Технология правки деталей с одновременной отделочно-упрочняющей обработкой поверхности




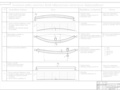
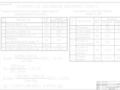
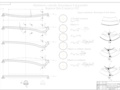
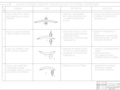
- Добавлен: 25.10.2022
- Размер: 2 MB
- Закачек: 0
Описание
Состав проекта
![]() |
![]() ![]() |
![]() |
![]() ![]() ![]() ![]() |
![]() ![]() ![]() ![]() |
![]() ![]() ![]() ![]() |
![]() ![]() ![]() |
![]() ![]() ![]() ![]() |
![]() ![]() ![]() ![]() |
![]() ![]() ![]() ![]() |
![]() ![]() |
![]() ![]() |
![]() ![]() |
![]() ![]() |
![]() ![]() |
![]() ![]() |
![]() ![]() |
![]() ![]() |
![]() ![]() |
![]() ![]() |
![]() ![]() ![]() |
![]() ![]() |
![]() ![]() |
![]() ![]() |
Дополнительная информация
7 лист(Технология).dwg

пластическим деформированием
ехнология правки деталей с одновременной
отделочно-упрочняющей
обработкой поверхности
Измерение радиального биения
в 5-ти точках по длине вала
Определение плоскости
индикатор часового типа ИЧ-10
Натяг ножки индикатора к
поверхности детали 2 3 мм
Расчет остаточной деформации изгиба
Построение графика упругой линии
Определение максимального прогиба
Программное обеспечение XL
Точность расчета максимального
прогиба оси заготовки 0
Деформирование заготовки на
расчетную величину f
Приспособление для деформирования
Индикатор часового вида типа ИЧ-10
Обеспечение упругой деформации
Устройство для отделочно-
упрочняющей обработки
измерение радиального биения
Индикатор часового типа ИЧ-10
Натяг ножки индикатоора
к поверхности детали 2 3 мм
Построение графика упругой линии детали
Определение остаточного прогиба
Расчет степени исправления W
Точность расчета остаточного
прогиба оси детали 0
Точность расчета степени
Технология правки нежестких валов поверхностным пластическим деформированием
Наименование операции
Отделочно-упрочняющая обработка
6 лист(Техвозможности).dwg

отделочно-упрочняющей
обработкой поверхности
Форма оси вала в момент прогиба при положении люнета
в начале обрабатываемого участка
Эпюра упругого момента
возникающая от приложения силы со
стороны опорного элемента
Условие работоспособности метода
Допустимый изгибающий момент: [M
Допустимое усилие изгиба: [Р
Допустимая величина прогиба: [f
Допустимая исходная деформация
которую можно исправить:
Технологические возможности метода
возникающие в теле детали
3 лист (Исследование возможностей).dwg

возникающие в результате
вращения вала в процессе ППД
Технология правки деталей с одновременной
отделочно-упрочняющей
обработкой поверхности
возникающие в результате
а) Исходное положение
+ + + + + + + + + + + + + + + + + + + + + + + +
Поворот на четверть оборота
Поворот на полоборота
возникающие в теле детали
4+5 листы(Мат.модель).dwg
Технология правки деталей с одновременной
отделочно-упрочняющей
обработкой поверхности
Эпюра напряжений со стороны индентора
по длине детали под
воздействием опорного элемента
Распределение деформации
от процесса ППД по глубине
Распределение деформаций и напряжений
от упругого изгиба по глубине
Схема распространения деформаций
в теле детали при обработке ППД
Схема внедрения сферического индентора
учитывающая упругое восстановление.
Эпюра суммарных напряжений и деформаций
от упругого изгиба заготовки и процесса ППД
Напряжения от процесса ППД
Анализ напряженного состояния заготовки в процессе обработки
2 лист(Технология).dwg

остаточных деформаций
Технология правки деталей с одновременной
отделочно-упрочняющей
обработкой поверхности
ПРАВКА ППД С БАЗИРОВАНИЕМ
ПРАВКА ППД С ИНСТРУМЕНТОМ С
ТРЕМЯ НАКАТНЫМИ ЭЛЕМЕНТАМИ
ПРАВКА ППД ДВУМЯ ДИАМЕТ-
РАЛЬНО РАСПОЛОЖЕННЫМИ
ЭЛЕМЕНТАМИ - ДЕФОРМИРУЮЩИМ
НЫЙ НА ИЗМЕНЕНИИ УПРУГОНАП-
ПОВЫШЕНИЕ ЭФФЕКТИВНОСТИ
РАСШИРЕНИЕ ТЕХНОЛОГИЧЕСКИХ
ЭФФЕКТИВНОСТИ ПРАВКИ
УМЕНЬШЕНИЕ ТРУДОЁМКОСТИ
СЕБЕСТОИМОСТИ ОБРАБОТКИ
ВОЗМОЖНОСТЬ ИСПРАВЛЯТЬ
ОСТАТОЧНЫЕ ДЕФОРМАЦИИ ИЗГИБА
ВОЗМОЖНОСТЬ ОДНОВРЕМЕННОГО
ИСПРАВЛЕНИЯ ОСТАТОЧНЫХ
ДЕФОРМАЦИЙ ИЗГИБА И КРУЧЕНИЯ
НЕ ОБЕСПЕЧИВАЕТ ОТДЕЛОЧНО-
УПРОЧНЯЮЩУЮ ОБРАБОТКУ
ВСЕЙ ПОВЕРХНОСТИ ВАЛА
НЕВОЗМОЖНОСТЬ ИСПРАВЛЕНИЙ
ВАЛОВ С МАЛЫМИ ИСХОДНЫМИ
ПОГРЕШНСОТЬ ОБРАБОТКИ
ВСЛЕДСТВИЕ НЕОДНОРОДНОСТИ
ПЛАСТИЧЕСКОЙ ДЕФОРМАЦИИ
ОБРАБОТКИ ВСЛЕДСТВИЕ
КОЛЕБАНИЯ ГЛУБИНЫ ВНЕДРЕНИЯ
8 лист (Экономика).dwg

Технология правки деталей с одновременной
отделочно-упрочняющей
обработкой поверхности
Калькуляция и структура текущих
Технологическая себестоимость
Снижение трудоемкости
производительности труда
Снижение себестоимости
Условно-годовая экономия
Технико-экономические показатели эффективности
разрабатываемой технологии
ЭКОНОМИЧЕСКОЕ ОБОСНОВАНИЕ ДИПЛОМНОГО ПРОЕКТА
Эуг = (Сзав.б-Сзав.пр)Пг = 343769
1 лист(Технология).dwg

остаточных деформаций
Технология правки деталей с одновременной
отделочно-упрочняющей
обработкой поверхности
СПОСОБ ПРАВКИ ППД С ИЗМЕНЕ-
НИЕМ ПРИВЕДЁННОГО РАДИУСА
ПРАВКА ППД ВАЛОВ РОЛИКАМИ
С ДВУМЯ РАЗНЫМИ ПРОФИЛЯМИ
ПРАВКА ППД РОЛИКОМ С ИЗМЕ-
НЕНИЕМ РАДИУСА КРИВИЗНЫ
ПРАВКА ППД УСТРОЙСТВОМ
И ПРАВЯЩИЙ РОЛИКИ С РАЗЛИЧ-
НЫМИ РАДИУСАМИ КРИВИЗНЫ
ПОЗВОЛЯЕТ СИНХРОНИЗИРО-
ВАТЬ ЗАКОН ИЗМЕНЕНИЯ СИЛЫ
С УГЛОВЫМ ПЕРЕМЕЩЕНИЕМ
ОБЕСПЕЧЕНИЕ ПРОЦЕССА УПРОЧ-
НЕНИЯ ВСЕЙ ОБРАБАТЫВАЕМОЙ
РАСШИРЕНИЕ ТЕХНОЛОГИЧЕСКИХ
ПОВЫШЕНИЕ ПРОИЗВОДИТЕЛЬНОС-
БОЛЬШАЯ ПОГРЕШНОСТЬ ОБРАБОТКИ
СНИЖЕНИЕ ТЕХНОЛОГИЧЕСКИХ
НЕВЫСОКАЯ ПРОИЗВОДИТЕЛЬ-
НЕВОЗМОЖНОСТЬ ИСПРАВЛЕНИЯ
КОРОБЛЕНИЯ ВАЛОВ С МАЛЫМИ
СЛОЖНОСТЬ ПОЗИЦИОНИРОВАНИЯ
АДАПТИВНОЙ СИСТЕМЫ В
ПРОИЗВОДСТВЕННЫХ УСЛОВИЯХ
НЕВОЗМОЖНОСТЬ ИСПРАВЛЕ-
АНАЛИЗ СПОСОБОВ СНИЖЕНИЯ ТЕХНОЛОГИЧЕСКИХ ОСТАТОЧНЫХ ДЕФОРМАЦИЙ
ПОВЫШЕНИЕ КАЧЕСТВА ПРАВКИ
Пояснительная записка.doc
Достижение заданной точности нежёстких деталей сопряжено со значительными трудностями из–за возникновения технологических упругих и остаточных деформаций.
В связи с этим перспективными являются методы правки деталей совмещенные с финишной обработкой. В этом направлении самыми перспективными являются методы правки поверхностным пластическим деформированием. Они позволяют решить одновременно ряд задач: провести собственно правку снизить шероховатость поверхности и упрочнить поверхностный слой.
Среди разработанных на данный момент методов правки ППД практически отсутствуют методы которые было бы возможно применять на производстве. Это происходит из-за трудности их внедрения и отсутствия каких-либо расчетных зависимостей.
Поэтому возникла необходимость разработки простого в эксплуатации и высокотехнологичного метода правки ППД и разработка математической модели для него.
Проблема достижения заданной точности деталей в типовых технологических процессах изготовления.
Проблема повышения точности путём снижения технологических остаточных деформаций продолжает оставаться актуальной несмотря на то что способность деталей деформироваться при нарушении их равновесного напряженного состояния была обнаружена Н.В. Калакуцким ещё в конце XIX века. Однако в то время из–за низких прочностных свойств конструкционных материалов изготовляли достаточно жесткие детали у которых доля технологических остаточных деформаций в общем балансе точности была невелика[21]. Бурное развитие техники сопровождалось созданием новых материалов которые в свою очередь способствовали увеличению числа нежестких изделий. С уменьшением жесткости деталей происходило существенное увеличение доли технологических остаточных деформаций в суммарной погрешности обработки. Более того она часто оказывалась доминирующей при изготовлении прецизионных изделий. Вместе с тем значительно возросли требования к точности. В частности допустимые отклонения от прямолинейности оси высокоточных валов достигли уровня менее 10 мкмм что по крайней мере на порядок ниже величины возникающих при обработке остаточных деформаций изгиба. Поэтому борьба с технологическими остаточными деформациями стала одной из острых проблем в технологии машиностроения.
В технологических процессах изготовления нежестких деталей основным методом снижения остаточных деформаций является обработка резанием в сочетании с межоперационной правкой упругопластическим изгибом и термической стабилизацией остаточных напряжений. Достижение требуемой точности при обработке резанием основано на постепенном уменьшении фактической глубины резания на каждом последующем проходе. Это обусловлено прежде всего необходимостью минимизации неравномерности изменения напряженного состояния заготовки[12].
Установлено что точность обработки после каждого прохода повышается но в то же время находится в определенной зависимости от величины исходной остаточной деформации. При этом на разных стадиях обработки происходит изменение знака остаточных деформаций с неизменным уменьшением их по абсолютной величине (рис. 1.1). Данная закономерность имеет место до определенного числа проходов свыше которого происходит увеличение остаточных деформаций изгиба. Этот факт можно объяснить тем что по мере снятия технологического припуска сопровождающегося снижением жесткости обрабатываемой детали возрастает роль факторов обуславливающих собственную погрешность обработки. В определенный момент собственная погрешность приводит к увеличению неравномерности изменения напряженного состояния заготовки и как следствие снижению точности. На окончательных операциях технологические остаточные деформации достигают наименьших значений т.е. достигается «критическая» точность присущая данной технологии. Причем как правило «критическая» не соответствует требуемой точности т.к. остаточные деформации изгиба превышают допуск на отклонение от прямолинейности оси изделия. В итоге более 50 % обработанных в партии деталей уходит в брак. Процент брака зависит от величины исходной остаточной деформации достигающей до 25 ммм у заготовок из горячекатаного прутка.
Статистическая обработка экспериментальных данных[11] позволила установить что 68 % валов из обрабатываемой партии имеют изогнутую ось форма которой наиболее близко аппроксимируется уравнением параболы второй степени:
У 24 % деталей кривая изогнутой оси аппроксимируется по закону синуса:
где f(z) – текущее значение остаточной деформации изгиба;
Рис. 1.1. Графики изменения остаточных деформаций изгиба на различных операциях токарной обработки валов изготовленных из коррозионно-стойкой стали с критерием жесткости k = 40: III – черновое; III IV V – получистовое; VI – чистовое; 1) = 09 мм; 2) =055 мм
- максимальное значение остаточной деформации; z – текущая координата по длине детали.
Остальные 8 % деталей имеют винтообразное закручивание вдоль продольной оси. При этом среднее арифметическое значение угла закручивания сечений друг относительно друга составляет 8º.
Особо важная роль при изготовлении нежестких деталей отводится финишным операциям технологического процесса. Они в значительной мере определяют точность изделий и качество их поверхностного слоя. В большинстве случаев окончательная обработка деталей производится шлифованием для которого характерно большое теплообразование и неравномерное абразивное воздействие на обрабатываемую поверхность. Эти факторы приводят к неравномерному изменению напряженного состояния заготовки и как следствие увеличению остаточных деформаций изгиба сформированных предшествующей обработкой.
