Барабанный тормозной механизм с пневмоприводом с компенсатором износа для автомобиля КамАЗ 55102




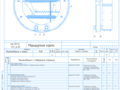
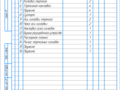
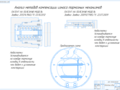
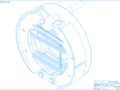
- Добавлен: 04.11.2022
- Размер: 8 MB
- Закачек: 2
Описание
Состав проекта
![]() |
![]() |
![]() ![]() ![]() |
![]() ![]() ![]() |
![]() ![]() ![]() |
![]() ![]() ![]() |
![]() ![]() ![]() |
![]() ![]() ![]() |
![]() ![]() ![]() |
![]() ![]() ![]() |
![]() ![]() ![]() |
![]() ![]() ![]() |
![]() ![]() ![]() |
![]() ![]() ![]() |
![]() |
![]() |
![]() |
![]() |
![]() |
![]() |
![]() |
![]() |
![]() |
![]() ![]() ![]() |
![]() |
![]() |
![]() |
![]() |
![]() |
![]() |
![]() |
![]() |
![]() ![]() ![]() |
![]() |
![]() |
![]() |
![]() |
![]() |
![]() |
![]() |
![]() |
![]() |
![]() |
![]() |
![]() ![]() ![]() ![]() |
![]() |
![]() ![]() ![]() |
![]() |
![]() |
![]() |
![]() |
![]() ![]() ![]() ![]() |
![]() ![]() ![]() ![]() |
![]() ![]() ![]() ![]() |
![]() ![]() ![]() ![]() |
![]() ![]() ![]() ![]() |
![]() ![]() ![]() ![]() |
![]() ![]() ![]() |
![]() ![]() ![]() |
![]() |
![]() ![]() ![]() |
![]() ![]() ![]() ![]() |
![]() ![]() ![]() ![]() |
![]() ![]() ![]() ![]() |
![]() ![]() ![]() |
Дополнительная информация
введение+.doc
Доля грузооборота обслуживаемого АТ в мире увеличилась с 508 до 706%; при этом доля грузооборота железнодорожного транспорта как основного конкурента АТ сократилась с 278 до 138% по итогам 2002 г. Сокращение доли обслуживаемого грузооборота произошло и по другим видам транспорта. Приоритетную роль АТ сохраняет и по видам перевозок в странах Европейского Союза. В общем объеме перевозок грузов в мире осуществляемых всеми видами транспорта доля АТ составляет 546% а в перевозках пассажиров - 527%.
Барабанные тормоза используются на многих грузовых автомобилях реже — легковых машинах и мотовездеходах. Главное преимущество барабанного тормозного механизма — в том что его мощность (определяемую площадью пятна контакта колодок с поверхностью барабана) можно очень легко повышать за счёт увеличения как диаметра барабана так и его ширины (в то время как дискового — только за счёт увеличения диаметра диска который в большинстве случаев ограничен размером обода колеса внутри которого тормозной диск установлен). Это позволяет даже при не слишком высокой удельной эффективности (тормозное усилие на единицу площади колодок) достичь очень высоких абсолютных значений тормозного усилия необходимых для замедления и остановки тяжёлого транспорта вроде грузовиков или автобусов. Барабанный механизм сравнительно хорошо защищён от попадания воды и пыли его колодки намного меньше изнашиваются на запылённой или грунтовой дороге чем открыто установленные колодки дискового механизма что делает его более долговечным и вообще более подходящим для плохих дорожных условий. Использование барабанных тормозов упрощает оснащение автомобиля стояночным тормозом. Барабанные тормоза не выделяют много тепла что делает возможным применение сравнительно дешёвых безопасных в обращении и не гигроскопичных тормозных жидкостей на масло-спиртовой основе (ЭСК БСК и подобные) имеющие низкую температуру кипения.
Рецензияооо.doc
выполненный Королевым Андреем Сергеевичем студентом группы НТС_Б-81 кафедры К4-Кф автомобиле- и тракторостроения по направлению подготовки 190100.62 Наземные транспортные системы Калужского филиала государственного образовательного учреждения высшего профессионального образования «Московский государственный технический университет имени Н.Э. Баумана»
Квалификационная работа бакалавра состоит из 9 листов графической части формата А1 90 листов расчётно-пояснительной записки формата А4.
Квалификационная работа направлена на решение вопросов совершенствования
технологической схемы и конструкции тормозного механизма автомобиля КамАЗ 55102.
Разработка технологической схемы и конструкции тормозного механизма автомобиля КамАЗ 55102 позволила снизить износ тормозного механизма и повысить надежность.
В квалификационной работе бакалавра выполнены: обоснование актуальности темы квалификационной работы; выполнен расчет тормозного механизма; анализ методов компенсации износа; расчет на прочность выносливость; анализ напряжений перемещений запаса прочности; разработка последовательности сборки изделия; исследование показателей разработанной системы.
Графическая часть дипломного проекта достаточно раскрывает его содержание структура работы соблюдена выстроена логично и грамотно.
Цель работы автором достигнута тема раскрыта основные части проекта связаны между собой выполненный объем работы соответствует заданию на разработку проекта. Выполненный дипломный проект удовлетворяет требованиям правил по выполнению и оформления проектно-конструкторской документации.
Выполненная работа удовлетворяет требования правил проектно-конструкторской документации который в целом заслуживает оценки «отлично» а его автор Королев Андрей Сергеевич присвоения степени бакалавра по направлению подготовки 190100.62 Наземные транспортные системы.
Старший преподаватель кафедры Механизация сельскохозяйственного производства КФ РГАУ-МСХА им. К.А.Тимирязева Шаповалов А.П.
Заключение+.doc
Проделанной работой были достигнуты следующие результаты:
в результате анализа тормозной системы было выявлено слабое место системы;
в результате патентного обзора была определена наиболее эффективная схема улучшения тормозного механизма;
в результате анализа темы выявлены пути интеграции компенсатора износа в тормозной механизм;
разработана маршрутная карта сборки изделия;
произведен анализ конструкции на прочность;
произведен математический расчет параметров тормозного механизма;
Все полученные в ходе выполнения дипломного проекта результаты имеют технологическое обоснование и при возможности их финансирования могут быть воплощены в действительности.
эконом часть+.doc
1 Обоснование необходимости модернизации механизма
Модернизация механизма состоит в установке компенсатора износа. Это обуславливается тем что грузовые автомобили используются в более тяжелых условиях чем легковые автомобили в процессе эксплуатации поломки могут произойти на достаточно отдаленных от ремонтных мастерских местностях а более важным фактором является безопасность при движении как самого водителя так и груза.
2 Существующие аналоги механизмов на рынке
Существующим аналогом механизма является тормозной механизм заднего тормоза автомобиля Volkswagen golf2. По сравнению с разрабатываемым механизмом golf2 оснащен гидроприводом вместо пневматического. В остальном принцип действия этих механизмов не различается с разностью того что разрабатываемый механизм предполагает более высокие нагрузки при торможении.
Рис. 4.1 – Аналогичный механизм компенсации износа тормозов.
3 Выпуск автомобилей
На 2012 год автомобильным заводом «КамАЗ» производиться около 50000 автомобилей. На множестве из этих автомобилей возможно установить разрабатываемый тормозной механизм.
4 Среда эксплуатации
Средой эксплуатации являются дороги вне города т.к. вслед за федеральным законом о запрете на въезд на МКАД многотонных грузовиков в дневное время последовало подобное распоряжение администрации г.Калуги о запрете въезда многотонных грузовиков на городские улицы в дневное время.
4.1 Влияние среды эксплуатации
Множество факторов влияет на работу тормозных механизмов вне города. К таким относятся: пыль и грязь которые может ослабить работу тормозов при попадании в полость тормозного барабана; большие нагрузки на тормозной барабан при торможении на спусках; ударные нагрузки на автомобиль при езде по кочкам и бездорожью.
6 Калькуляция затрат
6.1 Материальные затраты
Таблица 4.6.1 – материальные затраты на детали исходного изделия (без применения компенсатора износа)
Ось тормозной колодки 2шт
Накладка тормозной колодки 4шт
Ролик колодки в сборе
Чека оси тормозной колодки 2шт
Рычаг тормозных колодок
Таблица 4.6.2 – материальные затраты на детали для модернизации изделия
На производство 1 изделия уходит 100 кВт Ээнергии стоимостью 4 руб.
6.2 Трудовые затраты и затраты на социальное страхование
изделие выпускается за 3 дня при условии работы рабочими в 3 смены с оплатой 1500 руб. за смену с учетом социального страхования ПФР (30 %) ФОМС (5.1 %) ФСС (2.9 %) .
Итого 13905 руб.изд.
6.3 Затраты на аренду помещения
Используется арендуемое помещение площадью 20 м2 стоимостью 400 руб.мес.
Итого 800 руб.мес. или 80 руб.изд.
Себестоимость оригинального изделия составляет 19741 руб. Себестоимость улучшенного изделия составляет 20651 руб. Соотношение 100:104. Это улучшение будет практически незначительно по стоимости выше чем оригинальное изделие но вследствие этого возможно повысить срок службы ответственных деталей тормозного механизма при осуществлении своевременного ТО и замены таких менее ответственных деталей как тормозные накладки и пружины. Срок службы тормозных механизмов возрастет со среднего значения эксплуатации до отказа 50 тыс. км. до 70 тыс. км. пробега автомобиля соотношение 100:140.
Ekologia_DIPLOM+.doc
1 Обеспечение безопасности труда при изготовление тормозного механизма для КамАЗ 55102
Одной из важнейших составляющих охраны труда является защита от вредных производственных факторов которые негативно влияют на состояние здоровья работников. Отклонения от допустимых условий деятельности вызывающие эти негативные факторы отрицательно влияют на производительность труда ухудшают самочувствие приводят к травмам заболеваниям а иногда и к гибели людей.
В связи с этим весьма актуальными являются анализ опасных и вредных факторов на рабочем месте а также разработка мероприятий направленных на обеспечение безопасных и комфортных условий труда.
При производстве стальных механических изделий возможно охарактеризовать воздействие на работников следующих опасных и вредных производственных факторов:
повышенный уровень шума на рабочем месте;
несоответствие нормам параметров микроклимата;
повышенное содержание вредных веществ в воздухе рабочей зоны
недостаточная освещенность рабочей зоны;
1.1 Обеспечение защиты от шума
Шум отрицательно влияет на организм человека и в первую очередь на его центральную нервную и сердечнососудистую системы. Длительное воздействие шума снижает остроту зрения и слуха повышает кровяное давление. Кроме того при действии шума снижаются работоспособность сосредоточение внимания точность выполнения работ связанных с приемом и анализом информации производительность труда
Шумом называют всякий нежелательный звук. Длительное воздействие интенсивного шума (выше 80 дБА) на человека приводит к частичной или полной потере слуха. В зависимости от длительности и интенсивности воздействия шума происходит большее или меньшее снижение чувствительности органов слуха которое выражается либо:
а) во временном смещении порога слышимости которое исчезает после окончания воздействия шума;
б) в необратимой потере слуха (тугоухость) характеризуемой постоянным изменением порога слышимости.
Допустимый уровень шума регламентируется в соответствии с [31]. При нормирование шума определяют следующие параметры:
) уровень звукового давления (дБ) в октавных полосах частот со среднегеометрическими частотами 31.5 63 125 250 500 1000 2000 4000 8000 Гц;
) уровни звукового давления (дБ);
На рассматриваемом рабочем месте шум непостоянный. Источником шума является фрезерно-сверлильный станок JET JMD-45PF. Шум действует на рабочего в течение 8 часов с перерывами. Шум измеряли в заводской лаборатории с помощью шумомера ВШВ – 003 с октавными фильтрами. Получены следующие значения уровней звукового давления которые сравниваются с нормативными значениями (таблица 5.1):
Таблица 5.1 – Замеренные уровни звукового давления
Уровни звукового давления дБ в октавных полосах со среднегеометрическими частотами Гц.
Допустимый уровень звукового давления
Фактический уровень звукового давления
Из приведенных данных видно что фактический уровень звукового давления и эквивалентный уровень звука не соответствуют требованиям [32].
Уровень шума в лаборатории в течение рабочего дня непостоянен. При этом в течение одного часа действует шум с уровнем звука 769 дБА в течение следующих двух часов с уровнем звука 79 дБА остальное время 75 дБА. Учитывая данный факт гигиеническую оценку уровня шума необходимо производить по эквивалентному уровню шума.
где – относительное время воздействия шума класса i в процентах от общего времени работы
– уровень звука (дБа) шума класса i.
Как видим для постоянных рабочих мест и рабочих зон лаборатории имеет место превышение предельно допустимых уровней по эквивалентному уровню шума на 9 дБА. Значит рабочее место по показателю уровня шума относится к классу условий труда 3.2 – вредный.
