Установка для прогонки резьбы вала якоря генератора



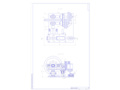
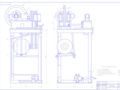
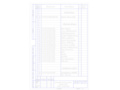
- Добавлен: 25.10.2022
- Размер: 970 KB
- Закачек: 0
Описание
Состав проекта
![]() |
![]() |
![]() ![]() ![]() ![]() |
![]() ![]() ![]() ![]() |
![]() ![]() ![]() ![]() |
![]() ![]() ![]() |
![]() ![]() ![]() |
![]() ![]() ![]() |
![]() |
![]() ![]() ![]() |
![]() ![]() ![]() |
![]() ![]() ![]() |
![]() ![]() ![]() |
![]() ![]() ![]() |
![]() ![]() ![]() |
![]() ![]() ![]() |
![]() ![]() ![]() |
Дополнительная информация
Спецификация ВО v 5.spw

Тиски пневматические
Цилиндр пневматический
Электродвигатель 4АМ80А8У3
А1-ВО 2 v5.cdw

А1-ВО v 5.cdw

Усилие подачи шпинделя
Частота вращения шпинделя
Установка для прогонки
А1-ВО v 5.dwg
Усилие подачи шпинделя
Частота вращения шпинделя
Установка для прогонки
Спецификация ВО v 5.dwg
КП.ПРЭТО.00.00.000 ВО
Тиски пневматические
Цилиндр пневматический
Электродвигатель 4АМ80А8У3
Содержание.docx
Проектирование и расчет силовых механизмов и привода
разрабатываемого модернизируемого узла 11
Расчет наиболее нагруженных элементов конструкции на прочность 17
Эксплуатация и техническое обслуживание оборудования правила техники безопасности при работе ..19
Список использованных источников 24
Приложение:Спецификация .25
3 Расчетная элементов конструкции на прочность.docx
1 Выбор нагруженного элемента
Наиболее нагруженными элементами конструкции пневмотисков являются: резьба на штоке и на шпильках пневмоцилиндра а также ось ролика в клиновом механизме (см. рисунок 2.1 3.1)
2 Выбор материала для штока и шпилек пневмоцилиндра оси ролика область применения вид термообработки и физико-механические свойства
Для изготовления штока и шпилек пневмоцилиндра применяем качественную углеродистую сталь 45 го ГОСТ 1050-88; вид термообработки - нормализация твердость НВ 207; область применения - ответственные детали различного характера (корпуса валы оси фланцы кольца кронштейны); допускаемые напряжения при растяжении [] = 60 70 МПа; допускаемые напряжения при статической нагрузке при срезе [] = 123МПа; при смятии
3 Составление расчетной схемы
Составляем расчетную схему (рис. 3.1) с указанием действующих сил
Рисунок 3.1 – Расчетная схема для расчета оси на срез и смятие
Определим диаметр оси ролика из условия обеспечения прочности при работе на срез и смятие.
Условие прочности для стержня установленного без зазора по напряжениям среза МПа имеет вид:
где F=W - внешняя нагрузка Н
d - диаметр стержня (оси) мм
i=2 - число плоскостей среза
[СР] - допускаемое напряжение среза МПа
Выразив из (3.1) d определим требуемый диаметр оси из условия прочности на срез.
Принимаем диаметр оси d = 16мм.
Определим напряжения смятия см (МПа) для выбранного диаметра оси и сравним его с допустимым.
где 2 - длина контактирующей поверхности (см. рисунок 3.1) мм
[см] - допускаемое напряжение смятия МПа
Принимаем 2=16мм тогда
Полученное см=59 Мпа ≤ [см]=294 МПа; следовательно условие прочности обеспечивается.
2 Расчетная часть .docx
1 Расчет пневмопривода и клинового механизма
1.1 Составление расчетной схемы
Составляем расчетную схему (рисунок. 2.1) с указанием действующих сил.
Рисунок 2.1 – Расчетная схема пневмотисков
1.2 Определение требуемого усилия на штоке пневмоцилиндра
Определяем требуемое усилие на штоке пневмоцилиндра по формуле
где - соответственно приведенный угол трения качения на наклонной и горизонтальной плоскостях клина;
Для упрощения расчетов используем заданное передаточное отношение сил(коэффициент усиления)[2с.134].
Для угла скоса клина α =16º передаточное [2приложение] отношение сил i=WQ = 2.5.
Q=W17=35002.5 = 1400 H.
