Ремонт зубьев ковша экскаватора




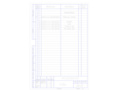
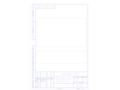
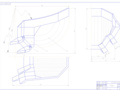
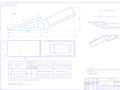
- Добавлен: 25.10.2022
- Размер: 3 MB
- Закачек: 1
Описание
Состав проекта
![]() |
![]() |
![]() ![]() ![]() ![]() |
![]() ![]() ![]() ![]() |
![]() |
![]() ![]() ![]() ![]() |
![]() ![]() ![]() ![]() |
![]() ![]() ![]() |
![]() ![]() ![]() ![]() |
![]() |
![]() ![]() ![]() |
![]() ![]() |
![]() |
![]() ![]() ![]() |
![]() ![]() ![]() |
![]() |
![]() ![]() ![]() |
![]() ![]() ![]() ![]() |
![]() |
![]() ![]() ![]() |
Дополнительная информация
Ковш.cdw

Зуб.cdw

Наплавка проволокой под слоем флюса
Электрошлаковая наплавка
Износ зуба по ширине
Наплавка под слоем флюса
Наплавка порошковой лентой
Техпроцесс восстановления:
наплавка (Деф.1;2); закалка (Деф.1;2); контроль
Сталь 110Г13Л ГОСТ 2176-77
Ресурс восстановленного зуба должен быть не менне 80% от
Остальные ТТ по СТБ 1014-95.
Зуб бракуется при изгибе и повреждении хвостовой части.
Схемы базирования зуба
-при наплавке режущей кромки
Ковш.cdw

Зуб.cdw

Наплавка проволокой под слоем флюса
Электрошлаковая наплавка
Износ зуба по ширине
Наплавка под слоем флюса
Наплавка порошковой лентой
Техпроцесс восстановления:
наплавка (Деф.1;2); закалка (Деф.1;2); контроль
Сталь 110Г13Л ГОСТ 2176-77
Ресурс восстановленного зуба должен быть не менне 80% от
Остальные ТТ по СТБ 1014-95.
Зуб бракуется при изгибе и повреждении хвостовой части.
Схемы базирования зуба
-при наплавке режущей кромки
Спецификация.cdw

ДП.0312-псм-1062.005.001
ДП.0312-псм-1062.005.002
ДП.0312-псм-1062.005.003
ДП.0312-псм-1062.005.004
Планировка цеха для ремонта.cdw

Зуб.dwg
Наплавка проволокой под слоем флюса
Электрошлаковая наплавка
Износ зуба по ширине
Наплавка под слоем флюса
Наплавка порошковой лентой
Техпроцесс восстановления:
наплавка (Деф.1;2); закалка (Деф.1;2); контроль
Сталь 110Г13Л ГОСТ 2176-77
Ресурс восстановленного зуба должен быть не менне 80% от
Остальные ТТ по СТБ 1014-95.
Зуб бракуется при изгибе и повреждении хвостовой части.
Схемы базирования зуба
-при наплавке режущей кромки
Спецификация.dwg
ДП.0312-псм-1062.005.001
ДП.0312-псм-1062.005.002
ДП.0312-псм-1062.005.003
ДП.0312-псм-1062.005.004
Спецификация.cdw

ДП.0312-псм-1062.005.001
ДП.0312-псм-1062.005.002
ДП.0312-псм-1062.005.003
ДП.0312-псм-1062.005.004
Планировка цеха для ремонта.cdw

ПЗ.docx
Федеральное государственное бюджетное агентство железнодорожного транспорта
Федеральное государственноебюджетное учреждениевысшего профессионального образования
«Дальневосточный государственный университет
Кафедра: «Транспортно-технологические комплексы»
по дисциплине: «Технология машиностроения и ремонт машин»
На тему: «Ремонт зубьев »
Аналитический обзор ..
Технологический контроль чертежа детали и анализ технологичности конструкции .
Материалы для наплавки 3.1 Технология 3.2 Механизированная наплавка ..3.3 проверка качество наплавки 3.4 Режим наплавки 3.5 Техника наплавки 3.6 Оборудование для наплавки 3.7 Аппараты для наплавки ..3.8 Организация рабочего места ..
Зубья ковшей одноковшовых экскаваторов .
Экономическая часть ..
Техника безопасности .
В практике эксплуатации путевых машин большую роль играют кюветоочистительные машины (КОМ-300) машины для вырезки балласта (МВБ) уборочные машины (УМ-С) машины для нарезки кюветов и т.д. рабочим органом которых является роторное колесо с ковшами. С целью повышения производительности целесообразно модернизировать привод и конструкцию ротора. Известно широкое применение роторных экскаваторов на открытых горных разработках месторождений полезных ископаемых. По процессу выемки в наибольшей степени соответствуют условиям работы путевых машин добычные роторные экскаваторы применяемые на разработке огнеупорных глин.
В металлургии важное место занимает производство огнеупорных изделий (своды печей огнеупорный кирпич и т.п.). Для их изготовления требуется огнеупорное сырье. Месторождение огнеупорного сырья представляет собой сложно структурный пласт. Эффективная разработка такого пласта достигается только с применением роторных экскаваторов.
В связи с этим возникает актуальная проблема модернизации роторных экскаваторов
Экскаваторы – один из основных механизмов для выполнения строительных работ. Существует много разных видов экскаваторов: с малой вместимостью ковша экскаваторов на автошасси гидравлических 3-й размерной группы гусеничные экскаваторы и другие. Современный экскаватор - это не просто землеройная машина а многофункциональный комплекс способный выполнять очень широкий спектр общестроительных и дорожных работ а также мелиоративных металло- и лесозаготовительных мусороперерабатывающих сельскохозяйственных и т.д. Гусеничные экскаваторы успешно работают на сносе зданий и при аварийно-спасательных работах.Роторные экскаваторы относятся к экскаваторным машинам непрерывного действия. Рабочим органом такого экскаватора является роторный ковш то есть непрерывно вращающийся барабан с размещенными на нем ковшами которые в одной точке цикла вращения зачерпывают сыпучие породы а в противоположные выгружают их на транспортерную ленту по которой породы перемешаются к отгрузочному сектору. Диаметры роторных барабанов могут колебаться от двух до восемнадцати метров. Большинство роторных экскаваторов оснащаются гусеничным ходом а особенно крупные экскаваторы имеют железнодорожный ход. Производительность роторного экскаватора может достирать пятнадцати тысяч кубометров в час. Роторные экскаваторы в большинстве случаев работают в карьерах для добычи рыхлых пород и пород средней крепости. Роторные экскаваторы предназначенные для карьерной добычи угля способны создавать большое усилие резания. Условия залегания глин и каолинов определяют специфику работы добычных роторных экскаваторов и особые требования к их конструкции. Должна быть обеспечена полнота выемки сортовых слоев марок огнеупорных глин и каолинов с минимальным засорением разубоживанием и технологическими потерями особенно на контактах с почвой и кровлей а также при удалении прослоек песка и некондиционных слоев.Предлагается следующая классификация основных месторождений огнеупорного сырья:
Сложное строение пласта с 4-6 и более литологическими разновидностями сложным напластованием и переменной мощностью слоя.
Менее сложное строение пласта с 2-4 литологическими разновидностями.
Простое строение пласта полезного ископаемого с одним или двумя литологическими разновидностями выдержанной мощности и преимущественным распространением одного сорта.
