Ремонт корпуса дифференциала МТЗ-80


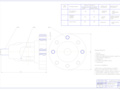
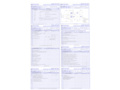
- Добавлен: 25.10.2022
- Размер: 599 KB
- Закачек: 2
Описание
Состав проекта
![]() |
![]() |
![]() ![]() ![]() ![]() |
![]() ![]() ![]() ![]() |
![]() ![]() ![]() |
![]() ![]() ![]() |
![]() ![]() ![]() ![]() |
![]() ![]() ![]() ![]() |
![]() |
![]() ![]() ![]() |
Дополнительная информация
дифференциалv13.cdw

резьбы номинального
Сверление поврежденной резьбы и нарезка новой;
Раззенкование отверстия;
Установка резьбовых втулок;
Технические требования
Обеспечить частоту вращения шпинделя
вертикально сверлильного станка 710мин -1
Развальцовщик и втулку обильно смазать маслом
. Раззенковать отверстие глубиной 2
Обеспечить усили при вворачивании вставки 3-4 кг
Наименование дефекта
Коэффицент повторяемости
Курсовой проект по ТМРПТДСМ
КазГАСУ группа 0ДМ-401
технокарта Контроля чист555v13.cdw

Моющее средство Лобомид 102
Сверлить опуская шпиндель с небольшим усилием пока
сверло не пройдет на сквозь отверстия
Наварачиваем на развальцовщик
предварительно смазанную маслом втулку
и вкручиваем в резьбовое отверстие
пока втулка не сядет на раззенкованное седло
ВВернуть калибр в восстановленную резьбу
если калибр вворачивается свободно
резьба восстановленна удачно
и готова к использованию
Обозначение комплекта ТД
Наименование комплекта ТД
ВЕДОМОСТЬ ТЕХНОЛОГИЧЕСКИХ ДОКУМЕНТОВ
Корпус дифференциала
наименование операции
наименование оборудования
сб. единицы или материала
наименование дефекта
КАРТА ТЕХНОЛОГИЧЕСКОГО ПРОЦЕССА ДЕФЕКТАЦИИ
Обозначение документа
КАРТА ТИПОВОГО ТЕХНОЛОГИЧЕСКОГО ПРОЦЕССА МЕХАНИЧЕКОЙ ОБРАБОТКИ
КАРТА ТИПОВОГО ТЕХНОЛОГИЧЕСКОГО ПРОЦЕССА МЕХАНИЧЕСКОЙ ОБРАБОТКИ
Стол для дефектации ОРГ-14-6801-090
Корпус фифференциала
Износ шейки под подшипник
Микротрещина в корпусе
Очиститель пароводоструйный ОМ-5359
Тара для деталей на очистку
Стол для дефектации ОРГ-14-6801-090 А.ГОСНИТИ
Резьбовой калибр М14х1
5 Сверелени поврежденной резьбы и нарезка новой
Универсальный вертикально-сверлильный станок 2С125-04
0 Зенкование отверстия
; длина 80мм; глубина фаски 2
Компрессор Fubau air master 76
Пневмопистолет для продувки
Насадка для продувки
0 Установка Резьбовых втулок
Тиски слесарные 7200-0203-13
Втулка ремонтная М15
Стол для дефектации ОРГ-14-6801-096 А.ГОСНИТИ
Отверстие под резьбу
5 Сверление поврежденной резьбы и нарезка новой
Закрепить дифференциал на сверлильном станке
Установить сверло в патроне станка
Обеспечить частоту вращения шпинделя 710 мин -1
Снять сверло с патрона и установить метчик М15.9х1
Обеспечить частоту вращения шпинделя 35 мин-1
Нарезать метчиком резьбу
Снять метчик с патрона и усановить фрезу М14х1
Зенковать отверстие до глубина фаски фрезы 2
Тщательно продуть все отвертия от стружки пневмопистолетом
Снисаем дифференциал со станка
Устанавливаем дифференциал на тиски
Выворачиваем развальцовщик
Демонтируем деталь с тисков
Контроль восстановленной детали
КАРТА ТЕХНОЛОГИЧЕСКОГО ПРОЦЕССА КОНТРОЛЯ
Унифицированная форма ведомости технологических документов
Карта технологического процесса дефектации
КАРТА ТИПОВОГО ТЕХНОЛОГИЧЕСКОГО ПРОЦЕССА МЕХАНИЧЕКОЙ ОБРАБОТКИ
дифференциал.dwg
резьбы номинального
Сверление поврежденной резьбы и нарезка новой;
Раззенкование отверстия;
Установка резьбовых втулок;
Технические требования
Обеспечить частоту вращения шпинделя
вертикально сверлильного станка 710мин -1
Развальцовщик и втулку обильно смазать маслом
. Раззенковать отверстие глубиной 2
Обеспечить усили при вворачивании вставки 3-4 кг
Наименование дефекта
Коэффицент повторяемости
Курсовой проект по ТМРПТДСМ
КазГАСУ группа 0ДМ-401
технокарта Контроля чист555.dwg
Моющее средство Лобомид 102
Сверлить опуская шпиндель с небольшим усилием пока
сверло не пройдет на сквозь отверстия
Наварачиваем на развальцовщик
предварительно смазанную маслом втулку
и вкручиваем в резьбовое отверстие
пока втулка не сядет на раззенкованное седло
ВВернуть калибр в восстановленную резьбу
если калибр вворачивается свободно
резьба восстановленна удачно
и готова к использованию
Обозначение комплекта ТД
Наименование комплекта ТД
ВЕДОМОСТЬ ТЕХНОЛОГИЧЕСКИХ ДОКУМЕНТОВ
Корпус дифференциала
наименование операции
наименование оборудования
сб. единицы или материала
наименование дефекта
КАРТА ТЕХНОЛОГИЧЕСКОГО ПРОЦЕССА ДЕФЕКТАЦИИ
Обозначение документа
КАРТА ТИПОВОГО ТЕХНОЛОГИЧЕСКОГО ПРОЦЕССА МЕХАНИЧЕКОЙ ОБРАБОТКИ
КАРТА ТИПОВОГО ТЕХНОЛОГИЧЕСКОГО ПРОЦЕССА МЕХАНИЧЕСКОЙ ОБРАБОТКИ
Стол для дефектации ОРГ-14-6801-090
