среды
устья нефтяных скважин
Нефть и попутный газ
4.1 Средства обеспечения взрывопожаробезопасности
В здании насосной содержатся следующие горючие вещества: метанол при контакте с воздухом образует взрывоопасную смесь (температура вспышки 11°С); масло – воспламеняющаяся жидкость (температура вспышки 230°С).
Согласно СНиП 21-01-97 «Пожарная безопасность зданий и сооружений» применяют методы:
в зданиях насосной должны быть предусмотрены конструктивные объемно-планировочные и инженерно-технические решения обеспечивающие в случае пожара возможность эвакуации персонала наружу на прилегающую к зданию территорию до наступления угрозы их жизни и здоровью вследствие воздействия опасных факторов пожара;
возможность спасения людей;
возможность доступа личного состава пожарных подразделений и подачи средств пожаротушения к очагу пожара а также проведения мероприятий по спасению людей и материальных ценностей;
нераспространение пожара на рядом расположенные здания в том числе при обрушении горящего здания.
В процессе строительства необходимо обеспечить:
приоритетное выполнение противопожарных мероприятий предусмотренных проектом разработанным в соответствии с действующими нормами и утвержденным в установленном порядке (должны использоваться непожароопасные (КО) и малопожароопасные (К1) конструкции из негорючих строительных материалов;
внутри технологических зданий необходима установка противопожарных преград);
в процессе эксплуатации соблюдение противопожарных правил предусмотренных ППБ 01-03;
наличие и исправное содержание средств борьбы с пожаром;
не допускать изменений конструктивных объемно-планировочных и инженерно-технических решений без проекта разработанного в соответствии с действующими нормами и утвержденного в установленном порядке;
при проведении ремонтных работ не допускать применения конструкций и материалов не отвечающих требованиям действующих норм;
во всех производственных административных складских и вспомогательных помещениях на видных местах должны быть вывешены таблички с указанием номера телефона вызова пожарной охраны;
определены и оборудованы места для курения должна быть разработана инструкция определяющая действия персонала по обеспечению безопасной и быстрой эвакуации людей по которой не реже одного раза в полугодие должны проводиться практические тренировки всех задействованных для эвакуации работников.
5 Экологичность проекта
В настоящее время охрана окружающей среды стала одной из актуальнейших проблем современности.
Необходимость бережного отношения к природе за последние десятилетия получила глубокое отражение в различных государственных решениях и постановлениях.
Поэтому большое значение при ведении буровых работ имеют технико-экономические аспекты охраны окружающей природной среды заключающиеся в рациональном выборе технологии производственных процессов технических средств обеспечивающих при наименьших экономических затратах реализацию необходимых природоохранных мероприятий.
При проведении бурения могут возникнуть следующие основные виды нарушений природной среды:
- отчуждение и вывод из строя плодородных земель;
- нерациональное и бесконтрольное использование земельных участков под планировку буровых площадок и инженерных коммуникаций прокладываемых к буровым;
- нарушение почвенного слоя и уменьшение продуктивности почв на месте ведения буровых работ;
- поступление в водоносные горизонты и продуктивные пласты химических реагентов применяемых в качестве добавок к промывочным жидкостям;
- переток подземных вод из одного водоносного горизонта в другой или в продуктивный пласт (нефтяной или газовый) или переток углеводорода из одного продуктивного пласта в другой по затрубному пространству в стволе скважины при неудовлетворительной организации разобщения пластов;
- утечка и проникновение в продуктивный горизонт масел нефтепродуктов и глинистых растворов обработанных химическими реагентами;
- загрязнение поверхностных вод различными маслами нефтепродуктами и химическими веществами что ведет к последующему проникновению этих вод в скважину;
- загрязнение подъемных вод при использовании таких технических и технологических средств при бурении эксплуатационных скважин на нефть и газ как торпедирование солянокислотная обработка призабойной зоны и гидроразрыв пласта.
Для предотвращения ущерба который наносится проведением буровых работ необходимо выполнить следующий комплекс природоохранных мероприятий которые прямо или косвенно связаны с применяемой технологией бурения:
тип промывочной жидкости химические реагенты и материалы используемые при регулировании свойств раствора следует выбирать с учетом геолого-гидрогеологических условии месторождения;
нельзя забуривать скважину с использованием эмульсионной промывочной жидкости;
конструкция циркуляционной системы сооружаемой с учетом конкретных местных условий должна исключать возможность утечки отработанной жидкости в грунт;
запрещается сбрасывать отработанный раствор в гидрографическую сеть отдельные водоемы почву;
для защиты водоносных горизонтов и продуктивных углеводородных пластов из различных перетоков и загрязнений вредными веществами необходимо осуществлять их надежную изоляцию путем спуска обсадных колонн цементирования тампонирования и другими средствами устраняющими сообщение горизонта со стволом скважины;
захоронение остатков вредных химических веществ реагентов непригодных для бурения следует проводить в землю в изолированных или искусственно созданных полостях в местах где отсутствуют водоемы питьевого назначения под слоем земли не менее 1 м с последующей рекультивацией этой площади;
при кустовом бурении необходимо в обязательном порядке проводить обваловку буровой площадки.
При аварийных разливах нефти ее локализацию сбор и ликвидацию проводят экспедиционным отрядом аварийно-спасательных и подводно-технических работ.
Основные виды воздействия на окружающую природную среду при строительстве скважин заключаются: в изъятии полезных ископаемых (нефти газоконденсата газа); в отчуждении земель во временное и постоянное пользование; в изменении среды обитания представителей растительного и животного мира; в попадании химических веществ твердых и жидких производственных и бытовых и отходов в недра шума и вибрации.
Наибольшую экологическую опасность при возникновении аварийных ситуаций представляют неуправляемые поступления пластовых флюидов по скважинам (открытые фонтаны и выбросы). Вторым по значимости фактором потенциальной экологической опасности является разливы жидких углеводородов из хранилищ и трубопроводов.
Мероприятия по предупреждению и ликвидации разливов включают эффективные средства удержания разлитых жидкостей на месте для сведения до минимума последствий разливов и утечек.
В планах ликвидации аварий учитываются возможный объем и тип разливаемой жидкости указываются типы технических средств для борьбы с разливами потребность в рабочей силе организационные мероприятия обеспечивающие эффективную ликвидацию больших и малых разливов а так же перечень наиболее уязвимых и чувствительных участков вместе со средствами их защиты. План также предусматривает способы удаления разлитой нефти загрязненного грунта и мусора а также доставку на место персонала привлеченного к ликвидации разлива. При применении химических диспергаторов для борьбы с разливами нефти необходимо иметь разрешение санитарных и природоохранных органов на их использование.
В целях предупреждения загрязнения атмосферного воздуха предусматривается ряд мероприятий по сокращению выбросов вредных веществ в атмосферу: полная герметизация системы сбора и транспорта продукции скважин; защита оборудования и трубопроводов от коррозии; оснащение предохранительными клапанами всей аппаратуры в которой может возникнуть давление превышающее расчетное с учетом требований «Правил устройства и безопасной эксплуатации сосудов работающих под давлением» утилизация попутного нефтяного газа.
Наземное технологическое оборудование должно обеспечить сбор и подготовку к транспорту или хранению не только основного полезного ископаемого (нефти газа) но и попутно добываемых кондиционных продуктов (конденсата серы инертных газов микроэлементов и т.д.).
Сокращению потерь и утилизации углеводородов при эксплуатации месторождений нефти и газа способствует применение закрытых герметизированных систем сбора подготовки и транспорта нефти газа и конденсата улавливание и использование низконапорного нефтяного газа с установок товарной подготовки нефти и концевых ступеней сепарации с помощью вакуумных и компрессорных установок с последующей переработкой этого ценного сырья на газоперерабатывающих заводах и др.
Обеспечение надежной безаварийной работы систем сбора подготовки транспорта и хранения нефти и газа имеет весьма важное значение для предотвращения потерь добываемых полезных ископаемых и следовательно охраны недр и рационального использования природных ресурсов.
Внешняя и внутренняя коррозия при эксплуатации нефтяных и газовых месторождений является одной из главных причин преждевременного выхода из строя наземного нефтегазопромыслового оборудования подземных коммуникаций и трубопроводов.
Защита этого оборудования от коррозии обеспечение плановых сроков его службы особенно в условиях его контакта с высокоагрессивными коррозионноактивными средами представляет собой чрезвычайно важную и сложную задачу.
Для ее решения осуществляют широкий комплекс мер технологического и специального плана.
К технологическим методам защиты оборудования и трубопроводов от коррозии относят различные мероприятия предупредительного характера направленные на сохранение первоначально низких коррозионных свойств среды или создание таких условия эксплуатации которые при одной и той же агрессивности среды обеспечивали бы ее минимальное коррозионное воздействие на поверхность металла. Основными задачами таких методов являются: предотвращение попадания в добываемую нефть нефтяной газ кислорода; предотвращение смешивания сероводородсодержащей нефти вод и газов с продукцией не содержащей его; снижение коррозионной агрессивности среды с помощью деаэраторов и других средств; создание противокоррозионных условий для надежной эксплуатации действующего оборудования (изменение конструкции снижение механических нагрузок и др.).
В связи с тем что эти меры необходимо предусматривать для всех систем нефтедобычи технологические методы защиты от коррозии должны носить комплексный характер и применяться одновременно на всех объектах подготовки нефти и газа и утилизации сточных вод.
6 Чрезвычайные ситуации
Для Тюменской области характерны следующие чрезвычайные ситуации (ЧС):
природного характера:
паводковые наводнения;
лесные и торфяные пожары;
сильные морозы (ниже -400С);
метели и снежные заносы;
техногенного характера
разливы сильнодействующих ядовитых веществ (СДЯВ);
отключение электроэнергии и др.
По статическим материалам или путём экспертных оценок определяют-ся наиболее вероятные ЧС на объекте прогнозируется их последствия и разрабатываются мероприятия по их предотвращению.
Одним из примеров ЧС могут быть взрывы газовых баллонов или взры-воопасных смесей при проведении работ в газоопасной зоне.
Производственные аварии возможны самые разнообразные. Причина-ми их могут являться стихийные бедствия (землетрясения оползни обледе-нения и т.п.) а также нарушения технологии производства и правил техники безопасности.