Многолетняя практика показала что типовые технологии изготовления нежестких деталей обладают большой трудоёмкостью и низкой эффективностью в достижении точности. В результате создался значительный разрыв между возрастающими требованиями к точности и технологиями изготовления. Причина такого положения кроется в устаревших подходах к проектированию технологий предусматривающих завышенные диаметры заготовок и многопроходную токарную обработку и недостаточно учитывающих причины механизм и закономерности образования технологических остаточных деформаций.
Причины и механизм образования технологических остаточных деформаций.
1. Технологические начальные напряжения в деталях.
В течение длительного времени считалось что образование технологических остаточных деформаций происходит под воздействием остаточных напряжений. Такой взгляд на роль остаточных напряжений является ошибочным т.к. остаточные напряжения уравновешены в поперечном сечении и не могут вызвать деформацию детали без нарушения их равновесия по какой-либо причине (например неравномерной релаксации нарушения сплошности и др.)[13]. Следовательно деформация детали может происходить только под воздействием неуравновешенных напряжений. Таковыми являются начальные напряжения под которыми понимаются неуравновешенные напряжения в детали после обработки но до её деформации[19].
К начальным напряжениям можно отнести:
– неуравновешенные напряжения сформированные в детали в процессе обработки вследствие неоднородной упругопластической деформации и неравномерных объёмных изменений материала по сечению детали обусловленных нагревом и структурно-фазовыми превращениями;
– неуравновешенные напряжения образованные из наследственных т.е. сформированных предшествующей обработкой остаточных напряжений которые претерпели неравномерное изменение по поперечному сечению в процессе обработки детали на проводимой технологической операции;
– неуравновешенные напряжения возникшие из наследственных остаточных напряжений равновесие которых нарушено релаксационными процессами.
В большинстве случаев процесс обработки детали сопровождается так называемой первоначальной деформацией 0 которая вносится в поверхностный слой и вызывает начальные напряжения н. Начальные напряжения связаны с первоначальной деформацией зависимостью[11]:
Вид обработки и условия её проведения определяют знак и характер распределения начальных напряжений в поперечном сечении детали. При этом объемное поле начальных напряжений в детали можно представить в виде трёх взаимно перпендикулярных составляющих осевых тангенциальных и радиальных напряжений первого рода (рис. 2.1).
Ориентация составляющих связана с направлением векторов формообразующих движений. В дальнейшем будем рассматривать только напряжения первого рода т.к. именно они оказывают существенное влияние на точность и другие эксплуатационные свойства деталей.
Действие сформированных в процессе обработки начальных напряжений (рис. 2.2) эквивалентно действию внутренних сил и моментов стремящихся вызвать деформации детали. Этому препятствуют внешние связи образованные при закреплении заготовки. Величина внутренних сил и моментов зависит от интегральных характеристик Рн и eн эпюры начальных напряжений. Интегральная характеристика Рн представляет собой вектор прикладываемый в центре тяжести эпюры и равный по величине ее площади
где а – глубина распространения начальных напряжений; sн(х) – начальные напряжения; х – текущая координата по толщине детали.
Показатель Рн учитывает уровень и глубину распространения начальных напряжений в поперечном сечении детали не раскрывая сложный характер их распределения[20]. Расстояние от поверхности детали до центра тяжести эпюры eн обуславливает изгибающий момент от начальных напряжений. Интегральные показатели Рн и eн с одной стороны характеризуют распределение начальных напряжений в теле детали с другой – влияние технологических параметров процесса обработки на напряженное состояние детали. Оценить это влияние можно при помощи экспериментальных зависимостей:
где х1 х2 х3 – независимые технологические параметры; C0 C1 a a1 b b1g g1 – коэффициенты регрессии.
Начальные напряжения являются фундаментальным понятием теории остаточных напряжений позволяющим однозначно определить причины и механизм образования остаточных деформаций.
2. Роль начальных напряжений в образовании технологических остаточных деформаций.
После раскрепления детали т.е. после снятия всех внешних связей и нагрузок происходит процесс разгрузки при котором действие внутренних сил и моментов обусловленных осевыми начальными напряжениями в общем случае вызывает изгибную f и продольную D деформации. Действие неравномерных тангенциальных и радиальных напряжений приводит соответственно к закручиванию и искажению формы поперечных сечений. Происходящие деформации сопровождаются перераспределением начальных напряжений по поперечному сечению детали. При этом начальные напряжения уравновешиваясь превращаются в остаточные напряжения у которых главный вектор и главный момент в сечении равны нулю.
Проф. А.Н. Овсеенко [18] была установлена связь между начальными и остаточными напряжениями которая выражается зависимостью:
где sоо(х) и sно(х) – соответственно осевые остаточные и начальные напряжения; sмо(х) и sро – часть начальных напряжений которые
Рис. 2.1. Схема ориентации составляющих начальных напряжений.
Рис. 2.2. Принципиальная схема образования остаточных напряжений и деформаций при односторонней обработке детали: 1 – начальные напряжения; 23 – часть начальных напряжений которые релаксируют в результате продольной и изгибной деформаций; 4 – суммарные начальные напряжения которые релаксируют в результате деформаций; 5 – образованные остаточные напряжения (по А.Н. Овсеенко).
релаксируют в результате изгибной и продольной деформаций.
Из выражения (2.4) и схемы на рис. 2.2 следует что образование технологических остаточных деформаций и напряжений представляет собой единый взаимосвязанный процесс в основе которого лежит формирование и перераспределение начальных напряжений. Именно технологические начальные а не остаточные напряжения являются причиной образования остаточных деформаций в случае отсутствия изменения упругонапряженного состояния заготовки. Этот факт объясняет что образование малых деформаций не связано с формированием небольших по величине остаточных напряжений в теле детали. Точно также в случае возникновения больших остаточных деформаций детали нельзя утверждать что в ней сформировались большие остаточные напряжения. При больших остаточных деформациях эпюра остаточных напряжений как правило существенно отличается от эпюры начальных напряжений в сторону уменьшения. Причем величина остаточной деформации изгиба определяется не уровнем начальных напряжений а асимметрией их распределения относительно оси заготовки. К тому же определенной величине остаточной деформации изгиба может соответствовать множество законов распределения начальных напряжений в теле детали.
3. Причины и механизмы образования технологических остаточных деформаций.
Из описанного выше видно что процесс образования технологических остаточных деформаций состоит из двух этапов: образования деформаций после обработки и раскрепления детали либо в процессе обработки если закрепление заготовки допускает её деформацию; образования деформаций во время хранения транспортировки и эксплуатации изделия. Эти этапы существенно отличаются уровнем возникающих остаточных деформаций. Поэтому для того чтобы правильно выбрать рациональные пути обеспечения и сохранения заданной точности необходимо отличать причины образования остаточных деформаций от причин возникновения несимметричного (неравномерного) распределения по сечению детали начальных напряжений. Так причинами несимметричного распределения начальных напряжений являются:
– асимметричная обработка связанная с неравномерным удалением технологического припуска обработкой шпоночных пазов лысок местным упрочнением несимметричным нанесением покрытий а также правка упругопластическим изгибом и др.
– неравномерное протекание процессов релаксации остаточных напряжений и структурно-фазовых превращений в материале детали в процессе (например термической) обработки и после ее окончания (при хранении транспортировке и эксплуатации изделия).
Изложенное выше показывает что образование остаточных деформаций при проведении различных технологических операций и после их завершения происходит по – разному. Но в основе их образования лежат две основные причины:
Несимметричное распределение относительно оси детали технологических начальных напряжений.
Изменение в процессе обработки упругонапряженного состояния заготовки которое возникает перед обработкой при закреплении в станочных приспособлениях или во время обработки в результате действия технологической оснастки. Последнее происходит при закреплении заготовки таким способом который допускает её деформацию. Это характерно для случаев когда изогнутая ось заготовки совмещается с её номинальным положением или когда ось заготовки отклоняется от номинального положения но при вращении в поперечном сечении не образуются равные по величине знакопеременные напряжения.
Очевидно что первая причина является доминирующей и тем самым определяет величину и характер изменения пространственной погрешности. Однако может оказаться и так что обе причины достаточно сильно влияют на неравномерность изменения напряженного состояния заготовки. В этом случае значительно усложняется прогнозирование технологических остаточных деформаций. Кроме того может возникнуть несимметричное относительно оси детали распределение наследственных остаточных напряжений (см. рис. 2.2) которое как правило приводит к существенному изменению напряженного состояния детали при последующей обработке и как следствие к большим технологическим остаточным деформациям.
4. Механизм образования технологических остаточных деформаций.
Механизм образования остаточных деформаций и напряжений при механической обработке лезвийным инструментом заготовки нежесткого вала можно представить следующим образом [7 18].
Перед обработкой заготовку 1 (рис. 2.3) имеющую исходную остаточную деформацию устанавливают и закрепляют в подвижном трехопорном люнете 6 переднем 3 и заднем подпружиненном 4 центрах. Подпружиненный центр позволяет при обработке предотвратить потерю продольной устойчивости заготовки 2 и образование дополнительных напряжений в сечении детали. Потеря устойчивости возникает из-за невозможности удлинения заготовки при обработке с жестко фиксированным задним центром. Удлинение заготовки 1 происходит при её выпрямлении в результате совмещения подвижным люнетом 6 изогнутой оси с линией центров.
В процессе обработки заготовки 2 вместе с неравномерным припуском удаляются наследственные остаточные напряжения с поверхностного слоя. В результате формируется несимметричная относительно оси детали эпюра начальных напряжений о.
Рис.2.3. Схема формирования неуравновешенного напряженного состояния детали при механической обработке:
– заготовка в исходном положении перед обработкой; 2 – заготовка в процессе обработки; 3 4 – передний и задний подпружиненный центры соответственно; 5 – резец; 6 – кулачки подвижного люнета; 7 – поводок; эпюры напряжений: наследственные остаточные напряжения (a); напряжения от упругого изгиба заготовки люнетом (б); начальные напряжения вносимые процессом резания (в); начальные напряжения образованные из остаточных путем удаления припуска (г); напряжения от упругого изгиба заготовки после удаления припуска (д)
Снятие инструментом 5 неравномерного припуска по окружности поперечного сечения связано с вращением заготовки 2 относительно линии центров с некоторым эксцентриситетом e. Это приводит к тому что резец 5 снимает больший припуск t1 с выпуклой стороны и меньший t2 с вогнутой стороны заготовки.
Вместе с тем изменяется упругонапряженное состояние заготовки. Это происходит из-за того что вместе с припуском снимается часть напряжений sу которые возникают в поперечном сечении вследствие упругой деформации заготовки люнетом перемещающимся вдоль образующей вала в процессе обработки. В общем случае величина упругой деформации в текущем сечении определяется разностью f(z) - e(z). Кроме того сам процесс обработки вследствие изменения силы резания вносит во вновь образованный поверхностный слой несимметричную относительно оси детали эпюру начальных напряжений sн.
Важной особенностью рассматриваемой схемы обработки (рис. 2.3) является относительное снижение величины эксцентриситета e(z) вращения заготовки по длине обработки. Это обусловлено процессом непрерывного деформирования заготовки под воздействием изгибающего момента от начальных напряжений. Снижающаяся в результате этого исходная остаточная деформация f(z) приводит к уменьшению эксцентриситета e(z). Данное обстоятельство в свою очередь уменьшает величину изгибающего момента от начальных напряжений по длине заготовки. В результате происходит изменение формы кривой оси детали и смещение максимального значения остаточной деформации изгиба относительно ее середины.
Рассмотренные процессы нарушают равновесие напряженно-деформированного состояния заготовки которое отвечало исходной остаточной деформации и эпюре наследственных остаточных напряжений sо. При этом три эпюры в г д (рис.2.3) неуравновешенных напряжений образованные в поперечном сечении заготовки при разгрузке являются источниками деформаций которые формируют новое остаточное напряженно-деформированное состояние детали.
Перераспределение начальных напряжений (рис. 2.4 а и в) сопровождается изгибными f1 f2 и продольными D1 D2 деформациями (рис. 2.4 б и г). При этом необходимо отметить что изгибающие моменты обусловленные начальными напряжениями sн и sно могут деформировать деталь в разные стороны. Продольные силы обусловленные этими напряжений также могут быть направлены в противоположные стороны. Изменение эпюр начальных напряжений sн sно при их превращении в остаточные напряжения sо обусловлен двумя факторами: величиной интегральных характеристик Рн и их разностью в зонах выше и ниже оси заготовки.
Уменьшенная по площади эпюра напряжений sу от упругого изгиба заготовки (рис. 2.4 д) при разгрузке снимается полностью (без образования остаточных напряжений). Возникающая при этом деформация изгиба f3 (рис. 2.4 е) неизменно происходит в сторону исходной остаточной деформации .
По абсолютному значению деформация f3 меньше упругой деформации ( – e) на величину пропорциональную площади снятых вместе с припуском напряжений sу. Таким образом только за счет изменения упругонапряженного состояния заготовки исходная остаточная деформация уменьшается на величину df = – f3.
В результате деформаций происходящих при разгрузке деталь принимает новое равновесное напряженно-деформированное состояние которое характеризуется результирующими изгибной fост и продольной Dост остаточными деформациями а также результирующей эпюрой остаточных напряжений (рис. 2.4 ж).
Результирующие остаточные деформации fост и Dост представляют собой алгебраическую (или векторную) сумму составляющих
Рис. 2.4. Схемы формирования остаточного напряженно-деформированного состояния детали: уравновешивание начальных напряжений н сформированных процессом резания (а); остаточные деформации и напряжения возникающие после уравновешивания начальных напряжений н (б); уравновешивание начальных напряжений но образованных из наследственных остаточных напряжений (в); остаточные деформации и напряжения возникающие после уравновешивания начальных напряжений но (г); уравновешивание напряжений у от упругого изгиба заготовки после снятия припуска (д); остаточная деформация после уравновешивания напряжений у (е); результирующие остаточные деформации и напряжения (ж).