Корпус фифференциала
Износ шейки под подшипник
Микротрещина в корпусе
Очиститель пароводоструйный ОМ-5359
Тара для деталей на очистку
Стол для дефектации ОРГ-14-6801-090 А.ГОСНИТИ
Резьбовой калибр М14х1
5 Сверелени поврежденной резьбы и нарезка новой
Универсальный вертикально-сверлильный станок 2С125-04
0 Зенкование отверстия
; длина 80мм; глубина фаски 2
Компрессор Fubau air master 76
Пневмопистолет для продувки
Насадка для продувки
0 Установка Резьбовых втулок
Тиски слесарные 7200-0203-13
Втулка ремонтная М15
Стол для дефектации ОРГ-14-6801-096 А.ГОСНИТИ
Отверстие под резьбу
5 Сверление поврежденной резьбы и нарезка новой
Закрепить дифференциал на сверлильном станке
Установить сверло в патроне станка
Обеспечить частоту вращения шпинделя 710 мин -1
Снять сверло с патрона и установить метчик М15.9х1
Обеспечить частоту вращения шпинделя 35 мин-1
Нарезать метчиком резьбу
Снять метчик с патрона и усановить фрезу М14х1
Зенковать отверстие до глубина фаски фрезы 2
Тщательно продуть все отвертия от стружки пневмопистолетом
Снисаем дифференциал со станка
Устанавливаем дифференциал на тиски
Выворачиваем развальцовщик
Демонтируем деталь с тисков
Контроль восстановленной детали
КАРТА ТЕХНОЛОГИЧЕСКОГО ПРОЦЕССА КОНТРОЛЯ
Унифицированная форма ведомости технологических документов
Карта технологического процесса дефектации
КАРТА ТИПОВОГО ТЕХНОЛОГИЧЕСКОГО ПРОЦЕССА МЕХАНИЧЕКОЙ ОБРАБОТКИ
дифференциал.cdw

резьбы номинального
Сверление поврежденной резьбы и нарезка новой;
Раззенкование отверстия;
Установка резьбовых втулок;
Технические требования
Обеспечить частоту вращения шпинделя
вертикально сверлильного станка 710мин -1
Развальцовщик и втулку обильно смазать маслом
. Раззенковать отверстие глубиной 2
Обеспечить усили при вворачивании вставки 3-4 кг
Наименование дефекта
Коэффицент повторяемости
Курсовой проект по ТМРПТДСМ
КазГАСУ группа 0ДМ-401
технокарта Контроля чист555.cdw

Моющее средство Лобомид 102
Сверлить опуская шпиндель с небольшим усилием пока
сверло не пройдет на сквозь отверстия
Наварачиваем на развальцовщик
предварительно смазанную маслом втулку
и вкручиваем в резьбовое отверстие
пока втулка не сядет на раззенкованное седло
ВВернуть калибр в восстановленную резьбу
если калибр вворачивается свободно
резьба восстановленна удачно
и готова к использованию
Обозначение комплекта ТД
Наименование комплекта ТД
ВЕДОМОСТЬ ТЕХНОЛОГИЧЕСКИХ ДОКУМЕНТОВ
Корпус дифференциала
наименование операции
наименование оборудования
сб. единицы или материала
наименование дефекта
КАРТА ТЕХНОЛОГИЧЕСКОГО ПРОЦЕССА ДЕФЕКТАЦИИ
Обозначение документа
КАРТА ТИПОВОГО ТЕХНОЛОГИЧЕСКОГО ПРОЦЕССА МЕХАНИЧЕКОЙ ОБРАБОТКИ
КАРТА ТИПОВОГО ТЕХНОЛОГИЧЕСКОГО ПРОЦЕССА МЕХАНИЧЕСКОЙ ОБРАБОТКИ
Стол для дефектации ОРГ-14-6801-090
Корпус фифференциала
Износ шейки под подшипник
Микротрещина в корпусе
Очиститель пароводоструйный ОМ-5359
Тара для деталей на очистку
Стол для дефектации ОРГ-14-6801-090 А.ГОСНИТИ
Резьбовой калибр М14х1
5 Сверелени поврежденной резьбы и нарезка новой
Универсальный вертикально-сверлильный станок 2С125-04
0 Зенкование отверстия
; длина 80мм; глубина фаски 2
Компрессор Fubau air master 76
Пневмопистолет для продувки
Насадка для продувки
0 Установка Резьбовых втулок
Тиски слесарные 7200-0203-13
Втулка ремонтная М15
Стол для дефектации ОРГ-14-6801-096 А.ГОСНИТИ
Отверстие под резьбу
5 Сверление поврежденной резьбы и нарезка новой
Закрепить дифференциал на сверлильном станке
Установить сверло в патроне станка
Обеспечить частоту вращения шпинделя 710 мин -1
Снять сверло с патрона и установить метчик М15.9х1
Обеспечить частоту вращения шпинделя 35 мин-1
Нарезать метчиком резьбу
Снять метчик с патрона и усановить фрезу М14х1
Зенковать отверстие до глубина фаски фрезы 2
Тщательно продуть все отвертия от стружки пневмопистолетом
Снисаем дифференциал со станка
Устанавливаем дифференциал на тиски
Выворачиваем развальцовщик
Демонтируем деталь с тисков
Контроль восстановленной детали
КАРТА ТЕХНОЛОГИЧЕСКОГО ПРОЦЕССА КОНТРОЛЯ
Унифицированная форма ведомости технологических документов
Карта технологического процесса дефектации
КАРТА ТИПОВОГО ТЕХНОЛОГИЧЕСКОГО ПРОЦЕССА МЕХАНИЧЕКОЙ ОБРАБОТКИ
Введение.docx
Казанский государственный архитектурно-строительный университет
Кафедра: “Дорожно-строительные машины”
Курсовой проект по дисциплине:
Технология машиностроения производства и ремонт подъемно-транспортных дорожно-строительных машин
Тема: Ремонт корпуса дифференциала МТЗ-80
Руководитель доктор технических наук Адигамов Н.Р.