3 Выбор номинального давления
При расчетах пневмопривода расчетное давление сжатого воздуха рекомендуется принимать равным р = 05 МПа.
4 Определение параметров пневмоцилиндра
Толкающее усилие Q1=Q=1400 H;
Диаметр пневмоцилиндра D:
где – механический КПД пневмоцилиндра
Принятые размеры пневмоцилиндра представлены в таблице 2.1.
Таблица 2.1 – Размеры пневмоцилиндра
Диаметр цилиндра D мм
резьба штока наружная
резьба в отверстии для подвода воздуха
толщина стенки цилиндра для стали h мм
диаметр резьбы на шпильках
Площадь штоковой полости F2:
Фактическое толкающее усилие Q1:
Фактическое толкающее усилие Q1 больше требуемого равного 1400 Н. Возврат поршня в исходное положение происходит под действием пружины.
Скорость движения поршня за рабочий ход :
Принимаем скорость движения поршня = 01 мс (из условия безударного подвода).
Время движения поршня t:
Расход воздуха за рабочий ход V:
5 Определение внутреннего диаметра трубопровода
где – скорость движения воздуха в трубопроводе мс
6 Устройство и принцип действия пневмопривода
- вентиль; 2- фильтр-влагоотделитель; 3- редукционный клапан; 4- манометр; 5- маслораспылитель; 6- реле; 7- обратный клапан; 8- глушитель; 9- пневмо-распределитель; 10- пневмоцилиндр.
Рисунок 2.2 - Схема пневмопривода
Пневмоцилиндр работает следующим образом. Сжатый воздух из сети через вентиль 1 поступает в фильтр-влагоотделитель 2. Редукционный клапан 3 предназначен для понижения давления сжатого воздуха поступающего из пневмосети до заданного. С помощью манометра 4 осуществляется контроль давления сжатого воздуха подаваемого в пневмоцилиндр. Маслораспылитель 5 обеспечивает подачу смазочной жидкости в поток сжатого воздуха. Реле 6 предназначено для контроля давления (01 063 МПа) сжатого воздуха и подачи сигнала при достижении заданного давления а также для отключения электродвигателей станка при аварийном падении давления. Для защиты от аварийного падения давления в пневмосети предусмотрен обратный клапан 7.
Для управления подачей сжатого воздуха в пневмоцилиндр 10 применяется пневмо-распределитель 9. Отработавший сжатый воздух должен выбрасываться в атмосферу через глушитель 8.
7 Выбор пневмоаппаратуры
Выбираем пневмоаппаратуру: влагоотделитепь редукционный пневмоклапан маслораспылитель исходя из наибольшего расхода воздуха.
Выбираем влагоотделитель В41-13 (см. таблицу 2.2)
Таблица 2.2 - Влагоотделитель В41-13
Наибольший расход воздуха м3мин при давлении 04 МПа
Выбираем редукционный пневмоклапан БВ57-13 (см. таблицу 2.3)
Таблица 2.3 - Редукционный пневмоклапан БВ57-13
Выбираем маслораспылитель В44-23 (см. таблицу 2.4)
Таблица 2.4 - Маслораспылитель В44-23
Маслораспылитель работает при давлении воздуха 02 063 МПа.
8 Выбор материала для штока и шпилек пневмоцилиндра оси ролика область применения вид термообработки и физико-механические свойства
Для изготовления штока и шпилек пневмоцилиндра применяем качественную углеродистую сталь 45 го ГОСТ 1050-88; вид термообработки - нормализация твердость НВ 207; область применения - ответственные детали различного характера (корпуса валы оси фланцы кольца кронштейны); допускаемые напряжения при растяжении [] = 60 70 МПа; допускаемые напряжения при статической нагрузке при срезе [] = 123МПа; при смятии [] = 294 МПа.
9 Расчет внутреннего диаметра шпилек для крепления крышек внутреннего диаметра резьбы на штоке
Внутренний диаметр шпилек d1:
где α – коэффициент затяжки резьбы
Внутренний диаметр резьбы на штоке d2:
В пункте 2.4 (см. таблицу 2.1) были приняты следующие размеры пневмоцилиндра: резьба штока наружная М18 диаметр резьбы на шпильках – М12. Следовательно прочность резьбы на штоке и на шпильках обеспечивается.
01 Введение .docx
Достижение поставленной цели возможно путем улучшения использования автомобильного парка за счет выпуска более надежных автомобилей и восстановления утраченной работоспособности их на авторемонтных предприятиях.