Наиболее типичными последствиями аварий могут быть взры-вы пожары затопления заражения окружающей среды ядовитыми сильно-действующими веществами.
Задача каждого работающего на предприятии знать основные правила поведения при авариях уметь действовать в сложившейся при этом обста-новке. К примеру существуют определенные правила и последовательность отключения электроэнергии остановки транспортирующих устройств агре-гатов и аппаратов перекрытия сырьевых газовых паровых и водяных ком-муникаций в соответствии с технологическим процессом и техникой безо-пасности нарушения которых могут усугубить и усложнить обстановку; эти правила и последовательность действий надо изучить их нужно уметь прак-тически выполнять.
В аварийной ситуации важной задачей является организация своевременного оповещения об аварии. С возникновением аварии рабочие и служащие входящие в состав формирования ГО обязаны незамедлительно прибыть в места их сбора.
7 Определение вероятных параметров ударной волны при взрыве газовоздушной или паровоздушной смеси
Одной из наиболее частых аварий является взрыв. При выборе электрооборудования для объектов добычи нефти и газа необходимо учитывать специфические условия работы электрических установок связанных с наличием взрывоопасных газов и паров.
К взрывоопасным относятся смеси с воздухом горючих газов и паров горючих жидкостей с температурой вспышки 450С и ниже а также горючей пыли или волокон с нижним пределом взрываемости не выше 65 гсм3.
На рисунке 5.1 изображена примерная схема распространения ударной волны по зонам.
– зона детонации; 2 – зона действия продуктов взрыва; 3 – зона ударной волны; R1 – радиус первой зоны; R2 – радиус второй зоны; r2 – расстояние от центра взрыва до элемента предприятия (во 2 зоне); r3 – расстояние от центра взрыва до элемента предприятия (в 3 зоне)
Рисунок 5.1 – Схема распространения ударной волны по зонам
При взрыве газовоздушной смеси весом в 15т находится на расстоянии менее 65 м от эпицентра взрыва опасно для жизни.
Для насосов и другого оборудования:
слабые разрушения при Δpф = 025÷04 атм.;
средние разрушения при Δpф = 04÷06 атм.;
сильные разрушения при Δpф = 06÷07 атм.
где – количество газа т.
Разность давлений в первой зоне кПа; разность давлений во второй зоне:
При разность давлений в третьей зоне
Радиус зоны опасной для жизни человека:
По рассчитанному избыточному давлению можно сделать вывод:
степень разрушения окружающих зданий (трубопроводов) в зоне 1 будет - сильная;
степень разрушения в зоне 2 – сильная;
степень разрушения в зоне 3 – слабая.
8 Организационно технические мероприятия по предотвращению ЧС
На производственных объектах исключаются переливы кислот при заполнении емкостей.
Транспортировка этих опасных жидкостей по специальным трубопроводам (из свинца винипласта специальной стали и т.п.) с автоматическим контролем за перекачкой; слив кислоты из железнодорожных цистерн выполняется при помощи гибких шлангов.
Для наполнения мелкой тары применяются сифоны оборудованные устройствами для создания вакуума.
При разливе кислоты ее нейтрализуют каустической содой или известью.
Наиболее вредным веществом является метанол.
Метанол – бесцветная прозрачная жидкость по запаху и вкусу напоминающая винный (этиловый) спирт.
Плотность его 079 гсм3 температура кипения 645 °С.
Растворим в спиртах и других органических соединениях смешивается с водой во всех соотношениях легко воспламеняется.
Температура вспышки 16°С.
При испарении взрывоопасен.
Пределы воспламенения метанола в воздухе 672÷365 %.
ПДК метанола в рабочей зоне производственных помещений – 5 мгм3.
Метанол – сильный яд действующий преимущественно на нервную и сосудистую системы.
В организм человека он может проникнуть через дыхательные пути и кожу.
Особенно опасен прием метанола внутрь: 5÷10 г метанола могут вызвать тяжелое отравление; 30 г является смертельной дозой.
Симптомы отравления: головная боль головокружение тошнота рвота боль в желудке общая слабость раздражение слизистых оболочек мелькание в глазах в тяжелых случаях – потеря зрения и смерть.
Технические решения принятые в данном дипломном проекте соответствуют требованиям промышленной безопасности согласно Федеральному закону «О промышленной безопасности опасных производственных объектов» от 21.07.97 №116-ФЗ и постановлению Правительства Российской Федерации от 10.03.99 №263 «Об организации и осуществлении производственного контроля соблюдения требований промышленной безопасности на опасном производственном объекте».
Модернизация не повлияла на экологичность окружающей среды. Благодаря принятому техническому решению уменьшилось время на спуск и установку клина-отклонителя в скважине.
Раздел 2.docx
1 Патентно-информационный поиск
Произведен патентный поиск глубиной в 10 лет.
В патенте № 2183247 предоставлена следующая формула изобретения.
Клин-отклонитель (рисунок 2.1) включает корпус рабочая поверхность которого в поперечном сечении имеет форму продольного желоба.
В головной части корпуса выполнены отверстия для связи со спускаемым буровым инструментом посредством срезных элементов.
В хвостовой части корпуса под углом к продольной оси клина-отклонителя выполнена резьба для его связи с хвостовиком а в корпусе выполнен осевой продольный канал с выходом его на рабочую поверхность.
На расстоянии не менее чем половины длины клина-отклонителя от его хвостовой части симметрично продольной плоскости клина-отклонителя на его боковой поверхности ниже продольного желоба выполнены продольные лыски которые в поперечном сечении представляют собой две пересекающиеся вне диаметра корпуса клина-отклонителя хорды.
Угол между лысками составляет 60° при этом осевой канал в корпусе связан с упомянутыми лысками посредством радиальных отверстий а резьба хвостовой части выполнена под углом к продольной оси клина-отклонителя.
На резьбе закреплен хвостовик имеющий длину до 12 длины клина-отклонителя.
К хвостовику может быть закреплен фильтр имеющий посадочный фланец под посадочное седло устанавливаемое в скважине.
Такое выполнение клина-отклонителя позволяет упростить его конструкцию и одновременно повысить качество работы при отклонении ствола скважины
в заданном направлении а также при забуривании нового ствола из первоначальной скважины.
Рисунок 2.1 – Клин-отклонитель
В патенте № 2368753 [18] предоставлена следующая формула изобретения:
Устройство для ориентирования клина-отклонителя в скважине включающее полый корпус выполненный с возможностью соединения с транспортировочной колонной седло помещенное в корпусе и выполненное с центральным осевым каналом по меньшей мере с одним периферийным каналом и по меньшей мере с одним радиальным каналом запорный элемент для седла выполненный с цилиндрическим удлинителем под центральный осевой канал седла имеющим со стороны свободного торца карман перегородку центрального осевого канала образующую с цилиндрическим удлинителем камеру шарик размещенный в камере фиксирующий запорный элемент над седлом и имеющий возможность его размещения в кармане для посадки запорного элемента на седло в рабочем положении устройства диск с центральным осевым каналом и по меньшей мере с одним периферийным осевым каналом зафиксированный в корпусе над запорным элементом подпружиненный шток размещенный в центральном осевом канале диска и связанный одним концом с этим диском а другим концом – с запорным элементом хвостовик обсадной колонны с обратным клапаном и клин-отклонитель размещенный между хвостовиком и корпусом жестко связанный с нижней частью последнего и имеющий возможность вращения относительно хвостовика при этом диск связан со штоком и имеет на его внешней стороне метку на одной оси с карманом.
Описание предлагаемой конструкции
Изобретение поясняется чертежами:
на рисунке 2.2 – изображено устройство в транспортном положении;
на рисунке 2.3 – устройство в момент его настройки перед спуском в скважину;
на рисунке 2.4 – устройство в рабочем положении.
Устройство (рисунок 2.1) включает полый (составной) корпус 1 выполненный с возможностью соединения с транспортировочной колонной (на рисунках 2.1 и 2.3 условно не показана).
В корпусе помещено седло 2 выполнен шпоночный паз 3 установлена перегородка 4 и выполнен радиальный канал 5 по меньшей мере один и осевой канал 6 по меньшей мере один.
Устройство имеет ориентирующий узел который выполняет функцию дроссельно-запорного клапана.
Этот узел установлен в полом корпусе 1 и состоит из запорного элемента (тарелки) 7 с цилиндрическим удлинителем 7а под центральный осевой канал седла штока 8 диска 9 со шлицами 10 центральным осевым каналом 10а и периферийным осевым каналом 11 по меньшей мере одним пружины 12 шайбы 13 гаек 14.
Подпружиненный шток 8 размещен в центральном осевом канале диска 9.
Этот диск закреплен от поворота на штоке 8 посредством шпонки 15 со стороны центрального осевого канала 10а диска 9.
В камере 16 образованной корпусом 1 перегородкой 4 и цилиндрическим удлинителем 7а запорного элемента 7 расположен шарик 17.
Со стороны свободного торца удлинителя запорного элемента 7 выполнен карман 18 на одной оси с которым на внешней (доступной для контроля) поверхности диска 9 выполнена метка 19.
Рисунок 2.2 – Устройство в транспортном положении
Установка (фиксация) ориентирующего узла в корпусе 1 осуществлена с помощью шпонки 20.
Регулировка давления срабатывания ориентирующего узла предусмотрена посредством сжатия пружины 12 гайками 14 перед спуском устройства в скважину.
Клин-отклонитель 21 установленный в нижней части устройства в исходном положении жестко связан с полым корпусом 1 и имеет возможность совместного с устройством вращения относительно хвостовика 22.
Гидравлически управляемые элементы хвостовика – якорный и пакерный узлы механизм разъединения транспортировочной колонны от хвостовика необходимые непосредственно для хвостовика (не показаны) расположены между устройством по данному изобретению и обратным клапаном 23 которым оборудован хвостовик 22.
Устройство может быть использовано в наклонном и горизонтальном участке ствола скважины.
Подготовку устройства к работе осуществляют в два этапа. На первом этапе необходимые операции осуществляют на поверхности перед спуском устройства в скважину (рисунок 2.2).
