Станок зубострогальный 5236П



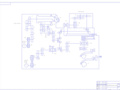
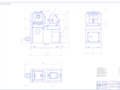
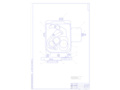
- Добавлен: 25.10.2022
- Размер: 981 KB
- Закачек: 0
Описание
Состав проекта
![]() |
![]() ![]() ![]() |
![]() ![]() ![]() ![]() |
![]() ![]() ![]() ![]() |
![]() ![]() ![]() ![]() |
![]() ![]() |
![]() ![]() |
![]() ![]() |
Дополнительная информация
rrryiresryer.docx
Использование совершенных методов проектирования изготовления сборки и утилизации технологического оборудования имеет первостепенное значение. Качество технической системы надежность долговечность и экономичность в эксплуатации зависят не только от совершенства ее конструкции но и от технологии ее изготовления.
Основные предпосылки определяющие важнейшие направления развития технологического оборудования в станкостроении:
-разработка способов обработки на основе новых физических явлений и процессов;
-совершенствование существующего и разработка нового высокопроизводительного оборудования для отделочной обработки обеспечивающего заданную точность и качество;
-совершенствование существующего и разработка нового высокопроизводительного оборудования для выполнения получистовой и чистовой обработки лезвийным режущим инструментом;
-комплексная автоматизация технологического оборудования основанная на разработке новых и совершенствовании имеющихся автоматизированных и полуавтоматизированных станков станков с ЧПУ средств активного контроля быстродействующей технологической оснастки групповых методов обработки;
-развитие технологического оборудования основанного на процессах формообразования пластическим деформированием и поверхностно пластическим деформированием для отделочных операций;
-совершенствование технологического оборудования основанного на электрофизических и электрохимических процессах.
Зубострогальный станок модели 5236П предназначен для нарезания конических зубчатых колёс с прямым зубом двумя резцами методом обкатки. Станок обеспечивает нарезание колес 67-й степени точности. Повышенная точность обеспечивается применением в конечных звеньях кинематических цепей высокоточных червячных передач с большим передаточным отношением.
Описание основных узлов
Форма боковой поверхности зуба конического прямозубого колеса образуется двумя производящими линиями: прямой линией - форма зуба по длине и пространственной кривой несколько отличающийся от плоской эвольвенты - форма зуба по профилю.
При обработке сначала получают форму зуба по длине методом следа а затем по профилю - методом обката.
Конические колёса служат для передачи вращения между валами с пересекающимися осями. Их называют угловыми передачами. В наиболее распространённом случае когда угол между осями валов равен 90° передача называется ортогональной.
На рис. 1 представлена схема зацепления двух конических колёс а на рис. 2 - элементы конического зубчатого колеса. При проектировании конической зубчатой передачи обычно задают передаточное отношение i12 и угол 5 между осями колес 1 и 2 (рис. 1).
Рисунок 1 - Схема зацепления двух конических колёс
Рисунок 2 - Элементы конического зубчатого колеса
Рисунок 3 - Общий вид станка модели 5236П:
- бабка передняя; 2 - люлька; 3 - суппорт; 4 - резец; 5 - заготовка; 6 - счётчик циклов; 7 - рукоятка крана охлаждения; 8 - крышка гитары деления; 9 - бабка изделия; 10 - вал перемещения бабки изделия; 11 - гайка; 12 - основание бабки изделия; 13 - стол; 14 - лимб установки припуска на чистовую обработку при двухпроходной работе; 15 - рукоятка перемещения стола и зажима изделия; 16 - редукционный клапан для изменения усилия зажима изделия; 17 - дверца упорного барабана; 18 - крышка узла гидравлики; 19 - маслоуказатель; 20 - станина; 21 - дверца гитары обкатки; 22 - винт установки резцов по высоте; 23 - пульт управления; 24 - крышка гитары скоростей
Рисунок 4 - Реверсивный механизм с составным зубчатым колесом
Общий вид станка показан на рис. 4. На станке слева закреплена передняя бабка 1 внутри которой находится люлька 2 в виде барабана с опорами качения по наружному диаметру. На торце люльки расположены направляющие скольжения для двух суппортов 3 с закреплёнными на них резцами 4.
