Восстановление приводного колеса мостового крана



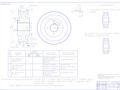
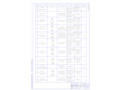
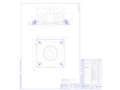
- Добавлен: 25.10.2022
- Размер: 2 MB
- Закачек: 3
Описание
Состав проекта
![]() |
![]() ![]() ![]() |
![]() ![]() ![]() |
![]() ![]() ![]() |
![]() ![]() ![]() |
![]() ![]() ![]() |
![]() ![]() ![]() |
![]() ![]() ![]() |
![]() |
![]() ![]() |
![]() ![]() |
![]() ![]() ![]() ![]() |
![]() |
![]() ![]() ![]() ![]() |
![]() ![]() |
![]() ![]() ![]() ![]() |
Дополнительная информация
записка.docx
Конструкторская разработка приспособления для растачивания отверстия_26
В настоящее время в условиях все возрастающей напряженности работы машин связанной с увеличением мощности скорости давления а также с повышенными требованиями к точности их работы вопросы надежности приобретают исключительно большое значение. На ремонт и восстановление работоспособности машин затрачиваются огромные ресурсы. Это во многом объясняется низкой прочностью поверхностного слоя сопрягаемых деталей машин который составляет всего долю процента от всей массы деталей. Следовательно для повышения долговечности машин решающее значение имеет упрочнение трущихся поверхностей деталей в процессе их изготовления и ремонта.
Целью курсовой работы является разработка технологического процесса восстановления колеса мостового крана грузоподъемностью 15 т.
Требования Правил устройства и безопасной эксплуатации ГПК и других нормативных документов на колеса кранов
Крановые колеса – составляющая крановой техники несущая огромную нагрузку. Применяются в грузоподъемных кранах и механизмах.
Типы крановых колес (в зависимости от модели и назначения крана)
Крановые колеса обычно различают по форме обода колеса и по числу реборд. Форма обода бывает цилиндрической и конической. Если колеса соединены с механизмом крана или тележки они называются приводными или ведущими (рисунок 1) остальные колеса – ведомые. Также колеса отличаются ступицей по – внутреннему диаметру на установку шарикоподшипников или вала с двумя буксами на роликоподшипниках (рисунок 2).
Рисунок 1 – Приводное колесо мостового крана
Изготовление крановых колес
Крановые колеса изготавливаются стандартных размеров возможно изготовление и по чертежам заказчика. Производятся с требованиями ГОСТ 28648-90. Поверхность катания и реборд кранового колеса подвергается термической обработке до требуемой по стандарту твердости с плавным переходом закаленных слоев к незакаленным. Глубина закаленных слоев может достигать 30 мм в зависимости от диаметра. Заготовки крановых колес производят методом штамповки свободной ковки или литья.
Для контроля соответствия крановых колес требованиям ГОСТ 28648-90 проводятся приемосдаточные испытания. У каждого колеса проверяют размеры точность изготовления шероховатость и твердость поверхностей. Твердость поверхности катания и реборд проверяется по ГОСТ 9012. Контроль глубины закалки в проводится на поперечном темплете колеса по ГОСТ 9012 или ГОСТ 9013.
Рисунок 2 – Колесо мостового крана с валом и роликоподшипниками
Эксплуатация крановых колес допускается при износе их реборд не более 50% первоначальной толщины и (или) поверхности катания не более 115% первоначального диаметра.
Для поддержания кранов в рабочем состоянии при износе колес их необходимо своевременно заменять или восстанавливать.
Восстановление и упрочнение крановых колес происходит методом наплавки и нанесения упрочняющего слоя с последующей механической обработкой. Технология и свариваемые материалы позволяют получать твердость до 50 ед. HRC. Срок эксплуатации восстановленных крановых колес не меньше чем у новых.
Технические требования:
Колеса должны изготовляться в соответствии с требованиями ГОСТ 28648-90 по рабочим чертежам утвержденным в установленном порядке.
Колеса должны изготовляться из стали марки 75 или 65Г по ГОСТ 14959. Допускается изготовление колес из стали марки 2 по ГОСТ 10791 а применяемых в механизмах групп режима работы 1М - 3М по ГОСТ 25835 из других марок сталей с механическими характеристиками не ниже чем стали марки 45 по ГОСТ 1050.
Допуски припуски и кузнечные напуски для штампованных колес по ГОСТ 7505 припуски и допуски на кованые колеса - по II группе ГОСТ 7062.
Твердость поверхности катания и реборд изготовленных из сталей марок 75 и 65Г должна быть от 320 до 390 НВ.
По согласованию с потребителем допускается изготовление колес из других марок сталей указанных в п. 2.2 с твердостью поверхностей катания и реборд не менее 280 НВ для механизмов режимных групп 1М и 2М по ГОСТ 25835 и не менее 300 НВ для механизмов режимных групп 3М и 4М по ГОСТ 25835 при условии безопасной эксплуатации изделий.
Для одноребордного колеса шероховатость одной из поверхностей обода должна быть Ra 125 мкм шероховатость другой Ra 100 мкм.
Торцовое биение поверхности обода с шероховатостью Ra 125 мкм не должно быть более 01 мм на 500 мм диаметра.
На каждом колесе поставляемом как запасная часть на поверхности обода с шероховатостью Ra 100 мкм должны быть нанесены ударным способом размеры D X B и клеймо ОТК.
На колесах поставляемых в составе крана или тележки допускается нанесение только клейма ОТК.
Консервация — по ГОСТ 9.014.