С повышением интенсивности использования автомобильного парка растет потребность в ремонте автомобилей агрегатов и узлов для выполнения которого необходимо хорошо организованное авторемонтное производство оснащенное современной производственно-технической базой.
Повышение надежности капитально отремонтированных автомобилей и агрегатов может быть достигнуто путем специализации и концентрации производства улучшения технологии ремонта механизации и автоматизации технологических операций на всех стадиях производственного процесса повышения технического уровня авторемонтного производства на основе реализации организационной и технологической преемственности с автомобилестроением.
Только при этих условиях становится возможной рациональная организация ремонта и внедрение на предприятиях высокоэффективных методов ремонта обеспечивающих улучшение качества и снижение себестоимости ремонта автомобилей и их агрегатов.
При концентрации и специализации авторемонтного производства представляется возможным приблизить организацию ремонта к уровню автомобилестроения с внедрением комплексной механизации и частичной автоматизации производственных процессов.
Для осуществления этих процессов необходимо разнообразное технологическое оборудование. Во многих случаях возможно использование типового предусмотренного государственными стандартами оборудования производимого промышленностью относительно большими или малыми сериями. Вместе с тем для механизации и автоматизации производственных процессов необходимо значительное количество специального оборудования. Это оборудование как правило в силу своего назначения отлично от типовых конструкций и не предусмотрено ГОСТом и поэтому относится к нестандартизированному оборудованию.
В отличие от автомобилестроения в авторемонтном производстве в значительно большей степени используется нестандартизированное оборудование изготовляемое средствами самих авторемонтных предприятий или объединений. Такое оборудование проектируется или в отраслевых опытно-конструкторских организациях или в производственных объединениях или непосредственно на предприятиях где необходимо механизировать производственные процессы.
Решение этих задач требует хорошо оснащенной и рационально размещенной ремонтной базы и высококвалифицированных специалистов с глубокими знаниями теории и практики проектирования технологической оснастки и ее модернизации.
В связи с этим в учебном процессе высших учебных заведений значительное место отводится самостоятельным работам выполняемым студентами старших курсов таким как курсовые работы или проекты по дисциплине «Проектирование расчет и эксплуатация технологического оборудования»
Выполнение курсовой работы позволит получить закрепить знания полученные студентами во время лекционных и практических занятий и самостоятельных занятиях не только по данной дисциплине но и по другим техническим дисциплинам. Она должна научить студентов пользоваться справочной литературой ГОСТами таблицами номограммами нормами умело сочетая справочные данные с теоретическими знаниями полученными в процессе изучения курса.
При выполнение данной курсовой работы особое внимание уделяется самостоятельному творчеству студента с целью развития его инициативы в решении технических и организационных задач а также детального и творческого анализа существующих технологических процессов современного существующего и создаваемого а также модернизируемого оборудования.
В курсовой работе дано описание конструкции разрабатываемого оборудования модели 6606-75А выполнен расчет пневмопривода а также расчет наиболее нагруженных элементов конструкции на прочность даны описания мероприятий по охране труда при работе на данном оборудовании правила его эксплуатации и технического обслуживания.
5 Список использованных источников 1.docx
Оборудование для ремонта автомобилей. Справочник. Под ред. М.М. Шахнеса.-М.:Транспорт 1978.
Горохов В.А. Проектирование и расчет приспособлений. – Мн: Высшая школа 1986г.
Методические указания к выполнению курсовой работы и практической работы по дисциплине «Проектирование расчет и эксплуатация технологического оборудования» для студентов специальности 1-37 01 06 «Техническая эксплуатация автомобилей» УО БГТУ. – Брест 2005.
Т.С.Сокол Охрана труда. – Мн.: Дизайн ПРО 2005
4 Эксплуатация и техническое обслуживание автомобилей 1.docx
1 Рекомендуемая система ТО и ремонта оборудования
Рекомендуемая к внедрению в АТП планово-предупредительная система ТО и ремонта технологического оборудования включает в себя следующие технические воздействия: каждосменное техническое обслуживание профилактический ремонт первый ремонт второй ремонт. При этом все указанные виды технических воздействий являются плановыми и обязательными.
Каждосменное обслуживание (СО) включает работы по подготовке и использованию оборудования – обтирка подключение к источнику питания установка сборочных единиц снятых после прошедшей смены обеспечение необходимыми инструментами приспособлениями материалами дозаправка смазочными материалами и рабочими жидкостями проверка работоспособности и т.п.