Бабку изделия 9 с закреплённой на шпинделе заготовкой 5 вместе с основанием 12 разворачивают на столе 13 вокруг вертикальной оси чтобы обеспечить необходимый угол между осями заготовки и люльки (воображаемого производящего колеса). Для совмещения вершин конусов этих колёс бабку изделия перемещают вдоль оси шпинделя по направляющим основаниям 12.
Управление необходимыми переключениями в течение цикла осуществляется распределительным валом который за цикл совершает один оборот. Конструктивно он выполнен из двух частей (валы XXIV и XXV) соединённых между собой кинематической цепью с передаточным числом 1:1 и включает: вал XXIV червячную передачу 160 цилиндрические колёса 50-50-50 червячную передачу 160 вал XXV.
Кулачки К2 и К3 управляют движением стола К4 воздействует на микропереключатель счётчика циклов (числа нарезанных зубьев) для остановки полуавтомата после обработки всех зубьев и К5 переключат электродвигатель постоянного тока М2 с рабочей на ускоренную частоту вращения. Кулачок Кь расположенный на валу XXV управляет реверсом.
Возвратно-поступательное движение резцов со скоростью резания осуществляется приводом от асинхронного электродвигателя М1 через ременную передачу и систему зубчатых передач до центрального вала IV люльки Л. Кривошипно-шатунный механизм КМ преобразует вращение вала IV в возвратно-поступательное движение рычага Р1 вокруг оси V переходящее затем в возвратно-поступательное движение ползунов П; и П2 с резцами.
Рисунок 5 - Кинематическая схема станка 5236П
Структурная схема привода станка
Кинематическая структура станка (рис. 6) состоит из двух групп формообразования Фv (П1) и ФS(В2В3) группы деления Д(В3) и вспомогательного движения Всп. а также группы установочного движения Уст. (П5) - для отвода стола с изделием и подвода его в зону резания.
Рисунок 6 – Структурная схема станка
Структура группы Фv (П1) простая и внутренняя связь обеспечивается связью поступательной пары ползуна с резцами и люлькой. Внешняя связь группы Фv (П1) состоит из кинематической цепи 1-2-3 между двигателем М1 и ползунами и обеспечивает условие согласования перемещений её конечных звеньев:
Группа движения подачи ФS(В2В3) сложная её внутренняя связь обеспечивается кинематической цепью 12-11-10-98-7-6-17 между люлькой и шпинделем заготовки называемой цепью профилирования или обката. Эта цепь с органом настройки (гитарой обката ix) должна обеспечивать следующее условие кинематического согласования конечных звеньев
Внешняя связь группы ФS обеспечивает передачу движения от двигателя М2 во внутреннюю связь группы цепи 4-56. Органом настройки на скорость обкаточного движения подачи является сам электродвигатель М2 который имеет плавное регулирование частот вращения в пределах 300 3000 мин-1.
Помимо настройки на скорость движение обката Ф S (В2 В3) должно настраиваться на путь-угол качания 9° люльки необходимый для полного профилирования одного зуба нарезаемого колеса после чего люлька должна возвратиться в исходное положение для профилирования следующего зуба.
Прекращение движения обката и возвращение люльки в исходное положение осуществляется с помощью специального реверса в виде составного зубчатого колеса составленного из нескольких зубчатых секторов внешнего и внутреннего зацепления.
Реверсивное колесо состоит из двух участков: первый из них - цельный кольцеобразный с наружным венцом Z = 120 и внутренним Z = 80.
Второй участок - составной подковообразный зубья наружного и внутреннего венцов которого являются продолжением зубьев первого участка и соединяются между собой полушестернями Z = 20 (10) образуя подкову.
Вал XII ведущей шестерни Z = 20 находится в рычаге Р2 который может поворачиваться относительно оси вала XI и перемещаться вдоль неё для осуществления необходимого зацепления то с наружным то с внутренним кольцом реверсивного колеса.