Дефекты крановых колес предельные нормы их браковки
В процессе движения крана реборды крановых колес подвергаются значительному износу. Скорость износа реборд крановых колес зависит от величины сил трения возникающих в месте контакта реборды кранового колеса с головкой рельса. Колесо из-за знакопеременных кратковременных нагрузок подвергается быстрому усталостному износу.
Рисунок 3 – Основные дефекты колеса мостового крана при которых эксплуатация крана запрещается
По данным Справочника по кранам срок службы реборд крановых колес может составлять от нескольких лет до нескольких месяцев. На долговечность реборд колес влияют твердость поверхности точность установки. Высокая твердость реборд повышает срок службы колеса до его ремонта и или замены однако приводит к интенсивному износу головки кранового рельса. Среди факторов определяющих износ основная роль принадлежит химическому составу упрочняющей (в первую очередь термической) обработке и формируемым ими структуре и физико-механическим свойствам поверхностных слоев металлов и сплавов.
К числу свойств материалов оказывающих значительное влияние на износостойкость в первую очередь относятся сопротивление сжатию изгибу сдвигу силы молекулярного сцепления твердость вязкость устойчивость механических свойств против воздействия высоких температур и давлений.
Механические свойства материалов определяют фактическую площадь касания и через нее влияют на интенсивность износа. При соприкосновении двух поверхностей их контакт происходит главным образом по вершинам неровностей причем фактическая площадь контакта очень мала. Поэтому даже при небольшой нагрузке местные давления на площадках фактического контакта достигают высоких значений и вызывают пластическое течение металла. Пластическая деформация продолжается до тех пор пока площадь контакта не окажется достаточной для данной нагрузки. Таким образом в процессе износа может наблюдаться увеличение фактической площади контакта и повышение микротвердости поверхностных слоев металла.
Предсказать износостойкость металлов только на основании исследования их механических свойств удается далеко не во всех случаях.
Кроме того следует иметь в виду что установить предел прочности предел текучести а также пластические и динамические свойства поверхностных слоев весьма сложно поэтому в большинстве случаев исследовалась только зависимость износостойкости металла от твердости.
Относительную износостойкость обычно рассматривают как характеристику прочности материала приведенного в состояние наклепа. Этот параметр характеризует механические свойства поверхностного слоя изделия и служит для оценки износостойкости при абразивном износе. Если твердость абразивных зерен значительно выше чем твердость изнашиваемой стали то износ зависит от разницы твердостей абразива и стали. Если твердость стали ниже твердости абразивных зерен но приближается к ней то при уменьшении этой разницы наблюдается уменьшение износа. Наконец если твердость абразивных зерен ниже твердости стали то износ зависит от разности в твердости и быстро уменьшается с увеличением этой разницы. Как известно твердость характеризует сопротивление металла вдавливанию индентора однако при испытании на твердость не выявляются микротрещины концентраторы напряжений и другие потенциальные источники разрушения. Кроме того неодинаков характер силового воздействия на металл при вдавливании индентора и при абразивном изнашивании. Так при абразивном износе наблюдаются две стадии разрушения металла – внедрение абразивной частицы в трущуюся поверхность и срезание стружки или пластическое деформирование. Испытание на твердость в какой-то степени характеризует способность металла сопротивляться внедрению абразивных частиц однако сопротивление снятию микростружки при этом не выявляется. Сопротивление металла на второй стадии абразивного износа по-видимому определяется сопротивлением движению дислокаций(сопротивлением пластическому деформированию под действием тангенциальных сил) и зависит от напряжений необходимых для преодоления дислокациями барьеров в виде чужеродных атомов частиц другой фазы и др.
Таким образом сопротивление металла на второй стадии износа определяется в основном не его твердостью а структурой.
Особенно существенно влияет на износостойкость углерод. Содержание углерода в приделах от 015 до 112% в условиях сухого трения при скорости
скольжения 05 мсек и удельном давлении 5 Мнм2 (05 кГмм2) показало что с увеличением содержания углерода износостойкость увеличивается.
Нормативный срок службы колеса крана определяется ТКП 45-1.03-103-2009 (02250). На основании этого документа составляется акт осмотра крановых колес с бальной характеристикой каждого из дефектов. В табл. 1 приведены наиболее распространенные и нормируемые дефекты.
Таблица 1 - Основные характерные дефекты и повреждения крановых колес.
Контролируемый узел (элемент)
Показатель дефекта при котором дальнейшая эксплуатация не допускается
Вид контроля применяемые средства
- трещины любых размеров;
- износ поверхности катания 4% по диаметру;
- износ реборды до толщины 15 мм в средней части по высоте;
После дефектовки всего крана составляется перечень документов:
Ведомость дефектов (передается владельцу крана и в СКТБ краностроения).
Справка о характере работ выполняемых краном.
Выписка из паспорта об основных параметрах крана.
Копия приказа владельца крана о проведении обследования.
Акт о проведении статических и динамических испытаний.
Результаты проверки химического состава и механических свойств металла несущих элементов металлоконструкций (если проводились).
Заключение по результатам неразрушающего контроля (если проводился) с указанием вида контроля и мест где это выполнялось.
Заключение о состоянии кранового пути.
После этого колесо направляется на ремонтный участок (РММ) где по карте контроля еще раз проводится более детальное обследование колеса и при возможности ремонта колесо восстанавливается в основном автоматической дуговой наплавкой под слоем флюса.
В нашем случае колесо поступило со следующими дефектами:
Износ беговой дорожки и реборд;
Износ поверхности отверстия;
Износ шпоночного паза по ширине.
Колесо изготовлено из стали марки Сталь 65Г ГОСТ 14959-79.
Предельные нормы выбраковки крановых колес приведены в табл.2
Таблица 2 – Предельные нормы выбраковки крановых колес [6].