Для снижения уровня шума в лаборатории необходимо проводятся технические мероприятия:
- устранить причины возникновения шума или снижение его в источнике;
- ослабить шум на путях от источника;
- провести непосредственную защиту рабочих.
Наиболее эффективным средством снижения шума является замена шумных технологических операций на малошумные или полностью бесшумные однако этот путь борьбы не всегда возможен поэтому большое значение имеет снижение его в источнике. Снижение шума в источнике достигается путем совершенствования конструкции или схемы той части оборудования которая производит шум использования в конструкции материалов с пониженными акустическими свойствами оборудования на источнике шума дополнительного звукоизолирующего устройства или ограждения расположенного по возможности ближе к источнику.
Одним из наиболее простых технических средств борьбы с шумом на путях передачи является звукоизолирующий кожух который может закрывать отдельный шумный узел машины.
Значительный эффект снижения шума от оборудования дает применение акустических экранов отгораживающих шумный механизм от рабочего места или зоны обслуживания машины.
Применение звукопоглощающих облицовок для отделки потолка и стен шумных помещений приводит к изменению спектра шума в сторону более низких частот что даже при относительно небольшом снижении уровня существенно улучшает условия труда.
Для снижения уровня шума поставим звукоизолирующую перегородку. Рассчитаем толщину звукоизолирующей перегородки для снижения уровня звукового давления по методике [33]. Максимальное превышение уровня звукового давления наблюдается на частоте 4000 Гц (измеренное значение составляет – 75 дБ допустимый уровень – 66 дБ).
Эффективность звукоизоляции однородной перегородки (дБ) рассчитывается по формуле:
где -масса 1 изолирующей перегородки кг; - частота Гц;
Масса звукоизолирующей перегородки определяется по формуле:
где - толщина звукоизолирующей перегородки мм; - плотность звукоизолирующего материала ;
Тогда толщина звукоизолирующего материала определяется как:
Значит чтобы снизить уровень звукового давления на 23 дБ необходимо установить звукоизолирующую перегородку (из алюминия) толщиной = 11 мм.
Таблица 5.2 – Параметры микроклимата в механическом цехе.
Наименование параметра
Значение измеренного параметра фактическое
Нормативные показатели
Относительная влажность %
Скорость движения воздуха не более мс
Параметры соответствуют требованиям [34] для работы на предприятии.
2 Обеспечение нормируемого содержания вредных веществ в воздухе рабочей зоны
При операции фрезерования и сверления стали не имеет прямого химического воздействия на материал следовательно разрушение материала не происходит. Выделение вредных веществ в рабочую зону не осуществляется следовательно Дополнительных мер защиты разрабатывать не нужно.
2.1 Обеспечение освещенности в рабочей зоне
Операции по механической обработки резины не требует особой точности зрительной работы. Работа относится к VIII (б) разряду зрительной работы [35] имеющиеся цеховое освещение обеспечивает необходимое освещение на рабочем месте.
2.2 Обеспечение безопасности окружающей среды при изготовлении колесного движителя для трактора
В результате производственной и хозяйственной деятельности на предприятии образуются отходы V и IV класса опасности.
Таблица 5.3 – Классы отходов образующихся на предприятии.
Наименование отходов
Лом стальной несортированный
Абразивно-металлическая пыль
2.3 Расчет абразивно-металлической пыли
Таблица 5.4 – Образование отходов абразивно-металлической пыли.
Опасные свойства отхода
Класс опасности отхода
Металлообработка абразивная (по тому ПДВ)
данные не установлены
Формула расчета нормативного количества абразивно-металлической пыли:
M = Q * d (1-d) (5.2.1)
Q - валовый выброс абразивно-металлической пыли по данным проекта ПДВ тгод;
d - степень очистки на ПГУ (в пылеулавливающем аппарате) по
данным проекта ПДВ доли от 1.
Q=10.000000-Валовый выброс по ПДВ
d=0.40-Степень очистки на ПГУ
Наименование ПГУ: "ПГУ1
M=06667-Нормативная масса т
3 Меры при хранения отходов
На территории предприятия организованы места временного хранения (накопления) отходов откуда они по мере накопления вывозятся на предприятия осуществляющие переработку использование обезвреживание или захоронение отходов.
При организации мест временного хранения (накопления) отходов приняты меры по обеспечению экологической безопасности. Оборудование мест временного хранения (накопления) проведено с учетом класса опасности физико-химических свойств реакционной способности образующихся отходов а также с учетом требований соответствующих ГОСТов и СНиП.
Отходы хранятся на открытых местах временного хранения (накопления) отходов.
Поскольку размещаемые отходы по своей природе и принятых способах хранения практически не выделяют в атмосферный воздух вредных веществ и не загрязняют почву а также подземные и поверхностные воды количества временного накопления отходов до их вывоза или использования определены из соображений пожарной безопасности правил содержания территории целесообразности сроков реализации технологических возможностей перерабатывающего оборудования в преобладающем большинстве случаев возможностями транспорта.
2+.doc
1 Обзор и анализ выполненных конструкторских решений
Тормозные системы существенно влияют на безопасность движения автомобиля. Поэтому к тормозным системам кроме общих требований к конструкции автомобиля предъявляются повышенные специальные требования. В соответствии с этими требованиями тормозные системы должны обеспечивать:
минимальный тормозной путь или максимальное замедление при торможении;
сохранение устойчивости автомобиля при торможении;
стабильность тормозных свойств при неоднократных торможениях;
минимальное время срабатывания при торможении;
пропорциональность между усилием на тормозной педали и тормозными силами на колесах автомобиля (силовое следящее действие);
легкость управления.
Требования к тормозным системам регламентируются Правилами № 13 ЕЭК ООН применяемыми в России.
Подробный анализ темы дал понять что хоть барабанные тормоза и слабо подвержены износу но в той же мере существует высокая доля вероятности отказа тормоза за счет большего количества установленных механизмов (по сравнению с дисковыми тормозами) и как следствие из этого непостоянных и пропускаемых ТО автомобиля. При этом возможны повреждение тормозного барабана если фрикционные тормозные накладки будут истерты.
Тормозные колодки - это залог безопасности. Восстановление тормозных колодок непрофессиональными методами может привести к фатальным последствиям. Не всегда даже крупное автопредприятие располагает необходимым оборудованием и навыками для профессионального восстановления тормозных колодок.
Тормозные накладки предназначены для работы в тормозных механизмах барабанного типа прицепов грузовых автомобилей автобусов трамваев и других транспортных средств замедления движения и остановки механизмов. Они предупреждают износ тормозного барабана обладают высокой прочностью подходят для применения в любых климатических зонах.
При проверке эксплуатация тормозного диска допускается до минимально допустимой толщины B = 37 мм. Тормозные диски как правило не нуждаются в обслуживании т.е. их проточка при замене тормозных колодок не требуется. Такая проточка имеет смысл только если нужно увеличить площадь поверхности трения тормозного диска. Например при весьма сильных и глубоких рисках на всей поверхности тормозного диска. Из соображений безопасности минимальная толщина тормозного диска после проточки должна быть не менее 39-40 мм.
Однако некоторые изготовители транспортных средств имеют свои требования по необходимости проточки тормозных дисков которые следует учитывать. Вследствие этого предлагается внести конструкторские модификации барабанного тормозного механизма с целью увеличить срок службы фрикционных накладок.
С этой целью предлагается решать эту проблему используя идею наличия системы предотвращающий скорый износ фрикционных накладок за счет увеличения пятна контакта и усилия в гидравлических тормозных механизмах заднего моста автомобилей Volkswagen golf 2.
Рисунок 2.1 – Компоненты механизма заднего тормоза
- клин; 2 – тормозной цилиндр; болт (6 Нм); 4 - болты крепления цилиндра; 5 – заглушка; 6 – направляющие фиксаторов; 7 – цапфа ступицы; 8 – шпилька; 9 – пружинная шайба; 10 – тормозной щит; 11 – тормозная колодка; 12 – нижняя стяжная пружина; 13 – пружина фиксатора; 14 – шайба фиксатора; 15 – пружина регулировочного устройства; 16 – нижняя стяжная пружина; 17 – распорная планка.
Принцип действия этой системы состоит в следующем. При постепенном истирании фрикционных накладок отверстие между распорной планкой и колодкой расширяется а рычаг находящийся в этом отверстии под действием пружины опускается в это отверстие. Тем самым компенсируется износ колодок («подводит их»). За счет постепенного опускания рычага диаметр барабана остается прежним несмотря на истирание фрикционных тормозных накладок следовательно такие тормоза в нуждаются в замене накладок только в самом крайнем случае.
2 Описание принципа работы выбранного узла
Широко распространенные на автомобилях барабанные тормозные механизмы отличаются силовым воздействием колодок с разжимным устройством и барабаном а также расположением опор тормозных колодок.
Схема барабанного тормозного механизма с равными приводными силами и односторонним расположением опор а также статическая характеристика механизма представлены на рис. 2.2
Рис. 2.2 Схема (а) и статическая характеристика (б) барабанного тормозного механизма с равными приводными силами и односторонним расположением опор: 1 — первичная колодка; 2 — вторичная колодка; 3 — тормозной цилиндр; а с —расчетные размеры.
Для этого тормозного механизма характерным является следующее. Приводные силы и прижимающие колодки 1 и 2 к барабану равны () так как площади поршней тормозного цилиндра 3 одинаковы. Нормальные реакции барабана и на колодки не равны между собой (). Момент создаваемый силой трения и действующий на колодку 1 совпадает по направлению с моментом приводной силы вследствие чего колодка захватывается барабаном а сила трения способствует прижатию колодки к барабану. Момент силы трения действующий на колодку 2 противоположен по направлению моменту приводной силы и поэтому сила трения препятствует прижатию колодки 2 к тормозному барабану.
Колодка 1 называется первичной (активной самоприжимной) а колодка 2— вторичной (пассивной самоотжимной). Первичная колодка нагружается больше чем вторичная. При вращении колеса в противоположную сторону (движение автомобиля задним ходом) функции колодок изменяются и колодка 2 работает как первичная а колодка 1 — как вторичная.
В связи с тем что реакции барабана и на колодки а также силы трения и не равны между собой подшипники ступицы колеса нагружаются дополнительной силой. Такой тормозной механизм является неуравновешенным. Число торможений при движении автомобиля вперед значительно больше чем при движении задним ходом. Поэтому тормозная накладка первичной колодки изнашивается гораздо интенсивнее чем вторичной. Для уравнивания изнашивания фрикционная накладка первичной колодки обычно делается длиннее чем у вторичной колодки ( где — угол охвата соответственно первичной и вторичной колодок).
Принцип действия: При работающем двигателе и отпущенной педали компрессор накачивает воздух в баллоны где он хранится под давлением. Из баллонов воздух поступает к тормозному крану от тормозного крана воздух поступает через верхнюю секцию в баллоны прицепа. При нажатии на педаль тормоза верхняя секция закрывается и воздух прекращает поступать к прицепу. Тормозной кран прицепа открывается и воздух из баллонов прицепа поступает в пневмокамеры прицепа и прицеп начинает затормаживать. Нижняя секция тормозного крана автомобиля открывается и воздух поступает из баллонов автомобиля к пневмокамерам автомобиля и автомобиль начинает затормаживать. Воздух поступая в пневмокамеры давит на диафрагму она сжимая пружину смещается и давит на толкатель а он передаёт усилие на рычаг и валик разжимного кулака. Разжимной кулак поворачивается и разводит колодки. Колодки прижимаются к барабану и за счёт трения затормаживают его. При отпускании педали тормоза всё возвращается в исходное положение за счёт возвратных пружин а воздух из пневмокамер выходит в атмосферу через кран.
При движении автомобиля вперед при торможении каждая колодка работает как первичная и эффективность тормозного механизма при одинаковых размерах его основных деталей выше чем у тормозного механизма с совмещенными опорами. При торможении во время движения задним ходом колодки работают как вторичные поэтому эффективность механизма значительно снижается. Следовательно тормозной механизм является нереверсивным. Интенсивность изнашивания тормозных накладок колодок одинакова так как обе колодки работают в одних и тех же режимах.
3 Обоснование принятых решений
При решении этого вопроса (износа тормозных колодо) наиболее подходящей является система основанная на использовании распорной планки и подпружиненного рычага. Подобная конструкция не только является более простой для реализации но и может своими технологическими экономическими и прочими характеристиками. Рассмотрим вопрос более подробно и сравним характеристики тормозного механизма до и после принятие предложения по улучшению. С точки зрения точки экономики производство такого механизма будет незначительно увеличено но эти потери можно сократить и финансово выиграть на этом. Так как любой клиент при получении полной информации о механизме согласится что это того стоит. С технологической точки значительно упрощает ТО тормозов и их использование т.к. при первой установке тормозного механизма о не вообще можно не беспокоится до самого выхода тормоза из строя при этом не сокращается а даже продлевается срок службы.
