Зернометатель




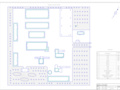
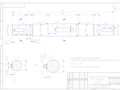
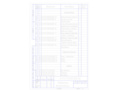
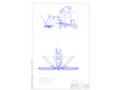
- Добавлен: 25.10.2022
- Размер: 5 MB
- Закачек: 2
Описание
Состав проекта
![]() |
![]() |
![]() ![]() |
![]() ![]() |
![]() ![]() |
![]() ![]() |
![]() ![]() ![]() ![]() |
![]() ![]() |
![]() ![]() ![]() ![]() |
![]() ![]() ![]() ![]() |
![]() ![]() |
![]() ![]() ![]() ![]() |
![]() ![]() ![]() ![]() |
![]() ![]() ![]() ![]() |
![]() ![]() |
![]() ![]() ![]() ![]() |
![]() ![]() |
![]() ![]() |
![]() ![]() ![]() ![]() |
![]() ![]() ![]() ![]() |
![]() |
![]() ![]() ![]() |
![]() ![]() ![]() |
![]() ![]() ![]() |
![]() ![]() ![]() |
![]() ![]() ![]() |
![]() ![]() ![]() |
![]() ![]() ![]() |
![]() ![]() ![]() |
![]() ![]() ![]() |
![]() |
![]() ![]() |
![]() ![]() |
![]() ![]() ![]() ![]() |
![]() ![]() ![]() ![]() |
![]() ![]() ![]() ![]() |
![]() ![]() |
![]() ![]() |
![]() ![]() ![]() ![]() |
![]() ![]() |
![]() ![]() ![]() ![]() |
Дополнительная информация
Ротор со ступицей.dwg

Общий вид.dwg

Установленная мощность -
Высота подъема зерна - 1
*Размеры для справок.
Заедание вращающихся деталей не допускается.
Направляющая.dwg

Экономика.dwg

Балансовая стоимость
атраты на зароботную
затраты на ремонты и тех.
эксплуотационных затрат
Стоимость травмируемого
Дополнительная экономи
Общая годовая экономия
Чистый дисконтированный
Технико-экономические
Лопатка.dwg

Вал привода ротора.dwg

Неуказанные предельные отклонения размеров выполнить валов
Остальные кромки притупить R 0
Готовый план мехтока.dwg