Дефекты при наличии которых элемент выбраковывается
Ходовые колеса кранов и тележек
Трещины любых размеров
Выработка поверхности реборды до 50% от первоначальной толщины
Выработка поверхности катания уменьшающая первоначальный диаметр колеса на 2%
Разность диаметров колес связанных между собой кинематически более 05%*
* Для механизмов с центральным приводом.
Колесо с указанием мест дефектов приведено на рисунке 1.
Рисунок 4 – Места дефектов кранового колеса
Анализ научно-технической и патентной литературы по ремонту колес кранов
1.Анализ научно-технической литературы
Колесо крана восстанавливается наплавкой. Рассмотрим способы наплавки а также технические требования на наплавку колеса.
Поверхности колеса подлежащие восстановлению методом наплавки должны быть очищены от загрязнений окалины следов коррозии и обезжирены.
Биение колеса подлежащей наплавке не должно превышать 05 мм.
Наплавка восстанавливаемой поверхности может производиться методами:
а)автоматической наплавки под слоем флюса (флюс АН-348А АН-348АМ; проволока Св-08А Св-08ГА Нп-30);
б)полуавтоматической наплавки в среде углекислого газа (углекислота сварочная проволока Св-08Г2С диаметром 16–20 мм);
в)ручной дуговой наплавки штучными электродами применяемыми для сварки или специальными электродами для наплавки.
Наплавку поверхностей колеса с требованиями повышенной износостойкости рекомендуется выполнять проволоками Св-18ХГС Нп-40Г Нп-30ХГСА и др. с последующим медленным остыванием.
При наплавке деталей из углеродистых и низколегированных сталей с содержанием углерода более 037 % процесс следует производить с предварительным нагревом поверхности до температуры от 523 К (250 °С) до 573 К (300 °С). По окончании наплавки следует обеспечить медленное остывание наплавленного металла (обкладка асбестом остывание в сухом песке в печи и т. п.).
Производить наплавку поверхностей деталей при температуре ниже 278 К (5 °С) не допускается.
Наплавка металла — это нанесение металла на поверхность детали с помощью сварки.
По техническим признакам различают следующие виды наплавки:
- по степени механизации процесса — ручная механизированная автоматизированная автоматическая;
- по способу защиты металла в зоне сварки — под слоем флюса под расплавленной обмазкой электрода в вакууме и в защитном газе;
- по характеру протекания процесса — непрерывные и прерывные.
Ручную электродуговую наплавку (рисунок 5) выполняют на постоянном и переменном токе штучными неплавящимися или плавящимися электродами. В качестве неплавящегося электрода чаще всего используют графитовые (угольные) стержни. На наплавляемую поверхность наносят слой наплавочной смеси или пасты соответствующего состава и расплавляют теплом дуги. Толщина наплавленного слоя -1-3 мм. Угольным электродом по слою смеси чаще всего наплавляют плоские поверхности. Более распространена наплавка плавящимися покрытыми электродами.
Рисунок 5 – Реборда кранового колеса с электродуговой наплавкой
Достоинства способа: простота и маневренность;
Недостатки: низкая производительность (1-3 кгч) тяжелые условия труда снижение усталостной прочности наплавленных деталей.
При наплавке в среде защитных газов (рисунок 6) зона горения электрической дуги и расплавленного металла защищается от кислорода и азота воздуха струей нейтрального (защитного) газа. В качестве защитных газов применяются углекислый газ аргон гелий и смеси газов. Углекислый газ надежно изолирует зону наплавки от окружающей среды и обеспечивает получение наплавленного металла высокого качества с минимальным количеством пор и окислов. Расход газа при сварке составляет 8—15 лмин и наплавке — 10—16 лмин.
Рисунок 6 - Схема наплавки в среде углекислого газа: 1- наплавочная головка; 2 - зона подачи СО2;3 - наплавленный металл; 4 - деталь.
Таблица 3 - Режимы наплавки деталей в среде углекислого газа СО
Скорость наплавки мч
электродной проволоки
Рисунок 7 - Схема установки для полуавтоматической наплавки в среде защитного газа: 1 — баллон с газом 2 — осушитель; 3 — подогреватель; 4 — редуктор; 5 — аппаратный ящик; 6 — расходомер; 7 — регулятор давления; 8 — электромагнитный клапан; 9 — механизм подачи проволоки; 10 — наплавочная головка; 11 —восстанавливаемая деталь; 12 — водяной насос с регулятором давления; 13 — электрод; 14 — сварочная ванна; 15 — слой защитного газа (СО); 16 — источник сварочного тока (сварочный генератор)
Наплавка деталей в среде углекислого газа имеет следующие преимущества: высокое качество наплавленных швов возможность наблюдения за ходом наплавки возможность наплавки деталей любых диаметров.
К недостаткам наплавки деталей в среде углекислого газа относятся повышение разбрызгивания металла (до 10—12%) органическое изменение состава наплавляемого металла понижение износостойкости наплавленного слоя снижение усталостной прочности деталей на 10—50 %.
Наплавкой в среде защитных газов восстанавливаются детали трансмиссии и ходовой части строительных машин.
Сущность наплавки под слоем флюса (рисунок 8) состоит в том что сварочная дуга возникающая между электродом и изделием защищается от окисления кислородом воздуха слоем расплавленного гранулированного флюса толщиной 20—40 мм. Флюс поступающий в зону сварочной дуги плавится под действием выделяемого ею тепла.
Принципиальная схема полуавтоматической электродуговой наплавки деталей под слоем флюса показана на рисунке 9.
Сварочный ток от источника тока по проводам подводится к контактам касающимся сварочной проволоки и медной шины расположенной на патроне.