Ведущая шестерня Z = 20 во время рабочего хода зацеплена с наружным венцом Z =120 реверсивного колеса и после того как реверсивное колесо совершит пять полных оборотов перемещается вдоль зуба под действием кулачка на валу XXV и переходит в зацепление с составным участком. Затем по полушестерне Z = 20 (10) шестерня Z = 20 входит в зацепление с внутренним венцом Z = 64 (80) и наконец перемещаясь вдоль зуба с его цельным участком.
После того как реверсивное колесо сделает пять оборотов в обратную сторону (холостой ход) ведущая шестерня Z = 20 перемещается вдоль зуба на составной участок и по полушестерне Z = 20 (10) на его наружный венец. Затем шестерня Z = 20 перемещается вдоль зуба на наружный венец цельного участка реверсивного колеса и цикл начинается снова.
Таким образом реверсивное колесо за цикл в одну и другую сторону при зацеплении шестерни Z = 20 совершает пять полных оборотов и неполный шестой оборот при зацеплении с подковообразным колесом Z = 20 (10).
Реализация основных методов формообразования поверхностей
Профили зубьев могут быть образованы перекатыванием без скольжения плоскости S по основным конусам в виде специфических эвольвент. При качении плоскости S по основному конусу 1 точка Р0 опишет сферическую эвольвенту МгЭг а при качении по основному конусу 2 - сферическую эвольвенту М2Э2 . Если такие же сферические эвольвенты построить для других точек плоскости S расположенных на прямой ОР0 то эти эвольвенты будут образовывать поверхности зубьев фактически точного эвольвентного конического зацепления.
Размеры зубьев конических колёс в различных сечениях неодинаковы. Стандартный модуль т принято назначать для внешнего торцевого сечения зубьев.
Проектирование и изготовление точного эвольвентного конического зацепления трудно осуществить практически так как сфера не разворачивается на плоскость. Поэтому применяют приближённый метод профилирования зубьев который заключается в следующем.
Рассматривая точное очертание зубьев (рис. 7) можно увидеть что торцевые поверхности зубьев на сфере образуют сферические пояса шириной а. Ширина а поясов весьма мала по сравнению с радиусом R той сферы на которой они расположены. Поэтому можно с достаточной точностью заменить сферические пояса поясами лежащими на конусах образующие которых касательны к сфере радиуса R в точках принадлежащих окружностям I и II.
Если теперь представить два начальных конуса в их проекции на плоскость содержащую оси начальных конусов то построение конусов на поверхности которых лежат торцевые поверхности зубьев может быть сделано следующим образом.
Пусть начальный конус S1 проектируется в виде треугольника AOP0. При точном построении профиля конус головок проектируется в виде треугольника bОb а конус ножек - в виде треугольника аОа. При точном проектировании сечения торцевых поверхностей зубьев плоскость поверхностей представляется в виде дуг аb лежащих на проекции сферы радиуса R. Так как конусы на которых должны лежать торцевые поверхности приближённых профилей зубьев должны касаться сферы по начальным окружностям то для нахождения проекций этих конусов через точку Р0 проводим прямую O1O2 перпендикулярную к прямой OP0. В пересечении с осями 1 и 2 получаем точки O1 и O2 представляющие собой вершины искомых конусов.
Рисунок 7 - Расположение профилей зубьев конических колёс на сферической поверхности
Рисунок 8 - Проекции начальных конусов на плоскость
Проекциями конусов первого и второго колеса являются соответственно треугольники O1AP0 и O2BP0. Сечения профилей торцов изображаются прямыми а' и b' лежащими на построенном конусе вместо кривых ab. Очевидно что чем больше отношение радиуса сферы к модулю зубьев тем меньше ошибка которую мы допускаем заменяя построения профилей зубьев образованных сферическими эвольвентами построением зубьев на поверхности конусов O1 AP0 и O2BP0.
Конусы с вершинами в точках O1 и O2 носят название дополнительных. Построение профилей торцевых поверхностей зубьев не встретит теперь никаких трудностей так как дополнительные конусы могут быть развёрнуты на плоскость и следовательно всё построение сведётся к построению на плоскости.
Метод обката основан на воспроизведении зацепления пары сопряжённых конических колёс одним из которых является обрабатываемое колесо а другим - имитируемое одним зубом или впадиной плосковершинное коническое производящее зубчатое колесо.