Для этого метку 19 диска устанавливают в полом корпусе 1 относительно клина-отклонителя 21с заданным углом при котором после спуска устройства в скважину и приведения его в рабочее положение клин-отклонитель 21 занял бы необходимое расчетное положение относительно хвостовика.
Рисунок 2.2 – Устройство в момент его настройки перед спуском
После спуска устройства в скважину с расположением хвостовика на заданной глубине приступают ко второму этапу работ.
Для этого включают насос с заданной производительностью и осуществляют циркуляцию бурового раствора через осевой периферийный канал 11 диска 9 и радиальный канал 5 корпуса 1.
При этом шарик 17 находящийся в камере 16 не дает возможности запорному элементу (тарелке) 7 сесть в седло 2 и таким образом закрыть ориентирующий узел – дроссельно-запорный клапан устройства.
После появления циркуляции останавливают прокачку бурового раствора и повернув устройство на 10÷15 градусов относительно стола ротора включают насос и повторяют эти операции до момента когда положение кармана 18 запорного элемента 7 совпадет с положением шарика 17 постоянно находящегося за счет сил гравитации в нижней части камеры 16.
Рисунок 2.3 – Устройство в рабочем положении
В этом случае шарик 17 заходит в карман 18 и запорный элемент 7 при посадке в седло 2 закрывает радиальный канал 5 корпуса 1.
В результате прекращается циркуляция и давление в нагнетательной линии растет.
Для проверки точности установки устройства отключают насос снимают избыточное давление в устройстве и затем вновь его создают.
Дополнительно убеждаются в отсутствии циркуляции и заданной установке устройства.
При дальнейшем увеличении давления приводтся в действие гидравлически управляемые элементы хвостовика – якорный и пакерный узлы и разъединение транспортировочной колонны с предлагаемым устройством.
Клин-отклонитель в скважине может быть закреплен с применением известных приемов например порцией цемента которая может быть подана через заколонное пространство транспортировочной колонны.
Для отсоединения клина-отклонителя от транспортировочной колонны могут быть использованы тоже известные средства например левый переводник или срезные элементы.
В результате в скважине после проведения описанных операций и подъема предлагаемого устройства остается хвостовик 22 с обратным клапаном а также зафиксированный в стволе скважины и сориентированный клин-отклонитель.
Сориентированный клин-отклонитель обеспечивает возможность забуривания бокового ствола скважины.
Эксплуатация спущенного в скважину хвостовика 22 предусмотрена через фильтровую часть колонны труб (не показана) и обратный клапан 23.
Аннотация.docx
Произведён анализ конструкции описание модернизации а так же все необходимые расчёты для подтверждения целесообразности предлагаемой модернизации.
Произведён расчёт экономической эффективности проекта и анализ безопасности и экологичности проекта.
Пояснительная записка включает 3 таблицы 78 формул 12 рисунков 79 страниц список используемой литературы.
Раздел 6.docx
В процессе усовершенствования механизмов всегда ставятся задачи по повышению их надежности долговечности и уменьшению вреда который они могут принести окружающей среде.
Однако при выполнении этих требований необходимо учитывать что повышение соответствия машин и механизмов этим требованиям напрямую связано с их стоимостью.
Поэтому улучшение качества устройства для ориентирования клина-отклонителя должно соизмеряться с повышением его стоимости и осуществляться только в случае если оно приносит и экономический эффект при его использовании.
Прирост потока денежной наличности рассчитывается по следующей формуле
где – экономия затрат в t-ом году от проведения модернизации руб.;
– капитальные затраты в t-ом году связанные с проведением мероприятия руб.;
– прирост величины налоговых выплат в t-ом году руб.
2 Расчет экономии затрат
Экономия затрат осуществляется вследствие сокращения времени на монтаж клина-отклонителя в скважине и рассчитывается по формуле
где – количество часов на установку клина-отклонителя до модернизации;
– количество часов на установку клина-отклонителя после модернизации;
– стоимость одного бригадо-часа работ руб.
где – заработная плата руб.;
– единый социальный налог руб.;
– транспортные затраты руб.;
– материалы и оборудование МБП руб.;
– амортизация основных средств руб.;
– услуги вспомогательных цехов руб.;
– затраты на электроэнергию руб.;
– накладные расходы руб.;
– рентабельность руб.
3 Расчет капитальных затрат
Капитальные затраты на проведение модернизации связаны с затратами на проектирование системы ее изготовление транспортировку и монтаж:
где – затраты на проектирование (разработку) системы руб.;
– затраты на изготовление руб.
– затраты на транспортировку руб.
– затраты на монтаж установку и запуск в работу руб.
Затраты на разработку можно представить в виде
где – месячный оклад разработчика руб.;
– трудоемкость разработки проекта и проектной документации ч*мес.;
– соответственно коэффициенты доплат к заработной плате и районный коэффициент доли ед.;
– единый социальный налог доли ед.;
– коэффициент накладных расходов доли ед.
Затраты на изготовление модернизации рассчитаем по формуле
где – затраты на материалы руб.;
– затраты на основную заработную плату изготовителя руб.;
– затраты на доплату к зарплате с учетом районного коэффициента руб.;
– затраты на выплату единого социального налога руб.;
– затраты на электроэнергию руб.
Затраты на материалы определяем по формуле
где – вид материала;
– количество i-го материала кг.
В качестве материала берется сталь Сталь 50 стоимостью 40 руб. за 1 кг.
Затраты на основную заработную плату при изготовлении устройства равны
где – оклад изготовителя руб.;
– трудоемкость изготовления устройства чмес.
Доплата к заработной плате изготовителя с учетом районного коэффициента равна
где – районный коэффициент доли ед.;
Единый социальный налог определяется по формуле
где – коэффициент учитывающий затраты на единый социальный налог доли ед.
Затраты на электроэнергию рассчитаем по формуле
где – стоимость одного кВтч электроэнергии руб.;
– коэффициент интенсивного использования оборудования доли ед.;
– время использования
– количество использованных приборов шт.
Подставим все полученные значения
Затраты на транспортировку изделия равны
где – коэффициент учитывающий затраты на транспортировку изделия.
Затраты на монтаж установку и запуск в работу у заказчика
где – коэффициент учитывающий затраты на монтаж установку и запуск в работу
Подставим все полученные значения в формулу
При расчёте налогов необходимо обязательно рассчитать прирост налога на имущество и налога на прибыль
Расчет налога на имущество можно произвести по формуле
где – остаточная стоимость имущества в 1-ом году руб.;
– ставка налога на имущество % (в 2010 году равная 22%)
где – капитальные вложения руб.;
– дополнительные амортизационные отчисления руб.
где – норма амортизации основных фондов или износа нематериальных активов %.
Расчёт налога на прибыль можно произвести по формуле
где – прирост прибыли облагаемой налогом руб.;
– налог на прибыль % (в 2010 году равный 20%)
где – прирост прибыли от реализации руб.;
– прирост прибыли от реализации выбывшего имущества руб.
Подставим все получившиеся значения в формулу и занесем в таблицу 6.1.
Прирост накопленного потока денежной наличности определяется за все годы расчётного периода
Приросты дисконтированных потоков денежной наличности и чистой текущей стоимости определяются по следующим формулам
Таблица 6.1 – Расчет всех основных экономических показателей за 5 лет
На основании данных таблицы 4.1 строятся график профилей и (рисунок 6.1).
Рисунок 4.1 – Профили и
Определяем срок окупаемости проекта
Определяем коэффициент отдачи капитала
Проект к риску не чувствителен срок окупаемости около 5-ти месяцев при коэффициенте отдачи капитала 12.
Раздел 4.docx
Буровые установки предназначены для сооружения скважин. Конструкция скважины во многом определяет типоразмер БУ. Буровая установка состоит из отдельных сооружений агрегатов и механизмов. Процесс бурения представляет собой отдельные последовательные или повторяющиеся операции которые выполняет буровая бригада с помощью механизмов. По функциональному назначению всё оборудование можно условно подразделить на две группы: подземное и наземное. Если подземное оборудование предназначено непосредственно для бурения скважины то наземное приводит его в движение и обслуживает его работу.
Рисунок 4.1 – Классификация бурового оборудования
Бурильная колонна выполняет функцию непосредственного углубления скважины и расширения ствола состоит из бурильных труб забойного двигателя и породоразрушающего устройства работает в наиболее тяжелых условиях. Вращающаяся бурильная колонна подвергается большим растягивающими или сжимающим нагрузкам кручению и циклическому изгибу. Главное требование к ней – обеспечение несущей способности и надежности её элементов.
Обсадная колонна состоит из труб длиной 9÷13 метров одинакового наружного диаметра с различными толщинами стенок. В процессе эксплуатации обсадные колонны подвержены наружному и внутреннему давлению а так же осевому растяжению от собственного веса. Равнопрочность колонны по длине достигается путем подбора по расчету труб с различными толщинами стенок из сталей разных групп прочности.
Наземное оборудование монтируют двумя способами: блочно-агрегатным и крупноблочным и предназначено в основном для выполнения СПО вращения колонны обеспечения промывки скважины буровыми растворами. Наземное оборудование можно разделить на две подгруппы: основное и вспомогательное. К основному оборудованию относятся вышки буровые насосы роторы вертлюги и оборудование подъемного комплекса. Вспомогательное оборудование дополняет основное и облегчает его работу. Эта группа состоит из компрессоров циркуляционной системы оборудования устья скважины и СПО измерительных и пускорегулирующих устройств.
Вышка или мачта – основное несущее сооружение буровой установки. Предназначена для монтажа кронблока подвести талевой системы размещения средств механизации СПО. В процессе эксплуатации вышки воспринимают все нагрузки от веса бурильных или обсадных колонн и пульсирующие ветровые нагрузки. Хотя вышки представляют собой стационарную конструкцию (отсутствуют движущиеся части) они подвержены износу в процессе эксплуатации. Специфичность износа заключается в том что несущая способность конструкции со временем значительно снижается. Это связано с атмосферной коррозией стали под напряжением. Особенно опасна коррозия в сочленениях и местах сварки. Поэтому повышение надежности и долговечности вышек необходимо связывать с защитой их от коррозии.