Рама с метателем.dwg

Наставка.dwg

Неуказаный размер выреза равен 5мм.
Вывод.docx
ВВЕДЕНИЕ, раздел 1.doc
Увеличение производства зерна в последние годы вызывает определённую сложность в его производстве. Особое внимание в производстве зерновых уделяется послеуборочной обработке зерна. Зерновой ворох поступающий на послеуборочную обработку представляет собой смесь зерна основной культуры семян других растений (сорных) минеральных (комочки земли) и органических (полова частицы растений) примесей. Задачей послеуборочной обработки является доведение качества зерна до требуемых кондиций установленных государственным стандартом.
Большое значение в послеуборочной обработке уделяется предварительной очистке зернового вороха. Качество и степень предварительной очистки оказывают большое влияние на качество выполнения остальных операций послеуборочной обработки (первичная и вторичная очистка). Традиционная технология очистки зерна предусматривает последовательный пропуск зернового вороха через целый комплекс зерноочистительных машин на каждом из которых выделяются примеси различного состава. В результате этого зерно основной культуры подвергается многократному воздействию рабочих органов что приводит к повышению дробления и травмирования зерна и в итоге сказывается на его товарных продовольственных и семенных качествах как готового продукта.
Кроме этого сложные погодные условия и увеличение урожайности зерновых вызывают колебания качественных и количественных характеристик зернового вороха в частности влажности и засорённости. Увеличение допускаемых норм влажности и засорённости приводит к снижению производительности зерноочистительных машин на 2% на каждый процент увеличения засорённости и на 5% на каждый процент увеличения влажности 28.
Неравномерность поступления зерновой массы с полей приводит к скоплению зерна в буртах на открытых площадках зернотоков. Вследствие несвоевременной предварительной очистки т.е. хранения в течении 1-2 суток свежеубранного зернового вороха на площадке зернотока приводит к снижению энергии прорастания до 18% а всхожести семян до 8% 13 45 46 47. Во избежание последствий такого рода в сельскохозяйственном производстве предусмотрены рабочие органы машин предназначенные для перелопачивания свежеубранного зернового вороха – это метатели. Несмотря на разнообразие конструкций метательных рабочих органов наибольшее распространение для обработки зерна получили ленточные метатели. Так метательный рабочий орган применяется в конструкции машин ЗМ и ЗПС. Также метательный рабочий орган является неотъемлемой частью пневмоинерционных сепараторов которые были разработаны в 80-е годы под руководством Н.И. Косилова 1. Пневмоинерционные сепараторы предназначены для очистки грубого зернового вороха и разделения его на фракции.
Исследованиями 2 устновлено что применение метательного рабочего органа в процессе предварительной очистки зернового вороха позволяет снизить его влажность на 3% избавиться от вредителей и разделить зёрна на сорта. Однако применение метательных машин ограничено вследствие повреждения зерна между бесконечной лентой и прижимным барабаном 3. Кроме этого использование машин марки ЗПС не даёт существенных результатов (частичного подсушивания и предварительной очистки) при обработке увлажнённого зернового вороха из-за незначительной скорости метания.
Анализ конструкций зернометательных машин показал что они требуют дальнейшего совершенствования с целью снижения травмирования зерна и повышения эффективности работы.
1 Характеристика землепользования
Центральный населённый пункт хозяйства село Краснопартизанское размещён в 6 км. От районного центра ст. Павловская и в 174 км. от г. Краснодара.
Связь с районным центром осуществляется по дороге имеющей асфальтное покрытие. В ст. Павловской находятся пункты сдачи сельскохозяйственной продукции: элеватор сахарный завод и др. базы снабжения; объединения «Сельхозтехники» и «Сельхозхимия» ж.д. станция.
На территории хозяйства хорошо развита сеть внутрихозяйственных дорог. Бригадные станы тока машинные дворы и животноводческие фермы обеспечиваются связью по дорогам с асфальтным и гравийным покрытием земельные участки с производственными центрами в основном по улучшенным грунтовым дорогам.
Земли хозяйства размещены в одном массиве. Общая площадь составляет 10544 га. в том числе сельскохозяйственных угодий 9360 га. из них пашни – 9093 га. Распаханность территории высокая – 862%.
Климатические условия хозяйства соответствуют биологическим требованиям большинства сельскохозяйственных культур возделываемых в данной природно – сельскохозяйственной зоне и позволяют при соответствующем росте матриально – технической базы значительно увеличить наращивание биологической массы.
Территория хозяйства представляет слаборазвитую равнину сильно расчлененную многочисленными балками и рекой Тихонькой. Долина реки развита слабо. Склоны балок обычно неширокие пологие они повсеместно распаханы до основания. Глубокие участки балок заболочены.
2 Краткая историческая справка
За период существования хозяйства было произведено зерновых культур 196353 тонны подсолнечника 148672 тонн.
До 2009 года в хозяйстве находилось поголовье КРС в количестве 1500 голов. Было произведено мяса в живом весе 3986 тонн.
Численность работающих изменилась с 470 человек в 2002 году до 148 человек в 2009 году.
Экономическую характеристику хозяйства начинают с определения размеров предприятия. Для того чтобы определить размеры предприятия необходимо охарактеризовать данные о производстве валовой и товарной продукции об общей земельной площади численности работников стоимости основных фондов приведенных в таблице 1.1
Отношение 2009г. в % 2007г. 2008г.
Общая земельная площадь га
-сельскохозяйственных угодий
Среднегодовая численность работников человек
- в том числе занятых в сельском хозяйстве
Среднегодовая стоимость основных фондов тыс.руб.
Произведено валовой продукции тыс.руб.
- фактическая стоимость
- стоимость товарной продукции ( в ценах реализации) тыс. руб.1
Послеуборочная обработка зерна направлена на приведение убранной с полей зерновой массы в стойкое при хранении и улучшения качества принятого зерна. Полный цикл послеуборочной обработки включает в себя: приёмку зерна предварительную очистку от примесей и формирование партий сушку и активное вентилирование.
Одно из важных мероприятий в послеуборочной обработке занимает - предварительная очистка которая позволяет повысить сыпучесть материала снизить затраты на сушку и в целом повысить производительность остальных зерноочистительных машин.
5 Анализ конструкций зернометателей
В разное время в сельскохозяйственном производстве нашли применение три основных вида зернометателей: ленточные вентиляторные и лопастные. Наибольшее распространение из них получили ленточные и вентиляторные зерномёты.
5.1 Ленточные зернометатели
После зерновой материал поступал на сито 9 освобождался от крупных примесей и поступал на сита 10 11 и 12 для окончательной очистки от примесей.
Выше рассмотренные зернометательные машины имеют целый ряд недостатков. Одним из основных недостатков является травмирование зерна рабочим органом зернометателя. Характер травмирования заключается в истирании скольжении и сжатии зернового вороха на большой скорости в промежутке между прижимным барабанном и бесконечной лентой. Применение прорезиненной бесконечной ленты в зернометателе приводило к быстрому её износу. Неправильное регулирование ленты натяжением приводило к тому что она часто набегала на торцевые рёбра цилиндрических барабанов.
В последствии зерномёты созданные И.А. Бороненко были лишены последнего недостатка. Для обеспечения плавности и устойчивой работы бесконечной ленты поверхности ведущего и ведомого барабанов посредине были выполнены слегка выпуклыми. Применение данного элемента в конструкции барабанов позволило увеличить срок службы ленты которая работала три-четыре сезона против ленты применяемой на зернопульте ВИМ-10 которая не выдерживала и одного сезона. Подобные зернопульты были сконструированы Лопатинским зерносовхозом. Все барабаны этого зернопульта были изготовлены пустотелыми из берёзовых досок и соответственно выглядели бочкообразно. Применение деревянных барабанов подобной формы в конструкции данного метателя с одной стороны обеспечивало устойчивую работу машины а с другой не обеспечивало длительного срока службы барабанов.
Ленточный метательный рабочий орган использовали также в зерноочистительных машинах высокой производительности. Примером служит зерноочистительный агрегат конструкции Гладышева (рисунок 1.3). Зерномёт дополнительно очищает и разделяет зерно по удельному весу. Его использовали также для загрузки зерна в автомобили.
В сельскохозяйственном производстве широкое применение получили также зернометатели ЗМ-30 4 разработанный на базе известных ленточных зернопультов. Метатель позволяет загружать склады с высотой укладки до 35-40 метров а также формировать высокие бурты на открытых токах. Триммер метателя может поворачиваться вокруг своей оси что даёт возможность непрерывно погружать зерно в машины и автопоезда а при погрузке складов – перемещать зерно по обе стороны или ссыпать его сзади погрузчика.
На базе ЗМ-30 был разработан зернометатель ЗМ-60 (ЗММ-90) который имеет те же габаритные размеры но имеет производительность вдвое больше и соответственно мощность больше на 45 кВт. Впоследствии ЗМ-60 был модернизирован на ЗМ-60А. Самоходный метатель включает раму 1 установленную на трёхколёсный ход загрузочный механизм 3 с питателями 4 механизм 5 самохода электропривод 6 и поворотный триммер 7 с направляющей трубой 8 (рисунок 1.4).
Несмотря на возможности зернометательных машин и необходимость выполнения некоторых операций предварительной обработки зернового вороха многие зернометательные машины и зернопогрузчики вообще были сняты с производства. Это связано с многочисленными жалобами агрономов ещё в начале 60-х годов на то что зернометатели в процессе работы повреждают зерно в несколько раз превышая допустимые нормы. В частности по результатам исследований учёных С.А. Чазова и В.Ф. Плаксина известно 5 что травмирование зерна зернопультом составляло 165 % (таблица 1.2).
Таблица 1.2 – Результаты по травмированию семян зернопультом
в том числе зародыша
После зернопульта за 2 м
После зернопульта за 4 м
После зернопульта за 8 м
Результаты отчётов МИС по дроблению зерна метателями 73 75 81 представлены в таблице 1.3
Таблица 1.3 – Результаты по дроблению зерна метателями
На сегодняшний момент ЗМ-60А (или ЗМЗ-60) является одной из основных зернометательных установок применяемых в сельскохозяйственном производстве 6. В процессе работы этот метатель повреждает зерно и не производит чёткого разделения зернового вороха при метании (особенно в безветренную погоду) так как происходит скольжения зернового вороха в промежутке между прижимным барабаном. Поэтому одинаковые частицы по размерам и аэродинамическим свойствам падают на разном расстоянии от машины тем самым вновь перемешиваясь с сорной примесью.
Применение ЗПС-100А в этом направлении также не даёт ощутимых результатов так как из-за низкой скорости выбрасываемой струи и создание при этом попутного воздушного потока происходит незначительное охлаждения и отделение сорной примеси от зернового вороха.
С учётом выше изложенных недостатков на сегодняшний день ленточные метательные машины применяются только для обработки фуражного зерна.
5.2. Вентиляторные зернометатели
Для снижения травмирования зерна были разработаны вентиляторные метатели. Вентиляторные метатели применяли двух типов: с короткой выкидной трубой и с приставным трубопроводом.
Рабочий процесс вентиляторного зернометателя осуществляется так. Питатель опускают на бурт зерна и скребками подают его в засыпной ковш. Из ковша зерно засасывается в патрубок 6 из которого выбрасывается воздушным потоком. Для погрузки зерна в автомобиль предусматривается удлинённый сменный патрубок.
Конструкция машины предложенная М.М. Мисник (рисунок 1.6) относится ко второму типу вентиляторных зернометателей с приставным трубопроводом. Данный зерномёт предназначен для транспортирования зерна семян половы на расстоянии до 100 метров и в высоту до 15 метров. При оборудовании машины ёмкостью в 10-12 т можно за 15-2 мин загрузить зерном автомобиль. В состав зернопульта входит (рисунок 1.6) рама 1 вентилятор 4 бункер 5 питатель 6 трубопровод 7 и электродвигатель 8. К раме крепится корпус вентилятора 2. Корпус состоит из двух деревянных щёк между которыми расположен жестяной кожух вентилятора 3. Скорость воздуха создаваемая вентилятором составляет 70 мс.
Электродвигатель мощностью 7 кВт с частотой вращения 1450 обмин. Производительность установки 5 тч. При отсоединении трубы установка используется как обычный метатель зерна. Как отмечал Кукибный А.А. преимуществами данного зерномёта является простота конструкции сравнительно невысокая металлоемкость и надёжность. Распространенного применения этот зерномёт не получил по нескольким причинам. Во-первых из-за большой энергоёмкости рабочего процесса во-вторых из-за низкой производительности машины.
В настоящее время в небольших семеноводческих станциях и предприятиях используется агрегат на основе вентиляторного зернопульта – загрузчик семян броскового типа ЗСБ-4. Применение данной машины ограничено вследствие малой производительности – 4 тч. ЗБС-4 предназначается для подачи сыпучих семян трав зерновых крупяных культур в селекционно-семеноводческие машины.
В последствии сельскохозяйственные предприятия отказались от использования вентиляторных зернопультов. Главной причиной является большая энергоёмкость и значительные затраты труда на осуществление рабочего процесса таких машин. Кроме этого происходит повреждения зерна при его обработке на машинах данного типа вследствие больших скоростей метания.
5.3 Лопастные зернометатели
Лопастной зерномёт представляет собой сдвоенный ротор 1 (рисунок 1.7) который имеет 20 прямых лопаток из которых 10 коротких 3 а остальные – длинные 4 находящиеся в кожухе с раструбом 3. Подача зерна к ротору торцевая с двух сторон. К ротору зерно подаётся вспомогательными винтами 5 и 6 окружная скорость которых 10 мс (диаметр 130 мм). Диаметр ротора составляет 315 мм а окружная скорость 235 мс.