Зав. кафедрой профессор Сахапов Р.Л.
Описание устройства анализ работы и характеристика причин потерь работоспособности дифференциала .. 4
Разработка структурной схемы сборки .7
Разработка карты технологического процесса дефектации и выбор контрольно-измерительных средств 9
Выбор рационального способа восстановления дефекта деталей .13
Разработка ремонтного чертежа корпуса дифференциала 17
Разработка маршрутных и операционных карт восстановления корпуса дифференциала .19
Расчет и выбор режимов введения резьбовых вставок и на обработку отверстия под резьбу корпуса дифференциала .23
Техническое нормирование ремонтных работ .24
Расчет технико-экономических показателей восстановления корпуса дифференциала .26
Разработка мероприятий по охране труди и защите окружающей среды при восстановлении корпуса дифференциала 30
Список используемой литературы 33
В настоящее время на техническое обслуживание и ремонт автомобилей сельскохозяйственного назначения приходится 1520 % себестоимости транспортного процесса. Причем недостаточная надёжность машин сказывается на уменьшении их производительности что обусловлено простоями в ремонте.
Повышение надежности техники в межремонтном периоде зависит от совершенствования системы ее обслуживания и ремонта от ее гибкости позволяющей наиболее эффективно использовать ресурсы составных частей автомобилей. Эффективность системы технического обслуживания и ремонта повышается при правильном использовании попутных замен деталей при отказе агрегата возможности изменения периодичности ремонтно-обслуживающих воздействий в соответствии с техническим состоянием при диагностировании. По сравнению с автомобильной техникой для других видов машин применяется большее число видов ремонта большие диапазоны кратности периодичностей то есть им присуща большая гибкость системы ремонта и большая степень использования ресурса агрегатов. Но совершенствование системы ремонтных воздействий ведется как правило без исследования целесообразности изменения структуры ремонтного цикла а путем уточнения нормативов. Актуальность указанной задачи подтверждается и тем что на техническое обслуживание автомобиля затрачивается во много раз больше труда и средств чем на его производство. Эффективность ремонта сельскохозяйственной техники определяется восстановлением изношенных деталей. Этим самым решается проблема обеспечения эксплуатируемых машин запасными частями то есть восстановление деталей. Очень важно на стадии ремонта сделать качественную дефектовку очистку детали. Важно подобрать нужные измерительные приборы для выявления дефектов. Если деталь или механизм отремонтирован качественно с учетом технологий то ресурс детали или механизма будет высоким. В данной работе будет описан полный процесс по ремонту корпуса дифференциала МТЗ-80 с соблюдением технологического процесса.
Описание устройства анализ работы и характеристика причин потерь работоспособности дифференциала
Дифференциал представляет собой планетарный механизм предназначенный для распределения подводимого крутящего момента между полуосями и обеспечения вращения ведущих колес с различной частотой на поворотах и на участках пути имеющих неровности.
На повороте колеса перемещаются по дугам разной длины. Если бы колеса были закреплены на сплошной оси а следовательно вращались с одинаковой частотой то их перемещение сопровождалось бы проскальзыванием относительно грунта и закручиванием общей оси. Поэтому ведущие колеса устанавливают на отдельных полуосях соединяя их дифференциалом.
Рис 1. Дифференциал МТЗ-80:
Где 15-Крпус; 12-шайба опорная; 16-полуось; 17-кольцо; 18-сателит;19-ось;
Облегчая поворот трактора дифференциал может ухудшать его тяговые качества. Например когда сцепление одного колеса на скользком грунте недостаточно другое колесо хотя и имеет лучшее сцепление с почвой не сможет его реализовать и развить большую силу тяги чем колесо на скользком грунте. Чтобы устранить этот недостаток на тракторе введен механизм автоматической блокировки дифференциала который позволяет обеспечивать колесам разные по величине тяговые усилия.
Рассмотрим работу дифференциала
В работе симметричного межколесного дифференциала можно выделить три характерных режима:
прямолинейное движение;
движение в повороте;
движение по скользкой дороге.