Профилактический ремонт (ПР) включает комплекс операций ТО профилактического назначения и ремонтные работы по устранению отдельных неисправностей оборудования: смазочно-очистительные и регулировочные работы; контроль технического состояния агрегатов и образца в целом в статическом и динамическом режиме; крепежные работы; наладка и юстировка диагностического оборудования.
Первый ремонт (Р-1) включает работы проводимые с разборкой и капитальным ремонтом отдельных узлов и механизмов оборудования заменой некоторых деталей углубленной проверкой технического состояния и регулировкой устранением неисправностей сборкой и испытанием оборудования.
Второй ремонт (Р-2) включает работы по капитальному ремонту всех основных агрегатов и частей оборудования в том числе демонтажно-монтажные слесарно-механические сварочные кузнечные электротехнические и другие и предназначен для полного восстановления надежности и работоспособности оборудования до уровня установленного нормативно-техническими показателями нового оборудования.
С учетом обобщенной оценки оборудования и работ по его обслуживанию и ремонту разработана классификация всего перечня образцов технологического оборудования при этом выделяют три группы (см. таблицу 4.1).
Таблица 4.1 – Классификация технологического оборудования по общему критерию
Группа технологического оборудования
Характеристика оборудования по обобщенному критерию
Оборудование не сложное по устройству и восстановлению работоспособности. Не требуется никакой системы ТО и ремонта. При повреждении образца его заменяют новым или восстанавливают с помощью простейших средств и методов силами АТП. ТО не проводится или ограничивается рядом простейших операций.
Оборудование средней сложности устройства и восстановления работоспособности; система ТО и ремонта для многих образцов; может включать все ранее указанные виды ТО и ремонта. Вследствие принципиально различных конструкций содержание ТО и ремонтов также различное. ТО кроме ежедневных операций включает систематическую проверку технического состояния привода рабочих органов герметичности трубопроводов и узлов действия и показаний контрольных приборов устройств и самописцев регулировку узлов и механизмов замену уплотнительных деталей смазку отдельных частей. Ремонт заключается в замене изношенных деталей новыми устранении неисправностей и отказов проведении юстировочных работ и т.д.
Образцы оборудования большой сложности состоящие из ряда различных агрегатов и систем требующие для восстановления работоспособности выполнения специальных и точных работ. Система ТО и ремонта включает поименованные ранее виды технических воздействий. ТО оборудования данной группы включает более расширенный комплекс подготовительных операций выполняемых ежедневно чем по второй группе и ряд дополнительных работ по обслуживанию наиболее сложных механизмов и рабочих органов передаточных устройств систем управления и др. Ремонт кроме перечисленных позиций по второй группе может включать изготовление деталей с высокой точностью устранение неисправностей и отказов электронных сигнальных и измерительных систем работы со сложными и точными настройками и отладками агрегатов узлов и т.д.
Проектируемое оборудование (прототип: модель 6606-72А) относится ко второй группе технологического оборудования.
Поскольку в настоящее время для большинства образцов второй и третей группы недостаточно изучен вопрос по частоте возникновения отказов неисправностей организации работ для их устранения то не существует окончательно обоснованных рекомендаций по периодичности проведения ТО и ремонта технологического оборудования. Наиболее приемлемыми являются рекомендации ГОСНИТИ согласно которым периодичность ПР должна составлять раз в квартал Р-1 – раз в полугодие.
Предлагается следующая периодичность для образцов технологического оборудования:
ПР – ежеквартальная;
2 Правила техники безопасности при работе на оборудовании технические требования и эксплуатация оборудования
К оборудованию приспособлениям[4] и инструменту предъявляется ряд общих требований:
- Оборудование инструмент и приспособления должны в течение всего срока эксплуатации отвечать требованиям безопасности в соответствии с ГОСТ 12.2.003-91 "Система стандартов безопасности труда. Оборудование производственное. Общие требования безопасности" утвержденным постановлением Государственного комитета СССР по управлению качеством продукции и стандартам от 6 июня 1991 г. N 807 (далее - ГОСТ 12.2.003-91) а также настоящим Правилам. При размещении оборудования на производственных участках должны учитываться требования ОНТП 01-86.
- Весь ручной слесарно-кузнечный инструмент как находящийся в инструментальной так и выданный на руки необходимо осматривать не реже одного раза в квартал а также непосредственно перед применением ответственным за исправное состояние инструмента. Неисправный инструмент подлежит изъятию и восстановительному ремонту.
- Стационарное оборудование должно устанавливаться на фундаменты и надежно крепиться болтами. Опасные места должны ограждаться.