4 Анализ напряжений распорной планки
Таблица 2.1 – характеристики материала
Таблица 2.2 – распределение напряжений
VON: Напряжение Von Mises
Рис. 2.3 – запас прочности
Таблица 2.3 – распределение напряжений
URES: Результирующее перемещение
Рис. 2.4 – статическое перемещение
Рис 2.5 – статическое узловое напряжение
5 Исследование показателей разработанной системы
На примере модели тормозного режима качения колеса рассмотрим работу тормозного механизма и его характеристики. Наиболее полное представление о технико-экономических показателях можно получить при использовании программ САПРа. Воспользуемся средствами моделирования MatLABSimuLink для получения зависимостей показателей тормозного механизма.
5.1 Моделирование тормозного режима качения колеса
Расчетная схема для тормозного режима качения колеса представлена на рис.2.6:
Рис. 2.6 Расчетная схема
Запишем уравнения движения колеса:
Где V – скорость; R Px – сила действующая со стороны остова Mт – ведущий момент rd – свободный радиус mf – момент сопротивления качению.
Где - радиус качения без скольжения.
Здесь .Где Rz – реакция поверхности.
Момент сопротивления
Коэффициент взаимодействия движителя с опорным основанием рассчитывается по формуле:
Коэффициент буксования Где – угловая скорость.
Математическую модель системы будем составлять с помощью программы MatLABSimuLink. Для этого необходимо задать исходные данные (рис.2.7)
Рис. 2.7 Задание исходных данных (m-file)
Исходя из записанных выше выражений составим математическую модель системы (рис.2.8):
Рис.2.8 Математическая модель системы
Рис. 2.9 График зависимости скорости движения от времени
Таким образом полученная зависимость показывает что скорость торможения убывает линейно. Так при изменении времени от 0 до 3.7 с скорость уменьшилась от 22 до 0 мс.
6 Расчеты подтверждающие работоспособность конструкции
Известны три метода расчета: аналитический графоаналитический и графический. Воспользуемся аналитическим методом определения тормозного момента создаваемого тормозом.
Вывод формул для расчета тормозного момента основывается на рассмотрении равновесия колодки ( с одной или двумя степенями свободы) под действием внешних сил. При этом делаются следующие допущения:
Давление на накладку на выделенном элементарном участке расположенном под углом к линии ОС (см. рис5) одинаково по всей ширине накладки;
Закон распределения давлений по длине накладки не изменяется с изменением сил F разжимающих колодки где pma
Коэффициент трения между накладкой и барабаном остается постоянной на всех режимах торможения
На элементарный участок накладки dα действуют элементарная нормальная реакция dN со стороны барабана и возникающая при вращении барабана элементарная сила трения dF в плоскости где касательной к поверхности трения: где b – ширина накладки r – радиус тормозного барабана.
Подставляя в последнее выражение значение p согласно формуле получаем
Тормозной момент М12 на колодке создаваемый силами трения между накладкой и барабаном (2.3) Для определия pmax записывается сумма моментов относительно точки поворота колодки С: (2.4)
Заметим что на колодках двумя степенями свободы точкой поворота колодки является точка соприкосновения ее с плоской опорой.
Подставляя выражение dF и dN и учитывая что l=r-scos α после преобразований имеем
Подставив выражение (2.5) в уравнение (2.3) и разделив числитель и знаменатель на получаем уравнение для тормозного уравения одной колодки
Знак «минус» в знаменателе уравнения (2.6) берется для активной колодки а знак «плюс» для пассивной. Общий тормозной момент двухколодочного тормоза складывается из моментов обоих колодок т.е. .
Полученные уравнения (2.5) (2.9) действительны для всех барабанных тормозных механизмов как с самоустанавливающимися колодками с двумя степенями свободы так и с колодками с одной степенью свободы.
После интегрирования выражений (2.7) и (2.8) получаем при синусоидальном распределении давлений
Подставляем эти значения в (2.7) получаем для колодок с 2 степенями свободы
Знак «+» и φ1 в полученных уравнениях берутся для передней активной колодки а знак «-» и φ2 – для задней пассивной колодки. На основе характера изнашивания накладок существующих тормозов с самоустанавливающимися колодками принимается φ1=40 50° и φ2=20 30°.
Заметим что при φ1=0 и φ2=0 выражение (2.12) приобретает вид (2.10).
Согласно формуле (2.9)
Для тормозов с двумя одинаковыми активными или пассивными колодками тормозной момент и приводная сила определяется по формулам:
Тормоза с фиксированным разжимным кулаком или клином при приработанных накладках имеют M1=M2 т.е.
Из условия равновесия разжимного кулака (см. рис. 2.4 а) имеем
Исключая из уранений (2.13) и (2.14) поочередно F1 и F2 находим зависимость последних от F’ и конструктивных параметров (при допущении h1h2): где F’ – сила действующая на рычаг разжимного кулака; dk – диаметр начальной окружности разжимного кулака (рис 2.13).
Подставляя выражения F1 и F2 из (2.15) в уравнение (2.9) получаем тормозной момент для тормоза с фиксированным разжимным кулаком:
Эффективность тормозов оценивается коэффициентом эффективности тормоза
Расчет тормозного барабана. Ввиду сложности и большой трудоемкости точного расчета тормозного барабана используют приближенную методику его расчета на прочность и жесткость. При этом предполагают что барабан состоит из двух частей: цилиндра 1 и диска 2 (рис 2.14) которые соединены друг с другом шлицами так что деформации цилиндра и диска не зависимы а шлицы нужны лишь для передачи крутящего момента.
Рассматривая барабан как тонкостенный цилиндр бесконечной длины используем формулу для расчета тонкостенных сосудов где pcp – среднее давление на накладку: d6 – диаметр барабана м; – сопротивление разрыву в диаметральном сочетании барабана Па; s – расчетная толщина стенки барабана м; Mtma – коэффициент трения; Ан – суммарная площадь накладок м^2.
1+.doc
1 Анализ рынка автосервисных услуг в г. Калуга
За последние годы сеть автосервисов г. Калуге претерпела значительные изменения. По данным Госкомстата ЦФО объем технического обслуживания и ремонта транспортных средств государственными и муниципальными предприятиями сократился с 2% в 2003 году до 01% в 2009 году т.е. сфера автосервиса полностью находится в негосударственной собственности.
Проведенный и анализ автосервисных услуг показал что спрос напрямую зависит от качества и комплексности оказываемых услуг т.е. чем выше уровень предлагаемых услуг и шире их спектр тем меньше работ осуществляется в порядке самообслуживания тем выше доля работ приходящихся на автсвисные предприятия. Уровень качества услуг оказывает двойное воздействие. Во-первых прямо влияет на объемы выполняемых автосервисных работ в текущем периоде. Во-вторых создает базу для расширенного автосервиса в будущем.
По данным налоговых органов на сегодняшний день в Калужской области зарегистрировано 653 предпринимателя занимающихся ремонтом и техническим обслуживанием автотранспортных средств. В том числе в г. Калуге зарегистрировано 225 предпринимателей.
По экспертным данным в городе функционируют более 100 предприятий по ремонту и обслуживанию транспортных средств из них имеют сертификаты соответствия 70 предприятий.
На территории города сформировались и выделились несколько крупных станций технического обслуживания оказывающих широкий перечень услуг (таблица 1.1) располагающих современным технологическим оборудованием производственными помещениями [1].
Таблица 1.1 – Процентное соотношение услуг оказываемых автосервисными предприятиями
Шиномонтажные работы
Ремонт и регулировка
Проверка и регулировка
Кузовные работы и работы связанные с покраской автомобиля
Работы по диагностике и устранению
неисправностей электрической и электронной
Техническое обслуживание автомобилей
Диагностика и ремонт двигателей
Подготовка автомобилей к прохождению
государственного технического осмотра
Из автосервисов с широким спектром услуг можно выделить: «Касам-авто» Дженсер-Азарово СТО А-1 Мастер-Сервис Автомастер «Омега». К предприятиям специализирующихся по видам работ можно отнести «Инком-Авто» которые занимаются диагностикой ремонтом и регулировкой рулевого управления тормозной системы и системы подвески автомобиля. Но самое большое количество предприятий – это небольшие мастерские в которых как правило работают несколько человек оснащенные старым оборудованием.
Подводя итоги необходимо отметить следующее: - рынок технического обслуживания и ремонта автотранспортных средств в городе растет быстрыми темпами. Доминирующее положение на рынке автосервисных услуг занимают субъекты малого предпринимательства. Ежегодно увеличивается парк автомобилей которое ведет к увеличению числа потребителей следовательно – увеличению числа автосервисных предприятий в том числе непрофессиональных и незарегистрированных мастерских. Актуальной остается проблема квалификации персонала. Около 60% производственных рабочих не имеют специального образования. Во многих мастерских организация приема заказа не соответствует правилам предоставления автосервисных услуг. Неудовлетворенность качеством предоставляемых услуг является основной проблемой в данной сфере услуг которая требует кардинального решения.
Экономическая политика которую проводит Калужская область изменила структуру промышленного комплекса создала условия для появления высокотехнологичных производств. В области сконцентрировано 770 различных предприятий. Они формирует порядка 35% ВРП и обеспечивают более половины налоговых поступлений в областной бюджет. В промышленности работает почти треть населения области.
Традиционно основу промышленности региона составляет машиностроительный комплекс. На сегодняшний день в структуре промышленного производства его доля значительно выросла и составляет почти 70%. Ежегодно в регионе увеличивается доля высокотехнологичных производств только в 2012 году прирост например фармацевтического производства составил 43%. За последние шесть лет объем промышленного производства в Калужской области вырос в два с половиной раза. Фактически к существовавшей промышленности Калужской области добавилось еще полторы.
Рис. 1.1 – структура обрабатывающих производств Калужской области
За последние шесть лет объем промышленного производства в Калужской области вырос в два с половиной раза. Фактически к существовавшей промышленности Калужской области добавилось еще полторы.
В 2012 году значительно увеличилось производство легковых и грузовых автомобилей (на 223% и на 234% соответственно) прирост фармацевтического производства составил 43%. Возросло производство паровых турбин на 159% телевизионных приемников на 137% мотоблоков и мотокультиваторов на 128% готовых металлических изделий на 21%.
2 Назначение и типы тормозных сиситем
Тормозной называется система управления автомобилем которая служит для уменьшения скорости движения остановки и удержания автомобиля на месте. Тормозная система обеспечивает безопасность при движении и остановках.
Современные автомобили оборудуются несколькими тормозными системами имеющими различное назначение. На рис. 1.2 представлены типы тормозных систем применяемых на автомобилях.
Рабочая тормозная система предназначена для снижения скорости движения автомобиля вплоть до полной его остановки. Она является наиболее эффективной из всех тормозных систем действует на все колеса автомобиля и используется для служебного и экстренного (аварийного) торможения автомобиля. Рабочую тормозную систему часто называют ножной так как она приводится в действие от тормозной педали ногой водителя.
Стояночная тормозная система служит для удержания на месте неподвижного автомобиля. Она воздействует только на задние колеса автомобиля или на вал трансмиссии. Стояночную тормозную систему называют ручной так как она приводится в действие от рычага рукой водителя.
Запасная тормозная система является резервной она предназначена для остановки автомобиля при выходе из строя рабочей тормозной системы. При отсутствии на автомобиле отдельной запасной тормозной системы ее функции может выполнять исправная часть рабочей тормозной системы (первичный или вторичный контур) или стояночная тормозная система.
Рис. 1.2 - Типы тормозных систем
Вспомогательная тормозная система служит для ограничения скорости движения автомобиля на длинных и затяжных спусках. Она выполняется независимой от других тормозных систем и представляет собой тормоз-замедлитель который обычно действует
на вал трансмиссии. Вспомогательную тормозную систему используют для служебного торможения с целью уменьшения изнашивания рабочей тормозной системы и повышения безопасности движения в горных условиях где при частых торможениях тормозные механизмы колес сильно нагреваются и быстро выходят из строя. Так если у грузового автомобиля на загородном шоссе число торможений на 100 км пути составляет 125 то в горных условиях оно возрастает до 1000.
Прицепная тормозная система предназначена для снижения скорости движения остановки и удержания на месте прицепа а также автоматической его остановки при отрыве от автомобиля- тягача.
Рабочей стояночной и запасной тормозными системами оборудуются все автомобили а вспомогательной тормозной системой — только грузовые автомобили большой грузоподъемности полной массой свыше 12 т и автобусы полной массой более 5 т. Прицепной тормозной системой оборудуются прицепы работающие в составе автопоездов.
Совокупность всех тормозных систем называется тормозным управлением автомобиля.
Каждая тормозная система состоит из одного или нескольких тормозных механизмов (тормозов) и тормозного привода. Тормозные механизмы осуществляют процесс торможения автомобиля а тормозной привод управляет тормозными механизмами.