При прямолинейном движенииколеса встречают равное сопротивление дороги. Крутящий момент от главной передачи передается на корпус дифференциала вместе с которым перемещаются сателлиты. Сателлиты обегая полуосевые шестерни передают крутящий момент на ведущие колеса в равном соотношении. Так как сателлиты на осях не вращаются полуосевые шестерни движутся с равной угловой скоростью. При этом частота вращения каждой из шестерен равна частоте вращения ведомой шестерни главной передачи.
При движении в поворотевнутреннее ведущее колесо (расположенное ближе к центру поворота) встречает большее сопротивление чем наружное колесо. Внутренняя полуосевая шестерня замедляется и заставляет сателлиты вращаться вокруг своей оси которые в свою очередь увеличивают частоту вращения наружной полуосевой шестерни. Движение ведущих колес с разными угловыми скоростями позволяет проходить поворот без пробуксовки. При этом в сумме частоты вращения внутренней и наружной полуосевых шестерен всегда равна удвоенной частоте вращения ведомой шестерни главной передачи. Крутящий момент независимо от разных угловых скоростей распределяется на ведущие колеса в равном соотношении.
При движении по скользкой дорогеодно из колес встречает большее сопротивление тогда как другое проскальзывает - буксует.
Дифференциал в силу своей конструкции заставляет вращаться буксующее колесо с увеличивающейся скоростью. Другое колесо при этом останавливается. Сила тяги на буксующем колесе по причине низкой силы сцепления мала поэтому и крутящий момент на этом колесе тоже мал. А так как дифференциал у нас симметричный то на другом колесе крутящий момент тоже будет небольшим. Тупиковая ситуация – автомобиль не может сдвинуться с места.
Для продолжения движения необходимо увеличить крутящий момент на свободном колесе. Это осуществляется с помощьюблокировки дифференциала.
Причинами выхода из строя дифференциала могут быть конструктивные недостатки. Например деталь сделана с большими конструктивными недоработками - коробка дифференциала имеет слабое сварное соединение и ненадежную конструкцию сателлитов и осей что приводит к преждевременному выходу из строя всего агрегата. Наиболее распространенная причина выхода из строя дифференциала это обрыв сварного соединения самого корпуса. То небольшое количество сварных точек просто не выдерживает нагрузки которые несут редуктора как переднего так и заднего моста и происходит обрыв сварки и последствия этого весьма не предсказуемы. Так же не выдерживают нагрузок шестерни и оси сателлитов - не редки случай когда крошатся зубья сателлитов и ломаются оси.Так же причинами выхода из строя дифференциала могут стать износ шейки посадочного места под подшипник износ резьбовых соединений.
Разработка структурной схемы сборки
Перед разработкой технологического процесса сборки изделия (узла) составляют технологические схемы общей и узловой сборки. Эти схемы изображают последовательность сборки машин узла или подузла из ее элементов.
Каждую деталь на схеме сборки изображают в виде прямоугольника разделенного на три части в которых указывают номер детали по спецификации наименование детали и число собираемых деталей.
При разработке схемы сборки вначале выбирают так называемую базовую деталь или базовый узел. Таким базовым элементом является элемент собираемого узла на который устанавливают остальные детали.
От базового элемента проводят прямую линию к которой подводят прямоугольники обозначающие сборочные элементы в порядке их присоединения. В конце линии прямоугольником обозначают узел (подузел изделие) в сборе.
Для сборки дифференциала требуется следующий перечень инструментов:
Ключи гаечные ГОСТ 2839-80;
Тиски слесарные ГОСТ 4045-75;
Прибор для лазерной центровки Квант-ЛМ.
Структурная схема сборки рассматриваемого устройства представлена на рисунке 2.
Корпус дифференциала
Рис 2. Структурная схема дифференциала
Разработка карты технологического процесса дефектации и выбор контрольно-измерительных средств
Для определения технического состояния деталей (сборочных единиц) их подвергают дефектации то есть устанавливают три категории деталей: годные утильные и требующие восстановления. На участках дефектации осуществляется сортировка деталей которые как правило помечаются краской:
Годные детали-зеленой краской;
Годные детали которые можно использовать только в сопряжении с новыми деталями-желтой краской;
Детали подлежащие восстановлению силами своего предприятия - белой краской;
Детали подлежащие восстановлению по кооперации - синим цветом;
Детали подлежащие утилизации - красной краской.
Исходные данные для разработки технологического процесса дефектации-технические требования на капитальный ремонт соответствующий машины в которой на каждую деталь (узел) приводится эскиз перечень всех дефектов средства контроля и рекомендации по ремонту.
При проектировании технологического процесса составляется карта эскизов и карта технологического процесса дефектации. Необходимое число изображений (видов разрезов сечений и выносных элементов) на эскизе устанавливают из условия обеспечения наглядности и ясности расположения контролируемых поверхностей детали что позволит качественно провести технологический процесс дефектации.
Контролируемые поверхности следует обводить сплошной линией в 2 3 раза толще основной остальные участки детали делают тонкими контурными линиями.
На эскизе детали все дефектные поверхности нумеруют по часовой стрелке арабскими цифрами которые указывают в окружности диаметром 6 8 мм и соединяют с размерными линиями.
На карте технологического процесса дефектации приводят:
Наименование и обозначение изделия измерительного инструмента или способа установления дефекта;
Разряд работы код тарифной сетки и виды нормы.
Приведем перечень дефектов рассматриваемой детали:
Повреждение резьбы на корпусе дифференциала;
Износ шейки посадочного места под подшипник;
Микротрещина в корпусе дифференциала.