обусловленных перераспределением неуравновешенных напряжений sн sно sу т.е.
Таким образом при совместном действии неуравновешенных напряжений может происходить взаимная компенсация составляющих остаточных деформаций. Так в результате алгебраического сложения изгибных деформаций f1 и f2 (см. рис. 2.4 б и г) происходит снижение результирующей остаточной деформации изгиба fост. Взаимная компенсация зависит от тождественности знаков начальных напряжений sн sно и напряжений sу. Следовательно значения результирующих остаточных деформаций fост и Dост во многом определяются параметрами и sо напряженно-деформированного состояния заготовки которые сформированы в результате предшествующей обработки. Пооперационная зависимость параметров напряженно-деформированного состояния является проявлением технологической наследственности под которой понимается перенос (копирование) параметров и свойств обрабатываемой детали от предшествующих операций технологического процесса к последующим.
5. Влияние технологической наследственности на образование остаточных деформаций.
При обработке нежестких деталей наряду с геометрическим копированием погрешности формы которое обусловлено упругими деформациями элементов технологической системы имеет место копирование пространственной погрешности. До последнего времени причиной копирования пространственной погрешности считали остаточное напряженное состояние детали. Его причисляли к отрицательным факторам технологической наследственности снижающим точность нежёстких деталей. Действительно уровень остаточных напряжений в заготовке оказывает решающее влияние на величину технологических остаточных деформаций при удалении больших и неравномерных припусков[7]. Поэтому на уменьшение остаточных напряжений в типовых технологических процессах изготовления нежестких деталей тратились значительные усилия. Снижение уровня остаточных напряжений традиционно достигалось термической и вибрационной стабилизирующими операциями. Делалось это с единственной целью – уменьшить вероятность образования технологических остаточных деформаций вне зависимости от того благоприятные или неблагоприятные с точки зрения эксплуатационных свойств изделия сформированы остаточные напряжения. При этом термические (отпуск отжиг нормализация и т.п.) и упрочняющие (обкатывание алмазное выглаживание обдувка дробью и др.) операции по той же причине считали технологическими «барьерами» ослабляющими влияние напряженного состояния на точность детали. Однако многочисленные исследования [4 14] показали что в большинстве случаев напряженное состояние детали преодолевает технологический «барьер» в виде термической и упрочняющей обработки за счет увеличения пространственной погрешности. Этот факт доказывает что напряженное состояние нельзя считать фактором технологической наследственности оказывающим отрицательное действие на точность т.к. само по себе напряженное состояние не отражает наследственную взаимосвязь остаточных напряжений и деформаций. В этой связи представляется необходимым в качестве отрицательного фактора технологической наследственности использовать неравномерное изменение напряженного состояния детали. Это верно по своей сути т.к. равномерное изменение напряженного состояния детали не приводит к образованию пространственной погрешности и следовательно не оказывает влияние на точность обработки. Кроме того этот фактор в полной мере отражает взаимосвязь остаточных напряжений и деформаций и соответствует действительным причинам образования пространственной погрешности.
6 Основные пути повышения точности деталей.
Закономерности образования остаточных деформаций изгиба при механической обработке позволили проф. А.Н. Овсеенко сформулировать условия бездеформационной обработки [20]:
– При двухсторонней обработке необходимо чтобы в каждом сечении детали суммарный изгибающий момент от действия удаляемых вместе с припуском на обработку наследственных остаточных напряжений sо и вносимых процессом обработки дополнительных начальных напряжений sн с одной стороны был равен аналогичному суммарному изгибающему моменту возникающему при обработке противоположной стороны (рис. 2.5 а):
– при односторонней обработке детали необходимо чтобы изгибающие моменты от удаляемых вместе с припуском наследственных остаточных sо и вносимых обработкой начальных напряжений sн были равны (рис. 2.5 б);
– в случае отсутствия наследственных остаточных напряжений необходимо чтобы величина интегральной характеристики Рн эпюры начальных напряжений sн была как можно меньше (рис. 2.5 в).
Выявленные закономерности проявления технологической наследственности и условия бездеформационной обработки позволили разработать новые подходы к проектированию технологических процессов изготовления нежестких деталей. Суть их заключается в создании систем управления напряженным состоянием деталей [20]. Управление производится путём регулирования остаточных напряжений в заготовках с учетом последующей обработки распределения припуска на обработку с учетом остаточных напряжений в заготовке выбора рациональных методов режимов обработки и геометрии инструмента корректировки технологических баз и др. Это приводит к снижению пространственной погрешности вследствие уменьшения изгибающего момента обусловленного начальными напряжениями. Однако технологии изготовления нежестких
Рис. 2.5. Схемы изменения напряженного состояния в детали удовлетворяющего условиям бездеформационной обработки: а) при двухсторонней обработке; б) при односторонней обработке; в) при односторонней обработке в случае отсутствия наследственных остаточных напряжений.
Рис. 2.6. Эпюра распределения остаточных напряжений по поперечному сечению детали после правки упругопластическим изгибом (по А.П. Абрамову).
деталей основанные на управлении напряженным состоянием деталей реализуют экстенсивный путь достижения точности т.е. путем постепенного снижения пространственной погрешности от одной технологической операции к другой позволяют добиться минимальных остаточных деформаций.
Анализ рассмотренных выше путей достижения заданной точности показывает наличие противоречия между точностью и производительностью обработки. Указанные пути достижения требуемой точности базируются главным образом на пассивном ослаблении причин образования пространственной погрешности за счет потери производительности обработки и увеличения себестоимости изделия.
Учитывая значимость проблемы повышения точности нежестких деталей для машиностроения необходимы принципиально новые пути достижения и повышения точности основанные на нестандартных решениях. Достижение высокой точности с одновременным увеличением производительности обработки возможно только на основе совершенствования технологии и разработки прогрессивных методов снижения технологических остаточных деформаций. При этом особое внимание должно уделяться разработке комбинированных методов способных совмещать процесс снижения остаточных деформаций с удалением технологического припуска или с формированием необходимых физико-механических свойств материала в рамках одной технологической операции. Это направление включает в себя методы механической термической и электрохимической обработки в основе которых лежит управление напряженным состоянием детали. Управление напряженным состоянием осуществляется с целью создания изгибающего момента обусловленного начальными напряжениями противоположного знака по отношению к исходной остаточной деформации изгиба. Оно производится в процессе обработки детали путем изменения технологических или физических параметров. Эти методы являются технологическими «барьерами» на пути пространственной погрешности и позволяют изменить структуру технологических операций повышая тем самым производительность обработки.
Однако указанные методы не всегда приводят к желаемым результатам из-за значительной погрешности обработки связанной с удалением поверхностного слоя материала имеющего наследственные остаточные напряжения. В этом случае возникает необходимость проведения операций правки. Однако применение традиционной правки упругопластическим изгибом для деталей ответственного назначения не желательно т.к. она имеет ряд серьёзных недостатков. Во-первых правка изгибом трудно поддаётся контролю. Во-вторых она снижает усталостную прочность деталей и может привести к появлению микротрещин в поверхностном слое. В-третьих она формирует несимметричные в поперечном сечении детали остаточные напряжения (рис. 2.6). Это как правило приводит к образованию значительных остаточных деформаций изгиба как при последующей механической обработке так и в процессе эксплуатации изделия.
На завершающем этапе изготовления нежестких деталей наиболее эффективны методы снижения технологических остаточных деформаций при обработке поверхностным пластическим деформировании (ППД). Они позволяют снизить влияние технологической наследственности на конечные остаточные деформации благодаря тому что глубина распространения начальных напряжений от процесса ППД значительно превышает глубину активной части эпюры остаточных напряжений сформированных предшествующей обработкой. Правка ППД исключает появление трещин и создает в поверхностном слое остаточные напряжения сжатия улучшая тем самым такие эксплуатационные свойства деталей как усталостная прочность контактная выносливость и долговечность.
Изложенное выше показывает что полное снятие наследственных остаточных напряжений в большинстве случаев нецелесообразно по ряду причин. Во-первых после термообработки возникают дополнительные и как правило значительные остаточные деформации изгиба. Во-вторых последующая обработка заготовки имеющей остаточную деформацию приводит к образованию несимметричных начальных напряжений в поперечном сечении. В-третьих деталь вступает в период эксплуатации с минимальным уровнем остаточных напряжений что снижает эксплуатационные свойства изделия. Следовательно традиционно выполняемые термические вибрационные операции значительно снижающие уровень остаточных напряжений нельзя использовать в качестве технологических «барьеров» на пути отрицательного фактора технологической наследственности каким является неравномерное изменение напряженного состояния.
Анализ закономерностей проявления технологической наследственности при механической обработке показывает что технологии изготовления нежестких деталей необходимо проектировать с учетом уровня остаточных деформаций и напряжений. Кроме того необходимо использовать методы снижения технологических остаточных деформаций которые основаны на управлении напряженным состоянием деталей в процессе обработки и являются действительными технологическими «барьерами» на пути пространственной погрешности.
8. Постановка цели и задач дипломного проекта.
В связи со всем вышесказанным целью дипломного проекта является восстановление точности и обеспечение качества поверхностного слоя деталей правкой ППД. Поставленную цель необходимо достигать решением следующих задач:
)Проведение анализа способов процесса правки ППД.
)Исследование возможности управления упругонапряженным состоянием детали путем приложения поперечной силы;
)Разработка способа правки ППД основанного на изменении упругонапряженного состояния заготовки;
)Объяснение физической сущности способа.
)Разработка математической модели способа.
)Разработка технологии правки деталей поверхностным пластическим деформированием;
)Вывод результатов по проделанной работе.
Правка валов поверхностным пластическим деформированием.
1 Особенности методов правки поверхностным пластическим деформированием.
Первые методы правки ППД были разработаны около 30 лет тому назад. Они созданы благодаря знаниям причин и механизма образования технологических остаточных деформаций. В этих методах успешно реализована научная идея о превращении отрицательного фактора технологической наследственности каким является неравномерное изменение напряженного состояния детали в положительный фактор т. е. технологическая остаточная деформация может быть устранена в процессе обработки путем приложения к заготовке определенной системы нагрузок позволяющей получить такое неуравновешенное напряженное состояние детали которое при разгрузке вызовет деформацию изгиба обратного знака по отношению к исходной остаточной деформации. [11]
Правка ППД открыла новые технологические возможности методов поверхностного упрочнения (обкатывания роликом или шаром алмазного выглаживания чеканки и др.). Однако изначально правка ППД проводилась только с целью устранения технологических остаточных деформаций и не предусматривала отделочно-упрочняющую обработку всей поверхности детали. В этом случае локальная пластическая деформация поверхности с вогнутой стороны вала приводила либо к образованию вмятины от инструмента либо к возникновению неоднородности шероховатости и физико-механических свойств рабочей поверхности детали. Это обстоятельство существенно сдерживало широкое применение методов правки ППД в машиностроительном производстве особенно при изготовлении деталей ответственного назначения.
По мере раскрытия причин и закономерностей образования остаточных деформаций разрабатывались новые методы правки ППД.
2 Принципиальные технологические схемы управления напряженным состоянием деталей.
Решение задачи устранения остаточных деформаций правкой ППД имеет физический и технологический аспекты. Физический аспект заключается в выборе и обосновании законов распределения начальных напряжений в поперечном и продольном сечениях детали позволяющих устранить пространственную погрешность. Технологический – в технологическом обеспечении выбранных законов распределения начальных напряжений путём назначения условий обработки и параметров режима ППД.
Была разработана классификация всех способов правки ППД по признаку характеризующему технологическое управление напряженным состоянием детали [17]. Она включает в себя две основные принципиальные схемы технологического управления напряженным состоянием деталей типа валов при правке ППД (рис. 3.1).
Из рис. 3.1 видно что технологическое управление напряженным состоянием детали при обработке ППД с целью повышения её точности возможно двумя основными путями:
) изменением интенсивности пластической деформации в зоне контакта инструмента с деталью которая служит характеристикой режима поверхностного упрочнения и определяет распределение начальных напряжений в поверхностном слое. Следует отметить что интенсивность пластической деформации зависит от собственно деформации и протекающих при этом процессов теплообразования и структурно-фазовых превращений которые в значительной степени обусловлены структурным состоянием обрабатываемого материала;
) изменением упругонапряженного состояния детали которое формируется перед обработкой или в процессе обработки за счёт дополнительного в основном силового воздействия технологической
Рис. 3.1. Структурная схема основных путей управления напряженным состоянием детали при правке ППД.
оснастки на заготовку.
Условное разделение путей управления напряженным состоянием детали не отрицает их совмещения при проведении правки ППД. Более того совмещение этих направлений позволяет добиться высокой эффективности и производительности процесса правки ППД.
Представленные технологические схемы могут быть реализованы системами адаптивного и косвенного управления напряженным состоянием [11]. Адаптивное управление может производиться только в случае определения остаточных деформаций изгиба непосредственно в процессе обработки. Это возможно при закреплении заготовки таким способом который допускает её деформацию под воздействием изгибающих моментов обусловленных начальными напряжениями. В этом случае деформирование заготовки в процессе обработки является непрерывным процессом состоящим из множества чередующихся этапов нагружения и разгрузки. При этом текущее значение деформации изгиба можно определить либо отклонению обрабатываемой поверхности от базового положения либо по величине упругой силы действующей со стороны заготовки на опору. Косвенное управление отличается от адаптивного тем что осуществляется без обратной связи.
3. Анализ существующих методов правки деталей поверхностным пластическим деформированием.
Нами был проведен анализ существующих методов ППД и выявлены основные недостатки рассмотренных способов
В способе правки ППД с изменением приведенного радиуса кривизны [26] обкатывание вращающегося вала осуществляют роликом (рис. 3.2) выполненным асимметричным в поперечном сечении. Ролик имеет участок рабочей поверхности а с образующей в виде дуги бесконечно большого радиуса и участок б очерченный по радиусу. Участки рабочей поверхности с
Рис. 3.2. Конструкция ролика.