В процессе обработки они взаимно обкатываются с целью образования профиля зуба методом обката. Так как реального производящего колеса нет а есть только имитация его движения которую осуществляет люлька то такое колесо называют воображаемым производящим колесом. Профиль зуба или впадин между двумя соседними зубьями воображаемого производящего колеса также имитируется движением режущих (производящих) кромок инструмента перемещающихся с достаточно большой скоростью по прямой линии характеризующей форму зуба по длине обрабатываемого колеса.
Уравнение кинематического баланса привода главного движения
В данном станке нет механизма сообщающего заготовке отдельное движение деления. Заготовка вращается всегда в одном направлении а люлька с резцами после обработки одного зуба изменяет вращение на противоположное и возвращается в исходное положение. За это время происходит поворот заготовки на Zi Z3 оборота при этом распределительный вал совершает одни оборот.
Цепь деления связывает вращение распределительного вала (РВ) с вращением заготовки. За один оборот вала РВ заготовка поворачивается на Zi зубьев пропускаемых при делении причём Zi не должно иметь общих множителей с числом зубьев нарезаемого колеса Z3 . В противоположном случае после некоторого числа делений резцы повторно будут попадать в уже обработанные впадины а часть зубьев останется необработанной.
Расчётные перемещения запишутся:
Уравнение кинематического баланса:
откуда формула настройки цепи деления:
где Z Z3 - число нарезаемых на заготовке зубьев.
При подборе сменных зубчатых колёс гитары деления необходимо соблюдать условия:
с 70; f 100; 89 с + d 128; 100 e + f 168.
Система управления станка
Установить поворотные сегменты ползунов с закрепленными в них резцами на угол конусности зуба - угол между боковой поверхностью зуба у его основания и осевой линией зуба. Резцовые суппорты 4 (рис. 9) с резцедержателями 2 смонтированы на поворотных сегментах которые прилегают к торцу корпуса люльки и могут поворачиваться на угол до 8° при помощи винта 1.
Для установки суппортов на угол конусности зуба необходимо отвернуть гайки 5 и поворачивая вначале верхний сегмент а затем нижний посредством винтов 1 установить необходимый угол по шкале и нониусу 6. После произведенной установки гайки 5 затянуть.
Рисунок 9 - Схема люльки:
- винт угла поворота суппорта; 2 - резцедержатель; 3 - винт закрепления резцедержателя;
- суппорт; 5 - гайки зажима поворотного сегмента; 6 - шкала; 7 - Т-образный паз;
- винт закрепления резца; 9 - шкала для контроля угла качания
При черновом зубонарезании припуск на последующую чистовую обработку обеспечивается установкой угла сегментов больше расчётного на величину w. Добавочный угол установки суппортов для черновой обработки определяется по формуле:
где S2 - припуск на каждую сторону зуба (мм) который принимается в зависимости от модуля нарезаемого колеса.
Для установки угла качания люльки необходимо открыть дверцу 17. На рабочем ходу включают станок и останавливают его в тот момент когда риска на кольце упорного барабана «середина обката» совпадет с имеющимся там указателем затем открыв дверцу гитары обкатки снимают ведомую сменную шестерню и ключом надетым на вал червяка поворачивают люльку на требуемый угол по шкале 9 после чего надевают сменную шестерню.
Установка поворотной плиты.
При чистовом нарезании зубьев бабка изделия с поворотной плитой устанавливается на угол равный углу конуса впадин qf нарезаемого колеса. При черновом зубонарезании межзубовая впадина обычно прорезается глубже на величину h =05-01 мм для того чтобы при чистовой обработке резец не резал своей вершиной. Угол установки поворотной плиты при черновом нарезании (с целью оставления припуска на чистовую обработку) должен быть больше угла qf на величину . Это делается также для того чтобы при всех погрешностях установки поворотной плиты у чистовых резцов не работали тыловые кромки так как они имеют отрицательные углы и не предназначены для резания металла.
Для установки бабки изделия на угол внутреннего конуса нарезаемой шестерни необходимо освободить гайки 3 поворотной плиты и повернуть бабку изделия на требуемый угол по шкале и нониусу 2. После перемещения закрепить гайки 3.