Дальность метания 17 м. Производительность зерномёта 60 тч. Требуемая мощность 12 кВт. Существенным недостатком в работе этой машины является травмирование зернового материала метательным рабочим органом. Повреждение зерна происходит за счёт ударного воздействия лопаток ротора о кожух и обратно. Поэтому данную конструкцию зерномёта нельзя использовать для работы с семенным зерном.
Оригинальную конструкцию метательной машины имеет турбопульт системы Григоровича (рисунок 1.8).
Турбопульт предназначен для работы на зерновых складах и токах а также для разравнивания зерна в трюмах судов. Турбопульт состоит из турбины 3 винта 4 и электродвигателя 1. Винт подаёт зерно из кучи в турбину. В кожухе 2 турбины 3 находится диск прикреплённый к валу электродвигателя. К диску приварены 12 больших и 12 малых лопаток чередующихся между собой. При вращении диска лопатки сообщают зерну необходимую скорость. Материал выбрасывается из трубы 5. Производительность турбопульта 20-25 тч. Мощность электродвигателя 32 кВт. Достоинством этой машины является то что она имеет небольшие габаритные размеры и незначительную мощность электродвигателя. Несмотря на достоинства этого зерномёта из-за травмирования зерна лопатками диска вследствие большой окружной скорости не получил большого распространения.
По исследованиям Кукибного А.А. 7 известно что для подъема насыпи в складах и выполнения погрузочно-разгрузочных операций а также для проветривания зерна в передвижном ленточном конвейере применяли барабаны-зерноукладчики или крыльчатки. Барабан-зерноукладчик включает барабан на поверхности которого расположены продольные лопасти покрытые резиной. Ось барабана прикрепляется к раме конвейера. Барабан-зерноукладчик приводится во вращение от концевого барабана с помощью ремённой передачи. Зерновые материалы бросаются лопастями на высоту 45 м что является весьма важным для немеханизированных складов. По устройству и принципу работы крыльчатка имеет много общего с барабаном-зерноукладчиком и применяется для заполнения дальних площадок склада. Применение барабана-зерноукладчика или крыльчатки в составе передвижного ленточного конвейера значительно снижает затраты энергии и труда.
Лопастные (роторные) зернометательные машины по сравнению с ленточными и вентиляторными пользовались незначительным спросом у сельскохозяйственных предприятий. Недоверие вызывало то что в процессе работы на зерно оказывалось значительное ударное воздействие рабочих органов лопастных машин. Хотя по сравнению с остальными метательными машинами лопастные обладают меньшей металлоемкостью конструкции и меньшей энергоёмкостью выполняемого процесса.
5.4 Зернометательные рабочие органы Ханхасаева Г.Ф.
Порционные зернометательные установки разработанные под руководством Ханхасаева Г.Ф. можно отнести также и к комбинированным метательным рабочим органам. Под комбинированным зернометателем понимается устройство сочетающее два типа метателей. Устройство рабочего органа такого метателя заключается в сочетании ленточного и лопастного зернопультов.
Порционный метатель по 8. Авторы: Ханхасаев Г.Ф. Кирилов К.А. Хамаганов А.Г. Нуртазин И.Т. Мунхоев Н.И. и Ханхасаев А.Н.
Порционный метатель состоит из ведущего 1 ведомого 2 и лопастного 3 барабанов охваченных бесконечной лентой 4 и приемного бункера 5 (рисунок 1.9). Лопастной барабан 3 консольно установлен на двух подшипниковых опорах 6 содержит несущий диск 7 закреплённый на валу 8 с помощью болтов 9 и соединённый посредством лопаток 10 с кольцеобразным торцевым диском 11. Лопатки 10 наклонены под углом 450 вперёд в сторону вращения барабана 3 и образуют две группы в каждой из которых начиная с минимального размера каждая последующая лопатка длиннее предыдущей на заданную величину.
Принцип работы метателя аналогичен выше рассмотренному метателю. Отличие состоит в том что каждая последующая лопатка лопастного барабана длиннее предыдущей лопатки поэтому забирают материала ещё больше. Если зерновка не попала на предыдущую лопатку то её обязательно подхватит последующая т.е. будет происходить наиболее полное заполнение межлопаточного пространства лопастного барабана поступаемым материалом и тем самым повысится производительность метателя.
Некоторые из конструкций выше рассмотренных зернометателей разработанные под руководством Ханхасаева Г.Ф. рекомендованы для обработки семян зерновых материалов. Несмотря на оригинальную конструкцию комбинированных (порционных) зернометателей они снижают повреждение зерна но не значительно. Это особенно проявляется при повышении скорости метания свыше 14 мс. Повреждение зерна происходит во внутренней полости лопастного барабана непосредственно в зоне контакта лопаток барабана и зерна из-за большой разности скоростей движения материала и лопаток барабана. Часть зерна повреждается также между бесконечной лентой и кромкой лопатки прижимного барабана. Чтобы снизить травмирование такого рода необходимо техническое решение позволяющее уменьшить до минимума разность скоростей движения зернового вороха и лопаток прижимного барабана. Кроме выше перечисленного в работах Ханхасаева Г.Ф. недостаточно уделено внимание теоретическому обоснованию процесса взаимодействия зерновки с лопаткой.
Рисунок. 1.10 – Комбайн ДОН – 1500Б.
Комбайн зерноуборочный самоходный "ДОН-1500Б" предназначен для уборки зерновых колосовых культур на равнинных полях с уклоном поля не более 80 во всех зерносеющих хозяйствах. Комбайн производит срез или подбор хлебной массы обмолот сепарацию зерна сбор и выгрузку зерна из бункера уборку незерновой части урожая.
Зерноуборочный самоходный комбайн "ДОН-1500Б" состоит из жатвенной части платформы – подборщика молотилки бункера с выгрузным устройством приспособленный для уборки незерновой части урожая (копнитель измельчитель капот) моторной установки силовой передачи ходовой системы органов управления кабины с площадкой управления гидравлической системы электрооборудования и электронной системы контроля.
Основные регулировки:
- высота среза (копирующими башмаками гидроцилиндром подъема жатки управляемым из кабины);
- обороты молотильного барабана изменением частоты вращения клиноременным вариатором – гидроцилиндром управляемым из кабины;
- обороты вентилятора изменением частоты вращения клиноременным вариатором – гидроцилиндром управляемым из кабины;
- зазор между барабаном и подбарабаньем на выходе в зависимости от убираемой культуры устанавливается рычагом механизма управления подбарабаньем установленным на площадке водителя;
- зазоры между гребенками решет и жалюзями изменяются в зависимости от количества вороха поворотом рычага через съемный лючок в левой панели.
Таблица 1.4 – Техническая характеристика.
Габаритные размеры комбайна с
жатвенной частью шириной захвата 6 м
-в рабочем положении
Вместимость зернового бункера м3
Рабочая скорость кмч
Рисунок. 1.10 – Зернометатель самопередвижной ЗМ – 60
Техническая характеристика принцип работы достоинства и недостатки представлены в пункте 1.5.1.
Рисунок. 1.11 – ЗАВ – 40.
Зерноочистительный агрегат ЗАВ-40 предназначен для механизированной очистки вороха зерновых культур с комплексной механизацией погрузочно-разгрузочных работ. В результате обработки за однократный пропуск через машины продовольственное зерно доводиться до базисных кондиций а семена - до норм чистоты не ниже III класса.
Таблица 1.5 – Техническая характеристика.
Предварительная очистка
Производительностьтч
Входные параметры зерна
Объемная масса 760 кгм3
сорной примеси до 10%
соломистой примеси до 1%
засоренность до 10%
средняя натура 760 гл
Вместимость емкостейм
Бункер чистого зерна – 64
Бункер отходов – 48
Высота под бункером – 3м;
мощность комплекса – 405 кВт;
обслуживающий персонал – 1 чел;
Производительность зависит от засоренности и влажности зерна и уменьшается при повышении этих параметров.
- качественная работа комплекса;
- предварительная очистка возможность семенной очистки;
- возможность обработки менее качественного зерна;
- увеличенный объем бункеров;
- рациональное распределение автомобильной техники при отгрузке зерна и вороха;
- доступная цена комплекса в своем классе;
- высота под бункерами 3м (проезд «Камаза») – Возможность последующего доведения до миниэлеваторного комплекса (сушилка силосы).
- не самая высокая производительность (40-50 тч);
- невозможность предварительного расслоения вороха перед подачей на рабочие органы;
- влияние гравитационных сил многократно действующих на семенной материал.
Таблица 1.5 – Комплектация.
Машина первичной очистки зерна ЗВС-20А
Блок триерный БТ-600
Машина предварительной очистки зерна МПО-50
Нория 2НПК-20(129 м)
Рисунок. 1.12 – Технологическая схема ЗАВ – 40.
На основании выше изложенного сформулирована цель проекта заключается в снижении травмирования семян роторным зернометателем за счёт совершенствования его параметров и технологического процесса работы.
Для достижения поставленной в проекте цели определены следующие задачи исследования:
Произвести агротехническую оценку работы зернообрабатывающих машин на предприятии.
Исследовать некоторые механические характеристики зерна районированных сортов пшеницы.
Теоретически обосновать параметры и режимы работы роторного метателя зерна.
Произвести прочностной расчёт предлагаемого рабочего органа.
Определить экономическую эффективность использования разработанного технического средства.
раздел 2.doc
1 Методика и результаты исследований посевных качеств
К основным посевным качествам семян относят силу роста всхожесть и энергию прорастания. Эти показатели определяли путём проращивания.
Для определения силы роста из семян основной культуры отбирают 4 пробы семян по 100 штук. Семена проращивают между полосками увлажненной фильтровальной бумаги помещая в рулон I пробу в I00 семян. Полосы бумаги нарезают размером 20x100 см. Для ложа используется двойная полоса бумаги для покрытия - одинарная. На первой полосе записывается номер образца номер повторности дата закладки семян на проращивание а также посередине проводится карандашом линия на которую раскладывают семена. Сложенные полосы фильтровальной бумаги увлажняют водой опуская в воду а затем давая избытку воды стечь и кладут на стол так чтобы полоса с надписями была внизу. Семена раскладывают равномерно вдоль всей проведенной линии зародышем вниз. Затем берут одинарную полосу бумаги увлажняют её и накрывают ею семена. Чтобы улучшить воздухообмен при прорастании семян в зоне расположения семян накладывают коррексовую ленту.
Полосы фильтровальной бумаги с семенами свертывают в рулоны и ставят вертикально в сосуды на дно которых наливается небольшое количество воды. Сосуды помещают в термостат проращивание ведут течение 5 дней при температуре + 20°С в темноте.
После окончания срока проращивания рулоны разворачивают снимают коррексовую ленту и верхнюю полосу фильтровальной бумаги и проводят оценку проростков.
К нормально развитым относят проростки имеющие здоровые корешки и росток у зерновых культур корешков должно быть не менее двух. Ростки должны быть с неповрежденным колеоптилем а зеленые листочки в колеоптиле должны занимать не менее половины его длины.
Таблица 2.1 – Средние результаты по определению силы роста.
1.2 Всхожесть и энергия прорастания
Под всхожестью понимается процент нормально проросших семян за определенный срок в оптимальных условиях температуры влажности и освещения. Энергия прорастания показывает дружность появления нормальных проростков за более короткий срок.
Для проведения опыта произвели отбор навесок зерна. Далее из каждой навески выделяли четыре пробы по 100 семян.
Всхожесть и энергию прорастания определяли способом проращивания – в рулонах. На двух слоях увлажнённой фильтрованной бумаги размером 10×100 см (± 2 см) разложили одну пробу семян зародышами вниз по линии проведённой на расстоянии 2-3 см от верхнего края листа. Сверху семена накрывали полоской увлажнённой бумаги такого же размера. Затем полосы неплотно свёртывали и в вертикальном положении помещали в растильню.
Энергию прорастания семян определяли через четыре дня после закладки пробы. Всхожесть определяли через 8 дней после закладки. К числу нормально проросших относят семена имеющие не мене двух нормально развитых корешков размером более длины семени и росток размером не мене половины его длины с просматривающимися первичными листочками.
Конечный результат всхожести и энергии прорастания выразили в процентах и вычислили как среднее арифметическое из четырёх анализируемых сотен семян (таблица 2.2).
Таблица 2.2 – Результаты исследований
2 Определение микротравмирования зерна пшеницы
Микротравмирование зерна определяли методом окрашивания. Образцы отбирали по ГОСТ 12036-80. Анализировали пробы по сто семян в четырёхкратной повторности а в некоторых случаях количество повторностей увеличивали из-за значительного расхождения результатов между пробами. При анализе выделяли зёрна по типам повреждений: с повреждённым зародышем с повреждённой оболочкой зародыша и повреждённым эндоспермом. По методике С.А. Чазова предварительно каждую пробу зерна выдерживали 15 мин. в концентрированном растворе поваренной соли чтобы избежать окрашивания полноценных зёрен. Окрашивание проводили в 05% растворе конгорота в течение 5 мин. Затем раствор красителя сливали и зерно несколько раз промывали водой а затем рассыпали на марле для подсушивания. Подсушенные зёрна просматривали под лупой (×15).
Таблица 2.3 – Результаты исследований микроповреждений зерна
Анализ результатов исследований за два последние года подтверждают закономерность с увеличением числа операций обработки зерна снижаются соответственно его посевные качества и увеличивается повреждаемость.
3 Оборудование и методика определения прочностных свойств зерна пшеницы.
Исследования свойств зерна пшеницы проводились под действием нагрузок возникающих в реальных условиях работы рабочего органа экспериментального роторного зернометателя. Испытаниям подвергали единичные зёрна на сжатие.
Под действием статических нагрузок действующих на зерно при сжатии необходимо определить следующие величины:
- допускаемые усилия при которых в структуре зерновки начинают появляться микротрещины;
- усилие соответствующее пределу прочности зерновки;
- деформацию зерновки на различных этапах нагружения;
- коэффициент продольной упругости первого рода (модуль Юнга) характеризующий упругие свойства зерна.