В качестве оборудования для дефектации принимаем стол для дефектации ОРГ-14-68-01-090. А ГОСНИТИ.
Для контроля размеров при дефектации выбирают средства измерения. При выборе средств измерения руководствуются следующими положениями:
Точность измерительного средства должна быть достаточно высокой по сравнению с заданной точностью
Трудоемкость измерений и их стоимость должны быть по возможности наиболее низкими.
Выбор средств измерения производится следующим образом:
По известному номинальному размеру и величине допуска контролируемого размера детали по ГОСТ 8.051-81 определяют допускаемую предельную погрешность измерения;
По литературе выбирают измерительные средства для измерения размера.
При выборе средства измерения должно соблюдаться следующее условие: предельная погрешность средств измерения должна быть меньше допустимой погрешность измерения то есть
Где - допускаемая погрешность измерения;
- предельная погрешность измерительного средства.
Дефекты резьбовых отверстий возможно контролировать резьбовым калибром соответствующей резьбы.
Рис 3. Резьбовой калибр.
Калибр резьбовой- калибр для контроля размеров резьбы: наружного внутреннего и среднего диаметра резьбы; шага резьбы и высоты исходного треугольника. Является калибром предельного вида и подразделяется на проходной и непроходной.Выбираем резьбовой калибр М14х15.
По известному номинальному размеру для контроля дефекта 2
Определяем предельную погрешность измерения согласно литературе [5]
=16 мкм. Выбираем средство измерения с учетом выполнения условия (1) – нутрометр микрометрический (ГОСТ 10-88) предельная погрешность которого
Рис 4. Микрометрический нутрометр.
Микрометрический нутромер реализует абсолютный метод измерения. Прибор предназначен для высокоточного измерения диаметра отверстий а тек же и наружных диаметров.
Для выявления дефекта 3 выбираем Магнитно-вихретоковый дефектоскоп ВИД-345 предназначен для выявления и определения глубины трещин в металлических конструкциях в т.ч. под слоем изоляционного покрытия иили коррозии. Предельная погрешность глубины трещин 02 + 01h мм где h глубина трещины.
ширина 4 мм глубина 12 мм раскрытие 005мм.
Магнитно-вихретоковый дефектоскоп ВИД-345
Выбор рационального способа восстановления дефекта деталей
Из всего многообразия способов восстановления изношенных деталей встает важная задача выбора способа устранения дефекта (комплекса одинаковых дефектов). При этом должен быть выбран наиболее рациональный способ восстановления технически обоснованный и экономический целесообразный.
При выборе рационального способа восстановления деталей руководствуются следующими критериями:
– технологическим (применяемости);
– техническим (долговечности);
– технико-экономическим (обобщающим).
Технологический критерий - характеризует принципиальную возможность применения нескольких способов восстановления исходя из конструктивно-технических особенностей детали или определенных групп деталей.
К числу конструктивно-технических особенностей относятся геометрическая форма и размеры материал термическая или другой вид поверхностной обработки твердость шероховатость поверхности и точность изготовления детали характер нагрузки вид трения и износа размеры износа.
Технический критерий - оценивает каждый способ (выбранный по технологическому признаку) устранения дефектов детали с точки зрения восстановления (иногда и улучшения) свойств поверхностей т.е. обеспечения работоспособности за счет достаточной твердости износостойкости и сцепляемости покрытия восстановленной детали.
Для каждого выбранного способа дается комплексная качественная оценка по значению коэффициента долговечности Кд определяемому по формуле:
где – коэффициент износостойкости покрытия;
– коэффициент выносливости покрытия;
– коэффициент сцепляемости покрытия;
– поправочный коэффициент учитывающий фактическую работоспособности восстановленной детали в условиях эксплуатации ( = 08 09).
По физическому смыслу коэффициент долговечности пропорционален сроку службы деталей в эксплуатации и следовательно рациональным поэтому критерию будет способ у которого .
Выбрав один или несколько способов устранения дефектов которые обеспечивают необходимые твердость износостойкость выносливость и другие показатели окончательное решение о его целесообразности принимают по технико-экономическому критерию.
Технико-экономический критерий связывает стоимость восстановления детали с её долговечностью после устранения дефектов. Условие технико-экономической эффективности способа восстановления детали определяется по следующей формуле:
где – стоимость восстановления детали руб.;
– стоимость новой детали руб.
Если неизвестна стоимость новой детали критерий оценивают по следующей формуле:
где – коэффициент технико-экономической эффективности;
– себестоимость восстановления 1 м2 изношенной поверхности детали руб.м2 .
Эффективным считают способ у которого . Если будет больше стоимости 1 новой детали необходимо решить вопрос о целесообразности восстановления детали.
Установив рациональный способ устранения дефектов (группы дефектов) деталей приступают к проектированию технологического процесса восстановления деталей.
Примем для дефекта 1 в качестве возможных способов восстановления детали резьбовые вставки и наплавка с нарезанием резьбы и рассчитаем для каждого из способов технический и технико-экономический критерий. Значение коэффициентов при расчете определяем из таблицы 1 литературы [1] значение коэффициента примем равным 08.
Исходя из условия наиболее эффективным способом является метод резьбовых втулок.
Рассмотрим технико-экономический критерий способов восстановления используя формулу (4). Значения также принимаем из таблицы 1 литературы [1].
Исходя из условия наиболее эффективным способом является метод резьбовых втулки.