Подъемный комплекс БУ обеспечивает выполнение наиболее трудоемких в бурении спускоподъемных операций производит подачу долота по мере углубления ствола он необходим для ликвидации осложнений и аварийных ситуаций в скважине. Подъемный комплекс состоит из трех основных узлов: талевой системы буровой лебедки и силового привода. К агрегатам подъемного комплекса предъявляются повышенные требования с точки зрения надежности. Большинство ответственных деталей при работе подвержены действию переменных нагрузок и могут разрушатся от усталости металла. Поломки ответственных деталей приводят к авариям. В этой связи к оборудованию при проектировании и изготовлении Госгортехнадзором предъявляются повышенные требования.
Буровые лебедки – один из основных узлов подъемного комплекса. Назначение буровой лебедки – создание тягового или тормозного усилия в ведущей ветви талевого каната. Лебедки передает вращение ротору создают усилие на машинных ключах подтаскивают и поднимают грузы.
Талевые системы служат для уменьшения натяжения ведущей ветви каната навитого на барабан лебедки. Представляет собой полиспаст и состоит из неподвижного и подвижного блоков соединенных талевым канатом.
Талевые канаты – самый ответственный элемент подъемного комплекса. Канат подвергается растяжению и переменного изгибу. На выносливость талевых канатов значительно влияет качество смазки.
В процессе эксплуатации талевая система воспринимает переменные нагрузки в следствии чего в ответственных деталях могут возникать усталостные трещины. Для предупреждения усталостного разрушения деталей системы необходимо периодически проводить дефектоскопию.
Привод обеспечивает работу всех узлов и агрегатов БУ. По виду первичного источника энергии приводы бывают дизельными газотурбинными и электрическими. Различают два вида привода – основной и вспомогательный. Привод лебедки насосов ротора – основной (силовой). Привод компрессоров глиномешалки вибросита и т.д. – вспомогательный. Применение и использование разных типов привода мотивируется конкретными условиями работы установки и конструкторскими решениями при её проектировании.
Вертлюг выполняет роль соединительного звена между талевой системой и бурильной колонной воспринимает две нагрузки: от веса бурильной колонны и от внутреннего давления бурового раствора. Надежность вертлюга зависит главным образом от работоспособности подшипникового и сальникового узлов.
Ротор приводит во вращение колонну бурильных труб путем передачи крутящего момента ведущей трубе или путем восприятия активного момента забойного двигателя; предназначен для удержания на столе бурильной или обсадной колонн; используется при ловильных работах. Ресурс работы ротора зависит от работоспособности главной опоры воспринимающей реакцию от нагрузок в зубчатом соединении и осевую нагрузку от трения ведущей трубы с зажимом стола.
Буровые насосы являются преобразователями топливной или электрической энергии двигателей привода в гидравлическую энергию потока бурового раствора. Насосы эксплуатируются в очень тяжелых и неблагоприятных условиях что определяется в основном физическими и химическими свойствами буровых растворов. Детали и узлы насосов подвержены интенсивному абразивному износу. На работоспособность деталей насосов влияет коррозионная активность буровых растворов. В работе буровых насосов нередки кратковременные перегрузки от резкого повышения давления при осложнениях в стволе скважины. Тяжелые условия эксплуатации не позволяют в настоящее время обеспечить достаточную надежность насосов. Этим вызвана необходимость устанавливать в насосной группе БУ дополнительный резервный насос.
Оборудование пневмосистемы предназначено для дистанционного оперативного управления исполнительными механизмами БУ. Источник энергии для привода оборудования пневмосистемы – сжатый воздух получаемый с помощью компрессоров. Для накопления запаса сжатого воздуха служат воздухосборники. Надежность работы пневмосистемы зависит от качества осушки воздуха.
Оборудование циркуляционной системы предназначено для приготовления транспортировки и очистки раствора. Состоит из вибросит глиномешалок гидромешалок дегазаторов гидроциклонов пластоотделителей насосов перемешивателей емкостей желобных систем и т.д. все виды оборудования подвержены в процессе эксплуатации абразивному и коррозионному износу.
Оборудование устья скважины кроме непосредственной герметизации должно позволять управление скважиной путем создания противодавления на продуктивные пласты.
В целом условия эксплуатации БУ характеризуются постоянным воздействием на узлы и детали статических и циклических нагрузок. Допускаются кратковременные статические перегрузки но при этом необходимо чтобы результирующие напряжения в деталях не превышали предел текучести материала. Циклические перегрузки иногда оказываются длительными что вызывает усталостное разрушение конструкций. В узлах и деталях одновременно возникают нормальные и касательные напряжения как статические так и переменные. Нарушение характеризуется асимметричным циклом или сложным напряженным состоянием. При этом многие детали работают в непосредственном контакте с поверхностно-активными коррозионными средами которые значительно ускоряют их разрушение при одновременном воздействии переменных нагрузок. Абсолютные потери металла вследствие коррозионного растворения не играют существенной роли. Ресурс оборудования часто определяют местные коррозионные повреждения которые локализуются в наиболее напряженных зонах и вызывают зарождение усталостных трещин.
В процессе углубления скважины буровое оборудование эксплуатируется в двух основных режимах связанных с работой бурильной колонны: режим вращения долота (бурение) и режим спуска или подъема бурильной колонны. Оба эти режима являются нестационарными.
В режиме бурения нагрузки возникают вследствие необходимости передачи долоту крутящего момента поддержания на весу бурильной колонны и прокачки по ЦС бурового раствора. В связи с неоднородностью горных пород и их физико-механических свойств разрушение долотом забоя и углубление скважины происходит неравномерно. Соответственно изменяется растягивающая нагрузка на крюке талевой системы. Эти изменения соответствуют пульсирующему циклу с небольшими частотой и амплитудой.
Величина крутящего момента передаваемого долоту зависит главным образом от момента трения бурильной колонны о стенки скважины и момента сопротивления долота.
Напорная часть циркуляционной системы нагружена в процессе бурения избыточным внутренним давлением 1040 Мпа. Практика показывает что пульсирующие давление бурового раствора влияет на работоспособность узлов нагнетательного манифольда вплоть до вертлюга. Пульсацию раствора следует рассматривать как переменные нагрузки которые расстраивают резьбовые соединения и вызывают коррозионно-усталостные разрушения сварных соединений. После вертлюга пульсация раствора не может существенно влиять на прочность деталей бурильной колонны в связи с тем что на них действуют значительно большие механические переменные нагрузки. Наиболее нагруженной БУ оказывается при подъеме колонн. Процесс подъема колонны цикличен поэтому и нагрузки действующие на детали механизмов подъемного комплекса носят переменный характер как по времени так и по величине. Действующие нагрузки следует рассматривать как статические и динамические.
Таким образом на узлы и детали БУ действуют нагрузки трех видов: статические динамические и переменные. Под статическими будем понимать постоянные или медленно изменяющиеся по времени нагрузки. Напряжения возникающие от динамических нагрузок подсчитываются с помощью коэффициента динамических перегрузок. Переменные нагрузки бывают значительно меньше статических однако при длительной эксплуатации они могут быть более опасными вследствие усталостного разрушения деталей.
В процессе эксплуатации оборудования происходит качественное изменение состояния деталей и узлов вызванное износом взаимосвязанных рабочих поверхностей. Полностью избежать изнашивания оборудования невозможно.
Однако правильная эксплуатация бурового оборудования применение высококачественных смазочных материалов и систем технического обслуживания способствует продлению межремонтного периода работы оборудования.
Система технического обслуживания и планового ремонта бурового оборудования предусматривает проведение ряда регламентированных операций содержащихся в ГОСТ 18322-78.
Техническое обслуживание – комплекс операций или операция по поддержанию работоспособности или исправности изделия при использовании по назначению ожидании хранении и транспортировке. Оно содержит регламентированные в конструкторской документации операции для поддержания работоспособности или исправности изделия в течении срока его службы. В техническое обслуживание могут входить мойка изделия контроль его технического состояния очистка смазывание крепление болтовых соединений замена некоторых составных частей регулировка.
Ремонт – комплекс операций по восстановлению исправности или работоспособности изделий и восстановлению ресурсов изделий или их составных частей. В ремонт могут входить разборка контроль технического состояния изделия восстановление деталей сборка и т.д. содержание части операций ремонта может совпадать с содержанием некоторых операций технического обслуживания. Ремонт любого вида должен сопровождаться выдачей определенных гарантий на последующий срок эксплуатации.
Основой проведения качественного и своевременного ремонта является система ТО и ПР. (техническое обслуживание и плановый ремонт). Эта система состоит из следующих основных разделов: система технического обслуживания и планового ремонта структура и длительность ремонтных циклов и межремонтного периода организация оперативно-технического учета и отчетности. ТО и ПР оборудования проводится после определения периода его эксплуатации. Чередование и периодичность ТО и ПР определяются длительностью межремонтного периода каждого агрегата входящего в состав установки.
Система ТО и ПР устанавливает принципиальные основы организации их что создает необходимые предпосылки для более эффективного использования оборудования увеличения межремонтного периода уменьшение интенсивности износа сопряженных деталей обеспечивает возможность более тщательной подготовки ремонтных работ проведение их в кратчайшие сроки и на высоком техническом уровне. Планирование подготовка и организация ТО и ПР направлены на проведение их в кратчайшие сроки и с минимальными затратами. Технологическая подготовка заключается в разработке технических условий на капитальный ремонт технологических процессов разборки сборки восстановления и составления дефектных ведомостей.
Организация ремонтных работ включает планирование работ по ремонту техническую подготовку производства применение прогрессивных технологий ремонта механизацию слесарно-сборочных работ развитие специализации ремонта по видам оборудования расширение области применения агрегатного и поточного метода ремонта обеспечение ремонтной документацией.
Системой ТО и ПР бурового оборудования действующей в нефтяной промышленности предусмотрены техническое обслуживание (ТО) текущий ремонт (ТР) капитальный ремонт (КР).
Техническое обслуживание (ТО) – подразделяется на два вида - периодическое и сезонное. Периодическое ТО выполняется через установленные в эксплуатационной документации значения наработки или интервала времени (например ТО1 ТО2 ТО3). Сезонное ТО включает в себя операции по замене сезонных сортов масел установке или снятию утеплений агрегатов предпускового подогрева и т.д. ТО оборудования проводится силами эксплуатационного персонала буровой или силами ремонтной бригады. Результаты ТО фиксируются в журнале. Комплекс ТО регламентируется инструкциями заводов изготовителей.