Установка длины хода и места действия резцов. Длина хода резцов l должна быть больше чем длина зуба b нарезаемого колеса на величину перебега причём со стороны толстого конца зуба рекомендуемый выход резца - 5 мм а со стороны тонкого - 3 мм таким образом l = 3 + 5 = 8 мм. Этот перебег даёт возможность резцовой колодке встать в рабочее положение до начала резания и своевременно отойти от заготовки при холостом ходе для предохранения режущих кромок резцов от поломки.
Для установки длины хода резцов нужно открыть крышку передней бабки чтобы иметь доступ к люльке.
Люлька имеет роликовую переднюю опору 1 хвостовая часть поддерживается парой радиально-упорных подшипников
Червячное колесо 3 поворачивает люльку. Внутри хвостовой части вращается вал 4 привода главного движения (его передняя опора - шарикоподшипник 13 сзади - два игольчатых подшипника 5). Зубчатое колесо 6 передает движение валу 4 а также через торцевую шпонку 10 зубья муфты 7 - 8 и шлицы - валу 12 кривошипного механизма. Вал 12 эксцентрично расположен внутри вала 4 и связан с кривошипным пальцем 14.
Чтобы регулировать длину хода резцов необходимо изменить расстояние между осями вала 4 и пальца 14. Для этого отпускают гайку 9 разъединяют полумуфты 7 и 8 (на них имеются деления соответствующие длинам хода резцов) поворачивают вал 12 относительно вала 4 на выборочную длину хода резцов и в нужном положении фиксируют гайкой 9.
Зона действия резцов по отношению к венцу обрабатываемого зубчатого колеса устанавливается перемещением соответствующих суппортов вдоль Т-образных пазов люльки и последующим закреплением гайками.
Устройства для крепления инструментов
Установка резцов. При установке зубострогальных резцов выполняются два условия: теоретическая вершина А резцов (точка пересечения линий проходящих через режущие кромки резца) должна совпадать с плоскостью перпендикулярной к оси люльки и проходящей через центр станка (ось поворота поворотной плиты); линия движения вершины А резцов должна проходить через ось люльки (производящего колеса).
Рисунок 10 - Люлька станка модели 5236П
Резцы устанавливают по двум приборам которые маркированы словами «верхний» и «нижний» обозначающими для установки какого именно резца предназначен прибор.
На рис. 10 показан «верхний» прибор представляющий собой кронштейн 3 имеющий шпонку 10 и винт 9 с гайкой 4. На кронштейне закреплена пластина 2 в паз которой вставлен калибр 12 и прижат пластиной 14.
При установке резца Р прибор устанавливается на ползун 8 с таким расчётом чтобы его шпонка 10 с головкой винта 9 вошли в паз а затем прибор закрепляется гайкой 4. Такая установка обеспечивает совпадение поверхности 11 с плоскостью I-I перпендикулярной оси люльки и проходящей через центр станка а линия пересечения поверхности 11 с поверхностью 13 - прохождение её через ось люльки.
Рисунок 11 - Установка зубострогальных резцов по прибору
Резец Р устанавливается с базированием по поверхности 15 резцедержателя 6 и по поверхностям 16 17 клина 18 а затем слегка прижимается винтом 5. Поверхность 17 клина 18 по отношению к поверхности 11 прибора расположена под углом 12°. Поэтому передвигая резец по длине добиваются такого положения когда вершинная режущая кромка его коснётся поверхности 11 пластины 2.
Если же перемещать клин 17 по длине то резец будет поворачиваться вокруг поверхности 15. Таким образом регулируется профильный угол инструмента Р. На клине 18 имеется шкала а на резцедержателе 6 - указатель указывающий на нуль когда профильный угол равен 20°. После установки резца по длине и углу он закрепляется в резцедержателе окончательно.
По высоте резец регулируют перемещением всего суппорта с резцедержателем 6 относительно паза ползуна 8. Таким образом регулируя резец Р по длине углу и высоте добиваются прилегания его режущих кромок к поверхностям 11 и 13 прибора. Прилегание определяют визуально на просвет или на краску.