Селективная разработка пласта огнеупорного сырья с применением роторных экскаваторов в зависимости от сложности строения продуктивной толщи может осуществляться горизонтальными стружками вертикальными однорядными стружками вертикальными многорядными стружками.На месторождениях первых двух типов разработку забоя ведут роторными экскаваторами горизонтальными стружками так как этот способ является наиболее приемлемым для раздельной разработки маломощных пластов. Третий тип месторождений разрабатывают одноковшовыми экскаваторами.Разработка забоя горизонтальными стружками заключается в том что исполнительным органом в забое пласта последовательно вынимаются горизонтальные стружки. Основные достоинства этого способа - низкий процент смешивания сортов сырья и меньшая длина суммарного пути перемещений ротора. К недостаткам этого способа следует отнести уменьшение обрабатываемой высоты уступа то есть максимальная высота подъема стрелы используется более эффективно при разработке вертикальными стружками.Многолетний опыт подтверждает что наиболее эффективными выемочно-погрузочными машинами на карьерах огнеупорных глин и каолинов являются роторные экскаваторы. Решающими преимуществами роторных экскаваторов перед одноковшовыми а также перед другими механизмами (бульдозеры скреперы и пр.) являются следующие: высокая производительность относительно небольшая металлоемкость возможность селективной разработки пластов сложного строения приспособленность рабочего оборудования к частым изменениям мощности пласта и отдельных его слоев возможность применения в непрерывно-поточных технологических схемах позволяющих автоматизировать процесс производства.Отечественной промышленностью выпускаются роторные экскаваторы на базе дизель-электрических одноковшовых экскаваторов четвертой и шестой размерных групп для разработки грунта выше уровня стоянки до 75 м. и ниже этого уровня до 35 м. при радиусе копания до 115 м и технической производительности в грунтах I категории до 550 м3ч. По удельной энергоемкости эти машины находятся на уровне лучших экскаваторов непрерывного действия (022 024 кВт-чм3) но уступают им по удельной материалоемкости (100 140 кгч). От базовых одноковшовых экскаваторов в конструкциях роторных стреловых экскаваторов сохраняются ходовые и опорно-поворотные устройства частично или полностью платформу на которой располагают силовую дизель-генераторную установку (обычно в хвостовой части платформы с целью ее уравновешивания) насосную станцию механизмы поворота кабину с органами управления и две стойки-пилоны. В верхней части пилонов шарнирно закрепляют стрелу с ротором на конце и приемным ленточным конвейером расположенным вдоль стрелы. Для работы на уступах различных уровней стрела может поворачиваться относительно шарнира на пилоне в вертикальной плоскости посредством гидроцилиндра. Ротор с ковшами и тарельчатым питателем приводится во вращение от электродвигателя через систему карданных валов и зубчатых передач а приемный конвейер — мотор-барабаном. Последний представляет собой барабан со встроенным в него электродвигателем и зубчатым редуктором. Отвальный конвейер опирается на центрально установленный подпятник с индивидуальным электрическим приводом обеспечивающим конвейеру независимый поворот в плане относительно поворотной платформы. Вертикальное положение отвального конвейера в зависимости от высоты разгрузки регулируют гидроцилиндром шарнирно закрепленным на кронштейнах стоек-пилонов с возможностью соосного вращения с отвальным конвейером. Привод отвального конвейера осуществляется мотор-барабаном на его дальнем конце.Дли работы верхним копанием (выше уровня стоянки экскаватора) машину располагают перед забоем на расстоянии вылета стрелы. Отвальный конвейер устанавливают по высоте и в плане в положение разгрузки. Вертикальными перемещениями стрелы при вращающемся роторе последний заглубляют в грунт на высоту уступа. Фиксируя в этом вертикальном положении стрелу одновременным поворотом платформы и вращением ротора при движении ковшей снизу вверх разрабатывают грунт отделяя его от массива вынося ковшами вверх и разгружая на тарельчатый питатель выполненный в виде наклонного вращающегося диска. С помощью скребка грунт ссыпается с тарельчатого питателя на приемный ленточный конвейер транспортируется им и перегружается в центральной части поворотной платформы на отвальный конвейер которым выносится и разгружается в транспортное средство или в отвал. При разгрузке в транспортные средства положение отвального конвейера в плане неизменно а при разгрузке в отвал конвейер может находиться в одном положении или поворачиваться для распределения отсыпанного грунта ровным слоем в пределах отведенной полосы. В конце поворотного перемещения платформы ограниченного шириной захватки забоя ротор со стрелой опускают до уровня следующего уступа и реверсивным движением поворотной платформы при прежнем направлении вращения ротора повторяют экскавацию грунта. После разработки последнего уступа чаше всего соответствующего уровню стоянки экскаватора машину переметают в направлении к забою на новую стоянку и повторяют землеройный процесс.Для работы нижним копанием ковши на роторе переставляют поворачивая их на 180о для возможности разработки грунта вращением ротора в направлении обратном прежнему направлению. Опустив стрелу экскавацию грунта осуществляют по описанной выше схеме для верхнего копания. Для надежного транспортирования грунта круто наклоненным приемным конвейером используют прижимной конвейер который устанавливают над приемным конвейером. Грунт перемешается между лентами двух конвейеров движущимися в одном направлении.Для добычи полезных ископаемых открытым способом а также для вскрышных работ применяют мощные роторные комплексы производительностью до 5000 м3ч в составе роторного экскаватора и накопительно-перегрузочных устройств с железнодорожными или автомобильными транспортными средствами на карьерно-добычных работах или транспортного отвального оборудования непрерывного действия на вскрышных работах. По своей структуре эти экскаваторы сходны с описанными выше строительными экскаваторами но отличаются от них размерами и конструктивными решениями отдельных узлов. Фактическая эксплуатационная производительность этих комплексов в значительной мере зависит от типа транспортных средств которыми в основном определяются размеры вынужденных простоев экскаватора меньшие для отвального оборудования непрерывного действия и большие для железнодорожного транспорта особенно одноколейного.
Технологический контроль чертежа детали и анализ технологичности конструкции.
Роторный траншейный экскаватор (рис. 1 а) состоит из гусеничного тягача 1 и навесного рабочего органа для рытья траншей и отброса грунта шарнирно соединенных между собой в вертикальной плоскости. Рабочий орган машины - опирающийся на четыре пары роликов 13 жесткий ротор 12 с 14-ю ковшами 11 внутри которого помещен поперечный двухсекционный ленточный конвейер 10 состоящий из горизонтальной и наклонной (откидной) секций. Позади ротора установлен зачистной башмак 9 для зачистки и сглаживания дна траншей. У тягача уширен и удлинен гусеничный движитель для повышения устойчивости и проходимости машины и исключения возможного обрушения стенок траншеи при движении над ней тягача.
Рисунок 1. Роторный траншейный экскаватор
В трансмиссию тягача включен гидромеханический ходоуменьшитель для бесступенчатого регулирования рабочих скоростей движения машины при копании траншей. На тягаче установлена
дополнительная рама 2 с размещенными на ней механизмами привода 7и подъема-опускания рабочего органа. Рама имеет две наклонные направляющие 14 по которым с помощью пары гидроцилиндров 3 и двух пластинчатых цепей 4 гидравлического подъемного механизма перемещаются ползуны 15 переднего конца рамы 8 рабочего органа при переводе его из транспортного положения в рабочее и наоборот. Подъем-опускание задней части рабочего органа (рис. 1 б) осуществляются парой гидроцилиндров 5 штоки которых шарнирно прикреплены к верхней части стоек 16 связанных с задним концом рамы 8 цепями 6. При копании траншеи задняя часть рабочего органа находится в подвешенном состоянии Установка откидной части ленточного конвейера в наклонное рабочее положение и опускание ее при транспортировке машины производятся гидроцилиндром 19 через полиспаст 17 с траверсой 18. Изменением угла наклона откидной части конвейера достигается различная дальность отброса грунта в сторону от траншеи.
Роторное колесо (рис. 2) состоит из двух кольцевых обечаек 6 связанных между собой ковшами 1 и поперечными стяжками 3. Каждый ковш открыт с двух сторон и имеет в передней части карманы 4 для крепления сменных зубьев 5 а в задней - цепное днище 2 способствующее лучшей разгрузке ковша особенно при разработке вязких и увлажненных грунтов. С наружной стороны колец ротора приклепаны секции круговых зубчатых реек 7 находящиеся в постоянном зацеплении с двумя ведущими шестернями 8 механизма привода роторного колеса. В зависимости от грунтовых условий ковши ротора оснащаются сменными зубьями-клыками двух типов: с наплавкой передней режущей грани для разработки не мерзлых грунтов и армированных твердосплавными износостойкими пластинами для мерзлых. Специальная расстановка зубьев на ковшах позволяет вести разработку тяжелых и мерзлых грунтов крупным сколом и обеспечивает хорошую наполняемость ковшей при работе в легких грунтах.