Оборудование. Для проведения экспериментальных исследований по определению выше перечисленных характеристик разработана специальная установка состоящая из пресса с приводом от электродвигателя (12 В) с блоком питания и пультом управления усилителя сигнала фильтра сигнала и ЭВМ снабжённой платой АЦП(рисунок 2.1).
Составной частью пресса (рисунок 2.2) является металлическая платформа с поперечиной ; на платформе установлена тензобалка. Зерно устанавливается в стальную рамку со штоком (фиксатор положения зерна). Стальная рамка жёстко крепится на свободном конце тензобалки . Нагрузка создаётся с помощью винта М 13х250 закреплённого на поперечине в направляющей с внутренней резьбой. С помощью вращения винта от электродвигателя создавали усилие сжатия которое передавалось через шток рамки на зерно и соответственно на тензобалку.
Рисунок. 2.1 – Общий вид установки.
Рисунок. 2.2 – Пресс для испытаний единичных зёрен при статическом сжатии:
– металлическая платформа 2 – поперечина 3 – тензобалка 4 – зерно 5 – стальная рамка 6 – шток (фиксатор положения зерна) 7 – винт М13x15x250 8 – направляющая 9 – электродвигатель.
Методика проведения опыта. Испытаниям подвергали единичные зёрна пшеницы. Для опытов использовали навески семян после каждой операции обработки в хозяйстве. Нагружение производили со скоростью (перемещения штока) V=5 ммс. Микроповреждение исходного материала 49% и влажность – 13 %. При измерении усилия и деформации предельная погрешность составила 04. Доверительную вероятность принимаем равной α=095. Исходя из этого количество повторностей каждого опыта составляет 27 57 принимаем для нашего случая 30 повторностей. Для каждого опыта из навесок отбирали по 30 полноценных зёрен не имеющих наружных повреждений.
Опыт проходил в следующей последовательности. Зерно устанавливали в стальную рамку 5 которое свободно фиксировалось и удерживалось в определённом положении под собственным весом штока 6 (рисунок 2.2). Зёрна испытывали в различных положениях указанных на рисунке 2.3. Далее за счёт принудительного вращения винта 7 установленного в неподвижной направляющей 8 создавали усилие сжатия.
В процессе испытаний получали рабочие диаграммы сжатия зависимости усилия от деформации по которым определяли величину деформации соответствующую величине усилия на определённый момент нагружения (рисунок 2.4).
После проведения каждой серии опыта производилась тарировка тензобалки общим весом до 25 кг грузами массой 05 кг. Также проводилась тарировка величины перемещения подвижного реохорда в диапазоне от 0 до 5 мм. Для этого использовали пластины различной толщины с точностью до 005 мм.
Методика обработки данных опыта. Результатом проведения опытов на сжатие единичных зёрен являлось получение одновременно двух диаграмм: усилия и деформации сжатия в зависимости от времени.
Полученные диаграммы сжатия в большинстве случаев подобны и поэтому дают основание для описания процесса разрушения зёрен при сжатии. На каждой из полученных диаграмм были отмечены участки характеризующие процесс сопротивления зёрен внешней нагрузке.
После обработки 30 диаграмм сжатия зерна каждой серии определяли средние величины усилий и деформации соответствующие каждой фазе разрушения как среднее арифметическое вариационного ряда отдельных измерений по формуле 57:
где - сумма всех наблюдённых величин;
т – число повторностей (измерений).
Для оценки величины случайной ошибки определим среднее квадратичное отклонение от среднего значения случайной величины:
где - сумма квадратов отклонений случайной величины от среднего её значения.
Для оценки относительной изменчивости применяли коэффициент вариации:
4 Результаты исследований прочностных свойств зерна пшеницы
По степени травмирования повреждения зерна классифицируют на 2 большие группы: макро и микротравмы 19. Первая группа включает повреждения связанные с отчленением от семени какой-то части её органического вещества по второй - повреждение тканей семени (уколы вмятины ссадины и т.п.) не сопровождающиеся потерей вещества семени.
В процессе исследования свойств зерна при сжатии на установке 20 были получены диаграммы сжатия единичных зёрен.
Известна характерная особенность строения структуры зерна – анизотропия то есть неодинаковость его свойств по различным направлениям которая сильно проявляется при оценке механических свойств 45. Признаком проявления такого свойства служит неравномерность строения структуры зерна в состав которой входят: слои оболочек белковый каркас крахмальный наполнитель (в виде зёрен) зародыш 19.
В процессе опытов была подтверждена закономерность анизотропных свойств зерна (пшеницы) то есть на величину сопротивления влияет и положение зерна в момент нагружения.
Известно что характеристикой прочности любого материала является напряжение. На основе «рабочих диаграмм» определены предельные напряжения. Результаты расчётов представлены в таблице. По результатам расчётов построены диаграммы зависимости от относительной деформации (рисунок 2.5).
где Р – усилие сжатия на прессе Н;
А – площадь поперечного сечения зерновки мм2.
l – первоначальный размер зерновки мм.
Проанализировав диаграммы напряжений и оценив состояние структуры зерна на каждом из её участков можно определить значение напряжения при котором в структуре зерновки начинают появляться микротрещины. Величина напряжения (допускаемого) не вызывающего значительных изменений в структуре зерна мягкой пшеницы в положении «бочёк-бочёк» составляет 105 Нмм2 в положении «спинка-бороздка» - 849 Нмм2 в положении «стоя» - 79 Нмм2.
Анализ полученных результатов прочностных характеристик зерна после каждой из операций его обработки позволил построить графическую зависимость предела прочности зерна от количества пропусков через машины (рисунок 2.6). Прочность зёрен с увеличением количества пропусков через машины снижается особенно эффективно это наблюдается в положении «стоя».
5 Определение коэффициента упругости 1 рода (модуля Юнга)
Одной из величин характеризующих способность материала сопротивляться сжатию в пределах упругой деформации является коэффициент продольной упругости 1 рода (модуль Юнга). Чем больше модуль Юнга тем больше материал сопротивляется внешним нагрузкам в пределах упругой деформации. По результатам проделанных испытаний по формуле закона Гука определяли модуль Юнга. Для твёрдой пшеницы вл.(13%) модуль Юнга составил спинка-бороздка Е=506 МПА бочёк-бочёк Е=624 МПА стоя Е=476 МПА.
раздел 4.doc
1 Кинематический расчёт привода
Полная мощность двигателя привода метательного рабочего органа 7:
где N1 – мощность двигателя затрачиваемая на сообщение частицам кинетической энергии кВт;
N2 – мощность двигателя расходуемая на удары лопастей о частицы кВт;
N3 – мощность двигателя расходуемая на преодоление трения частиц материала о диск и лопасти кВт;
N4 – мощность двигателя расходуемая на преодоление сопротивления трения в опорах диска кВт.
где Q – производительность машины Q=40 тч;
Va – скорость метания Va=14 мс;
V0 – начальная скорость движения по лопаткам диска V0=2 мс;
– коэффициент полезного действия привода;
где кл – кпд клиноремённой передачи 1=095;
п – кпд пары подшипников качения 1=099;
т – число пар подшипников качения т=2;
где Vср – средняя линейная скорость движения лопатки в зоне подачи материала на диск Vср=10 мс.
где f – коэффициент трения зерна о лопатку f=04;
R0 –радиус встречи материала с лопатками диска R0=016 м;
Vs – наибольшая относительная скорость движения зерновки по лопаткам диска Vs=104 мс;
где G – вес диска с валов G=23 кг;
q0 – вес находящегося на диске груза q0=116 кг;
f1 – коэффициент трения в опорах диска f1=0002;
d – диаметр цапфы вала d=0035 м;
n – число оборотов диска n=600 мин-1.
Окончательно расчётная мощность электродвигателя будет равна
Учитывая заданную структуру привода принимаем электродвигатель 4А100L6У3 исполнение закрытое Рном=22 кВт nдв=n2=950 мин–1 dв=28мм (9. с163).
Частота вращения выходного вала n2=600 мин–1.
Передаточное отношение привода и клиноремённой передачи:
Основные габаритные размеры: 1=365 мм Н=263 мм D=235 мм.
Таблица 4.1 - Установочные и присоединительные размеры электродвигателя мм
Вращающий момент на ведомом шкиве:
2 Расчет клиноремённой передачи
Таблица 4.2 – Исходные данные
2.1 Определение вращающего момента на валу ведущего шкива 9
2.2 Определение диаметров шкивов
Диаметр ведущего шкива
Из конструктивных соображений принимаем d1=160 мм.
Диаметр ведомого шкива определим по формуле
где =002 – коэффициент относительного скольжения;
Принимаем d2= 250 мм.
2.3 Кинематический расчёт передачи
Уточняем передаточное отношение
Фактическая окружная скорость составит
2.4 Выбор сечения ремня
Принимаем ремень нормального сечения тип А с кордшнуровым сердечником (обозначение А ГОСТ 1284.1-89)
2.5 Геометрический расчёт
- межосевое расстояние
- уточняем межосевое расстояние
- угол обхвата ведущего шкива
2.6 Расчёт тяговой способности передачи т.е. определяем допускаемую мощность передаваемую одним клиновым ремнём 9:
где - допускаемая мощность передаваемая одним ремнем
[Ро]=165 кВт для V=69 мс и d1=160 мм;
Ср- коэффициент режима работы для 2-х сменной Ср= 09;
Сα- коэффициент угла обхвата Сα= 098;
Сi – коэффициент учитывающий влияние передаточного отношения
СL – коэффициент учитывающий отклонение принятой длинны ремня от базовой СL= 107;
СZ - коэффициент числа ремней в передаче Сz=095.
2.7 Определим число ремней необходимое для передачи заданной мощности:
2.8 Определяем силы действующие в ветвях ремня
- сила предварительного натяжения одного ремня
где А – площадь сечения ремня А= 81 мм2;
o – напряжение в ремне от предварительного натяжения o=15 МПа.
- окружная сила приходящуюся на один ремень
Ft = P1 V·z = 2269·2 = 1383 Н.(4.19)
- сила натяжения ведущей ветви одного ремня
F1=F0+05Ft= 1215+05·1383 = 1906 Н.(4.20)
- сила действующаю на валы в ременной передаче
Fв=2Foz sinα2 = 2·1215·2·sin1692 = 484 Н.(4.21)
2.9 Проверяем ремень по числу пробегов
2.10 Выполним проверочный расчет принятой ременной передачи по максимальным напряжениям в ремне:
- напряжения от окружной силы
t= FtА= 138381 = 171 МПа.(4.23)
- напряжения от изгиба ремня на ведущем шкиве
где Е=90 мПа - модуль продольной упругости;
- напряжения в ремне от центробежных сил
v= r·V2·10-6=1200·692·10-6 = 001 МПа.(4.25)
мах= о+05t+и+ v = 15+05·171+315+001 = 55 МПа [ ]=10МПа.(4.26)
Прочность принятых ремней сечения А обеспечена.
2.11 Определяем размеры ступицы шкивов:
- внутренний диаметр ступицы
принимаем dст1=28 мм;
принимаем из конструктивных соображений dст2=34 мм;
- наружный диаметр ступицы
Dст1 = (15 18)dст1 = (15 18)·28=(42 50) мм (4.29)
принимаем Dcт1=60 мм;
Dст2 = (15 18)dст2 =(15 18)·42=(63 76) мм(4.30)
принимаем Dcт2=66мм;
lст1 = (15 2)dст1 = (15 2)·28=(42 56) мм(4.31)
lст2 = (15 2)dст2 = (15 2)·42=(63 84) мм(4.32)
- ширина обода шкива
3.1 Проектный расчёт
Рисунок 4.4 – Эскиз вала
Диаметр наиболее тонкой части вала на которой закреплены диски метателя определим из условия
где Т2 – вращающий момент на одном диске метателя
Из конструктивных соображений принимаем d1=34 мм.
Диаметр под подшипник d2 = 40 мм.
Диаметр под ведомый шкив клиноременной передачи d3 = 42 мм.
3.2 Проверочный расчёт вала на статическую прочность
расстояние между опорой и посадочным местом диска принимаем
расстояние между опорой и посадочным шкива на валу принимаем
FВ=484 Н - давление со стороны шкива на вал;
α=700 – угол наклона клиноремённой передачи к горизонту;
FZB=FB·s FYB=FB·cosα=484·cos700=1655 H;
G1=G2=100 – вес дисков;
Т2=333 Нм – вращающий момент на ведомом шкиве;
Т2=1665 Нм – вращающий момент приходящийся на один диск метателя.
Пользуясь принципом независимости действия сил рассмотрим изгиб вала в двух плоскостях – в вертикальной и горизонтальной.
Вертикальная плоскость.
Определим реакции в опорах
Выполним проверку правильности определения реакций из условия
Определим изгибающие моменты в каждом характерном сечении вала:
Горизонтальная плоскость.
Определим суммарный изгибающий момент в каждом характерном сечении
Построим эпюру внутреннего крутящего момента
По третьей теории прочности определим расчётный момент в каждом характерном сечении
Уточняем диаметры в опасных сечениях по формуле:
где []F = допускаемое напряжение на изгиб []F = 50 Нмм2 3с.11.
Оставляем раннее принятые диаметры вала.
4 Выбор и проверка подшипников
Исходные данные к расчёту
Опоры А и В нагружены равнозначно. При nвала= 600 >10 принимаем подшипники качения и проверяем их по динамической грузоподъёмности С.
Так как осевая нагрузка равна нулю выбираем радиальные шариковые подшипники таблица П3. 10.
Принимаем на каждую опору два радиальных шариковых подшипника особо легкой серии при dп=40мм №80108 для которого D=68 мм; В=15 мм; С=168 кН; С0=93 кН стр. 393 П3 10.
где Pэ – эквивалентная нагрузка.
Для радиальных подшипников эквивалентная нагрузка вычисляется по формуле:
Pэ=Х×V×R×Kб×KT(4.43)
где Х=1 – коэффициент радиальной нагрузки таблица 9.18 10;
V=1 - коэффициент (вращается внутреннее кольцо) стр.212 2;
Кб=22 – коэффициент безопасности для центробежных аппаратов 10 таблица 9.19;
КТ = 11 – температурный коэффициент по 10 таблица 9.20.
Pэ=1·1·3878·22·11=968 Н
Расчетная долговечность ч
> [L]=14400 ч.(4.44)
5 Выбор и проверка прочности шпоночных соединений
Принимаем шпонки призматические. Размеры сечений шпонок пазов и длины шпонок по ГОСТ 23360-78 (см. 10 табл. 8.9). Материал шпонок — сталь 45 нормализованная. Напряжения смятия и условие прочности по формуле:
Допускаемые напряжения смятия при стальной ступице [s]см=100 120Нмм2 10стр.170.
Выбираем по таблице 8.9 10 и проверяем шпонку под ступицей диска метателя. Для диаметра вала d=34 мм; сечение - bh=108 мм; глубина паза вала t1=5 мм; глубина паза втулки t =33 мм; длина шпонки момент Т2 =333 Н×м;
Выбираем по таблице 8.9 10 и проверяем шпонку под шкивом клиноременной передачи. Для диаметра вала d=42 мм; сечение - bh=128 мм; глубина паза вала t1=50 мм; глубина паза втулки t=33 мм; длина шпонки l=51 мм.
раздел 3.doc
И РЕЖИМОВ РАБОТЫ ЛОПАСТНОГО МЕТАТЕЛЬНОГО
1 Техническое описание модернизированного ЗМ-60
В сельскохозяйственном производстве широкое применение получили также зернометатели ЗМ-60А.
Как отмечалось ранее применяемые в сельскохозяйственном производстве метательные рабочие органы имеют ряд недостатков основным из которых является повреждение зерна. По функциональной структуре все применяемые аппараты струйного типа. Основной целью выполняемых операций этих аппаратов является предварительная очистка зернового вороха от грубых примесей (по аэродинамическим свойствам) и частично подсушивание перерабатываемого материала при скоростях как правило не более 10 мс т. к. дальнейшее превышение скорости ведёт к значительному увеличению повреждению зерна.