- Устройства для остановки и пуска оборудования должны располагаться так чтобы ими можно было удобно пользоваться с рабочего места и исключалась возможность самопроизвольного их включения.
- Все электродвигатели оборудование с электрическим приводом а также пульты управления необходимо надежно заземлять или занулять. Работать без заземления или зануления не допускается.
- Ввод в эксплуатацию нового или прошедшего капитальный ремонт оборудования производится только после приема его комиссией с участием работников службы охраны труда организации. Эксплуатируемое оборудование должно быть исправно и его техническое состояние должно находиться под контролем главного механика и руководителя производственного участка.
- На неисправное оборудование руководитель участка навешивает табличку: "Не включать неисправен". Такое оборудование должно быть отключено или обесточено выключен привод и тому подобное оборудование.
- Не допускается работать на оборудовании со снятым незакрепленным или неисправным ограждением.
- Во время работы оборудования не допускается его чистка смазка или ремонт.
- Электротельферы лебедки и другое оборудование применяемое для перемещения агрегатов и тяжелых деталей должны иметь яркую окраску (черные полосы на желтом фоне) в соответствии с ГОСТ 12.4.026-76.
- Манометры должны проходить государственную поверку не реже одного раза в 12 месяцев иметь штамп государственного поверителя и быть опломбированы. На циферблате манометра установленного на оборудовании должна быть нанесена красная черта соответствующая предельному рабочему давлению. Наносить черту на стекло манометра не допускается.
К пневматическим цилиндрам предъявляется ряд технических требований которые должны обеспечивать:
- герметичность при давлении сжатого воздуха 06 МПа; утечки его через тела крышек по резьбе и стыкам а также через уплотнения поршня и штока не допускаются;
- проверку на прочность при давлении 09 МПа при этом наружные утечки не допускаются;
- испытание на работоспособность путем перемещения штока из одного крайнего положения в другое в диапазоне рабочих давлений 02 06 МПа причем перемещения должны быть плавными без рывков и заеданий;
- давление трогания с места без нагрузки не выше 003 МПа при диаметре цилиндра D=25 63мм; 0025 МПа при D = 80 125мм и 002 МПа при D = 160 320 мм;
- очистку всех воздушных каналов перед сборкой и проверку на проходимость;
- усилие развиваемое поршнем цилиндра во время его перемещения при давлении 06 МПа не менее 85 % от максимального расчетного;
- смазку трущихся поверхностей;
- работу пневмопривода без потери герметичности;
- долговечность для цилиндров с уплотнением поршня манжетами не менее 400000 двойных ходов при длине хода равной двум диаметрам цилиндра а для цилиндров с уплотнением поршня кольцами круглого сечения — не менее 150000 двойных ходов.
При монтаже и эксплуатации пневматических цилиндров необходимо соблюдать следующие условия:
- цилиндры должны быть надежно закреплены на месте их установки;
- все виды крепления цилиндров кроме шарнирного следует осуществлять при помощи болтов или шпилек с равномерной их затяжкой;
- при монтаже нужно строго соблюдать параллельность оси цилиндра к направляющим движения рабочего органа;
- цилиндр требуется присоединять к пневматической системе трубопроводами диаметр которых соответствует диаметру рабочих отверстий в крышках цилиндра для подвода сжатого воздуха;
- трубопровод перед монтажом необходимо тщательно очистить и продуть сжатым воздухом:
- при монтаже трубопровода нужно предусматривать уклон для стока конденсата причем избегать воздушных мешков где он может скопляться. Присоединять трубы к цилиндру надо по возможности снизу;
- для надежной работы цилиндра сжатый воздух требуется очистить от влаги загрязнений и насыщать распыленным маслом;
- шток цилиндра должен быть защищен от ударов. В процессе эксплуатации на него не должна действовать поперечная нагрузка а также попадать абразивная пыль грязь стружка;
- перед длительной остановкой цилиндр следует обильно смазывать.
Заключение.docx
В результате расчета пневмопривода определены параметры пневмоцилиндра выбрана соответствующая пневмоаппаратура а также выполнен расчет на прочность наиболее нагруженных элементов конструкции.
1 Общая часть .docx
Прототип разрабатываемого[1с.357] оборудования - установка модель 6606-72А.Установка предназначена для прогонки резьбы вала якоря генератора. В конструкции установки модели 6606-72 А предусмотрены пневмопривод и клиновые механизмы.