Рис. 3.3. Схема обработки вала
профилем большого и малого радиуса расположены диаметрально противоположно. Меньший радиус профиля рабочей поверхности ролика составляет 001 01 его диаметра. При этом диаметр ролика равен диаметру обрабатываемой детали. В процессе обработки (рис. 3.3) ролику сообщают движение подачи вдоль образующей вала при этом он поджимается к поверхности детали с постоянной силой Р. Перед обработкой ролики выставляют в таком положении чтобы плоскость деформации заготовки совпадала с осью симметрии роликов. При этом участок их рабочей поверхности с профилем малого радиуса находится в контакте с вогнутой а участок с профилем большого радиуса – с выпуклой стороной вала. В результате поверхностный слой детали с вогнутой стороны будет получать большую степень деформации чем с выпуклой стороны. При больших усилиях деформирования обработку производят несколькими роликами.
К недостаткам указанного способа следует отнести смещение относительно плоскости прогиба вала области большей степени наклепа что приводит к погрешности обработки. Кроме того при обработке поверхность детали не получает равномерного упрочнения.
В способе комбинированной обработки валов роликами с двумя разными профилями [22] правку ведут роликами с постоянным усилием от конца вала к наибольшему изгибу причем на каждом ролике (рис. 3.4) выполнены два профиля с радиусами R=(007—0l)d и r=(001—003) d где d — диаметр ролика.
При вращении вала с его вогнутой стороной будет всегда контактировать профиль малого радиуса а с выпуклой – профиль большого радиуса. В результате поверхностный слой детали с вогнутой стороны вала получает большую степень деформации чем с выпуклой стороны (рис. 3.5). Технология правки упрощается так как отпадает необходимость постоянно следить за изменяющимся прогибом вала ибо при достижении прямолинейности оси вала процесс правки прекращается автоматически. Это происходит потому что в контакт с обрабатываемой поверхностью вступают
Рис. 3.4. Конструкция ролика.
Рис. 3.5. Схема обработки вала.
оба профиля и обрабатывают цилиндрическую поверхность со всех сторон равномерно.
При обработке вала с прямолинейной осью интенсивность пластической деформации остается величиной постоянной по контуру поперечного сечения что позволяет обеспечить эффективное равномерное упрочнение цилиндрической поверхности вала.
Обработку вала можно вести одним или несколькими роликами которые равномерно расположены по окружности вала при условии что каждый ролик нагружается индивидуально упругим элементом например пружиной.
Указанный способ позволяет обеспечить процесс упрочнения всей обрабатываемой поверхности вала а также расширить диапазон размеров обрабатываемых валов.
К недостаткам способа следует отнести невысокую производительность вследствие переустановки обрабатываемой детали и невозможность исправления коробления валов с малыми исходными прогибами (что обычно имеет место на практике) поскольку степень деформации вогнутой и выпуклой стороны вала практически одинакова.
В способе правки валов роликом с изменением радиуса кривизны обработку осуществляют роликом содержащим опорный и правящий деформирующие элементы (рис. 3.6) причем радиус R рабочего профиля опорного элемента R выполнен большим чем радиус r рабочего профиля правящего элемента а диаметры опорного и правящего элемента выполнены равными. Радиусы рабочих профилей опорного и правящего элементов сопряжены прямолинейной образующей длина которой выбирается из условия: 0l(1..:2)(R-r).
В процессе обработки (рис. 3.7) валу сообщают вращение а ролику - движение подачи вдоль образующей вала с постоянной силой прижатия. При этом с вогнутой поверхностью вала всегда будет контактировать профиль малого радиуса а с выпуклой - профиль большого радиуса.
Рис. 3.6. Конструкция ролика.
Рис. 3.7. Схема обработки вала.
Одновременно с накатыванием поверхности вала идет процесс его правки строго в плоскости изгиба. Предложенным роликом можно обрабатывать валы с образующей сложной геометрической формы причем вал в поперечном сечении может быть некруглым.
К преимуществам способа следует отнести: повышение производительности обработки т.к. деталь не требуется переустанавливать в процессе обработки; повышение качества обработки т.к. опорный и правящий элементы роликов не разделены канавкой; резкое повышение эффективности правки т.к. разность между r и R ничем не ограничивается; расширение технологических возможностей в результате того что ролики имеют сложную конфигурацию- это позволяет получать разные глубины наклепа при использовании одного ролика.
Недостатками указанного способа являются невозможность исправления малых по величине остаточных деформаций смещение области наклепа относительно плоскости деформации за счет проскальзывания а также сложность изготовления ролика.
В способе правки ППД реализованном устройством содержащим опорный и правящий ролики [24] обработку ведут головкой содержащей вилку со смонтированными в ней с возможностью вращения опорным и правящим дисками.
При этом радиус рабочего профиля опорного диска больше радиуса рабочего профиля правящего диска а касательная к рабочим профилям обоих дисков параллельна оси их вращения. В процессе обработки (рис. 3.8) детали 1 сообщают вращение а головку нагружают постоянным усилием P и сообщают ему осевую подачу S до тех пор пока она не переместится до сечения вала с наибольшим прогибом (из положения I в положение II). Останавливают процесс переворачивают головку на 180° вокруг оси хвостовика 4 и продолжают процесс перемещая головку из положения I в положение III. При вращении детали 1 в контакт с ее вогнутой поверхностью всегда вступает только правящий диск 2 а с выпуклой поверхностью
Рис. 3.8. Схема обработки вала.
только опорный диск 3. Так как они имеют различные диаметры и радиусы профилей степень пластической деформации при постоянном усилии на вогнутой и выпуклой поверхностях вала различна. В связи с этим протекает процесс правки который автоматически прекращается при достижении прямолинейности оси вала и продолжается обычное накатывание поверхности.
Предложенной головкой можно обрабатывать валы с прямолинейной образующей например цилиндрические или конические причем в поперечном сечении вал может быть некруглым например эллипсным. Обработку вала можно вести одной или несколькими головками которые располагают вокруг вала. В этом случае разгружаются подшипники шпинделя.
К недостаткам следует отнести невысокую производительность вследствие переустановки головки для правки.
В способе комбинированной обработки цилиндрических валов с базированием в подвижном люнете [27] при котором осуществляют поверхностное пластическое деформирование вращающегося вала с одновременной правкой его деформирующим инструментом на вогнутой поверхности вала осуществляют более интенсивную пластическую деформацию чем на выпуклой поверхности (рис. 3.9). Это достигается за счет того что за один оборот вала происходитизменение силовых параметров способа (натяга или усилия накатывания) от максимума до минимума а это сказывается на изменение интенсивности пластической деформации сильнее по сравнению с изменением профильного радиуса ролика при постоянном усилии накатывания. Перед обработкой один конец вала закрепляют с возможностью покачивания в любой плоскости а другой конец вала устанавливают в подвижный люнет за которым располагают деформирующий инструмент причем инструменту и люнету сообщают движение подачи вдоль оси вала в одном направлении. При этом подача инструмента и подвижного люнета могут быть равны или отличаться.
Рис. 3.9 Схема обработки вала.
В данном способе можно использовать самый разнообразный инструмент для ППД который охватывает очень широкий диапазон обрабатываемых деталей с точки зрения их размеров твердости материала и др. свойств. Например при правке нежестких валов когда большие усилия недопустимы обработку можно вести центробежным упрочнителем. При обработке закаленных валов использовать выглаживатели и т.д.
Недостатком указанного способа является невозможность обработки всего вала целиком.
В способе правки валов [28] обработку осуществляют роликом содержащим три накатных элемента. Из которых два крайних выполнены в виде соосных дисков с одинаковой жесткостью равного диаметра со скругленным профилем а средний - в виде диска с прямолинейной образующей. Средний накатной элемент выполнен с жесткостью равной или меньшей жесткости двух крайних накатных элементов при одинаковом диаметре всех накатных элементов.
Приспособление с роликом устанавливают в начале обрабатываемой поверхности и создают усилие накатывания Р например пружиной. Детали 3 сообщают вращение ролику - осевую подачу S. Ролик вращаясь от детали производит ППД ее поверхности. При обкатывании обрабатываемой детали ролик последовательно занимает относительно нее три характерных положения (рис. 3.10). При этом усилие накатывания будет по-разному распределяться на накатные элементы ролика. При обкатывании вогнутой поверхности вала работают диски 1 и 2 осуществляя интенсивное упрочнение поверхности.
При обработке выпуклой поверхности в связи с упругостью среднего элемента интенсивность ППД резко уменьшается. За счет этой разницы ППД идет процесс правки. Предлагаемыми роликами можно обрабатывать валы с прямолинейной образующей например цилиндрические или конические причем в поперечном сечении вал может быть не круглым а например эллипсным и т.п. Обработку вала можно вести одним или несколькими
Рис. 3.10. Схема обработки вала.
Рис. 3.11. Схема обработки вала.
роликами которые располагают по окружности вала. При этом каждый ролик должен нагружаться упругим элементом (например пружиной) и иметь возможность самоустановки по образующей детали.
Недостатком данного способа является невозможность исправления малых исходных прогибов вала.
В способе правки ППД [29] обработку вращающегося вала (рис. 3.11) осуществляют двумя диаметрально расположенными элементами - деформирующим 2 и опорным 3 которым сообщают осевую подачу относительно вала накатывание идет с переменным по окружности вала усилием. Рабочий профиль деформирующего элемента - накатной ролик 2 выполнен радиусным его радиус обеспечивает эффективную поверхностную пластическую деформацию вала 1. Опорный ролик 3 имеет форму цилиндра с прямолинейной образующей длину которой выбирают малой чтобы ролик 3 не осуществлял ППД поверхности вала 1. Обработку осуществляют устройством в котором деформирующий элемент 2 и опорный ролик 3 связаны между собой упругим элементом и системой рычагов с передаточным отношением больше единицы. Рычаги связаны тягой выполненной регулируемой по длине также как плечи рычагов что расширяет технологические возможности способа. Таким образом обеспечивается автоматическое регулирование усилия накатывания при вращении вала. В результате деформирующий элемент 2 воздействуют на вогнутую поверхность вала с большим усилием чем на выпуклую. Таким образом поверхностный слой детали с вогнутой стороны вала получает большую степень деформации чем с выпуклой стороны. При достижении прямолинейности оси вала процесс правки автоматически прекращается.
Преимуществами способа является уменьшение трудоемкости обработки за счет автоматического управления усилием деформирования и использования в качестве деформирующих элементов как роликов так алмазных выглаживателей.
Способ рекомендуется использовать на автоматических станках и в автоматических линиях так как не требуется дополнительных технических средств для слежения за процессом правки.
К недостаткам способа следует отнести сложность реализации силы прижатия инструмента и погрешность обработки возникающей вследствие неоднородности степени пластической деформации по контуру детали.
Во всех рассмотренных выше способах отсутствие каких-либо расчетных зависимостей между исходным прогибом оси вала и степенью деформации (усилием деформирования) снижает технологические возможности способов вследствие того что недостаточная степень деформации вогнутой стороны вала может привести к незначительному устранению коробления детали а большая степень деформации - к перегибу оси вала в противоположную сторону относительно ее номинального положения. Но основным недостатком всех вышеуказанных методов является их низкая технологичность что является барьером на пути их широкого внедрения в производство.
В этой связи актуальной является разработка методов ППД которые обеспечивают устранение пространственной погрешности нежестких деталей типа валов путем управления их напряженным состоянием.
Поэтому оптимальным из рассмотренных способов на мой взгляд является способ правки ППД [23] с предварительным изгибом заготовки изгибающими моментами (рис. 3.12) реализующий тем самым второе направление напряженным состоянием заготовки.
4. Особенности формирования предварительного упругонапряженного состояния заготовки.
Следует отметить что определение «предварительное» по отношению к упругонапряженному состоянию носит условный характер т.к. упругое деформирование заготовки может осуществляться как перед обработкой так
Рис. 3.12. Схема обработки вала.
и непосредственно в процессе обработки.
При правке ППД можно реализовать несколько способов упругого деформирования вращающейся и неподвижной детали.
Упругое деформирование заготовки по схеме чистого изгиба осуществляется в направлении противоположном исходной остаточной деформации (рис. 3.13 а) путем приложения к её концам внешних изгибающих моментов со стороны специальных планшайб. Величина упругой деформации в середине заготовки (рис. 3.13 б) в общем случае составляет ( + ) где – деформация перегиба отсчитываемая от линии центров. В результате в крайних волокнах с исходных выпуклой и вогнутой сторон детали из равнопрочной стали формируются равные максимальные напряжения
«Заневоливание» детали в таком положении планшайбами позволяет сохранить полученное упругонапряженное состояние неизменным как при вращении детали (рис. 3.13 в) так и в случае когда деталь остаётся неподвижной (рис. 3.13 б) в процессе обработки. Но анализ экспериментальных данных правки ППД проведенной устройством в котором изгиб заготовки осуществлялся путем приложения изгибающих моментов показал что при правке возникает погрешность обработки которая обусловлена негативным влиянием радиального биения заготовки на глубину внедрения инструмента. Радиальное биение происходит при планетарном вращении детали вокруг линии центров.
Радиального биения не возникает в случае когда упругое деформирование детали осуществляется путем приложением поперечной силы осуществляется с помощью дополнительных опор в виде разного рода люнетов. При совмещении дополнительными опорами изогнутой оси
Рис. 3.13. Схемы создания предварительного упругонапряженного состояния заготовки путем приложения изгибающих моментов: исходная остаточная деформация заготовки (а); напряжения в поперечном сечении от упругого изгиба детали (б); напряжения в поперечном сечении при вращении детали (в).