Текущий ремонт (ТР) осуществляется в процессе эксплуатации в целях гарантированного обеспечения работоспособности оборудования. При ТР проводится частичная разборка оборудования ремонт отдельных узлов или замена изношенных деталей регулировка и испытание согласно инструкции по эксплуатации. Неисправные детали и узлы ремонтируются в мастерских. ТР проводится ремонтными бригадами с привлечением обслуживающего персонала в соответствии с планами.
Капитальный ремонт (КР) проводится в целях восстановления работоспособности и ресурса оборудования. При КР осуществляется полная разборка оборудования мойка и дефектоскопия деталей ремонт регулировка сборка испытание под нагрузкой и окраска. КР проводится в соответствии с планом-графиком ремонта на специализированных заводах оснащенных соответствующим технологическим оборудованием. Порядок сдачи в ремонт испытание и приемка после ремонта определяются техническими условиями на капитальный ремонт оборудования.
Организация ТО и ПР осуществляется под методическим и техническим руководством службы главного механика. Практическое проведение возлагается на базы производственного обслуживания централизованные ремонтные заводы.
Таким образом действующая система ТО и ПР оборудования предусматривает проведение комплекса мероприятий предупредительного характера направленных на поддержание оборудования в постоянной эксплуатационной готовности и обеспечивающих наибольшую производительность и высокое качество буровых работ увеличение межремонтных сроков службы снижение затрат на ремонт и эксплуатацию оборудования повышение качества ремонтных работ.
Технологический процесс капитального ремонта представляет собой комплекс технологических и вспомогательных операций по восстановлению работоспособности оборудования выполняемых в определенной последовательности и включает в себя: приемку оборудования в ремонт; моечно-очистные операции; разборку оборудования на агрегаты сборочные единицы и детали контроль сортировку и ремонт деталей их комплектацию; сборку сборочных единиц агрегатов и оборудования в целом; обкатку и испытание оборудования после сборки; окраску и сдачу оборудования из ремонта.
Сдача оборудования в ремонт производится в соответствии с графиком ППР и в эти сроки персонал готовит оборудования к сдаче.
К подготовительным работам относятся: слив масла топлива и жидкостей а также предварительная очистка осмотр и монтаж оборудования консервация. Оборудование отправляемое в ремонт должно быть полностью укомплектовано.
Очищенное оборудование поступает на разборку. От качества разборки и сохранения деталей от поверхности зависят сроки качество и стоимость ремонта. Оборудование разбирается по схеме которая вначале определяет последовательность разборки на агрегаты и сборочные единицы а затем разборку на детали. Порядок выполнения отдельных операций требования к сохранению комплектности деталей даются в виде пояснений и указаний.
Разборку выполняют на одном рабочем месте силами бригады или на нескольких рабочих местах разборочной линии. При разборке широко используют различное подъемно-транспортное оборудование. Для сокращения продолжительности и снижения трудоемкости используют механизированный инструмент гидравлические домкраты прессы и съемники. Разборку оборудования производят на специальных стендах.
После разборки детали оборудования направляются на контрольно-сортировочный участок где устанавливается их техническое состояние возможность дальнейшего использования номенклатура ремонтируемых деталей. Для контроля состояния деталей применяют следующие методы дефектоскопии: наружный осмотр и остукивание; обмер с использованием соответствующих измерительных приборов и специальные методы неразрушающего контроля для выявления скрытых дефектов. На рем. предприятиях нефтяной и газовой промышленности наибольшее применение для обнаружения скрытых дефектов нашли капиллярные методы ультразвуковая дефектоскопия и гидравлические испытания.
Капиллярные методы обнаружения скрытых дефектов основаны на капиллярном проникновении жидкости хорошо смачивающей материал детали в трещины поры и другие неплотности. К капиллярным методам относится обнаружение трещин с помощью масла и керосина. очищенный участок детали покрывают на 5 минут прогретым маслом керосином или красителем. затем тщательно вытирают и покрывают меловым раствором сушат после чего прогревают до 50°С. При наличии трещины масло выступает наружу и контуры трещины обозначаются на меловом покрытии. При люминесцентном методе вместо красителя используется флоуресцирующая жидкость.
Для выявления скрытых трещин широко применяется магнитная дефектоскопия. Деталь посыпается ферромагнитным порошком который при намагничивании детали концентрируется на трещине. На ремонтных предприятиях нефтяной промышленности широко используют ультразвуковую дефектоскопию. Сущность её заключается в способности ультразвуковых колебаний проникать вглубь материала контролируемого изделия и отражаться от дефектов являющихся нарушением сплошности материала. Ультразвуковыми колебаниями принято называть упругие механические колебания с частотой более 20 кГц. Ультразвуковая дефектоскопия осуществляется тремя методами: теневым резонансным и эхо-методом.
Наибольшее применение для контроля деталей получил импульсный эхо-метод основанный на принципе посылки в материал контролируемой детали ультразвуковых колебаний и приема отраженных волн.
На каждую машину по результатам контроля и сортировки деталей составляется дефектная ведомость на основании которой определяется содержание и объем работ по ремонту и потребность в новых деталях.
Перед сборкой вращающихся деталей или сборных единиц необходимо устранить их неуравновешенность которая вызывает вибрации повышенный износ и ускорение разрушения многих деталей. Борьба с неуравновешенностью деталей – важное условие повышение ресурса отремонтированных машин. Для уравновешивания деталей и сборочных единиц применяют балансировку.
В процессе балансировки определяют места и величины дисбаланса а затем уменьшают его до допустимого предела удаляя излишний материал или устанавливая дополнительные грузы. основными причинами неуравновешенности являются: неточность размеров формы деталей и сборки неравномерность размещения массы металла а так же неравномерный износ детали в процессе эксплуатации.
Различают статическую и динамическую неуравновешенности.
Статическая неуравновешенность возникает вследствие смещения центра тяжести относительно оси вращения и проявляется в статическом состоянии. Она свойственна деталям типа дисков т.е. таким деталям у которых диаметр превышает длину. К таким деталям относятся рабочие колеса центробежных насосов турбин компрессоров и т.д. для устранения статической неуравновешенности применяют различные методы статической балансировки: уменьшают массу тяжелой части детали утяжеляют легкую часть детали. Балансировку осуществляют на специальных стендах. Статистическая балансировка является далеко не универсальным методом уравновешивания деталей.
Динамическая неуравновешенность присущая деталям и узлам у которых длина больше диаметра и динамическая балансировка осуществляется на станках различной конструкции имеющих электрические или механические устройства для точного определения величины и места расположения неуравновешенной силы что значительно упрощает процесс балансировки.
Технологический процесс сборки при ремонте оборудования принципиально не отличается от процесса сборки при изготовлении аналогичного оборудования и заключается в последовательном соединении деталей в сборочные узлы и единицы а затем в машину. Последовательность сборки определяется технологической схемой. Схема сборки является основным оперативным документом. Наиболее простой организационной формой сборки является стационарная сборка без расчленения процесса. По этому методу машины собирают на одном рабочем месте куда поступают все детали и собранные сборочные единицы.
При сборке с операционным расчленением процесса собираемая машина остается неподвижной или перемещается в процессе сборки производимой бригадой члены которой специализируются на выполнении конкретных операций.
Завершающими операциями процесса ремонта являются приработка и испытание агрегатов и машин. Совершенно обязателен окончательный контроль после сборки агрегата в целом после чего производится приработка (обкатка) машины.
Различают холодную и горячую приработку. При холодной приработке машину испытывают без нагрузки и приводят в действия от постороннего источника энергии. При горячей приработке машину полностью собирают и прирабатывают под нагрузкой. Продолжительность приработки различна в зависимости от типа и назначения оборудования. Весь период приработки контролируется персоналом с использованием необходимых контрольно-измерительных приборов. Обычно полностью собранную машину подвергают приемочным контрольным и специальным испытаниям.
Приемочные испытания устанавливают соответствия фактических эксплуатационных характеристик машины техническим условиям и проводятся на стендах в условиях приближенных к эксплуатационным. При внесении в машину каких-либо новых элементов проводят специальные испытания. Результаты испытаний оформляются в виде акта а данные испытаний отмечаются в паспорте отремонтированной машины.
Заключение.docx
В наклонных скважинах с зенитным углом отклонения обсаженного ствола в месте забуривания более 20° применение существующих вырезающих устройств с круговым фрезерованием становится сложным вследствие нарушения центровки режущего органа под действием собственного веса и получения одностороннего щелевидного окна. Для решения этих вопросов было необходимо разработать надежные центрирующие элементы и подобрать соответствующий режим работы вырезающего устройства по фрезерованию окна в эксплуатационных колоннах имеющих зенитный угол в месте забуривания бокового ствола 20° и более. В условно-вертикальных скважинах применение клиновых отклонителей и райберов также связано со значительными осложнениями из-за наличия проблемы ориентации отклонителя.
В результате проведенной модернизации был предложен ориентированный клин-отклонитель который обеспечивает возможность забуривания бокового ствола скважины
Список литературы.docx
Анурьев В.И. Справочник конструктора-машиностроителя: т. 3. – М.: Машиностроение 1982. – 859 с.
Безопасность жизнедеятельности и промышленная безопасность: Учебное пособие под ред. Шантарина В. Д.– Тюмень: ТюмГНГУ 2001 г 308 с.
Бухаленко Е.И. и др. Нефтепромысловое оборудование: Справочник. – М.: Недра 1990. – 559 с.
Гилязов Р.М. Рамазанов Г.С. Янтурин Р.А. Технология строительства скважин с боковыми стволами. – Уфа. Монография 2002. – 290 с.
Иогансен К.В. Спутник буровика: Справочник. – 3-е изд. перераб. и доп. – М.: Недра 1990. – 303с.
Масленников И.К. Буровой инструмент: Справочник. – М.: 1989. – 430 с.
Павлов Я.М. Детали машин. – М.: Машиностроение 1987. – 534с.