3 Требования к тормозным системам
Тормозные системы существенно влияют на безопасность движения автомобиля. Поэтому к тормозным системам кроме общих требований к конструкции автомобиля предъявляются повышенные специальные требования. В соответствии с этими требованиями тормозные системы должны обеспечивать:
минимальный тормозной путь или максимальное замедление при торможении;
сохранение устойчивости автомобиля при торможении;
стабильность тормозных свойств при неоднократных торможениях;
минимальное время срабатывания при торможении;
пропорциональность между усилием на тормозной педали и тормозными силами на колесах автомобиля (силовое следящее действие);
легкость управления.
Требования к тормозным системам регламентируются Правилами № 13 ЕЭК ООН применяемыми в России.
Рассмотрим указанные требования.
3.1 Минимальный тормозной путь
Тормозные системы автомобиля должны быть высокоэффективными. При интенсивном движении число дорожно-транспортных происшествий и аварий уменьшится если максимальное значение замедления будет высоким и приблизительно одинаковым у разных по типу и массе автомобилей движущихся в потоке. Одновременно должны быть близкими друг к другу и тормозные пути автомобилей (разница не более 15%).
При минимальном тормозном пути будет обеспечиваться не только высокая безопасность движения но и увеличение средней скорости автомобиля.
Необходимыми условиями получения минимального тормозного пути являются минимальное время срабатывания тормозного привода одновременное торможение всех колес автомобиля возможность доведения тормозных сил на всех колесах автомобиля до максимального значения по сцеплению и обеспечение необходимого распределения тормозных сил между колесами автомобиля в соответствии с нагрузками на колеса.
3.2 Устойчивость при торможении
Выполнение этого требования повышает эффективность торможения автомобиля на дорогах с малым коэффициентом сцепления (скользкие обледенелые и т. п.) и способствует повышению безопасности движения.
Для выполнения указанного требования необходимо чтобы тормозные силы на левых и правых колесах автомобиля при торможении были одинаковы (разница не более 15 %) и распределялись между передними и задними колесами в соответствии с приходящимися на них нагрузками или пропорционально нормальным реакциям на колесах:
Такая пропорциональность между тормозными силами и нагрузками на передних и задних колесах может быть достигнута различными способами например с помощью регуляторов тормозных сил которые регулируют тормозные силы на колесах моста в зависимости от нагрузки приходящейся на мост. Соблюдение указанной пропорциональности обеспечит торможение автомобиля с максимальным замедлением в любых дорожных условиях.
3.3 Стабильность при торможении
Указанное требование связано с нагревом тормозных механизмов во время торможения и возможным нарушением их действия при нагреве. Так при нагреве уменьшается коэффициент трения между фрикционными накладками колодок и тормозными барабанами (дисками). Кроме того нагрев тормозных накладок существенно влияет на их изнашивание. И чем выше температура тормозных накладок при торможении тем больше их изнашивание.
Стабильность тормозных свойств при неоднократных торможениях автомобиля может быть обеспечена если тормозные накладки будут иметь коэффициент трения равный 03 035 мало зависящий от скорости скольжения нагрева и попадания на них воды.
3.4 Минимальное время срабатывания
Время срабатывания тормозной системы при торможении оказывает существенное влияние на тормозной путь автомобиля и следовательно на безопасность его движения.
Время срабатывания тормозной системы зависит главным образом от типа тормозного привода и должно составлять 02 05 с при гидравлическом приводе 06 08 с при пневматическом приводе и 1 2 с для автопоезда с пневматическим тормозным приводом. Выполнение указанного требования обеспечивает значительное повышение безопасности движения автомобиля в различных дорожных условиях.
3.5 Силовое следящее действие
Указанное требование связано с обеспечением пропорциональности между усилием на тормозной педали и тормозными силами на колесах автомобиля при торможении. Выполнение этого требования при плавном увеличении тормозных сил на колесах автомобиля обеспечивает сохранение удобства езды для пассажиров.
3.6 Легкость управления
Это требование необходимо для облегчения работы водителя усложняющейся из-за частых торможений автомобиля особенно в условиях города и в горных условиях. Так торможение в горных условиях осуществляется в 8 —10 раз чаще чем в обычных условиях на загородном шоссе.
Усилие на тормозной педали при торможении автомобилей должно составлять 500 700 Н (меньшее значение — для легковых автомобилей) при ходе педали 80 180 мм. Усилие на рычаге стояночной тормозной системы не должно превышать 400 Н при небольшом ходе рычага (300 мм).
Легкость управления достигается соответствующим выбором передаточных чисел тормозной системы жесткостью тормозного привода и малыми потерями в приводе. Кроме того сиденье водителя должно быть регулируемым и обеспечивать удобную его посадку при которой спина упирается в спинку сиденья а усилие на тормозной педали создается коленным суставом. В этом случае водитель может создать на тормозной педали усилие превышающее его массу на 10 20 %. Наибольшее усилие на рычаге стояночной тормозной системы (до 500 700 Н) можно получить при таком расположении рычага когда прилагаемое усилие к рычагу направлено снизу вверх.
4 Тормозные механизмы
Тормозными называются механизмы осуществляющие процесс торможения автомобиля. Тормозные механизмы служат для принудительного замедления автомобиля. Современные автомобили оборудуются различными типами тормозных механизмов (рис. 1.3).
Рис. 1.3 Типы тормозных механизмов классифицированных по различным признакам
Тормозные механизмы могут осуществлять принудительное замедление автомобиля различными способами — механическим (фрикционным) гидравлическим электрическим и внеколесным торможением.
Фрикционные тормозные механизмы (дисковые и барабанные) получили наиболее широкое распространение на автомобилях. Дисковые тормозные механизмы применяются для передних и задних колес легковых автомобилей большого класса и для передних колес легковых автомобилей малого и среднего классов. Барабанные тормозные механизмы используют на грузовых автомобилях независимо от их грузоподъемности в качестве колесных и трансмиссионных и на легковых автомобилях малого и среднего классов для задних колес.
Фрикционный тормозной механизм включает в себя вращающуюся часть (барабан диск) тормозной элемент (колодки) прижимное (кулачковое поршневое) регулировочное (эксцентрики) и охлаждающее (ребра каналы) устройства.
Рис. 1.4 - Фрикционные тормозные механизмы: а — барабанный; б — дисковый; 1 — ось; 2 6 8 9 — колодки; 3 7 — диски; 4 — кулак; 5 — тормозной барабан.
На рис.1.4 представлены схемы барабанного и дискового тормозных механизмов.
В барабанном тормозном механизме тормозной барабан 5 соединен с колесом автомобиля и вращается вместе с ним. Тормозные колодки 2 и 6 с фрикционными накладками установлены нижними концами на оси 7 закрепленной на неподвижном тормозном диске 3. Колодки могут поворачиваться на оси 1. Между верхними концами колодок находится разжимной кулак 4. При торможении кулак 4 разводит колодки 2 и 6 прижимая их к вращающемуся с колесом барабану 5. Торможение колеса происходит за счет сил трения возникающих между фрикционными накладками колодок и тормозным барабаном.
В дисковом тормозном механизме тормозной диск 7 связан с колесом автомобиля и вращается вместе с ним. С обеих сторон тормозного диска установлены две невращающихся колодки 8 и 9 с фрикционными накладками. При торможении колеса колодки прижимаются к диску создавая тормозной момент препятствующий вращению колеса.
Дисковые тормозные механизмы по сравнению с барабанными имеют меньшую массу более компактны более стабильны и лучше охлаждаются. Однако они менее эффективны имеют более быстрое изнашивание фрикционных накладок и хуже защищены от загрязнения.
5 Оценочные параметры и принципиальные схемы колесных тормозных механизмов
Конструкции колесных тормозных механизмов разных типов оценивают определенными параметрами основываясь на принципиальных схемах механизмов. Оценочные параметры тормозных механизмов
К оцениваемым параметрам конструкции тормозного механизма относятся эффективность стабильность уравновешенность и реверсивность.
Стабильностью называется сохранение эффективности работы тормозного механизма при уменьшении коэффициента трения. Стабильность представляет собой зависимость коэффициента эффективности от коэффициента трения и может быть выражена графиком статической характеристики тормозного механизма. Лучшую стабильность имеют тормозные механизмы с линейной статической характеристикой. От стабильности зависит достижение равных тормозных сил не только на колесах одного моста но также и на правых и левых колесах автомобиля что определяет безопасность при торможении.
5.2 Уравновешенность
Уравновешенным является тормозной механизм в котором при торможении силы трения не создают дополнительную нагрузку на подшипники колес и другие детали. Неуравновешенным считается тормозной механизм работа которого приводит к нагружению подшипников колес автомобиля.
Реверсивностью называется равная эффективность тормозного механизма при движении автомобиля вперед и назад. Реверсивность тормозного механизма определяет независимость величины создаваемого им тормозного момента от направления движения автомобиля.
6 Принципиальные схемы тормозных механизмов
6.1 Барабанные тормозные механизмы
Широко распространенные на автомобилях барабанные тормозные механизмы отличаются силовым воздействием колодок с разжимным устройством и барабаном а также расположением опор тормозных колодок.
Схема барабанного тормозного механизма с гидравлическим приводом с равными приводными силами и односторонним расположением опор а также статическая характеристика механизма представлены на рис. 1.5.
Рис. 1.5 - Схема (а) и статическая характеристика (б) барабанного тормозного механизма с гидравлическим приводом с равными приводными силами и односторонним расположением опор: 1 — первичная колодка; 2 — вторичная колодка; 3 — тормозной цилиндр; а с —расчетные размеры.
Для этого тормозного механизма характерным является следующее. Приводные силы и прижимающие колодки 1 и 2 к барабану равны () так как площади поршней тормозного цилиндра 3 одинаковы. Нормальные реакции барабана и на колодки не равны между собой (). Момент создаваемый силой трения и действующий на колодку 1 совпадает по направлению с моментом приводной силы вследствие чего колодка захватывается барабаном а сила трения способствует прижатию колодки к барабану. Момент силы трения действующий на колодку 2 противоположен по направлению моменту приводной силы и поэтому сила трения препятствует прижатию колодки 2 к тормозному барабану.
Колодка 1 называется первичной (активной самоприжимной) а колодка 2— вторичной (пассивной самоотжимной). Первичная колодка нагружается больше чем вторичная. При вращении колеса в противоположную сторону (движение автомобиля задним ходом) функции колодок изменяются и колодка 2 работает как первичная а колодка 1 — как вторичная.
В связи с тем что реакции барабана и на колодки а также силы трения и не равны между собой подшипники ступицы колеса нагружаются дополнительной силой. Такой тормозной механизм является неуравновешенным. Число торможений при движении автомобиля вперед значительно больше чем при движении задним ходом. Поэтому тормозная накладка первичной колодки изнашивается гораздо интенсивнее чем вторичной. Для уравнивания изнашивания фрикционная накладка первичной колодки обычно делается длиннее чем у вторичной колодки ( где — угол охвата соответственно первичной и вторичной колодок).
Этот тормозной механизм работает с одинаковой эффективностью при движении автомобиля вперед и задним ходом так как разность реакций тормозного барабана на колодки не зависит от направления вращения барабана. Следовательно механизм является реверсивным. Его статическая характеристика нелинейная (рис. 1.5 б).
Тормозные механизмы такого типа применяются на грузовых автомобилях средней грузоподъемности и в качестве задних тормозных механизмов на легковых автомобилях.
Тормозной момент создаваемый тормозным механизмом:
или с учетом значения сил трения и
где - коэффициент трения.
Из условия равновесия тормозящего колеса имеем:
— для первичной колодки;
— для вторичной колодки.
Подставив в эти уравнения выражения для сил трения и получим соответственно для первичной и вторичной колодок:
Схема барабанного тормозного механизма с равными перемещениями колодок и его статическая характеристика представлены на рис. 1.6. Тормозные колодки механизма разжимаются кулаком который имеет симметричный профиль и обеспечивает одинаковое перемещение колодок.
В этом тормозном механизме при любом повороте разжимного кулака приводные силы и находятся на одинаковом расстоянии от оси кулака. Реакции барабана на колодки силы трения и углы охвата колодок равны (; ; ). Приводные силы и не одинаковы: на первичную колодку действует меньшая приводная сила чем на вторичную колодку (). Тормозной механизм реверсивный и эффективность его действия одинакова как при движении вперед так и при движении назад. Интенсивность изнашивания тормозных накладок обеих колодок одинакова. Механизм практически является уравновешенным и имеет линейную статическую характеристику.
Из условия равновесия для первичной и вторичной тормозных колодок соответственно имеем:
Тормозные механизмы такого типа имеют низкий КПД кулачкового разжимного устройства равный 06 08. Они требуют значительных приводных сил и поэтому применяются на грузовых автомобилях и автобусах с пневматическим тормозным приводом.