Рис. 3.14. Схемы создания предварительного упругонапряженного состояния заготовки путем приложения поперечной силы: а) при совмещении с линией центров; б) при >; в) при =; г) при .
Рис. 3.15. Прогибы возникающие при вращении вала.
а) исходное положение; б) поворот на 0°; в) поворот на 90°; г) поворот на 180°.
заготовки с линией центров (рис. 3.14а) величина максимальных напряжений будет изменяться
При > максимальные напряжения с исходной выпуклой стороны заготовки (рис.3.14 б) изменяются
Прогибы вала возникающие в данном случае показаны на рис. 3.15.
При = максимальные напряжения с исходной выпуклой стороны заготовки (рис.3.14 в) изменяются
При максимальные напряжения с исходной выпуклой стороны заготовки (рис.3.13 б) изменяются
Способ правки деталей с одновременной отделочно-упрочняющей обработкой поверхности.
Нами был разработан способ для правки деталей с одновременной отделочно-упрчняющей обработкой поверхности и подана заявка на изобретение [25]. Разработанный способ правки основан на изменении предварительного упругодеформированного состояния заготовки в процессе обработки при постоянных режимах ППД.
Способ отличается от рассмотренного ранее способа тем что предварительное деформирование осуществляется путем приложения поперечной силы а не изгибающих моментов.
Физическая сущность исправления технологической остаточной деформации изгиба разработанным способом правки ППД заключается в создании предварительных напряжений в заготовке в процессе её обработки путем упругого изгиба сосредоточенной силой в направлении упрочняющего инструмента и изменении упругонапряженного состояния при поверхностном деформировании осуществляемом на постоянных параметрах режима ППД. Изменение предварительного упругонапряженного состояния позволяет при разгрузке уменьшить упругую отдачу детали и устранить таким образом исходную остаточную деформацию.
Предварительное упругое деформирование заготовки осуществляют путем приложения поперечной силы позволяющей в каждом поперечном сечении обрабатываемого участка выполнить условие (4.1)
где - общая деформация заготовки перед обработкой отсчитываемая от линия центров в текущем поперечном сечении z;
- максимальная исходная деформация заготовки в середине детали полученная до правки;
- изгибная деформация создаваемая инструментом перед обработкой отсчитываемая от оси заготовки.
Обработку ППД производят только на некотором участке заготовки расположенном симметрично относительно ее середины (Рис.4.1).
Исправление вала объясняется следующим.
При вращении вал испытывает знакопеременное нагружение которое обусловлено исходным прогибом детали. Причем при повороте исходной вогнутой стороны заготовки к деформирующему инструменту в ее поверхностном слое всегда возникает упругая деформация растяжения большая по величине чем при повороте исходной выпуклой стороны (Рис.3.14 г). Эта деформация алгебраически складывается с упруго-пластической деформацией которая развивается в поверхностном слое под воздействием инструмента в процессе ППД. В результате сложения деформаций как в упругой области так и в области пластического течения материала интенсивность пластической деформации с вогнутой стороны выше чем с выпуклой стороны. Это приводит к увеличению уровня и глубины распространения начальных напряжений с исходной вогнутой стороны и уменьшению – с исходной выпуклой стороны заготовки. Таким образом в поверхностном слое формируется несимметричная относительно оси заготовки эпюра начальных напряжений которая после обработки и раскрепления детали вызывает в поперечном сечении обработанного участка изгибающий момент устраняющий исходную остаточную деформацию.
Для данного метода было разработано устройство для правки валов с предварительным изгибом заготовки (Рис.4.2 4.3). Оно включает в себя закаленный шар 8 диаметром 87 мм и опорный элемент в виде призмы 6 с двумя сглаживающими роликами 7. Призма с опорными роликами крепится в напрявляющих суппорта и имеет возможность перемещаться с помощью винтовой пары 4 а обкатывающее устройство в резцедержателе токарного станка и в процессе поверхностного деформирования имеют возможность перемещаются вдоль образующей заготовки.
Сам процесс правки осуществляется следующим образом.
Обрабатываемый вал 1 устанавливают в переднем 2 и заднем 3 центрах токарного станка в положении выпуклостью к деформирующему инструменту 8. С вогнутой стороны вала 1 прикладывают поперечную силу Ру со стороны опорного элемента путем перемещения каретки 5 посредством винтовой пары 4 (рис.4.4). Таким образом осуществляют предварительное упругое деформирование вала 1 на величину fобщ в плоскости коробления изделия 1 в направлении деформирующего инструмента 8. В таком положении механизм предварительного нагружения обрабатываемой детали 1 и обкатывающее устройство перемещают вдоль образующей детали 1 к началу обрабатываемого участка вала 1. К детали 1 подводят деформирующий инструмент 8 и устанавливают давление в гидроцилиндре 9 (рис. 4.2). При этом деформирующий инструмент 8 поджимается к обрабатываемой поверхности детали 1 с величиной рабочего усилия Р которое выбирают из условия осуществления оптимального режима пластического деформирования. Включают привод вращения изделия 1 а обкатывающему устройству и механизму предварительного нагружения обрабатываемой детали 1 сообщают продольное движение подачи. Деталь 1 в процессе обработки вращается вокруг своей центральной оси
Рис.4.1. Схема деформации вала.
Рис.4.2. Схема устройства для обработки.
Рис. 4.3. Внешний вид устройства.
Рис.4.4. Схема изгиба заготовки перед обработкой.
Рис. 4.5. Схема обработки.
смещенной относительно линии центров 2 3 в каждом поперечном сечении обрабатываемого участка на величину fобщ (рис. 4.5) детали поперечной силой на определенную величину по всему обрабатываемому участку.
Таким образом производят обкатку упругодеформированного вала на участке длиной l который симметрично расположен относительно середины детали (L2) где L – длина вала.
Разработанный способ реализует косвенное управление напряженным состоянием при правке ППД что делает его более технологичным по сравнению с другими методами правки ППД и следовательно более адаптированным к производственным условиям.
1. Разработка математической модели способа правки.
В процессе вращения деталь испытывает знакопеременное нагружение со стороны опорного элемента. Это объясняется изначальным короблением и предварительным изгибом заготовки. Чтобы лучше понимать суть происходящих изменений нужно рассмотреть несколько положений вала в процессе обработки.
Упругий изгиб создается приложением поперечной силы вызывающей необходимую деформацию в месте приложения силы со стороны опорного элемента который перемещается вдоль оси в процессе обработки. Сама деталь вращается в процессе обработки.
При вращении детали (рис.4.6 4.7) в поверхностном слое под инструментом будут развиваться упругие напряжения значение которых в можно выразить формулами
Рис. 4.6. Положение вала при повороте исходной выпуклой стороны к индентору.
Рис. 4.7. Положение вала при повороте исходной вогнутой стороны к индентору.
Рис. 4.8. Упругие напряжения возникающие от усилия изгиба.
где Е – модуль упругости I рода материала;
R – радиус заготовки;
- величина исходной деформации в центральном сечении;
- текущая исходная деформация детали в сечении с координатой e где e – расстояние от края вала до обрабатываемого участка;
L – общая длина заготовки;
– угол поворота детали от исходного положения;
- коэффициент изгиба.
Тем самым в сечении детали будут возникать упругие напряжения которые представлены на рис. 4.8.
Также можно рассчитать и построить эпюру возникающих напряжений в крайних волокнах вдоль оси заготовки (рис. 4.9).
Для начала необходимо рассчитать исходную деформацию в начале и конце обрабатываемого участка. Для этого можно воспользоваться формулой кривой оси заготовки аппроксимируемой параболой второй степени:
Процесс образования остаточных деформаций и напряжений можно описать основываясь на закон сложения напряжений и деформаций. Под воздействием внешней изгибающей силы приложенной к заготовке и инструмента в процессе ППД в поверхностном слое формируются напряжения под нагрузкой т.е. полные напряжения. Эпюра полных напряжений может быть предсказана на основании известной диаграммы растяжения (сжатия) для данного материала которая может быть аппроксимирована двойной линейной функцией (рис. 4.10) в области равномерной деформации.
Рис. 4.9. Эпюры распределения упругих напряжений вдоль образующей заготовки.
Рис. 4.10. Напряжения от процесса ППД.
Рис. 4.11. Распределение деформации и напряжений от процесса ППД по глубине.
На основании представления о том что эпюра напряжений под нагрузкой в поверхностном слое воспроизводит в определенном масштабе диаграмму деформирования материала и связана прямой зависимостью с эпюрой деформаций определим напряженно-деформированное состояние материала поверхностного слоя под воздействием инструмента в процессе ППД (рис. 4.11).
Для построения эпюры деформаций и напряжений возникающих от процесса ППД необходимо рассчитать ряд параметров.
ППД необходимо проводить с деформацией близкой к равномерной допустимой при которой не происходит разрушения материала поверхностного слоя детали[10]. Эту деформацию определяют по пластической твердости НД [9]:
где НД – пластическая твердость определяемая по ГОСТ 18835-73 или ориентировочно по эмпирической зависимости НД=0486НВ1124 [16].
Расчет силы прижатия инструмента будем производить по методике изожженной у Черненко О. С. [30].
Для начала рассчитаем коэффициент стеснения:
с = 257 – 07sinφ (4.5)
где sinφ – полный угол внедрения индентора (рис.4.12) равный .
После определяем давление текучести в контакте:
где - предел текучести.
Число циклов нагружения поверхности в результате обработки можно рассчитать по формуле:
S – продольная подача.
Рис. 4.12. Схема внедрения сферического индентора.
Также необходимо определить пластическую составляющую полной деформации:
где - упругая составляющая деформации равная:
где q – среднее давление в контакте которое в данном случае можно определить как 08НВ.
В результате повторного нагружения поверхности в процессе обработки механические свойства изменяются. Это изменение можно выразить через коэффициент цикличности:
где КН – эмпирический коэффициент нагружения показывающий долю упрочнения материала зависящую от режима пластического деформирования равен (032 046) [30];
t – коэффициента зависящие от материала;
- коэффициент упрочнения зависящий от способности материала к упрочнению.
где еК – истинная (логарифмическая) деформация при растяжении которая рассчитывается по формуле:
где - относительное сужение образца.
Также представляет собой касательный модель который изменяется по мере упрочнения:
Теперь определяем среднее давление в контакте инструмента с деталью:
Определим силу которую необходимо приложить к инструменту для того чтобы получить равномерную допустимую деформацию:
Определение глубины пластически деформированного слоя будем вести по формуле:
Приведенный радиус контакта рассчитывается следующим образом:
где -большая и малая полуоси остаточной вмятины инструмента;
- радиус инструмента.
Из геометрической связи углов и глубины деформированного слоя можно рассчитать глубину упругодеформированного слоя:
Граница разделения упругой и упруго – пластической составляющих деформаций обусловлена равенством:
Определим предел текучести материала увеличенный в результате упрочнения при повторных нагружениях индентора в процессе ППД:
Деформация текучести которая соответствует :
Напряжения на поверхности рассчитываем по формуле
Определим изменение глубины деформированного слоя происходящего вследствие наложения деформаций от упругого изгиба заготовки на деформацию от силового воздействия инструмента.
Из рис. 4.13 определяем:
где * - значение упругих напряжений на уровне aS равное:
Подставив (4.24) в (4.23) и преобразовав получаем:
где где - максимальное значение деформации заготовки вызванное действием внешних изгибающих моментов равное .
Алгебраическое сложение деформаций от процесса ППД и упругого изгиба заготовки позволит определить деформации напряжения глубину пластически деформированного слоя с исходной выпуклой и вогнутой сторон заготовки (рис. 4.14). Для удобства расчетов разобьем суммарную эпюру напряжений на 3 части как показано на рис. 4.14.
Для того чтобы рассчитать изгибающий момент необходимо рассчитать интегральную характеристику эпюры напряжений которой является площадь эпюры:
Рис. 4.13. Схема распространения деформаций в теле детали при обработке ППД.
Рис. 4.14. Суммарные деформации и напряжения от процесса ППД и упругого изгиба.
Элементарный изгибающий момент относительно центра сечения:
где - радиус от центра сечения 0 до центра тяжести эпюры напряжений;
- плечо относительно плоскости XZ
- плечо относительно плоскости
Интегрируя выражение (4.27) получим изгибающий момент в поперечном сечении:
Согласно рассчитанным значениям напряжений строим диаграмму (рис. 4.14) и рассчитываем площади.
Для начала рассчитаем интегральные характеристики части эпюры №1 (рис.4.14 1)
Определяем амплитуду изменения площади эпюры начальных напряжений для исходной выпуклой стороны:
Рассчитаем е10 – среднее расстояние от поверхности детали до центра тяжести эпюры и е1А – амплитудное расстояние от поверхности детали до центра тяжести эпюры для исходного выпуклого волокна.
В таком случае расстояние от оси детали до центра тяжести части эпюры №1:
Примем следующие коэффициенты:
Подставляя рассчитанные значения в формулу (4.27) получаем выражение для момента от первой части эпюры:
Далее рассчитаем интегральные характеристики для второй части эпюры:
Тогда элементарный момент от второй части эпюры будет иметь вид:
Аналогично составляя формулу для момента от третьей части эпюры получаем:
Просуммировав все три части эпюры и проинтегрировав получаем формулу изгибающего момента в сечении:
2. Определение допустимой остаточной деформации изгиба заготовки.
Технологические возможности метода ограничены тем обстоятельством что при большой величине деформации от воздействия поперечной силы в крайних сечениях обрабатываемого участка вала может начаться пластическое течение поверхностного слоя материала.
Следовательно было не обходимо просчитать максимальную величину исходной деформации которую можно исправить.
К валу который условно считается прямолинейным в сечении с координатой е соответствующем крайнему сечению обрабатываемого участка прикладывается поперечная сила P (рис. 4.21).
Силе P соответствует величина изгиба равная
где - исходная остаточная деформация в середине заготовки;
– коэффициент изгиба выбирающийся из условия оптимальных режимов обработки.