Рисунок 8 – Наплавка колеса крана под слоем флюса
Для наплавки деталей под слоем флюса выпускаются наплавочные головки различных конструкций: ПШ-5 ПШ-54 ПДШ-500 ПДШМ-500 АБС А-409 А-580 ПАУ-1 ОСК-1252М. Наплавочная головка устанавливается на суппорт токарно-винторезного станка и перемещается при наплавке деталей с помощью ходового винта токарно-винторезного станка.
Рисунок 9 - Схема установки для полуавтоматической электродуговой наплавки деталей под слоем флюса: 1 — патрон токарно-винторезного станка; 2 — восстанавливаемая деталь; 3 — слой шлака; 4 — наплавленный металл; 5 — флюс; 6 — электродная проволока; 7 — контакт провода от источника тока с электродной проволокой; 8 — наплавочная головка; 9 — бункер с флюсом; 10 — контакт провода от источника тока с медной шиной патрона (деталью);
е — смещение электрода относительно вертикальной оси детали (эксцентриситет электрода)
Твердость наплавленного слоя порошковыми проволоками достигает HRC 52—56.
Режимы наплавки цилиндрических поверхностей при постоянном токе обратной полярности представлены в табл. 2.
Таблица 4 - Параметры наплавки цилиндрических поверхностей электродной проволокой диаметром 12—25 мм с вылетом 20—30 мм
Преимущества восстановления деталей наплавкой под слоем флюса следующие: производительность автоматической наплавки под слоем флюса выше в 3—5 раз по сравнению с ручной сваркой; высокое качество наплавленного металла и высокая его износостойкость; для выполнения работ не требуется высокой квалификации сварщика.
К недостаткам наплавки деталей под слоем флюса относятся большая зона термического влияния значительный нагрев деталей малых размеров снижение усталостной прочности деталей на 20—40 %.
2.Анализ патентной литературы
На концерне «Азовмаш» с участием Приазовского государственного технического университета [7] разработана новая порошковая лента ПЛН-7 для наплавки колес мостовых кранов. Для исследования влияния легирующих элементов на структуру и свойства наплавленного металла изготовляли двухзамковые порошковые ленты в соответствии с ГОСТ 26467-85 оболочкой которых служила лента из стали 08кп. В качестве порошковой шихты использовали среднеуглеродистый ферромарганец металлический хром феррохром феррованадий мрамор. Железный порошок. Наплавку производили на образцах из стали 45 в три слоя.
Обрабатываемость наплавленного металла твердосплавным инструментом предложенной геометрии вполне удовлетворительная. Производство нового наплавочного материала и наплавка изношенных колес мостовых кранов освоены в концерне «Азовмаш».
Выбор и обоснование способов устранения дефектов
Для восстановления внутренних поверхностей используем наплавку в среде СО2. Основное преимущество этого процесса – небольшой нагрев детали (не более 100ºС) и возможность регулирования твердости наплавленного слоя в зависимости от марки наплавочной проволоки и использования охлаждения при наплавке а также высокая производительность до 25 кгчас. Для наплавки используем проволоку Нп-50 диаметром 15 мм. Охлаждающая жидкость – 5% - ный раствор кальцинированной соды расход 05 1 лмин. Наплавка ведется постоянным током при обратной полярности при напряжении 12 28 В. Оборудование для наплавки: токарный станок 3А228 установка А-1897-4 и наплавочная головка ГМВК-2.
Наплавку наружных поверхностей производим полуавтоматом А-547Р проволокой Св08Г2С ГОСТ 2246-70 под флюсом АН-348.
Для токарной обработки используется расточный резец 2140-0001 ГОСТ 18882-73 с углом в плане 60 градусов с пластинами из твердого сплава Т15К16. Размеры контролируются микрометром МК 250-1 ГОСТ 6507-90.
Для точения и шлифования используем токарный станок ДИП-300. Для шлифования устанавливаем шлифовальный круг вместо резца и приспособление для центровки. Техническая характеристика станка приведена в табл. 3.
Таблица 5 – Техническая характеристика станка ДИП-300.
Диаметр обрабатываемых поверхностей:
Наибольшая длина обрабатываемой заготовки
Пределы рабочих подач стола
Пределы частот вращения шпинделя
Пределы поперечных подач изделия
Мощность электродвигателя
Для закалки используется печь сопротивления.
Способы нагрева поверхностей деталей на установках в зависимости от их типа: одновременный непрерывно-последовательный или методом обкатки.
Закалка деталей производится в наладочном или полуавтоматическом режимах посредством спрейерного охлаждения водой сжатым воздухом или другой технологической средой а также окунанием в масло. Установки удобны в эксплуатации требуют минимальных затрат времени при монтаже и пуске в эксплуатацию.
Таблица 6 -Техническая характеристика печи сопротивления для закалки .
Наименование показателя
Значение показателя
Габариты закаливаемых деталей мм
- диаметр установочный максимальный
- длина закалочная и установочная
- длина установочная в люнете
Масса закаливаемой детали кг
Габаритные размеры установки мм
Наличие верхнего центра
Для протягивания шпоночного паза применяем горизонтально-протяжной станок 7Б55 и протяжку 2405-1171 ГОСТ 18217-90.
Таблица 7 - Техническая характеристика горизонтально-протяжного станка 7Б55.
Максимальная тяговая сила кН
наибольшая длина рабочего хода салазок мм
пределы скоростей рабочего хода ммин
подвода и отвода протяжки ммин
габаритные размеры станка мм
Для контроля используем микрометр МК 250-1 ГОСТ 6507-90 и штангенциркуль ШЦ -1-250-01 ГОСТ 166-89 и шаблон.