Рис. 1.6 Схема (а) и статическая характеристика (б) барабанного тормозного механизма с равными перемещениями колодок: 1 — первичная колодка; 2 — вторичная колодка; 3 — разжимной кулак.
7 Эффективность и стабильность тормозных механизмов
На рис. 1.7 представлены статические характеристики различных тормозных механизмов принципиальные схемы которых были рассмотрены ранее. Эти характеристики позволяют провести сравнительную оценку механизмов при одинаковых параметрах и коэффициенте трения . Из рисунка следует что тормозной механизм с равными перемещениями колодок является наименее эффективным среди барабанных механизмов. Если принять коэффициент эффективности то у тормозного механизма с равными тормозными силами и односторонним расположением опор эффективность выше на 22% (). У тормозного механизма с равными тормозными силами и разнесенными опорами коэффициент эффективности выше на 60 % ().
Из рисунка также видно что тормозной механизм с равными перемещениями колодок обладает наибольшей стабильностью среди указанных барабанных механизмов так как имеет линейную статическую характеристику. При уменьшении коэффициента трения вследствие ряда причин (нагрев замасливание загрязнение и др.) коэффициент эффективности этого механизма снижается в меньшей степени чем у других механизмов.
Из сравнения статических характеристик тормозных механизмов следует что эффективность и стабильность механизмов взаимосвязаны. Так чем большей эффективностью обладает тормозной механизм тем меньше его стабильность.
Для сравнения на рис. 10 штриховой линией нанесена статическая характеристика дискового тормозного механизма. Характеристика его линейна. Это свидетельствует о том что дисковый тормозной механизм имеет высокую стабильность и наименьшую эффективность среди рассмотренных тормозных механизмов.
Рис. 1.7 Статические характеристики тормозных механизмов: 1 — дисковый; 2 — с равными перемещениями колодок; 3 — с равными приводными силами и односторонним расположением опор; 4 — с равными приводными силами и разнесенными опорами
В настоящее время предпочтение отдается стабильности а не эффективности тормозных механизмов в связи с тем что необходимый тормозной момент можно получить путем увеличения приводных сил (применение вакуумного усилителя колесных тормозных цилиндров большего диаметра и др.).
8 Пневматический тормозной привод
Подача компрессора тормозного пневмопривода
где — число цилиндров компрессора; — диаметр цилиндра; — ход поршня; — частота вращения компрессора; = 06 — коэффициент подачи компрессора.
Объем воздушных баллонов (ресиверов) должен быть в 20—25 раз больше объема исполнительных приборов пневмопривода.
Усилие на тормозной педали определяется по максимальному тормозному моменту передаваемому колесом.
Тормозной механизм колеса имеет равные перемещения колодок равные моменты передаваемые первичной и вторичной колодками и неравные приводные силы ().
Рис. 1.8 Схема для расчета пневматического тормозного привода: 1 — педаль; 2 — тормозной кран; 3 — тормозная камера.
Определив значения приводных сил и (см. рис. 1.6) находим момент на валу разжимного кулака тормозного механизма
где е = const (см. рис. 1.8).
Усилие на штоке тормозной камеры
где — расстояние от оси вала разжимного кулака до оси штока тормозной камеры.
Давление воздуха в тормозной камере при торможении
где - площадь поршня.
Усилие на поршне тормозного крана при торможении
Где — усилие пружины; усилие на тормозной педали
где — параметры показанные на рис. 1.8.
Для грузовых автомобилей допустимое усилие [] на тормозной педали не должно превышать 700 Н а наибольший ход педали S — 180 мм.
Литература.doc
Техническое обслуживание и ремонт автомобилей: пособие по дипломному проектированию. Под общ. ред. Суханов Б.Н. Борзых И.О.– М.: Транспорт 2001.
Техника и технология сферы сервиса: метод. указ. по выполнению контрольной работы А. В. Боровиков Г.В. Парантаев. – СПб.: СПбГУСЭ 2006.
Межотраслевые правила по охране труда на автомобильном транспорте ПОТ РМ-027-2003 .М.:НЦЭНАС 2004 .
Кузнецов Е. С. Техническая эксплуатация автомобилей: учебник для вузов. – 3-е изд. перераб. и доп. – М.: - Транспорт 2004.
Отчёты годовые комитета транспорта г.Калуга за 2012 г.
Алекса Н.Н. Алексеенко В.Н. Гредескул А.Б. Теория эксплуатационных свойств автотранспортных средств в примерах и заданиях: Учеб. пособ. –К.: УМК ВО 1999. –100 с.
Машков Е.А. Техническое обслуживание и текущий ремонт автомобилей КАМАЗ: Иллюстрированное издание. - Издательство «Третий Рим»
Гришкевич А.И. Ломако Д.М. Автушко В.П. и др.; Автомобили: Конструкция конструирование и расчет. Системы управления и ходовая часть: Учеб. Пособие для вузов Под ред. А.И. Гришкевича.- Мн.: Высш. Шк. 1997. – 200с.: ил.
Иванов М.Н. Детали машин. – М.: Высшая школа 1991
РД 37.009.026 – 92. Положение о техническом обслуживании и ремонте автотранспортных средств принадлежащих гражданам (легковые и грузовые автомобили автобусы минитракторы) 1998.
Системный подход в управлении качеством услуг технического обслуживания и ремонта автомобилей Проблемы развития автомобилестроения в России. М.: Машиностроение 1999.
Краткий справочник для инженеров и студентов: Высшая математика. Физика. Теоретическая механика. Сопротивление материалов. А.Д.Полянин В.Д.Полянина В.А.Попова и др.: под ред. А.А.Варламов – М.: Международная программа образования 1996.
Вахламов В.К. Автомобили: Конструкция и элементы расчета: учебник для студ. Высш. Учеб. Заведений В.К. Вахламов. – М. : Издательский центр «Академия» 2006. – 460 с.
Домников И.Ф. Техническое обслуживании и ремонт машин. – М.: Росинформагротех 2006.
Беляев Н.М. Сопротивление материалов- 2-е изд. перераб. и доп. – М.: Наука 1976.
Гжиров Р.И. “Краткий справочник конструктора”. – М.:Машиностроение 1983 г.
Пашина С.Н. Экономика автомобильного транспорта. Изд. 5-е перераб. и доп. – М.: Высшая школа 2005.
Фалько С.Г. Экономика предприятия. – М.: Дрофа 2003.
Шкрабак В.С. Луковников А.В. Тургиев А.К. Безопасность жизнедеятельности на производстве. – М.: Колос2002.
Практикум по охране труда Д.А.Бутко В.Л.Лущенков Б.И.Зотов и др.: под ред. А.И.Зеленухина. – М.:Колос 1996.
Анурьев В. И. Справочник конструктора-машиностроителя. В 3 т. Т.1 Под ред. И.Н. Жестковой. – 8-е изд. перераб. и доп.. – М.: Машиностроение 2001.
Экологическая безопасность: учебное пособие Лиханов В.А. Лопатин О.П. Вылегжанин П.Н. и др.: под ред.Зяблых Р.Ю. – Киров: ФГОУ ВПО 2005.
Инженерная экология и экологический менеджмент: учебное пособие М.В.Буторина П.В.Воробьёва А.П.Дмитриева и др.: под редакцией Н.И.Иванова-М.: «Логос»-2003.
СН 2.2.42.1.8.562-96 «Санитарные нормы допустимых уровней шума на рабочих местах»
СН 2.2.42.1.8.564-96 «Шум на рабочих местах в помещениях жилых общественных зданий и на территории жилой застройки»
ГОСТ 12.1.003-83 «ССБТ. Шум. Общие требования безопасности»
ГОСТ 12.1.005-88 «Общие санитарно-гигиенические требования к воздуху рабочей зоны»
СНиП 23-050-95 «естественное и искусственное освещение»
ГОСТ 12.1004-91ССБТ «Пожарная безопасность»
Об отходах производства и потребления: закон РФ от 24.06.1998 № 89-ФЗ (в ред. 30.12.2008)
Об охране окружающей среды: закон РФ от 10.01.2002г. № 7-ФЗ
0.Содержание х.doc
1 Анализ рынка автосервисных услуг в г. Калуга . 16
2 Назначение и типы тормозных сиситем . 20
3 Требования к тормозным системам 20
3.1 Минимальный тормозной путь.. . 20
3.2 Устойчивость при торможении ..21
3.3 Стабильность при торможении . .21
3.4 Минимальное время срабатывания 22
3.5 Силовое следящее действие. 22
3.6 Легкость управления. . .. 22
4 Тормозные механизмы. 24
5 Оценочные параметры и принципиальные схемы колесных тормозных механизмов . 27
5.2 Уравновешенность 27
5.3 Реверсивность . .. 27
6 Принципиальные схемы тормозных механизмов 29
6.1 Барабанные тормозные механизмы 29
7 Эффективность и стабильность тормозных механизмов . 33
8 Пневматический тормозной привод .. 35
9 Выбор и обоснование улучшения конструкции 36
Проектно-конструкторская часть . 37
1 Обзор и анализ выполненных конструкторских решений .37
2 Обоснование принятых решений .. 40
3 Анализ напряжений распорной планки 41
3.1 Напряжение .. 41
3.2 Перемещение. .. 41
3.3 Запас прочности .. 42
4 Исследование показателей разработанной системы ..43
4.1 Моделирование тормозного режима качения колеса .. 45
5 Описание принципа работы выбранного узла.. ..49
6 Расчеты подтверждающие работоспособность конструкции 52
Технологическая часть 58
1 Техническое обслуживание. . 58
1.1 Регулирование . 59
4 Диагностирование 65
4.1 Проверка свободного и полного хода педали тормоза . 65
4.2 Проверка герметичности тормозной системы 66
Экономическая часть . 69
1 Обоснование необходимости модернизации механизма 70
2 Существующие аналоги механизмов на рынке . 71
3 Выпуск автомобилей . . 72
4 Среда эксплуатации 73
4.1 Влияние среды эксплуатации ..73
6 Калькуляция затрат 75
6.1 Материальные затраты 75
6.2 Трудовые затраты и затраты на социальное страхование 76
6.3 Затраты на аренду помещения . 76
Охрана труда и экология 78
1 Обеспечение безопасности труда при изготовление тормозного механизма для КамАЗ 55102 78
1.1 Обеспечение защиты от шума .. 79
2 Обеспечение нормируемого содержания вредных веществ в воздухе рабочей зоны 84
2.1 Обеспечение освещенности в рабочей зоне . 84
2.2 Обеспечение безопасности окружающей среды при изготовлении колесного движителя для трактора 84
2.3 Расчет абразивно-металлической пыли 85
3 Меры при хранения отходов . 86
3+.doc
1 Техническое обслуживание
К основным неисправностям тормозной системы относятся: неэффективное действие тормозов заедание тормозных колодок неравномерное действие тормозных механизмов плохое растормаживание утечка тормозной жидкости и попадание воздуха в систему гидравлического привода снижение давления в системе пневматического привода а также негерметичность системы пневматического тормозного привода.
Неэффективное действие тормозной системы является результатом загрязнения или замасливания тормозных колодок нарушения регулировки тормозного привода и тормозных механизмов попадания воздуха в систему привода уменьшения объема тормозной жидкости негерметичности в соединениях пневматического привода.
Заедание тормозных механизмов может произойти в результате следующих причин: поломки стяжных пружин обрыва заклепок фрикционных накладок а также в результате засорения компенсационного отверстия в главном тормозном цилиндре или заклинивания поршней в колесных тормозных цилиндрах.
Неравномерное действие тормозных механизмов может привести к заносу автомобиля или к его уводу в сторону. Неравномерное торможение является следствием неправильной регулировки тормозных механизмов.
При ежедневном техническом обслуживании автомобиля необходимо проверять работу тормозов в начале движения а также герметичность соединений в трубопроводах и узлах пневмопривода. Утечку воздуха определяют по снижению давления на манометре или на слух. Утечку воздуха определяют при неработающем двигателе.
В автомобилях с пневматическим приводом системы торможения регулировка зазора осуществляется при помощи регулировочного червяка который устанавливается в рычаге разжимного кулака. Для регулировки зазора необходимо вывесить колесо и затем поворачивая ключ червяка за его квадратную головку довести колодки до контакта с барабаном. После доведения колодки необходимо поворачивать червяк в обратном направлении до тех пор пока колесо автомобиля не начнет свободно вращаться. Правильность регулировки зазора проверяют при помощи щупа. При правильной регулировке зазор должен составлять 02-04 мм у осей колодок а ход штока тормозной камеры должен быть в пределах от 20 до 40 мм.
В тормозных системах с пневматическим приводом свободный ход педали регулируют изменением длины тяги которая соединяет педаль тормоза с промежуточным рычагом привода тормозного крана. После регулировки свободный ход педали должен составлять 14-22 мм. Рабочее давление в пневматической тормозной системе должно регулироваться автоматически и составлять 06-075 МПа.