В результате приложения силы в поперечном сечении е возникает изгибающий момент равный по величине:
где L – общая длина заготовки;
е – расстояние от края заготовки до обрабатываемого участка.
В результате возникновения изгибающего момента в поперечном сечении в крайних волокнах возникают напряжения (рис. 4.22) которые по своей величине не должна превышать предела текучести:
где R – радиус заготовки;
I – момент инерции сечения.
Из этого условия получаем что максимально допустимый изгибающий момент равен:
Подставив в формулу (4.53) выражение (4.51) мы получим выражение для допустимой величины деформирующей силы:
Зная величину допустимой силы можно рассчитать деформацию которую эта сила вызывает в приложенном сечении. Т.е. мы имеем возможность рассчитать величину максимально допустимой деформации вала.
Рис. 4.24. Форма оси вала в момент прогиба при положении люнета
в начале обрабатываемого участка.
Рис. 4.25. Упругие напряжения возникающие в теле детали.
где E – модуль упругости I рода материала детали.
Из выражений (4.54) и (4.55) следует:
Так же известно что
Подставив (4.58) и (4.50) в (4.57) можно рассчитать величину предельно допустимой исходной деформации которую можно исправить данным методом.
3. Технология и методика правки деталей с одновременной отделочно-упрочняющей обработкой поверхности.
Технология правки нежестких валов методом поверхностного пластического деформирования включает в себя следующие операции:
)Определение плоскости деформации детали (рис. 4.26.).
На данной стадии технологического процесса находится максимальный исходный прогиб заготовки определяется плоскость деформации детали и проводится измерение радиального биения в пяти точках по длине вала. Данные измерения проводятся с помощью индикатора часового типа ИЧ-10. Натяг ножки индикатора к поверхности вала должен быть в пределах 2 3 мм. Пять точек для измерения радиального биения для образцов длиной 500 мм брались исходя из следующего: первая и пятая точки находились по краям заготовки приблизительно 15 мм с каждого края; вторая и четвертая точки рассчитывались как среднее значение между краевыми точками и серединой образца (расстояние от края до такой точки 1325 мм); 3 точка бралась точно по середине заготовки 250 мм.
Пять точек для измерения радиального биения для образцов длиной 400 мм определялись аналогично образцам 500 мм отличия лишь в числовых значениях. Так средняя третья точка находилась на расстоянии 200 мм от края заготовки; первая и пятая точки также как и для образцов длиной 500 мм отсчитывались по 15 мм с края детали. Вторая и четвертая точки брались как середина между 1 и 3 точками и 3 и 5 точками (получились на расстоянии 1075 мм от края вала).
) Расчет остаточной деформации изгиба и построение графика упругой линии заготовки с определением максимального прогиба оси заготовки (рис. 4.27).
Здесь по полученным на предыдущей стадии результатам измерения радиального биения рассчитывается остаточная деформация изгиба вала строится график по рассчитанной остаточной деформации и по графику методом отсекания краевых точек определяется максимальный прогиб оси заготовки. Точность расчета максимального прогиба оси заготовки 0005 мм.
) Деформирование заготовки на расчетную величину максимального прогиба fобщ (рис. 4.28).
Для проведения данной операции необходимо специальное приспособление для деформирования и магнитная стойка с индикатором часового типа ИЧ-10 для отслеживания величины . Сам процесс деформирования осуществляется специальным приспособлением на величину которая получена либо по графику (если коэффициент изгиба = 0) либо по расчетам с введением коэффициента изгиба
Рис. 4.26. Определение плоскости деформации детали.
Рис 4.27. Расчет остаточной деформации изгиба.
Рис. 4.28. Деформирование заготовки на величину максимального прогиба.
Рис. 4.29. Отделочно-упрочняющая обработка.
Рис. 4.30. Контроль качества обработанной поверхности.
Рис. 4.31. Расчет остаточной деформации изгиба.
Обеспечение упругой деформации должно производиться с точностью 001 мм.
) Отделочно-упрочняющая обработка (рис. 4.29).
На данной стадии проведения эксперимента проводится правка с одновременной отделочно-упрочняющей обработкой поверхности уже деформированной на величину заготовки. Правка осуществляется обкатывающим устройством закрепленным в резцедержателе токарного станка имеющего возможность перемещаться вдоль образующей заготовки с определенной подачей и специальным приспособлением для деформирования выполненного в виде призмы с опорными роликами которое закреплено на суппорте токарного станка и перемещающегося в процессе правки вместе с обкатывающим устройством. Деформирующие ролики призмы должны быть симметрично расположены относительно линии центров и шарика обкатывающего устройства. Призма с роликами поджимает заготовку с противоположной относительно обкатывающего устройства стороны.
) Следующей операция технологического процесса является контроль качества (рис. 4.30).
Здесь как и на первой стадии проводится измерение радиального биения в пяти точках по длине вала. Определяется где находится плоскость деформации т.е. произошло ли исправление вала или нет.
) Расчет остаточной деформации изгиба и построение графика упругой линии детали после обработки ППД (рис. 4.31).
Данная операция является последней стадией. Здесь проводится расчет остаточной деформации построение графика упругой линии по этим расчетам определение остаточного прогиба оси детали с точностью 0005 мм и расчет степени исправления W с точностью 1%. Таким образом результаты полученные на данной стадии являются основным показателем того как и на сколько произошло исправление вала.
Экономическое обоснование проекта.
В дипломном проекте поставлена цель восстановления точности и обеспечения качества поверхностного слоя деталей правкой ППД.
В основном разделе дипломного проекта после проведенных научно – исследовательских работ был разработан метод для правки поверхностным пластическим деформированием нежестких деталей представляющий собой альтернативу правке упруго-пластическим изгибом которую применяют на производстве. В экономическом разделе будет произведено экономическое обоснование дипломного проекта. Расчет затрат будет производиться по заводской и проектируемой технологиям. Внедрение разработанного способа упрочнения позволит повысить качество изготавливаемых изделий.
Исходные данные не требующие расчета представлены в таблице 5.1.
Условное обозначение
Коэффициент транспортно-заготовительных расходов
Коэффициент учитывающий затраты на монтаж (демонтаж) оборудования
Коэффициент доплат к основной заработной плате
Продолжение табл. 5.1.
Коэффициент отчислений на дополнительную заработную плату
Коэффициент отчислений на социальные нужды
Коэффициент цеховых расходов
Коэффициент заводских расходов
Коэффициент внепроизводственных расходов
Коэффициент учитывающий прибыль предприятия
Норма амортизационных отчислений на оборудование
Норма амортизационных отчислений на площадь
Стоимость эксплуатации площадей
Стоимость приобретения производственных площадей
Стоимость электроэнергии
Площадь занимаемая оборудованием
Часовая тарифная ставка
Нормативный коэффициент экономической эффективности дополнительных капитальных вложений
Срок службы изделия по базовому проектному варианту
Балансовая стоимость оборудования:
CPU INTEL CELERON 2300
монитор 17” CTX VL500
станок токарно-винторезный 1К625ДГ
контрольно-измерительное приспособление
печь СШО – 10.1010М1
2. Расчёт нормы времени на правку изделия.
tШТ = tМАШ + tВСП + tОБСЛ + tОТЛ + tП-З (5.1)
где tМАШ – машинное время;
tВСП – вспомогательное время tВСП = 10% от tМАШ;
tОБСЛ – время на обслуживание оборудования и рабочего места tОБСЛ = 10% от tМАШ;
tОТЛ – время на личный отдых рабочего tОТЛ = 3% от tМАШ;
tП-З– время подготовительно-заключительное tП-З= 2% от tМАШ.
Расчет произведем в табличной форме.
Расчет нормы времени на правку изделия. Таблица 5.2
Расчет режимов изгиба
Продолжение табл. 5.2.
Расчет режимов на ЭВМ
3. Расчёт фонда времени работы оборудования.
3.1. Расчет номинального годового фонда времени работы оборудования.
FН = (ДРТСМ _ ДПТП)С (5.2)
где ДР – количество рабочих дней в году;
ТСМ – продолжительность смены (8 часов);
ТП – количество часов на которые сокращается смена в предпраздничные дни;
ДП – количество предпраздничных дней;
С – количество смен.
FН = (2788 – 81)1 = 2216 часов
3.2. Расчет эффективного фонда времени работы оборудования.
FЭ = FН(1 – В100) (5.3)
где В – плановые потери рабочего времени (7%).
FЭ = 2216(1 – 7100) = 2061 час.
4. Расчет годовой программы правки изделий.
где FЭ – годовой эффективный фонд времени работы оборудования;
tШТ – штучная норма времени.
ПГБАЗ = 2061161= 1280 шт.
ПГПР = 2061073 = 28233 шт.
Принимаем ПГ = 1280 шт.
5. Расчёт технологической себестоимости затрат на правку изделия по базовому и проектному варианту.
5.1. Расчет затрат на оплату труда
а) заработная плата основная:
ЗОСН = СЧtШТКД (5.5)
где СЧ – часовая тарифная ставка;
tШТ – штучное время;
КД – коэффициент доплат к основной зплате.
ЗОСНБ = 1919161188 = 5808 руб.
ЗОСНПР = 1919073188 = 263 руб.
б) заработная плата дополнительная:
ЗДОП = ЗОСНКДОП (5.6)
где КДОП – коэффициент отчислений на дополнительную зплату.
ЗДОПБ = 5808018 = 105 руб.
ЗДОППР= 263018 = 47 руб.
в) фонд оплаты труда:
Ф.О.Т = ЗОСН + ЗДОП (5.7)
Ф.О.ТБ = 5808 + 105 = 6858 руб.
Ф.О.ТПР = 263 + 47 = 31 руб.
5.2. Расчет отчислений на социальные нужды.
ОСС = Ф.О.Т КСС (5.8)
где КСС – коэффициент отчислений на социальные нужды.
ОССБ = 68580356 = 244 руб.
ОССПР = 310356 = 11 руб.
5.3. Расчет затрат на амортизацию оборудования.
АОБ = (ЦОБНАtМАШ)(FЭ100) (5.9)
где ЦОБ – стоимость оборудования;
НА – норма амортизационных отчислений на оборудование;
FЭ – эффективный фонд времени;
tМАШ – время машинное.
Расчет затрат на амортизацию оборудования. Таблица 5.3
Печь СШО – 10.1010М1
Продолжение табл. 5.3.
Токарно-винторезный станок 1К625ДГ
Контрольно-измерительное приспособление
5.4 Расчет затрат на электроэнергию.
ЗЭ-Э = (МУСТtМАШЦЭ-Э)КПД (5.10)
где МУСТ – потребляемая мощность оборудования;
ЦЭ-Э– стоимость электроэнергии;
КПД – коэффициент полезного действия.
Расчет затрат на электроэнергию. Таблица 5.4
5.5. Расчет общих затрат на оборудование.
РОБ = АОБ + ЗЭ-Э (5.11)
РОББ = 803 + 557= 6373 руб.
РОБПР = 283 + 15= 433 руб.
5.6. Расчет затрат на содержание и амортизацию площадей.
а) затраты на содержание и эксплуатацию площадей:
ЗПЛ = (СЭКСПftШТ) FЭ (5.12)
где СЭКСП – стоимость эксплуатации площадей;
f – площадь необходимая для изготовления приспособления;
tШТ – общее время необходимое для создания приспособления.
ЗПЛ Б= (200040161)2061 = 625 руб.
ЗПЛ ПР=(200030073)2061 = 213 руб.
б) затраты на амортизацию площадей:
АПЛ = (ЦПЛНА.ПЛtШТf)(FЭ100) (5.13)
где ЦПЛ – стоимость приобретения площадей;
НА.ПЛ – норма амортизации площадей.
АПЛБ = (3000516140)(2061100) = 469 руб.
АПЛПР = (3000507330)(2061100) = 159 руб.
в) итого расходы на содержание и амортизацию площадей составят:
РПЛ = ЗПЛ + АПЛ (5.14)
РПЛ Б = 625 + 469 = 672 руб.
РПЛ ПР = 213 + 159 = 229 руб.
5.7. Расчет технологической себестоимости правки изделия.
СТЕХ = Ф.О.Т + ОСС + РОБ + РПЛ (5.15)
СТЕХБ = 6858 + 244 + 6373 + 672 = 224 руб.
СТЕХПР = 31 + 11 + 433 + 229 = 692 руб.
6. Расчет цеховой себестоимости правки изделия.
СЦЕХ = СТЕХ + ЗОСН КЦЕХ (5.16)
где КЦЕХ – коэффициент цеховых расходов.
СЦЕХБ = 224 + 5808215= 3489 руб.
СЦЕХПР = 692 + 263215= 1257 руб.
7. Расчет заводской себестоимости правки изделия.
СЗАВ = СЦЕХ + ЗОСН КЗАВ (5.17)
где КЗАВ – коэффициент заводских расходов.
СЗАВБ = 3489 + 580815 = 43602 руб.
СЗАВПР = 1257 + 26315 = 16515 руб.
8. Калькуляция заводской себестоимости затрат на правку изделия.
Расчет произведем в табличной форме. Таблица 5.5
Отчисления на социальные
Расходы на оборудование
Расходы на производственные площади
Себестоимость технологическая
Себестоимость цеховая
Продолжение табл. 5.5.
Себестоимость заводская
Себестоимость с учетом НИР
9. Расчет капитальных вложений в оборудование и площади по базовому и проектному вариантам.
9.1. Расчет капитальных затрат для осуществления технологического процесса.
где n – количество оборудования;
ЦОБ – стоимость оборудования;
КМОНТ – коэффициент учитывающий затраты на монтаж и демонтаж оборудования;
К ТЗ - коэффициент транспортно – заготовительных расходов.
КОББ = 3620001051035 = 3934035 руб.
КОБПР = 4051511051035 = 4402986 руб.