Известным фактом является то что при метании в виде сплошной струи создаётся сопутствующий воздушный поток. В результате чего затрудняется выделение примесей разного состава из массы зернового вороха. Однако данный процесс может быть эффективным лишь в одном случае это образованием тонкослойной струи. Применение такого процесса не практикуется в производстве из-за низкой производительности и большой энергоёмкости. Решить задачу такого типа можно применением рабочих органов веерного типа. Так в процессе веерного метания можно повысить эффективность предварительной очистки проветривания и снижения влажности и температуры свежеубранного зернового вороха. К аппаратам такого типа можно отнести лопастной метательный рабочий орган.
В процессе разработки лопастного метательного рабочего органа предварительно необходимо задаться условием чтобы скорость зерна на выходе из аппарата была бы не меньше 10 мс и при этом повреждение зерна соответствовало агротехническим требованиям.
Рабочий процесс метательного рабочего органа. Частицы зернового вороха из подающего механизма через трубопроводы заканчивающиеся криволинейным желобом попадают на лопатки метательного диска с начальной скоростью.
При вращении диска частица испытывает влияние центробежной силы под действием которой перемещается относительно лопатки. Таким образом частица участвует в двух движениях: переносном вместе с лопаткой ускоряющей крыльчатки и относительном (уже относительно лопатки). На выходе ускоряющей крыльчатки зерновка движется по поверхности лопатки прямолинейно и сходит с периферии лопатки со скоростью равной геометрической сумме скоростей переносного и относительного движения. Зерновка покидает лопатку с определённой скоростью и под определённым углом который принято называть углом схода. В реальных условиях работы рабочего органа участвует поток частиц (сыпучее тело) и на выходе диска соответственно получается веер который характеризуется параметром – угол сектора рассева. За угол сектора рассева принимают разность между векторами скоростей бросания крайних частиц.
Для выполнения технологического процесса работы метателя необходимо чтобы веерное распределение зерна осуществлялось в плоскости вращения диска по одну сторону от него (вдоль метателя) т.е. чтобы значение угла сектора метания не превышало 2αт2кр т.е. необходимо чтобы выполнялось условие:
В противном случае будет наблюдаться значительный разброс зерна во все стороны.
Определённый интерес при разработке параметров аппарата представляет способ подачи зернового материала на лопатки диска метателя. На основе анализа литературных источников для поисковых экспериментов использовали два способа подачи зернового материала на лопатки диска метателя.
По первому способу подача осуществлялась с торцевой стороны лопатки (рисунок 3.1 а). В результате выявлено что в момент встречи потока частиц зерна с лопатками происходит отскок и наблюдается хаотичное движение частиц в межлопаточном пространстве. Исходя из этого данный способ подачи не приемлем т.к. не удовлетворяет требованиям технологического процесса работы метателя.
Второй способ подачи осуществляли во внутреннюю полость ускоряющей крыльчатки (рисунок 3.1 б) т.е. вдоль лопаток. В этом случае рабочий процесс осуществлялся так как это описано выше.
Предварительно задавшись основными кинематическими параметрами технологического процесса работы метателя с необходимо определить геометрические параметры ускоряющей крыльчатки и наружного лопастного диска. Величина окружной скорости зерновки определяется по известной формуле:
где 2 – угловая скорость диска с-1;
R2 – наибольший радиус наружного диска м.
Пользуясь формулой (3.2) можно предварительно определить диаметр наружного диска который при частоте вращения не менее 550 обмин и необходимой скорости схода не менее 10 мс составит не менее 04 м.
2 Анализ ударного взаимодействия частицы зерна с лопаткой
В процессе работы аппарата предполагается что взаимодействие зерновки с лопаткой происходит в определённом положении зерновки (спинкой или бороздкой) показанном на рисунке 3.2:
При анализе процесса взаимодействия частицы с лопаткой принимаем идеализированную форму зерновки – эллипсоид вращения.
В процессе взаимодействия частиц зерна с лопатками роторного метателя происходит удар. Определяющими факторами которого являются форма лопатки и зерна и скорость в момент удара. При ударе частицы о лопатку характеристикой степени взаимодействия является мгновенная сила. Характеристикой прочности обрабатываемого материала является напряжение. Известно что чем больше мера воздействия внешней нагрузки на зерно тем больше зерно повреждается. Исходя из выше изложенного мгновенную силу при ударе можно рассчитать по гипотезе предложенной Герцем который рассматривает процесс удара тел в пределах упругой деформации.
Предполагая что взаимодействие при ударе частицы о лопатку происходит в точке получаем зависимость мгновенной силы:
где - сближение тел в точке контакта (упругая деформация зерновки);
k – коэффициент зависящий от кривизны поверхностей тел в точке контакта и от свойств материала
Е1 Е2 - модули Юнга и коэффициенты поперечной деформации (Пуассона) зерна и материала лопатки.
Анализ зависимости (3.3) указывает на то что чем меньше коэф. К тем меньше сила а следовательно и повреждаемость зерна.
При определении кривизны зерновки учитывая допущение что форма зерновки представляет собой эллипсоид вращения её размеры обозначим как полуоси а и c с шириной b (рисунок 3.3).
Известно что коэффициент Пуассона для всех материалов колеблется в пределах от 0 до 05 и для многих материалов в среднем от 025 до 035. Поэтому принимаем и для зерна и для материала лопатки .
При определении кривизны зерновки учитывая допущение что форма зерновки представляет собой эллипсоид вращения её размеры обозначим как полуоси а и c с шириной b (рисунок 3.3).
Анализ выражения (3.5) применительно к нашим условиям показывает что модуль Юнга для стали Ест=Е2=2×105 МПа значительно больше чем для зерна Езер=Е1=10-40 МПа поэтому выражение в скобках близко к 1. При меньшей разности между модулями Юнга зерна и контактируемого материала коэффициент k снижается и зависит также от размеров зерна. Для выявления данной закономерности были построены графики зависимости коэф. от модуля Юнга предполагаемого материала лопатки (рисунок 3.4). В результате построения графиков выявлено что с увеличением и модуля Юнга материала лопатки и размеров единичных зёрен коэффициент k увеличивается. Так значение коэффициента k для фракции крупного зерна примерно в два раза больше чем для мелкой фракции.
В момент удара когда скорость сближения тел будет равна нулю упругая деформация зерновки составит:
где Vн – относительная скорость соударяющихся тел (в дальнейшем будет рассматриваться как нормальная составляющая относительной скорости тел в начальный момент удара ).
С учётом всех преобразований мгновенная сила в момент удара составит:
Анализ формулы (3.7) показывает что мгновенная сила при ударе зависит и от скорости в начальный момент удара.
Используя теорему об изменении количества движения материальной точки и рассмотрев схемы взаимодействия зерна с лопаткой до и после удара получаем: составляющие относительной скорости частицы до удара:
В результате полученной зависимости (3.9) установлено что для снижения величины скорости Vn1 необходимо стремится к снижению частоты вращения лопаток уменьшению радиуса подачи зерна на лопатки увеличению угла постановки лопаток назад по ходу вращения и увеличению начальной скорости зерновки.
Влияние угла постановки лопатки к начальному радиусу показано на графике зависимости (рисунок 3.6). В результате полученной зависимости видно что с увеличением угла постановки лопатки с 200 до 600 (назад по ходу вращения) величина Vn1 уменьшается в 3-5 раз.
Как было сказано ранее мгновенная сила оказывает влияние на повреждаемость зерна. Однако характеристикой прочности является напряжение которое определяется по заисимости
где А – площадь поперечного сечения.
В результате полученных значений нормальной составляющей относительной скорости Vn1 и коэффициента k рассмотрим более подробно влияние этих факторов на величину напряжения (3.10).
В результате полученных зависимостей (рисунок 3.7) видно что с увеличением коэффициента k с 3 до 15 единиц величина нормального напряжения увеличивается в среднем в 2 раза.
Увеличение скорости Vn1 от 2 до 10 мс приводит к увеличению напряжения в 10 раз что в свою очередь влияет на качество обрабатываемого материала.
В результате проведённого анализа вытекает что чем меньше модуль Юнга материала лопатки тем меньше и напряжения в зерне при ударе о лопатку. Для рассматриваемого диапазона модуля Юнга более всего подходят следующие материалы: капролон полиэтилен и различные пластиковые материалы.
3 Анализ движения частиц зерна по лопаткам метательного диска
Как было отмечено ранее при взаимодействии зерна с лопаткой происходит повреждение зерна за счёт удара. Безударное взаимодействие возможно при условии P=N=0. В реальных условиях работы выполнение этого условия практически невозможно потому что с лопаткой метателя взаимодействует поток частиц. Снижение удара (мгновенной силы) может быть достигнуто снижением угловой скорости и постановкой лопаток назад по ходу вращения. Снижение угловой скорости может привести к нарушению технологического процесса работы аппарата. При постановке лопаток назад по ходу вращения приводит к снижению начальной скорости при метании и соответственно сказывается на качестве обрабатываемого зерна. Во избежание последствий такого рода необходимо применять криволинейные лопатки.
При исследовании процесса взаимодействия зерновки с криволинейной лопаткой за основу была принята математическая модель описания процесса предложенная В.П. Забродиным 39 40 соответственно с некоторыми преобразовании для рассматриваемого случая так как предложенная модель справедлива для диска с вертикальной осью вращения. Рабочая поверхность лопатки наружного диска в плане представлена в виде сектора окружности радиуса rл. Лопатка установлена на угол R0 назад по ходу вращения и выполнена вогнутой в направлении вращения для повышения эффективности процесса метания. Радиус кривизны лопатки rл и угол раствора л определяются по формулам:
где - угол раствора лопатки.
Процесс взаимодействия зерновки с криволинейными лопатками для представленного рабочего органа более подробно представлен в трудах Бутенко А.Ф. 21.
Приведём некоторые из закономерностей.
Нелинейное дифференциальное уравнение второго порядка (движения зерновки по криволинейной лопатке):
Решение уравнения (3.11) может быть выполнено численным методом Рунге-Кутта 14. Для этого необходимо уравнение (3.11) представить в виде системы дифференциальных уравнений:
Решаем систему уравнений (3.12) используя начальные условия t=0 =0 Vr2=Va1.. При этом находим время относительного движения t2 по лопатке на пути равном max=rл×л и относительную скорость движения Vr2 при сходе зерновки с лопатки.
Угол поворота диска за время относительного движения t2 зерна по лопаткам равен 2t2 а угол схода равен:
Угол схода зерна с лопаток наружного диска значительное влияние оказывает на величину угла сектора рассева от которой зависят качественные показатели работы.
Величина угла наклона лопатки в месте наибольшего радиуса встречи зерновки с лопаткой определится:
и тогда угол схода составит:
В результате анализа взаимодействия зерновки с криволинейной лопаткой окончательно величина угла сектора рассева определится выражением:
В результате анализа формулы (3.15) выявлено с увеличением R0max наблюдается увеличение сектора рассева. При увеличении начальной скорости зерна угол сектора рассева уменьшатся. Также с увеличением угловой скорости диска происходит увеличение угла сектора рассева.
В результате анализа математической модели взаимодействия зерна с лопатками диска метателя выявлены основные параметры и факторы влияющие на технологический процесс работы метателя с ускоряющей крыльчаткой.
С целью снижения травмирования обрабатываемого зерна на поверхности лопаток устанавливаются полиэтиленовые накладки на половину высоты лопатки с внутренней стороны. Удерживаются накладки на лопатках за счёт центробежной силы при вращении диска.
При установке лопаток назад по ходу вращения величина мгновенной силы уменьшается за счёт снижения удара в направлении нормали к лопатке но ведёт к снижению скорости метания. Устранение этого недостатка достигается постановкой криволинейных лопаток на наружном диске.
Длина криволинейных лопаток метательного диска колеблется в пределах от 94 до 120 мм в зависимости от кривизны и углов постановки лопаток.
4 Обоснование постановки наружной направляющей камеры (кожуха)
Геометрические размеры направляющей камеры определяются в зависимости от геометрических размеров наружного диска и технологических параметров работы экспериментального роторного метателя. Ширина направляющей камеры на 20 мм больше ширины наружного диска. Положение нижней стенки камеры определяется положением угла сектора рассева относительно горизонта который определяется формулой (2.37). Соответственно высота направляющей камеры определяется углом сектора рассева который определяется по формуле (2.45).
Анотация.docx
Цель проекта заключается в снижении травмирования семян роторным зернометателем за счёт совершенствования его параметров и технологического процесса работы.
В пояснительной записке приведены доводы подтверждающие необходимость модернизации зернометательных машин за счет совершенствования параметров и технологического процесса работы произведены исследования прочностных свойств семян а так же и посевных свойств семян произведен расчёт параметров передач. Данные результатов были обработаны и сделаны соответствующие выводы. Произведен экономический расчет эффективности повышения надежности узлов передних колес автомобилей с коническими подшипниками.
При выполнении работы была использована рекомендуемая литература сделаны выводы по дипломной работе.
Графическая часть выполнена в соответствии с требованиями и указаниями стандартов.
Содержание.doc
2 Краткая историческая справка 8