Привод стояночной тормозной системы регулируется за счет изменения длины наконечника уравнителя длины троса который связан с рычагом. Ход рычага отрегулированного привода стояночной системы торможения должен составлять 3-4 щелчка запирающего устройства.
На грузовых автомобилях регулировка стояночной системы торможения осуществляется за счет изменения длины тяги. Длину тяги изменяют отвертывая или завертывая регулировочную вилку. В отрегулированной тормозной системе в затянутом состоянии рычаг должен перемещаться не более чем на половину зубчатого сектора запирающего устройства.
Если тормозная тяга укорочена до предела и при этом не обеспечивает полного затормаживания при перемещении стопорной защелки за шесть щелчков то в этом случае необходимо перенести палец тяги к которому присоединен верхний конец тяги в следующее отверстие регулировочного рычага тормоза при этом обязательно нужно надежно затянуть и зашплинтовать гайку. После этого нужно повторить регулировку длины тяги в указанном выше порядке.
При ремонте тормозные механизмы снимают с автомобиля разбирают затем очищают от грязи и пыли а также от остатков тормозной жидкости. Детали тормозных механизмов очищают специальным моющим раствором затем водой а после этого продувают сжатым воздухом.
Разборку колесного тормозного механизма начинают со снятия тормозного барабана. После тормозного барабана снимают стяжные цилиндры тормозной цилиндр. Если на рабочей поверхности имеются различные царапины или небольшие риски то ее необходимо зачистить мелкозернистой шлифовальной бумагой. Если глубина рисок большая то барабан растачивают. После расточки барабана необходимо заменить накладки на увеличенный размер. Кроме этого смена накладок осуществляется если расстояние до головки заклепок буден менее 05 мм или в том случае если толщина клееных накладок будет менее 08 от толщины новой накладки.
Клепку новой накладки осуществляют в следующем порядке В начале новую накладку устанавливают и закрепляют на колодке при помощи струбцин. После этого со стороны колодки в накладке просверливают отверстия которые предназначены для заклепок. Просверленные отверстия снаружи раззенковывают на глубину 3-4 мм. Клепка накладок осуществляется медными бронзовыми или алюминиевыми заклепками.
Перед тем как приклеить накладку на колонку ее поверхность необходимо зачистить мелкой зернистой шлифовальной бумагой а после этого обезжирить. После этого на поверхность накладки наносят два слоя клея с выдержкой в 15 минут.
Сборка осуществляется в специальном приспособлении. После сборки механизм необходимо просушить в нагревательной печи при температуре 150-180 °С в течение 45 минут.
К основным неисправностям тормозной системы относятся:
– недостаточная эффективность торможения;
– заклинивание поршней в колесных цилиндрах;
– износ накладок тормозных колодок;
– перегрев тормозных механизмов;
– потеря герметичности одного из контуров в этом случае получается провал педали тормоза;
– применение колодок с несоответствующими накладками;
– неправильная регулировка привода регулятора давления;
При возникновении неисправностей в тормозной системе автомобили поступают в автосервис на текущий ремонт.
При текущем ремонте проводятся следующие работы:
– проверка элементов тормозной системы;
– замена тормозных шлангов;
– проверка тормозного цилиндра;
– замена тормозной жидкости;
– прокачка тормозной системы;
– проверка и регулировка свободного хода педали тормоза;
– проверка регулятора давления;
– проверка вакуумного усилителя тормозов;
– проверка и регулировка стояночного тормоза;
– техническое обслуживание антиблокировочной системы тормозов (АБС).
Кроме вышеперечисленных неисправностей в гидравлическом тормозном приводе возникает износ рабочих поверхностей главных и колесных цилиндров разрушение резиновых манжет а также нарушение герметичности трубопроводов шлангов и арматуры.
Тормозные цилиндры которые имеют небольшие риски или царапины восстанавливают хонингованием. При значительной величине износа тормозные цилиндры необходимо расточить до ремонтного размера. После растачивания необходимо провести хонингование.
К основным дефектам гидравлического усилителя тормозной системы относятся износ царапины риски на рабочей поверхности цилиндра и поршня неплотное прилегание шарика к своему гнезду смятие кромок пальцевых диафрагм а также износ и разрушение манжет.
Цилиндр гидравлического усилителя восстанавливают шлифовкой но на глубину не более чем на 01 мм. Неисправный поршень меняют на новый. Изношенные резиновые уплотнения также меняют на новые.
К основным дефектам пневматического тормозного привода относятся повреждения диафрагм тормозного клапана тормозных камер риски на клапанах и седлах клапанов изогнутость штоков износ втулок и отверстий под рычаги поломка и потеря упругости пружин; износ деталей кривошипно-шатунного и клапанного механизмов компрессоров.
Наиболее сильно изнашивающимися деталями компрессора являются: цилиндры кольца поршни подшипники клапаны а также седла клапанов.
Нарушение герметичности пневматического привода тормозной системы происходит- из-за износа уплотнительного устройства заднего конца коленчатого вала а также из-за разрушения диафрагмы загрузочного устройства.
После разборки пнемопривода детали уплотнительного устройства необходимо промыть в керосине затем удалить закоксовавшееся масло и заусенцы и затем снова собрать. Диафрагма заменяется на новую.
Воздушный фильтр тормозной системы необходимо разобрать затем промыть фильтрующий элемент в керосине а затем продуть сжатым воздухом. Перед установкой воздушный фильтр необходимо смочить в моторном масле.
После сборки и ремонта компрессор тормозной системы должен пройти испытания и приработку на специальном стенде.
При ремонте тормозного крана его снимают с автомобиля. Его разборку производят в тисках контролируя состояние всех составляющих его деталей. После замены поврежденных деталей тормозной кран собирают.
Отремонтированные или замененные узлы тормозной системы устанавливают на свои места после чего выполняют регулировочные работы.
Для оценки состояния тормозного механизма степени его износа и выявления причин неисправностей производятся следующие операции:
- проверка свободного и полного хода педали тормоза;
- проверка герметичности тормозной системы;
- проверка колодок дисковых или барабанных тормозов;
- проверка работоспособности стояночного тормоза регулятора давления вакуумного усилителя тормозов;
4.1 Проверка свободного и полного хода педали тормоза
Свободный ход педали тормоза должен быть не больше 20— 40 мм. Увеличение свободного хода сопровождается уменьшением рабочего хода педали которого может оказаться недостаточным для перемещения поршня на требуемую величину. В результате давление воздуха в верхней секции тормозного крана будет меньше расчетного. Это может явиться причиной недостаточной эффективности торможения автомобиля. При полном нажатии на педаль она не должна доходить до пола кабины на 10—30 мм. Регулирование положения педали относительно пола кабины осуществляется изменением длины тяги регулировочной вилкой. При полном ходе педали тормоза равном 90—130 мм ход рычага тормозного крана должен быть равен 311—391 мм.
Упругая характеристика упругого элемента тормозного крана обеспечивает плавное нарастание давления в верхней секции крана. Если упругий элемент разрушен то его упругая сила уменьшится и следящий поршень будет подниматься вверх и закрывать воздушный клапан при меньшем чем по норме давлении сжатого воздуха. Поэтому давление воздуха на выводах I II будет меньше необходимого и недостаточным для торможения автомобиля с заданной эффективностью.
Когда тормозной кран не обеспечивает полного растормаживания автомобиля эту неисправность обнаруживают по резкому увеличению сопротивления движению. Это может быть следствием отсутствия свободного хода педали тормоза или заедания поршней. В результате длительной работы уплотнение поршней ухудшается и в тормозной кран проникает пыль которая накапливается проникает в смазку и образует с нею маловязкую абразивную композицию. Возможна также поломка пружины. Это может вызвать заедание не только поршней но и клапанов толкателя Заедание каждой из названных деталей вызывает разные последствия.
4.2 Проверка герметичности тормозной системы
Тормозные камеры среднего и заднего мостов снабжены энергоаккумуляторами.
При торможении рабочей тормозной системой сжатый воздух подается в наддиафрагменную полость. Диафрагма прогибаясь воздействует на диск перемещая шток и поворачивает регулировочный рычаг с разжимным кулачком тормозного механизма. Торможение колес среднего и заднего мостов происходит так же как и передних колес. При включении стояночной тормозной системы воздух из-под поршня энергоаккумулятора выпускается пружина разжимается и поршень перемещается вправо. Толкатель через диафрагму воздействует на шток который перемещаясь поворачивает регулировочный рычаг — автомобиль затормаживается. При выключении стояночной тормозной системы сжатый воздух поступает под поршень энергоаккумулятора который перемещаясь влево сжимает пружину и дает возможность штоку тормозной камеры под действием возвратной пружины энергоаккумулятора вернуться в исходное положение.
В случае аварийного затормаживания автомобиля и невозможности воспользоваться системой аварийного оттормаживания необходимо вывернуть винты устройства аварийного оттормаживания автомобиля.
Защитные клапаны предназначены для разделения подачи сжатого воздуха и отключения поврежденного контура с целью сохранения сжатого воздуха в других контурах.
Для автоматического регулирования давления в тормозных камерах среднего и заднего мостов автомобиля в зависимости от осевой нагрузки при торможении используется регулятор тормозных сил который устанавливают на раме автомобиля и соединяют упругим элементом на. штанге с балками среднего и заднего мостов автомобиля.
Контроль за исправностью тормозных систем обеспечивается световой и звуковой сигнализацией датчиками которой являются пневматические выключатели в разных точках системы пневматического привода.
Давление в первом и втором контурах контролируют по двухстрелочному манометру на панели приборов в кабине автомобиля.
Для отбора сжатого воздуха из системы и проверки ее работы предусмотрены клапаны контрольного вывода установленные в различных точках тормозных контуров. Герметичность контуров пневматического привода тормозов необходима для обеспечения надежности в работе и безопасности движения. Проверка герметичности производится по показаниям манометра контрольным лампам а также на слух.
Автомобиль КамАЗ может быть использован для работы с полуприцепом и прицепом.
анотация.doc
В исследовательской части был проведен анализ тормозных механизмов и возможностей их улучшения.
В конструкторской части была разработана принципиальная схема тормозного механизма проведены исследования на прочность и выносливость проведен расчет параметров системы разработана последовательность сборки изделия.
В технологической части разработан технологический процесс технического обслуживания регулирования и диагностики тормозного механизма.
В экономической части были рассчитаны затраты на изготовления механизма рассчитан экономический эффект.
В разделе безопасность труда и промышленная экология произведена оценка опасных и вредных факторов при изготовлении механизма вычислены безопасные уровни шума.
The given work aims to develop a drum brake.
In a research part of an analysis of brake mechanisms and opportunities for improvement.
In a design part of the concept was developed brake conducted research on the strength and endurance and the calculation of the parameters of the system developed by the sequence assembly.
In an economic part expenses processing have been calculated targeted cost saving.
In section safety of work and industrial ecology evaluated dangerous and harmful factors in the manufacture of machinery calculated safe levels of noise.
Чертеж3.cdw
Усилие тормозной педали по ОСТ 37-001.016-70 147 Н;
время сробатывания привода 0.05 0.1 с
тормозныхмагистралях 2 3 МПа; передаточное число
педали Uп=4.5 5.2; удельное давление на поверхности
тормозной накладки 1.5 2.5 МПа
Чертеж.cdw
Е. Клапан контрольного вывода контура
С. Клапан контрольного вывода контура
D. Клапан контрольного вывода контура
Масловлагоотделитель
Предохранитель от замерзания
Тройной защитный клапан
Пневматический цилидр привода механизмов вспомогательного
Пневматический цилиндр привода механизмов вспомогательного
Кран управления стояночным тормозом
Конденсационный ресивер
Кран слива конденсата
Датчик падения давления
Клапан защитный. Одинарный защитный клапан
Двухсекционный тормозной кран
Пневмоэлектрический датчик включения электромагнита
пневсоклвпана прицепа (полуприцепа)
Клапан ограничения давления
Двухстрелочный манометр
Тормозная передняя камера типа 24
Перепуской двухмагистральный клапан
Ускорительный клапан
Регулятор тормозных сил
Клапан управления тормозами прицепа с двухпроводным
Тормозная камера с пружинным энерго акамулятором типа
Клапан управления тормозами прицепа с однопроводным
Датчик включения сигнала торможения
Соединительные головки типа "Палм
Соединительная головка типа "А
Чертеж.cdw

КФ МГТУ им. Н.Э. Баумана
математическая модель системы торможения автомобиля
График зависимости скорости движения от времени
Уравнения движения колеса
записка курсач.doc
Обзор и анализ выполненных конструкторских решений.6
2.Обоснование принятых решений.9
3.Ожидаемые технико-экономические показатели.10
3.1 Моделирование тормозного режима качения колеса.11
Описание принципа работы выбранного узла.14
1.Расчеты подтверждающие работоспособность конструкции.17
2. ТО и обслуживание механизма.23
Техническое задание.