Правила безопасности в нефтяной и газовой промышленности (ПБ 08-624-03 2003г.).
Северинчик Н.А. Машины и оборудование для бурения скважин. – М.: Недра 1986. – 368 с.
Сулейманов М.М. и др. Охрана труда в нефтяной промышленности. М. Недра 1980 г 392 с.
Султанов Б.З. Ишемгужин Е.И. Шамассов Н.Х. Сорокин В.Н. Работа бурильной колонны в скважине. М.: Недра 1973. – 213с.
Сызранцев В.Н. Бочарников В.Ф. Анашкина А.Е. Петрухин В.В. Савин А.Е. Методические указания к курсовому проектированию по дициплинам «Машины и оборудование для бурения нефтяных и газовых скважин на суше» «Машины и оборудование для добычи и подготовки нефти и газа на суше». – Тюмень: Нефтегазовый университет 2005. – 35 с.
Трубы нефтяного сортамента: Справочник А.Е. Сароян Н.Д. Щербюк Н.В. Якубовский и др.; Под общ. ред. А.Е. Сарояна. – М.: Недра 1987. – 488 с.
Шумова З.И. Собкина И.В. Справочник по турбобурам. – М. Недра 1970. – 191 с.
Пат.2183247 РФ МПК 7 E21B00708. Клин-отклонитель Общество с ограниченной ответственностью «НЕФТЬИНВЕСТСЕРВИС». 200013236003. Заявлено 27.04.99; Опубл. 14.05.00; Бюл.13. – 2 с.
Пат.2368753 РФ МПК E21B 708. Устройство для ориентирования клина-отклонителя в скважине Ю.А. Осипов В.И. Ванифатьев; С.В. Дмитрук; А.М. Володин; С.В. Терентьев; А.А. Степанов. 200712764903. Заявлено 19.07.07; Опубл. 27.01.09; Бюл.27. – 7 с.
Раздел 3.docx
1 Исходные данные для расчета
глубина забуривания бокового ствола ;
длина колонны бурильных труб ;
вес одного погонного метра бурильных труб ;
длина колонны утяжеленных бурильных труб ;
вес одного погонного метра утяжеленных бурильных труб ;
вес клина отклонителя с устройством ;
удельный вес бурового раствора .
2 Расчет болта на срез
Клин вместе с ориентирующим устройством спускается в скважину на колонне бурильных труб крепятся они между собой чаще всего на срезных болтах. Известно что при диаметре клина равным 137 мм усилие среза болтов для соединения клина-отклонителя и спускного клина равняется 55 кН рассчитаем необходимый диаметр болтов.
Расчет стержня при срезе проводится по формуле [2]:
где – внешняя сила действующая на стержень (болт);
– допускаемое напряжение при срезе.
Т.к. в нашем случае болт выполнен из стали 40ХН то .
Берется болт М16 из стали 40ХН.
3 Расчет болта на смятие
На смятие болт рассчитывается по формуле
где – высота участка смятия;
– допускаемое напряжение на смятие.
4 Расчет корпуса устройства на прочность
Определяем толщину стенки устройства
где – наружный диаметр устройства;
- внутренний диаметр устройства.
По формуле Барлоу находим напряжение на разрыв от внутреннего давления:
где – перепад давления в устройстве
Перепад давления при заданном расходе 18 лс находим из уравнения:
где – заданный расход бурового раствора;
– стандартный расход бурового раствора;
– перепад давления при стандартном расходе.
Стандартный перепад давления равен 15 МПа при стандартном расходе 20 лс.
Определим допускаемое напряжение материала корпуса устройства
где – временное сопротивление материала.
Т.к. корпус устройства выполнен из стали 35ХМ то [1].
Определяем коэффициент запаса прочности:
Что является намного больше допустимого следовательно корпус устройства выдержит нагрузки в процессе работы.
5 Определение страгивающей нагрузки в резьбовом соединении бурильной колонны
Под действием собственного веса колонны в резьбах трубы и муфты возникают осевые растягивающие напряжения и радиальные напряжения жатия для трубы и растяжения для муфты.
При достижении определенной величины эти напряжения способны расстраивать резьбовое соединение что выражается в выдергивании резьбы трубы из муфты.
Осевые нагрузки вызывающие расстройства резьбового соединения называют страгивающими .
Для труб с треугольной резьбой они составляют 60-75% от нагрузок вызывающих разрушение труб по телу.
Определим величину страгивающей нагрузки в бурильной колонне при проведении операции по зарезке бокового ствола при следующих параметрах:
резьба замковая з-121 гост 5286-75;
условный диаметр бурильной трубы ;
диаметр проходного сечения ;
число ниток на длине резьбы 1 дюйм 5;
средний диаметр резьбы в основной плоскости ;
предел текучести материала .
Формула для расчета страгивающей нагрузки
где – средний диаметр резьбы в основной плоскости;
– толщина стенки во впадине резьбы в основной плоскости;
– предел текучести материала;
– угол профиля (равен 60о);
– угол трения (равен 9о).
Толщина стенки во впадине резьбы в основной плоскости определяется по формуле
где – наружный диаметр резьбы в основной плоскости;
– внутренний диаметр резьбы в основной плоскости
Определяем расчетную нагрузку по формуле:
где – вес бурильной колонны;
– вес бурового раствора;
– вес клина отклонителя с устройством.
Определяем все бурильной колонны
где – вес колонны бурильных труб;
– вес колонны утяжеленных бурильных труб.
Определяем вес колонны бурильных труб:
где – вес одного погонного метра бурильных труб;
– длина колонны бурильных труб
Определяем вес колонны утяжеленных бурильных труб
где – вес одного погонного метра утяжеленных бурильных труб;
– длина колонны утяжеленных бурильных труб.
Определяем вес бурового раствора
где – площадь бурильной колонны;
– длина бурильной колонны;
– удельный вес бурового раствора.
Площадь бурильной колонны определяется
где – диаметр проходного сечения
следовательно резьбовое соединение выдержит нагрузку.
6 Определение отклоняющей силы на долоте
Рассмотрим бурильную колонну находящуюся в прямолинейной но не вертикальной скважине (рисунок 3.1).
Дифференциальное уравнение упругой линии имеет вид
где – поперечная составляющая от веса единицы длины колонны в промывочной жидкости;
– отклоняющая сила на долоте;
– продольная нагрузка.
Рисунок 3.1 – Схема к расчету низа бурильной колонны в наклонной скважине
где и – постоянные интегрирования.
где – расстояние от долота до точки касания;
– кажущийся радиус кривизны.
Подставляя граничные условия в выражение получим систему уравнений
Решая систему уравнений относительно Q и C получим
Формула устанавливает взаимосвязь составляющей реакции забоя перпендикулярной оси скважины кажущегося радиуса жесткости и веса единицы длины колонны.
Коэффициент k определяется по формуле
где – жесткость колонны.
Далее определяем поперечные составляющие колонны
где – поперечная составляющая от веса единицы длины долота с переводником;
– поперечная составляющая от веса единицы длины калибратора;
– поперечная составляющая от веса единицы длины колонны.
– распределенная нагрузка от веса горизонтальной колонны;
– масса долота с переводником;
– масса трехшарошечного долота [6];
– масса переводника [15];
– масса калибратора;
– длина долота с переводником;
– длина калибратора.
Масса долота с переводником
Распределенная нагрузка от веса горизонтальной колонны
где – масса одного погонного метра трубы НКТ с высаженными внутрь концами диаметром 73 мм;
Приведенная составляющая от веса элементов бурильной колонны
На профиль скважины существенно влияет отклоняющая сила на долоте.
Для рассмотренной компоновки она составила .
7 Определение максимального изгибающего момента
Определим реакции в точках А и Д.
Для этого составим следующие уравнения
Рисунок 3.2 – Расчетная схема КНБК эпюра изгибающих моментов и сил
Проведем проверку правильности определения реакций:
Следовательно реакции определены верно.
Построим эпюру поперечных сил ().
Определим сечение в котором момент будет максимальным (точка экстремума)
Построим эпюру изгибающих моментов ().
Определим максимальный момент
Максимальный изгибающий момент приходится на место установки калибратора.
8 Расчет резьбы на прочность
В большинстве случаев разрушение резьбы носит усталостный характер.
Усталостное разрушение резьбового соединения (от знакопеременного изгиба) происходит во многих случаях по последнему витку резьбы который находится в сопряжении.
Разрушение замкового соединения может произойти вследствие недостаточного или чрезмерного крутящего момента свинчивания.
Соединения необходимо свинчивать таким крутящим моментом чтобы при воздействии на них всех видов нагрузок предотвратилось раскрытие стыка по упорному торцу.
При этом крутящий момент свинчивания не должен создавать осевую нагрузку с напряжениями достигающими или превышающими предел текучести материала замка.
Максимально допустимую нагрузку определяют исходя из площади опасного сечения по полному витку резьбы и предела текучести
где – площадь опасного сечения ;
где – наружный диаметр резьбы в основной плоскости З-76 ГОСТ 5286-89;
– диаметр проходного отверстия.
Проверяется прочность витков резьбы на срез.
Нагрузка вызывающая срез витков резьбы (при равномерном распределении)
где – внутренний диаметр резьбы З-76 (диаметр конуса в плоскости приведения;
– коэффициент полноты для замковой стандартной резьбы З-76 ГОСТ5286-89;
– длина свинчивания резьбы;
– предел прочности материала на срез МПа.
где – предел прочности материала
Напряжение среза определяется по формуле
Срез резьбы не произойдет.
Напряжение смятия витков резьбы определяется по формуле
где – допускаемое напряжение на смятие материала;
– наружный диаметр резьбы в плоскости приведения;
Прочность обеспечивается смятие резьбы не произойдет.
Напряжение изгиба витков резьбы определяется по формуле
где – число витков резьбы.
Прочность обеспечивается разрушение не произойдет.
Раздел 1.docx
1 Технология и техника бурения боковых стволов
Основной проблемой бурения боковых стволов в настоящее время является вырезание окна в эксплуатационной колонне скважины и забуривание на начальном участке бокового ствола (рисунок 1.1) обеспечивающее надежный выход инструмента из старого ствола.