4 Послеуборочная обработка зерна на примере хозяйства
5 Анализ конструкций зернометателей ..11
АГРОТЕХНИЧЕСКАЯ ОЦЕНКА ЗЕРНООБРАБАТЫВАЮЩИХ
1 Методика и результаты исследований посевных качеств
обработанного зерна 30
1.2 Всхожесть и энергия прорастания . ..31
2. Определение микротравмирования зерна пшеницы .. 32
3. Оборудование и методика определения прочностных свойств зерна пшеницы ..33
4. Результаты исследований прочностных свойств зерна пшеницы .37
5Определение коэффициента упругости 1 рода (модуля Юнга) ..40
ТЕОРЕТИЧЕСКОЕ ОБОСНОВАНИЕ ПАРАМЕТРОВ И РЕЖИМОВ РАБОТЫ ЛОПАСТНОГО МЕТАТЕЛЬНОГО РАБОЧЕГО ОРГАНА
1 Техническое описание модернизированного ЗМ-60 41
2 Анализ ударного взаимодействия частицы зерна с лопаткой 44
3 Анализ движения частиц зерна по лопаткам метательного диска .50
4 Обоснование постановки наружной направляющей камеры (кожуха) 55
ПРОЧНОСТНОЙ РАСЧЁТ МЕТАТЕЛЬНОГО РАБОЧЕГО ОРГАНА
1 Кинематический расчёт привода 56
2 Расчет клиноремённой передачи 58
3.1 Проектный расчёт ..63
3.2 Проверочный расчёт вала на статическую прочность 64
4 Выбор и проверка подшипников 67
5 Выбор и проверка прочности шпоночных соединений ..68
БЕЗОПАСНОСТЬ ЖИЗНЕДЕЯТЕЛЬНОСТИ.
2 Инструкция по охране труда при перелопачивании зерна с помощью электрифицированного зернометателя ..76
3 Экологическая безопасность проекта 79
РАСЧЕТ КАПИТАЛЬНЫХ ВЛОЖЕНИЙ 82
1 Расчёт эксплуотационных затрат 87
2 Определение чистого дисконтируемого дохода ..91
3 Определение индексадоходности .. 92
4 Определение срока окупаемости капитальных вложений .92
ВЫВОДЫ И ПРЕДЛОЖЕНИЯ ..94
Раздел 5-6.docx
В соответствии со ст.217 ТК РФ у каждого работодателя осуществляющего производственную деятельность численность работников которого превышает 50 человек создается служба ОТ (далее — Служба охраны труда) или вводится должность специалиста по ОТ имеющего соответствующую подготовку или опыт работы в этой области.
Cлужба охраны труда предусматривает регламентацию их должностных обязанностей закрепление за каждым из них определенных функций по ОТ в подразделениях организации в соответствии с должностными инструкциями. Для проведения мероприятий по охране труда (обучение инструктажи семинары лекции и др.) оборудован кабинет по охране труда.
- организация работы по обеспечению выполнения работниками требований ОТ;
- организация работы по предупреждению производственного травматизма и профессиональных заболеваний по улучшению УТ;
- информирование и консультирование работников организации в т.ч. ее руководителя по вопросам ОТ;
- изучение и распространение передового опыта в области ОТ пропаганда охраны труда.
- учет и анализ состояния и причин производственного травматизма профессиональных заболеваний и заболеваний обусловленных производственными факторами (воздействие которых на работника может привести к его заболеванию травме);
- оказание помощи подразделениям в определении параметров вредных и опасных производственных факторов;
- методическое руководство аттестацией рабочих мест по условиям труда сертификацией работ по охране труда и контроль за их проведением;
- участие в работе комиссий по приемке в эксплуатацию объектов производственного назначения отремонтированных установок агрегатов станков и др. оборудования;
- согласование разрабатываемой в организации проектной конструкторской технологической и др. документации в части требований ОТ;
- разработка совместно с др. подразделениями планов программ по улучшению условий и охраны труда предупреждению производственного травматизма профессиональных заболеваний;
- участие в составлении разделов коллективного договора касающихся ОТ соглашения по ОТ;
- оказание помощи руководителям подразделений в составлении списков профессий и должностей в соответствии с которыми работники должны проходить обязательные предварительные и периодические медицинские осмотры
Выдача СИЗ производиться в соответствии со статьей 17 Федерального закона «Об основах охраны труда в Российской Федерации» и статьей 149 Кодекса законов о труде Российской Федерации работникам занятым на работах с вредными или опасными условиями труда а также на работах выполняемых в особых температурных условиях или связанных с загрязнением выдаются бесплатно сертифицированные специальная одежда специальная обувь и другие средства индивидуальной защиты (в дальнейшем - средства индивидуальной защиты) в соответствии с нормами утвержденными в порядке определенном Правительством Российской Федерации.
Приобретение средств индивидуальной защиты и обеспечение ими работников в соответствии с требованиями охраны труда производится за счет средств работодателя (статьи 8 14 и 17 Федерального закона «Об основах охраны труда в Российской Федерации») (п. 1 в ред. Постановления Минтруда РФ от 29.10.1999 №39)
Контроль за выдачей СИЗ производиться за счёт заполнения работником личной карточки учёта выдачи средств индивидуальной защиты.
Оформление льгот и компенсаций производиться путём заполнения формы №1 (Условия труда) «Утверждена Постановлением Госкомстата России от 31 июля 1996 г. №91»
Обучение производиться в соответствии с общим положением ГОСТ 12.0.004-90. дата введения 01.07.91.
Настоящий стандарт устанавливает порядок и виды обучения и проверки знаний по безопасности труда и других видов деятельности рабочих служащих руководителей и специалистов народного хозяйства а также учащихся.
Инструктаж по охране труда характеру и времени проведения подразделяют:
) первичный на рабочем месте;
Все требования правила а также формы протокола личной карты и журналов проведения всех видов инструктажа представлены на стр. 298 – 305 11
1.1 Расчёт необходимого числа противопожарных щитов на зернотоку
Выбор типа и расчет необходимого количества щитов в защищаемом помещении или на объекте следует производить в зависимости от предельной площади а также класса пожара горючих веществ и материалов:
класс А - пожары твердых веществ в основном органического происхождения горение которых сопровождается тлением (древесина текстиль бумага);
класс В - пожары горючих жидкостей или плавящихся твердых веществ;
класс С - пожары газов;
класс D - пожары металлов и их сплавов;
класс (Е) - пожары связанные с горением электроустановок.
Для размещения первичных средств пожаротушения немеханизированного инструмента и пожарного инвентаря в производственных и складских помещениях не оборудованных внутренним противопожарным водопроводом и автоматическими установками пожаротушения а также на территории предприятий (организаций) не имеющих наружного противопожарного водопровода или при удалении зданий (сооружений) наружных технологических установок этих предприятий на расстояние более 100 м от наружных пожарных водоисточников должны оборудоваться пожарные щиты. Необходимое количество пожарных щитов и их тип определяются в зависимости от категории помещений зданий (сооружений) и наружных технологических установок по взрывопожарной и пожарной опасности предельной защищаемой площади одним пожарным щитом и класса пожара в соответствии с таблицей 5.1.
Таблица 5.1 – Нормы оснащения зданий (сооружений) и территорий пожарными щитами
Наименование функционального назначения помещений и категория помещений или наружных технологических установок по взрывопожарной и пожарной опасности
Предельная защищаемая площадь одним пожарным щитом м2
А Б и В (горючие газы и жидкости)
В (твердые горючие вещества и материалы)
Помещения и открытые площадки предприятий (организаций) по первичной переработке сельскохозяйственных культур
Помещения различного назначения при проведении сварочных или других огнеопасных работ
Из предложенного нам ассортимента целесообразно выбрать щит типа ЩП – СХ(оснащение см. таблицу 5.2)
Исходя из расчёта что один щит способен обеспечить пожарную безопасность на площади равной 1000 м2 и зная то что площадь зернотока равна 16000 м2 принимаем необходимое нам число ЩП – СХ равное 1615
Также одним из немаловажных первичных средств пожаротушения являются противопожарные колодца и водоёмы.
Их следует располагать на территории наиболее пожароопасных производственных участков или объектов на расстоянии не ближе 10 м от зданий I и II степеней огнестойкости и не ближе 30 м от зданий III V степеней огнестойкости. Пожарных водоемов должно быть не менее двух а их объем независимо от расчетного значения должен быть не менее 50 м3. Радиус обслуживания одного водоема при использовании пожарных автомобилей и автонасосов принимают равным 200 м при использовании прицепных мотопомп – 150 м переносных мотопомп – 100 м.
Рядом с пожарными водоемами следует оборудовать площадку с твердым покрытием. Размеры площадки должны быть достаточны для свободного маневрирования и размещения забирающей воду техники.
Требуемый запас воды на наружное пожаротушение м3 рассчитывают по формуле:
где – удельный расход воды на наружное пожаротушение 6;
– расчетное время тушения одного пожара принимается равным 3ч;
– число одновременно возможных пожаров: = 1 при плошали предприятия менее 15 км2= 2 при площади 15 км2 и более.
Необходимый объем воды для внутреннего пожаротушения м3 рассчитывают в зависимости от расхода воды на одну струю и числа одновременно действующих струй по формуле
где и m – соответственно расход воды на одну струю и число струй. Для производственных зданий и гаражей высотой до 50 м принимают = 2.5 лс и m = 2.
Полная вместимость пожарного резервуара м3
где: – регулируемый запас воды для хозяйственно-технических нужд м3.12
2 Инструкция по охране труда при перелопачивании зерна с помощью электрифицированного зернометателя .
2.1 Общие требования охраны труда
Настоящая Инструкция предназначена для машинистов (операторов) обслуживающих электрифицированные зерноочистительные и сортировальные машины зернопогрузчики транспортеры автомобилеподъемники.
К работе в качестве машинистов (операторов) зерноочистительных и сортировальных машин зернопогрузчиков допускаются лица не моложе 18 лет прошедшие профессиональную подготовку и имеющие квалификационную группу по электробезопасности.
Включение и выключение обслуживаемых электрифицированных машин разрешается проводить только машинистам (операторам).
- нарушение изоляции силового кабеля;
- наличие зерна на поверхности пола рабочего места;
- недостаточная освещенность рабочей зоны;
- устранение повреждений смазка регулировка и очистка машин при включенных двигателях машин;
- передвижение по территории зернотока несамоходных машин без отключения их от электросети;
- натяжение силового кабеля или наезд на него при передвижении машин с приводом от колес;
- передвижение машин по территории зернотока без разрешения заведующего током;
- самостоятельное открытие распределительных щитов;
- оставление без надзора работающих машин;
- нахождение под поднятым автомобилеподъемником стрелой зернопогрузчика транспортера;
- допуск к машинам посторонних лиц;
- отдых и курение в неустановленных местах;
- работа в одежде со свободно развевающимися концами;
При работе пользуйтесь комбинезонами хлопчатобумажными (ГОСТ 12.4.100 - для мужчин ГОСТ 12.4.099 - для женщин) и ботинками (ГОСТ 5394).
Подходы подъезды к машине агрегату держите свободными в целях возможной эвакуации или подъезда пожарной техники.
2.2 Требования охраны труда перед началом работы
Получить у заведующего током задание и инструкции по его безопасному выполнению.
Произведите смазку машин согласно руководству завода-изготовителя.
Передвижные машины и оборудование установите на площадке так чтобы ветер относил пыль из рабочей зоны.
Проверьте наличие и исправность защитных ограждений приводов рабочих органов.
Обеспечьте защиту токопроводящих проводов и кабелей к электрифицированным машинам и установкам от механических повреждений или подвесьте их на недоступную для повреждения машинами и прикосновения людьми высоту.
Проверьте надежность крепления и наличие заземления электрооборудования машин и пультов управления ими. Не приступайте к работе на машинах при открытых дверцах пультов управления снятых крышках магнитных пускателей и другой электроаппаратуры.
Проверьте натяжение транспортерного полотна и убедитесь в надежности ограждения мест набегания цепи на звёздочки.
Опробуйте работу машины на холостом ходу обнаруженные недостатки устраните.
Во время подготовки машин к работе на пульте управления вывесите плакат "Не включать! Работают люди!".
2.3 Требования охраны труда во время работы
Перед пуском машин убедитесь в отсутствии людей вблизи них и подайте звуковой сигнал. Включать и выключать машину разрешается только машинисту.
Не работайте со снятыми ограждениями ременных и цепных передач и других вращающихся частей зерноочистительных машин муфт блоков натяжных устройств а также движущихся частей машин и механизмов находящихся в местах свободных для доступа.
Устраняйте повреждения производите очистку машины от зерна и примесей смазку и регулировку только при выключенном рубильнике отключенном штепсельном разъеме и остановленной машине.
При обслуживании и очистке высокорасположенных узлов машин и электрооборудования пользуйтесь стремянкой или переносной лестницей с опорными наконечниками исключающими возможность скольжения ее по полу (земле площадке и т.п.).
Не допускайте накопления пыли соломистых отходов зерновых остатков и другого мусора около машин в рабочей зоне.
Не оставляйте работающие машины без наблюдения.
Для обрушения сводов зерна используйте специальные скребки с длинными ручками позволяющими находиться на безопасном расстоянии от призмы обрушения насыпи и исключить возможность быть засыпанным зерном.
Не перешагивайте через скребковые цепи загрузочных транспортеров работающих машин.
2.4 Требования охраны труда в аварийных ситуациях
При появлении напряжения на корпусе машины немедленно отключите общий рубильник.
В случае возникновения опасности травмирования работников а также при появлении дыма запаха гари необычного шума немедленно остановите работу и сообщите заведующему током. Отключение машин производите с пульта управления или ближайшей "Кнопкой аварийного отключения".
2.5 Требования охраны труда по окончании работы
Отключите машину от питающей сети.
После всех вышеперечисленных мероприятий принимаются меры личной гигиены. Привести в порядок и сдать средства индивидуальной защиты на хранение в установленном порядке.
Вымыть лицо и руки теплой водой с мылом принять душ.13
3 Экологическая безопасность проекта.