Разработать барабанный тормозной механизм с пневмоприводом грузового автомобиля с колесной формулой 6х4. Проанализировать общие разработки принцип действия экономические и технические показатели возможности улучшения барабанного тормозного механизма; проанализировать все эти аспекты и произвести конструкторские улучшения механизма в техническо-экономических показателях.
В барабанном тормозном механизме с двумя рабочими цилиндрами эффективность работы повышается за счёт вращения барабана при движении автомобиля которое при торможении стремится ещё сильнее прижать к нему колодки («увлекая» их за собой и дополнительно проворачивая их вокруг своих осей) в итоге также уменьшая необходимое усилие на педали тормоза (водителю достаточно легкого нажатия на педаль чтобы колодки коснулись барабана после чего этот эффект начинает работать как своеобразный «усилитель») — на дисковых тормозных механизмах такой эффект совершенно отсутствует так как диск вращается в направлении перпендикулярном к направлению действия тормозного усилия. Поэтому автомобили с дисковыми тормозами особенно на всех колёсах в абсолютном большинстве случаев снабжаются сервоприводом (усилителем) тормозов — без него усилие на педали было бы чрезмерно велико. При движении вперёд с усилением действует передняя колодка которая называется набегающей в противоположность к задней соответственно вторичной тормозной колодке.
Барабанные тормоза используются на многих грузовых автомобилях реже — легковых машинах и мотовездеходах. Главное преимущество барабанного тормозного механизма — в том что его мощность (определяемую площадью пятна контакта колодок с поверхностью барабана) можно очень легко повышать за счёт увеличения как диаметра барабана так и его ширины (в то время как дискового — только за счёт увеличения диаметра диска который в большинстве случаев ограничен размером обода колеса внутри которого тормозной диск установлен). Это позволяет даже при не слишком высокой удельной эффективности (тормозное усилие на единицу площади колодок) достичь очень высоких абсолютных значений тормозного усилия необходимых для замедления и остановки тяжёлого транспорта вроде грузовиков или автобусов. Барабанный механизм сравнительно хорошо защищён от попадания воды и пыли его колодки намного меньше изнашиваются на запылённой или грунтовой дороге чем открыто установленные колодки дискового механизма что делает его более долговечным и вообще более подходящим для плохих дорожных условий. Использование барабанных тормозов упрощает оснащение автомобиля стояночным тормозом. Барабанные тормоза не выделяют много тепла что делает возможным применение сравнительно дешёвых безопасных в обращении и не гигроскопичных тормозных жидкостей на масло-спиртовой основе (ЭСК БСК и подобные) имеющие низкую температуру кипения.
В то же время барабанные тормоза срабатывают медленнее чем дисковые имеют менее стабильные характеристики (что в первую очередь обусловлено непостоянством пятна контакта колодки и внутренней поверхности тормозного барабана) и меньшие возможности для регулировки. Поэтому на быстроходных легковых автомобилях обычно применяют как минимум передние дисковые тормозные механизмы.
Обзор и анализ выполненных конструкторских решений.
Тормозные системы существенно влияют на безопасность движения автомобиля. Поэтому к тормозным системам кроме общих требований к конструкции автомобиля предъявляются повышенные специальные требования. В соответствии с этими требованиями тормозные системы должны обеспечивать:
минимальный тормозной путь или максимальное замедление при торможении;
сохранение устойчивости автомобиля при торможении;
стабильность тормозных свойств при неоднократных торможениях;
минимальное время срабатывания при торможении;
пропорциональность между усилием на тормозной педали и тормозными силами на колесах автомобиля (силовое следящее действие);
легкость управления.
Требования к тормозным системам регламентируются Правилами № 13 ЕЭК ООН применяемыми в России.
Подробный анализ темы дал понять что хоть барабанные тормоза и слабо подвержены износу но в той же мере существует высокая доля вероятности отказа тормоза за счет большего количества установленных механизмов (по сравнению с дисковыми тормозами) и как следствие из этого непостоянных и пропускаемых ТО автомобиля. При этом возможны повреждение тормозного барабана если фрикционные тормозные накладки будут истерты.
Тормозные колодки - это залог безопасности. Восстановление тормозных колодок непрофессиональными методами может привести к фатальным последствиям. Не всегда даже крупное автопредприятие располагает необходимым оборудованием и навыками для профессионального восстановления тормозных колодок.
Тормозные накладки предназначены для работы в тормозных механизмах барабанного типа прицепов грузовых автомобилей автобусов трамваев и других транспортных средств замедления движения и остановки механизмов. Они предупреждают износ тормозного барабана обладают высокой прочностью подходят для применения в любых климатических зонах.
При проверке эксплуатация тормозного диска допускается до минимально допустимой толщины B = 37 мм. Тормозные диски как правило не нуждаются в обслуживании т.е. их проточка при замене тормозных колодок не требуется. Такая проточка имеет смысл только если нужно увеличить площадь поверхности трения тормозного диска. Например при весьма сильных и глубоких рисках на всей поверхности тормозного диска. Из соображений безопасности минимальная толщина тормозного диска после проточки должна быть не менее 39-40 мм.
Однако некоторые изготовители транспортных средств имеют свои требования по необходимости проточки тормозных дисков которые следует учитывать.
В следствии всего предлагается внести конструкторские модификации барабанного тормозного механизма с целью увеличить срок службы фрикционных накладок.
С этой целью предлагается решать эту проблему используя идею наличия системы предотвращающий скорый износ фрикционных накладок за счет увеличения пятна контакта и усилия в гидравлических тормозных механизмах заднего моста автомобилей Volkswagen golf 2.
Принцип действия этой системы состоит в следующем. При постепенном истирании фрикционных накладок отверстии между распорной планкой и колодкой расширяется а рычаг находящийся в этом отверстии под действием пружины опускается в это отверстие. Тем самым компенсируется износ колодок («подводит их») за счет постепенного опускания рычага диаметр барабана остается прежним несмотря на истирание фрикционных тормозных накладок следовательно такие тормоза в нуждаются в замене накладок только в самом крайнем случае.
2.Обоснование принятых решений.
При решении этого вопроса (износа тормозных колодо) наиболее подходящей является система основанная на использовании распорной планки и подпружиненного рычага. Подобная конструкция не только является более простой для реализации но и может своими технологическими экономическими и прочими характеристиками. Рассмотрим вопрос более подробно и сравним характеристики тормозного механизма до и после принятие предложения по улучшению. С точки зрения точки экономики производство такого механизма будет незначительно увеличено но эти потери можно сократить и финансово выиграть на этом. Так как любой клиент при получении полной информации о механизме согласится что это того стоит. С технологической точки значительно упрощает ТО тормозов и их использование т.к. при первой установке тормозного механизма о не вообще можно не беспокоится до самого выхода тормоза из строя при этом не сокращается а даже продлевается срок службы.
3.Ожидаемые технико-экономические показатели.
На примере модели тормозного режима качения колеса рассмотрим работу тормозного механизма и его характеристики. Наиболее полное представление о технико-экономических показателях можно получить при использовании программ САПРа. Воспользуемся средствами моделирования MatLABSimuLink для получения зависимостей показателей тормозного механизма.
3.1 Моделирование тормозного режима качения колеса.
Расчетная схема для тормозного режима качения колеса представлена на рис.3:
Рис.1 Расчетная схема
Запишем уравнения движения колеса:
Где V – скорость; R Px – сила действующая со стороны остова Mт – ведущий момент rd – свободный радиус mf – момент сопротивления качению.
Где - радиус качения без скольжения.
Здесь .Где Rz – реакция поверхности.
Момент сопротивления
Коэффициент взаимодействия движителя с опорным основанием рассчитывается по формуле:
Коэффициент буксования Где – угловая скорость.
Математическую модель системы будем составлять с помощью программы MatLABSimuLink. Для этого необходимо задать исходные данные (рис.4)
Рис.2. Задание исходных данных (m-file)
Исходя из записанных выше выражений составим математическую модель системы (рис.3):
Рис.3. Математическая модель системы без АБС
Рис. 4 График зависимости скорости движения от времени без использов ания АБС
Описание принципа работы выбранного узла.
Широко распространенные на автомобилях барабанные тормозные механизмы отличаются силовым воздействием колодок с разжимным устройством и барабаном а также расположением опор тормозных колодок.
Схема барабанного тормозного механизма с равными приводными силами и односторонним расположением опор а также статическая характеристика механизма представлены на рис. 5.
Рис. 5. Схема (а) и статическая характеристика (б) барабанного тормозного механизма с равными приводными силами и односторонним расположением опор: 1 — первичная колодка; 2 — вторичная колодка; 3 — тормозной цилиндр; а с —расчетные размеры.
Для этого тормозного механизма характерным является следующее. Приводные силы и прижимающие колодки 1 и 2 к барабану равны () так как площади поршней тормозного цилиндра 3 одинаковы. Нормальные реакции барабана и на колодки не равны между собой (). Момент создаваемый силой трения и действующий на колодку 1 совпадает по направлению с моментом приводной силы вследствие чего колодка захватывается барабаном а сила трения способствует прижатию колодки к барабану. Момент силы трения действующий на колодку 2 противоположен по направлению моменту приводной силы и поэтому сила трения препятствует прижатию колодки 2 к тормозному барабану.
Колодка 1 называется первичной (активной самоприжимной) а колодка 2— вторичной (пассивной самоотжимной). Первичная колодка нагружается больше чем вторичная. При вращении колеса в противоположную сторону (движение автомобиля задним ходом) функции колодок изменяются и колодка 2 работает как первичная а колодка 1 — как вторичная.
В связи с тем что реакции барабана и на колодки а также силы трения и не равны между собой подшипники ступицы колеса нагружаются дополнительной силой. Такой тормозной механизм является неуравновешенным. Число торможений при движении автомобиля вперед значительно больше чем при движении задним ходом. Поэтому тормозная накладка первичной колодки изнашивается гораздо интенсивнее чем вторичной. Для уравнивания изнашивания фрикционная накладка первичной колодки обычно делается длиннее чем у вторичной колодки ( где — угол охвата соответственно первичной и вторичной колодок).
Принцип действия: При работающем двигателе и отпущенной педали компрессор накачивает воздух в баллоны где он хранится под давлением. Из баллонов воздух поступает к тормозному крану от тормозного крана воздух поступает через верхнюю секцию в баллоны прицепа. При нажатии на педаль тормоза верхняя секция закрывается и воздух прекращает поступать к прицепу. Тормозной кран прицепа открывается и воздух из баллонов прицепа поступает в пневмокамеры прицепа и прицеп начинает затормаживать. Нижняя секция тормозного крана автомобиля открывается и воздух поступает из баллонов автомобиля к пневмокамерам автомобиля и автомобиль начинает затормаживать. Воздух поступая в пневмокамеры давит на диафрагму она сжимая пружину смещается и давит на толкатель а он передаёт усилие на рычаг и валик разжимного кулака. Разжимной кулак поворачивается и разводит колодки. Колодки прижимаются к барабану и за счёт трения затормаживают его. При отпускании педали тормоза всё возвращается в исходное положение за счёт возвратных пружин а воздух из пневмокамер выходит в атмосферу через кран.
При движении автомобиля вперед при торможении каждая колодка работает как первичная и эффективность тормозного механизма при одинаковых размерах его основных деталей выше чем у тормозного механизма с совмещенными опорами. При торможении во время движения задним ходом колодки работают как вторичные поэтому эффективность механизма значительно снижается. Следовательно тормозной механизм является нереверсивным. Интенсивность изнашивания тормозных накладок колодок одинакова так как обе колодки работают в одних и тех же режимах.
1.Расчеты подтверждающие работоспособность конструкции.
Известны три метода расчета: аналитический графоаналитический и графический. Воспользуемся аналитическим методом определения тормозного момента создаваемого тормозом.
Вывод формул для расчета тормозного момента основывается на рассмотрении равновесия колодки ( с одной или двумя степенями свободы) под действием внешних сил. При этом делаются следующие допущения:
Давление на накладку на выделенном элементарном участке расположенном под углом к линии ОС (см. рис5) одинаково по всей ширине накладки;
Закон распределения давлений по длине накладки не изменяется с изменением сил F разжимающих колодки где pma
Коэффициент трения между накладкой и барабаном остается постоянной на всех режимах торможения
На элементарный участок накладки dα действуют элементарная нормальная реакция dN со стороны барабана и возникающая при вращении барабана элементарная сила трения dF в плоскости где касательной к поверхности трения: где b – ширина накладки r – радиус тормозного барабана.
Подставляя в последнее выражение значение p согласно формуле получаем
Тормозной момент М12 на колодке создаваемый силами трения между накладкой и барабаном (2.3) Для определия pmax записывается сумма моментов относительно точки поворота колодки С: (2.4)
Заметим что на колодках двумя степенями свободы точкой поворота колодки является точка соприкосновения ее с плоской опорой.