Проектирование технологического процесса восстановления кранового колеса
При составлении технологического маршрута необходимо учитывать следующие требования:
одноимённые операции по всем дефектам маршрута должны быть объединены;
каждая последующая операция должна обеспечить сохранность качества работы поверхностей детали достигнутую при предыдущих операциях;
в начале должны идти подготовительные операции затем восстановительные слесарно-механические шлифовальные и доводочные.
План рациональной последовательности технологического процесса восстановления кранового колеса принимаем следующий:
5 Моечная операция (очистка колеса от грязи и старой смазки).
0 Дефектация (дефектовать колесо).
5 Наплавочная операция (наплавить наружные поверхности).
0 Наплавочная операция (наплавить отверстие).
5 Наплавочная (наплавить шпоночный паз).
0 Токарная операция (точить наружные поверхности).
5 Токарная операция (точить внутренние поверхности).
0 Закалка (закалить наружную поверхность).
5 Протяжная (протянуть шпоночный паз).
0 Шлифовальная операция (шлифовать внутренние поверхности).
5 Контрольная операция (контролировать восстановленные поверхности).
Технологический маршрут восстановления с указанием оборудования и режимов представлен в приложении А курсовой работы.
Расчет режимов и норм времени при обработке
Произведем расчет основных параметров для основных операций: наплавка поверхности и точения поверхностей
Операция 025 – Наплавочная
Наплавляем отверстие под подшипник до диаметра d=120 мм.
Режим наплавки включает в себя показатели: величину и род тока и напряжение дуги скорость наплавки скорость подачи электродной проволоки шаг наплавки смещение электрода от зенита частоту вращения детали.
Для наплавки выбираем проволоку ПП-3Х2В8Т диаметром 18 мм.
Величина тока зависит от диаметра электродной проволоки скорости ее подачи и от диаметра детали.
Плотность тока равна:
- площадь сечения порошковой проволоки мм:
где - диаметр электродной проволоки.
Напряжение наплавки
Скорость автоматической наплавки определяется по формуле:
где - толщина наплавляемого слоя;
- шаг наплавки который выбирается в зависимости от толщины наплавляемого слоя;
- коэффициент наплавления;
- скорость подачи электродной проволоки ммин:
где - диаметр наплавляемой детали;
- частота вращения детали.
Тогда скорость наплавки равна:
Особенность нормирования при автоматической наплавке на специальной установке или приспособленном токарном станке состоит в необходимости учета как факторов сварочного процесса так и режимов используемых при токарной обработке.
Норма штучно-калькуляционного времени:
где - основное время мин;
- вспомогательное время мин;
- время обслуживания рабочего места мин;
- подготовительно-заключительное время на одну деталь мин.
В зависимости от того какие параметры процесса автоматической наплавки известны определение нормы времени осуществляется по формуле:
- при известной скорости наплавки и шаге наплавки:
- скорость наплавки;
- общая длина наплавляемых поверхностей;
- диаметр наплавляемой детали;
- толщина наплавляемого слоя за один проход;
3 - коэффициент учитывающий время обслуживания рабочего места отдых и личные надобности рабочего;
- вспомогательное время на установку закрепление и снятие детали;
- время на очистку и контроль погонного метра наплавленного валика;
- длина валика наплавленного валика м:
- подготовительно-заключительное время на ознакомление с работой наладку оборудования и сдачу наплавленных деталей и оснастки.
Тогда норма штучно-калькуляционного времени будет равно:
Операция 030 – Токарная
Растачиваем отверстие диаметром d=118 мм до диаметра D=120М7 мм длиной Lр=5825 мм на токарном станке. Параметр шероховатости обрабатываемой поверхности Ra=16 мкм. Назначим режим резания.
Глубина резания при снятии припуска за один рабочий проход
Назначаем подачу. Для Ra=16 мкм S0=005-015 ммоб. Принимаем S0=015 ммоб.
Назначаем период стойкости резца Тр=30 мин.
Скорость резания определим из формулы
где Vтабл – скорость ммин выбираемая по таблице;
К1 – коэффициент зависящий от обрабатываемого материала;
К2 – коэффициент зависящий от типа материала и стойкости инструмента;
К3 – коэффициент зависящий от диаметра прутка при его обработке;
Рассчитываем число оборотов шпинделя станка по
где D – диаметр отверстия до которого нужно обработать поверхность детали;
Vp – скорость резания ммин;
К – коэффициент увеличения частоты вращения при сверлении и уменьшения при развёртывании и нарезании резьбы;
Корректируем частоту вращения по данным станка и устанавливаем действительную частоту вращения
Тогда уточним величины Vp ммин по принятым значениям nд обмин
Определяем длину рабочего хода суппорта
Lр – длина резания мм;
Lп – величина подвода врезания перебега инструмента мм;
Lд –дополнительная длина хода инструмента мм вызванная особенностями наладки или конфигурации детали;
Рассчитаем основное технологическое время
где L– длинa рабочего хода суппорта мм;
n – частота вращения шпинделя обмин;
где PZТАБЛ – осевая сила резания кН;
t – глубина резания;
Найдем мощность резания
где Pz– сила резания кВт;
Vд – скорость резания ммин;
Проверка достаточности мощности.
где Nд – мощность электропривода станка кВт;
Обработка возможна: Nр N (88 11 кВт).
Конструкторская разработка приспособления для растачивания отверстия
При обработке внутренних поверхностей с диаметрами более 100 мм возникает необходимость в спецоснастке станков токарной группы либо применение в техпроцессе горизонтально-расточных станков которые очень дорогие и для ремонтного производства установка этих станков является экономически невыгодным. Остается вариант с применением спецоснастки.
Произведем анализ станочных приспособлений.
По целевому назначению приспособления делят на следующие группы:
Станочные для установки и закрепления обрабатываемых заготовок. Эти приспособления подразделяют на сверлильные фрезерные расточные токарные и др. (по группам станков).