Рисунок 2. Ротор экскаваторов ЭТР-223А ЭТР-224А
Привод ходового устройства экскаватора при движении на рабочих скоростях осуществляется от гидромеханического ходоуменьшителя включающего насос 8 (рис. 3) переменной производительности гидромотор 12 и понижающий редуктор. Гидрообъемный привод ходоуменьшителя выполнен по схеме гидронасос - гидромотор. Вращение от гидромотора через понижающие передачи раздаточного редуктора 7 передается сначала на средний а затем на нижний валы коробки передач 2 тягача далее через коническую передачу 20 бортовые фрикционы 3 и бортовые редукторы 4 на ведущие звездочки 21 гусеничного движителя.
Рисунок 3. Кинематическая схема экскаваторов ЭТР-223А ЭТР-224А
Скорость рабочего хода в диапазоне 10 300 мч регулируется изменением производительности насоса 8. При передвижении машины на
транспортных скоростях (15 62 кмч) крутящий момент от дизеля 1 передается ведущим звездочкам 21 гусениц 5 через главную муфту сцепления тракторную коробку передач 2 коническую пару 20 бортовые редукторы 4 и фрикционы 3. Привод ротора 74осуществляется от вала отбора мощности тягача через раздаточный редуктор 7 конический редуктор 10 с дифференциальным механизмом цепные шарнирные передачи 11 и консольные одноступенчатые редукторы 12. От редуктора 12 движение передается полувалам привода ротора на которых закреплены приводные шестерни 18 зацепляющиеся с зубчатым венцом 15 ротора.В трансмиссию привода ротора включена предохранительная муфта 9 предельного момента.Роторное колесо может вращаться с двумя скоростями (013 и 016 с-1) вперед и с одной скоростью назад. Пониженная частота вращения ротора необходима при разработке талых грунтов с крупными каменистыми включениями и мерзлых грунтов. Привод верхнего и нижнего барабанов отвального конвейера 13 обеспечивается индивидуальными гидромоторами 16 питающимися через гидрораспределитель от насоса 6. Для натяжения ленты конвейера барабаны снабжены винтовыми натяжными устройствами 17.
Материалы для наплавки.
Получение нужных физических свойств наплавленного металла определяется главным образом применяемыми при наплавке материалами. Электродные материалы наплавочные порошки флюсы защитные газы.
Электроды для ручной дуговой наплавки. Химический состав и диаметр электродного стержня масса и химический состав покрытия определяют механические свойства наплавленного металла технологические свойства электродов режимы наплавки.Для ручной дуговой наплавки поверхностным слоем с особыми свойствами применяют электроды по ГОСТ 10051-75. Кроме этого могут применяться электроды для сварки конструкционных и теплоустойчвых сталей по ГОСТ 9467-75 в также электроды для сварки высоколегированных со особыми свойствами по ГОСТ 10052-75. Некоторые марки специальных электродов для наплавки чугуна и цветных металлов (меди бронз алюминия и др.) выпускаются промышленностью по техническим условиям. Сварочно – технологические свойства и общая характеристика наиболее распространенных марок электродов приведены в Таблице 3.
Сварочно-технологические свойства электродов для ручной наплавки.
Наплавочная проволока. Наиболее распространенным материалом для механизированной электродуговой наплавки является стальная наплавочная проволока сплошного сечения по ГОСТ 10543 – 75. Стандартом предусмотрено 9 марок углеродистой 11 марок легированной и 10 марок высоколегированной проволоки.Для механизированной наплавки применяют также стальную сварочную проволоку по ГОСТ 2246 – 70. Этот стандарт предусматривает 6 марокнизкоуглеродистой 30 марок легированной и 41 марку высоколегированной проволоки.Для наплавки бронзы применяют проволоку по ГОСТ 16130 – 72. Проволоку из алюминиево-железистой бронзы БрАЖМц 10-3-15 алюминиево-марганцовистой бронзы БрАМц 9-2 кремниево-марганцовистой бронзы БрКМц 3-1 используют для наплавки под флюсом АН-2- и АН-60 слоя бронзы на стальную основу при изготовлении биметаллических деталей металлургического оборудования работающих в качестве пар трения например сухарей и камней шпиндельных соединений привода валков прокатных станов.
Флюсы и защитные газы. Флюсы подразделяют по их назначению способу изготовления химическому составу строению частиц. Различают флюсы общего назначения и специальные. Первые используют для механизированной дуговой наплавки углеродистых и низколегированных сталей вторые – для дуговой и электрошлаковой наплавки легированных сталей и сплавов цветных металлов.Плавленые флюсы изготовляют плавлением шихты в электрических или пламенных печах с последующим гранулированием расплава мокрым или сухим способом. Исходные материалы для производства плавленого флюса: кварцевый песок марганцовая руда глинозем плавиковый шпат полевой шпат магнезит и т. П. Для изготовления керамических флюсов применяют смеси порошкообразных материалов замешанных на жидком стекле и гранулированных до заданной фракции с последующей сушкой и прокалкой.
Для дуговой автоматической наплавки углеродистой и низколегированной проволокой используют плавленые высококремнистые марганцевые флюсы АН-348А АН-348АН ОСЦ-45М АН-60 ФЦ-9. Для дуговой наплавки легированной и высоколегированной проволокой и лентой применяют плавленые низколегированные флюсы АН-20С АН-20СМ АН-20П АН-60 АН-22 АН-26 АН-30 АН-70 48-ОФ-6. Для получения легированной и высоколегированного наплавленного металла применяют углеродистую электродную проволоку Св-08 в сочетании с керамическими флюсами типа ЖСН или АНК. Для электрошлаковой наплавки используют флюсы АН-348А Ан-8. Для наплавки высококремнистых чугунов используют безмарганцевые флюс Ан-28 наплавку медными сплавами выполняют под флюсом АН-60 АН-348А. Защитные газы выпускают по ГОСТ 10157 – 79 (аргон); ГОСТ 20461 – 75 (гелий); ГОСТ 9293 – 74 (азот) и поставляют в стальных баллонах соответствующей окраски.
Неплавящиеся электроды. Неплавящиеся электроды из вольфрама а также из специального электротехнического угля и синтетического графита. В качестве вольфрамовых электродов применяют прутки из чистого вольфрама и из вольфрама с присадками оксидов лантана тория иттрия при этом обеспечиваются эмиссионная способность и устойчивость дугового разряда повышается стойкость электродов (табл. №4).
Характеристика прутков из вольфрама.
Технические условия
Тарированный вольфрам
Лантарированный вольфрам
Иттрированный вольфрам
При наплавке вольфрамовыми электродами для защиты их от окисления применяют инертные газы (аргон гелий) и их смеси между собой или с активными газами (кислород углекислым газом водородом азотом). Вольфрамовые электроды используют при дуговой наплавке в защитном газе плазменной наплавке плазменном напылении.Электроды из вольфрама изготовляют методом волочения или ковки с последующем шлифовании до нужного диаметра. Наплавку вольфрамовыми электродами проводят постоянным или переменным током прямой полярности что обеспечивает их минимальный расход. С этой же целью осуществляют мероприятия исключающие применения защитного газа высокой влажности возбуждение дуги непосредственным замыканием электрода на изделия ( возбуждать дугу следует только с помощью осциллятора) окисление электрода воздухом (подучу защитного газа необходимо начинать до включения тока а прекращать после его включения и остывания электрода до потемнения). При наплавке переменным током конец электрода затачивают в виде сферы при наплавки постоянным током – в виде конуса.При наплавки торрированными электродами следует выполнять санитарные нормы и правила работы с радиоактивными веществами. Угольные электроды для наплавки изготовляют из электротехнического угля в соответствии с ГОСТ 10720 – 75. Стандартом предусмотрены электроды марки СК имеющие круглое сечение диаметром 4 6 8 10 15 18 мм и длину 250 мм с омедненной и неомедненной поверхности. В отличие от вольфрама угольные электроды имеют низкую теплопроводность. По сравнению с угольными графитовые электроды обладают большой стойкостью против окисления при высоких температурах.