Подставляя выражение dF и dN и учитывая что l=r-scos α после преобразований имеем
Подставив выражение (2.5) в уравнение (2.3) и разделив числитель и знаменатель на получаем уравнение для тормозного уравения одной колодки
Знак «минус» в знаменателе уравнения (2.6) берется для активной колодки а знак «плюс» для пассивной. Общий тормозной момент двухколодочного тормоза складывается из моментов обоих колодок т.е. .
Полученные уравнения (2.5) (2.9) действительны для всех барабанных тормозных механизмов как с самоустанавливающимися колодками с двумя степенями свободы так и с колодками с одной степенью свободы.
После интегрирования выражений (2.7) и (2.8) получаем при синусоидальном распределении давлений
Подставляем эти значения в (2.7) получаем для колодок с 2 степенями свободы
Знак «+» и φ1 в полученных уравнениях берутся для передней активной колодки а знак «-» и φ2 – для задней пассивной колодки. На основе характера изнашивания накладок существующих тормозов с самоустанавливающимися колодками принимается φ1=40 50° и φ2=20 30°.
Заметим что при φ1=0 и φ2=0 выражение (2.12) приобретает вид (2.10).
Согласно формуле (2.9)
Для тормозов с двумя одинаковыми активными или пассивными колодками тормозной момент и приводная сила определяется по формулам:
Тормоза с фиксированным разжимным кулаком или клином при приработанных накладках имеют M1=M2 т.е.
Из условия равновесия разжимного кулака (см. рис. 2.4 а) имеем
Исключая из уранений (2.13) и (2.14) поочередно F1 и F2 находим зависимость последних от F’ и конструктивных параметров (при допущении h1h2): где F’ – сила действующая на рычаг разжимного кулака; dk – диаметр начальной окружности разжимного кулака (рис 2.13).
Подставляя выражения F1 и F2 из (2.15) в уравнение (2.9) получаем тормозной момент для тормоза с фиксированным разжимным кулаком:
Эффективность тормозов оценивается коэффициентом эффективности тормоза
Расчет тормозного барабана. Ввиду сложности и большой трудоемкости точного расчета тормозного барабана используют приближенную методику его расчета на прочность и жесткость. При этом предполагают что барабан состоит из двух частей: цилиндра 1 и диска 2 (рис 2.14) которые соединены друг с другом шлицами так что деформации цилиндра и диска не зависимы а шлицы нужны лишь для передачи крутящего момента.
Рассматривая барабан как тонкостенный цилиндр бесконечной длины используем формулу для расчета тонкостенных сосудов где pcp – среднее давление на накладку: d6 – диаметр барабана м; – сопротивление разрыву в диаметральном сочетании барабана Па; s – расчетная толщина стенки барабана м; Mtma – коэффициент трения; Ан – суммарная площадь накладок м^2. Толщина стенки барабана
2. ТО и обслуживание механизма.
Для поддержания тормозной системы в исправном состоянии необходимо тщательно следить за техническим состоянием тормозных механизмов и их приводом. Нельзя допускать эксплуатации автомобилей (согласно правилам дорожного движения) у которых будут обнаружены следующие основные неисправности тормозной системы:
- рабочий тормоз не обеспечивает равномерного затормаживания всех колес при этом автомобиль в момент торможения разворачивается на угол более 8° или занимает полосу движения шириной более 35 м;
- при однократном нажатии на педаль рабочего тормоза не обеспечивается эффективность торможения;
- нарушена герметичность пневматической системы привода тормозов что вызывает падение давления воздуха при неработающем компрессоре на 003 МПа в течение 30 мин при свободном положении органов управления тормозами или в течение 15 мин при включенных органах управления тормозами;
- не работает манометр системы пневматических тормозов;
- компрессор не обеспечивает установленного давления воздуха в системе пневматических тормозов;
- отсутствует рабочая тормозная система прицепа (полуприцепа) если она предусмотрена заводом-изготовителем;
- рычаг стояночного тормоза не удерживается запирающим устройством;
- стояночный тормоз не удерживает автомобиль независимо от условий загрузки на уклоне не менее 16%.
В число работ по техническому обслуживанию тормозной системы входят следующие операции.
Проверка работы компрессора пневматического привода. Перед проверкой работы компрессора регулируют натяжение приводного ремня. Ремень привода должен быть натянут так чтобы при нажиме на середину ветви с усилием 30 Н прогиб ремня составлял 5-8 мм. При необходимости увеличить натяг ремня пользуются натяжным устройством позволяющим смещать ось шкива. Отпустив гайку на оси шкива и контргайку натяжного устройства поворачивают за барашек его винт до получения требуемого натяжения ремня.
Через 10-12 тыс. км пробега автомобиля надо снять заднюю крышку и проверить надежноть уплотнения.
Через 40-50 тыс. км пробега снимают головку компрессора и очищают поршни клапаны и их седла пружины а также воздушные каналы от имеющихся на них отложений. При потере герметичности клапаны притирают к седлам.
Собирая головку смазывают маслом для двигателей стержни разгрузочных клапанов и ось коромысла регулируют зазоры между регулировочными винтами коромысла и стержнями разгрузочных клапанов так чтобы они составляли 025-035 мм. Необходимо также очищать воздушный фильтр компрессора.
Проверка и регулировка регулятора давления. Регулятор давления должен автоматически поддерживать в заданных пределах давление воздуха подаваемого компрессором. Проверяют регулятор по манометру на специальном стенде.
Если давление воздуха подаваемого компрессором выходит за указанные пределы то регулятор давления следует отрегулировать.
Регулятор давления диафрагменного типа применяемый на автомобилях МАЗ регулируют изменяя натяжение двух цилиндрических пружин концентрично расположенных в верхнем корпусе регулятора. Для этого расшплинтовывают фасонную гайку подвертывают ее для увеличения давления. Снижение давления достигается уменьшением натяжения пружин.
Регулятор с клапанами шарикового типа устанавливаемый на автомобилях КрАЗ регулируют следующим образом.
Сняв кожух и отвернув контргайку поворачивают регулировочный колпак сжимающий пружину. Для увеличения давления при котором срабатывает регулятор и отключается компрессор регулировочный колпак завинчивают а для уменьшения давления отвинчивают. Затем проверяют момент срабатывания регулятора давления и включение компрессора. Если давление при котором включается компрессор выходит за пределы нормы то изменяют число регулировочных прокладок под седлом клапана. Для повышения давления число прокладок увеличивают а для снижения уменьшают.
По окончании регулировки прокладками проверяют давление отключения компрессора и если оно выходит за пределы нормы завертывают или отвертывают колпак как было указано выше. Закончив все работы туго затягивают контргайку фиксирующую положение регулировочного колпака.
Регулировка предохранительного клапана. Для предотвращения чрезмерного повышения давления в пневматической системе (при неисправном регуляторе) предусмотрена установка предохранительного клапана. На автомобилях МАЗ он располагается на компрессоре в блоке с регулятором давления а у автомобилей КрАЗ — на тройнике левого воздушного ресивера.
Регулируют клапан на срабатывание при указанном давлении регулировочным винтом ввернутым в корпус клапана и фиксируемым контргайкой. Ввертывая винт в корпус повышают давление при котором срабатывает клапан вывертывая — уменьшают его.
В данной работе был разработан барабанный тормозной механизм с пневмоприводом грузового автомобиля с колесной формулой 6х4. Проанализированы общие разработки принцип действия экономические и технические показатели возможности улучшения барабанного тормозного механизма; проанализированы все эти аспекты и произведены конструкторские улучшения механизма в техническо-экономических показателях. Все характеристики разработанного продукта полностью оправдывают ожидания которые были поставлены перед началом работы.
Алекса Н.Н. Алексеенко В.Н. Гредескул А.Б. Теория эксплуатационных свойств автотранспортных средств в примерах и заданиях: Учеб. пособ. –К.: УМК ВО 1999. –100 с.
Машков Е.А. Техническое обслуживание и текущий ремонт автомобилей КАМАЗ: Иллюстрированное издание. - Изжательство «Третий Рим»1997 – 88 с.
Вахламов В.К. Автомобили: Конструкция и элементы расчета: учебник для студ. Высш. Учеб. Заведений В.К. Вахламов. – М. : Издательский центр «Академия» 2006. – 460 с.
Комков Е.В. Volkswagen golf 2jetta 2: руководство по эксплуатации ремонту и техническому обслуживанию: Иллюстрированное издание. – «Атласы автомобилей» Москва 2002. – 250 с.
А.И. Гришкевич Д.М. Ломако В.П. Автушко и др.; Автомобили: Конструкция конструирование и расчет. Системы управления и ходовая часть: Учеб. Пособие для вузов Под ред. А.И. Гришкевича.- Мн.: Высш. Шк. 1997. – 200с.: ил.
4.cdw

2.cdw

Е. Клапан контрольного вывода контура
С. Клапан контрольного вывода контура
D. Клапан контрольного вывода контура
КФ МГТУ им. Н.Э. Баумана
Масловлагоотделитель
Предохранитель от замерзания
Тройной защитный клапан
Пневматический цилидр привода механизмов вспомогательного
Пневматический цилиндр привода механизмов вспомогательного
Кран управления стояночным тормозом
Конденсационный ресивер
Кран слива конденсата
Датчик падения давления
Клапан защитный. Одинарный защитный клапан
Двухсекционный тормозной кран
Пневмоэлектрический датчик включения электромагнита
пневсоклвпана прицепа (полуприцепа)
Клапан ограничения давления
Двухстрелочный манометр
Тормозная передняя камера типа 24
Перепуской двухмагистральный клапан
Ускорительный клапан
Регулятор тормозных сил
Клапан управления тормозами прицепа с двухпроводным
Тормозная камера с пружинным энерго акамулятором типа
Клапан управления тормозами прицепа с однопроводным
Датчик включения сигнала торможения
Соединительные головки типа "Палм
Соединительная головка типа "А
8 Анализ.cdw

Деформированная планка
Распределение напряжений
Распределение смещений
3.cdw

КФ МГТУ им. Н.Э. Баумана
Ролик колодки тормоза
Ось ролика колодки тормоза
Накладка осей колодок
Пружина регулировочного устройства
Рычаг тормозных колодок
5.1A3.cdw

1.cdw

Тех характеристика автомобиля:
Тип двигателя дизельный 4-х тактный V-образный
Максимальная мощность
Максимальный крутящий момент
Коробка перемены передач
-ти ступенчатая с делителем
Передаточные числа КПП:
Передаточные числа делителя:
Передаточное число главной передачи
Минимальный радиус поворота
Максимальная скорость
Полная масса автомобиля
Снаряженная масса автомобиля
Чертеж.cdw
КФ МГТУ им. Н.Э. Баумана
математическая модель системы торможения автомобиля
График зависимости скорости движения от времени
Уравнения движения колеса
7.cdw

Заявка: 201214196011
Заявка: Заявка: 200912798511
на каждую тормозную
колодку в отдельности
что ведет к усложнению
КФ МГТУ им. Н.Э. Баумана
Анализ методов компенсации износа тормозных механизмов
5.2A3.cdw

Маршрутная карта(№13) - копия.cdw

съёмников и приспособлений
для разборочно-сборочных работ
Наименование и марка
Наименование и содержание операции
Ролик колодки в сборе
Запрессовать ось ролика колодки (4) в отверстие ролика колодки (3)
Колодка тормозная в сборе
Проклепать тормозную колодку (5) заклепками (17)
Установить тормозные накладки (6)
Установить ролик колодки в сборе
Установить рычаг тормозных колодок(14)
Тормозной механизм в сборе
Установить кронштейн оси колодок (18) на суппорт (8)
Совместиь оси колодок (9) с кронштейном оси колодок (18)
Закрутить гайку (19) на осях колодки (9)
Установить тормозные колодки в сборе на оси колодки (9)
Устаноить накладку осей колодок (11) на оси колодок
Зачековать оси колодок (9) чеками (10)
Установить разжимной рычаг (2)
Установить распорную планку (13)
Установить клин (1) в зазор между распорной планкой (13) и тормозной колодкой в сборе
Установить пружину (12) в отверстия рычага и тормозной колодки в сборе
Установить пружину (15) в паз распорной планки (13) и в отверстие тормозной колодки в сборе
Установить пружину (16) в паз рычага тормозной колодки (14) и отверстие тормозной колодки в сборе
Установить пружины (7) в отверстия тормозных колодок в сборе
спец.cdw
Ролик колодки тормоза
Ось ролика колодки тормоза
Накладка осей колодок
Пружина регулировочного устройства
Рычаг тормозных колодок
Рекомендуемые чертежи
- 09.04.2015
Свободное скачивание на сегодня
Другие проекты
- 29.08.2014