Станочные для установки и закрепления рабочего инструмента. К ним относятся патроны для сверл разверток метчиков многошпиндельные сверлильные и фрезерные головки инструментальные державки для токарно-револьверных станков и автоматов и другие устройства. Эти приспособления называются вспомогательным инструментом.
Сборочные используемые для соединения деталей в изделия. Применяют следующие типы приспособлений: а) для крепления базовых деталей собираемого изделия; б) для обеспечения правильной установки соединяемых элементов изделия; в) для предварительного деформирования устанавливаемых упругих элементов (пружин разрезных колец); г) для запрессовки клепки развальцовывания и других операций когда при сборке требуются большие силы.
Контрольные применяемые для проверки заготовок при промежуточном и окончательном контроле деталей а также при сборке машин.
Приспособления для захвата перемещения и перевертывания заготовок деталей и собираемых изделий.
По степени специализации станочные приспособления делят на следующие группы: универсально-безналадочные (УБП) универсально-наладочные (УНП) универсально-сборные (УСП) сборно-разборные (СРП) неразборные специальные (НСП) специализированные наладочные (СНП).
К группе УБП относятся универсальные приспособления общего назначения: центры поводковые устройства оправки токарные патроны цанговые приспособления плиты магнитные и электромагнитные столы и т.д. Они изготовляются как принадлежность к станку заводом изготовителем станков или специализированными предприятиями. УБН применяют в единичном и мелкосерийном производстве; на станках с ЧПУ – в мелкосерийном производстве.
Группа УНП включает приспособления состоящие из постоянной части и сменных наладок. Постоянная часть во всех случаях остается неизменной а сменная наладка заменяется в зависимости от конкретной обрабатываемой детали. Постоянная часть включает в себя корпус и зажимное устройство с приводом (чаще пневматическим). Иногда в нее встраивают делительное устройство и другие элементы кроме опорных и направляющих. Постоянная часть изготавливается заранее и применяется многократно. Перед очередным использованием УНП требуется произвести лишь смену наладки или некоторую дополнительную обработку. Наладка представляет собой сменные опорные и направляющие элементы. Каждый комплект наладки предназначен только для данной детали и конкретной операции ее обработки и в этом случае является специальным. С помощью УНП заготовка устанавливается с такой же точностью и быстротой как и при использовании дорогостоящего специального приспособления. Универсальность УНП несколько ограничена определенными размерами постоянной части которая обычно нормализуется в пределах предприятия или отрасли. К числу нормализованных приспособлений на базе которых собирают УНП относятся машинные тиски скальчатые кондукторы пневматические патроны со сменным кулачками планшайбы с переставными угольниками для растачивания на токарном станке деталей сложной формы и т.д. УНП применяют в серийном производстве; на станках с ЧПУ – в мелкосерийном производстве.
УСП включают приспособления компонуемые из нормализованных деталей и узлов. Каждая компоновка УСП обладает всеми основными свойствами специального приспособления: предназначена для обработки конкретной детали на определенной операции и обеспечивает базирование заготовки без выверки и требуемую точность. По истечении надобности в таком приспособлении оно разбирается на составные детали и узлы которые могут быть многократно использованы для компоновки других приспособлений. Отличительной особенностью УСП является крестообразное взаимно-перпендикулярное расположение на сопрягаемых поверхностях Т-образных и шпоночных пазов. Основные детали и сборочные единицы из которых компонуются УСП условно подразделяются на семь групп: 1) базовые детали (плиты прямоугольные и круглые угольники); 2) корпусные детали (опоры призмы подкладки и т.д.); 3) установочные детали (шпонки штыри пальцы и т.д.); 4) прижимные детали (прихваты планки); 5) крепежные детали (болты шпильки винты и т.д.); 6) разные детали (ушки вилки хомутики оси рукоятки и т.д.); 7) сборочные единицы (поворотные головки кронштейны центровые бабки и др.).
В приборостроении и машиностроении используют комплекты УСП-8 с шириной пазов 8 мм и диаметром крепежных элементов (8 мм для обработки малогабаритных заготовок (220(120(100 мм). УСП-12 предназначены для обработки заготовок размерами 700(400(200 мм а УСП-16 для заготовки размерами 2500(2500(1000 мм.
УСП применяют в единичном и мелкосерийном производстве. При использовании вместо ручных зажимов гидро- или пневмозажимов УСП можно применять и в крупносерийном производстве. На станках с ЧПУ УСП применяются в единичном и мелкосерийном производстве.
Система СРП является разновидностью системы УСП. В компоновках СРП в отличие от УСП количество сборочных единиц преобладает над деталями. Приспособления переналаживаются посредством перекомпоновки регулирования положения базирующих и зажимных элементов или замены сменных наладок. СРП обычно собирают на период выпуска определенного изделия. После обработки партии деталей приспособление снимают со станка и хранят до запуска в обработку новой партии. Разбирают СРП только при смене объекта производства. Компоновки СРП собирают из стандартных деталей и сборочных единиц фиксируемых относительно друг друга системой палец-отверстие. Для этой цели в базовых деталях имеются сетки точных координатно-фиксирующих отверстий. К столу станка детали и сборочные единицы СРП крепятся посредством Т-образных пазов. СРП применяются в единичном и мелкосерийном производстве а на станках с ЧПУ – в мелкосерийном производстве.
Приспособления группы НСП служат для обработки только определенной детали на одной конкретной операции. Специальные приспособления обладают большими преимуществами – позволяют без выверки придать заготовке требуемое положение относительно станка и режущего инструмента и благодаря этому при одной настройке обработать всю партию заготовок. К НСП относятся патроны для токарных автоматов и полуавтоматов мембранные патроны гидропластмассовые приспособления и др. НСП применяются в крупносерийном и массовом производствах. На станках с ЧПУ такие приспособления можно применять лишь как исключение если нельзя применить ни одну из переналаживаемых систем.