К негативным факторам возникающим при эксплуатации данного проекта относятся: вибрация электромагнитные излучения и шум.
Отрицательное действие шума на организм человека в наибольшей степени сказывается на органах слуха и центральной нервной системе а также может оказывать влияние на органы зрения изменяются ритмы дыхания и сердечной деятельности повышается внутричерепное и кровяное давление появляются головные боли и головокружение нарушается процесс пищеварения.
Для ослабления шума следует заменять по возможности ударные действия безударными; демпфировать вибрации соударяющихся деталей и отдельных узлов путем сочленения их с материалами имеющими большое внутреннее трение уменьшать интенсивность вибраций деталей имеющих большие поверхности путем их облицовки
При невозможности снижения шума в источнике до допустимого уровня (ПДУ) можно использовать противошумные наушники к примеру наушники противошумные ЭКО+ модель EP-106.14
Вибрация вызывает в организме человека многочисленные реакции которые являются причиной функциональных расстройств различных органов. Под воздействием вибрации происходят изменения в периферической и центральной нервной системах сердечно-сосудистой системе опорно-двигательном аппарате. В российских стандартах ГОСТ 12.1.012-90(1996) и СН 2.2.4 2.1.8.566-96 нормируются как значения виброускорения так и виброскорости. При этом нормы для этих двух параметров связаны между собой. При нормировании используются также их логарифмические уровни. Допустимый уровень вибрации в жилых и общественных зданиях - это уровень фактора который не вызывает у человека значительного беспокойства и существенных изменений показателей функционального состояния систем и анализаторов чувствительных к вибрационному воздействию.
Важную роль в снижении виброактивности имеет балансировка вращающихся частей машин которую осуществляют на специальных станках. Балансировка может быть статическая когда неуравновешенные массы ротора приводятся к одной эквивалентной массе смещенной относительно оси вращения и динамическая когда балансировку проводят двумя массами располагаемыми в двух плоскостях.
Основной способ снижения вибрации зубчатых колес – обеспечение высокой точности изготовления с использованием процесса шлифования зубьев. Вибрацию также можно снизить путем демпфирования колебаний в масляном слое и изготовлением колес из материалов с высокими демпфирующими свойствами.
Требования к условиям производственных воздействий ЭМП которые должны соблюдаться при проектировании реконструкции строительстве производственных объектов при проектировании изготовлении и эксплуатации отечественных и импортных технических средств являющихся источниками ЭМП определены СанПиН 2.2.4.1191-03.
Основным способом защиты от ЭМП является экранирование.
Экранирование источников излучения используют для снижения интенсивности ЭМП на рабочем месте или ограждения опасных зон излучения. Для этих целей применяют экраны в виде замкнутых камер шкафов кожухов выполненных из металлических листов.14
РАСЧЕТ КАПИТАЛЬНЫХ ВЛОЖЕНИЙ
В большинстве дипломных проектов рассматриваются капитальные вложения направляемые на модернизацию используемого в производственном процессе оборудования а в некоторых случаях на разработку или приобретение новой машины (оборудования) или их комплекса поэтому балансовая стоимость оборудования определяется в каждом случае в соответствии с конкретными условиями поставленными в предыдущих частях дипломного проекта.
Балансовая стоимость модернизированной машины (оборудования) может быть определена как сумма балансовой стоимости модернизируемой (исходной) машины (оборудования) и затрат на ее модернизацию
где: БИСХ - балансовая стоимость машины (оборудования) в исходном варианте руб.;
ДМ- цена демонтируемых деталей по цене лома руб.;
БПР - балансовая стоимость машины (оборудования) в проектируемом варианте руб.;
БИСХ - балансовая стоимость модернизируемой машины руб.;
ΣМ - затраты на модернизацию руб.
В тех случаях когда сравниваемые машины резко отличаются сложностью конструкции материалами изготовления и величиной серийного выпуска необходимо определить затраты на их изготовление или модернизацию.
Затраты на изготовление или модернизацию конс!рк:!ии можно определить по отдельным статьям:
- затраты на материалы и покупные изделия;
- транспортно-заготовительные расходы;
- основная и дополнительная зарплата начисления на фонд заработной платы (единый социальный налог):
- общепроизводственные (цеховые) и общехозяйственные (общезаводские) расходы.
Затраты на материалы и покупные изоелия определяются на основании объемов установленных согласно чертежам и текущих цен. определяемых по прейскурантам торгующих организаций и заключенным договорам на поставку материалов и покупных изделий.
Таблица 6.1 – Затраты на материалы и покупаемые изделия
Наименование и марка материала
Затраты на материалы
Двутавр ГОСТ 8239-89
Труба прямоугольная ГОСТ 8645-68
Демонтируемые детали
Транспортно-заготовительные расходы определяются в процентах от стоимости покупных материалов и изделий. Величина процента определяется по фактическим данным предприятия.
где: - сумма транспортно-заготовительных расходов руб.;
- сумма затрат необходимая для приобретения требующихся материалов руб.;
% - процент транспортно-заготовительных расходов (по фактическим данным предприятия) %.
Основная зарплата работников занимающихся изготовлением (модернизацией) конструкции определяется по часовым тарифным ставкам и трудоемкости выполняемых работ согласно хронометражу или нормативным справочникам.
Трудоемкость и основная заработная плата на изготовление (модернизацию) конструкторской разработки по видам работ может быть определена с помощью таблицы 6.2.
Таблица 6.2 – Трудоёмкость и основная зароботная плата при изготовлении (модернизации) конструкции
Трудоёмкость чел.-ч.
Часовая тарифная ставка руб.
Затраты на основную зарплату руб.
Размер дополнительной заработной платы определяется по проценту от основной зарплаты.
где: ДЗ - сумма дополнительной заработной платы руб.;
ОЗ - сумма основной заработной платы руб.
% - процент дополнительной заработной платы (по фактическим данным предприятия) %.
Размер начислений на фонд заработной платы (единый социальный налог) определяется согласно законодательным актам РФ по установленному проценту от суммы основной и дополнительной зарплаты;
- для сельскохозяйственных предприятий - 261% (Пенсионный фонд РФ - 20.6°о. Фонд социального страхования РФ - 29%; Фонды обязательного медицинского страхования (федеральный и территориальный) - 26%);
- для промышленных предприятий - 356% (Пенсионный фонд РФ -280%; Фонд социального страхования РФ - 4.0%: Фонды обязательного медицинского страхования (федеральный и территориальный) - 36%).
где: ОС - размер начислений на фонд заработной платы руб.:
ОЗ - сумма основной заработной платы руб.;
ДЗ - сумма дополнительной заработной платы руб.;
% - процент отчислений в фонды социальной защиты (единый социальный налог) %.
Размер общепроизводственных (цеховых) и общехозяйственных (общезаводских) расходов определяется в процентах от основной зарплаты на изготовление (модернизацию) конструкции. Размеры процентов берутся по фактическим данным предприятия.
где: ОП - общепроизводственные расходы руб.;
% - процент общепроизводственных расходов (по фактическим данным предприятия) %.
где: ОХ - общехозяйственные расходы руб.;
% - процент общехозяйственных расходов (по фактическим данным предприятия) %.
При определении размера элементов эксплуатационных затрат необходимо пользоваться действующими справочными и нормативными данными.
Элементы эксплуатационных затрат рассчитываются по следующим формулам.
1 Расчёт эксплуотационных затрат
Затраты на заработную плату рабочих занятых на выполнении производственных процессов или операций:
где - количество рабочих смен машины (оборудования) в году;
tсм - продолжительность рабочего процесса в течение смены ч;
Л - количество работников занятых на выполнении производственного процесса чел.;
Ст - часовая тарифная ставка соответствующего разряда работника
% - процент учитывающий начисление дополнительной заработной
платы (по фактическим данным предприятия) %;
% - процент отчислений в фонды социального страхования (единый социальный налог) %.
Если в производственном процессе (на выполнении операции) занято несколько работников с разной квалификацией (труд которых оплачивается по отличающимся тарифным ставкам) необходимо определить размер заработной платы по каждой категории работников. Затем для определения затрат на заработную плату работников занятых на выполнении производственного процесса (операции) необходимо просуммировать затраты на заработную плату по каждой категории работников.
Размер ежегодных амортизационных отчислений:
где А - размер ежегодных амортизационных отчислении руб.;
Б - балансовая стоимость машины (оборудования) руб.;
5% - норма ежегодных амортизационных отчислений %.
Затраты на ремонты и техническое обслужжание машин:
где: Р - размер отчислений на ремонты и техническое обслуживание в течение года руб.:
р% - процент ежегодных отчислений на ремонты и техническое обслуживание машин (оборудования) (по фактически данным предприятия - средний % отчислений за 3-4 предшествующих года). %.
Затраты на расходуемую электроэнергию.
Затраты на электрическую энергию потребляемую оборудованием при производстве продукции определяются по формуле
где: Сэ - затраты на потребляемую электроэнергию руб.;
- потребность электроэнергии для производства годового объема работ кВтч;
Цэ - стоимость 1 кВтч электроэнергии 312 руб.кВтч.
где: - потребляемая мощность установленного оборудования кВт;
- продолжительность смены работы машины (оборудования) ч;
- количество смен работы оборудования в год;
- коэффициент загрузки оборудования. (г3 в среднем 085);
- коэффициент одновременности работы оборудования ^ = 06-07;
- коэффициент учитывающий потери в сети кс = 096;
КПД - коэффициент полезного действия электродвигателей. КПД= 085 -090.
Прочие эксплуатационные затраты планируются в размере 3 - 5 % от суммы эксплуатационных затрат или по фактическим данным предприятия в среднем за 3 - 4 предшествующих года:
Таким образом общий размер эксплуатационных затрат составит:
Степень снижения эксплуатационных затрат определяется по формуле:
Стоимость травмируемого зерна:
где: – стоимость травмируемого зерна;
- производительность тч;
- процент травмирования %;
- цена 1 т. зерна рубт.
Экономи за счёт снижения травмирования зерна:
2 Определение чистого дисконтируемого дохода
Чистый дисконтированный доход определяется как сумма текущих эффектов за весь расчетный период приведенная к начальному моменту.
Так как в конструкторской части дипломных проектов выполняемых по кафедре МП СХП в большинстве случаев предусматриваются единовременные капитальные вложения на изготовление (модернизацию) машин или оборудования и годовая экономия от внедрения проектируемого варианта одинакова по всему горизонту дисконтирования то чистый дисконтированный доход рассчитывается с использованием коэффициента капитализации. При этом в эксплуатационные затраты не включаются амортизационные отчисления.
Если капиталовложения производятся единовременно на начальном этапе освоения проекта (t = 0) то капитальные вложения не дисконтируются.
где - чистый дисконтированный доход руб.;
- общая годовая экономия руб.;
- сумма амортизационных отчислений в исходном и проектируемом вариантах соответственно
К - размер дополнительных капиталовложений (или затраты на модернизацию) руб.
3 Определение индексадоходности
Индекс (коэффициент) доходности (ИД) представляет собой отношение суммы приведенных эффектов или величины чистого дисконтированного дохода за срок службы оборудования к величине капиталовложений:
4 Определение срока окупаемости капитальных вложений
Так как ИД>1 проект эффективен.
Срок окупаемости (Ток) - это минимальный временной интервал (от начала осуществления проекта) за пределами которого ЧЦД становится и в дальнейшем остается неотрицательным. Срок окупаемости капиталовложений можно определить следующим образом:
Таблица 6.3 – Показатели экономической эфективности проекта.
Наименование показателей
Балансовая стоимость руб.
Затраты на заработную плату рабочих руб.
Размер ежегодных амортизационных отчислений руб.
Затраты на ремонты и тех. обслуживание машины руб.
Затраты на электроэнергию руб.
Эксплуатационные затраты руб.
Степень снижения эксплуатационных затрат руб.
Стоимость травмируемого зерна руб.
Дополнительная экономия за счёт снижения травмирования зерна руб.
Общая годовая экономия руб.
Чистый дисконтированный доход руб.
Индекс доходности ед.
Срок окупаемости ед.
Список Литературы.docx
Никитин А.К. Способ подготовки посевного материала путём использования ленточного зернопульта А.А. Никитин. Волгоградское издательство. 1957. 43 с.
Пугачёв А.Н. Повреждение зерна машинами А.Н. Пугачёв М.: Колос 1976. – 320 с.
Руководство к самоходному зернометателю ЗМ-30. УВД Житомирской обл. 1972. – 63 с.
Чазов С.А. Пути снижения травмирования семян С.А. Чазов В.Ф. Плаксин Селекция и семеноводство № 4 1969. – С. 101-105.
Сельскохозяйственная техника. Каталог Т 2 Под редакцией академика ВАСХНИЛ В.И. Черноиванова. М.: Информагротех. 1991. – 367 с.
Кукибный А.А. Метательные машины А.А Кукибный. М.: Машиностроение 1964 – 195 с.
А. с. 1643348 СССР МКИ3 5 В 65 G 3104 Порционный метатель Г.Ф. Ханхасаев И.Т. Нуртазин К.А. Кирилов А.Г. Хамаганов и А.Н. Ханхасаев (СССР). – 468504703 (22); Заявл. 28.04.89; Опубл. 23.04.91 Бюл. № 15
Чернавский С.А. Курсовое проектирование деталей машин. М.: Машиностроение 1988. 416 с.
Сборник нормативных документов по охране труда [Текст] под ред. Е.П. Палькеева- М: Нела-информ 2002. – 374 стр.
Зотов В.И. Проектирование и расчет средств обеспечения безопасности [Текст] В.И. Зотов Б.И. Курдюмов. - М.: КолосС 2005. - 216 с.
Безопасность жизнедеятельности. Охрана труда: Учебное пособие для вузов А. В. Фролов Т. Н. Бакаева; под. общ. ред. А. В. Фролова. – Ростов нД.: Феникс 2005. – 736 с.: ил. – (Учебники).
Мельников С.В. Планирование эксперимента в исследованиях сельскохозяйственных процессов С.В. Мельников В.Р. Алёшкин П.М. Рощин. Л.: Колос. 1980. – 168 с.
Бадина Г.В. Семеноводство полевых культур Г.В. Бадина Ю.Н. Яблоков С.М. Синицина. Л.: Колос 1983. – 273 с.
Кондратьев Р.Б. Семенное зерно Сибири Р.Б. Кондратьев. М.: Рос агропромиздат 1988 – 134 с.
Ротор со ступицей.dwg