9.2. Расчет затрат на площадь необходимую для осуществления техпроцесса.
где f – площадь необходимая для тех. процесса;
ЦПЛ – стоимость приобретения площадей.
КПЛБ = 403000 = 120000 руб.
КПЛПР = 303000 = 90000 руб.
9.3. Расчет общих капиталовложений.
где – КОБЩ. – общие вложения.
КОБЩБ = 3934035 + 120000 = 5134035 руб.
КОБЩПР = 4402986 + 90000 + 14920= 5452186 руб.
9.4. Расчет удельных капиталовложений.
где ПГ – годовая программа выпуска изделий.
КУДБ = 5134035 1280 = 401 руб.
КУДПР = 5452186 1280 = 4413 руб.
9.5. Расчет дополнительных капиталовложений.
КДОП = К ОБЩ.ПР – КОБЩ.Б (5.22)
КДОП = 5302986 – 5134035 = 168951 руб.
10. Экономическая эффективность дипломного проекта.
10.1. Показатели снижения трудоемкости.
ΔtШТ = (161-073)161100 % = 546 %
10.2. Показатель снижения себестоимости.
ΔСтех = (43602 – 16745)43602100 % = 616 %
10.3. Условно-годовая экономия.
ЭУГ = (43602 – 16745)1280 = 3437696 руб.
10.4. Годовой экономический эффект в сфере производства.
ЭГ = ЭУГ – ЕНКДОП (5.26)
где ЕН – нормативный коэффициент экономической эффективности капвложений.
ЭГ = 3437696 - 033168951 = 3381942 руб.
10.5. Экономический эффект в сфере эксплуатации.
где Т2 и Т1 – срок службы по проектному и базовому вариантам соответственно.
ЭГ ЭКОН = ((4360221+033401)-(16745+0334413))1280 = 884801 руб.
В данной главе были получены следующие экономические показатели.
Заводская себестоимость правки по базовому варианту составила 43602 рубля по проектному 16515 рубля. Произошло снижение трудоемкости на 546 % что привело к снижению себестоимости на 616 % по сравнению с базовой технологией. Условно-годовая экономия составила 3437696 рубля. Годовой экономический эффект в сфере производства с учетом капитальных вложений составил 3381942 рубля в сфере эксплуатации за счет повышения срока службы 884801 рубля.
Разработанные расчетные схемы позволяют расширить технологические возможности метода ППД которые повышает качество и производительность правки деталей обеспечивая экономическую эффективность.
Охрана труда и безопасность проекта.
1. Описание участка для выполнения научно-исследовательской работы.
В лаборатории в которой велась научно-исследовательская работа имеются: токарный станок и круглошлифовальный станок. Все это оборудование позволяет провести экспериментальные исследования в области правки ППД но при этом является источниками вредных и опасных факторов негативно влияющих на здоровье и трудоспособность человека.
Ширина проходов между оборудованием . Организация рабочего места должна удовлетворять эргономическим требованиям ГОСТ 12.2.061-81. Объем производственного помещения на одного рабочего должен быть а площадь 45 м2 исключая площади занимаемыми оборудованием проходами.
Спецификация оборудования для рабочего места. Таблица 6.1
Наименование оборудования
Операции выполняемые на этом оборудовании
Токарный станок 1К62
Круглошлифовальный станок
Рис. 6.1. Схема планировки лаборатории для проведения исследований в области правки ППД: 1-токарный станок; 2-круглошлифовальный станок; 3-пожарный щит; 4-ящик с песком; 5-огнетушитель ОУ-5; 6-бытовое помещение; 7-шкаф с инструментами.
Расстояние между станками не менее 20 м; расстояние от стен не менее 15 м.
2. Идентификация опасных и вредных производственных факторов разрабатываемого производственного объекта по ГОСТ 12.0.003-74.
Опасные и вредные производственные факторы. Таблица 6.2.
Наименование опасного и вредного производственного фактора
Виды работ оборудование технологические операции при которых встречается данный производственный фактор
Электромагнитное излучение
Электрооборудование установки измерительные приборы автоматические системы контроля
Неблагоприятные метеорологические условия в производственных помещениях (влажность пыль)
3. Воздействие производственных факторов на организм человека.
3.1. Воздействие электромагнитного излучения и допустимый для человека уровень его интенсивности.
Критерием безопасности для человека находящегося в электрическом поле промышленной частоты принята напряженность этого поля. Гигиенические нормы для персонала который систематически находится в этой зоне установлены ГОСТ 12.1.006-84 «ССБТ. Электрические поля токов промышленной частоты напряжением 400 кВ и выше. Общие требования безопасности». Нормируется время пребывания человека в электрическом поле в зависимости от напряженности: менее 5 кВм – без ограничений; от 5 до 10 кВм – не более 180 минут; свыше 10 15 кВм – не более 90 минут; свыше 15 20 кВм – не более 10 минут; свыше 20 25 кВм – не более 5 минут[8].
Наиболее интенсивно электромагнитные поля воздействуют на органы с большим содержанием воды. Перегрев же особенно вреден для тканей со слаборазвитой сосудистой системой или с недостаточным кровообращением (глаза мозг почки желудок желчный пузырь и мочевой) так как кровеносную систему можно уподобить системе водного охлаждения. Облучение глаз вызывает помутнение хрусталика (катаракту) которое обнаруживается не сразу а через несколько дней или недель после облучения.
При воздействии полей имеющих напряженность выше предельно допустимого уровня развиваются нарушения со стороны нервной сердечно-сосудистой систем органов дыхания органов пищеварения и некоторых биохимических показателей крови.
Воздействие электрического поля промышленной частоты на организм человека сводится к влиянию электрического поля непосредственно на мозг и центральную нервную систему.
3.2. Действие шума на человека.
В зависимости от уровня и характера шума его продолжительности а также индивидуальных особенностей человека шум может оказывать на него различное действие.
Предельно допустимый уровень шума регламентируется по ГОСТ 12.1.00-83 и СН 2.2.42.1.8.562-96 и составляет для рабочих зон в производственных помещениях 85 дБ.
Отсутствие необходимой тишины особенно в ночное время приводит к преждевременной усталости а часто и к заболеваниям.
Человек работая при шуме привыкает к нему но продолжительное действие сильного шума вызывает общее утомление может привести к ухудшению слуха а иногда и к глухоте нарушается процесс пищеварения происходят изменения объема внутренних органов[3].
Воздействуя на кору головного мозга шум оказывает раздражающее действие ускоряя процесс утомления ослабляет внимание и замедляет психические реакции. По этим причинам сильный шум в условиях производства может способствовать возникновению травматизма так как на фоне этого шума не слышно сигналов транспорта автопогрузчиков и других машин.
При воздействии шума очень высоких уровней (более 145 дБ) возможен разрыв барабанной перепонки.
3.3. Влияние неблагоприятных метеорологических условий в производственных помещениях на человека.
Пыль вредные вещества.
По СанПиН 2.2.4.548-96 установлены предельно допустимые концентрации вредных веществ в воздухе рабочей зоны производственных помещений (кремнеземсодержащие пыли – 1 мгм3; окись железа – 4 6 мгм3; окись углерода аммиак – 20 мгм3; топливный бензин – 100 мгм3; ацетон – 200 мгм3).
Вредные вещества проникают в организм человека главным образом через дыхательные пути а также через кожу с пищей. Большинство этих веществ относится к опасным и вредным производственным факторам поскольку они оказывают токсическое действие на организм человека. В результате их действия у человека возникает болезненное состояние – отравление опасность которого зависит от продолжительности воздействия концентрации и вида вещества.
Ряд вредных веществ оказывает на организм человека преимущественно фиброгенное действие вызывая раздражение слизистых оболочек дыхательных путей и оседая в легких практически не попадая к круг кровообращения вследствие плохой растворимости в биологических средах (крови лимфе). В основном – это пыли металлов. Эти пыли образуются при металлообработке прокатке штамповке в литейном производстве и т.д.
В результате воздействия вредных веществ могут возникать профессиональные заболевания; так при длительном вдыхании пыли – пневмокониозы. Наиболее тяжелым из них является силикоз возникающий при попадании в легкие пыли содержащей двуокись кремния. Пыль образующаяся при сварке а также шлифовании может быть причиной заболевания пневмокониозом.
Одной из основных мер по оздоровлению воздушной среды является вентиляция воздуха.
Влажность воздуха определяется содержанием в нем водяных паров. Различают абсолютную максимальную и относительную влажность воздуха.
Оптимальные величины относительной влажности составляют 40 – 60 % [6].
Влажность воздуха оказывает большое влияние на терморегуляцию организма. Повышенная влажность (j > 85 %) затрудняет терморегуляцию из-за снижения испарения пота а слишком низкая влажность (j 20 %) вызывает пересыхание слизистых оболочек дыхательных путей и снижению защитной деятельности мерцательного эпителия верхних дыхательных путей. Повышенная влажность воздуха в сочетании с низкими температурами оказывает значительное охлаждающее действие а в сочетании с высокими – способствуют перегреванию организма. Для борьбы с повышенной влажностью используется система вентиляции воздуха.
3.4 Действие вибрации на человека.
Причиной возникновения вибраций являются возникающие при работе машин и агрегатов неуравновешенные силовые воздействия.
Воздействие вибраций на человека чаще всего связано с колебаниями обусловленными внешним переменным силовым воздействием на машину либо на отдельную ее систему. Возникновение такого рода колебаний может быть связано не только с силовым но и с кинематическим возбуждением например в транспортных средствах при их движении по неровному пути.
Различают общую и локальную вибрации. Общая вибрация вызывает сотрясение всего организма местная вовлекает в колебательные движения отдельные части тела. Общей вибрации подвергаются транспортные рабочие операторы крупных штампов и другого оборудования. Локальной вибрации подвергаются работающие с ручным электрическим пневматическим и механизированным инструментом.
Систематическое воздействие общих вибраций характеризующихся высоким уровнем виброскорости может быть причиной вибрационной болезни - стойких нарушений физиологических функций организма обусловленных преимущественно воздействием вибрации на нервную систему. Эти нарушения проявляются в виде головных болей головокружений плохого сна пониженной работоспособности плохого самочувствия нарушение сердечней деятельности.
Вибрация может не вызывать болезненных ощущений но затруднить проведение производственных процессов.
Локальная вибрация вызывает спазмы сосудов которые начинаются с концевых фаланг пальцев и распространяются на всю кисть предплечье захватывают сосуды сердца. Вследствие этого происходит ухудшение снабжения конечностей кровью. Одновременно наблюдается воздействие вибрации на нервные окончания мышечные и костные ткани. Выражающиеся в нарушении чувствительности кожи окостенение сухожилий мышц и отложений солей в суставах кистей рук и пальцев что приводит к болям деформации и уменьшению подвижности суставов. Все указанные изменения усиливаются в холодный и уменьшаются в теплый период года.
3.Организационные технические мероприятия по созданию безопасных условий труда.
4.1. Методы защиты от электромагнитных полей.
Ослабление мощности электромагнитного поля на рабочем месте можно достигнуть путем увеличения расстояния между источником излучения и рабочим местом; уменьшения мощности излучения генератора а также установки отражающего или поглощающего экранов между источником и рабочим местом; применение индивидуальных средств защиты.
В данной лаборатории для защиты от электромагнитных излучений рекомендуется применять установку экранов. Экранируют либо источник излучения либо рабочее место. Отражающие экраны делают из хорошо проводящих металлов – меди латуни алюминия стали.
Одним из способов снижения излучаемой мощности является правильный выбор генератора. В тех случаях когда необходимо уменьшить мощности излучения генератора применяют поглотители мощности которые полностью поглощают или ослабляют в необходимой степени передаваемую энергию на пути от генератора к излучающему устройству.
Для защиты от электрических полей промышленной частоты необходимо увеличивать высоту подвеса фазных проводов ЛЭП уменьшать расстояние между ними.
4.2. Защита от шума.
В лаборатории используемой для проведения научно-исследовательской работы проводимой в данном дипломном проекте борьба с шумом посредством уменьшения его в источнике является наиболее рациональной[3].
Уменьшение механического шума может быть достигнуто путем совершенствования технологических процессов и оборудования.
Нередко повышенный уровень шума является следствием неисправности или износа механизмов в этом случае своевременный ремонт позволяет снизить шум.
Шумы электромагнитного происхождения возникают в электрических машинах и оборудовании. Снижение электромагнитного шума осуществляется путем конструктивных изменений в электрических машинах. В трансформаторах необходимо применять более плотную прессовку пакетов использовать демпфирующие материалы.
Также для снижения шума применяются следующие меры: изменение направленности излучения шума рациональная планировка предприятий и цехов акустическая обработка помещений применение различных звукоизолирующих ограждений на пути распространения шума.
Также возможно применение средств индивидуальной защиты (противошумов): вкладышей наушников и шлемов.
4.3. Системы вентиляции.
Основные нормы и требования проектирования вентиляции приведены в ГОСТ 12.1.021-88.
По способу перемещения воздуха вентиляция бывает с естественным побуждением (естественной) и с механическим (механической). Возможно также их сочетание (смешанная вентиляция).
В зависимости от того для чего служит система вентиляции - для подачи (притока) или удаления (вытяжки) воздуха из помещения или (и) для того и другого одновременно она называется приточной вытяжной или приточно-вытяжной.
В данной лаборатории для проведения НИР следует применить общеобменную вентиляцию. Действие общеобменной вентиляции основано на разбавлении загрязненного нагретого влажного воздуха помещения свежим воздухом до предельно допустимых норм. Эту систему вентиляции наиболее часто применяют в случаях когда вредные вещества теплота влага выделяются равномерно по всему помещению. При такой вентиляции обеспечивается поддержание необходимых параметров воздушной среды во всем объеме помещения.