Ручная наплавка. Ручная наплавка износостойких сплавов на рабочие органы мелиоративных машин из-за универсальности и простоты широко распространена на ремонтных и эксплуатационных предприятий.Электродуговая наплавка. При такой наплавке между электродом и деталью возникает электрическая дуга. Под действием выделяемой ею теплоты подплавляются поверхность детали и присадочный металл которые прочно соединяются и затем кристаллизуется.В качестве электродов применяют плавящиеся сплошные или трубчатые металлические стрежни и неплавящиеся вольфрамовые угольные и углеродные электроды. Плавящиеся электроды обычно выпускают диаметром от 3 до 6 мм.При использовании сплошным металлическим стержнем легированием наплавленного металла происходит или за счет легирующих элементов содержащихся в самом стержне или за счет легирующих элементов находящихся в их обмазке. Диаметр электрода выбирается в зависимости от толщины наплавляемой детали. Так для деталей толщиной 1-2 3-5 4-10 10-24 мм и более берут электроды диаметром соответственно 2-3 3-4 4-5 и 5-7 мм. В случае применение трубчатых электродов легирующие элементы располагаются во внутренней полости трубки. Зона наплавочной дуги защищена от кислорода и азота воздуха веществами находящимися в обмазке электродов. Питание электрической дуги может быть как от переменного так и от постоянного тока. Дуга на постоянном токе более устойчива. Для уменьшения глубины проплавления основного металла при наплавке постоянным током применяют обратную полярность. Для повышения производительности пользуются прямой полярностью. При наплавке особенно износостойких материалов типа рэлит и вокара пользуются металлическим электродом и присадочным прутком ( Рис.1 ).
Рис.1 Наплавка специальным металлическим электродом и присадочным прутком 1 – присадочный пруток; 2 – основной электрод; 3 - наплавленный слой; 4 – основной металл.
При наплавке переменным током на обоих полюсах электродуги выделяется приблизительно одинаковое количество теплоты. Для получения широкого валика электроду сообщают сложное движение. Валикрекомендуется делать шириной не более 25 диаметр электрода. Угол наклона электрода к наплавляемой поверхности 45 градусов. Длину дуги устанавливают приблизительно равной диаметру электрода. Если длина дуги больше такую дугу называют длинной меньше – короткой. С сокращением длины дуги уменьшается потери теплоты и соответственно повышается производительность наплавки. Режимы на различные виды сталей приведены в таблице 5. В среднем плотность тока поддерживают 11 – 12 Амм2.
Режимы наплавки плавящимися электродами.
Значение характеристик при диаметре электрода мм
Неплавящиеся графитовые и угольные электроды при наплавке применяют для легирования при помощи порошка или присадочного стержня. Порошок укладывают в валик шириной 30 – 50 мм и толщиной в 2 – 3 раза большей чем заданная толщина наплавляемого слоя уплотняют и выравнивают мерным шаблоном. Получаемый за один проход слой наплавленного металла должен быть толщиной не более 2 мм и шириной менее 50 мм. Допускается наплавлять не более двух-трех слоев.
При использовании неплавящихся электродов применяют постоянный ток плотностью 12 – 15 Амм2 для угольных электродов и 18 – 25 Aмм2 – для графитовых. На рисунке 2 показана схема наплавки угольным электродом. Диаметр неплавящихся электродов должен быть от 5 до 40 мм.
- слой порошка износостойкого сплаватолщиной 3 5 мм; 2 - слой прокаленной буры толщиной 02 03 мм; 3 - угольный электрод; 4 — слой наплавленного металла; 5 - наплавляемая деталь;А - общее направление наплавки.
Некоторые режимы наплавки этими электродами при постоянном токе прямой полярности приведены в таблице 6.
Режимы наплавки неплавящимся электродом.
Качество наплавленного слоя при использовании угольных и графитовых электродов недостаточно высокое из-за окисления легирующих элементов образование пор внедрения в наплавленный слой неметаллических частиц и т. п. Поэтому рекомендуется применение вольфрамовых электродов и использование аргона для защиты зоны дуги. В этом случае можно применять горелки и прочее оборудование предназначенное для аргонодуговой сварки. Режим такой наплавки приведены в таблице 7.
Режимы аргонодуговой наплавки.
Диаметр присадочной проволоки мм
Сила сварочного тока А
При ручной наплавке стержневым и трубчатыми электродами один рабочий наплавляет за 1 час около 08 – 1кг сплава.Электродуговая наплавка металлическим электродом с присадочным прутком заключается в том что в зону электродной дуги вводят присадочный пруток. Его периодически прижимают к кромке электрода в результате чего дуга возникает не только между электродами и деталью но и между прутком и деталью. При этом способе производительность работы повышается на 30 – 40% (около 1 – 13 кгч) но при этом требуется ток повышенной плотности. Диаметр присадочного прутка должен быть на 1 – 2 мм больше диаметра электрода. Наплавка пучком электродов характеризуется тем что увеличивается количество одновременно расплавляемого электродного металла. Такая наплавка происходит под действием блуждающей дуги (рис.3).Электрическая дуга переходит с электрода на электрод несколько раз в секунду проплавления основного металла. Производительность этого способа 12 – 16 кгч.
Рис.3.Схема горения в пучке электродов : 12 и 3 – электроды.
При наплавке пучком электродов можно пользоваться как переменным так и постоянным током. Рекомендуется режимы и техникоэкономические показатели наплавки приведены в таблице 8 и 9.
Режимы наплавки пучком электродов.
Значение характеристики при электродов в пучке
Технико-экономические показатели наплавки пучком электродов.
Значение показателя при числе электродов в пучке
Производительность наплавки %
Газопламенная наплавка. Процесс осуществляется под действием теплоты выделяющейся при горении газа в струе кислорода. Основным газом служит ацетилен. В зависимости от соотношения газа и кислорода различают три вида пламени : нейтральное (избыток кислорода 10 – 30 %) окислительное (кислорода более 30%) науглероживающее (в смеси преобладает ацетилен). Производительность газопламенной наплавки 07 – 08 кгч. Способ применяют как правило для наплавки мелких деталей. При использовании присадочных прутков перед началом наплавки поверхность подогревают горелкой расположенной на расстоянии 15 – 20 мм. Затем горелку пододвигают на расстояние 3 – 5 мм и в зону пламени вводят присадочный пруток. В начале наплавки угол наклона горелки составляет 80 градусов в дальнейшем его несколько уменьшают. Схема газовой наплавки показана на рисунке 4.
Рис.4.Наплавка газовым пламенем:1 - наплавленный слой; 2 - присадочный пруток; 3 — газовая горелка; 4 - наплавляемая деталь; А — направление наплавки
Газовую грелку перемещают слева направо присадочный пруток следует за ней. Диаметр присадочного металла при толщине детали до 15 мм и 6 – 8 мм – при большей толщине. Применяют прутки из сплавов ЦС-1 рэлит вокара. Газопорошковая наплавка – разновидность газопламенной. При такой наплавке присадочный легированный порошок (например ФБХ-6-2 или сталинит) поступает в зону пламени через закрепленную на стволе горелки воронку в зависимости от давления кислорода. Горелку располагают под углом 80 градусов к наплавляемой поверхности. Зерна порошка должны быть размером 40 150 мкм и температурой плавления не выше 1200 1300 С. Высокой плотности наплавленного металла достигают при использовании нейтрального и науглероживающего пламени. Толщина наносимого за один проход слоя металла не должно превышать 1 мм.Плазменная ручная наплавка. При этом способе плазменную горелку перемещают слева направо перед присадочный пруток а дугу направляют на жидкую ванну металла и формирующийся наплавленный металл. Благодаря подобной схеме процесса обеспечивается хорошая защита расплавления основного металла. Толщина создаваемого за один проход слоя – от 05 до 6 мм при ширине валика от 8 10 мм (без поперечных колебаний горелки) до 25 мм (с поперечными колебаниями). Процесс проводят при силе тока 90 100 А .Метод рекомендуется использовать для наплавки композиционных сплавов.