К группе СНП относятся специальные приспособления обладающие определенной универсальностью вследствие введения в их конструкцию элементов допускающих наладку приспособления путем регулировки. Благодаря этому одно и тоже приспособление можно применять для обработки ряда деталей одной конструкторско-технологической группы. К СНП относятся переналаживаемые планшайбы патроны оправки кондукторы и т.д. СНП применяют в серийном и крупносерийном производствах; на станках с ЧПУ – в серийном производстве.
Кроме вышеперечисленных групп приспособлений на станках с ЧПУ и обрабатывающих центрах используются и другие группы приспособлений: механизированные универсально-сборные (УСПМ) и универсально-сборные переналаживаемые (УСПО).
Приспособление (рисунок 10) работает следующим образом: корпусная деталь устанавливается на плиту 1 прихваты 2 устанавливаются на буртик колеса. Прихваты прижимаются к плите при помощи шпильки 3 с гайкой 4. Центрирование катка производится на проточке в плите. Для удобства прихваты снабжены пружинами 5.
Расчет приспособление сводится к определению силы прижатия корпуса к плите.
Сила прижатия находится по формуле
где - сила прижатия одним прижимом Н;
- количество прижимов в приспособлении .
где - зажимное усилие для винтового зажима Н;
- плечо действия силы мм ;
- плечо действия силы мм .
Зажимное усилие для винтовым зажимов рассчитывается по формуле [6]
где L - длина рукоятки (ключа) мм ;
- средний радиус резьбы мм ;
- угол подъема резьбы по условию самоторможения резьбы;
-приведенный угол трения;
- коэффициент трения;
- диаметр винта мм ;
Рисунок 10 – Приспособление: 1 - плита 2 – прихваты 3 - шпильки 4 - гайки 5 - пружины.
Тогда сила прижатия одного прижима равна
Сила прижатия всех прижимов приспособления
Сравниваем со значением силы резания
Таким образом растачивание отверстия под подшипники возможно на данном приспособлении.
Рациональное и экономное использование дорогостоящих и дефицитных легирующих сталей для наплавки представляет собой важную народнохозяйственную задачу. Одним из путей решения этой задачи является изготовление деталей машин и инструмента из сравнительно дешевых марок малоуглеродистых и низколегированных сталей с рабочими поверхностями наплавленными высокопрочными и износостойкими легированными сплавами.
В курсовой работе разработан технологический процесс восстановления кранового приводного колеса мостового крана грузоподъемностью 15 т. В качестве способа восстановления выбрана дуговая наплавка в среде защитных газов для внутренних поверхностей и наплавка под флюсом для наружных. Произведен расчет режимов обработки и норм времени для основных восстановительных операций. В качестве приспособления разработано приспособление для растачивания отверстия.
Список использованных источников
Технический кодекс установившейся практики ТКП 45-1.03-103-2009 (02250) «КРАНЫ ГРУЗОПОДЪЕМНЫЕ. КАПИТАЛЬНЫЙ ПОЛНОКОМПЛЕКТНЫЙ И КАПИТАЛЬНО-ВОССТАНОВИТЕЛЬНЫЙ
РЕМОНТЫ».Правила выполнения. Министерство архитектуры и строительства Республики Беларусь. Минск 2009.
Алексеев Е.К. Мельник В.И. Сварочное дело. Госстройиздат 1959г.
Д.Л. Глизманенко Сварка и резка металлов. Издание пятое переработанное. Москва 1970г.
Гарост М.М. Масловская Е. М. Учебно - методическое пособие к курсовой работе по дисциплине «Технология производства и ремонта машин» – Минск: БНТУ 2008.
Ансеров М.А. “Приспособление для машинорежущих станков” М. “Машиностроение” 1975 г.
Моисеев В.В. “Проектирования приспособлений для металлорежущих станков” Методическое пособие. Ю-Сах ЮСГПИ 1994 г.
ПРАВИЛА УСТРОЙСТВА И БЕЗОПАСНОЙ ЭКСПЛУАТАЦИИ ГРУЗОПОДЪЕМНЫХ КРАНОВ (с учетом изменений внесенных постановлением Министерства по чрезвычайным ситуациям Республики Беларусь от 08.10.2007 №84 рег. №817287 от 22.10.2007).
Новый наплавочный материал для повышения долговечности ходовых колес мостовых кранов Л.С. Малинов Е.Я. Харланов и др. Сварочное производство 1988. №9; с. 18-20.
Влияние плазменной обработки на напряженно-деформированное и структурное состояние гребней бандажей колес локомотивов С.Н. Киселев А.В. Саврухин и др. Сварочное производство 2001 №6; с. 9-17.
эскиз для токарной.doc
Точить поверхность выдерживая размеры 1- 3.
Техпроцесс.DOC
Министерство образования Республики Беларусь
Белорусский национальный технический университет
Руководитель Гарост М.М.
ТЕХНОЛОГИЧЕСКОГО ПРОЦЕССА ВОССТАНОВЛЕНИЯ
КОЛЕСА МОСТОВОГО КРАНА ГРУЗОПОДЕМНОСТЬЮ 10т
ГОСТ 3.118-82 форма 1
Код наименование операции
Обозначение документации
Код наименование оборудования
РМ 005 Моечная ИОТ №5
Машина моечная ОМ-837 Щетка металлическая резиновые перчатки ГОСТ 124015-82 «Лабомид-101» ТУ38-30728-71 ветошь 25. 1-2
РМ 010 Дефектовочная ИОТ №10
Стол дефектовщика станок токарно-винторезный ДИП-300 оправки штангенциркуль ШЦ-1-160-01 ШЦ-1-250-01 ГОСТ 166-89
линейка стальная нутромер микрометрический НИ-100-150 ГОСТ 868-75 ветошь 25 ГОСТ 5354-79.