4.4. Защита от вибрации
В данной технологии вибрация не превышает установленной нормы (50 Гц СН 2.2.42.1.8.566-96) на большинстве операций. Локальные вибрации отсутствуют так как не происходит контакта конечностей с вибрирующим инструментом. Незначительная общая вибрация возникает в процессе самой правки ППД. Для ее устранения применяется резиновый коврик на пол.
4.Обеспечение электробезопасности на производственном участке.
Электробезопасность на производственном участке обеспечивается соответствующей конструкцией электроустановок; применением технических способов и средств защиты; организационными и техническим мероприятиями (ГОСТ 12.1.018-92).
По категории электробезопасности данная лаборатория относится к 3 классу[6].
Конструкция электроустановок должна соответствовать условиям их эксплуатации и обеспечивать защиту персонала от соприкосновения с токоведущими движущимися частями а оборудования – от попадания внутрь посторонних твердых тел и воды.
Основными техническими способами и средствами защиты от поражения электрическим током используемыми отдельно или в сочетании друг с другом являются: защитное заземление; зануление; выравнивание потенциалов; малое напряжение; электрическое разделение сетей; защитное отключение; изоляция токоведущих частей (рабочая дополнительная усиленная двойная); компенсация токов замыкания на землю; оградительные устройства; предупредительная сигнализация блокировка знаки безопасности; изолирующие защитные и предохранительные приспособления.
На нашем оборудовании доступа к узлам находящимся под высоким напряжением не имеется. Высокое напряжение многократно механически защищено. На оборудовании имеется защитное заземление токоведущие части хорошо изолированы.
5.Обеспечение пожаробезопасности на производственном участке.
Пожарная безопасность данного производственного объекта и взрывобезопасность производственных процессов обеспечивается разработкой и осуществлением систем предотвращения пожаров и взрывов и систем пожарной защиты и взрывозащиты[6].
Система предотвращения пожара должна разрабатываться по каждому конкретному объекту из расчета что нормативная вероятность возникновения пожара и взрыва принимается равной не более 10-6 в год в расчете на отдельный пожароопасный узел (элемент) данного объекта (ГОСТ 12.1.004-91) или взрывоопасный участок (ГОСТ 12.1.010-91). Вероятность воздействия опасных факторов взрыва на людей в течение года также не должна превышать 10-6 на человека (ГОСТ 12.1.010-91).
Производственный участок разрабатываемый в данном дипломном проекте по категории взрывной взрывопожарной и пожарной опасности относится к классу Г.
Для предотвращения пожаров и взрывов необходимо прежде всего исключить образование горючей и взрывоопасной среды а также предотвратить возникновение в горючей среде (или внесение в нее) источников (импульсов) зажигания. Эти задачи решаются как на стадии проектирования технологических процессов и производственного оборудования так и в процессе эксплуатации предприятий.
6.Инженерные расчеты.
6.1.Расчет искусственного освещения.
Свет является одним из важнейших условий существования человека так как влияет на состояние его организма. Правильно организованное освещение стимулирует процессы нервной деятельности и повышает работоспособность. При недостаточном освещении человек работает менее продуктивно быстро устает растет вероятность ошибочных действий что может привести к травматизму.
Количество светильников определяется по формуле[1]:
где Е – минимальная нормируемая освещенность Е = 200 лк;
S – площадь помещения S = 20 м2;
k – коэффициент запаса учитывающий старение ламп запыление и загрязнение светильников k = 13;
z – коэффициент неравномерности освещенности z = 13;
Ф – световой поток одной лампы лампа ДРЛ 250 Ф = 12500 лм;
- коэффициент использования светового потока зависящий от КПД светильника коэффициента отражения потолка стен высоты подвеса светильников и размеров помещения.
Для определения коэффициента необходимо вычислить индекс помещения:
где b – ширина помещения b = 8 м;
h – высота светильника над рабочей частью h = 3 м.
Следовательно = 48 %
6.2.Расчет системы вентиляции.
При проведении экспериментов важно использовать местную вытяжную вентиляцию расположенную над установкой ИПА то есть у места выделения вредных веществ. Вытяжная вентиляция выполняется в виде местного отсоса – вытяжного шкафа.
Объем воздуха удаляемого вытяжным шкафом определяется по формуле[1]:
где F – площадь открытого проема F = 4 м2;
V – средняя скорость движения всасываемого воздуха в открытом проеме V = 08 мс.
7.Экологическая экспертиза разрабатываемого объекта
Целью экологической экспертизы является превентивный контроль экологической безопасности осуществление государственного контроля в области охраны окружающей среды и рационального использования природных ресурсов.
Предприятия машиностроения постоянно выбрасывают в атмосферу загрязненный воздух. Результатом этого является присутствие вредных веществ в воздухе города которое приводит к возникновению различных болезней людей ухудшению экологической обстановки на планете.
Для снижения выброса вредных веществ в атмосферу необходимо детально проработать технологический процесс с целью снижения количества выбросов токсичных веществ.
При проведении научно-исследовательской работы в области правки ППД воздух рабочей зоны загрязняется абразивной пылью и другими вредными веществами поэтому перед выбросом в атмосферу воздух должен тщательно очищаться. Таким образом вредные вещества из рабочей зоны выводятся с помощью приточно-вытяжной вентиляции: приточная вентиляция подает воздух в рабочую зону а вытяжная удаляет – обе работают одновременно. Количество попадаемого и вытягиваемого воздуха выбирается с учетом требований предъявляемых к системе вентиляции. Место для забора свежего воздуха выбирается с учетом направления ветра с наветренной стороны по отношению к выбросным отверстиям вдали от мест загрязнения. На производстве должны быть разработаны и установлены специальные системы очистки воздуха перед его выбросом в атмосферу.
9. Безопасность объекта при аварийных и чрезвычайных ситуациях
Крупные аварии на предприятии могут возникать в результате стихийных бедствий нарушении технологии производства нарушения правил эксплуатации оборудования и установленных мер безопасности.
Стихийные бедствия – явления природы вызывающие экстремальные ситуации такие как землетрясения наводнения пожары. Под аварией понимают внезапную остановку работы или нарушение процесса производства на промышленном предприятии приводящее к повреждению или уничтожению материальных ценностей. Под катастрофой понимают внезапное бедствие событие влекущее за собой трагические последствия. Катастрофы сопровождаются разрушением зданий различных сооружений уничтожением материальных ценностей и гибелью людей. Наиболее опасным следствием крупных аварий являются пожары и взрывы[5].
Для ликвидации последствий вызванных стихийными бедствиями или катастрофами привлекаются формирования общего назначения и служб гражданской обороны. Основная задача формирований при ликвидации – спасение людей и материальных ценностей. Организация работ производится с учетом обстановки степени разрушения и повреждения зданий. Работы производятся в сжатые сроки так как необходимо быстро спасти людей и оказать им медицинскую помощь а также предотвратить последствия катастрофы.
К мероприятиям по предотвращению крупных аварий и катастроф относятся: закладка в проекты вновь создаваемых объектов планировочных технических и технологических решений которые должны максимально уменьшить вероятность возникновения аварий или значительно снизить материальный ущерб если авария произойдет. Кроме того должны быть предусмотрены мероприятия по эвакуации персонала при чрезвычайных ситуациях (ЧС). В случае появления непосредственной опасности возникновения ЧС в штабе гражданской обороны должен производится инструктаж людей по необходимым действиям при ЧС.
При проектировании рабочего участка для научно-исследовательской работы в области правки ППД учитываются все возможные опасные критические и аварийные ситуации которые могут возникнуть в процессе работы а также рассматриваются вопросы об их предотвращении.
В разделе «Охрана труда и безопасность объекта» были рассмотрены возможные опасные факторы данной технологии их влияние на организм человека и меры их предотвращения.
Рассмотренные выше мероприятия достаточны для проведения научно-исследовательской работы в области правки ППД так как они снижают влияние вредных и опасных факторов до предусмотренных норм и повышают безопасность при проведении работ.
В данной работе был разработан способ правки валов методом ППД. Данный способ позволяет одновременно с финишной обработкой деталей проводить правку изделия. Тем самым решается комплексная задача обеспечения качества нежестких валов так как повышается их точность снижается шероховатость и упрочняется поверхностный слой.
Разработанный способ высокотехнологичен прост в эксплуатации и не требует высоко уровня знаний.
Так же этот метод относится к высоким технологиям так как качество правки достигается не путем совершенствования оборудования и высокоточной настройки а за счет управления напряженным состоянием детали. То есть идет превращение отрицательного фактора обработки в положительный.
Так же была разработана математическая модель способа позволяющая рассчитать вызываемый обработкой изгибающий момент и оптимальные режимы поверхностного пластического деформирования.
Задачи дипломного проекта выполнены цель достигнута.
СПИСОК ИСПОЛЬЗОВАННЫХ ИСТОЧНИКОВ.
Безопасное взаимодействие человека с техническими системами:
Безопасность и экологичность объекта дипломного проекта. Методические указания. Сост. Горина Л. Н. – Тольятти: ТГУ 2003.
Борьба с шумом на производстве: Справочник Е.Я. Юдин Л.А. Борисов И. Горенштейн и др.; Под общ. ред. Е.Я. Юдина. – М.: Машиностроение 1985. – 400с.
Букатый С. А. Дмитриев В. А. Папшев Д. Д. Оптимизация режимовупрочнения по допускаемым деформациям деталей Вестник машиностроения. -1990. -№8. -с. 58-61.
Вахтин А.К. Меры безопасности при ликвидации стихийных бедствий и производственных аварий - М: Энергоатомиздат 1984 288 с.
Горина Л.Н. Обеспечение безопасных условий труда на производстве. – Учеб. пособие. – Тольятти: ТолПИ 2000. – 68с.
Дальский А. М. Технологическое обеспечение надежности высокоточных деталей машин. -М.: Машиностроение 1975. -223 с.
Долин П.А. Основы техники безопасности в электроустановках - М: Энергоиздат 1984 450 с.
Дрозд М. С. Определение механических свойств металла без разрущения. -М.: Металлургия 1965 -171 с.
Дрозд М. С. Сидякин Ю. И. Метод оптимизации технологических параметров режима упрочняющего обкатывания деталей роликами. -Вестник машиностроения. 1984 №1 с. 26-28
Зайдес С. А. Мураткин Г. В. Упрочнение восстановление правка валов: Учебное пособие Под ред. С. А. Зайдеса - Иркутск: Изд-во ИрГТУ. - 2005. 336с.
Коклер Я. Д. Математический анализ точности механической обработки деталей. -Киев: Техника 1976. -200 с.
Корбин М. М. Дехтярь Л. И. Определение внутренних напряжений в цилиндрических деталях. -М.: Машиностроение 1965. -175 с.
Кувалдин Ю. И. Васильевых Л. А. Изменение пространственных погрешностей валов при термической обработке. Известия ВУЗов. - Машиностроение. -1987. -№9. -с. 111-115.
Кудинова Г. Э. Методическое руководство по расчету экономического раздела дипломных проектов для студентов 6-го и 5-го курса специальности ОТСП 1205 и ВДМ 1206
Малинин Н. Н. Прикладная теория пластичности и ползучести. Изд. 2-е перераб. и дополн. -М.: Машиностроение 1975. -400 с.
Мураткин Г. В. Повышение точности нежестких деталей типа валов путем управления их напряженным состоянием при обработке методами ППД: Автореферат дис. канд. техн. наук. -Москва 2000. -20с.
Овсеенко А. Н. Технологические начальные напряжения и методы их определения. -М.: Труды ЦНИИТМАШ. - 1986. -№ 196. -с. 9-15
Овсеенко А. Н. Технологические основы методов снижения остаточных деформаций и обеспечния качества обработки высоконагруженных деталей энергомашин: Автореферат дис. Докт. Техн. Наук. Москва 1985. -32 с.
Овсеенко А. Н. Технологические остаточные деформации маложестких деталей и методы их снижения. Вестник машиностроения. -1991. -№2. -с 58-61.
Соколовский А. П. Курс технологии машиностроения. Ч. 1. -М. -Л.: Машгиз 1947. -436 с.
Способ комбинированной обработки валов: А.С. 1504071 (СССР). -Опубл. в Б. И. Емельянов Б.Н.. Громова Л.А. -1989. -№ 32
Способ обработки нежестких валов: Патент 2021098 (РФ). -Опубл. в Б.И. Мазур В.К. Мураткин Г.В. -1994. -№ 19.
Способ правки нежестких валов: А.С. 1532120 (СССР). - Опубл. в Б.И. Колот В.А. Плеханов В.Н. Никогосян О.Л. -1989. -№ 48.
Способ правки с одновременной отделочно-упрочняющей обработкой нежестких валов: МКИ В21 D 316 В 24В3904.Мураткин Г. В. Котова И. В. Синцов А. С.
Способ холодной правки деталей типа вала: А. С. 1159681 (СССР). - Опубл. В Б. И.Кудрявцев И. В. Кудрявцев П. И. Грудская Р. Е. Савина Н. М. -1985. -№21.
Способ холодной правки деталей типа вала: А.С. 1159681 (СССР). - Опубл. в Б.И. Кудрявцев В.И. Кудрявцев П.И. Грудская Р.Е. Саввина Н.М. -1985. -№ 21.
Способ холодной правки нежестких деталей типа валов: А.С. 1516171 (СССР). - Опубл. в Б.И. Колот В.А. Плеханов В.Н. Никогосян О.Л. -1989. -№ 39.
Устройство для правки с одновременным накатыванием деталей типа вала: А.С. 1682149 (СССР). – Опубл. в Б.И. Емельянов В.Н. Усачев В.П. – 1991. - № 37.
Черненко О. С. Повышение производительности процесса и точности изделий при поверхностном пластическом деформировании на основе совершенствования технологии операций и инструмента. дисс. канд. техн. наук. Тольятти 1987.
Рекомендуемые чертежи
- 04.02.2024
- 01.07.2014
- 24.01.2023
- 24.01.2023