Известны два способа вскрытия окна применяемые на практике:
вырезание окна с помощью райбера по клиновому отклонителю;
полное вырезание участка эксплуатационной колонны с последующей установкой цементного моста.
На базе опыта бурения боковых стволов установлены границы применения обоих способов.
В наклонных скважинах с зенитным углом отклонения обсаженного ствола в месте забуривания более 20° применение существующих вырезающих устройств с круговым фрезерованием становится сложным вследствие нарушения центровки режущего органа под действием собственного веса и получения одностороннего щелевидного окна. Для решения этих вопросов необходимо разработать надежные центрирующие элементы и подобрать соответствующий режим работы вырезающего устройства по фрезерованию окна в эксплуатационных колоннах имеющих зенитный угол в месте забуривания бокового ствола 20° и более. В условно-вертикальных скважинах применение клиновых отклонителей и райберов также связано со значительными осложнениями из-за наличия проблемы ориентации отклонителя. Требуется использовать дорогостоящее оборудование для навигации. Поэтому клиновые отклонители становятся предпочтительнее при зенитных углах основного ствола более 20°.
В этих условиях для ориентации возможно применение серийно выпускаемых приборов.
а – вырезание окна в эксплуатационной колонне; б – вырезание части эксплуатационной колонны; в – извлечение верхней незацементированной части эксплуатационной колонны; г – комбинированный способ бурения бокового ствола; д – бурение бокового ствола с открытого забоя; 1 – клин-отклонитель; 2 – цементный мост
Рисунок 1.1 – Технологические способы забуривания боковых стволов:
Забуривание через окно в обсадной колонне проводят в три этапа:
установка клинового отклонителя;
забуривание бокового ствола.
2 Анализ конструкция клиньев-отклонителей отечественного производства
Клин предназначен для обеспечения необходимого отклонения вырезающих фрез и фрезеров-райберов от оси основного ствола скважины при прорезании «окна» в эксплуатационной колонне а также для отклонения режущего и бурильного инструмента при бурении дополнительного ствола скважины. Клин-отклонитель после спуска остается в скважине постоянно.
Особенность клина-отклонителя серии КОП состоит в том что корпус узла фиксации после подготовки клина-отклонителя к спуску в скважину становится связанным с желобной частью через шарнирное соединение а подвижный элемент служащий для выдвижения расклинивающей плашки находится внутри этого корпуса и срабатывает только при непосредственной опоре клина-отклонителя на забой.
Тем самым исключается преждевременное срабатывание узла фиксации клина-отклонителя при его транспортировки до забоя которое может произойти из-за разной толщины стенок обсадной колонны или недостаточной подготовки колонны для проведения работ по зарезке бокового ствола.
При посадке на забой под весом бурильного инструмента клин-отклонитель принудительно изгибается относительно оси шарнира таким образом что верхняя часть желоба прижимается к одной стороне колонны а нижняя часть желоба – к другой что обеспечивает лучшее дальнейшее прохождение инструмента в интервале установки клина-отклонителя а также возможность установки данного клина-отклонителя в интервалах с большим углом наклона ствола скважины.
Основной недостаток серийных отечественных отклонителей заключается в низкой надежности их фиксации в эксплуатационной колонне.
В процессе бурения бокового ствола часто наблюдались случаи произвольного поворота клинового отклонителя вокруг своей оси и радиальные смещения его верхней кромки.
Повороту отклонителя вокруг своей оси способствует низкая надежность фиксации сухарей якоря которые под действием тех или иных сил могут срываться с поверхности колонны.
Это приводит к необходимости перебуривания бокового ствола.
Существует множество конструкций отклонителей которые отличаются друг от друга формой рабочей части клина и способом их фиксации в колонне.
Наибольшее распространение при создании окна получили стационарные клиновые отклонители.
Такие отклонители фиксируются в колонне на расчетной глубине путем установки на цементный мост металлический забой или стык муфтового соединения обсадной колонны.
В отечественной практике наибольшее распространение получили отклоняющие клинья с фиксацией корпуса в колонне с помощью плашек устанавливаемых на цементный забой.
За рубежом чаще применяют плашечное закрепление с установкой отклоняющего клина в месте стыка труб как более экономичный способ.
В нашей стране применялись отклонители с плоской и желобообразной формой рабочей части клина.
Эти конструкции из-за ненадежности крепления в колонне не могли обеспечить заданных параметров забуривания боковых стволов.
Помимо плашечного клинового отклонителя существуют заливные отклонители однако основной их недостаток состоит в том что в заливаемых отклоните лях канал для подачи цементного раствора выполнен по оси направляющего клина и ввиду малого угла направляющей плоскости (15÷3°) центральный цилиндрический канал в направляющей плоскости клина приобретает вид продольного окна длина которого намного превышает диаметр отверстия.
Указанное является причиной отклонения вырезающего инструмента от направляющей плоскости
В связи с этим создана конструкция клинового отклонителя позволившего избежать указанные осложнения.
Эта конструкция обеспечила надежно фиксацию отклонителя путем его полного цементирования в эксплуатационной колонне.
Конструкция включает дополнительный спускной клин примыкающий к основному и образующий с последним цилиндрическую поверхность.
Оба клина снабжены каналами для прохождения цементного раствора.
После спуска отклонителя до упора в цементный мост и частичной разгрузки веса колонны закачивают цементный раствор до полного заполнения им клина-отклонителя.
Затем производят полную разгрузку веса колонны в результате чего срезаются шпильки соединяющие отклоните ль со спускным клином.
После этого выполняют подъем спускного клина и последующий спуск райбера после затвердевания цемента.
Основной отклонитель при этом остается надежно зафиксированным в эксплуатационной колонне.
3 Анализ конструкций клиньев-отклонителей зарубежного производства
За рубежом широко применяются уипстоки представляющие собой комбинацию клина с шарнирным роторным отклонителем а также кривые переводники.
Реже применяют эксцентричные отклонители обычно вместе с гидравлическими забойными двигателями.
В последнее время все более широко используются гидравлические и гидромеханические отклонители в том числе с дистанционным управлением.
Серийный выпуск уипстоков налажен фирмой «Эй-Уан Бит энд Тул Ко.» (г. Оклахома-Сити штат Оклахома США).
Почти все они состоят из двух секций соединенных между собой шарниром.
Шарнир при помощи болтового соединения настраивается на определенное смещение.
Обе секции изготавливаются отливкой из легированной стали.
Одна из секций выполняется с вогнутой направляющей поверхностью по которой скользит зарезное обычно алмазное долото формирующее новый ствол.
В зависимости от назначения и условий зарезки нового ствола уипстоки распределяются на пять основных типов:
для твердых и крепких забоев;
для выпрямления искривленных необсаженных участков скважин;
для посадки образования окна и нового ствола в скважине закрепленной обсадными трубами;
для соединения с пакером или посадки в него;
для жесткого закрепления цементом и отвода ствола в заданном направлении при сложных ситуациях в скважине.
Уипстоки первого и последнего типов могут быть изготовлены в жесткой модификации без шарнира.
Все уипстоки выпускаются 18 размеров диаметрами от 889 до 2921 мм.
Фирма «Истмен Уипсток Инк.» (г. Хьюстон штат Техас США) также изготовляет уипстоки но иной чем описанные выше конструкции в основном трубные желобообразные.
Она же выпускает кривые переводники с наружными диаметрами от 127 до 2413 мм в 12 размерах с различными углами отклонения оси резьбы относительно оси переводника.
Этой же фирмой выпускаются эксцентричные отклонители «Ребель» для искривления скважин в крепких породах на угол не менее 10°.
Они изготавливаются из немагнитных УБТ с накладками и выпускаются шести размеров под скважины диаметрами от 1524 до 3111 мм.
Указанная фирма выпускает также инструмент для направленной ориентации (ДОТ).
Он устанавливается непосредственно над забойным двигателем и включает кривой переводник трубный немагнитный корпус вставной патрон опускаемый в корпус на канате самописец и ориентирующее устройство.
В процессе бурения этот инструмент фиксирует время зенитный угол искривления ориентацию забоя и текущее смещение от заданного положения.
Трубные уипстоки и отклонители типа Р-1 изготавливаются фирмой «Кэвинз Ойл Велл Тулз» (г. Лонг-Бич штат Калифорния США).
Кривые переводники продаются румынской фирмой «Индустриалэкспортимпорт-Петромин» четырех размеров наружными диаметрами от 1206 до 2413 мм с углами отклонения γ равными 1° 1°30' 2° 2°30' и 3°.
Кривые переводники с углом γ от 1о до 2о30’ выпускает и французская фирма «Дрилстар».
Английская фирма «Даррон Ойл Тулз» изготовляет кривые переводники с углом γ от 1° до 3°30' и эксцентричные отклонители с дугообразными боковыми накладками.
Эксцентричные отклонители с боковыми накладками выпускаются также и фирмой «Боб Курне Ко». (г. Лафейетт штат Луизиана США).
Корпорация «Смит Интернейшнл Инк.» изготовляет корпуса забойного двигателя с односторонним упругим утолщением и гидромеханические шарнирные отклонители Дайне Флекс которые управляются давлением промывочной жидкости или другого текучего вещества (флюида).
Отклонитель Дайне Флекс состоит из цилиндрического корпуса подпружиненного верхнего поршня соединенного с ним нижнего поршня кулачкового механизма шарнира и вставного затвора.
Последний обычно бросают в бурильную колонну и под давлением очищающего агента он садится в свое гнездо.
Давление очищающего агента заставляет поршни опуститься поворачивая при помощи кулачкового механизма нижнюю часть отклонителя вокруг шарнира.
Возникающее при этом боковое усилие прижимает долото к стенке скважины.
Извлекают затвор при помощи овершота на канате.
Описанный отклонитель допускает чередовать бурение с отклонителем и без отклонения ствола скважины без подъема бурильной колонны.
Спускоподъемные операции производят при нейтральном положении отклонителя.
Отклонение в заданном азимутальном направлении обеспечивают ориентированным спуском бурильной колонны.
Той же корпорацией изготовляются устройства (точнее системы) с дистанционным забойным ориентированием с поверхности: Би Джей Теледрифт и Би Джей Тилеориентайр.