РМ015Наплавочная ИОТ №15
Полуавтомат сварочный А-547-Р бункер щетка металлическая резиновые перчатки ГОСТ 124015-82 напильник 2820-0018 ГОСТ 1465-80.
РМ020 Наплавочная ИОТ №20
Установка для наплавки А-1897-4 выпрямитель сварочный блок питания БП-2 клещи щетка металлическая
резиновые перчатки ГОСТ 124015-82 напильник 2820-0018 ГОСТ 1465-80.
РМ025 Наплавочная ИОТ №25
Токарно-винторезный ДИП-300 установка для наплавки А-1897-4 выпрямитель сварочный блок питания БП-2 клещи щетка металлическая.
Наименование детали сборочной единицы или материала
РМ 030 Токарная ИОТ №30
Станок токарно-винторезный ДИП-300 резец 2120-0062 ВК6 ГОСТ 18881-73штангенциркуль ШЦ-1-160-01 ШЦ-1-250-01 ГОСТ 166-89.
РМ 035 Токарная ИОТ №35
Станок токарный расточной ДИП-300 головка расточная резец 2142-0002 ВК6 ГОСТ 18881-73штангенциркуль ШЦ-1-160-01 ГОСТ 166-89.
РМ 040 Протяжная ИОТ №40
Горизонтально-протяжной станок 7Б55 протяжка ГОСТ 18217-90 штангенциркуль ШЦ-1-160-01 ГОСТ 166-89
Т 045 Термическая ИОТ №45
Печь для закалки сопротивления пресс Роквелла перчатки ГОСТ 124015-82.
РМ 050 Шлифовальная ИОТ №50
Станок круглошлифовальный 3Е184ШВ приспособление для контроля диаметров круг шлифовальный 600х100х30 524 А зернистость Э46-60
штангенциркуль ШЦ-1-160-01 ГОСТ 166-89.
РМ 055 Контрольная ИОТ №55
линейка стальная пресс Роквелла нутромер индикаторный НИ-100-1500ГОСТ 868-75 ветошь 25 ГОСТ 5354-79.
Министерство Образования Республики Беларусь.doc
Белорусский национальный технический университет
Кафедра “Строительные и дорожные машины”
по дисциплине «Технология производства и ремонта машин»
На тему: «Разработать технологический процесс восстановления приводного колеса мостового крана грузоподъемностью 15т
ПОЯСНИТЕЛЬНАЯ ЗАПИСКА
Исполнитель: студент гр. 114121
Руководитель: Гарост М.М.
Операционная карта для наплавки.doc
Наименование операции
Оборудование устройство ЧПУ
Обозначение программы
Наплавить поверхность выдерживая размеры 1-2
Токарный станок ДИП-300 установка А-1897-4
Контролировать наплавленную поверхность
Штангенциркуль ШЦ-1-160-01 ГОСТ 166-89
ШЦ-1-250-01 ГОСТ 166-89
Рукавицы ГОСТ 12.4020-82
ОПЕРАЦИОННАЯ КАРТА НАПЛАВКИ
эскиз для наплавки.doc
Наплавить поверхности выдерживая размеры 1-2.
Операционная карта для токарная.doc
Наименование операции
Оборудование устройство с ЧПУ
Обозначение программы
Установить деталь на столе и закрепить.
Переход 1: Точить поверхность резцом проходным 2140-0042 Т15К6 ГОСТ 18882-73 выдерживая размеры.
Снять деталь контролировать все обработанные поверхности: штангенциркулями ШЦ1-250-01 ШЦ2-160-005 ГОСТ166-89;
ОПЕРАЦИОННАЯ КАРТА МЕХАНИЧЕСКОЙ ОБРАБОТКИ
Маршрутный процесс восстановления.dwg

тошь 25 ГОСТ 5354-79
- дефектовать колесо
станок токарно-винторез-
-наплавить наружные по-
Полуавтомат сварочный
Проволока порошковая
-наплавить шпоночный
-наплавить поверхность
для наплавки А-1897-4
выпрямитель сварочный
Токарно-винторезный
-точить наружные повер-
Станок токарно-винто-
- точить поверхность под
-протянуть шпоночный
Горизонтально-протяжной
- закалить наружные повер-
-шлифовать поверхности
- контролировать вос-
тановленные поверхности
приспособление для кон-
Маршрутный технологический
процесс восстановления колеса
Наименование операции
Основное оборудование
Машина моечная ОМ-837
Ремонтный чертеж приводное колесо.dwg

противоположной стороны
Наплавить порошковой
проволокой под слоем флюса
механическая обработка.
защитных газов наплавочной
Колесо бракуется при наличии трещин и усталостного выкрашивания
Технологический маршрут восстановления: точить (Деф 2)
- при наплавке и точении беговой дорожки
точении и шлифовании отверстия
протягивании шпоночного паза
повторяемости дефекта
проволокой в среде за-
Износ беговых дорожек
Износ шпоночного паза
Твердость наружных поверхностей НRC 41 52
Срок службы восстановленного колеса должен составлять не
менее 80% от срока службы новой детали.
Остальные ТТ по СТБ 1014-95.
Ручная дуговая наплавка.
Приспособа.dwg

Размеры для справок.
Сопрягаемых поверхности подвижных деталей смазать
смазкой ЦИАТИМ-221 ГОСТ 9433-80.
Остальные ТТ по СТБ 1022-96.