1 Особенности конструкции пневмопривода
Данные приводы состоят из пневмодвигателя пневматической аппаратуры и воздухопроводов.
Пневматические приводы подразделяются по виду пневмодвигателя на поршневые и диафрагменные по схеме действия - на одно- и двусторонние по методу компоновки с приспособлением — на встроенные и агрегатированные по виду установки - на стационарные и вращающиеся по количеству приводов - на одинарные и сдвоенные.
К преимуществам приводов следует отнести быстроту действия (05 12 с) постоянство усилия зажима и возможность его регулировки простоту конструкции и эксплуатации независимость работоспособности от колебаний температуры окружающей среды.
Оптимальная рабочая скорость исполнительного механизма при применении пневмопривода составляет 01 2 мс. При меньших скоростях возникают вибрации и неравномерность хода. Экономически целесообразно применение пневмопривода в механизмах с усилием до 30 кН и пневмоцилиндров с максимальным диаметром 250 мм.
Недостатками пневмопривода являются довольно низкий коэффициент полезного действия большие габариты по сравнению с гидроприводом (из-за применения низкого давления воздуха) неравномерность перемещения рабочих органов особенно при переменных усилиях невозможность остановки в середине хода.
Для надежной работы пневмопривода необходимо обеспечить отделение влаги возможность внесения смазочного материала защиту от превышения или падения давления сжатого воздуха.
2 Клиновые механизмы
Клиновые механизмы компактны по конструкции обеспечивают постоянство сил закрепления и самоторможение однако требуют хорошей защиты от загрязнения и попадания стружки. Клиновые механизмы бывают с односкосым клином без роликов и с роликами которые обычно применяются в качестве усилителей пневмо- и гидроприводов и многоклиновые самоцентрирующие используемые в конструкциях патронов и оправок.
Клиновые механизмы с роликами обычно используются в качестве усилителей и являются несамотормозящими.
3 Описание конструкции и принципа действия прототипа
Общий вид прототипа модели 6606-72А представлен на рисунке 1.1
Рисунок 1.1 – Установка для прогонки резьбы вала якоря генератора
Пневматические тиски установки для прогонки резьбы вала якоря генератора (модель 6606-72А) представлены на рисунке 1.2
Рисунок 1.2 – Пневматические тиски установки для прогонки резьбы вала якоря генератора (модель 6606-72А)
Установка (см. рисунок 1.1 1.2) состоит из рамы 1 [1с.358] пневматических тисков 3 фрикционного привода 4 с автоматическим реверсированием пневмоцилиндра 5 управляемого педалью 6 и электродвигателя 2 с клиноременной передачей. Пневматические тиски служат для установки и зажима якоря и состоят из неподвижного регулируемого прижима 7 подвижного прижима 8 клинового усилителя 9 и пневмоцилиндра 10 управляемого ручным краном.
Фрикционный привод вращения шпинделя состоит из двух конических обрезиненных роликов 11 приводимых во вращение клиноременной передачей от электродвигателя через шкивы 12 шпинделя 14 с укрепленной в нем плашкой 13 вращающегося в подшипниках 16 и чугунного фрикционного диска 15 закрепленного на оси шпинделя. Подача якоря при прогонке резьбы производится с помощью пневмоцилиндра 5. Механизм подачи является одновременно и механизмом автоматического реверсирования так как шпиндель под действием усилия подачи смещается в осевом направлении и фрикционный диск прижимается к одному из двух конических роликов 11 изменяя при этом направление вращения при постоянном направлении вращения коленчатого вала двигателя. Включение цилиндра подачи производится ножной педалью 6.
Якорь устанавливают в тиски и зажимают в них. Включают привод вращения шпинделя и нажатием на педаль включают подачу якоря. Когда плашка шпинделя пройдет резьбу педаль опускают при этом происходит отвод якоря и реверс шпинделя. После отхода якоря в заднее положение отключают электродвигатель разжимают тиски и снимают якорь.
4 Технические характеристики прототипа
Технические характеристики прототипа приведены в таблице 1.1
Таблица 1.1 - Технические характеристики (модель 6606-72А)
Усилие зажима якоря Н
Усилие подачи шпинделя Н
Частота вращения шпинделя мин-1
Габаритные размеры мм
Исходные данные для расчета(согласно задани на выполнение курсовой работы) проектируемой установки представлены в таблице 1.2
Таблица 1.2 – Исходные данные
Усилие зажима якоря W Н
Ход штока(ход губок тисков) L мм
Давление в пневмосистеме МПа