2 Механизированная наплавка.
Легирование наплавленного металла при помощи флюсов. Легирование металла в этом случае осуществляется при автоматической и полуавтоматической электродуговой при ручной наплавке за счет перехода легирующих элементов из флюса и металла. От химического состава флюса и режима наплавки в значительной мере зависит содержание легирующих элементов образование карбидных композиций и пор в слое наплавленного металла формирование наплавленного валика и отделение шлаковой корки.Наплавку можно проводить металлическим электродом по слою шихты. Метод позволяет довести до 30% общее содержание легирующих компонентов в наплавленном металле. В первом случаи (рис.5а) наплавляемый участок засыпают толстым слоем (50 60 мм) гранулированного флюса оказывающего на расплавленный металл давление около 40 Па. Сквозь слой пропускают металлический электрод в виде одной или нескольких проволок диаметром 1 6мм или электродной ленты толщиной 04 1 мм и шириной 20 100 мм. Электродуга создается между электродом и деталью к которой подведен ток. Под действием дуги при движении электрода на поверхности изделия образуется валик расплавленного металла. Электродугой расплавляется нижний слой флюса. Создавшая полость горения с эластичной оболочкой из расплавленного флюса защищает расплавленный металл от кислорода и азота воздуха предупреждает разбрызгивание и уменьшается теплопотери. Этим способом можно наплавлять слой металла толщиной до 4 мм и более.
Рис. 5. Способы наплавки:а — под флюсом: 1 — электрод; 2 — ограничители; 3 — флюс; 4 — шлаковаякорка; 5 — наплавленный металл; 6 — деталь; 7 — путь движения электрода; б - угольным электродом по слою шихты: 1 — шихта; 2 — угольный электрод; 3 - слой наплавленного металла; 4 — приставные пластины.
Во втором случае (рис. 5 б) на деталь наносят легирующих шихту. Она расплавляется сверху электродугой образующейся между деталью и электродом. Этим способом можно наплавлять слои толщиной до 4 мм. Твердость и вязкость наплавленного слоя зависит т состава шихты.Неплавящиеся электроды изготавливают из вольфрама электротехнического угля и синтетического графита. Вольфрамы прутки выпускаются следующих наименований. Табл. 10.
Торированный вольфрам
Иттированный вольфрам
При работе с прутками ЭВТ необходимо соблюдать правила работы с радиоактивными веществами. Угольные электроды марки СК имеют круглое сечение и стандартные диаметры в 4 6 8 10 15 и 18мм при длине 250мм с омедненной и неомеднненой поверхностями. Эти электроды имеют более низкую по сравнению с вольфрамовыми теплопроводность. Графитовые электроды более стойки чем угольные к окислению при высоких температурах.
Способы расщепленной дуги и многоэлектродной наплавки (рис.6) характеризуется тем что дуга автоматически переходит с одной электрода на другой. Все электроды объединены общим токоподводом. По мере сгорания одного электрода и увеличение длины дуги она разрывается и мгновенно возникает на ближе расположенном к наплавляемой поверхности электроде. В результате перемещения дуги происходит рассеянное тепловложение в основной металл и обеспечивается незначительная глубина проплавления при достаточно высокой производительности процесса.
Рис. 6. Приспособление для многоэлектродной наплавки зубьев ковшей слоями металла шириной 120 мм: 1 — подставка; 2 - медная теплоотводящая планка; 3 - мундштук многоэлектродного аппарата; 4 - зуб.Силу постоянного тока обратной полярности в зависимости от диаметра электрода выбирают по таблице 11.
Режимы наплавки под флюсом.
Сила тока при наплавки А
Чем больше желаемая слоя тем больше следует выбирать диаметр электрода и силу тока. Благодаря многоэлектродной наплавке обеспечивает небольшая глубина и равномерность проплавления. Доля основного металла даже при интенсивных режимах не превышает 22 % тогда как после одноэлектродной наплавки она равна 60 70 %. При многоэлектродной наплавке сочетание электродов может быть различным что позволяет за один проход получать широкую полосу однородного металла или несколько рядом лежащих неоднородных полос. Угол наклона электрода для наплавки плоских поверхностей выбирают в пределах 30 – 50 градусах при этом вылет электрода должен быть больше так как в этом случае глубина проплавления уменьшается. Для электродов диаметром 2 – 3 мм вылет рекомендуется 20 – 30 мм диаметром 4 – 5 мм – 40 – 50 мм. При наплавке изношенной поверхности режимы процесса выбирают по таблице 12.
Режимы наплавки под флюсом изношенных поверхности.
Скорость подачи электрода мч
3 Проверка качества наплавки.
Основная причина появления дефектов в наплавленном слое – нарушение принятой технологии наплавки. Дефекты подразделяются на внутренние и наружные.Внутренние дефекты обнаружить наружным осмотром нельзя. К ним относятся непровар повышенная пористость наличие скрытых трещин и шлаковых включений значительный перегрев металла. Непровар – это отсутствие прочного сплавления между основным и наплавленным слоем или слоями металла. Этот дефект является следствием плохой подготовки наплавляемой поверхности в результате чего на ней остается ржавчина окалина жировые пятна грязь; недостаточной мощности электродуги; значительный колебаний силы тока и напряжения; плохого качества наплавочных материалов. Непровар на деталях подвергающихся абразивному изнашиванию под действием нагрузок высокой динамичности совершенно недопустим. По кромкам дефекта образуется концентрация напряжений приводящих к разрушению и отслаиванию наплавленного металла. Непровар устраняют вырубкой дефектных мест если это возможно и повторной наплавкой на заданных режимах.Поры образуется при быстром остывании наплавленного металла. В этом случае находящиеся в металле газы не выходят из него. Появлению пор способствует и образование усадочных раковин. Пористость металла отрицательно сказывается на его износостойкости особенно в условиях действия нагрузок высокой динамичности. Наплавленный слой интенсивно раскрашивается по всей своей толщине.
Поры в наплавленном металле появляется в следствие повышенной влажности флюса или электродных покрытий плохой подготовки наплавляемой поверхности недостаточной защиты наплавочной ванны и дуги от кислорода и азота воздуха высокого содержания углерода в наплавленном металле. Трещина – это местное тонкое разрушение наплавленного металла. Трещину нарушают в наплавленном слое сплошность понижает статическую и динамическую прочность слоя вследствие появлении локальных концентраций напряжения. Трещины образуются в результате увеличения глубины расплавления металла повышение интенсивности охлаждения в процессах наплавки углеродистых и конструкционных легированных сталей использования для наплавки легированных сталей электродов с высоким содержанием углерода наплавки при низких температурах. Перегрев наплавляемого металла способствует образование благоприятных структур в зоне сплавления металлов. Этот дефект можно устранить последующей термической обработкой всей наплавляемой детали.
Наружные дефекты Легко определяется визуально. К ним относятся незаваренные кратеры наплывы и прожоги наплавленного слоя а также деформации самой детали. Незаваренные кратеры на наплавленной поверхности является следствием низкой квалификации исполнителя.Наплыв представляет собой избыток наплавленного металла. Причинами его образования считается снижение скорости наплавки увеличение длины дуги отклонение перемещения электрода от заданной траектории. Наплыв может повлечь за собой непровар наплавленного слоя поэтому дефект рекомендуется вырубать и повторно заплавлять. Прожог образуется при сквозном проплавлении детали. Дефект является следствием завышения силы тока уменьшения скорости наплавки использования электродов увеличенного диаметра плохой техники владения электродом. Место прожога заплавляют подкладывая под внутреннюю поверхность детали медную пластинку.Деформация детали происходит в результате неравномерного охлаждения и нагревания. Этот дефект может быть вызван различными нарушениями технологии наплавки лишнем количеством наплавленного металла. Для предотвращения деформация деталь рекомендуется держать в жестком кондукторе. Деформацию устраняют способом холодной или горячей правки.Для обеспечения высокого качества продукции устанавливают контроль за проведением всех подготовительных и основных технологических операций. Его подразделяют на предварительный технологический и контроль готовых изделий.