Если необходимо изменить положение резца при дополнительных регулировках (подгонка пятна контакта в передаче) на прибор устанавливают индикатор часового типа 1 и закрепляют винтом 7. По его показанию резец смещается на необходимую величину от исходного положения.
Порядок установки и регулировки нижнего резца - тот же самый только с прибором имеющим маркировку «нижний».
Требования по охране труда
Общие требования безопасности
К самостоятельной работе на зубострогальных станках допускается обученный персонал прошедший медицинский осмотр инструктаж по охране труда на рабочем месте ознакомленный с правилами пожарной безопасности и усвоивший безопасные приемы работы.
Зуборезчику разрешается работать только на станках к которым он допущен и выполнять работу которая поручена ему руководителем цеха (участка).
Рабочий обслуживающий зубострогальные станки должен иметь; костюм хлопчатобумажный или полукомбинезон очки защитные ботинки юфтевые.
Если пол скользкий (облит маслом эмульсией) рабочий обязан потребовать чтобы его посыпали опилками или сделать это сам.
Зуборезчикуику запрещается:
-работать при отсутствии на полу под ногами деревянной решетки по длине станка исключающей попадание обуви между рейками и обеспечивающей свободное прохождение стружки;
-работать на станке с оборванным заземляющим проводом а также при отсутствии или неисправности блокировочных устройств;
-стоять и проходить под поднятым грузом;
-проходить в местах не предназначенных для прохода людей;
-заходить без разрешения за ограждения технологического оборудования;
-снимать ограждения опасных зон работающего оборудования;
-мыть руки в эмульсии масле керосине и вытирать их обтирочными концами загрязненными стружкой.
О каждом несчастном случае фрезеровщик обязан немедленно поставить в известность мастера и обратиться в медицинский пункт.
Требования безопасности перед началом работы
Перед началом работы зуборезчик обязан:
-принять станок от сменщика; проверить хорошо ли убраны станок и рабочее место. Не следует приступать к работе до устранения выявленных недостатков;
-надеть спецодежду застегнуть рукава и куртку надеть головной убор;
-проверить наличие и исправность защитного экрана и защитных очков предохранительных устройств защиты от стружки и охлаждающих жидкостей;
-отрегулировать местное освещение так чтобы рабочая зона была достаточно освещена и свет не слепил глаза;
-проверить наличие смазки станка. При смазке следует пользоваться только специальными приспособлениями;
-проверить на холостом ходу станка:
-исправность органов управления;
-исправность системы смазки и охлаждения;
-исправность фиксации рычагов включения и переключения (убедиться в том что возможность самопроизвольного переключения с холостого хода на рабочий исключена).
Зуборезчику запрещается:
-работать в тапочках сандалиях босоножках и т.п.;
-применять неисправные и неправильно заточенные инструменты и приспособления;
-прикасаться к токоведущим частям электрооборудования открывать дверцы электрошкафов. В случае необходимости следует обращаться к электромонтеру.
Требования безопасности во время работы
Во время работы зуборезчик обязан:
-перед установкой на станок обрабатываемой детали и приспособления очистить их от стружки и масла;
-тщательно очистить соприкасающиеся базовые и крепежные поверхности чтобы обеспечить правильную установку и прочность крепления;
-установку и снятие тяжелых деталей и приспособлений производить только с помощью грузоподъемных средств;
-поданные на обработку и обработанные детали укладывать устойчиво на подкладках;
-не опираться на станок во время его работы и не позволять это делать другим;
-при возникновении вибрации остановить станок проверить крепление фрезы и приспособлений принять меры к устранению вибрации;
-не оставлять ключ на головке затяжного болта после установки фрезы или оправки;
-при снятии переходной втулки оправки или фрезы из шпинделя пользоваться специальной выколоткой подложив на стол - станка деревянную подкладку;
-обрабатываемую деталь прочно и жестко закреплять в приспособлении; при этом усилия резания должны быть направлены на неподвижные опоры а не на зажимы;
-при креплении детали за необрабатываемые поверхности применять тиски и приспособления имеющие насечку на прижимных губках;
-при закреплении на станке приспособлений и обрабатываемых деталей пользоваться только специально предназначенной - рукояткой либо исправными стандартными ключами соответствующими размерам гаек и головок болтов;
-подачу детали к фрезе производить только тогда когда фреза получила рабочее вращение;
-при смене обрабатываемой детали или ее измерении отвести фрезу на безопасное расстояние и выключить подачу;
-не допускать скопления стружки. Удалять стружку следует только после полной остановки шпинделя специальными крючками с защитными чашками и щетками-сметками;
-не допускать уборщицу к уборке у станка во время его работы;
-остановить станок и выключить электрооборудование в следующих случаях:
-уходя от станка даже на короткое время;
-при временном прекращении работы;
-при перерыве в подаче электроэнергии;
-при уборке смазке чистке станка;
-при обнаружении какой-либо неисправности которая грозит опасностью;
-при подтягивании болтов гаек и других крепежных деталей.