4 Способы ориентирования клиньев-отклонителей
В основном в средствах контроля и измерения параметров ствола скважины и положения отклоняющих КНБК используются гидравлический кабельный и электромагнитный каналы связи. Измеряются следующие параметры: зенитный угол азимут положение отклонителя и глубина спуска системы (при оснащении глубиномером).
Для измерения фактической траектории обсаженного ствола скважины параметров дополнительного ствола и ориентирования отклоняющей КНБК внутри обсадной колонны и в открытом стволе используются гироскопические инклинометры и инклинометрические телеметрические системы ИГ-36 ИГ-50 ДНГ «Гидрокурсор» «SRO» ЭТО-2М МСТ-45 «Radius» 3TC 108-017.
В гироскопическом инклинометре отклонение от вертикали определяется измерительным потенциометром и совпадает с углом образованным вертикальной и продольной осями зонда.
Измеряемый азимут – это угол образованный проекцией вертикальной оси зонда на горизонтальную плоскость и ранее выбранным направлением.
Сигналы отклонения азимута поступающие из зонда посредством каротажного кабеля передаются на пульт измерения.
Измерительная часть системы образована компенсационными потенциометрами отклонителя и азимута с индикаторным микроамперметром.
Питающая часть системы оснащена разветвленным входом для питания прибора как постоянным так и переменным током.
Трансформаторные и выпрямительные контуры питающей системы служат для преодоления падений вызванных сопротивлением каротажного кабеля.
Конструкции приборов рассчитаны на подключение каротажных кабелей разных диаметров с числом жил не менее трех.
Для соблюдения правильных соотношений напряжения в приборе должно быть обеспечено определенное сопротивление проводов в используемом кабеле что достигается за счет подсоединения вспомогательных сопротивлений.
Для обеспечения более быстрого разбега гироскопа до рабочих оборотов служит вспомогательный источник питания установленный в зонде.
Инклинометрическая телеметрическая система позволяет проводить следующие операции:
ориентирование отклоняющей компоновки по заданному азимуту в стволе скважины путем измерения направления действия отклонителя относительно апсидальной плоскости;
определение угла закручивания бурильной колонны под действием реактивного вращающего момента забойного двигателя и его учет при бурении скважины с использованием отклоняющего инструмента;
проведение инклинометрических измерений непосредственно в процессе проводки скважины.
Комплект телеметрической системы типа СТТ (рисунок 1.2) включает следующие узлы: глубинный блок телеметрической системы глубинное измерительное устройство наземный пульт телеметрической системы наземное измерительное устройство присоединительный фильтр.
Связь глубинной аппаратуры с наземной может осуществляться по проводному каналу связи сбросового типа выполненному в виде стандартного каротажного кабеля снабженного контактными разъемами.
– эксцентрично расположенные грузы датчиков соответственно азимута и зенитного угла; 2 – груз рамы; 4 – заданное направление; 5 – метка отклонителя; 6 7 – реперная ось соответственно отклонителя и глубинного измерительного устройства; 8 – метка «0» глубинного измерительного устройства; 9 – след апсидальной плоскости; φ3 – проектный азимут скважины; – угол смещения определяемый как угол между меткой «0» глубинного измерительного устройства и направлением изгиба отклонителя; – угол поворота бурильной колонны; – угол установки отклонителя; 3 – заданный угол установки отклонителя; φ – фактический азимут скважины
Рисунок 1.2 – Схема измерительной части телеметрической системы СТТ:
Возможны два варианта спуска линии связи: через уплотнение вертлюга с использованием узла ввода кабеля в вертлюг и через специальное устройство для ввода кабеля в составе бурильной колонны.
В глубинном контейнере размещены датчики для измерения азимута угла положения отклонителя и зенитного угла.
Принцип действия датчика азимута основан на применении магнитного чувствительного элемента в виде стержня устанавливающегося по направлению магнитного меридиана.
Чувствительный элемент связан с ротором синусно-косинусного вращающего трансформатора работающего в режиме фазовращателя.
Работа датчика наклона основана на применении эксцентричного груза центр тяжести которого всегда находится на вертикали проходящей через ось груза.
Угол поворота посредством ротора трансформатора связанного с грузом преобразуется в фазу выходного сигнала пропорционального зенитному углу скважины.
Одному механическому градусу поворота ротора соответствует изменение фазы выходного сигнала на 6°.
Принцип действия датчика положения отклонителя основан на повороте рамки с эксцентричным грузом и укрепленными на ней датчиками азимута и наклона.
Угол поворота рамки преобразуется трансформатором в фазу выходного сигнала.
Одному механическому градусу соответствует изменение фазы выходного сигнала на 1°.
Пятидесятипериодные сигналы передаваемые датчиками имеют различную фазу (от 0 до 360°) и в зависимости от изменений измеряемого параметра поступают в глубинный передающий блок который осуществляет последовательный опрос во времени глубинных датчиков формирует суммарный широтно-импульсный модулированный сигнал и передает его в токопровод.
Типовая схема операций при ориентировании отклоняющих компоновок в вертикальных и наклонных стволах скважины следующая:
До сборки отклонителя с телеметрической системой на нижнем переводнике ее корпуса строго на верхней образующей наносится метка «0» соответствующая нулевому показателю датчика положения отклонителя.
После сборки отклонителя метка с верхнего переводника отклонителя переносится на нижний переводник телеметрической системы.
Измеряется угол от метки показывающей направления изгиба отклонителя до метки «0» телеметрической системы по направлению движения часовой стрелки если смотреть сверху вниз (рисунок 1.3).
А – при А > 360°; В – при А 360°; 1 – метка «0» глубинного измерительного устройства; 2 – заданное направление; 3 – метка отклонителя; 4 – апсидальная плоскость
Рисунок 1.4 – Схема ориентирования отклонителя:
При ориентировании отклонителя в стволе скважины с зенитным углом более 3° проводятся следующие измерения (рисунок 1.2):
определяют сумму заданного угла установки отклонителя и угла смещения меток «Отклонитель» и «0» то есть A = 3 + где 3 – заданный угол установки отклонителя; – угол смещения меток «Отклонитель» и «0»;
поворотом бурильной колонны достигают показаний цифрового индикатора «Отклонитель» равных ранее вычисленному значению угла А (если угол А > 360° то из него нужно вычесть 360°);
поворот бурильной колонны необходимо вести по направлению движения часовой стрелки;
после поворота бурильной колонны для снятия упругих деформаций колонны несколько раз приподнимают ее и опускают контролируя по индикатору «Отклонитель» полученное значение (в случае его изменения поворотом колонны достигают нужных показателей).
Для ориентирования отклонителя в вертикальном стволе скважины необходимо (см. рисунок 1.3):
определить сумму заданного азимута и измеренного угла смещения меток «Отклонитель» и «0» то есть A = 3 + где 3 – заданный азимут искривления ствола скважины; - угол смещения меток «Отклонитель» и «0»;
установить тумблер ОА (азимут отклонителя) на наземном пульте в верхнее положение;
поворотом бурильной колонны добиться показаний индикатора «Отклонитель» равных полученному значению А (в процессе бурения поддерживать указанные показания индикатора «Отклонитель»);
после набора зенитного угла по метке отклонителя тумблер ОА выключить и дальнейшее ориентирование отклонителя производить для условий наклонной скважины.
Также для ориентирования клина-отклонителя при установке его в момент спуска в скважину существует еще несколько способов:
метод визированного спуска;
ориентирование инструмента (колонны труб) при помощи меток и сумматора.
Меридианный способ ориентирования отклоняющих приспособлений (клина-отклонителя) осуществляется с помощью аппаратов забойного визирования и телеметрии.
Визированный спуск клина-отклонителя осуществляется с помощью двух визирных трубок.
Перед ориентированным спуском клина-отклонителя отбивается направление (репер) проектного азимута искривления ствола скважины на неподвижной части ротора.
Первая визирная трубка закрепляется под отклонителем так чтобы ее оптическая ось лежала в плоскости действия отклонителя.
При помощи визирной трубки поворотом инструмента (первой свечи) отклонитель при помощи ротора устанавливается таким образом чтобы нить визирной трубки совпала с нитью (риской) репера.
Вторая визирная трубка устанавливается на верхнем замке свечи и после наводки ее нити на репер без движения ротора фиксируется стопорным винтом.
Инструмент снимается с клиньев или элеватора снимается нижняя визирная трубка и свеча спускается в скважину и снова ставится на клинья при этом ведется наблюдение чтобы не был сбит хомут визирной трубки (положение зафиксированное наверху).
Затем навинчивается и закрепляется очередная свеча визирная трубка поворотом ротора наводится на репер и фиксируется верхняя визирная трубка.
Снимается нижняя визирная трубка и спускается инструмент в скважину на длину свечи.
Далее при спуске клина-отклонителя до заданной глубины при спуске последующих свечей все операции ориентации повторяются в описанной выше последовательности.
Принцип действия ориентированного спуска инструмента при помощи меток и сумматоров.
В этом способе каждая спускаемая в скважину свеча инструмента должна иметь на замковых (муфтовых) концах по одной образующей четкие метки которые наносятся с помощью специального шаблона.
Аналогично визированному спуску отклонителя отбивается направление (репер) проектного азимута искривления ствола скважины на неподвижной части ротора.
Во время спуска колонны в скважину на нижнем замке-муфте инструмента навинченной на отклонитель наносится метка-крест точно против риски имеющейся на поверхности отклонителя которая по направлению совмещается с репером.
Затем замеряется угломером дуга между меткой и меткой-крестом на нижнем замке и при спуске свечи в скважину эта метка-крест наносится на верхний замок этой свечи в том же направлении от существующей на ней метки.
После навинчивания последующей свечи метка-крест верхнего замка переносится на нижний замок навинченной свечи и замеряется дуга между меткой и вновь нанесенной меткой-крестом которая переносится на верхний замок после спуска свечи в скважину.
И так в такой последовательности по метке-кресту на верхнем замке последней трубы (свечи) определяется направление отклонителя в скважине.
После чего при необходимости метка-крест верхнего замка (муфты) последней свечи поворотом ротора ориентируется на репер.
Рекомендуемые чертежи
- 24.01.2023