Таким образом на основе анализа технологического технического и технико-экономического критериев делаем вывод что наиболее рациональным способом восстановления детали в месте дефекта 1 является метод резьбовых вставок. Допустимым методом восстановления детали в случае дефекта 1 является наплавка.
Для остальных дефектов с учетом технологического критерия назначаем следующие способы восстановления:
Износ шейки посадочного места под подшипник – вибродуговая наплавка (основной способ) и ручная электродуговая сварка (допустимый способ);
Микротрещина в корпусе дифференциала – металлизация (основной способ) и наплавка под слоем флюса (допустимый способ).
Разработка ремонтного чертежа корпуса дифференциала
Ремонтный чертеж выполняется перед разработкой технического процесса восстановления детали. Задачей ремонтного чертежа является передача информации по дефектам возникающим в процессе эксплуатации. На ремонтном чертеже указывается общий вид детали в тонких линиях согласно выбранному масштабу (с учетом полноты заполнения).
Места дефектов на ремонтном чертеже нумеруются и указываются на выносных полочках. Изношенные поверхности и дефекты выделяются жирной линией толщиной в два три раза больше основной. Размеры на этом чертеже указываются только по местам где имеются дефекты. Размеры указываются номинальные с указанием заданных отклонений. Так же на ремонтном чертеже указывается шероховатость поверхности и допуски отклонения формы и расположение поверхности после восстановления детали. Наличие добавочных видов обосновывается необходимостью показания того или иного дефекта и указания его параметром. В правой части чертежа вверху приводится таблица дефектов. В первой графе указывается номер дефекта во второй графе – наименование дефекта в третей графе указывается коэффициент повторяемости который в свою очередь подразделяется на коэффициент повторяемости от общего количества деталей и коэффициента повторяемости от деталей подлежащих ремонту. В следующей четвертой графе указывается основной способ устранения дефекта который определяется на основании выбора рационального способа восстановления детали. В пятой графе указывается допустимый способ устранения дефекта – это тот способ который может быть использован в случае невозможности использования основного способа восстановления дефектов. С правой стороны над штампом указываются технические требования которые необходимо выдержать при восстановлении этой детали. В штампе в основной графе указывается название детали с индексом РЧ. В графе “материалы” указывается исходный материал детали.
Кроме того на ремонтном чертеже указывается маршрут движения детали при ее восстановлении[2].
На ремонтном чертеже корпуса представлены следующие дефекты и способы их восстановления:
Для выбранного дефекта 1 составлен маршрут движения детали:
Рассверлить резьбовое отверстие;
Сделать в отверстии подрезку под буртик втулки используя фрезу;
Нарезать в нём резьбу особого профиля специальным метчиком;
Удалить стружку из резьбы при помощи продувочного пистолета;
Ввернуть в полученную резьбу ремонтную вставку (втулку) из прочной нержавеющей стали с помощью развальцовщика предварительно смазав развальцовщик моторным маслом;
Контроль восстановленной поверхности.
Для всех дефектов на ремонтном чертеже корпуса указаны коэффициенты повторяемости дефектов как от общего числа деталей так и от числа деталей подлежащих ремонту.
Разработка маршрутных и операционных карт восстановления корпуса дифференциала
Маршрутная карта (МК) восстановления составляется на все возможные дефекты согласно ЕСТД. Исходными данными для разработки МК служат карта эскизов или ремонтный чертеж схема выбранного рационального способа устранения дефектов сведения для выбора оборудования и оснастки разряд работы и нормы времени. В качестве эскиза к МК допускается применять ремонтный чертеж. При этом на нем должны быть пронумерованы все обрабатываемые поверхности указаны номера и наименования дефектов.
Карта эскизов (КЭ) к маршрутной карте восстановления является обязательным технологическим документом и составляется по ГОСТ 3.1118-82. На КЭ должны быть указаны данные необходимые для выполнения технологических процессов восстановления (размеры предельные отклонения обозначение шероховатости поверхностей технические требования и т.д.). Таблицы схемы технические требования а также номера и наименования дефектов указываются справа от изображения или под ним.
Приступая к разработке маршрутной карты по всем дефектам намечают последовательность выполнения операций технологического процесса восстановления. При этом строго придерживаются следующих основных положений:
-в одной операции совмещают восстановление нескольких изношенных поверхностей если их восстанавливают одним технологическим способом;
-в конце технологического процесса предусматривают финишные операции;
-контрольные операции записывают как правило в конце технологического процесса.
В МК указывают наименование номер по каталогу материал размер и массу детали. В соответствующей строке (служебный символ “А”) записывают кратко и четко и выражают глаголом в повелительном наклонении приводят наименование восстановленного элемента детали.
Допускается не включать в состав технологического операций операции перемещения.
В строке “оборудование приспособления инструмента” необходимо указать наименование инвентарный номер и ГОСТ на соответствующую технологическую операцию и оснастку по действующему классификатору.
Таблица 2 – Последовательность операций по восстановлению
Очиститель пароводоструйный
Тара для деталей на очистку; моющее средство Лабомид 102 концентрация 15 грл t=65 град.
Резьбовой калибр М14х15.
резьбы и нарезка новой
Универсальный вертикально-сверлильный станок 2С125-04.
Сверло d=140 мм; метчик М15.9×1.5.
0 Раззенкование отверстия
Фреза М14×1.25 d= 16.2 длина 80мм глубина фаски 28мм.
Компрессор FUBAG AIR MASTER KIT.
Пневмопистолет для продувки; насадка для продувки.