Во время работы на станке зуборезчику запрещается:
-работать на станке в рукавицах или перчатках а также с забинтованными пальцами без резиновых напальчников;
-брать и подавать через работающий станок какие-либо предметы подтягивать гайки болты и другие соединительные детали станка;
-обдувать сжатым воздухом из шланга обрабатываемую деталь;
-на ходу станка производить замеры проверять рукой чистоту поверхности обрабатываемой детали;
-тормозить вращение шпинделя нажимом руки на вращающиеся части станка;
-пользоваться местным освещением напряжением выше 42 В;
-охлаждать инструмент с помощью тряпок и концов;
-во время работы станка открывать и снимать ограждения и предохранительные устройства;
-удалять стружку непосредственно руками и инструментом;
-оставлять ключи приспособления и другие инструменты на работающем станке;
-находиться между деталью и станком при установке детали грузоподъемным краном.
Требования безопасности в аварийных ситуациях
В случае поломки станка отказа в работе пульта управления фрезеровщик должен отключить станок и сообщить об этом мастеру.
В случае загорания ветоши оборудования или возникновения пожара необходимо немедленно отключить станок сообщить о случившемся администрации и другим работникам цеха и приступить к ликвидации очага загорания.
В случае появления аварийной ситуации опасности для своего здоровья или здоровья окружающих людей следует отключить станок покинуть опасную зону и сообщить об опасности непосредственному руководителю.
Требования безопасности по окончании работы
По окончании работы зуборезчик обязан:
-выключить станок и электродвигатель;
-привести в порядок рабочее место:
-убрать со станка стружку и металлическую пыль;
-очистить станок от грязи;
-аккуратно сложить заготовки и инструменты на отведенное место;
-смазать трущиеся части станка;
-сдать станок сменщику или мастеру и сообщить обо всех неисправностях станка;
-снять спецодежду и повесить ее в шкаф вымыть лицо и руки теплой водой с мылом или принять душ.
Курмаз А.М. Металлорежущие станки А.М. Кучер М.М. Киватицкий А.А. Покровский. – М.: Машиностроение 1972. – 308 с.:ил.
Металлорежущие станки: Учебник П.И. Ящерицын В.Д. Ефремов; под ред. А.И. Кочергина. – Мн.:БГАТУ2001. – 446 с.:ил.
Детали машин. Проектирование: Справочное учебно-методическое пособие Л.В. Курмаз А.Т. Скойбеда. - 2-е изд. испр.:М.:Высш. Шк.2005. – 309 с.:ил.
Спецификация для общего вида станка
Спецификация для делительной бабки
kin.dwg

rrsrer-rrer2.dwg

Число зубьев нарезаемого колеса
Угол делительного конуса нарезаемых колёс
Наибольшая длина зуба
Наибольшая длина хода резцов
Число двойных ходов резцов в минуту
Расстояние от торца шпинделя делительной
бабки до центра станка
затрачиваемое на обработку одного
Наибольшая длина хода ползунов
Наибольшая высота обрабатываемого
Зубострогальный полуавтомат
rrrresrrsrrs-rrrryer.dwg

Обеспечить герметичность
Течь масла не допускается
Маркировать обозначение на табличке