Предварительный контроль включает в себя проверку качества подготовки наплавляемой поверхности сравнение с данными сертификатов и паспортов характеристик наплавляемых материалов и флюсов контроль процесса сушки электродов и флюсов.Технологический контроль преследует цель систематической проверки всех звеньев технологического процесса наплавки детали. Особое внимание уделяют контролю: качество основного металла детали; соответствие марки качество электродов флюсов; качество подготовки под наплавку а также технического состояния применяемого оборудования; квалификация наплавщиков и соблюдение установленного технологического процесса и режимов наплавки ( сила тока напряжение и длина дуги ). Помимо этого проверяют установку наплавляемой детали в кондукторе или приспособления траектории движения заданной дуги подачи флюса и работу наплавочной установки или стенда. Контроль готовых изделий представляет собой определение качества работы. Контроль качества наплавленного металла выполняют следующими основными способами.Внешний осмотр проводят невооруженным глазом с помощью 6 – 20-кратной лупы а также с использованием различного рода шаблонов и мерного инструмента для контроля слоя наплавленного металла по толщине и конфигурации.Металлографические способы представляет собой изучение микро- и микрошлифов. Такими способами можно определять наличие внутренних дефектов глубину зоны термического влияния твердость различных составляющих и структуру наплавленных слоев.К недостаткам металлографических способов относятся необходимость полного или частичного разрушения контролируемого изделия и то что различного рода дефекты обнаруживаются только на рассматриваемой поверхности шлифа. Способы весьма дороги и связаны с трудоемким приготовлением макро- и микрошлифа. Механические испытания наплавленного металла сводятся в основном к определению его поверхностной твердости с помощью приборов Бринелля Роквелла и Виккерса. На больших деталях твердость устанавливают переносным прибором Польди. Микротвердость отдельных составляющих наплавленного металла оценивают на приборах ПМТ-3.
Методы дефектоскопии ( ультразвуковой магнитный индукционный и люминесцентный ) позволяют устанавливать качество наплавленного металла на своей глубине нанесенного слоя. Рекомендуется применять ультразвуковые дефектоскопы УЗД-7Н НИИМ-5 и УЗД-59. При общей оценке качества наплавочных работ следует руководствоваться ГОСТ 15467 – 79 “Качество продукции. Показатели качества и методы оценки уровня качества продукции”. Химический спектральный анализ дают возможность установить химический состав наплавленного металла. Для химического анализа необходимо 30 40 г стружки толщиной 15 мм. Выявленные дефекты устраняют обработкой с помощью абразивного круга затем заплавляют вручную. Число трещин в наплавленном на рабочие органы слое износостойкого материала должно быть оговорено В ТУ на их изготовление или ремонт. Не допускается отслоение и выкрашивание наплавленного слоя.
Электроды марки ГН – 1 со стержнем из сплава сормайт -1 используя для ремонта и изготовления быстроизнашивающихся детали засыпных аппаратов доменных печей а марки ЦС – 1 с таким же стержнем автогрейдеров и др. Литые стержни кроме того используется для аргонодуговой наплавки вольфрамовых электродов.Для уменьшения доли основного металла в наплавке применяют пониженный сварочный ток обеспечивающие устойчивое горение дуги. При однослойной наплавке использование таким режимом уменьшает долю основного металла до 03 – 045. При поперечном колебании электрода эта доля может быть уменьшина до 025.Для наплавки твердых сплавов применяют порошкообразные зернистые материалы например сталинит который приготовляют перемешиванием порошков феррохрома чугунной стружки и нефтяного кокса. Этот материал используют для наплавки ножей бульдозеров детали ковшей экскаваторов.Электрошлаковую наплавку зубьев ковшей экскаваторов была проведена с применением композиционных наплавочных материалов. В результате износостойкость увеличилась в 25 раза. Установлено что в зоне контакта зерен рэлита с матрицей происходит встречная диффузия и перерасприделение W и Cr с образованием карбидов что способствует повышению износостойкости матричного сплава. Расход рэлита составляет 5-7 % от объема наплавленного металла причем в зоне передней грани зуба находится 70 – 80 % общего количество введенных армирующих частиц. В другом случаи электрошлаковую наплавку зубьев проводили под флюсом АН-20 и АН-384А ( 1:1 ) в полупостоянной ( шамотной ) форме вольфрамовым электродами диаметром 5 мм и длиной 600мм. Наплавленный слой 5мм при толщине слоя шихты 10мм. Параметра режима : ток 300-350 А напряжение 28-30 В глубина шлаковой ванны 40-45мм. Источник питания – однофазный трансформатор ТС-500. Наработка зубьев ковшей экскаваторов наплавленных износостойкими соединениям ( на основе карбидов хрома боридов титана ) и электродами Т-590 составила соответственно 4238 и 1400 м3 на 1г износа. Износостойкость зубьев наплавленных тугоплавкими соединениями на основе карбида и хрома. Износостойкость зубьев при наплавке электродами Т-590 повышается в 3 раза.Параметрами режима наплавки является при ручной дуговой наплавки величина род и полярность тока диаметр электрода напряжение скорость наплавки величина поперечного колебания конца электрода а так же величина вылета электрода состав и толщина покрытия электрода положения в процессе наплавки.Напряжение при наплавке на глубину провара оказывает дополнительное влияние. Ширина наплавки связана с напряжением при увеличением напряжения ширина наплавки увеличивается.
Техника наплавки должна обеспечивать хорошее формирование наплавленного металла отсутствие в нем дефектов в минимальное проплавление основного металла и максимально возможную производительность процесса. Каждый вид наплавки имеет свои основные элементы режима влияющие на производительность и качество процесса. Для дуговой наплавки основными элементами режима являются сила тока напряжение и скорость перемещения дуги вылет и число электродов шаг наплавки а также смещение электрода с зенита при наплавке тел вращения.Наплавку обычно ведут на постоянном токе обеспечивающую высокую стабильность процесса. Ток дуги при наплавке зависит от скорости подачи электродной проволоки. С увеличением скорости подачи возрастает сила тока а следовательно и производительность наплавки. Однако с возрастанием тока дуги увеличиваются глубина проплавления и доля основного металла в наплавленном. Кроме того образуются узкие и высокие валики ухудшается формирование наплавленного металла. Поэтому ток дуги ограничивается условиями качества наплавки. Напряжение дуги определяет форму наплавленного валика. Повышение напряжения дуги увеличивает ширину и уменьшает высоту валика при этом возрастают длина дуги и окисляемость легирующих примесей особенно углерода. В связи с этим стремятся к минимальному напряжении которое должно согласовываться с током дуги. При очень малом напряжении дуги получается узкий и высокий валик с плохим формированием. Увеличением напряжения и уменьшение тока дуги усиливает взаимодействие шлака и металла повышает окисляемость углерода хрома титана и других легирующих элементов. Обычно наплавку ведут при напряжении дуги 28-32 В и сила тока 300-450 А для электродной проволоки диаметром 3-4мм. Скорость перемещения дуги влияющая на форму наплавленного валика и его формирование выбирают в пределах 20-40 мч. Вылет электрода – участок ограниченный нижней контактной точкой мундштука и дугой -принимают 30-40мм в зависимости от диаметра и материала электрода. Число электродов влияет на производительность процесса и форму ванны. При наплавке один и двумя электродами применяют обратную полярность (плюс на электроде) обеспечивающую оптимальное формирование наплавленного металла. Наплавку тремя и более электродами с целью повышения скорости их плавления осуществляют на прямой полярности. С увеличением числа электродов подаваемых в общую ванну растет ширина валика и уменьшается глубина проплавления.*ри наплавке лентой также достигается малая глубина проплавления а доля основного металла в наплавленном первом слое может быть снижена до 20 %. Для снижения доли основного металла в наплавленном уменьшают шаг наплавки.