0 Установка резьбовых втулок
Тиски слесарные 7200-0203-13.
Развальцовщик (инструмент для вворачивания втулки); втулка ремонтная М15.6×1.25d= 16.0 мм; масло моторное 200 гр.
Стол для дефектации ОРГ-14-6801-090
Расчет и выбор режимов введения резьбовых вставок и на обработку отверстия под резьбу корпуса дифференциала.
Прежде всего как ввернуть резьбовую вставку в отверстие нужно подготовить это отверстие т.е. высверлить испорченную резьбу и нарезать новую.
Для высверливания испорченной резьбы воспользуемся настольным сверлильным станком СН-16.
Технические данные и характеристики настольного сверлильного станка СН-16
Наибольший диаметр сверления мм
Диапазон нарезаемой резьбы
Размер конуса шпинделя
Частоты вращения шпинделя мин-1
Наибольшее перемещение шпинделя мм
Размер рабочей поверхности стола мм
Количество Т-образных пазов
Ширина крепежных Т-образных пазов мм
Мощность двигателя кВт
Частоту вращения шпинделя примем 710 мин-1
Выбираем сверло d=140 мм ГОСТ 2034-80;
Фреза М14×1.25 d= 16.2мм для раззен кования отверстия до глубины заданной ограничителем на фрезе 28мм;
Метчиком М15.9×1.5 для нарезания резьбы;
Очистим отверстие от стружки сжатым воздухом под давление 2 Бар.
Развальцовщик для вворачивания резьбовой вставки;
Техническое нормирование ремонтных работ.
Нормируемое время – это время полезной работы связанной с выполнением производственного задания. Оно классифицируется на основное вспомогательное дополнительное и подготовительно-заключительное время. Все названные категории включают в состав технической нормы времени которая выражается следующей формулой:
где – норма времени (штучно – калькуляционное время);
– основное время т.е. время в течение которою происходит изменение размеров формы свойств внешнего вида обрабатываемой детали в результате какого-либо вида обработки мин. Так при механической обработке основным будет снятие стружки при электросварке – время плавления электрода при кузнечных работах – время в течение которого происходит деформация детали под воздействием молота и т.д. ;
– вспомогательное время т.е. время затрачиваемое на действия обеспечивающие выполнение основной работы (закрепление и снятие детали со станка измерение детали перестановка инструмента и т.д.) мин
– дополнительное время затрачиваемое на организацию и обслуживание рабочего места перерывы на отдых и естественные надобности исполнителя мин. ;
– подготовительно-заключительное время затрачиваемое на получение задания ознакомление с работой подготовку рабочего места наладку оборудования сдачу изготовленного изделия (дается на партию деталей) мин. ;
– количество обрабатываемых деталей в партии.
Сумма основного и вспомогательного времени составляет оперативное время:
В технологических картах обычно проставляется штучное время и подготовительно-заключительное время .
Расчет технико-экономических показателей восстановления корпуса дифференциала.
Окончательная оценка целесообразности применения разработанного технологического процесса восстановления детали проводится по технико-экономическому критерию который выражается неравенством:
Где – стоимость восстановления детали руб.;
– коэффициент долговечности =0504;
– стоимость новой детали (принимается по прейскурантам) руб.
Значение находят по формуле:
где – полная себестоимость детали руб.;
Н = 105 – прибыль (накопление) ремонтного предприятия руб.
Полную себестоимость восстановления детали рассчитывают по формуле:
где – заработная плата производственных рабочих с начислениями руб.;
– стоимость ремонтных материалов руб.;
и – соответственно общепроизводственные общехозяйственные и внепроизводственные накладные расходы руб.
Заработная плата складывается из основной дополнительной и начислений по социальному страхованию т.е.
Где - основная заработная плата руб.;
- дополнительная заработная плата руб.;
- начисления по социальному страхованию руб.
где – штучно-калькуляционное время ч;
– ставка рабочих исчисляемая по среднему разряду (устанавливают по маршрутной карте) =36 рубч;
– коэффициент учитывающий доплаты к основной заработной плате равный 1025 1030.
где – подготовительно-заключительное время определяется суммированием по всем операциям маршрутной карты =028 ч;
– штучное время т.е. полное время для выполнения всех операций техпроцесса (устанавливают по маршрутной карте) =123ч;
– число деталей в партии.
Дополнительная заработная плата производственных рабочих руб.:
Начисления по социальному страхованию руб:
Стоимость ремонтных материалов укрупнено можно определить исходя из доли заработной платы и доли стоимости материалов:
Зная процент общепроизводственных общехозяйственных и внепроизводственных накладных расходов устанавливают их стоимость:
Где - проценты на накладные расходы:
Полная себестоимость восстановленной детали:
После расчета стоимости восстановления детали и учета технико-экономического критерия необходимо сделать заключение о целесообразности применения на ремонтном предприятии разработанного технологического процесса.
Уровень рентабельности продукции % определяют по формуле:
Где - прейскурантная цена детали =250 руб.
Плановая фактическая прибыль предприятия руб.:
Где - годовая программа восстановления деталей =900 шт.
Разработка мероприятий по охране труди и защите окружающей среды при восстановлении корпуса дифференциала
До сверлильных работ необходимо ознакомиться с действующими правилами техники безопасности по эксплуатации сверлильных станков и ручных машин. Так же ознакомиться с правилами технической эксплуатации установок (ПТБ и ПТЭ) а также требований стандартов системы безопасности труда (ССБТ).