Заклепка 6 x 11.31 ГОСТ 14801-85
Болт М8-8g x 25.36 ГОСТ 7783-81
Гайка М8-6H.04 ГОСТ 5927-70
Шайба C. 8.31 ГОСТ 11371-78
Общий вид.dwg

Транспортёр загрузочный
Шплинт 5 x 28.4 ГОСТ 397-79
Шайба C. 20.31 ГОСТ 11371-78
Шайба C. 8.31 ГОСТ 11371-78
Болт М8-6g x 28.109.30ХГСА ГОСТ 7798-70
Гайка М8-6H.04 ГОСТ 5915-70
Направляющая.dwg

Крышка задняя кожуха
Крепление задней части кожуха
Болт М6-8gx14.109.30ХГСА ГОСТ 15589-70
Гайка М6-6H.04 ГОСТ 5927-70
Шайба C 6.31 ГОСТ 10450-78
Болт М8-6gx16.109.30ХГСА ГОСТ 7796-70
Шайба C.8.31 ГОСТ 11371-78
Гайка М8-6H.04 ГОСТ 5915-70
Ведомость документации.dwg

Схема технологическая
Агротехнические показатели
Анализ ударного воздействия
Напряжение в зерне при ударе
Технико-экономические
031.017.03.00.000 СБ
031.017.02.02.000 СБ
031.017.03.02.000 СБ
Рама с метателем.dwg

Ось регулировочного винта
Ось площадки двигателя
Подшипник824 ГОСТ 23179-78
Шплинт 2 x 14.4 ГОСТ 397-79
Ремень А ГОСТ 1284.1-89
Болт М6-8gx14.109.30ХГСА ГОСТ 15589-70
Гайка М6-6H.04 ГОСТ 5927-70
Шайба C 6.31 ГОСТ 10450-78
Болт М8-6gx16.109.30ХГСА ГОСТ 7796-70
Шайба C.8.31 ГОСТ 11371-78
Гайка М8-6H.04 ГОСТ 5915-70