6 Оборудование для наплавки.
Механизированную наплавку осуществляют с помощью установок в состав которых входит : наплавочные оборудование ( источники питания наплавочные аппараты аппаратура управления ) механическое сварочное оборудование ( манипуляторы механизмы крепления и перемещение наплавленного изделия и наплавочного аппарата ).
В качестве источников питания дуги при наплавке на переменном токе применяют сварочные трансформаторы при наплавки на постоянном токе дуговой наплавке под флюсом а также открытой дугой и в защитном газе применяют выпрямители и преобразователи тока.Для ручной дуговой наплавки используют источники переменного и постоянного тока однако в большой степени обеспечивают стабильность процесса и качество наплавки. Устойчивость процесса наплавки зависит в первую очередь от внешней характеристики источника питания – зависимости напряжения на его зажимах от тока нагрузки.Наиболее перспективными источниками питания постоянного тока являются полупроводниковые выпрямители. Их преимущество перед электромеханическими преобразователями весьма значительны и в основном сводится к таким показателями как экономичность надежность.
Трансформаторы для наплавки. Для ручной и механизированной наплавки применяют однофазные понижающие трансформаторы с воздушным охлаждением падающей или пологападающей характеристиками. К первой группе относятся трансформаторы с нормальным магнитным рассеянием и дополнительным индуктивным сопротивлением типа ТСД (рис. 7).
Рис. 7. Принципиальная электрическая схема трансформатора типа ТСД :1 - первичная обмотка; 2 - вторичнаяобмотка;3 - реактивная обмотка;4 - сердечник дросселя; 5 - привод перемещения сердечника; 6 - электрод;7 - наплавляемое изделие. Вторую группу составляют трансформаторы с увеличением магнитным рассеянием выполненные в одном корпусе ( СТШ ТДФ ТД ТС ). Технические характеристики приведены в таблице 13.
Технические характеристики сварочных трансформаторов.
Для электрошлаковой наплавки применяют одно или трехфазные трансформаторы с воденым или воздушным охлаждением (ТШС ТРКМ) и жесткой внешней характеристикой. Технические характеристики трансформаторов для электрошлаковой наплавки указаны в таблице 14.
Технические характеристики сварочных трансформаторов. Применяемых для электрошлаковой наплавки.
Пределы регулирования напряжения В
Выпрямители для наплавки. Основными элементами выпрямителей являются трансформатор с регулирующим устройством и блок вентилей селеновых или кремневых. В состав некоторых выпрямителей входит также дроссель предназначенный для улучшения процесса переноса электродного металла в дуге. В современных выпрямителей все более широкое применение находят транзисторы используемые для наплавленного регулирование тока и стабилизация выходных параметров источника.Наиболее распространенными выпускаемых промышленностью выпрямителях являются одно или трехфазное мостовые скемы двухпериодного выпрямления.Балласные реостаты. Для автоматической наплавки под флюсом можно применять многопостовые выпрямители и преобразователи с жесткой внешней характеристикой. В этом случае необходимые падающие внешние характеристики получают с помощью включения последовательно с дугой балласных реостатов. Схема включения многопостового преобразователя с балласным реостатами дона на рисунке 8.
Рис.8.Структурная электрическая схема балластного реостата РБ -501.
Технические характеристики балластных реостатов приведены в таблице 15.
Пределы регулирования
7 Аппараты для наплавки.
Механизированную наплавку осуществляет с помощью обычных сварочных аппаратов или специализированных полуавтоматов и автоматов обладающими определенными технологическими возможностями. Специализированные аппараты для наплавки должны обеспечивать: возможность выполнения широкослойной наплавки ( лентой расщепленным электродом колеблющимся в поперечном в поперечном направлении электродом );подачу специальным порошковой проволоки или порошковой лентой с большим содержанием легирующих элементов; регулирование доли основного металла в наплавленном слое; длительную бесперебойную работу для нанесения на поверхность изделия большого кол-ва металла.Полуавтоматы для наплавки. Полуавтоматы обеспечивает механизированную автоматическую подачу электродной проволоки все остальные движения необходимые для осуществления процесса наплавки выполняются в ручную. Полуавтомат сочетает в себе преимущества автомата с маневренностью электродержателя для ручной наплавки. Хорошее саморегулирования дуги при наплавке тонкой проволокой на больших плотностях тока позволяет легко компенсировать случайные изменения длины дугового промежутка вызванные неточностью ручного перемещения горелки полуавтомата. Основными элементами полуавтомата являются падающий механизм глубокий направляющий канал с ручной горелкой катушка с проволокой источник питания с пуско-легулирующей аппаратурой. Рисунок 9.
Рис.9 Полуавтомат А-1197:1- горелка; 2- подающий механизм; З - катушка для проволоки; 4- тележка.
8 Организация рабочего места.
Высокая производительность и качество ремонтных работ определяется рациональной организацией как рабочих мест наплавщиков так и всего участка. Рабочее место наплавщика огораживается стенками из непрозрачного и негорючего материала. Оно должно быть удобным для работы и отвечать всем требованиям безопасности труда. Рабочее место должно быть оборудовано столом-верстаком стулом а так же всем необходимым вспомогательным оборудованием ( манипуляторами позиционерами кантователями держателями приспособлениями и т. п.).В набор обязательно оборудования рабочего места наплавщика входят: шкаф для хранения личного инструмента и документации ( технологических карт чертежей справочных материалов инструкций и т. п. ); емкости для хранения наплавочных материалов ( электродов лент флюсов порошков ); набор электродержателей соединенных с отрезками медного кабеля длиной не менее 15м; набор слесарного инструмента ( кувалда молоток зубило напильник плоскогубцы стальные щетки электрический или пневматический инструмент необходимый измерительный инструмент ); передвижные для защиты от воздействия лучистой энергии и брызг расплавленного металла. Площадь рабочего места наплавщика должна составлять не менее 4 – 5 м2. Пол кабины делается из огнестойкого материала. В процессе работы а также после окончания рабочей смены рабочего места наплавщика следует убирать.
Расстановка наплавочного оборудования должно быть проведена в соответствии с правилами : расстояние между передвижными агрегатами и преобразователями – не менее 08 м между ними и стенами – преобразователями – 15 м ; проходы между сварочными трансформаторами – не менее 03 м между стеной и сварочным трансформатором – 05 м. Стеллажи и прочее оборудование должны отстоять от крупногабаритных наплавляемых деталей не менее чем на 1 м. Вокруг автоматических наплавочных установок предусматривается свободное пространство шириной 15 м.Освещенность рабочего места должна быть 50 лк при использовании ламп накаливания и 150 лк – люминесцентных. Стены участка окрашивают в светлые тона для снижения контраста с электродугой. Для того чтобы стены не отражали вредно действующие на человека ультрофеолетовые лучи возникающие при горении электрической дуги в краску для стен добавляют окись цинка титановые белила желтый крон. Недостаточная освещенность приводит к общей физической усталости притупляется внимание снижается производительность и качество работы.Прочно-вытяжные вентиляция необходима в помещении наплавочного участка. Расход воздуха должен быть не менее 40 м3ч на каждого рабочего. Вентилятор располагают так чтобы рабочий находился вне потока отсасываемых газов.Спецодежда наплавщика должна содержаться в порядке. Ее необходимо регулярно чистить.Индивидуальные щитки и маски массой не более 06 кг служат для защиты глаз и лица от излучения электрической дуги искр и брызг расплавленного металла. Изготовление щитков и масок регламетировано ГОСТ 12.4.035 – 78. Применяемые в них светофильтры марок Э-1 Э-2 Э-3 и Э-4 предназначены для работы соответственно с токами 30 – 75 75 – 200 200 – 400 и более 400 А. Рабочие занятые на вспомогательных работах применяют светофильтры В-1 В-2 и В-3. Для защиты светофильтров от брызг раскаленного металла щитки и маски комплектуются сменными стеклами.
Зубья ковшей одноковшовых экскаваторов.