Работа на сверлильных станках может сопровождаться наличием ряда вредных и опасных производственных факторов в том числе:
- электрический ток;
- мелкая стружка и аэрозоли смазочно-охлаждающей жидкости;
- отлетающие кусочки металла;
- высокая температура поверхности обрабатываемых деталей и инструмента;
- повышенный уровень вибрации;
- движущиеся машины и механизмы передвигающиеся изделия заготовки материалы;
- недостаточная освещенность рабочей зоны наличие прямой и отраженной блескости повышенная пульсация светового потока.
К самостоятельной работе на сверлильных станках допускается обученный персонал прошедший медицинский осмотр инструктаж по охране труда на рабочем месте ознакомленный с правилами пожарной безопасности и усвоивший безопасные приемы работы.
Сверловщику разрешается работать только на станках к которым он допущен и выполнять работу которая поручена ему администрацией цеха.
Персонал обслуживающий сверлильные станки должен иметь: костюм хлопчатобумажный или полукомбинезон очки защитные ботинки юфтевые.
Если пол скользкий (облит маслом эмульсией) рабочий обязан потребовать чтобы его посыпали опилками или сделать это самому.
Сверловщику запрещается:
- работать при отсутствии на полу под ногами деревянной решетки по длине
станка исключающей попадание обуви между рейками и обеспечивающей
свободное прохождение стружки;
- работать на станке с оборванным заземляющим проводом а также при отсутствии или неисправности блокировочных устройств;
- стоять и проходить под поднятым грузом;
- проходить в местах не предназначенных для прохода людей;
- заходить без разрешения за ограждения технологического оборудования;
- снимать ограждения опасных зон работающего оборудования;
- мыть руки в эмульсии масле керосине и вытирать их обтирочными концами загрязненными стружкой. О любом несчастном случае немедленно поставить в известность мастера и обратиться в медицинский пункт.
Требования безопасности перед началом работ
Перед началом работ сверловщик обязан:
- принять станок от сменщика: проверить хорошо ли убран станок и рабочее место. Не приступать к работе до устранения выявленных недостатков;
- надеть спецодежду застегнуть рукава и куртку надеть головной убор проверить наличие очков;
- отрегулировать местное освещение так чтобы рабочая зона была достаточно освещена и свет не слепил глаза;
- проверить наличие смазки станка. При смазке пользоваться только специальными приспособлениями;
- проверить на холостом ходу исправность станка.
После окончания работ сверловщик обязан:
- выключить станок и электродвигатель;
- привести в порядок рабочее место:
а) убрать со станка стружку и металлическую пыль;
б) очистить станок от грязи;
в) аккуратно сложить заготовки и инструмент на отведенное место;
г) смазать трущиеся части станка;
- сдать станок сменщику или мастеру и сообщить обо всех неисправностях станка;
- снять спецодежду и повесить в шкаф. Вымыть лицо и руки теплой водой с мылом или принять душ.
В процессе выполнения курсового проекта мы научились решать конкретные конструкторские технологические и организационно-экономические задачи в соответствии с заданием на проектирование. Научились правильно и с умением пользоваться справочной литературой различными техническими учебниками и книгами по ремонту деталей и сборочных единиц сельскохозяйственной техники.
На основе приобретенных знаний при изучении общетехнических и профилирующих дисциплин мы решали задачи связанные с организацией ремонта машин и механизмов что способствовало закреплению углублению и обобщению знаний полученных за время обучения.
В данном курсовом проекте разработан процесс восстановления резьбы на корпусе дифференциала методом резьбовых вставок.
Годовая программа 900 штук.
Норма времени на восстановление одной детали составило 90 мин.
Полная себестоимость восстановленной детали 22521 рублей.
Уровень рентабельности продукции составляет 153%.
Плановая прибыль предприятия составила 22311 руб.
Список используемой литературы
Курсовое и дипломное проектирование по надежности и ремонту машин И.С. Серый А.П. Смелов В.Е. Черкун. – 4-е изд. перераб. и доп. – М.: Агропромиздат 1991. – 184 с.: ил.
Технология ремонта машин: Учебник для вузов Е.А. Пучин О.Н. Дидманидзе В.С. Новиков и др.; Под ред. Е.А. Пучина. – М.: Изд-во УМЦ «Триада». – Ч. I. – 2006 . – 348 с.
Применение полимерных материалов при ремонте машин Кондратьев Г.И. и Шайхутдинов Р.Р. – Казань: Изд-во КГСХА 2006.
Проектирование технологических процессов восстановления изношенных деталей Новиков В.С. Очковский Н.А. Тельнов Н.Ф. Ачкасов К.А. – М.: МГАУ 1998. 52 с.
Р 50-60-88 Рекомендации. Единая система технологической документации. Правила оформления документов на технологические процессы ремонта.
Режущий инструмент. Курсовое и дипломное проектирование учеб. пособие под. ред. Е.Э. Фельдштейна - Мн.: дизайн ПРО 2002. – 320с.
ГОСТ 3.1103-82 «Основные надписи».
ГОСТ 3.1407-86 «Формы и требования к заполнению и оформлению документов на технологические процессы (операции) специализированные по методам сборки».
ГОСТ 3.1119-83 «Общие требования к комплектности и оформлению комплектов документов на единичные технологические процессы».
ГОСТ 3.1122-84 «Формы и правила оформления документов специального назначения».
ГОСТ 3.1105-84 «Формы и правила оформления документов общего назначения».
Рекомендуемые чертежи
- 11.12.2016
- 26.05.2014