Зубья изнашиваются до предельного значения при наиболее жестких условиях работы (разработка мерзлого грунта скальных пород) за 3 4 суток а в легких условиях их ресурс составляет 4 месяца и более.Форма износа зубьев ковшей сохраняется в течение всего времени работы зуба и зависит от типа грунта. На мелкодисперсных грунтах обладающих высокой абразивностью зуб заостряется на крупнокусковых — затупляется. Абразивное изнашивание зубьев в зависимости от типа грунта характеризуется появлением царапин глубиной 4 5 мм и длиной 40 50 мм а также выр ывов глубиной 3 5 мм и площадью до 8 12 мм2. Вся площадь зубьев покрыта макро- и микро царапинами и вырывами глубиной от 5 до 200 мк.Значение поверхностной твердости изготовленных из стали 110Г13Л зубьев в процессе их изнашивания под действием нагрузок высокой динамичности быстро возрастает до 40 НКС после чего стабилизируется. Исследования показали что наклеп распространяется на глубину 8мм а эпюра его распределения в целом повторяет эпюру распределения поверхностной твердости т. е. его максимум совпадает с максимумом эпюры износа. При этом наибольшие значения твердости совпадают с максимумами износа (рис. 10). Объясняется это явление тем что наклеп наиболее интенсивно образуется в зоне наиболее жестких контактов с грунтом т. е. в зоне максимального износа.
Рис. 10 Распределение наклепа по поверхности зуба ковша экскаватора из стали 110Г13Л работавшего на твердых грунтах : а – размещение экспериментальных участков 1 7по профилю зуба; б – изменение износа и твердости зуба; в – изменение твердости поверхности в зависимости от удельной работы ударов Ау.
Изменение в результате износа первоначальной формы зубьев рабочих органов одноковшовых экскаваторов приводит к резкому возрастанию сопротивлений снижающему их производительность. Так при достижении предельного износа зубьев ковшей одноковшовых экскаваторов сопротивление копанию возрастает до 230 %.При полном износе зубьев их угол заострения увеличивается в 2 25 раза достигая 65 70* а рабочая длина сокращается в 3 4 раза. Характер износа во многом определяется принятой схемой наплавки (рис. 11). Для ориентировочных расчетов предельный износ зуба принимают равным половине его рабочей длины.
Рис.11 Характер изменения формы зуба ковша в зависимости от места нанесения износостойкой наплавки.а – без наплавки; б – наплавка по двум плоскостям; в – наплавка по наружной плоскости; г – наплавка по внутренней плоскости.
Форма наплавки зубьев зависит от динамичности абразивного изнашивания. При незначительной динамичности когда наблюдается самозатачивание наплавке подвергают верхнюю грань зуба; при значительной динамичности когда радиус затупления возрастает проводят корончатую наплавку зуба (рис. 12).
Рис. 12 Корончатая наплавка зубаковша:1 –износостойкая наплавка; 2 – тело зуба.
Износ зубьев ковшей экскаваторов измеряется десятками миллиметров поэтому полностью восстановить их наплавкой невозможно. Исключением является метод электрошлаковой наплавки. В связи с этим наплавляют или новые зубья или в порядке профилактики зубья с изношенным первоначальным слоем наплавки.Профилактическую наплавку зубьев проводят как непосредственно на ковше так и в условиях наплавочного участка. Там их вместе с новыми зубьями укладывают в специальные кондукторы обеспечивающие горизонтальность наплавляемых поверхностей (рис. 13).
Рис 13. Установка зубьев ковшей экскаваторов при их наплавке :1 – электроды; 2 – направление движение стол.
Многоэлектродная наплавка зубьев ковшей экскаваторов износостойкими сплавами выполняется следующим оброем (Харьковский турбинный завод). Наплавляемые зубья устанавливают в кондуктор. Его располагают на столе специально переоборудованного токарного станка с высотой центров 200 мм который перемещается относительно автоматической наплавочной головки. Наплавка идет одновременно несколькими электродными проволоками под слоем флюса (рис.14). Легирующая шихта подается в слой флюса через боковой вырез дозатора закрепленного на головке. Для предотвращения сваривания зубьев между собой специальный механизм смещает их относительно один другого в процессе кристаллизации ванны на их стыке. Установка потребляет ток 950.. 1050 А при ширине ваплавки-60 мм. Максимальная ширина наплавленного слоя 120 мм толщина 5 6 мм. Износостойкость наплавленных зубьев в 2 3 раза больше новых.
Рис 14. Многоэлектродная наплавка:1 – электроды ; 2 – источник тока; 3 –флюс; 4 – наплавляемая деталь; 5 – наплавленный слой.
Экономическая часть.
Экономия (гр.) – бережливое ведение хозяйства в основе которого лежит уменьшение сдержек расходов затрат экономических ресурсов. Экономия достигает снижением потерь использованием ресурсо-сберегающих технологий рассчитанным ведением хозяйства правильной организации труда.Норма – установление документально подтверждённое величина определяющая нормативный уровень расходования ресурсов получение доходов прибыли затрат времени выработки продукции.Объектом нормирования является промышленного шва выполненного в нижнем положении при определении основного времени при наплавке.Сравнение времени работы испытываемого объекта с экономии. Этот метод недостаточно объективен так как в нем не учитывается физический объем выполнения работы и качество перерабатываемого материала которые определяют изнашивание рабочих органов.Физический объем выполнение работы испытываемых объектов с эталонным до их предельного износа.Подсчет экономической эффективности применения износостойких сплавов для повышения долговечности рабочих органов.
Ориентировочная стоимость некоторых наплавочных сплавов.
Хорошие результаты показали электрошлаковая наплавка зубьев экскаваторов проволокой VUS-TD16 состава С – 29 %; Сr – 144; W – 35; Mo – 15; V – 11 и Cu – 10 %. Использование ток 380 А напряжение 32В скорость подачи электрода 120мч. Зуб первоначально подогревали до 300 С. Время его наплавки 9 мин за это время наплавлялось 35 кг металла. Этими методами можно выполнять многократно. Износостойкость возрастала в 2 раза.
Техника безопасности.
Электросварочные и газосварочные и огневые работы.
Огневые и другие пожароопасные работы в подразделениях производства проводятся в соответствии с признаками регламентирующими их порядок проведения в которых учтены требования “Правил пожарной безопасности в РФ” ППБ 01-03 “Типовой инструкции по организации безопасного проведения огневых работ на взрывоопасных и взрывопожароопасных объектах” РД 09-364-00.На проведение всех видов огневых работ на временных местах необходимо оформлять наряд-допуск. На местах постоянного проведения огневых работ оформление наряда-допуска не требуется.Места проведение огневых работ должны быть обеспечены первичными средствами пожаротушения.Газоэлектросварочные и другие огневые работы относятся к работам к которым предъявляется дополнительные требования безопасности и установлен особый порядок допуска работников к их выполнению требующий специального обучения работников перед допуском их к самостоятельной работе. Требование безопасности при производстве электросварочных резательных и наплавочных работ изложены в инструкции ИОТ.Р.0-34; требования к хранению и эксплуатации газовых баллонов – в инструкции ИОТ.Р.0-84.
Требование безопасности в газовом хозяйстве.
В цехах производства вырабатываются или применяются :
- горючие газы : доменный коксовый природный и их смеси конвертерный пропан-бутан ;
- продукты разделения воздуха : кислород и инертные газы (азот аргон).
Все газы в повышенных концентрациях представляют опасность для находящихся в их зоне персонала. При запахе газа либо другом неприятном запахе необходимо немедленно вызвать работников газоспасательной станции. Постараться удалить персонал из опасной зоны. Зону оградить выставить дежурные посты находиться с проветренной стороны. При необходимости сообщить в добровольную газоспасательную дружину (ДГСД) цеха руководителю мастеру начальнику смены и диспетчеру.
Содержание кислорода в воздухе составляет от 19 до 23%. Низкое содержание кислорода в воздухе (менее 16%) очень опасно. При содержании кислорода в воздухе 14 до 10% возможна потеря сознания нарушается правильность суждений и чувствительность.
Рекомендуемые чертежи
- 16.04.2020